
STROITEL_NOE_MATERIALOVEDENIE_RYB_EV
.pdfжелезо углерода с получением железоуглеродистого сплава, именуемого чугуном, твердость повышается до 210—410, при сплаве железа с углеродом и хромом в виде инструментальной стали твердость составляет 450—700. В сплавах могут улучшаться и другие ценные для практики свойства, поэтому в строительстве в основном используют черные сплавы — стали и чугуны, из цветных — алюминий и сплавы на его основе.
541
19.2. ОСНОВЫ ПОЛУЧЕНИЯ ЧУГУНА И СТАЛИ
Все металлы получают из руд, залегающих в земной коре. В чистом (самородном) виде добывают только платину и золото. Вначале требуется из руды удалить пустую породу, т. е. примеси различных минералов. Процесс обогащения руды возможен с помощью воды, так как руда тяжелее пустой породы и при измельчении в потоке воды легкая порода выносится, а руда остается. Применяют и другие способы обогащения руды: механические, электромагнитные, физико-химические. Для выделения металла из обогащенной руды используют технологические приемы, основанные на восстановлении металла. Хорошим восстановителем служит уголь, так как атомы углерода относительно легко отдают свои электроны.
19.2.1. ПОЛУЧЕНИЕ ЧУГУНА
Для выплавки железа из руды разработан доменный процесс с получением в нем чугуна, поступающего затем на выработку стали. Домна — высокая шахтная печь высотой до 30 м, шириной более 6 м. Стенки доменной печи выложены из огнеупорного кирпича, а снаружи кладка заключена в стальной кожух толщиной 20—40 мм. Загрузка рудой, коксом, флюсом послойная, причем обычно железорудный материал переводится в сыпучий агломерат. Схема работы доменной печи (рис. 19.1): в нижней части домны сгорает кокс: С + О2 = СО2. Углекислый газ, поднимаясь, соприкасается с раскаленным коксом и переходит в оксид углерода: СО2 + С = 2СО. Еще выше в шахте оксид углерода взаимодействует с раскаленной рудой: СО + Fe2O3 = 2FeO + СО2 и далее: FeO + СО = Fe + CO2. Чугун стекает в нижнюю часть домны. Из домны чугун выпускают через спе- циальное отверстие — летку. Первые капли чугуна образуются при температуре 1250°С и стекают между кусками кокса в горне. Температура чугуна в домне равна 1480—1520°С. Содержание углерода в чугуне составляет 4—4,5%.
Флюсы играют роль плавня, способствуя переводу пустой породы в шлак. Доменный шлак с содержанием в нем СаЗЮз легче чугуна и собирается выше его с последующим выпуском наружу из другого отверстия домны. Он служит ценным сырьем для производства различных строительных материалов.
Выделяющиеся из домны газы, именуемые колошниковыми, содержат оксид углерода СО, поэтому как сгорающее топливо направляются для обогрева каналов кауперов домны и воздуха в них, который затем поступает в доменную печь и поддерживает в ней горение кокса. Каупер сложен из огнеупорного кирпича и заключен в железный кожух. Имеет нагреваемую насадку.
542
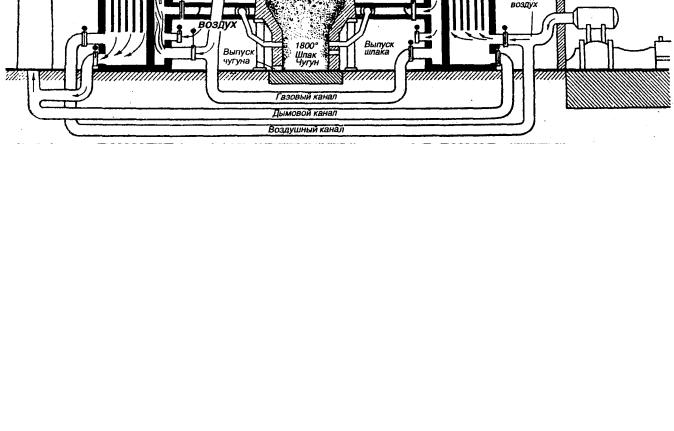
Рис. 19.1. Схема работы доменной печи
Запущенная в действие доменная печь функционирует непрерывно в течение нескольких лет. Руду, кокс и флюсы периодически добавляют через верхнее отверстие (колошник) печи. Также периодически производится выпуск из нее чугуна и шлака — через каждые 4—6 ч. При этом 99—99,8% железа переходит в чугун и только 0,2—1,0% — в шлак. Кроме углерода в составе чугуна присутствуют элементы кремния, марганца, серы, фосфора и пр. По назначению доменные чугуны разделяют на литейный и передельный. Литейный чугун переплавляют, и из него отливают чугунные изделия. Из передельного чугуна получают сталь. Он составляет около 90% всей выплавки чугуна. В нем содержится повышенное количество углерода, 0,3—1,2% Si, 0,2—1,0% Мn, 0,2—1,0% Р,
0,02—0,07% S.
Современная доменная печь может выплавлять 12000 т чугуна и выдает около 4000 т шлака, а также до 27000 т колошникового газа в сутки. Кроме процесса, осуществляемого в домне, существует вне-доменное производство железа, что относится к более прогрессивному способу. Он заключается в непосредственном получении железа из руды, минуя доменную печь. На производстве получают очень чистое металлическое железо без применения кокса. С этой целью при глубоком обогащении железных руд изготовляют концентраты с высоким содержанием железа (70—71,8%), почти полностью осво- божденные от серы и фосфора. Затем действуют твердым или газообразным восстановителем, получая металлизованные окатыши. Если используют твердый восстановитель — углерод (в виде каменного угля), тогда — с обжигом в шахтной печи, трубчатой печи, реторте. Если используют газообразный восстановитель — природный газ, тогда — с конвертированием газа в невысоких шахтных печах или ретортах. Способы металлизации могут быть и иными — в кипящем слое на решетке. Вследствие относительно низкой температуры бездоменного процесса получаемое железо, обычно спеченное в куски, содержит меньше примесей. Чугуны обладают высокими литейными свойствами, малой пластичностью. Они разделяются на белый и серый.
543
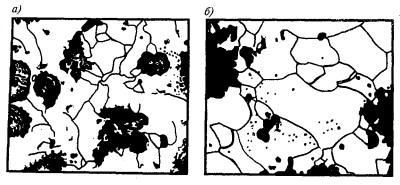
Белый чугун (передельный) содержит весь углерод в химически связанном состоянии в виде карбида железа, именуемого цементитом РезС. При нормальной температуре его структура слагается из двух фаз: феррита и цементита. Белым этот чугун называется потому, что в изломе он имеет матово-белый цвет. Белый чугун имеет высокую твердость и большую хрупкость, вследствие чего его невозможно обрабатывать режущим инструментом. Его применяют, главным образом, для выплавки стали, а также для получения ковкого чугуна.
Серые чугуны содержат углерод в свободном состоянии в виде графита (100% С); они называются серыми потому, что вследствие наличия в них графита имеют в изломе серый цвет. Содержание С — до 3,8%.
По форме графитовых включений серые чугуны разделяют на обычный серый с пластинчатым графитом, вермикулярный серый, высокопрочный и ковкий. По структуре металлической основы их разделяют на ферритный, ферритно-перлитный и перлитный.
Обычный серый чугун получают медленным охлаждением жидкого расплава или аустенита высокоуглеродистых сплавов. В нем частицы графита имеют пластинчатую форму. В зависимости от механических свойств и назначения серый чугун с пластинчатым графитом разделяют на марки: СЧ-25, СЧ-30, СЧ-35, СЧ-40, СЧ-45 (цифры показывают минимальный предел прочности при растяжении, кгс/мм2).
Вермикулярный серый чугун получают путем специальной плавки или обработки с изменением формы графита на волокнистую, червеобразную (вермикулярную), вследствие чего этот чугун обладает лучшими свойствами по сравнению с обычным серым чугуном. Высокопрочный чугун содержит шаровидный графит (рис. 19.2, а), получаемый при выплавке с присадкой небольшого количества магния или церия. Благодаря шаровидной форме графита прочность при растяжении и изгибе высокопрочного чугуна значительно выше, чем обычного серого чугуна с пластинчатым графитом.
Высокопрочный чугун разделяют на марки: ВЧ38-17, ВЧ42-12, ВЧ45-5, ВЧ50-2, ВЧ50-7, ВЧ70-2, ВЧ80-2, ВЧ100-2, ВЧ120-2. Буквы ВЧ означают высокопрочный чугун, первые числа за ними — минимальный предел прочности при растяжении (в кгс/мм2), а последующие числа — минимальное относительное удлинение (в %).
Рис. 19.2. Микроструктура высокопрочного ферритного чугуна с шаровидным графитом (а) (х250) и ковкого ферритного чугуна с хлопьевидным графитом (б) (х500)
Ковкий чугун содержит хлопьевидный графит (рис. 19.2, б). Его получают из белого чугуна путем графитизирующего отжига (томления), при котором происходит распад цементита. Хлопьевидный графит имеет почти равноосную компактную форму. Этот чугун разделяют на марки: КЧ3О-6, КЧ33-8, КЧ35-10, КЧ37-12, КЧ45-6, КЧ50-4, КЧ60-3,
КЧ63-2. В обозначение марки входят буквы КЧ (ковкий чугун), затем число — минимально допустимый предел прочности при растяжении (кгс/мм2), второе число — относительное удлинение (%).
544
Свойства серых чугунов зависят от свойств металлической основы, вида и количества графитных включений.
Графит имеет низкие показатели механических свойств, и включения его можно условно рассматривать как пустоты и трещины. Чем больше графита, крупнее графитные включения, тем ниже механические свойства чугуна и особенно прочность при растяжении и изгибе. Прочность при сжатии и твердость чугуна зависят в основном от металлической основы и мало отличаются от сталей.
Внекоторых случаях графитные включения полезны благодаря смазывающему действию графита. Такой чугун легче обрабатывается резанием, чем сталь, стружка становится ломкой, когда резец доходит до графитных включений.
Подобно другим железоуглеродным сплавам, чугуны содержат постоянные примеси кремния, марганца, серы и фосфора в больших количествах, чем в сталях. Эти примеси оказывают значительное влияние на графитизацию, структуру и свойства чугунов.
Вчугуны часто вводят также медь, алюминий, титан, хром, никель. Эти элементы оказывают влияние на процесс графитизации. Подобно сталям такие чугуны называют легированными.
Серые чугуны применяют при изготовлении опорных элементов для ферм, железобетонных балок и колонн, тюбингов в метро, при производстве многих других строительных конструкций, а также находят широкое применение в деталях машин, не подвергающихся большим растягивающим напряжениям и ударным нагрузкам.
545
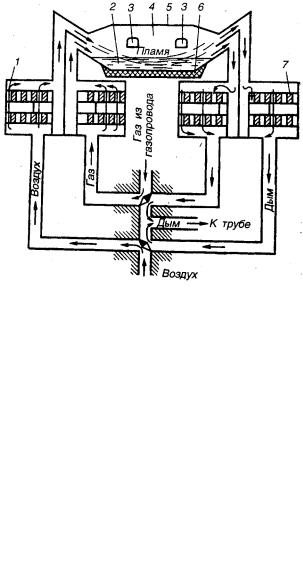
19.2.2. ПОЛУЧЕНИЕ СТАЛИ
Переработка передельного чугуна осуществляется с целью получения стали в результате освобождения его от некоторой части углерода методом окисления. При этом сталь может производиться тремя методами: конверторным — продувкой расплавленного чугуна сжатым воздухом или кислородом в больших грушевидных сосудах — конверторах с различной внутренней огнеупорной футеровкой (рис. 19.3); мартеновским — в печах Сименса-Мартена (рис. 19.4) с регенерацией тепла отходящих газов; электроллавкой — в электродуговых, индукционных или высокочастотных печах (рис. 19.5). При плавке в мартеновских печах или при электроплавке добавляется в расплавленный чугун железная руда или скрап (отходы ржавого железа, железный лом). Кислород добавляемых оксидов также выжигает примеси, а железо понижает содержание углерода в общей массе металла. Можно переплавлять в печи и железный лом, превращая его в продукт, годный к вторичному употреблению, что экономически весьма выгодно. При использовании железа, спеченного в куски при бездоменном производстве, сталь получают насыщением его углеродом с помощью переплавки с чугуном. Полученные тем или иным методом углеродистые стали с содержанием углерода до 1,3% широко используют в машиностроении, на транспорте, в строительстве и т. п.
Рис. 19.3. Конвертор для выплавки стали из чугуна:
1 — чугун; 2 — набойка; 3 — воздух; 4 — дутье; 5 — фурмы для подачи воздуха в металл
Рис. 19.4. Схема мартеновской печи 1,7 — регенераторы; 2 — расплавленные шлак и металл; 3 — завалочные окна; 4 — рабочее пространство; 5
— свод; 6 — под
546
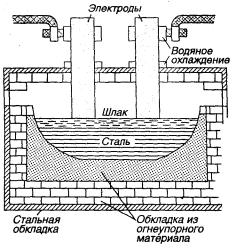
При производстве стали часто добавляют в печь легирующие вещества (металлы), получая специальные сорта стали с необходимыми свойствами, например хромонике — левую (нержавеющую) сталь и др. Упрочненные низколегированные стали, содержащие хром, никель, марганец, кремний, выпускают в качестве массовых технических материалов, тогда как специальные сорта с повышенной прочностью, жаростойкостью, коррозиестойкостью и другими улучшенными свойствами содержат увеличенное количе- ство легирующих компонентов. Нередко в качестве легирующего компонента выступает и железо в сплавах на основе алюминия, меди и других металлов.
Рис. 19.5. Схема электрической печи для выплавки специальных сталей
В конверторах выплавляется более 50% в мире стали, причем эта доля стали, выплавляемой высокопроизводительными методами (конвертор и электроплавка), имеет тенденцию к непрерывному увеличению, тогда как доля мартеновской выплавки постепенно уменьшается. У нас в стране на долю углеродистых сталей приходится около 90%, а легированных — 10%. Качество тех и других обусловлено в основном их составом и структурой как железоуглеродистого сплава. В нем железо образует термодинамически неустойчивое химическое соединение с углеродом Fe3С, называемое цементитом. Значительная часть железа находится в чистом виде с температурой плавления 1539°С. Железо имеет четыре полиморфные модификации: α-Fe, β-Fe, γ-Fe и δ-Fe, Практическое значение имеют модификации α-Fe и γ-Fe. Переход железа из одной модификации в другую происходит при определенных критических температурах. Модификация α-Fe имеет кубическую объемно-центрированную кристаллическую решетку, γ-Fe — кубическую гранецентрированную кристаллическую решетку. Переход железа из одной аллотропической формы в другую схематически показан на кривой охлаждения (рис. 19.6). В процессе охлаждения расплавленного железа при температуре 1535°С образуется площадка, характеризующая формирование кристаллической модификации δ-Fe; при температуре 1392°С происходит полиморфная модификация δ-Fe в модификацию γ-Fe, которая при температуре 898°С переходит в модификацию β-Fe; при температуре 768°С модификация β-Fe переходит в модификацию α-Fe. Изучение этих четырех форм сущест- вования кристаллического железа показало, что в модификации γ-Fe имеется межатомное расстояние в кристаллической решетке, меньшее, чем в модификации β-Fe, и поэтому переход γ-Fe в β-Fe сопровождается увеличением объема кристалла. Отмечено, что модификация α-Fe обладает магнитными свойствами (ферромагнит), тогда как модификация β-Fe этими свойствами почти не обладает, хотя кристаллические решетки их сходны между собой.
547
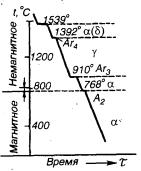
Рис. 19.6. Кривая охлаждения железа
Большое значение для практики имеет свойство модификации γ-Fe растворять до 2,14% углерода при температуре 1147°С с образованием твердого раствора и с внедрением атомов углерода в кристаллическую решетку. При повышении и понижении температуры растворимость углерода в модификации γ-Fe уменьшается. Твердый раствор углерода и других элементов (азот, водород) в модификации γ-Fe называется аустенитом (по имени ученого Р. Аустена), почти в 100 раз меньше углерода может раствориться в модификации α-Fe, причем твердые растворы углерода и других элементов в модификации α-Fe называют ферритом.
Кроме твердых растворов в железе, в железоуглеродистых сплавах может быть, как отмечено выше, химическое соединение железа с углеродом — карбид железа Fe3C. Это соединение, называемое цементитом, содержит 6,67% углерода, имеет сложное кристаллическое строение с плотноупакованной ромбической кристаллической решеткой. В сплавах цементит является метастабильной фазой. Его температура плавления равна примерно 1500°С. Он хорошо растворим в модификации γ-Fe, меньше — в δ-Fe и совсем мало — в α-Fe.
Феррит отличается мягкостью и пластичностью, его прочность сравнительно невысока предел прочности при растяжении 250 МПа, относительное удлинение 50%, твердость НВ составляет 800 МПа. Аустенит также имеет высокую пластичность, низкий предел прочности при растяжении. Твердость аустенита НВ 1700— 2200 МПа. Цементит обладает низкой пластичностью и высокой твердостью НВ, равной 10000 МПа, хрупкий.
548
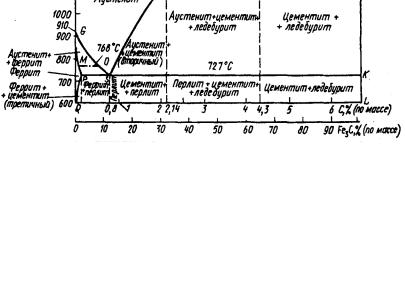
19.3. ДИАГРАММА СОСТОЯНИЯ ЖЕЛЕЗОУГЛЕРОДИСТЫХ СПЛАВОВ
Более полную систему железоуглеродистых сплавов и процессов формирования структур сталей и чугунов в наглядной форме представляют на диаграмме состояния железоуглеродистых сплавов. В частности, наглядно видно, как изменяется растворимость цементита в железе в зависимости от температуры.
На диаграмме (рис. 19.7) даны фазовый состав сплавов и их структура в интервале по составу от чистого железа до цементита (6,67% С). На оси абсцисс показано содержание углерода (С) в процентах по массе, на параллельной ей линии — содержание цементита, на оси ординат — температура.
Точка А на диаграмме отмечает температуру плавления чистого железа (1539°С), а точка D — цементита (1500°С). Линия ABCD является линией ликвидуса, a AHIECF — линией солидуса. Выше линии солидуса существует жидкий сплав (Ж) — жидкий раствор угле- рода в железе.
При охлаждении жидких сплавов сначала происходит кристаллизация, а затем после отвердевания — фазовые структурные превращения вследствие полиморфизма железа и изменения растворимости углерода в аустените и феррите. Все эти изменения наблюдаются на диаграмме железо — углерод, причем эту сложную диаграмму при ее изучении разделяют на части, рассматривая каждую из них как двухкомпонентную диаграмму.
Рис. 19.7. Диаграмма состояния железоуглеродистых сплавов
По содержанию углерода железоуглеродистые сплавы разделяют на стали, содержащие до 2,14% углерода, и чугуны с содержанием углерода более 2,14%. Принятая граница между сталями и чугу-нами соответствует наибольшей растворимости углерода в аустените.
Стали по содержанию углерода разделяют на доэвтектоидные, эвтёктоидные и заэвтектоидные.
Доэвтектоидными называют стали, содержащие 0,02—0,8% углерода. Весьма малоуглеродистые сплавы, содержащие до 0,02% (на диаграмме точка Р), называют техническим железом.
Кристаллизация доэвтектоидных сталей происходит между линиями ABC и АШЕ, и в этом интервале они состоят из жидкой фазы и феррита или аустенита. После окончания кристаллизации доэвтектоидные стали состоят из аустенита, не изменяющегося при ох- лаждении вплоть до линии GOS, именуемой линией верхних критических точек и обозначаемой через AC1. При дальнейшем охлаждении сталей образуются зерна феррита, а количество аустенита уменьшается.
549
На линии PSK при температуре 727°С происходит эвтектоидное (перлитное) превращение аустенита (точка S). Последний распадается, выделяя феррит и цементит, которые образуют эвтектоидную мельчайшую смесь — перлит, содержащий 0,8% углерода. Линия PSK называется линией нижних критических точек или линией перлитных превращений и обозначается через Ас\.
Структура перлита состоит из пластинок феррита и цементита, а на микрошлифе имеет вид перламутра (отсюда название перлита). После полного охлаждения доэвтектоидные стали состоят из феррита и перлита. С увеличением содержания углерода в стали снижает- ся количество феррита, но возрастает содержание перлита.
Заэвтектоидными называют стали, содержащие 0,8—2,14% углерода. При температурах выше линии SE находится в стали только аустенит. С охлаждением эта структурная составляющая стали становится насыщенной углеродом и из нее выделяется вторичный цементит (ниже линии SE). От температуры 727°С и ниже заэвтектоидные стали состоят из перлита и вторичного цементита.
Чугуны по содержанию углерода разделяют на доэвтектические, эвтектические и заэвтектические.
Доэвтектическими называют чугуны, содержащие 2,14—4,3% углерода. На диаграмме они располагаются в области между линиями ВС и ЕС; состоят из двух фаз — жидкости и кристаллов аустенита. При температуре эвтектики, равной 1147°С, оставшийся жидкий сплав кристаллизуется с превращением в эвтектику — ледебурит, которая в момент образования состоит из аустенита и цементита. Доэвтектические чугуны между линиями ЕС (1147°С) и PSK (727°С) состоят из аустенита, цементита и ледебурита. При температуре ниже 727°С аустенит превращается в перлит, а доэвтектические чу-гуны содержат перлит, цементит и ледебурит. С увеличением количества углерода в чугунах уменьшается содержание перлита и увеличивается — ледебурита.
Эвтектическим называют чугун при содержании углерода в количестве 4,3% (точка С); он кристаллизуется при постоянной температуре 1147°С с образованием эвтектики — ледебурита. Эвтектический чугун и при обычной температуре состоит из ледебурита.
Заэвтектияескими называют чугуны с содержанием углерода 4,3—6,67%. Они кристаллизуются по диаграмме состояния сплавов между линиями CD и CF с образованием в жидком сплаве кристаллов первичного цементита. При дальнейшем охлаждении оставшаяся жидкость затвердевает, образуя эвтектику — ледебурит. Заэвтек- тические чугуны после отвердевания состоят из цементита и ледебурита. При температуре 727°С входящий в ледебурит аустенит распадается с образованием перлита; при дальнейшем снижении температуры заэвтектические чугуны состоят из цементита (в виде пластин) и ледебурита. С увеличением количества углерода возрастает и содержание цементита.
550