
STROITEL_NOE_MATERIALOVEDENIE_RYB_EV
.pdf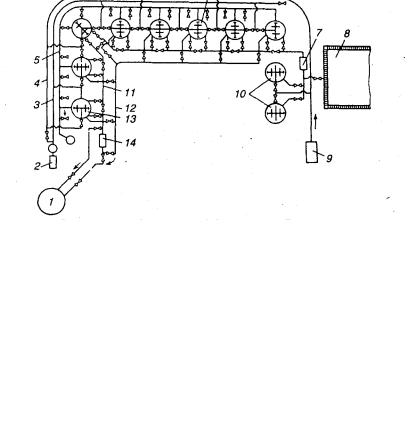
Рис. 10.1. Технологическая схема производства окисленного битума: a — в установках периодического действия: 1 — битумный куб; 2 — труба для отвода отработанного воздуха и газа; 3 — труба для подачи воздуха; 4 — компрессор; 5 — воздушная магистраль; 6 — насосы; 7 — магистраль для подачи битума; 8 — холодильник для охлаждения битума; 9 — маточник; 10 — газосборник; 11 — дымовая труба; 12 — теплообменник (емкость) для тяжелого нефтяного остатка; 13 — магистраль для подачи гудрона; 14 — раздаточник; б — в установках непрерывного действия: 1 — емкость для сырья; 2 — компрессорная установка; 3 — воздушная магистраль; 4 — паровая магистраль; 5 — обратная воздушная магистраль с ловушками; 6 — битумные кубы; 7 — насос; 8—аварийная емкость; 9 — парообразователь; 10 — раздаточник; 11 — подающая магистраль; 12 — обратная магистраль; 13 — насос; 14 — куб
Газы и пары выбрасываются в атмосферу, а окисленный битум стекает в приемный бак. Продолжительность окисления намного сокращается по сравнению с другими способами производства, а качество битума выше, чем при окислении в кубах.
Производство крекинговых битумов, которые тоже могут быть остаточными и окисленными, основано на расщеплении сырья при высоких температурах (до 450°С) и давлении (до 5 МПа). Мазут распадается на более легкие и устойчивые углеводороды и на менее легкие и неустойчивые углеводороды и их производные. Неустойчивые углеводороды в процессе полимеризации образуют асфальтено-смолистые вещества. Остаточные крекинг-битумы получают путем перегонки под вакуумом крекинг-остатков; окисленные — окислением тех же остатков в кубовых или трубчатых установках воздухом по технологическим схемам, принятым для производства обычных нефтяных битумов из гудронов.
361
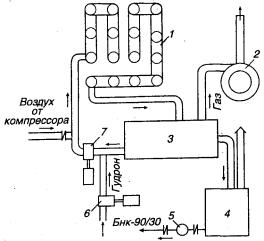
Рис. 10.2. Технологическая схема окисления битума на непрерывно-действующей трубчатой установке: 1 — реактор; 2 — циклонная печь для сжигания газа; 3 — сепаратор; 4 — продуктовый бак; 5 — продуктовый насос; 6 — насос сырьевой паровой; 7 — насос циркуляционный паровой
Битумы деасфальтизации получают из гудрона, обрабатываемого предварительно пропаном или дихлорэтиловым эфиром (хлорек-сом). С помощью такой обработки из масляного гудрона извлекается дополнительное количество горюче-смазочных фракций, тогда как асфальтены и тяжелые смолы оседают, образуя экстракт с малым содержанием масел. Из этого экстракта испаряют растворитель и получают битум, именуемый экстрактным (или битумом деасфальтизации). Он отличается невысоким качеством, имеет повышенную хрупкость при низких температурах. Для уменьшения вязкости этих битумов приходится перед употреблением смешивать их с гудроном.
Состав, структура и свойства битумов (природных и нефтяных) имеют некоторые непринципиальные различия. Вместе с тем, они характеризуются сложным и многообразным составом основных углеводородов, главным образом метанового (CnH2n+2), нафтенового (CnH2n) и ароматического (CnH2n-6) рядов. В состав основных угле- водородных соединений битума обычно входят также кислород, азот, сера, ванадий, железо, никель и другие элементы. Основная часть молекул битума состоит из 25 — 150 атомов углерода. В зависимости от числа атомов в молекулах и их взаимного расположения изменяются свойства вещества. Например, чем больше молекулярная масса одного и того же соединения, тем сильнее в нем межмолекулярное взаимодействие. Молекулярная масса молекул битумов составляет 400—5000. Ароматические углеводороды имеют повышенную устойчивость при воздействии теплоты, кислорода и ультрафиолетовых лучей; их окисление сопровождается образованием смол. Метановые углеводороды (парафины) представляют собой прямые цепи, состоящие из многократно повторяющихся звеньев -СН2- с метальными группами –СН3, при отрицательных темпера- турах способны выкристаллизовываться, ухудшая свойства битумов. Нафтеновые углеводороды при окислении частично переходят в смолы.
Элементарный состав битумов колеблется в пределах: С — 70—87%, Н — 8—12%,, О — 0,2—12%, S — 0,5—7%, N — до 1%. В нефтяных битумах содержание кислорода меньше (до 2%), чем в природных, а содержание углерода изменяется в меньших пределах (84— 87%); кислород, сера, азот входят в состав активных функциональных групп: ОН, N2H, SH, СООН. В целом, однако, элементарный состав дает лишь весьма приближенное представление о свойствах битумов, поэтому чаще пользуются групповым составом. Разделение битума на отдельные группы соединений, близких по строению и свойствам, основано на неодинаковой растворимости их в растворителях (бензоле, сероуглероде и др.), а также различной избирательной адсорбируемости силикагелем, флоридином и другими адсорбентами.
362
В групповой состав битума входят масла, извлекаемые растворением их в петролейном эфире или легком бензине. Масла состоят из углеводородов парафинового, нафтенового и ароматического рядов относительно несложного строения с молекулярной массой 300— 600. Они имеют светло-желтый цвет и придают битуму подвижность и текучесть. Истинная плотность менее 1 г/см3. Содержание масел в битумах 35—60% (по массе). Отношение количеств С:Н характеризует степень ароматичности и составляет для группы масел 0,55—0,60.
Вторым групповым компонентом битумов являются смолы. Они состоят из углеводородов циклического и гетероциклического строения с молекулярной массой 600—1000, имеют темно-коричневый цвет, истинную плотность, равную примерно 1 г/см3. Содержат наибольшее количество сернистых, азотистых и кислородных произ- водных углеводородов (эти соединения полярны), что придает им поверхностную активность, а битуму — улучшение адгезии к каменным материалам, которые участвуют в ИСК в качестве зернистых материалов (заполнителя). Величина С:Н составляет 0,6—0,8. Смолы хорошо растворяются в бензоле, хлороформе и представляют собой легкоплавкие, вязкопластичные вещества. Их присутствие при дает битуму эластичность, водоустойчивость. Содержание смол в битумах 20—40% (по массе).
Асфальтены — твердые неплавкие вещества с плотностью немного более 1 г/см3, их молекулярная масса составляет 1000—5000. Они растворимы в хлороформе, горячем бензоле и четыреххлори-стом углероде, но не растворимы в легком бензине. В асфальтенах атомное отношение С:Н составляет 0,8—1,0. Их содержание повышает температуростойкость, вязкость и твердость битумов. Обычно в битумах содержится 10— 40% (по массе) асфальтенов. Под действием ультрафиолетовых лучей они становятся нерастворимыми в бензоле, переходя в карбены.
Карбены и карбоиды содержатся в основном в крекинг-битумах в количестве 1—3%. Карбены по своим свойствам и составу близки к асфальтенам, но содержат больше углерода и имеют большую плотность. Они не растворяются в горячем бензоле и четыреххлористом углероде, растворимы только в сероуглероде. Карбоиды — твердые вещества, нерастворимые в известных растворителях. С увеличением содержания карбенов и карбоидов увеличивается вязкость и хрупкость битумов. Эти твердые вещества в битумах относятся к кислород- и серосодержащим полициклическим соедине- ниям.
Асфалътогеновые кислоты хорошо растворяются в этиловом спирте, являются полярными и выполняют функции поверхностно-активных веществ. К этой же группе относят ангидриды асфальтогеновых кислот. Общее содержание асфальтогеновых кислот и их ангидридов в битумах до 3%. Они способствуют высокой адгезии битумов к каменным материалам.
Парафины относятся к твердым метановым углеводородам, они ухудшают свойства битумов. Особенно неблагоприятное влияние оказывают крупнокристаллические парафины (снижается пластичность и увеличивается хрупкость битумов). Содержание парафинов в битумах может составлять 6—8%.
По внутреннему строению битум представляет собой сложную коллоидную систему, дисперсионной средой в которой является раствор смол в маслах, а дисперсной фазой — асфальтены, карбены и карбоиды, коллоидно-растворенные в среде до макромолекул раз- мером 18—20 мкм. В пограничной зоне адсорбированы асфальтогеновые кислоты, плотно удерживаемые на макромолекулах асфальтенов.
Под влиянием солнечной радиации, высоких температур, кислорода воздуха групповой состав битумов изменяется за счет химического перехода масел в смолы, а смол — в асфальтены. Групповые углеводороды входят в состав битумов в различных соотношениях их масс, что, естественно, предопределяет их структуру и свойства. Структура битумов становится то типа золь, с малой вязкостью, то более плотной типа гель, с повышенной вязкостью, что зависит и от температуры битума. При нагревании или
363
увеличении содержания масел структура гель переходит в золь. Вязкость битумов при их нагревании быстро изменяется — падает.
Твердые битумы (типа гель) характеризуются условно глубиной проникания стандартной иглы при действии на нее груза массой 100 г в течение 5 с при температуре 25°С или 200 г в течение 60 с при 0°С; она выражает величину, обратную вязкости, т. е. текучесть, и определяется пенетрометром в градусах. Каждый градус означает погружение иглы на 0,1 мм. При температурах 25°С пенетрация вязких и твердых битумов П25 = 5—300. Условная вязкость жидких битумов (типа золь) характеризуется временем истечения определенного количества битума (50 см3) через отверстие вискозиметра при одной-двух стандартных температурах, а именно: C255 и С605. Здесь верхний индекс — величина диаметра (в мм) стандартного отверстия, нижний — температура испытания.
Кроме пенетрации, у вязких и твердых битумов определяют еще пластичность и температуру размягчения. Пластичность определяют по растяжимости образцов- восьмерок на специальном приборе — дуктилометре при температурах — 25 и 0°С (для улучшенных битумов). Температура размягчения отражает переход битума из твердого или вязкопластического состояния в жидкое. Она определяется по методу «Кольца и шара». По особой методике нередко фиксируют также температуру перехода битума в хрупкое состояние (прибор Фрааса). По разности температур размягчения и хрупкости судят о качестве битумного материала: чем больше интервал этих температур (именуемый как интервал пластичности), тем выше качество. О теплоустойчивости битума судят по индексу пенетрации (ИП).
Существенной особенностью битумов является их высокая адгезия — прилипание к поверхности минеральных и органических материалов. Разработано несколько методов и приборов для определения адгезии. По визуальному методу степень прилипания битума к каменному материалу оценивается по пятибалльной шкале. Если пленка битума на поверхности гравия или щебня полностью сохранилась после кипячения в дистиллированной воде, прилипание битума отличное и оценивается 5 баллами; если пленка битума после кипячения полностью смещается с минеральных зерен и всплывает на поверхность воды, прилипание очень плохое и оценивается в 1 балл.
В зависимости от показателей основных свойств вязкие (твердые) нефтяные битумы подразделяют на марки. Битумы нефтяные (БН) вырабатывают четырех марок: БН 60/90, БН 90/130, БН 130/200, БН 200/300. Цифры дроби указывают на допустимые для данной марки пределы показателей пенетрации при 25°С. Битумы нефтяные дорожные выпускают пяти марок: БНД 40/60, БНД 60/90, БНД 90/130, БНД 130/200 и БНД 200/300.
Битумы марок БНД отличаются хорошим сцеплением с каменными материалами имеют
достаточно высокую пластичность при отрицательных |
температурах, проявляют |
стойкость к климатическим воздействиям. |
|
Для изготовления кровельных и гидроизоляционных материалов применяют битумы марок БНК 45/180 (пропиточные), БНК 90/40 и БНК 90/30 (покровные). Числитель дроби указывает среднее значение показателей температуры размягчения (в °С), знаменатель — среднее значение показателей пенетрации при температуре 25 °С (табл. 10.1-10.3). Предусмотрены марки нефтяных битумов и для некоторых других технологий — при изоляции трубопроводов от коррозии (марки БНИ), для строительных целей (марки БН), для приклеивания и окраски при устройстве гидроизоляции и изготовления лаков повы- шенной теплостойкости (марки улучшенных битумов, полученных с помощью особой химической обработки и т. п.).
Таблица 10.1. Характеристика битумов нефтяных дорожных (БНД) (ГОСТ 22245—76)
|
Нормы для марки |
|
|
|
|
Показатели |
БНД— |
БНД— |
БНД— |
БНД— |
БНД— |
|
130/200 |
200/300 |
90/130 |
«0/90 |
40/60 |
Глубина проникания иглы, мм: |
|
|
|
|
|
|
|
|
|
|
|
|
|
|
|
|
364 |
при 25°С |
|
201—300 |
131—200 |
91—130 |
61—90 |
40—60 |
при 0°С, не менее |
|
45 |
35 |
28 |
20 |
13 |
Температура размягчения |
по |
35 |
39 |
43 |
47 |
51 |
«Кольцу и шару», °С, не ниже |
|
|
|
|
|
|
Растяжимость, см, |
|
|
|
|
|
|
не менее: |
|
|
|
|
|
|
при 29°С |
|
— |
65 |
60 |
50 |
40 |
при 0°С |
|
20 |
6 |
4,2 |
3,5 |
— |
Таблица 10.2. Характеристика битумов нефтяных строительных (ГОСТ 6617—76)
Показатели |
Нормы для марки |
|
||
БН 50/50 |
БН 70/30 |
БН 90/10 |
||
|
||||
Глубина проникания иглы при 25°С, мм |
41—60 |
21—40 |
5—20 |
|
Температура размягчения по «Кольцу и шару», °С, не ниже |
50 |
70 |
90 |
|
Растяжимость при 25°С, см, не менее |
40 |
3 |
1 |
|
|
|
|
|
Таблица 10.3. Характеристика битумов нефтяных кровельных (ГОСТ 9548—74)
|
Нормы для марки |
|
||
Показатели |
БНК— |
БНК— |
БНК— |
|
|
45/180 |
90/40 |
90/30 |
|
Глубина проникания иглы при 25°С, мм |
140—300 |
35—45 |
25—5 |
|
Температура размягчения по «Кольцу и шару», |
||||
°С |
40—50 |
85—95 |
85—95 |
|
240 |
240 |
240 |
||
Температура вспышки, °С, не ниже |
||||
|
|
|
Кроме вязких (твердых) в строительстве используют жидкие битумы как подогретыми до температуры около 100°С, так и в холодном состоянии (температурой 15—20°С). Со временем жидкие битумы загустевают за счет испарения летучих фракций, окисления и других процессов. Важнейшие свойства жидких битумов: вязкость, скорость загустевания и свойства остатка после испарения летучих фракций, адгезия, температура вспышки, погодоустойчивость и др.
Взависимости от скорости загустевания жидкие битумы подразделяются на среднегустеющие (СГ), получаемые разжижением вязких дорожных битумов жидкими нефтепродуктами; медленногустеющие (МГ и МГО), получаемые из остаточных или частично окисленных нефтепродуктов или их смесей. Класс битума устанавливают по количеству испарившегося разжижителя при выдерживании образца битума в термостате или в вакуумтермостате при определенных температурах.
Взависимости от класса и вязкости жидкие битумы имеют марки: СГ 40/70, СГ 70/130, СГ
130/200, МГ 40/70, МГ 70/130, МГ 130/200, МГО 40/70, МГО 70/130, МГО 130/200.
Жидкие нефтяные битумы класса СГ приготовляют путем разжижения вязких битумов керосином, бензином, лигроином и др.; медленногустеющие битумы получают, применяя в качестве разжижителей масляные нефтепродукты, природные смолистые нефти, мазут и т. п. Медленногустеющие битумы могут быть природными — тяжелые смолистые нефти. При добавлении разжижителя происходит изменение дисперсной структуры вязкого битума. Некоторые разжижители могут вызвать коагуляцию дисперсной фазы битума и ухудшить его вяжущие свойства, поэтому разжижитель должен иметь требуемый фракционный состав и полярность, аналогичные вязкому битуму.
При приготовлении жидких битумов вязкие битумы нагревают до температуры 80—90°С, если применяют легкие разжижители, и до температуры 130—140°С — для тяжелых разжижителей; последние предварительно подогревают в отдельной емкости, а затем до- бавляют в разжижаемый битум при постоянном перемешивании смеси.
365
При нагревании жидких нефтяных битумов необходимо соблюдать требуемую температуру, предусмотренную нормативно-технической документацией для каждой марки, и более краткое выдерживание их при этих температурах. Требуется соблюдать также технику противопожарной безопасности. В качестве природных жидких битумов в строительстве используют тяжелые высокосмолистые нефти.
366
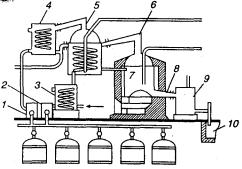
10.1.2. ДЕГТИ
Дегти — органические вяжущие вещества вязкой или жидкой консистенции, получаемые как побочный продукт при сухой (деструктивной, без доступа воздуха) перегонке твердых топлив (каменного или бурого угля, торфа, сланцев, древесины). Наибольшим распространением в строительстве пользуются каменноугольные дегтевые вяжущие вещества. Широко применяют также и сланцевые дегти, называемые сланцевыми битумами. Ниже рассмотрены технологии каменноугольных и сланцевых дегтей.
Производство каменноугольного дегтя. Вначале получают сырой каменноугольный деготь в процессе коксования или газификации угля, или полукоксования при выработке генераторного газа. С этой целью в коксовую печь загружают подготовленную шихту из обогащенных каменных углей разных марок. Шихту нагревают без доступа воздуха; коксование заканчивается при температуре 1100—1200°С после полного удаления из угля летучих веществ. В процессе коксования пары сырой каменноугольной смолы и ам- миачной воды улавливаются в холодильниках, где происходит их конденсация. Вместе с парами в холодильниках осаждаются мельчайшие твердые частицы угля и кокса. Далее продукты конденсации направляются в дегтеотстойники. В них частично сырая смола отделяется от аммиачной воды. Выход сырой смолы или сырого дегтя составляет до 5% массы коксуемого угля.
Вгазовых печах (ретортах) газификация каменного угля осуществляется при температуре 1250—1300°С, выход сырой смолы при этом еще меньше, чем при коксовании. Полукоксование шихты в печах производится при температуре 500—700°С с получением низкотемпературного сырого дегтя.
Сырой деготь содержит большое количество легколетучих и кристаллических, а также токсичных и окисляемых веществ, что приводит к резкому ухудшению его свойств во времени (старению). Поэтому его отправляют на дегтеперегонную установку. Технологи- ческая схема дегтеперегонной установки периодического действия показана на рис. 10.3.
Втеплообменник 5 загружают сырой деготь, и путем подогрева отходящими парами дегтевых масел до 80—100°С он частично обезвоживается. Далее этот деготь поступает в перегонный куб 7, где при подогреве из него выделяются пары масел, которые по шлемовой трубе 6 направляются в змеевик теплообменника. В холодильнике 3 происходит полная конденсация паров дегтя, после чего дистилляты поступают в сборники 1, в которых собирают фракции, отогнанные в определенных интервалах температур. После окончания перегонки в кубе остается пек, который через сливную трубу 8 выпускают в пекотушитель 9 (пеки легко воспламеняются уже при температуре 400°С). Охлажденный до 150°С пек поступает в пеко-вую яму или в тару. В сборник из теплообменника поступает конденсат, который образуется в холодильнике 4. Далее цикл повторяется.
Рис. 10.3. Технологическая схема дегтеперегонной установки периодического действия:
1, 2 — сборники продуктов перегонки; 3, 4 — водяные холодильники; 5 — тешюобменник-обеэвоживатель; 6 — шламовая труба; 7 — вертикальный куб; 8 — сливная труба; 9 — пекотушитель; 10 — пековая емкость
367
При непрерывном процессе перегонка сырого дегтя производится в вакууме. На таких установках кубы последовательно соединены трубопроводом, при этом деготь перемещается из одного куба в другой и в каждом кубе отгоняется определенная фракция. В последнем кубе собирается пек. Каменноугольные пеки выпускают двух видов: 1) среднетемпературный марок А и Б и 2) высокотемпературный (табл. 10.4).
368
Таблица 10.4. Технические характеристики каменноугольных пеков
Показатели |
|
Среднетемпературный |
Высокотемпературный |
|
|
А |
Б |
||
|
|
|
||
Внешний вид |
|
расплавленный или твердый в виде |
твердый в виде гранул |
|
|
чешуек или гранул черного цвета |
или чешуек черного цвета |
||
|
|
|||
Температура |
|
67—75 |
76—83 |
135—150 |
размягчения, |
°С |
|||
Зольность,%, не более |
|
0,4 |
0,4 |
0,4 |
|
|
|
|
|
Содержание воды, %, не |
4 |
|
3 |
|
более: в твердом |
|
0,5 |
|
— |
в жидком |
|
|
||
|
|
|
|
Истинная плотность пеков 1,1—1,26 г/см', температура вспышки в открытом тигле 170—
190°С.
Пеки не растворимы в воде, но хорошо растворяются в скипидаре сероуглероде и хлороформе, имеют достаточную стойкость к растворам солей и кислот, более гнилостойки, чем битумы. На основе пеков изготовляют приклеивающие мастики в гидроизоляционных работах. Для получения пека с повышенной температурой раз- мягчения проводят перегонку дегтя с рециркуляцией воздуха, при этом происходит отбор дистиллятов. Хлорирование и сульфирование пеков повышает их температуру размягчения до 140 С.
Свойства каменноугольных дегтей зависят от их состава и структуры Основным механическим свойством дегтей является вязкость, которая быстро снижается даже при незначительных повышениях температуры. Условная вязкость дегтей характеризуется временем истечения в секундах 50 мл дегтя через отверстие диаметром 5 или 10 мм при температуре 30 или 50°С. Вязкость дегтя определяют на стандартных вискозиметрах. В зависимости от вязкости дегти подразделяют на марки: Д-1, Д-2, Д-3, Д-4, Д-5, Д-6 (табл. 10.5.). Для получения дегтя требуемой вязкости нередко сплавляют два вида дегтя разной вязкости.
Таблица 10.5. Требования к каменноугольным дегтям
Показатели |
Нормы для марок |
|
|
|
|
||
Д-1 |
Д-2 |
Д-3 |
Д-4 |
Д-5 |
Д-6 |
|
|
|
|
||||||
Вязкость, с: |
|
|
|
|
|
|
|
C 5 |
5—70 |
— |
— |
— |
— |
— |
|
30 |
|
|
|
|
|
|
|
C10 |
— |
5—20 |
21— |
51— |
121— |
— |
|
30 |
|
|
50 |
120 |
200 |
|
|
|
|
|
|
|
|
|
|
C10 |
— |
— |
— |
— |
— |
100—80 |
|
50 |
|
|
|
|
|
|
|
Массовая доля воды, %, не более |
3 |
1 |
1 |
1 |
1 |
1 |
|
Массовая доля веществ, не растворимых в |
18 |
20 |
20 |
20 |
20 |
20 |
|
толуоле, %, не более |
|
|
|
|
|
|
|
Массовая доля фракций, %, перегоняемых |
|
|
|
|
|
|
|
до температуры, °С: |
|
|
|
|
|
|
|
170 |
3 |
2 |
1,5 |
1,5 |
1,5 |
1,5 |
|
270 |
20 |
20 |
15 |
15 |
15 |
10 |
или |
15 |
|
||||||
|
|
|
|
|
|
|
|
300 |
35 |
30 |
25 |
25 |
25 |
20 |
|
|
|
|
|
|
|
|
369 |
Температура размягчения остатка после |
45 |
65 |
65 |
65 |
65 |
70 |
отбора фракций до 300°С, не более |
|
|
|
|
|
|
Массовая доля фенола, %, не более |
5 |
3 |
2 |
2 |
2 |
2 |
Массовая доля нафталина, %, не более |
5 |
4 |
3 |
3 |
3 |
3 |
|
|
|
|
|
|
|
Как указывалось выше, дегти имеют повышенную способность к прилипанию благодаря большому количеству в их составе полярных групп веществ и фенолов. Однако фенолы токсичны, вымываются водой, поэтому их содержание ограничивают.
Биостойкость дегтей — высокая, цвет — черный, имеют специфический запах каменноугольной смолы, токсичны. Температура вспышкидегтей 150—190°С, температура воспламенения 180—270°С. Истинная плотность каменноугольных коксовых дегтей 1,1—1,3 г/см3, а газовых дегтей — 1,0—1,2 г/см3.
Низкая погодоустойчивость и старение дегтей происходят в связи с испарением летучих веществ; этому способствует также наличие в дегтях ненасыщенных высокомолекулярных углеводородов, которые окисляются и полимеризуются, и активных веществ. Со временем групповой состав дегтя изменяется, что приводит к потере им пластических свойств при пониженных температурах, увеличению хрупкости дегтевых материалов. Для установления стабильности свойств дегтя определяют его фракционный состав и проводят испытания остатка после нагревания до 300°С.
Погодоустойчивость и степень устойчивости к изменению вязкости дегтя оценивают по содержанию в нем легких, средних и тяжелых масел, которое определяется разгонкой пробы дегтя в специальном аппарате — стеклянном одношариковом дефлегматоре.
Температуру размягчения остатка, полученного после отгона фракций до 300°С, определяют так же, как и температуру размягчения битумов на приборе «Кольцо и шар». Для определения содержания фенолов в дегтях из фракции 170—270°С, полученной при перегонке пробы дегтя, извлекают фенолы щелочью и измеряют приращение объема щелочи. Определение нафталина заключается в измерении количества осадка, выде- лившегося при кристаллизации фракции 170—270°С.
С целью увеличения вязкости, повышения теплоустойчивости и улучшения других свойств в каменноугольную смолу или низкомарочный деготь при температуре 180— 200°С вводят серу и серосодержащие материалы. При этом происходит дегидратация углеводородов дегтя и изменяются межмолекулярные связи.
Улучшают качество дегтей введением минеральных дисперсных наполнителей в количестве до 30% (молотого известняка и доломита, каменноугольной и цементной пыли). Такие дегти называются наполненными. Их состав подбирают расчетом или
лабораторным путем. Наполненные дегти выпускают двух марок: ДН-7 вязкостью C1030 =
3—70 с и ДН вязкостью C1050 = 70—120 с.
Состав и структура каменноугольных дегтей и пеков. Дегти состоят из высокомолекулярных углеводородов в основном ароматического ряда и их производных, т. е. соединений углеводородов с серой, азотом и кислородом.
Дегти имеют переменный групповой состав в зависимости от сырья и технологии его переработки. Для определения группового состава деготь подвергают фракционной разгонке. В нем содержатся твердые, углистые неплавкие вещества, не растворимые в органических растворителях и называемые свободным углеродом, твердые неплавкие дегтевые смолы, растворимые только в пиридине; вязкопластичные плавкие дегтевые смолы, растворимые в бензоле и хлороформе, которые придают дегтям эластичность; жидкие дегтевые масла: легкие — с температурой кипения до 170°С, средние — 170— 270°С, тяжелые — 270—300°С и антраценовые — 300—600°С; твердый остаток свыше 360°С называется пеком (в древесных дегтях — варом).
370