
STROITEL_NOE_MATERIALOVEDENIE_RYB_EV
.pdf9.8.2. КРАТКИЕ СВЕДЕНИЯ ОБ ИСХОДНЫХ МАТЕРИАЛАХ
На действующих асбестоцементных заводах в качестве вяжущего используют клинкерный портландцемент марок 400 и 500. В нем не допускается содержание добавок, кроме гипса. Количество трех-кальциевого силиката (алита) должно быть не менее 52%, трехкальциевого алюмината — не более 8%, свободной извести — не более 1% (по массе). При автоклавном способе обработки изделий может применяться также песчанистый портландцемент, оптимальное содержание кварцевого тонкоизмельченного песка в котором зависит от количества трехкальциевого силиката в клинкере. С повышением содержания С3S в клинкере портландцемента увеличивается количество песка. Так, при выработке цемента с алитовым клинкером содержание песка доводится до 45%, а при белитовом клинкере — до 30—35%. Качество добавляемого песка регулируется — должно быть не менее 87% SiO2 и не более 3% оксидов калия и натрия, а количество пылевидных, илистых и глинистых примесей не должно превышать 10%, в том числе не более 3—5% глинистых частиц размером менее 0,005 мм. Для производства облицовочных изделий применяют белый и цветной портландцемент.
В производстве асбестоцементных изделий в нашей стране в основном используют хризотил-асбест. Он извлекается из серпентиновых пород, в которых расположен в виде жил. Среди крупнейших месторождений следует отметить Баженовское (Урал). Хризотил- асбест является водным силикатом магния — 3MgO·2SiO·2H2О. В нем почти всегда встречаются посторонние примеси — закисное железо, карбонаты, сульфаты и сульфиды. По структуре асбест — кристаллический минерал с ярко выраженным волокнистым строе- нием. Каждое кристаллическое волокно хризотил-асбеста состоит, в свою очередь, из огромного числа параллельно расположенных тончайших элементарных кристаллов — волоконец (фибрилл). В технологии асбестоцемента пользуются механическим распушением асбеста до разной степени тонкости волокон. Хризотил-асбест имеет высокую прочность на разрыв по оси волокнистости (до 26,0— 35,0 МПа) и достаточно высокую эластичность, хотя имеются также ломкие (хрупкие) разновидности, с пониженной прочностью на разрыв. По данным П.Н. Соколова, средние величины модулей упругости волокон хризотил-асбеста колеблются в пределах от 15,8·104 до 21·104 МПа. Волокна асбеста имеют поверхностный слой из гидроксильных групп, соединенных со смежным внутренним слоем из ионов магния, что придает поверхности высокую адсорбционную способность, а с водой легко образуют суспензию. Но количество адсорбированной воды на поверхности волокон асбеста сравнительно невелико — до 1,5—2,0%, поэтому при дозировании асбеста этой величиной обычно пренебрегают. Теплопроводность распушенного асбеста составляет 0,05—0,075 Вт/(м·К) в зависимости от его средней плотности, колеблющейся от 35 до 250 кг/м3. Асбест обладает разной длиной волокон — от долей миллиметра до 40 мм. По средней длине волокна и содержанию пыли асбест разделяют на сорта: средняя длина повышается от низшей марки 8-го сорта к высшей марке нулевого сорта.
Для производства асбестоцементных изделий применяют 3, 4, 5 и 6-й сорта асбеста. Более низкие сорта (7-й и 8-й) содержат очень короткие волокна (короче 1 мм), много пыли и «гали» (мелкие куски руды и породы), что снижает армирующие свойства асбеста, поэтому от их применения воздерживаются. Кроме сортности асбест разделяют по маркам. Каждому сорту соответствует несколько марок, отличающихся либо текстурой (полужесткая и мягкая в зависимости от степени расщепления или распушенности волокон в процессе обогащения), либо минимальным остатком (%) на верхнем сите специального контрольного аппарата. Чем выше сорт асбеста и жестче его текстура, тем выше качество изделий. Так, например, 3-му сорту по текстуре соответствуют три марки асбеста с полужесткой текстурой (П-3-70; П-3-60; П-3-50) и две марки с мягкой текстурой (М-3-70; М-3-60); 5-му сорту соответствуют четыре марки асбеста с полужесткой и четыре марки асбеста с мягкой текстурами и т. д.
341
Вода, используемая для распушки асбеста, промывочных работ и тем более для затворения цемента должна быть свободной от глинистых примесей, органических веществ или продуктов их разложения, минеральных солей. Ее температура в технологическом цикле обычно составляет 30—40°С. Нередко используют рекуперацион- ную воду, которая участвовала в предыдущих циклах технологического процесса. Ее отбирают из нижней части рекуператоров. В ней ограничивают содержание взвешенных веществ (например, не более 100 мг/л), величину рН (не менее 8,5).
Кроме трех основных компонентов в производстве асбестоце-ментных изделий применяют добавочные вещества — пластифицирующие, уплотняющие, гидрофобизирующие и др., а также пигменты для придания изделию определенной окраски. Особенно важно добавлять вещества, повышающие фильтруемость суспензии на стадии формования листов.
342
9.8.3. ОСНОВЫ ПРОИЗВОДСТВА АСБЕСТОЦЕМЕНТНЫХ ИЗДЕЛИЙ
Асбестоцементные изделия изготовляют в основном по мокрому способу формования. Значительно реже используют полусухой и сухой способы формования. Последний — при изготовлении только плоских листов и плиток.
Мокрый способ технологии начинается с составления смески из асбеста нескольких марок, с тем чтобы при формовании обеспечить высокую фильтрующую способность, плотность и водоудержание. После этого производится распушка волокон асбеста. Распушенный асбест тщательно перемешивают с цементом в воде до получения однородной массы. Последнюю разбавляют еще дополнительным количеством воды, в результате чего получается асбестоцементная суспензия, в которую, если требуется, могут вводиться добавочные вещества (добавки). В асбестоцементной суспензии масса воды бо- лее чем в 10 раз превышает массу цемента. Готовую суспензию направляют на формование асбестоцементных изделий — листов или труб. При этом большая часть (свыше 96%) свободной воды отфильтровывается и удаляется. Листам придают необходимые размеры и форму. Облицовочные листы и кровельные плитки дополнительно прессуют. Твердение вяжущей части, под влиянием которого асбестоцементные изделия приобретают требуемую механическую прочность, происходит на складах или в автоклавах (при песчанистом портландцементе). Готовым изделиям путем их окраски и лицевой обработки может быть придана необходимая внешняя поверхность.
К настоящему времени установились более или менее определенные составы (смески) асбеста разных месторождений при производстве асбестоцементных изделий. Они нормируются специальными технологическими картами.
Операция распушивания асбеста в значительной мере обусловливает качество продукции. На первой стадии механической обработки на бегунах в течение 12—15 мин ослабевает связь между тончайшими волокнами асбеста. На второй стадии — в голлендере-пушителе или другом аппарате (6—8 мин) происходит разделение асбеста на тончайшие волоконца. Обычно распушка предпочтительнее по мокрому способу, т. е. на бегунах в присутствии воды. Голлендер, т. е. металлический резервуар, внутри которого вращается барабан, снабженный ножами, является всегда гидравлическим пушителем, так как разделение асбеста, обмятого бегунами, на тончайшие волоконца происходит в карманах между ножами барабана в результате воздействия быстрых вихревых движений струй воды. В этом же аппарате обычно осуществляется и смешение распушенного асбеста с цементом в водной среде. Воду одновременно с загрузкой цемента добавляют из нижней части рекуператора (сборника отработанной воды).
Асбестоцементная масса сравнительно быстро (за 8—10 мин) приобретает достаточную однородность, так как мельчайшие зерна цемента, несущие на поверхности высокий отрицательный электрозаряд, быстро осаждаются и прочно удерживаются на развитой поверхности тонковолокнистого асбеста, также несущей высокий, но положительный заряд в водной и щелочной среде. Если используется песчанистый цемент, то и мельчайшие частицы диспергированного песка также осаждаются на волокнах асбеста, хотя и при более продолжительном смешивании суспензии (12—13 мин). Для получения подвижной суспензии требуется на 1 мас.ч. сухой асбестоцементной смеси добавлять не менее 4—5 мас.ч. воды, что уточняется расчетом в зависимости от сортов асбеста в смеске.
Изготовленная асбестоцементная масса поступает в ковшовую мешалку для получения определенного запаса массы, чтобы поддерживать непрерывность работы формовочной машины. Из мешалки масса направляется по желобу в металлические ванны, являющиеся частью листоформовочной машины. Одновременно в желоб непрерывно поступает рекуперационная вода, отбираемая из нижней части рекуператора, что позволяет поддерживать необходимую консистенцию массы. Асбестоцементная суспензия,
343
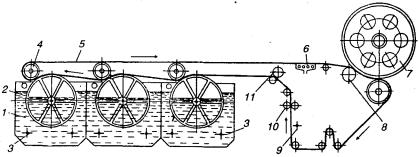
поступающая в ванны сетчатых цилиндров листоформовочной машины, обычно состоит из 8—10% сухого вещества на 90—92% воды. Но имеются и другие листоформовочные машины, на которых применяют асбестоцементную суспензию более высокой концентрации, например до 40—45% сухого вещества (в нем до 15% асбеста, до 85% цемента).
Формование листов и других асбестоцементных изделий мокрым способом производится на круглосетчатой формовочной машине (или полусухим — на фильтрующей ленте). Принцип формования изделий состоит в отфильтровывании воды из слоев асбестоцементной массы под влиянием гидростатического давления до необходимого уплотнения (рис. 9.30). С этой целью в металлической ванне 1, наполненной асбестоцементной суспензией, расположен полый каркасного типа цилиндр 2, обтянутый металлической сеткой (сетчатый барабан). На сетке масса осаждается тонким слоем и частично обезвоживается за счет фильтрации воды сквозь сетку. Вода из барабана отводится сначала в сгустители (рекуператоры) для отделения и возвращения в производство не осевшей части асбеста, а затем используется для промывки сетки и сукна и разжижения асбестоцементной массы в желобе. С поверхности барабана слой ас- бестоцементной массы снимается бесконечной суконной лентой 5. Пройдя на ленте вакуум-коробку 6 (с разрежением примерно 300 мм рт.ст.), предварительно обезвоженная асбестоцементная масса переносится к металлическому форматному барабану 7, который снимает массу с ленты сукна и навивает ее на свою поверхность концентрическими слоями, при этом она уплотняется между вращающимися металлическими цилиндрами. Когда асбестоцементный слой на барабане достигнет необходимой толщины, его разрезают по образующей цилиндра, и сырой лист снимают. Давление прессовой части листоформовочной машины составляет обычно 0,2— 0,4 МПа, для второго подрессовочного вала 10,0—12,0 МПа, для пресс-вала — до 40,0 МПа. В результате обжатий содержание влаги в листе значительно снижается и достигает 25%.
Рис. 9.30. Схема работы листоформовочной трехцилиндровой машины: 1 — ванна; 2 — полные барабаны с сетчатой поверхностью; 3 — асбестоцементная масса; 4 — прижимной валик; 5 — бесконечная лента сукна; 6 — вакуумная коробка; 7 — форматный барабан; 8 — опорный вал; 9 — пресс-вал; 10 — промывное устройство; 11 — отжимные валики
При изготовлении плоских мелких изделий лист дополнительно разрезают на плитки, которые стопками прессуют под высоким давлением (до 40 МПа) на гидравлическом прессе. Если изготовляют волокнистые листы, то волнирование производится на специальных станках скальчатого типа периодического действия. Имеются станки непрерывного действия, которые применяют во всех автоматизированных линиях.
Изделия твердеют в пропарочных камерах при температуре 50—60°С, относительной влажности 90—95% в течение 10—14 ч, а затем 5—1 сут в утепленном складе. Быстрее происходит твердение в автоклаве под действием пара давлением 0,8 МПа, что позволяет использовать песчанистый цемент и исключить выдерживание изделий на складе завода.
При производстве труб принципы формования остаются теми же, но используют специальные трубоформовочные машины со съемными форматными барабанами (скалками). У трубо- и листоформовочных машин не имеется принципиальных отличий в
344
конструкциях ванн сетчатых цилиндров, вакуумобезвоживающих устройств и устройств для очистки сукна.
При окончании процесса навивания асбестоцементных слоев форматную скалку снимают и устанавливают новую. Чтобы можно было легко вынуть скалку, диаметр трубы несколько увеличивают. С этой целью сетку у концов немного растягивают с помощью металлических клиньев и развальцовывают трубу на специальном каландре.
Сухой способ формования асбестоцементных листов предусматривает распушку асбеста и смешивание его с цементом и песком в сухом виде. Для последующего увлажнения добавляют 12—15% воды, а уплотняют массу на конвейерной ленте катками или под прессом. Твердеют изделия, к которым в основном относятся плитки для пола и облицовочные, в автоклавах. Сухой способ позволяет применять коротковолокнистый асбест преимущественно 6-го сорта.
345
9.8.4. ПРОДУКЦИЯ АСБЕСТОЦЕМЕНТНЫХ ЗАВОДОВ
Асбестоцементные изделия находят широкое применение при устройстве кровельных покрытий, в стеновых конструкциях, трубопроводах и т. п. Промышленность выпускает волнистые листы, плоские листы непрессованные и прессованные, электроизоляционные доски, некоторые специальные изделия — вентиляционные короба, листы для градирен, детали для сводов метрополитена, панели и др.
Волокнистые листы производят различных размеров по длине, ширине, толщине, шагу и высоте волны, а используют их для кровельных покрытий жилых, общественных и промышленных зданий. В широкой номенклатуре этих листов предусмотрены основные размеры: длина — в пределах от 1200 (листы ВО) до 2500 мм (листы усиленного профиля, унифицированного профиля и др.), ширина листов — от 686 до 1150 мм (в зависимости от профиля). Чем больше размеры по длине и ширине, тем толще листы — от 5,5 до 7,5 мм. Высота и шаг волны листов приняты соответственно в пределах 28—54 и 115—200 мм. В настоящее время предусмотрен выпуск листов пяти профилей. Имеется тенденция к дальнейшему увеличению размеров профилированных и плоских листов, так как при их использовании снижается расход древесины на обрешетку и строительные фермы, уменьшается трудоемкость и сокращаются сроки кровельных работ.
Плоские листы применяют для наружной и внутренней облицовки стен, потолков, перегородок и балконных ограждений. Их выпуcкают прессованными и непрессованными, с гладкой или тисненой (рельефной) поверхностью.
Для покрытия полов в кухнях, санитарных узлах, магазинах, столовых и других изготовляют плитки размером 150x150x10 (13) мм различной окраски.
Разработан и изготовляется ряд конструкций утепленных асбестоцементных плит для покрытий, например плиты АП, которые утеплены минеральной ватой, плиты АКП из двух асбестоцемент-ных листов, между которыми помещен утеплитель, и др. Разработаны
иприменяются также асбестоцементные стеновые панели с деревянным каркасом или бескаркасные. Их масса значительно меньше массы панелей из других материалов. Размеры и качественные показатели панелей и листов устанавливают соответствующие стандарты. Размеры крупноразмерных листов — 3600x1500; 3000x1200 мм и др., а мелкоразмерных — 1200x800 мм. Крупноразмерные листы могут выпускаться двоякой кривизны длиной до 5 м (для летних домиков).
Асбестоцементные трубы применяют для устройства водопровода и канализации в населенных пунктах. Безнапорные трубы используют при проведении дренажных линий, строительстве кабельных сетей и т. п. Внутренний диаметр труб (условный) составляет от 100 до 500 мм при длинах 3000 и 4000 мм (что зависит от типа трубоформовочных машин). Увеличивается выпуск труб длиной 5 и 6 м, что снижает количество стыков, расход муфт и уплотнительных колец.
Освоено производство асбестоцементных труб с газонепроницаемыми покрытиями из полимерных материалов. Такие трубы обладают высокой водо-, бензо- и маслостойкостью
инадежно заменяют стальные трубы.
346
9.8.5. ОСНОВНЫЕ СВОЙСТВА АСБЕСТОЦЕМЕНТНЫХ ИЗДЕЛИЙ
Основные свойства асбестоцемента — прочность и деформатив-ность при воздействии статических и динамических (ударных) нагрузок. Для повышения сопротивляемости изделий воздействию атмосферных осадков, агрессивной внешней среды необходимо также обеспечить их достаточную плотность — водонепроницаемость, минимально допустимое водопоглощение и др. Конкретные показатели качества асбестоцементных изделий определены в соответствующих стандартах. Так, например, согласно ГОСТ 16233—77 в отношении листов волнистых унифицированного профиля УВ среди других требований (формы, размеров, дефектов) предусматривается, что их средняя плотность в высушенном состоянии должна быть не менее 1,75 г/см3, что обеспечивает величину водопоглощения не более 25%. Минимальный предел прочности при изгибе волнистых листов в поперечном к гребням волн направлении и в зависимости от толщины листа и сортности должен быть, как минимум, в пределах от 15,7 до 19,6 МПа, листы должны быть морозостойкими и выдерживать в насыщенном водой состоянии не менее 25 циклов (у профиля УВ — не менее 50) попеременного замораживания и оттаивания без каких- либо признаков расслоения или повреждения, сохраняя после этого- испытания не менее 90% первоначальной величины предела прочности, чтобы при стандартном испытании они были водонепроницаемыми (табл. 9.9).
Таблица 9.9 Физико-технические характеристики асбестоцементных листов (волнистых и плоских)
|
|
Профиль волнистых листов |
Вид плоских листов |
|||
Показатели |
|
обыкновенн |
усиленны |
унифицированн |
прессованн |
непрессованн |
|
|
ый |
й |
ый |
ый |
ый |
Предел |
|
|
|
|
|
|
прочности |
при |
15,7 |
17,2 |
19,6 |
250 |
200 |
изгибе, МПа, не |
||||||
менее |
|
|
|
|
|
|
Ударная |
|
|
|
|
|
|
вязкость, |
|
1,5 |
1,6 |
1,6 |
2,6 |
2,5 |
кДж/м2, |
не |
|||||
менее |
|
|
|
|
|
|
Штамповал |
|
— |
1,72 |
2,15 |
— |
— |
нагрузка, кН |
|
|||||
|
|
|
|
|
|
|
Средняя |
|
|
|
|
|
|
плотность, |
|
1,6 |
1,63 |
1,75 |
1,8 |
1,7 |
г/см3, не менее |
|
|
|
|
|
|
Морозостойкос |
|
|
|
|
|
|
ть, циклов, не |
25 |
25 |
50 |
50 |
25 |
|
менее |
|
|
|
|
|
|
Прочность труб оценивают в основном пределом прочности при разрыве, что определяется гидравлическим давлением. По величине максимального рабочего давления напорные водопроводные трубы разделяют на классы: до 0,6 МПа — класс ВТ6, до 0,9 МПа — класс ВТ9, до 1,2 МПа — класс ВТ12 и др. Газопроводные трубы по мак- симальному рабочему давлению разделяют на марки: для газопроводов низкого давления (до 0,005 МПа) — марка ГАЗ-НД, для газопроводов среднего давления (до 0,3 МПа) — марка ГАЗ-СД. Для соединения труб используют асбестоцементные муфты самоуплот- няющиеся типа САМ.
347
К стандартным характеристикам качества асбестоцемента относится еще ударная вязкость, т. е. сопротивляемость изделий ударной нагрузке. Этот важный показатель качества изделий выражается работой, затрачиваемой на разрушение образцов стандартных размеров при ударном воздействии маятника. Так, листы УВ толщиной 6— 7,5 мм должны иметь ударную вязкость от 1,5 до 1,8 Дж/м2 в зависимости от сорта.
Из нестандартных характеристик качества асбестоцементных изделий в ответственных конструкциях при нагрузках свыше 30—40% от разрушающих часто определяют прочность с учетом ползучести, величину модуля упругости, теплостойкость и некоторые другие показатели свойств.
Ползучесть асбестоцемента по сравнению с бетонами значительно больше, что объясняется большим количеством геля в вяжущей части. По этой же причине величина ползучести и интенсивность ее прироста со временем уменьшаются, так как возрастает объем кристаллизационной структуры в цементном камне и уменьшается объем гелевой составляющей. Испытания показывают, что величина прогиба асбестоцементных плиток, находящихся под нагрузкой, равной 50% разрушающей, в 3—3,5 раза больше величины прогиба, возникающего под влиянием кратковременного воздействия той же нагрузки. Малозаметное проявление ползучести наблюдается при нагрузках, равных 25—35% от разрушающих. Тем не менее прочность асбестоцементных изделий и конструкций всегда рассчитывают с учетом ползучести.
Модуль упругости асбестоцемента зависит от величины нагрузки. Если последняя не превышает 75—85% разрушающей, то модуль упругости при растяжении (асбестоцемент в основном работает на растяжение) равен: 12000 МПа— у непрессованного асбестоцемента со средней плотностью до 1,7 кг/м3, изготовленного на 5-м и 6-м сортах асбеста; 18000 МПа --у прессованного асбестоцемента с объемной массой до 1,9 г/см3, изготовленного на 3-м и 4-м сортах асбеста. При напряжениях, больших чем 75—85% разрушающего, пропорциональность между направлением и деформацией нарушается, так как удлинение образцов растет быстрее соответствующих напряжений.
Модуль упругости увеличивается по мере повышения плотности и возраста асбестоцементных изделий, а также содержания асбеста.
Теплостойкость — способность асбестоцемента выдерживать без потери прочности высокие температуры. Исследования показывают, что с началом дегидратации гидросиликатов кальция при температуре 300°С начинается понижение прочности асбестоцемента. При температуре 400°С снижение прочности достигает уже заметной величины — до 10—15%. При дальнейшем повышении температуры создаются условия для дегидратации гидрата оксида кальция с новой потерей прочности асбестоцемента (до 45%), поэтому предельной температурой допустимого нагрева обычного асбестоцемента может быть принята температура 500°С, что и является его теплостойкостью.
Вцелях экономии асбеста, являющегося сравнительно дефицитным природным материалом, предпринимались попытки заменить часть его другими компонентами, сходными в той или иной мере с тонковолокнистой структурой асбеста.
Вэтом направлении проводились опыты по замене части асбеста стекловолокном, но они показали, что необходимо использовать щелочестойкое стекловолокно, так как обычное оказалось недолговечным и в эксплуатационный период асбестоцемент с добавлением нещелочестойкого стекловолокна быстро разрушался. В настоящее время изучена возможность использования для этих целей мергеле-вого и базальтового стекловолокна.
На протяжении многих лет в ряде стран до 10—12% асбеста в производстве асбестоцементных изделий заменялись базальтовой минеральной ватой, которая обладает щелочестойкостью, сравнительно высокой коррозиестойкостью. Предпринимались положительные попытки заменять часть асбеста органическими заполнителями, например целлюлозой, кострой (отход от переработки льна и конопли), что при условии их предварительной минерализации, например обработкой раствором хлористого кальция, дает эффект снижения расхода асбеста без заметного снижения качества асбестоцемента,
348
особенно при сухой технологии изготовления изделий. Заменой асбестового волокна стремились также понизить опасность применения асбеста в связи с подозрениями на его концеро-генность. Как установлено в настоящее время, такая опасность была сильно преувеличена и практически она весьма мала с безусловным сохранением асбеста как ценного сырья в производстве строительных материалов и изделий. Для повышения химической стойкости стекловолокна в зарубежных предложениях рекомендуется вводить оксиды циркония, а также новые составы стекловолокна.
349
9.9. СТРОИТЕЛЬНЫЕ МАТЕРИАЛЫ НА ОСНОВЕ МАГНЕЗИАЛЬНЫХ ВЯЖУЩИХ ВЕЩЕСТВ
На основе магнезиальных вяжущих веществ изготовляют ксилолит, фибролит, штукатурные растворы, некоторые архитектурные изделия, реже — бетоны.
Ксилолит — нередко именуемый и как магнолит, относится к типу деревобетонов и представляет собой мелкодисперсный конгломерат, в котором спрессованные древесные опилки и, возможно, древесная мука сцементированы в прочный и плотный каменный материал с помощью цемента Сореля. Последний приготовляется из каустического магнезита путем его затворения водным раствором хлористого магния (MgCl2). Соответствующие пластичные смеси ксилолитовой массы с красителем используют для устройства бесшовных полов, а без красителей — для устройства оснований под чистые полы из плиточных и рулонных полимерных материалов. Уложенный слой ксилолита уплотняют, циклюют, затирают и шлифуют. Из жесткой ксилолитовой массы прессуют плиточный материал для полов и ступеней в горячем состоянии под давлением 30 МПа. Обе разновидности полов отличаются бесшумностью, малой теплопроводностью, значительной твердостью (5—7,5 а для плиток 10—14 по Бринелю) и большой прочностью: при сжатии 20—40 МПа, при растяжении 3—5 МПа. Полы гигиеничны, негорючи и долговечны.
Вотличие от других неорганических вяжущих каустический магнезит, как отмечено выше, затворяется не на воде, а на водном растворе хлористого или сернокислого магния.
Для затворения возможно применять и некоторые другие соли — ZnCl2, FeSO4 и др. Соотношение по массе: MgO — 62—67% и Mg Cl2·6H2О — 38—33% (в пересчете на активный оксид магния). Для снижения гигроскопичности и повышения водостойкости
допускается вводить в смесь железный купорос FeSO4 с заменой до 50% раствора хлористого магния. Целесообразное соотношение по массе компонентов ксилолита устанавливают экспериментальным путем, причем всегда желательно использовать общий метод проектирования состава ИСК.
Вкачестве органического заполнителя можно применять не только опилки, но и древесную шерсть, древесную стружку хвойных пород, льняную костру и др.
Фибролит изготовляют в виде конструкционно-теплоизоляционного или теплоизоляционного материала, чаще всего плит толщиной 30, 50, 75 и 100 мм, шириной 500—600 мм, длиной до 2500 мм. Масса стружки или древесной шерсти составляет около 30% массы фибролита. В качестве вяжущего вещества чаще всего используют портландцемент, цемент Сореля.
Смесь, соответствующую составу фибролита, укладывают в формы и прессуют. Она твердеет в обжатом состоянии. Плиты сушат на заводе до влажности 15—20%. В зависимости от плотности (в кг/м3) фибролит подразделяют на марки: Ф300, Ф400 и Ф500. Теплопроводность плит 0,7—1,0 Вт/(м·К) при температуре 20°С.
При добавлении к магнезиальному вяжущему веществу поризу-ющих ингредиентов возможно получить не менее эффективные, чем фибролит, теплоизоляционные материалы
— пеномагнезит и газомагнезит.
Изложенное выше почти в полной мере относится и к использованию в качестве вяжущего вещества каустического доломита, хотя приходится учитывать его значительно меньшую прочность, чем каустического магнезита — в два-три раза. Вместе с тем оба этих магнезиальных вещества остаются воздушными и не обеспечивают стойкую микроструктуру ИСК на их основе при длительном контакте с водной средой.
Кроме горных пород магнезита и доломита в качестве сырья для получения магнезиальных вяжущих веществ используют техногенное магнезиальное сырье более сложного химического состава. Оно является попутным продуктом добычи и переработки горных пород ультраосновного состава при получении железа, меди, алмазов, асбеста и других полезных ископаемых. По ориентировочным подсчетам на горно-обогатительных
350