
STROITEL_NOE_MATERIALOVEDENIE_RYB_EV
.pdfэстрих-гипса наступает не ранее 2 ч, но его можно ускорить добавками, например КН8О4; предел прочности при сжатии составляет 10—20 МПа, а водостойкость несколько выше, чем у низкотемпературных гипсовых вяжущих и ангидритового цемента. Его применяют для изготовления декоративных и отделочных материалов, например, искусственного мрамора, штукатурных растворов, устройства бесшовных полов и подготовки оснований под линолеум и др.
В целях улучшения качества эстрих-гипса некоторыми исследователями (А.В. Волженсжим и др.) рекомендуется применять сырье с содержанием до 5—7% доломитов и известняков и до 7—10% глинистых примесей. Тогда возникает некоторое количество силикатов, алюминатов и ферритов кальция, повышающих водостойкость готового продукта обжига. Но ее можно повысить и введением гидрофобных добавок или минеральных — шлака, извести, портландцемента и др.
Воздушная строительная известь — вяжущее, получаемое равномерным и умеренным (до спекания) обжигом горных пород, содержащих большее или меньшее количество углекислого кальция.
Среди таких пород — известняки, мел, доломитизированные известняки, имеющие весьма ограниченное содержание (до 6% по массе) глинистых примесей. Имеются в породах и другие примеси—углекислый магний, кварц, оксид железа. Для получения воздушной извести требуется поддерживать температуру обжига на уровне 900—1200°С, что зависит в основном от состава сырья. Обжиг проводится до полного удаления углекислого газа в соответствии с уравнением термической диссоциации: CaCO3 + 178 кДж = CaO + CO2. Образуется белое огнестойкое вещество, техническое название которого — негашеная известь.
Сырье обжигают в печах различных конструкций: шахтных, вращающихся, циклонно- вихревых (во взвешенном состоянии), а также на движущихся агломерационных решетках. Распространен обжиг в шахтных печах, которые работают либо по пересыпному способу, либо с выносимыми топками (рис. 9.2). Они надежны в эксплуата- ции, позволяют использовать местные виды топлива и при меньшем его расходе на единицу готовой продукции. Загружаемый в шахтную печь известняк имеет обычно размеры 80—200 мм, а при обжиге во вращающейся печи используют дробленый известняк размером 5—20 и 20—40 мм. В процессе обжига сырья протекает декарбо- низация. При выходе из печи размеры обожженной (комовой) извести сохраняются в основном прежними до погрузки в печь, но за счет потери CO2 становятся высокопори- стыми и легкими. При дальнейшем измельчении комовой извести ее предварительно дро- бят до размера 15—20 мм. Далее — помол в шаровых одно- и многокамерных мельницах по замкнутому циклу с рассевом продукта в сепараторе. Получаемый продукт носит на- звание молотой негашеной извести того же состава (оксида кальция).
Молотая негашеная известь получила применение в качестве вяжущего вещества в результате исследований И.В. Смирнова в конце XIX — начале XX вв. Однако работать с ней сложнее, чем с гашеной известью, но по качеству она выше, являясь более активной в формировании структур ИСК.
Гашение комовой извести с превращением ее в тончайший порошок — уникальный технологический прием химического диспергирования. Оно производится в специальных гидраторах периодического или непрерывного действия. В условиях стройплощадки га- шение небольшого объема извести производят в творильных ящиках с сеткой для сцеживания разжиженного известкового теста (известкового молока) в гасильную яму, где оно выдерживается не менее двух недель. Опасно применять тесто, в котором имеется непогасившаяся известь.
Реакция гашения протекает с выделением большого количества теплоты: CaO + H2O → Ca(OH)3 + q, где q — количество теплоты, равное 1160 кДж (277 ккал) на 1 кг оксида кальция. Эта теплота вызывает вскипание воды, что послужило основанием именовать негашеную известь кипелкой. Погасившаяся известь превращается в тонкий рыхлый
221
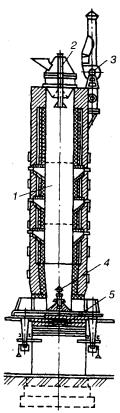
порошок со значительным увеличением в объеме (в 2,5—3 раза) — пушонку. При избытке воды (например, больше чем в среднем 1,5 л на 1 кг кипелки) известь переходит в известковое тесто; рабочее состояние — при 50% воды.
Рис. 9.2. Шахтная печь для обжига извести: 1 — шахта; 2 — загрузочный механизм; 3 — дымосос; 4 — гребень для подачи воздуха; 5 — разгрузочный механизм
Таким образом различают следующие виды воздушной извести: известь негашеная комовая, известь негашеная молотая, известь гашеная (пушонка), известковое тесто. Основным компонентом воздушной извести служит оксид кальция, которому практически всегда сопутствует оксид магния. По содержанию оксида магния (MgO) известь разделяют на маломагнезиальную (меньше 5%), магнезиальную (5—20%) и доломитовую (20—40%). Присутствие оксида магния, который находится обычно как бы в пережженном состоянии, замедляет скорость гашения извести. Различают известь быстрогасящуюся — при скорости ее гашения меньше 8 мин, сред-негасящуюся, если скорость не превышает 25 мин, и медленногася-щуюся — если скорость гашения составляет не менее 25 мин. За скорость гашения принимается время, прошедшее от момента приливания воды к извести до начала снижения максимальной температуры, что определяется в лаборатории завода.
В соответствии с ГОСТ 9179-77 строительная воздушная известь подразделяется на три сорта для негашеной извести, на два сорта для гашеной извести. Содержание активных СаО + MgO (в пересчете на сухое вещество) для негашеной извести без добавок должно быть соответственно для 1, 2 и 3-го сортов 90, 80 и 70%; для негашеной извести с добавками для 1-го и 2-го сортов — 65 и 55%. Строго нормируется допустимое содержание непогасивших-ся частиц, (в %). Прочность извести стандартом не нормируется, так как она невелика; у пушонки через 28 суток 0,5—1,0 МПа, у молотой извести 1,0—6,0 МПа. Средняя плотность пушонки равна 400—450 кг/м3.
Известь всех видов находит широкое применение в качестве вяжущего и водоудерживающего компонента в строительных растворах для кладки, штукатурки, а также в производстве строительных материалов как составная часть смешанных вяжущих
222
веществ и изделий, например для изготовления силикатных материалов автоклавного твердения. Основное количество извести, как и гипсовых вяжущих веществ, используют в производстве штучных и крупногабаритных изделий, в керамической промышленности, стеклоделии, металлургической промышленности и других отраслях.
Магнезиальные вяжущие вещества — продукты умеренного обжига природных карбонатных пород: магнезита и доломита с получением после тонкого помола соответственно каустического магнезита при температурах 750—850°С и каустического доломита при температурах 650—750°С. При обжиге природный магнезит разлагается и превращается в оксид магния по реакции: MgCO3 → MgO + СО2.
При условии полного выделения углекислого газа качество каустического магнезита тем выше, чем ниже температура обжига.
Оксид магния может получаться также обжигом металлургического магнезита при температурах 1100—1300°С, но вяжущими свойствами такой «намертво обожженный» магнезит почти не обладает и используется в качестве сырья для производства магнезито- вых огнеупоров.
В каустическом магнезите содержится оксида магния до 85% по массе и более, тогда как допустимое содержание оксида кальция лимитируется 2—5%. Он представляет собой тонкий порошок белого или желтоватого цвета. Начало схватывания должно наступать не ранее 20 мин, а конец схватывания — не позднее 6 ч от момента за-творения теста. Его истинная плотность 3,15—3,40 г/см3, что значительно выше, чем у извести и гипсов, а также выше, чем у портландцемента. По пределу прочности при растяжении образцов из теста нормальной густоты каустический магнезит должен иметь не менее 1,5 МПа. Предел прочности при сжатии образцов-кубиков из каустического магнезита состава 3:1 (3 части магнезита, 1 часть (по массе) сосновых опилок) изменяется от 30 до 50 МПа и выше.
Вторая разновидность магнезиального вяжущего вещества — каустический доломит — получается в соответствии с термохимической реакцией разложения: СаСО3·MgCO3 → СаСО3 + MgO + CO2. Видно, что при обжиге природный доломит разлагается с образова- нием в основном оксида магния, а большая часть карбоната кальция остается не разложившейся, так как температура его диссоциации, что уже отмечалось выше, равна около 900°С. В получаемом после обжига и помола каустическом доломите карбонат кальция остается в виде неактивного порошкообразного наполнителя, поэтому реакционная активность каустического магнезита выше, чем каустического доломита, и соответственно выше его прочность (прочность каустического доломита 10—30 МПа).
Оба вида магнезиальных вяжущих веществ затворяют в тесто не чистой водой, как другие неорганические вяжущие материалы, а водным раствором некоторых солей — хлористого магния, сернокислого магния, сернокислого железа, количество которых соответствует определенной плотности раствора. Получаемое после затворения вяжущее именуется цементом Сореля.
Магнезиальные вяжущие вещества характеризуются повышенной прочностью сцепления с каменными и древесными материалами, особенно прочностью на разрыв, например под действием центробежных сил. Поэтому их применяют в абразивном производстве для изготовления жерноточильных кругов, брусьев и др. Главное их назначение в строительстве — изготовление ксилолита для бесшовных полов или фибролита для производства теплоизоляционных изделий и перегородок. Их используют также для растворов при штукатурных работах, на изготовление подоконных плит, лестничных ступеней, кровельных плит и других строительных деталей.
Растворимое стекло и кислотоупорный цемент. Растворимое (жидкое) стекло
представляет собой щелочной натриевый или калиевый силикат переменного химического состава, выражаемого общей формулой R2O·nSiO2, где R может быть Na или K. Величина п — силикатный модуль, имеющий значение от 2,56 до 3,00, в зависимости от чего меняются основные свойства растворимого стекла. Жидкое стекло склеивает и твердеет на воздухе вследствие высыхания, а также выделения аморфного или
223
гелеобразного кремнезема под влиянием воды и углекислоты воздуха. Для ускорения твердения и повышения водостойкости вводят различные катализаторы, главным образом кремнефтористый натрий Na2SiFe. Они ускоряют выделение геля кремневой кислоты.
Сырьем для изготовления растворимого стекла служат чистый кварцевый песок, сода Na2CO3 или сульфат натрия Na2SO4. Значительно реже вторым компонентом служит поташ K2СО3. После варки тщательно перемешанной сырьевой смеси в стекловаренных печах при температуре 1300—1400°С жидкое стекло быстро охлаждается на металлических листах. Образуются полупрозрачные, зеленоватого цвета куски силикат- глыбы. Силикат-глыбу растворяют в автоклавах паром под давлением 0,6—0,8 МПа и температуре 150°С, переводя в состояние коллоидного раствора с истинной плотностью 1,40—1,55 г/см3 (табл. 9.1). Перед применением жидкого стекла производится дальнейшее разбавление раствора до необходимой консистенции.
Таблица 9.1. Свойства силикат-глыбы и жидкого стекла
Показатели |
Виды стекла |
|
||
содовое |
содово-сульфатное |
сульфатное |
||
|
||||
Истинная плотность |
1,50—1,55 |
1,48—1,50 |
1,48—1,50 |
|
Модуль силикатный стекла |
2,6—3,0 |
2,56—3,00 |
2,56—3,00 |
|
Содержание воды, %, не более |
57 |
60 |
60 |
Растворимое стекло хранят в закрытой таре, а перевозить его экономичнее в твердом виде (силикат-глыбы) с последующим растворением на стройках в передвижных или стационарных установках.
Этот вяжущий материал применяют для затворения кислотоупорного цемента при изготовлении соответствующего бетона, предохранения поверхности природных камней от выветривания, изготовления огнезащитных (для древесины) красок, замазок, устройства силикатированного шоссе на основе известнякового щебня, жароупорных бетонов, силикатизации (пропитки) грунтовых оснований и других целей.
Кислотоупорный цемент представляет собой кварцевый порошкообразный материал. Он изготовляется путем совместного помола или тщательного смешения раздельно измельченных: кварцевого песка и кремнефтористого натрия в соотношении 10:1 (по массе); затворяется на водном растворе жидкого стекла (силиката натрия) и после затвер- девания способен в строительных растворах или бетонах противостоять воздействию большинства минеральных и органических кислот. Водный раствор стекла принимается с истинной плотностью 1,345, что соответствует 37° по Боме. Содержание оксида кремния в кислотоупорном цементе превышает 92%. Тонкость его помола нормируется просеиванием на ряде стандартных сит. Обычно нормируются и требования к срокам схватывания цемента: начало для теста нормальной густоты должно наступать не ранее 20 мин, конец — не позднее 8 ч от начала затворения. Прочностная характеристика цемента выражается пределом прочности при растяжении стандартных образцов после твердения их в течение 30 суток. При хранении на воздухе без кипячения или после кипячения в серной кислоте предел прочности должен быть не менее 2 МПа. Керосинопоглощение образцов в 10-дневном возрасте должно быть не более 15%. Прочность кислотоупорного бетона достигает 50—60 МПа, но он теряет прочность в воде, а в едких щелочах разрушается. В бетонах используют кислотоупорные заполнители: кварцевый песок, андезит и др. Такие бетоны применяют на химических заводах для изготовления резервуаров, ванн и других емкостей, а растворы — при футеровке кислотоупорными плитками различных конструкций.
224
9.1.4. ГИДРАВЛИЧЕСКИЕ ВЯЖУЩИЕ ВЕЩЕСТВА И ИХ ПРОИЗВОДСТВО
Гидравлическая известь — продукт умеренного обжига (не до спекания) мергелистых известняков, содержащих от 6 до 20% глинистых примесей. Обычный интервал температур обжига составляет 900—1100°С, что зависит от состава сырья. Продукт обжига содержит не только свободную известь, но и химические соединения с оксидами глины: силикаты 2СаО·SiO2, алюминаты 2СаО·Al2О3, ферриты 2СаО·Fe2O3 кальция. Подобно воздушной извести этот продукт составляет комовую гидравлическую известь, которую подвергают помолу в мельницах с получением тонкомолотой негашеной извести. Реже используют другой вариант: комовую известь гасят, а непогасившиеся частицы (силикатов, алюминатов и ферритов) подвергают дополнительному измельчению с последующим смешением погасившейся и непогасившейся частей.
При взаимодействии с водой силикаты и алюминаты в извести остаются практически негидратированными. Только при гашении этой извести в тесто постепенно образуются гидросиликаты и гидроалюминаты кальция, что сопровождается набуханием этих соединений и переходом их в студнеобразное состояние. В зависимости от содержания в извести оксида кальция, по отношению к сумме диоксида кремния, полуторных оксидов алюминия и железа можно условно разделить на сильно гидравлическую и слабо
гидравлическую. Отношение m = |
%CaO |
называется модулем |
|
|
|||
%SiO2 + Al2O3 + Fe2O3 |
|||
|
|
основности и для сильногидравлической извести он равен 1,7—4,5, а для слабогидравлической — 4,5—9,0. Модуль основности характеризует способность извести к твердению в водной среде, а при m > 9,0 известь является типичным воздушным вяжущим веществом. Кроме того, модуль m косвенно отражает также и механическую прочность затвердевшего теста (или раствора). Следует отметить, что если для гашения извести воздушной в тесто требуется ввести 70—80% воды, то для гидравлической — около 20 %.
Гидравлическая известь не обладает высокой прочностью. При ее определении в образцах из раствора состава 1:3 (с нормальным песком) прочность при сжатии должна быть 2-5 МПа через 28 суток комбинированного хранения (7 суток во влажном воздухе и 21 сутки в воде).
В настоящее время гидравлическая известь имеет ограниченное применение — для строительных растворов и бетонов невысокой прочности, для кладки в сырых местах (подвалах, каналах), в малоэтажном строительстве и др. Совсем не изготовляется теперь роман-цемент — гидравлическое вяжущее вещество, получавшееся измельчением в тонкий порошок умеренно обожженных (не до спекания) известковых или магнезиальных мергелей при содержании в них глинистых примесей до 25—35%. Эту разновидность це- мента полностью вытеснил портландцемент.
Портландцемент — продукт тонкого измельчения клинкера, получаемого в результате равномерного обжига до спекания природного сырья (мергеля) или искусственной однородной сырьевой смеси определенного состава, содержащей известняк и глину. В процессе помола клинкера добавляют гипсовый камень в количестве до 3,5% (в пересчете на серный ангидрит). Можно частично заменить сырьевую смесь доменным шлаком, нефелиновым шламом, опокой и др. при условии, что сырье сохраняет необходимый рас- четный состав.
Природное минеральное сырье в виде известкового мергеля встречается редко, приходится ориентироваться, в основном, на искусственные сырьевые смеси. Как отмечено, они составляются с помощью пород с высоким содержанием углекислого кальция (чистых известняков, мела, известковых туфов, мергелистых известняков и др.) и пород, относящихся к глиноземистому сырью (тяжелые глины, мергелистые глины, глинистый сланец и др.). Исходя из химического состава сырьевой смеси и заданной
225
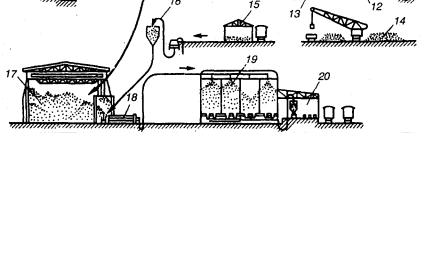
характеристики состава клинкера вычисляют соотношение между ее компонентами с воз- можно большей точностью. Вид сырья отражается на выборе оборудования, необходимого для его подготовки, обжига и помола продукта обжига с добавками и с переводом их в состояние однородного мельчайшего порошка — портландцемента.
В зависимости от характера приготовления сырьевой смеси различают мокрый, сухой и комбинированный способы производства портландцемента. Каждый из этих способов имеет свои особенности, достоинства и недостатки. В нашей стране на цементных заводах преобладает пока мокрый способ, хотя многие заводы перестраивают технологию на более экономичный по расходу топлива сухой и комбинированный способы.
При мокром способе (рис. 9.3) сырьевую смесь измельчают в шаровых мельницах в присутствии большого количества воды (до 36—42% массы сухого вещества) и получают жидкотекучую массу, или суспензию. Ее называют шламом. Из шлам-бассейна 7 масса направляется для обжига во вращающуюся печь 8. Мокрый способ целесообразно использовать при применении в качестве компонентов мела, сырой глины, что понижает расход электроэнергии на измельчение сырьевой смеси. При этом способе облегчается транспортирование и перемешивание сырьевой смеси, однако расход топлива на обжиг ее в печи в 1,5—2 раза больше, чем при сухом способе.
Рис. 9.3. Технологическая схема производства портландцемента по мокрому способу:
1 — подача известняка из карьера; 2 — дробилка для известняка; 3 — подача глины из карьера; 4 — подача воды; 5 — бассейн для размешивания глины; 6 — сырьевая мельница; 7 — шлам-бассейны; в — вращающаяся печь; 9 — холодильник; 10 — подача угольной пыли в печь; 11 — элеватор для подачи угля из дробилки в бункер; 12 — сушильный барабан для угля; 13 — мельница для угля; 14 — склад угля; 15 — склад гипса; 16 — элеватор для подачи гипса из дробилки в бункер; 17 — склад клинкера; 18 — шаровая мельница; 19 — силосы для цемента; 20 — упаковка цемента
При сухом способе готовят сухой порошок смеси исходных материалов (так называемая сырьевая мука), который обжигают во вращающейся печи.
Комбинированным называют способ производства, при котором сырьевая смесь для обжига подготавливается в виде гранул. Шлам обезвоживают до влажности 16—18% и полученный «сухарь» (корж) перерабатывают в гранулы на специальных грануляторах. Можно также увлажнять сырьевую муку до 12—15% и из нее изготовлять те же гранулы для обжига. Комбинированный способ, по сравнению с мокрым, дает до 20—30% экономии топлива.
При всех способах весьма важно обеспечить бесперебойное поступление сырьевой смеси на обжиг для получения из нее портланд-цементного клинкера.
Обжиг сырьевой смеси — центральный этап технологии цемента. Для обжига применяют два типа печей — шахтные и вращающиеся.
226
Для производства цемента мокрым и сухим способами применяют вращающиеся печи длиной от 150 до 230 м, диаметром 5—7 м и короткие длиной от 60 до 95 м с различными запечными устройствами (конвейерный кальцинатор, циклонные теплообменники, холо- дильники и др.).
Вращающуюся печь 8 (см. рис. 9.3) устанавливают с небольшим уклоном (3—4°) в сторону передвижения сырьевой смеси. Печь медленно (1—2 об/мин) вращается вокруг своей оси в подшипниках. Сырьевая смесь подается в печь автоматическим питателем с верхнего ее конца, а со стороны нижнего конца вдувают топливо — мазут, природный газ или воздушно-угольную смесь. Горячие газы направляются навстречу сырьевой массе. По всей длине вращающейся печи условно вьщеляют шесть зон, которые различают по основным физическим и химическим процессам, проходящим при нагревании. Внутри печи, облицованной надежной огнеупорной футеровкой, находятся различные внутрипечные устройства для лучшего перемешивания и интенсивного прогрева сырья (фильтр-подогреватели шлама, цепные завесы, металлические и керамические теплообменники).
Взоне сушки испаряется свободная вода. Подсушенный материал комкуется и распадается на гранулы. В зоне подогрева при температуре от 200 до 700°С сгорают органические примеси, удаляется химически связанная вода и образуется каолинитовый
ангидрит Al2O3·2SiO2. Обе эти подготовительные зоны составляют при мокром способе около половины длины печи, при сухом способе — значительно меньше. В зоне кальцинирования при интервале температур от 700 до 1100°С происходит диссоциация
карбонатов СаСО3 и MgCO3, а также разложение глинистого компонента на оксиды SiO2, Al2O3, Fe2О3. Они вступают в химическое взаимодействие с СаО. Протекают реакции, связанные с диффузионными процессами в твердом состоянии и с формированием новообразований (искусственных минералов). Вначале образуются однокальциевый
алюминат СаО·Al2О3 (или в условном обозначении СА), а затем двухкальциевый силикат 2СаО·SiO2 (или в условном обозначении C2S). При температуре, близкой к 1200°С, однокальциевый алюминат, насыщаясь известью, переходит в пентакальциевый
триалюминат 5СаО·3Al2О3 и затем в трехкальциевый алюминат 3СаО·Al2О3 (или С3А). Оксид железа образует с оксидом кальция двухкальциевый феррит 2СаО ·Fe2О3 (или С2F) и четырехкальциевый алюмо-феррит 4СаО·Al2О3·Fe2O3 (или C4AF).
При достижении температуры примерно 1300°С все реакции в твердой фазе в основном завершаются, но часть извести остается в свободном состоянии. При дальнейшем повышении температуры (1300—1450°С) происходит частичное плавление сырьевого
материала — спекание, чему особенно легко поддаются C4AF, СаО и MgO. Обычное содержание жидкой фазы при температурах спекания составляет 15—30%. В твердом
состоянии остается 2СаО·SiO2, но и он частично растворяется в этой жидкости, образуя с молекулярно-дисперсной известью трехкальциевый силикат 3СаО·SiO2 (или C3S), поскольку жидкая среда интенсифицирует диффузию молекул оксида кальция. C3S выделяется из жидкой среды вследствие меньшей растворимости в расплаве в виде мельчайших, но способных к росту кристаллов. Это новообразующееся вещество в кристаллическом состоянии является главной составной частью портландцемента. Для его более полного выделения из расплава требуется температура 1450—1500°С со сравнительно длительным сохранением этих тепловых условий. Но даже при самых благоприятных условиях перевод всего двухкальциевого силиката в более устойчивое состояние в виде трехкальциевого силиката затруднителен. Для поддержания
необходимой концентрации растворенных в расплаве извести и Ca2S потребовались бы весьма высокие температуры и длительный период времени.
Всырьевых смесях, насыщенных известью, некоторая часть ее может остаться неусвоенной в процессе обжига. Однако свободной извести в портландцементе не должно быть выше 1—1,5% во избежание неравномерного изменения объема при его твердении.
227

При медленном охлаждении продукта обжига жидкая фаза может почти полностью перейти в продукты кристаллизации, а при очень быстром — в переохлажденную жидкость (стекло). Обычные тепловые режимы в печи благоприятствуют и кристаллизации, и частичному застекловыванию, причем стекло окаймляет отдельные кристаллы.
Таким образом, в результате внутренних химических и физико-химических процессов при обжиге сырьевой смеси образуется клинкер, в составе которого имеются сложные соединения как в кристаллическом состоянии — C3S и C2S, так и в стеклообразном — С3А, С5А3, C4AF. Кроме того, присутствуют в нем MgO (главным образом в виде кристаллов периклаза), СаО и R2O — в стекловидной фазе. Некоторые из этих соединений называются искусственными минералами, а именно: соединения C3S и C2S называются соответственно алитом и белитом. Эти минералы не являются химически чистыми компонентами клинкера. Так, например, C3S может воспринять некоторое количество алюминатов; C4AF воспринимает немного трехкальциевого алюмината и т.д. Поэтому микроскопический анализ показывает состав, который не совпадает с расчетным составом. По расчетному Минералогическому [составу портландцементный клинкер можно разделить на группы: алитовый с содержанием алита свыше 55% и белита меньше 20%; белитовый — с содержанием алита меньше 40% и белита — больше 40%; нормальный с содержанием алита 40—55% и белита 20—40% при общем количестве во всех трех случаях С3А + C4AF 20—25% (по массе); алюминатный — при содержании С3А больше 10% и C4AF меньше 15%; .алюмоферритный — при содержании С3А меньше 10% и C4AF больше 15% при общем количестве силикатов, равном 75%.
Из вращающейся печи клинкер выходит в виде мелких гранул (10—40 мм) зеленовато- серого цвета, после чего его охлаждают воздухом до 100—200°С и направляют на магазинирование. Эта операция выражается в выдерживании клинкера на складе или в силосе для дальнейшего снижения его температуры и частичного самоизмельчения под влиянием тепловых перепадов, гашения свободной извести и других факторов.
При сухом способе подготовки сырья декарбонизация известняка обычно выносится за пределы вращающейся печи — в декарбонизаторы, что позволяет использовать теплоту отходящих газов, ускорить процесс обжига, снизить расход топлива и энергозатрат, металлоемкость оборудования за счет уменьшения длины печи.
На основании изложенного можно заключить, что получаемый портландцементный клинкер характеризуется содержанием отдельных оксидов; соотношениями между содержанием главнейших оксидов, выражаемыми в форме модулей и коэффициента насыщения; содержанием клинкерообразующих соединений — клинкерных минералов.
Главнейшими оксидами клинкера являются CaO, SiO2, Al2О3, Fe2O3. Среди других оксидов, оказывающих нередко существенное влияние на качество цемента, следует отметить MgO, SO3, N2О, K2О, TiO2, P2O5, Mn2О3. Три последних оксида встречаются в очень малых количествах и при расчетах обычно их не учитывают. Химический состав клинкера характеризуется следующими пределами содержания вышеуказанных оксидов
(% по массе): СаО — 62—67%; SiO2 — 20—24; Al2О3 — 4—8; Fe2O6 — 2—51, других оксидов (MgO, SO3) — 1—3%.
Имея химический состав, нетрудно определить приближенные значения модулей: основного, или гидравлического, m, который был указан выше при описании гидравлической извести (см. 8.2.1),
1 Для ориентировки следует учесть, что первый оксид (СаО) составляет 2/3 всего количества; каждый последующий (SiO2, A12O3, Fe2O3) — 1/3 количества предыдущего оксида («Мнемоническое правило»).
228
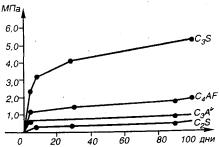
силикатного, |
или кремнеземного, n = |
%SiO |
2 |
и алюминатного, |
или |
|||
%Al2O3 + Fe2O3 |
||||||||
|
|
|
|
|
|
|||
глиноземного, |
p = |
Al2O3 |
. Модули должны быть в пределах: m = 1,9—2,4; n = 1,7—3,5; |
|||||
Fe2O3 |
||||||||
|
|
|
|
|
|
|
p = 1,0—2,5.
В настоящее время редко используется в расчетах основный, или гидравлический, модуль для характеристики клинкера. Однако всегда определяется коэффициент насыщения (КН), показывающий отношение количества извести, остающейся после полного насыщения
глинозема, оксида железа и серного ангидрита, к тому количеству |
|
|||||||
извести, |
которое |
необходимо |
для |
полного |
насыщения |
кремнезема: |
||
KH = |
CaO − (1,65Al2O3 + 0,35Fe2O3 ) |
. |
Этот коэффициент насыщения известью |
|||||
|
2,8SiO2
обычного цемента колеблется в пределах 0,82—0,95. Повышенное значение коэффициента насыщения (КН>1) означает наличие свободной извести, что может вызвать неравномерное изменение объема, трещинообразование, разрушение цементного камня и бетона. Его пониженное значение (КН<0,8) связано с замедленным процессом твердения цементного теста и уменьшением прочности (марки) портландцемента.
Указанные модули сравнительно четко характеризуют свойства цемента. Так, например, цементы с высоким силикатным модулем медленно схватываются и твердеют, но с течением времени они достигают весьма высоких прочностей. У таких цементов имеется повышенная стойкость к воздействию минерализованной воды. Однако в период изготовления клинкера с высоким силикатным модулем затрудняются процессы спекания, требуется повышенная температура. Наоборот, низкий силикатный модуль придает сырьевой смеси чрезмерную легкоплавкость и в связи с образованием натеков и кусков на футеровке печи также затрудняет обжиг.
Рис. 9.4. Пределы прочности клинкерных компонентов при испытании на сжатие в разные сроки твердения (по данным С.Д. Окорокова)
Цементы с высоким глиноземным модулем, что соответствует повышенному содержанию алюминатов кальция, быстрее схватываются и твердеют. Однако достигнутая в первые сроки прочность почти не возрастает при дальнейшем твердении. Такие цементы менее стойки к воздействию минерализованной воды. При малых значениях глиноземного модуля, т. е. при больших количествах в клинкере оксида железа, цементы медленнее схватываются и твердеют, но дают более высокую конечную прочность. Оксид железа облегчает обжиг клинкера, понижает температуру его спекания.
В цементах лимитируется содержание оксида магния (4—4,5%), так как, находясь в свободном состоянии, он может, вследствие медленной и более поздней гидратации, вызывать появление напряжений и трещин в изделиях. Основной характеристикой клинкера служит его минеральный состав, т. е. содержание C3S, C2S, С3А и C4AF. Учитывая, что каждому минералу портландцементного клинкера присущи свои особенности (рис. 9.4), которые в той или иной степени влияют на общие свойства
229
цемента, строителям нельзя обращать внимание только на прочностные показатели. По данным С.Д. Окорокова, наибольшей прочностью для всех сроков твердения обладает алит.
Наибольшей интенсивностью нарастания прочности отличается С3А, но он, как и C4AF, дает низкую прочность. Последнее место, как по абсолютным показателям прочности, так и по интенсивности роста прочности, занимает белит. Следует отметить, что в длительные периоды времени твердения белит способен набирать высокую прочность. Аналогичным образом ведут себя смеси из этих компонентов. Наибольшую прочность показали двухкомпонентные смеси алита и С3А, наименьшую — алит в смеси с белитом и алит в смеси с С4АР. Увеличение содержания С3А до 15% повышает прочность в первые сроки твердения, но в дальнейшем дает уменьшение прочности. Содержание С3А до 10% дает наилучший постоянный прирост прочности при объединении с C3S, хотя отдельно С3А как отмечалось выше, дает весьма малую прочность. В этом случае положительную роль сыграло присутствие в цементе гипса, который добавлялся при помоле клинкера. С ним образуется при твердении теста комплексная соль — кристаллический гидросульфоалюминат кальция 3СаО·Al2О3·3CaSO4·31 (или 32) Н2О, называемая эттрингит. О ней подробнее изложено ниже в связи с коррозией бетона (см. 9.10).
При оценке качества и выборе необходимого для конкретных целей цемента, кроме прочностных показателей принимают во внимание деформативные, усадочные, тепловыделение, коррозиестойкость, морозостойкость и стойкость к внешним условиям работы строительных конструкций и другие свойства. Присутствие искусственных минералов клинкера в различных количествах и сочетаниях вносит свои коррективы в соответствующие показатели цемента.
Деформативная способность — удароустойчивость и пластичность — значительно выше у алюмоферритного цемента (20% C4AF), практически лишенного трехкальциевого алюмината (по данным А.Е. Шейкина, С3А было 1%). Алитоалюмоферритный цемент (по данным А.В. Саталкина) дает почти в 2 раза большую предельную растяжимость, чем алюминатный цемент. Содержание С3А сильно уменьшает деформативную способность цемента, увеличивает вероятность трещинообразования. С3А является наиболее хрупким минералом, тогда как C4AF — наименее хрупким. Среднее положение занимают C3S и C2S. Аналогичное положение занимают минералы и по свойству их твердости.
Объемные деформации при твердении теста и бетона также зависят от минерального состава цемента. В.А. Кинд установил, что наибольшую усадку дает С3А, а затем C2S. Алит и алюмоферрит оказывают наименьшее влияние на объемные деформации цемента. Неодинаково у минералов цементного клинкера и тепловыделение, которое влияет на среднюю температуру, развивающуюся при твердении цементного теста. Так, например, наибольшее количество теплоты выделяют C3S и С3А, которая на третьем месяце тверде- ния составляет 200—220 кал/г. Третье место занимает C4AF — 100 и последнее место — C2S — 50—60 кал/г. Среднее количество теплоты, выделяемое цементами, колеблется в зависимости от минералогического состава от 50 до 140 кал/г, но в основном оно зависит от суммы C3S и С3А, как наиболее экзотермичных при твердении. По этой причине для бетонных работ в осенне-зимний период желательно использовать цемент с повышенным содержанием алита и С3А, то же — при необходимости сокращения сроков изготовления бетонных и железобетонных изделий, особенно тонкоребристого типа. При изготовлении массивных бетонных конструкций требуется цемент с возможно меньшей экзотермией, например, типа белитового.
Разрушение портландцемента при сульфатной агрессии связано с наличием в нем алюмината кальция. Следовательно, в этой среде у цемента должен быть повышенным силикатный модуль, уменьшенное содержание С3А, например не более 5%. Против воздействия кислот неустойчивы ни силикаты, ни алюминаты, так как происходит их растворение.
230