
STROITEL_NOE_MATERIALOVEDENIE_RYB_EV
.pdfДеготь представляет собой сложную дисперсную систему, средой в которой служат масла, а дисперсной фазой — свободный углерод и твердые смолы. На поверхности частиц углерода содержатся слои молекул вязкопластичных смол, кислых и основных веществ. В зависимости от концентрации таких мицелл изменяются структура и вязкостные свойства дегтя. Структура дегтя приближается к типу суспензии, поэтому вязкость существенно зависит от концентрации твердой фазы, механических и тепловых воздействий. При пониженных температурах некоторые ароматические углеводороды, находящиеся в маслах, могут выкристаллизовываться с образованием твердого нафталина, антрацена и др., что приводит к понижению вяжущих свойств дегтя. В отличие от битумов, в дегтях имеются не только анионо-, но и катионоактивные вещества, которые способствуют более тесному физико-химическому контакту с материалами, на которых деготь образует пленки. Дегти быстрее стареют, чем битумы, что приводит к охрупчиванию ИСК, изготовленных на их основе.
Вассортименте дегтевы-х материалов, кроме отогнанных, получаемых на дегтеперегонных установках, имеются еще и окисленные. Они получаются из отогнанных с помощью дополнительного окисления воздухом при температуре 170—200°С в кубовых аппаратах в течение 4—16 ч в зависимости от сырья и требуемой вязкости. Окисленные битумы выпускаются марок ДО-4, ДО-6, ДО-7 и ДО-8.
Встроительстве наибольшее применение имеют составленные (препарированные) дегти, получаемые смешением горячего пека с антраценовым маслом или другими жидкими дегтевыми веществами — пековой смолой, тяжелым маслом и др. Пек как твердое или вязкое аморфное вещество черного цвета состоит из смолистых веществ, свободного углерода, частиц кокса и угля, антрацена, фенантрена, нафталина и масел.
К одной из разновидностей дегтевых вяжущих веществ относится сланцевый деготь. По консистенции он разделяется на вязкий и жидкий, а по генезису — побочный продукт сухой (деструктивной) перегонки горючих сланцев, точнее, их органической части — керогена. Кероген нерастворим в органических растворителях и не выплавляется при обычном нагревании сланцев. Сухая перегонка горючих сланцев осуществляется в камерных печах при температуре 500—600°С без доступа воздуха. Элементарный состав колеблется в довольно широких пределах, что является характерной особенностью дегтя: углевода 55—80%, водорода 6—10%, кислорода 7—35%, серы 1,2—11%, азота 0,2—4,5%. Групповой состав,%: масла 46—60, смолы 18—27, асфальтены 12—30.
Сланцевые дегти значительно чаще именуют битумами, поскольку их групповой состав и свойства ближе к признакам битумных вяжущих веществ. Как и нефтяные битумы, они по консистенции разделяются на вязкие и жидкие.
Вязкие битумы сланцевые характеризуются: пенетрацией при температуре 25°С в пределах 110—330°С; температурой размягчения по прибору КиШ — свыше 30°С; температурой хрупкости — не более 14°С; температурой вспышки — не ниже 140°С. Они имеют марки: БСК 110/190, БСД 190/250 и БСД 250/330.
Жидкие битумы сланцевые по условной вязкости, определяемой вискозиметром,
подразделяют на марки С 12/20, С 20/35, С 35/70, С 70/130, С130/200. Они имеют температуру вспышки не ниже 130°С.
Сланцевые битумы отличаются от нефтяных меньшей тепло- и атмосферостойкостью. Процессы старения имеют в основном характер полимеризации и окисления ненасыщенных углеводородов, вымывания водорастворимых соединений и улетучивания. Битумы сланцевые применяют в дорожном строительстве, используют для приготовления эмульсий и паст, компаундированных вяжущих веществ, а также для кровельных работ. Они сравнительно легко совмещаются с нефтяными битумами и дегтевыми материалами. Опыт эксплуатации асфальтовых дорожных покрытий на основе сланцевых битумов (дегтей) показал, что перегрев каменных материалов приводит к повышению вязкости вяжущего вещества и снижению водоустойчивости и эластичности покрытия.
371
10.1.3. ОТВЕРДЕВАНИЕ БИТУМОВ И ДЕГТЕЙ
Отвердевание битумов и дегтей как основных органических вяжущих веществ может происходить в Объемном и пленочном состояниях. В объемном состоянии их вязкость повышается с переходом в вязкоупругое состояние в цистернах, котлах, сосудах и других емкостях; в пленочном происходит постепенное или быстрое структурирование органических вяжущих веществ в асфальтовых и дегтевых бетонах и растворах, в кровельных и гидроизоляционных материалах и изделиях, а также в других ИСК, в которых эти вещества выполняют вяжущие функции в пленочном состоянии, формируя матричную часть конгломерата.
Основной причиной изменения реологических свойств битума и дегтя в неподвижной емкости служит снижение температуры, что сопряжено с уменьшением интенсивности движения дискретных частиц в жидкой среде. В качестве дискретных частиц разной степени плотности выступают: в битумах — асфальтены с адсорбированными асфальтогеновыми кислотами, карбены и карбоиды; в дегтях — частицы свободного углерода с адсорбированными фенольными соединениями. Жидкой средой у битумов служат истинные растворы смол в маслах; у дегтей — истинный раствор масел различной молекулярной массы. Микроскопическую неоднородность обе дисперсные системы проявляют в период постепенного охлаждения, локальных сгущений молекул и их ассоциаций с переходом в сравнительно крупные макрочастицы (от 20 до 2000 А). Накопление таких частиц образует самостоятельную дисперсную фазу. И хотя частицы ее еще нельзя обнаружить с помощью обычного микроскопа, но фаза в целом уже обладает реальной и высокоразвитой поверхностью. Поверхность имеет большую энергетическую активность и адсорбционную способность, в частности к поглощению из системы поверх- ностно-активных веществ.
Развивается также процесс спонтанного уплотнения частиц при охлаждении битума и дегтя в емкостях с эффектом структурирования. Следует отметить, что такой процесс напоминает образование центров кристаллизации (и вообще центров выделения новой фазы) в растворах неорганических солей. В органических системах жидкая среда является основным носителем потенциальных центров выделения новой фазы. При охлаждении она поддерживает непрерывный процесс структурообразования и формирования частиц различной дисперсности и плотности. В их центре сосредоточиваются твердые и лиофильные асфальтены в битумах или частицы свободного углерода в дегтях. При высокой концентрации мицелл возможно их непосредственное контактирование с переходом структуры битума в олеогель. Переход структуры битума из типа золь в тип гель может быть не только при понижении температуры, но и при возрастании количества асфальтенов больше 25—30% по массе. Так же влияет содержание парафина в битуме или нафталина в дегте, выделяющиеся кристаллы которых тем крупнее, чем медленнее понижалась температура вяжущих веществ. Битум в состоянии структуры гель представляет собой как бы единую мицеллярную пространственную сетку, в промежутках которой находится иммобилизованная и свободная жидкие среды. Происходит своеобразная инверсия фаз: жидкая среда становится в этой структуре дискретной фазой, а твердая — континуальной, непрерывной средой. Гелеобразный характер битума проявляется в наличии температурного интервала плавления и синерезиса, в повышенной упругости и эластичности.
Аналогичные изменения в структуре происходят при изменении температуры дегтя в емкостях, но только при менее развитой поверхности частиц твердой фазы. В результате деготь отличается отсутствием гелеобразного состояния и меньшей вязкостью, чем битумы. Исключение могут составить сланцевые дегти.
Битум и деготь переходят из объемного в пленочное состояние с помощью порошкообразного или зернистого минерального материала. Исходная вязкость этих вяжущих в пленочном состоянии всегда несколько выше, так как часть пленочного
372
вещества находится в адсорбционно-сольватированном состоянии. С понижением температуры возникают центры сосредоточения (микрозародыши) мицелл. Их рост и увеличение концентрации переводит жидкостные пленки в состояние повышенной вязкости и к тенденции упорядочения расположения молекул и мицелл. Постепенно или быстро пленки становятся вязкоупругими или твердыми. В исследованиях было установлено, что их хрупкость (появление трещин на пленке, нанесенной на поверхность металлической пластинки, при изгибе) соответствует примерно температуре, когда вязкость вяжущего вещества (битума) равна 4·108 Па·с. Эта температура хрупкости возрастает с увеличением толщины пленки, снижением скорости охлаждения, увеличением продолжительности и числа циклов воздействия климатических (атмосфер- ных) факторов. При относительно медленном отвердевании пленок вяжущего вещества возрастают упорядоченность и ориентированность микрочастиц, возможна кристаллизация, например парафиновых углеводородов в битумах, нафталиновых — в деггях.
При использовании жидких и разжиженных битумов возникает дополнительный процесс испарения легких фракций, что также относится к одному из факторов их отвердевания. В эксплуатационный период возможны процессы полимеризации и синерезиса битума или сублимация некоторых фракций дегтя, что также связано с ростом вязкости и вероятностью охрупчивания ИСК(на основе органических вяжущих веществ. В результате этих процессов уменьшается содержание жидкой среды, увеличивается количество ориен- тированных моно- и полислоев, снижается фазовое отношение, под которым, как уже отмечалось, условно понимается величина отношения массы жидкой среды к массе твердой фазы, что типично и для других вяжущих веществ, выполняющих функции матричной части конгломерата.
373

10.1.4. МИНЕРАЛЬНЫЕ НАПОЛНИТЕЛИ В КАЧЕСТВЕ АСФАЛЬТИРУЮЩИХ ДОБАВОК
Минеральный порошок получают путем измельчения известняков и доломитов, известняковых или доломитовых асфальтовых пород и основных доменных шлаков. Породы камня используются с прочностью на сжатие не менее 20 МПа. Одной из основных качественных характеристик порошка служит тонкость помола. Необходимо, чтобы частицы мельче 0,071 мм содержались в порошке не менее 70% по массе (при мокром рассеве). Через сито с отверстиями 1,25 мм порошок должен проходить полностью, а с отверстиями 0,315 мм — не менее 90% от массы порошка. Среди других требований к качеству минерального порошка, используемого в производстве асфальтового бетона, следует выделить пористость в уплотненном состоянии порошка под нагрузкой 30,0 МПа — не более 40% по объему. Она всегда возрастает с увеличением одноразмерности частиц. Коэффициент водостойкости образцов из смеси порошка с би- тумом — не менее 0,7—0,8. Показатель битумоемкости (ПБ) — не более 100 г.
Определяют его по формуле: ПБ = ρ МП 15 100, , где ρмп — истинная плотность
Q
порошка, г/см3; Q — количество порошка, г.
К важным показателям, влияющим на водостойкость, морозостойкость, долговечность и другие характеристики бинарной дисперсной системы, относят коэффициент гидрофильное™ порошка. Определяют его величину по формуле: К = VВ/VK (для фракции 1,25 мм), где VB и VK — объемы, которые составляют навески минерального порошка после набухания в течение 3-х суток соответственно в воде и керосине. Величина К должна быть не выше 1. Кроме того, гидрофильность может оцениваться по скорости капиллярного насыщения водой, которая должна быть не более 0,75— 3,0 мм/мин, или по высоте подъема жидкости по трубке с порошком с определением краевого угла смачивания и др.
Взаводских условиях минеральные порошки должны находиться в условиях, предохраняющих их от увлажнения и слеживаемости, так как они используются в сухом, рыхлом (без комков) состоянии. В них ограничивается содержание глинистых частиц пределом до 1,5%, определяемое по количеству оксидов железа и алюминия. Не- допустимы и другие загрязняющие примеси.
Вкачестве минеральных порошков допускается использовать другие породы, не содержащие глинистых примесей, а также основные доменные шлаки.
374
10.1.5. ФОРМИРОВАНИЕ АСФАЛЬТОВОГО ВЯЖУЩЕГО ВЕЩЕСТВА
При взаимодействии битумов и минеральных порошков типа кальцита, доломита, известняка с высоким положительным потенциалом и большим количеством адсорбционных центров в виде катионов Са2+ или Mg2+ происходит интенсивный перевод битума из объемного состояния в состояние диффузно-сольватированных оболочек. При таком структурировании образуются сравнительно прочные физические и хемосорбционные связи — своеобразные «анкерные» контакты, крепко удерживающие битумные пленки на поверхности частиц порошков. При применении этих порошков в асфальтовых бетонах целесообразно использовать битум высокой активности (см. 8.4).
При взаимодействии битумов и минеральных порошков типа кварца, каолинита, кремния, гранита и других аналогичных адсорбентов с высоким потенциалом отрицательного знака в виде ионов кислорода О2- происходит наименьшее снижение полярности фаз в битумоминеральной системе. Порошки этой группы при контакте с битумом вызывают отрицательную адсорбцию. Их роль ограничивается механическим заполнением микрополостей битумной пространственной сетки. Пленки битума очень слабо удерживаются на поверхности частиц порошка единичными «анкерами».
Другие разновидности порошков с пониженным потенциалом отрицательного знака (типа полевых шпатов, слюды, роговой обманки и т. п.) или с преимущественно нейтральной поверхностью частиц (типа талька, графита) занимают по активности при взаимодействии с битумом как бы промежуточные положения.
К моменту выхода из смесительного аппарата перемешанного битумно-минерального вещества в основном заканчиваются процессы образования адсорбционных монослоев и диффузно-сольватиро-ванных оболочек, т. е. завершается микроструктурообразование. Оптимум содержания битума, характеризующийся сплошностью пленки минимальной толщины при минимальном количестве объемного битума в бинарной системе асфальтового вяжущего вещества, устанавливается при проектировании оптимального состава.
375
10.2. ЗАПОЛНЯЮЩИЕ КОМПОНЕНТЫ В ИСК НА ОСНОВЕ ОРГАНИЧЕСКИХ ВЯЖУЩИХ ВЕЩЕСТВ
Для производства асфальтового бетона используются крупно- и мелкозернистые заполнители, т. е. щебень или гравий и песок.
Щебень изготовляют из прочных морозостойких невыветрелых горных пород магматического, осадочного или метаморфического происхождения, а также некоторых разновидностей атмосферных и прочных шлаков. Чаще других пород употребляют граниты, габбро, диабаз, базальт, андезиты, гнейс, трахиты, известняки и доломиты. Предпочтительнее применять изверженные основные породы, а из шлаков — доменные и цветной металлургии, если последние не вызывают экологических сомнений в их качестве и составе. Не применяются горные породы выветрелые и затронутые выветриванием, со значительным содержанием глинистых примесей — мергели и мергелистые известняки, глинистые песчаники и глинистые сланцы. В щебне не допускается глинистых и пылеватых фракций свыше 2% по массе, тем более комков глины, суглинка и других загрязняющих веществ. Ограничивается применение метаморфических пород, так как кварцит нуждается в добавлении извести, цемента или других активизаторов, без которых он показывает слабое сцепление с битумом, а гнейсы и сланцы дают при дроблении в щебень повышенное количество плоской щебенки (лещадки), мрамор — дорогостоящий сырьевой материал, используемый в декоративном строительстве. Из осадочных пород распространены в производстве асфальтового бетона гравийные материалы в дробленом состоянии, из скальных пород — известняк.
Горные породы магматического и метаморфического происхождения принимаются с пределом прочности при сжатии в водонасы-щенном состоянии не менее 100 МПа, а осадочные породы и доменные шлаки — не менее 80 МПа. Для нижнего слоя дорожных покрытий требования к прочности камня снижаются на 20—25%. Важно, чтобы щебень был однородным по прочности и содержал щебенок пластинчатых (лещадки) и игольчатых (пальцы) с отношением взаимно перпендикулярных измерений больше 2 не более 15% по массе для верхнего и 25% — для нижнего слоев асфальтового бетона в покрытии.
Независимо от происхождения горной породы щебень из нее должен выдерживать не менее 50 циклов испытания на морозостойкость для верхнего и 25 — для нижнего слоев покрытия, причем потеря в массе допускается соответственно не более 5 и 10%. Щебень должен быть по возможности кубической формы, что зависит не только от структуры и сложения пород, но и от режима дробления камня. Рекомендуется двух- или трехступенчатое дробление с завершающим пропуском материала через щековую дробилку с шириной щели, равной максимальному размеру щебня. Крупность щебня обычно находится в пределах от 3—5 до 40 мм; для верхнего слоя покрытия она ограничивается более узким интервалом фракций.
Гравий, как правило, неоднороден по минералогическому составу и вследствие гладкой поверхности или утраты своей свежести дает слабое сцепление с асфальтовым вяжущим веществом. Поэтому принято не менее 50% гравия дробить перед применением его в со- ставе асфальтобетона. Кремнистых частиц в щебне, полученном дроблением гравия, должно содержаться не более 25%, а зерен слабых пород — не более 10% по массе.
Вцелях обеспечения однородного гранулометрического состава щебень или дробленый гравий при хранении сортируется по фракциям: 20—40; 10—20; 5(3)—10 мм.
Всоответствии с теорией ИСК допускается понижать предел прочности камня для заполнителя в асфальтовом бетоне. Минимальный уровень ее зависит от расчетной прочности асфальтового вяжущего вещества оптимальной структуры (R') при Б*/П, (где Б
— количество битума, П — количество минерального порошка по массе), которая составляет верхний предел прочности камня. Нижний ее предел устанавливают по реальному отношению Б/П в асфальтобетоне. И тогда требуется тщательная проверка
376
асфальтового бетона на полный комплекс показателей его физико-механических свойств. Переход к низкопрочным породам камня связан не с кажущимся упрочнением камня под влиянием органического вяжущего вещества, а со снижением внутреннего напряжения (релаксацией) в пленках битума или прослойках асфальтового вяжущего вещества. На щебень передаются пониженные напряжения по сравнению с реально приложенными. По этой причине при низкой прочности камня всегда предпочтительнее асфальтовые бетоны порфировой оптимальной структуры, когда асфальтовяжущее вещество особенно рельефно выступает как матричная часть в виде каркаса.
Песок применяют природный и искусственного дробления; из природных песков — горные, речные, морские, озерные и др. Всегда желательно использовать пески с более остроугольными частицами, поэтому чаще — горные, предварительно разделенные по фракциям, а затем получаемые смешением отдельных фракций в определенных соотношениях (по массе), найденных опытным путем. Пески разделяют на две фракции: крупную и мелкую. За граничную фракцию при разделении песка принимается либо 1,25 мм, либо 0,63 мм в зависимости от крупности этого материала. Модуль крупности песка должен быть по возможности выше 2,5; содержание зерен крупнее 0,63 мм — не менее 50%. Но могут использоваться пески и средней крупности с модулем крупности 2,5—2,0 с содержанием зерен крупнее 0,63 мм в количестве 35—50% по массе.
Дробленый песок получают из невыветрелых и, по возможности, некарбонатных горных пород, или кристаллических металлургических шлаков, имеющих прочность не ниже прочности щебня, применяемого в асфальтовом бетоне. В дробленом песке рекомендуется иметь не менее 25% по массе фракции 0,63—2 мм, что регулируется добавлением высевок от отходов камнедробления. В процессе проектирования оптимального состава асфальтового бетона может быть обосновано применение некоторой доли мелких песков с модулем крупности, меньшим 2,0. Максимальный размер зерен песка 3 или 5 мм. Гранулометрический состав песков определяют просеиванием через сита с размером отверстий 5; 2,5; 1,25; 0,63; 0,30; 0,14 мм.
Сквозь сито с отверстиями 0,14 мм (сито № 014) должно проходить не более 15% принятой пробы. В песке не допускается комков глины, суглинков, а количество пылевидных, глинистых и илистых примесей допускается не более 3% от массы природного песка и не более 5% от массы дробленого песка. Эти требования стандарта проверяют методами отмучивания песка в воде.
Качество песков, особенно мелких, повышают предварительной физико-химической активацией. С этой целью производят механическое перемешивание песка с известью, вносимой в количестве 2,5—5% по массе. Такая операция неизбежно сопровождается освежением частиц песка без заметного их доизмельчения. Использование активированного песка, по данным Л.Б. Гезенцвея, особенно целесообразно при производстве мелкозернистого (песчаного) асфальтового бетона.
В процессе перемешивания компонентов иногда вводят поверхностно-активные добавки в количестве 0,2—0,5% (редко до 1,0%) от массы минерального материала. Добавки могут быть: анионоактив-ными веществами — ферролигносульфонат, нафтенаты меди или алюминия; катионоактивными веществами — жирные высшие амины, четырехзамещенные соли аммония, катонин и др.
377
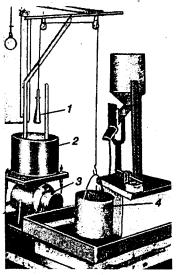
10.3. ОСНОВНЫЕ РАЗНОВИДНОСТИ ИСК НА ОСНОВЕ ОРГАНИЧЕСКИХ ВЯЖУЩИХ ВЕЩЕСТВ
10.3.1. АСФАЛЬТОВЫЕ БЕТОНЫ
Асфальтовый бетон (асфальтобетон) — строительный материал, получаемый в результате отвердевания уплотненной рационально подобранной смеси, состоящей из асфальтового вяжущего вещества и заполняющих компонентов. При отсутствии в смеси крупного заполнителя — щебня или гравия — получаемый строительный конгломерат именуется песчаным асфальтом или асфальтовым раствором. Асфальтовые бетоны и растворы используют в строительстве при возведении магистральных, городских, аэродромных, дорожных, кровельных и других покрытий, гидротехнических, мостовых, промышленных, жилищно-гражданских и иных зданий и сооружений. В зависимости от температуры укладки асфальтобетонной массы различают асфальтобетоны горячие, теплые и холодные. Соответственно используют битумные материалы более вязкие при горячем асфальтобетоне, более мягкие с повышенной пенетрацией — при теплом и жидкие, высокоподвижные битумы или битумные эмульсии — при холодном асфальтобетоне. Горячие и теплые асфальтобетоны подразделяют на плотные с остаточной пористостью от 2 до 7% и пористые— для нижних слоев покрытий и основания — с пористостью 7—12% и высокопористые с пористостью 12—18%.
По технологическому признаку асфальтобетонной массы в процессе ее укладки и уплотнения асфальтобетоны и растворы могут быть жесткими, пластичными и литыми. Для уплотнения жестких и пластичных масс используют тяжелые и средние катки; литую асфальтобетонную массу уплотняют специальными валками, легкими катками или приглаживанием укладочными машинами. С увеличением пластичности массы, определяемой на приборе удобообрабатываемости конструкции И.А. Рыбьева (рис. 10.4), снижается расход энергии, затрачиваемой на уплотнение смеси. Однако появляется тенденция к понижению прочности готового покрытия, возрастает способность его к пластическим деформациям, особенно при нарушенной оптимальной структуре ас- фальтобетона.
Рис. 10.4. Прибор для определения удобообрабатываемости асфальтобетонной массы (конструкция И.А. Рыбьева): 1 — конус; 2 — форма с испытуемой массой; 3 — вибратор; 4 — насыпной груз
Производство асфальтобетонной массы осуществляется на специальных заводах: стационарных и временных. Стационарный асфальтобетонный завод (АБЗ) выпускает массу в больших количествах и предназначен для строительства асфальтобетонных
378
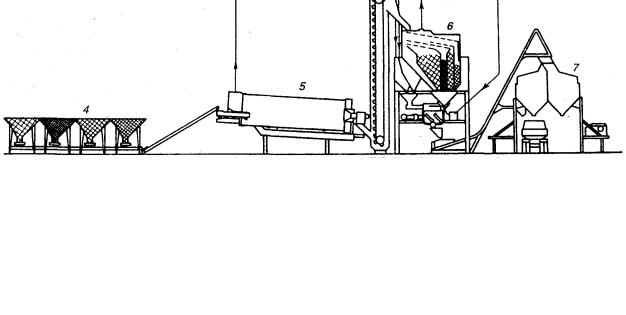
покрытий на крупных и густо сконцентрированных строительных объектах, работы на которых выполняют в течение нескольких лет, например АБЗ для строительства город- ских дорожных покрытий. Временные АБЗ предназначены для обслуживания асфальтобетонной массой небольших объектов или крупных, но сильно растянутых в одном направлении, — магистральных автомобильных дорог и др.
Заводы по производству горячей (она является основной продукцией заводов) асфальтобетонной массы относятся к высокомеханизированным предприятиям. На современных заводах достигнута не только полная механизация, но и автоматизация основных технологических операций. В состав завода входят: смесительный цех, машины и оборудование которого предназначены для приготовления асфальтобетонной массы, дробильно-сортировочный цех для изготовления щебня и его фракционирования, помольный цех для изготовления минерального порошка, цех битумного хозяйства, энергосиловое и паросиловое отделения, складское хозяйство, ремонтно-механические мастерские и лаборатория при отделе технического контроля качества. Современные заводы, в целях избежания излишней запыленности территории, ориентируются на централизи-рованное снабжение их материалами с каменно-заготовительных и нефтяных баз. Основная операция технологии — смешение исходных и подготовленных материалов, принимаемых в определенных количествах по проектному составу. Температура выпускаемой из смесительного аппарата массы 150—180°С или ниже у теплых и холодных масс. На рис. 10.5 показана технологическая схема механической (смесительной) установки ДС-84-2. Иногда в состав асфальтобетонной массы одновременно с битумом вводят поверхностно-активную добавку, дозируемую с помощью специального дозатора.
Рис. 10.5. Технологическая схема производства асфальтобетонной массы:
1 — агрегат пылеулавливания; 2 — агрегат минерального порошка; 3 — битумоплавильный агрегат; 4 — агрегат питания; 5 — сушильный агрегат; 6 — смесительный агрегат; 7 — накопительный бункер
Наиболее часто используют лопастные смесители. Быстрое перемешивание в смесителях этого типа достигается при турбулентно-вращательном движении массы за счет повышенной частоты вращения валов лопастей мешалки — до 200 об/мин вместо обыч- ных 70—80 об/мин при производительности от 50 до 120 т/ч. Облегчает и ускоряет перемешивание песчаной асфальтобетонной массы предварительное активирование минерального порошка или введение активных добавок непосредственно в смеситель в период перемешивания. Вследствие большого количества кварцевого песка в массе
379
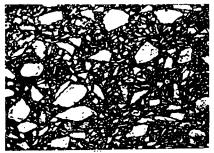
благоприятное влияние приносит добавление извести-пушонки в количестве 3—4% массы минерального порошка. Чтобы не остудить асфальтобетонную массу в пути следования к месту ее укладки, особенно в холодную и ветреную погоду или при большой дальности перевозки (более 20 км), кузов автомобиля-самосвала рекомендуется покрывать брезентом, матами, деревянными щитами или оборудовать двойными стенками для обогрева выхлопными газами. Температуру массы, прибывшей на строительный объект, контролируют не менее чем в трех точках кузова на глубине 10—15 см от поверхности.
Укладывают горячую массу механическими укладчиками, а при устройстве покрытий на большой площади или при большой ширине проезжей части (покрытия) — двумя или более асфальтоукладчиками одновременно. Чем выше температура воздуха и лучше учас- ток защищен от ветра, тем больше длина укладываемой полосы. Так, например, при температуре более +25°С и хорошей защите от ветра длина полос составляет 100—200 м, при +5—10°С она составляет 25—60 м. Самый распространенный способ уплотнения распределенной горячей массы при больших масштабах строительства дорожных и аэродромных покрытий — укатка катками (статического действия, вибрационными, пневмоколесными), а в помещениях — площадочными вибраторами. Первичное уплотнение уложенного слоя производится трамбующим брусом асфальтоукладчика. Монолитный асфальтобетон в покрытии должен удовлетворять определенным техническим требованиям.
Отвердевший и готовый к эксплуатации в покрытиях горячий асфальтобетон характеризуется, подобно другим ИСК, своей структурой и свойствами.
Структура асфальтобетона (рис. 10.6) состоит из заполняющей смеси щебня (или гравия) и песка, скрепленной в монолит матричным асфальтовяжущим веществом. Микроструктура вяжущей части характеризуется непрерывной пространственной сеткой связующего вещества (битума) и дискретными частицами минерального порошка, выполняющего роль асфальтирующей добавки. Структура асфальтобетона, как и других ИСК, включает также поры и контактные зоны. В зависимости от соотношения масс составляющих материалов асфальтовый бетон может иметь порфировую, контактную и законтактную структуры, каждая из которых при высоком качестве этого материала должна быть оптимальной. Последняя естественно отражает своеобразие принятых технологических параметров, режимов изготовления этой продукции при принятых исходных материалах.
Рис. 10.6. Конгломератная структура асфальтового бетона
В теории ИСК предпочтение отдается общему методу проектирования состава асфальтобетона. Он обеспечивает получение необходимого материала не только с заданными показателями свойств, но и с их экстремальными числовыми значениями. Приходится учитывать, что реальные свойства асфальтобетона не остаются постоянными, так как внешние условия могут быстро изменяться, а вместе с ними должны изменяться и свойства покрытия из асфальтового бетона. При обычной температуре (20—25°С) четко проявляются упруго- и эластичновязкие его свойства, при повышенных температурах — вязкопластические, а при пониженных, отрицательных температурах асфальтобетон становится упругохрупким телом. Но он чувствительно реагирует не только на колебания
380