
STROITEL_NOE_MATERIALOVEDENIE_RYB_EV
.pdfМорозостойкость этого кирпича — 25, 35, 50 циклов марки по прочности: 125, 150, 200, 250, 300, водопоглощение — не менее 6%. Не допускаются недожог и известковые включения в сырье, вызывающие дутики и разрушение кирпича.
Кислотоупорные керамические изделия имеют высокую плотность, водопоглощение не более 0,4—10%, Rсж — не менее 35— 150 МПа, кислотостойкость — не менее 95—99%, термическую стойкость — 2—15 теплосмен.
Кирпич кислотоупорный выпускают высокой и первой категории качества классов А, Б, В
ичетырех форм: прямой — КП, клиновой (торцовый — КТ и ребровый — КР), радиальный (поперечный — КРП и продольный — КРПР) и фасонный (слезник — КФ). Размеры кирпича прямого 230x113x65 мм. Эти изделия применяют для устройства фундаментов, футеровки химических аппаратов, кладки колосников, настилки полов, устройства сточных желобов предприятий химической промышленности.
Плитки кислотоупорные и термокислотоупорные керамические предназначаются для футеровки реакционных аппаратов, отбельных башен, емкостей, целлюлозно-варочных котлов, защиты строительных конструкций от кислотных сред. В зависимости от назначе- ния они имеют разные марки и форму. Плитки производятся высшего и первого сортов шести марок: кислотоупорные фарфоровые — КФ, термокислотоупорные дунитовые — ТКД, термокислотоупорные для гидролизной промышленности — ТКГ, кислотоупорные для строительных конструкций — КС, кислотоупорные шамотные — КШ и термокислотоупорные шамотные ТКШ.
Трубы кислотоупорные керамические и фасонные части к ним предназначаются для устройства кислотопроводов и газопроводов. Они имеют плотный спекшийся черепок, с наружной и внутренней стороны их покрывают глазурью. Они должны выдерживать гид- равлическое давление не менее 5 атм (0,5 МПа).
Огнеупорные материалы применяют при строительстве печей, топок и других аппаратов, работающих при высоких температурах, в виде кирпичей, фасонных изделий или блочных элементов. К ним предъявляются требования по прочности, огнеупорности, термостойкости (способности огнеупоров выдерживать без разрушения резкие колебания температуры), химической стойкости против воздействия различных газов, расплавленных металлов, шлаков, стекломассы. Их разделяют на огнеупорные с температурой плавления 1580—1770°С, высокоогнеупорные — 1770—2000°С и высшей огнеупорности с температурой плавления выше 2000°С. По пористости огнеупорные материалы бывают: особо плотными, высокоплотными, уплотненными, среднеплотными, низкоплотными, высокопористыми, ультрапористыми. По способу формования: пластично-формованными, прессованными, сухоформованными, горячепрессован-ными, плавленолитыми и неформованными (без определенной формы и размеров).
В зависимости от химико-минерального состава огнеупорные изделия подразделяются на кремнеземистые, алюмосиликатные, высокомагнезиальные, магнезиально-известковые, магнезиально-си-ликатные, углеродистые, карбидкремниевые, цирконистые, оксидные, бескислородные и др. Наибольшее распространение в строительстве получили кремнеземистые и алюмосиликатные огнеупоры. По применению они бывают: 1) общего назначения; 2) для определенных тепловых агрегатов и устройств.
К кремнеземистым огнеупорам относят динасовые, динасохро-митовые и кварцевые изделия. Динас изготовляют из кварцитов или песчаников с введением в состав шихты от 1,5 до 2,5% минерализаторов (извести, железной окалины и др.). Смешивание измельченного кварцита с минерализатором, а также связующим органическим веществом (СДБ) и водой производят в смесительных бегунах. После формования сырец сушат и обжигают. Их применяют для кладки сводов и стен мартеновских, стекловаренных печей
идругих тепловых агрегатов. Их огнеупорность не ниже 1690—1710°С, Rсж ≥ 17,5—30 Н/мм2.
521
Кварцевые огнеупоры изготовляют из обогащенного кварцевого песка путем его плавки в специальных печах с последующим прессованием в виде брусьев. Последние применяют для кладки бассейнов стекловаренных печей.
Высокоогнеупорные карбидкремниевые изделия (на кремнеземистой, алюмосиликатной и нитридной связках) выпускают пяти марок: КК — карбидкремниевые на кремнеземистой связке; ККУ -карбидкремниевые на кремнеземистой связке улучшенные; КА — карбидкремниевые на алюмосиликатной связке; КАУ - то же, улучшенные; КН — карбидокремниевые на нитридной связке. Их Rсж ≥ 25—100 Н/мм2, температура начала размягчения не ниже 1500—1700°С.
Алюмосиликатные (глиноземистые) огнеупоры изготовляют из измельченных кварцевых пород и шамота (наполнитель), а в качестве связки используют глину или каолин. После формования сырец сушат и обжигают. Изделия применяют для футеровки коксовых пе- чей, вагранок и др. Огнеупорность изделий на каолиновой связке не ниже 1710°С, на глиняной — не ниже 1580°С.
Шамотные изделия формуют из керамических масс, изготовленных из огнеупорного шамота и огнеупорной глины (или смеси глины и каолина), с последующим обжигом. Производство их осуществляется пластическим или полусухим прессованием. Их огнеупорность — до 730°С, Rсж > 13—23 Н/мм2. Пористость шамотных изделий зависит в основном от вида применяемого шамота и его количества. Их применяют для футеровки вращающихся цементных печей, керамических печей, обмуровки топок паровых котлов.
Высокоглиноземистые огнеупоры изготовляют из высокоглиноземистого сырья (бокситов, диаспора, корунда и др.) обжигом до спекания или методом литья из расплава. Их огнеупорность до 2000°С; применяют для кладки стекловаренных печей.
Кроме упомянутых в качестве огнеупорных употребляют изделия, в составе расплавленной шихты которых содержатся диоксид циркония, циркон и технический глинозем, а также магнезиальные, хромо-магнезиальные, шпинельные, доломитовые и другие огнеупоры.
Для получения технической керамики высшей огнеупорности применяют чистые оксиды
(BeO, MgO, CaO, Al2O3, ZrO2 и др.). Изделия формуют методами прессования порошков, шликерным литьем, горячим литьем под давлением. Обжиг производят до спекания, поэ- тому керамический материал имеет плотный черепок с водопоглощением, равным нулю. Температура плавления керамики чистых оксидов 2000—2500°С.
За последние годы получены некислородные огнеупорные материалы с температурами плавления до 4000°С. Для улучшения деформативных свойств изготовляют металлокерамику (керметы), которую получают путем обжига до спекания изделий из смеси керамического порошка с порошкообразным металлом. Керметы применяют для из- готовления деталей оборудования, работающих при высоких температурах, и инструментов, обладающих высокой твердостью.
В тепловых агрегатах для уменьшения расхода топлива применяют керамические теплоизоляционные изделия и огнеупорные легковесы. Для их изготовления используют выгорающие добавки, газообразователи, вспениватели и другие порообразующие вещества. Изделия получают как из керамических масс с введением в них огнеупорных или тугоплавких пористых заполнителей, так и из поризо-ванных керамических или огнеупорных масс без заполнителей. Отформованные из этих масс изделия сушат, а затем обжигают при высоких температурах. Теплоизоляционные изделия применяют при температурах до 900—1200°С, а огнеупорные легковесы до 1000— 1650°С и выше.
Теплоизоляционные изделия из трепелов (диатомитов) с пенооб-разующими или выгорающими добавками выпускают в виде кирпича, скорлуп и сегментов марок 350, 400, 500, 600 по средней плотности. Формование массы влажностью 50% производят на ленточном прессе, после сушки сырец обжигают. При температуре 350°С теплопроводность λ ≤ 0,116—0,168 Вт/(м·К), при температуре 25°С λ ≤ 0,079—0,116 Вт/(м·К).
522
Теплоизоляционные перлитокерамические изделия изготовляют из вспученного перлитового песка со средней плотностью до 80 кг/м3 на основе керамофосфатного связующего, легкоплавких или огнеупорных глин. В состав шихты могут быть введены огнеупорные компоненты, например шамот и др. Получаемые легковесные перлитосодержащие огнеупоры используют при температуре до 1300—1500°С. Вермикулитокерамические изделия прессуют из массы, состоящей из вермикулита и бентонитовой глины с введением в нее пены, а иногда и асбеста. По способу ВНИИСТРОМа высушенную огнеупорную глину после помола смешивают с вспученным вермикулитом в соотношении 1:3, после чего вводят алюминиевую пудру. Полученную массу укладывают в форму, виброуплототняют, сушат и обжигают.
Используют также волокнистые теплоизоляционные материалы из различных видов волокон — кремнеземистых, кварцевых, каолиновых, а также стеклокристаллических
(Al2O3 и ZrO2).
В последнее время на рынке строительных материалов находит спрос высокопористый керамический «Редоксит», получаемый своеобразным «вспучиванием» сырья при обжиге. Из 1 м3 исходной глины получают до 8 м3 готовых изделий с изотропией свойств по всему объему. Используют «Редоксит» для отделки стеновых блоков и плит, внутренних перегородок, изоляции междуэтажных и чердачных перекрытий, постройки хозяйственных бытовых сооружений: складов, гаражей, ангаров и др.
Относительно новым строительным материалом является керамический гранит, получаемый из экологически чистых природных продуктов, тщательно очищаемых от посторонних примесей, с добавлением естественных оксидных пигментов 10—12 цветовых оттенков. Плиты прессуют при давлении 45 МПа, после формования — обжигают в вакуумных печах при температуре 1200°С.
По прочности, износостойкости, морозостойкости, твердости керамический гранит превосходит натуральный и не имеет радиационного фона, а по шкале Мооса его твердость равна 8.
Этот новый материал используют для отделки промышленных предприятий, торговых центров, аэропортов, облицовки стен в банках, гостиницах. Так, например, он был применен для отделки Инкомбанка, ГУМа, аэропортов «Шереметьево» и «Домодедово» и других объектов.
523
Глава 18
Стеклянные и другие плавленые материалы и изделия
18.1. ЗНАЧЕНИЕ СТЕКЛЯННЫХ ИЗДЕЛИЙ В СТРОИТЕЛЬСТВЕ
История стекла уходит в глубокую древность. Известно, например, что в Египте и Месопотамии умели делать стекло почти 6000 лет назад. В России первый стекольный завод был построен в 1638 г. недалеко от г. Воскресенска. Большой вклад в технологию стекла внесли отечественные ученые: М.В. Ломоносов, Д.И. Менделеев, К.Г. Лаксман, А.А. Лебедев, В.Е. Тищенко и др. В современном строительстве значительно расширилась область применения архитектурно-строительных изделий из стекла. Конструктивно- строительные элементы — стеклоблоки, стеклопрофилит и стекло-пакеты — являются эффективным светопрозрачным строительным материалом.
За последние годы освоено получение полированного стекла путем формования непрерывной ленты на расплаве металла; химической обработкой поверхностей получают сверхпрочное листовое стекло, которое примерно в 20 раз прочнее обычного и в несколько раз прочнее закаленного. В химической и пищевой промышленности широко применяют стеклянные трубы, двери из закаленного стекла. Вспениванием стекла получают пеностекло — эффективный теплоизоляционный материал, который хорошо поддается механической обработке. Из стекла вырабатывают прочные нити, из которых изготовляют ткани, а из последних в сочетании с полимерами — стеклопластики. Синтезированы стекла с избирательным светопропусканием, выпускаются прочные, долговечные стеклокристаллические материалы — ситаллы, создано электровакуумное стекло для СВЧ — приборов с повышенной химической устойчивостью. Освоена технология ионообменного упрочнения очковых стекол и ветровых стекол автомобилей. Разработана технология особо чистого кварцевого стекла (КС-4В), новая технология утолщенного стекла (8—30 мм). Новым направлением в стекольном материаловедении являются синтез и технология получения биоактивных материалов на основе стекла, ситаллов, керамики и других неорганических материалов для применения в хирургии, ортопедии, стоматологии.
524
18.2. СОСТАВ И СТРОЕНИЕ СТЕКОЛ
Стекла являются неорганическими аморфными термопластичными материалами (микроконгломератами), обладающими рядом специфических свойств. По своему строению и составу они представляют собой системы типа истинного затвердевшего раствора из химических соединений кислотных и основных оксидов. Имеется условное деление оксидов, входящих в стекло, на стеклообразователи и модификаторы. Оксиды SiO2, В2О3, Р2О5 относятся к стеклообразующим, поскольку каждый из них в чистом виде может самостоятельно образовать стекло; например, при 100%-ном содержании SiO2 можно получить кварцевое стекло, которое обладает наиболее высокой температурой размягчения (1250°С). Так называется температура, при которой абсолютная вязкость стекла составляет 107—108 Па·с. Введением оксидов-модификаторов (Na2O, K2О, CaO, BaO, MgO, PbO, Al2O3, Fe2О3, Sb2O3, ZnO и др.) существенно снижают температуру размягчения стекла и придают стеклу необходимые свойства.
Если главную стеклообразующую часть стекол составляет SiO2, тогда стекла называют силикатными. В зависимости от вида и содержания добавочных оксидов стекла называют алюмосшшкатными, бороалюмосшшкатными, алюмофосфатными и т. п. В строительстве в основном применяют силикатные стекла. Подбором химического состава стекла предопределяют смесь оксидов, называемую шихтой.
Для получения силикатного стекла шихту приготовляют из различных сырьевых материалов, содержащих необходимые оксиды: кварцевый песок, сода или сульфат натрия, поташ, известняк и мел, доломит, пегматит, каолин, полевой шпат и др. В малых количествах в составы вводят стеклянный бой, красители (оксиды меди, хрома, кобальта, марганца и др.), осветлители (триоксид мышьяка, селитру и др.), глушители и др. В последнее время используют отходы: доменные шлаки, кварцсодержащие материалы, тетраборат кальция и другие. Перемешивание измельченных компонентов в строго отдозированных количествах (согласно расчетам) производят в смесителях барабанного или тарельчатого типа. Готовую шихту загружают в ванную печь—бассейн, сложенный из огнеупорных брусьев, или в горшковую печь. Бассейны больших ванных печей вмещают до 2500 т стекломассы — пластичного расплава шихты, образующегося при температуре свыше 1000°С.
При нагревании шихты до температуры 1100—1150°С происходят химические процессы силикатообразования, а при дальнейшем повышении температуры — стеклообразования. Шихта превращается в однородную (гомогенную) стекломассу, но со значительным содержанием в ней газовых включений (H2O, СО2 и др.). Осветление и дальнейшая гомогенизация стекломассы осуществляются при температуре 1500—1600°С, вязкость ее при этом уменьшается (до 10 Па·с), что облегчает удаление газовой фазы. Последний этап варки стекла — охлаждение (студка) стекломассы. Чем медленнее происходит охлаждение стекломассы, тем больше вероятность перехода ее в кристаллическое состояние; чем выше скорость охлаждения, тем более высокой температуре соответствует «замороженное» состояние структуры.
Практически формовка стекла, отобранного из печи, может производиться при вязкости его не менее 100 и не более 105 Па·с. К концу формовки вязкость может быть до 108 Па·с. У различных стекол зависимость вязкости г| от температуры различна (рис. 18.1). Оче- видно, что стекло легче обрабатывать, если стекломасса длинная, когда высокая вязкость обеспечивается при сравнительно медленном охлаждении. Например, стекла щелочные не только легкоплавкие, но и длинные. Введение CaO, MgO, Al2O3 переводит щелочные стекла в более короткие. Готовые стеклянные изделия часто подвергают отжигу, т. е. нагреву до достаточно высокой температуры (температуры отжига) с последующим медленным охлаждением. Отжигом снимают внутренние температурные напряжения в отформованных изделиях, что предотвращает их трещинообразование. При необходи-
525
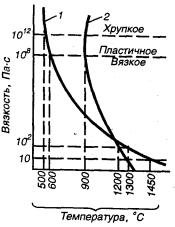
мости стекло можно снова нагреть и расплавить, при этом оно приобретает первоначальные свойства стекломассы, и переформовать в новые изделия.
Рис. 18.1. Характер зависимости вязкости стекломассы от температуры: 1 — стекломасса длинная; 2 — стекломасса короткая
В процессе производства стекла и особенно на стадии его охлаждения возникает структура, которая может быть охарактеризована как промежуточная между полной беспорядочностью частиц
жидкого расплава и полной упорядоченностью частиц вещества в кристаллическом состоянии. Неорганические стекла — это по существу субмикрогетерогенные системы, что позволяет по одной из гипотез рассматривать их структуру как скопление микрокристаллических, а точнее — кристаллитных образований размером от 10 до 300
o
A .
Согласно другой гипотезе в структуре стекла имеется непрерывная беспорядочная пространственная сетка (трехмерная). В ее узлах расположены ионы, атомы или группировки атомов. Например, в кварцевом стекле ионы Si расположены в центре тетраэдров, в углах которых размещены ионы О. При соединении тетраэдров SiO4 между собой (через один ион кислорода) вершинами образуется непрерывная пространственная сетка, или каркас стекла (рис. 18.2). В промежутках между тетраэдрами могут располагаться ионы металлов (флюсов), например в силикатных стеклах. Тогда возникают не только ковалентные, как в кварцевых стеклах, но и ионные связи, которые частично разобщают тетраэдры, уменьшают количество и силу поперечных связей (рис. 18.3), за счет чего уменьшается стабильность, характерная для структуры стеклообразных чистых оксидов, легче предотвращается кристаллизация, понижается температура плавления. Всякое силикатное стекло можно рассматривать как совокупность различных по составу и строению кремнекислородных комплексов. Кристаллитная гипотеза Лебедева и гипотеза неупорядоченной сетки Захариасена рассматривают стекло как полимерное образование в виде непрерывной пространственной сетки с различной степенью упорядоченности в расположении атомов. Максимально упорядоченные области — кристаллиты, т. е. преде- льно маленькие кристаллы, состоящие из очень небольшого числа элементарных ячеек.
526

Рис. 18.2. Ионные связи в молекуле кварцевого |
Рис. 18.3. Ионные связи в присутствии флюса |
стекла |
(Na) |
В настоящее время большинство ученых придерживается полимерного полиморфно- кристаллоидного строения стекла. Кристаллоид — частицы вещества, находящиеся в молекулярном раздроблении и способные к кристаллизации. Носители дальнего порядка (ДП) — кристаллиты — модифицируются в кристаллоиды, не имеющие дальнего порядка, а понятие полимеризации расширяется в понятие полиморфной полимеризации, в. которой участвуют кристаллоиды. Природа стекла и его свойства определяются концентрационным соотношением кристаллоидов различных полиморфных модификаций (ПМ) и его изменением в зависимости от внешних воздействий (температура, давление и др.). При охлаждении стекломассы происходит: а) перемещение и объединение звеньев цепей, фрагментов двух- и трехмерных сеток, т. е. полимеризация и б) превращение кристаллоидов одних ПМ в кристаллоиды других ПМ, причем второе при стеклообразовании является определяющим. Таким образом, полимерно-кристаллитная концепция трансформируется в полимерно-кристаллоидную концепцию, а учитывая, что при стеклообразовании сополимеризуются кристаллоиды различных ПМ, — в концепцию полимерного полиморфно-кристаллоидного строения стекла, в котором порядок и некоторый беспорядок сосуществуют.
527
18.3. СВОЙСТВА СТЕКОЛ
Свойства стекол зависят не только от химического состава, технологических режимов варки, но и от термической обработки. Важным условием формирования свойств является характер технологии закалки при быстром охлаждении и отжига — при медленном ох- лаждении. В стеклообразном состоянии могут быть получены многие вещества. В строительстве в основном применяют силикатное стекло, основным стеклообразующим оксидом в котором служит SiO2. Химический состав силикатных стекол (% по массе):
SiO2 — 64—73,4; Na2O — 10—15,5; К2О — 0—5; СаО — 2,5—26,5; MgO — 0-45; АШз — 0—7,2; Fe2O3 — 0—0,4; SO3 — 0—0,5; В2О3 — 0—5. Средняя плотность стекол изменяется в пределах 2,2—6 г/см3. Самые тяжелые стекла содержат оксиды свинца, висмута, а самые легкие — оксиды лития, бериллия, бора. Модуль упругости стекол 4,5·104—9,8·104 МПа. Стекло в процессе эксплуатации в строительных конструкциях подвергается в основном изгибу, растяжению и удару. Расчетный теоретический предел прочности при растяжении стекла составляет 12000 МПа, практический Rp — 30—80 МПа, что объясняется наличием в стекле микронеоднородностей, микротрещин, внутренних напряжений, пороков стекла (свилей), инородных включений и др. Предел прочности стекла при сжатии Rсж составляет 600—1000 МПа и более. Стекло плохо сопротивляется удару, т. е. оно относится к хрупким материалам. Прочность при ударном изгибе составляет ≈ 0,2 МПа. Большое влияние на сопротивление удару оказывает состояние поверхности стекла и наличие в нем пороков. У закаленных стекол сопротивление удару в 5—6 раз больше, чем у отожженных.
Оптические свойства стекла характеризуются в основном свето-пропусканием (прозрачностью). Обычные силикатные стекла хорошо пропускают всю видимую часть спектра и практически не пропускают ультрафиолетовые и инфракрасные лучи. По оптическим свойствам различают прозрачное, окрашенное, бесцветное и рассеивающее стекло. Силикатное стекло обладает высокой стойкостью к большинству реагентов, за исключением плавиковой и фосфорной кислот. В настоящее время получено ячеистое стекло и электровакуумное стекло с повышенной химической стойкостью. Температур- ный коэффициент линейного расширения обычных строительных стекол изменяется от 9·10-6 до 15·10-6 1/°C. От него зависит сопротивляемость стекла резким изменениям температуры (термическая стойкость). На термостойкость стекла влияют также состояние поверхности, форма, размеры изделий, их толщина. Наиболее низкий коэффициент температурного расширения у кварцевого стекла — 5,8·10-7 1/°С. Теплопроводность стекол 0,5—1 Вт/(м·К). Наибольшую теплопроводность имеет кварцевое стекло — 1,34 Вт/(м·К). Малой теплопроводностью обладают стекла с большим содержанием щелочных оксидов. Звукоизолирующая способность стекла относительно высока (при толщине стекла 1 см она соответствует кирпичной стене в полкирпича — 12 см).
528
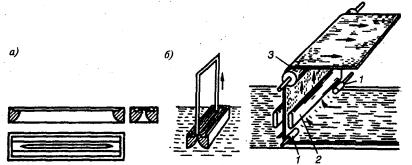
18.4. ОСНОВЫ ПРОИЗВОДСТВА СТЕКЛА
Производство строительного стекла состоит из подготовки сырьевых материалов (дробление, помол, сушка, просеивание и др.), приготовления шихты определенного химического состава, варки стекла, формования изделий и их отжига.
Варят стекло в стеклоплавильных печах непрерывного (ванные печи) или периодического (горшковые печи) действия. Стекловарение завершается студкой стекломассы до температуры, при которой она приобретает вязкость, необходимую для формования изде- лий.
Формование изделий осуществляют различными способами: вытягиванием ленты стекла лодочным и безлодочным способами, прокатом, литьем, прессованием, выдуванием. Вытягиванием изготовляют листовые стекла толщиной 2—6 мм, стеклянные трубы, стекловолокно. Сущность лодочного способа получения листового стекла заключается в следующем. В бассейн (он обычно имеет длину 5—6 м при глубине 1,2—1,5 м) с готовой стекломассой, охлаждаемой до температуры, соответствующей необходимой вязкости (не ниже 102 Па-с) погружается лодочка. Лодочка — это длинный прямоугольный шамотный брус со сквозным продольным вырезом, переходящим в верхней части в узкую щель. Под влиянием гидростатического напора стекломасса выдавливается через щель; растекания при этом не происходит (рис. 18.4). Если опустить на стекломассу, выдавливаемую из щели лодочки, горизонтально подвешенную стальную раму — «приманку», а затем от- тягивать ее вверх с помощью валиков специальной машины ВВС (вертикального вытягивания стекла), то за приманкой потянется лента стекла. Отформованная лента стекла охлаждается и отжигается в шахте машины. После выхода из шахты от нее отрезают листы требуемых размеров.
При безлодочном способе (вертикальном и вертикально-горизонтальном) в стекломассу погружают огнеупорный поплавок со сквозной щелью или без нее. Поплавок способствует созданию направленного потока стекломассы, помогающего стабилизировать формование ленты стекла. При этом способе лента стекла поднимается непосредственно со свободной поверхности стекломассы с помощью бортоформующих роликов (рис. 18.5).
Методом проката, при котором стекломасса сливается на гладкую поверхность и прокатывается валками с гладкой или узорчатой поверхностью, изготовляют крупноразмерное листовое стекло (гладкое и узорчатое), коврово-мозаичные плитки, а также стекло, армированное металлической сеткой (рис. 18.6).
Рис. 18.4. Лодочный способ вытягивания стекла: |
Рис. 18.5. Схема безлодочного вытягивания |
а — лодка; б — схема вытягивания ленты стекла |
стекла: 1 — растягивающие ролики; 2 — |
|
холодильник; 3 — перегибной вал |
Стекло с высоким качеством поверхности и утолщенное (8—30 мм) получают эффективным флоат-способом (рис. 18.7). При этом способе формование ленты стекла происходит на поверхности расплавленного олова в результате растекания стекломассы. Такое стекло не нуждается в последующей полировке, имеет ровные края.
529
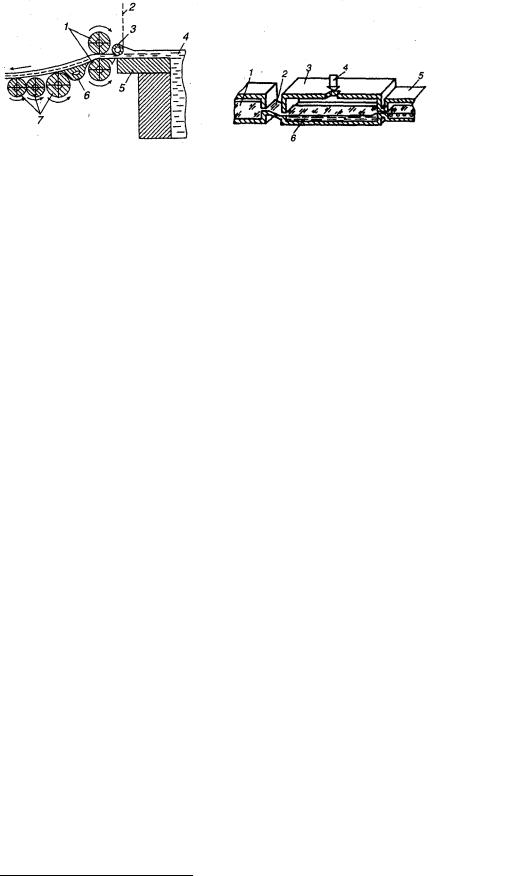
Рис. 18.6. Схема непрерывной прокатки |
Рис. 18.7. Схема установки для производства |
листового стекла: 1 — прокатные валки; 2 — |
стекла по способу флоат-процесса: 1 — |
арматурная сетка; 3 — валик для арматурной |
стекловаренная печь; 2 — лоток для слива стекла; |
сетки; 4 — выработочная часть стекловаренной |
3 — флоат-ванна; 4 — место подачи газов |
печи; 5 — сливной порог, 6 — плита; 7 — |
защитной атмосферы; 5 — печь отжига; б — |
транспортирующие валики |
расплав олова |
Прокатывая стекло и загибая его края в форме швеллера или коробки, получают профильное стекло. При изготовлении труб используют способ вальцевания, при котором непрерывная струя стекломассы поступает на вращающийся вал, распределяется по его поверхности по спирали, затем развальцовывается и разглаживается с помощью роликов. Методом прессования в формах с помощью керна (пуансона), создающего давление на стекломассу, изготовляют изделия крупных размеров и большой толщины (стеклоблоки). Методом центробежного формования (частота вращения форм 800—1200 об/мин) изго- товляют цилиндры, трубы, свето- и радиотехнические приборы.
Отформованные изделия обязательно отжигают для уменьшения внутренних напряжений в специальных печах или в шахтах машин ВВС.
Если стекло нагреть до пластичного состояния, а затем резко охладить его, то можно вызвать появление равномерно распределенных остаточных напряжений, которые придают стеклу повышенную механическую прочность при ударе и изгибе, повышенную термостойкость. Этот процесс называют закалкой; для закалки используют электрические печи или шахтные закалочные агрегаты.
Высокопрочные стекла получают путем химического и термохимического упрочнения его поверхности1; Некоторые стеклоизделия подвергают декоративной обработке, в частности напылению
стеклопорошков плазменной горелкой на их подложки (листовое стекло, посуду). Листовое стекло шлифуют, полируют. Отходы шлифования можно использовать при производстве автоклавных силикатных материалов.
Разновидности ИСК, вяжущая часть которых представлена затвердевшим неорганическим стеклорасплавом, называют стекло-конгломератами. Их изготовляют пока в небольшом объеме, например стеклокремнезит, стекломрамор, стеклошамотный огнеупор.
Общие закономерности формирования их структуры соответствуют общей теории ИСК. В качестве заполнителей могут использоваться отходы от ремонта различных печей (динасовые, шамотные, магнезитовые, шпинелевые и др.), а также горные породы: кварцевый песок, мраморная крошка и др. Стекломасса при затвердевании вступает в физико-химическое взаимодействие с заполнителями, вследствие чего образуются пограничные контактные зоны. Изготовление стеклоконгломератов может производиться по двум принципиальным технологическим схемам: 1) расплав стекломассы в минимально необходимом количестве вводят в плотную смесь огнеупорных заполнителей, температура плавления которых выше
1 Железцов В. А., Янбаева Г.У. и др. Способ упрочнения изделий из стекла. Авт. св. №793206. Б.И. 1981, 12,
с.5
Железцов В. А., Янбаева Г.У. Зависимость ионного обменного упрочнения - 1 от его термической предыстории. — Физика и химия стекла, 1983, т. 9. № 4.
530