
- •к.т.н., начальник отдела ОНИР СиМУ ЭЛТИ, сопредседатель секции №1
- •д.т.н., профессор, зав. каф. фмпк эфф, председатель секции № 9
- •СЕКЦИЯ 1. ЭЛЕКТРОЭНЕРГЕТИКА
- •АВТОМАТИЗАЦИЯ РАСЧЕТА СТРУКТУРНОЙ НАДЕЖНОСТИ ЭЛЕКТРИЧЕСКИХ СХЕМ
- •ОСОБЕННОСТИ МОДЕЛИРОВАНИЯ ЭЛЕКТРИЧЕСКОГОПОЛЯ В МОРСКОЙ ВОДЕ
- •КАБЕЛЬ ДЛЯ ЭЛЕКТРОПИТАНИЯ ГЕНЕРАТОРОВ НИЗКОТЕМПЕРАТУРНОЙ ПЛАЗМЫ
- •Колпаков В.А., Паранин В.Д., Мокеев Д.А………………...86
- •СПОСОБЫ СЕЛЕКЦИИ КОРОТКИХ ЗАМЫКАНИЙ НА ЛИНИЯХ ЭЛЕКТРОПЕРЕДАЧИ
- •СЕКЦИЯ 2. ПРИБОРОСТРОЕНИЕ
- •ИСПОЛЬЗОВАНИЕ КОМПЬЮТЕРНОГО МОДЕЛИРОВАНИЯ ПРИ ИССЛЕДОВАНИИ СПОСОБА КОМПЕНСАЦИИ ДЕЙСТВИЯ ВИБРАЦИИ НА ГИРОМАЯТНИК
- •РАЗРАБОТКА И ИССЛЕДОВАНИЕ МИКРОМЕХАНИЧЕСКОГО ГИРОСКОПА
- •НОРМИРОВАНИЕ ШИХТОВЫХ МАТЕРИАЛОВ ДЛЯ ПРОИЗВОДСТВА ОТЛИВОК ИЗ АЛЮМИНИЕВЫХ СПЛАВОВ
- •ИНВЕРТОРНЫЙ ИСТОЧНИК ПИТАНИЯ ДЛЯ СВАРКИ МОДУЛИРОВАННЫМ ТОКОМ
- •ИССЛЕДОВАНИЕ ВЛИЯНИЯ ОТКЛОНЕНИЯ КОРПУСА НА ЦИКЛ РАБОТЫ ПНЕВМОГИДРАВЛИЧЕСКОГО УДАРНОГО МЕХАНИЗМА
- •ДИНАМИЧЕСКИЕ ПРОЦЕССЫ В БУРОВОЙ КОЛОННЕ ПРИ ВРАЩАТЕЛЬНО-УДАРНОМ БУРЕНИИ СКВАЖИН МАЛЫХ ДИАМЕТРОВ
- •СЕКЦИЯ 4. ЭЛЕКТРОМЕХАНИКА
- •ВЛИЯНИЕ ДЛИНЫ АСИНХРОННОГО ДВИГАТЕЛЯ НА ЭФФЕКТИВНОСТЬ КРЕПЛЕНИЯ
- •РЕЗУЛЬТАТЫ ЭКСПЕРИМЕНТАЛЬНЫХ ИССЛЕДОВАНИЙ ХАРАКТЕРИСТИК СИНХРОННОГО ГИБРИДНОГО ДВИГАТЕЛЯ
- •РАЗРАБОТКА ЭЛЕКТРОМЕХАНИЧЕСКОГО ПРЕОБРАЗОВАТЕЛЯ С АКТИВНЫМ И РЕАКТИВНЫМ ДИСКАМИ В МАГНИТНОЙ СИСТЕМЕ
- •ПРОГРАММА ВЫЯВЛЕНИЯ ФАКТОРОВ РИСКА РАКА МОЛОЧНОЙ ЖЕЛЕЗЫ С ИСПОЛЬЗОВАНИЕМ МЕТОДА МЕТА-АНАЛИЗА
- •ИССЛЕДОВАНИЕ ВОЗМОЖНОСТИ ИСПОЛЬЗОВАНИЯ МЕТОДА ФОТОМЕТРИРОВАНИЯ КАПЕЛЬНЫХ ПРОБ ДЛЯ ОЦЕНКИ АГРЕГАЦИОННЫХ СВОЙСТВ КЛЕТОК КРОВИ
- •ИСПОЛЬЗОВАНИЕ МИКРОВОЛНОВОЙ РАДИОТЕРМОМЕТРИИ В ДИАГНОСТИКЕ РАКА МОЛОЧНОЙ ЖЕЛЕЗЫ
- •УСТАНОВКА ДЛЯ ОПРЕДЕЛЕНИЯ ГИДРОДИНАМИЧЕСКИХ ХАРАКТЕРИСТИК КЛАПАННЫХ ЗАМЕНИТЕЛЕЙ, КАК ПОКАЗАТЕЛЕЙ КАЧЕСТВА И ПРИГОДНОСТИ ДЛЯ КАРДИОХИРУРГИИ
- •Введение
- •ЭКОНОМИЧНЫЙ И ЭКОНОМНЫЙ УМЗЧ 2×200Вт С БЛОКОМ ПИТАНИЯ
- •Мариненко А.В.
- •Благодарности
- •Компонента
- •МЕТОДИКА ОБРАБОТКИ КАРТИН ИНТЕРФЕРЕНЦИОННЫХ ПОЛОС
- •ЛИТЕРАТУРА:
- •Описание процесса моделирования
- •Вывод
- •Благодарности
- •ИСПОЛЬЗОВАНИЕ КОМПЬЮТЕРНОГО МОДЕЛИРОВАНИЯ ПРИ ИССЛЕДОВАНИИ СПОСОБА КОМПЕНСАЦИИ ДЕЙСТВИЯ ВИБРАЦИИ
- •НА ГИРОМАЯТНИК
- •Перспективы
- •Экспериментальная часть
- •Заключение
- •Рисунок 3. Результаты моделирования работы системы
- •ЛИТЕРАТУРА:
- •СКОРОСТНОЙ ЭФФЕКТ В ВИХРЕТОКОВОМ КОНТРОЛЕ
- •Введение
- •Благодарности
- •ЛИТЕРАТУРА:
- •E-mail: yuyug@npi.tpu.ru
- •Наименование параметра
- •Полоса
- •частот, Гц
- •Результаты и обсуждение
- •ЛИТЕРАТУРА:
- •ЛИТЕРАТУРА:
- •Тогда энергия, переданная упругому элементу, согласно (2) будет равна:
- •ПРОБЛЕМА ИССЛЕДОВАНИЯ ТРЕХЗВЕННЫХ МЕХАНИЗМОВ
- •ЛИТЕРАТУРА:
- •420066, г. Казань, Красносельская ул., 51
- •E-mail: BakirovAR@rambler.ru
- •420066, г. Казань, Красносельская ул., 51
- •E-mail: BakirovAR@rambler.ru
- •Введение
- •Выводы
- •Выводы
- •ОПТИМИЗАЦИЯ РЕЖИМОВ ЭКСПЛУАТАЦИИ УСТАНОВОК ТИПА УЭЦН С ПЧ
- •ЦИФРОВАЯ ЛАБОРАТОРИЯ ЭЛЕКТРОМЕХАНИКА
- •ЭЛЕКТРОМАГНИТНЫЙ МОМЕНТ В ИНДУКЦИОННЫХ ДВИГАТЕЛЯХ
- •Материал и методы исследования
- •Заключение и некоторые перспективы
- •ЛИТЕРАТУРА:

XIII Международная научно-практическая конференция «СОВРЕМЕННЫЕ ТЕХНИКА И ТЕХНОЛОГИИ»
рения на конечном этапе возрастала в большей степени), либо путем корректировки кривой суммарного среднего виброускорения от коллектора и якоря электродвигателя (необходимо, чтобы кривая была более пологая).
Характер кривой ускорения, обеспечиваемого нажимной пружиной, зависит от свойств пружины, типа нажимного устройства, марки щетки, а также интенсивности ее изнашивания, которая, в свою очередь, определяется комплексом конструкторскотехнологических параметров, характеризующих проектирование и производство электрических машин. Влияние данных факторов подлежит теоретическому анализу с целью выработки рекомендаций по повышению ресурсных характеристик коллекторных электрических машин наряду с общеизвестными
направлениями их совершенствования - повышением монолитности коллектора и качества подшипниковых узлов.
ЛИТЕРАТУРА:
1.Качин С.И., Боровиков Ю.С., Нечаев М.А. Программно-аппаратный комплекс для оценки механического состояния скользящих контактов коллекторных электрических машин электроприводов. // Известия Томского поли-технического университета. – 2004. -
т.307, №1.
2.Фиш А.Я., Тарнопольский Ю.М., Акунц К.А., Петров А.В. Коллекторы электрических машин на пластмассе. – М: Государственное энергети-ческое издательство, 1963. -192с.
3.Руссов В.А. Спектральная вибродиагностика. – Пермь, 1996.
ОПТИМИЗАЦИЯ РЕЖИМОВ ЭКСПЛУАТАЦИИ УСТАНОВОК ТИПА УЭЦН С ПЧ
Козлов В.В.
Тюменский государственный нефтегазовый университет, г. Тюмень, ул. Володарского 38
Е-mail: kvassmail@mail.ru
В настоящее время в нефтедобывающей отрасли все большее применение находит частотно-регулируемый привод. Это дает возможность повысить адаптивность установки к возможностям пласта и значительно снизить отрицательный эффект, вызванный не- соответ-ствиием выбранного типоразмера оборудования требуемому в каждом конкретном случае.
Но при этом из анализа информации поступающей с нефтепромыслов Юганского региона установлено, что использование ПЧ не дает какого-либо прироста межремонтного периода (МРП), потому что существующие методы и алгоритмы управления не учитывают интенсивность расходования ресурса оборудования и не ставят одной из целей управления его экономию и продление срока службы установки, в то время как увеличение МРП, особенно на высокодебитных скважинах, должно дать значительный экономический эффект.
Таким образом, требуется разработка принципиально новых методов и алгоритмов управления установками типа УЭЦН с ПЧ, учитывающих указанные факторы. Это особенно актуально для месторождений с высо-
ким уровнем солеотложения на рабочих органах насоса и их абразивного износа, где происходит более интенсивное расходование ресурса оборудования.
Явление солеотложения приводит к изменению со временем величины момента статического сопротивления насоса Мст. Основной причиной этого является подкли-нивание рабочих колес из-за отложения на их поверхностях содержащихся в пластовой жидкости солей. Все это происходит на фоне процесса регулирования скорости вращения насоса, которое так же приводит к изменению рабочей точки, при этом момент статического сопротивления насоса на интервале управления имеет тенденцию к увеличению.
Если допустить, чтобы он сравнялся или превысил максимальный момент, развиваемый двигателем, произойдет заклинивание насоса и выход УЭЦН из строя. Поэтому на нефтепромыслах практикуется увеличение величины питающего напряжения ПЭД, что позволяет увеличить максимальный момент, развиваемый двигателем, и тем самым, его перегрузочную способность, снизив этим риск заклинивания. Отрицательным эффектом в
432

Современные техника и технологии 2007
данном случае является увеличение тепловых потерь в двигателе.
Абразивный износ, вызывая изменение гидравлической характеристики насоса и уменьшение потока перекачиваемой жидкости, за счет появления паразитных, локальных потоков при сохранении потребляемой погружным электродвигателем мощности, приводит к ухудшению режима его охлаждения. В совокупности с указанным выше увеличением тепловых потерь это вызывает перегрев двигателя и повышенный износ ресурса его изоляции, который, как правило, в расчет не принимается, но в значительной степени определяет продолжительность МРП.
Исследовав характер протекания процесса солеотложения, можно сделать вывод, что подклинивание рабочих органов насоса происходит в момент пуска установки после ее простоя при циклическом режиме работы скважины или после аварийной остановки. То есть поддержание необходимой перегрузочной способности двигателя необходимо только на время вывода скважины на установившийся режим. В остальное время перегрузочную способность двигателя можно снижать до минимально необходимого уровня, который определяется величиной момента статического сопротивления насоса и требованиями оптимального режима работы двигателя с точки зрения потерь электроэнергии в нем.
При этом возникает необходимость в определении момента статического сопротивления насоса, которая в данном случае представляет собой сложную техническую задачу, так как непосредственное измерение невозможно.
Для организации согласованного управления по частоте и величине питающего напряжения с учетом указанных выше факторов предлагается использовать математическую модель системы «УЭЦН-скважина». Она вклю-чает в себя уравнения асинхронного двигателя, насоса и преобразователя частоты, а так же уравнения, описывающие темп солеотложения и абразивного износа и учитывающие влияние длинного кабеля и трансформатора.
Стратегия управления будет определяться из следующих условий:
Qпл – Qн → 0 , |
(1) |
где Qн – производительность насоса; Qпл – величина максимально возмож-
ного потока жидкости из пласта.
M (t) |
= |
Mст (t) + ε, |
(2) |
где |
M, |
Mст (t) – |
электромагнитный мо- |
мент развиваемый двигателем и момент статического сопротивления насоса, соответственно;
|
ε – малая величина, ε >0. |
||||
P → min |
|
|
(3) |
||
где |
P – |
потери в двигателе. |
|||
n |
|
|
|
(4) |
|
∑( |
qi + Pi ) ti |
→ min |
|||
|
|||||
i=1 |
|
Pi – |
величина потерь дебита и |
||
где |
qi, |
электроэнергии на i-м интервале управления, выраженная в рублях.
Таким образом, уравнения (1,2,3) определяют технологический оптимум работы установки УЭЦН и нацелены на согласование производительности установки с возможностями пласта с одной стороны и экономное расходование ресурса насоса и двигателя, с другой. Условие (4) определяет экономическую целесообразность принятой стратегии управления и имеет ключевое значения при принятии окончательного решения.
Описанная методика отличается от применяемой сейчас на практике. Она обеспечивает увеличение продолжительности МРП за счет экономии ресурса УЭЦН в начальный период эксплуатации, с возможностью последующего его использования на конечном периоде, когда насос работает при повышенных нагрузках.
ЛИТЕРАТУРА:
1.Лысова О.А., Ведерников В.А. Системы управления электроприводов. Тюмень, 2005.
2.Ведерников В.А., Лысова О.А. Оптимизация системы электропривода погружного насоса. Изв. вузов. Нефть и газ.- 2002. № 5,
с.88 -94.
3.Ведерников В.А., Гапанович В.С. Модели управления системами «скважина – УЭЦН». Изв. вузов. Нефть и газ.- 2006. №1,
с.15-20.
433

XIII Международная научно-практическая конференция «СОВРЕМЕННЫЕ ТЕХНИКА И ТЕХНОЛОГИИ»
ЦИФРОВАЯ ЛАБОРАТОРИЯ ЭЛЕКТРОМЕХАНИКА
Корнеев К. В.
Новосибирский Государственный Технический Университет, Россия, г. Новосибирск, пр. к. Маркса, 20
E-mail: heart1981@mail.ru
Изучение электромеханических процессов, которые происходят в электрической машине за время переходного процесса, являет собой сложную задачу и связанно с решением различных аналитических и численных задач. Большую роль в данном вопросе играет математическое моделирование, на базе моделей различной степени сложности. В настоящее время широкие возможности для проведения математического моделирования предоставляет вычислительная техника. Так же широк и выбор необходимого программного обеспечения. Которые позволяют исследователю провести исследования полностью используя потенциал вычислительной техники, таким образом, уменьшив время необходимое на проведение исследований и имея возможность изменения параметров исследуемого объекта, в более широких пределах, нежели при проведении физического эксперимента, [1].
Ярким примером служит система инже-
нерных расчетов Matlab (Matrix laboratory),
позволяющая решать весь спектр задач, возникающих в различных областях человеческой деятельности. На базе данного программного продукта и его приложения GUIDE (Graphical User Interface Development) [2], яв-
ляющегося средой визуального программирования, был создан программный комплекс
DLEM (Digital Laboratory of Electromechanics),
позволяющий производить математическое моделирование различных режимов работы электрических машин. Основой графического интерфейса служит окно Windows, со всеми присущими ему атрибутами. Главное меню предоставляет пользователю возможность выбора типа машины и режима ее работы, реализованного на базе стандартных элементов Windows – это кнопки, выпадающие списки, переключатели. В соответствии со сделанным пользователем выбором, производится последовательный переход к модулю, отвечающему за проведение математического моделирования выбранного объекта. Каждый расчетный модуль содержит в своем составе меню, содержащее описанные выше элементы, а так же поля для ввода параметров электрической машины и других, необходимых для расчета данных. Необходимо отметить, что в каждом программном модуле
пользователю предоставляется возможность сохранения введенных параметров и полученных результатов. Так же, каждый программный модуль предоставляет пользователю возможность получить пример параметров, которые необходимы для расчета, и произвести исследования с их помощью. В состав каждого расчетного модуля входят исполняемые файлы, содержащие математические модели, расчетные алгоритмы и т. д. Таким образом, программный комплекс DLEM содержит необходимый графический интерфейс и пользователю необходимы минимальные знания по программированию для проведения исследования предоставленной номенклатуры электрических машин и режимов их работы, которые включают в себя:
•Прямой пуск двигателя постоянного тока независимого и параллельного возбуждения;
•Внезапное короткое замыкание генератора постоянного тока параллельного и смешанного возбуждения
•Внезапное короткое замыкание синхронного генератора с демпферным контуром
ибез него, с возможностью проведения анализа влияния параметров электрической машины на переходный процесс;
•Прямой пуск асинхронного двигателя с короткозамкнутым ротором, с возможностью проведения исследований в различных системах координат.
Во всех случаях математическое моделирование производится на основании математической модели машины в ортогональной системе координат, в которой преобразованные контуры обмоток статора и ротора неподвижны относительно друг друга.
Для машин постоянного тока математические модели созданы на базе общепринятых допущений, позволяющих рассматривать некоторую идеализированную электрическую машину, которая характеризуется: отсутствием насыщения магнитной цепи, гистерезиса и потерь в стали; отсутствие вытеснения тока в меди обмоток; синусоидальное распределение в пространстве кривых МДС и индукции; независимостью индуктивных сопротивлений обмоток машины от положения ротора; полной симметрией обмотки якоря.
434

Современные техника и технологии 2007
Математическая модель представляет собой систему уравнений электрических контуров машины в неподвижной координатной системе статора (αβ) и уравнения движения, при рассмотрении внезапного короткого замыкания полагаем, что частота вращения ротора неизменна в течение переходного процесса. Система уравнений записана относительно токов и является системой дифференциальных уравнений с постоянными коэффициентами. Результатом математического моделирования, по введенным пользователем данным, являются осциллограммы токов в различных контурах, а так же при рассмотрении пуска и частоты вращения. Таким образом, данный модуль предоставляет возможность исследования процессов электромеханического преобразования энергии в машинах постоянного тока и полезен при их изучении в рамках учебного процесса.
Математической моделью синхронного генератора является система уравнений Пар- ка-Горева, записанная в относительных единицах. Система уравнений, так же является системой дифференциальных уравнение с постоянными коэффициентами. В данном случае, система уравнений записана относительно потокосцеплений, с последующим вычислением необходимых величин. Результатами являются осциллограммы токов контуров статора и ротора по соответствующим осям d и q; электромагнитного момента; токов фаз в соответствии с заданным начальным углом поворота ротора. При моделировании принимались допущения, что частота вращения ротора неизменна, в течение переходного процесса. Т. к. генератор находиться в режиме короткого замыкания, то реакция якоря - размагничивающая и результирующий магнитный поток незначителен, в результате чего магнитная система машины не насыщенна. Необходимо отметить, что уровень принимаемых допущений, при моделировании внезапного короткого замыкания синхронного генератора, позволяет проводить исследования с достаточной степенью точности и таким образом данный программный модуль может быть полезен как в инженерной деятельности, так и в учебном процессе. Так с его помощью были проведены исследования внезапного короткого замыкания различных генераторов, в частности Саяно-Шушенского гидрогенератора. Проведенный анализ и сравнение полученных результатов с опытными данными, показали, что математическая модель удовлетворяет необходимым критериям точности.
Программный продукт позволяет произвести математическое моделирование асинхронного двигателя в различных системах
координат: неподвижной координатной системе статора, вращающейся координатной системе ротора, синхронно вращающейся координатной системе. Моделирование производится с учетом эффекта вытеснения тока в пазу ротора, а так же насыщения коронок зубцов. Учет вытеснения тока производиться на основании предложенного в [3] метода для расчета сопротивлений многозвенной схемы замещения стержня ротора. Основанного на том, что при известной конфигурации магнитных линий потока рассеяния в пазу, массивный проводник (стержень короткозамкнутой обмотки), представляем как совокупность большого количества элементарных слоев, изолированного друг от друга бесконечно малым слоем изоляции, границы которых определяются магнитными силовыми линиями. На основании изложенной в [3] методики создана модель, которая производит расчет зависимости индуктивного и активного сопротивления ротора от скольжения, которая затем используется непосредственно при моделировании переходного процесса. Данные зависимости были получены с применением сплайн интерполяции и таким образом математическая модель, для всех координатных систем, представляет собой систему дифференциальных уравнений с переменными коэффициентами. Как показали проведенные исследования, представленная математическая модель удовлетворяет необходимой точности и погрешность, в сравнении с характеристиками, рассчитанными по стандартной методике, составляет порядка 5% для двигателя 4А132М8У. проведенные на основании данного программного модуля исследования показали, что применение синхронно вращающейся системы координат, в сравнении с традиционно применяемой координатной системой статора, в некоторых случаях более рационально. Т. к. на одинаковом временном промежутке для расчета в координатной систем статора требуется разбиение временного интервала в 200 эл. сек. на 661 интервал, а для синхронно вращающейся координатной системы 409. Таким образом, данная модель так же может служить, как в учебных, так и инженерных целях.
В свою очередь, необходимо отметить, что данный программный комплекс является открытым, что позволяет пользователю, при необходимости внести в него дополнения и уточнения, в соответствии с решаемой задачей. Таким образом, имея возможность применения одних и тех же, программных модулей для различных математических моделей, являет собой возможность построения моделей различного уровня сложности. В настоящий программный продукт DLEM, заложены
435

XIII Международная научно-практическая конференция «СОВРЕМЕННЫЕ ТЕХНИКА И ТЕХНОЛОГИИ»
широкие возможности по исследованию электрических машин, так отдельные модули уже внедрены и используется в учебном процессе на кафедре "Электромеханика" Новосибирского Государственного Технического Университета. В настоящее время ведется работа по расширению данного программного продукта и по внедрению его в учебный процесс. Расширение данного программного продукта может позволить охватить большой комплекс проводимых исследований в области переходных процессов в электрических машинах.
ЛИТЕРАТУРА:
1. Пастухов В. В., Шорников Ю. В., Ландовский В. В., Жданов Т. С. Автоматизация
машинных экспериментов с динамическими моделями электромеханических систем // Коллективная монография Автоматизированные электромеханические системы. Новоси-
бирск: НГТУ, 2004. – 276 с.
2.Корнеев К. В. Моделирование электрических машин в MATLAB с применением среды GUIDE // Материалы всероссийской научной конференции молодых ученых в 7-ми частях. Новосибирск: НГТУ, 2006, часть 3 -245 с.
3.Проектирование электрических машин: Уч. пос. для вузов/ И. П. Копылов, Ф. А. Горяинов, Б. К. Клоков и др.; Под ред. И. П. Копылова. – М.: Энергия, 1980. – 496 с., ил.
МЕТОДЫ АНАЛИЗА И СИНТЕЗА СИСТЕМ ЛОГИЧЕСКОГО УПРАВЛЕНИЯ ШАХТНЫХ ПОДЪЕМНЫХ УСТАНОВОК
Кубарев В.А.
ГОУ ВПО «СибГИУ», 654007, Россия, г. Новокузнецк, ул. Кирова, 42 kva2003@nightmail.ru
Современное состояние ни в области сис- |
|
тем управления за последние 10 -15 лет пре- |
|
терпело, коренные изменения в части эле- |
|
ментной базы создаваемых систем, в части |
|
же методов проектирования подобных корен- |
|
ных изменений не наблюдается. Известные |
|
системы логического управления часто соз- |
|
даются и выпускаются недостаточно прора- |
|
ботанными с точки зрения системного подхо- |
|
да. И это несмотря на то, что система логиче- |
|
ского управления, например, электроприво- |
|
дом шахтной подъемной установки, является |
|
более сложной системой, чем система авто- |
|
матического регулирования (САР), или сис- |
|
тема управления возбуждением гонного син- |
Рисунок 1 – Место СЛУ в системе управ- |
хронного (СУВСД) или подъемного двигателя |
|
(СВДПТ), так как в задачу САР входит лишь |
ления электроприводом и её взаимосвязи |
поддержание постоянства выходной величи- |
Как видно из рисунка 1 система логиче- |
ны, а система логического управления явля- |
|
ется связующем звеном между системой |
ского управления через определенные пара- |
управления загрузкой скипа (СУЗС), САР, |
метры (ток, сигналы управления) связана со |
СУВСД, СВДПТ (Рисунок 1). |
всеми системами подъемной установки и яв- |
|
ляется её центром, поэтому её разработке |
|
должно уделяться не меньше внимания, чем |
|
разработке САР или СВСД. Поэтому в данной |
|
статье делается попытка показать методику |
|
исследования и синтеза СЛУ. |
|
Система управления подъемной установ- |
|
кой в целом включает в себя 6 асинхронно |
436

Современные техника и технологии 2007
взаимодействующих управляющих систем (Рисунок 1):
1.Систему логического управления.
2.Программируемый аппарат задания контроля движения и технологических защит.
3.Систему управления загрузкой скипа.
4.Систему автоматического регулирования скорости, которая поддерживает постоянство скорости подъема сосуда.
5.Систему возбуждения двигателя постоянного тока (подъемного двигателя)
6.Систему управления возбуждением синхронного двигателя.
Одним из наиболее подходящих методов для анализа подобных систем является предлагаемая методика. Данная методика включает в себя следующие этапы:
1) Производится функциональный анализ системы управления, целью которого является выделение отдельных функционально автономных блоков системы.
2) Составляется обобщенный граф работы каждой из подсистем.
3) Составляется детальный граф работы каждой из подсистем, характеризующий переходы подсистем из одного состояния в другое и сигналы событий, передаваемые от одной подсистемы другой.
4) На основе составленных графов и проведенного анализа определяется оптимальный граф.
Ниже представлены графы функционирования основных логических подсистем системы управления подъемной установки, то есть ПАЗК, СЛУ, СУЗС. Точками обозначены состояния подсистем, сплошными линиями – переходы из состояния в состояние, пунктирными линиями – сигналы событий, передаваемые от одной подсистемы к другой.
На рисунке 2 представлен обобщенный граф работы системы автоматики шахтной подъемной установки. На данном графе обозначены следующие состояния ПАЗК: 1) «Не готов» — Устройство работоспособно ожидает команды на переход в режим «Готовность»
2)«Готовность» — Устройство ожидает команды на пуск машины для перехода в режим «Работа» 3) «Работа» — Машина запущена, идет циклическое отслеживание состояния процесса «Подъем» 4) «Авария» — зафиксирован критический сбой, происходит аварийное прерывание процесса «Подъем», цикл подъема сосуда прекращается, система ожидает вмешательства оператора.
Следующей подсистемой является программируемый аппарат задания, контроля движения и технологических защит шахтной подъемной установки. За основу возьмем граф представленный в [1, стр. 116-121] (Рисунок 3).
Рисунок 2 – Обобщенный граф работы системы технологической автоматики ШПУ
Рисунок 3 – Граф работы ПАЗК
На данном графе обозначены следующие состояния ПАЗК: 5) «Не готов», 6) «Готовность», 7) «Работа», 8) «Предаварийное состояние» — зафиксирован некритический сбой в устройстве, цикл подъема может быть завершен 9) «Авария». Режимы работы 5, 6, 7, 9 соответствуют описанию рисунка 2.
Далее составляем граф работы системы автоматики дозаторной (Рисунок 4). Состояния системы автоматики дозаторной можно представить в следующей последовательности:
10) «Ожидание приема скипа».11) «Ожидание загрузки» — скип под загрузкой, система ждет команды на открытие дозаторов. 12) Открытие дозатора 14) «Загрузка» — затвор открыт, наполнение скипа. 15) «Закрытие дозатора» 16) «Готов к отправке» — затвор закрыт, скип заполнен и готов к отправке (передается сигнал 15-27)
На заключительном этапе можно составить граф работы СЛУ с учетом передаваемых в неё сигналов из других подсистем (Рисунок 5).
437

XIII Международная научно-практическая конференция «СОВРЕМЕННЫЕ ТЕХНИКА И ТЕХНОЛОГИИ»
Рисунок 4 – Граф работы системы автоматики дозаторной
Рисунок 5 – Граф работы системы логического управления ШПУ
21) «Авария» — критический сбой.. 22) «Не готов» — Ожидается включение ВАБ, масляных выключателей и цепи предохранительного торможения (ТП). 23) «МВ» — включение масляных выключателей главных вводов. 24) Проверка готовности систем автоматики 25) Включение ВАБ 26) Сбор цепи ТП. 27) Готовность к отправке. 28) Разрешение работы САР. 29) Ожидание нарастания тока, до тока растормаживания 30) Растормаживание 31) Процесс «Подъем». 32) Разгрузка скипа — переход на узел 27
Использование представлений процессов управления в виде графов и структур позволяет четко отслеживать топологию и структуру взаимодействия каждой подсистемы как части единого целого.
ЛИТЕРАТУРА:
1. Островлянчик В. Ю., Модзелевский Д. Е. Принципы построения алгоритмических структур систем логического управления современного электропривода. // Автоматизированный электропривод и промышленная электроника в металлургической и горнотопливной отраслях: Труды Второй всероссийской научно практической конференции / Под. Ред. В.Ю. Островлянчика, П. Н. Кунинина, Новокузнецк, 2004 г. — 253 с.
МЕТОДИКА ОПРЕДЕЛЕНИЯ СТАТИЧЕСКИХ РЕЖИМОВ ПРЕОБРАЗОВАТЕЛЕЙ С ИСКУССТВЕННОЙ КОММУТАЦИЕЙ
ЛадановА. С., ЗайцевА. И.
Воронежскийгосударственныйтехническийуниверситет,
г. Воронеж, пр-ктМосковский, д. 14;
Е-mail: ladanov_alex_s@mail.ru
Использование в вентильных системах полностью управляемых элементов (силовых транзисторов, запираемых тиристоров) позволяет осуществлять работу выпрямителей
врежиме с опережающими углами включения. Основным отличием подобных систем с полупроводниковыми приборами заключается
втом, что мощность, идущая на их выключение, мала по сравнению с однооперационными тиристорами, что позволяет без погрешности рассматривать их как системы с мгновенно действующими ключами. При этих ус-
ловиях проведем в данной статье исследование режимов цепей постоянного и переменного тока m-фазного преобразователя с шунтирующей цепью на вентилях, которые могут выключаться тем или иным способом.
При анализе принимаются следующие допущения: - питание системы осуществляется от сети бесконечной мощности, то есть ее активное и индуктивное сопротивления равны нулю; - включение и выключение вентилей происходит мгновенно и без затрат дополнительной энергии; - падение напряжения на вентилях
438

|
|
|
|
|
|
|
|
|
|
|
|
|
|
|
Современные техника и технологии 2007 |
|||||||||||||||||||||||||
преобразователя |
являются |
постоянными |
и |
|
|
E + EВ ; |
|
|
|
|
|
|
|
|
|
|
|
|
|
|
|
|
|
|
|
|
|
|||||||||||||
равны друг другу; |
- |
нагрузка состоит из неиз- |
е = |
|
|
|
|
|
|
|
|
|
|
|
|
|
|
|
|
|
|
|
|
|
|
|
|
|
||||||||||||
менной по величине индуктивности, омического |
|
|
UМ |
|
|
|
|
|
|
|
|
|
|
|
|
|
|
|
|
|
|
|
|
|
|
|
|
|||||||||||||
и относительный ток |
|
|
|
|
|
|||||||||||||||||||||||||||||||||||
сопротивления и ЭДС постоянного тока. |
|
|
|
|
|
|
|
|||||||||||||||||||||||||||||||||
|
|
й= i |
= i ЧR , |
|
|
|
|
|
|
|
|
|
|
|
|
|
|
|
|
|
|
|||||||||||||||||||
При сделанных допущениях эквивалентная |
|
|
|
|
|
|
|
|
|
|
|
|
|
|
|
|
|
|
||||||||||||||||||||||
схема замещения в однофазном исполнении |
|
|
IМ |
UМ |
|
|
|
|
|
|
|
|
|
|
|
|
|
|
|
|
|
|
|
|
|
|||||||||||||||
будет иметь вид, изображенный на рис.1. На |
где Е – ЭДС цепи постоянного тока; ЕВ – |
|||||||||||||||||||||||||||||||||||||||
этой схеме управляемый вентиль представля- |
падение |
напряжения |
|
|
|
на |
|
соответствующем |
||||||||||||||||||||||||||||||||
ется автоматическим выключателем К, который |
вентиле; UМ – амплитуда синусоидального |
|||||||||||||||||||||||||||||||||||||||
в соответствующие моменты времени периоди- |
напряжения сети; i - мгновенное значение то- |
|||||||||||||||||||||||||||||||||||||||
чески |
мгновенно |
|
производит |
необходимую |
ка; R |
- активное сопротивление цепи нагруз- |
||||||||||||||||||||||||||||||||||
коммутацию в главной и шунтирующей цепях. |
ки. |
|
|
|
|
|
|
|
|
|
|
|
|
|
|
|
|
|
|
|
|
|
|
|
|
|
|
|
||||||||||||
При этих выключениях согласно принятым до- |
Электромагнитную инерцию цепи посто- |
|||||||||||||||||||||||||||||||||||||||
пущениям, ток нагрузки мгновенно переходит с |
янного тока будем учитывать параметрами |
|||||||||||||||||||||||||||||||||||||||
неизменной величиной в силовую или шунти- |
нагрузки |
|
|
|
|
|
|
|
|
|
|
|
|
|
|
|
|
|
|
|
|
|
|
|
|
|
||||||||||||||
рующие цепи, оставаясь неизменным по вели- |
tgи= |
щL = щT . |
|
|
|
|
|
|
|
|
|
|
|
|
|
|||||||||||||||||||||||||
чине и напряжению в нагрузке. Падение напря- |
|
|
|
|
|
|
|
|
|
|
|
|
|
|||||||||||||||||||||||||||
жения на вентилях учитывается ЭДС ЕВ |
без |
|
|
|
R |
|
|
|
|
|
|
|
|
|
|
|
|
|
|
|
|
|
|
|
|
|
|
|
|
|||||||||||
Разделив оба уравнения (1) на UМ и заме- |
||||||||||||||||||||||||||||||||||||||||
внутреннего сопротивления, включенной про- |
||||||||||||||||||||||||||||||||||||||||
нив время угловой координатой ν=ω t, полу- |
||||||||||||||||||||||||||||||||||||||||
тив тока. |
|
|
|
|
|
|
|
|
|
|
чим выражение в относительных единицах |
|||||||||||||||||||||||||||||
|
|
|
|
|
|
|
|
|
|
|
|
|||||||||||||||||||||||||||||
|
|
|
|
|
e = Um sin ωt |
|
|
|
|
|
ι |
и |
= cosθsin |
( |
ν |
в |
|
|
−θ+ ν |
) |
−ε + |
|
|
|
|
|||||||||||||||
|
|
|
|
|
|
|
|
|
iи |
|
|
|
|
|
|
|
|
|
|
|
|
|
|
|
|
|
|
|
|
|
|
|
|
(2) |
||||||
|
|
|
|
|
|
|
|
|
|
|
|
|
|
|
|
|
|
|
|
|
|
|
|
|
|
|
|
|
|
|
|
|
|
−νtgθ |
|
|||||
|
|
|
|
|
|
|
|
|
|
|
+ ε −cos |
θsin |
( |
ν |
|
|
|
−θ |
) |
+ ι |
|
e |
|
|
||||||||||||||||
|
|
|
|
|
|
|
|
|
|
|
|
в |
|
|
|
; |
|
|
||||||||||||||||||||||
В |
|
|
|
|
|
|
|
|
|
|
|
|
|
|
|
|
|
|
|
|
|
|
|
|
|
|
ои |
|
|
|
|
|||||||||
|
|
|
|
|
|
|
|
|
|
|
ι |
|
= (ε+ ι |
|
|
)е−νtgθ |
|
−ε. |
|
|
|
|
|
|
|
|
|
|
|
|
||||||||||
|
|
|
|
|
|
|
|
|
|
|
|
п |
оп |
|
|
|
|
|
|
|
|
|
|
|
|
|
||||||||||||||
|
Ев |
|
L |
|
|
R |
|
|
Е |
|
|
|
|
|
|
|
|
|
|
|
|
|
|
|
|
|
|
|
|
|
|
|
|
|
|
|
|
|
||
|
|
|
|
|
|
|
Решение |
|
дифференциальных |
уравнений |
||||||||||||||||||||||||||||||
К |
|
|
|
|
|
|
|
|
|
id |
|
|||||||||||||||||||||||||||||
|
|
|
|
|
|
|
|
|
|
|
(2) даст следующие выражения для тока на- |
|||||||||||||||||||||||||||||
|
|
|
|
|
|
|
|
|
|
|
|
|||||||||||||||||||||||||||||
|
|
|
|
|
|
|
ud |
|
|
|
|
грузки в момент включения и паузы в относи- |
||||||||||||||||||||||||||||
|
|
|
Вш |
|
|
|
|
|
iп |
|
|
тельных единицах |
|
|
|
|
|
|
|
|
|
|
|
|
|
|||||||||||||||
|
|
|
|
|
|
|
|
|
|
ι |
|
= cosθsin |
( |
ν |
|
|
|
|
−θ+ ν |
) |
|
−ε + |
|
|
|
|||||||||||||||
|
|
|
|
|
|
|
|
|
|
|
|
|
|
|
|
|
|
|
|
|||||||||||||||||||||
Рис.1. Эквивалентная схема замещения |
|
и |
|
|
|
|
|
|
|
в |
|
|
−θ |
|
|
|
|
|
|
|
|
(3) |
||||||||||||||||||
+ ε −cos |
θsin |
( |
ν |
в |
) |
+ ι |
e−νtgθ; |
|||||||||||||||||||||||||||||||||
|
|
|
|
|
|
|
|
|
|
|
|
|
|
|
|
|
|
|
|
|
|
|
|
|
|
|
|
|
ои |
|
|
|
|
|
||||||
|
|
|
|
|
|
|
|
|
|
|
|
ι |
|
= (ε+ ι |
|
|
)е−νtgθ |
−ε, |
|
|
|
|
|
|
|
|
|
|
||||||||||||
В соответствии со схемой замещения |
п |
оп |
|
|
|
|
|
|
|
|
|
|
||||||||||||||||||||||||||||
|
|
|
|
|
|
|
|
|
|
|
|
|
|
|
|
|
|
|
|
|
|
|
|
|
|
|
|
|||||||||||||
время, в течение которого ключ К замыкает |
где ιои и ιоп – начальные значения токов в |
|||||||||||||||||||||||||||||||||||||||
главную цепь, будем называть временем |
моментвключенияипаузысоответственно. |
|||||||||||||||||||||||||||||||||||||||
включения, а время, в течение которого ключ |
Определим действующее ιд и среднее ιср |
|||||||||||||||||||||||||||||||||||||||
замыкает шунтирующую цепь – временем |
значения токов в элементах схемы |
|
||||||||||||||||||||||||||||||||||||||
паузы. |
|
|
|
|
|
|
|
|
|
|
|
|
|
|
|
λ |
|
|
|
|
|
|
|
|
|
|
|
|
λп |
|
|
|
|
|
|
|
|
|
||
Аналитические процессы в схеме на рис.1 |
ιср = 2mπ |
∫ιи (ν)dν + ∫ιп |
|
(ν)dν |
; |
(4) |
||||||||||||||||||||||||||||||||||
описываются |
системой |
дифференциальных |
|
|
|
|
0 |
|
|
|
|
|
|
|
|
|
|
|
|
0 |
|
|
|
|
|
|
|
|
|
|||||||||||
|
|
|
|
|
|
|
|
|
|
|
|
|
|
|
|
|
|
|
|
|
|
|
|
|
|
|
|
|||||||||||||
уравнений при включенном состоянии и паузе |
|
|
|
2mπ |
|
λ |
|
|
|
|
|
|
|
|
|
|
|
λп |
|
|
|
|
|
|
2 |
|
||||||||||||||
соответственно |
|
|
|
|
|
|
|
|
|
ιд |
= |
|
∫ιи2 |
(ν)dν + ∫ιп2 (ν)dν |
|
. |
(5) |
|||||||||||||||||||||||
|
|
|
|
|
|
|
|
|
|
|
|
|
|
|
|
|
0 |
|
|
|
|
|
|
|
|
|
|
|
|
0 |
|
|
|
|
|
|
|
|
|
|
UM ×sin (νв + ωt) |
= E + EВ |
+ i × R + L |
di |
|
|
|
|
|
|
|
|
|
|
|
|
|
|
|
|
|
|
|
|
|
|
|
|
|
|
|
|
|
|
|
||||||
dt |
; |
(1) |
где λ - |
|
продолжительность включенного |
|||||||||||||||||||||||||||||||||||
|
|
|
|
di |
|
|
|
|
состояния вентилей; m – число фаз преобра- |
|||||||||||||||||||||||||||||||
0 = E + Eв + i × R + L |
, |
|
|
|
|
|
|
|||||||||||||||||||||||||||||||||
dt |
|
|
|
|
|
|
зователя. |
|
|
|
|
|
|
|
|
|
|
|
|
|
|
|
|
|
|
|
|
|
|
|
|
|||||||||
|
|
|
|
|
|
|
|
|
|
|
Нужно иметь в виду, что в зависимости от ха- |
|||||||||||||||||||||||||||||
где t – время, отсчитываемое от момента |
||||||||||||||||||||||||||||||||||||||||
замыкания той или иной цепи. |
|
|
|
|
рактератока нагрузкиввыражении(4)-(5) следует |
|||||||||||||||||||||||||||||||||||
Для упрощения выводов и удобств в ис- |
подставлять соответствующие подинтегральные |
|||||||||||||||||||||||||||||||||||||||
пользовании полученных результатов примем |
функции и пределы интегрирования. Интегралы в |
|||||||||||||||||||||||||||||||||||||||
при исследовании метод относительных еди- |
квадратных скобках зависимостей (4) и (5) пред- |
|||||||||||||||||||||||||||||||||||||||
ниц, развитый применительно к вентильным |
ставляют собой средние и квадратичные площа- |
|||||||||||||||||||||||||||||||||||||||
системам А.А. Булгаковым [1]. В качестве ба- |
ди импульсов токов через соответствующие вен- |
|||||||||||||||||||||||||||||||||||||||
зовых величин примем амплитуды синусои- |
тили системы, откуда могут быть найдены непо- |
|||||||||||||||||||||||||||||||||||||||
дального напряжения сети UM и ток короткого |
средственнотоки. |
|
|
|
|
|
|
|
|
|
|
|
|
|
|
|
|
|||||||||||||||||||||||
замыкания, определяемый амплитудой на- |
При исследовании выпрямительных схем |
|||||||||||||||||||||||||||||||||||||||
пряжения сети и активным сопротивлением |
оказывается необходимым знать спектраль- |
|||||||||||||||||||||||||||||||||||||||
цепи постоянного тока Iкз=IM=UM/R. |
|
|
|
ный состав импульсов токов, проходящего |
||||||||||||||||||||||||||||||||||||
Обозначим через относительное напря- |
через силовые вентили преобразователей. |
|||||||||||||||||||||||||||||||||||||||
жение |
|
|
|
|
|
|
|
|
|
|
|
Выражение |
|
для |
|
|
|
тока |
|
силовых вентилей (2) |
||||||||||||||||||||
|
|
|
|
|
|
|
|
|
|
|
|
|
|
|
|
|
|
|
|
|
|
|
|
|
|
|
|
|
|
|
|
|
|
|
|
|
|
|
439 |

XIII Международная научно-практическая конференция «СОВРЕМЕННЫЕ ТЕХНИКА И ТЕХНОЛОГИИ»
можно представить в идее следующего ряда Фурье [2]:
∞ |
|
|
ιи = ιср.и + ∑ιки sin (кν + ψк )= |
, |
(6) |
к=1 |
∞∞
=ιср.и + ∑ак sin кν + ∑bк cosкν
к=1 к=1
где ιср.и – среднее значение тока силовых вентилейсистемызапериодпитающегонапряжения;
ιки = ак2 + bк2 - амплитуда к-ой гармоник импульса
тока; ψк=arctg(bк/ак) – фаза к-ой гармоники относительно напряжения сети переменного тока найденногокак
ϕк=-arctg(bк/ак)+νв. (7)
Коэффициенты ряда Фурье ак и bк находятся с помощью интегралов
ак |
= |
1 |
∫λ |
ιи (ν)sin кνdν ; |
(8) |
||||
π |
|||||||||
|
|
|
0 |
|
|
|
|
||
|
|
|
|
|
|
|
|
||
b |
|
= |
1 |
λ |
ι |
и ( |
ν cos кνdν . |
(9) |
|
к |
|
∫ |
|||||||
|
|
π |
|
) |
|
||||
|
|
|
0 |
|
|
|
|
||
|
|
|
|
|
|
|
|
С помощью выражений (4)-(9) после интегрирования и преобразований можно получить для любого из рассматриваемых режимов работы преобразователя величины соответствующих токов в относительных единицах, которые протекают в различных элементах системы, а также их гармонический состав. Расчетные формулы будут представлять собой функции искомых величин от углов включения и продолжительности включения, в которых характеристики нагрузки (tgθ и ε) можно считать параметрами. Итогом таких вычислений будет выбор элементов преобразователя и расчет его характеристик. Здесь следует заметить, что возможность полного управления вентилями преобразователя (типа IGBT, GTO, IGCT и др.), независимо от способа управления, дает некоторую область углов включения и продолжительность включений, обеспечивающих для данных параметров нагрузки постоянство величины среднего тока. То есть можно, придерживаясь определенного закона управления вентилями, получать наиболее желаемые в каждом конкретном случае энергетические показатели установки.
Исходя из вышеизложенного, можно установить следующий порядок расчета статических параметров режимов рассматриваемых преобразователей на полностью управляемых элементах:
1.Определяется параметр нагрузки tgθ и задается определенный закон изменения углов включения, обеспечивающий требуемые энергетические показатели системы.
2.Задается величина ЭДС в цепи постоянного тока преобразователя, то есть вели-
чина ε.
3. Для данных tgθ и ε, учитывая закон
управления углами включения, находятся границы различных токовых режимов преобразователя.
4. Для ряда углов продолжительности включения силовых вентилей, начиная с нулевого значения, находятся нужные токи и их спектральный состав. При этом для каждой продолжительности включения следует проверять режим работы преобразователя с тем, чтобы в дальнейшем оперировать соответствующими выражениями. В результате такого расчета получаются статические характеристики данного преобразователя с нагрузкой, имеющей определенный tgθ и ЭДС постоянного тока ε.
5. Изменяется величина ЭДС постоянного тока ε и расчет повторяется, начиная с п.3.
По рекомендуемой методике на ЭВМ были рассчитаны соответствующие универсальные кривые в относительных единицах для ряда фиксированных значений параметров нагрузки (tgθ) в предположении, что закон управления углами включения обеспечивает включение очередных вентилей при минимально возможных углах. С помощью данных кривых и таблиц для конкретного привода с известным характером нагрузки нетрудно найти энергетические показатели системы – КПД и коэффициент мощности, а также оценена величина «генерируемой» реактивной мощности емкостного режима.
Полученные результаты расчётов режимов искусственной коммутации являются исходными для расчета режимов мостового выпрямителя в режиме комбинированной коммутации. В этом случае катодная группа вентилей работает в режиме искусственной коммутации, генерируя реактивную мощность емкостного характера, а анодная группа работает в режиме естественной коммутации. Так как катодная и анодная группы вентилей соединены последовательно, то происходит взаимная компенсация этих реактивных мощностей при соответствующем подборе углов управления в каждой группе ошибка здесь возникает лишь при нагрузке близкой к режиму холостого хода преобразователя из-за соизмеримости энергий, поступающих в нагрузку из сети и системы искусственной коммутации.
ЛИТЕРАТУРА:
1.Булгаков А.А. Новая теория управляемых выпрямителей. – М.: Наука, 1970 – 320 с.
2.Заде Л., Дезоер Ч. Теория линейных систем. Метод пространства состояний. – М.: Наука, 1970 – 703с.
440

Современные техника и технологии 2007
КОМПЛЕКСНАЯ АВТОМАТИЗАЦИЯ ТЕХНОЛОГИЧЕСКОГО ПРОЦЕССА ДОЗИРОВАНИЯ СЫПУЧИХ МАТЕРИАЛОВ
Ляпушкин С.В. , Гусев Н.В.
Томский политехнический университет, Россия, г.Томск, пр.Ленина, 30
E-mail: LSW777@mail.ru
Технологический процесс дозирования сыпучих материалов широко используется в пищевой, строительной и фармацевтической промышленности. Себестоимость продукции зависит от производительности технологического процесса и точности дозирования. Автоматизация процесса дозирования позволяет регулировать производительность и максимально увеличить точность дозирования, что особенно актуально при приготовлении дорогостоящих смесей.
На кафедре «Электропривода и электрооборудования» Томского политехнического университета разрабатывается лабораторный стенд «Система автоматического дозирования сыпучих материалов». На данном лабораторном стенде, студенты специальности «Электропривод и автоматика промышленных установок и технологических комплексов», будут выполнять лабораторные работы на примере реального решения комплексной автоматизации технологического процесса.
Автоматическая система имеет 3 уровня управления. На верхнем уровне управления располагается персональный компьютер с установленной SCADA системой управления технологическим процессом. На среднем уровне находится микроконтроллер фирмы Fastwel RTU188-BS. Данный контроллер имеет 16 дискретных неизолированных входоввыходов, 16 оптоизолированных входов, 8 аналоговых входов с разрешением 12 бит, два последовательных порта: с интерфейса-
ми RS-232 (порт 0) и RS-485 либо RS-232 (порт 1), флэш-память 512 кбайт, ОЗУ 512 кбайт. Тактовая частота процессора 40 МГц. Контроллер является конструктивно законченным устройством и может устанавливаться на DIN-рейку. Также на среднем уровне находится панель релейной коммутации, которая осуществляет сопряжение порта выходных сигналов контроллера и обмоток силовых контакторов. Контроллер и модули релейной коммутации питаются от блоков пита-
ния LOGO POWER фирмы Siemens на 5 В и на 24 В. На нижнем уровне располагается преобразователь частоты, силовые контакторы управления исполнительными двигателями и датчики с соответствующими устройствами преобразования сигналов.
Функциональная схема автоматической системы дозирования сыпучих материалов представлена на рис.1.
Рис.1 Объектом автоматизации является:
1.Шнековый питатель, со встроенным расходным бункером, управляемый от моторредуктора мощностью 0.75 кВт.
2.Бункер дозатора установленный на 3-х тензо-датчиках веса фирмы «Тензо-М».
3.Задвижка дозатора, управляемая от асинхронного двигателя.
Задание на вес определяется студентом в SCADA системе на персональном компьютере. Цифровой сигнал пропорциональный заданному весу поступает в контроллер на вход программно выполненного регулятора веса. Параметры регулятора веса настраиваются по критерию оптимального управления - получения максимальной производительности при заданной точности дозирования. Выход регулятора веса является заданием на частоту преобразователя и соответственно скорости двигателя шнекового питателя. Также при поступлении сигнала с контроллера, коммутируется цепь контактора в силовой цепи шнекового питателя.
Перемещение материала происходит из расходного бункера в бункер дозатора с помощью шнекового питателя. Для лабораторных целей, в качестве дозируемого материала будет использоваться сухой песок, хотя для научных целей могут быть использованы другие материалы разной влажности, плотности и гранулического состава.
441
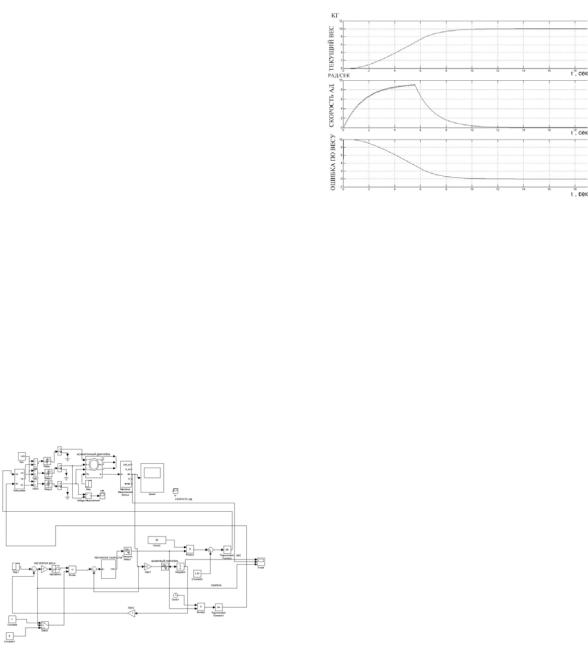
XIII Международная научно-практическая конференция «СОВРЕМЕННЫЕ ТЕХНИКА И ТЕХНОЛОГИИ»
Дозирование материала происходит в бункере дозатора располагаемом на раме. Измерение текущего веса бункера-дозатора осуществляется тремя тензодатчиками типа МК2-1-С3 фирмы «Тензо-М» (г. Москва). Сигналы с тензодатчиков поступают в суммирующий блок, а затем в нормирующий усилитель НУ-420DC, которые находятся в непосредственной близости от датчиков. Здесь сигнал усиливается, гальванически изолируется и нормализуется в стандартный токовый сигнал 4…20 мА. В этом виде информация о весе поступает в контроллер.
Программа регулятора веса написана таким образом , чтобы при приближении текущего веса к заданному частота на выходе преобразователя изменяется плавно от 50 Гц до 3.5 Гц. При приближении частоты к нижней границе, асинхронный двигатель отключается с помощью панели релейной коммутации по сигналу с контроллера.
Один из критериев оптимальности данной системы является точность дозирования. Масса дозируемого материала будет больше на величину массы «падающего столба» даже при остановки асинхронного двигателя. Поэтому нужно конечный этап дозирования делать на пониженной скорости, т.к. масса «падающего столба» прямопропорциональна скорости двигателя и уровню заполнения бункера дозатора.
Программное обеспечение на верхнем уровне разработано в среде Delphi 7 и работает под управлением операционной среды Windows XP. На среднем уровне программное обеспечение реализовано на языке программирования C++ версии 3.11. В качестве операционной системы используется предустановленная дисковая операционная система
FDOS фирмы Fastwel.
Практические исследования можно подтвердить на математической модели в среде моделирования Matlab-7. Имитационная модель данной системы изображена на рис.2.
Рис.2
Регулятор веса представлен пропорциональным звеном, регулятор скорости пропор- ционально-интегральный. Шнековый питатель состоит из пропорционального звена, рассчитанного исходя из геометрических параметров шнека и заданной производительности, и интегрирующего звена имитирующего накопления массы в бункере дозатора. Также в модели шнекового питателя учитывается транспортная задержка.
В модели используется скалярное управление асинхронным двигателем, также как в лабораторном стенде.
Результаты моделирования представлены на рис.3.
Рис.3 Как видно из графиков остановка шнеко-
вого питателя происходит при пониженной скорости, что обеспечивает достаточную точность дозирования.
Лабораторная установка позволит обеспечить цикл лабораторных работ по курсу комплексная автоматизация технологических процессов:
1.Исследование системы автоматического дозирования сыпучих материалов.
2.Изучение SCADA систем для визуализации и контроля технологического процесса.
3.Изучение технических средств автоматизации.
ЛИТЕРАТУРА:
1.В. Букреев, Н.Гусев, М.Нечаев, И.Краснов, Р.Гурьев, С.Кремис
АСУ ТП производства комбикормов на ба-
зе контроллера Fastwel RTU188-BS//СТА №1 ,2006 –с. 74-79.
2.Герман-Галкин С.Г. Компьютерное моделирование полупроводниковых систем в MATLAB 6.0: Учебное пособие. - СПб.: КО-
РОНА принт, 2001.-320 с.
3.Шрейнер Р.Т. Математическое моделирование электроприводов переменного тока с полупроводниковыми преобразователями частоты. Екатеринбург.
УРО РАН, 2000. 654 с.
442

Современные техника и технологии 2007
БЕССЕНСОРНЫЕ ИМПУЛЬСНО-ФАЗОВЫЕ ЭЛЕКТРОПРИВОДЫ С ЦИФРОВЫМ УПРАВЛЕНИЕМ
Николаев И.Б., Фалеев М. В., Самок С.Г. Ивановский государственный энергетический университет,
Россия г. Иваново, ул. Рабфаковская, 34 E-mail. epbfm8@yandex.ru
Развитие технологий машинного производства и появление новых высоких и наукоемких технологий связано с повышением точностных параметров технологических процессов. Это обеспечение прецизионности размерной обработки, повышение точности подачи материалов, стабилизации температуры, давления и ряда других параметров. Характерными примерами критических технологий являются мехатроника и нанотехнология.
В машиностроении регулируемость технологических процессов, обеспечение высокой точности и адаптация к изменяющимся условиям эксплуатации реализуется посредством автоматизированного электропривода. Для современного технологического оборудования характерно широкое использование высокоточных электроприводов, характеристики которых во многом определяют технические возможности станков, прокатных станов, прессов, сборочных агрегатов, робототехнических комплексов, медицинского оборудования, следящих систем и многих других машин производственного и специального назначения.
И если ранее считалось, что регулируемый привод является энергетической и кибернетической (в смысле управления) основой машиностроения, то в последние годы основное внимание уделяется интеллектуальным системам с высоким качеством регулирования выходных параметров – прецизионным электроприводам.
Наблюдающийся в последнее десятилетие рост предложения высокопроизводительных вычислительных средств привел к широкому использованию в качестве базовых аппаратных средств управления прецизионными электроприводами специализированных DSP-микроконтроллеров семейства "Motor Control", выпускаемых фирмами "Analog Devices", "Texas Instruments", "Microchip" и рядом других. Правда, назвать такие БИС микроконтроллерами можно с большой натяжкой из-за специфики встроенного набора периферийных устройств. Более строгим для таких устройств является появившейся в литературе термин "Система на Кристалле" (СНК). Применение СНК упрощает процесс создания электроприводов и дает отличные результаты
особенно для электроприводов общепромышленных механизмов. В какой-то степени это соответствует пожеланиям части разработчиков средств автоматизации, поскольку снимает с них проблемы создания аппаратных средств системы управления и сводит поставленную задачу к разработке соответствующих программных средств.
Однако жесткая конфигурация аппаратных средств часто приводит к неоправданному усложнению программного обеспечения и росту требований к возможностям процессорного ядра и ограничениям в выборе возможных принципов управления. При использовании СНК разработчик volens-nolens вынужден ограничиться лишь набором периферии, предусмотренном производителем БИС. А поскольку последние ориентируются на потребности рынка, то при разработке СНК используются методы и средства, которые находят наиболее широкое применение в этой области. Во многом это сдерживает инициативу создателей прецизионных электроприводов, укладывая их разработки в прокрустово ложе известных технических решений. Поэтому в ряде случаев является рациональным применение цифровых систем, не ограничивающих разработчика выбором технических средств управления из прекрасного, но строго определенного набора периферийных устройств.
В рамках синергетической теории управления проблема увеличения точностных показателей работы электропривода решается за счет расширения фазового пространства системы и непосредственного измерения всех ее компонент. Поэтому общепринятым является использование многоконтурных и модальных систем управления на базе аппаратных средств определения внутренних составляющих фазового пространства, таких как токи и напряжения на статорных обмотках двигателей переменного тока. Такой способ построения оправдывает себя в "бессенсорных" электроприводах, основной чертой которых является отсутствие средств непосредственного измерения параметров движения. Однако существует пока еще относительно небольшой, но все более расширяющийся класс устройств, к которым предъявляются жесткие требования в отношении по-
443
XIII Международная научно-практическая конференция «СОВРЕМЕННЫЕ ТЕХНИКА И ТЕХНОЛОГИИ»
грешности воспроизведения траектории движения механизмов технологических агрегатов и многократной повторяемости параметров движения с широкими пределами регулирования управляемых переменных.
В этом сегменте непосредственное определение параметров движения (положения, скорости и ускорения) является неотъемлемой чертой электропривода, а измерение внутренних переменных состояния системы не представляется условием, необходимым для обеспечения работоспособности системы, которое для своей реализации требует применения дополнительных аппаратных и программных средств. Для восстановления этих переменных посредством наблюдающих устройств вполне достаточно информации о параметрах движения, получаемых с импульсных датчиков положения механизма (ДПМ). Такой подход позволяет полностью отказаться от использования дополнительных измерителей и аналого-цифровых преобразователей, что положительно сказывается на стабильности характеристик и надежности электропривода.
Другим фактором, повышающим эксплуатационные характеристики электропривода, является использование принципа фазовой синхронизации, обеспечивающего высокую достоверность воспроизведения параметров за счет организации управления не по скорости механизма, а по его положению относительно заданного значения. Использование этого принципа позволяет создавать эффективные системы для управления электроприводами с двигателями постоянного и переменного тока Необходимость обеспечения высокого качества управления параметрами движения и робастности системы управления требует применения нелинейных и адаптивных регуляторов. Одним из способов решения этой задачи является использование нечетких регуляторов (НР). Применение таких регуляторов для управления нестационарными и нелинейными объектами показывает их высокую эффективность и в ряде случаев существенные преимущества перед линейными цифровыми регуляторами. Такие бессенсорные импульсно-фазовые электроприводы (БИФП) могут использоваться в технологических установках требующих: стабилизации скорости или текущего положения вала, позиционирования, позиционно-силового управления и синхронно-синфазного движения механизмов многодвигательных агрегатов.
Однако применение этого принципа требует выполнения ряда операций управления над импульсными последовательностями, реализация которых средствами СНК приво-
дит к использованию достаточно искусственных технических приемов, далеко не всегда положительно сказывающих на характеристиках разработанных устройств. Это является мощным сдерживающим фактором широкого распространения импульсно-фазовых прецизионных электроприводов.
Мощным толчком по расширению сферы применения таких электроприводов явилось появление конфигурируемых систем на кристалле (КСНК). Размещение на одном кристалле процессорного ядра и конфигурируемой логической матрицы (CSL) позволяет существенно уменьшить габариты устройства, а главное повысить его помехозащищенность и надежность. Кроме того, важным преимуществом КСНК является высокая гибкость формирования набора внешних устройств с различными алгоритмами работы. Такие системы имеют один существенный недостаток с точки зрения традиционного подхода к проектированию замкнутых электроприводов – отсутствие встроенных аналого-цифровых преобразователей. Однако при принятой концепции построения БИФП их применение не является необходимым.
Разработанный на базе вышеизложенных принципов построения бессенсорный им- пульсно-фазовый электропривод базируется на КСНК выпускаемой фирмой "Triscend" ("Zilogic Semiconductor"). Регулятор выполнен на базе быстродействующего (10 MIPS) ядра TURBO52, связанного многоразрядной шиной CSI с программируемой логической матрицей, обеспечивающей взаимодействие с узлами технологического агрегата. При этом функции CSL не ограничиваются только этими задачами. Её наличие позволяет существенно повысить быстродействие системы за счет выполнения ряда вычислительных операций аппаратными средствами. Так средствами программируемой логики реализуются функции цифрового сигнального процессора. Решение этой задачи при использовании встроенного в кристалл блока прямого доступа к памяти (DMA) позволяет существенно ускорить выполнение функций управления электроприводом, связанных с реализацией цифровых рекурсивных фильтров достаточно большой размерности. Для электроприводов переменного тока характерно использование преобразования Парка-Кларка, обеспечивающего взаимодействие систем координат двигателя и регулятора. Чисто программная его реализация требует выполнения достаточно трудоемких вычислительных операций и связано с относительно большими затратами времени. При использовании КСНК выполнение этих преобразований может быть выполнено аппаратными средствами. Все это
444
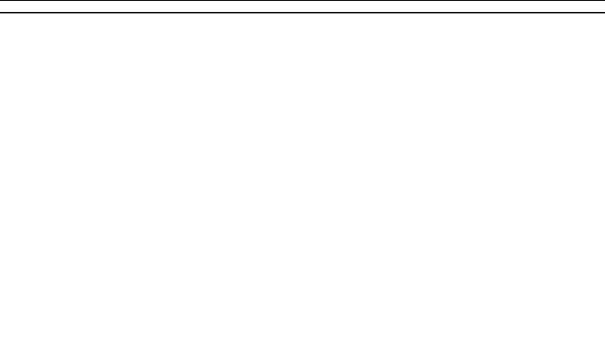
Современные техника и технологии 2007
позволяет создавать интеллектуальные пре- |
Специфика используемого ДПМ во многом |
|||||
цизионные системы электропривода даже на |
определяет |
конфигурацию |
аппаратных |
|||
базе относительно недорогих 8-разрядных |
средств системы управления. |
|
||||
микроконтроллеров, что существенно снижа- |
Испытания |
электропривода |
показывают, |
|||
ет стоимость |
разрабатываемых |
систем |
что предельный диапазон регулирования ско- |
|||
управления, разработанные контроллеры яв- |
рости в зависимости от разрешающей спо- |
|||||
ляются многофункциональными и могут ис- |
собности датчика положения |
составляет |
||||
пользоваться практически с любыми типами |
(10000-50000):1 при погрешности отработки |
|||||
двигателей |
|
|
|
траектории ±1.5 дискреты. БИФП находят |
||
Предложенная концепция положена в ос- |
свое применение в испытательной технике, |
|||||
нову ряда прецизионных электроприводов. В |
станкостроении, робототехнике. Высокие тех- |
|||||
таких электроприводах в |
качестве |
датчика |
нические характеристики таких электропри- |
|||
положения механизма могут использоваться |
водов позволяют использовать их в стацио- |
|||||
фотоимпульсные |
или электромашинные (си- |
нарных и подвижных системах стабилизации |
||||
нусно-косинусные вращающиеся трансфор- |
и наведения. |
|
|
|||
маторы) измерительные |
преобразователи. |
|
|
|
ЭЛЕКТРОПРИВОД СКАНИРОВАНИЯ УРОВНЯ ВЕЩЕСТВА В ОБЪЕКТЕ
Новиков Е.Н., Полунин Д.В., Горбачёв С.А.
Томский политехнический университет, Россия, г. Томск, пр. Ленина, 30 E-mail: siberia99@mail.ru
Электропривод широко используется во всех отраслях народного хозяйства, не исключая и химическую промышленность. Это один из самых энергоемких потребителей и преобразователей энергии.
Теория регулируемого электропривода, насчитывает уже не один десяток лет, постоянно совершенствуется вместе с совершенствованием конструктивных решений. Особенно интенсивное развитие она получила в последнее время, благодаря усовершенствованию традиционных и созданию новых силовых управляемых полупроводниковых приборов, интегральных схем, развитию цифровых информационных технологий и разработке разнообразных систем микропроцессорного управления.
Вхимической промышленности, больше чем в какой-либо другой, требуется автоматизация производства, так как технологические процессы весьма сложны, отличаются быстротой протекания, высокой чувствительностью к нарушениям установленного режима, вредностью для здоровья людей, взрыво- и пожароопасностью. Во многих производствах используются высокие давления и температуры, создающие дополнительные трудности управления производством и опасность для обслуживающего персонала.
Вданной работе разрабатывается электропривод сканирования уровня вещества в
объекте, который может быть использован в химической промышленности для определения силы ионизирующего излучения.
Разработка производится на базе системы используемой в составе технологического оборудования СХК. На Радиохимическом заводе в составе Сибирского химического комбината используется система сканирования для определения уровня ионизирующего излучения, специализированная для работы в агрессивных средах. Работа системы в целом осуществляется электроприводом с двигателем постоянного тока. Сканирование объекта ведется периодически. Применение данной системы позволяет ограничить доступ рабочего персонала на объект, тем самым оградить людей от влияния опасных для жизни излучений [1].
Данная система состоит из следующих элементов: датчик (зонд), измерительные приборы, электропривод, содержащий двигатель постоянного тока, редуктор и пусковой рубильник. Сканирующий зонд крепится тросом на вал двигателя. Двигатель крепится на верхней части объекта, подлежащего сканированию. Панель системы управления находится на расстоянии, обеспечивающем защиту персонала от воздействий агрессивной среды.
Процесс сканирования заключается в следующем. Сначала включается измери-
445
XIII Международная научно-практическая конференция «СОВРЕМЕННЫЕ ТЕХНИКА И ТЕХНОЛОГИИ»
тельная аппаратура, затем запускается двигатель, одновременно фиксируются показания сканирующего зонда, который начинает опускаться в объекте. После прохождения зондом заранее определённой длины пути, снятие показаний зонда прекращается, и он возвращается в исходное состояние. Но в данной системе существует ряд недостатков. Существенный недостаток – наличие в двигателе щёточно-коллекторного узла и редуктора, который снижает надёжность, увеличивает момент инерции, создаёт радиопомехи, взрывоопасность и т.д. Так же, существует проблема старения троса, вследствие чего происходит искажение сигнала от датчика.
Создаваемые двигателем помехи отрицательно влияют на показания сканирующего зонда, сигнал может исказиться на столько, что будут сделаны неправильные выводы, что может привести к аварии на производстве. Взрывоопасность в химическом производстве абсолютно неприемлема. Снижение надёжности ведёт к частым ремонтным процедурам и техническому обслуживанию.
Необходимость в проведении данного рода работ связана с потребностью внедрения современных и качественно новых методов контроля и диагностики в химическую промышленность.
В результате обобщённого анализа систем сканирования, их достоинств и недостатков, а также с учётом конкретных требований к будущей системе, была синтезирована система сканирования уровня вещества в объекте. Система состоит из следующих элементов:
•барабан;
•синхронный двигатель;
•преобразователь частоты;
•компьютер;
•нагрузочный трос;
•капсула с датчиком;
•полупроводниковый датчик;
•объект;
•направляющая трубка;
•блок оцифровки сигнала;
•информационный кабель
1.Барабан представляет собой полый цилиндр, в котором размещается электродвигатель, преобразователь частоты и блок оцифровки сигнала от вала двигателя, для мониторинга положения вала в любой момент времени.
2.Проектируемый электродвигатель относиться к классу синхронных машин. Предполагается спроектировать его таким образом, чтобы избежать использования в системе редуктора. Для этого были приняты следующие параметры:
•Частота вращения вала двигателя n=2-5 об/мин, с поддержкой постоянного момента на выходном валу М=2 Н·м;
•Число пар полюсов 2р=18;
•Число стержней z=27;
•Диаметр D=105 мм;
•Ток статора I=2А;
•Длина вала двигателя L=100мм.
3.Блок оцифровки сигнала представляет собой устройство, обеспечивающее преобразование дискретных и аналоговых сигналов с датчиков положения на валу двигателя
вцифровые сигналы, передаваемые на компьютер или контроллер. Передача данных осуществляется по интерфейсу RS-485.
4.В качестве преобразователя частоты был использован высокопроизводительный и малошумный инвертор серии 4FVR-E11S-4EN фирмы – производителя Fuji Electric. Он предназначен для преобразования частоты трехфазной синхронной машины и является автономным инвертором напряжения
Работа системы управления осуществляется следующим образом: с блока ЭВМ через блок преобразователя интерфейсов сигнал о включении электропривода поступает на устройство преобразования частоты. После начала работы электропривода, по достижении капсулой критической точки (дна или поверхности объекта), дискретный сигнал с концевых выключателей через устройство ввода дискретных сигналов (УВ дискрет.) системы сканирования, поступает на ПЧ и в определенный момент времени, для обеспечения надежности работы системы осуществляется остановка работы привода. Далее осуществляется реверс двигателя, и движение капсулы начинается в обратном направлении.
В управлении системой используется универсальный логический модуль LOGO!. Данное устройство имеет как аналоговые, так
идискретные входы. Логические модули LOGO! являются компактными функционально законченными универсальными изделиями. Они предназначены для построения простейших устройств автоматики с логической обработкой информации. Алгоритм функционирования модулей задается программой, составленной из набора встроенных функций. Программирование модулей LOGO!Basic может производиться с их клавиатуры без использования дополнительного программного обеспечения.
В качестве датчика в системе сканирования используется сцинтилляционный детектор ионизирующего излучения (ИИ) на основе фотоэлектронного умножителя (ФЭУ) из материала NaJ(Tl).
В основу работы сцинтилляционных детекторов положена способность ряда ве-
446
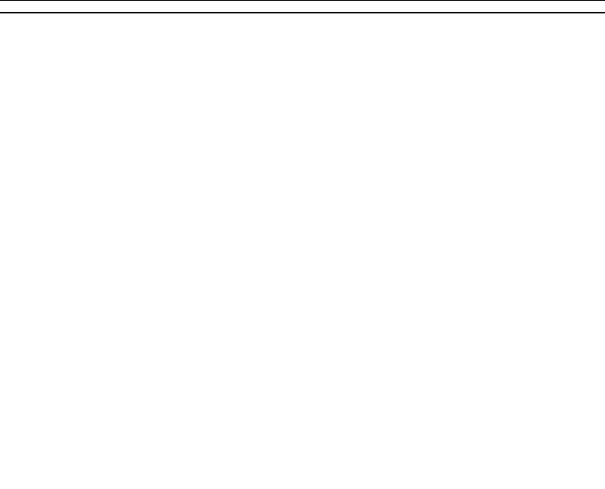
Современные техника и технологии 2007
ществ (сцинтилляторов) испускать видимое (сцинтилляции, вспышки) излучение под воздействием заряженных частиц. Кванты света при этом поглощаются фотокатодом с испусканием электронов (фотоэффект), которые затем с помощью ФЭУ преобразуются в электрический сигнал, по величине которого и скорости счета импульсов судят о мощности дозы или плотности потока ИИ.
Сам сцинтилляционный детектор помещается в светонепроницаемый корпус. В качестве сцинтилляторов используются неорганические и органические кристаллы, пластмассы и жидкости, инертные газы и их смеси.
Проектирование электродвигателя является наиболее важной задачей в этой работе. При проектировании планируется использовать прикладной пакет программ MatLab, в котором уже реализована методика параметрического и энергетического расчета подобных электрических машин.
Применение частотно-регулируемого ЭП обуславливается, прежде всего, высокими показателями надежности, плавным регули-
рованием скорости в широком диапазоне в обе стороны от естественной характеристики. При этом получаемые характеристики обладают высокой жесткостью.
В результате выполнения работы должен быть разработан электропривод сканирования уровня гамма-излучения в объекте, позволяющий отслеживать распределение ионизирующего излучения в агрессивной среде.
ЛИТЕРАТУРА:
[1]Автоматизированные контрольноизмерительные приборы для химических производств: Уч. пос. для техн. спец. вузов./ М.В.Кулаков, С.И.Щепкин. – М.: Машгиз, 1961.-548 с.: ил.
[2]Садовский Л.А. Перспективы применения новых типов двигателей в современных регулируемых и следящих электроприводах //
Приводная техника.-2003.-3.- С.31-39.
[3]Электромашинные устройства автоматики: Учебник для вузов / Ю.А.Сабинин. – Л.: Энергоатомиздат. Ленингр. отд-ние, 1988.-408 с.: ил.
МОДЕЛЬ ВЕНТИЛЬНОГО ДВИГАТЕЛЯ СО СВОЙСТВОМ ЖИВУЧЕСТИ
Образцов К.В.
Томский политехнический университет
E-mail: kobraztsov@mail.ru
В настоящее время всё большую долю рынка завоевывает электропривод переменного тока, а именно асинхронные, синхронные и вентильные электроприводы переменного тока с преобразователем частоты. Вентильным двигателем называется устройство, состоящее из электродвигателя, управляемого преобразователя частоты в функции от положения ротора двигателя.
Данная работа посвящена разработке модели трёхфазного вентильного двигателя, обладающего свойством живучести.
Согласно ГОСТ 27.002-89 под понятием «живучесть» понимается свойство объекта, состоящее в его способности противостоять развитию критических отказов из дефектов и повреждений при установленной системе технического обслуживания и ремонта, или свойство объекта сохранять ограниченную работоспособность при воздействиях, не предусмотренных условиями эксплуатации, или свойство объекта сохранять ограниченную работоспо-
собность при наличии дефектов или повреждений определенного вида, а также при отказе некоторых компонентов.
В практике существует ряд установок, в которых необходимо сохранить живучесть и продолжать движение, несмотря на выход из строя одной из фазных обмоток двигателя или вентилей преобразователя. Например, электропривода, работающие в экстремальных условиях – в космосе, авиации и т.д. Обычно применяют резервирование, Это увеличивает стоимость, уменьшает эффективность и приводит к недоиспользованию ресурсов. Однако существует возможность работы трехфазного электропривода в двухфазном режиме при обрыве одной из фаз двигателя или выхода из строя одного из вентилей ПЧ [1].
Для работы двигателя в аварийном режиме необходимо обеспечить с помощью микропроцессорной системы управления ВД с питанием каждой обмотки фазы отдельно. Это позволяет
447

XIII Международная научно-практическая конференция «СОВРЕМЕННЫЕ ТЕХНИКА И ТЕХНОЛОГИИ»
в случае аварии одной из фаз обеспечить неза- |
оставшихся в работе обмоток двигателя при |
висимое питание двух оставшихся фаз. |
выходе из строя одной из них. Функциональная |
Необходимо разработать систему, которая |
схема такой системы показана на рисунке 1. |
будет изменять угол сдвига фаз питающего тока |
|
|
8 |
|
|
|
|
БД |
|
|
|
11 |
9 |
5 |
2 |
|
ЗЧВ |
МК |
ПЯ1 |
|
|
|
|
|
ДТ1 |
|
|
|
|
1 |
|
|
6 |
3 |
СМ |
10 |
|
ПЯ2 |
α |
ДП |
|
|
|
ДТ2 |
|
|
7
ПЯ3 4 ДТ3
Рисунок 1. Функциональная схема привода с микроконтроллерным управлением
Обозначения блоков на рисунке 1: |
|
|
|
|
|
|
|
импульсной модуляции и вырабатывает три би- |
|||||||||||||||||||||
1 – синхронная машина; |
|
|
|
|
|
|
|
|
|
|
|
та отказа a, b, c, составляющих слово состояния |
|||||||||||||||||
2, 3, 4 - датчики тока в каждой фазе; |
|
|
|
|
|
|
|
электропривода, поступающее в микроконтрол- |
|||||||||||||||||||||
5, 6, 7 – преобразовательные ячейки инвер- |
|
|
лер 9 (МК). По значениям сигналов с выходов |
||||||||||||||||||||||||||
тора, питающего ВД; |
|
|
|
|
|
|
|
|
|
|
|
датчиков тока 2 (ДТ1), 3 (ДТ2), 4 (ДТ3) в микро- |
|||||||||||||||||
8 - блок диагностики; |
|
|
|
|
|
|
|
|
|
|
|
контроллере 9 (МК) корректируют мгновенные |
|||||||||||||||||
9 – микроконтроллер; |
|
|
|
|
|
|
|
|
|
|
|
значения фазных токов синхронной машины 1 |
|||||||||||||||||
10 – датчик положения ротора; |
|
|
|
|
|
|
|
|
|
|
(СМ) в случае обнаружения отказа в одной из |
||||||||||||||||||
11 – задатчик частоты вращения. |
|
|
|
|
|
|
|
фаз. |
|
|
|
|
|
|
|
|
|
||||||||||||
Блок диагностики 8 (БД) представляет собой |
|
|
|
ВД представляет собой сложное электро- |
|||||||||||||||||||||||||
|
|
механическое устройство, поведение которого |
|||||||||||||||||||||||||||
диагностическое |
|
|
|
устройство, |
определяющее |
|
|
описывается совокупностью |
электромагнитных |
||||||||||||||||||||
отказ или двигателя, или ПЧ. Вариант исполне- |
|
|
и электромеханических процессов. Синхронный |
||||||||||||||||||||||||||
ния блока диагностики 8 (БД) описан в [2]. Вход- |
|
|
двигатель |
|
описывается |
дифференциальными |
|||||||||||||||||||||||
ной величиной электропривода является сигнал |
|
|
уравнениями в той или иной системе координат. |
||||||||||||||||||||||||||
с задатчика частоты вращения 11 (ЗЧВ). Из бло- |
|
|
Наиболее часто для его описания используют |
||||||||||||||||||||||||||
ка датчика положения ротора 10 (ДП) поступает |
|
|
систему координат d, q, связанную с ротором [3]. |
||||||||||||||||||||||||||
в микроконтроллер 9 (МК) сигнал углового по- |
|
|
Это уравнения Парка-Горева. |
|
|
|
|
|
|||||||||||||||||||||
ложения вала синхронной машины 1 (СМ), по |
|
|
|
Однако эти уравнения применимы при ус- |
|||||||||||||||||||||||||
которому микроконтроллер 9 (МК) вырабатыва- |
|
|
ловии полной симметрии фаз питающего на- |
||||||||||||||||||||||||||
ет задания для каждой фазы, поступающие в |
|
|
пряжения, что не выполняется в случае двух- |
||||||||||||||||||||||||||
преобразовательные ячейки 5 (ПЯ1), 6 (ПЯ2), 7 |
|
|
фазного питания. Поэтому для описания про- |
||||||||||||||||||||||||||
(ПЯ3). Блок диагностики 8 (БД) анализирует со- |
|
|
цессов в системе использовались уравнения, |
||||||||||||||||||||||||||
стояние преобразовательных ячеек 5 (ПЯ1), 6 |
|
|
связанные с обмотками статора (систему не- |
||||||||||||||||||||||||||
(ПЯ2), 7 (ПЯ3) на каждом интервале широтно- |
|
|
подвижных координат a, b, c): |
|
|
|
|
|
|||||||||||||||||||||
U a = r ia + |
L |
d |
(2 ia −ib −ic ) |
−ce |
|
dϑ |
sin(α) |
|
|
|
|
|
|
|
|
|
|
|
|
|
|
||||||||
|
|
|
|
dt |
|
dt |
|
|
|
|
|
|
d(2 ic −ia −ib ) |
|
|
|
|
|
|
||||||||||
|
|
|
|
|
|
|
|
|
|
|
|
|
|
|
|
|
|
|
|
|
|
|
|
|
|||||
U b = r ib + |
L |
d(2 ib −ia −ic ) |
−ce |
dϑ |
|
sin(α + |
2π |
) U c = r ic + |
L |
−ce |
dϑ |
sin(α + |
4π |
) |
|||||||||||||||
|
|
|
|
dt |
|
dt |
3 |
|
dt |
|
dt |
3 |
|||||||||||||||||
|
|
dϑ |
|
|
|
|
|
2π |
|
|
|
|
|
|
|
|
|
||||||||||||
3 k Фm |
|
(ia sin(α) +ib sin(α + |
|
|
|
|
|
|
|
|
|
|
|
|
|
|
|||||||||||||
|
|
|
|
|
) + J |
|
d 2ϑ |
= M − M |
Н . |
|
|
|
|
|
|
|
|||||||||||||
|
dt |
|
|
3 |
|
|
|
|
|
|
|
||||||||||||||||||
M = 2 |
|
|
|
|
|
|
|
|
|
|
|
|
|
p |
|
|
|
|
|
|
|
|
|||||||
|
|
|
|
4π |
|
|
|
|
|
|
|
|
|
|
|
dt 2 |
|
|
|
|
|
|
|
|
|
||||
+ic sin(α + |
|
)) |
|
|
|
|
|
|
|
|
|
|
|
|
|
|
|
|
|
|
|
|
|
|
|||||
|
3 |
|
|
|
|
|
|
|
|
|
|
|
|
|
|
|
|
|
|
|
|
|
|
||||||
|
|
|
|
|
|
|
|
|
|
|
|
|
|
|
|
|
|
|
|
|
|
|
|
|
|
|
|
448

Современные техника и технологии 2007
где:
Ua, Ub, Uс - напряжения в обмотках статора; ia, ib, ic - токистатора;
r, - сопротивлениe фазной обмотки статора; L – индуктивность фазной обмотки статора;
Ce – коэффициент пропорциональности между ЭДС и угловой скоростью ротора;
k - коэффициент пропорциональности между моментом и произведением токов статора и потока ротора;
Фm - поток ротора; J - момент инерции;
MН – момент нагрузки.
При разработке модели ВД были приняты |
ных моделирования и данных эксперимента для |
||
следующие допущения: магнитная цепь двига- |
ДСТ– 0.18 [4] получили расхождения не хуже |
||
теля принималась ненасыщенной; потери в ста- |
7%, что говорит о достаточной адекватности |
||
ли и механические потери пренебрежимо малы; |
модели. |
|
|
распределение индукции и МДС синусоидаль- |
|
|
|
ное; высшие гармоники отсутствуют; воздушный |
ЛИТЕРАТУРА: |
|
|
зазор равномерен; механические связи нагрузки |
1. А.с. СССР № 1746482, МКИ3 Н 02 Р |
||
и двигателя абсолютно жёсткие; не учитывалась |
7/42. – Опубл. в Б.И., 1992, № 25. |
||
взаимная индуктивность фаз двигателя. |
2. |
Однокопылов |
Г.И. Датчик состояния |
Впервые разработана модель, которая по- |
преобразовательной ячейки //IV Международ- |
||
зволяет проводить исследования процессов в |
ная научно-техническая конференция «Микро- |
||
ВД в трёхфазном и двухфазном режимах и их |
процессорные, аналоговые и цифровые систе- |
||
сравнительный анализ. |
мы: проектирование и схемотехника, теория и |
||
Для исследования работы трехфазного вен- |
вопросы применения», Новочеркасск: Изд-во |
||
тильного двигателя в двухфазном режиме были |
ЮРГТУ 2004. – 70 с. |
|
|
проведены исследования переходных процес- |
3. Косулин В.Д. и др. Вентильные элек- |
||
сов, при которых двигатель пускается и разго- |
тродвигатели малой мощности для промыш- |
||
няется в трехфазном режиме, а затем происхо- |
ленных роботов. – Л.: Энергоатомиздат, 1988 |
||
дит обрыв одной из фаз. |
4. |
Однокопылов |
Г.И., Однокопылов И.Г. |
Исследования динамических характеристик |
Обеспечение живучести электродвигателей пе- |
||
системы проводились на имитационной модели |
ременного тока: Монография. - Томск: Изд-во |
||
в среде Delphi 6. В результате сравнения дан- |
ТПУ, 2005. – 187 с. |
|
ПРИНЦИП ПОСТРОЕНИЯ ОРАНИЧИТЕЛЯ ГРУЗОПОДЪЕМНОСТИ НА ОСНОВЕ ВИБРОДИАГНОСТИКИ КРАНОВОГО ЭЛЕКТРОПРИВОДА
Однокопылов И.Г. Томский политехнический университет
634050 г. Томск, ул. Усова 7 odivan@yandex.ru
Надёжность и безопасность находящихся |
козловых и мостовых кранов отработали свой |
в эксплуатации электрических грузоподъём- |
нормативный срок службы, а это предусмат- |
ных кранов мостового и козлового типа, осо- |
ривает, в соответствии с действующими ру- |
бенно отработавших нормативный срок служ- |
ководящими документами [1], их реконструк- |
бы, в значительной степени определяются |
цию, согласованную с заводом изготовите- |
уровнем их оснащённости приборами и уст- |
лем, либо ограничение их первоначальной |
ройствами безопасности, важнейшими из ко- |
нормативной грузоподъемности. |
торых являются ограничители грузоподъём- |
Существует в настоящее время множест- |
ности и регистраторы параметров работы |
во методов ограничения грузоподъемности |
крана. В настоящее время около 90% всех |
кранов мостового типа [2]. В выпускаемых |
449
XIII Международная научно-практическая конференция «СОВРЕМЕННЫЕ ТЕХНИКА И ТЕХНОЛОГИИ»
промышленностью ограничителях грузоподъёмности для кранов мостового типа в основном используются методы непосредственного измерения механических напряжений, возникающих от действия перемещаемого груза (прямые методы). Оснащение таким ограничителем требует внесения изменений в металлоконструкцию крана, что повышает стоимость оборудования, а внешние датчики силы существенно уменьшают надежность ограничителя, вследствие их отказов.
В настоящее время для используемых в промышленности нерегулируемых асинхронных крановых электроприводов перспективным является разработка ограничителя грузоподъемности с использованием современных программируемых микроконтроллеров и косвенных методов измерения массы поднимаемого груза на основе информативных параметров асинхронного двигателя. Наиболее удобным информативным параметром асинхронного двигателя зависящим от массы поднимаемого груза является частота вращения вала двигателя [2].
Предложен новый подход определения частоты вращения вала двигателя по спектральному анализу (преобразование Фурье) вибраций станины двигателя. Частотный анализ вибраций двигателя широко используют в области диагностики различных дефектов двигателя (повреждение подшипниковых узлов, дисбаланс, расцентровка валов, резонанс) [3]. С помощью частотного анализа в ограничителе грузоподъемности можно непрерывно определять частоту вращения вала кранового двигателя, используя акселерометр, который крепится или на станине асинхронного двигателя или на опорной плите. Сигнал с выхода акселерометра подвергается спектральному анализу, из которого выявляется пиковое значение амплитуды сигнала, соответствующее частоте вращения вала двигателя.
Установка акселерометра на неподвижную часть электрического крана – на опорную плиту, или на станину двигателя позволяет определить частоту вращения двигателя на неподвижной части кранового двигателя, что облегчает монтаж и повышает надежность ограничителя грузоподъемности в целом.
Для проверки работоспособности предложенного способа был проведен эксперимент с использованием двигателя постоянного тока со встроенным тахогенератором марки PIVT 6-25/3. На корпусе двигателя был закреплен акселерометр (интегральный датчик ускорения) фирмы Analog devices Inc. марки ADXL202. Затем при работе двигателя на максимальной скорости 17 об/с и при скорости 9 об/с был сохранен сигнал, снимаемый с акселерометра, на компьютере. После спектрального анализа в программном пакете WinПОС были получены зависимости значений амплитуд An гармоник колебаний станины двигателя (нормированных в пределах 0..1) от частоты колебаний двигателя f (Гц), которые представлены на рис. 1.а) и рис. 2.а). Из рисунков видно, что частота, которой соответствует пик амплитуды колебаний двигателя An, составляет 17 Гц для рис.1.а) и 9 Гц для рис.2.а), что будет соответствовать частоте вращения вала двигателя n=17 об/с и n=9об/с. Это было подтверждено показаниями встроенного тахогенератора. Зависимости частоты вращения вала двигателя (сигнал тахогенератора) nтг от времени t представлены на рис. 1.б) и рис. 2.б), откуда следует, что nтг=17 об/с и nтг=9 об/с соответственно.
Т.к. данный эксперимент проводился на хорошо сбалансированном двигателе малой мощности с высококачественными подшипниками, то можно считать, что частота вращения вала двигателя, выявленная из сигнала виброграммы соответствует значению показания тахогенератора, поэтому данный метод можно использовать в ограничителе грузоподъемности электрического крана.
а)
б) Рис. 1. Виброграмма сигнала акселерометра Аn (а) и временная диаграмма сигнала тахоге-
нератора nтг (б) при скорости вращения двигателя 17 об/с.
450

Современные техника и технологии 2007
а)
б) Рис. 2. Виброграмма сигнала акселерометра Аn (а) и временная диаграмма сигнала тахоге-
нератора nтг (б) при скорости вращения двигателя 9 об/с.
Кроме того, использование данного метода позволяет вести и диагностику механических узлов кранового электропривода, редуктора, тормозного устройства, двигателя, и т.д. При расширении диапазона спектра виброграммы до десятков кГц [4] можно выявить дефекты подшипникового узла кранового двигателя, которые являются основными при отказе двигателей [3]. В области низких частот виброграммы (единицы Гц) можно выявить дефекты, связанные с началом разрушения металлоконструкции электрического крана. Таким образом, непрерывная вибродиагностика выявления различных дефектов в основных узлах электрического крана позволяет повысить его безопасность.
Выводы. Предложен и экспериментально проверен способ определения скорости вращения двигателя по виброграммам станины двигателя без датчика скорости, позволяющий определить с достаточной точностью частоту вращения вала двигателя и вычислить массу поднимаемого груза. Установка
акселерометра, жестко закрепленного на станине двигателя, повышает надежность ограничителя грузоподъемности и позволяет непрерывно вести диагностику подшипникового узла приводного двигателя и выявить начало разрушения металлоконструкции крана.
ЛИТЕРАТУРА:
1.Правила устройства и безопасной эксплуатации грузоподъемных кранов (ПБ 10- 382-00).- М.: ПИО ОБТ, 2000.- 268 с.
2.Дементьев Ю.Н., Однокопылов Г.И., Однокопылов И.Г., Асинхронный электропривод кранового механизма с микроконтроллерным ограничителем грузоподъемности // Изв. Вузов. Электромеханика, №3, 2006, с.: 49-53.
3.Шевчук В.П. Обеспечение работоспособности электрических машин в горнодобывающей промышленности: Автореф. дис. на соиск. учен. степени канд.техн.наук. Томск, 2005. Томский политех. ун-т.
4.http://www.vibration.ru.
УПРУГИЕЭЛЕМЕНТЫВМИКРОЭЛЕКТРОМЕХАНИЧЕСКИХСИСТЕМАХ
ПутиловаА.И.
Томскийполитехническийуниверситет, Россия, г.Томск, пр. Ленина, 30
E-mail: putilovaai@elti.tpu.ru
В последние годы появился значительный |
системы управления в одном технологиче- |
интерес к емкостным устройствам, методам |
ском процессе [1]. |
их расчета и конструирования. Это вызвано |
В основе всего многообразия емкостных |
стремительным развитием технологий микро- |
устройств лежат 3 основные конструкции: |
электроники, которые позволяют создавать |
микродвигатели с воздушным зазором, мик- |
емкостные двигатели малых размеров и их |
родвигатели с катящимся ротором и микро- |
|
двигатели с подвижными гибкими элемента- |
451

XIII Международная научно-практическая конференция «СОВРЕМЕННЫЕ ТЕХНИКА И ТЕХНОЛОГИИ»
ми. Последние имеют наибольшую перспективу при разработке высокоточных позиционных систем.
Математическое описание емкостных микродвигателей основано на законах электромеханического преобразования энергии, теории упругости и электростатики.
В состав микросистем входят упругие элементы, в которых внешние воздействия различного рода приводят к деформации и изменению их потенциальной энергии. Далее эти изменения в микросистемах могут использоваться различным образом. К настоящему времени имеется несколько основных типов упругих элементов, которые получили широкое практическое применение. Применимость того или иного типа упругих элементов в значительной мере определяется технологией их изготовления и соответствием основным идеям технологии микросистемной техники.
Упругие элементы балочного типа. Уп-
ругие элементы этого типа обычно представляют собой прямоугольную кремниевую балочку, жесткозащемленную с одной стороны
(рис. 1).
Рисунок 1 - Консольно-защемленный упругий элемент балочного типа: 1 — область защемления, 2— упругий элемент
Двухопорные упругие элементы ба-
лочного типа. Балочные элементы могут иметь и две области защемления. Схема нагружения таких элементов приведена на рис. 2.
Рисунок2 - Схеманагруженияупругого элемента с двумяобластямизащемления
Упругие элементы мембранного типа.
Упругие элементы данного типа представляют собой тонкую монокристаллическую пластинку, жесткозащемленную по контуру (рис. 3).
Рисунок 3 - Виды упругих элементов мембранного типа: 1 — кольцо жесткости, 2— мембрана, 3—жесткий центр
Торсионные зеркала. Торсионные зер-
кала представляют собой тонкую кремниевую пластинку, прикрепленную с помощью тонких полосок (торсионов) к рамке-основанию. Вся конструкция — это единый монокристалл кремния (рис. 4).
Рисунок 4 - Схема торсионного зеркала: 1 — рамка-основание, 2— микрозеркало, 3— торсионные подвески, 4— управляющие электроды
Упругие элементы гребенчатого типа.
Эти упругие элементы представляют собой систему двух гребенчатых электродов, отделенных друг от друга небольшим воздушным зазором. Один из электродов неподвижен, а другой может перемещаться, так что расстояние между электродами может изменяться при возникновении электростатического взаимодействия (рис. 5).
Рисунок 5 - Упругий элемент гребенчатого типа: 1 — области закрепления гребенчатых структур, 2— неподвижные электроды, 3— подвижные электроды
При создании микромеханических датчиков давления необходимо обеспечить требуемые значения таких параметров, как верхняя граничная частота fгр и допустимая не-
равномерность амплитудной частотной характеристики ε f для широкополосных датчи-
ков или время установления tуст (ε%) и до-
пустимое значение относительного выброса δ переходной характеристики для импульсных датчиков (датчиков ударных волн). Поэтому необходимо иметь возможность их оценки уже на этапе проектирования.
Оценить эти параметры можно, используя динамические характеристики микромеханической системы. В принципе под динамической характеристикой системы можно понимать любое соотношение, заданное аналитически, графически или в виде таблицы, кото-
452

Современные техника и технологии 2007
рое позволяет рассчитать поведение системы во времени. Наиболее часто в качестве динамической характеристики используются дифференциальные уравнения, записанные в различной форме. Проведем моделирование передаточной характеристики полупроводникового чувствительного элемента датчика давления с учетом упругих свойств материала мембраны и потерь за счет внешних и внутренних факторов. В качестве мембраны рассмотрим прямоугольную жесткозащемленную пластинку. Передаточную характеристику чувствительного элемента найдем в результате решения дифференциального уравнения, описывающего колебания тонкой пластинки
где ρ – плотность материала пластинки; μ
– коэффициент, характеризующий затухание под действием внешних факторов; μ1 – коэффициент внутреннего трения (по гипотезе вязкого трения); q(x, y, t) – интенсивность внешней нагрузки; оператор
Здесь ω0 - собственная частота колебательной системы, 0.5 h - декремент затухания, Q
- добротность, F (x, y) =U0 (x)V0 ( y) . Обобщенная частотная характеристика в
этом случае может быть представлена в виде
АЧХ
ФЧХ
Динамические характеристики рассматриваемой системы будут иметь вид (рис. 6).
Dij – жесткости пластинки при изгибе;
W=W (x, y,t) - прогиб пластинки. [2]
Врезультате решения по методу Бубнова
–Галеркина и с учетом некоторых допущений передаточная функция для тонкой жесткозащемленной пластинки может быть представлена в виде передаточной функции колебательной системы второго порядка. Для таких систем передаточная функция имеет вид
Она зависит от трех параметров: коэффициента усиления k = (m ω02 )−1, постоянной
времени T = ω0−1 и коэффициента демпфиро-
вания (степени успокоения) d = |
0.5 |
h |
= |
0.5 . |
|
ω |
|
|
Q |
|
0 |
|
|
Рисунок 6 – ЛАЧХ и переходные процессы
В результате исследований было выяснено, что на динамические характеристики микроэлектромеханической системы влияют геометрические размеры пластинки и величина добротности.
ЛИТЕРАТУРА:
1.Дятлов В.Л., Коняшкин В.В., Потапов Б.С., Фадеев С.И. Пленочная электромеханика. – Новосибирск: Наука, 1991. – 247 с.
2.Гридчин В.А., Драгунов В.П. Физика микросистем: Учеб. пособие. В 2 ч. Ч. 1. — Новосибирск: Изд-во НГТУ, 2004. — 416 с. — (Серия «Учебники НгТУ»).
453

XIII Международная научно-практическая конференция «СОВРЕМЕННЫЕ ТЕХНИКА И ТЕХНОЛОГИИ»
ВОССТАНОВЛЕНИЕ ИЗНОШЕННЫХ ДЕТАЛЕЙ ЭЛЕКТРИЧЕСКИХ МАШИН КОМПОЗИЦИОННЫМИ ЭЛЕКТРОХИМИЧЕСКИМИ ПОКРЫТИЯМИ ЖЕЛЕЗО-КОРУНД
Рябихин А.С, Суворин А.В., Петухов Р.А.
Политехнический институт ФГОУ ВПО «Сибирский федеральный университет»
E-mail:rom_pet1@mail.ru
Электрохимические железные покрытия имеют недостаточно высокую микротвердость, появление микротрещин при увеличении толщины покрытия и недостаточную устойчивость к трению.
Добавление в электролит порошка корунда (окись алюминия Aℓ2O3) позволяет получать более качественные покрытия. Твердые частицы окисла (микротвердость корунда 2225 ГПа) увеличивает износостойкость электрохимических железных покрытий при работе сопряженных деталей в смазке, при сухом трении и значительно уменьшает задиры трущейся поверхности.
Процесс осуществляется в хлористых, сернокислых, и смешанных электролитах. Наиболее широкое применение получили хлористые электролиты, отличающиеся высокой концентрацией солей, интенсивностью наращивания осадка и возможностью получения покрытий большей толщины.
В состав электролита входит, хлористое железо FeCℓ2 700 г/л, окись алюминия (корунд М5) Aℓ2O3 50-75 г/л, плотность тока 20-25
А/дм2 , температура электролита составляет
40 0С.
Применение композиционных электрохимических покрытий железо-корунд уменьшает количество трещин в покрытии. Положительное действие частиц корунда особенно заметно в условиях образования хрупких покрытий (низкие температуры и высокие плотности тока). Природа этого явления может быть объяснена тем, что реализация внутренних напряжений растяжения, свойственных электролитическому железу, происходит вокруг частиц второй фазы покрытия.
износ мг /ч |
|
|
|
|
10.0 |
|
|
|
|
7.5 |
|
|
|
|
5.0 |
|
|
|
|
2.5 |
|
|
|
2 |
|
|
|
|
|
|
|
|
|
1 |
0 |
25 |
50 |
75 |
100 корунд г/л |
Рисунок 1. Влияние концентрации окиси алюминия на скорость износа покрытия и сопряженного с ним чугуна при работе в мосле, при удельном давлении 1,5 МПа.
1- износ покрытия, 2- износ сопряженного чугуна
Композиционные электрохимические покрытия железо-корунд обладают высокой износостойкостью и в то же время не чувствительны к ударным нагрузкам, т.е. нехрупкие. Получить такое покрытие позволяет сочетание пластической металлической матрицы и твердых частиц оксида. Твердые частицы в условиях всестороннего обжатия также могут проявлять признаки пластичности. С увеличением концентрации частиц в покрытии увеличивается его износостойкость, которая достигает максимума при достаточном количестве частиц для восприятия нагрузки, а объем металлической матрицы (связки) еще настолько велик, что в состоянии удерживать частицы от выкрашивания. С дальнейшим увеличением концентрации частиц в покрытии, а следовательно, с уменьшением объема металлической связки частиц в покрытии становится так много, что они начинают соприкасаться, уменьшая до минимума влияние матрицы на прочность композиции. При чрезмерной концентрации частицы выкрашиваются даже при незначительных нагрузках, так как в композиционные покрытия они химически не связаны с матрицей, а существует только механическая связь. Выкрашиваясь, частицы в большом количестве попадают в зону трения, резко увеличивая износ. При большой концентрации частиц в покрытии прочность материала композиционные покрытия будет недостаточна, поскольку металлическая связка не будет выполнять своих функций.
454

Современные техника и технологии 2007
износ мг /ч |
|
|
|
|
75 |
|
|
|
1 |
50 |
|
|
|
2 |
25 |
|
|
3 |
|
|
5 |
|
4 |
|
|
|
|
|
|
0 |
25 |
50 |
75 |
Р, МПа |
|
Рисунок 2 - Влияние удельного давления на скорость износа композиционных электрохимических покрытий на основе железа и сопряженной сними колодки при работе в мосле.
1- сталь 40Х, 2- чистое электролитическое железо, кривая 3- железо-дисульфид молибдена 6 г/л, 4- железо-карбид титана 50 г/л, 5- железо-корунд 50-75 г/л
Твердые частицы окислов увеличивают износостойкость электролитических железных покрытий при работе сопряженных деталей в смазке загрязненной абразивными частицами. Покрытия железо - корунд, полученные из электролита с концентрацией добавки 50-100 г/л, при удельном давлении 1,5 МПа, износостойкость больше в 6,5 - 7,5 раза, чем чистое электролитическое железо. Износ чугунной буксы при этом уменьшился с 2,8 до 1,9 мг/ч. На рисунке 1 демонстрирует влияние концентрации окиси алюминия на скорость износа покрытия и сопряженного с ним чугуна. Опыты, проведенные при более высоких удельных давлениях (25; 50; 75 МПа), позволили выяснить, что оптимальной износостойкостью в данных условиях трения обладали покрытия, полученные из электролитов с 50 - 75 г/л Aℓ2O3, у которых при нагрузке 25-50 МПа износостойкость была в 28 - 45 раза выше износостойкости чистого электролитического железа. Износ сопряженной с ними чугунной буксы был несколько меньше или соответствовал износу буксы, сопряженной с чистым железом. Влияние удельного давления на скорость износа композиционных электрохимических покрытий на основе железа представлена на рисунке 2.
Исследование износа покрытий при сухом трении показало большие преимущества композиционных электрохимических покрытий с окисью алюминия перед другими видами покрытий и чистым электролитическим железом рисунке 3. Так, при удельном давлении 8,1 МПа скорость износа чистого электролитического железа составляла 91 мг/ч, осадков железо - карбид бора - 29,4 мг/ч, а осадков железо - окись алюминия (50-75г/л) 5 мг/ч.
Схватывание и катастрофический износ мягких (микротвердость 4,5 ГПа) покрытий железо - карбид титана наступали уже на первых минутах работы при 4,0 МПа (рис.3, кривая 1). Первые признаки схватывания твердого электролитического железа (микротвердость 5,8 ГПа), заключающиеся в колебании момента трения, наступали при 5,5 МПа (рис.3, кривая 3). Износ буксы при этом резко возрастал. Возможно, вследствие абразивного воздействия диспергированных частиц чугуна возрастал также износ покрытия. Но имевшийся на поверхности покрытия бурый налет окислов способствовал предотвращению интенсивного схватывания и задира поверхностей.
износ мг /ч |
|
|
|
|
|
100 |
|
2 |
|
|
|
|
|
3 |
|
|
|
75 |
|
|
|
|
|
50 |
1 |
|
|
4 |
|
|
|
|
|
||
|
|
|
|
|
|
25 |
|
|
|
|
|
|
|
|
|
5 |
|
0 |
5 |
10 |
15 |
20 |
Р, МПа |
Рисунок 3. Скорость износа композиционные электрохимические покрытия на основе железа при сухом трении
1- железо-карбид титана 50 г/л, 2- железодисульфид молибдена 6 г/л,
3- чистое электролитическое железо, 4- железо-карбид бора 100 г/л,
5- железо-корунд 50-75 г/л Электролитическое железо и композиционные электрохимические покрытия на основе железа по истечению 20 минут сухом трении с сопряженной чугунной обкладкой, при удельном давлении 15 МПа, на поверхности покрытия появлялись задиры. Что приводило к значительному износу покрытия и сопряженной поверхности. Композиционное покрытие железо-корунд при сухом трении и удельном давлении 25 МПа не образовывало зади-
ров.
Вывод: Исследования износостойкости композиционных электрохимических покрытий на основе железа, полученных из хлористого электролита с добавкой порошка корунда, показали, что при наличии 4-8% (массы) включений износ покрытии снижается более чем в 4-5 раз, а коэффициент трения-с 0.1 до 0.02. Оптимальные по износостойкости и пластичности покрытия, имеющие наибольшую область когерентного рассеяния, содержали 6-1% (масс.) корунда. Такие покрытия рекомендованы для производственного использования в целях восстановления и упрочнения деталей электрических машин. Отмечается
455
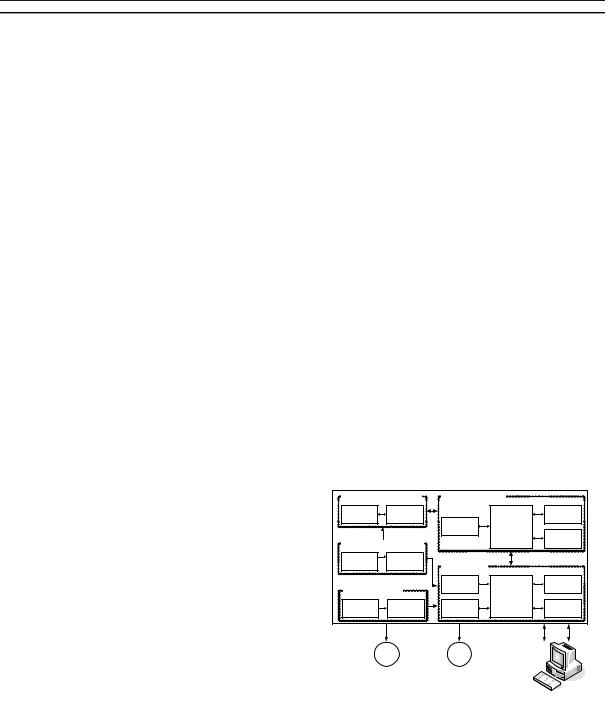
XIII Международная научно-практическая конференция «СОВРЕМЕННЫЕ ТЕХНИКА И ТЕХНОЛОГИИ»
повышенная величина блоков мозаики у ком- |
2. Петров Ю.Н., Восстановление деталей |
позиционных электрохимических покрытий по |
электролитическим железом., 1983, Кишинев, |
сравнению с чистыми покрытиями и большое |
Институт прил. Физики,115с. |
изменение микротвердости. |
3. Вячеславов П.М., Электрическое осаж- |
|
дение сплавов ,1977, Ленинград, Машино- |
ЛИТЕРАТУРА: |
строение, 94с. |
1. Сайфуллин Р.С., Комбинированные |
|
электрохимические покрытия и материалы., |
|
1972, Химик , 193с. |
|
АППАРАТНО-ПРОГРАММНЫЙ КОМПЛЕКС ДЛЯ КОНТРОЛЯ И ДИАГНО-
СТИРОВАНИЯ СКОЛЬЗЯЩЕГО КОНТАКТА ЭЛЕКТРИЧЕСКИХ МАШИН
Саблуков В.Ю., Боровиков Ю.С. Томский политехнический университет
634050, Томск, пр. Ленина, 30 E-mail: vitaly.sablukov@mail.ru
При изготовлении, испытании и эксплуатации коллекторных электрических машин возникает необходимость проводить комплексные исследования поведения коллекторов и колебаний щеток при высоких скоростях вращения, поскольку щеточно-коллекторный узел во многом определяет качество работы и срок службы машины в целом.
Для динамического контроля профиля коллекторов широкое применение получил бесконтактный метод электромагнитного зондирования. Известные приборы, предназначенные для вышеупомянутых измерений, контролируют зазоры между датчиком и контролируемой поверхностью и позволяют измерять общие биения коллектора и амплитуды вибрации элементов щеточного узла. Общим недостатком этих устройств является то, что зазоры между датчиком и пластинами коллектора определяются не только деформацией коллектора, но и его радиальным перемещением и вибрацией в направлении коллектора.
Кроме того, в процессе измерений возникают температурная погрешность, погрешность, обусловленная различием удельных сопротивлений поверхностного слоя коллекторных пластин (в том числе и из-за влияния температуры), погрешность, связанная с неидентичностью установки датчиков в процессе тарирования и в процессе измерения на реальном объекте.
В данной работе рассматривается аппаратнопрограммный комплекс (АПК), который позволяет минимизировать выше названные погрешности, а также выделять из измеренного сигнала паразитные составляющие.
Структурная схема АПК представлена на рисунке 1. Комплекс состоит из следующих основных блоков:
-профилометр;
-системная плата;
-модуль аналогово-цифрового преобразования (АЦП);
-модуль управления электродвигателем (ЭД);
-модуль синхронизации;
-персональный компьютер (ПК).
Как видно из схемы АПК, представляет собой многопроцессорное устройство, построенное по модульному принципу. Системная плата является элементом, координирующим работу всех модулей, входящих в состав комплекса. На системной плате также размещен драйвер шагового двигателя (ШД), который используется для перемещения токовихревого датчика профилометра с точностью 1,25 мкм.
Модуль управления ЭД |
Системная плата |
|
||
Микро |
ПП RS-232 |
|
|
Драйвер |
контроллер |
|
|
ШД |
|
|
Слоты |
Микро |
||
|
|
|
||
|
|
расширения |
контроллер |
|
Модуль синхронизации |
|
|
ПП RS-232 |
|
|
|
|
||
Оптичекие |
Преобразо- |
|
|
|
диоды |
ватель |
Модуль АЦП |
|
|
|
|
АЦП |
|
USB |
Профилометр |
|
контроллер |
||
|
Микро |
|||
|
|
|||
|
|
|
|
|
Токовихре- |
Преобразо- |
|
контроллер |
|
ОЗУ |
|
ПП RS-232 |
||
вой датчик |
ватель |
|
||
|
|
|
||
|
|
|
RS-232 |
USB |
|
ЭД |
ШД |
|
|
Рис. 1. Структурная схема программноаппаратного комплекса
456

Современные техника и технологии 2007
Основным модулем АПК является модуль АЦП. Этот элемент комплекса обладает следующими возможностями:
- прием и передача данных по интерфейсу RS-232 со скорость до 120 Кбит/с и по интерфейсу USB со скоростью до 6 Мбит/с;
ме. Таким образом, оператор задает лишь параметры измерений и получает профилограмму, в которой погрешности минимизированы.
Еще одним немаловажным достоинством АПК является возможность проводить непре-
-оцифровка 14-разрядным АЦП аналорывные измерения. Это позволяет получить
гового сигнала с частотой до 1МГц; |
профилограмму за любое заданное количест- |
|
- |
хранение в памяти до 15000 значений |
во оборотов, причем измерения можно про- |
выборок; |
водить без модуля синхронизации. |
|
- |
определение частоты вращения; |
В качестве примера была снята профило- |
-автоматическая развертка сигнала в грамма коллектора с 22 ламелями за 200
зависимости от количества выборок, частоты вращения коллектора, количества оборотов, которые необходимо оцифровать;
- непрерывная оцифровка сигнала. Среди режимов работы микроконтролле-
ра два режима приема/передачи данных (по интерфейсам USB и RS-232) и два режима оцифровки сигнала. В первом режиме - режиме непрерывной оцифровки сигнала максимальная частота дискретизации составляет около 400 КГц. Во втором режиме, когда данные с АЦП сохраняются в памяти блока цифрового преобразования сигнала, максимальная частота дискретизации составляет 1 МГц, однако в отличии от первого режима, число выборок ограничено 15000. Таким образом, в зависимости от задачи, можно выбирать режим, либо с максимальной частотой дискретизации, либо с неограниченным количеством выборок.
Все модули АПК могут работать, как в составе комплекса, так и автономно. Кроме того, системная плата имеет слоты расширения, что позволяет добавлять новые функциональные модули. Таким образом, при установке нескольких модулей АЦП, АПК становиться многоканальным.
ПК предназначен для управления работой аппаратной части комплекса, приема результатов измерений и их математической обработки. Обмен данными возможен, как по последовательному интерфейсу RS-232, так и по интерфейсу USB. Для этой цели в среде программирования Borland Delphi 7.0 была разработана программа, которая позволяет задавать параметры измерений и сохранять экспериментальные данные.
Несомненным преимуществом разработанного АПК является реализация методики базовой коррекции [1], позволяющей устранить погрешности, обусловленные неодинаковыми удельными электрическими сопротивлениями ламелей и неточностью ориентации датчика относительно измеряемой поверхности. Расчет коэффициентов базовой коррекции, перемещение токовихревого датчика, проведение серий измерений может быть осуществлено в автоматическом режи-
оборотов на скорости вращения 19000 об/мин. На рисунке 2 показана часть этой профилограммы, из которой видно, что радиальные перемещения и вибрации в направлении коллектора оказывают значительное влияние на измеренный профиль, это подтверждается наличием низкочастотных составляющих в спектре (рис. 3).
|
860,0 |
|
мкм |
850,0 |
|
профиля, |
840,0 |
|
измеренного |
830,0 |
|
820,0 |
||
Высота |
810,0 |
|
800,0 |
||
|
||
|
790,0 |
1 |
23 |
45 |
67 |
89 |
Номер ламели
Рис. 2. Профилограмма профиля коллектора
Кроме того, в спектре присутствуют составляющие, связанные с геометрической формой коллектора, которые проявляются на частотах кратных частоте вращения fВР. Это гармоники профиля, определяемые эксцентриситетом коллектора (частота fВР), овальностью (частота 2fВР), трехгранностью (частота 3fВР) и т.д.
|
16 |
|
|
|
|
|
|
|
|
|
|
|
|
14 |
|
|
|
|
|
|
|
|
|
|
|
|
12 |
|
|
|
|
|
|
|
|
|
|
|
мкм |
10 |
|
|
|
|
|
|
|
|
|
|
|
, |
|
|
|
|
|
|
|
|
|
|
|
|
Амплитуда |
8 |
|
|
|
|
|
|
|
|
|
|
|
6 |
|
|
|
|
|
|
|
|
|
|
|
|
|
|
|
|
|
|
|
|
|
|
|
|
|
|
4 |
|
|
|
|
|
|
|
|
|
|
|
|
2 |
|
|
|
|
|
|
|
|
|
|
|
|
0 |
|
|
|
|
|
|
|
|
|
|
|
|
2 |
316 |
631 |
946 |
1260 |
1575 |
1890 |
2205 |
2519 |
2834 |
3149 |
3463 |
|
|
|
|
|
|
Частота, Гц |
|
|
|
|
|
Рис. 3. Спектрограмма профиля коллектора
Основными причинами появления в спектре низкочастотных составляющих являются дефекты подшипникового узла. Численные значения частот этих составляющих зависят от соотношения геометрических размеров подшипника и оборотной частоты вращения ротора механизма.
457
XIII Международная научно-практическая конференция «СОВРЕМЕННЫЕ ТЕХНИКА И ТЕХНОЛОГИИ»
Внагруженном подшипнике можно дифференцировать четыре основные, характерные, применяемые для диагностики частоты - внешней обоймы подшипника, внутренней обоймы, частоты сепаратора и частоты тел качения [2].
Врассматриваемом спектре частота около 100 Гц соответствует частоте сепаратора
fC.
|
1 |
|
|
DТК |
|
|
|
fС = |
fВР 1 |
− |
cos j |
, |
|||
2 |
DC |
||||||
|
|
|
|
|
где DТК - диаметр тела качения; DС - средний диаметр сепаратора; j - угол контакта тела качения с обоймой. Эта составляющая вибрации появляется, если одно из тел качения имеет меньший (больший) диаметр.
Для определения истинных перепадов между пластинами необходимо из измеренного профиля вычесть паразитные составляющие и гармоники связанные с геометрической формой коллектора.
Внастоящее время ведутся испытания 2-
хканального АПК, который позволит на этапе формирования аналогового сигнала профилометра убрать паразитные вибрации. Предметом исследований также является анализ нестационарных сигналов при помощи вейвлет- преобразования.
ЛИТЕРАТУРА:
1.Патент РФ № 2234054. МПК G 01 B 7/14. Способ измерения зазора между измерительным преобразователем и контролируемой поверхностью (варианты) / С.И. Качин, Ю.С. Боровиков, М.А. Нечаев, О.С. Ка-
чин. Заявлено 17.07.2003; Опубл. 10.08.2004, Бюл. № 22. – 11 с.: ил.
2.http://www.vibrocenter.ru/book6.htm.
458

Современные техника и технологии 2007
ДИНАМИЧЕСКИЕ ХАРАКТЕРИСТИКИ ЭЛЕКТРОПРИВОДА ЛАБОРАТОРНОГО СТЕНДА
Е.С. Салтыкова, В.О. Поздеев, К.В. Образцов Томский политехнический университет
E-mail: kobraztsov@mail.ru
Необходимыми для будущего инженера навыками являются навыки по исследованию и настройке электроприводов (ЭП). Для приобретения этих навыков студенты старших курсов специальности «Электропривод» в ряде дисциплин изучают теоретически, а затем и практически реально действующие ЭП на лабораторных стендах. ЭП унифицированные комплектные трёхфазные реверсивные постоянного тока серии ЭПУ1-2-….П предназначены для широкого применения в станкостроении и других отраслях промышленности.
Электропривод представляет собой устройство управления с обратной связью по скорости двигателя и диапазоном регулирования скорости двигателя до 1:10000. Электропривод осуществляет плавное регулирование скорости электродвигателя вниз от номинальной путем изменения напряжения на якоре при постоянном напряжении возбуждения. При таком способе регулирования сохраняется постоянный момент на валу электродвигателя.
Силовая схема состоит из силового согласующего трансформатора, двух управляемых выпрямителей и высокомоментного двигателя с встроенным тахогенератором. В состав СУ ЭПУ 1-2-…..П входят: регулятор скорости (РС), нелинейное звено, переключатель характеристик, управляющий орган, система импульсно-фазового управления (СИФУ), функциональный преобразователь, узел зависимого токоограничения, логическое устройство и блок защит.
СУ выполнена одноконтурной с одним ПИ-регулятором скорости. На входе РС сум-
мируются сигналы задания и обратной связи по скорости (с тахогенератора). Затем сигнал с регулятора скорости проходит через нелинейное звено, предназначенное для улучшения динамических характеристик привода при работе в области прерывистых токов. Затем сигнал управления поступает на переключатель характеристик и поступает в СИФУ.
Для ограничения максимального тока двигателя введен узел зависимого токоограничения, который обеспечивает ограничение тока якоря на заданном уровне «токовая отсечка» и зависимое токоограничение в функции скорости вращения.
Функциональный преобразователь ЭДС предназначен для линеаризации нелинейной регулировочной характеристики тиристорного преобразователя в режиме непрерывного тока.
Логическое устройство осуществляет раздельное управление силовыми тиристорными комплектами преобразователя.
Для предотвращения аварийных ситуаций предусмотрен блок защит. При их срабатывании осуществляется блокировка регулятора и управляющих импульсов СИФУ.
В данной работе на основании данных о параметрах системы был проведён расчёт параметров силовой цепи, затем определена область существования электромеханических характеристик электропривода.
Методика синтеза одноконтурных структур тиристорных регулируемых электроприводов (РЭП) постоянного тока изложена в [1].
Структурная схема одноконтурной линеаризованной САУ РЭП приведена на рис. 1, где приняты следующие обозначения:
459

XIII Международная научно-практическая конференция «СОВРЕМЕННЫЕ ТЕХНИКА И ТЕХНОЛОГИИ» |
|||||||||||
|
|
|
|
КТ * Imax |
|
|
С |
|
|
|
|
|
|
|
|
|
|
КТП |
|
|
|
|
|
|
|
|
|
Uрсmax |
|
|
|
|
|
|
|
|
|
|
|
(+) |
|
|
|
|
MC |
|
|
|
|
|
|
|
|
|
|
|
|
||
UЗС |
|
UРС |
|
НЗ1 |
|
ЕТП |
|
|
|
(-) |
|
|
|
|
|
|
|
|
|
||||
|
|
UУ |
СИФУ |
1/ RЯЦ |
I |
|
1 |
ω1 |
|||
фильтр |
ПИ - РС |
|
|
|
С |
||||||
|
|
|
|
||||||||
|
|
|
UТО |
|
- ТП |
|
TЯЦ*p - 1 |
|
|
J*p |
|
|
(-) |
|
(+) |
(-) |
|
(-) |
|
|
|
|
|
|
|
|
|
|
|
|
|
||||
|
|
|
ЗТО |
UУ ДОП |
|
|
ЕДВ |
|
С |
|
|
|
|
|
НЗ2 |
|
|
|
|
|
|
||
|
|
|
|
|
|
|
|
|
|
|
|
|
КС |
|
|
|
|
КТ |
|
|
|
|
|
|
|
|
|
|
|
|
|
|
|
|
|
|
Iдоп (ω) |
|
|
|
|
|
|
|
|
|
|
Рис. 1. Структурная схема нелинейной САУ электропривода. |
|
|
Рис. 2. Имитационная модель нелинейной САУ электропривода ЭПУ1
Фильтр - фильтр на входе электропривода, оптимизирующий реакцию контура скорости на управляющее воздействие, с передаточной функцией в общем случае
W(p)ф = Т1р +1 ;
Т2 р +1
ПИ-РС - регулятор скорости пропорционально - интегрального типа с передаточной функцией
W(p)рс = Крс Трср+1.
Трср
Для расчёта переходных процессов проведён синтез линеаризованной САУ РЭП по структуре 2а по методике Поздеева. По результатам синтеза определены значения коэффициента усиления и постоянные времени регулятора скорости и фильтра на входе РЭП и коэффициенты обратных связей по скорости и току. На ЭВМ рассчитаны ЛАЧХ и ЛФЧХ замкнутого контура положения и определены показатели быстродействия: полоса пропускания по модулю и по фазе.
Исследования динамических свойств САУ РЭП, структурная схема которой представлены на рисунке 1, были проведены на ЭВМ в программной среде MATLAB 7[2]. Разработана имитационная модель нелинейной САУ
РЭП, показанная на рисунке 2 и учитывающая следующие нелинейности: ограничение на выходе РС и устройство зависимого от скорости токоограничения (UZTO).
В структуре на рисунке 2 для упрощения и наглядности несколько элементов, на которых реализуется узел зависимого токоограничения, объединены в подсистему UZTO.
Исследования проводились по изучению влияния на показатели качества САУ РЭП величины и формы сигнала задания и момента нагрузки.
По результатам исследований сделаны следующие краткие выводы:
•для отработки без перерегулирования по скорости для средних и больших заданий необходимо принять адаптивный регулятор скорости.
•в линеаризованной системе ожидаемые показатели качества согласно методике Поздеева в целом совпадают с полученными при моделировании.
•различного рода нелинейности оказывают существенное влияние на показатели качества особенно: насыщение регуляторов и зависимое токоограничение от скорости.
Проделан подробный анализ влияния выше перечисленных нелинейностей на качество работы САУ РЭП и даны практические рекомендации.
460

|
|
Современные техника и технологии 2007 |
|
Исследования системы проводились и на |
|
имитационной модели, и на реальной уста- |
ЛИТЕРАТУРА: |
|
новке. Исследовались динамические харак- |
3. Удут Л.С., Мальцева О.П., Кояин Н.В. |
|
теристики привода, а также влияние пара- |
Проектирование автоматизированных тири- |
|
метров ПИ-регулятора на показатели качест- |
сторных электроприводов постоянного тока. |
|
ва системы. В результате моделирования |
Учеб. Пособие. – Томск: Изд. ТПИ, 1991. - 104 |
|
были найдены параметры оптимальной на- |
с. |
|
стройки. Показатели качества одноконтурной |
4. Герман-Галкин С.Г. Компьютерное |
|
САУ РЭП, полученные на имитационной мо- |
моделирование полупроводниковых систем в |
|
дели, совпали с ожидаемыми. Небольшое |
MATLAB 6.1: Учебное пособие. – СПб.: КО- |
|
отличие реальных показателей качества от |
РОНА принт, 2001. |
|
полученных при моделировании объясняется |
|
|
наличием погрешностей. |
|
ОБ ЭФФЕКТЕ «МАГНИТНОЙ ПРУЖИНЫ» В СИНХРОННОМ ГЕНЕРАТОРЕ ВОЗВРАТНО-ПОСТУПАТЕЛЬНОГО ДВИЖЕНИЯ
Саттаров P.P., Бабикова Н.Л. Исеева Р.Р.
Уфимский государственный авиационный технический университет, Россия, г. Уфа, ул. К. Маркса, 12
E-mail: Nat.16.01@mail.ru
В настоящее время большое внимание уделяется автономным экологически чистым источникам энергии, преобразующим сопутствующую «бесплатную» энергию движения (колебания и т.д.) какой-либо среды или тела в электрическую. В использовании человека находятся различные электронные устройства (сотовый телефон, аудиопроигрыватели, фотоаппараты и т. д.), требующие подзарядки аккумуляторных батарей. Одним из наиболее перспективных направлений в этой области является разработка и исследование синхронных генераторов воз- вратно-поступательного движения с возбуждением от постоянных магнитов для работы в зарядных устройствах.
На кафедре электромеханики ведется разработка новых конструкций синхронных генераторов возвратно-поступательного движения. Генератор возвратно-поступательного движения содержит цилиндрический герметизированный ферромагнитный корпус, обмотки и подвижную часть, состоящую из постоянного магнита и полюсных наконечников.
При возвратно-поступательном движении подвижной части (индуктора) создается ЭДС, величина которой зависит от скорости движения и при последовательносогласном соединении обмоток суммируется. Выводы от обмоток через выпрямитель подключены к зарядному конденсатору, с
которого снимается напряжение для питания электрической схемы. Торможение магнитной системы обусловлено магнитной силой («магнитной пружиной»), и дополняется герметизацией корпуса, так как при движении магнита газ (например, воздух) сжимается в замкнутой полости (срабатывает «пневматическая пружина»).
В дальнейшем будет дана простейшая оценка действия «магнитной пружины».
Сила, развиваемая «магнитной пружиной» определяется, как отношение разницы электромагнитных энергий рабочих зазоров последующего (i+1) и предыдущего (i) положения подвижной части генератора
W(i+1)i , к приращению её перемещения X
энергетическим методом [1].
В работе определяется приращение электромагнитной силы действующей на втягивание подвижной части (индуктора) генератора.
За начальное, принято положение индуктора генератора, показанное на рисунке 1. Для определения энергии магнитного поля при перемещении индуктора (рисунок 2) произведён расчёт полной энергии магнитного поля в рабочем зазоре генератора.
Приняты следующие обозначения: магнитное поле в части полюсного наконечника, находящегося внутри магнитопровода - участок 1; магнитное поле в части полюсного
461

XIII Международная научно-практическая конференция «СОВРЕМЕННЫЕ ТЕХНИКА И ТЕХНОЛОГИИ»
наконечника, находящегося вне магнитопровода - участок 2.
Рисунок. 1 . Исходное положение подвижной части генератора
Рисунок 2. Изменение магнитного поля при перемещении подвижной части генератора на выходе из магнитопровода
Индукция в рабочем зазоре участка 1:
Вδ1 = Фм ,
Sδ1
где Фм - основной магнитный поток;
Sδ1 - средняя площадь сечения рабочего
зазора генератора на участке 1. Индукция в рабочем зазоре участка 2:
Вδ 2 = Фм , .
Sδ 2
где Фм - основной магнитный поток;
Sδ 2 - средняя площадь сечения рабочего зазора генератора на участке 2.
При расчете магнитной цепи принято, что магнитное сопротивление ферромагнитного магнитопровода равно нулю, также не учитывается эффект выпучивания.
Магнитный поток цепи с учетом потока рассеяния:
Ф = f σ Gм ,
м м σ + GGм
где fм - МДС магнита,
|
Gδ1 Gδ 2 |
- эквивалентная проводи- |
||||
G = G |
+ G |
|
||||
|
δ1 |
|
|
δ 2 |
|
|
мость рабочих зазоров; |
||||||
Gδ1 = μ0 |
Sδ1 |
|
- эквивалентная проводи- |
|||
δ |
1 |
|
|
|||
|
|
|
|
|
|
мость воздушного зазора участка 1 без учета насыщения
Gδ 2 = μ0 |
Sδ 2 - эквивалентная проводи- |
||
δ |
2 |
|
|
|
|
|
мость воздушного зазора участка 1 без учета насыщения
Gм - проводимость магнита.
Магнитное поле рассеяния учитывается при расчетах введением коэффициента рассеяния
σ равным 1,3 [3].
Полная энергия магнитного поля в рабочем зазоре генератора
W =W1 +W2.
где W =V |
B |
2 |
. |
- магнитная энергия в |
δ1 |
|
|||
1 1 |
2 μ0 |
|
|
|
воздушном объёме участка 1 |
W2 =V2 |
B 2 |
- магнитная энергия в |
δ 2 |
||
2 μ0 |
воздушном объёме участка 2.
В дальнейшем расчёте при смещении ин-
дуктора на X , аналогично, в новом положении индуктора.
Разность энергий магнитного поля последующего (i+1) и предыдущего (i) положения подвижной части генератора
W(i+1)i =W(i+1) −Wi .
Электромагнитная сила, действующая на подвижную часть генератора
F |
= |
W(i+1)i |
. |
эм(i) |
|
X |
|
|
|
Результаты расчетов для одной из конструкции синхронного генератора возвратнопоступательного движения представлены на рисунке 3 в виде графика Fэм = f (x) ,
где х - перемещение подвижной части генератора от начального положения.
462
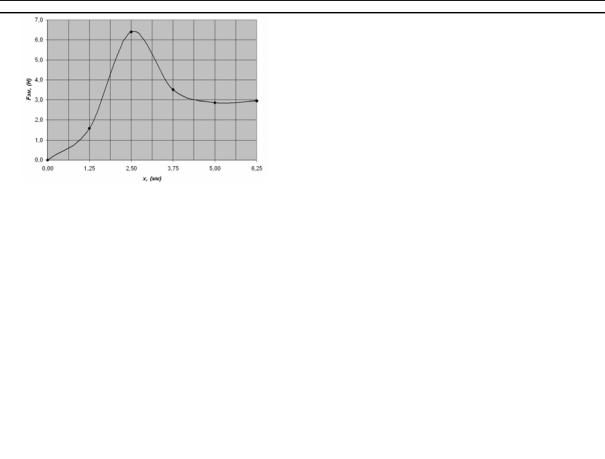
Современные техника и технологии 2007
Рисунок 3. Зависимость электромагнитной силы от перемещения подвижной части генератора
на выходе из магнитопровода Для того, чтобы подвижная часть гене-
ратора остановилась под действием магнитной пружины необходимо равенство работы электромагнитной силы и кинетической энергии подвижной части. Проведенные расчеты показывают, что торможение может быть обеспечено только за счет электромагнитных сил.
В работе проведен анализ эффекта «магнитной пружины» в синхронном генера-
торе возвратно-поступательного движения в режиме холостого хода.
Показано, что в подобной конструкции синхронного генератора может быть обеспечено торможение без использования механических пружин.
Использование предлагаемого синхронного генератора возвратно-поступательного движения в качестве автономного источника электроэнергии по сравнению с известными конструкциями обеспечит:
- отсутствие дополнительных механических пружин для поддержания подвижной части генератора в рабочем зазоре;
-прочность и надежность конструкции;
-высокую технологичность конструкции.
ЛИТЕРАТУРА:
1.ИвановСмоленский А.В. Электромагнитные силы и преобразование энергии в электрических машинах: Учеб.пособие для вузов по спец."Электромеханика".-М.:
Высш.шк., 1989.-311с.
2. М.Я. Хитерер, И.Е. Овчинников. Синхронные электрические машины возвратнопоступательного. движения. - СПб.: Корона принт, 2004. - 386 с.
ИМИТАЦИОННАЯ МОДЕЛЬ ЧАСТОТНО-РЕГУЛИРУЕМОГО АСИНХРОННОГО ЭЛЕКТРОПРИВОДА ЛИФТА НА БАЗЕ ПРЕОБРАЗОВАТЕЛЯ ЧАСТОТЫ ФИРМЫ DANFOSS
Смирнов А.О.
Томский политехнический университет, Россия, г. Томск, пр. Ленина, 30 E-mail smirao2005@rambler.ru
В работе представлена имитационная модель частотно-регулируемого асинхронного электропривода лифта на базе преобразователя частоты(ПЧ) фирмы DANFOSS, позволяющая проводить исследования данной системы в неподвижной и вращающейся системе координат в динамических режимах работы. Получены динамические характеристики, которые позволяют говорить о предельно высоком быстродействии САР, контуров тока, высокой точности и широком диапазоне исследуемых частот.
Современный уровень развития силовой электроники и микропроцессорных систем управления обеспечивает широкое распространение частотно-регулируемого асинхронного электропривода. Системы векторного управления позволяют создавать электроприводы переменного тока, не уступающие по своим характеристикам приводам постоянного тока. Достоинствами системы преобразователь частоты - асинхронный двигатель, яв-
ляются простота в эксплуатации и дешевизна двигателя, недостатками – относительно большая стоимость преобразователя частоты.
Целью данной работы является исследование регулируемого асинхронного электропривода лифта на базе преобразователя частоты фирмы DANFOSS, в динамических режимах методом имитационного моделирования.
Функциональная схема управления лифтом приведена на рис. 1.
463

XIII Международная научно-практическая конференция «СОВРЕМЕННЫЕ ТЕХНИКА И ТЕХНОЛОГИИ»
ProgLogContr
СистемаМикро- |
управленияконтроллер |
Система |
|
|
|
|
|
Кабина |
Управления |
|
|
АД |
|
|
|
|
|
|
|
лифта |
||
АД лифта |
|
|
|
|
|
|
|
|
|
|
|
|
|
|
|
|
|
|
|
|
Рисунок 1. – Функциональная схема САУ пассажирским лифтом
В диаграмме работы лифта можно выделить следующие режимы:
1.разгон электродвигателя до устано- вив-шейся скорости υуст;
2.движение с установившейся скоро-
стью;
3.уменьшение скорости при подходе к этажу назначения (непосредственно до 0 или до малой скорости дотягивания);
торможение и остановка кабины лифта на этаже назначения с требуемой точностью
Режим работы электропривода лифта характеризуется частыми включениями и отключениями, т.е. является в основном динамическим.
Во время переходных процессов электропривод обеспечивать разгон и замедление кабины с максимальными допустимыми значениями ускорения и рывка с их ограничением.
При этом применение регулируемого асинхронного электропривода позволяет оптимизировать работу электропривода в динамических режимах, стабилизировать диаграмму движения, уменьшить время перемещения лифта между этажами и повысить его производительность.
Поэтому исследование частотнорегулируемого асинхронного электропривода лифта на базе преобразователя частоты фирмы DANFOSS является актуальным и современным.
На рисунке 2 представлена имитационная модель частотно-регулируемого асинхронного электропривода лифта на базе преобразователя частоты фирмы DANFOSS, с помощью которой производились исследования ЭП в динамических режимах.
Рисунок. 2 Имитационная модель частотнорегулируемого асинхронного электропривода лифта на базе преобразователя частоты фирмы DANFOSS
Имитационная мдель состоит:
1.Микроконтроллер
2.Асинхронный двигатель
3.Система управления АД лифта
4.Кабина лифта
На рисунках 3-5 приведены зависимости скорости, момента, перемещения, потока от времени при подъеме пустой кабины с помощью асинхронного двигателя на холостом ходу с последующим набросом нагрузки.
Подъем с пустой кабиной
Рисунок 3 - Переходный процесс по моменту при подъеме пустой кабины в АСУ ЭП лифта
Рисунок 4 - Переходный процесс по скорости при подъеме пустой кабины в АСУ ЭП лифта
Рисунок 5 - Переходный процесс по перемещению при подъеме пустой кабины в АСУ ЭП лифта
464

|
|
Современные техника и технологии 2007 |
|
Как видно из графиков переходных |
ные процессы протекают с высокими показа- |
процессов при спуске или подъеме все вели- |
телями качества, что позволяет применять |
|
чины (т.е. скорость, момент и перемещение) |
данную систему преобразователь частоты – |
|
выходят на свои номинальные значения. В |
асинхронный двигатель в различных отраслях |
|
момент наложения механического тормоза |
промышленности. |
|
все величины спадают до нуля. При этом на |
|
|
двигателе напряжение тоже спадает до нуля. |
ЛИТЕРАТУРА: |
|
В момент отпускания механического тормоза |
1. Рудаков В.В., Столяров И.М., Дартау |
|
скорость возрастает до своего критического |
В.А. Асинхронные электроприводы с вектор- |
|
значения, а затем устанавливается до своего |
ным управлением. – Л.: Энергоатомиздат, |
|
номинального значения 148.5 рад/с (при этом |
1987.- 420с. |
|
перерегулирование составляет 8.1%). При |
2. Терехов В.М. Системы управления |
|
этом переходный процесс по моменту имеет |
электроприводов: Учебник для студ. высш. |
|
колебательный |
учеб. заведений / В.М. Терехов, О.И. Осипов; |
|
|
Анализ проведенных исследований раз- |
Под ред. В.М Терехова. – М.: Издательский |
личных динамических режимов в частотно- |
центр «Академия», 2005.-304с. |
|
регулируемом асинхронном электроприводе |
Ключев.В.И. Теория электропривода. М.: |
|
лифта на базе преобразователя частоты |
Энергоатомиздат, 2001.704 с. |
|
фирмы DANFOSS показывает, что переход- |
http://www.abb.com/ru |
БЕЗДАТЧИКОВАЯ СИСТЕМА РЕГУЛИРОВАНИЯ ДАВЛЕНИЯ ЦЕНТРОБЕЖНОГО НАСОСА НА БАЗЕ ПРЕОБРАЗОВАТЕЛЬНОЙ ТЕХНИКИ
Толпаров Д.В.
Томскийполитехническийуниверситет, Россия, г.Томск, пр. Ленина, 30 E-mail: tdv@elti.tpu.ru
За последние десять лет внедрение преобразовательной техники на насосном оборудовании в различных системах позволило достичь высоких показателей регулирования технологических параметров, повысить надёжность работы процессов, снизить общий уровень энергопотребления. Наряду с этим значительное количество систем с насосным оборудованием после модернизации не получили указанных преимуществ. При этом бесперебойность регулирования параметров в этих процессах существенно снизилась. Одна из основных причин неисправностей заключается в низкой надёжности системы первичных измерителей технологических параметров, их высокой чувствительности к различного рода помехам при значительном удалении от управляющих устройств. Подобные проблемы часто наблюдаются в системах, в которых осуществляется регулирование величины давления центробежных насосов по заданному закону. В большинстве схем датчики устанавливается непосредственно во всасывающей и нагнетаемой стороне насосов. Информация с них используется для формиро-
вания обратной связи в замкнутой системе регулирования давления с помощью классического ПИД-регулятора. Другой подход к организации системы регулирования давления насоса заключается в формировании частоты вращения насоса, соответствующей потребляемой мощности при заданной величине давления. Для этого необходимо измерение и регулирование потребляемой мощности и частоты вращения асинхронного двигателя.
Подобные системы существуют у лидеров рынка насосного оборудования и реализованы на базе единого мехатронного блока, включающего насос, электродвигатель и преобразователь частоты. Однако номенклатурный ряд подобных насосов относительно небольшой, а система управления построена с учётом характеристик конкретной модели. Возможность реализации подобной системы на базе комплектного общепромышленного преобразователя частоты за счёт его стандартных функциональных возможностей позволит достичь максимальной надёжности насосных систем. Универсализация и обучение бездатчиковой системы позволяют ис-
465

XIII Международная научно-практическая конференция «СОВРЕМЕННЫЕ ТЕХНИКА И ТЕХНОЛОГИИ»
пользовать её для регулирования давления различных типов центробежных насосов.
Построение системы регулирования давления в разомкнутом контуре основано на известных соотношениях между расходом (Q), напором (H), мощностью (P) и скоростью вращения (n) насосного агрегата [1]:
Н(n,Q) = А |
1 |
n2 + B |
n |
Q + C |
Q2 |
|
|||
|
|
1 |
|
|
1 |
|
|
|
|
|
|
|
n2 Q − B |
|
n Q2 + C |
|
n3 |
||
Р(n, Q) = А |
2 |
2 |
2 |
||||||
|
|
|
|
|
|
где А1, А2 , В1, В2 , С1, С2 - коэффициенты,
определяемые конструкцией насоса.
Для определения величин коэффициентов необходимо произвести измерение параметров Q, H, P насоса в трёх различных режимах работы на номинальной скорости вращения:
1)Измерение H0 , P0 при работе насоса на закрытую системуQ0 = 0 ;
2)Измерение Hном, Pном, Qном при работе насоса в номинальной рабочей точке с максимальным КПД;
3)Измерение Hмакс, Pмакс, Qмакс при работе насоса на максимально допустимом расходе системы.
Используя данные измерений Н, Р, Q из соотношений для насоса определяются тре-
буемые коэффициенты А1, А2 , В1, В2 , С1, С2 :
Н |
0 |
= |
А |
1 |
n |
2 + B n 0 + C |
0 |
|
|
|
|
А |
1 |
|
|
||||||||||||||||
|
|
|
|
|
|
|
|
|
|
1 |
|
|
|
|
|
|
1 |
|
|
|
|
|
|
|
|
||||||
|
|
|
= А |
|
|
n |
2 0 − B |
|
n 0 + C |
|
n3 |
|
|
|
|
|
|||||||||||||||
Р |
0 |
2 |
2 |
2 |
|
|
C2 |
|
|
||||||||||||||||||||||
|
|
|
|
|
|
|
|
|
|
|
|
|
|
|
|
|
|
|
|
|
|
|
|
|
|
||||||
Н |
ном |
= Н |
0 |
+ B n |
Q |
ном |
+ C |
|
Q2 |
|
|
|
|
|
С |
|
|||||||||||||||
|
|
|
|
|
|
|
|
1 |
|
|
|
|
|
1 |
|
ном |
|
|
|
1 |
|
||||||||||
|
|
|
|
= Н |
|
+ B n Q |
|
|
+ C |
|
Q |
|
|
|
|
||||||||||||||||
Н |
макс |
0 |
макс |
|
2 |
|
|
|
|
В1 |
|
||||||||||||||||||||
|
|
|
|
|
|
|
|
|
1 |
|
|
|
|
|
|
1 |
|
макс |
|
|
|
|
|
|
|||||||
|
ном = А2 n |
2 |
Qном − B2 |
|
|
|
|
2 |
|
|
|
|
|
|
|
А2 |
|||||||||||||||
Р |
|
n Qном + Р0 |
|
|
|
||||||||||||||||||||||||||
|
|
|
|
= А |
|
|
n2 Q |
|
|
|
|
− B |
|
n |
Q2 |
|
+ Р |
|
|
|
|||||||||||
Р |
макс |
2 |
макс |
2 |
|
0 |
|
|
B2 |
||||||||||||||||||||||
|
|
|
|
|
|
|
|
|
|
|
|
|
макс |
|
|
|
|
|
Для построения характеристики управления насосом в разомкнутом контуре необходимо исключить из уравнений параметр расхода системы:
Н(n,Q) = А1 n2 + B1 n Q + C1 Q2C1 Q2 + B1 n Q + А1 n2 − Н(n,Q) = 0
Решением данного квадратного уравнения будет один из положительных корней:
Q(n, Н) = −(B1 n) − (B1 n)2 −4 C1 (А1 n2 − Н) 2 C1
После подстановки в выражение потребляемой мощности насосного агрегата получим:
Р(n, Н) = А2 n2 Q(n, H) − B2 n Q(n, H)2 +C2 n3
Данное выражение используется для формирования характеристики управления
Р = f (n) |Hзад .
Характер зависимости Q = f (n, Н) опре-
деляет ряд ограничений для использования на различных типах центробежных насосов. Только для насосов, у которых характеристика Н = f (Q) носит строго спадающий характер
и отсутствуют экстремумы, возможно построить зависимость Р = f (n) |Hзад . Следовательно для центробежных насосов с полуоткрытыми, открытыми рабочими колёсами указанные выше соотношения не могут использоваться для регулирования давления в разомкнутом контуре. Другое ограничение для использования данной зависимости заключается в работе насоса на систему со статической составляющей напора. При этом снижение частоты вращения приводит к более интенсивному изменению расхода и КПД системы [2]. В закрытых системах циркуляции теплоносителя или хладагента отсутствует статическая составляющая нагрузки. Поэтому именно в данных системах возможно использование бездатчиковой системы регулирования давления. Дополнительное ограничение накладывает функция энергопотребления от расхода системы. Жёсткая характеристика мощности сильно снижает точность управления по разомкнутому контуру.
Первые результаты моделирования в среде визуального моделирования Simulink, входящей в универсальный программный пакет Matlab, показали возможность регулирования давления в разомкнутой бездатчиковой системе. На рисунке 1 приведён пример структуры управляющей части исследуемой системы. После замены в выражении потребляемой мощности параметра скорости насоса на частоту вращения, получаем характеристику Р = F(f , Н) . В модели производится пре-
образование сигнала заданного давления в мощность. Далее сравниваются величины заданной и измеренной мощности. Сигнал ошибки поступает на регулятор, который формирует приращение частоты в зависимости от знака и величины разностного сигнала. После расчёта частоты вращения производится корректировка заданной мощности по характеристикеР = F(f , Н) .
466

Современные техника и технологии 2007
Рис.1. Структурная схема управляющей части формирования задания частоты вращения насоса в функции заданного давления Из структуры следует, что её устойчивая работа зависит от соотношения электромагнитной и механической постоянных времени. Механическая постоянная времени должна быть на порядок больше, чем электромагнитная. Иначе возможность измерения и регулирования мощности по внутреннему контуру относительно работы внешнего будет невоз-
можно.
Дальнейшее исследование бездатчиковой структуры управления центробежным насосом позволит определить оптимальную структуру регулятора и критерии его настройки. Практическая реализация подобной системы требует разработки алгоритма формирования характеристики управления по паспортным или измеренным данным, а также автоматизацию процесса измерения рабочих параметров насоса в процессе наладки. На сегодняшний день практическое ограничение для массового внедрения данной системы заключается в сложной настройке.
При использовании иных интерполяционных функций и регуляторов для формирования зависимости Р = F(f , Н) возможно исполь-
зовать бездатчиковую структуру для регулирования давления центробежных насосов, имеющих характеристики с экстремумами и неоднозначными зависимостями давления от расхода. Дополнительно с помощью данного подхода бездатчикового регулирования давления можно реализовать обратную задачу определения текущего расхода насоса, что позволит отследить ряд аварий в системе трубопроводов.
На сегодняшний день существует возможность практически использовать данную систему управления для бесперебойности процесса регулирования в комбинации с классической схемой с обратной связью. Такое взаимодействие позволит снизить затраты на настройку системы благодаря использованию информации обратной связи для построения характеристики управления бездатчиковой структуры.
ЛИТЕРАТУРА:
1.Онищенко Г.Б.. Электропривод турбомеханизмов:. М.: Энергия, 1972 г. - 240 с.
2.Иванов Г.М., Онищенко Г.Б., Автоматизированный электропривод в химической промышленности:. М.: Машиностроение, 1975
г. - 312 с.
3.MG.10.T1.02 Sensorless Pump Control for VLT, руководство по программированию опции преобразователей частоты Danfoss, - 22 с.
ИМИТАЦИОННОЕ МОДЕЛИРОВАНИЕ АСИНХРОННОГО ДВИГАТЕЛЯ НА БАЗЕ МИКРОПРОЦЕССОРА СЕРИИ TMS320F2812
Тургенев Д.В., Шмидт О.Р., Ланграф С.В.
Томский политехнический университет, Россия, г.Томск, пр.Ленина, 30
E-mail: Dmitry_turgenev@elti.tpu.ru, shmidt@elti.tpu.ru, langraf@elti.tpu.ru
Развитие человеческой цивилизации невозможно без постоянного совершенствования машин и механизмов, которые становятся все “умнее”, производительнее и удобнее в использовании за счет применения цифровых систем управления. Серия микроконтролле-
ров Texas Instruments C2000 [1] является на сегодняшний день одной из наиболее интересных для специалистов в области электропривода, так как имеет эффективную систему
команд и широкую гамму встроенных периферийных устройств, позволяющих решать самые разнообразные задачи. Эта серия ориентирована на так называемое управление событиями в реальном времени и имеет необходимые для этого специализированные периферийные устройства: контроллер прерываний, процессор событий. Это все необходимо для создания быстродействующих и
467

XIII Международная научно-практическая конференция «СОВРЕМЕННЫЕ ТЕХНИКА И ТЕХНОЛОГИИ»
надежных систем управления, без которых в настоящее время уже не обойтись.
Моделирование асинхронного двигателя в реальном масштабе времени необходимо по нескольким причинам, а именно: получение реальных переходных процессов выбранного двигателя; оценка правильности переходных процессов без подачи напряжения на двигатель; построение систем управления.
Проанализировав данную проблему, был выявлен ряд необходимых для ее решения задач:
-организовать выполнение периодических процедур с периодом;
-сформировать управляющие сигналы для двухфазной имитационной модели асинхронного двигателя;
-разработать имитационную модель асинхронного двигателя в реальном масштабе времени.
Каждая задача была решена с помощью программного обеспечения Code Composer Studio v3.1 (CCS) и библиотеки DMCLIB_281x_v321, прилагаемых фирмой
Texas Instruments вместе с микропроцессором.
Первая задача решалась следующим образом: была составлена программа, при выполнении которой светодиод выдает внешний сигнал с частотами 1, 2 и 3 Гц, режим, при котором лампочка горит постоянно, либо не горит ни при каких условиях. Правильность работы программы сразу же проверяется на реальном микропроцессоре следующим образом: загружаем программу в микропроцессор и запускаем на выполнение. Лампочка начинает моргать. С помощью обыкновенных наручных часов определяем, число вспышек светодиода в минуту. Соответствующее количество вспышек в минуту свидетельствует
оправильной конфигурации аппаратных прерываний.
При решении второй задачи необходимо обеспечить ограничение интенсивности изменения входного сигнала. С этой целью был сформирован задатчик интенсивности (Рисунок 1).
Выходной сигнал задатчика интенсивности является входным для формирователя сигнала «пилообразной» формы. По сути дела «пилообразный» сигнал является углом поворота вектора напряжения, который мы получим с помощью обратного преобразования Парка (Рисунок 1). Проверка правильности выходного «пилообразного» сигнала осуществляется следующим образом: период сигнала с частотой 50 Гц должен соответствовать 0.02 с (Рисунок 2).
Рисунок 1 – Формирование напряжений
Рисунок 2 – Пилообразный сигнал
На Рисунке 2 приняты следующие обозначения:
К – количество «импульсов» «пилообразного» сигнала
Т – период 10 «импульсов» «пилообразного» сигнала
Tим = КТ = 0.20510 = 0.0205с - период одного
«импульса».
Обратное преобразование Парка преобразует входные сигналы (угол поворота и 2 постоянных напряжения) в два синусоидальных сигнала, сдвинутых друг относительно друга на 90 градусов и фазой, зависящей от заданного угла поворота. Правильность выходной синусоиды проверяется аналогично предыдущему случаю (Рисунок 3).
Рисунок 3 – Проверка правильности сигнала
На данном этапе можно сделать вывод о том, что была построена система, формирующая сигналы напряжений для имитационной модели.
Изначально двухфазная имитационная модель асинхронного электродвигателя создавалась в программной среде MatLab 7.1 на базе структурной схемы с помощью типовых динамических звеньев [2]. За основу был принят асинхронный двигатель АИМ 100L4 мощностью 4 кВт. Далее был составлен программный алгоритм, описывающий имитационную модель асинхронного электродвигателя в переходных режимах. Реализация производилась на базе системы дифференци-
468

|
|
Современные техника и технологии 2007 |
альных уравнений, записанных в разностной |
создании имитационной модели последова- |
|
форме. Система решалась численным мето- |
тельно использовалась абсолютная и относи- |
|
дом Эйлера первого порядка. Результаты ра- |
тельная системы единиц. Результаты работы |
|
боты в виде переходных процессов по скоро- |
в номинальном режиме соответствуют ожи- |
|
сти, моменту и составляющим тока в среде |
даемым. |
|
MatLab 7.1 представлены на Рисунке 4а. При |
|
а)
б)
Рисунок 4 – Графики переходных процессов имитационной модели двигателя:
а) в среде MatLab 7.1, б) в среде Code Composer Studio v3.1
По итогам проделанной работы видно, что переходные процессы имитационной модели, реализованной на базе микропроцессора TMS320F2812, точно совпадают с переходными процессами, полученными в среде MatLab 7.1. Основное преимущество полученной модели это возможность её работы в режиме реального времени, т.е. в темпе протекания переходных процессов. Основываясь на результатах данной работы, в дальнейшем
планируется построение системы управления двигателем.
ЛИТЕРАТУРА:
1.C281x C/C++ Header Files and Peripheral Examples, Texas Instruments, SPRC097.
2.Шмидт О. Р. «Имитационное моделирование АД с векторным управлением в среде MatLab 7.1» //Материалы всероссийской научной конференции молодых ученых в 7-ти частях. Новосибирск. Изд-во НГТУ, 2006, Часть 3 – 245 с.
469

XIII Международная научно-практическая конференция «СОВРЕМЕННЫЕ ТЕХНИКА И ТЕХНОЛОГИИ»
ИССЛЕДОВАНИЕ ХАРАКТЕРИСТИК НАСОСНЫХ АГРЕГАТОВ И ТРУБОПРОВОДОВ
Тютева П.В., Муравлева О.О.
Томский политехнический университет, Россия, г. Томск, пр. Ленина 30
E-mail: TyutevaPV@sibmail.com
На перекачку сточных и чистых вод в России расходуется 90..130 млрд. кВт·ч электроэнергии. Стоимость электроэнергии в общей сумме эксплуатационных расходов на водо- проводно-канализационных предприятиях, в случае использования поверхностных вод, составляет 40..50 %. При использовании подземных вод этот показатель увеличивается до 70..80 %. Несмотря на это, созданию экономичных режимов работы насосных установок пока еще уделяется недостаточное внимание. В результате 5..15 % энергии нерационально теряется в процессе перекачки чистых и сточных вод, в отдельных случаях этот показатель увеличивается до 25..30 % [1].
Целью данной работы является количественный анализ характеристик насосных агрегатов и трубопроводов при их различных режимах работы.
Режим работы насосной установки тесно связан с режимом работы системы транспортировки жидкости в целом. Одной из основных причин неэкономичной работы насосной установки является несоответствие рабочих параметров насоса (напор Н, подача Q) режиму работы системы. В некоторых условиях могут возникнуть не только неэкономичные режимы, но даже опасные для насосов и системы трубопроводов режимы работы.
Преднамеренное изменение подачи и напора насосов в соответствии с переменным режимом работы системы водоподачи или водоотведения называется регулированием. Центробежные насосы регулируются изменением частоты вращения двигателя или изменением степени открытия задвижки на напорной линии.
В условиях практического водопотребления требуется частое изменение подачи воды из-за большого числа разнородных потребителей. Большое различие в количестве потребляемой воды в течении суток требует увязки водоподачи и водопотребления для любого момента времени. При этом требуется не только обеспечение требуемой подачи, но и сохранение высокого КПД в зоне регулирования насосного агрегата. В целях стабильного поддержания расчетного напора могут быть реализованы следующие решения:
1. Частотное регулирование – установка насосных агрегатов с регулируемым приводом, в этом случае при значительном изменении напоров в городской сети целесообразно применение частотного регулирования, а при небольших – параметрического.
При выборе типа регулирования следует иметь в виду, что частотное регулирование осуществляется в более широком диапазоне, чем параметрическое, но последнее значительно дешевле.
2. Дроссельное регулирование – дросселирование напорной линии насоса.
Прикрывая или открывая затвор, изменяют крутизну характеристики Н-Q трубопровода, которая зависит от его гидравлического сопротивления.
Проведем анализ экономической эффективности регулирования подачи воды по анализу характеристик насосной установки и трубопровода. На рис. 1 показаны характеристики насоса К45/30 и трубопровода при различных способах регулирования в относительных единицах. При этом пусть изменение подачи воды происходит в зоне незначительного изменения КПД насоса (рис. 2).
Характеристики насоса, показывающие взаимозависимость напора H, подачи Q, затрат мощности N и КПД насоса η при n1=nн=2900 об/мин, взяты из справочной литературы [2]. На практике при выборе насосов и электроприводов к ним недостаточно знать только заводские характеристики насосов
H=f(Q) и N=f(Q) при n=nн.
H*, o.e. |
|
|
|
|
|
|
|
||
|
1.2 |
Насос |
|
|
С |
|
|
|
|
|
|
|
|
|
|
|
|||
|
|
|
|
|
В |
|
|
||
|
1.0 |
|
|
|
|
|
А |
|
|
|
|
|
|
D |
|
|
n1=nн |
||
|
|
|
|
|
|
|
|||
|
0.8 |
|
|
|
F |
|
n2<n1 |
|
|
|
|
|
|
|
n3<n2 |
|
|||
|
|
|
|
|
|
|
|||
N*, o.e. |
0.6 |
|
|
|
|
|
|
|
|
1.2 |
|
Трубопровод |
|
B’ |
A’ |
n1=nн |
|||
1.0 |
|
|
C’ |
||||||
0.4 |
|
|
|
D’ |
|
n2<n1 |
|||
0.8 |
|
|
|
|
|
||||
|
|
|
F’ |
|
|
n3<n2 |
|||
0.6 |
|
|
|
|
|
|
|||
|
|
|
|
|
|
|
|||
0.4 |
0.2 |
|
|
|
|
|
|
|
|
0.2 |
|
|
|
|
Q*3 |
Q*2 |
Q*1 |
|
|
0 |
0 |
|
|
|
|
||||
0.2 |
0.4 |
0.6 |
0.8 |
1.0 |
1.2 Q*, o.e. |
||||
|
|
||||||||
Рис. 1. Характеристики насоса и трубопрово- |
|||||||||
да при различных способах регулирования |
470

Современные техника и технологии 2007
η, o.e. |
|
|
|
|
|
|
|
0.8 |
|
|
|
|
|
|
|
0.6 |
|
|
|
|
|
|
|
0.4 |
|
|
|
|
|
|
|
0.2 |
|
|
|
|
|
|
|
0 |
|
|
|
Q*3 |
Q*2 |
Q*1 |
|
0.2 |
0.4 |
0.6 |
0.8 |
|
1.0 |
1.2 Q*, o.e. |
|
|
|
||||||
Рис. 2. Характеристика η=f(Q*) насоса К45/30 |
Необходимо определенное множество этих кривых в нужных диапазонах изменения, так как при изменении частоты вращения рабочего колеса насоса ведет к изменению всех его рабочих параметров. Задаваясь точками известных кривых, аппроксимируем кривые полиномом и получаем зависимости:
Н* =−559,3 10−3 (Q* )2 +515,7 10−3 Q* +1,1; (1)
N * =−472,3 10−3 (Q* )2 +1143,5 10−3 Q* +0,21 . (2)
Для нахождения формулы для построения зависимостей H*=f(Q*) и N*=f(Q*) при любом значении n используют формулы приведения [3]:
|
|
|
nн |
2 |
|
|
3 |
||
Q* =Q* |
nн |
|
, H * =H * |
|
, N * =N * |
nн |
|
. (3) |
|
|
|
|
|||||||
i |
|
i |
|
|
i |
|
|
||
ni |
|
ni |
ni |
|
|
Решая совместно уравнения (1), (2) и (3) получаем зависимости характеристик насоса при любом значении частоты вращения рабочего колеса:
|
|
|
|
|
|
|
|
|
|
|
|
|
n |
|
н |
|
2 |
|
|
|
2 |
|
|
|
|||||||||
|
* |
|
|
|
−3 |
|
|
* |
|
|
|
|
|
|
nн |
|
|
|
|
|
|
|
|||||||||||
H i |
=−559,3 10 |
|
|
|
|
|
|
|
|
|
|
|
|
|
+ |
|
|
|
|
|
|||||||||||||
|
|
Qi |
|
|
|
|
|
|
|
|
|
|
|
|
|
|
|
|
|||||||||||||||
|
|
|
|
|
|
|
|
|
|
|
|
|
ni |
|
|
ni |
|
|
|
|
|
|
|||||||||||
|
|
|
|
|
−3 |
|
* |
|
|
|
nн |
|
|
|
|
|
|
|
2 |
|
|
|
2 |
|
|||||||||
|
|
|
|
|
|
|
|
|
|
|
nн |
|
|
nн |
|
|
|||||||||||||||||
|
|
+515,7 10 |
|
|
|
Qi |
|
|
|
|
|
|
|
|
|
|
|
|
+1,1 |
|
|
|
; |
|
|||||||||
|
|
|
|
|
|
ni |
|
|
|
|
|
|
|
|
|
||||||||||||||||||
|
|
|
|
|
|
|
|
|
|
|
|
|
|
ni |
|
|
|
|
|
ni |
|
|
|
||||||||||
|
|
|
|
|
|
|
|
|
nн |
|
2 |
|
|
|
|
|
|
3 |
|
|
|
|
|
|
|||||||||
* |
|
|
−3 |
|
* |
|
|
|
nн |
|
|
|
|
|
|
|
|
||||||||||||||||
Ni |
=−472,3 10 |
|
|
|
|
|
|
|
|
|
|
|
+ |
|
|
|
|
|
|||||||||||||||
|
|
|
Qi |
|
ni |
|
|
|
|
|
|
|
|
|
|
|
|
|
|
||||||||||||||
|
|
|
|
|
|
|
|
|
|
|
|
ni |
|
|
|
|
|
|
|
||||||||||||||
|
|
|
|
−3 |
|
* |
|
|
nн |
|
|
|
|
|
|
3 |
|
|
|
|
|
3 |
|
||||||||||
|
|
|
|
|
|
|
|
|
nн |
|
|
|
nн |
|
|
||||||||||||||||||
|
|
+1143,5 10 |
|
|
|
Qi |
|
|
|
|
|
|
|
|
|
|
|
|
+0,21 |
|
|
|
; |
||||||||||
|
|
|
|
|
|
ni |
|
|
|
|
|
|
|
||||||||||||||||||||
|
|
|
|
|
|
|
|
|
|
|
|
|
ni |
|
|
|
|
|
ni |
|
|
Используя полученные зависимости, строим характеристики при n2= 2400 об/мин и n3= 2100 об/мин.
Метод частотного регулирования обладает большим преимуществом. Это важно, так как при автоматизации насосных установок главной задачей является обеспечение подачи необходимого количества воды при заданном напоре и минимальной затрате электроэнергии.
Характеристика трубопровода проходит через точку А характеристики H*=f(Q*), полученной при n1=nн=2900 об/мин, когда по усло-
виям работы системы требуется обеспечить расход воды от величины Q*1 до Q*3.
При частотном регулировании, и неизменной характеристике трубопроводной сети и при изменении частоты вращения электропривода насоса можно получить характери-
стики H*=f(Q*) при n2= 2400 об/мин и n3= 2100
об/мин. Из рис. 1 видно, что при частоте вращения n2 подачу Q*2 можно осуществить в точке D, а подачу Q*3 можно осуществить в точке F при частоте вращения n3.
При использовании дроссельного регулирования неизменной остается характеристика насоса, производительности Q*2 до Q*3 осуществляются в точках В и С соответственно, с помощью изменения степени открытия задвижки.
Рассмотрим для этих двух вариантов изменение потребляемой мощности по графикам N*=f(Q*). При дросселировании и частоте вращения nн расходам Q*1, Q*2 и Q*3 на характеристике N*=f(Q*) при nн, соответствуют мощности точек A’, B’ и C’. Если менять подачу изменением частоты вращения, то тогда при n2 и n3 рассмотрим соответствующие зависимости N*=f(Q*). При частотном регулировании расходам Q*1, Q*2 и Q*3 на соответствующих кривых соответствуют точки A’, D’ и F’. На рис. 3 представлены зависимости экономии потребляемой мощности N* при частотном и дроссельном регулировании производительности насосного агрегата ( Q* - уменьшение подачи насосного агрегата по сравнению с Q*1).
N*, o.e. |
|
|
|
|
|
|
|
0,3 |
|
|
Частотное |
|
|
||
0,25 |
|
|
|
|
|||
|
|
|
|
|
|
|
|
0,2 |
|
|
|
|
|
|
|
0,15 |
|
|
|
|
|
|
|
0,1 |
|
|
Дроссельное |
|
|
||
|
|
|
|
|
|
|
|
0,05 |
|
|
|
|
|
|
|
0 |
0,05 |
0,1 |
0,15 |
0,2 |
0,25 |
0,3 |
Q*, o.e. |
Рис. 3. Зависимость экономии потребляемой энергии N*=f( Q*) при различных способах регулирования
Метод частотного регулирования обладает большим преимуществом по сравнению с дроссельным регулированием производительности насоса. Так, например, уменьшение подачи на 30 % дает экономию потребляемой энергии при дроссельном регулировании 9 %, а при частотном – 30 %. Кроме того, при частотном регулировании напор не превышает номинального значения, что ведет к увеличению срока службы оборудования.
Таким образом, использование приведенной последовательности расчета характери-
471

XIII Международная научно-практическая конференция «СОВРЕМЕННЫЕ ТЕХНИКА И ТЕХНОЛОГИИ»
стик насоса при различных частотах вращения, на примере К45/30, позволяет произвести совместный анализ характеристик трубопровода и насосной установки, что дает возможность оценить экономический эффект при использовании различных способов регулирования. Наибольший эффект наблюдается при внедрении регулируемого электропривода, который позволяет частоты вращения рабочего колеса насоса, характеристика трубопровода остается неизменной. Повышение же гидравлического сопротивления ведет к росту напора сверх номинального значения, увеличивая количество утечек и снижая продолжительность срока службы оборудования. Так использование метода частотного регулирования величины производительности позволяет снизить расход энергии в 3 раза по сравнению с методом дроссельного регулирования. Получены количественные характе-
ристики потребляемой энергии при дроссельном и частотном регулировании, которые необходимы для экономической оценки способов регулирования при различных расходах воды и оптимизации насосных агрегатов, в частности асинхронных двигателей, которые являются их силовой частью.
ЛИТЕРАТУРА:
1.Лезнов Б.С. Энергосбережение и регулируемый электропривод в насосных установках. – М. : ИК «Ягоба» – «Биоинформсер-
вис», 1998. – 179 с.
2.Каталог насосов 2000-2003. ОАО "Ясногорский машзавод". -Ясногорск, 2002. -71 с.
3.Карелин В.Я. Насосы и насосные станции : учебник / В. Я. Карелин, А. В. Минаев. – 2-е изд., перераб. и доп. – М. : Стройиз-
дат, 1986. – 320 с.
АНАЛИЗ ПРИМЕНЕНИЯ ДИСКОВОЙ МАШИНЫ С МАГНИТНОЙ СВЯЗЬЮ ДВУХ РОТОРОВ В СОСТАВЕ ОБОРУДОВАНИЯ ЯДЕРНО-ХИМИЧЕСКОЙ ОТРАСЛИ
Федянин А.Л., Леонов С.В., Муравлев О.П. Томский политехнический университет
E-mail: siberia99@mail.ru
Химическая промышленность в настоящее время – это сложный комплекс машин и механизмов, в который входят аппараты и машины химического производства, емкостное оборудование для хранения жидкостей и газов, трубопроводы. Все технологические цепочки на любом химическом производстве поддерживаются широким спектром вспомогательного оборудования, например: всевозможные механизмы по перемешиванию веществ, дозированию сырья, расфасовке продуктов производства, контрольно измерительные приборы и автоматика.
В ряде случаев при разработке технологического оборудования возникает ряд проблем. Одна из которых является вопрос герметизации разрабатываемого оборудования. Так, например, через место ввода движущихся частей при повышении давления или температуры возникает опасность выброса из технологического аппарата в окружающую среду высокотоксичных и агрессивных материалов. В результате одновременно с развитием аварийных ситуаций вследствие вне-
штатной работы технологического оборудования может быть нанесен непоправимый ущерб здоровью обслуживающего персонала.
В целом конструкции сальников для аппаратов высокого давления чрезвычайно сложны и не всегда обеспечивают необходимую герметичность. При этом потери мощности на момент сухого трения зачастую превышают расход энергии на перемещение исполнительных механизмов. Второй способ, основанный на разности давлений, применим когда попадание воздуха в аппарат не приводит к изменению свойств продукта химической реакции. В данном случае разработчик допускает завышенные значения массогабаритных показателей установки.
Данная техническая задача может быть решена путём применения синхронной электрической машины дискового типа. В предложенной конструкции (рис. 1) экранирующая перегородка выполнена из нержавеющей стали, и находится в воздушном зазоре между статором и первым ротором. При этом первый ротор функционирует в агрессивной
472
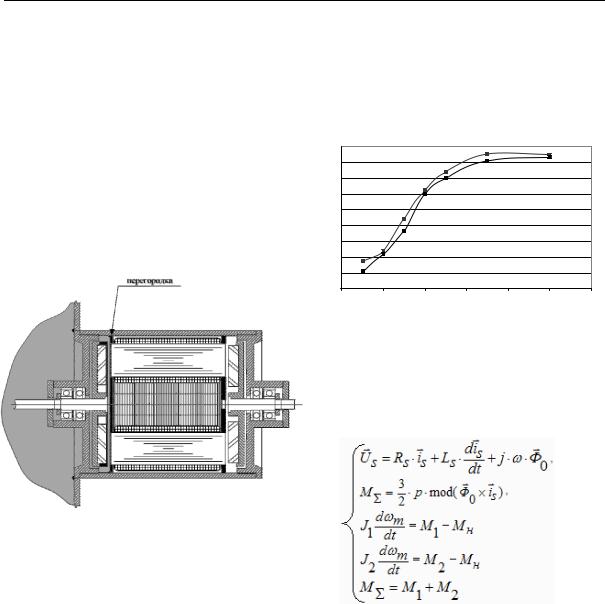
Современные техника и технологии 2007
среде и имеет магнитную связь не только с магнитным полем статора, но и со вторым ротором машины.
Очевидным преимуществом такой конструкции является ее абсолютная герметичность за счет отсутствия механической связи между роторами. При этом в образовании электромагнитного момента участвуют оба ротора, на которых установлены полюсы выполненные из редкоземельных постоянных магнитов. Основная часть машины находиться вне зоны технологического процесса, что способствует увеличению надежности функционирования оборудования и повышению срока службы электропривода, а также улучшению охлаждения и доступности при проведении планового ремонта.
Рис. 1. Конструкция герметичной синхронной машины дискового типа: 1) ротор 1; 2) немагнитный экран; 3) стержень статора; 4) ротор 2
Существенным отличием является только то, что за счет отсутствия прямой связи между дисками, при пуске один из роторов, не имеющий нагрузки на валу, сдвигается относительно второго ротора на некоторый угол, тем самым обеспечивая более синусоидальное распределение МДС в воздушном зазоре электрической машины и снижение «зубцового эффекта».
Все это даёт преимущество не только в распределении МДС, но и в плавности движения ротора. На предварительном этапе был выполнен ряд экспериментальных и теоретических исследований, электрической машины такого типа, направленных на определение наиболее эффективных режимов работы двигателя, а так же исследование энергетических возможностей, таких как, мощность, КПД, момент на валу.
При сравнении экспериментальных характеристик с результатами теоретических исследований, получены приемлемые значения погрешности расчета (не более 10%),
подтверждающие высокую точность описания электромагнитных процессов методом интегрирования по источникам поля.
В результате проведения ряда экспериментальных исследований по определению КПД и момента наиболее оптимальным диапазоном работы двигателя являются пределы от 400 до 1000 об/мин.
90 |
|
|
|
|
|
|
80 |
|
|
|
|
|
|
70 |
|
|
|
|
|
|
60 |
|
|
|
|
|
|
%50 |
|
|
|
|
|
|
КПД40 |
|
|
|
|
|
|
30 |
|
|
|
|
|
|
20 |
|
|
|
|
|
|
10 |
|
|
|
|
|
|
0 |
|
|
|
|
|
|
0 |
200 |
400 |
600 |
800 |
1000 |
1200 |
|
|
|
Об/мин |
|
|
|
Рис. 2. Эффективность преобразования энергии при установке герметизирующего экрана Для моделирования синхронного герметичного привода, с целью проверки пригодности разработанной системы для возможной эксплуатации на СХК, был использован прикладной пакет Matlab с комплектом имитаци-
онного моделирования Simulink.
где J – момент инерции первого либо второго ротора. При этом момент инерции первого ротора отличается от момента инерции второго ротора на величину момента инерции механизма. В расчетах принимались типовые величины присущие реальным устройствам, которые желательно герметизировать.
При выводе уравнений, описывающих поведение синхронной машины, сделаны следующие общепринятые допущения:
считается, что машина симметричная с идеальными обмотками, обеспечивающими синусоидальное распределение магнитодвижущей силы и магнитного потока вдоль воздушного зазора, который принимается одинаковым по окружности ротора,
не учитывается влияние насыщения магнитной цепи, что позволяет принять значения индуктивностей постоянными,
не учитываются потери энергии в стали ротора,
473
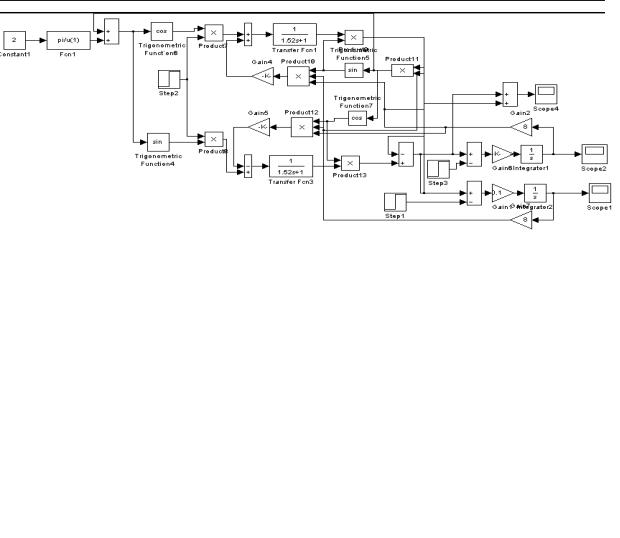
XIII Международная научно-практическая конференция «СОВРЕМЕННЫЕ ТЕХНИКА И ТЕХНОЛОГИИ»
предполагается, что отсутствуют напряжения и токи нулевой последовательности, т.е. мгновенные значения напряжений и токов фаз: aA+uB+uС=0; iA+iB+iС=O.
Теоретические исследования отразили границы устойчивой работы двигателя при
питании от преобразователя частоты и также показали возможность рассогласования скоростей роторов при высоких скоростях работы машины.
Рис. 3. Модель синхронной машины с двумя роторами в неподвижной системе координат
В |
результате |
выполнения |
ряда |
2. |
Электроприводы регулирующих орга- |
|||
экспериментальных |
и |
теоретических |
нов энергетических реакторов: Основы проек- |
|||||
исследований |
по |
определению |
КПД, |
тирования / Г.П. Юркевич. и др. – М.: Энерго- |
||||
мощности и момента были получены |
атомиздат, 1985. – 240 с. |
|||||||
наилучшие |
режимы |
работы |
герметичного |
3. |
Муравлев О.П., Леонов С.В., Калаев |
|||
двигателя |
с |
двумя |
магнитосвязанными |
В.Е., Федянин А.Л., Лялин А.В. Исследование |
||||
роторами. |
|
|
|
|
|
герметичной синхронной машины дискового |
||
ЛИТЕРАТУРА: |
|
|
|
типа // Изв. вузов. Электромеханика. – 2006. – |
||||
1. Генкин А.Э. Оборудование химиче- |
№3. – С. 23–25. |
|||||||
ских заводов. – М.: Высшая школа, 1986. – |
|
|
||||||
280 с. |
|
|
|
|
|
|
|
|
СУЩЕСТВУЮЩИЕ МЕТОДЫ РАСЧЕТОВ РЕЖИМОВ ЭКСТРУЗИИ И ВУЛКАНИЗАЦИИ НА АНВ И ЛКНВ
Флеминг И.В.
Томский Политехнический университет, Россия, г. Томск, пр. Ленина 30. E-mail: flash2000/@pochtamt.ru
Процессы экструзии и вулканизации являются одними из самых важных при изготовлении кабелей с резиновой изоляцией и оболочкой. Такие отрасли промышленности, как добывающая, металлургическая, химическая используют кабели с резиновой изоляцией, исходя из условий эксплуатации.
Расчет процесса вулканизации.
Кабели и провода после наложения изоляции или оболочки из резиновых смесей подвергаются вулканизации.
Процесс вулканизации состоит в нагреве резиновой смеси до температуры, при которой вулканизующийся агент вступает в реакцию с каучуком. Вследствие чего макромолекулы каучука связываются между собой силами главных валентностей с образованием единой пространственной структуры, характер которой и обуславливает физикохимические и механические свойства вулканизатов. В процессе вулканизации возникают также силы межмолекулярного взаимодейст-
474

Современные техника и технологии 2007
вия, которые также влияют на механические свойства вулканизата [4].
Для получения качественного изделия необходимы точные и быстрые методы определения скорости вулканизации.
Скорость присоединения серы к каучуку можно определить:
К = |
|
1 |
ln |
Sобщ |
|
τ |
Sобщ − Scвяз |
||||
|
|
K- постоянная для данной резиновой смеси и данных условий вулканизации;
τ - продолжительность вулканизации;
Sобщ |
- общее содержание серы в |
резиновой смеси от веса каучука;
Sсвяз - количество связанной серы, %[4];
Но скорость присоединения серы к каучуку не может точно определить скорость вулканизации, поскольку число атомов серы, присоединяющееся на одну поперечную связь, и количество серы, которое присоединяется к каучуку различными другими путями непостоянно, кроме этого анализ занимает много времени, а значит дорог [3].
Важным параметром процесса вулканизации является эффект вулканизации, который определяет количественную степень вулканизации.
E = Jτ , усл ед
J – скорость вулканизации; τ - время вулканизации.
Для резиновых смесей, свулканизованных в одинаковой степени, эффекты вулканизации равны. Чтобы получить одинаковую степень вулканизации при разных температурах, а, следовательно, и разных скоростях J1 и J2, следует так подобрать времена вулканизации τ1 и τ2 , чтобы соблюдалось условие:
J1τ1 = J2τ2
Наиболее просто эффект вулканизации вычисляется графически.
Оптимальное время вулканизации резиновой смеси можно определить и в лабораторных условиях путем вулканизации нескольких образцов в гидравлическом прессе при различном времени. Далее на разрывных машинах определяют прочность на разрыв этих пластин и выявляют оптимум вулканизации. Располагая такими сведениями, рассчитывают время вулканизации при рабочем давлении пара АНВ. Для этого пользуются данными зависимости температуры насыщенного пара от давления и коэффициентами скорости вулканизации[2].
Данный метод широко применяется, но необходимо вулканизировать большое количество образцов, что приводит к расходу ма-
териала и времени, а значит и увеличению стоимости.
Также в лабораторных условиях скорость вулканизации можно определить с помощью приборов типа вискозиметра Муни. Каждый из них измеряет определенное свойство периодически непрерывно во время вулканизации.
Данные методы точнее, по сравнению с измерением прочностных свойств чувствительны к небольшим изменениям, влияющим на вулканизационные характеристики [3].
Недостатком лабораторных методов является то, что условия вулканизации резины в прессе и в трубе не одинаковы. Прогрев резины происходит с двух сторон, в то время как прогрев резиновой оболочки или изоляции происходит только с внешней стороны. Кроме того, необходимо учитывать, что часть тепла, получаемое изделием в АНВ, расходуется на нагрев жилы. Вследствие этого, фактическая скорость не достигает расчетной величины (особенно при толщине оболочки больше 2 мм). Плюс к этому необходимо использовать дополнительное оборудование.
Часто для определения времени вулканизации используют температурный коэффициент вулканизации, отношение продолжительности вулканизации при температуре t к продолжительности вулканизации при температуре t+10 0С при условии, что в обоих случаях достигаются одинаковые свойства вулканиза-
тов [4].
Недостатком данного метода является достаточно большая погрешность, которая возрастает с увеличением разницы температур между применяемой температурой и принятой в качестве «основной».
Из-за того, что указанные методы определения оптимального времени (скорости) вулканизации либо дороги, либо неточны, на практике используют материал, в большей степени полученный опытным путем.
Расчет процесса экструзии.
Процесс экструзии резиновой смеси очень сложно просчитать теоретически из-за непредсказуемости резиновых смесей.
Наиболее часто встречается в литературе расчет часовой производительности червячного пресса:
Qч = 60F cosπDсрα niγ10−3 , кг \ ч
i – число заходов нарезки червяка; γ- удельный вес смеси; α - угол винтовой нарезки червяка;
F- площадь поперечного сечения червяка; n- скорость движения червяка, об/мин Dср – средний диаметр червяка, см. [1,5] Данная формула дает максимальную тео-
ретическую производительность червячного пресса. Практически производительность
475
XIII Международная научно-практическая конференция «СОВРЕМЕННЫЕ ТЕХНИКА И ТЕХНОЛОГИИ»
пресса значительно ниже. Это обусловлено наличием противодавления, неполное заполнение нарезки червяка резиновой смесью, а также тем, что имеются окружные и осевые смещения отдельных участков смеси, заполняющей нарезку червяка, вызванные окружными и осевыми усилиями. [1]
Указанные факторы можно учесть коэффициентом, который находиться в пределах
0,1…0,3.
Данный расчет процесса экструзии можно назвать грубым из-за широкого колебания коэффициента. Кроме того, расчет сделан исходя из следующих упрощений:
•расплав резиновой смеси является ньютоновской жидкостью, то есть вязкость не зависит от скорости и напряжения сдвига, а зависит только от температуры;
•скорость сдвига по длине канала червяка одинакова;
•вязкость расплава по высоте нарезки червяка постоянна.
Кроме этого не учитываются некоторые факторы, оказывающие значительное влияние на производительность:
•способ питания экструдера ;
•температура резины, поступающей в загрузочную воронку;
•температурные режимы червяка и цилиндра;
•физико-механические свойства резин. Температурный режим цилиндра и масса
резиновой смеси, загружаемой в воронку, пропорционально влияет на производительность червячного пресса. Теоретический расчет температур этих зон экструдера и количества подаваемой резиновой смеси, учитывающий вышеперечисленные факторы, мог бы значительно снизить затраты по следующим причинам:
•снижение расхода резиновой смеси, в результате меньшего разброса толщины оболочки или изоляции;
•рациональное использование энергии на подогрев и охлаждение цилиндра;
•выбор оптимальной скорости опрессования.
Однако на практике температуры зон экструдера выбираются лишь из соображений равномерного подогрева резиновой смеси при пластификации в червячном прессе.
Остальные параметры технологического процесса экструзии на заводах также в большей степени подбираются методом подбора. Что приводит к увеличению нагрузки на технический персонал предприятия, перерасходу материалов и энергии, кроме этого возрастает возможность появления брака.
Делая вывод, можно сказать, что использование расчетов процессов вулканизации и экструзии может значительно повысить производительность и уменьшить стоимость кабеля с резиновой изоляцией и оболочкой.
Надо отметить, что получить такие расчеты крайне нелегко, так как процесс пластификации резины является сложным физикохимическим процессом, который невозможно описать одним уравнением.
Для того, чтобы решить задачу по расчету параметров технологического процесса вулканизации и экструзии на АНВ (ЛКНВ) необходимо провести исследования реологических свойств резиновых смесей и определения коэффициента вулканизации. На основе полученных данных можно разработать методику расчета технологических параметров ЛКНВ. На данный момент разработаны теоретические расчеты, но они используются лишь в учебном процессе[6,7].
ЛИТЕРАТУРА:
1.Леонов В.М. Пешков И.Б. Холодный С.Д. Основы кабельной техники. Учебник для ВУЗов М.: «Академия», 2006.
2.Глупушкин П.М. Саакян А.Е. Кабельные резины.М.-Л.: «Энергия», 1966.
3.Аллигер Г. Сьетун И. Вулканизация эластомеров. М.: «Химия», 1968.
4.Кошелев Ф.Ф.и др. Общая технология резин. Уч. Пособие для ВУЗов.М.: «Химия», 1967.
5.Чудаков П.И. Наложение резиновой изоляции и оболочки на кабели и провода. Уч. Пособие для рабочих и мастеров заводов.
М.: «Энергия», 1966.
6.Татарников А.А. Методическая разработка для расчета с помощью номограмм режимов вулканизации резиновой оболочки кабеля. Томск, 1974.
7.Татарников А.А. Особенности процесса экструзии резиновых смесей. Метод. пособие.М.: ЦНИИТЭ, 1989.
476

Современные техника и технологии 2007
ИСПОЛЬЗОВАНИЕ СИСТЕМ АВТОМАТИЧЕСКОГО РЕГУЛИРОВАНИЯ ДЛЯ ПОВЫШЕНИЯ ЭНЕРГЕТИЧЕСКИХ ПОКАЗАТЕЛЕЙ ВИБРАЦИОННЫХ МАШИН
Цурпал С. В., Глазырин А. С.
Томский политехнический университет, Россия, г. Томск, пр. Ленина, 30
E-mail: GuSMaN204@mail.ru
Вибромашины (ВМ) или машины возврат- но-поступательного движения относятся к классу электромагнитных устройств и, конструктивно, выполнены в виде электромагнита, якорь которого является рабочим органом устройства. Как объект управления, вибромашина, характеризуется звеном первого порядка (электрическая часть) и звеном второго порядка (механическая часть, с амплитудночастотной характеристикой (АЧХ) изображенной на рис. 1), инерционностью магнитной системы можно пренебречь. Входной координатой является амплитуда входного напряжения, выходной – амплитуда колебаний якоря.
Рисунок 1 – АЧХ механической части Основные области применения ВМ: пода-
ча, дозирование сыпучих материалов, перемешивание жидкостей, просеивание и грохочение в строительстве и т. д. Наиболее перспективное применение - разжижение высоковязких нефтепродуктов. Так обработка нефти электромагнитным активатором (вибромашина с якорем – активатором специальной формы) позволяет снизить её вязкость и статическое напряжение сдвига (даже нетекучих нефтей при температурах -450С) на время не менее 40 часов.
Основное назначение систем автоматического управления (САУ), построенных на базе вибромашин – это стабилизация амплитуды колебаний якоря. Исходя из свойств объекта управления (АЧХ), возможны следующие способы регулирования амплитуды колебаний (рис. 2): изменением амплитуды входного напряжения, изменением частоты входного напряжения или изменением и амплитуды и частоты входного напряжения.
Рисунок 2 – Классификация систем автоматизированного управления вибромашинами Наиболее простым способом является способ изменения амплитуды входного напряжения [1]. Обычно этот способ используется при относительно постоянных параметрах нагрузки (масса, коэффициент демпфирования), так как значительное колебание вышеуказанных параметров приведет к значительным снижениям КПД устройства. Обычно в качестве рабочей частоты используется частота промышленной сети, а управление амплитудой колебаний осуществляется
посредством управляемого выпрямителя. Другим способом регулирования ампли-
туды колебаний является регулирование частоты входного напряжения [1, 2, 4, 6]. Как уже отмечалось выше, механическая система имеет второй порядок, а, следовательно, на механических координатах наблюдаются резонансные явления, при которых амплитуда колебаний возрастает в несколько раз. Таким образом, изменяя частоту входного напряжения, можно в широком диапазоне регулировать амплитуду колебаний. Для улучшения динамических свойств система управления может содержать АЧХ механической части, причем дорезонансная часть не совпадает с послерезонансной, поэтому если АЧХ задается участком прямой, необходимо учесть этот факт. Как и для предыдущего случая, данный способ обладает достаточно низким КПД и может использоваться при относительном постоянстве параметров нагрузки и в небольшом диапазоне регулирования.
При одновременном (совмещенном) регулировании частоты и амплитуды входного напряжения [3, 5], можно добиться как максимального КПД устройства, так и максимальной выходной мощности в широком диапазо-
477

XIII Международная научно-практическая конференция «СОВРЕМЕННЫЕ ТЕХНИКА И ТЕХНОЛОГИИ»
не изменения параметров нагрузки. Одно- |
Принцип работы САУ следующий: каналы |
|||
временное |
регулирование двух координат |
регулирования частоты (2) и регулирования |
||
позволяет |
получить высокие динамические |
выходной мощности (1) работают поочеред- |
||
показатели, но подобные системы сложны, и |
но, начиная с (2). Взаимоисключение каналов |
|||
крайне неустойчивы к резким изменениям |
происходит |
благодаря |
синхронизирующим |
|
параметров нагрузки и аварийным ситуациям, |
связям, показанным полужирным. Так связь |
|||
а вид переходных процессов трудно предска- |
из блока стабилизации тока катушек в блок |
|||
зуем и может быть несовместим с технологи- |
выбора направления по частоте блокирует |
|||
ческим процессом, что значительно затруд- |
поиск резонансной частоты до завершения |
|||
няет их использование в автоматических сис- |
переходных |
процессов в |
электромагнитном |
|
темах. |
|
контуре, а связь из детектора колебаний час- |
||
В отличие от совмещенного регулирова- |
тоты в блок стабилизации зазора и защит |
|||
ния координат, системы с поочередным |
блокирует увеличение амплитуды колебаний |
|||
управлением гораздо более устойчивы, но |
до завершения поиска резонансной частоты. |
|||
обладают низкими динамическими показате- |
На блок стабилизации зазора также возлага- |
|||
лями, сохраняя при этом высокие энергетиче- |
ются функции недопущения и обработки ава- |
|||
ские показатели. Так как динамика не самый |
рийных ситуаций. В случае превышения на- |
|||
важный параметр для электромагнитных ак- |
пряжением (UKC), током (IK) или зазором (вос- |
|||
тиваторов, то наиболее предпочтительны |
становленным по значению с датчика ускоре- |
|||
САУ с поочередным регулированием коорди- |
ния и значением текущей частоты) предель- |
|||
нат. |
|
ных значений, снижается задание на дейст- |
||
Предлагаем САУ с поочередным управ- |
вующий ток катушек и происходит переклю- |
|||
лением координатами, направленную в пер- |
чение на канал регулирования частоты. Что- |
|||
вую очередь на использование с электромаг- |
бы исключить колебания амплитуды якоря |
|||
нитными активаторами. Основные возможно- |
возле пороговых значений, вводятся зоны |
|||
сти САУ: настройка на резонансную частоту |
нечувствительности для каждой из выше ука- |
|||
(максимальный КПД), настройка на предель- |
занных величин. Колебания амплитуды якоря |
|||
ную амплитуду колебаний (максимальная |
вызваны в первую очередь изменением час- |
|||
мощность), поддержание высоких энергети- |
тоты, так как после настройки на максималь- |
|||
ческих показателей при медленно изменяю- |
ную амплитуду колебаний, этот канал практи- |
|||
щихся параметрах нагрузки и перенастройка |
чески не используется и система находится в |
|||
после резких изменений. Микропроцессорная |
режиме постоянной подстройки резонансной |
|||
реализация (TMS320F2812) системы позво- |
частоты. Для обеспечения максимального |
|||
ляет использовать один микроконтроллер для |
КПД необходимо чтобы, ток через катушки |
|||
управления до 4 устройств, а также подклю- |
протекал ровно полпериода, поэтому форма |
|||
чение САУ к системе управления верхнего |
тока формируется принудительно (релейным |
|||
уровня. |
|
способом), используя значения текущей ам- |
||
Функциональная схема устройства приве- |
плитуды и частоты тока катушек. |
|||
дена на рис. 3, где АИН – автономный инвер- |
На рис. 4 приведены временные зависи- |
|||
тор напряжения, VTПЧ – управляющий вход |
мости координат, поясняющие работу устрой- |
|||
АИН, iK – ток катушек ВМ, UKC – напряжение |
ства: верхняя зависимость – частота, нижняя |
|||
на катушках, ДУ – датчик ускорения, закреп- |
– зазор. |
|
|
ленный на якоре ВМ.
|
Рисунок 4 – Временные зависимости коорди- |
|
нат |
|
Из зависимостей видны: этап настройки |
|
на резонанс (до 12 секунд), этап выбора пре- |
Рисунок 3 – Функциональная схема САУ |
дельного минимального зазора (до 50 се- |
кунд), остальное время ведется подстройка |
478

|
|
|
Современные техника и технологии 2007 |
на резонансную частоту и предельный мини- |
отрасли позволяет повысить производитель- |
||
мальный зазор. |
ность добычи и транспортировки нефти. |
||
|
Таким образом, разработанный способ |
|
|
поочередного регулирования координат по- |
|
ЛИТЕРАТУРА: |
|
зволяет получить САУ устойчивую во всем |
1. |
Быховский И. И., Попов С. И. Автомати- |
|
диапазоне нагрузок и обеспечивающую высо- |
зация резонансных вибромашин. ЦНИИТЭ, |
||
кие энергетические показатели. Микропро- |
строймаш, 1972. |
||
цессорная реализация позволяет создавать |
2. |
Авторское свидетельство СССР |
|
на базе одного микроконтроллера несколько |
№781780. |
||
САУ с возможностью подключения к системе |
3. |
Авторское свидетельство СССР |
|
верхнего уровня. Согласно рис. 4, система |
№1072013. |
||
управления обладает низкими динамически- |
4. |
Авторское свидетельство СССР |
|
ми свойствами, но с учетом того, что рабочие |
№1137451. |
||
циклы обработки нефти длятся несколько ча- |
5. |
Авторское свидетельство СССР |
|
сов, то время настройки 30-40 секунд пренеб- |
№1348794. |
||
режимо мало. |
6. |
Авторское свидетельство СССР |
|
|
Из всего вышесказанного следует, что ис- |
№1674078. |
|
пользование разработанной САУ в нефтяной |
|
|
ФУНКЦИОНАЛЬНАЯ ДИАГНОСТИКА ЭЛЕКТРИЧЕСКИХ МАШИН НЕЙРОСЕТЕВЫМ МЕТОДОМ
Шевчук В.П., Гусев В.В. Мирнинский политехнический институт (филиал)
Якутского государственного университета 678170, Республика Саха (Якутия) г. Мирный, ул. Тихонова, 5/1
E-mail: SheVP@rambler.ru, chief_chef@rambler.ru, chief-chef@yandex.ru
В настоящее время в горной промышленности страны на многих предприятиях происходит реорганизация процессов управления, и в том числе процесса управления состоянием основных фондов. До 40 % в производственной себестоимости предприятий горной промышленности составляют затраты на ремонт и техническое обслуживание оборудования. Переориентация производства горнодобывающих предприятий на бизнесдеятельность в условиях конкуренции и возрастания значимости ресурсов для собственников предприятий требуют принципиально нового подхода к обеспечению надежности, эффективности и безопасности эксплуатации горных машин. Действующие системы технического обслуживания и ремонта стали одним из критических факторов в обеспечении производительной и экономичной работы горного оборудования[1].
Анализ режимов работы подземных горных машин показывает, что эффективность и эксплуатационная надежность электроприводов агрегата будет определяется величиной и характером внешних нагрузок, динамическими свойствам электропривода как сис-
темы и надежностью его компонентов. Для электродвигателей и всех активных механических элементов электропривода характерен стохастический режим работы, характеризующийся вероятностными характеристиками момента нагрузки на валу, приводящий в результате к поломкам механических элементов из-за интенсивного накопления усталостных повреждений, а также тепловому и вибромеханическому износу изоляции обмоток, выплавлению стержней короткозамкнутого ротора и другим неисправностям.
Практика эксплуатации горнопроходческого комбайна ALPINE AHM105 на руднике «Интернациональный» показала, что большинство отказов работы эл. двигателей приходится на главный привод электродвигателя режущего органа. Выявленные дефекты можно разделить на два типа, а именно механические (разбалансировка ротора, дефекты подшипникового узла, нарушение целостности водяной рубашки охлаждения) и электрические (межвитковые замыкания статорных обмоток, ослабление контактных соединений, обрыв датчиков температуры.).
479
XIII Международная научно-практическая конференция «СОВРЕМЕННЫЕ ТЕХНИКА И ТЕХНОЛОГИИ»
Отказы |
|
электродвигателей |
вызывают |
состояния (потокосцеплений статора, ротора |
||||||||||||||||||||||||||||||||||||||
длительные |
|
|
простои |
|
горно-шахтного |
и цепи намагничивания) математическая |
||||||||||||||||||||||||||||||||||||
оборудования, приводящие к большому |
модель |
|
АД |
|
|
выражается |
|
уравнениями |
||||||||||||||||||||||||||||||||||
материальному ущербу. По этим причинам, |
обобщенной электрической машины [4]. |
|
|
|||||||||||||||||||||||||||||||||||||||
из-за |
тяжелых |
условий |
работы, |
|
|
|
s |
|
d |
s |
|
d |
|
|
|
|
|
|
|
|
|
|
|
|
|
|
|
|
|
|
|
|||||||||||
обусловленных влиянием окружающей среды |
|
|
rα |
+ |
|
Lα |
|
|
|
|
M |
|
|
|
0 |
|
|
|
|
0 |
|
|
|
|
|
|||||||||||||||||
S |
|
dt |
|
dt |
|
|
|
|
|
|
|
|
s |
|
|
|||||||||||||||||||||||||||
|
|
|
|
|
|
|
|
|
|
|
|
|
|
|
|
|
|
|
|
|
|
|
|
|
||||||||||||||||||
в |
подземных |
|
выработках, |
к |
Uα |
|
|
d |
|
|
|
|
|
r |
|
|
d r |
|
|
|
r |
|
|
|
|
|
|
|
|
iα |
|
|
||||||||||
|
|
|
|
|
|
|
|
|
|
|
|
|
|
|
|
|
|
|
|
|
|
|
|
|
|
|
|
|
|
|
|
|
|
|
|
|
|
|
||||
взрывозащищенным |
|
асинхронным |
0 |
|
dt M |
|
|
|
rα + dt Lα |
|
|
|
Lβωr |
|
Mωr |
|
iαr |
|
|
|||||||||||||||||||||||
электродвигателям (АД) |
предъявляются вы- |
|
|
= |
|
|
|
|
|
|
r |
|
|
|
|
|
|
|
r |
|
d |
r |
|
d |
|
|
|
|
|
r |
|
|||||||||||
0 |
|
−Mω |
|
|
|
|
|
|
|
|
|
|
|
|
|
|
|
|
|
iβ |
|
|
||||||||||||||||||||
сокие требования. |
|
|
|
|
|
|
|
|
−L |
ω |
|
|
|
|
r |
|
+ |
|
L |
|
|
|
|
M |
|
|
||||||||||||||||
|
|
|
|
|
|
|
|
|
|
dt |
|
dt |
|
|||||||||||||||||||||||||||||
|
наиболее |
из |
US |
|
|
|
|
r |
|
|
|
α |
|
r |
|
|
|
β |
|
β |
|
|
|
|
s |
|
|
|||||||||||||||
В |
этих |
условиях |
β |
|
|
|
|
|
|
|
|
|
|
|
|
|
|
|
|
|
|
d |
|
|
s |
d s |
|
iβ |
|
|
||||||||||||
перспективным |
методом |
диагностирования |
|
|
|
|
0 |
|
|
|
|
0 |
|
|
|
|
|
|
|
|
|
M |
|
rβ + |
|
|
|
Lβ |
|
|
|
|||||||||||
|
|
|
|
|
|
|
|
|
|
|
|
|
|
|
dt |
|
dt |
|
, (1) |
|||||||||||||||||||||||
|
|
|
|
|
|
|
|
|
|
|
|
|
|
|
|
|
|
|
|
|
|
|
|
|
|
|||||||||||||||||
является |
имитационное |
моделирование, |
|
где iαs , iβs , iαr , iβr , - |
токи в обмотках статора и |
|||||||||||||||||||||||||||||||||||||
реализуемое |
на |
основе |
искусственных |
|
|
|
|
|
|
|
|
|
|
|
|
|
|
|
α |
|
|
|
|
β , |
|
|
|
|
|
|
|
|
|
|
||||||||
нейронных сетей (ИНС). Нейронные сети - это |
ротора |
по |
осям |
|
|
|
|
и |
|
соответственно; |
||||||||||||||||||||||||||||||||
метод имитации процессов и явлений, |
Uαs , Uβs |
- |
напряжения на обмотках статора; |
|||||||||||||||||||||||||||||||||||||||
позволяющих |
|
воспроизводить |
сложные |
ωr - частота вращения ротора; |
|
|
|
|
|
|
|
|
||||||||||||||||||||||||||||||
зависимости. По своей природе нейронные |
rαs , rβs , rαr , rβr |
- |
||||||||||||||||||||||||||||||||||||||||
сети являются нелинейными. Кроме того, во |
активные сопротивления обмоток статора и |
|||||||||||||||||||||||||||||||||||||||||
многих случаях они позволяют преодолеть |
ротора |
по |
осям |
|
|
|
α |
|
и |
|
β , |
соответственно; |
||||||||||||||||||||||||||||||
«проклятие размерности», обусловленное |
Lαs , Lsβ , Lαr , Lrβ |
|
|
|
|
|
|
|
|
|
|
|
|
|
|
|
|
|
|
|
|
|
|
|
||||||||||||||||||
тем, что моделирование нелинейных явлений |
|
|
- |
|
|
|
полные |
индуктивности |
||||||||||||||||||||||||||||||||||
в случае большого числа переменных |
обмоток статора и ротора по осям α |
и β , |
||||||||||||||||||||||||||||||||||||||||
требует |
|
|
огромного |
количества |
||||||||||||||||||||||||||||||||||||||
вычислительных |
ресурсов. |
Специфичность |
соответственно. |
|
|
|
|
Полные |
индуктивности |
|||||||||||||||||||||||||||||||||
информационных |
моделей |
проявляется не |
определяются |
|
|
|
|
|
|
|
суммой |
|
|
|
|
|
взаимной |
|||||||||||||||||||||||||
только в способах их синтеза, но и характере |
индуктивности M и индуктивности рассеяния |
|||||||||||||||||||||||||||||||||||||||||
делаемых приближений (и связанных с ними |
Lσ . |
|
|
|
|
|
|
|
|
|
|
|
|
|
|
|
|
|
|
|
|
|
|
|
|
|
|
|
|
|
|
|
|
|||||||||
ошибок). Отличия в поведении системы и ее |
|
Для |
|
математического |
моделирования |
|||||||||||||||||||||||||||||||||||||
информационной |
модели |
возникают |
|
|
||||||||||||||||||||||||||||||||||||||
электродвигателя в переходных режимах ра- |
||||||||||||||||||||||||||||||||||||||||||
вследствие |
|
свойств |
экспериментальных |
боты систему уравнений (1) необходимо до- |
||||||||||||||||||||||||||||||||||||||
данных [2]. |
|
|
|
|
|
|
|
|
полнить уравнением движения ротора: |
|
|
|
||||||||||||||||||||||||||||||
При |
для |
разработки |
мониторинговых |
|
|
|
||||||||||||||||||||||||||||||||||||
систем диагностики и защиты агрегатов с |
|
|
|
|
d |
ωr |
= |
p |
|
(Mвр |
− Mc ) |
|
|
|
|
|
|
|
|
|
|
|
|
|||||||||||||||||||
электрическими |
машинами требуется |
иметь |
|
|
|
|
|
|
|
|
|
|
|
|
|
|
|
|
|
|||||||||||||||||||||||
|
|
|
dt |
J |
|
|
|
|
|
|
|
|
|
|
|
|
||||||||||||||||||||||||||
математические |
|
алгоритмы, |
адекватно |
|
|
|
|
|
|
|
|
|
|
|
|
|
|
|
|
, |
|
|
|
|
|
|
J |
(2) |
|
|
||||||||||||
отражающие |
отклонения |
контролируемых |
|
где |
p — число пар полюсов; |
|
|
- момент |
||||||||||||||||||||||||||||||||||
параметров от допустимых, знать причину их |
инерции ротора; |
|
|
M |
c |
|
- |
момент нагрузки на |
||||||||||||||||||||||||||||||||||
появления |
и |
определить |
минимальный |
|
|
|
|
|
|
|
|
|
|
|
|
|
|
|
|
|
|
|
|
|
|
|
|
|
|
|
|
|
M вр |
|
||||||||
перечень |
|
входных |
сигналов |
|
после |
валу или момент сопротивления; |
|
- |
||||||||||||||||||||||||||||||||||
предварительной |
обработки |
|
для |
электромагнитный |
|
|
|
|
вращающий |
|
|
момент, |
||||||||||||||||||||||||||||||
дальнейшего принятия решений[3]. |
|
|
определяемый |
|
|
|
|
|
взаимодействием |
|
токов |
|||||||||||||||||||||||||||||||
Для качественного моделирования и по- |
|
|
|
|
|
|
||||||||||||||||||||||||||||||||||||
обмоток статора и ротора |
|
|
|
|
|
|
|
|
|
|
|
|||||||||||||||||||||||||||||||
следующей эффективной работы ИНС необ- |
|
|
Mвр |
= m M (iβs iαr −iαs iβr ) |
|
|
|
|
|
|
|
|
|
|
|
|||||||||||||||||||||||||||
ходим большой объем измерительной ин- |
|
|
|
|
|
|
|
|
|
|
|
|
|
|||||||||||||||||||||||||||||
формации от объекта исследовании от объ- |
|
|
|
|
|
|
|
2 |
|
|
|
|
|
|
|
|
|
|
|
|
, |
|
|
|
|
|
|
|
(3) |
|
|
|||||||||||
екта исследования. Информацию о физиче- |
|
где m - число фаз. |
|
|
|
|
|
|
|
|
|
|
|
|
|
|
||||||||||||||||||||||||||
ских процессах в двигателе необходимо |
|
Таким образом, значение параметров |
||||||||||||||||||||||||||||||||||||||||
представить виде двух переменных состав- |
электрических машин |
|
|
в начальный момент |
||||||||||||||||||||||||||||||||||||||
ляющих: |
|
|
|
|
|
|
|
|
времени, |
|
работа |
|
в |
|
|
режиме |
|
ХХ, |
и |
•Значение токов, напряжений, и динамическом режиме работы будут являться
времени пуска в начальный момент пуска;
• Значение непрерывно измеряемых фазных токов и напряжений обмотки статора, а при работе АД со статической нагрузкой требуется также датчик частоты вращения ротора.
Для определения параметров (активных сопротивлений и индуктивностей рассеяния статора и ротора) и компонента вектора
выборкой дынных в цепи диагностических моделей. Прогнозирование изменения значений этих параметров и сравнение их с критическим значением позволит определить момент возникновения аварийной ситуации. На рис.1 представлена диаграмма процессов численного эксперимента имитационного моделирования работы АД.
480

Современные техника и технологии 2007
Рис.1. Диаграмма процессов численного эксперимента предназначенного для исследования эффективности нейросетевых методов прогноза показателей АД
Важно отметить, что вся информация, |
|
|
|
|
|||
которую сеть имеет о задаче, содержится в |
ЛИТЕРАТУРА: |
|
|
||||
наборе примеров. Поэтому качество обучения |
1. |
Козярук А.Е. Проблемы и задачи по- |
|||||
сети напрямую зависит от количества примеров |
вышения эффективности горного оборудова- |
||||||
в обучающей выборке, а также от того, |
ния средствами электропривода и автомати- |
||||||
насколько полно эти примеры описывают |
ки. // Горное оборудование и электромехани- |
||||||
данную задачу. Обученная нейронная сеть |
ка 2005, №5 |
|
|
||||
эл.машины способна устойчиво распозна- |
2. |
Проказов С.А. Нейросетевые методы |
|||||
вать как одиночные, так и кратные |
и программное обеспечение для решения за- |
||||||
дефекты |
в условиях |
зашумленности |
дач нефтепромысловой геологии. Авторефе- |
||||
значений прямых показателей. |
|
рат диссертации. Томск, 2003 |
|
||||
Всё вышеизложенное позволяет считать, |
3. |
Ветров В.И., Ерушин В.П., Тимофеев |
|||||
что исследования в области нейросетевых |
И.П. Электромеханические преобразоварели, |
||||||
методов |
моделирования |
процессов |
диагностика и защита: Новосибиск: Изд-во |
||||
диагностирования работы |
электрических |
НГТУ, 2000. |
|
|
|||
машин, а также разработка нейроимитаторов, |
4. |
Копылов |
И.П. |
Математическое |
|||
являются |
актуальными |
и |
представляют |
моделирование электрических машин. М.: |
|||
теоретический и практический интерес. |
Высшая школа,1994. |
|
|
ДИАГНОСТИЧЕСКИЕ ПРИЗНАКИ ДЕФЕКТОВ ПОДШИПНИКОВЫХ УЗЛОВ
Шевчук В.П.
Мирнинский политехнический институт (филиал)
Якутского государственного университета 678170, Республика Саха (Якутия) г. Мирный, ул. Тихонова, 5/1;
E-mail: SheVP@rambler.ru, chief_chef@rambler.ru, chief-chef@yandex.ru
Проведенные исследования условий эксплуатации электрических машин средней мощности, а также крупных электрических машин переменного тока, анализ факторов, определяющих уровень надежности их подшипниковых узлов, а также данные ряда информационных источников [1, 2, 3, 4, 6, 7] показывают, что одним из основных источников вибрации механического происхождения электрической машины
являются дефекты изготовления, сборки и износа элементов подшипниковых узлов.
Практически все дефекты изготовления подшипников качения, такие, как овальность и гранность дорожек качения, разномерность тел качения, отклонение их форм от расчетных, оказывают непосредственное влияние на уровень низкочастотной вибрации электрических машин средней мощности, а
481
XIII Международная научно-практическая конференция «СОВРЕМЕННЫЕ ТЕХНИКА И ТЕХНОЛОГИИ»
также |
крупных |
электрических |
машин |
достигает уровня аналогичных дефектов |
переменного тока. |
|
|
изготовления элементов подшипниковых |
Кдефектам изготовления и сборки узлов.
подшипниковых узлов |
|
электрических машин |
|
Коррозия приводит к появлению дефектов |
||||||||||
переменного тока относятся овальность и |
поверхностей качения и сепаратора. Ее |
|||||||||||||
гранность посадочных мест вала ротора, |
появление связано с воздействием на металл |
|||||||||||||
перекос внутреннего и наружного колец |
агрессивных |
жидкостей |
и |
агрессивной |
||||||||||
подшипника, появление радиального натяга в |
окружающей среды. Признаками коррозии |
|||||||||||||
подшипнике, перекос соединительных муфт. |
являются наличие коричневатых пятен на |
|||||||||||||
При посадке подшипника на вал с натягом его |
элементах |
подшипникового |
узла |
и |
||||||||||
внутреннее |
кольцо |
|
повторяет |
|
форму |
увеличение |
|
уровней |
низкочастотных |
|||||
посадочного места. В этом случае разделить |
составляющих |
|
вибрации |
электрической |
||||||||||
дефекты изготовления подшипников (их |
машины. Выражения (1 – 4) могут быть |
|||||||||||||
внутренних колец) и дефекты изготовления |
использованы для определения как основных, |
|||||||||||||
посадочных |
мест |
|
не |
представляется |
так и кратных им частот спектральных |
|||||||||
возможным, так как они оказывают |
составляющих |
|
вибрации |
электрических |
||||||||||
совместное |
воздействие |
на |
вибрацию |
машин средней мощности, а также крупных |
||||||||||
электрической машины. |
|
|
|
|
электрических машин переменного тока, на |
|||||||||
Радиальный натяг в подшипниках из-за |
которых |
проявляются износовые дефекты |
||||||||||||
неточности |
изготовления |
посадочных мест |
подшипниковых |
узлов. |
|
Основным |
||||||||
оказывает |
влияние |
|
на |
низкочастотную |
диагностическим признаком, по которому |
|||||||||
вибрацию. Так, чрезмерный натяг вызывает |
возможно отличить низкочастотную вибрацию |
|||||||||||||
увеличение |
диаметра |
внутреннего |
кольца |
подшипника с дефектами износа от вибрации |
||||||||||
подшипника, что, в свою очередь, влечет за |
с |
дефектами |
изготовления, |
является |
||||||||||
собой уменьшение |
|
радиального |
зазора |
увеличение |
|
уровней |
спектральных |
|||||||
подшипника. При этом увеличивается число |
составляющих |
|
вибраций |
электрических |
||||||||||
шариков, находящихся одновременно в |
машин переменного тока на основных и |
|||||||||||||
состоянии контакта с обоими кольцами |
кратных им частотах в процессе развития |
|||||||||||||
подшипника. |
На |
вибрацию |
начинают |
дефектов. Для обнаружения и оценки |
||||||||||
сказываться дефекты наружного кольца. |
износовых дефектов подшипников - износа |
|||||||||||||
Перекос колец подшипника приводит к |
поверхностей качения и сепаратора, вмятин, |
|||||||||||||
перераспределению нагрузки на тела качения |
трещин, |
раковин и сколов |
на |
дорожках |
и |
–наиболее нагруженными из них телах качения (за исключением изменения
оказываются |
находящиеся |
в |
двух |
режима |
|
|
|
трения) |
|
|
|
– |
наибольшей |
||||||||||||||||||
противоположных точках кольца. При переко- |
эффективностью |
|
|
|
|
|
|
|
обладает |
|
|
метод |
|||||||||||||||||||
се наружного кольца подшипника растет |
спектрального |
|
|
|
|
|
|
|
|
анализа |
|
огибающей |
|||||||||||||||||||
уровень вибрации на четных гармониках |
высокочастотных |
|
|
|
|
составляющих |
сигнала |
||||||||||||||||||||||||
частоты fн, внутреннего кольца – на |
вибрации, |
|
|
|
|
создаваемой |
|
ударными |
|||||||||||||||||||||||
удвоенной частоте вращения ротора 2 fr. |
|
импульсами [2, 8]. |
|
|
|
|
|
|
|
(1) |
|
||||||||||||||||||||
Опыт эксплуатации электрических машин |
|
|
|
|
|
fr |
|
|
|
|
|
dт.к. cosα |
|
|
|||||||||||||||||
средней |
мощности, а |
также |
крупных |
|
|
fc |
= |
|
|
|
|
|
|
|
|
|
|
|
|
|
|
|
|
|
|
|
|
||||
|
|
|
|
|
|
|
|
|
|
|
|
|
|
|
|
|
|
|
|||||||||||||
|
|
2 |
1 − |
|
|
|
|
dс |
|
|
, |
|
|
|
|
||||||||||||||||
электрических |
машин |
переменного |
тока |
|
|
|
|
|
|
|
|
|
|
|
|
|
|
|
|
|
|
|
|
|
|||||||
|
|
|
|
|
|
|
|
|
|
dс |
|
|
|
|
|
|
|
|
|
|
|||||||||||
показывает, |
что |
|
большинство |
|
|
|
|
|
|
|
|
|
|
|
|
|
|
|
(2) |
|
|||||||||||
|
|
|
|
|
|
|
|
|
fm.к. = |
|
|
|
|
|
|
|
|
|
|
|
|
|
|
|
|
|
|
||||
|
|
|
|
|
|
|
|
|
|
|
|
|
|
|
|
|
|
|
|
|
|
|
|
||||||||
преждевременных отказов |
подшипниковых |
|
|
fc |
|
|
|
|
|
+cosα , |
|
|
|
|
|||||||||||||||||
|
|
|
|
|
|
|
|
dт.к. |
|
|
|
|
|
|
|
|
|
|
|||||||||||||
узлов обусловлено их перегрузкой, износом, |
|
|
|
|
|
|
|
|
|
|
|
|
|
|
|
|
|
dт.к. cos α |
|
|
|
|
|||||||||
коррозией, |
неудовлетворительной |
смазкой, |
|
|
|
|
|
|
|
|
|
|
|
|
|
|
|
|
|
|
(3) |
||||||||||
|
|
fн = fс zm.к. = |
|
fr |
|
|
|
|
|
|
|||||||||||||||||||||
|
|
|
|
|
|
|
|
|
|
|
|
1 − |
|
|
|
zm.к. , |
|
||||||||||||||
загрязнениями и перегревом. В конце срока |
|
|
|
|
|
|
|
dc |
|
||||||||||||||||||||||
|
|
|
|
|
|
|
|
|
|
|
2 |
|
|
|
|
|
|
|
|
|
|||||||||||
службы |
при |
усталостных |
отказах |
|
|
= (f |
|
|
|
|
)z |
|
|
|
|
|
|
|
fr |
|
|
dт.к. cosα |
|
|
, (4) |
||||||
подшипников |
происходит |
разрушение |
f |
в |
r |
− f |
|
m.к. |
= |
|
1 |
+ |
z |
m.к. |
|||||||||||||||||
|
|
|
|
||||||||||||||||||||||||||||
дорожек |
качения |
и |
последующее |
|
|
|
|
c |
|
|
|
2 |
|
|
dc |
|
|
|
|||||||||||||
|
|
|
|
|
|
|
|
|
|
|
|
|
|
|
|
|
|
|
|
|
|||||||||||
выкрашивание отдельных частиц металла. |
Каждый из видов дефектов износа на |
||||||||||||||||||||||||||||||
Выкрашивание может происходить как на |
основных и кратных им частотах приводит к |
||||||||||||||||||||||||||||||
внешнем, так и на внутреннем кольце или на |
появлению |
|
|
|
в |
|
|
|
|
|
|
спектре |
|
огибающей |
|||||||||||||||||
телах качения подшипника. Появление |
гармонических составляющих вибраций. По |
||||||||||||||||||||||||||||||
раковин, трещин и сколов на поверхностях |
результатам |
|
анализа |
|
спектра |
огибающей |
|||||||||||||||||||||||||
качения так же, как и дефекты изготовления |
вибрации |
|
|
|
определяются |
парциальные |
|||||||||||||||||||||||||
подшипниковых |
узлов, |
|
отмечается |
в |
глубины амплитудной модуляции случайного |
||||||||||||||||||||||||||
низкочастотном спектре вибрации. Их |
сигнала, |
|
|
являющиеся |
|
диагностическими |
|||||||||||||||||||||||||
проявление становится заметным тогда, |
параметрами, |
|
|
|
|
|
по |
|
|
величине |
|
которых |
|||||||||||||||||||
когда величина |
локального |
дефекта износа |
проводится |
|
|
|
|
|
|
|
|
|
|
оценка |
|
состояния |
482

Современные техника и технологии 2007
подшипникового узла. Для электрических |
повышенной |
вибрации, |
причин |
ее |
|||||||||||||||
машин пороговые значения диагностического |
возникновения. Это, в свою очередь, требует |
||||||||||||||||||
параметра (глубины амплитудной модуляции) |
развития |
методов |
виброакустических |
||||||||||||||||
составляют: момент образования дефекта – |
исследований. |
|
|
|
|
|
|||||||||||||
5%-ная модуляция; предаварийное состояние |
Анализ |
существующих |
методов |
||||||||||||||||
подшипникового узла в результате развития |
технической |
|
|
|
диагностики |
||||||||||||||
дефекта – 20%-ная модуляция [5]. |
|
|
|
электрооборудования, |
в |
том |
числе |
||||||||||||
Существенный вклад в общий уровень |
электрических машин переменного тока и их |
||||||||||||||||||
вибрации |
электрической машины |
вносят |
узлов |
показывает, |
что |
наибольшей |
|||||||||||||
случайные вибрации, создаваемые силами |
универсальностью |
и |
информативностью |
||||||||||||||||
трения |
|
в |
подшипниковых |
узлах |
с |
обладают методы вибрационной диагностики. |
|||||||||||||
подшипниками качения. В подшипниках |
|
|
|
|
|
|
|
|
|||||||||||
|
|
|
|
|
|
|
|
||||||||||||
качения |
силы |
трения |
и |
создаваемая ими |
ЛИТЕРАТУРА: |
|
|
|
|
|
|||||||||
вибрация |
зависят |
от |
сил |
нормального |
|
|
|
|
|
||||||||||
1. |
Бровман Я.С., Демирчан К.С., Шмутер |
||||||||||||||||||
давления на поверхности качения и |
|||||||||||||||||||
С.Л. Диагностика источников вибрации асин- |
|||||||||||||||||||
коэффициента |
трения |
качения |
[2]. |
хронного двигателя // Электротехника. – 1973. |
|||||||||||||||
Создаваемая |
|
ими |
|
вибрация |
|
имеет |
- № 1. |
|
|
|
|
|
|
|
|||||
достаточно сложную зависимость уровня от |
2. |
Вибрация |
и |
вибродиагностика |
|||||||||||||||
скорости |
вращения ротора |
электрической |
|||||||||||||||||
судового электрооборудования / А.А. |
|||||||||||||||||||
машины. Кроме того, уровни случайной |
Александров, А.В. Барков, Н.А. Баркова, В.А. |
||||||||||||||||||
вибрации, создаваемой силами трения каче- |
Шафранский // Качество и надежность. – Л.: |
||||||||||||||||||
ния, в значительной степени определяются |
Судостроение, 1986. – 276 с. |
|
|
|
|||||||||||||||
чистотой |
поверхности |
|
качения, |
скорости |
3. Лазаревский И.А., Шафранский |
В.А. |
|||||||||||||
вращения подшипника, его размеров, |
|||||||||||||||||||
Выбор диагностических параметров электри- |
|||||||||||||||||||
количеством, типом, а также состоянием |
ческих машин //Судостроение. – 1976. - № 10. |
||||||||||||||||||
смазки. Увеличение или уменьшение объема |
– С. 15–16. |
|
|
|
|
|
|
||||||||||||
смазки |
или |
|
ее |
старение |
приводят |
к |
4. |
Михайлов В.И., |
Саверский А.С., Ша- |
||||||||||
увеличению сил трения качения и, |
|||||||||||||||||||
повалов А.Т. Определение вибродиагности- |
|||||||||||||||||||
соответственно, росту уровней спектральных |
ческих |
признаков |
усталостного разрушения |
||||||||||||||||
составляющих вибрации. Загрязнение смазки |
подшипников качения асинхронного двигате- |
||||||||||||||||||
абразивными частицами, продуктами износа |
ля //Тр. ВНИИЭМ. – 1981. – Т. – 68. – С. 102 – |
||||||||||||||||||
поверхностей качения и сепаратора ведет к |
109. |
|
|
|
|
|
|
|
|||||||||||
износу рабочих |
поверхностей |
подшипников, |
5. |
Павлов К.А., Воронкин В.А. |
Выявле- |
||||||||||||||
увеличению |
|
|
их |
|
шероховатости. |
||||||||||||||
|
|
|
ние дефектов подшипниковых узлов электро- |
||||||||||||||||
Рассмотренные дефекты износа – ухудшение |
машин в процессе эксплуатации методами |
||||||||||||||||||
параметров смазки и износ поверхностей |
вибродиагностики // Качество и надежность |
||||||||||||||||||
качения – наибольшее влияние оказывают на |
электрических |
машин |
и |
электро- |
|||||||||||||||
уровни |
спектральных |
|
составляющих |
оборудования: Тр. ВНИИЭМ. – М. – 1986. – Т. |
|||||||||||||||
высокочастотной вибрации на частотах 5-20 |
81. – С. 57 – 6 2. |
|
|
|
|
|
|||||||||||||
кГц [2, |
5]. |
В |
этом |
случае в |
качестве |
|
|
|
|
|
|||||||||
диагностического |
признака |
может |
быть |
6. Чащин Д.И. Система обеспечения на- |
|||||||||||||||
дежности подшипниковых узлов низковольт- |
|||||||||||||||||||
использовано |
|
увеличение |
|
уровня |
ных двигателей: Автореф. дис. канд. техн. |
||||||||||||||
спектральных |
|
|
|
|
составляющих |
наук. – Томск, 1985. – 20 с. |
|
|
|
||||||||||
высокочастотной вибрации. |
|
|
|
|
7. |
Чуб |
Е.Ф. |
Реконструкция |
и |
||||||||||
Борьба с шумом и вибрациями на |
|||||||||||||||||||
эксплуатация опор с подшипниками качения: |
|||||||||||||||||||
промышленных объектах является одной из |
Справочник. – М.: Машиностроение, 1981. – |
||||||||||||||||||
важнейших проблем. Уменьшение вибрации |
365 с. |
|
|
|
|
|
|
|
|||||||||||
необходимо |
для повышения |
надежности |
и |
8. Mc Fadden, Smith J.D. Vibration moni- |
|||||||||||||||
долговечности |
|
электрических |
|
машин |
|||||||||||||||
|
|
toring of rolling element bearings bythe high- |
|||||||||||||||||
переменного тока, сокращения длительности |
frequency resonanse technique-a review. – Tri- |
||||||||||||||||||
и улучшения качества ремонтов. Разработка |
boloqy Jnternational. – 1984, vol. 17. - № 1. – P. |
||||||||||||||||||
эффективных средств для этих целей |
3–10. |
|
|
|
|
|
|
|
|||||||||||
невозможна |
|
без |
|
знания |
источников |
|
|
|
|
|
|
|
|
483

XIII Международная научно-практическая конференция «СОВРЕМЕННЫЕ ТЕХНИКА И ТЕХНОЛОГИИ»
СИСТЕМА МОНИТОРИНГА ИСКРЕНИЯ КОЛЛЕКТОРНО-ЩЕТОЧНОГО УЗЛА ТЯГОВЫХ ЭЛЕКТРОДВИГАТЕЛЕЙ ЭЛЕКТРОВОЗА
Шибаев Д.Е., Осадченко А.А.
Томский политехнический университет, Россия, г. Томск, пр. Ленина, 30.
E-mail: DISSEMBLERSDE@MAIL.RU
В современных условиях развития электровозостроения, увеличения мощностей современных электровозов, остро стоит необходимость мониторинга состояния тяговых электродвигателей (ТЭД) электровоза в процессе эксплуатации. Существующие методы оценки искрения коллекторно-щеточного узла не позволяют проводить мониторинг в условиях эксплуатации на электровозе. На базе кафедры электрических машин и аппаратов ТПУ разработан метод оценки искрения коллекторных машин постоянного тока [1]. Реализация этого метода предложена в качестве измерительного датчика в системе мониторинга искрения. Монтаж этого датчика не предполагает конструктивных изменений кол- лекторно-щеточного узла (КЩУ) ТЭД, надежен в эксплуатации и не требует дополнительного питания. Система мониторинга искрения состоит из измерительного датчика, аналого-цифрового преобразователя, компьютера с установленным программным обеспечением и линий связи.
Измерительными датчиками оснащаются все испытуемые двигатели электровоза, сигнал с которых подается на вход аналогоцифрового преобразователя и дальше на компьютер, где происходит централизованная программная обработка информации о наличии и величине искрения КЩУ двигателей. Программное обеспечение позволяет оценивать уровень искрения в баллах по ГОСТ 18374 в режиме реального времени, а также производить запись информации о состоянии коллекторно-щеточного узла на всем пути следования электровоза.
Для калибровки датчика и проверки правильности показания приборов используется визуальная оценка качества коммутации. Однако, общепринятая в настоящее время система контроля качества коммутации по визуальному наблюдению искрения в соответствии с ГОСТ 183-74 не осуществима, как в процессе эксплуатации машин постоянного тока, так и в условиях испытательной станции. Для наблюдения искрения между щёткой и коллектором разработано устройство визуального наблюдения, состоящее из аналоговой Web-камеры с инфракрасной подсветкой. Фокусировка аналоговой Webкамеры на испытуемый КЩУ производится
при помощи специально изготовленного манипулятора, который позволяет изменять положение Web -камеры в двух плоскостях.
По данным проведённых опытов, как на испытательной станции локомотивного депо Тайга, так и на электровозе 2ЭС5К, показания датчика подтверждены показаниями устройства визуального наблюдения. На рис. 1 показано искрения двигателя НБ-514б, установленного на электровозе 2ЭС5К “Ермак”.
Искрение
В рамках эксплуатационных испытаний электровозов нового поколения 2ЭС5К “Ермак” проводился мониторинг качества коммутации коллекторно-щеточного узла 4-х ТЭД электровоза. Коммутационные испытания проводились в режиме опытной эксплуатации электровоза 2ЭС5К “Ермак” на полигоне Смоляниново - Находка в четном направлении. На этом полигоне реализованы основные режимы работы электровоза: тяга, рекуперативное торможение при различных токовых нагрузках. Результаты испытаний показали удовлетворительную работу двигателей в коммутационном отношении. При реализованных нагрузках двигателей практически отсутствовало видимое искрение даже при токах до 900 А. На рис.2 представлена зависимость коммутационной загруженности 2-х ТЭД от токов.
484