
- •к.т.н., начальник отдела ОНИР СиМУ ЭЛТИ, сопредседатель секции №1
- •д.т.н., профессор, зав. каф. фмпк эфф, председатель секции № 9
- •СЕКЦИЯ 1. ЭЛЕКТРОЭНЕРГЕТИКА
- •АВТОМАТИЗАЦИЯ РАСЧЕТА СТРУКТУРНОЙ НАДЕЖНОСТИ ЭЛЕКТРИЧЕСКИХ СХЕМ
- •ОСОБЕННОСТИ МОДЕЛИРОВАНИЯ ЭЛЕКТРИЧЕСКОГОПОЛЯ В МОРСКОЙ ВОДЕ
- •КАБЕЛЬ ДЛЯ ЭЛЕКТРОПИТАНИЯ ГЕНЕРАТОРОВ НИЗКОТЕМПЕРАТУРНОЙ ПЛАЗМЫ
- •Колпаков В.А., Паранин В.Д., Мокеев Д.А………………...86
- •СПОСОБЫ СЕЛЕКЦИИ КОРОТКИХ ЗАМЫКАНИЙ НА ЛИНИЯХ ЭЛЕКТРОПЕРЕДАЧИ
- •СЕКЦИЯ 2. ПРИБОРОСТРОЕНИЕ
- •ИСПОЛЬЗОВАНИЕ КОМПЬЮТЕРНОГО МОДЕЛИРОВАНИЯ ПРИ ИССЛЕДОВАНИИ СПОСОБА КОМПЕНСАЦИИ ДЕЙСТВИЯ ВИБРАЦИИ НА ГИРОМАЯТНИК
- •РАЗРАБОТКА И ИССЛЕДОВАНИЕ МИКРОМЕХАНИЧЕСКОГО ГИРОСКОПА
- •НОРМИРОВАНИЕ ШИХТОВЫХ МАТЕРИАЛОВ ДЛЯ ПРОИЗВОДСТВА ОТЛИВОК ИЗ АЛЮМИНИЕВЫХ СПЛАВОВ
- •ИНВЕРТОРНЫЙ ИСТОЧНИК ПИТАНИЯ ДЛЯ СВАРКИ МОДУЛИРОВАННЫМ ТОКОМ
- •ИССЛЕДОВАНИЕ ВЛИЯНИЯ ОТКЛОНЕНИЯ КОРПУСА НА ЦИКЛ РАБОТЫ ПНЕВМОГИДРАВЛИЧЕСКОГО УДАРНОГО МЕХАНИЗМА
- •ДИНАМИЧЕСКИЕ ПРОЦЕССЫ В БУРОВОЙ КОЛОННЕ ПРИ ВРАЩАТЕЛЬНО-УДАРНОМ БУРЕНИИ СКВАЖИН МАЛЫХ ДИАМЕТРОВ
- •СЕКЦИЯ 4. ЭЛЕКТРОМЕХАНИКА
- •ВЛИЯНИЕ ДЛИНЫ АСИНХРОННОГО ДВИГАТЕЛЯ НА ЭФФЕКТИВНОСТЬ КРЕПЛЕНИЯ
- •РЕЗУЛЬТАТЫ ЭКСПЕРИМЕНТАЛЬНЫХ ИССЛЕДОВАНИЙ ХАРАКТЕРИСТИК СИНХРОННОГО ГИБРИДНОГО ДВИГАТЕЛЯ
- •РАЗРАБОТКА ЭЛЕКТРОМЕХАНИЧЕСКОГО ПРЕОБРАЗОВАТЕЛЯ С АКТИВНЫМ И РЕАКТИВНЫМ ДИСКАМИ В МАГНИТНОЙ СИСТЕМЕ
- •ПРОГРАММА ВЫЯВЛЕНИЯ ФАКТОРОВ РИСКА РАКА МОЛОЧНОЙ ЖЕЛЕЗЫ С ИСПОЛЬЗОВАНИЕМ МЕТОДА МЕТА-АНАЛИЗА
- •ИССЛЕДОВАНИЕ ВОЗМОЖНОСТИ ИСПОЛЬЗОВАНИЯ МЕТОДА ФОТОМЕТРИРОВАНИЯ КАПЕЛЬНЫХ ПРОБ ДЛЯ ОЦЕНКИ АГРЕГАЦИОННЫХ СВОЙСТВ КЛЕТОК КРОВИ
- •ИСПОЛЬЗОВАНИЕ МИКРОВОЛНОВОЙ РАДИОТЕРМОМЕТРИИ В ДИАГНОСТИКЕ РАКА МОЛОЧНОЙ ЖЕЛЕЗЫ
- •УСТАНОВКА ДЛЯ ОПРЕДЕЛЕНИЯ ГИДРОДИНАМИЧЕСКИХ ХАРАКТЕРИСТИК КЛАПАННЫХ ЗАМЕНИТЕЛЕЙ, КАК ПОКАЗАТЕЛЕЙ КАЧЕСТВА И ПРИГОДНОСТИ ДЛЯ КАРДИОХИРУРГИИ
- •Введение
- •ЭКОНОМИЧНЫЙ И ЭКОНОМНЫЙ УМЗЧ 2×200Вт С БЛОКОМ ПИТАНИЯ
- •Мариненко А.В.
- •Благодарности
- •Компонента
- •МЕТОДИКА ОБРАБОТКИ КАРТИН ИНТЕРФЕРЕНЦИОННЫХ ПОЛОС
- •ЛИТЕРАТУРА:
- •Описание процесса моделирования
- •Вывод
- •Благодарности
- •ИСПОЛЬЗОВАНИЕ КОМПЬЮТЕРНОГО МОДЕЛИРОВАНИЯ ПРИ ИССЛЕДОВАНИИ СПОСОБА КОМПЕНСАЦИИ ДЕЙСТВИЯ ВИБРАЦИИ
- •НА ГИРОМАЯТНИК
- •Перспективы
- •Экспериментальная часть
- •Заключение
- •Рисунок 3. Результаты моделирования работы системы
- •ЛИТЕРАТУРА:
- •СКОРОСТНОЙ ЭФФЕКТ В ВИХРЕТОКОВОМ КОНТРОЛЕ
- •Введение
- •Благодарности
- •ЛИТЕРАТУРА:
- •E-mail: yuyug@npi.tpu.ru
- •Наименование параметра
- •Полоса
- •частот, Гц
- •Результаты и обсуждение
- •ЛИТЕРАТУРА:
- •ЛИТЕРАТУРА:
- •Тогда энергия, переданная упругому элементу, согласно (2) будет равна:
- •ПРОБЛЕМА ИССЛЕДОВАНИЯ ТРЕХЗВЕННЫХ МЕХАНИЗМОВ
- •ЛИТЕРАТУРА:
- •420066, г. Казань, Красносельская ул., 51
- •E-mail: BakirovAR@rambler.ru
- •420066, г. Казань, Красносельская ул., 51
- •E-mail: BakirovAR@rambler.ru
- •Введение
- •Выводы
- •Выводы
- •ОПТИМИЗАЦИЯ РЕЖИМОВ ЭКСПЛУАТАЦИИ УСТАНОВОК ТИПА УЭЦН С ПЧ
- •ЦИФРОВАЯ ЛАБОРАТОРИЯ ЭЛЕКТРОМЕХАНИКА
- •ЭЛЕКТРОМАГНИТНЫЙ МОМЕНТ В ИНДУКЦИОННЫХ ДВИГАТЕЛЯХ
- •Материал и методы исследования
- •Заключение и некоторые перспективы
- •ЛИТЕРАТУРА:

Современные техника и технологии 2007
|
|
|
|
|
|
|
dx =Vdt = |
Ndt . |
|
|
|
|
|
|
|
|
|
|
|
|
|
|
|
|
2 |
|
|
|
|
|
|
|
|
|
|
|
|
|
|
|
|
|
|
|
|
|
|
|
|
|
|
|
|
|
|
|
|
||||||
|
|
|
|
|
|
|
|
|
|
|
|
|
|
|
|
|
|
|
|
|
|
|
|
|
|
|
|
|
|
|
|
|
|
|
|
|
|
|
|
|
|
|
|
|
|
|
|
|
|
|
|
|
|
|
|||||||||
|
|
|
|
|
|
|
C |
|
|
|
|
|
|
W2 |
|
= |
|
CV0 |
W2 |
|
|
, |
|
|
|
|
|
|
|
|
|
|
|
|
|
|
|
|
|
|
|
|
|
|
|
|
|||||||||||||||||
Тогда |
энергия, |
|
|
|
|
|
|
|
|
|
|
δ 2 |
|
|
|
|
|
|
|
|
|
|
|
|
|
|
|
|
|
|
|
|
|
|
|
|
|
|
|
|
|
||||||||||||||||||||||
переданная упругому |
|
|
|
где |
|
|
|
|
|
|
|
|
|
|
|
|
|
|
|
|
|
|
|
|
|
|
|
|
|
|
|
|
|
|
|
|
|
|
|
|
|
|
|
|
|
||||||||||||||||||
телу за время удара t, равна: |
|
|
|
|
|
|
|
|
|
|
|
|
|
|
|
|
|
|
|
|
|
|
|
|
|
|
|
|
|
|
|
|
|
|
|
|
|
|
|
|
|
|
|
|
|
|
|||||||||||||||||
|
|
|
W2 =T∫{(E2,12 |
+2E2,1rt1 +r12t2 )e2r1t +(E2,22 |
+2E2,2r2t +r22t2 )e2r2t |
|
|
||||||||||||||||||||||||||||||||||||||||||||||||||||||||
W = ∫N dx = |
1 |
|
∫t |
|
N 2 dt |
|
|
|
(2) |
|
|
− |
|
||||||||||||||||||||||||||||||||||||||||||||||||||
C |
|
|
|
|
|
||||||||||||||||||||||||||||||||||||||||||||||||||||||||||
|
|
|
|
|
0 |
|
|
|
|
|
|
|
|
|
|
|
0 |
|
|
|
|
|
|
|
|
|
|
|
|
|
|
|
|
|
|
|
|
|
|
|
|
|
|
|
|
|
|
|
|
|
|
|
|
}dt |
|
|
|
|
|
|
|
||
Коэффициент |
|
|
передачи |
энергии |
η |
−2[E2,1E2,2 +(r1E2,2 +r2E2,1)t +r1r2t2 ]e−2εt |
|
|
|
|
|
|
|
|
|||||||||||||||||||||||||||||||||||||||||||||||||
определяем по формуле: |
|
|
|
|
|
|
|
|
E |
|
|
|
= |
3 +δ |
|
|
E −1 |
|
|
|
|
E |
|
|
= |
|
3 −δ |
E −1 |
|
|
|
|
|
|
|
|
|
||||||||||||||||||||||||||
η = W |
|
|
|
|
|
|
|
|
|
|
|
|
|
|
|
|
|
2,1 |
|
|
|
|
|
|
2δ |
|
|
1 |
|
|
|
|
|
|
|
|
|
2,2 |
|
|
|
2δ |
1 |
|
|
|
|
|
|
|
|
|
|
|
|||||||||
|
|
|
|
|
|
|
|
|
|
|
|
|
|
|
|
|
|
|
В результате интегрирования имеем: |
|
|
||||||||||||||||||||||||||||||||||||||||||
|
A0 |
|
|
|
|
|
|
|
|
|
|
|
|
|
|
|
|
|
|
||||||||||||||||||||||||||||||||||||||||||||
|
|
|
|
|
|
|
|
|
|
|
|
|
|
|
|
|
|
|
|
|
|
|
|
|
|
|
2 |
|
|
1 |
|
|
|
|
|
|
{E2,2 i |
|
|
|
|
|
|
|
|
|
|
|
|
|
|
|
|
|
|||||||||
где |
энергия |
|
|
удара |
|
А0 задана |
или |
|
|
|
2ε |
|
|
= ∑ |
|
|
|
|
|
− E2,i + 0,5 − |
|
|
|
|
|
|
|
||||||||||||||||||||||||||||||||||||
|
|
|
|
|
|
W2 |
|
|
|
|
|
|
|
|
|
|
|
|
|||||||||||||||||||||||||||||||||||||||||||||
|
|
|
|
|
|
|
|
|
|
|
|
|
i |
|
|
|
|
|
|
|
|
|
|||||||||||||||||||||||||||||||||||||||||
определяется по формуле А0=mV02/2; |
|
|
|
|
|
|
|
|
|
|
|
|
|
i=1 |
|
1 + (− |
1) |
|
δ |
|
|
|
|
|
|
|
2 −rT +0,5]}−(4) |
|
|||||||||||||||||||||||||||||||||||
V0 – предударная скорость. |
|
|
|
|
|
−e2riT [E2 |
−E |
(2rT +1)+rTT |
|
||||||||||||||||||||||||||||||||||||||||||||||||||||||
|
|
|
|
|
|
|
|
|
|
|
|
|
|
2,i |
|
|
|
2,i |
|
|
|
|
|
i |
|
|
|
|
|
|
|
i |
|
|
i |
|
|
|
|
|
|
|
|
|
|
|
|||||||||||||||||
Из закона сохранения энергии следует: |
|
|
|
−2E |
|
|
E |
+ |
3(1+δ2 )E1 |
|
−2 −δ |
|
+2e−2εT {E |
|
E +[(1−31( |
+δ |
2 )E ) |
/ 2δ] |
|||||||||||||||||||||||||||||||||||||||||||||
|
|
|
|
|
|
|
|
2 |
|
|
|
|
|
|
|
|
|
|
|
|
|
|
0 |
|
|||||||||||||||||||||||||||||||||||||||
|
|
|
|
|
|
|
|
|
|
|
|
|
|
|
|
|
|
|
|
2,1 |
2,2 |
|
|
|
|
δ |
|
|
|
|
|
|
|
|
|
|
|
|
|
|
2,1 |
|
2,2 |
|
|
|
|
|
1 |
|
|||||||||||||
|
|
|
|
|
m |
VOT |
= A −W , |
|
|
|
|
|
|
|
|
|
|
|
|
|
|
|
|
|
|
|
|
|
+εT +0,5) } |
|
|
|
|
|
|
|
|
|
|
|
|
|
|
|
|
||||||||||||||||||
|
|
|
|
|
|
|
|
|
|
|
|
|
|
|
|
|
|
|
|
|
|
|
2 |
|
2 |
|
|
|
|
|
|
|
|
|
|
|
|
|
|
|
|
||||||||||||||||||||||
|
|
|
|
|
|
|
|
|
|
|
|
|
|
|
|
|
|
|
|
|
|
|
|
|
|
|
|
|
|
|
|
|
|
|
|
|
|
|
|
||||||||||||||||||||||||
|
|
|
|
|
|
|
|
2 |
0 |
|
|
|
|
|
|
|
|
(1+2εT)+δ0 (ε T |
|
|
|
|
|
|
|
|
|
|
|
|
|
|
|
|
|
|
|||||||||||||||||||||||||||
|
|
|
|
|
|
|
|
|
|
|
|
|
|
|
|
|
|
|
|
|
|
|
|
|
|
|
|
|
|
|
|
|
|
|
|
|
|
|
|
|
|
|
|
|
|
|
|
|
|
|
|
|
|
|
|
|
|
|
|
|
|
||
где скорость отскока Vот = RV0; |
|
|
|
|
Если удар заканчивается во втором |
|
|
||||||||||||||||||||||||||||||||||||||||||||||||||||||||
R |
– |
коэффициент |
|
восстановления |
|
|
|
|
|
||||||||||||||||||||||||||||||||||||||||||||||||||||||
скорости. |
|
|
|
|
|
|
|
|
|
|
|
|
|
периоде, то в (4) |
|
|
вместо Т надо подставить |
|
|||||||||||||||||||||||||||||||||||||||||||||
Отсюда находим: |
|
|
|
|
|
|
время ударного взаимодействия в этом |
|
|
||||||||||||||||||||||||||||||||||||||||||||||||||||||
R = |
1−η |
|
|
|
|
|
|
|
|
|
|
|
|
периоде t0, которое определяется как |
|
|
|
||||||||||||||||||||||||||||||||||||||||||||||
|
|
|
|
|
|
|
|
|
|
|
|
корень уравнения (3) при N2(t)=0. Для |
|
|
|
||||||||||||||||||||||||||||||||||||||||||||||||
Таким образом, основная проблема |
|
|
|
||||||||||||||||||||||||||||||||||||||||||||||||||||||||||||
третьего периода силу удара (2) |
|
|
|
|
|
|
|
||||||||||||||||||||||||||||||||||||||||||||||||||||||||
заключается в определении энергии, |
представим в виде: |
|
|
|
|
|
|
|
|
|
|
|
|
|
|
|
|
|
|
|
|
||||||||||||||||||||||||||||||||||||||||||
переданной |
|
|
упругому |
|
элементу |
в |
|
|
|
= V0C |
2 |
(− |
1)i+1 (a |
|
|
|
|
2 )erit |
|
|
|
|
3 , |
|
(5) |
|
|||||||||||||||||||||||||||||||||||||
|
|
|
|
N |
|
|
+ в |
r t +δr 2t |
= V0CN |
|
|
||||||||||||||||||||||||||||||||||||||||||||||||||||
результате удара, |
|
по формуле (2). |
|
|
|
3 |
|
|
|
|
|
|
∑ |
|
|
|
|
|
|
|
|
|
|
i |
|
|
|
|
i i |
|
|
|
i |
|
|
|
|
|
|
|
|
|
|
|
|
|
|
||||||||||||||||
|
|
|
|
|
2δ |
2 |
|
|
|
|
|
|
|
|
|
|
|
|
|
|
|
|
|
|
|
|
|
|
|
2δ |
2 |
|
|
|
|
|
|||||||||||||||||||||||||||
В работе |
[2] |
получены |
выражения для |
|
|
|
|
|
|
|
i=1 |
|
|
|
|
|
|
|
|
|
|
|
|
|
|
|
|
|
|
|
|
|
|
|
|
|
|
|
|
|
|
|
|
|
|
||||||||||||||||||
|
|
|
где |
|
|
|
a |
= (3 ±δ )E |
|
− 2E − |
δ0 |
; в1,2 =(3±δ)E1 m1−δ |
|||||||||||||||||||||||||||||||||||||||||||||||||||
определения |
силы удара |
на |
контактной |
|
|
|
|
|
|
2 |
|||||||||||||||||||||||||||||||||||||||||||||||||||||
|
|
|
|
|
|
|
|||||||||||||||||||||||||||||||||||||||||||||||||||||||||
|
|
|
|
|
|
|
|
|
|
1,2 |
|
|
|
|
|
|
|
|
|
|
|
|
|
|
|
|
|
1 |
|
δ |
|
|
|
|
|
|
|
|
|
|
|
|
|
|
|||||||||||||||||||
поверхности в каждом периоде волнового |
|
|
|
|
|
|
|
|
|
|
|
|
(3 +δ )E1 |
|
|
|
|
|
|
|
|
|
|
|
|
|
|
(3 −δ )E1 |
|
|
|
|
|
|
|||||||||||||||||||||||||||||
|
|
|
|
|
|
|
|
|
|
|
|
|
|
|
|
|
|
|
er1T − |
|
−1 + r T er2T |
||||||||||||||||||||||||||||||||||||||||||
взаимодействия. |
Вид |
этих |
выражений |
|
|
|
E |
2 |
|
= |
|
|
− |
1r T |
|||||||||||||||||||||||||||||||||||||||||||||||||
зависит от знака параметра: |
|
|
|
|
|
|
|
|
|
|
|
|
|
2δ |
|
|
|
|
|
|
|
|
1 |
|
|
|
|
|
|
2δ |
|
|
|
|
2 |
|
|
||||||||||||||||||||||||||
|
|
|
|
|
|
|
|
|
|
|
|
|
|
|
|
|
|
|
|
|
|
|
|
|
|
|
|
|
|
|
|
|
|
|
|
|
δ 2 = 1− 4C 2 .
mg0
При δ 2 > 0 это выражение для первого периода имеет вид (2)
|
N1 = |
CV0 (er1t − er2t ) |
, |
|||
|
|
|
||||
|
= −ε(1 mδ ); |
|
δ |
|||
где r |
ε = |
g0 |
. |
|||
1,2 |
|
|
2C |
|||
|
|
|
|
Тогда энергия, переданная упругому элементу, согласно (2) будет равна:
|
|
|
1 |
|
T |
|
|
|
|
|
|
|
2 |
, |
|
|
|
|
|
|
||||
|
|
|
|
|
2 |
|
CV 0 W 1 |
|
|
|
|
|
||||||||||||
W 1 = |
|
|
∫ |
N 1 dt = |
|
|
|
|
|
|
|
|
|
|
|
|
|
|
|
|
||||
C |
|
|
|
δ |
2 |
|
|
|
|
|
|
|
|
|
|
|||||||||
|
|
|
0 |
|
|
|
|
|
|
|
|
|
|
|
|
|
|
|
|
|
||||
где Т=2l/a – период (или приведенный |
||||||||||||||||||||||||
период) колебаний стержня; |
|
|
|
|
||||||||||||||||||||
|
W |
= |
|
(1−e2r1T |
) |
+ |
(1−e2r2T ) |
|
+2(1 |
−e−2εT ) |
/ 2ε |
|||||||||||||
|
|
|
|
|
|
|
|
|||||||||||||||||
|
1 |
|
|
(1−δ) |
|
|
|
|
(1+δ) |
|
|
|
|
|
||||||||||
|
|
|
|
|
|
|
|
|
|
|
|
|
|
|
||||||||||
Для второго периода колебаний (2) |
(3) |
|||||||||||||||||||||||
|
CV0 |
|
3 + δ |
|
|
|
|
r1t |
|
|
3 −δ |
|
|
|
r2t |
|||||||||
N 2(t ) = |
|
|
|
|
|
|
|
E1 −1 + r1t e |
|
|
− |
|
|
|
|
E1 |
−1 |
+ r2t e |
|
|
||||
δ |
|
2δ |
|
|
|
2δ |
|
|||||||||||||||||
|
|
|
|
|
|
|
|
|
|
|
|
|
|
|
|
|
где E1 =er1T −er2T .
После подстановки этого выражения в (2), получим:
Квадрат |
безразмерной |
силы |
представим в виде: |
|
|
|
|
|
|
|
|
|
|
|
|
|
|
|
|
|
2 = g + g |
|
|
|
−2g |
|
|
, |
|
|
|
|
|
|
|
|
|
|
|
|||||||||
|
|
|
|
|
|
|
|
|
|
N |
2 |
|
|
3 |
|
|
|
|
|
|
|
|
|||||||||||||||||||||
|
|
|
|
|
|
|
|
|
|
3 |
|
|
1 |
|
|
|
|
|
|
|
|
|
|
+ d4,i xi4 )exi |
|
||||||||||||||||||
гдеgi = (d0,i + d1,i xi |
|
+ d2,i xi2 |
+ d3,i xi3 |
|
|||||||||||||||||||||||||||||||||||||||
Здесь обозначено: |
|
|
|
|
|
|
|
|
|
|
|
|
|
|
|
|
|
|
|
|
|||||||||||||||||||||||
|
d 0 ,1 |
|
|
|
|
|
|
|
|
a12 |
|
|
|
d1,1 |
|
|
|
|
|
|
|
a1 в1 |
|
|
|
|
|
|
|
|
|||||||||||||
|
|
|
|
|
|
|
|
|
|
|
|
|
|
|
|
|
|
|
|
|
|
|
|
|
|||||||||||||||||||
|
d 0 , 2 |
= |
|
|
|
|
|
a 22 |
|
, |
|
d1,2 |
= |
|
|
|
|
|
|
a |
2 в2 |
|
|
|
|
|
, |
|
|
||||||||||||||
|
d 0 , 3 |
|
|
|
|
|
|
|
|
a1 a 2 |
|
|
|
d1,3 |
|
|
[а1в2 (1 + δ ) |
+ а2 в1 (1 −δ )]/ 2 |
|
|
|
||||||||||||||||||||||
|
|
d |
2,1 |
|
|
|
|
|
|
|
|
|
|
|
|
|
|
|
|
|
|
в |
2 + 2δа |
|
|
|
|
|
|
|
|
|
|
|
|
|
|
||||||
|
|
|
|
|
|
|
|
|
|
|
|
|
|
|
|
|
|
|
|
|
|
|
|
|
|
|
|
|
|
|
|
|
|
||||||||||
|
|
|
|
|
|
|
1 |
|
|
|
|
|
|
|
|
|
1 |
|
|
|
1 |
|
|
|
|
|
|
|
|
|
|
, |
|
|
|||||||||
|
|
d2,2 |
= |
|
|
|
|
|
|
|
|
|
|
|
|
в22 + 2δа2 |
|
|
|
|
|
|
|
|
|
|
|
|
|||||||||||||||
|
|
4 |
|
|
|
|
|
|
|
|
|
|
|
|
|
|
|
|
|
|
|
|
|
|
|
|
|
|
|||||||||||||||
|
|
d |
2,3 |
|
|
|
|
δа (1 +δ )2 +δа |
2 |
(1 −δ )2 + в в |
δ |
0 |
|
|
|
|
|||||||||||||||||||||||||||
|
|
|
|
|
|
|
|
|
1 |
|
|
|
|
|
|
|
|
|
|
|
|
|
|
|
|
|
|
|
1 |
2 |
|
|
|
|
|
||||||||
|
d3,1 |
|
|
|
|
|
|
|
|
|
|
|
|
|
|
|
|
2в |
|
|
|
|
|
|
|
|
|
|
|
|
d4,1 |
|
|
|
|
|
1 |
|
|||||
|
|
|
|
|
|
|
|
|
|
|
|
|
|
|
|
|
|
|
|
|
|
|
|
|
|
|
|
|
|
|
|
|
|
|
|||||||||
|
|
|
|
|
|
|
δ |
|
|
|
|
|
|
|
|
|
1 |
|
|
|
|
|
|
|
|
|
|
, |
|
|
|
δ 2 |
, |
||||||||||
|
d3,2 |
|
= |
|
|
|
|
|
|
|
|
|
|
|
2в2 |
|
|
|
|
|
|
|
|
|
|
|
d |
|
= |
1 |
|||||||||||||
|
d3,3 |
|
|
8 |
|
δ0 [в1 (1+δ )+ в2 |
(1−δ )] |
|
|
d4,34,2 |
|
|
16 |
δ02 |
|
||||||||||||||||||||||||||||
|
|
|
|
|
|
|
|
|
|
|
|
|
|
|
|
r |
|
|
|
|
|
|
|
|
|
|
|
|
|
|
|
|
|
|
|
|
|
|
|
|
|
||
|
|
|
|
|
|
|
|
|
|
|
|
|
|
|
|
|
|
|
|
|
|
|
|
|
|
|
|
|
|
|
|
|
|
|
|
|
|
|
|
|
|||
|
|
|
|
|
|
X = 2t |
|
r1 |
. |
|
|
|
|
|
|
|
|
|
(10) |
|
|
|
|
|
|
|
|||||||||||||||||
|
|
|
|
|
|
|
|
|
|
|
|
|
|
|
|
2 |
|
|
|
|
|
|
|
|
|
|
|
|
|
|
|
|
|
|
|
|
|
|
|
|
|
||
|
|
|
|
|
|
|
|
|
|
|
|
|
|
|
−ε |
|
|
|
|
|
|
|
|
|
|
|
|
|
|
|
|
|
|
|
|
|
|
|
|
|
|||
По формуле (2) теперь получаем: |
|
|
|||||||||||||||||||||||||||||||||||||||||
|
2 ( |
|
|
|
|
W33 ) |
|
= |
CV0 |
|
|
|
|
|
|
|
|
|
|
||||||||||||||||||||||||
W = CV |
W31 + |
W32 − |
W3 |
|
|
|
|
|
|
|
|
||||||||||||||||||||||||||||||||
|
|
|
|
|
|
|
|
|
|
4δ 4 |
|
|
|
|
4δ 4 |
|
|
|
|
|
|
|
|
||||||||||||||||||||
3 |
|
|
|
0 |
|
|
|
|
|
|
|
|
|
|
|
|
|
|
|
|
|
|
|
|
|
|
321
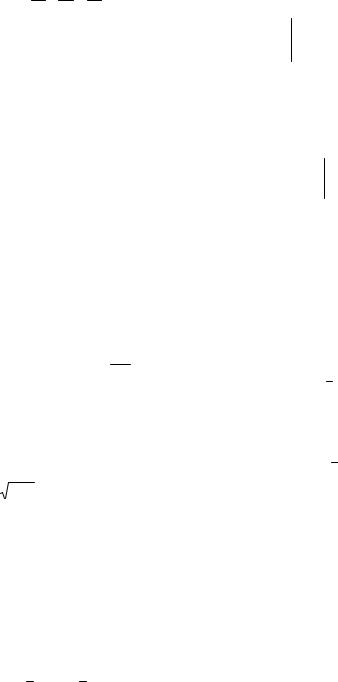
XIII Международная научно-практическая конференция «СОВРЕМЕННЫЕ ТЕХНИКА И ТЕХНОЛОГИИ»
где |
__ |
3i |
= − |
− |
e |
xi |
) |
+ |
xi |
|
|
|
W |
|
{ Di (1 |
|
|
|
|
(d3,i −4d4,i )+d4,i xi3]exi}/2ri |
|||
{[−Di +d0,i +0.5xi (Di −d0,i +d1,i )+xi2 |
Di = d0,i − d1,i + 2d 2,i − 6d3,i + 24d4,i
Если удар заканчивается в третьем периоде, то t = t0, где t0 – корень уравнения
(5) при N3(t) = 0; В противном случае t = T. Аналогично ведется расчет и для последующих периодов. Общая энергия, переданная упругому элементу, определяется суммированием по периодам:
W =CV02 (W1 +W2 +W3 / 4δ2 +...)/δ2
Рассмотрим теперь случай δ 2 < 0. Сила удара в первом периоде определяется выражением (2)
N1 |
= 2V0 |
C |
e |
−εt |
sin εδ1t |
|
(6) |
|
||||||||||||
|
|
|
|
|
|
|||||||||||||||
δ |
1 |
|
|
|
|
|
|
|
|
|
|
|||||||||
|
|
|
|
|
|
|
|
|
|
|
|
|
|
|
|
|
|
|
|
|
гдеδ12 |
= −δ 2 |
= |
|
|
|
4c2 |
|
= δ0 |
−1. |
|
|
|
||||||||
|
mg0 −1 |
|
|
|
||||||||||||||||
|
|
|
|
|
|
|
|
|
|
|
|
|
|
|
|
|
||||
Определим |
|
|
|
энергию, |
переданную |
|
||||||||||||||
упругому элементу в результате удара: |
||||||||||||||||||||
|
4c |
|
T |
|
|
|
|
|
|
|
|
|
4CV02 |
|
|
|
(14) |
|||
|
2 |
−εt |
|
|
|
2 |
|
|
|
|
W1 |
|
|
|||||||
W1 = |
|
V0 |
∫e |
|
|
sin |
|
|
|
εδ1tdt |
= |
|
|
|
|
, |
|
|||
δ 2 |
|
|
|
|
|
|
δ 2 |
|
|
|||||||||||
1 |
|
0 |
|
|
|
|
|
|
|
|
|
|
|
|
1 |
|
|
|
|
|
= |
3E1 |
|
; x = 2U = 2εδ1t . |
|
E |
|
||||
δ1 − |
1 |
||||
|
|
|
Чтобы взять интеграл (2) необходимо предварительно вычислить следующие интегралы ( q = 2εδ1T ):
|
|
Jos |
|
|
q |
−2εt |
|
|
|
sin x |
|
|
δ 2 |
|||
|
|
Joc |
|
|
= ∫e |
|
|
|
|
|
cos x |
dx = |
1 |
|||
|
|
|
|
0 |
|
|
|
|
|
|
|
δ 0 |
||||
|
|
1 |
|
|
− e−2εT |
|
δ1−1 sin q + cos q |
|
|
|||||||
|
|
|
|
|
||||||||||||
|
|
|
|
|
|
|
|
−1 |
|
|
|
|
|
; |
||
|
|
1/ δ1 |
|
|
|
|
|
cos q − sin q |
|
|
||||||
|
|
|
|
|
δ1 |
|
|
|||||||||
Jis |
|
= T∫e−2εt εt |
|
sin x |
|
dt , |
|
|
||||||||
|
|
|
|
|
||||||||||||
|
|
|
|
|
||||||||||||
Joc |
|
|
0 |
|
|
|
|
cos x |
|
|
|
|
|
J1s ={ e−2εT [(δ12 −1)sinq −2δ1 cosq −q(sinq +δ1 cosq)δ0 /δ1 ]+ +2δ1 }/ 4εδ02
J1c = { e−2εT [(δ12 −1)cosq − 2δ1Sinq −q(cosq −δ1Sinq)δ0 /δ1 ]+
+1−δ12 }/ 4εδ02
J 2s |
|
T |
sinx |
dt, |
|
|
|
||
J 2c |
|
= ∫e−2εt ε 2t2 |
cosx |
|
|
0 |
|
||
|
|
|
где
|
|
δ12 |
|
|
|
−2ET |
|
1 |
|
2 |
|
2 |
|
|
|
|
|
|
|
|
|
||||||||
W1 |
= |
|
|
1 |
− e |
1 |
+ |
|
|
sin 2εδ1T + |
|
sin |
|
εδ1T |
4εδ |
|
δ |
|
δ 2 |
|
|||||||||
|
|
0 |
|
|
|
|
1 |
|
|
|
|
|||
|
|
|
|
|
|
|
|
|
1 |
|
|
|
Из выражения (6) следует, что ударное взаимодействие может закончиться в первом периоде до прихода отраженных волн. Найдем продолжительность удара из условия N1=0:
t y = δπ1ε
Если t y <Т, то удар закончится в
первом периоде. Для этого случая:
W1 =CV02 (1−e−2π /δ1 )/ Eδ0 = A0 (1−e−2π /δ1 )
Теперь коэффициент восстановления скорости определяется так:
R = 1−η = e |
−π / δ1 |
|
|
η = 1 |
− e |
−2π / δ1 |
|
|
|
|
|||||||||||||||
|
|
|
|
|
|
|
|
|
|
|
|
|
|||||||||||||
Если |
t y >T, |
|
то необходимо рассмотреть |
||||||||||||||||||||||
второй |
|
период |
ударного |
взаимодействия. |
|||||||||||||||||||||
Для этого случая сила удара определяется |
|||||||||||||||||||||||||
выражением (2) |
|
|
|
|
|
|
|
|
|
|
|
|
|
|
|
|
|||||||||
|
|
|
|
|
ε |
|
|
|
|
|
|
|
|
|
|
|
|
|
|
|
|
|
|
||
|
|
|
|
|
|
|
|
|
|
|
|
|
|
|
|
|
|
|
(7) |
|
|||||
N2 =CVe0 −εt 3 |
|
1 |
sinU +E1 cosU +εt(δ1 cosU −sinU) /δ1 |
|
|||||||||||||||||||||
|
|
||||||||||||||||||||||||
|
|
|
|
|
|
|
|
|
|
|
|
|
|
|
|
|
|
|
|
|
|
|
|
|
|
|
|
|
|
|
δ1 −1 |
|
|
|
|
|
|
|
|
|
|
|
|
|
|
|
|||||
где |
U = εδ |
t; |
|
E =e−εT sinεδT |
|
|
|
|
|
|
|||||||||||||||
|
|
|
|
|
|
|
|
|
1 |
|
|
|
1 |
|
|
|
|
1 |
|
|
|
|
|
|
|
Квадрат силы удара: |
|
|
|
|
|
|
|
|
|
|
|||||||||||||||
N |
2 |
|
|
2 |
e |
−2εt |
{ |
|
|
2 |
+ E |
2 |
|
|
2 |
− E |
2 |
|
|
|
|||||
|
|
|
|
|
|
|
|||||||||||||||||||
2 |
= 4CV |
|
|
E |
|
|
/ 2 − 0,5 E |
|
|
cos x + E E sin x |
|||||||||||||||
|
|
|
0 |
|
|
|
|
|
|
1 |
|
|
|
|
1 |
|
1 |
|
|
+εt[E1δ1 − E + (E1δ1 + E )cos x + (2E1 −δ1 )Sinx]+
+0,5ε2t2 [1+δ12 + (δ12 −1)cos x − 2δ1Sinx] }/δ12
где
J2s = [ |
2δ13 −(q2 + 2δ1q + 2δ12 )(sinq +δ1 cosq)e−2εT +8εδ13 (J1c −δ1J1s )+ |
|||||||||||||||||||||
+ 2δ 2 (J |
oc |
−δ |
J |
os |
) |
]/8εδ2δ |
0 |
|
|
|
|
|||||||||||
1 |
|
|
1 |
|
|
1 |
|
|
|
|
|
|||||||||||
J2c = [ |
2δ13 −(q2 + 2δ1q + 2δ12 )(cos q −δ1 sin q)e−2εT − |
|||||||||||||||||||||
−8εδ13 (J1s −δ1 J1c )− 2δ12 (Jos −δ1 Joc ) ]/ 8εδ12δ0 |
||||||||||||||||||||||
С |
|
|
учетом этого |
энергию, переданную |
||||||||||||||||||
во втором периоде можно записать так: |
||||||||||||||||||||||
|
W 2 = 4 CV 02 |
W 2 |
/ δ 12 |
|
|
|
|
|||||||||||||||
где |
|
1 |
|
(E |
|
|
+ E12 )(1 − e−2εT )+ |
1 |
(E1δ1 − |
|
) |
|||||||||||
|
|
= |
|
|
2 |
|
|
|||||||||||||||
|
W2 |
|
E |
|||||||||||||||||||
|
|
|
|
|
|
|
|
|||||||||||||||
|
|
|
|
|
|
4ε |
|
|
|
|
|
|
|
|
|
4ε |
||||||
|
[1 − |
(1 + 2εT )e −2εT ]+ δ0 |
[1 − (2ε 2T 2 + 2εT +1)e−2εT ]+ |
|||||||||||||||||||
|
|
|
|
|
|
|
|
|
|
|
|
|
|
|
|
8ε |
|
|
|
|
|
|
|
|
E1 |
|
|
Jos |
|
|
2 − E12 |
|
|||||||||||||
+ |
|
E |
− |
E |
Jos + (2E1 −δ1 )J1s + |
|||||||||||||||||
|
|
|
|
|
4εδ1 |
|||||||||||||||||
|
|
2εδ1 |
|
|
|
|
|
|
|
|
|
|
+ (E1δ1 + E)J1c −δ1 J 2s + (δ12 −1)J2c / 2
Если удар заканчивается в этом периоде, то здесь Т надо заменить на t0, которое находится как корень уравнения
(7) при N2=0. Аналогично ведутся расчеты
идля последующих периодов. Анализ
показывает, |
что |
|
при |
δ 2 < 0 |
продолжительность |
удара |
ty |
значительно |
|
меньше, чем |
при |
δ 2 > 0 . Так, |
например, |
|
проведенные |
расчеты |
для |
реальных |
параметров системы показывает, что удар
практически |
всегда |
заканчивается |
во |
втором периоде при |
δ 2 < 0 и в третьем |
||
+ |
|
|
|
периоде при δ 2 > 0 .
322

Современные техника и технологии 2007
ЛИТЕРАТУРА: |
2. Бакиров |
Ж.Б., Касымханов С.Ж. |
1. Методика расчета импульсных |
“Продольный удар по упругому стержню”// |
|
установок / ИГД имени Скочинского. – 1973. – |
Вестник КарГТУ, |
серия математика. №3(35), |
43 с. |
2004. с. 75-79. |
|
РАЗРАБОТКАЭЛЕКТРОПРИВОДАВЫСОКОТОЧНОГОПЕРЕМЕЩЕНИЯ СВЕРХЗВУКОВОЙГАЗОПЛАМЕННОЙГОРЕЛКИ
КиселевВ.С. НагорныйД.А.
АлтайскийГосударственныйТехническийУниверситетимИ.И. Ползунова,
Россия, г. Барнаул, пр. Ленина, 46 E-mail: smalla1@inbox.ru
Проблема автоматизации и роботизации |
газопламенных установок, а именно низкой |
|||||||||||||||||||
высокотехнологичных |
процессов |
в |
стоимостью и высокой мобильностью. |
|
||||||||||||||||
сложившихся |
|
условиях |
необходимости |
|
Сверхзвуковая |
газопорошковая |
наплавка |
|||||||||||||
модернизации |
промышленности |
в |
России |
применяется |
главным |
образом |
|
для |
||||||||||||
особенно актуальна вследствие малой доли |
изготовления |
новых |
|
и восстановления |
||||||||||||||||
российских |
|
производителей |
на |
рынке |
изношенных деталей массового производства |
|||||||||||||||
современных |
|
типов |
|
электропривода. |
на |
машиностроительных |
предприятиях, |
|||||||||||||
Электроприводы на основе синхронно- |
подведомственных Ростехнадзору, к которым |
|||||||||||||||||||
шаговых |
|
двигателей |
и |
|
асинхронных |
относятся мосты, строительные сооружения, |
||||||||||||||
двигателей |
|
|
с |
низкочастотными |
железнодорожный |
транспорт |
и котельное |
|||||||||||||
преобразователями |
частоты |
|
находят |
оборудование. В частности, занимается |
||||||||||||||||
широкое |
применение |
для |
промышленных |
изготовлением |
и |
ремонтом |
деталей |
|||||||||||||
роботов |
|
|
и |
|
автоматизированных |
подвижного состава железно-дорожного |
||||||||||||||
технологических комплексов. |
|
|
|
|
|
транспорта одно из самых динамично |
||||||||||||||
На современном этапе развития техники и |
развивающихся |
крупных |
предприятий |
|||||||||||||||||
технологии |
нанесения |
защитных |
покрытий |
Алтайского края – ОАО «Алтай-вагон». Также |
||||||||||||||||
существует |
|
тенденция |
|
модернизации |
занимается |
производством |
и |
ремонтом |
||||||||||||
газопламенного способа нанесения защитных |
котлов с «кипящим слоем» ОАО «Бийский |
|||||||||||||||||||
покрытий, связанная с переходом на |
котельный завод», постоянно наращивающий |
|||||||||||||||||||
использование сверхзвуковых газовых струй. |
производство котлов с «кипящим слоем» |
|||||||||||||||||||
В этом случае сверхзвуковая газовая струя |
малой и средней мощности. |
|
|
|
||||||||||||||||
генерируется |
специальной |
|
горелкой |
со |
|
В |
соответствии |
с |
технологическими |
|||||||||||
сверхзвуковым соплом Лаваля, конфигурация |
требованиями, |
предъявляемыми |
к |
|||||||||||||||||
внутреннего |
сечения |
которого |
позволяет |
организации |
перемещения |
сверхзвуковой |
||||||||||||||
максимально |
сконцентрировать |
плотность |
газопламенной горелки |
при |
производстве |
|||||||||||||||
тепловой мощности газового пламени в пятне |
износостойкой наплавки, чрезвычайно остро |
|||||||||||||||||||
нагрева. |
|
|
|
|
|
|
|
|
|
|
встает |
проблема |
автоматизации |
данного |
||||||
Более |
сосредоточенное |
пятно |
нагрева |
высокотехнологического |
|
|
процесса. |
|||||||||||||
сверхзвуковой струи позволяет за короткий |
Автоматизация |
процесса |
сверхзвуковой |
|||||||||||||||||
промежуток |
времени |
оплавить |
|
частицы |
газопорошковой |
износостойкой |
наплавки |
|||||||||||||
порошка и навести жидкую металлическую |
позволит |
обеспечить |
|
повторяемость |
||||||||||||||||
ванну из основного и присадочного металла |
технологического |
процесса |
износостойкой |
|||||||||||||||||
в поверхностных слоях защищаемой детали. |
наплавки и |
|
стабильность |
качества |
||||||||||||||||
Данный |
процесс |
позволяет |
перейти |
на |
наносимого покрытия. |
|
|
|
|
|
||||||||||
качественно новый технологический уровень |
|
Наиболее |
|
приемлемыми |
типами |
|||||||||||||||
нанесения |
|
|
защитных |
|
|
покрытий, |
электропривода |
|
для |
организации |
||||||||||
формирующий металлическую связь между |
перемещения |
сверхзвуковой |
газопламенной |
|||||||||||||||||
материалом основы и покрытием - |
горелки |
являются |
|
электропривод |
с |
|||||||||||||||
сверхзвуковую |
газопорошковую |
наплавку. |
синхронно-шаговыми |
|
двигателями |
и |
||||||||||||||
Аппаратура |
|
для |
|
сверхзвуковой |
асинхронными |
|
двигателями |
|
с |
|||||||||||
газопорошковой |
износостойкой |
наплавки |
низкочастотными |
|
|
преобразователями |
||||||||||||||
обладает всеми достоинствами дозвуковых |
частоты. С применением современных типов |
323
XIII Международная научно-практическая конференция «СОВРЕМЕННЫЕ ТЕХНИКА И ТЕХНОЛОГИИ»
электропривода |
необходимо |
организовать |
применением |
|
микроконтроллерного |
|||||||||||||||
высокоточное |
перемещение |
сверхзвуковой |
управления; |
|
|
|
|
|
|
|
||||||||||
газопламенной |
|
горелки |
при |
производстве |
3) |
|
Высокая |
надежность |
|
и |
||||||||||
износостойкой наплавки. При этом у |
помехоустойчивость; |
|
|
|
|
|
||||||||||||||
российских |
разработчиков |
сведений |
об |
4) Малые габариты; |
|
|
|
|
|
|||||||||||
автоматизации |
|
процесса |
сверхзвуковой |
5) Низкая стоимость изготовления и |
||||||||||||||||
газопорошковой |
износостойкой |
наплавки |
не |
обслуживания. |
|
|
|
|
|
|
|
|||||||||
обнаружено. |
|
Применение |
|
зарубежных |
В данной работе предлагается переход от |
|||||||||||||||
автоматизированных |
|
|
сверхзвуковых |
процессов |
газопламенного |
напыления |
к |
|||||||||||||
газопламенных |
|
установок |
|
в |
процессе |
высокотехнологическому |
|
|
процессу |
|||||||||||
изготовления и восстановления деталей с |
автоматизированной |
|
сверхзвуковой |
|||||||||||||||||
защитными |
покрытиями |
|
для |
объектов |
газопорошковой износостойкой наплавки при |
|||||||||||||||
Ростехнадзора нецелесообразно по технико- |
изготовлении и восстановлении деталей с |
|||||||||||||||||||
экономическим соображениям. Также следует |
защитными |
|
покрытиями |
для |
объектов |
|||||||||||||||
отметить, что данные установки используют |
Ростехнадзора. |
|
|
Использование |
||||||||||||||||
при |
работе |
|
дорогостоящие |
импортные |
сверхзвуковой |
|
газопорошковой |
наплавки |
||||||||||||
порошковые |
|
материалы |
|
сверхмелкой |
позволяет |
|
|
значительно |
|
повысить |
||||||||||
фракции, что резко удорожает производство |
концентрацию ввода тепла, а также |
|||||||||||||||||||
защитного покрытия. |
|
|
|
|
|
|
исключить |
|
недостатки, |
свойственные |
||||||||||
Автоматизация |
|
производственного |
покрытиям, |
|
полученным |
|
дозвуковым |
|||||||||||||
процесса |
сверхзвуковой |
|
газопорошковой |
газопламенным напылением. |
|
|
|
|
||||||||||||
износостойкой |
|
наплавки |
заключается |
в |
На разработанное в процессе выполнения |
|||||||||||||||
разработке алгоритма перемещения горелки, |
данного |
|
проекта |
устройство |
|
для |
||||||||||||||
построении |
оригинальных |
кинематических |
сверхзвуковой |
|
газопорошковой |
наплавки |
||||||||||||||
схем и электропривода данной аппаратуры. |
получен патент РФ. Также получено |
|||||||||||||||||||
При |
этом |
предусматривается |
возможность |
положительное решение на |
низкочастотный |
|||||||||||||||
регулирования |
|
скорости |
|
перемещения |
преобразователь |
частоты, |
позволяющий |
|||||||||||||
сверхзвуковой |
|
газопламенной |
горелки |
в |
осуществить |
|
современное |
векторное |
||||||||||||
необходимых пределах, а также расстояния |
управление |
трехфазным |
асинхронным |
|||||||||||||||||
между срезом сопла горелки и защищаемой |
двигателем. |
|
|
|
|
|
|
|
||||||||||||
поверхностью с обеспечением необходимой |
Следует отметить, что разработанный |
|||||||||||||||||||
точности |
позиционирования. |
Также |
авторами |
|
|
бизнес-план |
инновационного |
|||||||||||||
разработанная |
|
технология |
|
наплавки |
– |
проекта |
|
|
«Разработка |
|
комплекса |
|||||||||
разделение |
процесса |
нанесения |
защитного |
автоматизированного |
оборудования |
и |
||||||||||||||
покрытия на данный конкретный участок |
технологии создания, диагностики и контроля |
|||||||||||||||||||
защищаемой детали на два этапа. Первый |
качества защитных покрытий на деталях |
|||||||||||||||||||
технологический этап – разогрев металла |
котлов |
с |
|
«кипящим |
слоем»», |
стал |
||||||||||||||
сверхзвуковой струей без порошка с |
финалистом |
открытого |
|
инновационного |
||||||||||||||||
обеспечением |
|
оптимального |
расстояния |
конкурса СПбГПУ «Инновация 2006» и |
||||||||||||||||
между срезом сопла горелки и защищаемой |
выставлен на сайте Северо-Западного центра |
|||||||||||||||||||
поверхностью. Второй технологический этап – |
венчурных |
инвестиций |
для |
проведения |
||||||||||||||||
непосредственное осуществление |
наплавки |
электронных торгов. В рамках данного |
||||||||||||||||||
сверхзвуковой струей с порошком с большего |
инновационного |
проекта |
производится |
|||||||||||||||||
расстояния, чем при разогреве металла, |
разработка |
электропривода |
высокоточного |
|||||||||||||||||
требующий |
осуществления |
регулирования |
перемещения |
сверхзвуковой |
газопламенной |
|||||||||||||||
расстояния между срезом сопла горелки и |
горелки |
при |
производстве |
износостойкой |
||||||||||||||||
защищаемой |
поверхностью |
в |
заданном |
наплавки на трубы поверхностей нагрева |
||||||||||||||||
диапазоне |
|
в |
процессе |
|
наплавки |
котлов с «кипящим слоем». |
|
|
|
|
||||||||||
быстродействующим электроприводом. |
|
Разрабатываемый |
|
электропривод |
||||||||||||||||
Основные требования |
к |
электроприводу |
высокоточного |
перемещения |
сверхзвуковой |
|||||||||||||||
автоматизированных |
|
|
технологических |
газопламенной |
горелки |
при производстве |
||||||||||||||
комплексов |
|
|
|
для |
|
сверхзвуковой |
износостойкой |
|
наплавки |
на |
трубы |
|||||||||
газопорошковой износостойкой наплавки: |
|
поверхностей нагрева котлов с «кипящим |
||||||||||||||||||
1) |
|
|
Алгоритм |
|
|
управления |
слоем» |
|
обеспечивает |
|
осуществление |
|||||||||
электроприводом, обеспечивающий заданные |
реверсивного |
перемещения |
сверхзвуковой |
|||||||||||||||||
технологические |
параметры |
сверхзвуковой |
газопламенной |
|
горелки. |
Необходимая |
||||||||||||||
газопламенной наплавки; |
|
|
|
|
|
точность |
|
позиционирования |
и |
заданный |
||||||||||
2) |
Современная |
быстродействующая |
диапазон |
|
|
регулирования |
скорости |
|||||||||||||
система управления |
электроприводом |
с |
перемещения горелки вдоль окружности трубы |
|||||||||||||||||
|
|
|
|
|
|
|
|
|
|
|
нагрева |
|
достигается |
|
применением |
324

Современные техника и технологии 2007
современных |
типов |
электропривода |
с |
|
|
|
|
|
|
|||||
быстродействующей |
микроконтроллерной |
ЛИТЕРАТУРА: |
|
|
|
|||||||||
системой управления. |
|
|
|
|
|
1. |
Материалы |
Всероссийской |
||||||
В |
разрабатываемом |
|
электроприводе |
конференции по приоритетному направлению |
||||||||||
высокоточного |
перемещения |
сверхзвуковой |
программы |
|
«ЭНЕРГЕТИКА |
|
И |
|||||||
газопламенной |
горелки |
при производстве |
ЭНЕРГОСБЕРЕЖЕНИЕ». |
Киселев |
В.С. |
|||||||||
износостойкой |
наплавки |
на |
трубы |
Разработка |
системы |
автоматического |
||||||||
поверхностей нагрева котлов с «кипящим |
управления |
электроприводом перемещения |
||||||||||||
слоем» |
|
применен |
синхронно-шаговый |
сверхзвуковой |
газопламенной |
|
горелки. |
|||||||
двигатель |
для |
электропривода |
главного |
Научный руководитель: д.т.н., проф. М.В. |
||||||||||
движения. Для привода подачи в зависимости |
Радченко. Томск 2006. |
|
|
|
||||||||||
от |
|
предъявляемых |
|
требований |
2. Конференция "Наука. Технологии. |
|||||||||
разрабатывается два варианта реализации: |
Инновации" (НТИ-2005) cntrs@center.nstu.ru. |
|||||||||||||
на |
основе |
синхронно-шагового |
и |
3. С.А. Маньковский, Д.А. Нагорный, М.В. |
||||||||||
асинхронного двигателя |
с |
низкочастотным |
Радченко, Ю.О. Шевцов. Тезисы: Проблемы и |
|||||||||||
преобразователем |
частоты. |
Также |
пути решения |
вопросов |
восстановления |
|||||||||
автоматизированный |
|
технологический |
деталей железнодорожного состава. Научный |
|||||||||||
комплекс |
сверхзвуковой |
|
газопорошковой |
руководитель: д.т.н., проф. М.В. Радченко. |
||||||||||
износостойкой |
наплавки |
|
для |
создания |
4. Д.А. Нагорный, С.А. Маньковский, М.В. |
|||||||||
защитных |
покрытий |
на |
деталях |
котлов |
с |
Радченко, Ю.О. Шевцов. Эффективные |
||||||||
«кипящим слоем» будет обладать высокой |
газодинамические |
методы |
нанесения |
|||||||||||
мобильностью, что делает его незаменимым |
защитных |
покрытий |
на |
объектах |
||||||||||
при производстве ремонтных работ на котлах |
теплоэнергетики. |
Научный |
руководитель: |
|||||||||||
с «кипящим слоем» непосредственно в |
д.т.н., проф. М.В. Радченко. |
|
|
|
||||||||||
муниципальных котельных. |
|
|
|
|
|
|
|
|
|
О СТРУКТУРНОМ ПРЕОБРАЗОВАНИИ КИНЕМАТИЧЕСКИХ ЦЕПЕЙ МЕХАНИЗИРОВАННЫХ КРЕПЕЙ С ЦЕЛЬЮ ОПТИМИЗАЦИИ ИХ ФУНКЦИОНАЛЬНЫХ ВОЗМОЖНОСТЕЙ
Князев А.С., Дворников Л.Т.
Сибирский государственный индустриальный университет,
Россия, г.Новокузнецк, ул. Кирова, 42
E-mail: knyazev_a.s@mail.ru
Современные |
угледобывающие |
комплектуемые из отдельных повторяющихся |
|||||||||||||||
комплексы, работающие на пологих и |
секций [1]. |
|
|
|
|
|
|
|
|
||||||||
пологонаклонных пластах, включают в себя: |
|
|
|
|
|
|
|
|
|
|
|
|
|
||||
комбайн для выемки угля на полную |
|
|
|
|
|
|
|
|
|
|
|
|
|
||||
|
|
|
|
|
|
|
|
|
|
|
|
|
|||||
мощность пласта; передвижной забойный |
|
|
|
|
|
|
|
|
|
|
|
|
|
||||
конвейер с мощной |
рамой, пригодной |
для |
|
|
|
|
|
3 |
|
|
|
||||||
работы с нее забойных машин и укладки |
2 |
|
|
|
|
|
|||||||||||
|
|
|
|
|
|
|
|
|
|
||||||||
необходимых |
коммуникаций |
по |
лаве |
|
|
|
|
|
|
|
|
|
|
|
|
|
|
(кабелей, шлангов и пр.); механизированные |
|
|
|
|
|
|
|
|
|
|
|
|
|
||||
крепи; кабелеукладчик; энергопоезд и другое |
|
|
|
|
|
|
|
|
|
|
|
|
|
||||
оборудование. |
|
|
|
|
|
|
|
|
|
|
|
|
|
|
|
|
|
Крепление и управление кровлей - один |
|
|
|
|
|
|
|
|
|
|
|
|
|
||||
из важных и пока еще наиболее трудоемких |
|
|
|
|
|
4 |
|
|
|
|
|
||||||
процессов добычи полезных ископаемых из |
|
|
|
|
|
|
|
|
|
|
|||||||
|
|
|
|
|
|
|
|
|
|
|
|
|
|||||
длинных очистных забоев. В последнее |
|
1 |
|
|
5 |
||||||||||||
время, для крепления и управления кровлей |
|
|
|
|
|
||||||||||||
|
|
|
|
|
|
|
|
|
|
|
|
|
|||||
широкое применение получили |
|
|
|
|
|
|
|
|
|
|
|
|
|
|
|
||
механизированные крепи. Обратим особое |
Рисунок 1 – Секция механизированной |
||||||||||||||||
внимание на механизированные крепи, |
|
||||||||||||||||
|
|
|
|
|
|
|
крепи с одним гидродомкратом |
325

XIII Международная научно-практическая конференция «СОВРЕМЕННЫЕ ТЕХНИКА И ТЕХНОЛОГИИ»
|
|
|
|
|
|
|
задать два независимых движения распорных |
||||||||
Секция механизированной крепи (рисунок |
гидродомкратов, чтобы вся конструкция |
||||||||||||||
1), обычно содержит в своем составе |
совершала предсказуемые движения. Однако |
||||||||||||||
распорный гидродомкрат 1, козырек 2, звено |
синхронную |
работу |
двух |
параллельных |
|||||||||||
ограждения 3, первое коромысло 4 звена |
гидродомкратов обеспечить сложно из-за |
||||||||||||||
ограждения 3, второе коромысло 5 звена |
случайных |
различий |
в |
силах |
их |
||||||||||
ограждения |
3. |
Управление движением |
сопротивления, а потому их взаимовлияние |
||||||||||||
поддерживающего |
звена |
или |
звена |
может приводить к заклиниванию и |
|||||||||||
поддержки |
перекрытия, |
как |
правило, |
искажению заданного закона движения. |
|||||||||||
осуществляется распорным гидродомкратом, |
Представляется |
более |
целесообразным |
||||||||||||
шток которого опирается в одну из точек |
создавать секции механизированных крепей в |
||||||||||||||
звена поддержки. Часто это обстоятельство |
виде одностепенных кинематических цепей с |
||||||||||||||
приводит к появлению значительного по |
использованием |
дополнительных |
стержней, |
||||||||||||
длине вылета козырька, подверженного |
обеспечивающих |
увеличение |
жесткости |
||||||||||||
изгибу |
под |
действием |
неравномерного |
конструкции |
и |
заданную |
|
определенность |
|||||||
давления |
кровли. |
В |
этих |
случаях |
движения. |
|
|
|
|
|
|
|
|||
параллельно |
первому |
гидродомкрату |
|
|
|
|
|
|
|
|
|||||
устанавливается |
второй гидродомкрат 6, |
|
|
|
|
|
|
|
|
||||||
который |
забирает |
на |
себя |
часть |
нагрузки |
5 |
|
6 |
4 |
|
|
|
|
||
кровли (рисунок 2). |
|
|
|
|
|
|
|
|
|
|
|
||||
|
|
|
|
|
|
|
|
|
|
7 |
|
||||
|
|
|
|
|
|
|
|
|
|
|
|
|
|
||
|
|
|
|
|
|
|
А |
3 |
|
|
|
|
|
|
|
|
|
|
|
|
|
|
|
|
|
|
|
|
|
||
|
|
|
|
|
|
|
( А1.А2 ,А3 ) |
|
|
|
|
|
|
|
|
|
|
|
|
|
3 |
|
2 |
|
|
8 |
|
|
|
|
|
|
2 |
|
|
|
|
|
|
|
|
|
|
||||
|
|
|
|
|
|
|
|
|
|
|
9 |
|
|||
|
|
|
|
|
|
|
|
|
|
|
|
|
|
||
|
|
|
6 |
|
|
|
|
1 |
|
|
|
|
|
|
|
|
|
|
|
|
|
|
|
|
|
|
|
|
|
||
1 |
|
|
|
4 |
|
|
|
|
|
|
|
|
|
|
|
|
|
|
|
|
|
Рисунок 3 – Секция механизированной |
|||||||||
|
|
|
|
|
|
|
|||||||||
|
|
|
|
|
5 |
|
крепи по патенту №2234606 |
|
|||||||
|
|
|
|
|
|
|
Одна из таких цепей приведена на |
||||||||
Рисунок 2 – Секция механизированной |
рисунке 3 (по патенту [3]). В ней используется |
||||||||||||||
распорный |
гидродомкрат |
1 |
с поршнем |
и |
|||||||||||
крепи с двумя гидродомкратами |
|||||||||||||||
штоком 2, трехшарнирное звено 3, |
|||||||||||||||
|
|
|
|
|
|
|
|||||||||
С точки зрения работы плоских |
распределяющее действие сил на две точки, |
||||||||||||||
звено поддержки 4, первый шатун 5 звена |
|||||||||||||||
механических систем, подвижность схемы на |
поддержки 4, второй шатун 6 звена |
||||||||||||||
рисунке |
|
1 |
(без |
|
дополнительного |
поддержки 4, звено ограждения 7, первое |
|||||||||
гидродомкрата) |
определяется |
согласно |
коромысло 8 звена ограждения 7, второе |
||||||||||||
известной формуле Чебышева П.Л. [2, стр. 47 |
коромысло 9 звена ограждения 7. |
|
|
||||||||||||
фор.(2.8)] имеющей вид: |
|
|
Эта схема может явиться прототипом |
||||||||||||
|
W = 3 n− 2 p5 |
= 3 5 − 2 14 =1, |
|||||||||||||
|
создания |
нового |
поколения |
секций |
|||||||||||
где W - подвижность механизма; |
механизированных |
крепей |
для |
горного |
|||||||||||
n - число подвижных звеньев; |
|
производства. |
|
|
|
|
|
|
p5 - число кинематических пар пятого
класса.
Т.е. достаточно одного движения – распорного гидродомкрата, чтобы вся конструкция совершала предсказуемые движения.
Аналогично определим работоспособность схемы на рисунке 2 (с дополнительным гидродомкратом)
W = 3 n − 2 p5 = 3 8 − 2 11 = 2 .
Эта система, оказывается, по подвижности двухстепенной, т.е. необходимо
326

Современные техника и технологии 2007
Рисунок 4 – План смещений секции механизированной крепи по патенту №2234606
Обратимся к кинематике секции механизированной крепи, показанной на рисунке 3. Движение звеньев в секции осуществляется от приводного гидродомкрата. В поршневую полость гидродомкрата 1 подается под давлением жидкость – техническое масло, при этом начинается движение поршня со штоком 2.
Начнем решение задачи с конца механизма, т.е. зададимся некоторым смещением точки К относительно точки N ( Sk )
отложим это смещение от полюса плана P ( pk )(рисунок 4).
Для нахождения смещения точки H составим систему уравнений
|
|
|
= |
|
|
+ |
|
, |
|
|
|
HK, |
||
SH |
SK |
SHK |
SHK |
|||||||||||
|
|
|
|
|
|
|
|
|
||||||
|
|
SHM HM. |
||||||||||||
SH = SHM , |
На продолжении линии kh на плане пропорционально длинам HK и HG находим точку g, которая определит в масштабе построения смещение шарнира G ( SG ).
По принципу подобия находим и точку f на плане.
Для нахождения смещения точки Е составим систему уравнений
|
|
|
= |
|
|
+ |
|
|
, |
|
|
|
EG, |
|||
SE |
SG |
SEG |
SEG |
|||||||||||||
|
|
|
|
|
|
|
|
|
|
|
||||||
|
|
|
|
SEF EF. |
||||||||||||
SE = SF + SEF , |
|
На продолжении линии ge на плане в соответствующей пропорции находим
положение точки d и её смещение
SD = pd μS ,
где μS – масштаб построения
Далее, находим смещение точки С, проводя из e и из f до пересечения перпендикулярные линии соответственно отрезкам EC и FC. Смещение точки В найдется из системы уравнений
|
|
|
= |
|
|
+ |
|
|
, |
|
|
BC, |
|||
SB |
SC |
SBC |
SBC |
||||||||||||
|
|
|
|
|
|
|
|
|
|
||||||
|
|
|
SBD BD. |
||||||||||||
SB = SD + SBD , |
После этого строим на плане треугольник cba подобный треугольнику CBA на механизме и сходственно расположенный ему. Завершим построение, проводя из полюса линию перпендикулярную LA, а из точки a линию параллельную LA. Получим отрезок а1а2, который и является смещением, происходящим в гидродомкрате 1. По этому известному смещению находим масштаб построения и все действительные смещения точек.
ЛИТЕРАТУРА:
1.Сафохин М.С. Горные машины и оборудование: Учебник для ВУЗов. / М.С. Сафохин, Б.А. Александров, В.И. Нестеров – М.: Недра, 1995. – 463 с.
2.Артоболевский И.И. Теория механизмов и машин. – М.: Наука, 1975.
3.Патент №2234606, Секция механизированной крепи. / Дворников Л.Т.,
Ерёмин Д.С. – Опубл. 20.08.2004. Бюл. №23.
ВЛИЯНИЕ ИЗНОСА КОНТАКТНОГО НАКОНЕЧНИКА НА СТАБИЛЬНОСТЬ ПРОЦЕССА МЕХАНИЗИРОВАННОЙ СВАРКИ ПЛАВЛЕНИЕМ
Колмогоров Д.Е.
Юргинский технологический институт (филиал)
Томского политехнического университета, Россия, Кемеровская обл., г. Юрга, ул. Ленинградская,26
E-mail: dek-79@mail.ru
Износ контактного наконечника в процессе сварки вызывает отклонение электрических параметров цепи наконечник – изделие. Так в результате износа ухудшается электрический контакт с электродной проволокой, увеличивается контактное сопротивление, изменяется вылет электрода, что в свою очередь влияет на напряжение сварочной дуги и стабильность процесса
сварки в целом. Для выработки рекомендаций по применению на производстве контактных наконечников изготовленных из различных материалов необходимо исследовать влияние износа канала наконечника на стабильность процесса сварки, а именно:
-потери на угар и разбрызгивание;
-стабильность подачи сварочной проволоки;
327

XIII Международная научно-практическая конференция «СОВРЕМЕННЫЕ ТЕХНИКА И ТЕХНОЛОГИИ»
|
- стабильность процесса зажигания дуги. |
|
При использовании сварочной проволоки |
||||||||||||||||
|
В настоящей работе были проведены |
с |
омедненной |
поверхностью |
ψ,(%) |
||||||||||||||
исследования |
влияния |
износа |
контактного |
значительно ниже для новых наконечников, |
|||||||||||||||
наконечника на потери электродного металла |
чем при использовании стальной проволоки |
||||||||||||||||||
на |
угар |
|
и |
разбрызгивание. |
При |
(рисунок 2). С износом наконечников |
|||||||||||||
механизированной сварке в СО2 потери |
наблюдается значительный рост ψ,(%), по |
||||||||||||||||||
электродного металла весьма велики. Однако |
сравнению |
с |
использованием |
стальной |
|||||||||||||||
коэффициент потерь ψ не должен превышать |
проволоки. Недопустимым ψ,(%) обладают |
||||||||||||||||||
10-15% в зависимости от диаметра |
наконечники из композиционного |
материала |
|||||||||||||||||
электродной |
проволоки |
[1]. |
Исследования |
ДУКМ |
М70. |
Наименьшими |
|
потерями |
|||||||||||
проводили |
с |
использованием |
контактных |
обладают наконечники из меди М1. |
|
|
|||||||||||||
наконечников, изготовленных из следующих |
|
|
|
|
|
|
|
|
|
|
|
||||||||
материалов: |
|
композиционный |
материал |
|
|
|
|
|
|
|
|
|
|
|
|||||
ДУКМ М70 (ОАО «Уралэлектромедь», г. |
|
|
|
|
|
|
|
|
|
|
|
||||||||
Верхняя |
Пышма), |
медь |
М1 |
и |
|
|
|
|
|
|
|
|
|
|
|
||||
меднохромоциркониевый |
сплав |
(CuCrZr) |
|
|
|
|
|
|
|
|
|
|
|
||||||
(ООО «Сварка», г. Санкт-Петербург). |
|
|
|
|
|
|
|
|
|
|
|
||||||||
Исследовались |
|
новые |
|
контактные |
|
|
|
|
|
|
|
|
|
|
|
||||
наконечники (без выработки канала) и с |
|
|
|
|
|
|
|
|
|
|
|
||||||||
выработкой канала, соответствующей двум |
|
|
|
|
|
|
|
|
|
|
|
||||||||
часам механического износа. |
|
|
|
|
|
|
|
|
|
|
|
|
|
|
|||||
|
Использовалась сварочная проволока Св- |
|
Рисунок 2 – Iсв = 200А, Uд = 20В; |
||||||||||||||||
08Г2С по ГОСТ 2246-70 стальная без |
|
||||||||||||||||||
сварочная |
проволока |
|
с |
омедненной |
|||||||||||||||
покрытия и с омедненной поверхностью |
поверхностью, подающие ролики с насечкой. |
||||||||||||||||||
диаметром 1,2 мм. |
|
|
|
|
|
На |
режимах |
с |
|
максимальным |
|||||||||
|
Сварочное |
|
оборудование: |
источник |
|
|
|||||||||||||
|
|
разбрызгиванием (Iсв = 250А, Uд = 26В) при |
|||||||||||||||||
питания ВДУ-506, сварочный полуавтомат |
использовании проволоки без покрытия на |
||||||||||||||||||
ПДГ-508 (подающие ролики с насечкой); |
новых наконечниках ψ,(%) незначительно |
||||||||||||||||||
источник питания ВС-300Б, полуавтомат ПДГ- |
превышает |
|
допустимые |
|
значения |
||||||||||||||
421 |
(подающие |
ролики |
без |
насечки). |
(исключение |
- |
наконечник |
из |
|
меди |
М1) |
||||||||
Коэффициент |
|
потерь |
на |
угар |
и |
|
|||||||||||||
|
(рисунок 3). При использовании наконечников |
||||||||||||||||||
разбрызгивание |
оценивался |
по |
известной |
с |
выработкой |
|
потери |
|
существенно |
||||||||||
методике [2]. |
|
|
|
|
|
|
|
возрастают для материалов ДУКМ М70 и |
|||||||||||
|
Согласно |
экспериментальным данным |
|||||||||||||||||
|
CuCrZr. Наконечники из меди имеют |
||||||||||||||||||
(рисунок 1) коэффициент потерь ψ,(%) для |
наименьший ψ,(%), хотя при износе |
||||||||||||||||||
всех трех материалов практически одинаков |
превышается допустимое значение на 1%. |
||||||||||||||||||
при использовании новых наконечников, |
|
|
|
|
|
|
|
|
|
|
|
||||||||
сварочной |
проволоки |
без |
покрытия, |
|
|
|
|
|
|
|
|
|
|
|
|||||
подающих роликов с насечкой и режима |
|
|
|
|
|
|
|
|
|
|
|
||||||||
сварки Iсв = 200А, Uд = 20В (среднее |
|
|
|
|
|
|
|
|
|
|
|
||||||||
разбрызгивание для проволоки ø1,2 мм). При |
|
|
|
|
|
|
|
|
|
|
|
||||||||
использовании наконечников с выработанным |
|
|
|
|
|
|
|
|
|
|
|
||||||||
каналом потери увеличились незначительно, |
|
|
|
|
|
|
|
|
|
|
|
||||||||
и входят в допустимые пределы 10-12% для |
|
|
|
|
|
|
|
|
|
|
|
||||||||
данного диаметра сварочной проволоки [1]. |
|
|
|
|
|
|
|
|
|
|
|
||||||||
Наименьшими |
|
потерями |
|
обладают |
|
|
|
|
|
|
|
|
|
|
|
||||
наконечники из меди М1. |
|
|
|
|
|
|
|
|
|
|
|
|
|
|
|
||||
|
|
|
|
|
|
|
|
|
|
Рисунок 3 – Iсв = 250А, Uд = 26В; |
|||||||||
|
|
|
|
|
|
|
|
|
сварочная |
проволока |
без |
|
покрытия, |
||||||
|
|
|
|
|
|
|
|
|
подающие ролики с насечкой. |
|
|
|
|||||||
|
|
|
|
|
|
|
|
|
|
При использовании сварочной проволоки |
|||||||||
|
|
|
|
|
|
|
|
|
с омедненной поверхностью на режимах с |
||||||||||
|
|
|
|
|
|
|
|
|
максимальным |
разбрызгиванием |
ψ,(%) |
||||||||
|
|
|
|
|
|
|
|
|
снижается по сравнению со стальной |
||||||||||
|
|
|
|
|
|
|
|
|
проволокой. Для наконечников без выработки |
||||||||||
|
|
|
|
|
|
|
|
|
из композиционного материала ψ,(%) имеет |
||||||||||
|
Рисунок 1 – Iсв = 200А, Uд = 20В; |
предельное |
|
значение |
|
|
12%, |
из |
|||||||||||
|
меднохромоциркониевого |
|
сплава |
ψ,(%) |
|||||||||||||||
сварочная |
проволока |
без |
покрытия, |
превышает |
на |
1% |
допустимое |
значение, |
|||||||||||
подающие ролики с насечкой. |
|
|
|
(рисунок |
4). |
Для |
наконечников |
из |
меди, |
328

Современные техника и технологии 2007
потери в 2 раза ниже по сравнению с использованием стальной проволоки. С износом ψ,(%) увеличивается. В допустимые пределы входит только ψ,(%) при использовании наконечника из меди М1.
Рисунок 4 – Iсв = 250А, Uд = 26В;
сварочная проволока с омедненной поверхностью, подающие ролики с насечкой.
Рисунок 5 – Iсв = 250А, Uд = 26В;
сварочная проволока без покрытия, подающие ролики без насечки.
Применение механизма подачи с роликами без насечки на режимах с максимальным разбрызгиванием в 1,5-2 раза снижает ψ,(%) на новых наконечниках по сравнению с механизмом подачи имеющим ролики с насечкой при использовании сварочной проволоки без покрытия (рисунок 5). Износ контактных наконечников увеличивает ψ,(%), однако для всех материалов не превышает допустимого значения.
Использование сварочной проволоки с омедненной поверхностью еще больше снижает коэффициент ψ,(%) на режимах с максимальным разбрызгиванием и использовании механизма подачи с роликами без насечек (рисунок 6). С износом контактных наконечников коэффициент ψ,(%) увеличивается в среднем в 2 раза. Потери при использовании наконечника из ДУКМ М70 превышают допустимые значения. Наконечники из меди имеют наименьший
ψ,(%).
Рисунок 6 – Iсв = 250А, Uд = 26В;
сварочная проволока с омедненной поверхностью, подающие ролики без насечки.
По результатам проведенных исследований можно сделать следующие выводы:
1.С выработкой канала наконечника увеличиваются потери электродного металла на угар и разбрызгивание независимо от материала наконечника.
2.Применение механизма подачи проволоки с гладкими роликами снижает потери электродного металла на угар и разбрызгивание в 1,5-2 раза.
3.Контактные наконечники из композиционного материала ДУКМ М70 целесообразно использовать в сочетании со сварочной проволокой без покрытия.
4.Наименьшие потери наблюдаются при использовании контактных наконечников из меди в сочетании с омедненной сварочной проволокой и подающими роликами без насечки.
Задачи дальнейших исследований:
1.Исследовать влияние износа контактных наконечников из различных материалов на стабильность подачи сварочной проволоки;
2.Исследовать влияние износа контактных наконечников из различных материалов на стабильность процесса зажигания дуги;
3.Разработать рекомендации по применению контактных наконечников из различных материалов в соответствие с режимами сварки.
ЛИТЕРАТУРА:
1.Потапьевский А.Г. Сварка в углекислом газе. – М.: Машиностроение, 1984. – 80с.
2.Федько В.Т. Технология, теоретические основы и средства снижения трудоемкости при сварке в углекислом газе: Учебник. – Томск: Изд-во Том. ун-та, 2004. – 398с.
329

XIII Международная научно-практическая конференция «СОВРЕМЕННЫЕ ТЕХНИКА И ТЕХНОЛОГИИ»
ИССЛЕДОВАНИЕ СТАТИЧЕСКИХ ХАРАКТЕРИСТИК РУКАВОВ ВЫСОКОГО ДАВЛЕНИЯ
К.А. Кувшинов, А.Ю. Супрунов, П.Я. Крауиньш Томский политехнический университет, Россия, 634050, г.Томск, пр.Ленина, 30
E-mail:kuvschinovk@mail.ru
Исследование упругих оболочек (рукавов |
Для |
оценки |
точности |
полученной |
||||||||||||
высокого давления) в исполнительных |
зависимости проводилось экспериментальное |
|||||||||||||||
механизмах |
гидровибраторов |
для |
создания |
исследование |
|
|
|
кинематической |
||||||||
механических, колебаний известно, хорошо |
характеристики на лабораторной установке, |
|||||||||||||||
изучено и дает существенные преимущества |
принципиальная схема которой показана на |
|||||||||||||||
по сравнению с другими типами вибраторов: |
рис.1. Здесь 1 – исследуемая оболочка, 2 – |
|||||||||||||||
простоту конструкции |
и |
технологичность |
регулятор поджатия, 3 – плунжер, 4 – |
|||||||||||||
изготовления, |
|
герметичность |
рабочих |
градуированная стеклянная трубка, 5 – |
||||||||||||
полостей, удобство встраивания в машины, |
часовой индикатор. С помощью регулятора 2 |
|||||||||||||||
обусловленное |
|
гибкостью |
|
рукавов, |
задавалась деформация х1, а по уровню |
|||||||||||
возможность |
|
получать |
|
большие, |
жидкости в трубке определялся вытесняемый |
|||||||||||
вибротяговые усилия, а также управлять |
объем. |
|
|
|
|
|
|
|
||||||||
резонансом системы. |
|
|
|
|
|
|
|
|
|
|
|
|
|
|||
Однако применение оболочек в качестве |
|
|
|
|
|
|
|
|
||||||||
рабочих |
камер |
генератора |
придает |
|
|
|
|
|
|
|
|
|||||
дополнительные |
качества |
таким |
системам |
|
|
|
|
|
|
|
|
|||||
практически |
|
полное |
устранение |
утечек |
|
|
|
|
|
|
|
|
||||
жидкости, |
позволяет |
|
отказаться |
от |
|
|
|
|
|
|
|
|
||||
прецизионных |
деталей |
в |
генераторе |
|
|
|
|
|
|
|
|
|||||
колебаний, |
|
|
применить |
|
объемное |
|
|
|
|
|
|
|
|
|||
регулирование амплитуды за счет изменения |
|
|
|
|
|
|
|
|
||||||||
рабочего объема генератора, а при |
|
|
|
|
|
|
|
|
||||||||
определенных |
соотношениях |
параметров |
|
|
|
|
|
|
|
|
||||||
генератора |
и |
исполнительного механизма |
|
|
|
|
|
|
|
|
||||||
реализовать параметрический |
резонансный |
|
|
|
|
|
|
|
|
|||||||
режим. |
|
|
|
|
|
|
|
|
|
|
|
|
|
|
|
|
Данная |
тема |
посвящена |
исследованию |
|
|
|
|
|
|
|
|
|||||
кинематики генератора колебаний, его |
Рис 2. Кинематическая характеристика |
|||||||||||||||
статических и динамических (частотных) |
||||||||||||||||
характеристик на холостых режимах работы, |
|
|
оболочки. |
|
|
|
||||||||||
а также анализу нелинейных факторов, |
На рис. 2 показаны экспериментальные |
|||||||||||||||
определяющих |
|
свойства |
|
не |
|
только |
зависимости кинематической характеристики, |
|||||||||
генератора, но и всей системы: нагрузка |
построенные по выражению (1). Качественно |
|||||||||||||||
исполнительный механизм генератор-привод. |
характер кривых не отличается, но |
|||||||||||||||
|
|
|
|
|
|
|
|
|
экспериментальные |
кривые располагаются |
||||||
|
|
|
|
|
|
|
|
|
несколько выше расчетных. Это обусловлено |
|||||||
|
|
|
|
|
|
|
|
|
влиянием граничных деформаций длиной lгр в |
|||||||
|
|
|
|
|
|
|
|
|
зоне |
перехода |
|
оболочки |
от |
|||
|
|
|
|
|
|
|
|
|
деформированного сечения к круглому, где |
|||||||
|
|
|
|
|
|
|
|
|
происходит дополнительное |
вытеснение |
||||||
|
|
|
|
|
|
|
|
|
жидкости. |
|
|
|
|
|
|
|
|
|
|
|
|
|
|
|
|
Для дальнейшего |
анализа |
генератора |
|||||
|
|
|
|
|
|
|
|
|
удобно перейти к отсчету вытесняемого |
|||||||
|
|
|
|
|
|
|
|
|
объема, |
|
относительно |
|
некоторого |
|||
|
|
|
|
|
|
|
|
|
предварительно |
|
деформированного |
|||||
|
|
|
|
|
|
|
|
|
состояния оболочки, что соответствует |
|||||||
|
|
|
|
|
|
|
|
|
реальной |
схеме циклической |
деформации |
|||||
|
|
|
|
|
|
|
|
|
оболочки в генераторе колебании. |
|
||||||
Рис 1. Расчетная и принципиальная схема |
W |
|
= π B (d |
|
− h |
) , |
|
(1) |
||||||||
|
|
генератора |
|
|
|
|
( x1 ) |
4 |
0 |
( x1 ) |
|
|
|
|||
|
|
|
|
|
|
|
|
|
|
|
|
|
|
|
|
330

Современные техника и технологии 2007
Где h(x1) – текущее состояние оболочки по внутренней поверхности.
Задавая теперь деформацию ± х1 относительно начального h, производя преобразования получим кинематическую характеристику генератора:
W |
) |
= π B |
dH − h |
x |
+ |
π B x2 |
(2) |
|
|
||||||||
( x |
2 |
1 |
|
4 |
1 |
|
||
1 |
|
|
|
|
|
|||
|
|
|
|
|
|
|
|
Где dH – начальный диаметр оболочки, а h – начальное поджатие по наружней поверхности.
На величину начального поджатия должны быть наложены условия:
hmax = dH − x01 |
(3) |
hmax = dH −0.5d0 + x01 |
(4) |
регулирования вытесняемого объема жидкости за счет изменения параметра h. Так как в генераторе деформация задается гармонической функцией:
x1 = x01Sinω1t,
Из анализа зависимости следует, что с увеличением давления количество вытесняемой из оболочки жидкости уменьшается, то есть уменьшается рабочий
объем Wr .
Таким образом, статическое давление создаваемое в оболочке, как бы увеличивает ее предварительное поджатие по внутренней поверхности, что приводит к снижению рабочего объема генератора.
ЛИТЕРАТУРА:
Условие |
(3) |
обеспечивает |
безотрывный |
1. Крауиньш |
П.Я. |
Кузьмин |
В.А. |
||||
Особенности |
|
расчета |
|
|
объемных |
||||||
характер движения задающего плунжера и |
гидравлических |
|
вибраторов |
с |
упругими |
||||||
оболочки, |
а |
условие |
(4) |
выражает |
элементами |
// |
Гидропривод |
и |
системы |
||
предельную радиальную деформацию, при |
управления (строительных, тяговых и |
||||||||||
которой |
обеспечивается |
|
циклическая |
дорожных машин) |
Межвузовский сборник. – |
||||||
прочность металлического каркаса рукава. |
Новосибирск 1976 – С. 66–74. |
|
|
|
|||||||
Анализ |
кинематической |
характеристики |
|
|
|
||||||
генератора |
(2.4) |
указывает |
на |
возможность |
|
|
|
|
|
|
|
АНАЛИЗ ТЕХНОЛОГИИ ПОЛУЧЕНИЯ ПОЛЫХ ЦИЛИНДРИЧЕСКИХ ЗАГОТОВОК СТРУЙНЫМ ФОРМОВАНИЕМ
Лагуткин С.В.
Новоуральский государственный технологический институт, Россия, 624130, г.Новоуральск, Свердловской обл., ул.Ленина, 85 E-mail: nil8@npi.novouralsk.ru
В настоящее время в промышленно развитых странах, таких как Германия, Великобритания, Австрия и Дания активно внедряется технология струйного формования заготовок как альтернатива традиционному литью и методам порошковой металлургии [1]. Основными преимуществами новой технологии следует назвать низкую сегрегацию, однородную мелкозернистую структуру изделий, регулируемую пористость и возможность создания совершенно новых композиционных материалов. Вместе с тем, она не лишена характерных недостатков, присущих любому новому методу обработки металлов. Анализу технологических особенностей струйного формования и посвящен данный обзор.
В общем случае можно выделить три типа получаемых струйным формованием
заготовок: плоские (листовые), сплошные цилиндрические и полые цилиндрические (трубы), в зависимости от формы подложки и режимов ее перемещения (рис.1).
Рис.1. Типы заготовок, получаемых струйным формованием
Оборудование, применяемое для формования конкретного типа заготовки,
331

XIII Международная научно-практическая конференция «СОВРЕМЕННЫЕ ТЕХНИКА И ТЕХНОЛОГИИ»
ничем не отличается (за исключением привода подложки) и укрупнено состоит из следующих элементов (рис.2):
•Плавильный агрегат с разливочным устройством (например, вакуумная индукционная печь с поворотным тиглем и обогреваемой промежуточной воронкой);
•Газовая форсунка свободного слива с дополнительным инжектором;
•Камера распыления модульной конструкции (в большинстве случаев, с контролируемой атмосферой и водоохлаждаемыми стенками);
•Система газоподготовки (как правило, на основе мембранных или криогенных газификаторов);
•Узел подачи внедряемого порошкового материала (устанавливается в качестве опции для получения заготовок типа ММС – Metal Matrix Composite);
•Система очистки отработавшего газа, включающая циклон, фильтр, вытяжной вентилятор и трубу рассеяния (на рисунке не показаны);
•Привод подложки формуемой заготовки;
•Контрольно-измерительные приборы
иаппаратура, связанные в единый комплекс.
Рис.2. Схема технологии струйного формования
Наибольшее распространение в массовом производстве получили полые цилиндрические заготовки, формирование которых наглядно показано на фотографиях (рис.3). Ведущие мировые производители,
такие как концерн Dymler-Chrysler, Ford Motor Company, SKF, Wieland, используют их для изготовления гильз двигателей внутреннего сгорания, колец подшипников качения, а также, всевозможных вкладышей и втулок подшипников скольжения, обладающих повышенным ресурсом, нагрузочной способностью и другими улучшенными потребительскими свойствами (рис.4).
Рис.3. Процесс формования полых цилиндрических заготовок
Рис.4. Образцы изделий, полученных из трубчатых заготовок
Прогресс в данной области применения вызван следующими неоспоримыми достоинствами технологии:
• Универсальность, то есть возможность получения заготовок большого диапазона диаметров и длин (от 20 мм и больше, внешние размеры ограничены лишь габаритами камеры, в которой происходит формование, и ёмкостью плавильной печи). При этом обеспечивается любая заданная толщина стенки с относительно малым припуском. Подобная универсальность позволяет охватить широкую номенклатуру выпускаемых изделий без переналадки оборудования и в кратчайшие сроки – достаточно установить трубу-подложку требуемого диаметра и выбрать необходимые режимы ее перемещения.
Рис.5. Этапы получения обечайки D = 1000 мм:
формование – охлаждение – механообработка – прокатка
• Возможность |
управления |
структурой получаемой |
заготовки (от |
332

Современные техника и технологии 2007
кристаллической до аморфной) за счет |
• |
Необходимость |
|
использования |
|||||||||||||
выбранных режимов формования. |
|
подложек и их дальнейшего удаления |
|||||||||||||||
• |
Возможность |
|
|
получения |
механическим |
|
путем, |
|
например, |
||||||||
высококачественных |
композиционных |
растачиванием (рис.7). |
|
|
|
|
|
||||||||||
материалов путем добавления порошков- |
|
|
|
|
|
|
|
|
|
||||||||
присадок различного назначения в газ, |
|
|
|
|
|
|
|
|
|
||||||||
подаваемый |
на |
распыление |
|
базового |
|
|
|
|
|
|
|
|
|
||||
металла или сплава. |
|
|
|
|
|
|
|
|
|
|
|
|
|
||||
• |
Возможность |
регулирования |
|
|
|
|
|
|
|
|
|
||||||
пористости заготовки по толщине в |
|
|
|
|
|
|
|
|
|
||||||||
процессе ее получения (рис.6). |
|
|
|
|
|
|
|
|
|
|
|
|
|||||
|
|
|
|
|
|
|
|
Рис.7. Механическая обработка заготовки |
|||||||||
|
|
|
|
|
|
|
|
|
|
после получения |
|
|
|
||||
|
|
|
|
|
|
|
|
• Низкий ресурс разливочного узла – |
|||||||||
|
|
|
|
|
|
|
|
каждый |
последующий |
слив |
|
расплава |
|||||
|
|
|
|
|
|
|
|
предполагает использование нового сливного |
|||||||||
|
|
|
|
|
|
|
|
стакана |
промежуточной |
|
|
воронки, |
|||||
Рис.6. Срез заготовки и диаграмма его |
изготавливаемого, |
как |
|
правило, |
из |
||||||||||||
дорогостоящей керамики на основе оксидов |
|||||||||||||||||
|
|
пористости |
|
|
|
||||||||||||
|
|
|
|
|
алюминия и циркония. |
|
|
|
|
|
|||||||
В |
качестве сопутствующих |
|
недостатков |
|
|
стоимость |
|||||||||||
технологии струйного формования |
следует |
• |
Высокая |
|
|
|
|||||||||||
вспомогательного |
|
|
оборудования, |
||||||||||||||
выделить следующее: |
|
|
|
|
включающего |
систему |
газоподготовки |
и |
|||||||||
• |
Невысокая производительность (до |
||||||||||||||||
300 |
кг/ч) |
и |
дискретность |
|
процесса |
газоочистки. |
|
опыта |
работы |
с |
|||||||
формования. |
|
|
|
|
|
|
• |
Отсутствие |
|||||||||
|
|
|
|
|
|
подобными технологиями в нашей стране. |
|
||||||||||
• |
Большой |
|
расход |
|
|
газа- |
|
||||||||||
энергоносителя, |
в |
подавляющем |
Вышеизложенное |
позволяет |
сделать |
||||||||||||
вывод, что при решении указанных проблем |
|||||||||||||||||
большинстве |
случаев, |
технически |
чистого |
||||||||||||||
азота. |
|
|
|
|
|
|
|
рассмотренную технологию |
можно |
назвать |
|||||||
|
|
|
|
|
|
|
одной из наиболее перспективных для |
||||||||||
• |
Технологическая |
|
|
сложность |
|||||||||||||
реализации |
процесса |
– |
формование |
создания определенной высокотехнологичной |
|||||||||||||
напрямую зависит от |
работы |
|
достаточно |
продукции, |
|
|
|
повышающей |
|||||||||
«капризного» |
в |
промышленных |
условиях |
конкурентоспособность |
|
отечественного |
|||||||||||
распылительного узла. |
|
|
|
|
машиностроения на мировом рынке. |
|
|
||||||||||
|
|
|
|
ЛИТЕРАТУРА: |
|
|
|
|
|
|
|||||||
• |
Неэффективное |
использование |
|
3rd |
International |
||||||||||||
1. |
Proceedings |
of |
|||||||||||||||
материала – часть распыляемого металла |
Conference on Spray Deposition and Melt |
||||||||||||||||
уходит не на получение заготовки, а на |
Atomization SDMA2006 and 6th International |
||||||||||||||||
образование частиц порошка. При этом |
Conference on Spray Forming ICSF VI |
||||||||||||||||
коэффициент |
использования |
|
материала |
(September 04-06, 2006, SFB372, Bremen, |
|||||||||||||
сильно зависит от геометрии факела |
Germany) – V.1-4. |
|
|
|
|
|
|
||||||||||
распыления |
и |
диаметра |
|
формуемой |
|
|
|
|
|
|
|
|
|
заготовки.
333

XIII Международная научно-практическая конференция «СОВРЕМЕННЫЕ ТЕХНИКА И ТЕХНОЛОГИИ»
РАСЧЁТ ПРОЧНОСТИ БАЛКИ РАМПЫ ВЕРТОЛЕТА*
Медведев Д.В., Куркина Л.А., Егодуров Г.С.
Восточно-Сибирский государственный технологический университет, Россия, Г.Улан-Удэ, ул.Ключевская 40в
E-mail: office@esstu.ru
На рис.1 предоставлена расчетная схема балки рампы вертолета переменной жесткости. Требуется проверить прочность и жесткость этой балки[1]
Рис.1 Расчетная схема балки рампы вертолета
Задачу решаем используя математическую программу Mathcad[1,2]. Он позволяет достаточно просто реализовать вычислительный алгоритм любой сложности. Большой набор встроенных специализированных функций делает его особенно удобной для расчета конструкций
на |
прочность. |
Традиционное |
программирование разводит |
во времени |
процесс решения задачи на три независимых этапа: программа пишется, а за тем отлаживается и оптимизируется. В среде Mathcad эти процессы слиты воедино, то есть создание "программы" идет параллельно с ее отладкой.
Исходные данные будем вводить с российскими размерностями. Но предварительно, встроенные в MathCAD размерности, будем менять с английского названия на российские, записав:
м:=m Н:=N кг:=kg мм:=103m
Па:=Pa рад:=rad кН:=103N МПа:=106Pa
Материал балки – алюминиевый сплав АЛ4: σu:=400МПа – предел прочности материала; E:=0,72·МПа – предел упругости материала; Геометрические размеры балки:
l:=3086·мм |
l1:=543·мм |
l2:=2000·мм |
h1:=178.7мм h2:=80.7мм |
d:=2.5мм |
|
b:=60мм c:=3мм |
a:=1мм |
e:=22мм |
Нагрузка:
qe :=150 Hм
-интенсивность распределенной нагрузки; F := 5.5кН - сосредоточенная сила. Закон изменения высоты сечения балки:
h(z) := h + |
h2 − h1 |
z |
|
||
1 |
l |
|
|
|
Для проверки правильности аналитического выражения h(z) строим график изменения высоты сечения по длине балки (рис2).
Рис.2. График изменения высоты сечения балки
Определяем геометрические характеристики поперечного сечения балки. Сечение разбиваем на четыре фигуры, так как показано на рис 1.
Определяем осевой момент инерции Ix:
Ix=Ix.1-Ix.2-Ix.3+Ix4
где
I x.1 |
= |
bh(z)3 |
I x.2 = |
(b − d)(h(z) − 2 c)3 |
|
|||
12 |
|
|
12 |
|
||||
|
|
|
(c = e)]3 |
|
|
|||
I x.3 |
d[h(z) − 2 |
I x.4 |
= |
a[h(z) − 2 |
(c + e)] |
|||
|
12 |
|
12 |
|
||||
|
|
|
|
|
|
Программные модули для расчета
Ix(z),Wx(z)
334

Современные техника и технологии 2007
|
0if 0 ≤ z ≤ l |
|
||||||
|
|
|||||||
|
b h( z) 3 |
− |
|
(b − d ) (h( z) − 2 |
c) 3 |
|||
|
|
12 |
12 |
|
|
|||
|
|
|
|
|
||||
Ix(z)= |
|
− d[h( z) − 2 (c + e)]3 |
|
|||||
|
+ |
|
||||||
|
|
|
12 |
|
|
|
||
|
|
|
|
|
|
|
||
|
+ |
a[h( z) − 2 (c + e)]3 |
|
|
||||
|
|
|
|
12 |
|
|
|
0if 0 ≤ z ≤ l
Wx (z):= Ix (z)
h(z)
2
z := 0,0.1..3.086
Рис.2 График изменения момента инерции
Разбиваем балку на три участка, отбрасываем опоры и заменяем их реакциями Ra и Rb, которые определяем из уравнений моментов относительно опор∑ M a = 0, ∑ M b = 0 :
Given Ra := qe l |
Rb := qe l |
Rb l − F (l1 +l2 ) − F l1 − qe l 12 = 0
− Ra l + F (l1 +l2 ) + F l1 − qe l 12 = 0
Find(R |
|
, R |
|
|
5.731 10 |
3 |
|
H |
a |
b |
) = |
|
3 |
|
|||
|
|
|
5.731 10 |
|
|
|||
|
|
|
|
|
|
|
|
Программный модуль для вычисления
M x (z)
|
|
R Z − |
q |
e |
z |
2 |
|
if 0 ≤ z ≤ l |
I |
|
|
||||||||
|
|
|
|
|
|
|
|
|
|
|
|||||||||
|
|
|
α |
|
2 |
|
|
|
|
|
|
|
|
|
|
||||
|
|
|
|
|
|
|
|
|
|
|
|
|
|
|
|||||
|
|
|
|
|
|
|
|
|
|
|
|
|
|
|
|
||||
|
|
|
Ra z... |
|
|
|
|
|
|
|
|
|
|
l |
|
|
|||
|
|
|
|
|
|
|
|
|
|
|
|
|
|
I |
|||||
M x (z) := |
+ −F(z − Il )... iflI |
|
|
|
|
|
|
||||||||||||
≤ z ≤ |
+l2 |
|
|||||||||||||||||
|
|
+ − |
qe z |
2 |
|
|
|
|
|
|
|
|
|
|
|||||
|
|
|
|
|
|
|
|
|
|
|
|
|
|
|
|||||
|
|
|
|
|
|
|
|
|
|
|
|
|
|||||||
|
|
|
2 |
|
|
|
|
|
|
|
|
|
|
|
|
|
|||
|
|
Rb (l − z)... |
2 |
|
|
|
l |
I |
|
|
|
|
|
||||||
|
|
|
qe (l − z) |
|
|
|
|
|
≤ z ≤ l |
||||||||||
|
|
|
|
|
if |
|
|
|
|||||||||||
|
+ − |
2 |
|
|
|
|
|
|
|
+l2 |
|
|
|
|
|||||
|
|
|
|
|
|
|
|
|
|
|
|
|
|
|
|
|
Рис.3 Эпюра изгибающих моментов
M x (z)
Программный модуль для определения
σ z
0if 0 ≤ z ≤ l
σ(z) := M x (z)
Wx (z)
Найдем экстремальное значение σ max(z)
при помощи вычислительного блока Given / Maximize [3]
Given 0.5 l ≤ z ≥ 1 l
Maximize (σ, z) = 2.543 103 мм
σmax (2.543 103 мм) =158МПа
Определяем |
коэффициент |
запаса по |
|||||||
пределу прочности nu |
|
|
|
|
|||||
nu = |
|
σu |
|
nu = 2.532 |
|||||
σ |
adm |
||||||||
|
|
|
|
|
|||||
|
|
|
|
|
|
||||
Прогибы и углы поворота сечений балки |
|||||||||
Given |
|
|
d 2 |
v(z) = |
|
M x (z) |
|||
|
|
dz 2 |
|
E I x (z) |
|
Граничные условия: v(0)=0 v(3.086)=0
v := odesolve(z,3.06,1000)...z := 0,005...3.086
335

XIII Международная научно-практическая конференция «СОВРЕМЕННЫЕ ТЕХНИКА И ТЕХНОЛОГИИ»
Рис.5 Эпюры прогибов ν(z) и углов
поворота v(z) сечений по длине балки Рассчитаем экстремальное значение прогибаν(z) балки, используя блок: Given /
Minimize
Начальное значение аргумента z:=0.5·l
Given. 0.5 l ≤ z ≤ 0.8 l
Minimize(v, z) =1.738×103 мм
zопт :=1.738×103 мм v(1.738) = −31мм
Таким образом, результаты расчета показывают, что прочность и жесткость балки рампы удовлетворяют требованиям, предъявляемым к таким элементам вертолета.
ЛИТЕРАТУРА:
1.Феодосьев В.И. Сопротивление материалов. – М.; Наука, 1986. – 512 с.
2.Кирьянов Д.В. Самоучитель Mathcad 13.
–СПб.; БХВ – Петербург, 2006. – 528 с.
3.Вафин Р.К., Егодуров Г.С., Зангеев Б.И. Расчеты на прочность элементов машиностроительных конструкций в среде
MathCAD. – Улан-Удэ: Бурят. кн. изд-во, 2005.
–600с.
* Работа поддержана программой «Развитие научного потенциала высшей школы(2006-2008годы)» № РНП 2.1.2.5517.
КОМБИНИРОВАННОЕ ВЫДАВЛИВАНИЕ ДВУПОЛОСТНОЙ ВТУЛКИ
Медведев М.В., Маркечко И.В., Грязнов В.В.
Омский государственный технический университет, 644050, Россия, г. Омск, пр. Мира, 11 E-mail: maksim-medvedev@mail.ru
Расчетная схема процесса выдавливания |
В процессе выдавливания двуполостной |
|||
двуполостных втулок представлена на рис. 1. |
втулки, пренебрегая |
стадией заполнения |
||
|
пространства |
между |
контейнерной |
частью |
|
матрицы и осаживаемой заготовкой, можно |
|||
|
выделить |
два |
основных |
этапа |
|
деформирования заготовки (рис. 2). |
|
Рис. 1. Схема процесса |
|
комбинированного выдавливания |
|
двуполостной втулки: 1 - пуансон; 2 - |
|
матрица; 3 - поковка; 4 – контрпуансон. |
Рис. 2. Этапы деформирования заготовки. |
336

Современные техника и технологии 2007
На первом этапе течение металла может происходить, в общем случае, по схеме комбинированного выдавливания с двумя очагами деформации (с высотами h1 и h2), разделенными недеформируемой зоной 5. При течении металла в зазор между пуансоном и контейнером образуется верхняя полость втулки диаметром 2RП (верхний очаг, зоны 1 и 2), а при прямом выдавливании в зазор между контрпуансоном и контейнером - нижняя полость диаметром 2RОП (нижний очаг, зоны 3 и 4). Этот этап определяется условием существования “жесткой” зоны 5.
Второй этап начинается с момента вовлечения всего объема металла заготовки, находящегося между торцами пуансона и контрпуансона, в пластическую деформацию. Процесс заканчивается при достижении донышком S заданной толщины. Если
S |
≤ 1 |
, |
то |
процесс |
деформации |
|
h1 + h2 |
||||||
|
|
|
|
|
двуполостной втулки начинается со второго этапа.
Принятая расчетная схема представляет собой систему кинематически возможных полей скоростей, удовлетворяющих условию несжимаемости и граничным условиям (VZ изменяется по линейному закону, а Vρ определяется из условия постоянства объема).
Формоизменение в любой момент деформации зависит от размеров инструмента и трех неизвестных параметров h1, h2 и k, где k – задает соотношение скоростей течения металла в прямом (k=1) и обратном (k=0) направлениях. При комбинированном выдавливании 0<k<1.
Параметры h1, h2 и k определим с использованием вариационного принципа возможных изменений деформированного состояния, отвечающего условию минимума полной энергии деформации, то есть h1, h2 и k должны принимать значения, соответствующие минимальным усилиям на пуансоне, в любой момент деформирования.
Полную мощность деформации определяем по формуле
NД |
M |
N |
L |
|
= ∑ NВ +∑NС +∑NТР , |
(1) |
|||
|
m=1 |
n=1 |
l=1 |
|
где M – количество пластических зон; NВ – мощность внутренних сил;
N – количество границ сдвига;
NС – мощность сопротивления сил сдвига; L – количество границ трения;
NТР – мощность сопротивления сил трения.
Разделив левую и правую части выражения (1) на скорость деформирования V0, площадь торца пуансона FП, и предел
текучести материала σS получим выражение для определения относительного удельного усилия на пуансоне
p |
= |
|
|
NД |
. |
(2) |
||
у |
S |
у |
S |
F V |
||||
|
|
|
||||||
|
|
|
П 0 |
|
|
Продифференцировав выражение (2) по неизвестным параметрам h1, h2 и k и приравняв их к нулю, получим систему из трех уравнений
∂(p/уS ) =0
∂h1
∂(p/уS ) =0 .
∂h2
∂(p/уS ) =0
∂k
Эта система уравнений приводится к виду
hX1 =F1(k) |
|
|
hX2 =F2 (k) |
|
(3) |
, |
||
|
|
|
F3 (hX1,hX2 ,k)=0 |
|
где hX1 и hX2 выделены в явном виде относительно параметра k.
В результате дальнейших преобразований (3) получаем нелинейное алгебраическое уравнение
F(k)=0.
Решение данного уравнения дает несколько корней. Нахождение действительного корня связано с проверкой условия минимума полной энергии, что равнозначно отысканию минимального значения функции
p |
= F(k) . |
(4) |
|
||
уS |
|
Полученное уравнение (4) корректируется в зависимости от этапа деформирования
(h1+h2>S или h1+h2≤S) и условия (RП=RОП, RП<RОП или RП>RОП).
Расчеты проведены для процессов с различными размерами инструмента и H=32 мм:
-2RК=45 мм; 2RП=25 мм; 2RОП=35 мм (на рис. 3, 4, 5 и 6 кривая 1);
-2RК=45 мм; 2RП=25 мм; 2RОП=25 мм (на рис. 3, 4, 5 и 6 кривая 2);
-2RК=45 мм; 2RП=25 мм; 2RОП=15 мм (на рис. 3, 4, 5 и 6 кривая 3).
337

XIII Международная научно-практическая конференция «СОВРЕМЕННЫЕ ТЕХНИКА И ТЕХНОЛОГИИ»
Рис. 3. Зависимость полного усилия на пуансоне от относительного изменения расстояния между пуансоном и контрпуансоном.
Рис. 4. Зависимость коэффициента k от относительного изменения расстояния между пуансоном и контрпуансоном.
Рис. 5. Зависимость относительной высоты верхней полости от относительного изменения расстояния между пуансоном и контрпуансоном
Рис. 6. Зависимости относительной высоты нижней полости от относительного изменения расстояния между пуансоном и контрпуансоном.
Для проверки адекватности математической модели проведены эксперименты по выдавливанию двуполостных втулок из свинца с H=32 мм на гидравлической разрывной машине ГРМ-1 с записью машинных графиков зависимости усилия на пуансоне от его хода. В экспериментальных исследованиях использовалась оснастка с размерами: 2RК=45 мм; 2RП=25 мм; 2RОП=25
мм. В результате преобразований машинных графиков построена кривая зависимости полного усилия на пуансоне от относительного изменения расстояния между пуансоном и контрпуансоном (на рис.3 кривая 2'). На рис. 5 и 6 точкой 2'' изображено конечное формоизменение.
Вывод: расхождение расчетных и экспериментальных данных по конечному формоизменению и силовому режиму не превышает 10%, что вполне допустимо для практических расчетов.
ЛИТЕРАТУРА:
1.Евстратов В.А. Теория обработки металлов давлением.-Харьков: Вища школа, 1981.-284 с.
2.Изготовление заготовок и деталей пластическим деформированием/ Богоявленский К.Н., Рис В.В., Шелестеев А.М.-Л.: Политехника, 1991.-351 с.: ил.
3.Математическое моделирование процессов ОМД/ Гуляев Ю.Г., Чукмасов С.А., Губинский А.В.-Киев: Наукова думка, 1986.- 240 с.
4.Третьяков А.В., Зюзин В.И. Механические свойства металлов и сплавов при обработке давлением.-М.: Металлургия, 1973.-224 с.
338

Современные техника и технологии 2007
НАПЛАВКА ТРЕХФАЗНОЙ ДУГОЙ ПЛАВЯЩИМИСЯ ЭЛЕКТРОДАМИ
Мейстер Р.А., Падар В.А., Безруких А.А.
Красноярский политехнический институт СФУ, Россия, г. Красноярск, ул. Киренского, 26
Однодуговой способ наплавки покрытыми |
витков алюминиевой обмотки сечением 32 |
||||||||||||||||
электродами |
|
получил |
|
широкое |
мм2, выполнялся отвод и дополнительно |
||||||||||||
распространение. |
|
Его |
недостатками |
наматывали |
5 |
|
витков. |
|
Плавное |
||||||||
считается |
низкая |
производительность |
и |
регулирование |
токов |
|
в |
электродах |
|||||||||
необходимость нанесения четырех-пяти |
осуществляли, |
изменяя |
зазор |
между |
|||||||||||||
слоев для получения требуемого состава |
стержнями |
|
и |
приставным |
ярмом. |
||||||||||||
наплавленного металла. |
|
|
|
|
Дополнительно ток в каждом электроде |
||||||||||||
Применение |
|
переменного |
тока |
в |
регулировался |
отдельным |
дросселем с |
||||||||||
сварочном |
|
производстве |
позволяет |
кольцевым |
|
магнитопроводом |
|
и |
|||||||||
использовать простые и дешевые источники |
секционированной обмоткой. Преимуществом |
||||||||||||||||
питания, обладающие более высокими КПД в |
отдельного дросселя является возможность |
||||||||||||||||
сравнении с источниками постоянного тока. |
регулирования |
и |
выравнивания |
тока |
|||||||||||||
Кроме того, сварочная дуга переменного тока |
короткого замыкания в каждой фазе, что |
||||||||||||||||
свободна от такого недостатка как магнитное |
улучшает равномерность плавления каждого |
||||||||||||||||
дутье. |
|
|
|
|
|
|
|
|
электрода и динамические свойства в |
||||||||
Преимуществами |
трехфазной |
дуги |
сравнении с шихтованным магнитопроводом. |
||||||||||||||
является |
большая |
производительность, |
Электроды фиксировались в простейшем |
||||||||||||||
возможность |
|
снижения |
|
глубины |
электрододержателе, |
|
имеющем |
|
три |
||||||||
проплавления за счет уменьшения тока в |
параллельные |
медные |
пластины, |
||||||||||||||
фазе детали. Также при горении трехфазной |
изолированные |
|
электроизоляционными |
||||||||||||||
дуги металл в сварочной ванне интенсивно |
прокладками. |
|
|
|
|
|
|
|
|||||||||
перемешивается, |
|
что |
обеспечивает |
Одинаковое расстояние между двумя и |
|||||||||||||
мелкозернистую структуру сварного шва. |
|
тремя |
параллельными |
|
электродами |
||||||||||||
За последние |
десятилетия |
отсутствуют |
обеспечивает |
равные |
электрические |
||||||||||||
сведения о применении сварки и наплавки |
параметры режимов в каждом электроде, что |
||||||||||||||||
трехфазной дугой покрытыми электродами и |
способствует |
равномерному |
плавлению |
||||||||||||||
нет сведений о наплавке независимой |
электродов и улучшает формирование швов. |
||||||||||||||||
трехфазной дугой тремя электродами. В |
Электроды |
связывались |
тонкой |
||||||||||||||
связи с появлением в России и за рубежом |
проволокой или тонкими нитками. Но при |
||||||||||||||||
электродов диаметром 1,6–3 мм появилась |
приближении дуги к местам крепления и |
||||||||||||||||
возможность |
|
уменьшить |
|
массу |
нагреве электродов нитки обгорают, что |
||||||||||||
электрододержателей для сварки трехфазной |
вызывает «расхождение» электродов и |
||||||||||||||||
дугой и токоподводящих проводов, что |
изменение режимов наплавки. Проволока при |
||||||||||||||||
являлось существенным недостатком сварки |
расплавлении |
обмазки |
вызывает |
короткие |
|||||||||||||
трехфазной дугой [1]. |
|
|
|
|
|
замыкания между стержнями электродов и |
|||||||||||
Цель работы – при наплавке покрытыми |
нарушение |
стабильности |
режима |
горения |
|||||||||||||
электродами |
обеспечить |
формирование |
трехфазной дуги. |
|
|
|
|
|
|
||||||||
валиков с минимальной долей участия |
Наиболее |
простой |
и |
приемлемый |
|||||||||||||
основного металла в наплавленном и |
результат |
обеспечивается |
обмазкой |
||||||||||||||
обеспечить |
формирование |
швов |
при |
связанных |
нитками |
электродов |
силикатным |
||||||||||
наплавке в углекислом газе проволокой |
клеем с последующей просушкой при |
||||||||||||||||
диаметром 1,2 мм. |
|
|
|
|
|
|
температуре 200 °С. |
|
|
|
|
|
|
||||
Для питания трехфазной дуги применяли |
Также |
применялся |
вариант |
окунания |
|||||||||||||
трансформатор от выпрямителя ВСС-300 с |
связанных нитками электродов в жидкое |
||||||||||||||||
падающей характеристикой и трансформатор |
стекло с последующей просушкой. |
|
|
||||||||||||||
ТШС-1000-3 с жесткой характеристикой. У |
Показатели |
устойчивости |
горения |
||||||||||||||
трансформатора ТШС-1000-3 падающая |
трехфазной дуги не могут оцениваться по |
||||||||||||||||
характеристика |
обеспечивалась |
отдельным |
показателям для однодуговой сварки [2]. |
||||||||||||||
трехфазным |
|
|
дросселем. |
Площадь |
Например, показатель эластичности дуги |
||||||||||||
поперченного |
|
сечения |
стержней |
неприемлем для независимой |
трехфазной |
||||||||||||
шихтованного магнитопровода составляла 72 |
дуги, так как независимая трехфазная |
дуга |
|||||||||||||||
см2. На каждом стержне |
наматывалось |
25 |
(между электродами) |
горит |
при |
любом |
339
XIII Международная научно-практическая конференция «СОВРЕМЕННЫЕ ТЕХНИКА И ТЕХНОЛОГИИ»
расстоянии от изделия. К наиболее важным |
При напряжении холостого хода 70–80 В |
|||||||||||||
показателям устойчивого горения трехфазной |
зажигание независимой дуги осуществляется |
|||||||||||||
дуги следует отнести: зажигание дуги, |
шунтированием тока через деталь и на токах |
|||||||||||||
равномерность |
|
плавления |
электродов, |
в электродах 70–90 А обеспечивается |
||||||||||
потери |
на |
|
угар |
и |
разбрызгивание, |
удовлетворительное |
формирование |
|||||||
формирование шва и отсутствие застывшей |
наплавленного металла с долей участия |
|||||||||||||
капли на торцах электродов после угасания |
основного металла в наплавленном 9–10 %. |
|||||||||||||
дуги. При наплавке независимой дугой тремя |
При расстоянии от концов электродов до |
|||||||||||||
электродами расстояние от дуги до детали |
детали 6–8 мм потери на угар и |
|||||||||||||
также |
характеризует |
|
устойчивость |
ее |
разбрызгивание составляют 10–11 %. |
|||||||||
горения. |
|
|
|
|
|
|
|
|
|
Увеличение диаметра электродов и |
||||
При |
питании |
независимой |
трехфазной |
расстояния между ними ухудшает зажигание |
||||||||||
дуги от трансформатора |
выпрямителя ВСС- |
независимой трехфазной дуги. |
|
|||||||||||
300 из-за низкого напряжения холостого хода |
При напряжении холостого хода 80 В |
|||||||||||||
чаще |
наблюдалась |
|
неравномерность |
зажигание |
трехфазной независимой дуги |
|||||||||
плавления |
электродов |
и |
ухудшение |
электродами диаметром 3 мм улучшается в |
||||||||||
зажигания дуги. Поэтому питание дуги |
случае подключения нулевого провода к |
|||||||||||||
осуществлялось |
|
трансформатором |
|
ТШС- |
изделию. После зажигания независимой дуги |
|||||||||
1000-3. |
|
|
|
|
|
|
|
|
|
нулевой провод от детали отключается. При |
||||
При наплавке двумя электродами МР-3 |
токах в электродах 100–140 А и напряжении |
|||||||||||||
диаметром 2 мм режимы были следующие: |
дуг 30–40 В доля участия основного металла |
|||||||||||||
Uxx = 80 В, расстояние между стержнями |
в наплавленном увеличивается. |
|
||||||||||||
электродов 1,2 мм, токи в электродах 60–70 |
В настоящее время известны случаи |
|||||||||||||
А, ток в детали 80–85 А, напряжения дуг 30– |
применения трехфазной дуги для сварки в |
|||||||||||||
35 В. В случае касания детали одновременно |
углекислом газе [3]. |
|
|
|||||||||||
двумя электродами дуга зажигается с одного- |
Оценивалась |
устойчивость |
горения |
|||||||||||
двух касаний. Расположение спаренных |
трехфазной дугой в углекислом газе |
|||||||||||||
электродов вдоль и поперек шва не ухудшает |
проволокой СВ08Г2С диаметром 1,2 мм без |
|||||||||||||
его формирование. |
|
|
|
|
|
|
регулятора тока в фазе изделия. |
|
||||||
Для |
|
устранения |
неравномерного |
На пластины из стали 09Г2С толщиной 8 |
||||||||||
плавления |
трех |
электродов |
|
перед |
мм, зачищенные до металлического блеска, |
|||||||||
зажиганием |
дуги |
необходимо |
обеспечить |
омедненной |
проволокой |
наплавляли |
||||||||
одинаковый ток короткого замыкания в |
одиночные валики. Для питания дуги |
|||||||||||||
каждой фазе. Зажигание осуществляется |
использовали трансформатор ТШС-1000-3, в |
|||||||||||||
одновременным |
касанием детали |
концами |
котором для снижения напряжения холостого |
|||||||||||
трех электродов и шунтированием токов |
хода |
первичную |
обмотку |
соединяли |
||||||||||
через деталь. |
|
|
|
|
|
|
|
«звездой», а вторичную – «треугольником». |
||||||
При наплавке тремя электродами на |
Для |
создания |
пологопадающей |
|||||||||||
зачищенную |
до |
металлического |
блеска |
характеристики в каждую фазу включали |
||||||||||
пластину на режимах (токи в электродах и |
активные сопротивления. |
|
||||||||||||
детали 70 А, напряжения на дугах 28–30 В) |
Электрические |
параметры |
режимов |
|||||||||||
потери на угар и разбрызгивание составляют |
контролировались |
по |
показаниям |
|||||||||||
10,7 %, а коэффициент наплавки 8 г/А час. |
амперметров и вольтметров, записывали |
|||||||||||||
Коэффициент |
наплавки |
определялся по |
осциллографом Н-700, проводили визуальное |
|||||||||||
формуле |
|
|
|
|
|
|
|
|
|
наблюдение за горением дуги, измеряли |
||||
|
|
|
|
|
|
|
|
|
|
потери на угар и разбрызгивание. Сварочную |
||||
|
|
Qн = Gн 3600/3 It, |
|
|
горелку для подачи двух проволок |
|||||||||
|
|
|
|
|
|
|
|
|
|
подвешивали к сварочному автомату, при |
||||
где Gн – масса наплавленного металла в |
этом |
плоскость |
электродных |
проволок |
||||||||||
граммах; I – ток в электроде, А; t – время |
располагали |
перпендикулярно направлению |
||||||||||||
горения дуги, с. |
|
|
|
|
|
|
|
наплавки. Расстояние между проволоками в |
||||||
На аналогичном режиме один электрод |
зоне касания детали составляло 1–2 мм, что |
|||||||||||||
диаметром 2 мм плавится на 20–25 % |
обеспечивало близкий к симметричному по |
|||||||||||||
дольше, |
|
что |
свидетельствует |
о |
токам режим I1 = I2 = I3, где I1, I2 – токи в |
|||||||||
подогревающем действии трех дуг и лучшем |
электродах, I3 – ток в детали. Вылет |
|||||||||||||
использовании энергии в трехфазной дуге в |
электродных проволок 10–12 мм; отношение |
|||||||||||||
сравнении с однофазной. |
|
|
|
|
напряжений холостого хода и дуги 1,2–1,3, |
|||||||||
Доля участия основного металла в |
скорость |
|
сварки |
0,47– |
||||||||||
наплавленном не превышает 10 %, что |
1,44 см/с, расход газа 25–30 л/мин. Выявлено, |
|||||||||||||
невозможно при однодуговой наплавке. |
|
что |
формирование |
наплавленного металла |
340

Современные техника и технологии 2007
вполне удовлетворительное. С увеличением |
|
|
|
|
||||
токов в электродах до 250–350 А потери на |
ЛИТЕРАТУРА: |
|
|
|||||
угар и разбрызгивание уменьшаются и |
1. Г.П. |
Михайлов. |
Сварка |
трехфазной |
||||
составляют 5–12 %, что сравнимо с |
дугой. Машгиз, Москва, Свердловск, 1956. 239 |
|||||||
наблюдаемыми при горении дуги постоянного |
с. |
|
|
|
||||
тока. |
|
|
|
|
2. ГОСТ 25616–83. Источники питания для |
|||
Выводы: |
|
|
|
|
дуговой |
сварки. |
Методы |
испытания |
1) Наплавка трехфазной и независимой |
сварочных свойств. |
|
|
|||||
трехфазной |
дугой |
увеличивает |
3. Сюкасев Г.М., Масленников В.Н., Хова- |
|||||
производительность |
и |
уменьшает |
долю |
нец В.К. Сварка трехфазной дугой в СО2 |
||||
участия основного металла в наплавленном. |
кольцевых |
швов воздушного |
выключателя |
|||||
2) Для наплавки возможно использовать |
ВВ-330Б. – В кн.: Сварочное производство: |
|||||||
серийные |
источники |
питания |
с |
Труды вузов Уральской зоны. Свердловск: |
||||
незначительными усовершенствованиями. |
УПИ им. С.М. Кирова, 1973. № 208. С. 145– |
|||||||
3) При |
сварке |
в |
углекислом |
газе |
148. |
|
|
|
обеспечивается формирование швов. |
|
|
|
|
|
ГОРЕНИЕ ДУГИ НА МАЛЫХ ТОКАХ В ЗАЩИТНЫХ ГАЗАХ ПЛАВЯЩИМСЯ ЭЛЕКТРОДОМ
Мейстер А.Р., Мейстер Р.А.
Сибирский федеральный университет, Россия, г. Красноярск, ул. Киренского, 26
E-mail: evangelist1@mail.ru
Обычная схема возбуждения дуги при |
наклона электрода не более 60°, скорость |
||||||||||
сварке плавящимся |
электродом |
диаметром |
подачи электрода не более 700 м/ч, схема не |
||||||||
0,8-2 мм предусматривает его непрерывную |
работает |
при |
питании |
дуги |
от |
||||||
подачу под напряжением холостого хода |
преобразователей |
и выпрямителей |
с |
||||||||
источника питания к изделию до их |
диодами [2]. |
|
|
|
|
||||||
соприкосновения. Под действием тока |
Минимальный ток горения дуги в течение |
||||||||||
короткого замыкания происходит разогрев и |
20 мс для дуги в углекислом газе электродной |
||||||||||
выброс металла электрода после нескольких |
проволокой Св-08Г2С диаметром 1,6 и 2 мм |
||||||||||
таких |
соприкосновений, |
прежде |
чем |
составляет 2-4 А [3]. |
|
|
|
||||
установится процесс сварки. По ГОСТ 25616- |
Зафиксировано |
устойчивое |
длительное |
||||||||
83 допускается возбуждение дуги после трех- |
горение дуги на малых токах в защитных |
||||||||||
четырех |
соприкосновений |
электрода |
с |
газах при неподвижном вылете электродной |
|||||||
изделием [1]. |
|
|
|
|
|
проволоки 10-30 мм и питании дуги от |
|||||
В |
большинстве |
отечественных |
и |
однофазного выпрямителя с конденсаторным |
|||||||
зарубежных источниках питания таких фирм, |
умножителем напряжения и крутопадающей |
||||||||||
как ВНИИЭСО, Lincoln, KEMPPI, Cemont, |
характеристикой. Напряжение холостого хода |
||||||||||
Messer, ESAB и др. для улучшения зажигания |
при выключенных |
конденсаторах емкостью |
|||||||||
сварочной дуги применяются «горячий старт» |
2000 мкФ составляло 23-35 В, а при |
||||||||||
(Hot Start) и изменение скорости подачи |
включенных конденсаторах – в 2,82 раза |
||||||||||
электродной проволоки или их комбинация. |
больше. В цепь питания дуги включался |
||||||||||
Исследования показали, что ни «горячий |
дроссель индуктивностью 5-15 мГн, дуга |
||||||||||
старт», ни программирование изменения |
зажигалась касанием изделия торцом вылета |
||||||||||
скорости подачи электродной проволоки не |
и последующим отрывом от изделия. |
|
|||||||||
решают задачу надежного и управляемого |
Во всех случаях дуга зажигалась с |
||||||||||
зажигания сварочной дуги. Разработан |
первого касания концом вылета изделия. В |
||||||||||
способ безконтактного зажигания дуги, |
процессе горения дуги на торце вылета |
||||||||||
который |
имеет |
недостатки: |
диаметр |
образовывалась капля. После угасания дуги |
|||||||
застывшей капли на конце электрода не |
наличие застывшей капли на торце электрода |
||||||||||
должен превышать полутора-двух диаметров |
диаметром в 2,5-3,5 раза больше диаметра |
||||||||||
электрода, минимальное расстояние от |
электрода не препятствует ее зажиганию. |
|
|||||||||
электрода до изделия не менее 3-5 мм, угол |
|
|
|
|
|
341
XIII Международная научно-практическая конференция «СОВРЕМЕННЫЕ ТЕХНИКА И ТЕХНОЛОГИИ»
Длительное горение дуги на токе 2-3 А позволяет упростить зажигание дуги при механизированной сварке, учитывая, что объем ее применения больше чем на порядок превосходит автоматическую сварку в углекислом газе.
Зажигание дуги осуществляется следующим образом. За счет включения конденсаторов устанавливается напряжение холостого хода выпрямителя с крутопадающей характеристикой в 2,82 раза больше напряжения холостого хода. Дроссель индуктивностью 5-15 мГн включается в сварочную цепь.
Устанавливается вылет 10dЭ (dЭ – диаметр проволоки), и после подачи защитного газа касанием торцом электродной проволоки изделия на токе 2-6 А зажигается дуга.
После разогрева торца вылета, образования на торце вылета жидкой прослойки металла и ионизации дугового промежутка через 0,5-1 секунды после зажигания дуги кнопкой на рукоятке сварочной горелки включается двигатель подачи проволоки, зажигается основная дуга между торцом подогретого вылета и изделием на токе, который зависит от скорости подачи проволоки. Цепь вспомогательной дуги отключается через 0,2- 0,3 с. (Положительное решение на патент от
17.01.2007, заявка №200611302. Приоритет от 18.04.2006). При перерывах в горении дуги капля, застывшая на торце электродной проволоки не препятствует зажиганию дуги на токе 2-5 А.
Сварка в углекислом газе проволокой диаметром 0,8 мм применяется для ремонта кузовов автомобилей. При питании дуги от традиционных источников питания минимальный ток для диаметра проволоки 0,8 мм – 50 А, а для диаметра проволоки 1,2 мм – 80 А [4]. Данное обстоятельство затрудняет сварку стали толщиной 0,5-0,7 мм без прожогов.
Разработан самоорганизующийся (синергетический) процесс сварки короткой дугой, расширяющий минимальные режимы по току для диаметра электродной проволоки 0,8 мм – 18 А, а для диаметра 1,2 мм – 40 А [5].
Также получено хорошее формирование швов в углекислом газе на обратной полярности на следующих режимах наплавки: dПР=0,8 мм, UХХ=61 В (без конденсаторов –
23,75 В), IД=10-30 А, UД=19-19,5 В, вылет – 10
мм, расход газа – 10 литров в минуту, скорость наплавки 5-17 м/ч. На аналогичных режимах минимальный ток для
проволоки диаметром 1,2 мм составляет 45-50 А.
Процесс горения происходит с короткими замыканиями, разбрызгивание минимальное.
На токе 10-12 А визуально различимы капли на торце вылета.
Наклон внешней характеристики выпрямителя составлял 0,037 В/А, индуктивность дросселя – 0,6 мГн, скорость подачи проволоки 55,5 м/ч.
Всвязи со сложностью слежения за стыком при автоматической сварке швов переменной кривизны полуавтоматом проволокой диаметром 0,8 мм на токе 10-12,5
Асваривалась малоуглеродистая сталь толщиной 0,6-0,7 мм «на весу». Горелка направлялась «углом назад». С целью уменьшения вероятности прожогов дугу следует направлять на жидкую ванну расплавленного металла. На токе 10-12,5 А обеспечивается полное проплавление при ширине шва 3,8-4,2 мм и высоте усиления 1,5-2 мм. Также обеспечивается хорошее формирование шва при скорости сварки 5 м/ч в автоматическом режиме.
Имеются сведения о применении аргона и азота для сварки стали 1Х18Н9Т плавящимся электродом [6].
Вавтоматическом режиме проволокой 1Х18Н9Т диаметром 0,8 мм в азоте высокой чистоты и в аргоне наплавлялись одиночные валики на малоуглеродистую сталь толщиной 0,6 мм, зачищенную до металлического блеска.
При наплавке в азоте на режимах аналогичных в углекислом газе сварочный ток был на 25 % меньше. При сварочном токе 1012 А, скорости подачи проволоки 73,5 м/ч и скорости сварки 5 м/ч обеспечивается хорошее формирование швов с полным проплавлением и минимальным разбрызгиванием.
При наплавке в азоте на токе 10-12 А индуктивность дросселя составляла 1,24 мГн. Увеличение индуктивности дросселя до 2,5 мГн ухудшает формирование швов.
На данных режимах при выключенных конденсаторах и без индуктивности в сварочной цепи формирование наплавленных валиков неудовлетворительное.
При хорошем формировании наплавленных валиков в углекислом газе и азоте на осциллограммах тока и напряжения наблюдаются короткие замыкания.
При наплавке проволокой 1Х18Н9Т диаметром 0,8 мм в аргоне на малоуглеродистую сталь толщиной 0,7 мм, с индуктивностью сварочной цепи 0,6 и 1,24 мГн и скорости подачи 73,5 м/ч наблюдается крупнокапельный перенос с редкими
342
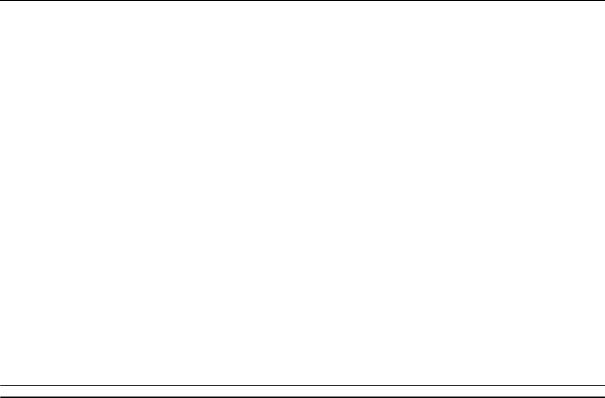
Современные техника и технологии 2007
короткими замыканиями. Вместо шва на |
рук. Работы Н.Г. Дюргеров. – Ростов на Дону, |
|||||||
изделии фиксируются отдельные капли. |
2005. – 39 с. |
|
|
|
||||
Выводы: |
|
|
3. |
Ленивкин, |
В.А. |
Технологические |
||
|
|
свойства сварочной дуги в защитных газах / |
||||||
1. Разработан способ зажигания дуги |
В.А. Ленивкин, Н.Г. Дюргеров, Х.Н. Сагиров. – |
|||||||
плавящимся электродом. |
|
М.: Машиностроение, 1989. – 264 с. |
|
|||||
2. |
Впервые |
|
зафиксировано |
4. |
Потапьевский, |
А.Г. Сварка в защитных |
||
формирование валиков в углекислом газе и |
газах плавящимся электродом / А.Г. |
|||||||
азоте плавящимся электродом на токе 10-12 |
Потапьевский. – М.: Машиностроение, 1974. – |
|||||||
А. |
|
|
|
240 с. |
|
|
|
|
|
|
|
|
5. |
Сагиров, |
Д.Х. |
Разработка |
|
ЛИТЕРАТУРА: |
|
|
самоорганизующегося |
процесса |
и |
|||
1. |
Сагиров, Х.Н. Зажигание сварочной дуги |
оборудования для сварки короткой дугой в |
||||||
/ Х.Н. Сагиров, Н.Г. Дюргеров, И.С. Морозкин. |
углекислом газе: автореферат дис. … канд. |
|||||||
– Ростов на Дону.: Изд-во «ГЕФЕСТ», 1999. – |
техн. наук.: 05.03.06 / Д.Х. Сагиров; рук. |
|||||||
200 с. |
|
|
работы Н.Г. Дюргеров. – Ростов на Дону., |
|||||
2. |
Морозкин, |
И.С. |
Управление |
2006. – 21 с. |
|
|
|
|
электрическими |
и |
механическими |
6. Медовар, Б.И. Сварка жаропрочных |
|||||
параметрами процесса зажигания дуги при |
аустенитных сталей и сплавов / Б.И. |
|||||||
механизированной сварке: автореферат дис. |
Медовар, М.: Машиностроение, 1966. 428 с. |
|
||||||
… докт. техн. наук: 05.03.06 / И.С. Морозкин, |
|
|
|
|
|
ПРОЕКТИРОВАНИЕ МАРШРУТОВ ОБРАБОТКИ ДЕТАЛЕЙ С ИСПОЛЬЗОВАНИЕМ ГРАФОВЫХ СТРУКТУР
Михайлов С.Г., Инхеев Д.Б., Елаева Н.К., Восточно-Сибирский государственный технологический университет,
г. Улан-Удэ, ул. Ключевская,40а, tmmskesstu@mail.ru
Работа |
по |
построению |
маршрутов |
• |
детали гостированные (болты, винты, |
|||||
обработки новых изделий остаётся наиболее |
гайки…); |
|
|
|||||||
трудоемким |
этапом |
в |
|
деятельности |
• |
детали высокой степени унификации |
||||
технолога. Так как в ряде изделий |
(валы, втулки, зубчатые колеса…); |
|
||||||||
используется |
|
большое |
|
количество |
• детали средней степени унификации, |
|||||
элементов, хорошо поддающихся типизации и |
не являющиеся типовыми, но относящиеся к |
|||||||||
унификации, работа технолога может быть в |
одной группе, в которой может быть |
|||||||||
достаточной |
степени |
автоматизирована за |
построена одна деталь, включающая все |
|||||||
счет возможности выполнения формализации |
элементы группы; |
|
|
|||||||
сведений о процессах и деталях. Благодаря |
• |
оригинальные детали, которые могут |
||||||||
этому сокращаются в 1,5-2 раза сроки |
быть составлены на основе классификации |
|||||||||
разработки отдельных видов изделий, а |
элементарных поверхностей. |
|
||||||||
также в 2-3 раза уменьшается объем |
Разработанная |
программа |
||||||||
конструкторско-технологической |
|
автоматизированного |
проектирования |
|||||||
документации. Все это дает возможность |
маршрутов обработки, основанная на |
|||||||||
уменьшить |
количество |
проектируемой |
комплексе подпрограмм, |
позволяет: |
|
|||||
оснастки, увеличить серийность производства |
• |
получить |
конструкторско- |
|||||||
и т.д. |
|
|
|
|
|
|||||
|
|
|
|
|
технологический код детали; |
|
||||
На первом |
этапе |
необходимо провести |
все |
|||||||
глубокий анализ изделий, выпускаемых |
• |
автоматически |
получить |
|||||||
возможные маршруты обработки этой детали; |
||||||||||
предприятием и спрогнозировать развитие |
• |
из всех возможных вариантов |
||||||||
деталей-аналогов. Исходя из конструктивных |
||||||||||
выбрать тот, который удовлетворяет нашим |
||||||||||
и габаритных особенностей, проводят |
условиям, или найти оптимальный маршрут |
|||||||||
классификацию и унификацию деталей и их |
автоматически по заданным параметрам; |
|
||||||||
элементов. По |
степени унификации можно |
|
|
|
|
выделить:
343

XIII Международная научно-практическая конференция «СОВРЕМЕННЫЕ ТЕХНИКА И ТЕХНОЛОГИИ»
• |
автоматически |
заполнить |
графа связей между действиями (видами |
||||
маршрутную карту обработки детали. |
|
обработки), используется матрица смежности |
|||||
Программа |
|
разработана |
с |
P*P, где Р – количество действий (рис.1). |
|||
использованием |
сетевых |
моделей [1], |
где |
|
|||
|
|
|
|
|
|
1, если вершина vi смежна с вершиной v j , |
|
поиск |
маршрутов |
осуществляется проходом |
P[i, j] = |
|
|||
|
|||||||
по графу. Граф представляет собой |
0, если вершины vi и v j не смежны. |
||||||
|
|||||||
множество |
действий, |
связанных |
и |
|
|
||
упорядоченных между собой. Для описания |
|
|
|
|
Рис.1 матрица смежности [PxP] |
|
|
||
При проходе по графу используются |
количество действий, F – количество условий |
|||||
данные о самих действиях (данные о |
(рис.2). |
|
|
|||
конструкторско-технологических |
|
1, если действиеvi требует условиеv j , |
||||
характеристиках |
деталей), |
которые |
PF[i, j] = |
|
|
|
|
0, иначе. |
|||||
представлены в виде матрицы P*F, где Р – |
|
|||||
|
|
|
|
|
|
|
Рис.2 Матрица необходимых условий [PxF] |
|
|||||
Принцип |
унификации |
реализуется |
с |
конструкторско-технологический код. На |
|||||
помощью |
конструкторско-технологического |
основе |
кода |
формируется |
матрица |
||||
классификатора, |
где |
с |
помощью |
ограничений V*F, V – класс свойств, F – |
|||||
информационно-поисковой |
системы |
по |
количество условий (рис.3). |
|
|||||
текстовому |
описанию детали |
формируется |
|
|
|
|
Рис.3 Матрица ограничений [VxF]
В результате обработки и анализа данных получаем все возможные маршруты обработки данной детали (Рис.4).
344

Современные техника и технологии 2007
Рис.4 Вариант маршрута обработки детали
Разработанный комплекс создан в программной среде MS EXCEL и Delphi и состоит из двух частей. Первая часть включает опрос экспертов, учитывая их компетентность, присваивает каждому эксперту свой вес и на основе этого и проставленных оценок оценивает конечные маршруты. Во второй части для автоматизации выбора оптимального маршрута обработки детали учитывается экспертная оценка и ряд числовых критериев. Программа позволяет получить оптимальный
вариант маршрута обработки детали и автоматически заполняет маршрутную карту обработки детали.
Система выполнена с учетом иерархического принципа, является открытой для дальнейшего наращивания.
ЛИТЕРАТУРА:
1. Диалоговое проектирование технологических процессов / Н.М.Капустин, В.В.Павлов, Л.А.Козлов и др. М.: Машиностроение, 1983,275с.
ИССЛЕДОВАНИЕ НАПРЯЖЕННО-ДЕФОРМИРОВАННОГО СОСТОЯНИЯ РАЗНОМОДУЛЬНЫХ ТОНКОСТЕННЫХ ЭЛЕМЕНТОВ
С РАЗРЫВНЫМИ ПАРАМЕТРАМИ
Моисеенко М.О.
Томский Государственный архитектурно-строительный университет,
Россия, г.Томск, пл.Соляная,2
E-mail: MMO77@mail.ru
В работе рассматривается система прямоугольных в плане пологих оболочек и пластин, которые могут располагаться под углом друг к другу, образуя складку, под действием поперечной нагрузки. Панели подкреплены в продольном направлении
дискретно расположенными призматическими рёбрами жёсткости, с постоянным поперечным сечением hp * bp, с эксцентриситетом η относительно срединной
поверхности панели, а также, подкреплены перекрёстной системой второстепенных рёбер и имеют прямоугольные отверстия.
Граничные условия в продольном направлении постоянны, а в поперечном направлении могут быть разными. Материал панелей и рёбер разномодульный. Толщина панелей меняется, а также может иметь начальные погиби – W0. Перемещения панелей сравнимы с их толщиной. Определяется НДС в панелях и рёбрах по модели С.П. Тимошенко [2], для которой
345
XIII Международная научно-практическая конференция «СОВРЕМЕННЫЕ ТЕХНИКА И ТЕХНОЛОГИИ»
характерно разделение перемещений, вызванных изгибом и сдвигом.
Деформации панелей ex(z),e(yz),ez(z) записываются через кривизны k1, k2 ,
перемещения u, v, w, w0 соответственно вдоль координатных осей. Для панели:
ex(z) = ∂u |
+ kx w + |
1 |
|
( ∂w)2 − |
1 |
|
( ∂w0 )2 |
− z |
∂ϕx , |
||||||||||||||||
|
|
|
|
||||||||||||||||||||||
|
|
|
∂x |
|
|
|
|
2 |
|
∂x |
2 |
|
∂x |
|
|
∂x |
|||||||||
exy(z) = ∂v + ∂u kxw + |
∂w ∂w |
|
− ∂w0 ∂w0 − |
|
|
|
|||||||||||||||||||
|
|
|
∂x |
∂y |
|
|
|
|
∂x ∂y |
|
|
|
|
|
∂x ∂y |
|
|
|
|
||||||
− z( |
∂ϕx + |
∂ϕy |
) . |
|
x ↔ y |
(1) |
|
|
|
|
|
||||||||||||||
|
|
|
|
|
|
||||||||||||||||||||
|
|
∂y |
∂x |
|
|
|
|
|
|
|
|
|
|
|
|
|
|
|
|
|
|
|
|||
Деформации для арматуры в панели: |
|
|
|
||||||||||||||||||||||
e |
xа |
= |
∂u |
+ k |
x |
w + |
1 |
( |
∂w |
)2 − |
|
1 |
( |
|
∂w0 |
)2 − h |
|
∂ϕx |
, |
||||||
|
2 |
|
2 |
|
|
||||||||||||||||||||
|
|
∂x |
|
|
|
|
|
∂x |
|
|
∂x |
ax ∂x |
|||||||||||||
|
|
|
|
|
|
|
|
|
x ↔ y |
(2) |
|
|
|
|
|
|
|
||||||||
Деформации |
|
|
продольных |
e(z) |
|
|
и |
||||||||||||||||||
|
|
|
|
|
|
|
|
|
|
|
|
|
|
|
|
|
|
|
|
|
|
1 |
|
|
|
поперечных e2(z) рёбер записываем с учётом эксцентриситетов − η1,η2 относительно срединной поверхности:
(z) |
|
|
|
∂u |
+ k x w |
|
|
1 |
|
|
∂w |
|
2 |
|
|
1 |
|
|
∂w0 |
|
|
2 |
|
h ∂ϕx |
|
|||||||||||||||||||||
e1 |
|
= |
|
∂x |
+ |
|
|
( ∂x ) |
|
− |
|
|
( |
|
|
|
|
|
) |
|
|
− |
|
|
|
|
− |
|||||||||||||||||||
|
|
2 |
|
|
2 |
|
∂x |
|
|
|
|
2 |
|
|
∂x |
|||||||||||||||||||||||||||||||
|
|
|
|
|
|
|
|
|
− (z − |
h |
) |
∂ϕ'x , |
x ↔ y , 1 ↔ 2 |
|
|
|
|
|
|
|
||||||||||||||||||||||||||
|
|
|
|
|
|
|
|
|
|
|
|
|
|
|
|
|
|
|||||||||||||||||||||||||||||
|
|
|
|
|
|
|
|
|
|
|
|
2 |
|
|
|
∂x |
|
|
|
|
|
|
|
|
|
|
|
|
∂w0 ∂w0 |
|
|
|
|
|
||||||||||||
|
|
e(z) |
= |
∂u |
+ |
∂v |
+ |
∂w ∂w |
|
− |
− |
|
|
|
|
|||||||||||||||||||||||||||||||
|
|
|
|
12 |
|
|
∂y |
|
|
|
∂x |
|
|
∂x ∂y |
|
|
|
|
∂x ∂y |
|
|
|
|
|
|
|||||||||||||||||||||
|
|
|
|
h |
|
|
|
∂ϕy |
|
|
∂ϕ |
x |
|
|
|
|
|
|
|
|
|
h |
|
|
|
∂ϕ′ |
|
|
|
|
∂ϕ′y |
|
|
|
|
|||||||||||
|
− |
|
|
( |
|
|
|
+ |
|
|
|
|
|
|
) −(z |
|
− |
|
|
) |
( |
|
|
|
x |
+ |
|
|
|
|
) . |
|
||||||||||||||
|
2 |
|
|
∂x |
|
|
|
|
∂y |
|
2 |
|
|
|
|
|
∂x |
|
|
|||||||||||||||||||||||||||
|
|
|
|
|
|
|
|
|
|
|
|
|
|
|
|
|
|
|
|
|
|
|
|
|
|
∂y |
|
|
|
|
|
|
|
|
|
|||||||||||
|
|
|
|
|
|
|
|
|
|
|
|
|
|
|
|
|
|
|
(3) |
|
|
|
|
|
|
|
|
|
|
|
|
|
|
|
|
|
|
|
|
|
|
|
|
|||
Деформация арматуры в рёбрах: |
|
|
|
|
|
|
|
|
||||||||||||||||||||||||||||||||||||||
|
|
e |
|
|
|
|
= ∂u |
+ k |
x |
w + |
1 |
( |
∂w)2 |
− |
|
1 |
( |
∂w0 )2 − |
|
|||||||||||||||||||||||||||
|
|
|
|
|
|
2 |
2 |
|
||||||||||||||||||||||||||||||||||||||
|
|
|
|
1ар |
∂x |
|
|
|
|
|
|
|
|
|
|
|
∂x |
|
|
|
|
|
|
∂x |
|
|
|
|
|
|
|
|||||||||||||||
|
− |
h |
|
∂ϕx |
−(h1ap − |
h |
) |
∂ϕ'x |
, x ↔ y , 1 ↔ 2 |
|
||||||||||||||||||||||||||||||||||||
|
|
|
|
|
|
|||||||||||||||||||||||||||||||||||||||||
|
|
|
|
2 |
|
|
|
∂x |
|
|
|
|
|
|
|
|
|
2 |
|
|
|
∂x |
|
|
|
|
|
|
|
|
|
|
|
|
|
|
|
|
|
|
||||||
|
|
|
|
|
|
|
|
|
|
|
|
|
|
|
|
|
|
|
|
|
(4) |
|
|
|
|
|
|
|
|
|
|
|
|
|
|
|
|
|
|
|
|
Где: ϕx ,ϕy ― углы поворота касательной
соответственно в плоскостях xoz, yoz в панели.
ϕ |
= |
∂w |
+ |
αh2 |
2ϕ |
; x ↔ y , 1 ↔ 2 |
|
∂x |
6(1− ν) |
||||||
1х |
|
|
1x |
|
|||
|
|
|
|
|
(5) |
|
Заменяются упрощенными зависимостями:
ϕ |
= |
∂w |
+ |
αh2 |
2 ( |
∂w); x ↔ y , 1 ↔ 2 |
|
∂x |
6(1−ν) |
||||||
1х |
|
|
|
∂x |
(6)
Где α - числовой коэффициент, связывающий средние касательные напряжения в центре тяжести сечения. Выражения (6) отличаются от (5) тем, что под оператором Лапласа стоит не угол поворота
от изгиба, а суммарный угол поворота касательной. В качестве физических уравнений принимаются соотношения нелинейно-упругого материала с переменными параметрами упругости Ес,ν
[1]. Для панели:
Е(z) = |
σ |
i = E |
|
|
4 |
|
E2 |
e2 ) , |
||||||
|
|
(1− |
|
|
|
0 |
|
|||||||
|
|
27 R2 |
||||||||||||
с |
|
ei |
0 |
|
|
i |
||||||||
|
|
|
|
|
|
|
|
|
|
|
|
пр |
|
|
σ(xz) = |
Е(z) |
(ex(z) |
+ νe(yz) ) ; |
|
||||||||||
|
c |
|
|
x ↔ y ; |
||||||||||
|
−ν2 |
|||||||||||||
1 |
|
|
|
|
|
|
|
|
|
|
||||
|
(z) |
|
|
Еc(z) |
|
(z) |
|
|
|
|
|
|||
τx |
|
= |
|
|
|
|
exy |
. |
|
(7) |
||||
|
|
2(1 + ν) |
|
|||||||||||
|
|
|
|
|
|
|
|
|
|
|
|
|||
Для арматуры в панели: |
|
|
|
|
|
|
||||||||
σха = Ecaexa ; |
σyа = Ecaeya ; |
(8) |
||||||||||||
|
|
|
|
|
Для ребра: |
|
|
|
||||||
σ1(z) = Ec(z)e1(z) ; |
|
|
|
1 ↔ 2 |
(9) |
|||||||||
Для арматуры ребра: |
|
|
|
|
|
|
|
|
||||||
σ1ар = Ecаe1ар; |
|
|
1 ↔ 2 |
(10) |
Секущие модули упругости E cj( z1) , E cj( z2) ,
функции сжимаемости материала μ(cjz1) , μ(cjz2) ,
модуль сдвига G (jz) , коэффициенты линейного расширения α (jz1T) , α (jz2)T
существенно зависят от знаков напряжений и их значений для разномодульного материала. В работе взята модифицированная модель С.А. Амбарцумяна, изложенная в работе [3],
при этом если σ (xz ) 0 , σ (yxz ) 0 ,то
( z ) |
|
1 |
|
|
|
|
σ (xz ) − σ (yz ) |
|
, |
|||||
G j |
= |
|
|
|
|
|
|
|
|
|
|
|
|
|
2 |
|
(1 + μ |
( z ) |
) |
σ (xz ) |
− (1 |
+ μ |
( z ) |
) |
σ (yz ) |
||||
|
|
|
|
cj 1 |
|
cj 2 |
|
|
|
|||||
|
|
|
E ( z ) |
E ( z ) |
||||||||||
|
|
|
|
|
|
|
|
|
||||||
|
|
|
|
|
|
|
cj 1 |
|
|
|
|
cj 2 |
(11)
где
cj1 = {( j = 1 σ(xz) ≤ 0) ( j = 2 σ(xz) ≥ 0;
cj 2 = {( j = 1 σ (yz ) ≤ 0 ) ( j = 2 σ (yz ) ≥ 0 .
Усилия и моменты, отнесённые к единице
длины сечения, имеют вид: |
|
|
|
|
|
|
|
|||||||||||
N |
x.o |
= ∫0,5h σ |
x.o |
dz; |
|
M |
x.o |
|
= ∫0,5h |
|
σ |
x.o |
zdz; |
|||||
|
|
−0,5h |
|
|
|
|
−0,5h |
|
|
|
||||||||
H o = ∫−0,50,5hh τxy.o zdz; |
|
|
|
|
|
|
|
|
|
|||||||||
N x. p = ∫−0,50,5hphp σx. p dz; |
|
|
|
|
|
|
|
|
|
|||||||||
M |
x. p |
= |
∫0,5hp |
|
σ |
x. p |
zdz; |
M |
kp |
= ∫0,5hp |
τ |
zy. p |
zdz. |
|||||
|
|
|
−0,5hp |
|
|
|
|
−0,5hp |
|
|
|
|||||||
So = ∫−00,5,5hh τxy.odz; |
|
x ↔ y . |
(12) |
|
|
346

Современные техника и технологии 2007
Приведённые соотношения позволяют определить НДС в панелях и рёбрах при известных перемещениях конструкции.
Условие появления трещины разрушения принимаем в виде наиболее распространённых критериев прочности: Г. Генки, Г.А. Гениева, Н.И. Карпенко [2]. При выполнении одного из этих условий для любого волокна, в зависимости от знака и величин полученных напряжений, выявляются зоны пластичности или возникновение трещин.
В качестве элементов основной системы выбираем целую панель с второстепенными рёбрами и целое подкрепляющее главное ребро [1], так как это позволяет обходиться меньшим числом неизвестных. Вдоль каждой узловой линии по всей длине пролёта вводятся непрерывно распределённые связи четырёх типов, продольные, поперечные, вертикальные и угловые вокруг продольной оси. Расчётная схема получаем по методу перемещений, а неизвестные амплитуды соответствующих функциональных перемещений находим из условия стационарности энергии системы. Алгоритм расчёта строим на минимизации функционала энергии, выраженного через варьируемые параметры функций перемещений, методом сопряжённых градиентов, на каждом этапе приближения [1]. Решение нелинейной задачи на этапе нагружения q + q строится с помощью
метода переменных параметров упругости с использованием секущих модулей упругости и функций сжимаемости предыдущего шага. Интегрирование по объёму элементов конструкции проводится численно.
Пример 1. Исследование влияния стрелы подъёма разномодульной подкреплённой пологой оболочки на её напряжённодеформированное состояние
На рис. 2 представлены основные размеры оболочки и подкрепляющих рёбер. Здесь же приведены графики зависимости относительных прогибов и интенсивности напряжений в зависимости от относительной высоты подъёма.
Рис. 2. Влияния относительной стрелы подъёма разномодульной, подкреплённой пологой оболочки на её напряжённодеформированное состояние при q = 0,5 МПа: а – геометрические и физические характеристики; б – график изменения интенсивности напряжений возле ребра для волокон панели: ВН – нижних; ВВ – верхних; г
– график изменения интенсивности напряжений в центре панели для волокон панели: СН – нижних; СВ – верхних
ЛИТЕРАТУРА:
1.Попов О.Н., Малиновский А.П., Моисеенко М.О.: Нелинейные задачи ребристых оболочек. ― Томск: изд-во Томск. гос. архит.-строит. ун-та, 2004. ― 172 с.
2.Санджаровский Р.С., Мусабаев Т.Т.: Расчёт неупругих композитных оболочек и пластин с учётом поперечных сдвигов // Изв. вузов “Строительство”. 1999. №8. – С. 13-22.
3.Петров В.В., Овчинников И.Г., Иноземцев В.К.: Деформирование элементов конструкций из нелинейного разномодульного неоднородного материала. Изд-во Сарат. ун-
та, 1989.160 с.
347

XIII Международная научно-практическая конференция «СОВРЕМЕННЫЕ ТЕХНИКА И ТЕХНОЛОГИИ»
ПРОБЛЕМЫ ГИДРОУСИЛЕНИЯ В ЗАМКНУТЫХ ГИДРАВЛИЧЕСКИХ СИСТЕМАХ
Мошкин С.Н., Дворников Л.Т.
Сибирский государственный индустриальный университет, Россия, г.Новокузнецк, ул. Кирова, 42
E-mail: hochusubaru@mail.ru
Существует множество способов приложения усилия на объект. Один из способов – создание усилия при помощи гидроцилиндра. Гидроцилиндр – устройство, преобразующее энергию потока рабочей среды (жидкости) в энергию поступательного движения [1]. Одним из видов гидроцилиндров является поршневой гидроцилиндр двустороннего действия с односторонним штоком (рисунок 1).
S q
F
Рисунок 1 - Поршневой гидроцилиндр двустороннего действия с односторонним штоком
Проблемой такого гидроцилиндра является невозможность изменения кинематических и силовых параметров между входным и выходным звеньями. Эту особенность можно устранить, применяя гидравлический преобразователь, в частности – гидравлический усилитель.
Хорошо известна теория сообщающихся сосудов. Если на шток поршня 1 (рисунок 2,а) сечением S1 воздействовать силой F1, то под поршнем в гидросистеме возникнет давление
p = |
F1 |
|
|
|
S |
, |
(1) |
||
|
||||
|
1 |
а на штоке второго поршня сечением S2, очевидно, можно получить усилие
S2 |
|
F2 = p S2 = F1 S1 . |
(2) |
нажатии на поршень силой F1 (рисунок 2,b) под нижним поршнем возникнет давление p, которое будет воздействовать и на верхний поршень. Если рассмотреть равновесие верхнего поршня вместе со штоком, то вполне очевидным окажется соотношение
F2 = p S2 .
(3)
Рисунок 2
Из условия равновесия нижнего поршня можно записать, что
F1 + F2 = p S1 . |
(4) |
Подставив значение p из (3) в (4), легко получим, что
F |
= |
F1 S2 |
|
|
|
|
|||
2 |
|
S1 − S2 . |
(5) |
|
|
|
В соотношении (5) содержится тот эффект, который и был заявлен авторами (по авторскому свидетельству [2]). Он заключается в возможности получить усилие F2 теоретически сколько угодно большим, приближая значения S2 и S1 и тем, уменьшая знаменатель дроби.
Если же штоки поршней сообщающихся сосудов соединить между собой, например, так как показано на рис. 2,b, то соотношение между силами и давлением в гидросистеме существенно изменится. Действительно, при
348

Современные техника и технологии 2007
Рисунок 3
Коэффициентом усиления при этом является отношение
k = |
F2 |
= |
|
|
S2 |
|
|
|
|
F |
S |
1 |
− S |
2 . |
(6) |
||||
|
|
||||||||
|
1 |
|
|
|
Уже при значении S2/S1 = 0,9 (рисунок 3) можно добиться k = 9, а при значении S2/S1 = 0,98 получим k = 49.
В 1972 г. Госкомитетом по делам изобретений СССР было принято решение о признании вышеописанной системы изобретением и о выдаче на него Авторского свидетельства № 360832 [2]. Однако, одновременно было принято решение Комитета по делам изобретений СССР о признании этого изобретения не подлежащим публикации в открытой печати.
Хохриным М.В. и Дворниковым Л.Т. было предложено использовать преобразователи по А.с. № 360832 [2] в виде горизонтального каскада. Такой каскад, состоящий из трех пар взаимодействующих между собой гидроцилиндров, показан на рисунке 4 (по патенту [3])
Рисунок 4
Взаимодействующие пары гидроцилиндров обозначим цифрами 1, 2 и 3. Первую пару назовем силовой, вторую – промежуточной, третью – рабочей.
Коэффициент усиления в данном гидравлическом преобразователе будет равен
k∑ = |
|
D2 |
(D2 |
− d 2 |
) (D2 |
− d 2 |
) |
|
|
||||
|
32 |
|
21 |
|
21 |
|
31 |
|
31 |
|
|
|
|
(D2 |
− D2 |
) (D2 |
− |
D2 |
) (D2 |
− D2 |
) |
. |
|||||
11 |
|
12 |
|
21 |
|
22 |
|
31 |
|
32 |
|
(7)
Укажем на то, что все приведенные конструкции имеют один важный недостаток - объект воздействия в них не может оставаться неподвижным. Эта проблема также может быть разрешена, что было показано в дипломном проекте Зимарина П.А., защищенным в1999 году в Сибирском Государственном Индустриальном Университете. В проекте был разработан гидравлический пресс, схема которого приведена на рисунке 5.
Пресс (рисунок 5) состоит из нагрузочного гидроцилиндра 1, неподвижных штока и поршня 2 нагрузочного гидроцилиндра, выполненных за одно целое со столом 3 пресса, подвижных тяг 4, жестко соединяющих нагрузочный гидроцилиндр и рабочий гидроцилиндр 5, одна из тяг при этом одновременно выполняет роль трубопровода 6. Шток поршня 7 рабочего гидроцилиндра выполняет функцию прессующего пуансона, который взаимодействует с объектом прессования 8.
Рисунок 5 Работает пресс следующим образом.
При подаче рабочей жидкости в надпоршневую полость нагрузочного цилиндра 1, последний из-за того, что шток и поршень 2 жестко связаны со столом и станиной, получит движение вверх. Через тягу 4 цилиндр 1 увлечет за собой рабочий гидроцилиндр 5. При этом в бесштоковой полости нагрузочного гидроцилиндра возникнет давление р, такое же давление возникнет и в бесштоковой полости рабочего
349

XIII Международная научно-практическая конференция «СОВРЕМЕННЫЕ ТЕХНИКА И ТЕХНОЛОГИИ»
гидроцилиндра 5. Так как площадь сечения |
Таким образом, в данном докладе |
||||
нижнего цилиндра S1 принимается большей |
описаны способы увеличения выходного |
||||
площади сечения верхнего цилиндра S2, то |
давления системы |
с использованием |
|||
вертикальное (вниз) смещение штока 7 |
гидравлических |
преобразователей |
|||
окажется |
большим, |
чем |
смещение |
давления. |
|
нагрузочного гидроцилиндра 1, что приведет к |
|
|
|||
воздействию штока 7 на объект прессования |
ЛИТЕРАТУРА: |
|
|||
8, т.е. к выполнению рабочего процесса. |
1. Крайнев А.Ф. Словарь – справочник |
||||
Если подать жидкость в штоковую полость |
по механизмам. Москва |
||||
рабочего цилиндра 5, поршень со штоком 7 |
"Машиностроение", 1987г. – 560 стр. |
||||
отойдет от объекта прессования, рабочий |
2. SU, авторское свидетельство |
||||
процесс закончится. |
|
|
№360832, кл. В 30 В 15/16, 1976. |
||
Используя |
несколько |
преобразователей в |
3. Патент №2191698, |
||
гидравлической системе можно подводя одно |
Преобразователь давления гидропресса |
||||
давление получать разное давление на |
/ Дворников Л.Т., Хохрин М.В. – Опубл. |
||||
выходах. |
|
|
|
27.10.2002 Бюл. №30. |
|
ГРАФИКИ ИЗНОСА ЗУБЬЕВ ЧЕРВЯЧНОЙ ФРЕЗЫ С ЗАБОРНЫМ КОНУСОМ И БЕЗ НЕГО В РАЗНЫЕ ПЕРИОДЫ
НАРЕЗАНИЯ КОЛЕСА ПРИ РАЗЛИЧНЫХ СПОСОБАХ ВРЕЗАНИЯ
Ничков А.В.
Уральский государственный технический университет – УПИ, Россия, г.Екатеринбург, ул. Мира, 19
E-mail: nav@delcam-ural.ru
При выборе оптимального варианта врезания червячной фрезы в заготовку необходимо располагать графиками износа зубьев червячной фрезы и длиной ее загруженного участка. Для этого была использована методика, базирующаяся на связи износа зубьев червячной фрезы с размерами срезаемых ими слоев [1].
Опыты отличались величиной и положением (L1) заборного конуса относительно межосевого перпендикуляра на момент окончания врезания фрезы в заготовку
испособом врезания: осевым, радиальным, тангенциальным, радиально-осевым, тангенциально-радиальным, тангенциальноосевым. Были определены графики износа зубьев червячной фрезы (рис.1) за период врезания (кривая 1), последующий период профилирования зубьев колеса (кривая 2) и суммарный график износа (кривая 3). Для червячных фрез с заборным конусом были получены графики износа при черновом
зубофрезеровании (рис.1,а–г), когда L1 =0 и одна из сторон зубьев колеса частично недопрофилируется, и при чистовом зубофрезеровании (рис.1,д-е), когда L1=–20мм
изубья колеса полностью профилируются. Для сравнительной оценки характера влияния
заборного конуса и способа врезания фрезы в заготовку на ее износ определены аналогичные графики износа червячной фрезы без заборного конуса при осевом (рис.1, ж) и радиальном (рис.1,з) врезании.
Расчеты выполнены для случая нарезания зубчатого колеса (m=6мм, z1=60, β1=20°, ширина 60мм, материал – 18ХНМА) по технологической схеме I (направление витков фрезы и зубьев колеса разноименное, осевая подача встречная) червячной фрезой (Rао=75мм, z1O=1, zO=10) с углом заборного конуса ψ=0, 5° и 10°. Соотношения подач назначались такими, чтобы врезание происходило за 9 оборотов колеса. На рисунках указаны некоторые дополнительные условия проведения опытов, а именно, L1 – положение основания конуса относительно межосевого перпендикуляра в момент окончания врезания, и угол заборного конуса ψ.
Из анализа графиков износа зубьев фрезы можно сделать вывод о характере кривой износа, максимальной величине износа hmax, длине загруженного участка Lр фрезы с учетом профилирования зубьев колеса, коэффициенте
расхода инструмента kр= Lр hmax. Так, например, из графиков видна неравномерность
350
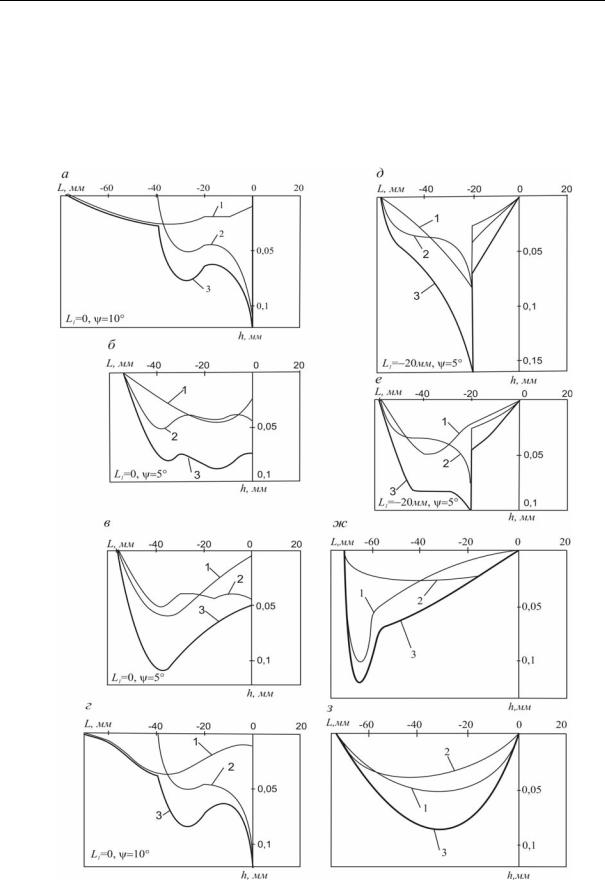
Современные техника и технологии 2007
износа зубьев фрезы из-за срезания ими разных слоев металла. Для случая чернового зубофрезерования наилучшим по всем параметрам оказался вариант на рис.1,б
(hmax=0,09мм, Lр=74мм, kр=6,7). Для чистового зубофрезерования по параметрам hmax и kр
лучшим оказался вариант на рис.1,з
(hmax=0,08мм, kр =7,4), а по параметру Lр –
варианты на рис,1,д,е (Lр=79мм). Таким образом, выбор способа врезания, наличие или
отсутствие заборного конуса, его положение L1 относительно межосевого перпендикуляра и угол ψ оказывают существенное влияние на износ и распределение износа по зубьям фрезы, вследствие чего эти параметры необходимо учитывать при конструировании инструмента и разработке технологического процесса обработки зубьев колеса.
1.
Рис.1. Графики износа зубьев червячной фрезы за период врезания (кривая 1), последующий период профилирования зубьев колеса (кривая 2) и суммарный график износа (кривая 3). Фреза с заборным конусом: а – врезание тангенциальное, б – радиальное, в –
351

XIII Международная научно-практическая конференция «СОВРЕМЕННЫЕ ТЕХНИКА И ТЕХНОЛОГИИ»
радиально-осевое, г – тангенциально-осевое, д –радиальное, е – тангенциально-радиальное. Фреза без заборного конуса: ж – врезание осевое, з – радиальное.
ЛИТЕРАТУРА:
1. Ничков А.Г. Основы комплексного исследования процесса зубофрезерования и оптимизации его конструктивных и технологических параметров в простых и комбинированных схемах нарезания зубчатых колес червячными фрезами / Автореферат дисс. на соискание ученой степени д-ра. техн. наук. Тула, 1991.
ИСТОЧНИК ПАРОВ МЕТАЛЛОВ
Овчинников И.С, Петрова Ю.С, Ярославцева Т.Ю 634050, Томск -50, пр. Ленина 40
Томский государственный университет систем управления и радиоэлектроники. (3822) 423394,
E-mail: ng@muma.tusur.ru
Аннотация. В работе рассматривается возможность получения пленок с высоким КПД испарения за счет учета взаимодействия потока пара и электронного пучка.
Суть проблемы. В настоящее время наиболее воспроизводимые пленки для микроэлектроники получают методом термического испарения материалов в вакууме. При этом КПД, равный отношению площади пленки к площади поверхности разлета паров очень низок и составляет 0,1%. Для ряда приборов микроэлектроники требуются пленки, легированные редкими материалами, но при таком малом КПД это наталкивается на экономические ограничения.
Пути решения проблемы. Одним из путей решения проблемы КПД является использование закономерностей взаимодействия молекул пара с направленным потоком заряженных частиц (ионов или электронов). В предельном случае
вприближении модели механического взаимодействия частиц часть частиц может отразиться от потока заряженных частиц как от «горячей сковородки».
Метод решения. В первом приближении поток пара имеет тепловые скорости. Частица
вэлектрическом поле может приобрести скорость выше тепловой.
Кинетическая энергия молекул описывается уравнением:
E = 32 kT = mv2 2
С другой стороны, энергия, приобретенная частицей в электрическом поле, выражается соотношением:
E = |
mv2 |
= eU |
|
2 |
|||
|
|
где: k- – постоянная Больцмана; Т – температура; m, v – масса и скорость частицы; е – заряд электрона; U – напряжение.
Таким образом, в зависимости от соотношения энергий частиц плазмы возможно изменение траекторий частиц пара. Из теории взаимодействия частиц следуют, что частицы пара можно отнести к тяжелым частицам, взаимодействующим с соизмеримыми по массе молекулами газа или ионами [1]. Взаимодействие электронов с паром может привести к ионизации молекул пара и изменению состава пленки.
Экспериментальные исследования. На рис.1 представлен молекулярный источник с высоким КПД испарения. Источник состоит из холодного алюминиевого катода и анода в виде трубы с боковыми отверстиями. Через катод пропущен держатель, удерживающий тигель и служащий формирователем кольцевого электронного пучка.
Источник работает следующим образом. Первоначально в объеме источника реализуется давление 1-5 Па. Затем система промывается инертным газом (гелием). На катод подается высокое напряжение (~5-10 кВ). В системе возникает высоковольтный тлеющий разряд. Ионы из плазмы разряда бомбардируют катод, из которого выбивают электроны. Электронный пучок током 5-10 мА генерируется в виде цилиндра, окружающего тигель. Затем на внутренний анод (формирователь пучка) 9 подается напряжение положительной полярности (~100
352

Современные техника и технологии 2007
В). Электронный поток устремляется на тигель и нагревает его. Степень нагрева может меняться с помощью потенциала, подаваемого на тигель. Первоначально удаляется поверхностное покрытие материала в тигле (стеарина на церии), препятствующего окислению металла. Затем из тигля испаряется материал, и разряд начинает гореть в парах испаряемого материала. Об этом свидетельствует изменение вольтамперной характеристики.
После прогрева тигля (5-10 мин) тигель с помощью держателя поднимается. Поворотом держателя тигля заслонка открывается. Давление пара превышает давление остаточного газа. Начинается диффузное испарение пара из тигля. Электронный пучок, воздействуя на поток пара, приводит к эффекту его экранирования, («как от горячей сковородки»), что уменьшает потери пара в радиальном направлении. Эффект экранирования объясняется тем, что скорость молекул пара – тепловая, а скорость частиц плазмы пучка выше тепловой и пропорциональна энергии пучка. Число молекул, имеющих радиальные скорости, после многократных отражений от электронного потока, также попадают на подложку. Пар начинает конденсироваться на подложку в виде пленки. В итоге достигаются малые потери испаряемого материала. Часть потерь обусловлена тем, что при испарении, часть пара испаряется в направлении, почти обратном первоначальному. С ростом энергии пучка эффект экранирования усиливается, достигая 100 % на срезе тигля при U>10 кВ. При испарении более тугоплавких материалов, наоборот, экранирование уменьшается.
Рис.1. Схема источника паров металлов. 1,3 – токовводы; 2,11 – изолятор; 4, 5 – составной катод; 6 – отверстие анода; 7,8 – тигель с металлом; 9,10 – стенки анода; 12 – уплотнение; 13, 15 – фланцы; 14 – сильфон; 16 – электронный луч; 17 – поток пара.
На рис.2 представлены характеристики при работе на различных давлениях на воздухе и на парах церия.
Рис.2. а) вольтамперная характеристика источника. 1-10 Па, 2-5Па, 3-1Па (рабочий газ-воздух);
б) управляющая характеристика источника от давления. 1- U=10кВ, 2-U=5 кВ; (рабочий газ-гелий).
Полученные результаты. Источник устойчиво работает при вакууме, обеспечиваемом механическим вакуумным насосом. Это открывает перспективы получение окисных пленок на смесях инертного газа и кислорода или на парах воды. КПД, оцененный по микро весовым измерениям, составил 50%. На гелии источник работает на более высоком давлении. По данным эллипсометрических измерений в пленке можно обеспечить относительно постоянный стехиометрический состав.
Выводы. Источник представляет интерес для напыления драгоценных материалов и окисных пленок. Экспериментальная модель может использоваться в лабораторных условиях.
ЛИТЕРАТУРА:
1. А.Н. Пустовит. Неупругие столкновения атомных частиц средних энергий. Качественная модель потерь энергии при столкновении. Труды 17 межд конф «Взаимодействие ионов с поверхностью ВИП
2005». Звенигород, Россия, 2005, с 562-563.
353

XIII Международная научно-практическая конференция «СОВРЕМЕННЫЕ ТЕХНИКА И ТЕХНОЛОГИИ»
РАСЧЕТ ИЗМЕНЕНИЯ РАЗМЕРОВ ТОЛСТОСТЕННЫХ ВТУЛОК С ОТВЕРСТИЯМИ МАЛОГО ДИАМЕТРА,
ОБРАБАТЫВАЕМЫМИ ДОРНОВАНИЕМ С БОЛЬШИМИ НАТЯГАМИ
Охотин И.С., Скворцов В.Ф.
Томский политехнический университет, Россия, г. Томск, пр. Ленина, 30
E-mail: ngc224@yandex.ru
Дорнование отверстий малого диаметра
( d =1…5 |
мм) |
в |
толстостенных |
втулках |
( D / d ≥ 3, |
где |
D |
- наружный |
диаметр), |
выполняемое с большими натягами (до 0,1 d и более) является эффективным методом их отделочной обработки [1]. Дорнование может выполняться непосредственно после сверления отверстий и обеспечивать их высокую точность и качество поверхностного слоя. Вместе с тем, при дорновании с
большими |
натягами |
по |
наиболее |
распространенной |
схеме |
сжатия |
|
наблюдается |
существенное |
увеличение |
наружного диаметра втулок и их некоторое укорочение [2]. Проектируя операцию дорнования отверстий, указанные изменения размеров втулок необходимо заранее рассчитать.
Для определения наружного диаметра втулок после дорнования, следуя [3], запишем очевидные соотношения
D0 = d0 + 2t0 ; |
D = d + 2t , |
где D0 , D , d0 , |
d , t0 , t - соответственно, |
наружный диаметр, диаметр отверстия и толщина стенки втулки до и после дорнования. Вычитая из первого соотношения второе, после преобразований получим
|
t |
|
|
|
|
|
a |
|
|
|
d |
0 |
0,785 |
|
|||
|
|
|
|
|
|
|
|
|
|
|
|
|
|
|
. |
(3) |
|
|
t |
|
=1−0,689 d |
0 |
|
D |
|
||||||||||
|
|
0 |
|
|
|
|
|
|
|
|
0 |
|
|
|
|||
Введем обозначение |
|
|
|||||||||||||||
|
|
|
|
a |
|
d |
0 |
0,785 |
|
|
|||||||
|
|
|
|
|
|
|
|
|
|
|
|
|
= K , |
|
|||
1 − 0,689 d |
|
D |
|
|
|
(4) |
|||||||||||
|
|
|
|
|
|
||||||||||||
|
|
|
|
|
0 |
|
|
|
0 |
|
|
|
|
|
|
с учетом которого уравнения (1) и (2) соответственно примут вид
D − D0 |
= d − d0 − 2t0 (1 − K) ; |
(5) |
D − D0 |
= a − 2t0 (1 − K ) . |
(6) |
Для определения высоты втулок после дорнования воспользуемся условием постоянства объема металла при пластическом деформировании. Исходя из этого условия, запишем
L = L |
d0 +t0 |
|
t0 |
, |
(7) |
|
d +t |
t |
|||||
0 |
|
|
|
где L0 , L - соответственно высота втулок
до и после дорнования. Учитывая принятое обозначение (4), из уравнения (7) будем иметь
|
|
|
|
t |
|
|
D − D0 |
= d − d0 |
|
− |
|
|
(1) |
− 2t0 1 |
t0 |
. |
||||
|
|
|
|
|
|
|
Если |
принять d − d0 = a ( a |
- натяг |
дорнования), то уравнение (1) перепишется так
|
|
|
t |
|
|
D − D0 |
|
− |
|
|
(2) |
= a − 2t0 1 |
t0 |
. |
|||
|
|
|
|
|
Таким образом, для определения наружного диаметра втулок после дорнования необходимо иметь зависимость относительного утонения стенки от основных факторов дорнования. Эта зависимость, полученная аппроксимацией экспериментальных данных [2] при дорнования по схеме сжатия имеет вид
L = L |
d0 + t0 |
|
1 |
. |
(8) |
|
|
||||
0 d + Kt0 |
|
K |
|
Если принять d − d0 = a , то из уравнения
(8) получим
L = L |
|
d0 + t0 |
|
1 |
. |
(9) |
|
+ a + Kt0 |
|
||||
0 d0 |
|
K |
|
На рис.1…4 результаты расчетов по формулам (5), (6), (8) и (9) сопоставлены с результатами экспериментов [2]. Последние выполняли на втулках из стали 20 (НВ 1470 МПа) с диаметром отверстий d0 =2,16 мм и
высотой L0 =8 мм. Наружный диаметр втулок
варьировали |
в |
пределах |
5…14 мм |
( D0 / d0 =2,3…6,5). |
Дорнование |
отверстий |
|
производили |
по |
схеме сжатия |
однозубыми |
354

|
|
|
|
|
|
|
|
|
|
|
|
|
|
|
|
|
Современные техника и технологии 2007 |
|||||||
прошивками |
из |
|
твердого |
сплава |
ВК8 |
с |
D-D , |
|
|
|
|
|
|
|||||||||||
помощью специального приспособления |
[1]. |
0,20 |
|
|
|
|
|
|
||||||||||||||||
мм |
|
|
|
|
|
|
||||||||||||||||||
Углы |
конусов |
прошивок |
составляли |
|
6°, |
0,16 |
|
|
|
|
|
|
||||||||||||
ширина |
соединяющей |
их |
цилиндрической |
|
|
|
|
|
|
|||||||||||||||
|
|
|
|
|
|
|
||||||||||||||||||
ленточки – около 2 мм. В качестве смазочного |
0,12 |
|
|
1 |
|
|
|
|||||||||||||||||
материала |
при |
|
дорновании |
использовали |
|
|
|
|
|
|
||||||||||||||
жидкость |
|
МР-7. |
Измерения |
|
диаметров |
|
|
|
2 |
|
|
|
||||||||||||
отверстий втулок выполняли на компараторе |
0,08 |
|
|
|
|
|
||||||||||||||||||
|
|
|
|
|
|
|||||||||||||||||||
с |
перфлектометром |
|
фирмы |
«Leitz» |
|
|
|
3 |
|
|
|
|||||||||||||
(Германия) с ценой деления 0, 0002 мм, |
0,04 |
|
|
|
|
|
|
|||||||||||||||||
наружных диаметров – на вертикальном |
|
|
|
|
|
|
|
|||||||||||||||||
оптиметре модели ИКВ с ценой деления 0, |
0,00 |
|
|
|
|
|
|
|||||||||||||||||
001 мм, высоты – на микроскопе УИМ-21 с |
0,05 |
0,10 |
0,15 |
0,20 |
0,25 |
0,30 |
a,0,35мм |
|||||||||||||||||
ценой деления 0, 001 мм. |
|
|
|
|
|
|
|
|
|
|
|
|
|
|
|
|||||||||
|
Отметим, |
что |
именно |
на |
|
основе |
этих |
Рис. 2. Зависимости приращения |
||||||||||||||||
экспериментов была получена и приведенная |
||||||||||||||||||||||||
наружного диаметра втулок от натяга при |
||||||||||||||||||||||||
выше зависимость (3). |
|
|
|
|
|
|
|
|
|
|||||||||||||||
|
|
|
|
|
|
|
|
|
одноцикловом дорновании отверстий: 1 - |
|||||||||||||||
|
Из рис.1 и 2 следует, что уравнение (5), |
|||||||||||||||||||||||
|
|
|
D0 / d0 =2,5; |
|
|
|||||||||||||||||||
как и следовало ожидать, позволяет |
|
|
|
|
||||||||||||||||||||
определять наружный диаметр втулок после |
2 - |
D0 / d0 =3,7; 3 - D0 / d0 =5,6; |
||||||||||||||||||||||
дорнования с меньшей погрешностью, чем |
- эксперимент, |
- расчет по уравнению |
||||||||||||||||||||||
уравнение (6). Однако, использование |
|
|
|
(6) |
|
|
|
|||||||||||||||||
последнего является предпочтительным, так |
|
|
|
|
|
|
|
|||||||||||||||||
как |
не |
|
|
требует |
|
знания |
диаметра |
Погрешность |
расчета |
высоты |
втулок |
|||||||||||||
обработанного |
|
дорнованием |
|
отверстия, |
||||||||||||||||||||
расчетное определение которого связано с |
после дорнования по уравнению (8) |
|||||||||||||||||||||||
известными трудностями. |
|
|
|
|
|
|
|
|
несколько меньше, чем по уравнению (9). |
|||||||||||||||
|
|
|
|
|
|
|
|
|
|
|
|
|
|
|
|
|
Однако в обоих случаях эта погрешность |
|||||||
|
D-D |
, |
|
|
|
|
|
|
|
|
|
|
|
|
|
|
довольно значительна. Поэтому уравнения |
|||||||
|
0,20 |
|
|
|
|
|
|
|
|
|
|
|
|
|
|
(8) и (9) могут быть применены только для |
||||||||
|
мм |
|
|
|
|
|
|
|
|
|
|
|
|
|
|
|
ориентировочных расчетов. |
|
|
|
||||
|
0,16 |
|
|
|
|
|
|
|
|
|
|
|
|
|
|
|
|
|
||||||
|
|
|
|
|
|
|
|
|
|
|
|
|
|
|
|
|
|
|
|
|
|
|||
|
|
|
|
|
|
|
|
|
|
|
|
|
|
|
|
|
0,10 |
|
|
|
|
|
|
|
|
0,12 |
|
|
|
|
|
|
|
|
|
|
|
|
|
|
L 0 -L, |
|
|
|
|
|
|
||
|
|
|
|
|
|
|
|
|
|
|
|
|
|
|
мм |
|
|
1 |
|
|
|
|||
|
|
|
|
|
|
|
1 |
|
|
|
|
|
|
|
|
|
|
|
|
|
|
|
||
|
|
|
|
|
|
|
|
|
|
|
|
|
|
|
|
0,05 |
|
|
|
|
|
|
||
|
0,08 |
|
|
|
|
|
|
|
|
|
|
|
|
|
|
|
|
|
|
|
|
|||
|
|
|
|
|
2 |
|
|
|
|
|
|
|
|
|
|
|
|
|
|
|
|
|||
|
|
|
|
|
|
|
|
|
|
|
|
|
|
|
|
|
|
|
2 |
|
|
|
||
|
0,04 |
|
|
|
|
|
|
|
|
|
|
|
|
|
|
|
|
|
|
|
|
|||
|
|
|
|
|
3 |
|
|
|
|
|
|
|
|
|
0,00 |
|
|
|
|
|
|
|||
|
|
|
|
|
|
|
|
|
|
|
|
|
|
|
|
|
|
|
|
|
|
|||
|
|
|
|
|
|
|
|
|
|
|
|
|
|
|
|
|
|
|
|
3 |
|
|
|
|
|
0,00 |
|
|
|
|
|
|
|
|
|
|
|
|
|
|
|
|
|
|
|
|
|
||
|
|
0,05 |
|
0,10 |
0,15 |
0,20 |
0,25 |
|
0,30 |
d-d |
|
мм |
-0,05 |
|
|
|
|
|
|
|||||
|
|
|
|
|
0,350 |
|
0,05 |
0,10 |
0,15 |
0,20 |
0,25 |
0,30 |
d-d мм |
|||||||||||
|
|
|
|
|
|
|
|
|
|
|
|
|
|
|
|
|
0,350 |
|
|
Рис. 1. Зависимости приращения |
Рис. 3. Зависимости укорочения втулок от |
||||||||
наружного диаметра втулок от приращения |
|||||||||||
|
диаметра отверстий при одноцикловом |
приращения диаметра отверстий при |
|||||||||
|
|
|
|
дорновании: |
|
|
|
одноцикловом дорновании: |
|||
1 - |
D / d |
0 |
=2,5; 2 - D / d |
0 |
=3,7; 3 - D / d |
0 |
=5,6; |
1 - D0 / d0 =2,5; 2 - D0 / d0 =3,7; 3 - D0 / d0 =5,6; |
|||
|
0 |
|
0 |
|
0 |
|
- эксперимент, |
- расчет по |
|||
|
|
|
|
- эксперимент, |
- расчет по |
||||||
|
|
|
|
уравнению (5) |
|
|
|
уравнению (8) |
|
355

XIII Международная научно-практическая конференция «СОВРЕМЕННЫЕ ТЕХНИКА И ТЕХНОЛОГИИ» |
|||||||||||||
|
0,100 |
|
|
|
|
|
ЛИТЕРАТУРА: |
|
|
|
|
||
|
L 0 -L, |
|
|
|
|
|
|
|
|
|
|||
|
мм |
|
|
|
1 |
|
1. |
Скворцов В.Ф., |
Арляпов |
А.Ю. |
|||
|
|
|
|
|
|
||||||||
|
0,050 |
|
|
|
|
|
Дорнование |
глубоких |
|
отверстий |
малого |
||
|
|
|
|
|
|
диаметра. –Томск: Изд-во ТПУ, 2005. -92 с. |
|||||||
|
|
|
|
|
|
|
|||||||
|
|
|
|
|
2 |
|
2. |
Скворцов В.Ф., |
Арляпов А.Ю., Охотин |
||||
|
0,000 |
|
|
|
|
|
И.С. Особенности процесса дорнования |
||||||
|
|
|
|
|
3 |
|
отверстий малого диаметра в толстостенных |
||||||
|
-0,050 |
|
|
|
|
|
втулках, выполняемого с большими натягами |
||||||
|
|
|
|
|
|
// Обработка металлов. -2006. |
-№4 |
(33). –с. |
|||||
|
0,05 |
0,10 |
0,15 |
0,20 |
0,25 |
0,30 a,0,35мм |
|||||||
|
15-17. |
|
|
|
|
|
|
||||||
|
|
|
|
|
|
|
|
|
|
|
|
|
|
Рис. 4. Зависимости укорочения втулок от |
3. |
Розенберг |
О.А. |
Механика |
|||||||||
взаимодействия инструмента с изделием при |
|||||||||||||
|
натяга при одноцикловом дорновании |
деформирующем протягивании. –Киев: Наук. |
|||||||||||
|
|
|
отверстий: |
|
думка, 1981. -188 с. |
|
|
|
|
||||
1 - |
D0 / d0 =2,5; 2 - D0 / d0 =3,7; 3 - |
D0 / d0 =5,6; |
|
|
|
|
|
|
|
||||
|
- эксперимент, |
- расчет по уравнению |
|
|
|
|
|
|
|
||||
|
|
|
|
(9) |
|
|
|
|
|
|
|
|
|
ОЦЕНКА ДЕФОРМИРОВАННОГО СОСТОЯНИЯ СТАЛИ 110Г13Л, ОБРАЗЦЫ ИЗ КОТОРОЙ ПОДВЕРЖЕНЫ НАГРУЖЕНИЮ УДАРНОЙ ВОЛНОЙ
Петров А.Ф., Гуськов А.В., Милевский К.Е.
Новосибирский государственный технический университет,
Россия, г. Новосибирск, пр. К.Маркса 20 E-mail: conf_npo@craft.nstu.ru
В данной работе целью является, оценка деформированного состояния стали 110Г13Л, литой закаленной на аустенит, под воздействием ударной волны. Выбрана, схема упрочнения стали пластическим взрывчатым веществом из условий: используется высокоэнергетическое взрывчатое вещество; взрывчатое вещество располагается непосредственно на поверхности упрочняемого изделия; схема расположения взрывчатого вещества позволяет убрать краевые эффекты [1]. Геометрические размеры, «рабочая поверхность» образца, определяют выбор
метода делительных сеток |
для оценки |
напряженно-деформированного |
состояния |
образцов после взрывной обработки. На втором плане стоит разработка схемы нагружения, которая включает в себя: описание образцов (геометрические размеры, химический состав, физико-механические
свойства исследуемых |
образцов), |
схема |
|
крепления |
образцов |
(взаимное |
|
расположение |
образцов |
друг относительно |
друга, расположение взрывчатого вещества на образцах, схема расположения электродетонатора), технология нанесения делительной сетки на образец.
Исследуемые образцы плавки №149732, из стали 110Г13Л представлены на рис.1, проходят закалку на чистый аустенит и имеют химический состав и механические свойства, соответствующие II группе качества металла
[2].
Рисунок 1 Геометрические размеры образцов
На один из исследуемых образцов наносили сетку царапанием с помощью чертилки и штангенциркуля (рис.2). Данный способ нанесения сетки позволил
выдерживать базу сетки с точностью 2 ± 0,5 мм.
Исходные образцы до нагружения подвергались металлографическому анализу. Каждому «квадрату» сетки присваивалось буквенно-цифровое обозначение, которое позволяет говорить о выбранном «квадрате». Для анализа микроструктуры «квадраты» выборочно фотографировались.
356

Современные техника и технологии 2007
Рисунок 2 Сетка, наносимая на исходный образец (штриховкой обозначены фотографируемые области)
Крепление образцов осуществляли так, чтобы шлифованные поверхности образцов располагались друг к другу. Такая схема крепления позволяет сохранить нанесенную сетку, предохраняя ее от разрушения продуктами детонации.
Рисунок 3 Схема крепления образцов
Далее расположено описание проведения эксперимента и обработка полученных результатов. Нагружение проводилось во взрывной камере в заводских условиях, взрывчатое вещество, высотой 12 мм, инициировалось от капсюля детонатора ЭДВ - 1. После чего образцы отделяли друг от друга и повторно фотографировали как сам образец (х6,5), так и «квадраты» сетки, которым было присвоено буквенно-цифровое обозначение (х50(200)). После взрывного нагружения проводились замеры твердости упрочняемых поверхностей по Роквеллу. Для исследуемого образца определялось среднее значение твердости по замерам в нескольких точках упрочняемой поверхности по всей глубине детали Обработка полученных
результатов представлена в виде зависимостей распределения величин твердости и относительных деформаций Ех, Еy, Ez от глубины образца и представлена на рисунке 4.
Рисунок 4 Графики распределения величин твердости и относительных деформаций Ех, Еy, Ez от глубины образца при нагружении ударной волной
Относительные деформации определяли по перемещениям узлов сетки, как представлено на рисунке 5.
Рисунок 5 Деформация «квадрата» сетки
Рисунок 6 Твердость образцов на поверхности в зависимости от степени деформации
1- статическое сжатие; 2 - осадка ударами
357