
- •к.т.н., начальник отдела ОНИР СиМУ ЭЛТИ, сопредседатель секции №1
- •д.т.н., профессор, зав. каф. фмпк эфф, председатель секции № 9
- •СЕКЦИЯ 1. ЭЛЕКТРОЭНЕРГЕТИКА
- •АВТОМАТИЗАЦИЯ РАСЧЕТА СТРУКТУРНОЙ НАДЕЖНОСТИ ЭЛЕКТРИЧЕСКИХ СХЕМ
- •ОСОБЕННОСТИ МОДЕЛИРОВАНИЯ ЭЛЕКТРИЧЕСКОГОПОЛЯ В МОРСКОЙ ВОДЕ
- •КАБЕЛЬ ДЛЯ ЭЛЕКТРОПИТАНИЯ ГЕНЕРАТОРОВ НИЗКОТЕМПЕРАТУРНОЙ ПЛАЗМЫ
- •Колпаков В.А., Паранин В.Д., Мокеев Д.А………………...86
- •СПОСОБЫ СЕЛЕКЦИИ КОРОТКИХ ЗАМЫКАНИЙ НА ЛИНИЯХ ЭЛЕКТРОПЕРЕДАЧИ
- •СЕКЦИЯ 2. ПРИБОРОСТРОЕНИЕ
- •ИСПОЛЬЗОВАНИЕ КОМПЬЮТЕРНОГО МОДЕЛИРОВАНИЯ ПРИ ИССЛЕДОВАНИИ СПОСОБА КОМПЕНСАЦИИ ДЕЙСТВИЯ ВИБРАЦИИ НА ГИРОМАЯТНИК
- •РАЗРАБОТКА И ИССЛЕДОВАНИЕ МИКРОМЕХАНИЧЕСКОГО ГИРОСКОПА
- •НОРМИРОВАНИЕ ШИХТОВЫХ МАТЕРИАЛОВ ДЛЯ ПРОИЗВОДСТВА ОТЛИВОК ИЗ АЛЮМИНИЕВЫХ СПЛАВОВ
- •ИНВЕРТОРНЫЙ ИСТОЧНИК ПИТАНИЯ ДЛЯ СВАРКИ МОДУЛИРОВАННЫМ ТОКОМ
- •ИССЛЕДОВАНИЕ ВЛИЯНИЯ ОТКЛОНЕНИЯ КОРПУСА НА ЦИКЛ РАБОТЫ ПНЕВМОГИДРАВЛИЧЕСКОГО УДАРНОГО МЕХАНИЗМА
- •ДИНАМИЧЕСКИЕ ПРОЦЕССЫ В БУРОВОЙ КОЛОННЕ ПРИ ВРАЩАТЕЛЬНО-УДАРНОМ БУРЕНИИ СКВАЖИН МАЛЫХ ДИАМЕТРОВ
- •СЕКЦИЯ 4. ЭЛЕКТРОМЕХАНИКА
- •ВЛИЯНИЕ ДЛИНЫ АСИНХРОННОГО ДВИГАТЕЛЯ НА ЭФФЕКТИВНОСТЬ КРЕПЛЕНИЯ
- •РЕЗУЛЬТАТЫ ЭКСПЕРИМЕНТАЛЬНЫХ ИССЛЕДОВАНИЙ ХАРАКТЕРИСТИК СИНХРОННОГО ГИБРИДНОГО ДВИГАТЕЛЯ
- •РАЗРАБОТКА ЭЛЕКТРОМЕХАНИЧЕСКОГО ПРЕОБРАЗОВАТЕЛЯ С АКТИВНЫМ И РЕАКТИВНЫМ ДИСКАМИ В МАГНИТНОЙ СИСТЕМЕ
- •ПРОГРАММА ВЫЯВЛЕНИЯ ФАКТОРОВ РИСКА РАКА МОЛОЧНОЙ ЖЕЛЕЗЫ С ИСПОЛЬЗОВАНИЕМ МЕТОДА МЕТА-АНАЛИЗА
- •ИССЛЕДОВАНИЕ ВОЗМОЖНОСТИ ИСПОЛЬЗОВАНИЯ МЕТОДА ФОТОМЕТРИРОВАНИЯ КАПЕЛЬНЫХ ПРОБ ДЛЯ ОЦЕНКИ АГРЕГАЦИОННЫХ СВОЙСТВ КЛЕТОК КРОВИ
- •ИСПОЛЬЗОВАНИЕ МИКРОВОЛНОВОЙ РАДИОТЕРМОМЕТРИИ В ДИАГНОСТИКЕ РАКА МОЛОЧНОЙ ЖЕЛЕЗЫ
- •УСТАНОВКА ДЛЯ ОПРЕДЕЛЕНИЯ ГИДРОДИНАМИЧЕСКИХ ХАРАКТЕРИСТИК КЛАПАННЫХ ЗАМЕНИТЕЛЕЙ, КАК ПОКАЗАТЕЛЕЙ КАЧЕСТВА И ПРИГОДНОСТИ ДЛЯ КАРДИОХИРУРГИИ
- •Введение
- •ЭКОНОМИЧНЫЙ И ЭКОНОМНЫЙ УМЗЧ 2×200Вт С БЛОКОМ ПИТАНИЯ
- •Мариненко А.В.
- •Благодарности
- •Компонента
- •МЕТОДИКА ОБРАБОТКИ КАРТИН ИНТЕРФЕРЕНЦИОННЫХ ПОЛОС
- •ЛИТЕРАТУРА:
- •Описание процесса моделирования
- •Вывод
- •Благодарности
- •ИСПОЛЬЗОВАНИЕ КОМПЬЮТЕРНОГО МОДЕЛИРОВАНИЯ ПРИ ИССЛЕДОВАНИИ СПОСОБА КОМПЕНСАЦИИ ДЕЙСТВИЯ ВИБРАЦИИ
- •НА ГИРОМАЯТНИК
- •Перспективы
- •Экспериментальная часть
- •Заключение
- •Рисунок 3. Результаты моделирования работы системы
- •ЛИТЕРАТУРА:
- •СКОРОСТНОЙ ЭФФЕКТ В ВИХРЕТОКОВОМ КОНТРОЛЕ
- •Введение
- •Благодарности
- •ЛИТЕРАТУРА:
- •E-mail: yuyug@npi.tpu.ru
- •Наименование параметра
- •Полоса
- •частот, Гц
- •Результаты и обсуждение
- •ЛИТЕРАТУРА:
- •ЛИТЕРАТУРА:
- •Тогда энергия, переданная упругому элементу, согласно (2) будет равна:
- •ПРОБЛЕМА ИССЛЕДОВАНИЯ ТРЕХЗВЕННЫХ МЕХАНИЗМОВ
- •ЛИТЕРАТУРА:
- •420066, г. Казань, Красносельская ул., 51
- •E-mail: BakirovAR@rambler.ru
- •420066, г. Казань, Красносельская ул., 51
- •E-mail: BakirovAR@rambler.ru
- •Введение
- •Выводы
- •Выводы
- •ОПТИМИЗАЦИЯ РЕЖИМОВ ЭКСПЛУАТАЦИИ УСТАНОВОК ТИПА УЭЦН С ПЧ
- •ЦИФРОВАЯ ЛАБОРАТОРИЯ ЭЛЕКТРОМЕХАНИКА
- •ЭЛЕКТРОМАГНИТНЫЙ МОМЕНТ В ИНДУКЦИОННЫХ ДВИГАТЕЛЯХ
- •Материал и методы исследования
- •Заключение и некоторые перспективы
- •ЛИТЕРАТУРА:

XIII Международная научно-практическая конференция «СОВРЕМЕННЫЕ ТЕХНИКА И ТЕХНОЛОГИИ»
время смены инструмента, мин.; Т – стойкость токарных резцов, мин.
Стойкость резцов зависит от режимов резания по следующей зависимости:
T = |
v Cv kv |
, |
(3) |
|
t x s y |
||||
|
|
|
где v – скорость резания, м/мин; Сv – постоянная величина для определения группы обрабатываемого материала; kм – коэффициент, зависящий от свойств обрабатываемых материалов и режущего инструмента, от его геометрии, износа, а
также от смазочно-охлаждающейся жидкости; x,y – показатели степени, зависящие от свойств инструмента и условий резания.
Подставляя (3) в (2) и принимая за возмущающее воздействие изменение величины припуска z при постоянной t получим целевую функцию:
Р = |
t s(z) |
, |
(4) |
x y |
1 + τсм t m s m
(v Cv kv )m1
Рис.1 Визуальная форма для исследования параметров процесса резания
Таким образом, графический интерфейс |
|
|
||
позволяет на основе выбранных исходных |
ЛИТЕРАТУРА: |
|
||
параметров прогнозировать |
оптимальные |
1.Справочник |
технолога- |
|
режимы резания в соответствии с заданными |
машиностроителя, под ред. А.Г. Косиловой и |
|||
критериями эффективности. |
|
|
Р.К. Мещерякова, М.; Машиностроение, |
|
Данная методика может быть применена |
1985г. |
|
||
и для других видов обработки: фрезерной, |
2.Макаров А.Д. Оптимизация процессов |
|||
сверлильной и т.д. |
с |
небольшими |
резания. М.: Машиностроение, 1976г. |
|
изменениями математических |
моделей и с |
3.Мудров А.Е. Численные методы для |
||
созданием базы данных для этих видов |
ПЭВМ на языках Бейсик, Фортран, Паскаль. |
|||
обработки. |
|
|
Томск, МП «PACKD», 1991 |
|
362

Современные техника и технологии 2007
ВЛИЯНИЕ ГАЗОДИНАМИЧЕСКОГО УДАРА НА РАЗБРЫЗГИВАНИЕ ЭЛЕКТРОДНОГО МЕТАЛЛА ПРИ СВАРКЕ В АКТИВНЫХ ГАЗАХ
Солодский С.А., Брунов О. Г. Юргинский технологический институт (филиал)
Томского политехнического университета,
Россия, Кемеровская обл., г. Юрга, ул. Ленинградская,26 E-mail: serdgio80@inbox.ru
Одним из недостатков сварки в среде активных газов является повышенное разбрызгивание электродного металла. Известно, что одной из причин разбрызгивания при механизированной сварке в защитных газах является газодинамический удар, возникающий при испарении перемычки между сварочной проволокой и каплей, переходящей в сварочную ванну. Возникающее при этом давление направлено радиально от места взрыва. Следовательно, при газодинамическом ударе возникает вероятность выброса брызг жидкого металла не только самой перемычки, но и жидкого металла, находящегося на торце электрода. Переход капли расплавленного металла в сварочную ванну, от которого зависит термодинамические, физико-химические и другие свойства сварного шва, мало изучен. Существует два способа снижения разбрызгивания при газодинамическом ударе:
а) снижение силы тока во время взрыва перемычки;
б) уменьшение количества жидкого металла на торце электродной проволоки.
Первый способ достигается при сварке модулированным сварочным током, когда во время взрыва перемычки ток снижается до минимального значения.
Второй способ достигается при сварке с импульсной подачей сварочной проволоки, когда переход капли происходит во время паузы в подаче сварочной проволоки.
Если провести сравнение традиционного способа сварки с непрерывной подачей проволоки и сварки с импульсной подачей проволоки, можно заметить, что при одном и том же значении сварочного тока и соответственно, при одинаковой силе взрыва, сварка с импульсной подачей сварочной проволоки имеет меньшее разбрызгивание по сравнению со сваркой с непрерывной подачей, это можно объяснить следующим различием процессов.
При традиционном способе во время и после образования перемычки продолжается движение проволоки, а, учитывая, что линия сплавления практически остается на месте,
если же линия сплавления опускается, то увеличивается ток короткого замыкания [1], следовательно, увеличивается скорость плавления проволоки. А часть проволоки, находящаяся выше перемычки увеличивается во время ее движения, продолжает плавиться и под действием Джоулева тепла, увеличивает количество жидкого металла на торце электродной проволоки. Поэтому, когда происходит газодинамический взрыв перемычки, именно эта дополнительная масса может быть выброшена за пределы сварочной ванны, что является причиной увеличения разбрызгивания. И чем больше сварочный ток при механизированной сварке, то есть выше скорость подачи проволоки и, тем большее количество проволоки расплавится во время короткого замыкания за счет тепла, вырабатываемого проходящим током по закону Джоуля – Ленца. Количество расплавившейся проволоки за время обрыва перемычки можно определить из следующего выражения
m = |
I U t |
(1) |
q |
|
где q – удельная теплота плавления электродной проволоки, для стали.
Известно, что скорость подачи проволоки равна скорости ее плавления, и определим ее из выражения (2) [2]
υпл = 9.6 10 |
−2 |
|
I U |
+ 6.4 10 |
−5 |
|
I 2 l м/час.(2) |
|
|
d 2 |
|
d 4 |
|
Для определения необходимого диапазона изменения тока воспользуемся графиком разбрызгивания для различных диаметров проволоки из [3]. Учитывая, что [4] задав в качестве начальных условий диаметр проволоки и вылет электрода, строим номограмму по которой можно определить скорость плавления проволоки в зависимости от силы тока, а затем, учитывая время разрыва перемычки, определим количество проволоки, расплавленное за время короткого замыкания с учетом того, что линия сплавления практически неподвижна [1].
363

XIII Международная научно-практическая конференция «СОВРЕМЕННЫЕ ТЕХНИКА И ТЕХНОЛОГИИ»
Рис.1 Номограмма зависимости скорости плавления сварочной проволоки от силы тока
(dпр. = 1.2мм, l = 12мм)
При расчетах взята возрастающая ветвь разбрызгивания [3], так как дальнейшее увеличение тока приводит к снижению разбрызгивания за счет увеличения электродинамической силы. Полученные с помощью киносъемки данные говорят о том что 35% цикла занимает короткое замыкание, а образование перемычки начинается спустя 14% времени после начала короткого замыкания, таким образом, приняв частоту коротких замыканий равную 50 Гц можно сказать, что время накопления капли, которая может быть выброшена при газодинамическом ударе равно tобр. = 0.0042с. Для получения зависимости массы жидкого металла, который может быть выброшен при газодинамическом взрыве с торца электрода необходимо принять начальные условия. На основании этих данных можно построить номограмму зависимости массы разбрызгиваемой капли от силы тока.
Рис.2 Зависимость вероятной массы разбрызгиваемого металла в зависимости от силы тока при непрерывной подаче проволоки dпр.=1.2мм
В то же время при сварке с импульсной подачей сварочной проволоки во время
короткого замыкания скорость проволоки равна нулю, таким образом, при плавлении электродной проволоки увеличивается длина перемычки, что приводит к повышению ее сопротивления и из закона Джоуля – Ленца снижается скорость плавления проволоки
υпл. = |
m |
= |
I 2 |
R |
(3) |
t |
q |
|
|||
|
|
|
где R – сопротивление перемычки. Процесс взрыва перемычки при
традиционном способе и при сварке с импульсной подачей сварочной проволоки представлен на рис. 3
Рис.3 Газодинамический удар при взрыве перемычки: а) при импульсной подаче сварочной проволоки; б) при непрерывной подаче
Итоги исследований проведенных по методике ГОСТ 25616 – 83 представлены в
(табл.1)
Сравнивая полученные результаты с известными [5], (для проволоки dэл. – 1.2 мм,
ηр. – 5 ÷ 8%; dэл – 1.6 мм, ηр. – 6 ÷10%)
можно сказать, что при сварке с импульсной подачей до двух раз снижает разбрызгивание электродной проволоки. Следовательно, использование импульсной подачи сварочной проволоки с определенным алгоритмом движения приводит к значительному уменьшению разбрызгивания.
Рассмотренный процесс мало изучен и требует дальнейших исследований.
Выводы:
1)Количество металла выбрасываемого при газодинамическом ударе зависит от количества проволоки поданного во время короткого замыкания.
2)Остановка сварочной проволоки во время короткого замыкания уменьшает количество жидкого металла на торце электрода, в результате уменьшается размер брызг, что позволяет снизить разбрызгивание.
364

Современные техника и технологии 2007
Таблица 1 Результаты измерений наплавки и разбрызгивания при сварке с импульсной подачей электродной проволоки.
|
|
№ |
PПР. |
PПЛ. |
|
PПЛ.+ΗН |
|
PБ.-ПЛ. |
PБ.-СП. |
DЭЛ |
|
|
ΗР. |
|
|
|
|||||
|
|
|
|
|
|
|
|
|
|
|
|
|
|
|
|
|
|
|
|
|
|
|
|
г |
|
г |
|
г |
|
% |
|
г |
% |
г |
% |
ММ |
|
|
% |
|
|
|
|
|
|
|
|
|
|
|
|
|
|
|
|
||||||||||
|
|
|
|
|
|
|
|
|
|
|
|
|
|
|
|
|
|
|
|
|
|
|
|
1 |
31.39 |
1620.4 |
|
30.4 |
|
96.85 |
|
0.6 |
1.9 |
0.2 |
0.63 |
|
|
|
|
|
|
|
|
|
|
|
|
|
|
|
|
|
|
|
|
|
|
|
|
|
|
|
|
|
|
|
|
|
|
|
|
|
|
|
|
|
|
|
|
|
|
|
|
|
|
|
|
|
|
2 |
36.27 |
1650.8 |
|
34.4 |
|
94.84 |
|
1.11 |
3.06 |
0.5 |
1.37 |
1.2 |
|
|
4.1 |
|
|
|
|
|
|
|
|
|
|
|
|
|
|
|
|
|
|
|
|
|
|
|
|||
|
|
|
|
|
|
|
|
|
|
|
|
|
|
|
|
|
|
|
|
|
|
|
|
3 |
42.49 |
1685.2 |
|
40.9 |
|
96.26 |
|
0.85 |
2.0 |
0.21 |
0.49 |
|
|
|
|
|
|
|
|
|
|
|
|
|
|
|
|
|
|
|
|
|
|
|
|
|
|
|
|
|
|
|
|
|
|
|
|
|
|
|
|
|
|
|
|
|
|
|
|
|
|
|
|
|
|
4 |
29.12 |
1602.83 |
|
28.4 |
|
97.52 |
|
0.52 |
1.78 |
0.12 |
0.41 |
|
|
|
|
|
|
|
|
|
|
|
|
|
|
|
|
|
|
|
|
|
|
|
|
|
|
|
|
|
|
|
|
|
|
|
|
|
|
|
|
|
|
|
|
|
|
|
|
|
|
|
|
|
|
5 |
35.67 |
1631.2 |
3 |
|
34.91 |
|
97.86 |
|
0.51 |
1.43 |
0.34 |
0.95 |
1.6 |
|
|
2.75 |
|
|
|
|
|
|
|
|
|
|
|
|
|
|
|
|
|
|
|
|
|
|
|
|
|
|
|
|
|
|
|
|
|
|
|
|
|
|
|
|
|
|
|
|
|
|
|
|
|
6 |
34.01 |
1666.14 |
|
32.78 |
|
96.38 |
|
0.87 |
2.56 |
0.37 |
1.08 |
|
|
|
|
|
|
|
|
|
|
|
|
|
|
|
|
|
|
|
|
|
|
|
|
|
|
|
|
|
|
|
|
|
|
|
|
|
|
|
|
|
|
|
|||||||||
где Pпр – вес мерного отрезка проволоки; |
проволоки как частный случай импульсно- |
||||||||||||||||||||
Pпл. – вес образца; Pпл.+ηн. – вес |
дуговой сварки. // Сварочное производство. – |
||||||||||||||||||||
наплавленного образца без брызг; Pб.-пл. – |
2006. №7. – С.6 – 8. |
|
|
|
|
||||||||||||||||
вес брызг на пластине; Pб.-сп. – вес брызг |
|
3. Потапьевский А.Г. Сварка в защитных |
|||||||||||||||||||
налипших на сопло; ηр. – коэффициент |
газах плавящимся электродом. – М: |
||||||||||||||||||||
разбрызгивания. |
|
|
|
|
|
|
|
|
|
Машиностроение, 1974. 240с. |
|
|
|
||||||||
|
|
|
|
|
|
|
|
|
|
|
|
|
|
|
4. Федько |
В.Т. |
Дуговая |
сварка |
|||
ЛИТЕРАТУРА: |
|
|
|
|
|
|
|
плавлением. Томск: Издательство ТПУ, 1994. |
|||||||||||||
1. |
Заруба |
И.И. |
|
Природа |
коротких |
– 240 с. |
|
|
|
|
|
|
|||||||||
замыканий дуги при сварке в углекислом газе. |
|
5. Федько В.Т. Теория, технология |
и |
||||||||||||||||||
// Автоматическая сварка. – 1973. – №5. – С. |
средства |
снижения |
набрызгивания |
и |
|||||||||||||||||
14 17. |
|
|
|
|
|
|
|
|
|
|
|
|
трудоемкости при сварке в углекислом газе. – |
||||||||
2. |
Федько |
В.Т., |
Брунов |
О.Г., |
Соколов |
Томск: Издательство ТПУ, 1998. – 432 с. |
|
П.Д. Сварка с импульсной подачей сварочной
МОДУЛЬНАЯ ПЛАНЕТАРНАЯ КОРОБКА ПЕРЕДАЧ
Становской А.В., Брюхов В.В.
Томскийполитехническийуниверситет, Россия, г. Томск, пр. Ленина, 30 E-mail: tm@mail.tomsknet.ru
В машиностроении существует |
ряд |
Недостатком |
известных |
механизмов |
|||
устройств |
предназначенных |
для |
является |
необходимость |
переключения, |
||
переключения передач в разных схемах |
путем перемещения подвижных блоков по |
||||||
управлением |
являются |
либо |
несущим валам, что приводит к появлению |
||||
двухпозиционная дисковая муфта, либо |
вибраций и различного рода неточностей. |
||||||
тормоз и блокировочная муфта. |
|
Модульная планетарная коробка передач |
|||||
|
|
|
(МПКП) |
создана |
с |
целью упрощения |
365
XIII Международная научно-практическая конференция «СОВРЕМЕННЫЕ ТЕХНИКА И ТЕХНОЛОГИИ»
системы |
управления |
переключением |
Элементы |
переключения |
|
передач, |
||||||
скоростей в коробке с минимальным числом |
выполненные в виде тормозов, имеют |
|||||||||||
планетарных |
модулей |
и |
элементов |
значительно |
|
более |
простую |
систему |
||||
управления. |
|
|
|
управления, чем блокировочные дисковые |
||||||||
МПКП можно отнести к механизмам |
муфты. |
Ленточные |
тормоза |
|
требуют |
|||||||
ступенчатого |
переключения |
|
скоростей и |
меньшего |
давления и |
расхода жидкости в |
||||||
может |
использоваться для |
построения |
гидравлической системе управления. |
|
|
|||||||
коробок передач в станкостроении, а также в |
МПКП |
наиболее |
экономична |
для |
||||||||
транспортном машиностроении. |
|
автомобилей, которые большую часть |
||||||||||
МПКП основана на методе перебора |
времени работают на более низких |
|||||||||||
передаточных |
отношений |
|
соединенных |
передачах. Это городской автомобиль и |
||||||||
последовательно повышающих планетарных |
автобус, а также тяжелая техника, такая как |
|||||||||||
модулей. Перебор передаточных отношений |
трактор, карьерный самосвал, |
бульдозер и |
||||||||||
осуществляется с помощью тормозов (рис.1), |
т.п. |
|
|
|
|
|
|
|
||||
которые в каждом планетарном модуле |
При |
электронной |
системе |
управления |
||||||||
включены между входным и выходным |
тормозами |
|
предложенная |
ступенчатая |
||||||||
звеньями. Таким образом, МПКП ступенчато |
коробка передач преобразуется в МПКП с |
|||||||||||
изменяет скорость вращения. |
|
|
непрерывным потоком мощности. |
|
|
|||||||
Для получения ряда понижающих передач |
Для примера в табл.1 и табл.2 приведены |
|||||||||||
на входе или выходе коробки передач может |
схемы включения и КПД передач при расчете |
|||||||||||
быть включена дополнительная понижающая |
МПКП в диапазоне переключения передач |
|||||||||||
передача, с передаточным отношением, |
4,6-0,78 при постоянном шаге 1,29. |
|
|
|||||||||
равным |
|
требуемому |
передаточному |
|
|
|
|
|
|
|
|
отношению низшей передачи.
Табл.1. Схема включения передач с первичной понижающей передачей
|
|
Передаточное |
|
|
|
|
|
|
|
|
|
|
|
|
Общее |
||||
|
|
|
|
|
|
|
|
|
|
|
|
|
|
передаточное |
|||||
|
|
отношение |
|
|
Тормоз 1 |
|
Тормоз 2 |
Тормоз 3 |
|
||||||||||
|
|
|
|
|
|
отношение |
|||||||||||||
|
|
|
|
|
|
|
|
|
|
|
|
|
|
|
|
||||
|
|
|
|
|
|
|
|
|
|
|
|
|
|
|
|
|
|
|
|
|
|
0,17 |
|
|
|
включен |
|
включен |
включен |
|
|
0, 78 |
|
||||||
|
|
|
|
|
|
|
|
|
|
|
|
|
|
|
|
|
|
|
|
|
|
0,22 |
|
|
|
включен |
|
включен |
выключен |
|
|
1 |
|
||||||
|
|
|
|
|
|
|
|
|
|
|
|
|
|
|
|
|
|
|
|
|
|
0,28 |
|
|
|
включен |
выключен |
включен |
|
|
1,29 |
|
|||||||
|
|
|
|
|
|
|
|
|
|
|
|
|
|
|
|
|
|
|
|
|
|
0,36 |
|
|
|
включен |
выключен |
выключен |
|
|
1,66 |
|
|||||||
|
|
|
|
|
|
|
|
|
|
|
|
|
|
|
|
|
|
|
|
|
|
0,47 |
|
|
|
выключен |
|
включен |
включен |
|
|
2,15 |
|
||||||
|
|
|
|
|
|
|
|
|
|
|
|
|
|
|
|
|
|
|
|
|
|
0,6 |
|
|
|
выключен |
|
включен |
выключен |
|
|
2,77 |
|
||||||
|
|
|
|
|
|
|
|
|
|
|
|
|
|
|
|
|
|
|
|
|
|
0,77 |
|
|
|
выключен |
выключен |
включен |
|
|
3,57 |
|
|||||||
|
|
|
|
|
|
|
|
|
|
|
|
|
|
|
|
|
|
|
|
|
|
1 |
|
|
|
выключен |
выключен |
выключен |
|
|
4,6 |
|
|||||||
|
|
|
|
|
|
|
|
|
|
|
|
|
|
|
|
|
|
|
|
Табл.2. Расчетный КПД |
|
|
|
|
|
|
|
|
|
|
|
|
|
|
|||||
|
|
|
|
|
|
|
|
|
|
|
|
|
|
|
|
|
|
|
|
|
|
Передача |
|
1 |
|
2 |
|
3 |
|
4 |
|
5 |
6 |
|
7 |
|
8 |
|
|
|
Передаточное |
|
4,6 |
|
3,57 |
|
2,77 |
|
2,15 |
|
1,66 |
1,29 |
|
1 |
|
0,78 |
|
||
|
|
число |
|
|
|
|
|
|
|
|
|||||||||
|
|
|
|
|
|
|
|
|
|
|
|
|
|
|
|
|
|
|
|
|
|
Расчетный |
|
0,98 |
|
0,94 |
|
0,94 |
|
0,90 |
|
0,94 |
0,90 |
|
0,90 |
|
0,87 |
|
|
|
|
КПД |
|
|
|
|
|
|
|
|
|||||||||
|
|
|
|
|
|
|
|
|
|
|
|
|
|
|
|
|
|
|
366
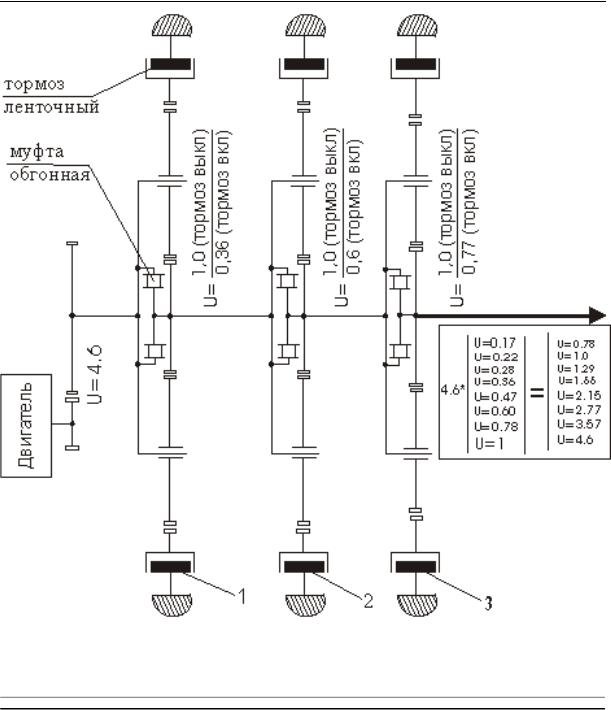
Современные техника и технологии 2007
Рис.1. Модульная планетарная коробка передач (восемь скоростей)
ИСКЛЮЧЕНИЕ ИЗБЫТОЧНЫХ СВЯЗЕЙ В ПЛОСКИХ МЕХАНИЗМАХ
Стариков С.П., Гудимова Л.Н.
Сибирский государственный индустриальный университет, г. Новокузнецк, ул. Кирова, 42
E–mail: rector@sibsiu.ru
Создание механизмов, в которых избыточные связи отсутствуют, является одной из самых актуальных задач теории структуры механических систем. В работе профессора Дворникова Л.Т. [1] была предложена методика устранения избыточных связей в кинематических
цепях, которая сводится к составлению системы двух уравнений, описывающих рассматриваемую схему одновременно и как плоскую, и как пространственную (нулевого семейства), виде
367

XIII Международная научно-практическая конференция «СОВРЕМЕННЫЕ ТЕХНИКА И ТЕХНОЛОГИИ»
1 |
3n |
−W |
|
|
∑ pk = |
|
|
, |
|
|
2 |
|
||
k=5 |
|
|
(1) |
|
1 |
|
|
|
|
∑k pk = 6n −W , |
|
|||
k=5 |
|
|
|
|
где W - требуемая подвижность цепи, k - класс кинематических пар (k=5,4,3,2,1), n - число звеньев кинематической цепи.
Развитие изложенного в [1] метода покажем на конкретном примере: преобразуем шестизвенный плоский шарнирный механизм (рисунок 1), состоящий из пяти подвижных звеньев n=5, семи кинематических пар пятого класса p5=7 с W=1, в безызбыточный.
B |
|
D |
C |
E |
|
|
|
F
A
G
Рисунок 1 - Шестизвенный шарнирный механизм
Определим в нем число избыточных связей по известной формуле q =W+5p5-6n =1+ 35 - 30 = 6.
Приступая к решению, условимся, что кинематические пары первого и второго классов исключаем из рассмотрения, в силу сложности для реализации, тогда система (1) примет вид
|
|
|
3n −W |
|
(2) |
||
p5 |
+ p4 |
+ p3 = |
|
|
|
, |
|
|
|
2 |
|
||||
|
|
|
|
|
|
|
|
5 p + 4 p + 3 p |
3 |
= 6n −W . |
|
||||
|
5 |
4 |
|
|
|
|
Выразим из первого уравнения системы (2) количество кинематических пар третьего класса
p |
3 |
= |
3n −W |
− p |
− p , |
(3) |
|
|
|||||
|
|
2 |
4 |
5 |
|
|
|
|
|
|
|
|
Подставим (3) во второе уравнение системы (2), и после преобразования получим, что
p4 = |
3n + W |
− 2 p5 . |
(4) |
|||
|
2 |
|
||||
|
|
|
|
|
||
Найденное значение p4, подставим в |
||||||
уравнение (3) и найдем, что |
(5) |
|||||
p3 |
|
= p5 −W . |
|
|||
Из полученных зависимостей (4) и (5) с |
||||||
учетом, что n=5 составим систему |
(6) |
|||||
p |
|
= 8 − 2 p , |
|
|||
|
4 |
|
5 |
|
|
|
p3 |
= p5 − 1. |
|
|
|||
Эта система имеет четыре целочисленных |
||||||
положительных решения |
|
|||||
p5 = 4, p4 = 0, p3 = 3, |
|
|||||
p5 = 3, p4 = 2, p3 = 2, |
(7) |
|||||
p5 = 2, p4 = 4, p3 = |
1, |
|||||
|
p5 = 1, p4 = 6 , p3 = 0.
Как было показано ранее в работе [2], безызбыточным механизм можно считать лишь тогда, когда отсутствуют избыточные связи в механизме в целом (родовые) так и в каждом из его контурах (контурные).
Уравнения (7) позволяют исключить лишь родовые избыточные связи. Для полного же устранения избыточных связей проведем разделение механизма на простые контуры (рисунок 2)
а) |
C |
b) |
|
|
|
B |
D |
|
E |
|
|
|
||
|
|
|
|
|
A |
G |
|
|
F |
|
|
|
|
|
c) |
D |
d) |
B |
C |
|
|
E |
F A
G
Рисунок 2 - Разделения механизма на контуры
Первая часть первого разделения, содержащая контур ABCG (рисунок 2,а) имеет n=3, p5 = 4 и W=1; уравнения (4) и
(5) при этих условиях дадут систему
p |
|
= 5 − 2 p , |
(8) |
|
4 |
5 |
|
p3 |
= p5 − 1. |
|
Вторая часть первого разделения DEF (рисунок 2,b) состоит из n=2, p5 = 3 и W=0, и уравнения (4) и (5) запишутся в виде
|
p |
= 3 − 2 p , |
(9) |
|
|
4 |
|
5 |
|
|
p3 |
= p5 . |
|
|
|
Система (8) будет иметь два решения |
|||
p5 |
= 2, p4 |
= 1, p3 = 1, |
(10) |
|
p5 = 1, p4 = 3, p3 = 0. |
(11) |
|||
|
||||
|
Система (9) также дает два решения |
|||
p5 |
= 1, p4 |
= 1, p3 = 1, |
(12) |
|
p5 = 0, p4 = 3, p3 = 0. |
(13) |
|||
|
Комплексных суммарных решений для первого разделения механизма исходя из его рассмотрения по частям, будет четыре, это алгебраические суммы решений (10) и (12); (10) и (13); (11) и (12); (11) и (13).
Эти решения удовлетворяют исключению избыточных контурных связей
p5 |
= 3, p4 |
= 2, p3 |
= 2, |
|
|
p5 |
= 2, p4 |
= 4, p3 |
= 1, |
(14) |
|
p5 |
= 2, p4 |
= 4, p3 |
= 1, |
||
|
|||||
p5 |
= 1, p4 = 6, p3 = 0. |
|
|||
|
Сравнивая результаты решений (7) и |
(14) делаем вывод, что только первое уравнение из (7) не может быть использовано для устранения и родовых и контурных избыточных связей, остальные удовлетворяют условию задачи.
Рассмотрим второе разделение исследуемого механизма, в нем контур
GDEF (рисунок 3,с) имеет |
n=3, p5 = 4 и |
|
W=1; уравнения (4) и (5) запишутся так |
||
p |
= 5 − 2 p , |
(15) |
4 |
5 |
|
p3 |
= p5 − 1. |
|
Системы (15) дает два решения
368

Современные техника и технологии 2007
1.p5 |
= 2, p4 |
= 1, p3 |
= 1, |
(16) |
2.p5 |
= 1, p4 |
= 3, p3 |
= 0. |
(17) |
|
Оставшиеся два звена ABС (рисунок 3,d) имеют n=2, p5 = 3 и W=0, для них система уравнений по (4) и (5) примет вид
p |
|
= 3 − 2 p , |
(18) |
|
4 |
5 |
|
p3 |
= p5 . |
|
Система (18) также имеет два решения
p5 |
= 1, p4 = 1, p3 = 1, |
(19) |
p5 |
= 0, p4 = 3, p3 = 0. |
(20) |
|
Комплексные суммарные решения (16) и (19); (16) и (20); (17) и (19); (17) и (20) окажутся такими
p5 = 3, p4 = 2, p3 = 2,
двумя уравнениями. Для наиболее простой организации привода соединим ведущее звено (АВ) и звено (EF) со стойкой шарниром , т.е. А= p5, F= p5.
Принятые условия не противоречат записанной системе уравнений, т.к. везде, где слева стоят эти буквы, справа есть кинематические пары p5. Преобразуем систему (23) с учетом принятых условий
B + C + D + E + G = p5 + 2 p4 + 2 p3 |
|
||||||
|
|
|
|
|
+ p3 |
|
|
B + C +G = p5 + p4 |
(24) |
||||||
|
+ p3 |
|
|
|
|||
D + E = p4 |
|
|
|
|
|||
D + E + G = p |
5 |
+ p |
4 |
+ p |
3 |
|
|
|
|
|
|
|
|||
|
+ p3 . |
|
|
|
|
||
B + C = p4 |
|
|
|
|
p5 = 2, p4 = 4, p3 |
= 1, |
(21) |
|
|
|
Теперь, |
подставим третье уравнение |
|||||||||||
p5 = 2, p4 = 4, p3 = 1, |
|
системы (24) в четвертое и получим p4+ |
||||||||||||||||
|
|
|||||||||||||||||
|
|
p3+G = p5 +p4 + p3, т.е. G = p5. С учетом |
||||||||||||||||
p5 = 1, p4 = 6, p3 |
= 0. |
|
|
|||||||||||||||
|
|
полученного значения имеем по два |
||||||||||||||||
|
Анализ полученных решений (21) и (7) |
также |
тождественных решения B+C = p4+p3 и |
|||||||||||||||
исключает использование первого уравнения (7), |
D+E = p4+p3. Это означает, что от замены |
|||||||||||||||||
как не совпадающего ни с одним из уравнений |
пар в точках В и С; и в D и E на пары p4 и |
|||||||||||||||||
(21). |
|
|
|
|
p3 безызбыточность механизма будет |
|||||||||||||
|
Дальнейшее решение задачи проведем по |
гарантирована. На рисунке 3,а изображен |
||||||||||||||||
второму уравнению (7), т. е. примем p5 = 3, p4 |
безызбыточный шестизвенный механизм, |
|||||||||||||||||
=2, |
|
|
|
|
|
после проведенного решения. Определим |
||||||||||||
|
p3 =2. Это решение появилось из пяти |
число избыточных связей в этом |
||||||||||||||||
независимых друг от друга частных решений, а |
механизме q = W + 5p5 + 4 p4 + 3 p3 - 6n |
|||||||||||||||||
именно, из второго уравнения (7) общего |
=1+15+8+6 -30 = 0. |
|
|
|
|
|
||||||||||||
решения, |
из уравнений (10), |
(12), (16) и |
(19). |
|
а) |
|
|
|
D |
|
b) |
|
|
|
||||
Объединим эти решения в систему |
|
|
|
B |
C |
|
|
|
|
|
|
|
||||||
|
|
A |
|
G |
E |
|
P5 |
P4 |
P3 |
|
||||||||
|
3 p5 + 2 p4 + 2 p3 , |
|
|
|
|
|
|
F |
|
|
|
|||||||
|
|
|
|
|
|
|
|
|
|
|
|
|
|
|
|
|
||
|
|
|
|
|
|
|
|
|
|
|
|
|
|
|
|
|
|
|
|
|
|
|
|
|
Рисунок 3- (а - безызбыточный механизм, |
||||||||||||
|
2 p5 + p4 + p3 , |
|
|
|
|
|||||||||||||
|
|
|
|
(22) |
|
|
b-условное изображение кинематических |
|||||||||||
|
p5 + p4 + p3 , |
|
|
|
||||||||||||||
|
|
|
|
|
|
|
|
|
|
|
|
|
|
пар) |
|
|
|
|
|
2 p5 + p4 + p3 , |
|
|
|
|
|
|
|
|
|
|
|
|
|
|
|||
|
|
|
|
|
|
|
|
|
|
|
|
|
|
|
|
|
|
|
|
p5 + p4 + p3 . |
|
|
|
|
|
При построении были |
использованы |
||||||||||
|
Теперь найдем, какие (адресно) шарниры |
|
|
|||||||||||||||
|
три вида пар: p5 - обычный шарнир, p4 - |
|||||||||||||||||
исследуемого механизма необходимо заменить |
сферический шарнир с пальцем, p3 - |
|||||||||||||||||
на пары более высоких классов и на какие |
сферический шарнир без пальца (рисунок |
|||||||||||||||||
именно. Для этого составим систему уравнений |
3,b). |
|
|
|
|
|
|
|
|
|
|
|||||||
так: в левых частях запишем суммы |
|
|
|
|
|
|
|
|
|
|
|
|
|
|||||
обозначенных буквами кинематических пар, |
|
|
ЛИТЕРАТУРА: |
|
|
|
|
|
||||||||||
входящих в рассматриваемый |
механизм |
и его |
|
|
1. Дворников Л.Т. Опыт структурного |
|||||||||||||
разделения, а в правых частях их же в виде |
синтеза. |
|
|
ТММ, |
|
Санкт- |
||||||||||||
суммы соответствующих решений по (22) |
|
Петербург,2004,вып,2,т.2,с.3…17 |
|
|
||||||||||||||
A + B + C + D + E + F +G = 3 p5 + 2 p4 + 2 p3 , |
|
2. |
Дворников |
Л.Т., Гудимова |
Л.Н. |
К |
||||||||||||
|
+ B + C |
+G = 2 p5 |
+ p4 + p3 , |
|
|
разработке |
метода |
исключения |
||||||||||
A |
(23) |
|
||||||||||||||||
|
+ E + F |
= p5 + p4 |
+ p3 , |
|
избыточных связей в плоских механизмах. |
|||||||||||||
D |
|
|
||||||||||||||||
D + E + F +G = 2 p5 + p4 + p3 , |
|
|
//Материалы четырнадцатой научно- |
|||||||||||||||
|
|
|
|
|
|
практической конференции по проблемам |
||||||||||||
|
+ B + C |
= p5 + p4 + p3 . |
|
|
механики |
и |
машиностроения. |
/ |
||||||||||
A |
|
|
||||||||||||||||
|
Система содержит семь неизвестных и пять |
СибГИУ.Новокузнецк, 2004. – С. 47-60. |
|
|||||||||||||||
|
|
|
|
|
|
|
|
|
|
|
|
|
|
|||||
уравнений, чтобы ее решить |
зададимся |
еще |
|
|
|
|
|
|
|
|
|
|
|
|
|
369

XIII Международная научно-практическая конференция «СОВРЕМЕННЫЕ ТЕХНИКА И ТЕХНОЛОГИИ»
КИНЕТОСТАТИЧЕСКОЕ ИССЛЕДОВАНИЕ ПЛОСКОЙ ШЕСТИЗВЕННОЙ ШАРНИРНОЙ ГРУППЫ АССУРА С ЧЕТЫРЕХУГОЛЬНЫМ ЗАМКНУТЫМ ИЗМЕНЯЕМЫМ КОНТУРОМ
Стариков С. П., Дворников Л. Т.
Сибирский государственный индустриальный университет,
Россия, г. Новокузнецк, ул. Кирова, 47 E-mail: starikov_sp@mail.ru
Представленная в заглавии задача до настоящего времени ни кем не была решена. Речь пойдет об одной из известных [1] десяти не распадающиеся на более простые шестизвенных групп Ассура. Прежде всего, сформулируем и докажем теорему о силах и реакции в трехшарнирном звене.
Если в трехшарнирном звене известны тангенциальные составляющие сил реакций во всех трех кинематических парах и перпендикулярные к ним направления не пересекаются в одной точке, то известными являются и полные реакции во всех кинематических парах.
Рассмотрим трехшарнирное звено (рисунок 1), в котором известны все тангенциальные составляющие реакций в
кинематических парах: RAτ , RBτ и RCτ .
|
|
|
RC |
|
|
h2 |
Rτ |
|
ε |
|
C |
RAτ |
|
|
|
|
h1 |
|
|
|
|
R n |
|
|
|
|
|
A |
|
|
C |
|
|
C |
B RBτ
Рисунок 1 – Трехшарнирное звено
При известных тангенциальных составляющих реакций в кинематических парах, оказываются известными и направления нормальных составляющих этих реакций. На пересечении продолжений направлений нормальных составляющих реакций в парах A и B, фиксируем точку ε . Эта точка принадлежит рассматриваемому звену. Следовательно, можно найти сумму моментов сил для треугольного звена относительно точки ε
∑M(ε ) = 0;
звена
т. е.
RτB εB − RτA εA + RCτ h2 +
+ RCn h1 + ... = 0,
(1)
где неизвестной оказывается единственная реакция, а именно RCn .
В (1) h1 и h2 – плечи реакций RCn и RCτ .
Момент внешних сил и сил инерции считается известными.
После определения составляющей реакции RCn , может быть найдена полная
реакция в шарнире C, т. е. RC из условия
RCτ + RCn = RC .
Далее, составив сумму сил для рассматриваемого трехшарнирного звена, можно определить нормальные составляющие реакций в шарнирах A и B:
∑F = 0 RAn и RBn .
|
|
|
|
|
звена |
|
|
|
|
|
|
|
|
|
|
|
Из условий |
|
|
Aτ + |
|
An = |
|
A |
и |
||||
|
|
R |
R |
R |
||||||||||
|
|
Bτ + |
|
Bn = |
|
B , |
определяются полные |
|||||||
R |
R |
R |
реакции в шарнирах A и B ( RA и RB ). Таким образом, удается определить
полные реакции во всех кинематических парах трехшарнирного звена.
Обратимся непосредственно к кинетостатическоому исследованию плоской шестизвенной группы Ассура с четырехугольным замкнутым изменяемым контуром (рисунок 2).
370

Современные техника и технологии 2007
|
|
|
|
|
ε′′ |
|
|
|
|
|
|
|
|
|
|
ε |
|
|
|
|
|
|
|
|
ε′ |
|
RBτ |
|
|
|
|
|
|
|
R n |
|
|
|
1 |
|
Rτ |
||
|
|
|
|
|
|
|
|
C 3 |
||
RAτ |
1 |
A1 |
|
|
B2 |
|
|
|
C |
|
|
|
A |
|
|
|
|
|
|
|
|
RKτ 6 |
K 1 5 |
E REτ 5 3 |
|
D |
||||||
|
|
|
6 |
|
|
|
|
RDτ |
|
|
|
|
H |
|
|
F |
RFτ |
3 |
|||
|
|
RHτ |
6 |
4 |
|
|
||||
|
|
|
|
|
4 |
G |
|
|
|
|
|
|
|
|
|
Rτ |
|
|
|
|
|
|
|
|
|
|
|
|
|
|
|
|
|
|
|
|
|
G4 |
|
|
|
|
|
Рисунок 2 - Шестизвенная группа с четырехугольным замкнутым изменяемым контуром
1) Прежде всего, рассмотрим равновесие всех трех поводков группы HK, FG и CD, из суммы моментов, относительно кинематических пар D, G и шарнира H для поводка 6, определяем тангенциальные составляющие реакции в кинематических
парах C, D и K ( |
|
|
|
τ |
, |
|
τ |
и |
|
|
τ |
): |
|
|
|
|
|||||||
R |
R |
R |
|
|
|
|
|||||||||||||||||
|
|
С3 |
|
F 4 |
|
|
|
K 6 |
|
|
|
|
|
|
|
||||||||
∑M(D) = 0 |
|
|
|
|
Cτ 3 ; |
|
|||||||||||||||||
R |
|
||||||||||||||||||||||
звено3 |
|
|
|
|
|
|
|
|
|
|
|
|
|
|
|
|
|
|
|
|
|||
∑M(G) = 0 |
|
|
Fτ 4 ; |
|
|||||||||||||||||||
R |
|
||||||||||||||||||||||
звено4 |
|
|
|
|
|
|
|
|
|
|
|
|
|
|
|
|
|
|
|
||||
∑M(H ) = 0 |
|
Kτ 6 . |
|
||||||||||||||||||||
R |
|
||||||||||||||||||||||
звено6 |
|
|
|
|
|
|
|
|
|
|
|
|
|
|
|
|
|
|
|
|
|||
Очевидным |
при |
|
этом |
|
|
|
являются |
||||||||||||||||
соотношения: |
|
τ |
= − |
|
τ |
, |
|
τ |
= − |
|
τ |
и |
|||||||||||
R |
R |
R |
R |
||||||||||||||||||||
|
|
|
С3 |
|
|
|
|
D3 |
|
|
F 4 |
|
G4 |
|
RKτ 6 = −RHτ 6 , как образующие пары сил.
2)На продолжении поводков FG и CD, фиксируем точку их пересечения – точку ε .
3)Взяв сумму моментов относительно точки ε для всей группы, определяем
тангенциальную составляющую реакции в шарнире A (направив тангенциальную составляющую перпендикулярно линии соединяющей точки ε и A, а нормальную составляющую реакции по этой линии):
∑M(ε) = 0 RAτ1 .
группа
4) На продолжении поводка KH и линии
Aε , фиксируем точку их пересечения – точку
ε ′ .
5) Взяв сумму моментов относительно
точки ε ′ для |
звена 1, |
определяем |
|
тангенциальную |
составляющую |
реакции в |
|
шарнире B (направив тангенциальную |
|||
составляющую |
перпендикулярно |
линии |
соединяющей точки ε ′ и B, а нормальную составляющую реакции по этой линии):
∑M(ε ′) = 0 RВτ1 .
звено1
6)На продолжении поводков FG и KH, фиксируем точку их пересечения – точку ε ′′ .
7)Взяв сумму моментов относительно
точки ε ′′ для |
звена 5, |
определяем |
|
тангенциальную |
составляющую |
реакции в |
|
шарнире E (направив тангенциальную |
|||
составляющую |
перпендикулярно |
линии |
соединяющей точки ε ′′ и E, а нормальную составляющую реакции по этой линии):
∑M(ε ′′) = 0 REτ 5 .
звено5
8) Выделяем звено 2. В нем известны тангенциальные составляющие реакций во всех трех кинематических парах и направления нормальных составляющих реакций не пересекаются в одной точке, следовательно, для этого звена применить
теорему о реакциях в трехшарнирном звене
и определить все полные реакции в шарнирах
E, B и C ( RE , RB и RC ).
9) Выделяем поводок CD, так как в этом поводке известна одна полная реакция в одной кинематической паре, то можно взять в нем сумму сил и определить полную реакцию во второй кинематической паре:
∑F = 0 RD .
звено3
10) Выделяем первое звено, взяв в нем сумму сил, определяем полные реакции в шарнирах A и K:
∑F = 0 RA и RK .
звено1
11) Выделяем поводок KH, так как в этом поводке известна одна полная реакция в одной кинематической паре, то можно взять в нем сумму сил и определить полную реакцию во второй кинематической паре:
∑F = 0 RH .
звено 6
371

XIII Международная научно-практическая конференция «СОВРЕМЕННЫЕ ТЕХНИКА И ТЕХНОЛОГИИ»
12) Выделяем пятое звено, взяв в нем сумму сил, определяем полную реакцию в шарнире F:
∑F = 0 RF .
звено5
13) Выделяем поводок GF, так как в этом поводке известна одна полная реакция в одной кинематической паре, то можно взять в нем сумму сил и определить полную реакцию во второй кинематической паре:
∑F = 0 RG .
звено 4
Таким образом, удалось определить полные реакции во всех кинематических парах.
Следовательно, группа полностью кинетостатически разрешена.
ЛИТЕРАТУРА:
1) Добровольский В. В. Основные принципы рациональной классификации механизмов, в кн. Структура и классификация механизмов. — М.: Изд-во АН СССР, 1939г.
СОВЕРШЕНСТВОВАНИЕ МЕТОДОВ ОБРАБОТКИ ДРЕВЕСИНЫ СТРОГАНИЕМ
Степанов Д.Е., Павлюк В.А., Нехорошков О.Н.
Томский государственный архитектурно-строительный университет
634003, г. Томск, пл. Соляная 2, тел (3822)-652-787 Е-mail: aspiranttsuab@mail.ru
В мировой практике деревообработки прослеживается стремление к улучшению качества продукции и снижению энергозатрат на ее производство. В деревообрабатывающем производстве одним из основных показателей качества является шероховатость обработки поверхности. Для уменьшения шероховатости поверхности при строгании используются различные способы, а именно: применяются сдвоенные ножи, используются различные способы крепления ножей для улучшения точности их установки, от которой в значительной степени зависит образование волн. Также для уменьшения сколов применяются прижимные приспособления. Известен также ряд изобретений, связанных с использованием спиральных ножей и различных способов их установки.
Сущность изобретения [1] вала деревообрабатывающего станка со спаренными ножами заключается в том, что каждый из ножей имеет две режущих кромки расположенные под разными углами к обрабатываемой поверхности, причем одна выступает над другой. Преимущество такой конструкции ножей заключается в том, что вторая кромка снимает гораздо меньший слой древесины и расположена под более тупым углом к обрабатываемой поверхности чем первая. Таким образом она выполняет роль цикли, позволяющей частично снять
шероховатости, образованные после срезания первым ножом. Недостатком этой конструкции является сложность заточки ножей. Представляется возможным усовершенствовать конструкцию ножей для упрощения и увеличения точности заточки, не изменяя сущности изобретения.
Образование сколов при обработке древесины, имеющей криволинейное расположение слоев и сучки, происходит в результате задира волокон, имеющих разную направленность. Для устранения этого явления используются прижимные приспособления, идущие впереди ножа [2] . Аналогичные устройства используются в станках для получения шпона и зарекомендовали себя с положительной стороны, что позволяет сделать вывод о целесообразности применения такой конструкции в строгальных станках.
Наиболее перспективными разработками с точки зрения снижения энергозатрат на обработку древесины фуговальными станками следует считать применение спиральных ножей или ножевых валов со спиральным расположением вставок. Аналогичные разработки в этом направлении были сделаны в области металлообработки, а именно при использовании фрез со спиральными режущими кромками. В этом случае в резание материала одновременно используется не вся длина кромок, а только
372

Современные техника и технологии 2007
их части, что позволяет значительно снизить удельный расход энергии на резание и уменьшить шероховатость обработки. Однако использование аналогичных фрез в деревообработке весьма проблематично в связи с тем, что при каждой переточке диаметр фрезы будет уменьшаться, поэтому для использования такого принципа обработки древесины используются спиральные ножи [3]. Самой большой проблемой в использовании таких ножей является их точная установка. Как правило
использование спиральных |
ножей дает |
некоторое искривление |
обработанной |
плоскости. Особенно в том случае когда ножи состоят из нескольких элементов. Такой
является |
спиральная ножевая |
головка. |
|
Массивный |
барабан, |
подвергнутый |
тщательной шлифовке и балансировке, снабжен 4-сторонними ножевыми вставками из твердого сплава. Вставки расположены в геликоидальных пазах в шахматном порядке, с наложением траекторий резания. Такая головка не только дает высочайшее качество поверхности, но и большую скорость удаления стружки, и низкий уровень шума. Каждая вставка может быть снята в индивидуальном порядке для заточки или замены.
Представляет интерес конструкции ножевых валов в которых ножи устанавливаются в нужное положение путем скручивания составных частей вала и соответственно ножей между ними [4]. Сущность изобретения: спиральный нож в станке закрепляется в пазах посредством клиньев и винтов. Крутящий момент от вала к спиральным ножам передается за счет сил трения, возникающих в конических сопряжениях колец с втулкой и резьбовыми втулками. Пружина обеспечивает торможение втулки. Спиральный нож устанавливается следующим образом: в сторону отводятся крайние кольца, нож вставляется в паз среднего кольца и зажимается клиньями, затем крайние кольца вращаются до тех пор, пока их пазы не совпадают с концами спиральных ножей. После этого кольца перемещают в осевом направлении к спиральному ножу. После попадания ножа в пазы крайних колец производят его крепление. Вращением резьбовых втулок обеспечивают фиксацию колец на валу. Съем спирального ножа производят следующим образом: освобождается крепление ножа в крайних кольцах при отводе последних в сторону от ножа, затем освобождается крепление ножа в среднем кольце с последующим свободным сниманием ножа.
Недостатком спиральных ножей является их небольшая толщина приводящая к вибрации и неустойчивости параметров обработки. При использовании таких ножей представляется целесообразным производить заточку без снятия с вала. Для этого требуется специальное оборудование и может проявляться недостаток описанный выше (уменьшение диаметра).
На основании анализа литературы был сделан вывод о перспективности направления снижения энергетических показателей резания путем использования прямых ножей и изменения угла встречи
режущих кромок с волокнами ϕ не 90o , как у
обычных станков (Рис. 1), а больше (Рис. 2). Для проверки этого предположения проведены экспериментальные исследования на фуговальном станке.
Рис. 1
Рис. 2
373
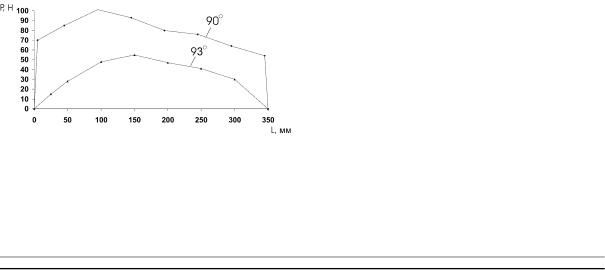
XIII Международная научно-практическая конференция «СОВРЕМЕННЫЕ ТЕХНИКА И ТЕХНОЛОГИИ»
Измерения силы сопротивления подаче заготовки производилось специально разработанным и изготовленным динамометрическим устройством, состоящим из корпуса, вала, пружины, рычага и пишущего устройства. Графики зависимости отображались на листе масштабной бумаги. Настройка угла встречи с волокнами осуществлялась путем изменения положения направляющего уголка относительно ножевого вала. Проведенные экспериментальные исследования показали (Рис. 3) существенное влияние величины угла встречи с волокнами на силовые показатели резания, при этом шероховатость поверхности, характеризующая качество обработки практически не изменяется. Согласно экспериментальным данным наиболее предпочтительным при обработке
сухой древесины является угол ϕ = 93o . При
обработке влажной древесины был получен положительный эффект, заключающийся в выявлении текстуры поверхности для использования в декоративных целях.
Рис. 3
Выводы:
1. Разработанные и применяемые ножевые валы со спиральными ножами
требуют дополнительной доработки для получения необходимого результата при обработке плоскостей изделий из дерева.
2.Применение сдвоенных ножей и прижимных устройств могут дать значительное улучшение качества обработанной поверхности.
3.Для устранения недостатков, связанных с использованием спиральных ножей и ножевых валов, более эффективным представляется использование обычных прямых ножей с изменением угла встречи режущих кромок с волокнами за счет
введения такого же угла ϕ1 = 3o между
направлениями векторов скорости резания V и скорости подачи U.
ЛИТЕРАТУРА:
1. Курбатов В.Г. Вал
деревообрабатывающего станка / Патент РФ на изобретение №2075377.
2.Китсуйи Хасегава[JP]
Строгальный станок / Патент РФ на
изобретение №2066272.
3.Любченко В.И. Резание древесины и древесных материалов. - М.: Лесная промышленность, 2002.
4.Большаков М.М. Ножевой вал
деревообрабатывающего станка / Патент РФ на изобретение №2051787.
РАСЧЕТ ТРАВЕРСЫ ДЛЯ ДЛИННОМЕРНЫХ ГРУЗОВ*
Цыремпилова З.В., Егодуров Г.С., Цынгеев Д.Н. Восточно-Сибирский государственный технологический университет,
Россия, Улан-Удэ, ул. Ключевкая40В E-mail: office@esstu.ru
В ОАО <Бурятзолото> грузоподъемными машинами перемещают штучные грузы, подают различные материалы к месту их укладки, производят погрузочно-разгрузочные операции на складах. Подъем длинномерных грузов весом F производят при помощи траверсы, подвешиваемой к крюку крана канатными стропами, которые направлены под углом α к вертикали (рис1а). Требуется определить размеры поперечного сечения
траверсы, обеспечив 6-ти кратный запас по пределу прочности, то есть nu =6 .Траверса изготавливается из трубы с внешним диаметром D (рис 1 ,2) и длинной l. Материал сталь3 по ГОСТ14249-89 с пределом прочности σu . Задачу решаем используя
математическую программу Mathcad[1,2].Он позволяет достаточно просто реализовать вычислительный алгоритм любой сложности. Большой набор встроенных
374

Современные техника и технологии 2007
специализированных функций делает его особенно удобной для расчета конструкций на прочность. Традиционное программирование разводит во времени процесс решения задачи на три независимых этапа: программа пишется, а за тем отлаживается и оптимизируется. В среде Mathcad эти процессы слиты воедино, то есть создание "программы" идет параллельно с ее отладкой.
Рис.1. Расчетная схема траверсы
Исходные данные будем вводить с российскими размерностями. Но предварительно, встроенные в MathCAD размерности, будем менять с английского названия на российские, записав:
N = |
1 |
|
F |
|
solve, N → 50000000000000000002 F(α) |
||||||||||||||
|
cos(α) |
||||||||||||||||||
2 |
|
|
|
|
|
|
|
|
|
|
|
|
|
|
|
||||
Следовательно, |
|
допускаемая |
|
продольная |
|||||||||||||||
сжимающая сила траверсы равна. |
|||||||||||||||||||
|
|
N = |
1 |
F |
|
тоесть |
N adm := |
1 |
F |
||||||||||
|
|
|
|
|
|||||||||||||||
|
|
|
2 |
|
|
|
|
|
|
|
|
|
|
|
|
2 |
|
||
Геометрические |
|
|
|
|
|
характеристики |
|||||||||||||
заданного |
|
|
|
поперечного |
|
|
|
|
сечения |
||||||||||
(рис.1,с),выраженные через диаметр <D>, |
|||||||||||||||||||
имеют вид [3]: |
|
|
|
|
|
|
|
|
|
|
|
|
|
||||||
Площадь поперечного сечения трубы |
|||||||||||||||||||
|
|
|
|
|
A = |
πD 2 |
− |
πD3 (0,9 D) 2 |
|||||||||||
|
|
|
|
|
|
4 |
|
|
|
4 |
|
|
|
|
|
||||
|
|
|
|
|
|
|
|
|
|
|
|
|
|
|
|
|
|||
Внешний диаметр трубы равен |
|||||||||||||||||||
|
|
|
|
|
|
|
|
D = |
|
|
A |
|
|
|
|
|
|
||
|
|
|
|
|
|
|
|
0.148 |
|
|
|
|
|
|
|||||
Осевой момент инерции |
|
|
|
|
|
||||||||||||||
|
|
|
|
|
|
|
πD |
4 |
|
|
0.9 D |
|
4 |
|
|||||
|
|
|
|
|
|
|
|
|
|
|
|
||||||||
|
|
|
|
I x = |
|
|
|
− |
|
|
|
|
|||||||
|
|
|
|
|
|
|
|
64 |
|
|
|
D |
|
|
|
Радиус инерции ix = IAx . Необходимый
размер сечения подбираем из условия устойчивости методом последовательных приближений [3].
σ = NAadm ≤ φ σ adm.c
м:=m, H:=N, kH:=103N Па:=Ра, МПа:=106*Ра, MM:=10-3m 0:=deg α := 45o F:=30kH μ :=1 l:=3м.
Материал - Cт3:
σ ус := 240МПа σ pr := 210МПа σи := 400МПа
Е:=2*105МПа nИ:=6
σ adm.c := σи − допускаемое напряжение nи
Вес поднимаемого груза поровну распределяется между точками подвеса к траверсе, вызывая растяжение наклонных канатов и сжатие самой траверсы. Таким образом, траверса работает на устойчивость и выполняет роль распорки, предохраняющей груз от возможного деформирования по горизонтали при наклонных канатах. Усилие в траверсе N найдено из условии равновесия узла (см.рис 1,b). а:=а F:=F
∑ F |
=0N |
k |
cos(α)− |
F |
=0solve, N |
k |
→ |
1 |
|
F |
|
|
|
|
|
||||||||
γ |
|
2 |
|
2 |
|
cos(α) |
|||||
|
|
|
|
|
|
||||||
∑ F z = 0 N k sin α − N = 0solve, N |
→ N k sin(α) |
||||||||||
|
sin(α) := 0.707, co(α) := 0.707 |
|
|
|
Первое приближение. Сначала площадь поперечного сечения определяем из расчета на простое сжатие (из условия прочности), то есть приняв
φ1 :=1 ; σ = NAadm ≤ σ adm.c φ1 ;
|
|
|
A := |
|
|
|
N adm |
|
|
|
; |
D := |
|
|
|
A |
; |
|
|
||||
|
|
|
|
|
|
σ |
adm.c |
φ |
|
|
|
0.148 |
|
|
|
||||||||
|
|
|
|
|
|
|
|
1 |
|
|
|
|
|
|
|
|
|
|
|
|
|||
|
πD 4 |
|
|
|
0.9 D 4 |
|
ix := |
|
|
|
I x |
|
|
μ l |
|
||||||||
I x := |
|
|
|
1 |
− |
|
|
|
|
|
; |
|
|
|
; |
λ1 := |
|
; |
|||||
|
64 |
D |
|
|
|
|
|
|
ix |
||||||||||||||
|
|
|
|
|
|
|
|
|
|
|
|
|
|
A |
|
|
|||||||
|
|
|
|
|
|
|
|
|
|
|
|
|
|
|
|
|
|
|
|
|
|
|
|
Используя |
встроенную функцию linterp |
||||||||||||||||||||||
( vλ, vφ, λ1 ) |
|
|
φ1 = 0.126 |
|
Далее |
определяем |
|||||||||||||||||
допускаемую |
|
|
нагрузку |
|
из |
|
|
условия |
|||||||||||||||
устойчивости |
|
|
|
|
|
|
|
|
N adm.1 := φ1 σ adm.c A |
||||||||||||||
N adm.1 |
=1.884kH |
|
|
|
|
|
|
|
|
|
|
|
|
|
|
|
|||||||
Поскольку |
|
N adm.1 < N adm , то |
размер |
<D> |
надо увеличить. Дальнейшие повторяющиеся вычисления запрограммируем, используя оператор цикла с предусловием While [1,2]. Сначала составляем два вектора данных: вектор νφ коэффициентов снижения
допускаемого напряжения на сжатие [3] и вектор νλ значений гибкости стержня, используя ранжированную переменную i [2]. Системной переменной ORIGIN – номер
375

XIII Международная научно-практическая конференция «СОВРЕМЕННЫЕ ТЕХНИКА И ТЕХНОЛОГИИ»
начального индекса элементов вектора (по |
|
|
умолчанию она равна нулю) |
присваиваем |
N adm.2 := φ0 σ adm.c A N adm.2 =14.68кН |
единицу: ORIGIN ≡1 i≡ 1…22 νλi |
≡ i 10 |
|
νφ ≡ (0.987 0.962 0.931 0.894 0.852 0.805 0754
0.686 0.612 0.542 0.478 0.419 0.364 0.315
0.276 0.244 0.218 0.196 0.177 0.161 0.147
0.135)
|
1 |
2 |
3 |
4 |
5 |
6 |
7 |
8 |
9 |
10 |
|
|
|
|
|
|
|
|
|
|
|
1 |
10 |
20 |
30 |
40 |
50 |
60 |
70 |
80 |
90 |
100 |
|
|
|
|
|
|
|
|
|
|
|
νλT =
D(φ0 ) :=
while
φ1 ← φ0
A ← |
|
Nadm |
|
|
|
|
|
|
|
||||
φ |
σ |
adm.c |
|
|
|
|
|||||||
|
|
1 |
|
|
|
|
|
|
|
||||
D ← |
|
|
A |
|
|
|
|
|
|
|
|||
|
0.148 |
|
|
0.9 D 4 |
|
||||||||
I x ← |
π |
D4 |
|
|
|||||||||
|
|
|
|
|
1 |
− |
|
|
|
||||
|
64 |
|
D |
||||||||||
|
|
|
|
|
|
|
|
|
|||||
|
|
|
|
|
|
|
|
|
|
|
|
|
|
ix ← |
|
I x |
|
|
|
|
|
|
|
|
|
||
|
A |
|
|
|
|
|
|
|
|
||||
|
|
|
|
|
|
|
|
|
|
|
|||
λ ← |
|
μ l |
|
|
|
|
|
|
|
|
|
||
|
ix |
|
|
|
|
|
|
|
|
||||
|
|
|
|
|
|
|
|
|
|
||||
φ11 ← l int erp(νλ,νφ, λ) |
|
|
D1 ← D
(break ) if (φ11 −φ1 ) 100% ≤ 5%
φ11
φ0 ← φ0 +φ11
2
D
|
|
D(0.5) = 0.066м D := 0.066м |
|
|
|
||||||||||
A := |
πD 2 |
|
π(0.9 D)2 |
I x |
|
|
πD 4 |
|
|
0.9D 4 |
|
||||
|
− |
|
|
|
|
:= |
|
1 |
− |
|
|
|
|||
4 |
|
|
4 |
|
64 |
D |
|||||||||
|
|
|
|
|
|
|
|
|
|
|
|
||||
|
|
|
|
|
|
|
|
|
|
|
|
|
|
|
|
|
ix := |
|
|
I x |
λ2 |
:= |
μ l |
λ2 |
=135.144 |
|
|
||||
|
|
|
A |
ix |
|
|
|
|
|||||||
|
|
|
|
|
|
|
|
|
|
|
|
|
|
:= |
|
N adm − N adm.2 |
|
100% |
= 2.123% |
|
|
N adm |
|||||
|
|
|
|
|||
|
λlim := |
π 2 E |
λlim = 96.952 |
|||
|
σ pr |
|||||
|
|
|
|
|
Поскольку λ2 > λlim , то критическую силу определяем по формуле Эйлера
Ncr := |
π 2 |
E I x |
Ncr = 70.253кН |
|
(μ l)2 |
||||
|
|
Коэффициент запаса устойчивости
ncr := |
Ncr |
ncr = 4.684 |
|
N adm |
|||
|
|
Для обеспечения требуемого условия прочности округляем полученные размеры поперечного сечения трубы до
|
D := 70мм |
|
d := 0.9D ,Тогда |
|
||||||
I x := |
π D 4 |
|
|
0.9 D 4 |
|
Ncr := |
π 2 |
E I x |
||
|
1 |
− |
|
|
|
|
|
|||
64 |
D |
(μ l)2 |
||||||||
|
|
|
|
|
|
|||||
|
|
|
|
|
|
|
|
|
|
ncr := |
Ncr |
ncr = 5.926 |
|
N adm |
|||
|
|
Таким образом, расчеты, выполненные нами в среде Mathcad, показывают, что при коэффициенте запаса по пределу прочности nи = 6 и при грузоподъемности F=30кН
поперечное сечение траверсы должно быть не менее D=70мм и d=64мм.
При помощи встроенной функции linterp ( νλ,νφ, λ2 ) - аппроксимирующей данные
векторов νλ и νφ линейной зависимостью, находим значение φ0 , где νφ -вектор действительных данных аргумента; νφ -
вектор действительных данных значении того же размера; λ2 -значение аргумента, при
котором вычисляется интерполирующая функция.
φ0 := l int erp(νλ,νφ, λ2 ) φ0 =0,339
Допускаемая нагрузка
ЛИТЕРАТУРА:
1.Очков В.Ф. Mathcad 12 для студентов и инженеров.- СПб.: БХВ - Петербург, 2005 - 464с.
2.Кирьянов Д.В. Самоучитель Mathcad 13. - СПб.: БХВ - Петербург, 2006. - 528 с. 3.ФеодосьевВ.И.Сопротивление материалов.
-М.: Наука, 1986. - 512 с.
*Работа поддержана программой «Развитие научного потенциала высшей школы(20062008годы)» № РНП 2.1.2.8630.
376

Современные техника и технологии 2007
НОВЫЙ ПОДХОД К ОЦЕНКЕ ПРОЧНОСТИ МАТЕРИАЛОВ ПО КРИТЕРИЯМ МЕХАНИКИ РАЗРУШЕНИЯ ПРИ СЛОЖНОМ СОПРОТИВЛЕНИИ
Цырфа А.А., Полянский А.А., Соляник А.С.
Томский политехнический университет, Россия, г. Томск, пр. Ленина, 30 e-mail: tzitfa@sibmail.com
В науке о прочности материалов одним из сложных, и до конца не решенным остается вопрос оценки прочности материалов при сложном сопротивлении (сложном напряженном состоянии). Выходом из этого затруднения является оценка прочности по теориям (гипотезам) прочности. Наибольшее распространение в инженерной расчетной практике получили теории: наибольших линейных деформаций; теория наибольших касательных напряжений ( к ней близка теория мора); энергетическая теория наибольшей потенциальной энергии деформации. Эти теории удовлетворительно оценивают прочность при условии выполнения гипотез сопротивлении материалов (гипотеза прочности, однородности, изотропности материалов).
Современное машиностроение в настоящее время требует оценки прочности изделий, в которых не выполняются эти гипотезы. Так крупногабаритные изделия, имеющие сварные швы (рулонированные сосуды высокого давления, толстостенные трубы, корпусные детали и.т.п.), практически не удается изготовить без дефектов, а также
оно могут |
появиться |
в процессе |
||
эксплуатации. |
Оценка |
прочности |
и |
|
долговечности |
их |
по |
критериям |
|
сопротивления |
материалов |
некорректно, |
поэтому, начиная с Гриффится [11] ученные стали разрабатывать критерии с позиции механики разрушения [1,2,9,12].
Предложен ряд критериев, которые в той или иной степени достоверно оценивают прочность тел с трещиной при простых схемах деформации - нормальный отрыв, продольный и поперечный сдвиг у берегов трещины(рис.1).
Рис.1 схема перемещений в зоне трещины К таким критериям, при хрупком
разрушении, можно отнести критический коэффициент интенсивности напряжений К1С,
К11С, К111С, (вязкость разрушения), деформационные критерии – критическое
раскрытие трещины δ1С при квазиупругом и вязком разрушении; критерий Макклинтока Ф.А. и Холла У.Дж.- величина придельной деформации у вершины трещины в локализованной области сравнимой с величиной зерна металла; размер пластической области у вершины трещины; её геометрические параметры; критическая длина трещины и др.
Однако применение этих критериев для сложных случаев напряжения тела с трещиной до сих пор не решено, а те которые разработаны, не дают общего подхода оценки прочности и направлены на решение, на решение конкретной задачи.
Поэтому поиск универсального подхода к этой проблеме актуален.
Самым простым подходом было бы сохранение подходов обычных теорий прочности к телам с трещиной. Такую мысль уже высказали некоторые исследователи [6], но развитие она не получила.
Предлагается подходы теории прочности применить к локализованной привершинной области трещины.
Напряженное состояние у вершины трещины описывается уравнениями [4], в которых помимо нагрузки вводят параметры трещины, её ориентации и координаты точки, в которой определяется напряжения. Поэтому общий подход можно сформулировать:
прочность тела с трещиной будет обоспечиваться до тех пор, пока некоторая функция главных напряжений у вершины трещины не достигнет предельной величины, определяемой из эксперимента.
Функцию выбираем по принятой гипотезе прочности. Этот подход универсален.
Например, для критерия – вязкость разрушения применительно к высокоупрочняемым сталям условие
запишется: Кэкв = К21 + 4К112 ≤ К1с Для пластины с произвольно
ориентированной трещиной:
К1 |
= σ |
πl sin 2 α , |
|
||
К2 |
=τ |
πl = |
σ |
πl sin 2α sin 2 |
α |
|
|
|
2 |
|
|
377

XIII Международная научно-практическая конференция «СОВРЕМЕННЫЕ ТЕХНИКА И ТЕХНОЛОГИИ»
,где α – угол между направлением трещины и направлением нагрузки.
Тогда при разрушении должно выполняться равенство:
К1с = σ разр πl
sin 4 α + sin 2 2α .
Откуда для нормально расположенной трещины: К1с = α1 πl ,
σ разр = |
σ 1 |
|
|
; |
|
|
||
|
sin 4 α + sin 2 2α |
где σ1 – напряжение при разрушении пластины с нормально ориентированной трещиной, т.е. разноориентированная трещина вносит поправку
f (α) = sin 4 α + sin 2 2α .
Для проверки правомерности данных подходов гипотез прочности сопротивления материалов к телу с трещиной были построены диаграммы предельного состояния для критерия Панасюка В.В. [3]с позиции трех вышеуказанных гипотез сопротивления материалов. На эти диаграммы были наложены точки соответствующие опытным результатам испытаний других исследователей Пука, Панасюка, Корнет – Грасси [7,8,10].
Экспериментальные точки достаточно близко ложатся на диаграммы придельных состояний. Такую же проверку привели и для интегральных и других критериев механики разрушения. Результаты сравнения также оказались вполне удовлетворительными [5] .
В заключении можно утверждать, что оценка прочности тел с трещиной по критериям механики разрушения с позиции гипотез прочности сопротивления материалов
является удовлетворительной и может быть рекомендована для практических расчетов деталей машин и элементов конструкций при наличии в них трещин при сложном сопротивлении.
ЛИТЕРАТУРА:
1.Леонов М.Я. , Упрощенная модель хрупкого тела, М., ВИНИТИ, 1960 г.
2.Панасюк В.В., О развитии произвольно ориентированной прямолинейной трещины при растяжении пластины., Прикладная механика.,1965 г.
3.Панасюк В.В. , Предельное равновесие хрупких тел с трещинами., Киев, Наукова думка.,1968 г.
4.Прикладные вопросы вязкости разрушения., М., Мир., 1968 г.
5.Соляник А.С., Экспериментальное исследование зоны разрушения металлов.,
Томск., 1978 г.
6.Черепанов Г.Н. , Некоторые основные вопросы линейной механики разрушения., Проблемы прочности., 1971 г.
7.Cornet I, Grassy R.C., Fracture of Inoculated Iron Under Biaxial Stresses Journal of App. Mach 1955.
8.Cornet I., A Study of Theories of Fracture Under Combined Stresses Trans. ASME,1961.
9.Irwin G.R., Encyclopedia of Physics.,
1958.
10.Grassy R.C.? Fracture of Gray Cast Iron Tubes Under Biaxial Stresses Journal of App.,1958.
11.Griffith A.A. The theory of rupture. Proc. I st. Intern. Congers. App. Mech. 1924.
12.Orovan E. Report on Progress in Physics, London. 1945.
ОБЗОР МЕТОДОВ РАСЧЕТА ТРЕНИЯ В ПЕРЕДАЧАХ ЗАЦЕПЛЕНИЕМ
Черемнов А.В., Ефременков Е.А.
Томский политехнический университет, Россия, г.Томск, пр.Ленина, 30
E-mail: Arsenij85@sibmail.com
Современные машины невозможно представить без передач зацеплением. В качестве таких передач могут выступать зубчатые, червячные, цевочные передачи, передачи с промежуточными телами качения (ПТК). В каждой из этих передач имеются контактирующие поверхности, следовательно, имеет место трение. Трение
– это основная причина износа деталей и
снижения КПД передач зацеплением. Изучению вопросов трения в зацеплении посвещано много работ [1,2,3]. В основном эти вопросы изучались в зубчатых передачах, как наиболее применимых в современном машиностроении. Однако, в последнее время, расширяется область применения передач с ПТК. Это связано с рядом достоинств, характерных этому виду передач
378

Современные техника и технологии 2007
зацеплением [4]: компактность конструкции; высокое передаточное отношение; малый момент инерции и высокий уровень динамичности; высокий крутящий момент, большие перегрузочные резервы; высокая продолжительность срока службы.
В Томском политехническом университете работы по изучению передач с ПТК ведутся с 70-х годов ХХ века. Недавно был разработан новый вид передачи с ПТК бессепараторного типа, точнее передачи со свободным или разгруженным сепаратором [5]. В данной передаче сепаратор служит только для удержания тел качения на определенном расстоянии друг от друга. Исключение сепаратора из силовой схемы, позволило повысить надежность передачи и снизить потери на трение в зацеплении. Данная передача имеет хорошие перспективы занять свое место на рынке. Однако, для успешного продвижения на рынок необходимо детальное изучение и исследование новой передачи, в том числе и вопросов трения. Для этого необходимо провести расчет трения в зацеплении и определить оптимальные параметры передачи.
Проанализируем имеющиеся методы определения трения для зубчатых передач. Способы расчета потерь на трения различны. Расчет передач на трение выполняют при оценке КПД передачи, при тепловой проверке механизма, при расчете на износ.
Рассмотрим тепловой расчет червячного редуктора, целью которого является проверка температуры масла в картере, которая не должна превышать допустимой. Температура масла при непрерывной работе без искусственного охлаждения определяется по известной формуле [6]:
tм = t + |
Fтр Vск |
|
K A |
||
|
(1)
где: Fmр – сила трения на быстроходном валу редуктора; Vск – скорость скольжения вала; К - коэффициент теплопередачи; А - площадь теплоотдающей поверхности корпуса редуктора; t - температура воздуха вне корпуса редуктора.
Из приведенной формулы видно, что снижение силы трения приводит к снижению температуры масла.
Таким образом, снижение силы трения в передачах является основной задачей при рассмотрении вопросов повышения надежности и КПД передач зацеплением и, как следствие, всего механизма в целом.
Как отмечалось ранее, наиболее изученными по вопросам, связанным с потерями на трение, являются зубчатые
передачи. Для них выработано множество рекомендаций и разработаны методы расчета.
Так, например, как отмечается в литературе [1], в зубчатом зацеплении потери на трение, для передач работающих без смазки, можно рассчитать по формулам молекулярно-механической теории трения. Кудрявцев В.Н. [2] предлагает рассчитать КПД зубчатой передачи с цилиндрическими зубчатыми колесами, учитывая только потери на трение в зацеплении, по формуле:
η ≈1 − 2,3 f ( Z11 ± Z12)
(2)
где: f – коэффициент трения в зацеплении; Z1, Z2 – числа зубьев шестерни и колеса соответственно. Формула (2) явно отражает зависимость КПД зубчатого зацепления от коэффициента трения.
В настоящее время методик определения потерь на трение в передаче с ПТК не существует. Мы предлагаем рассмотреть для передачи с ПТК бессепараторного типа три характерных области контакта (рис. 1).
I 1
II
2 3
III
Рис. 1. Области контакта 1 – профиль венца; 2 – тело качения; 3 –
профиль кулачка.
Как видно из рисунка, в области контакта I, тело качения находится в положении устойчивого равновесия и нагрузка на него не действует. Следовательно, потери на трение в этой области отсутствуют. И данную область можно исключить из рассмотрения.
Область III, как и область I, также является малонагруженной, поскольку тело качения выходит из рабочей зоны, передающей нагрузку. Соответственно, данная область также исключается из рассмотрения.
Наибольший интерес с точки зрения теории трения и износа представляет область II. Так как венец 1 (Рис. 1) в рассматриваемой передаче неподвижен, то в точке контакта венца1 и тела качения 2 наблюдается только сопротивление
379
XIII Международная научно-практическая конференция «СОВРЕМЕННЫЕ ТЕХНИКА И ТЕХНОЛОГИИ»
перекатыванию. Согласно [7] сила сопротивления перекатыванию в данной точке определится по формуле:
Fтр = μ |
N |
|
|
r |
(3) |
||
|
где: μ – коэффициент трения качения; N – сила нормального давления; r – радиус тела качения.
Для точки контакта профильного кулачка 3 и тела качения 2, помимо наличия трения качения, наблюдается трение скольжения [4], которое оказывает наибольшее влияние на потерю КПД передачи и приводит к нагреву. Однако исключать влияние трения качения не следует.
Как видно из рисунка, в области контакта II наблюдается изменение формы контакта: до точки перегиба профиля зуба и после. В связи с чем эту область, помимо сказанного выше, необходимо рассматривать как область сложного контакта, разделяя ее: 1) от впадины до точки перегиба – контакт тел с выпуклой и вогнутой поверхностями; 2) от точки перегиба до вершины зуба – контакт двух тел с выпуклыми поверхностями.
Помимо износа, связанного с трением скольжения и качения, существует абразивный износ. Абразивный износ, является самым опасным, так как в разы снижает срок службы изделия. Абразивный износ характерен для всех видов зацеплений, работающих под нагрузкой, т.к. поверхностные изменения, вызванные деформацией, приводят к появлению частиц износа. Таким образом, немаловажным оказывается расчет абразивного износа.
Для тяжелонагруженных зубчатых зацеплений, как отмечено в литературе [1], величину абразивного износа можно рассчитать статистическими методами. Особенность расчета зубчатых передач на износ заключается в том, что оценку износа можно свести к определению действия, производимого одной частицей, и суммированию этих независимых повреждений, что упрощает расчет. Передачи с ПТК также необходимо рассчитывать на абразивный износ, однако подобных методик расчета нет.
В качестве промежуточных тел качения целесообразно применять ролики [4]. Применение в качестве тел качения шариков рекомендуется только в кинематических или значительно недогруженных передачах, так как в ПТК, где в качестве тел качения применяются шарики температура на 40 – 50% выше. Это связано с увеличенной деформацией в зоне контакта и, как следствие, увеличением силы трения.
Таким образом, на основе сказанного выше, мы приходим к мнению, что передачи с ПТК являются перспективным видом передач, и способны потеснить, в силу своих техникоэкономических показателей, широко применяемые на данный момент виды передач.
Для снижения потерь на трение в передачах с ПКТ в качестве тел качения целесообразно применять ролики. Применение большего числа тел качения, как отмечено в работе [5], позволяет снизить потери на трение скольжения. С другой стороны при неизменных размерах передачи увеличение числа тел качения приведет к снижению их диаметра, а это в свою очередь, согласно формуле (3), приведет к увеличению потерь на трение качения. Для решения задачи определения оптимального соотношения между количеством и диаметром тел качения в передаче с ПТК и свободной обоймой необходимо проанализировать зацепление на основе теории трения, как это отмечалось выше, рассматривая сложный тип контакта поверхностей и на основании этого доработать конструкцию передач с ПТК. Другим путем снижения трения в зацеплении является применение антифрикционных покрытий или подбор смазочных материалов.
ЛИТЕРАТУРА:
1.Крагельский И.В., Добычин В.С., Комбалов В.С. Основы расчетов на трение и износ// М.: Машиностроение, 1977 – 526 с.
2.Кудрявцев В.Н. Планетарные передачи// М.: Машиностроение, 1966. – 307 с.
3.Журавлев Г.А. Условия трибосопряжения зубьев и пути совершенствования зубчатых зацеплений// Трение и износ. Минск. 1999. Т.20, N2. С. 175-
188.– Режим доступа: http://www.math.rsu.ru/niimpm/okp/public_rus.ht m
4.Панкратов Э.Н. Проектирование механических систем автоматизированных комплексов для механообрабатывающего производства// Издательство Томского университета, 1998 – 295 с.
5.Ефременков Е.А. Разработка методов и средств повышения эффективности передач с промежуточными телами качения// Томский политехнический университет, 2002 – 125 с.
6.Курсовое проектирование деталей машин: учебное пособие/ под ред. С. А. Чернавского. — М.: Машиностроение, 1979.
— 351 с.
7.Конвисаров Д.В. Трение и износ металлов// М.: Машгиз, 1947 – 184 с.
380

Современные техника и технологии 2007
ОПТИМИЗАЦИЯ РЕЖИМА ТЕХНИЧЕСКОГО ОБСЛУЖИВАНИЯ СТРОИТЕЛЬНЫХ И ДОРОЖНЫХ МАШИН
Чернухин Р.В.
Юргинский технологический институт Томского политехнического университета, г. Юрга, Кемеровская обл., ул. Заводская, 10
E-mail: rv_81@mail.ru
Актуальность |
|
решения |
проблемы |
|
|
|
|
|
|
|
|
||||
повышения |
|
надежности |
и |
прочности |
|
|
|
|
|
|
|
|
|||
строительной и дорожной техники вследствие |
|
|
|
|
|
|
|
|
|||||||
их комплексного |
характера |
неотрывно |
|
|
|
|
|
|
|
|
|||||
связана |
с |
|
современными |
методами |
|
|
|
|
|
|
|
|
|||
проектирования, |
|
технологического |
|
|
|
|
|
|
|
|
|||||
обеспечения, |
|
экономического |
и |
|
|
|
|
|
|
|
|
||||
организационного управления, планирования, |
|
|
|
|
|
|
|
|
|||||||
контроля и т.п. В настоящее время состояние |
|
|
|
|
|
|
|
|
|||||||
парка строительных и дорожных машин |
|
|
|
|
|
|
|
|
|||||||
находится далеко не в лучшем положении. |
|
|
|
|
|
|
|
|
|||||||
Практически отсутствует обновление техники, |
|
|
|
|
|
|
|
|
|||||||
так как нет средств на приобретение новых |
|
|
|
|
|
|
|
|
|||||||
единиц. Вследствие низкой фактической |
|
|
|
|
|
|
|
|
|||||||
надежности машин, в частности тракторов и |
|
|
|
|
|
|
|
|
|||||||
автогрейдеров и их элементов, уровень |
|
|
|
|
|
|
|
|
|||||||
отказов продолжает |
оставаться |
довольно |
|
Рис.1. Возрастная структура парка |
|
||||||||||
высоким. По этим причинам дорожно- |
|
|
|||||||||||||
строительные |
|
предприятия |
|
вынуждены |
|
дорожно-строительных предприятий г. |
|
||||||||
выполнять большие объемы работ по |
|
Юрга, Кемеровской обл. |
|
|
|||||||||||
техническому обслуживанию и ремонту. Рост |
|
Известны |
следующие |
|
стратегии |
||||||||||
потребности в запасных частях опережает |
|
|
|||||||||||||
рост парка дорожно-строительных машин. |
|
технического обслуживания, обеспечивающие |
|||||||||||||
Поскольку |
надежность и долговечность |
работоспособность |
машин: |
регламентная, |
|||||||||||
машин определяется не только качеством |
«по |
потребности», |
комбинированная, |
||||||||||||
проектирования и изготовления, но и |
планово-предупредительная. |
|
|
|
|||||||||||
режимом технического обслуживания, а также |
|
Применение |
регламентной |
стратегии |
|||||||||||
качеством |
их |
ремонта |
в |
процессе |
характеризуется проведением ТО или только |
||||||||||
эксплуатации, важной задачей является |
через определенные, твердо установленные |
||||||||||||||
установление |
|
рационального |
режима |
промежутки времени работы машины, или в |
|||||||||||
технического |
обслуживания |
и |
ремонта |
календарные сроки, независимо от времени |
|||||||||||
дорожно-строительных машин. |
|
|
работы (наработки) и фактического состояния |
||||||||||||
Опыт эксплуатации машин показывают, |
обслуживаемых машин. |
|
|
|
|
||||||||||
что система ТО машин нуждается в |
|
Стратегия «по потребности» применяется |
|||||||||||||
совершенствовании. |
Основными |
причинами |
для обслуживания машин по результатам |
||||||||||||
этого являются: |
|
|
|
|
|
диагностирования |
или |
при |
возникновении |
||||||
1) |
увеличение среднего возраста |
|
отказов. |
|
|
|
|
|
|
||||||
парка мобильных машин до 10…15 лет при |
|
|
Комбинированная |
стратегия |
допускает |
||||||||||
остаточной годности 30…40%; |
|
|
|
применение |
названных |
стратегий |
в |
||||||||
2) |
значительное снижение |
|
различных сочетаниях. |
|
|
|
|
||||||||
эксплуатационной надежности мобильных |
|
|
Стратегию планово-предупредительного |
||||||||||||
машин; |
|
|
|
|
|
|
|
обслуживания во многих случаях определяют |
|||||||
3) |
отсутствие у производителя |
|
как четкую и обеспечивающую наименьшие |
||||||||||||
техники материально-технологической базы |
|
затраты. Однако механизм реализации |
|||||||||||||
диагностирования, ТО и ремонта; |
|
|
данной стратегии по сути затратен. |
|
|
||||||||||
4) |
недопустимое снижение роли |
|
|
Следует учитывать, что планово- |
|||||||||||
инженерной службы по ТО и ремонту машин; |
|
предупредительная система ТО и ремонта в |
|||||||||||||
5) |
недостаточное использование |
|
своей основе содержит ряд допущений и |
||||||||||||
возможностей новых технологий, особенно |
|
построена |
на |
признании |
стабильной |
||||||||||
информационных. |
|
|
|
|
зависимости |
между наработкой |
машин |
и |
381
XIII Международная научно-практическая конференция «СОВРЕМЕННЫЕ ТЕХНИКА И ТЕХНОЛОГИИ»
потребностью |
и |
|
в |
периодическом |
минимальной. Такое значение и принято |
|||||||||||||||
обслуживании и ремонте. |
|
|
|
|
считать оптимально допустимым. |
|
|
|
||||||||||||
При выполнении планового обслуживания |
Необходимо |
выявить |
связь |
между |
||||||||||||||||
производится замена элементов, достигших |
надежностью элементов рабочих органов и их |
|||||||||||||||||||
своего предельного состояния. Кроме этого |
привода и потребительской стоимостью. Для |
|||||||||||||||||||
заменяют детали, вероятность отказа |
этого исследуется функция прогрессирующих |
|||||||||||||||||||
которых в период до следующего планового |
затрат на |
поддержание |
работоспособности |
|||||||||||||||||
ТО велика. |
|
|
|
|
|
|
|
элементов рабочих органов и их привода, с |
||||||||||||
Таким |
|
образом, |
выполняется |
помощью |
|
|
которой |
устанавливается |
||||||||||||
предупредительная |
замена, |
позволяющая |
зависимость |
потребительской |
стоимости |
их |
||||||||||||||
добиться |
некоторого |
уменьшения |
числа |
от изнашивания. На основе такого |
||||||||||||||||
отказов, однако, из-за недоиспользования |
сравнительного анализа можно экономически |
|||||||||||||||||||
ресурса деталей это влечет за собой |
обосновать наиболее эффективные варианты |
|||||||||||||||||||
увеличение расхода запасных частей. |
|
|
обслуживания и ремонта рабочих органов и |
|||||||||||||||||
Таким |
|
образом, |
|
эффективность |
их привода дорожно-строительных машин. |
|
||||||||||||||
ремонтно-эксплуатационных воздействий на |
Задача |
|
состоит |
|
в |
установлении |
||||||||||||||
узлы и агрегаты машин в значительной |
закономерности связей и соотношений между |
|||||||||||||||||||
степени зависят от научного обоснования |
вероятностными |
|
|
характеристиками |
||||||||||||||||
периодичности |
этих |
воздействий |
и |
надежности |
машин |
и |
их |
годностью |
||||||||||||
допустимых |
изменений |
технического |
(полезностью) |
или |
потребительской |
|||||||||||||||
состояния элементов машин. |
|
|
|
|
стоимостью. Для этого исследуется функция |
|||||||||||||||
Адекватным критерием |
оптимальности |
прогрессирующих |
затрат |
на |
поддержание |
|||||||||||||||
режима |
технического |
обслуживания |
и |
работоспособности машин или их частей в |
||||||||||||||||
ремонта элементов дорожно-строительных |
процессе старения, которая является |
|||||||||||||||||||
машин является технико-экономический |
наиболее |
приемлемым |
соизмерителем |
|||||||||||||||||
критерий, учитывающий надежность машин в |
годности физически разнородных элементов |
|||||||||||||||||||
процессе эксплуатации. |
|
|
|
|
|
машин и отражает величину затрат |
||||||||||||||
Основополагающее |
уравнение |
|
для |
общественного труда на их производство и |
||||||||||||||||
определения |
оптимальной |
величины |
эксплуатацию. Эта функция характеризует |
|||||||||||||||||
изменения параметра технического состояния |
качество |
|
|
машины |
|
количественными |
||||||||||||||
математически выражается как сумма двух |
методами, так как она показывает, насколько |
|||||||||||||||||||
составляющих: |
|
|
|
|
|
|
|
снизилась |
|
полезность |
(годность) |
или |
||||||||
F = E(Sg )+ C(Si )→ min , |
|
|
потребительская |
стоимость |
машины |
в |
||||||||||||||
|
|
результате того, что параметры технического |
||||||||||||||||||
|
|
|
|
|
|
|
|
|
состояния |
ее уже |
не |
равны |
исходным |
|||||||
где F – суммарная функция затрат, |
|
(паспортным) |
значениям |
и приближаются |
к |
|||||||||||||||
|
предельно допустимому уровню. |
|
|
|
||||||||||||||||
связанная с ремонтом и обслуживанием |
|
|
|
|
||||||||||||||||
|
Основой |
построения |
рациональной |
|||||||||||||||||
элемента; |
|
|
|
|
|
|
|
|
||||||||||||
|
|
|
|
|
|
|
|
системы |
|
технического |
обслуживания |
и |
||||||||
E(Sg) – функция затрат, зависящая от |
|
|
||||||||||||||||||
|
ремонта |
машин |
является обеспечение |
их |
||||||||||||||||
периодичности технического обслуживания; |
||||||||||||||||||||
соответствия |
функции |
прогрессирующих |
||||||||||||||||||
С(Si) – функция прогрессирующих затрат |
||||||||||||||||||||
затрат, |
|
характеризующей |
|
изменение |
||||||||||||||||
на поддержание работоспособности |
|
|
|
|
||||||||||||||||
|
|
потребительской |
стоимости |
машины |
||||||||||||||||
элемента. |
|
|
|
|
|
|
|
|
||||||||||||
|
|
|
|
|
|
|
|
вследствие износа ее элементов. На основе |
||||||||||||
|
|
|
|
|
|
|
|
|
||||||||||||
Первая |
составляющая |
|
E(Sg) |
такого |
сравнительного |
анализа |
можно |
|||||||||||||
|
экономически |
|
обосновать |
|
наиболее |
|||||||||||||||
определяется по экономическим признакам, а |
эффективные |
|
варианты |
|
ремонтно- |
|||||||||||||||
вторая |
С(Si) |
нуждается |
в |
|
особом |
обслуживающих |
воздействий |
на |
элементы |
|||||||||||
исследовании. |
|
|
|
|
|
|
|
машин. В условиях рыночных отношений |
||||||||||||
Слагаемые |
функции |
F |
оказывают |
|||||||||||||||||
потребителям для оценки годности и |
||||||||||||||||||||
противоположное влияние друг на друга. Чем |
приобретения машин необходимо знать, |
|||||||||||||||||||
больше |
вкладывается |
затрат |
|
на |
насколько та или иная машина или ее часть в |
|||||||||||||||
обслуживание и ремонт, тем меньше |
состоянии |
обеспечить |
работоспособность |
в |
||||||||||||||||
величина функции прогрессирующих затрат, |
течение определенного срока службы при |
|||||||||||||||||||
тем меньше доля внеплановых расходов, и |
условии, что свою технологическую задачу |
|||||||||||||||||||
напротив, |
|
если |
|
не |
то |
проводить |
она выполнит удовлетворительно. |
|
|
|
||||||||||
профилактические |
работы, |
влияние |
Функция прогрессирующих затрат C(Bt) на |
|||||||||||||||||
функции прогрессирующих затрат на общие |
||||||||||||||||||||
поддержание |
работоспособности |
машины |
||||||||||||||||||
затраты станет сразу же ощутимым. |
|
|
определяется как сумма двух составляющих |
|||||||||||||||||
В связи с вышеизложенным, можно найти |
такое значение, при котором функция F будет
382

Современные техника и технологии 2007
С(Вt ) = CNP (t) + СТМ (t),
где Bt – многомерный вектор технического состояния машины (узла) в момент времени t; СNP(t) – потери, связанные с уменьшением производительности машины в результате снижения тяговой силы
(мощности) и надежности;
CTM(t) – потери, связанные с перерасходом топливно-смазочных материалов в связи со снижением производительности машины.
ЛИТЕРАТУРА: |
|
|
1. Привалов |
П.В. |
Методология |
организации |
технического |
сервиса |
комплексов |
машин. |
– |
Новосибирский |
|
государственный |
аграрный |
университет, |
||
г.Новосибирск, 2001. – 236 с. |
|
|||
2. Привалов |
|
П.В. |
Организация |
технического сервиса машин в сельском хозяйстве и технологическое проектирование ремонтно-обслуживающих предприятий: учебное пособие для вузов. – Новосибирский государственный аграрный университет, г. Новосибирск, 2003 г. – 432 с.
ОПРЕДЕЛЕНИЕ ЭЛЕМЕНТОВ ТРАЕКТОРИИ ДВИЖЕНИЯ КАПЛИ
Шевчук М.В., Сапожков С.Б.
Юргинский технологический институт Томского политехнического университета, 652050, Кемеровская обл., г. Юрга, ул. Ленинградская, 26
E-mail: faeton44424mag@Rambler.ru
При сварке в СО2 из зоны дуги |
положение капли в конце 2, 3 и т.д. секунд, |
|||||
выбрасывается большое количество капель |
мы получим точки Б, В, и т.д. (рис. 1). |
|||||
жидкого металла различного размера. |
Сокращая |
последовательно |
|
промежутки |
||
Так как действие сил тяжести не зависит от |
времени, через которые мы определяли |
|||||
скорости полёта капли, понижение капли во |
положение капли, можно получить ряд очень |
|||||
время полета под линией выброса будет |
близко отстоящих друг от друга точек. |
|||||
совершаться по закону свободного падения |
Соединив эти точки кривой, мы получим |
|||||
тел, выпущенных под каким-то углом к |
графическое изображение траектории полёта |
|||||
горизонту и опишет кривую, показанную на |
капли без учёта силы сопротивления воздуха. |
|||||
рис.1 [1]. |
Математическим |
выражением закона |
||||
|
движения |
капли |
является |
уравнение |
||
|
траектории, которое отражает зависимость |
|||||
|
между координатами х и у в любой точке |
|||||
|
полёта капли. |
|
|
|
|
|
|
Выведем уравнение траектории капли, |
|||||
|
летящей под действием только одной силы |
|||||
|
тяжести. |
|
|
|
|
|
|
Допустим, |
что |
в |
безвоздушном |
||
|
пространстве капля вылетела из зоны дуги |
под углом выброса Θ0 с начальной скоростью равной V0 (рис. 2).
Рис. 1 – Понижение капли под линией выброса.
В конце первой секунды полёта под
действием силы тяжести капля будет не в точке "а'" или "а", а в точке А. Это
происходит в результате поступательного движения капли в первоначальном направлении и движения его под действием силы тяжести. Рассматривая аналогичное
383

XIII Международная научно-практическая конференция «СОВРЕМЕННЫЕ ТЕХНИКА И ТЕХНОЛОГИИ»
Рис. 2 – К выводу уравнения параболической траектории.
Вылетев из зоны дуги, капля опишет какую-то траекторию и упадёт в точке Д. Необходимо найти, на какой высоте над горизонтом летит капля на удалении X от точки вылета при данных значениях V0, Θ0. Для вывода уравнения поместим начало системы координат в точке вылета, как это показано на рис. 2. Из рисунка видно, что
Определим значения АВ и АС Значение АВ находится из треугольника ОАВ;
АС есть не что иное, как понижение капли под линией выброса за время его полёта до точки С. Понижение как путь, проходимый свободно падающим телом, определяется по формуле:
Время полёта капли до точки С находится следующим образом:
откуда
Из треугольника ОАВ видно, что
Таким образом:
Тогда:
Подставив найденные значения АВ и АС в выражение
получим уравнение траектории [1]:
(1)
где g – ускорение свободного падения; V0
– начальная скорость.
Вылетев из зоны дуги под действием газов, капля опишет траекторию, показанную на рис.3 [1].
Рис.3 – Элементы траектории:0 – точка вылета; S – вершина траектории; Н – высота траектории; С – точка падения; OS – восходящая ветвь траектории; SC – нисходящая ветвь траектории; Х – горизонтальная дальность; ӨС – угол падения; Y – угол возвышения; α – угол вылета; Ө0 – угол выброса
Все расчеты для вылета капель из зоны дуги ведутся по выведенному уравнению параболической траектории (1).
Полученное уравнение описывает траекторию капли, которая представляет параболу в безвоздушном пространстве под действием только одной силы тяжести.
Исходя из того, что траектория есть симметричная кривая и вершина её находится на половине полной горизонтальной дальности, можно написать для определения горизонтальной дальности
[1]:
|
|
|
|
|
(2) |
Преобразуем формулу (2) для начальной |
|||||
скорости и угла выброса [1]: |
|
||||
|
|
(3) |
|
|
. |
|
|
|
|
|
|
|
|
|
|
|
(4) |
Для |
определения |
|
времени |
полёта |
|
капли |
необходимо |
использовать уже |
|||
имеющуюся у нас при выводе уравнения |
|||||
траектории зависимость [1]: |
|
||||
|
|
|
. |
|
(5) |
Из этого выражения следует: |
|
||||
|
|
. |
|
|
(6) |
Высоту траектории |
|
можем Н определить |
|||
[2]: |
|
V 2 sin2 Θ |
|
|
|
|
Н = |
0 |
|
|
|
|
0 |
. |
(7) |
||
|
2g |
|
|||
|
|
|
|
|
Основной задачей, связанной с полетом капли, является решение вопроса о том, с
384

|
|
|
|
Современные техника и технологии 2007 |
какой начальной скоростью, под каким углом |
ЛИТЕРАТУРА: |
|||
вылета |
нужно |
выбросить |
каплю |
1.Наставление по стрелковому делу. |
определённой формы, чтобы она достигла |
Основы и правила стрельбы. – М.: |
|||
данной точки поверхности, а также время, за |
Воениздат., 1986. – 176с. |
|||
которое капля пролетает то или иное |
2.Огневая подготовка. Часть первая. |
|||
расстояние; общую дальность полёта капли и |
Основы и правила стрельбы. Управление |
|||
т.д. |
|
|
|
огнём. / Под общей редакцией к. в. н. доцента |
Проведенные расчеты, сделанные по |
Семёнова Ю.И. – М.: Воениздат., 1978. – |
|||
формулам параболической теории, позволят |
336с. |
|||
решить задачи по определению ее |
3.Шапиро Я.М. Внешняя баллистика. М., |
|||
элементов. |
|
|
|
1946. |
КРАСЧЕТУ УСИЛИЙ В ЗАЦЕПЛЕНИИ ПЕРЕДАЧ
СПТК И СВОБОДНОЙ ОБОЙМОЙ
Путятина Е.О., Шибинский К.Г., Ефременков Е. А. Томский политехнический университет, Россия, г. Томск, пр. Ленина, 30,
e-mail: shibinski@rambler.ru
Особенность силового расчета такого вида передач заключается в том, что при наличии N тел качения на угле зацепления профильное колесо представляет собой N – 1 раз статически неопределимую систему [1].
Определение усилий в зацеплении начнем со второго модуля передачи, изображенного на рис. 1:
Рис. 1. Второй модуль передачи. 1– кулачок; 2 – сепаратор; 3 – тело качения; 4 – профиль венца.
Рассмотрим зацепление тел качения и кулачка, для определения реакций, возникающих на телах качения, от действия кулачка.
Полагаем, что при неподвижных венце и телах качения к кулачку приложен некоторый момент Tвых, под действием которого за счет деформаций он (кулачок) повернется на некоторый угол β (рис.2).
Рис. 2. Деформационная схема зацепления тел качения и кулачка Пренебрегая деформациями тел качения, сепаратора, в котором находятся тела качения, опор кулачка, найдем, что деформация от смятия в контакте для
кулачка будет соответственно [1]:
δk4 = aК.4 β;,
δk5 = aК.5 β;
где δk4, |
δk5 |
– |
соответствующие |
деформации тел качения;
аК.4, аК.5 – соответствующие расстояния от центра вращения кулачка до
линий действия реакций.
Полагаем, что воспринимаемые телами качения нагрузки, равные усилиям PКi связаны линейной зависимостью соответственно с деформациями aК.4·β, aК.5·β.
Допущение это приемлемо, вследствие аналогичности положениям [1].
Максимальное усилие PКmax на кулачок возникает от тела качения с максимальным
385

XIII Международная научно-практическая конференция «СОВРЕМЕННЫЕ ТЕХНИКА И ТЕХНОЛОГИИ»
плечом аКmax, равным отрезку OP3 (рис.2).Усилие, передаваемое i-тым телом качения можно определить через пропорцию, которая после преобразований будет иметь вид:
P = P aКi ,
Кi К max r2 −e
Крутящий момент на выходном валу, жестко связанный с кулачком, можно определить по формуле:
n
Твых. =i =∑1PКi aКi ,
Преобразуя, получим:
PКmax =Tвыхn (r2 −e) .
∑ a2
i =1 Кi
Нагрузка на опоры выходного вала будет:
R |
= |
n |
R |
|
cosα )2 |
n |
R |
sinα )2 |
( ∑ |
|
+( ∑ |
||||||
вых |
i =1 |
|
Кi |
i |
i =1 Кi |
i |
||
|
|
|
.
Теперь перейдем к определению реакций тел качения на венец и сепаратор. При приложении крутящего момента к выходному валу он начнет поворачиваться, что приведет к появлению усилий от кулачка. Данные усилия действуют на тела качения, которые начинают обкатываться по профилю венца и поворачивают сепаратор. При описанных движениях от действия усилий возникают реакции (рис. 3):
Рис. 3. Схема зацепления тел качения, венца, сепаратора и кулачка.
Пользуясь принципом ДаламбераЛагранжа, построим треугольник сил, действующих на тело качения (рис. 4).
Зная направления всех реакций и величину усилия PКi , можно по теореме синусов определить значения реакций на венце RВ2i и сепараторе RС2i. Значения углов определяются из геометрических построений
и расчетов и здесь не приводятся. |
||||||
RВ2i |
= −PКi |
cos(γi |
−αi ) |
|||
cos(ψi |
+αi ) |
, |
||||
RС2i |
= −PКi |
|
sin(γi |
+ψi ) |
||
cos(ψi |
+αi ) |
. |
Зная реакции на сепараторе можно
определить момент на сепараторе:
n
ТС = r2 χ ∑ RC2i . i =1
Переходим к определению реакций и усилий в первом модуле передачи (рис. 5)
Рис. 5. Первый модуль передачи.
1 –генератор, 2 –тело качения, 3 –венец, 4 –сепаратор.
Момент на сепараторе будет действовать на тела качения, расположенные справа от линии центров, при вращении выходного звена (кулачка) против часовой стрелки. Под действием крутящего момента тела качения обкатываются по профилю венца и взаимодействуют с генератором. Под действием этих усилий, возникших от перемещений, генератор получит вращение.
Полагаем, что при неподвижных телах качения, венце и генераторе к сепаратору приложен некоторый момент TС, под действием которого за счет деформаций он (сепаратор) повернется на некоторый угол β
(рис. 6):
Рис. 4. Треугольник сил, действующих на тело качения.
386

Современные техника и технологии 2007
Рис. 6. Деформационная схема зацепления сепаратора и тел качения.
Аналогично расчету второй ступени передачи можно определить значения усилий от сепаратора.
Поскольку расстояние aс одинаковы, соответственно одинаковыми будут и реакции на тела качения. Реакции можно определить по следующей формуле:
RC1i = TnC ,
где Rc1i – реакция сепаратора на тело качения первого модуля;
n – число тел качения, находящихся в зацеплении первого модуля.
По аналогии с расчетом второго модуля, из треугольника сил (рис. 7), определим значения реакций на венце и генераторе.
Рис. 7. Треугольник сил, действующих на тело качения.
RГi = −RC1i |
cos(αi |
+ψi ) |
|
sin(αi |
+ψi ) |
. |
RВ1i = RГ2i + RC21i ,
Тогда крутящий момент на генераторе можно определить по формуле:
nr
Ткр.г. =i∑=1RГi Z22 sinαi .
Описанная методика расчета позволяет нам определить усилия в зацеплении передачи с промежуточными телами качения и свободной обоймой.
ЛИТЕРАТУРА:
1. В.Н. Кудрявцев. Планетарные передачи. 2-е изд., перераб. и доп. – М.: Машиностроение, 1966.
РАЗРАБОТКА ТЕХНОЛОГИИ ВОССТАНОВЛЕНИЯ И ИЗГОТОВЛЕНИЯ РАБОЧИХ ОРГАНОВ КОРМОДРОБИЛЬНЫХ МАШИН МОЛОТКОВОГО ТИПА
Ретюнский О.Ю., Юдина К.Н.
Юргинский технологический институт Томского политехнического университета г. Юрга, Кемеровская обл., ул. Ленинградская, 26
E-mail: retol@list.ru
Обеспечение продовольственной независимости и безопасности государства требует наличие высокоразвитого комплекса по переработке сельскохозяйственной продукции. К настоящему времени одним из сдерживающих факторов в решении проблемы является недостаточная эффективность машин комплекса по приготовлению комбинированных кормов.
В технологии приготовления кормов основными машинами являются измельчители, предназначенные для
дробления зерна, измельчения силосных культур и др.
Каждый тип измельчителей охватывает большую группу машин, отличающихся конструктивным исполнением и схемой организации рабочего процесса (например, дробилки – молотковые, щековые, конусные, дезинтеграторы и другие). Наиболее распространенными измельчителями являются молотковые дробилки ударного действия.
Дробилка состоит из корпуса с загрузочной горловиной, молоткового
387

|
XIII Международная научно-практическая конференция «СОВРЕМЕННЫЕ ТЕХНИКА И ТЕХНОЛОГИИ» |
|||||||||||||||||||
барабана |
|
с |
шарнирно-подвешенными |
износ |
|
рабочих |
|
органов |
|
(низкая |
||||||||||
молотками, решета и дек. |
|
|
|
|
износостойкость основных рабочих органов – |
|||||||||||||||
|
Рабочие |
органы |
дробилок |
– |
молотки |
молотков). К рабочим органам, изменяющим |
||||||||||||||
(рис.1) бывают двух видов: пластинчатые и |
качественное |
состояние |
|
перерабатываемого |
||||||||||||||||
объемные. |
|
|
|
|
|
|
|
материала, относят молотки, решета и деки; к |
||||||||||||
|
|
|
|
|
|
|
|
|
|
вспомогательным |
|
|
|
механизмам, |
||||||
|
|
|
|
|
|
|
|
|
|
обеспечивающим непрерывность протекания |
||||||||||
|
|
|
|
|
|
|
|
|
|
технологического процесса, - транспортеры- |
||||||||||
|
|
|
|
|
|
|
|
|
|
питатели, |
|
бункеры |
|
с |
дозаторами, |
|||||
|
|
|
|
|
|
|
|
|
|
вентиляторы, циклоны, фильтры, систему |
||||||||||
|
|
|
|
|
|
|
|
|
|
трубопроводов и выгрузные транспортеры. |
|
|||||||||
|
|
|
|
|
|
|
|
|
|
|
Предлагаемая |
разработка |
относится |
к |
||||||
|
|
|
|
|
|
|
|
|
|
сельскохозяйственному |
машиностроению, |
а |
||||||||
|
|
|
|
|
|
|
|
|
|
именно |
к |
конструктивным |
элементам |
|||||||
|
|
|
|
|
|
|
|
|
|
молотковых дробилок. В животноводстве для |
||||||||||
|
|
|
|
|
|
|
|
|
|
приготовления |
кормов |
из |
различных |
|||||||
|
|
|
|
|
|
|
|
|
|
зерновых культур (овес, пшеница и др.) |
||||||||||
|
|
Рис. 1 Конструкции молотков |
|
применяют |
молотковые |
|
дробилки |
(КДУ-2А |
||||||||||||
|
1 – ступенчатые нормальные; 2 – |
«Украинка» и т.п.), рабочим органом которых |
||||||||||||||||||
ступенчатые усиленные; 3 – прямоугольные; |
являются молотки, выполненные в виде |
|||||||||||||||||||
4 – фигурные типа фрезы; 5 – объемные АПК- |
пластины |
|
из |
дорогостоящих |
материалов |
|||||||||||||||
|
|
10; 6 – объемные ДДК; |
|
|
(сталей 65Г, 30ХГСА, ШХ15, 12X1ЗА и |
|||||||||||||||
|
|
|
|
|
|
|
|
|
|
другие). Тем не менее, они обладают низкой |
||||||||||
|
Пластинчатые |
|
молотки |
с |
|
двумя |
износостойкостью. При работе наблюдается |
|||||||||||||
отверстиями могут быть прямоугольными, со |
скругление лобовой грани молотков и вместо |
|||||||||||||||||||
ступенчатым концами и фигурными, а |
лобовых |
|
ударов |
дробимый |
|
материал |
||||||||||||||
объемные – сплошными и составными. В |
воспринимает удары с проскальзыванием, |
|||||||||||||||||||
кормодробилках |
|
|
отечественного |
что |
значительно |
ухудшает |
качество |
|||||||||||||
производства |
применяют |
пластинчатые |
дробления и взаимодействие кормосмеси с |
|||||||||||||||||
молотки |
|
(прямоугольные |
|
или |
со |
декой (решетом). Всё это сказывается |
на |
|||||||||||||
ступенчатыми концами). |
|
|
|
|
падении |
производительности дробилки |
на |
|||||||||||||
|
Для измельчения зерна и мягких |
30...45% и увеличении энергопотребления на |
||||||||||||||||||
продуктов |
используют тонкие |
молотки |
25...35%. |
|
|
|
|
|
|
|
|
|
||||||||
(толщиной 2-3 мм), а для стебельных кормов |
|
Перспективным |
решением |
задачи |
||||||||||||||||
– толщиной 6-8 мм и выше. При измельчении |
повышения |
ресурса |
молотков |
является |
||||||||||||||||
крупнокусковых |
материалов |
|
(початки, |
разработка |
|
и |
внедрение |
технологии |
||||||||||||
стержни |
початков, |
жмых) |
и |
|
сухой |
армирования |
рабочих |
|
углов |
|
твердыми |
|||||||||
листостебельной сечки (при производстве |
сплавами |
|
|
|
с |
|
применением |
|||||||||||||
травяной муки) применяют более толстые |
железоуглеродистых |
|
|
наплавочных |
||||||||||||||||
молотки (8-12 мм). |
|
|
|
|
|
|
материалов, позволяющих решать проблему |
|||||||||||||
|
Молотки изготовляют из марганцовистой |
прочности и твердости рабочих поверхностей. |
||||||||||||||||||
стали марки 65Г или из углеродистой стали с |
|
Известные |
молотки |
для |
молотковых |
|||||||||||||||
наплавкой рабочих кромок сормайтом. В |
дробилок, выполненные в виде пластины с |
|||||||||||||||||||
зависимости от материала и термообработки |
отверстиями для их шарнирной подвески, |
|||||||||||||||||||
молотки служат от 72 до 280 часов. |
|
|
обладают рядом недостатков: высокая |
|||||||||||||||||
|
Дробилки обладают рядом достоинств: |
скорость износа рабочей поверхности, |
||||||||||||||||||
простота устройства, высокая надежность в |
снижение производительности дробилки. |
|
||||||||||||||||||
работе, |
|
компактность |
|
установки, |
|
Взаимодействие молотка |
на |
высоких |
||||||||||||
динамичность рабочих режимов, высокие |
скоростях с дробимой средой приводит к |
|||||||||||||||||||
скорости |
|
рабочих |
органов |
и |
быстрому износу рабочей грани молотка (в |
|||||||||||||||
непосредственное соединение вала машины |
течение часа молоток воспринимает 10–50 |
|||||||||||||||||||
с |
электродвигателем |
|
обусловили |
млн. ударов с силой 10...20кг). Наибольший |
||||||||||||||||
возможность широкого применения их во всех |
износ наблюдается на вершине угла рабочей |
|||||||||||||||||||
отраслях хозяйства. |
|
|
|
|
|
|
части молотка. При этом молоток быстро |
|||||||||||||
|
Наряду с этим молотковые дробилки |
теряет первоначальную форму – образуется |
||||||||||||||||||
имеют |
ряд |
недостатков: |
|
высокая |
некоторая скругленная поверхность трения, |
|||||||||||||||
энергоемкость, |
|
неравномерность |
что приводит к падению производительности |
|||||||||||||||||
гранулометрического |
состава |
получаемого |
на 30-45% и увеличению потребляемой |
|||||||||||||||||
продукта |
с |
повышенным |
содержанием |
мощности на 25-30%. |
|
|
|
|
|
|||||||||||
переизмельченных |
|
частиц, |
|
интенсивный |
|
|
|
|
|
|
|
|
|
|
|
388

Современные техника и технологии 2007
Техническая задача – снижение скорости |
дробилки за счет снижения простоев |
||||||
износа рабочей поверхности молотка и |
связанных с заменой ее рабочих органов – |
||||||
увеличение производительности дробилки. |
молотков |
и |
снизить энергопотребление |
||||
Решение технической задачи достигается |
необходимое |
для производства единицы |
|||||
тем, что молоток дробилки (рис.2), |
продукции. |
|
|
|
|||
выполненный в виде пластины 1 по форме |
На рынке дробилки молоткового типа |
||||||
параллелограмма с отверстиями 2 для его |
занимают около 80% от всех применяемых |
||||||
крепления, |
дополнительно |
снабжен |
кормодробилок, кроме того, учитывая, что |
||||
твердосплавными |
вставками |
3, |
количество молотков, применяемых на |
||||
закрепленными |
в |
гранях |
рабочих |
дробилке колеблется от 90 до 1000 штук, то |
|||
поверхностей, причем вставки выполнены из |
предлагаемая |
технология |
упрочнения |
||||
твердых сплавов марки ВК (например, из ВК-6 |
твердым сплавом пластин молотков позволит |
||||||
или ВК-8), которые располагаются по углам |
получить |
значительный |
экономический |
||||
пластины, под острым углом α к рабочим |
эффект. |
|
|
|
|||
граням и закреплены в них посредством |
Кроме того, данный проект – молоток |
||||||
пайки на железоуглеродистом припое. |
дробилки относится к устройствам для |
||||||
|
|
|
|
измельчения материалов, а именно к |
|||
|
|
|
|
конструктивным элементам, и может быть |
|||
|
|
|
|
применен в строительной, горнорудной, |
|||
|
|
|
|
пищевой отраслях промышленности. |
|
|
|
|
|
|
ЛИТЕРАТУРА: |
|
|
|||
|
|
|
|
|
|
1. Балакир Э. и др. Повышение |
|||||
|
|
|
|
|
|
износостойкости молотков //Мукомольно- |
|||||
|
|
|
|
|
|
элеваторная |
|
и |
комбикормовая |
||
Рис. 2 Предлагаемая модель молотка |
промышленность. 1987, №2. |
|
|||||||||
2. Бойко А..М., Сизененко А.В. |
|||||||||||
|
|
|
|
|
|
||||||
Молоток дробилки работает следующим |
Повышение |
долговечности |
молотковых |
||||||||
рабочих |
органов |
кормодробилок |
|||||||||
образом: в процессе работы дробилки под |
//Исследование и конструирование машин и |
||||||||||
воздействием |
центробежной силы частицы |
оборудования для животноводства 1989, вып. |
|||||||||
измельчаемого продукта распределяются по |
14. |
|
|
|
|
||||||
периферии |
барабана, где попадают в зону |
3. Денисенко |
Н.И., |
Потомашев А.П. |
|||||||
действия молотка. При взаимодействии с |
|||||||||||
Повышение |
долговечности |
молотков |
|||||||||
рабочей |
|
поверхностью |
молотка |
||||||||
измельчаемый продукт оказывает на нее |
дробилок |
конструктивно-технологическими |
|||||||||
изнашивающее |
|
воздействие, |
которое |
методами //Исследование и конструирование |
|||||||
воспринимается |
жестко |
закрепленными в |
машин и оборудования для животноводства. |
||||||||
гранях твердосплавными вставками 3. |
Киев, 1988. |
|
|
|
|
||||||
Предлагаемая |
конструкция |
молотка |
4. Клименко Н.И., Тимановский А.В., |
||||||||
дробилки принципиально изменяет характер |
Журавель |
В.Ф. |
Сравнительная |
||||||||
износа |
и |
существенно |
повышает |
износостойкость |
дробильных |
молотков |
|||||
износостойкость и долговечность молотков за |
//Исследование и конструирование машин |
||||||||||
счет применения твердосплавных вставок в |
для животноводства и |
кормопроизводства |
|||||||||
рабочих гранях пластины в зоне ее |
ВНИИЖИВАШ. Киев, 1975, вып. №1. |
||||||||||
интенсивного износа. Данное решение |
|
|
|
|
|
||||||
позволяет |
повысить |
производительность |
|
|
|
|
|
389
XIII Международная научно-практическая конференция «СОВРЕМЕННЫЕ ТЕХНИКА И ТЕХНОЛОГИИ»
390

Секция 4
ЭЛЕКТРОМЕХАНИКА

XIII Международная научно-практическая конференция «СОВРЕМЕННЫЕ ТЕХНИКА И ТЕХНОЛОГИИ»
БЛОК ЧАСТОТНОГО РАЗГОНА ТРЕХФАЗНОГО АСИНХРОННОГО ДВИГАТЕЛЯ ТУРБОМОЛЕКУЛЯРНОГО НАСОСА
Асташкин С.С., Чернышева Т.А., Чернышев И.А.
Томский политехнический университет, Россия, г. Томск, пр. Ленина, 30
E-mail: chia_tomsk@rambler.ru
Турбомолекулярный насос предназначен для откачки неагрессивных газов и получения высокого вакуума в герметизированных объемах. В основе работы насоса лежит принцип перемещения молекул газа из откачиваемого объема лопатками ротора, вращающегося с высокой скоростью от электродвигателя, расположенного на одном валу с ротором.
Существует несколько различных вариантов построения турбомолекулярных насосов. Один из вариантов заключается в следующем. Насос состоит из серии вращающихся (ротор) и неподвижных (статор) пропеллеров. Пропеллеры ротора и статора чередуются и имеют противоположный наклон лопаток.
Работа насоса основана на передаче момента энергии от поверхности быстро вращающегося пропеллера к молекуле газа.
Скорость движения поверхности должна быть высокой для того, чтобы достичь оптимальной эффективности откачки (скорости откачки и отношения сжатия).
При столкновении молекулы газа с поверхностью пропеллера составляющая скорости движения молекулы, направленная вниз увеличивается, вследствие чего возрастает вероятность движения молекулы от области высокого вакуума к области низкого вакуума. Обычные турбомолекулярные насосы обеспечивают достаточно высокую скорость откачки, но имеют низкое отношение сжатия при давлении выше 10 мбар.
Насосы выполненные по системе «Drag» имеют низкую скорость откачки, но обеспечивают высокое отношение сжатия при давлении до 10 мбар.
Когда оба типа насосов объединены в один корпус, т.е. расположены на одной оси вращения, то насос может работать в широком диапазоне давлений.
Турбомолекулярные насосы нашли широкое применение в аналитических инструментах, масс-спектрометрах, анализаторах газа, в производстве полупроводников и других областях.
К основным характеристикам насосов относятся: производительность, скорость откачивания, отношение сжатия.
Функциональная схема блока разгона для трехфазного асинхронного двигателя турбомолекулярного насоса представлена на рис.1.
Принцип действия блока заключается в следующем. Напряжение величиной 50В поступает на силовой выпрямитель, который выполнен по мостовой схеме. Выпрямленное напряжение поступает на инвертор, а затем на двигатель. Сравнив существующие типы инверторов, и законы их управления, пришли к выводу, что для блока разгона требуется стабилизированный трехфазный инвертор напряжения на полевых транзисторах с ши- ротно-импульсной модуляцией сигнала. В этом случае будут соблюдены все требования к качеству выходного напряжения. С системы управления подается управляющий сигнал на драйвер, который формирует сигнал, необходимый для отпирания транзисторов.
Измерение напряжения осуществляется на делителе напряжения, величина с которого поступает в систему управления, для регулирования выходного напряжения.
В качестве датчика тока используется шунт, сигнал с которого так же поступает в систему управления, для регулирования выходного тока.
Детекция пересечения нуля используется для предварительного определения выходной частоты вращения двигателя.
Клавиатура используется для ввода номинальной частоты вращения двигателя, а так же для пуска и остановки двигателя.
На индикаторе отображается текущее значение частоты вращения двигателя, а перед пуском на нем отображается частота, которая вводится с клавиатуры.
Система управления выполняется на двух контроллерах AT90PWM3 и ATtiny2313 фирмы ATMEL.
AT90PWM3 служит для основного управления блоком. В данном контроллере есть встроенные специальные функции такие как: широтно-импульсный модулятор (ШИМ) для управления транзисторами; измерение тока; контроль перегрузки по току (с уставкой критической величины); измерение напряжения и половины напряжения; измерение частоты вращения двигателя с помощью датчиков Холла.
392

Современные техника и технологии 2007
Сигнал перегрузки по току формируется внешним компаратором. Пороговое напряжение компаратора можно регулировать с помощью внутреннего цифроаналогового преобразователя контроллера.
Контроллер ATtiny2313 служит для обработки сигналов, которые поступают на индикатор частоты, а также сигналов поступающих с клавиатуры.[1]
Эти два контроллера соединяются через специальный порт двухсторонней передачи данных.
Исследование динамических характеристик турбомолекулярного насоса можно проводить внеподвижной системе координат и во вращающейся системе координат.
Рис. 1. Функциональная схема блока разгона
Моделирование в неподвижной системе координат позволяет исследовать влияние на характер переходных процессов и динамическую механическую характеристику асинхронного двигателя таких характерных особенностей питающей сети, как:
•сдвиг по фазе питающих двигатель напряжений, отличающихся от стандартных значений;
•неравенство по амплитуде питающих двигатель напряжений.
Следует отметить, что при моделировании асинхронного двигателя в неподвижной системе координат на вход модели подаются
гармонические сигналы − 2 cos ф и
2 sin ф. При питании обмоток статора асинхронного двигателя от статических преобразователей частоты системы управления исследования выполняются во вращающейся системе координат. Используя вращающуюся систему координат для построения электроприводов с асинхронными двигателями, удается значительно упростить систему управления, перейдя от гармонических входных воздействий к аналоговым скалярным переменным.[2] Регулирование скорости осуществляется в соответствии с законом управления
U f 2 = const = k , который обычно использу-
ется в вентиляторах и насосах. Для рассматриваемой системы механические характеристики изображены на рис.2. Там же построена вентиляторная нагрузка в соответствии с выражением M c = k ω2 .
В программной среде Windora была составлена имитационная модель, на которой
проводилось исследование динамических характеристик. Исследования проводились без задатчика интенсивности, с задатчиком интенсивности, и с задатчиком интенсивности и вентиляторной нагрузкой.
Исследования показали, что при использовании задатчика интенсивности и моделировании вентиляторной нагрузки уменьшились частота и амплитуда момента (рис.3), а перерегулирование по скорости стало равно
0.
Рис.2. Механическая характеристика АД
Рис.3. Переходный процесс момента при
393

XIII Международная научно-практическая конференция «СОВРЕМЕННЫЕ ТЕХНИКА И ТЕХНОЛОГИИ»
U f 2 = const , при U зад =1о.е.
Экономический анализ разработанного блока разгона турбомолекулярного насоса показал, что стоимость данной системы гораздо ниже существующих аналогов.
ЛИТЕРАТУРА:
1.Евстифеев А.В. Микроконтроллеры
AVR семейств Tiny и Mega фирмы "ATMEL" / А. В. Евстифеев. - М. : Додэка-XXI, 2004. - 558
с. : ил.
2.Чернышев А.Ю., Чернышев И.А. Расчет характеристик электроприводов переменного тока: учебное пособие /; Томский политехнический университет. — Томск: Изд-во ТПУ, 2005.
ИССЛЕДОВАНИЕ КОММУТАЦИИ В КОЛЛЕКТОРНЫХ МАШИНАХ ПЕРЕМЕННОГО ТОКА
Ахмедзянов Г.Г.
Омский государственный университет путей сообщения, Россия, г. Омск, пр. Маркса, 35
E-mail: 1zzzz1@mail.ru
Коллекторные машины переменного тока, |
|
||||
благодаря своей простоте, надежности и вы- |
|
||||
соким массогабаритным показателям получи- |
|
||||
ли широкое применение в различных быто- |
|
||||
вых приборах, электрифицированном инст- |
|
||||
рументе и приводе автоматических устройств. |
|
||||
Надежность коллекторных машин пере- |
|
||||
менного тока в главной степени определяется |
|
||||
техническим |
состоянием |
коллекторно- |
|
||
щеточного узла. На его долю приходится в |
|
||||
среднем около 40% отказов, причем их боль- |
|
||||
шая часть является результатом износа ос- |
Рис.1 – Схема замещения |
||||
новных элементов скользящего контакта: |
коммутационного процесса |
||||
коллектора и щеток [1]. Этот износ является |
|
||||
следствием искрения под щеткой, возникаю- |
При составлении уравнения коммутации |
||||
щего в результате |
неудовлетворительной |
приняты следующие обозначения: |
|||
коммутации. |
|
|
|
Т – период коммутации (время короткого |
|
Исследование коммутации в коллектор- |
замыкания секции); |
||||
ных машинах переменного тока осложняется |
t0 – время, протекшее между ближайшим |
||||
наличием в коммутируемом контуре транс- |
нулевым значением тока в якоре и началом |
||||
форматорной |
и переменных |
составляющих |
коммутации (фаза коммутации); |
||
реактивной ЭДС [2]. Этим вопросом занима- |
RС – сопротивление коммутируемой сек- |
||||
лись многие ученные. Особо следует выде- |
ции; |
||||
лить работы Р. Рихтера, М. П. Костенко, К. И. |
Lс – индуктивность коммутируемой сек- |
||||
Шенфера, Ю. Е. Неболюбова. |
|
ции; |
|||
Для исследования искрения в этих маши- |
ϖк – число витков одной секции; |
||||
нах важно знать, как |
распределяется плот- |
ω=2πf – угловая скорость переменного то- |
|||
ность тока под поверхностью щетки. Для это- |
|||||
ка; |
|||||
го необходимо составить уравнение, описы- |
i – ток в короткозамкнутой секции; |
||||
вающее изменение тока в короткозамкнутой |
|||||
ia = I a sin ω(t +t0 ) – ток в секциях парал- |
|||||
секции в течении времени коммутации. Схема |
|||||
замещения короткозамкнутого |
контура для |
лельных ветвей; |
|||
случая, когда ширина щетки bщ равняется |
Ia – амплитудное значение тока в парал- |
||||
лельной ветви; |
|||||
коллекторному делению bк , представлена на |
|||||
рисунке 1. |
|
|
|
i2=i + ia – ток сбегающего края щетки; |
|
|
|
|
i1= ia – i – ток набегающего края щетки. |
||
|
|
|
|
394

Современные техника и технологии 2007
За время коммутации ток в короткозамк-
нутой секции |
изменяет свое |
значение с |
−I a sin ω t0 на |
+Ia sinω(t0 +T ), |
в результате |
чего в секции возникает ЭДС самоиндукции: eL = −L ddit . Магнитный поток возбуждения Фв ,
изменяющийся по синусоидальному закону, вызывает в короткозамкнутой секции трансформаторную ЭДС, отстающую от Фв по фа-
зе на 90° [3]:
et |
=ω ϖk |
Фв |
sin ω(t +t0 )− |
π . |
|
|
|
|
|
|
|
|
|
2 |
При расчете примем допущение отсутствия емкости между соседними коллекторными пластинами и взаимной индуктивности секций. Для набегающей части щетки принята
характеристика r1 = rщ Tt , а для сбегающей –
r2 = rщ TT− t .
По второму закона Кирхгофа составим уравнение для короткозамкнутой секции:
RСi + r2i2 −r1i1 = eL +et .
После подстановки и упрощения, уравнение принимает вид:
|
(T − 2t) Ia sinω(t0 +t) |
|
|
|
|
|
L |
di |
|
|
||||||||||||||
i = |
− |
|
|
|
dt |
|
|
+ |
||||||||||||||||
|
RС |
|
t |
(T −t)+T |
|
|
RС |
+ |
rT |
+ |
rT |
|||||||||||||
|
|
r |
|
|
|
t |
T −t |
|||||||||||||||||
|
|
T |
|
|
|
|
|
|
|
|
|
|
|
|
|
|
||||||||
|
|
ω ϖ |
k |
Ф |
sin |
ω(t |
0 |
+t)− π |
|
|
||||||||||||||
|
|
|
|
|
|
|
в |
|
|
|
|
|
2 |
|
|
|
||||||||
|
+ |
|
|
|
|
|
|
|
|
|
|
|
|
|
|
. |
|
|
||||||
|
|
|
|
|
|
R |
+ |
rT |
+ |
rT |
|
|
|
|
|
|
||||||||
|
|
|
|
|
|
|
|
|
|
|
|
|
|
|
|
|||||||||
|
|
|
|
|
|
|
|
|
|
|
|
|
|
|
|
|
|
|
|
|
||||
|
|
|
|
|
|
|
|
С |
|
t |
|
|
T −t |
|
|
|
|
|
|
|
|
|||
|
|
|
|
|
|
|
|
|
|
|
|
|
|
|
|
|
|
|
|
Для решения дифференциального уравнения используем функцию rkfixed программы Mathcad 2001i. Расчет проведен для сле-
дующих параметров |
машины: |
|
Ia = 23 А; |
|||
ω = 2π 50 = 314 |
с−1 ; T =10−3 |
|
с; R |
С |
=0,0045 О |
|
м, |
|
|
|
|
|
|
L =10-5 |
|
|
|
Ф = 800 103 |
||
r =0,024 Ом; |
Гн; ϖ |
k |
=2; |
|||
щ |
|
|
|
|
в |
Вб.
На рисунке 2 представлены два характерных графика изменения тока в короткозамк-
нутой секции для фаз коммутации π4 и 34π
(пунктиром показан график изменения тока, при условии, что в короткозамкнутом контуре отсутствуют ЭДС, т.е. происходит «коммутация сопротивлением»).
Рис. 2 – Кривые тока в короткозамкнутой секции
а) t 0 = T8 , б) t0 = 68T
Анализ полученных результатов показал, что в зависимости от фазы коммутации, в различных секциях якорной обмотки может осуществляться как замедленная, так и ускоренная коммутация. Для раздельной оценки интенсивности искрения секций коллекторной машины переменного тока с замедленной или ускоренной коммутацией, нужно учитывать не только полярность импульсов искрения, но и полярность напряжения якоря.
На основании проведенных теоретических и экспериментальных исследований, разработан прибор контроля коммутации коллекторных машин переменного тока по сигналу с разнополярных щеток ПКК-6УМ. Структурная схема прибора показана на рисунке 3.
Рис. 3 – Структурная схема прибора ПКК-6УМ
Сигнал с разнополярных щеток испытуемой машины ИМ содержит постоянную или переменную составляющую (в зависимости от способа питания) и высокочастотные импульсы, связанные с процессом коммутации. Масштабирующий усилитель МУ обеспечивает необходимый уровень входного сигнала. Усиленный сигнал поступает на вход фильтра высоких частот ФВЧ и управляющий вход
395