
- •к.т.н., начальник отдела ОНИР СиМУ ЭЛТИ, сопредседатель секции №1
- •д.т.н., профессор, зав. каф. фмпк эфф, председатель секции № 9
- •СЕКЦИЯ 1. ЭЛЕКТРОЭНЕРГЕТИКА
- •АВТОМАТИЗАЦИЯ РАСЧЕТА СТРУКТУРНОЙ НАДЕЖНОСТИ ЭЛЕКТРИЧЕСКИХ СХЕМ
- •ОСОБЕННОСТИ МОДЕЛИРОВАНИЯ ЭЛЕКТРИЧЕСКОГОПОЛЯ В МОРСКОЙ ВОДЕ
- •КАБЕЛЬ ДЛЯ ЭЛЕКТРОПИТАНИЯ ГЕНЕРАТОРОВ НИЗКОТЕМПЕРАТУРНОЙ ПЛАЗМЫ
- •Колпаков В.А., Паранин В.Д., Мокеев Д.А………………...86
- •СПОСОБЫ СЕЛЕКЦИИ КОРОТКИХ ЗАМЫКАНИЙ НА ЛИНИЯХ ЭЛЕКТРОПЕРЕДАЧИ
- •СЕКЦИЯ 2. ПРИБОРОСТРОЕНИЕ
- •ИСПОЛЬЗОВАНИЕ КОМПЬЮТЕРНОГО МОДЕЛИРОВАНИЯ ПРИ ИССЛЕДОВАНИИ СПОСОБА КОМПЕНСАЦИИ ДЕЙСТВИЯ ВИБРАЦИИ НА ГИРОМАЯТНИК
- •РАЗРАБОТКА И ИССЛЕДОВАНИЕ МИКРОМЕХАНИЧЕСКОГО ГИРОСКОПА
- •НОРМИРОВАНИЕ ШИХТОВЫХ МАТЕРИАЛОВ ДЛЯ ПРОИЗВОДСТВА ОТЛИВОК ИЗ АЛЮМИНИЕВЫХ СПЛАВОВ
- •ИНВЕРТОРНЫЙ ИСТОЧНИК ПИТАНИЯ ДЛЯ СВАРКИ МОДУЛИРОВАННЫМ ТОКОМ
- •ИССЛЕДОВАНИЕ ВЛИЯНИЯ ОТКЛОНЕНИЯ КОРПУСА НА ЦИКЛ РАБОТЫ ПНЕВМОГИДРАВЛИЧЕСКОГО УДАРНОГО МЕХАНИЗМА
- •ДИНАМИЧЕСКИЕ ПРОЦЕССЫ В БУРОВОЙ КОЛОННЕ ПРИ ВРАЩАТЕЛЬНО-УДАРНОМ БУРЕНИИ СКВАЖИН МАЛЫХ ДИАМЕТРОВ
- •СЕКЦИЯ 4. ЭЛЕКТРОМЕХАНИКА
- •ВЛИЯНИЕ ДЛИНЫ АСИНХРОННОГО ДВИГАТЕЛЯ НА ЭФФЕКТИВНОСТЬ КРЕПЛЕНИЯ
- •РЕЗУЛЬТАТЫ ЭКСПЕРИМЕНТАЛЬНЫХ ИССЛЕДОВАНИЙ ХАРАКТЕРИСТИК СИНХРОННОГО ГИБРИДНОГО ДВИГАТЕЛЯ
- •РАЗРАБОТКА ЭЛЕКТРОМЕХАНИЧЕСКОГО ПРЕОБРАЗОВАТЕЛЯ С АКТИВНЫМ И РЕАКТИВНЫМ ДИСКАМИ В МАГНИТНОЙ СИСТЕМЕ
- •ПРОГРАММА ВЫЯВЛЕНИЯ ФАКТОРОВ РИСКА РАКА МОЛОЧНОЙ ЖЕЛЕЗЫ С ИСПОЛЬЗОВАНИЕМ МЕТОДА МЕТА-АНАЛИЗА
- •ИССЛЕДОВАНИЕ ВОЗМОЖНОСТИ ИСПОЛЬЗОВАНИЯ МЕТОДА ФОТОМЕТРИРОВАНИЯ КАПЕЛЬНЫХ ПРОБ ДЛЯ ОЦЕНКИ АГРЕГАЦИОННЫХ СВОЙСТВ КЛЕТОК КРОВИ
- •ИСПОЛЬЗОВАНИЕ МИКРОВОЛНОВОЙ РАДИОТЕРМОМЕТРИИ В ДИАГНОСТИКЕ РАКА МОЛОЧНОЙ ЖЕЛЕЗЫ
- •УСТАНОВКА ДЛЯ ОПРЕДЕЛЕНИЯ ГИДРОДИНАМИЧЕСКИХ ХАРАКТЕРИСТИК КЛАПАННЫХ ЗАМЕНИТЕЛЕЙ, КАК ПОКАЗАТЕЛЕЙ КАЧЕСТВА И ПРИГОДНОСТИ ДЛЯ КАРДИОХИРУРГИИ
- •Введение
- •ЭКОНОМИЧНЫЙ И ЭКОНОМНЫЙ УМЗЧ 2×200Вт С БЛОКОМ ПИТАНИЯ
- •Мариненко А.В.
- •Благодарности
- •Компонента
- •МЕТОДИКА ОБРАБОТКИ КАРТИН ИНТЕРФЕРЕНЦИОННЫХ ПОЛОС
- •ЛИТЕРАТУРА:
- •Описание процесса моделирования
- •Вывод
- •Благодарности
- •ИСПОЛЬЗОВАНИЕ КОМПЬЮТЕРНОГО МОДЕЛИРОВАНИЯ ПРИ ИССЛЕДОВАНИИ СПОСОБА КОМПЕНСАЦИИ ДЕЙСТВИЯ ВИБРАЦИИ
- •НА ГИРОМАЯТНИК
- •Перспективы
- •Экспериментальная часть
- •Заключение
- •Рисунок 3. Результаты моделирования работы системы
- •ЛИТЕРАТУРА:
- •СКОРОСТНОЙ ЭФФЕКТ В ВИХРЕТОКОВОМ КОНТРОЛЕ
- •Введение
- •Благодарности
- •ЛИТЕРАТУРА:
- •E-mail: yuyug@npi.tpu.ru
- •Наименование параметра
- •Полоса
- •частот, Гц
- •Результаты и обсуждение
- •ЛИТЕРАТУРА:
- •ЛИТЕРАТУРА:
- •Тогда энергия, переданная упругому элементу, согласно (2) будет равна:
- •ПРОБЛЕМА ИССЛЕДОВАНИЯ ТРЕХЗВЕННЫХ МЕХАНИЗМОВ
- •ЛИТЕРАТУРА:
- •420066, г. Казань, Красносельская ул., 51
- •E-mail: BakirovAR@rambler.ru
- •420066, г. Казань, Красносельская ул., 51
- •E-mail: BakirovAR@rambler.ru
- •Введение
- •Выводы
- •Выводы
- •ОПТИМИЗАЦИЯ РЕЖИМОВ ЭКСПЛУАТАЦИИ УСТАНОВОК ТИПА УЭЦН С ПЧ
- •ЦИФРОВАЯ ЛАБОРАТОРИЯ ЭЛЕКТРОМЕХАНИКА
- •ЭЛЕКТРОМАГНИТНЫЙ МОМЕНТ В ИНДУКЦИОННЫХ ДВИГАТЕЛЯХ
- •Материал и методы исследования
- •Заключение и некоторые перспективы
- •ЛИТЕРАТУРА:

XIII Международная научно-практическая конференция «СОВРЕМЕННЫЕ ТЕХНИКА И ТЕХНОЛОГИИ»
ВНЕДРЕНИЕ МЕРОПРИЯТИЙ ПО СНИЖЕНИЮ ВИБРАЦИИ ШАРИКОПОДШИПНИКОВ НА ТЗПП
Юрченко О.А., Гормаков А.Н., Шепета Ю.А. Томский политехнический университет, Россия, г. Томск, пр. Ленина, 30
Томский завод приборных подшипников, Россия, г. Томск, ул. Ивановского, д.4 E-mail:dtps@lcg.tpu.ru
Одной из наиболее важных проблем на сегодняшний день является повышение качества и надежности механизмов, машин и оборудования в любой отрасли промышленности. На первый план выходят такие показатели качества как уровень вибрации и шума. Одним из основных источников вибрации и шума электрических машин является «неидеальность» подшипников качения, обусловленная погрешностями изготовления. Поэтому всё более актуальными становятся разработка и внедрение мероприятий по совершенствованию технологических процессов изготовления шарикоподшипников.
Томский завод приборных подшипников (ТЗПП) изготавливает шарикоподшипники малошумного исполнения 25-80018С2Ш3. Эти подшипники, в частности, используются в электродвигателях вентилятора отопителя автомобиля «Шевроле–Нива» [1]. Для контроля параметров вибрации используется прибор ИВП-3М, позволяющий производить измерения на стадии выходного контроля в 3- х полосах частот, нормы допустимого уровня вибрации для которых определены в соответствии с действующими российскими и международными стандартами.
Результаты теоретических и экспериментальных исследований по влиянию технологических погрешностей элементов подшипников, частоты вращения, влажности и объема смазки, некоторых конструктивных параметров и нагрузки на виброакустические характеристики приборных шарикоподшипников приведены в книге [2].
На ТЗПП в начале 2006 году контрольнометрологическим отделом, по результатам анализа факторов влияющих на вибрацию шарикоподшипников, была разработана и внедрена программа мероприятий по снижению вибрации. Эта программа включала в себя: ужесточение требований к промывке перед закладкой смазки (к основной промывке была добавлена промывка ультразвуком) и размагничиванию деталей шарикоподшипников перед сборкой (было увеличено число проходов); ужесточение норм значений круглости и волнистости дорожек качения наружных и внутренних колец (в результате введе-
ния суперфиниша дорожек качения). Нормы отклонения от круглости и волнистости дорожек качения колец шарикоподшипников представлены в таблице 1. Измерения геометрии колец подшипников на ТЗПП осуществляется на приборе «Талиронд» (Англия).
По истечении 7 месяцев после внедрения мероприятий по снижению вибрации шарикоподшипников были произведены измерения уровня вибрации. Для измерений была взята партия в 230 штук шарикоподшипников малошумного исполнения 25-80018С2Ш3 (такая же, как и при измерениях в предыдущем году). Измерения проводились в 3-х полосах частот:
•низкой – 50…300 Гц (норма уровня вибрации для 25-80018С2Ш3 на данной полосе частот составляет L=73 дБ).
•средней – 300…1800 Гц (норма уровня вибрации для 25–0018С2Ш3 на данной полосе частот составляет M=69 дБ).
•высокой – 1800…10000 Гц (норма уровня вибрации для 25-80018С2Ш3 на данной полосе частот составляет H=69 дБ).
Таблица 1. Нормы отклонения геометрии колец подшипников
Наименование параметра |
2005 |
2006 |
|
|
год |
год |
|
Отклонение волнистости |
0,2 |
0,16 |
|
наружных колец (01), мкм |
|||
|
|
||
Отклонение волнистости |
0,2 |
0,12 |
|
внутренних колец (02), мкм |
|||
|
|
||
Отклонение круглости |
1,5 |
1,5 |
|
наружных колец (01), мкм |
|||
|
|
||
Отклонение круглости |
1,5 |
0,8 |
|
внутренних колец (02), мкм |
|||
|
|
На основе результатов измерений, произведенных в декабре 2005 года, и в августе 2006 года, построены графики распределения подшипников по уровню вибрации (рис. 1). Для этого в начале производились измерения для каждого подшипника, а затем подсчитывалось количество подшипников, соответствующих измеренным уровням вибрации.
266

|
|
|
Современные техника и технологии 2007 |
|
По графикам можно судить об улучшении |
2) показывает, что благодаря внедрению ком- |
|
вибрационных |
параметров, особенно на |
плекса технологических мероприятий, про- |
|
средней полосе частот (рис. 1.б). Также видно |
цент подшипников, удовлетворяющий нормам |
||
уменьшение количества подшипников, уро- |
уровня вибрации 25-80018С2Ш3, повысился |
||
вень вибрации которых выше допустимого. |
для низкой полосы частот примерно на 4%, а |
||
Сравнение результатов измерений (таблица |
для средней полосы частот – на 14%. |
Рис. 1. Графики распределения подшипников по уровням вибрации в трех полосах частот
Таблица 2. Результаты измерения вибрации
Полоса |
Процент подшипников, удов- |
|
частот, Гц |
летворяющих нормам уров- |
|
|
ня вибрации 25-80018С2Ш3 |
|
|
2005 год |
2006 год |
50–300 |
66,9 |
71 |
300–1800 |
79 |
92,6 |
1800–10000 |
100 |
100 |
|
|
|
Заключение
Мероприятия, направленные на снижение вибрации шарикоподшипников, дали положительный результат, и, следовательно, должны использоваться в дальнейшем при произ-
водстве шарикоподшипников данной серии на ТЗПП.
ЛИТЕРАТУРА:
1.Татарова О.И., Гормаков А.Н., Шепета Ю.А. Анализ влияния технологических факторов на шум шарикоподшипников с защитными шайбами // Современные техника и технологии: Труды XII международной научнопрактической конференции. студентов и молодых ученых. –Томск. – 2006. – Т.1.С.130– 132.
2.Приборные шариковые подшипники: Справочник/Л.К.Волков, Г.А. Веркович, В.А. Голубков и др./ Под. ред. К.Н. Явленского – М.: Машиностроение, 1981. – 351 с.
267
XIII Международная научно-практическая конференция «СОВРЕМЕННЫЕ ТЕХНИКА И ТЕХНОЛОГИИ»
268

Секция 3
ТЕХНОЛОГИЯ, ОБОРУДОВАНИЕ И АВТОМАТИЗАЦИЯ МАШИНОСТРОИТЕЛЬНЫХ ПРОИЗВОДСТВ

XIII Международная научно-практическая конференция «СОВРЕМЕННЫЕ ТЕХНИКА И ТЕХНОЛОГИИ»
НОРМИРОВАНИЕ ШИХТОВЫХ МАТЕРИАЛОВ ДЛЯ ПРОИЗВОДСТВА ОТЛИВОК ИЗ АЛЮМИНИЕВЫХ СПЛАВОВ
Ахмедшин И.Т.
Уфимский государственный авиационный технический университет,
г.Уфа, ул. Карла Маркса, 12 E-mail: Akhmedshin@mail.ru
Существующая |
система |
нормирования |
с литниково-питающей системой (угар, |
||||||||||||||||||||||||
шихтовых |
материалов |
на |
предприятиях |
остаток металла в плавильно-заливочном |
|||||||||||||||||||||||
литейного |
|
производства |
унаследовала |
оборудовании, сплески, при плавке и |
|||||||||||||||||||||||
методы, |
|
|
выработанные |
|
несколько |
разливке металла в формы, унос металла с |
|||||||||||||||||||||
десятилетий назад, и представляет собой |
литейным шлаком и фильтром и т.д.); |
|
|||||||||||||||||||||||||
применение методов плановой экономики к |
Пб – |
брак |
отливки, % в массе |
||||||||||||||||||||||||
нормированию шихтовых |
материалов |
для |
изготовленных отливок (величина процента |
||||||||||||||||||||||||
литейного производства. Такая методика |
брака устанавливается на предприятии); |
|
|||||||||||||||||||||||||
предполагает |
использование |
усреднённых |
|
1− |
Пб |
|
– выход годного, %. |
|
|||||||||||||||||||
норм |
|
расхода |
шихтовых |
|
материалов, |
|
|
|
|||||||||||||||||||
|
|
|
|
|
|||||||||||||||||||||||
используемых для изготовления отливок из |
|
100 |
|
|
|
|
|
|
|
|
|
|
|||||||||||||||
2) массы безвозвратных потерь и |
|||||||||||||||||||||||||||
алюминиевых сплавов. Расчёты весов |
|||||||||||||||||||||||||||
компонентов шихты осуществлялись на тонну |
неиспользуемых отходов, образующихся при |
||||||||||||||||||||||||||
годного литья по каждой марке сплава и виду |
изготовлении отливки по формуле |
|
|
||||||||||||||||||||||||
литья, без нормирования материалов на одну |
|
|
gоп |
= Gш Поп , кг, |
|
|
|||||||||||||||||||||
отливку. Очевидно, что такая система |
|
|
|
|
|
100 |
|
|
|
|
|
||||||||||||||||
нормирования |
в современных |
условиях |
не |
где Gш – масса шихты (металлозавалки), |
|||||||||||||||||||||||
отражает |
действительного |
расходования |
|||||||||||||||||||||||||
необходимой для изготовления отливки, кг; |
|
||||||||||||||||||||||||||
первичных материалов. |
|
|
|
|
|
Поп – |
безвозвратные |
потери |
и |
||||||||||||||||||
Предлагаемая методика нормирования и |
|||||||||||||||||||||||||||
учёта |
первичных материалов |
предполагает |
неиспользуемые отходы, образующиеся при |
||||||||||||||||||||||||
использование не усреднённых норм, |
изготовлении |
отливки, |
% |
|
|
в массе шихты |
|||||||||||||||||||||
рассчитанных на тонну годного литья, а норм, |
(металлозавалке). Суммарные значения |
||||||||||||||||||||||||||
рассчитанных на одну отливку. В основу |
безвозвратных |
потерь |
и |
неиспользуемых |
|||||||||||||||||||||||
методики |
ложится |
|
ОСТ |
|
1.42141-82 |
отходов приведены в таблице 1 ОСТ 1.42141- |
|||||||||||||||||||||
«Нормативы |
|
расхода |
сплавов |
при |
82. |
|
|
|
|
|
|
|
|
|
|
|
|
||||||||||
изготовлении |
|
фасонных |
отливок |
из |
3) нормы расхода свежего материала для |
||||||||||||||||||||||
алюминиевых и магниевых сплавов» [1]. |
производства |
|
|
отливки |
(без |
учета |
|||||||||||||||||||||
Данный стандарт предусматривает расчёт: |
использования стружки) по формуле |
|
|||||||||||||||||||||||||
1) массы шихты (металлозавалки), |
|
|
Н′р′о = Gо + gоп , кг, (1) |
|
|
||||||||||||||||||||||
необходимой |
|
для |
|
изготовления годной |
где |
|
Н′′ро – норма расхода металла, |
||||||||||||||||||||
отливки с литниково-питающей системой, по |
|
||||||||||||||||||||||||||
формуле |
|
|
(Gо′ + Gобр ) Kизб |
|
|
|
|
необходимого для изготовления отливки, кг; |
|
||||||||||||||||||
|
|
|
Gш |
= |
|
, кг, |
|
Gо – масса отливки, кг; |
|
|
|
||||||||||||||||
|
|
|
|
|
|
|
|
|
|
|
|
|
|
|
|
|
|
||||||||||
|
|
|
|
|
|
1 − |
Пб |
|
|
|
|
|
gоп – |
масса |
безвозвратных |
потерь |
и |
||||||||||
|
|
Gо′ – |
|
|
|
100 |
|
|
|
|
|
неиспользуемых |
|
|
отходов |
металла, |
|||||||||||
где |
|
масса |
отливки |
с |
литниково- |
образующихся при изготовлении отливки, кг. |
|
||||||||||||||||||||
питающей системой (определяется из |
В связи с тем, что соотношение свежего |
||||||||||||||||||||||||||
технологической карты или взвешиванием), |
металла |
и |
|
|
возврата |
собственного |
|||||||||||||||||||||
кг; |
|
|
|
|
|
|
|
|
|
|
|
|
|
производства в шихте для различных сплавов |
|||||||||||||
G |
|
– |
масса |
образцов |
с |
литниково- |
неодинаково, |
|
|
|
|
ОСТ |
1.42141-82 |
||||||||||||||
обр |
|
|
|
|
|
|
|
|
|
|
|
|
предусматривает проверочный расчет массы |
||||||||||||||
питающей системой (масса образцов с |
|||||||||||||||||||||||||||
свежего металла в шихте по формуле |
|
||||||||||||||||||||||||||
литниково-питающей системой определяется |
|
|
|
|
|
|
Gш Посв |
|
|
|
|
||||||||||||||||
из технологической карты или взвешиванием |
|
G |
= |
|
, кг, |
|
|
||||||||||||||||||||
|
|
|
|
||||||||||||||||||||||||
из расчета на одну отливку), кг; |
|
|
|
|
|
св.м |
100 |
|
|
|
|
|
|||||||||||||||
|
|
|
|
|
|
|
|
|
|
|
|
||||||||||||||||
Kизб – |
|
|
коэффициент |
|
избытка, |
где Gсв.м – масса свежего металла, кг; |
|
учитывающий количество металла, которое необходимо расплавить сверх массы отливки
270

Современные техника и технологии 2007
Посв – процент освежения в соответствии
с действующей в отрасли технологической документацией, % от массы шихты.
В том случае, когда масса свежего металла, используемого в шихте ( Gсв.м ),
больше нормы расхода металла, необходимого для изготовления отливки ( Н′р′о ), рассчитанной по формуле (1), норму
расхода ( Н′р′о ) следует принять равной
массе используемого свежего металла, а излишек возврата собственного производства сдавать.
Массу сдаваемого возврата определять по формуле
Gвозв = Gсв.м − Нро , кг,
где Gвозв – масса сдаваемого возврата
собственного производства, кг.
ОСТ 1.42141-82 не включает в описание методику расчёта процента освежения для приготовления рабочего сплава. Значение процента освежения устанавливается на предприятии технологической документацией.
Возможны случаи, когда процент освежения ( Посв ) не задан технологической
документацией или задан интервалом, что усложняет задачу нормирования шихтовых материалов, так как формально это порождает бесконечное множество вариантов получения рабочего сплава, а значит и вариантов норм на шихтовые материалы. Такая множественность неприемлема для задачи нормирования материалов. Решение данной проблемы лежит в сужении множества возможных вариантов освежения по экономическим и технологическим критериям и выборе наиболее приемлемого процента освежения.
ОСТ 1.42141-82 не рассматривает те случаи, когда для приготовления рабочего сплава в качестве свежего металла-основы используется несколько компонентов. Свежий металл, используемый при приготовлении рабочего сплава (напр., АК7ч, АК9ч и др.), может состоять не из одного, а из нескольких первичных компонентов (напр., для сплава АК7Ч – алюминий марок А5, А6, А7, А8, силумин чушковой АК12, а также легирующих компонентов). В связи с этим, возникает необходимость разбивки и пересчёта нормы расхода свежего металла для каждого из используемых компонентов.
Данный пересчёт нормы на каждый составляющий компонент осуществляется на основе химического состава сплава (процентного соотношения химических элементов в рабочем сплаве), заданного
ГОСТом на сплав. Поскольку ГОСТ на сплав задает содержание химических элементов в виде интервалов, то необходимо вести расчет на среднюю величину. При этом расчёт ведётся на содержание основных элементов без учёта примесей. В общем виде, разбивка нормы свежего металла будет выглядеть следующим образом
n
GСв.Мет(НР.О. )= ∑Gi , кг,
1
где G1, G2,…, Gn – массы компонентов, составляющих свежую часть при приготовлении рабочего сплава.
Каждый из сплавов-компонентов (покупных материалов) вносит в рабочий сплав определённое количество основных элементов рабочего сплава (напр., рабочий сплав АК7Ч содержит 7,25% кремния, которого в сплаве-компоненте АК12 (силумин) содержится 11,5%). Поэтому расчёт массы используемого сплава-компонента в массе свежего металла следует вести по формуле:
Gi = GСв.Мет K1 , кг, (2)
K2
где К1 – процентное содержание основного элемента в рабочем сплаве, заданное ГОСТ на сплав,
К2 – процентное содержание основного элемента в сплаве-компоненте (покупном сплаве).
Расчёт массы легирующих компонентов, входящих в свежую часть GСв.Мет рабочего
сплава, необходимо осуществлять перед расчётом массы «чистого» алюминия. Это связано с тем, что легирующие сплавыкомпоненты могут содержать в своём составе алюминий - основу рабочего сплава. В этом случае, по формуле (2) рассчитываются массы легирующих сплавов-компонентов, а затем, используя полученный результат, вычисляется масса алюминия, содержащегося в сплаве-компоненте по формуле:
GAl(Gi) j = G100i K3 , кг,
гдеGAl(Gi) j - масса алюминия в сплаве-
компоненте, используемом для освежения и содержащем алюминий,
К3 – процентное содержание алюминия в сплаве-компоненте, которое задаётся ГОСТ на сплав-компонент (напр., МЛ5).
После расчёта масс всех вводимых легирующих компонентов, содержащих основной элемент – алюминий, подсчитывается масса свежего чистого алюминия, используемого для приготовления рабочего сплава, по формуле:
271

XIII Международная научно-практическая конференция «СОВРЕМЕННЫЕ ТЕХНИКА И ТЕХНОЛОГИИ»
n−1 |
m |
m |
GAl = GСв.Мет. (НР.О. ) −∑Gi −∑GAl(Gi) j , кг, |
∑GAl(Gi) j - общая масса алюминия, |
|
1 |
1 |
1 |
гдеGAl |
– масса свежего чистого |
алюминия, используемого для приготовления рабочего сплава,
GСв.Мет. - масса свежего чистого металла, включающая все компоненты
n −1
∑Gi - масса компонентов,
1
составляющих свежий металл, без учёта массы свежего чистого алюминия,
n – число компонентов, составляющих свежий металл,
содержащегося в сплавах-компонентах, составляющих свежий металл
m – число сплавов-компонентов, содержащих в своём составе алюминий.
ЛИТЕРАТУРА:
1. ОСТ 1.2141-82 «Нормативы расхода сплавов при изготовлении фасонных отливок»
МОДЕЛИРОВАНИЕ ТЕПЛОВЫХ ПРОЦЕССОВ ПРИ РАЗЛИЧНЫХ СПОСОБАХ СВАРКИ
Беляев А.В., Маминов А.С., Галимов Э.Р.
Казанский государственный технический университет им. А.Н.Туполева, Россия, г. Казань, К.Маркса, 10
E-mail: aleksei_belyaev@rambler.ru
Теплота, переданная источниками энергии свариваемому телу, распространяется в нем, подчиняясь законам теплопроводности. В действительности изучение температурных процессов в металле шва и вблизи него необходимо, главным образом, по двум причинам: для количественного описания многочисленных реакций, которые идут между жидким металлом и шлаком или газом, а также для определения условий кристаллизации металла, различных структурных превращений и термодеформационных процессов в металлах.
Однако, формирование свойств сварного шва, а тем более сварного соединения в целом, определяется не только химическим составом металла. Характер кристаллизации шва во многом влияет на его свойства. Свойства околошовной зоны и в определенной мере металла шва существенно зависят от температурного и термомеханического циклов, которые сопровождают процесс сварки. Для многих легированных сталей и сплавов эта фаза формирования сварного соединения предопределяет их механические свойства. Процесс сварки может создавать в металле такие скорости нагрева и охлаждения металла вследствие передачи теплоты по механизму теплопроводности,
которые часто невозможно организовать при термической обработке путем поверхностной теплопередачи. Образование сварного соединения сопровождается пластическими деформациями металла и возникновением собственных напряжений, которые также влияют на свойства соединений.
При сварке плавлением различные зоны сварного соединения (сварной шов, линия сплавления, зона термического влияния, основной металл) нагреваются до высоких температур, которые оказывают существенное влияние на его структуру и свойства, с образованием следующих зон – основного металла, сварного шва и зоны термического влияния (ЗТВ).
В работе рассматриваются основные схемы нагреваемого тела (тела, пластины, стержни), теплофизические величины и понятия (температура, температурное поле, теплоемкость, теплосодержание), закон Фурье и дифференциальное уравнение теплопроводности, поверхностная теплоотдача и граничные условия (конвективный и лучистый теплообмен), классификация источников теплоты (мгновенные точечные, линейные, плоские, непрерывно действующие и быстродвижущиеся), нагрев тел вращения (цилиндр, сфера, конус), распределенные
272

Современные техника и технологии 2007
источники |
|
|
|
теплоты |
|
|
(мгновенный |
и |
получить численное и графическое решение |
||||||||||||||||||
движущийся нормально круговой источник) и |
приращений |
температур |
вокруг |
источника |
|||||||||||||||||||||||
приращение |
|
|
температур. |
|
В |
|
расчетах |
сварочного тепла. |
|
|
|
|
|||||||||||||||
тепловых процессов при сварке широко |
Знание |
температурных полей позволяет |
|||||||||||||||||||||||||
используют зависимости, полученные путем |
прогнозировать |
изменение |
структуры |
||||||||||||||||||||||||
схематизации |
и |
упрощения |
действительных |
металла сварного соединения, выбрать |
|||||||||||||||||||||||
процессов |
|
|
|
|
распространения |
|
теплоты |
оптимальные |
параметры |
сварки |
( U д , Iсв , |
||||||||||||||||
(бесконечные и полубесконечные тела, |
vсв , d эл и др.), виды и режимы термической |
||||||||||||||||||||||||||
пластины, стержни и др.). |
|
|
|
|
|
|
|
|
|||||||||||||||||||
Расчетные |
|
|
методы |
|
базируются |
на |
обработки |
|
для |
улучшения |
служебных |
||||||||||||||||
следующем уравнении теплопроводности для |
свойств, а также устранения дефектных |
||||||||||||||||||||||||||
случая трехмерного тела с окружающим |
структур |
|
перегрева |
и |
|
определить |
|||||||||||||||||||||
пространством: |
|
|
|
|
|
|
|
|
|
|
|
|
|
|
|
|
адекватность |
|
расчетных |
и |
|||||||
∂T |
|
|
л |
|
∂ |
2 |
T |
|
∂ |
2 |
T |
|
∂ |
2 |
|
|
2 |
|
, |
|
экспериментальных |
методов |
распределения |
||||
= |
|
|
|
+ |
|
+ |
|
T |
= a |
T |
|
температуры |
при |
сварке |
различными |
||||||||||||
|
|
|
|
∂x2 |
∂y2 |
|
|
|
|
|
|
||||||||||||||||
∂t cс |
|
|
|
|
|
|
|
|
|
методами, |
видами, способами, |
приемами |
|||||||||||||||
|
|
|
∂z2 |
|
|
|
|
|
где 2T – оператор Лапласа; a = л/cс– |
сварки и др. |
|
коэффициент температуропроводности.
Для аналитических расчетов полей температур могут быть использованы вычислительные машины. В простейшем случае ЭВМ (электронно-вычислительная машина) используют для расчетов полей температур. Весьма эффективно использование ЭВМ в задачах оптимизации параметров режима сварки по скорости охлаждения в заданном интервале температур. Особый случай расчета тепловых процессов – расчет с учетом зависимости теплофизических характеристик
металла λ, a , cс , б от температуры.
Составлена |
программа для |
|
расчета |
|
|
|
|
|||
температурных полей в численном и |
|
|
|
|
||||||
графическом |
виде после продолжительного |
|
|
|
|
|||||
действия |
источника |
теплоты, |
когда |
Рис.1. |
Приращение |
температур |
в |
|||
достигается |
так |
называемое предельное |
предельном |
состоянии |
при движении |
|||||
состояние |
и |
температура |
точек |
в |
точечного источника теплоты на поверхности |
|||||
неподвижной |
системе |
координат |
перестает |
полубесконечного тела [q = 4000 Вт, v = 0,1 |
||||||
изменяться |
во времени, которое также |
см/с, а = 0,1см2/c, λ = 0,4 Вт/(см . К)] |
|
|||||||
называется квазистационарным: |
|
|
|
|
|
|
|
Tпр = |
q |
|
− |
v |
|
(R +x) |
, |
|
2a |
|
|||||||
2πλR e |
|
|
|
|||||
|
|
|
|
|
|
|||
где ДT – приращение |
|
температуры |
в |
|||||
рассматриваемой |
точке; |
|
|
R = |
x2 + y2 + z2 |
– |
расстояние до рассматриваемой точки от начала координат, см; q – мощность
источника теплоты, Вт; v – скорость сварки,
см/с; л – теплопроводность, Вт/(см . К); x – координата, см; a – коэффициент температуропроводности, см2/с.
Приводятся теоретические основы, методика, программа и результаты расчета температурных полей на ЭВМ при ручной дуговой, газовой, электрошлаковой, электронно-лучевой, плазменной, лазерной и других способах сварки на материалах различной конфигурации, которые позволяют
Существует много методов экспериментального определения температур. В работе рассматриваются экспериментальные способы определения температурных полей, которые используются при сварке, пайке, резке металлов, в том числе с использованием лазерного луча и др.: метод термокрасок, термокарандашей, метод термопар (свойства основных, применяемых для изготовления термопар приведены в таблице); мультиметры со встроенным термоинтерфейсом, прецизионные цифровые термометры с термопарами различных типов и материалов (на примере ATT-2002); оптические пирометры (С-500 “Самоцвет”, C- 500.7 “Кристалл”) и тепловизоры, а также на базе АЦП. Ниже на рис. 2 приведена принципиальная схема устройства термопары. Внешний вид мультиметра DT-
273

XIII Международная научно-практическая конференция «СОВРЕМЕННЫЕ ТЕХНИКА И ТЕХНОЛОГИИ»
838, прецизионного термометра, оптического |
термических циклов сварки, скоростей |
||||||||||
пирометра приведены на рис. 3. |
|
охлаждения, размеров зон термического |
|||||||||
В технике существуют также многие |
влияния и т.д. при сварке служат уравнения и |
||||||||||
другие методы измерения температуры, |
формулы. |
Экспериментальное |
определение |
||||||||
например, |
электронно-оптические |
температур |
при |
сварке |
|
имеет |
свои |
||||
преобразователи. |
|
|
|
преимущества перед расчетными, хотя и |
|||||||
|
|
|
|
уступает ему в возможности получения и |
|||||||
|
|
|
|
анализа общих закономерностей. Правильным |
|||||||
|
|
|
|
следует считать подход, при котором оба |
|||||||
Рис. 3. Принципиальная схема устройства |
метода дополняют друг друга, а решение об |
||||||||||
использовании |
того |
или |
иного |
метода |
|||||||
|
термопары |
|
принимается с учетом конкретной обстановки и |
||||||||
Регистрация |
измеренных |
температур |
|||||||||
поставленных задач. |
|
|
|
|
|||||||
обычно выполняется путем преобразования |
Апробирован |
метод |
|
определения |
|||||||
измеренного сигнала в электрический с |
|
||||||||||
температурных полей при ручной дуговой |
|||||||||||
последующей подачей его на показывающие |
сварке с применением мультиметра и |
||||||||||
или записывающие устройства (термо – э.д.с. |
термопары, термощупа и пирометра. Данные, |
||||||||||
термопар могут |
быть |
непосредственно |
полученные |
в |
ходе |
|
эксперимента |
||||
поданы на такие приборы). |
|
|
сравниваются с расчетными данными. |
|
|||||||
|
|
|
|
|
|||||||
|
|
|
|
Результаты данной работы освоены, |
|||||||
|
|
|
|
внедрены и используются на практических |
|||||||
|
|
|
|
занятиях |
по |
теории |
сварочных процессов |
||||
|
|
|
|
(ТСП). |
|
|
|
|
|
|
|
|
|
|
|
ЛИТЕРАТУРА: |
|
|
|
|
|||
|
|
|
|
1. Петров Г.Л., Тумарев А.С. Теория |
|||||||
|
|
|
|
сварочных |
|
процессов |
(с |
основами |
|||
|
|
|
|
физической химии). Учебник для вузов. Изд. |
|||||||
|
|
|
|
2-е, перераб. М., “Высшая школа”, 1977. 392 |
|||||||
|
|
|
|
с. с ил. |
|
|
|
|
|
|
|
а |
б |
|
в |
2. Теория |
сварочных процессов: Учеб. |
||||||
|
|
|
|
для вузов по спец. “Оборуд. и технология |
|||||||
Рис. 2. Внешний вид приборов для |
сварочн. пр-ва”/В.Н. Волченко, В.М.Винокуров |
||||||||||
измерения температуры: а – мультиметр DT- |
и др.; Под ред. В.В. Фролова. – М.: Высш. шк., |
||||||||||
838, б – прецизионный термометр, в – |
1988. 559 с.: ил. |
|
|
|
|
||||||
|
пирометр |
|
|
3. Кошкарев Б.Т. Теория сварочных |
|||||||
|
|
|
|
процессов. ДГТУ, 2003 г. |
|
|
|
||||
В расчете температурных полей для |
4. Королев Н.В. Расчеты тепловых |
||||||||||
качественной оценки основой для расчетов |
процессов |
при сварке. УГТУ-УПИ, |
2002 г. |
||||||||
нагрева и плавления металла, а также для |
|
|
|
|
|
|
|
||||
количественных расчетов |
при |
определении |
|
|
|
|
|
|
|
ЭКСПЕРИМЕНТАЛЬНАЯ УСТАНОВКА ДЛЯ ПИТАНИЯ ДУГИ В ДИНАМИЧЕСКОМ РЕЖИМЕ
Князьков А.Ф., Бирюкова О.С., Устинов В.А.
Томский политехнический университет, Россия, г. Томск, пр. Ленина,30
При сварке корневых слоев неповоротных стыков трубопроводов различного назначения предъявляются повышенные требования, так как в процессе эксплуатации металл шва контактирует с транспортируемым продуктом, который нередко бывает активным. Основным возмущением в процессе формирования сварного шва является
постоянное изменение пространственного положения сварочной ванны: нижнее, вертикальное, потолочное вследствие чего форма (геометрия) корневого слоя отклоняется от заданной.
В настоящее время для сварки корневого слоя при больших объемах работы используется автоматическая сварка
274

Современные техника и технологии 2007
плавящимся и неплавящимся электродом в |
динамических |
всплесков |
объясняется |
||||||||||||||||
защитных газах, как в непрерывном, так и в |
несоответствием |
|
термической |
эмиссии |
|||||||||||||||
импульсно-дуговом варианте. |
|
|
|
|
дугового разряда текущему значению тока |
||||||||||||||
Сварка |
корневого |
слоя |
|
может |
вследствие тепловой инерции. Недостаток |
||||||||||||||
осуществляться следующими способами: |
термической эмиссии в данном случае |
||||||||||||||||||
плавящимся |
|
электродом с |
подачей |
восполняется автоэлектронной эмиссией, что |
|||||||||||||||
присадочной проволоки в зону сварки, с |
вызывает увеличение напряжения дуги. |
||||||||||||||||||
изменением угла наклона [1]; |
|
|
|
|
Длительность импульсов менее чем 450-500 |
||||||||||||||
плавящимся |
электродом |
изнутри |
трубы |
мкс позволяет перевести дугу в динамический |
|||||||||||||||
специализированной |
|
установкой, |
режим. |
|
|
|
|
|
|
|
|
||||||||
используются 6 автоматических головок и |
Из выше сказанного и анализа |
||||||||||||||||||
специальная разделка кромок [2]; |
|
|
|
неупомянутых работ можно сделать вывод, |
|||||||||||||||
плавящимся |
|
электродом |
|
|
двумя |
что дуга горящая в динамическом режиме |
|||||||||||||
автоматическими головками, установленными |
является перспективным объектом в плане |
||||||||||||||||||
на трубе [2]; |
|
|
|
|
|
|
|
исследования |
применительно |
к |
сварке |
||||||||
неплавящимся |
электродом |
с |
подачей |
корневого слоя. Но в настоящее время |
|||||||||||||||
присадочной проволоки в зону сварки с |
отсутствуют источники для питания дуги |
||||||||||||||||||
изменением угла наклона [1]; |
|
|
|
|
горящей в динамическом режиме. |
|
|
||||||||||||
расщепленным электродом [2]; |
|
|
На |
|
рисунке |
|
1 |
представлена |
|||||||||||
|
|
разработанная |
|
авторами |
|
схема |
|||||||||||||
неплавящимся |
электродом |
|
за |
один |
|
|
|||||||||||||
полный |
оборот |
сварочной |
головки |
вокруг |
экспериментальной |
|
установки |
для |
|||||||||||
трубы [1]. |
|
|
|
|
|
|
|
|
исследования. |
|
Питание |
|
установки |
||||||
|
|
|
|
|
|
|
|
осуществляется от трехфазного выпрямителя |
|||||||||||
Известны работы по сварке корневого |
|||||||||||||||||||
слоя |
со |
|
сквозным |
проплавлением |
В с жесткой внешней характеристикой со |
||||||||||||||
неплавящимся остро заточенным электродом |
ступенчато |
регулируемым |
напряжением |
||||||||||||||||
в аргоне [3]. В данном способе неплавящийся |
холостого хода (20…60 В). Для уменьшения |
||||||||||||||||||
электрод затачивают на 30° и применяют |
внутреннего |
сопротивления выпрямителя к |
|||||||||||||||||
его клеммам через блокирующий диод |
|||||||||||||||||||
большие токи. Использование данного |
подключена батарея конденсаторов большой |
||||||||||||||||||
способа дает неплохие результаты по |
емкости С. Это необходимо для развязки |
||||||||||||||||||
качеству |
шва |
в |
первоначальный |
период |
|||||||||||||||
работы (исключается такие дефекты как |
импульсной части установки от цепи |
||||||||||||||||||
питающей дежурную дугу. Импульсная часть |
|||||||||||||||||||
непровары). |
|
В |
процессе |
|
работы, |
установки выполнена в виде мостового |
|||||||||||||
применяемые большие токи неблагоприятно |
тиристорного преобразователя, в одну |
||||||||||||||||||
сказываются |
на |
вольфрамовом |
|
электроде |
диагональ |
которого |
включен |
формирующий |
|||||||||||
(происходит |
|
|
изменение |
|
рабочей |
элемент ФЭ с ненулевыми начальными |
|||||||||||||
поверхности), |
что |
приводит |
к |
нарушению |
|||||||||||||||
процесса формирования корневого слоя. |
условиями. |
Особенностью |
используемого |
||||||||||||||||
формирующего |
|
элемента |
|
является |
|||||||||||||||
Авторами [4] рассмотрен способ сварки, |
|
|
|||||||||||||||||
формирование импульсов по форме близких |
|||||||||||||||||||
основанный сжатие дуги за счет питания ее |
к прямоугольной при поочередной подаче на |
||||||||||||||||||
кратковременными |
мощными |
импульсами |
него |
напряжения |
противоположной |
||||||||||||||
тока. |
Кратковременность |
накладываемых |
полярности, |
что |
осуществляется |
при |
|||||||||||||
импульсов |
|
|
|
позволяет |
|
|
получать |
поочередном включении пар тиристоров VS4, |
|||||||||||
контрагированный |
(сжатый) |
столб |
дуги, |
VS7 и VS5, VS6. Другая диагональ мостового |
|||||||||||||||
вследствие не успевания перехода дуги к |
|||||||||||||||||||
преобразователя включена последовательно |
|||||||||||||||||||
статическому состоянию из-за мгновенного |
в сварочную |
цепь, |
что |
обеспечивает |
|||||||||||||||
изменения значения тока и напряжения. |
протекание |
униполярных импульсов |
через |
||||||||||||||||
Как показано в работах [4, 5] перевод |
|||||||||||||||||||
дуговой промежуток. Длительность импульсов |
|||||||||||||||||||
стационарной дуги в динамический режим |
устанавливается параметрически в пределах |
||||||||||||||||||
позволяет |
управлять размером |
анодного |
50…500 мкс. |
|
|
|
|
|
|
||||||||||
пятна, |
то |
есть |
процессом тепловложения в |
Выключение |
указанных |
выше |
пар |
||||||||||||
изделие. На основе проведенных авторами |
|||||||||||||||||||
тиристоров |
|
мостового |
тиристорного |
||||||||||||||||
исследований видно, что с увеличением |
преобразователя осуществляется |
обратным |
|||||||||||||||||
длительности |
|
|
импульсов |
|
происходит |
напряжением формирующего элемента ФЭ, |
|||||||||||||
увеличение размеров анодного пятна. |
т.к. его напряжение, вследствие резонансного |
||||||||||||||||||
Быстрое переключение тока [5] приводит к |
перезаряда |
будет |
|
больше |
напряжения |
||||||||||||||
возникновению |
динамических |
всплесков, |
питающего выпрямителя. |
|
|
|
|||||||||||||
которые |
|
обуславливаются |
|
тепловой |
|
|
|
|
|
|
|
|
|
||||||
инерционностью. |
|
Существование |
|
|
|
|
|
|
|
|
|
275

XIII Международная научно-практическая конференция «СОВРЕМЕННЫЕ ТЕХНИКА И ТЕХНОЛОГИИ»
Рисунок 1. – Схема экспериментальной установки. |
|
|
|||
Для обеспечения непрерывности горения |
характеристика и |
регулируется величина |
|||
дуги при малой частоте следования |
дежурного тока в пределах 5…60 А. |
||||
импульсов |
мостовой |
преобразователь |
Управление мостовым преобразователем |
||
зашунтирован цепью питания дежурной дуги |
осуществляется |
схемой |
управления, |
||
состоящей из блокирующего диода VD1, |
функциональная схема которой представлена |
||||
дросселя L и балластного реостата Rб, за |
на рисунке 2. |
|
|
||
счет которого |
формируется крутопадающая |
|
|
|
Рисунок 2. – Функциональная схема управления. БП – блок питания; ЗУГ – задающий управляющий генератор; ТТ – тиристорный триггер; ИУ1, ИУ2 – импульсные усилители.
Питание |
схемы |
|
управления |
импульсов генератора поступают на пары |
||||||
осуществляется от блока питания БП. |
тиристоров VS4, VS7 и VS5,VS6. |
|||||||||
Частота |
работы |
установки |
|
задается |
Форма импульсов тока при нагружении на |
|||||
задающим |
|
управляющим |
|
генератором |
согласованное |
активное |
сопротивление |
|||
частоты - ЗУГ, частоту которого можно |
равное |
волновому |
сопротивлению |
|||||||
изменять от нескольких герц до десятков |
формирующего |
элемента |
ФЭ представлена |
|||||||
килогерц |
при |
соответствующем |
снижении |
на рисунке 3. |
|
|
|
|||
длительности |
|
|
|
импульсов. |
Разработанная установка позволяет |
|||||
Последовательность импульсов с генератора |
производить исследования динамики дуги и |
|||||||||
поступает на вход тиристорного Т – триггера |
анодного пятна на изделии в широком |
|||||||||
ТТ, который осуществляет деление частоты |
диапазоне параметров. |
|
||||||||
на два. С двух выходов Т – триггера |
|
|
|
|
||||||
последовательности |
импульсов |
с |
частотой |
|
|
|
|
|||
меньшей в 2 раза по отношению частоты |
|
|
|
|
||||||
задающего |
генератора |
и |
|
сдвинуты |
|
|
|
|
||
относительно друг друга, на период частоты |
|
|
|
|
276

Современные техника и технологии 2007
проникающей дугой острозаточенным вольфрамовым электродом в полевых условиях//Сварочное производство. – 1985.-
№6.-С.2-4.
Славин Г.А., Столпнер Е.А. Некоторые особенности дуги питаемой кратковременными импульсами тока//Сварочное производство. – 1974.-№2.-
С.3-5.
Трофимов Н.М., Синицкий Р.В. Динамические характеристики импульсной
|
Рисунок 3. – Осциллограмма тока. |
дуги при сварке в аргоне//Сварочное |
|
|
производство. – 1967.-№8.-С.17-19. |
||
ЛИТЕРАТУРА: |
|
|
|
Полосков С.И., Букаров |
В.А., Ищенко |
|
|
Ю.С. |
Особенности |
управления |
|
формированием корня шва при орбитальной сварке неповоротных стыков труб//Сварочное производство. – 2003.- №4.–С.3–9.
Березовский Б.М. Математические модели дуговой сварки: в 3 т. – том 2. Математическое моделирование и оптимизация формирования различных типов сварных швов. – Челябинск: Изд-во ЮУрГУ, 2003. – 601с.
Гарбуль А.Ф., Канашкин Ю.П. Сварка корня шва неповоротных стыков труб
ПОДГОТОВКА ПРОИЗВОДСТВА НА БАЗЕ АВТОМАТИЗИРОВАННОГО РАБОЧЕГО МЕСТА ТЕХНОЛОГА
Буланов А.Г. Комарницкий А.Н., Елаева Н.К.
Восточно-Сибирский государственный технологический университет, Улан-Удэ, Ключевская 42 «а»,e-mail: tmmskesstu@mail.ru
При |
автоматизации |
конструкторско- |
технологами в разнообразных пакетах, а для |
|||||||||
технологической подготовки |
|
производства |
программирования станка необходима точная |
|||||||||
требуется интеграция и автоматизация всех |
математическая модель детали, которая |
|||||||||||
работ в этой области в целях сокращения |
воссоздается технологом-программистом по |
|||||||||||
трудоемкости |
проектирования |
и |
расчета |
полученным чертежам. При переводе из |
||||||||
используемого |
оборудования, |
повышения |
разных пакетов точность модели снижается, |
|||||||||
качества |
проектных решений |
и |
уровня |
поэтому необходимо привести модель к |
||||||||
унификации технологических решений и т.д. |
унифицированному виду. |
|
|
|||||||||
На |
современном |
этапе |
основными |
Для |
конструкторов |
Улан-Удэнского |
||||||
задачами |
автоматизации |
|
в |
области |
авиационного завода на основе инструкций |
|||||||
конструкторско-технологической |
подготовки |
оговорен порядок разработки чертежей, |
||||||||||
производства можно считать использование |
расположение |
|
на различных |
уровнях |
||||||||
трехмерных моделей, созданных в таких |
контуров, групп, отверстий, размеров и т.д. |
|||||||||||
пакетах |
как |
AutoCAD, |
Cimatron, |
ADEM, |
Тем самым создаются предпосылки для |
|||||||
Компас и др. |
для разработки программ для |
сквозной |
автоматизации |
конструкторско- |
||||||||
станков с ЧПУ с двумя |
|
и более |
технологической |
|
подготовки |
производства, |
||||||
координатными осями. |
Такие модели могут |
являющейся |
ключом к |
рентабельности |
||||||||
быть созданы в конструкторском бюро и |
современного производства на базе единой |
|||||||||||
включены в конструкторскую документацию. В |
информационной |
модели |
изделия. |
|||||||||
ряде случаев |
модели |
деталей |
создаются |
Жизненный цикл этой модели обеспечивает |
277

XIII Международная научно-практическая конференция «СОВРЕМЕННЫЕ ТЕХНИКА И ТЕХНОЛОГИИ»
единое |
конструкторско-технологическое |
производится |
на основе |
трехмерной |
||||||
пространство, |
насыщенное |
инструментами |
электронной модели (Рис.1) и относится к |
|||||||
для решения |
широкого |
спектра |
задач. |
следующим |
видам |
механообработки: |
||||
Программирование |
станков |
с |
ЧПУ |
фрезерование, обработка отверстий и др. |
|
|
Рис.1 Трехмерная электронная модель типа Кронштейн |
|
|
||||||||
Расчет и контроль УП (управляющей |
конечном итоге сводится к основному набору |
|||||||||||
программы) на необходимое оборудование |
функциональных свойств и требований, |
|||||||||||
происходит в PFM файле. После расчёта УП |
которым она должна соответствовать: |
|||||||||||
запускается |
модуль расчета |
машинного |
1 Гибкая система адаптации под |
|||||||||
времени (Т.маш). Созданный электронный |
специфические условия того или иного |
|||||||||||
архив связанных txt и pfm файлов даёт |
предприятия, включающая в себя модули |
|||||||||||
возможность |
применить информацию |
для |
построения информационнотехнологических |
|||||||||
подготовки |
производства |
изготовления |
связей, пользовательских интерфейсов и |
|||||||||
деталей на станках с ЧПУ, рассчитать |
генерирования |
|
любой |
|
возможной |
|||||||
мощность, |
загрузку |
оборудования, |
технологической документации. |
|
||||||||
необходимое количество инструмента и т.д. |
2 |
Интеграция |
с |
конструкторским |
||||||||
В настоящее время нет универсального |
интерфейсом, |
позволяющая |
технологу |
|||||||||
пакета автоматизации рабочего места (АРМ) |
работать непосредственно с изображениями |
|||||||||||
для осуществления сквозной автоматизации |
трехмерного |
|
технологического |
объекта |
||||||||
конструкторско-технологической |
подготовки |
(созданных в таких пакетах как, Cimatron, |
||||||||||
производства, хотя |
Российский рынок САПР |
Adem, Компас, T-Flex и др.) и максимально |
||||||||||
предлагает |
пользователям |
целый |
ряд |
использовать |
визуальную |
информацию в |
||||||
программных продуктов, ориентированных на |
процессе технологического проектирования; |
|||||||||||
автоматизацию работы технолога. Основные |
3 |
Интеграция |
с системой управления |
|||||||||
цели АРМа - это сокращение трудоемкости |
базами данных, позволяющая использовать |
|||||||||||
проектирования и |
расчета |
используемого |
накопленный |
|
технологический |
опыт, |
||||||
оборудования, |
повышение |
качества |
справочную |
и |
специфическую информацию |
|||||||
проектных решений, повышение уровня |
предприятия, |
|
получать, |
обрабатывать |
||||||||
унификации технологических решений. Выбор |
рабочие |
параметры |
технологических |
|||||||||
базовой |
системы, |
|
построение |
объектов. |
|
|
|
|
|
автоматизированного рабочего места (АРМ) в
278

Современные техника и технологии 2007
4 |
Минимальный |
относительный |
объем |
производить формирование технологического |
||||||
временных |
и финансовых затрат |
(в |
том |
процесса поэтапно, редактирование 3D- |
||||||
числе на обучение пользователей и |
моделей, просмотр базы данных деталей, |
|||||||||
разработчиков). |
|
|
|
|
|
инструмента, оборудования и специального |
||||
Разрабатываемая |
|
система |
|
|
АРМ |
инструмента. |
Программирование станков с |
|||
технолога |
(рис.2) |
в |
первую |
очередь |
ЧПУ производится на основе |
трехмерной |
||||
рассчитана на поддержку жизненного цикла |
электронной модели для следующих видов |
|||||||||
подготовки производства на базе единой |
обработки: |
фрезерование, |
сверление, |
|||||||
информационной |
модели |
изделия. |
точение и электроэрозионная обработка. При |
|||||||
Предлагаемая программа по автоматизации |
расчёте управляющей программы происходит |
|||||||||
рабочего места технолога |
создана в среде |
расчет машинного времени. Система |
||||||||
Delphi. В системе сосредоточены средства |
является открытой для наращивания баз |
|||||||||
для |
трехмерного |
проектирования |
и |
данных. |
|
|
||||
конструирования, |
АРМ |
позволяет |
|
|
|
Рис.2 Этап формирования техпроцесса в АРМе
ИСПОЛЬЗОВАНИЯ ЭЛЕКТРОГИДРАВЛИЧЕСКОГО ДРОССЕЛИРУЮЩЕГО ГИДРОРАСПРЕДЕЛИТЕЛЯ С ПРОПОРЦИОНАЛЬНЫМ УПРАВЛЕНИЕМ В КАЧЕСТВЕ ПРОГРАММНО-УПРАВЛЯЕМОГО ЭЛЕМЕНТА ЗАДАНИЯ УСИЛИЯ НАГРУЖЕНИЯ
Буханченко С.Е., Литвинчук Р.
Томскийполитехническийуниверситет, Россия, г. Томск, пр. Ленина, 30 E-mail: triboss@tpu.ru
Современные методы нагружения узлов и механизмов в реальных машинах и средствах их испытания должны обеспечивать плавное приложение нагрузки и стабильность режима нагружения независимо от изменения в процессе испытания размеров образцов, их биения от возникающих моментов трения и т.д. Однако при наличии биения вращающихся валов или большой частоты возвратно-поступательного движения в
определенные моменты возникают условия, когда нагрузка полностью не передается в контакт, а в иные моменты возникают ударные нагрузки. Это препятствует обеспечению нормальной работы и проведению различных испытаний в узлах и механизмах машин при контролируемых условиях. Поэтому в таких случаях используют узлы нагружения, обладающие способностью демпфирования.
279

XIII Международная научно-практическая конференция «СОВРЕМЕННЫЕ ТЕХНИКА И ТЕХНОЛОГИИ»
В случае, когда необходимо воспроизвести сложный закон нагружения целесообразно применение средств, способных изменять силу нагружения по необходимому закону во времени. Наибольший интерес представляют гидравлические системы нагружения. Они позволяют создавать различные законы нагружения максимально приближенные к реальным условиям функционирования узлов и механизмов большинства машин при использовании электрогидравлических приводов с дроссельным регулированием.
Обычно управляющая часть системы нагружения состоит из электрического
устройства, которое воспринимает задающее воздействие от ЭВМ, и вырабатывают сигнал управления силовой частью. В силовую часть входят исполнительные механизмы и регулирующее устройство. Для уменьшения мощности, потребляемой управляющей частью, в регулирующее устройство, кроме распределителя потока рабочей жидкости, включен гидроусилитель.
Испытываемая в данной работе система нагружения является автоматической системой с цифровым управлением, структурная схема которой представлена на рис. 1.
Рис. 1. Структурная схема привода с цифровым управлением.
ПУДГР – программно-управляемый дросселирующий гидрораспределитель; УЭС – усилитель электрических сигналов; ЭМП – электромеханический преобразователь; ГУ – гидравлический усилитель; ИМ – исполнительный механизм.
В данной системе с дискретным управлением выходная величина FN, определяющая нормальное усилие нагружения, как и в системах с непрерывным управлением, является непрерывной функцией времени, что объясняется фильтрующими свойствами исполнительного механизма, не пропускающего изменяющиеся с большой частотой дискретные сигналы.
Основными элементами рассматриваемой системы нагружения являются:
-рабочая жидкость − индустриальное масло АМГ-10;
-магистральные линии: напорные – стальной трубопровод, сливные – гибкие шланги;
-насосная станция, работающая в режиме постоянного давления;
-золотниковый регулирующий элемент − программно-управляемый дросселирующий гидрораспределитель типа СК 3-211 (Болгария);
-гидравлические исполнительные
механизмы − гидроцилиндры двухстороннего действия.
ДГР типа СК3-211 являются представителем наиболее распространенных дросселирующих элементов, позволяющих бесступенчато регулировать площадь рабочего окна. Они отличаются простотой конструкции, надежностью работы, сравнительно небольшой мощностью,
необходимой для управления золотником, состоит из электрогидравлического преобразователя и распределителя. Принцип его функционирования описан в литературе. Возможные схемы подключения распределителя представлены на рис. 2, а экспериментальные статические характеристики представлены на рис. 3.
а)
280
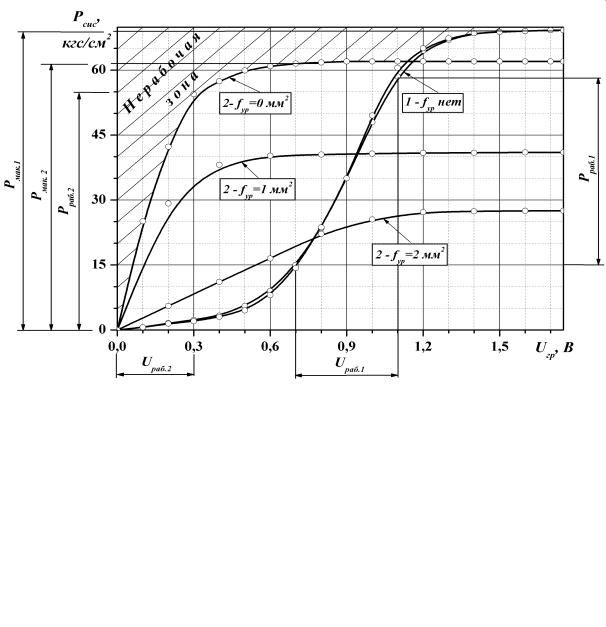
Современные техника и технологии 2007
б)
Рис. 2. Схемы возможного подключения дросселирующего гидрораспределителя СК3-211
Рис. 3. Экспериментальные статические характеристики дросселирующего гидрораспределителя СК3-211.
Во |
время |
проведения |
испытаний |
давлений в полостях А, В и Б, Г, при этом |
|||
нагружение |
осуществлялось |
двумя |
поршни подвергаются давлению с обоих |
||||
способами: |
|
|
торцов. |
|
|
|
|
- а) если давление в разгрузочных |
Задание нагрузки за счет разности |
||||||
полостях В и Г равно нулю (рис. 2 а), тогда |
давлений в полостях А, В и Б, Г обеспечивает |
||||||
нагружение происходит за счет создания |
более точный закон нагружения. То есть, при |
||||||
одинаковых или разных давлений в полостях |
подключении гидрораспределителя по схеме, |
||||||
А и Б, при этом каждый поршень |
изображенной |
на рис. 2 б обеспечивается |
|||||
подвергается давлению только с одного |
максимальная |
чувствительность |
и |
||||
торца; |
|
|
|
максимальная |
протяженность |
линейного |
|
- б) если давление в разгрузочных |
участка, характеризующаяся |
отсутствием |
|||||
полостях В и Г не равно нулю (рис. 2 б), то |
гистерезиса |
|
(рис. 3). |
||||
нагружение происходит за счет |
перепада |
|
|
|
|
281

XIII Международная научно-практическая конференция «СОВРЕМЕННЫЕ ТЕХНИКА И ТЕХНОЛОГИИ»
СПОСОБЫ СНИЖЕНИЯ ВИБРАЦИИ ПРИ РАБОТЕ РАСТОЧНОГО ИНСТРУМЕНТА
Валентов А.В., Зюзляев Д.С.
Юргинский технологический институт Томского политехнического университета, Россия, 652000, г. Юрга, ул. Ленинградская 26
E-mail: valentov@mail.ru
Перед современным машиностроением при растачивании отверстий особенно остро стоит вопрос о снижении вибрации и повышении жесткости инструмента. Вибрация отрицательно влияет на процесс формообразования, может вызывать повышенный износ инструмента, а в некоторых случаях даже выход из строя металлорежущего оборудования.
Оправки расточных инструментов отечественного производства нуждаются в увеличении жесткости и снижении возникающей в процессе резания вибрации.
Традиционные методы не позволяют получить достаточно высоких и стабильных результатов процесса растачивания. Поэтому предлагается методика изготовления оправок с избыточным гидравлическим давлением в теле оправки. (Рис. 1)
Рис. 1 Макет способа создания избыточного гидравлического давления в теле оправки.
Это может быть достигнуто заполнением полости оправки гидравлической жидкостью с высоким коэффициентом вязкости и введением в
эту полость плунжера. Так как жидкость практически несжимаема, давление будет передаваться на стенки оправки, снижая тем самым увеличивая вибростойкость системы и, соответственно, повышая жесткость последней, как показывает практика, на 15-20%. Кроме того, существует вероятность изготовления сотовой конструкции тела оправки в поперечном сечении.
Учитывая интенсификацию производства и стремление к концентрации операций, предлагается существенно повысить жесткость оправки, используя специальное приспособление, которое, помимо уменьшения вибрации и увеличения жесткости, выполняет
дополнительную операцию раскатки обработанной поверхности за счет установки свободно вращающихся сфер на концах насадного приспособления.
Линеаризация уравнения возникающей вибрации методом гармонического баланса выглядит следующим образом.
Основная идея метода гармонического баланса состоит в том, что колебание предполагается синусоидальным:
x=Acosωt, x=v=-Aωsinωt
Практически осуществляется замена негармонического колебания его первой гармоникой. Тогда восстанавливающая функция f(x,v) периодична с периодом Т=2π/ω и может быть разложена в ряд Фурье:
f (x, v) = f (Acosωt − Aω sin ωt) =
∞
=a0 + ∑(aν cosνωt + bν sin ωt)
ν=1
Ограничимся симметричными восстанавливающими функциями, для которых а0=0. В разложении будем пренебрегать членами с ν >1.
|
|
|
|
|
|
|
|
|
|
|
a |
b |
• |
|
|
f (x,ν) ≈ a |
cosωt + b sin ωt = |
1 x − |
|
1 |
x |
||||||||
|
|
|
||||||||||||
|
1 |
|
|
|
1 |
|
A |
Aω |
|
|||||
где: |
|
|
|
|
|
|
||||||||
|
|
|
|
|
|
|
|
|
||||||
a1 = |
1 |
|
π∫ f (a cosωt − Aω sin ωt) cosωtdωt |
|
||||||||||
π |
|
|||||||||||||
|
0 |
|
|
|
|
|
|
|
|
|
||||
b1 = |
1 |
π∫ f (a cosωt − Aωsin ωt) sin ωtdωt |
|
|
||||||||||
π |
|
|
||||||||||||
|
0 |
|
|
|
|
|
|
|
|
|
||||
|
|
|
|
|
Тогда |
нелинейные |
уравнения |
|
|
|||||
автоколебательных |
|
|
|
систем |
|
|
||||||||
•• |
|
|
|
|
• |
|
|
|
|
|
|
|
|
|
x |
+ f (x, x) = 0 будет иметь вид |
|
|
|
|
|||||||||
|
|
|
|
|
•• |
|
b |
• |
a |
|
|
|
|
|
|
|
|
|
|
x− |
|
1 |
x+ |
1 x |
= 0 |
|
|
|
|
|
|
|
|
|
Aω |
|
|
|
|
|||||
|
|
|
|
|
|
|
|
A |
|
|
|
|
|
Коэффициенты этого уравнения не постоянны и зависят от амплитуды колебаний A. Это связано с непостоянной
282

Современные техника и технологии 2007
во времени периодической силой, возникающей на режущем инструменте в процессе обработки.
Безразмерный коэффициент затухания
|
−b1 |
|
|
b1 |
||
D = |
|
Aω |
|
= − |
||
|
|
|
2ω a A |
|||
2 |
|
a |
|
|
||
1 |
|
|
1 |
|||
|
A |
|
|
|
Зависимость коэффициента демпфирования и относительного рассогласования от амплитуды представлена на рисунке 2
Рис. 2 Зависимость коэффициента демпфирования (сплошная линия) и относительного рассогласования (штрихпунктирная линия) от амплитуды.
Таким образом, вероятно создание системы контроля за наличием вибрации на расточной оправке в процессе растачивания заготовки на станке, работающей по следующей схеме.
Рис. 3 Система контроля вибрации на расточной оправке.
При снятии результатов экспериментов необходимо учитывать не только вибрацию, возникающую в процессе механической обработки, но и в переходных процессах, связанных с неоднородностью металла, а так же
с отклонениями формы обрабатываемой экспериментальной заготовки.
Тензорезисторы должны располагаться таким образом, чтобы не было взаимного влияния друг на друга, однако, их расположение должно быть выполнено так, чтобы получить максимально полную картину возникающих частот.
Кроме этого, необходимо различать амплитудную модуляцию и биение. Они имеют похожие временные реализации. Это действительно так, но с небольшой поправкой – в случае биений имеет место сдвиг фазы в точке полного взаимоуничтожений сигналов (Рис. 4)
Рис. 4 Характеристики амплитудной модуляции и биения
Из-за того, что эти сигналы немного различаются по частоте, их разность фаз изменяется в пределах от нуля до 360 градусов, а это означает, что их суммарная амплитуда будет то усиливаться (сигналы в фазе), то ослабляться (сигналы в противофазе). В спектре биения присутствуют компоненты с частотой и амплитудой каждого сигнала, и полностью отсутствуют боковые полосы. В данном примере амплитуды двух исходных сигналов различны, поэтому они не полностью взаимоуничтожаются в нулевой точке между максимумами. А значит, биение - это линейный процесс: оно не сопровождается появлением новых частотных компонент.
ЛИТЕРАТУРА: |
|
|
1. Колебания: |
Введение |
в |
исследование колебательных систем / К.
Магнус.– М.: Мир, 1982. – 304 с.
2. Электродинамика материальных сред: / Р.И. Соколовский. – Хабаровск:
Изд-во ДВГУПС, 2001. – 67 с. |
|
||
3. В.А. |
Романов, |
О.К. |
Слива |
Аналитическая динамика |
и |
теория |
колебаний. Учебное пособие./ Челябинск.
Изд-во ЮУрГУ, 2003 г., – 116с.
283

XIII Международная научно-практическая конференция «СОВРЕМЕННЫЕ ТЕХНИКА И ТЕХНОЛОГИИ»
ПОЗИЦИОНИРОВАНИЕ ИЗДЕЛИЙ ПРИ СВАРКЕ ПРОСТРАНСТВЕННЫХ ШВОВ СЛОЖНОЙ ФОРМЫ
Васильев М.Е., Щербинин С.В. Юргинский технологический институт ТПУ,
Россия, Кемеровская область, г.Юрга, ул. Достоевского, 6
E-mail: viking_r.b@mail.ru
При автоматической сварке и термической обработке деталей, ограниченных поверхностями сложной формы, важную роль играет точность позиционирования поверхности детали относительно источника теплового излучения [1]. Для позиционирования деталей могут быть использованы операционные автоматы [2]. На рис. 1 показано технологическое оборудование для лазерного упрочнения поверхностей деталей. Оно также может быть использовано для позиционирования изделий при сварке пространственных швов сложной формы.
Рис. 1. Технологическое оборудование для лазерного упрочнения поверхности детали
Данное оборудование содержит источник теплового излучения 1 (это может быть сварочная горелка) и операционный автомат 2, обеспечивающий крепление изделия, его позиционирование, а также продольное и поперечное перемещение и вращение при сварке шва. Обычно такое оборудование оснащено системой управления, которая построена на базе промышленного компьютера и модулем управления движением. Автоматизированное рабочее место оператора реализовано на базе промышленного компьютера с сенсорным экраном. Система управления во время работы производит регистрацию и хранение параметров технологического процесса с привязкой к реальному времени.
Наиболее важной стадией технологической подготовки производства с применением операционных автоматов является разработка управляющих программ (УП). При их составлении требуется определить траектории движения инструмента и исполнительных органов
автомата. Данная задача значительно усложняется, если речь идет об обработке деталей ограниченных сложными криволинейными поверхностями.
Подготовку геометрической информации для управляющих программ многокоординатных операционных автоматов можно осуществить в несколько этапов
-получение математической модели обрабатываемой поверхности детали;
-выбор и расчет траекторий обработки поверхности детали;
-определение траекторий движения инструмента и исполнительных органов автомата;
-составление управляющей программы перемещения инструмента и исполнительных органов автомата;
-выбор операционного автомата по количеству и взаимному расположению приводов манипулятора и платформы.
В докладе предлагается универсальный метод расчета положения сварочной горелки (электрода) для обеспечения роботизированной сварки по траектории любой сложности.
Исходными данными для расчета являются чертежи свариваемых деталей, на которых поверхности 1 и 2 (рис. 2), ограничивающие детали, заданы каркасом поперечных сечений. Известно положение крайних точек O и K траектории 3 сварного шва. Если шов выполняют по замкнутой траектории, то крайние точки будут совпадать.
Горелка (электрод) 4 (рис. 2) по отношению к траектории сварного шва 3 должна быть расположена следующим образом. Ось горелки находится в биссекторной плоскости 5, делящей
пополам двугранный угол β образованный касательными плоскостями к поверхностям свариваемых деталей 1 и 2
вточке Mi траектории шва. Известны: угол
αмежду осью горелки 4 и плоскостью нормалей 6; расстояние b от опорной точки F горелки до сварного шва 3, т.е. дина отрезка FMi=const=b.
284

Современные техника и технологии 2007
Рис. 2. Ориентация горелки к криволинейному сварному шву
Требуется определить последовательность положений в пространстве сварочной горелки (электрода) 4 ориентированного определенным образом к траектории сварного шва 3.
Для решения данной задачи необходимы математические модели поверхностей деталей 1 и 2 (рис. 2). При создании моделей необходимо учитывать, что они должны полностью обеспечивать вычислительные процедуры по расчету положения электрода. Наиболее удобно с этой точки зрения использовать для подготовки математических моделей сплайн-функции класса С2 [3, 4].
Дискретные |
положения |
электрода |
в |
пространстве |
определяем |
по следующему |
|
алгоритму (рис. 3). |
|
|
Рис. 3 Блок схема алгоритма расчета положений электрода
При соединении сваркой деталей ограниченных сложными криволинейными поверхностями возникает проблема в ровной резке и разделке кромок по определенной форме. Очевидно, что наиболее точно воспроизвести нужную форму кромок можно на оборудовании с числовым программным управлением. Для обеспечения подготовки кромок и процесса сварки необходима математическая модель траектории шва.
285
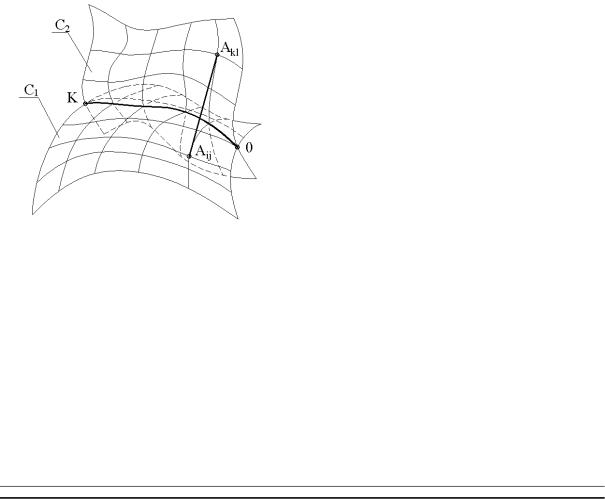
XIII Международная научно-практическая конференция «СОВРЕМЕННЫЕ ТЕХНИКА И ТЕХНОЛОГИИ»
Рис. 4 Траектория сварного шва.
Траекторию сварного шва определяем как результат пересечения двух поверхностей ограничивающих детали со стороны шва. (рис.4)
Таким образом получим необходимые данные для составления управляющих программ роботизированных комплексов для сварки криволинейных швов. Предлагаемый метод расчета положения горелки позволяет автоматизировать процесс подготовки управляющих программ, обеспечить необходимое качество изделий для роботизированных комплексов.
ЛИТЕРАТУРА:
1.Геттерт В., Герден Г и др. Сварочные роботы. – М.: Машиностроение, 1988. – 288 с.
2.Осипов Ю.М., Щербинин С.В. Геометрическое обеспечение работы многокоординатных операционных автоматов // Автоматизация и современные технологии. – 1999. - № 8. –
С. 2-3.
3.Завьялов Ю.С., Леус В.А., Скороспелов В.А. Сплайны в инженерной геометрии. – М.: Машиностроение, 1985. – 224 с.
4.Роджерс Д., Адамс Дж. Математические основы машинной графики. – М.: Мир, 2001. – 604 с.
5.Тертышный В.Т. Программирование перемещений при роботизированной сварке криволинейных швов // Автоматическая сварка. – 1993. - № 3. –
С. 48-52.
6.Львов Н.С., Гладков Э.А. Автоматика и автоматизация сварочных процессов. – М.: Машиностроение, 1982. – 302 с.
ПЕРСПЕКТИВЫ РАЗРАБОТКИ ДИНАМИЧЕСКОЙ МОДЕЛИ СВАРОЧНОЙ ВАННЫ ПРИ СВАРКЕ В СО2
Давыдов А.А., Чинахов Д.А.
Юргинский технологический институт (филиал) Томского политехнического университета
652000 Кемеровская обл., г. Юрга, ул. Ленинградская 26,
т. (384-51) 5-39-23, ф. (384-51) 6-26-83, prepod13@mail.ru, zver73@rambler.ru
На современном этапе развития сварочного производства важнейшим условием его совершенствования и развития является создание высокоэффективных методов и средств моделирования и имитации сварочных процессов, а также их контроля и оптимального управления в реальном масштабе времени. Большое внимание уделяется применению современных средств математического и компьютерного моделирования, которые превратились в мощный инструмент исследования и познания процессов, происходящих в сложных сварочных технологических системах.
Однако применение методов математического моделирования сдерживается отсутствием содержательных математических описаний процессов и явлений, протекающих в сварочной ванне. Решением данной задачи занимаются ученые в России и за рубежом [1-6]. Автором [1] предложена следующая классификация математических моделей сварочной ванны:
1.Плоская капиллярно-гидростаческая модель (ПКГСМ);
2.Объемная тепловая капиллярногидростаческая модель (ОТКГСМ);
3.Тепловая магнитогидродинамическая модель (ТМГДМ).
286

Современные техника и технологии 2007
Разработка динамической модели является актуальной задачей, решение которой позволит управлять процессами в сварочной ванне, зоне термического влияния и, как следствие, эксплуатационными свойствами сварного соединения в целом. Для разработки подобной модели необходимо решить комплекс сложных задач, т.е. определить закономерности и зависимости между явлениями и управляемыми параметрами сварочного процесса.
Перспективным направлением в этой области является использование программных продуктов общего назначения, основанных на численных математических методах (МКЭ). Наряду с такими пакетами как
ALGOL, ABAQUS, COSMOS/M, NASTRAN и
др. численное моделирование с помощью пакета ANSYS является мощным и надежным инструментом для достижения поставленной цели [7]. Подобные технологии обладают высокой точностью распределения всех физических величин при отслеживании процессов происходящих в сварочной ванне, как в пространстве, так и во времени. Они позволяют оценить вклад каждого физического явления в отдельности, отследить влияние изменений геометрии сварного соединения, граничных условий и свойств материалов.
По результатам ранее проведенных исследований установлено, что импульснодинамическое воздействие на расплавленный металл сварочной ванны оказывает положительное влияние на структуру и свойства многослойных сварных соединений из легированных сталей [8]
Для изучения механизма этого воздействия разрабатывается модель управления импульсно-динамическими воздействиями на расплавленный металл сварочной ванны. Для адекватного функционирования модели в ее состав необходимо включить подмодели: источника тепла и силового воздействия на ванну, термодинамических явлений в сварочной ванне, гидродинамических явлений в сварочной ванне, формирования поверхности расплава ванны, кристаллизации сварочной ванны, формирования шва и ЗТВ. Кроме этого, нужно определить наиболее значимые управляемые параметры процесса сварки, влияющие на физико-термические процессы в расплавленном металле сварочной ванны и явления на границе раздела трех фаз газ – жидкий металл – твердый металл (рис.1).
Рис. 1 Схема основных процессов, происходящих при дуговой сварке плавящимся электродом.
При этом немаловажным фактором является воздействие газового фронта на расплавленный металл сварочной ванны.
Для оценки влияния газового фронта на металл сварочной ванны планируется использование системы моделирования движения жидкости и газа FlowVision. Программный комплекс FlowVision решает трехмерные уравнения динамики жидкости и газа, которые включают в себя законы сохранения массы, импульса (уравнения Навье-Стокса), уравнения состояния. Для расчета сложных движений жидкости и газа, сопровождаемых дополнительными физическими явлениями, такими, как, турбулентность, горение и сжатие столба дуги, контактные границы раздела и так далее, в FlowVision включаются дополнительные уравнения, описывающие эти явления.
На данный момент средствами пакета
Ansys Multiphysics разрабатывается термодинамическая подмодель, описывающая температурную составляющую общей динамической модели сварочной ванны при сварке в защитных газах многослойных сварных соединений из высокопрочных легированных сталей.
Разработанная динамическая модель сварочной ванны будет использована для исследования влияния технологических факторов на процессы массопереноса в сварочной ванне, структуру и свойства сварных соединений, прогнозирования
287

XIII Международная научно-практическая конференция «СОВРЕМЕННЫЕ ТЕХНИКА И ТЕХНОЛОГИИ»
эксплуатационных |
свойств |
сварных |
аспекты |
компьютерного |
моделирования |
||||
конструкций на производстве при инженерных |
тепловых, деформационных процессов и |
||||||||
расчетах, а также в учебном процессе для |
структурообразования |
при |
сварке |
и |
|||||
подготовки студентов технических вузов. |
|
сопутствующих |
технологиях |
// Сварочное |
|||||
ЛИТЕРАТУРА: |
|
|
производство. 1998. №10. С.16-24. |
|
|||||
1. Березовский Б.М. Математические |
5 Судник В.А., Ерофеев В.А., Иванов А.В. |
||||||||
модели дуговой сварки: В 3 т – Том 1. |
Создание |
и |
внедрение |
компьютерных |
|||||
Математическое |
моделирование |
и |
технологий |
прогнозирования |
формирования |
||||
информационные |
технологии, |
модели |
шва при дуговой сварке // Сварочное |
||||||
сварочной ванны и формирования шва. – |
производство. 1997. №11. С.40-45. |
|
|||||||
Челябинск: Изд-во ЮУрГУ, 2002. – 585 с. |
|
6. V. Pavlyk, U. Dilthey. A numerical and |
|||||||
2 Полосков С.И., Ищенко Ю.С., Букаров |
experimental study of fluid flow and heat transfer |
||||||||
В.А. Анализ факторов, определяющих |
in stationary GTA weld pools // Mathematical |
||||||||
формирование |
сварочной ванны |
при |
modeling of weld phenomena 5. 1999. C. 135- |
||||||
орбитальной с варке неповоротных стыков |
163. |
|
|
|
|
|
|||
труб // Сварочное производство. 2003. №2. |
7. A. Spille-Kohoff. Моделирование |
||||||||
С.11-19. |
|
|
|
процессов дуговой сварки // Ansys solutions. |
|||||
3 Лесков Г.И., Пустовойт С.В. К вопросу о |
Русская редакция. Лето 2006. С. 36-39. |
|
|||||||
построении динамической модели сварочной |
8. Чинахов Д.А. Сварка многослойных |
||||||||
ванны / Автоматическая Сварка. 2001 №1. |
|
соединений из стали 30ХГСА // Технология |
|||||||
4 Киселев С.Н., Киселев А.С., Куркин А.С., |
металлов. 2005. № 11. С. 31-36 |
|
|||||||
Аладинский В.В., Маханев В.О. Современные |
|
|
|
|
|
|
ВЛИЯНИЕ РЕЖИМОВ ОТПУСКА НА СТРУКТУРУ И СВОЙСТВА НАПЛАВКИ ИЗ СТАЛИ ПР-Х18ФНМ
Дегтерев А.С., Дураков В.Г., Гнюсов С.Ф. Томский политехнический университет, Россия, г. Томск, пр. Ленина, 30, ТПУ
E-mail:ScotAS@mail.ru
Введение |
свойств |
электронно-лучевых |
наплавок |
Впроцессе эксплуатации машин и порошковой стали Х18ФНМ мартенситного
механизмов их детали зачастую работают в |
класса, имеющей высокую твердость, |
||||||||||||||||
жестких |
условиях |
|
контактирования |
с |
прочность и пластичность [2]. |
|
|
|
|||||||||
агрессивными |
средами |
и |
абразивом, |
Цель работы |
|
|
|
|
|
||||||||
вызывающими интенсивную коррозию и износ |
Изучить влияние режимов отпуска на |
||||||||||||||||
рабочих поверхностей. Потеря металла при |
структуру |
и |
свойства |
наплавки |
из |
||||||||||||
этом составляет 20 и 15 % соответственно [1]. |
высокохромистой порошковой стали Х18ФНМ, |
||||||||||||||||
Известно, |
|
что |
|
мартенситные |
выполненной с применением электронно- |
||||||||||||
высокохромистые |
стали, |
дополнительно |
лучевых технологий. |
|
|
|
|
|
|||||||||
легированные |
|
|
карбидообразующими |
Материал и методы исследования |
|
||||||||||||
элементами, |
обладают |
одновременно |
Наплавку осуществляли на электронно- |
||||||||||||||
высокой износо- и коррозионной стойкостью. |
лучевой установке, оснащенной электронной |
||||||||||||||||
Можно надеяться, что использование |
пушкой с плазменным катодом, блоком |
||||||||||||||||
высокоэнергетических |
методов |
наплавки, |
развертки луча и порошковым дозатором [3]. |
||||||||||||||
обеспечивающих |
быстрый |
нагрев |
и |
Примерный |
химический |
состав порошка |
|||||||||||
охлаждение |
наплавляемого |
металла, |
представлен в таблице 1. |
|
|
|
|
||||||||||
позволит |
сформировать |
метастабильную |
Таблица 1 |
|
|
|
|
|
|
||||||||
структуру |
матрицы |
с |
дисперсными |
|
C |
Cr |
Mo |
Ni |
V |
Fe |
|
|
|||||
карбидными выделениями. Это обеспечит |
|
|
|
|
|
|
|
|
|
||||||||
высокую |
износостойкость |
контактирующим |
|
0,8 |
18 |
>1 |
>1 |
>1 |
Основа |
|
|
||||||
поверхностям |
за |
счет |
дополнительного |
|
|
|
|
|
|
|
|
|
|||||
Исследуемая сталь была наплавлена на |
|||||||||||||||||
механизма упрочнения матрицы – структурно- |
|||||||||||||||||
массивную заготовку из стали 30 в вакууме. |
|||||||||||||||||
фазового превращения. Данная работа |
|
|
|
|
|
|
|
|
|
||||||||
посвящена |
исследованию |
структуры |
и |
|
|
|
|
|
|
|
|
|
288