
- •к.т.н., начальник отдела ОНИР СиМУ ЭЛТИ, сопредседатель секции №1
- •д.т.н., профессор, зав. каф. фмпк эфф, председатель секции № 9
- •СЕКЦИЯ 1. ЭЛЕКТРОЭНЕРГЕТИКА
- •АВТОМАТИЗАЦИЯ РАСЧЕТА СТРУКТУРНОЙ НАДЕЖНОСТИ ЭЛЕКТРИЧЕСКИХ СХЕМ
- •ОСОБЕННОСТИ МОДЕЛИРОВАНИЯ ЭЛЕКТРИЧЕСКОГОПОЛЯ В МОРСКОЙ ВОДЕ
- •КАБЕЛЬ ДЛЯ ЭЛЕКТРОПИТАНИЯ ГЕНЕРАТОРОВ НИЗКОТЕМПЕРАТУРНОЙ ПЛАЗМЫ
- •Колпаков В.А., Паранин В.Д., Мокеев Д.А………………...86
- •СПОСОБЫ СЕЛЕКЦИИ КОРОТКИХ ЗАМЫКАНИЙ НА ЛИНИЯХ ЭЛЕКТРОПЕРЕДАЧИ
- •СЕКЦИЯ 2. ПРИБОРОСТРОЕНИЕ
- •ИСПОЛЬЗОВАНИЕ КОМПЬЮТЕРНОГО МОДЕЛИРОВАНИЯ ПРИ ИССЛЕДОВАНИИ СПОСОБА КОМПЕНСАЦИИ ДЕЙСТВИЯ ВИБРАЦИИ НА ГИРОМАЯТНИК
- •РАЗРАБОТКА И ИССЛЕДОВАНИЕ МИКРОМЕХАНИЧЕСКОГО ГИРОСКОПА
- •НОРМИРОВАНИЕ ШИХТОВЫХ МАТЕРИАЛОВ ДЛЯ ПРОИЗВОДСТВА ОТЛИВОК ИЗ АЛЮМИНИЕВЫХ СПЛАВОВ
- •ИНВЕРТОРНЫЙ ИСТОЧНИК ПИТАНИЯ ДЛЯ СВАРКИ МОДУЛИРОВАННЫМ ТОКОМ
- •ИССЛЕДОВАНИЕ ВЛИЯНИЯ ОТКЛОНЕНИЯ КОРПУСА НА ЦИКЛ РАБОТЫ ПНЕВМОГИДРАВЛИЧЕСКОГО УДАРНОГО МЕХАНИЗМА
- •ДИНАМИЧЕСКИЕ ПРОЦЕССЫ В БУРОВОЙ КОЛОННЕ ПРИ ВРАЩАТЕЛЬНО-УДАРНОМ БУРЕНИИ СКВАЖИН МАЛЫХ ДИАМЕТРОВ
- •СЕКЦИЯ 4. ЭЛЕКТРОМЕХАНИКА
- •ВЛИЯНИЕ ДЛИНЫ АСИНХРОННОГО ДВИГАТЕЛЯ НА ЭФФЕКТИВНОСТЬ КРЕПЛЕНИЯ
- •РЕЗУЛЬТАТЫ ЭКСПЕРИМЕНТАЛЬНЫХ ИССЛЕДОВАНИЙ ХАРАКТЕРИСТИК СИНХРОННОГО ГИБРИДНОГО ДВИГАТЕЛЯ
- •РАЗРАБОТКА ЭЛЕКТРОМЕХАНИЧЕСКОГО ПРЕОБРАЗОВАТЕЛЯ С АКТИВНЫМ И РЕАКТИВНЫМ ДИСКАМИ В МАГНИТНОЙ СИСТЕМЕ
- •ПРОГРАММА ВЫЯВЛЕНИЯ ФАКТОРОВ РИСКА РАКА МОЛОЧНОЙ ЖЕЛЕЗЫ С ИСПОЛЬЗОВАНИЕМ МЕТОДА МЕТА-АНАЛИЗА
- •ИССЛЕДОВАНИЕ ВОЗМОЖНОСТИ ИСПОЛЬЗОВАНИЯ МЕТОДА ФОТОМЕТРИРОВАНИЯ КАПЕЛЬНЫХ ПРОБ ДЛЯ ОЦЕНКИ АГРЕГАЦИОННЫХ СВОЙСТВ КЛЕТОК КРОВИ
- •ИСПОЛЬЗОВАНИЕ МИКРОВОЛНОВОЙ РАДИОТЕРМОМЕТРИИ В ДИАГНОСТИКЕ РАКА МОЛОЧНОЙ ЖЕЛЕЗЫ
- •УСТАНОВКА ДЛЯ ОПРЕДЕЛЕНИЯ ГИДРОДИНАМИЧЕСКИХ ХАРАКТЕРИСТИК КЛАПАННЫХ ЗАМЕНИТЕЛЕЙ, КАК ПОКАЗАТЕЛЕЙ КАЧЕСТВА И ПРИГОДНОСТИ ДЛЯ КАРДИОХИРУРГИИ
- •Введение
- •ЭКОНОМИЧНЫЙ И ЭКОНОМНЫЙ УМЗЧ 2×200Вт С БЛОКОМ ПИТАНИЯ
- •Мариненко А.В.
- •Благодарности
- •Компонента
- •МЕТОДИКА ОБРАБОТКИ КАРТИН ИНТЕРФЕРЕНЦИОННЫХ ПОЛОС
- •ЛИТЕРАТУРА:
- •Описание процесса моделирования
- •Вывод
- •Благодарности
- •ИСПОЛЬЗОВАНИЕ КОМПЬЮТЕРНОГО МОДЕЛИРОВАНИЯ ПРИ ИССЛЕДОВАНИИ СПОСОБА КОМПЕНСАЦИИ ДЕЙСТВИЯ ВИБРАЦИИ
- •НА ГИРОМАЯТНИК
- •Перспективы
- •Экспериментальная часть
- •Заключение
- •Рисунок 3. Результаты моделирования работы системы
- •ЛИТЕРАТУРА:
- •СКОРОСТНОЙ ЭФФЕКТ В ВИХРЕТОКОВОМ КОНТРОЛЕ
- •Введение
- •Благодарности
- •ЛИТЕРАТУРА:
- •E-mail: yuyug@npi.tpu.ru
- •Наименование параметра
- •Полоса
- •частот, Гц
- •Результаты и обсуждение
- •ЛИТЕРАТУРА:
- •ЛИТЕРАТУРА:
- •Тогда энергия, переданная упругому элементу, согласно (2) будет равна:
- •ПРОБЛЕМА ИССЛЕДОВАНИЯ ТРЕХЗВЕННЫХ МЕХАНИЗМОВ
- •ЛИТЕРАТУРА:
- •420066, г. Казань, Красносельская ул., 51
- •E-mail: BakirovAR@rambler.ru
- •420066, г. Казань, Красносельская ул., 51
- •E-mail: BakirovAR@rambler.ru
- •Введение
- •Выводы
- •Выводы
- •ОПТИМИЗАЦИЯ РЕЖИМОВ ЭКСПЛУАТАЦИИ УСТАНОВОК ТИПА УЭЦН С ПЧ
- •ЦИФРОВАЯ ЛАБОРАТОРИЯ ЭЛЕКТРОМЕХАНИКА
- •ЭЛЕКТРОМАГНИТНЫЙ МОМЕНТ В ИНДУКЦИОННЫХ ДВИГАТЕЛЯХ
- •Материал и методы исследования
- •Заключение и некоторые перспективы
- •ЛИТЕРАТУРА:

Современные техника и технологии 2007
Кроме того, мост с термокомпенсационным термистором, также может выйти из состояния баланса под воздействием окружающей температуры. В блок АЦП будут поданы два напряжения пропорциональные нагреву каждого из термисторов и преобразованы в цифровые коды. Далее для сведения к минимуму воздействия окружающей температуры, программно будет вычислена разница между напряжением снятым с измерительного моста и термокомпенсационного. Теперь осталось вывести соответствующий результат на жидкокристал-лический индикатор. Процесс аналого-цифрового преобразования, вычисления соответствующего результата и вывода на жидкокристаллический индикатор циклически повторяется, поэтому выводимый результат постоянно обновляется в реальном времени.
Изначально планируется оснастить прибор только самыми элементарными функциями. С помощью четырех кнопок будет осуществляться все управление. Будет присутствовать кнопка «Сброс», позволяющая выполнить аппаратный сброс микроконтроллера и запустить программу сначала. С помощью кнопки «Память» можно будет остановить процесс измерения и отобразить на экране жидкокристаллического индикатора последнее измеренное значение мощности СВЧ излучения. В процессе работы прибора может случится ситуация, когда мосты незначительно выйдут из состояния баланса, например, вследствие погрешности регулировочных резисторов. В этом случае на экране индикатора будет отображаться число отличное от нуля. Чтобы скорректировать показания, прибор оснащен
двумя кнопками тонкой настройки, благодаря которым, его можно настроить.
Данный измерительный прибор изначально проектировался с учетом дальнейшего усовер-шенствования. Поэтому, устройство спроекти-ровано на базе микроконтроллера и состоит из двух печатных плат, первичного преобразователя с двумя термисторами и жидкокристаллического индикатора. Все отдельные блоки устройства соединены проводами. На одной из плат находятся оба моста Уитстона и два усилителя, на другой блок управления и микроконтроллер. Модульный подход позволяет изменять конструкцию с минимальными затратами [3].
В качестве дальнейшего развития проекта измерителя мощности можно организовать подключение к персональному компьютеру через последовательный порт с целью сохранения результатов измерения, а также дистанционного управления прибором.
ЛИТЕРАТУРА:
17.Аш Ж. Датчики измерительных систем: В 2-х книгах Кн. 2. Пер. с франц. – М.:
Мир, 1992. – 480 с.
18.Преобразователи измерительные первичные М5-40 –М5-45 /Техническое описание и инструкции по эксплуатации:
ГВ4.681.016 ТО.- 1985. – 44c.
19.Преснухин Л.Н. Шахнов В.А. Конструирование электронных вычислительных машин и систем. Учеб. для вузов по спец. «ЭВМ». – М.: Высш. шк., 1986. - 512 с.
20.PIC16F8XX техническая документа-
ция. http://www.microchip.ru
МЕТОДИКА ПОВЕРКИ ИНДУКТИВНОГО ДЕЛИТЕЛЯ НАПРЯЖЕНИЯ КАЛИБРАТОРА НАПРЯЖЕНИЯ И ТОКА GTIU-98
Мартыновская Т.А., Ким В.Л.
Томский политехнический университет, Россия, г. Томск, пр. Ленина, 30 E-mail: kimval11@rambler.ru
Методика |
поверки разрабатывалась |
в |
предназначен для поверки компараторов пе- |
рамках договора по теме «Разработка ком- |
ременного тока и напряжения промышленной |
||
плекта документов для целей утверждения |
частоты 50 Гц. Калибратор состоит из трех |
||
типа калибратора напряжения и тока GTIU- |
узлов – входного ВУ, узла формирования тес- |
||
98» (договор 1-211/06к от 15.11.2006 г.). |
|
товых напряжений УФТН и узла формирова- |
|
Калибратор напряжения и тока GTIU-98 |
ния тестовых токов УФТТ. С помощью ВУ |
||
выпускается |
ООО «Микро-код» г. Львов |
и |
обеспечивается преобразование сетевого |
|
|
|
203 |

XIII Международная научно-практическая конференция «СОВРЕМЕННЫЕ ТЕХНИКА И ТЕХНОЛОГИИ»
напряжения 220 В в регулируемые напряжение (0 – 220) В, подаваемое на вход УФТН, и ток (1 – 5) А, поступающий на УФТТ.
Согласно [1, 2] для внесения калибратора в Госреестр средств измерений России документацию на средства измерений зарубежного производства необходимо привести в соответствие с требованиями российского законодательства.
В работе рассматриваются вопросы разработки одного из основных документов – методики поверки УФТН. Документ по поверке
.[3] содержит вводную часть и основную часть, состоящую из разделов:
-операции поверки;
-средства поверки;
-требования безопасности;
-условия поверки;
-подготовка к поверке;
-проведение поверки;
-обработка результатов измерений;
-оформление результатов поверки. Среди общих разделов документа по по-
верке специфичным для конкретного объекта испытания является подраздел «Определение метрологических характеристик» из раздела «Проведение поверки», так как именно здесь необходимо указывать наименование и метод поверки, схемы подключения, формулы и т. д.
При системном проектировании калибратора еще на стадии разработки структурных и принципиальных схем учитывались особенности применения калибратора в качестве рабочего эталона. В связи с этим в калибраторе УФТН был выполнен самоповеряющимся на основе метода опорного потенциала [4, 5]. УФТН представляет собой трехдекадный автотрансформаторный индуктивный делитель напряжения (ИДН), выполненный на общем тороидальном ферромагнитном сердечнике [6]. Коэффициент передачи ИДН Kn изменяется в пределах 0,001 – 1,100 с дискретностью 0,001. Вторая, третья и отдельная одновитковая обмотка используются в качестве опорных при поверке первой, второй и третьей декад соответственно. Относительные погрешности коэффициентов передач декад определяются по формуле
|
1 |
n |
|
|
n |
|
δKn = |
|
∑ 10 |
|
Ui − ∑ |
Ui , |
|
|
||||||
|
n Uвх i=1 |
|
|
i=1 |
|
(1)
Заметим, что Ui , и в том числе раз-
ностное напряжение U11 одиннадцатой
секции, измеряются посредством высокочувствительного дифференциального указателя
– вольтметра HP 34401A с разрешающей способностью 100 нВ.
В таблице приведены результаты расчетов погрешностей при Uвх = 12 В.
Таблица. Относительные погрешности коэффициентов передач декад δKn ×10-4 %
Декады ИДН
Коэффици- |
Пер- |
Вторая |
Третья |
ент переда- |
вая |
|
|
чи Kn |
|
|
|
0,1 |
-183,74 |
-0,99 |
-0,11 |
0,2 |
87,56 |
-1,10 |
-0,12 |
0,3 |
-29,80 |
-0,44 |
-0,05 |
0,4 |
-62,94 |
-0,10 |
-0,01 |
0,5 |
28,34 |
-0,17 |
-0,02 |
0,6 |
7,06 |
-0,13 |
-0,01 |
0,7 |
-33,54 |
-0,22 |
-0,02 |
0,8 |
18,49 |
-0,09 |
-0,01 |
0,9 |
22,33 |
-0,02 |
0,00 |
1,0 |
0,00 |
0,00 |
0,00 |
Формула (1) неприменима для определения погрешности одиннадцатой секции декады. Поэтому в работе предлагается новый алгоритм расчета погрешности максимального коэффициента передачи ИДН:
- вычисляют номинальное напряжение на первом отводе первой декады по формуле
U1н =Uвх /10 ;
- вычисляют опорное напряжение по формуле
Uоп =U1н (1+δK1 ) − U1 ,
где δK1 − относительная погрешность ко-
эффициента передачи первой декады на первом отводе, т.е. при Кn = 0,1;
- вычисляют напряжение на одиннадцатой секции первой декады по формуле
U11 =Uоп + U11 ;
- вычисляют относительную погрешность максимального коэффициента передачи первой декады ИДН по формуле
δK11 = U11U−U1н 100% . 1н
где – разностное напряжение между напряжением i-той секции (Ui) и напряжением опорной обмотки (U0);
− номер отвода декадной обмотки.
204
Предел допускаемой относительной погрешности коэффициента передачи ИДН определяется как суммарная погрешность ИДН для диапазона изменения Кп от 0,900 до 1,100 по формуле
δΣ =δ1max +0,1δ2 max +0,01δ3max +δпп ,

Современные техника и технологии 2007
где δ1max − максимальное значение из относительных погрешностей коэффициентов
передач первой декады δK9 и δK11 ; δ2 max − максимальное значение из относительных погрешностей коэффициентов передач вто-
рой декады; δ3max − максимальное значение из относительных погрешностей коэффициентов передач третьей декады; δпп − макси-
мальное значение из относительных погрешностей коэффициентов передач, обусловленных напряжением «прямого прохождения».
Для определения аддитивной составляющей погрешности УФТН, вызванной напряжением «прямого прохождения» − Uпп, выполняют следующие операции:
- устанавливают входное напряжение равное 12 В;
- устанавливают на УФТН коэффициент передачи, равный 0,000;
- измеряют вольтметром HP 34401A напряжение «прямого прохождения» Uпп с точностью до единиц мкВ;
- вычисляют относительную погрешность составляющей коэффициента передачи, обусловленной напряжением «прямого прохождения» по формуле
δпп = Uпп 100% ,
Uвх
где Uпп – напряжение «прямого прохождения».
- повторяют вышеуказанные операции для входных напряжений 60 В, 120 В и 200 В.
Для дальнейших расчетов учитывают наибольшее значение δпп .
Результаты поверки считают положительными, если предел допускаемой относительной погрешности УФТН не превышает
0,05 %.
Разработанная методика поверки вместе с другими документами, необходимыми для утверждения типа калибратора GTIU-98, пе-
реданы заказчику. В дальнейшем комплект документов и калибратор должны пройти процедуру утверждения типа на Украине, а затем по существующему межгосударственному соглашению – и в России. После внесения в Госреестр средств измерений России изготовитель − ООО «Микро-код» может экспортировать калибратор в РФ. Калибратор напряжения и тока GTIU-98 с метрологическими характеристиками мирового уровня найдет широкое применение при проведении метрологических работ в электроэнергетике, приборостроении и др. областях.
ЛИТЕРАТУРА:
1.ПР 50.2.009-94 «Государственная система обеспечения единства измерений. Порядок проведения испытаний и утверждения типа средств измерений» - М.: Госстандарт России, 1994.
2.ПМГ 06-2001 «Правила по межгосударственной стандартизации. Порядок признания результатов испытаний и утверждения типа, поверки, метрологической аттестации средств измерений» - М.: ИПК Изд-во стандартов, 2002.
3.РМГ 51-2002 «Государственная система обеспечения единства измерений. Документы на методики поверки средств измерений» - М.: ИПК Изд-во стандартов, 2003.
4.Ling Shan-Kang. The calibration of the inductive voltage divider by the method of reference potential. Proc. “Acta IMECO”, Budapest, 1968, v. 2, P. 507-517.
5.Ким В.Л., Ройтман М.С. Эталонный индуктивный делитель напряжения. Известия Томского политехнического университета. 2003, Т. 306, №5.
6.Мартыновская Т.А., Ким В.Л. Методика поверки калибратора напряжения и тока GTIU-98 // Качество - стратегия XXI века: Материалы XI международной научнопрактической конференции - Томск, 7 декабря
2006. - Томск : Изд.ТПУ, 2006. - c. 136.
205

XIII Международная научно-практическая конференция «СОВРЕМЕННЫЕ ТЕХНИКА И ТЕХНОЛОГИИ»
ТЕХНОЛОГИЯ ОБРАБОТКИ ПРОФИЛЯ ЗУБЧАТОГО ВЕНЦА ЖЁСТКОГО КОЛЕСА ВОЛНОВОЙ ПЕРЕДАЧИ С ПРОМЕЖУТОЧНЫМИ ТЕЛАМИ
Москалюк И. А., Эдличко А. А.
Томский политехнический университет, Россия, г. Томск, пр. Ленина, 30 E-mail: puladura@sibmaill.com
В последнее время активно развивается |
перемещает их по радиальным пазам |
||||||||||||||||
принципиально новый тип передач, в которых |
сепаратора. Тела качения, в свою очередь, |
||||||||||||||||
момент |
|
передаётся |
|
посредством |
воздействуют на рабочую поверхность зубьев |
||||||||||||
промежуточных тел качения (шариков, |
венца, что обеспечивает возникновение |
||||||||||||||||
роликов), |
|
|
взаимодействующих |
с |
радиальной |
силы, |
|
заставляющей |
|||||||||
периодическими |
|
|
дорожками |
качения |
поворачиваться несущий сепаратор, если |
||||||||||||
сопрягаемых деталей. Такие передачи |
заторможено |
колесо, |
|
и, |
наоборот, |
||||||||||||
принято называть волновыми передачами с |
поворачивается колесо, если заторможен |
||||||||||||||||
промежуточными |
телами. |
Эта |
передача |
сепаратор. В этой передаче используется |
|||||||||||||
отличается |
|
от |
|
традиционной |
волновой |
волновой принцип движения, где за один |
|||||||||||
передачи с гибким звеном тем, что в ней нет |
оборот входного звена (генератора) выходное |
||||||||||||||||
деформируемых звеньев. Все звенья |
звено (сепаратор) поворачивается на один |
||||||||||||||||
передачи представляют собой жесткие тела, |
зуб. Устанавливая на одном генераторе |
||||||||||||||||
выполненные с высокой точностью. При |
последовательно два или три ряда тел |
||||||||||||||||
работе |
передачи |
между |
звеньями |
качения можно почти кратно повышать |
|||||||||||||
практически отсутствует трение скольжения, |
несущую способность передачи. |
|
|||||||||||||||
а присутствует трение качения. |
|
|
К достоинствам данного вида передач |
||||||||||||||
Волновая |
передача с |
промежуточными |
можно отнести следующее: |
|
|
|
|||||||||||
телами качения состоит из генератора, |
• высокие КПД и несущую способность; |
||||||||||||||||
выполненного |
|
|
в |
виде |
|
эксцентрика, |
• |
точность; |
|
|
|
|
|
|
|||
вращающегося вокруг оси О1. На этой же оси |
• |
плавность |
хода |
и |
малые |
массо- |
|||||||||||
установлен |
|
несущий |
|
сепаратор |
с |
габаритные показатели. |
|
|
|
|
|||||||
радиальными пазами, в которых с |
Высокие требования |
предъявляемые к |
|||||||||||||||
возможностью |
радиального |
перемещения, |
точности и долговечности редуктора, |
||||||||||||||
размещены тела качения (шарики или |
вызывают дополнительные |
технологические |
|||||||||||||||
ролики). Эти тела качения постоянно |
сложности в процессе изготовления основных |
||||||||||||||||
соприкасаются |
с |
рабочими |
поверхностями |
деталей передач редуктора. |
|
|
|
||||||||||
зубьев венца, описанных совокупностью |
Одной из важнейших деталей волнового |
||||||||||||||||
укороченных гипоциклоид (Рисунок 1). |
|
редуктора с промежуточными телами качения |
|||||||||||||||
|
|
|
|
|
|
|
|
|
|
является зубчатое колесо (Рисунок 2). К нему |
|||||||
|
|
|
|
|
|
|
|
|
|
предъявляются следующие требования [1]: |
|||||||
|
|
|
|
|
|
|
|
|
|
21. твердость |
|
зубчатого |
венца |
61-63 |
|||
|
|
|
|
|
|
|
|
|
|
HRCэ; |
|
|
|
|
|
|
|
|
|
|
|
|
|
|
|
|
|
22. шероховатость рабочей |
поверхности |
||||||
|
|
|
|
|
|
|
|
|
|
зубчатого венца не хуже 0,6 мкм Rа; |
|
||||||
|
|
|
|
|
|
|
|
|
|
23. отклонение |
от |
|
теоретического |
||||
|
|
|
|
|
|
|
|
|
|
профиля не должно превышать 4 мкм. |
|
Рисунок 1
При вращении генератора он своей поверхностью действует на тела качения и
206

Современные техника и технологии 2007
|
|
|
|
|
|
|
|
|
Под воздействием высоких температур в |
|||||||
|
|
|
|
|
|
|
|
|
зоне разряда происходят нагрев, расплав, и |
|||||||
|
|
|
|
|
|
|
|
|
частичное |
испарение |
металла. |
Для |
||||
|
|
|
|
|
|
|
|
|
получения высоких температур в зоне |
|||||||
|
|
|
|
|
|
|
|
|
разряда необходима большая концентрация |
|||||||
|
|
|
|
|
|
|
|
|
энергии. Для достижения этой цели |
|||||||
|
|
|
|
|
|
|
|
|
используется генератор импульсов. Процесс |
|||||||
|
|
|
|
|
|
|
|
|
ЭЭО происходит в рабочей жидкости, которая |
|||||||
|
|
|
|
|
|
|
|
|
заполняет пространство между электродами; |
|||||||
|
|
|
|
|
|
|
|
|
при этом один из электродов - заготовка, а |
|||||||
|
|
|
|
|
|
|
|
|
другой электрод-инструмент. |
|
|
|||||
|
|
|
|
|
|
|
|
|
Недостатками метода электроэрозионной |
|||||||
|
|
|
|
|
|
|
|
|
проволочной вырезки являются: |
|
|
|||||
|
|
|
|
|
|
|
|
|
• большая трудоёмкость (до 10 часов |
|||||||
|
|
|
Рисунок 2 |
|
|
|
на одну деталь); |
|
|
|
|
|
||||
|
|
|
|
|
|
• |
высокая стоимость оборудования; |
|
||||||||
Вышеприведенные |
требования |
не |
• |
высокая |
|
|
квалификация |
|||||||||
обслуживающего персонала. |
|
|
||||||||||||||
позволяют |
применять |
известные |
методы |
Технологические проблемы, связанные с |
||||||||||||
обработки, например фрезерование методом |
обработкой зубчатого венца на настоящий |
|||||||||||||||
обкатки. |
|
|
|
|
|
|
|
момент, препятствуют широкому внедрению в |
||||||||
Одним |
из |
применяемых |
методов |
серийное производство редукторов на базе |
||||||||||||
обработки зубчатого венца является метод, |
волновых |
передач |
с |
промежуточными |
||||||||||||
включающий следующие этапы[2]: |
|
|
телами. |
|
|
|
|
|
|
|||||||
• предварительная |
обработка |
профиля |
Для широкого внедрения данного вида |
|||||||||||||
фрезерованием на координатно-расточном |
передач в производство и технику |
|||||||||||||||
станке; |
|
|
|
|
|
|
|
|
необходимо совершенствовать технологию и |
|||||||
• получистовая |
|
обработка |
|
на |
методы получения профиля зубчатого венца. |
|||||||||||
координатно-шлифовальном станке; |
|
|
Основными направлениями решения этой |
|||||||||||||
• чистовая обработка проводится методом |
задачи можно определить следующие: |
|
||||||||||||||
пластической деформации-раскаткой. |
|
• |
использование |
|
производительных |
|||||||||||
К недостаткам данного метода можно |
процессов резания металлов; |
|
|
|||||||||||||
отнести: |
|
|
|
|
|
|
|
• |
модернизация и доработка серийных |
|||||||
• проблемы с обработкой сопряжений и |
металлорежущих станков. |
|
|
|
||||||||||||
малых радиусов; |
|
|
|
|
|
|
|
|
|
|
|
|
|
|||
• |
требуется |
изготовление |
сложных |
ЛИТЕРАТУРА: |
|
|
|
|
|
|||||||
приспособлений |
(для |
установки |
при |
1. Хохряков Б.Г. Вырезка сложных |
||||||||||||
обработке колеса шариковой передачи и |
деталей |
(волновых |
|
редукторов |
с |
|||||||||||
приспособление для раскатки зубьев колеса); |
промежуточными |
|
звеньями) |
|
на |
|||||||||||
• большие временные затраты на |
электроэрозионных станках. Трудный опыт |
|||||||||||||||
обработку и высокая стоимость; |
|
|
внедрения. // Двигатель -2001- №4. |
|
|
|||||||||||
• |
метод |
применим для |
опытного и |
2. Янгулов В. С. Редуктор системы |
||||||||||||
мелкосерийного производства. |
|
|
|
автоматического регулирования повышенной |
||||||||||||
На сегодняшний день одним из наиболее |
долговечности. |
- |
|
Томск. |
Томский |
|||||||||||
продуктивных |
методов |
получения |
профиля |
политехнический институт, 1984г. -217 с. |
|
|||||||||||
зубчатого |
венца |
является |
|
метод |
3. Беляев А. Е. Механические передачи с |
|||||||||||
электроэрозионной проволочной вырезки. |
шариковыми промежуточными телами / А. Е. |
|||||||||||||||
Электроэрозионная |
|
обработка |
Беляев; |
Томский |
|
политехнический |
||||||||||
заключается в изменении формы, размеров, |
университет. — Томск: Изд-во ТПУ, 1992. - |
|||||||||||||||
шероховатости |
и |
свойств |
поверхности |
231 с. |
|
|
|
|
|
|
|
|||||
заготовки |
под |
воздействием |
электрических |
4. http://www.nposibmach.ru/gear.html. |
|
|||||||||||
разрядов в результате электрической эрозии |
|
|
|
|
|
|
|
|
(ГОСТ 25331-82).
207

XIII Международная научно-практическая конференция «СОВРЕМЕННЫЕ ТЕХНИКА И ТЕХНОЛОГИИ»
ПРИМЕНЕНИЕ СОВРЕМЕННЫХ ИНФОРМАЦИОННЫХ ТЕХНОЛОГИЙ В МАГНИТОСТРИКЦИОННЫХ ПРЕОБРАЗОВАТЕЛЯХ ПЕРЕМЕЩЕНИЙ
Назаров А.Ш., Ясовеев В.Х.
Уфимский Государственный Авиационный Технический Университет, г. Уфа, ул. К. Маркса 12
E-mail: anv.naz@mail.ru
Повышение точности и помехоустойчивости МПП является одним из основных направлений их совершенствования. Необходимость оценки и подавления погрешностей вносимых различного вида помехами, присутствующими во входном сигнале, а также внутренними шумами, возникающими в тракте преобразования цифрового прибора, в последнее время стала весьма актуальной, в связи с растущими требованиями к точности МПП, а также повышением уровня помех.
Суть предлагаемого метода компенсации различного рода помех и акустических шумов, возникающих в УЗ волноводе, заключается во введении в структуру МПП аппаратных средств и программных алгоритмов, реализующих современные алгоритмы цифровой обработки сигналов ЦОС.
Реализовать функции цифровой фильтрации информационного сигнала без ощутимых потерь в быстродействии и весогабаритных характеристиках преобразователя на сегодняшний день позволяют высокопроизводительные микропроцессоры с ядром ARM, специализированные микропроцессоры цифровой обработки сигналов DSP(Didgital Signal
Processor) микропроцессоры – цифровые сигнальные процессоры, а также ПЛМ ПЛИСпрограммируемые логические матрицы.
Применение ЦОС технологий в МПП позволит осуществить следующие виды ЦО сигнала с первичного магнитострикционного преобразователя:
Спектральный анализ включающий в себя алгоритмы ДФП, БФП, а также Вейвлет анализ разработанный для решения задач, эффективность решения которых при использовании традиционного анализа Фурье невысока.
Цифровая фильтрация: КИХ или БИХ фильтр ЦФ с фиксированными коэффициентами ЦФ, а также адаптивный фильтр (компенсатор помех). Современные алгоритмы цифровой фильтрации позволяют осуществить фильтрацию гармонических помех, широкополосных шумов, нестационарных импульсных помех, приводящих к ложным срабатываниям, а следовательно к неправильной работе МПП.
Структурная схема подобного МПП, в соответствии с изложенной выше концепцией представлена на Рис. 1.
208

Современные техника и технологии 2007
Рис.1 Универсальная структура МПП реализующая ЦО информационного сигнала МПП. (МК-микроконтроллер, СУФ-схема управления и формирования).
Устройство работает следующим обра- |
ние которого необходимо определить, до |
|||
зом: управляющее устройство, в качестве |
точки максимального его перемещения (7). |
|||
которого может быть применен либо микро- |
Далее ультразвуковая волна, распро- |
|||
процессор МК, либо ПЛИС выдает сигнал на |
страняясь вдоль волновода вправо, достига- |
|||
схему управления и формирования импульса |
ет свободного (жестко защемленного) конца |
|||
записи СУФ, в этот же момент запускается |
ФВ и, отражаясь от него, изменяет направ- |
|||
интегрированный в МК счетчик времени из- |
ление движения на противоположное. При |
|||
мерительного интервала. |
прохождении ультразвуковой |
волны около |
||
Сформированный СУФ импульс напря- |
магнита (6) в обмотке катушки считывания |
|||
жения поступает в катушку возбужде- |
(2) вновь наведется ЭДС индукции. Мо- |
|||
ния(1), в которой под его действием |
дуль измерения перемещения производит |
|||
возникает переменное магнитное поле, |
фиксацию |
времени второго импульса счи- |
||
которое совместно с подмагничивающим |
тывания. Это время пропорционально рас- |
|||
полем постоянного магнита(5), возбу- |
стоянию 2Lх |
от контролируемого объек- |
||
ждает ультразвуковую волну в ферромаг- |
та(10) до точки отсчета (8) |
|
||
нитном волноводе (ФВ) (3), которая со ско- |
Таким образом, расчет перемещения |
|||
ростью С≈3000м/с (где С-скорость распро- |
сводится к |
необходимости |
определения |
|
странения крутильных колебаний в волно- |
расстояния Lх. |
|
|
|
воде из прецизионных сплавов 44НХМТ, |
Фиксация времени наведенных импуль- |
|||
42НХТЮ) распространяется по нему вдоль |
сов напряжения осуществляется следующим |
|||
катушки считывания(2) . При прохождении |
образом. Поступивший с катушки считывания |
|||
ультразвуковой волны около магнита (6) же- |
сигнал фильтруется, а также усиливается в |
|||
стко прикрепленного к контролируемому |
блоке аналогового нормирования импульсов |
|||
объекту, вследствие изменения магнитного |
считывания |
до |
соответствующего высокого |
|
потока с частотой ультразвуковых колеба- |
уровня (не превышающего уровня опорного |
|||
ний в обмотке катушки считывания (2) на- |
напряжения АЦП). Далее непрерывный ин- |
|||
ведется ЭДС индукции. Модуль измерения |
формационный |
сигнал x(t) |
поступает на |
|
перемещения производит фиксацию вре- |
вход быстродействующего АЦП(скорость |
|||
мени первого импульса считывания. Это |
преобразования которого должна состав- |
|||
время пропорционально расстоянию La от |
лять не менее 5000 кВыб/с), с помощью ко- |
|||
контролируемого объекта(10), перемеще- |
торого он преобразуется в дискретную по- |
|||
|
|
|
|
209 |

XIII Международная научно-практическая конференция «СОВРЕМЕННЫЕ ТЕХНИКА И ТЕХНОЛОГИИ»
следовательность отсчетов xn с шагом дис- |
вибрации, |
воздействия электромагнитных |
|||||||
кретизации τ [2]. |
полей, |
предъявляет повышенные требова- |
|||||||
Далее сформированная дискретная по- |
ния к их точности, надежности и целостности. |
||||||||
следовательность передается в адаптивный |
Поэтому в структуру МПП введен дополни- |
||||||||
ЦФ реализованный на базе ПЛМ ПЛИС [3], |
тельный |
|
управляющий |
|
|
ор- |
|||
либо на базе DSP процессора. |
ган(высокопроизводительный микроконтрол- |
||||||||
Затем отфильтрованный сигнал переда- |
лер или ПЛМ ПЛИС), который позволит взять |
||||||||
ется в управляющее устройство для даль- |
на себя такие функции |
как управление сис- |
|||||||
нейшей обработки(локализация и поиск экс- |
темой, контроль отказов и целостности при- |
||||||||
тремума для более точного определения из- |
бора |
повышение точности, непрерывность |
|||||||
мерительного интервала [2]) и вычисления |
измерений, а также повысить устойчивость к |
||||||||
текущего положения, скорости и ускорения |
сбоям во время слежения за объектом, пе- |
||||||||
контролируемого объекта. Также при помощи |
ремещение которого необходимо контроли- |
||||||||
устройства управления можно осуществлять |
ровать. |
|
|
|
|
|
|
|
|
высокоскоростной обмен данными с РС, при |
Подобный |
подход |
при проектировании |
||||||
помощи которого все основные информатив- |
позволит существенно повысить такие пара- |
||||||||
ные параметры датчика могут быть визуаль- |
метры МПП как помехоустойчивость, точ- |
||||||||
но контролироваться пользователем в режи- |
ность, отношение сигнал/шум, чувствитель- |
||||||||
ме реального времени. |
ность, целостность и надежность. |
|
|
|
|||||
По сравнению с фильтрами, выполнен- |
|
|
|
|
|
|
|
|
|
ными на дискретных и аналоговых элемен- |
ЛИТЕРАТУРА: |
|
|
|
|
|
|||
тах, цифровые фильтры более просты, на- |
1. |
Э. |
Айфичер |
«Цифровая обработка |
|||||
дежны и не нуждаются в настройке. Кроме |
сигналов: практический подход, 2-е издание» |
||||||||
очевидных преимуществ устранения ошибок |
Пер. с ангд. – М.: Издательский дом «Виль- |
||||||||
в фильтре, связанных с флуктуациями пара- |
ямс», 2004. – 992 с. : ил.-Парал. тит. англ. |
|
|||||||
метров пассивных компонентов во времени и |
2. Вдовин А. Ю., Радов М. |
Ю. |
Метод |
||||||
по температуре, дрейфом ОУ (в активных |
уменьшения случайной погрешности магни- |
||||||||
фильтрах) и т.д., цифровые фильтры способ- |
тострикционных преобразователей |
переме- |
|||||||
ны удовлетворять таким техническим требо- |
щений |
|
на |
основе |
DSP |
технологий |
|||
ваниям по своим параметрам, которые, в |
//Электронный научный журнал «ИССЛЕДО- |
||||||||
лучшем случае, было бы чрезвычайно трудно |
ВАНО В РОССИИ» http://zhurnal.ape.relarn.ru |
||||||||
или даже невозможно достичь в аналоговом |
3. Губанов Д.А., Стешенко В.Б, Храпов |
||||||||
исполнении, они имеют практически прямо- |
В.Ю., Шипулин С.Н. |
Перспективы реализа- |
|||||||
угольную амплитудно-частотную характери- |
ции алгоритмов цифровой фильтрации на |
||||||||
стику, что приближает их к идеальному |
основе |
|
ПЛИС |
фирмы |
“Altera” |
- |
|||
фильтру. Кроме того, характеристики цифро- |
mail@mgamma.msk.su |
|
|
|
|
||||
вого фильтра могут быть легко изменены |
4. С.В. Кононенко Обработка измери- |
||||||||
программно. |
тельной информаци преобразователей по- |
||||||||
Возможность применения МПП в экстре- |
ложения // Датчики и системы 2002 № 5. |
|
|||||||
мальных условиях - высокой температуры, |
|
|
|
|
|
|
|
|
|
МАГНИТОМЕТРИЧЕСКАЯ СИСТЕМА ДЛЯ ИЗУЧЕНИЯ ИМПУЛЬСНЫХ МАГНИТНЫХ ПОЛЕЙ
Нарыжнова З.В., Казаков В.Ю.
Томский политехнический университет, Россия, г. Томск, пр. Ленина, 30 E-mail: pjz@mail.ru
Разрабатываемая измерительная система предназначена для исследования характеристик ускоряющего магнитного поля бетатрона.
Измеряется проекция Bn вектора магнитной индукции B на некоторую ось n, которая
связана с катушкой первичного преобразователя:
Bn = (B*n0),
где n0 – единичный вектор, направленный вдоль оси n катушки. Далее предполагается, что катушка первичного магнитного преобра-
210

Современные техника и технологии 2007
зователя зафиксирована в пространстве и не меняет своей ориентации (n0 = const). Переменное магнитное поле имеет характер периодических импульсов частотой порядка 400 Гц. Величина магнитной индукции |Bn| достигает значения 0.1 Т, что соответствует магнитным полям средней силы [1].
Структурная схема магнитометрической системы представлена на рис. 1.
Рис. 1 Измерительная система состоит из ана-
логовой и цифровой частей. Имеется 11 аналоговых каналов, которые соответствуют вложенным виткам плоской катушки. Каждому каналу соответствует своя передаточная функция.
Аналоговая часть системы
В качестве первичного используется пассивный индукционный магнитометрический преобразователь, основанный на использовании явления электромагнитной индукции. В контуре, пронизываемым потоком магнитной индукции Ф(t) возникает эдс электромагнитной индукции e(t):
e(t) = − S w |
d Bср |
(t) |
, |
(1) |
dt |
|
|||
|
|
|
|
где S – площадь витка, w – количество витков, Bср (t) – средняя магнитная индукция по площади витка.
Рис. 2 На рис. 2 приведена структурная схема
аналоговой части магнитометрической системы. Здесь передаточная функция W1 – соответствует закону электромагнитной индукции (1) и имеет вид: W1 = - S w p.
Рис.3 В соответствии с эквивалентной схемой
катушки (рис.3) W2 имеет вид:
W2 = |
1 |
(2) |
1 + R C p + L C p2 |
где R – активное сопротивление катушки, L – индуктивность катушки, C – собственная емкость катушки. W3 – соответствует делителю с коэффициентом 1÷20 и имеет вид: W3=0.05. Результирующая передаточная функция аналогового канала имеет вид: W =
W1W2 W3, т.е.
|
−K p |
|
|
(3) |
|
W = |
1 + R C p + L C p2 , |
K = 0.05 S w |
|||
|
Цифровая часть системы
В состав входит: АЦП, плата управления, ПК (персональный компьютер).
Использован АЦП – AD 7484(Analog Devices). Основные характеристики АЦП: наибольшая частота дискретизации 3МГц; ширина полосы пропускания до 40МГц; диапазон входного сигнала от 0 до 2.5В; 14-разрядный; малошумящий; последовательного приближения [2].
АЦП и схемы обрамления расположены на плате EVAL-AD7484CB (Analog Devices).
Данная плата содержит 96 – контактный разъем [3].
Плата АЦП сопрягается с платой управления, Eval-Control Brd2 в состав которой входит: управляемый источник питания; DSP процессор типа ADSP-2189M; ОЗУ объемом 112 16-ти разрядных килослов. Данная плата обеспечивает обмен данными со скоростью 6 мегавыборок/с с платой АЦП и 32 кбайт/с с ПК. Для обмена с ПК используется двунаправленный принтерный порт (параллельный интерфейс Bi-Di). DSP процессор работает под управлением фирменного программного модуля ПО1 (рис.1), обеспечивающего управление АЦП и обмен данными и командами с ПК [4].
Используется ПК в стандартной комплектации с двунаправленным параллельным портом.
Программное обеспечение
Программа на ПК (ПО2) представляет собой набор независимых модулей (рис. 4), интегрированных в среде LabVEIW 6.0 (National Instruments).
211

XIII Международная научно-практическая конференция «СОВРЕМЕННЫЕ ТЕХНИКА И ТЕХНОЛОГИИ»
Частота импульсов напряжения на витке 400Гц, максимальное напряжение 2.5В.
На рис. 6 представлен график распределения Bn(r,t) при t=30 мс от начала импульса.
Рис. 4 Здесь блок 1 – интерфейс пользователя.
2 – блок записи сигнала с витка: 2а – подсистема настройки АЦП и управления сбором данных; 2б – драйвер параллельного порта. Результирующий сигнал записывается в файл на диске. Блок 3 – блок обработки результатов измерений: 3а – блок интегрирования и синхронизации сигнала; 3б – блок расчета распределения Bn(r,t) по радиусу зоны измерения. Блок 4 – блок настройки параметров магнитометрической системы.
Результаты
На данном этапе магнитометрическая система находится в стадии калибровки и пробных испытаний. На рис. 5 представлена типичная осциллограмма напряжения на витке с номером 9. Данный виток имеет радиус
65мм.
Рис. 5
Рис. 6. Из графика видно, что поле спадает по радиусу зоны измерения на 0.2Т.
Заключение
В данной работе представлены – описание структурной схемы магнитометрической системы; методы расчета измерительных преобразований для аналоговой части системы; структурная схема программного обеспечения магнитометрической системы, а также представлены некоторые результаты измерений. Предполагается дальнейшая работа по калибровке и оптимизации описанной выше измерительной системы.
ЛИТЕРАТУРЫ:
1.Панин В.В. Практическая магнитометрия; Измерения магнитных полей и электрических токов с помощью пассивных индукционных и холловских преобразователей /В.В. Панин, Б.М. Степанов. – М.: Машиностроение, 1978 . - 111 с.
2.Data Sheet.-AD7484.- Analog Devices,2002.
3.Technical Note.-EVAL-AD7484CB. - Analog Devices,2002.
4.Data Sheet.-Evaluation Board Controller. - Analog Devices,2002.
5.Тревис Дж. LabVieW для всех. - М.: ДМК Пресс,2005.
212

Современные техника и технологии 2007
ПЕРВИЧНЫЙПРЕОБРАЗОВАТЕЛЬБЕСКОНТАКТНОЙСИСТЕМЫ ИЗМЕРЕНИЙПАРАМЕТРОВИМПУЛЬСОВБОЛЬШИХТОКОВ
НаталиноваН. М.
Томскийполитехническийуниверситет, Россия, г.Томск, пр. Ленина, 30 E-mail: natalinova@tpu.ru
Известно много способов измерения тока, в зависимости от поставленной измерительной задачи, требования, предъявляемые к датчикам, могут быть различными. Среди известных на сегодняшний день методов для измерения переменных токов большой величины наиболее широко применяются следующие, в основе которых лежат: трансформаторы тока, шунты переменного тока, а также датчики Холла [1].
Датчики тока на основе трансформаторов тока могут использоваться только в цепях переменного тока. Недостатком таких датчиков является наличие гистерезиса, вследствие насыщения ферромагнитного сердечника, что приводит к снижению точностиДостоинствомизмерений. резистивных датчиков является их линейность и дешевизна, однако, при измерении больших токов наблюдается саморазогрев и термоЭДС, что приводит к изменению параметров датчика и соответственно к снижению точности измерения.
Измерительные шунты являются разновидностью резистивных датчиков, этот датчик представляет собой четырехконтактный резистор с двумя токовыми и двумя потенциальными контактами. Известно очень много вариантов конструктивного оформления шунтов. Основное затруднение при создании шунтов для измерения переменных токов величиной свыше единиц и десятков килоампер состоит в необходимости рассеяния тепловой мощности, выделяемой шунтом, при протекании токов большой величины, а также уменьшения индуктивной составляющей погрешности измерения тока.
Шунты переменного тока в настоящее время серийно не выпускаются. Отсутствие серийного производства обусловливает необходимость разработки и изготовления единичных вариантов шунтов переменного тока, предназначенных для решения частных измерительных задач. Для измерения тока источника питания прецизионного аппарата для точечной сварки на кафедре компьютерных измерительных систем и метрологии была разработана система измерения больших токов «СИБТ», первичным преобразователем которой является шунт из манганина коаксиальной конструкции, расчет которого приведен в [2]. Достоинством шунтов такой конст-
рукции является то, что они обладают очень малой индуктивностью.
Однако резистивные шунты являются контактными датчиками, поэтому их использование приводит к необходимости разрыва цепи. Анализ данных показал, что в ряде случаев разорвать цепь, для того чтобы измерить ток нецелесообразно или даже невозможно. Поэтому большое распространение в области измерения токов получил бесконтактный способ с помощью датчиков Холла. Измерение тока с помощью датчиков тока может осуществляться двумя способами [3]. Первый способ основан на прямом измерении напряженности магнитного поля, создаваемого протекающим током. Этот принцип работы датчика показан на рисунке 1.
Рисунок 1 – Способ прямого измерения тока с помощью датчиков Холла.
Измеряемый ток Iизм течет по проводнику, вокруг которого образуется магнитное поле, пропорциональное величине тока. В кольцевом магнитопроводе, охватывающим данный проводник с током, сделан пропил, в который вставлен датчик Холла. Выходное напряжение датчика Холла прямопропорционально измеряемому току Iизм.
Рисунок 2 – Компенсационный способ измерения тока на основе датчика Холла
213

XIII Международная научно-практическая конференция «СОВРЕМЕННЫЕ ТЕХНИКА И ТЕХНОЛОГИИ»
Второй способ измерения тока используют для измерения больших токов, этот способ подразумевает наличие специальной компенсационной обмотки на кольце магнитопровода (рис.2). Напряжение с датчика усиливается и подается на компенсирующую обмотку, магнитный поток которой стремится компенсировать магнитный поток магнитопровода до нуля. На выходе получаем ток компенсирующей обмотки. Измеряемый и компенсирующий токи находятся в соотношении:
Iизм = Ik Nk
(1),
где Iизм, Ik - измеряемый и компенсирующий токи соответственно, Nk - количество
витков компенсирующей обмотки. Из (1) видно, что для компенсации магнитного поля, образующегося током величиной 50 кА, компенсирующий ток должен быть равен 50/Nk кА. Следует заметить, что компенсационный способ оправдан для измерения токов величиной до 1 кА, т.к. увеличение числа витков компенсационной обмотки приводит к увеличению массы и габаритов датчика.
На кафедре компьютерных измерительных систем и метрологии томского политехнического университета предложена конструкция устройства для измерения параметров импульсов больших токов на основе датчиков Холла, позволяющая измерять токи порядка десятков кА (рис.3). Особенностью данной конструкции является то, что компенсация магнитного потока производится не на всем участке магнитопровода, а на ограниченном участке с магнитным сопротивлением, меньшим, чем сопротивление всей магнитной цепи.
Рисунок 3 – Конструкция датчика
Датчик Холла помещают в зазор магнитопровода, на этом участке магнитный поток раздваивается, поэтому величина магнитной индукции первого контура равна:
B1 = |
1 |
μμ0 |
Iизм (при а>>b) |
|
2 |
a |
|
||
где |
μ, μ0 |
- магнитная проницаемость ма- |
териала магнитопровода и магнитная прони-
цаемость вакуума соответственно. Величина второго контура магнитной индукции равна:
B2 = 12 μμ0 Ibk
(3)
Так как В1=В2, получаем, что при таком расположении зазоров a и b ток компенсационной обмотки Ik в a/b раз меньше измеряемого тока Iизм. Поэтому компенсационный ток будет равен:
Ik = Iизм Nkb a
(4)
С целью создания устройства для измерения тока была рассчитана конструкция датчика.
Исходные данные. Максимальный изме-
ряемый ток Iизм max=50 кА, значение выходного компенсационного тока при измерении мак-
симального тока Iк =1 А, количество витков катушки Nk=1000. Из выражения (4) получаем соотношение зазоров: a:b=50:1. В реализованном датчике a=50 мм, b=1 мм. Такая конструкция позволила в несколько раз уменьшить массу и габариты датчика для измерения больших токов.
На рисунке 4 приведена структурная схема датчика.
Рисунок 4 – Структурная схема датчика
Сигнал с датчика Холла подается на инструментальный усилитель, коэффициент усиления которого равен 1000. Далее сигнал поступает на усилитель мощности с коэффициентом усиления 10. Затем к усилителю мощности подключается компенсационная обмотка, ток компенсационной обмотки Iк пройдя через нагрузку, преобразовывается в напряжение, поэтому, в качестве выходного сигнала получаем напряжение Uвых .
ЛИТЕРАТУРА:
1 Данилов А. Современные промышленные датчики тока // Современная электрони-
ка. 2004. №10.
2. Наталинова Н. Расчет первичного пре-
образователя системы измерений токов
(2)
СИБТ //НАУКА, ТЕХНОЛОГИИ, ИННОВАЦИИ: Материалы всероссийской научной конференции молодых ученых в 7-и частях. - Ново-
214

|
|
Современные техника и технологии 2007 |
сибирск, 7-10 декабря 2006. - Новосибирск: |
4 Романенко Д. Датчики тока на основе |
|
НГТУ, 2006 - т. 2. - c. 42-43. |
эффекта Холла // Схемотехника. 2003. №6. |
|
|
3 Алдохин А. Компенсационный датчик |
|
тока с магнитным шунтом // Радио. 2002. №3. |
|
МАТЕМАТИЧЕСКОЕ МОДЕЛИРОВАНИЕ ЭЛЕКТРОЕМКОСТНОГО ПРЕОБРАЗОВАТЕЛЯ ПОТОЧНОГО ВЛАГОМЕРА НЕФТИ
Нефедова Е.С.
Самарский государственный технический университет, Россия, г. Самара, ул. Ново – Садовая, 10.
E-mail: nefedovaekaterina@rambler.ru
Электроемкостные преобразователи используют в диэлектрическом методе влагометрии, основанном на изменении диэлектрической проницаемости смеси «нефть – вода», связанной известной функциональной зависимостью с объемным содержанием воды. При этом водонефтяная эмульсия помещается в емкостной преобразователь, в котором измеряется емкость между двумя электродами. В нефтяных поточных влагомерах чаще всего применяют коаксиальные электроемкостные преобразователи, где первым электродом служит трубопровод, а потенциальный электрод выполнен в виде стержня
[1].
Возможны, однако, и другие конструктивные схемы электроемкостных преобразователей поточных влагомеров, выполненных, например, в виде плоских или сегментных электродов, определенным образом размещенных в сечении трубопровода [2].
Цель доклада – разработка математической модели электроемкостного преобразователя с двумя сегментными электродами цилиндрической формы.
Датчик – полый цилиндр радиуса «а», разрезанный по образующей на две половинки, разделенные небольшим зазором (Рис.1).
Рис.1. Датчик
Кэлектродам приложены потенциалы U1
иU2. тогда потенциал в любой точке внутри цилиндра определяется так:
|
U1 + U 2 |
|
U1 −U 2 |
∞ |
(−1)n−1 |
|
ρ |
2n−1 |
|
, (1) |
|
U = |
|
+ 2 |
|
∑ |
|
( |
|
) |
|
cos[(2n −1)Q] |
|
2 |
π |
2n −1 |
a |
|
|
||||||
|
|
|
|
n=1 |
|
|
|
|
|
|
|
где ρ и Q – цилиндрические координаты. Если U1 = - U2 = U0/2, то уравнение 1 име-
ет вид:
|
2U0 |
∞ |
(−1) |
n−1 |
|
ρ |
)2n−1 cos[(2n −1)Q] , |
U = |
∑ |
|
( |
||||
π |
2n −1 |
|
|||||
|
n=1 |
|
a |
||||
|
|
|
|
|
|
|
где U0 – напряжение приложенное к электрода.
Определим в общем виде измеряемую емкость С преобразователя, рабочий объем V которого заполнен неоднородной смесью с диэлектрической проницаемостью ε (М), зависящей от координаты точки М внутри объема.
Энергия электрического поля в контролируемом объеме V:
W = |
1 |
ε0 ∫ε(M )E |
2 |
(M )dVM = |
CU 2 |
, |
2 |
|
2 |
||||
|
|
V |
|
|
|
|
где ε (М) – напряженность электрического поля в точке М, U –приложенное напряжение.
Отсюда получим выражение для измеряемой емкости С.
|
ε0 |
∫ |
2 |
(2) |
C = |
|
ε(M )E (M )dVM , M V |
||
U 2 |
||||
|
|
V
Из уравнения (2) следует, что измеряемый сигнал – емкость С зависит от пространственных распределений диэлектрической проницаемости ε (М) смеси «нефть –вода», и напряженности электрического поля E(M) в рабочем объеме датчика. Объемное содержание влаги αв в водонефтяной эмульсии определяют по величине емкости С для датчи-
215

XIII Международная научно-практическая конференция «СОВРЕМЕННЫЕ ТЕХНИКА И ТЕХНОЛОГИИ»
ка с цилиндрическими и плоскими электродами соответственно:
Сц = |
2πε0 |
εэ(αв )l |
; Сп = |
ε0εэ(αв )d l |
, (3) |
|||
Cn |
Rn |
|
dn |
|||||
|
|
|
||||||
|
R0 |
|
|
|
||||
|
|
|
|
|
|
где Сц и Сn – измеряемые емкости цилиндрического и плоского конденсаторов, R0 и Rn
– радиусы внутреннего и внешнего коаксиальных электродов, l – длина датчика, а – ширина электрода, dn –расстояние между плоскими электродами, ε э(αв) – эквивалентная диэлектрическая проницаемость водонефтяной эмульсии.
Используя уравнения (2) и (3) получим связь между эквивалентной диэлектрической проницаемостью ε э и пространственным распределением диэлектрической проницаемостью ε (М) в рабочем объеме датчика с цилиндрическими и плоскими электродами:
|
ln |
Rn |
|
|
|
|
|
|
|||||
|
|
|
|
|
|
|
|
|
|
|
|
|
|
|
R0 |
∫ε(M )E |
2 |
|
|
||||||||
|
|
|
|
|
|||||||||
εэ(αв) = |
|
|
|
|
|
|
|
(M )dVM ; |
|
||||
2πlU |
2 |
|
|
, |
|||||||||
|
|
|
|
|
V |
|
|
|
|
||||
|
dn |
|
|
|
∫ε(M )E |
2 |
|
|
|
|
|||
εэ(αв) = |
|
|
|
(M )dVM . |
|
|
|||||||
alU |
2 |
|
|
|
|
|
|||||||
|
|
|
V |
|
|
|
|
|
|
где Е(М) – напряженность электрического поля в неоднородной диэлектрической среде с проницаемостью ε (М), М V. Причем электрическое поле в цилиндрическом конденсаторе при ε (М)=const существенно неоднородно в отличии от однородного поля датчика с плоскими электродами:
|
τ |
; R0 |
≤ R ≤ Rn . |
|
|
|
|||
2πε0εR |
||||
|
|
, |
||
E = |
|
|
||
U |
|
|
dn
где τ - поверхностная плотность электрического заряда на электродах датчика.
При калибровке поточного влагомера нефти на установке типа УПВН смесь «нефть
– вода» перемешивается до получения однородной водонефтяной эмульсии. Такое перемешивание практически невозможно реализовать в полевых условиях, что приводит к неоднородности распределения диэлектрической проницаемости смеси в рабочем объеме датчика, а следовательно к большим погрешностям определения влажности нефти и неустойчивой работе поточного влагомера. Влияние этого фактора на эффективность работы поточного влагомера нефти рассмотрим на модельной задаче с кусочно – неоднородной диэлектрической средой в рабочем объеме датчика, то есть представим конструктивные схемы электроемкостных преобразователей в виде многослойных цилиндриче-
ского и плоского конденсаторов соответственно
Многослойность заполнения межэлектродного пространства моделирует электрофизическую неоднородность двухфазного потока «нефть – вода», которая всегда имеет место, несмотря на принимаемые меры по перемешиванию смеси в потоке. Здесь идеализация состоит в том, что в случае цилиндрических коаксиальных электродов неоднородность имеет строго радиальный, азимутальный или осевой характер, а в случае плоских электродов неоднородность также одномерная по оси x,y или z. В последнем случае термин «продольная» или «поперечная» определяет ориентацию вектора электрического поля относительно границы раздела слоев. При этом предполагается, что поток направлен по оси z в обоих случаях
Составляющие эклектического поля датчика относительно напряжения имеют следующий вид:
Eρ = − ∂∂Uρ
EQ = − ∂∂UQ
В результате решения задачи получены математические выражения для ортогональной составляющей напряженности электрического поля.
|
|
|
2U0 |
∞ |
|
|
|
ρ |
|
||
Eρ |
= − |
∑ |
(−1)n−1( |
)2n−2 cos[(2n −1)Q] |
|||||||
|
|
|
π |
|
n=1 |
|
|
a |
|||
|
|
|
|
|
|
|
|
|
|
||
E |
= |
2U0 |
|
∞ |
(−1)n−1( |
ρ |
)2n−1 sin[(2n −1)Q] |
||||
|
∑ |
|
|||||||||
Q |
|
ρπ |
|
|
|
a |
|||||
|
|
|
|
n=1 |
|
|
|
|
|
|
Напряженность электрического поля относительно ортогональных составляющих имеет следующий вид:
E = Eρ2 + EQ2 ,
Следовательно
E = |
2aU0 a4 + ρ4 + 2a2ρ2 cos 2Q |
π[(a2 − ρ2 )2 + (2a ρ cos 2Q)2 |
График изменения напряженность в зависимости от радиуса датчика, показан на рисунке 2.
216
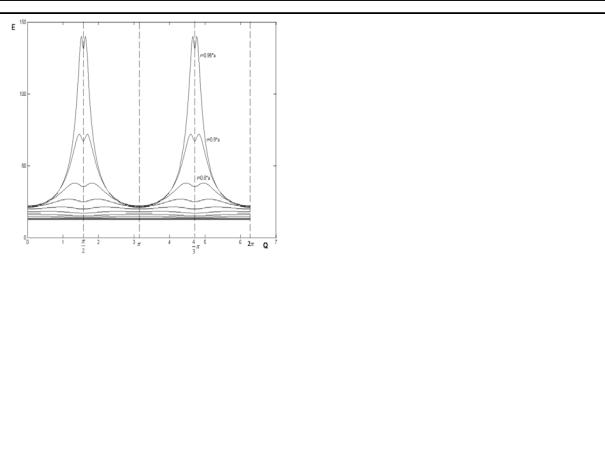
Современные техника и технологии 2007
Рис.2. График изменения напряженность в зависимости от радиуса датчика
Из графика видно, что максимальная напряженность достигается в местах разделения зазором.
Таким образом, была рассчитана напряженность электрического поля, на основание напряжения приложенного к электродам.
ЛИТЕРАТУРА:
1.Беляков В.Л. Автоматический контроль параметров нефтяных эмульсий. М.:
Недра, 1992, 203с.
2.Стеблев Ю.И. Компьютерный мониторинг сточных вод по комплексу электрофизических
параметров // Межвузовский сборник научных трудов «Автоматизация, диагностика и контроль технологических процессов и оборудования». Самара, 2001, Вып.1 С. 26-35.
3.Россель Ж. Общая физика.,
М.:Мир,1964,506с.
4.Гольдштейн Л.Д., Зернов Н.В. Элек-
тромагнитные поля и волны. М.: Советское радио, 1971,
661с.
5.Иоссель Ю.Я., Кочанов Э.С., Струй-
ский М.Г. Расчет электрической емкости. Ленинград,
Энергоиздат, 1981, 288с.
ОПРЕДЕЛЕНИЕ ХАРАКТЕРИСТИК МИКРОМЕХАНИЧЕСКОГО АКСЕЛЕРОМЕТРА
Новоселов А.А, Алтунин А.О., Мартемьянов В.М.
Томский политехнический университет,
Россия, г. Томск, пр. Ленина, 30 E-mail: novosel211k@sibmail.com
В настоящее время область применения микромеханических инерциальных датчиков чрезвычайно широка. Микромеханические датчики первичной информации позволяют создавать малогабаритные инерциальные навигационные системы, обеспечивающие необходимую точность определения параметров ориентации и координат подвижных объектов, робототехнических комплексов и др. Преимущества таких датчиков заключаются в том, что они являются недорогими элементами благодаря крупносерийному производству, имеют небольшие размеры, малую энергоемкость, и кроме того, являются достаточно прочными вследствие малого размера и прочности материалов, из которых они изготавливаются. Производство микромеханических акселерометров осуществляется с использованием технологий, развитых в последнее время в твердотельной электронике. Электромеханические узлы датчиков
формируются из неметаллических материалов (монокристаллический кремний, плавленый кварц, карбид кремния и др.) методами фотолитографии и изотропного (анизотропного) травления вместе с элементами электроники, датчиками съема и преобразования полезного сигнала, элементами формирования обратных связей [1]. Разработкой и производством микромеханических чувствительных элементов занимается ряд ведущих организаций, среди которых значительных результатов добилась фирма Analog Devices.
Исследованиям подвергался микромеханический акселерометр типа ADXL105 производства фирмы Analog Devices [2], который предполагается использовать при разработке измерителя угла отклонения объекта от плоскости горизонта. Известны конструкции таких измерителей, построенных на других чувствительных элементах [3]. С целью получения более полной информации о возможностях
217

XIII Международная научно-практическая конференция «СОВРЕМЕННЫЕ ТЕХНИКА И ТЕХНОЛОГИИ»
альтернативных схем подобных измерителей, а также применения микромеханических акселерометров в системах стабилизации и управления требуется проведение дополнительных исследований. В нашем случае была поставлена задача определения изменения выходного сигнала акселерометра в случае отклонения плоскости монтажа датчика от вертикальной плоскости, а также при изменении напряжения питания. Указанные условия вполне вероятны при практической эксплуатации разрабатываемого мобильного измерителя угла отклонения. Подключением соответствующих настроечных резисторов в цепи встроенного в датчик операционного усилителя была выставлена чувствительность акселерометра, равная 1,01 В/g при номинальном напряжении питания 5 В.
Панель, на которой крепится микромеханический акселерометр, смонтирована на вращающейся части поворотной головки, изготовленной на основе оптического квадранта КО-10, обеспечивающей неограниченный разворот корпуса акселерометра вокруг оси, перпендикулярной плоскости его монтажной поверхности (рис.1).
Рис.1. Акселерометр на поворотной головке
Поворотная головка в свою очередь установлена на наклонном стенде, обеспечивающем отклонение плоскости монтажа акселерометра от вертикальной плоскости. Угол этого отклонения контролировался с помощью второго оптического квадранта (рис. 2). Питание исследуемого акселерометра осуществлялось от регулируемого стабилизированного однополярного источника постоянного тока. Аналоговый выходной сигнал акселерометра измерялся с помощью цифрового мультиметра с ценой деления 0,01 В.
Рис.2. Экспериментальная установка
Результаты проведенных исследований показали, что при напряжении питания Uп = 5 В выходной сигнал изменяется при повороте датчика относительно его оси, перпендикулярной монтажной поверхности, по закону, близкому к гармоническому в диапазоне от 2,12 В до 4,14 В. Отклонение полученной зависимости от идеальной гармоники не превышает 8% (рис.3). Данный подход к оценке качества работы акселерометра позволяет обойтись без применения центрифуги, которую использовать в условиях учебной лаборатории практически невозможно. В нейтральном положении (когда ось чувствительности акселерометра горизонтальна) выходной сигнал имеет величину U0 = 3,13 В. При этом экспериментально определенная чувствительность акселерометра равна 1,01 В/g, что соответствует величине, заданной настроечными резисторами.
Рис.3. Определение погрешности акселерометра
Отклонение плоскости монтажа от вертикальной плоскости приводит к уменьшению диапазона выходного сигнала; так в частности при отклонении на угол β= 250 этот диапазон ограничен 2,20 В и 4,04 В. При этом чувствительность акселерометра уменьшается до величины k = 0,92 В/g (рис.4). Это обстоятельство подтверждает тот факт, что акселерометр в этом случае измеряет проекцию
218

Современные техника и технологии 2007
вектора ускорения силы тяжести на плоскость монтажной поверхности датчика g·cos β.
Рис.4. Изменение чувствительности акселерометра в зависимости от отклоне-
ния плоскости монтажной поверхности
Изменение напряжения питания приводит к существенному изменению чувствительности акселерометра k (рис.5). Экспериментально определено, что изменение чувствительности в пределах от 4 В до 5 В происходит с темпом 0,255 1/g.
Рис.5. Изменение чувствительности акселерометра при изменении напряжения
питания
Анализ полученных результатов показывает, что исследуемый микромеханический
акселерометр в качестве чувствительного элемента измерителя угла может обеспечить достаточную для практики точность измерений, если диапазон измеряемых углов не будет превышать + 900 , так как при увеличении указанного диапазона погрешность акселерометра возрастает. Влияние отклонения плоскости монтажной поверхности на погрешность измерения угла не столь велико при небольших величинах отклонения, которое можно контролировать при помощи простых чувствительных элементов, таких как жидкостные уровни, и, при необходимости, можно компенсировать это отклонение. Особое внимание необходимо уделить поддержанию стабильной величины напряжения источника питания, либо учитывать изменение напряжения при расчете величины угла в измерителях, которые в своем составе имеют вычислительные устройства.
Авторы полагают, что исследуемый микромеханический акселерометр имеет перспективы использования в различных измерительных устройствах и поэтому требуются его дальнейшие исследования при учете конкретных условий применения.
ЛИТЕРАТУРА:
1.Лестев А.М., Попова И.В. Современное состояние теории и практических разработок микромеханических гироскопов// Гироскопия и навигация. – 1998. - № 3. – С. 81 - 94.
2.http://www.analog.com
3.Дорохин Е.С., Мартынова А.Н., Мартемьянов В.М. Индикатор вертикали на основе электролитического датчика// XI Международная научн.-практ. Конференция студентов, аспирантов и молодых ученых « Современные техника и технологии», 29 марта – 2 апреля 2005 г. Изд-во ТПУ, Томск, - С. 102 - 104
219

XIII Международная научно-практическая конференция «СОВРЕМЕННЫЕ ТЕХНИКА И ТЕХНОЛОГИИ»
ПРИМЕНЕНИЕ КОРРЕЛЯЦИОННОГО МЕТОДА ПРИ ПОВЕРКЕ ИНДУКЦИОННЫХ СЧЕТЧИКОВ
Овчинникова К.С. Цимбалист Э.И.
Томский политехнический университет, Россия, г. Томск, пр. Ленина, 30 E-mail: son1@sibmail.com
Вработе обосновывается возможность использования корреляционного метода при поверке индукционных счетчиков в режиме малой потребляемой энергии. Приводится краткое описание структурной схемы поверочной установки, использующей корреляционный метод, и приводится оценка погрешности.
Введение
Несмотря на то, что в настоящее время происходит постепенное внедрение электронных счетчиков для учета электроэнергии, продолжает функционировать большое количество индукционных счетчиков, которым требуется периодическая поверка[1]. С этой целью испытательные лаборатории, аккредитованные на право поверки средств энергоучета, оснащены разного рода метрологическим оборудованием
(например, электроустановками типа: УМ1134, «Энергомер», «Вектор» и др).
Вустановках УМ1134 и «Вектор» используется метод сравнения с мерой, в котором измеряемую счетчиком энергию сравнивают со значением энергии, воспроизводимой мерой [2], а в установке «Энергомер» поверка осуществляется методом эталонного счетчика электрической энергии.
Спомощью данного метрологического оборудования можно довольно просто и с необходимой точностью осуществить поверку счетчиков активной и реактивной мощности.
К сожалению, при использовании такого оборудования поверка счетчиков на малых уровнях энергии и в режиме настройки самохода ведет к неоправданно высоким временным затратам.
Поэтому разработка методов и аппаратуры, способной минимизировать время поверки индукционных счетчиков в этих режимах, продолжает оставаться актуальной.
1.Постановка задачи и описание методов поверки
Классические методы, используемые при поверке индукционных счетчиков, базируются на подсчете числа оборотов диска ротора за определенное время. При этом используется передаточный коэффициент поверяемого счетчика, выраженный в оборотах диска ротора на киловатт-час (или киловар-час) энер-
гии. Желание уменьшить время поверки счетчика приводит к решению: поверку счетчика на малых токах следует проводить только на части угла поворота его диска, то есть за счет уменьшения градусной меры угла поворота. Так как неизвестно на какой части торца диска будет осуществляться поверка, то необходимо оцифровать и запоминать информацию
орельефе торца диска на его полном обороте. Такой подход, реализованный в установке «Вектор», ведет к увеличению памяти, необходимой для обработки информации.
Уменьшение памяти при сохранении минимального времени поверки возможно тогда, когда оцифровывается и запоминается информация о той части диска, которая необходима в настоящее время для поверки. Если в предыдущем подходе, реализованном в «Векторе», использовался один измерительный преобразователь для съема информации
оторце диска, то в предлагаемом методе должны быть использованы два датчика, зоны наблюдений которых разнесены на фиксированную угловую базу. В этом случае при заданной мощности, энергия, измеряемая поверяемым счетчиком, будет пропорциональна времени поворота торца диска на известный угол. С целью определения этого времени целесообразно использование корреляционного метода, в котором определяется транспортное запаздывание между сигналами с двух точек наблюдения торца диска за счет поиска экстремума взаимно корреляционной функции пары сигналов аналогичных по форме, но сдвинутых по оси времени.
Таким образом, задавая мощность Р0 эталонными средствами измерений повероч-
ной установки, и, определяя транспортное запаздывание сигналов, фиксируется значение эталонной энергии Э0. Энергия Э, определяемая поверяемым счетчиком , рассчитывается через его передаточный коэффициент
Ас.
2. Краткое описание установки
Рассматриваемая задача определения транспортного запаздывания двух сигналов при вращении диска ротора индукционного счетчика, реализуется в установке, часть структурной схемы которой приведена на рис.1.
220

Современные техника и технологии 2007
На торцевую поверхность, вращающегося диска проецируется световое инфракрасное излучение, воспринимаемое двумя фотодиодами, установленными на входах нормирующих усилителей. На рисунке 2. изображены временные диаграммы сигналов на выходе нормирующих усилителей 2 и 3, которые в дальнейшем мультиплексируются, преобразуются аналого-цифровым преобразователем и обрабатываются вычислительным блоком корреляционного измерителя.
Рисунок 1. Структурная схема установки (1-диск счетчика,2 и 3- нормирующие усилители , 4-мультиплексор,5-АЦП,6- корреляционный измеритель запаздыва- ния,7-световой поток).
Мгновенные значения сигналов с усилителей х(t), y(t) обусловлены яркостью, отра-
женного луча, которая изменяется из-за оптической неоднородности ребра диска: пятен, метки и изменения угла отражения луча в соответствии с микрорельефом поверхности.
Рисунок 2. Временные диаграммы сигналов на выходе нормирующих усилителей 2 и 3.
Взаимная корреляционная функция двух случайных процессов определяется по сле-
дующей |
|
формуле: |
|
|
1 |
TB −1 |
|
К(Lg) = |
∑[X (Ih − Lg) − m x ][Y(Ih - m y )] |
||
TB |
|||
|
I =0 |
,где h- шаг квантования по времени сигналов х(t), y(t) ;g- шаг квантования задержки X(Ih),
Y(Ih)-входные сигналы, квантованные по времени и уровню;I=0, 1…, TB-1, где TB-объем временной выборки; К(Lg)-значения взаимной
корреляционной функции; L=0,1,…,Lk-1, где Lk-число вычисляемых значений взаимной
корреляционной |
функции; m x , m y -мат. |
ожидания.
Вид графика взаимной корреляционной функции, показанной на рис.3, связан со спектральными свойствами входных сигналов.
Рисунок 3. График взаимно корреляционной
функции.
Корреляционная функция и спектр случайного процесса связаны парой преобразований Фурье. Чем более широкополосными являются входные сигналы, тем уже график корреляционной функции и острее ее пик. Поэтому спектр сигнала косвенно характеризует потенциальную точность фиксирования экстремума функции. Кроме того, верхняя граница спектра сигнала в соответствии с теоремой Котельникова определяет частоту квантования АЦП поверочной установки и тем самым ее потенциальное быстродействие.
3 Оценка погрешности метода
Относительная погрешность эталонной энергии Э0 поверочной установки при отсутствии корреляции между мощностью Р0 и времени t0, определяемым транспортным запаздыванием, находится как квадратный корень из суммы квадратов составляющих погрешностей. С другой стороны погрешность Э0 указывается в [1] и зависит от класса точности поверяемого счетчика и режима его поверки. При заданном значении погрешности калибратора мощности верхний предел погрешности t0/t0 становится известным и определяет значение шага квантования задержки g .
Используя программный пакет Lab VIEW, было проведено моделирование работы корреляционного измерителя, осуществлявшего обработку сигналов, изображенных на рис.2. Как видно из рис.3, корреляционная функция имеет ярко выраженный экстремум, который позволяет с необходимой точностью определить время t0 при задании эталонной энергии
221

XIII Международная научно-практическая конференция «СОВРЕМЕННЫЕ ТЕХНИКА И ТЕХНОЛОГИИ»
для эксплуатируемых типов |
индукционных |
энергии. Методика поверки».- М: Издво |
счетчиков. |
|
стандартов, 2004 г. |
|
|
2. РМГ 29-99 «Метрология. Основные |
ЛИТЕРАТУРА: |
|
термины и определения». - М.: Изд-во стан- |
1. ГОСТ 8.259-2004 «Счетчики электриче- |
дартов, 2000 г. |
|
ские индукционные активной |
и реактивной |
|
КОНТРОЛЬ ГЕРМЕТИЧНОСТИ ТРУБОПРОВОДОВ КОРРЕЛЯЦИОННЫМ МЕТОДОМ В УСЛОВИЯХ ИНТЕНСИВНЫХ КОРРЕЛИРОВАННЫХ ПОМЕХ
Овчинников А.Л.
ФГНУ «НИИ интроскопии», Россия, г. Томск, ул. Савиных, 7 E-mail: ovchinnikov_al@inbox.ru
Одним из основных источников помех при |
заглушенного с торцов участка трубы длиной |
||
контроле герметичности корреляционным ме- |
68м диаметром 100мм. Утечка находилась на |
||
тодом в городских условиях является шум |
расстоянии 30м от одного из торцов и моде- |
||
транспортных средств. Особенно сильно этот |
лировалась сквозным цилиндрическим отвер- |
||
вид помех сказывается при поиске утечек на |
стием диаметром 0,8 мм. Прием и обработка |
||
теплотрассах. Обусловлено это тем, что |
сигналов проводилась с помощью корреляци- |
||
внешние шумы могут свободно распростра- |
онного течеискателя ТАК-2005, разработан- |
||
няться по лотку, в котором уложены трубы, |
ного в ФГНУ «НИИ интроскопии». Исследова- |
||
как по волноводу. А поскольку в процессе |
лись сигналы утечки, зарегистрированные |
||
распространения, шумы возбуждают колеба- |
датчиками, уставленными на стенку трубы |
||
ния стенок трубопровода, сигналы помехи, |
при наличии и отсутствии внешних шумов. В |
||
регистрируемые |
приемными преобразовате- |
качестве источника шума использовался шум |
|
лями, могут оказаться коррелированными. В |
работающего автотранспорта. |
||
настоящее время в корреляционных течеи- |
На рис. 1 представлена спектрограмма |
||
скателях для отстройки от влияния помех ис- |
шума утечки. Как видно из графика основная |
||
пользуется набор НЧ и ВЧ фильтров, частоты |
мощность сигнала оказывается сосредото- |
||
среза которых устанавливаются оператором |
ченной в нескольких узких полосах частот в |
||
(или автоматически) исходя из максимума |
низкочастотной области спектра. На осталь- |
||
функции когерентности или модуля взаимной |
ных частотах отношение сигнал шум также |
||
спектральной плотности. Такой подход к |
больше 1. Как показали расчеты, централь- |
||
фильтрации сигнала оказывается эффектив- |
ные частоты максимальных составляющих |
||
ным, когда внешние шумы являются не кор- |
спектра сигнала кратны частоте радиального |
||
релированными, и их наличие не приводит к |
резонанса трубопровода. |
||
возникновению ложных корреляционных мак- |
|
||
симумов не связанных с утечкой, а сказыва- |
|
||
ется лишь в уменьшении амплитуды норми- |
|
||
рованной корреляционной функции. Однако в |
|
||
рассмотренном выше случае такой подход |
|
||
оказывается малопригодным, так как функция |
|
||
когерентности и модуль взаимного спектра |
|
||
будут содержать когерентные участки ни как |
|
||
не связанные с утечкой. В данной работе экс- |
|
||
периментально |
исследованы |
особенности |
|
проведения контроля в условиях коррелиро- |
|
||
ванных помех и получены рекомендации по |
|
||
проведению фильтрации сигнала. |
Рис. 1 Спектр шума утечки |
||
Исследования проводились |
на экспери- |
|
ментальной установке, которая состояла из
222

Современные техника и технологии 2007
На рис. 2 представлена спектрограмма шумов работающего автотранспорта.
Рис.2. Шум автотранспорта
При сравнении графиков на рис. 1 и 2 видно, что шум автотранспорта также возбуждает в трубопроводе резонансные колебания стенок трубопровода. То есть спектры полезного сигнала и помехи перекрываются. Однако, как показали дальнейшие более детальные экспериментальные исследования, на частотах выше 10 – 12кГц внешние шумы плохо возбуждают колебания стенок трубопровода и их уровень оказывается значительно ниже, чем уровень шумов утечки. Таким образом, при проведении контроля корреляционным методом в присутствии интенсивного шума анализ сигнала целесообразно проводить в высокочастотной области спектра.
Для проверки этого утверждения была проведена серия экспериментов. Расстояние между датчиками во всех экспериментах оставалось фиксированным и равнялось 34,5м, а расстояние от датчиков до утечки варьировалось от 0,5 до 27,5м с шагом 1м. На рис. 3 показана типичная корреляционная функция не фильтрованного сигнала.
Рис.3 Нормированная взаимнокорреляционная функция
Как и ожидалось, функция взаимной корреляции не фильтрованного сигнала содержит много максимумов, выделить среди которых максимум соответствующий точному местоположению утечки не представляется возможным. Применение высокочастотной
фильтрации также не дало удовлетворительного результата. По всей видимости, это вызвано присутствием в регистрируемом сигнале сигналов отраженных от торцов трубы. Поэтому для локализации утечки была выделена узкая полоса в высокочастотной области спектра. Причем в этой полосе фаза взаимной спектральной плотности представляла собой пилообразную функцию, содержащую несколько звеньев, которые хорошо аппроксимируются линейной функцией (рис. 4).
Рис. 4 Участок фазы взаимного спектра После фильтрации в этой полосе корреляционная функция стала иметь один четкий
максимум (рис. 5).
Рассмотренная методика фильтрации применялась ко всем экспериментальным точкам, после чего определялось расстояние до утечки и оценивалась погрешность локализации.
Рис.5 Нормированная взаимнокорреляционная функция после проведения фильтрации
На рис. 6 представлены графики зависимости точности определения местоположения утечки от расстояния до нее, рассчитанные при скорости звука определяемой скоростью Жуковского и экспериментальной скоростью полученной усреднением экспериментальных скоростей определенных в каждом опыте.
223

XIII Международная научно-практическая конференция «СОВРЕМЕННЫЕ ТЕХНИКА И ТЕХНОЛОГИИ»
Рис. 6 Зависимость погрешности локализации от расстояния до утечки при различных значениях скорости звука (1 – с=1250м/с, 2
с=1108м/с)
Как видно из графика 1 (рис. 6) использование в расчетах теоретического значения скорости приводит к большой методической погрешности. В то время как при расчетах с использованием экспериментально измерен-
ного значения скорости погрешность локализации определяется случайными факторами (график 2 (рис. 6). При этом в большинстве случаев погрешность не превышает 20см. Исключение имеет место на больших расстояниях до утечки, что обусловлено наличием отражающих поверхностей.
Выводы:
1.Спектры акустической помехи и спектры утечек перекрываются в низкочастотной области спектра.
2.Для повышения точности локализации фильтрацию сигнала следует проводить
вполосе, в которой фаза взаимного спектра аппроксимируется линейной функцией.
3.При проведении контроля на высоких частотах предварительно следует измерить скорость распространения звука в трубопроводе.
ОПИСАНИЕ МИКРОПЛАЗМЕННЫХ ПРОЦЕССОВ В ЭЛЕКТРОЛИТАХ ЛИНЕЙНЫМИ МОДЕЛЯМИ
Е.А. Попова
Томский политехнический университет, г.Томск, ул. Савиных, 7 E-mail: popowa@tpu.ru
Современная промышленность предъявляет высокие и разнообразные требования к качеству покрытий на металлах. Наиболее перспективным среди традиционных электрохимических методов является микроплазменный метод обработки поверхности [1] Суть метода состоит в том, что деталь обрабатывают в электролитах токами большой плотности, и в процессе нанесения покрытия наблюдается появление локальных плазменных разрядов.
Микроплазменные покрытия имеют различное назначение, в зависимости от него они должны удовлетворять разные требования к таким параметрам, как толщина, твердость, пористость, шероховатость и т.д. Проведены исследования [2,3] для определения влияния таких факторов, как время, температура, форма ванны, значение напряжения, на характеристики покрытий. Получены результаты, которые эффективно используются на практике. Но в силу сложности процесса требуется более глубокое изучение данного метода обработки поверхности материалов. В данной статье предлагается способ нахожде-
ния математической модели для описания микроплазменного процесса нанесения покрытий.
Используя регистрируемые входные и выходные сигналы процесса, можно построить модель процесса. Такой способ формирования модели процесса называется его идентификацией [4]. Если основные механизмы явлений, лежащих в основе технологии, понятны и имеются устоявшиеся модели, то появляется необходимость параметрической идентификации – определения конкретных констант, коэффициентов, и других параметров. В результате этого можно управлять процессом посредством изменения значений элементов схемы.
Процесс определения структуры и параметров модели состоит из несколько этапов.
1Организованный сбор необходимой и достаточной информации, т.е. сбор данных эксперимента;
2Структурная идентификация - определение структуры математической модели системы;
224
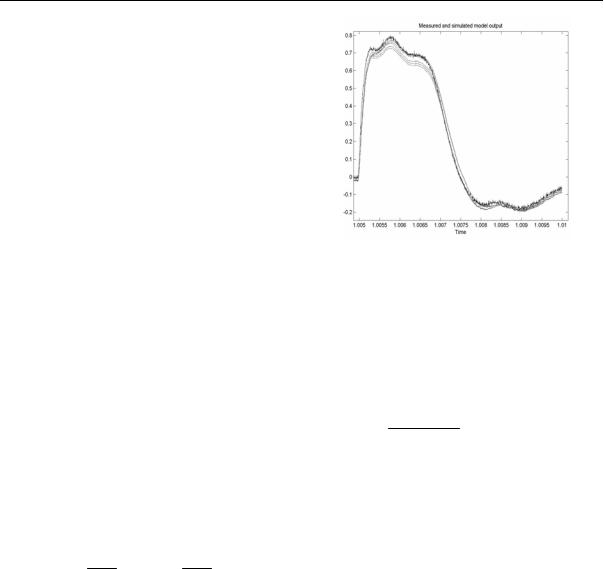
Современные техника и технологии 2007
3 Параметрическая идентификация - проведение идентифицирующего эксперимента и определение параметров модели по экспериментальным данным;
4 Проверка адекватности - проверка качества полученной модели в смысле выбранного критерия близости выходов модели и объекта.
Для описания микроплазменных процессов было предложено воспользоваться линейными моделями. Проверка адекватности моделей была произведена в программе MATLAB, представляющей собой интерактивную систему для выполнения инженерных и научных расчетов и ориентированную на работу с массивами данных.
Для исследований был проведен эксперимент: деталь прямоугольной формы погрузили в электролит, с источников подали напряжение 300 В. Через каждые моменты времени, равные 0,4 мкс, снимали значения тока, проходящего через деталь.
Микроплазменный процесс нанесения покрытия с точки зрения систем представляет собой дискретную систему, которую можно идентифицировать следующими моделями:
- модель ARX – модель
A(z)y[k] = B(z)x[k] + e[k],
A(z) = 1+ a 1z-1 + …+ a naz-na, B(z) = b0+ b 1z-1 + …+ b baz-ba,
e[k] – дискретный белый шум. - модель ARMAX
A(z)y[k] = B(z)x[k-nk]+ C(z)e[k], C(z) = 1+ c1z-1 + …+ cnc z-nc.
- модель БоксаДженкинса (BJ)
A(z) y[k] = FB((zz)) x[k − nk] + CD((zz)) e[k] ,
F = 1+ f1z-1 + …+ fnf z-nf ,
В = 1+ d1z-1 + …+ dnd z-nd и т.д.
Результаты исследований показали, что лучшими из класса параметрических аппроксимирующих моделей являются модели arx 120, amx 2221. bj 22221, pss2. Перебор других классов параметрических моделей и увеличение их степени дал результат, либо хуже либо не превышающий данный. Графики моделей представлены на рисунке 1.
Рисунок 1 – График моделей
Для отбора моделей в качестве первого критерия использовался коэффициент робастности, т. е процентное отношение выходного отклонения воспроизведенного моделью. Модель с наибольшим значением коэффициента робастности говорит о более высоком качестве модели, ее реализуемости на практике. Данное отношение определяется следующим выражением:
FIT =1 − norm((y − y")) norm y − yср
где y - это измеренные выходные данные, y” - прогнозированный выходной сигнал.
Таким образом, для вышеназванных моделей коэффициент робастности соответст-
венно равен 90.62, 92.16, 91.77 и 90.69. Исхо-
дя их этих данных, можно предположить, что модель amx 2221 обладает наибольшей точностью.
Но помимо коэффициента работоспособности существуют еще два критерия, с помощью которых можно оценить адекватность модели. Это остаточная сумма квадратов ошибки – функция потерь (Loss fen) и так называемый теоретический информационный критерий Акейке FPE (Final Prediction Error).
Функция потерь позволяет оценивать модели одного вида. В нашем случае функция потерь сама по себе не сильно информативна, поэтому для корректного определения адекватности воспользуемся критерием Акейке. Он позволяет сравнивать модели разных видов за счет того, что при его расчете используются количество неизвестных параметров и количество экспериментальных точек. Ниже приведена таблица расчетных данных.
Таблица 1 – Значения функций потерь и критерия Акейке
Модели |
Loss fen |
FPE |
arx 120 |
10е-5 |
10е-5 |
225

XIII Международная научно-практическая конференция «СОВРЕМЕННЫЕ ТЕХНИКА И ТЕХНОЛОГИИ»
|
|
|
amx 2221 |
6.40507e-5 |
6.43598e-5 |
bj 22221 |
6.29304e-5 |
6.3336e-5 |
pss2 |
6.40666e-5 |
6.43749e-5 |
Исходя из выше сказанного, можно сказать, что модель amx 2221, как и уровень робастности, имеет приемлемые значения выбранных критериев, и, несомненно, имеет более простую систему уравнений.
Уравнение модели выглядит следующим образом:
A(q)y(t) = B(q)u(t) + C(q)e(t),
A(q) = 1 - 1.836 (+-0.01123) q-1 + 0.8375 (+- 0.01124) q-2 ,
B(q) = 0.0004755 (+-3.275e-005) q-1 - 0.0004727 (+-3.271e-005) q-2,
C(q) = 1 - 1.662 (+-0.01565) q-1 + 0.7083 (+- 0.01539) q-2,
где y(t)- ток, u(t) – напряжение, e(t) – белый дискретный шум.
В среде MATLAB с использованием пакета Simulink была создана виртуальная функциональная блок-схема экспериментальной установка, с помощью которой была проведена проверка качества моделей с учетом выбранного критерия визуальной близости выхода модели и экспериментального сигнала. Проверка дала положительные результаты.
Таким образом, процесс нанесения микроплазменного покрытия можно описать математическим выражением в виде уравнения линейной модели. Из этого соображения вытекает задача для дальнейшего исследования – это с помощью коэффициентов уравнения определить конкретные параметры элементов электрической схемы.
ЛИТЕРАТУРА:
1.Мамаев А. И., В. А. Мамаева В. А. Сильнотоковые процессы в растворах электролитов. – Новосибирск: Издательство СО РАН, 2005. – 255 с.
2.Горчаков А.И., Семенова А.В., Сыровацкая Ю.В. и др. Влияние геометрических параметров микродугового оксидирования на равномерность покрытий, формируемых на алюминиевых сплавах //Физика и обработка материалов.- 2004. - № 1. - с.43-47.
3.Мамаев А.И. Физико-химические закономерности сильнотоковых импульсных процессов в растворах при нанесении оксидных покрытий и модифицировании поверхности. Докторская диссертация (02.00.04 - физическая химия). Томск. 1998.
Льюнг Л. Идентификация систем. Теория для пользователя. – М.: Наука. Гл. ред. физ.-
мат. лит., 1991. – 432
ОСОБЕННОСТИ ПРОЕКТИРОВАНИЯ АВТОНОМНЫХ ИЗМЕРИТЕЛЬНЫХ СИСТЕМ
Пушных М.А.
Томский политехнический университет, ЭФФ, КИСМ, Россия, г. Томск, ул. Савиных
E-mail: testmax@rambler.ru
Измерительные системы можно условно разделить на 2 группы:
-с сетевым питанием;
-с автономным питанием. Возможности систем I-ой группы доста-
точно обширны (в их составе большое количество датчиков, возможность передачи информации на значительные расстояния, многообразие схем учета и т.д.). Стоимость таких систем, как правило, высока.
Вторую группу обычно используют потребители, где на узлах учета не требуется реализация сложных схем учета. Особенность этой системы является их энергонезависимость и достаточно низкая стоимость. Все составляющие системы (датчики, устройства
226
обработки, передатчики) должны быть с низким энергопотреблением.
В настоящее время существует острая необходимость в автономных измерительных системах (АИС) для измерения параметров окружающей среды, контроля состояния автомобильных и железных дорог, функционирования протяженных трубопроводов, коммерческого и технического учета жидкостей, газов, электроэнергии. Очень важной является и проблема создания автономных измерительных систем для контроля технологических процессов распределённых на большой площади производств. Очевидно, что система должна состоять из аппаратных и программных средств вычислительной техники, что позволит полностью автоматизировать про-

Современные техника и технологии 2007
цесс измерения, обработки и хранения информации, а также представления результатов измерения оператору.
Особенности АИС заключаются в следующем:
-разобщённость составных частей;
-низкое энергопотребление;
-небольшая точность, по сравнению с ИС
ссетевым питанием;
-низкая стоимость.
Разобщенность составных частей заключается в том, что объекты измерения и устройства обработки могут находиться на больших расстояниях друг от друга, для связи с которыми используют маршрутизаторы, усилители или мобильные телефонным сетям.
В настоящее время решения с использованием беспроводного сетевого протокола считается наиболее перспективным для построения эффективных сетей, обеспечивающих измерения физических параметров, автоматизацию коммерческого и технического учета жидкости, газов, электроэнергии.[1]
Например, использование автономного счетчика-регистратора «Пульсар» НПО Тепловодохран с проводным каналом передачи информации в условиях городской и промышленной застройки может привести к невозможности построения сети.
Однако и решения, основанные на использовании протоколов Bluetooth, Wi-Fi, Zegbee на самом деле не выполняют всех требований по дальности действия, энергопотреблению, гибкости топологии и управлению сетью.
Большой популярностью пользуются специализированные контроллеры и приемопередатчики компаний Atmel и Texas Instruments. Они уже предназначены для использования в автономных измерительных системах со сверхнизким энергопотреблением.
При выборе аппаратной части АИС, следует уделять рассмотрению вопросов связанных с возможностью работы в режимах пониженного потребления. В низкопотребляющих измерительных системах среднее значение потребляемого тока определяет срок службы аккумулятора. Так, например, в автономном счетчике-регистраторе «Импульс», разработанным производственной компанией «СпецКИПавтоматика», системе используется батарея размера «С» с емкостью 8500 мАч, рассчитанная для работы без замены на 2 года. Это достигается путем применения низкопотребляющих контроллера и приемопередатчика, совместно с различными режимами сохранения энергии.[2]
Режимы пониженного потребления - важное свойство, дающее возможность микроконтроллеру удовлетворить требованиям по потреблению энергии. В основном низкопотребляющие микроконтроллеры имеют несколько режимов пониженного потребления, в которых они способны выполнять различные функции. В основном низкопотребляющие контроллеры имеют пять режимов пониженного потребления. В режиме Low-power mode zero (LPM0) отключается вычислительное ядро, но все остальные функции остаются активными. В режимах LPM1 и LPM2 в список отключенных функций добавляются различные функции синхронизации, например, синхронизация от низкочастотного задающего генератора, если не требуется высокая точность. LPM3 - наиболее часто используемый режим пониженного потребления, в котором остается активным только низкочастотный автогенератор и все периферийные устройства, использующие для работы синхросигналы этого автогенератора. LPM3 часто применяется для работы в прерывистом режиме, когда низкочастотный генератор применяется в качестве часов реального времени. В режиме LPM4 выключаются все встроенные задающие генераторы, что приводит к автоматическому отключению всех синхронных периферийных устройств. В этом режиме аналоговые периферийные устройства могут оставаться в активном режиме, но если отключить и их, то микроконтроллер (даже осуществляя регенерацию ОЗУ) будет потреблять всего 100 нА. Во многом потребление микроконтроллера зависит от системы синхронизации. Устройства могут входить в режим пониженного потребления и выходить из него от нескольких раз в секунду до нескольких сотен раз в секунду. Такая возможность дает контроллеру не дожидаться установления стабильных синхроимпульсов и потреблять довольно большой ток.
Система обработки прерываний способна вывести микроконтроллер из режима пониженного потребления, поэтому, чем больше имеется прерываний, тем больше гибкости микроконтроллер имеет для обеспечения снижения общего потребления. Кроме того, периферийные устройства могут управляться прерываниями от других периферийных устройств. Используя это преимущество можно управлять приемопередатчиком, активируя его в необходимый момент для обмена информацией.[3]
Точность измерений напрямую зависит от аналоговой части АИС, от вида измерения и подробно не рассматривается в этой статье.
Как было ранее отмечено одна из основных особенностей АИС это низкая стоимость
227

XIII Международная научно-практическая конференция «СОВРЕМЕННЫЕ ТЕХНИКА И ТЕХНОЛОГИИ»
по сравнению с ИС с сетевым питанием. Например, автономный счетчик - регистратор «Импульс» стоит порядка 100 долларов США, а аналогичная ИС с сетевым питанием около 1000 долларов США. Что говорит о высокой конкурентоспособности. Более подробно этот вопрос в этой статье не рассматривается.
Подводя итог вышесказанному, можно сказать, что элементы АИС являются разобщенными, находящимися на расстоянии друг от друга. Так в АИС используются специализированные низкопотребляющие микроконтроллеры и приемопередатчики, работающие
в различных режимах работы. АИС имеют не большую стоимость по сравнению с ИС с сетевым питанием, но низкая стоимость делает их более конкурентоспособными.
ЛИТЕРАТУРА:
1 Choosing a microcontroller for handheld measurement apps, Juan Alvarez, Texas Instruments, Dallas, TX
2www.skipa.ru\impulse.html
3Choosing a low-power MCU, Mike Mitchell, Texas Instruments, Dallas, TX
КОМПЛЕКС АВТОМАТИЗИРОВАННЫХ СИСТЕМ ДЛЯ ИСПЫТАНИЙ АСФАЛЬТОБИТУМНЫХ МАТЕРИАЛОВ ПРИМЕНЯЕМЫХ
ДЛЯ ДОРОЖНЫХ ПОКРЫТИЙ
Эфа А.К., Трофимов И.Н., *Рыбин Ю.К., **Цебенко Н.Н. Томский архитектурно-строительный университет,
Россия, г. Томск, пл. Соляная, 2
*Томский политехнический университет, Россия, г. Томск, пр. Ленина, 30
**Томский институт автоматики и электромеханики при ТУСУР, Россия, г. Томск, ул. Белинского, 53
E-mail: rybin@galore.tomsk.ru
Автомобильные дороги в Сибири эксплуатируются в экстремальных климатических условиях и, как правило, при повышенных транспортных нагрузках. В таких условиях длительность эксплуатации асфальтобетонного покрытия зависит от грамотного проектирования конструкции дорожной одежды, соблюдения технологии строительства и применяемых материалов. Особое место в этом занимает качество дорожного покрытия, в частности, качество применяемых битумоминеральных материалов, технология их приготовления и устройства покрытия. Битумоминеральные материалы, применяемые в дорожном строительстве, характеризуются многими параметрами, такими как прочность, упругость, сдвигоустойчивость, пластичность и зависимости их от температурных колебаний. Естественно, что прочность, упругость и сдвигоустойчивость определяются качеством связующих материалов и минеральных заполнителей.
Для комплексной оценки качества материалов, прогнозирования свойств и изменения параметров битумоминеральных материалов во времени и при действии внешних факторов они подвергаются необходимым
испытаниям. В докладе рассматриваются автоматизированные испытательные установки для определения прочности, упругости, сдвигоустойчивости и пластичности образцов дорожного покрытия из битумоминеральных материалов в условиях максимально приближённых к естественным условиям эксплуатации автомобильных дорог Сибирского региона.
Первая установка (см. рис. 1) содержит: -электромеханический стенд (ЭМСТ1) для создания ударного механического воздейст-
вия на образец;
-микропроцессорный электронный блок (ЭБ) для управления процессом испытаний, создания испытательных и управляющих воздействий, измерения силы ударного воздействия, температуры образца и линейных перемещений, отражающих деформацию образца;
-персональный компьютер (ПК на рисунке не показан) с прикладным программным обеспечением для дистанционного управления процессом испытаний, обработки, хранения, представления и документирования результатов испытаний.
228

Современные техника и технологии 2007
Установка имеет два режима управления испытаниями: местное с передней панели ЭБ и дистанционное с ПК связанного с ЭБ через интерфейс RS 232.
В режиме местного управления с помощью кнопок на передней панели ЭБ и регулятора воздушного клапана вводится программа испытаний:
-задаётся значение ударного усилия;
-устанавливается режим предварительного «обжатия» образца;
-вводится количество циклов нагружения (ударов) образца.
До проведения испытаний максимально приближённых к естественным условиям эксплуатации образцы предварительно помещают в морозильную камеру и выдерживают
вней при заданной температуре в течение нескольких часов. Затем образцы вынимают и помещают в ЭМСТ1. Испытания начинают с нажатия кнопки «ПУСК». В этот момент происходит срабатывание воздушного клапана 6, резкое перемещение плунжера 8 и ударное воздействие плунжера передаётся на образец 2 через датчик силы 7 и устройство 9. Под действием ударной нагрузки образец деформируется, изменяются его размеры. Датчики силы 7, линейных перемещений 1 и 3 и температуры 5 воспринимают значения этих величин, преобразуют их в электрические сиг-
налы и передают в ЭБ, в котором производится преобразование измеряемых величин в цифровую форму, обработка и запоминание. После окончания испытаний на дисплее ЭБ отображаются все измеренные параметры.
1, 3 - датчики линейных перемещений; 2 – испытуемый образец из асфальтоби-
тумной смеси; 4 – электронный блок системы; 5 - датчик температуры; 6 - воздушный компрессор с электромагнитным клапаном для создания ударного воздействия; 7 - датчик силы (нагрузки); 8 – плунжер и устройство 9, передающее механический удар на образец. Рисунок 1 - Упрощенная схема испытательной установки «ТомскАсфальтТест»
В дистанционном режиме управление испытаниями производится с ПК и все результаты измерений передаются в его память. Далее с помощью оригинального программ-
ного обеспечения производится их обработка и представление в виде графиков изменения нагрузки и перемещений во времени, вычисляются интегральные параметры образца и формируется протокол испытаний.
Установка имеет следующие технические характеристики:
-сила ударного воздействия от 100 до
10000 Н;
-погрешность измерения силы ± 10 Н;
-диапазон линейных перемещений 0 – 50
мкм;
-погрешность измерения ± 0,2 мкм;
-диапазон температур от - 40 до + 60 °С;
-погрешность измерения ± 0,5 °С;
-время силы воздействия и установления линейных перемещений 5 мс.
Отличительной особенностью установки является высокая точность и малое время измерений, поэтому при испытаниях можно зафиксировать процесс деформации образца и оценить его упругие и пластичные свойства в динамике через каждые 5 мс.
Вторая установка (см. рис.2) для определения пластичности содержит стенд для длительного механического воздействия, моделирующего действие колёс транспортных средств на плоские образцы из асфальтобитумных материалов и электронный блок для управления процессом испытаний, измерения параметров деформации образца, обработки, хранения, представления и документирования результатов испытаний.
1, 3 - датчики линейных перемещений; 2 – датчик температуры; 4 - испытуемые образцы из асфальтоби-
тумной смеси; 5 –водяная ванна; 6 – электронный блок обработки измери-
тельной системы.
Рисунок 2 – Упрощенная схема испытательной установки «ТомскАсфальтТест-2»
Установка содержит:
-электромеханический стенд (ЭМСТ2) для создания механического воздействия на образцы;
- микропроцессорный электронный блок (ЭБ) для управления процессом испытаний, измерения линейных перемещений и температуры образцов;
229

XIII Международная научно-практическая конференция «СОВРЕМЕННЫЕ ТЕХНИКА И ТЕХНОЛОГИИ»
-персональный компьютер (ПК на рисунке также не показан).
ЭМСТ2 содержит два подвижных колеса, которые совершают вращательнопоступательные движения в противоположных направлениях. Это сделано для уменьшения механических вибраций, возникающих при испытаниях. Наличие двух подвижных колёс позволяет проводить одновременно испытания двух образцов.
Установка так же имеет два режима управления испытаниями: местное и дистанционное.
Испытания в обоих режимах проходят следующим образом. Образцы 4 нагревают в водяной ванне 5 до заданной температуры, которая контролируется с помощью датчика температуры 2. Далее в ЭБ вводится программа испытаний, включающая число циклов испытаний и количество проходов колёс
вкаждом цикле. После нажатия кнопки «ПУСК» колёса ЭМСТ2 начинают синхронные возвратно-поступательные движения по образцам (электромеханический привод на схеме не показан). При этом на образцы оказывается заданное статическое и динамическое давление. По мере воздействия образцы уплотняются и колёса опускаются вниз. Их перемещение фиксируют датчики линейных перемещений 1 и 3. Количество проходов фиксирует концевой датчик.
Установка имеет следующие технические характеристики:
-сила статического давления от 100 до
10000 Н;
-диапазон линейных перемещений 0 – 20
мм;
-погрешность измерения перемещений ±
0,1 мм;
-диапазон температур от + 10 до +60 °С;
-погрешность измерения температуры ±
0,5 °С.
-количество проходов колёс в цикле от 1
до 1000;
-количество циклов испытаний от1 до 50. Важной особенностью, характеризующей
обе испытательные установки, является то, что при существенном отличии их электромеханической части электронный блок в обеих установках выполняет одинаковые функции: управление испытаниями, задание управляющих воздействий, измерение физических величин (линейных перемещений, давления, температуры), обработку и хранение результатов измерений. Эта универсальность электронного блока достигнута за счёт выбора оптимальной структуры ЭБ и её унификации. Для обеспечения этой универсальности электронные блоки конструктивно содержат универсальную материнскую плату, в которую вставляются унифицированные дочерние платы для сопряжения с датчиками физических величин и микропроцессорные платы управления испытаниями, измерения и хранения параметров и связи с внешним персональным компьютером. Максимальное количество таких плат до 8, а с учётом дополнительной платы возможного расширения – до
16.
Испытательные установки прошли апробацию в строительной лаборатории Томского архитектурно-строительного университета и рекомендованы для применения в отрасли.
ПРЕОБРАЗОВАТЕЛЬ ЧАСТОТЫ С КОДОВО-ИМПУЛЬСНЫМ РЕГУЛИРОВАНИЕМ ДЛЯ ИНДУКЦИОННОЙ ПЛАВКИ МЕТАЛЛОВ
Земан С.К., Сандырев О.Е.
ФГНУ “НИИ АЭМ” Россия, 634034, г. Томск, ул. Белинского, 53 E-mail: sandirev@mail.ru
Индукционная плавка металлов в последнее время получила широкое распространение, благодаря высокому качеству нагрева, отсутствием загрязнений, достижимостью любых температур, возможностью точного дозирования энергии, использования различных атмосфер и вакуума. При этом способе нагрева обеспечивается сбережение матери-
230
альных, трудовых и энергетических ресурсов
[1].
Особенностью этого способа плавки является изменение электрофизических параметров нагрузки в процессе нагрева, в нерегулируемых преобразователях частоты (ПЧ) это приводит к значительному завышению габаритной мощности элементов ПЧ. При

Современные техника и технологии 2007
этом, получить требуемую величину выходной мощности с помощью одной инверторной ячейки затруднительно, поэтому предлагается разделить весь поток электрической энергии на несколько каналов, и суммировать их в общем контуре. Схема шестиячейковой структуры использующей данный принцип изображена на рис.1.
Рис.1 Структура ПЧ с кодово-импульсным регулированием
В данной структуре, выходные напряжения регулируемых ячеек (ЯР), суммируются в последовательном резонансном контуре (RLC), где R – активное сопротивление нагрузки, L – реактивное сопротивление нагрузки, а С – величина емкости, компенсирующей реактивное сопротивление нагрузки [1].
Для регулирования такой структуры предлагается ввести кодово-импульсный способ, обеспечивающий следующие преимущества по отношению к остальным способам регулирования:
•Резонансный режим работы на протяжении всего периода регулирования, в результате чего значительно возрастает качество потребления электрической энергии от сети.
•Минимальные динамические потери на переключение полупроводниковых приборов инвертора, так как их переключение происходит при нуле тока [2].
Диаграммы выходного напряжения при пуске преобразователя представлены на рис.2.
Рис.2 Диаграммы выходного напряжения при пуске ПЧ
Видно, что применение в многоячейковом ПЧ кодово-импульсного способа регулирования позволяет получить плавный выход на рабочий режим работы ПЧ при достаточно высокой точности регулирования.
Управление такой структурой предлагается реализовать в цифровом виде, она имеет следующие преимущества:
•Настройка системы управления значительно упрощается;
•Параметры регулирования имеют высокую стабильность во времени, что определяет надежную работу всего ПЧ.
На рис.3 представлена структура цифровой системы управления, обеспечивающей функции: регулирования тока нагрузки, фазовой автоподстройки частоты, защиты полупроводниковых ключей инверторов от перегрузки по току и перегрева, драйверной защиты, индикации рабочих параметров и интерфейса связи с внешними устройствами.
В ПЧ предлагается применить двухконтурное управление. Первый контур управления обеспечивает программное уравновешивание тока нагрузки, упрощенный алгоритм которого представлен на рис.4.
231

XIII Международная научно-практическая конференция «СОВРЕМЕННЫЕ ТЕХНИКА И ТЕХНОЛОГИИ»
стной характер, выходное напряжение отстает по фазе от тока, значит, приращение рабочей частоты будет направлено в сторону ее увеличения. Рабочая частота ПЧ не изменяется в случае, если напряжение совпадает по фазе с током в пределах установленной зоны нечувствительности.
Рис.3 Структура цифровой системы управления
Согласно представленному алгоритму весь диапазон регулирования разбит на кодо- во-импульсные комбинации, причем каждая комбинация имеет свое значение среднего напряжения на выходе ПЧ. При достижении среднего текущего значения тока нагрузки верхней границы зоны нечувствительности (Iуст+ ), текущая кодово-импульсная комбинация переходит на один уровень ниже, соответственно значение среднего напряжения на выходе ПЧ уменьшается. Наоборот, при достижении среднего текущего значения тока нагрузки нижней границы зоны нечувствительности (Iуст– ), текущая кодовоимпульсная комбинация переходит на один уровень выше, увеличивая этим значение среднего напряжения на выходе ПЧ.
В процессе работы ПЧ индуктивная составляющая импеданса нагрузки изменяется в широких пределах, это приводит к нарушению резонансного режима работы ПЧ. Наиболее эффективным способом решения этой проблемы является применение фазовой автоподстройки рабочей частоты (ФАПЧ) ПЧ на частоту резонансного колебательного контура. Для этой цели предназначен второй контур управления, обеспечивающий функции ФАПЧ. Его предлагается реализовать по принципу программного уравновешивания рабочей частоты преобразователя. Критерием подстройки является минимизация фазового сдвига между выходным током и напряжением ПЧ. При этом рабочая частота изменяется дискретно с точностью определяемой шагом подстройки. Знак приращения рабочей частоты определяется характером нагрузки. А именно, если нагрузка носит индуктивный характер, ток отстает по фазе от выходного напряжения, значит, приращение рабочей частоты будет направлено в сторону ее уменьшения. Наоборот, если нагрузка носит емко-
Рис.4 Алгоритм управления ПЧ с кодовоимпульсным регулированием Преобразователь частоты с кодовоимпульсным регулированием позволяет реализовать современную высокотехнологич-ную установку для индукционной плавки металлов, обеспечивающую высокое качество по-
требляемой от сети электроэнергии.
ЛИТЕРАТУРА:
1 Индукционные печи для плавки металлов и сплавов Фарбман С.А., Колобнев
232

|
|
Современные техника и технологии 2007 |
И.Ф. Изд-во “Металлургия”, 1968, 5-е изд., с. |
напряжения. Схемотехника №7, 2001. С.17- |
|
496 |
19. |
|
|
2 Патанов Д.А. Общие проблемы сни- |
|
жения коммутационных потерь в инверторах |
|
ОЦЕНИВАНИЕ ДИНАМИЧЕСКИХ ХАРАКТЕРИСТИК СРЕДСТВ ИЗМЕРЕНИЙ
Сафонова Ю.В.
Томский политехнический университет, Россия, г. Томск, пр. Ленина, 30
E-mail: gifx@mail.ru
Динамические измерения, т.е. измерения с использованием средств измерений (далее
– СИ) в динамическом режиме, получают все большее распространение в технике и научных исследованиях. Эти измерения связаны в первую очередь с изучением закономерностей протекания физических процессов в исследуемых объектах. Поэтому роль ДИ особенно велика, во-первых, в областях науки, связанных с исследованием структуры материи, анализом и синтезом новых веществ и материалов, изучением объектов в экстремальных условиях, и, во-вторых, в отраслях техники и производства, для которых характерно создание новых технологических процессов и испытание новых машин, приборов и аппаратов.
Моя работа посвящена оцениванию динамических характеристик, поэтому более подробно остановимся именно на задачи нормирования и определения динамических характеристик СИ. Динамические характеристики необходимо знать для выбора СИ, оценивания погрешностей измерений и получения их результатов. Информация о динамических характеристиках должна содержаться в нормативно-технической документации.
Определяются динамические характеристики по реакции СИ на известный испытательный сигнал. Несмотря на различие источников испытательных сигналов в различных областях измерений, методология и теория решения задачи являются общими. Широкое применение здесь находят методы идентификации динамических объектов. Эти методы должны быть модифицированы с учетом специфики метрологии, которая заключается, в первую очередь, в тесной связи определения динамических характеристик и их нормирования, преимущественном использовании детерминированных испытательных сигналов, необходимости учитывать цели измерений и оценивать точность результатов измерений. [1]
В соответствии с ГОСТ 8.009-84 нормированию подлежат полные и частные динамические характеристики.
Полную динамическую характеристику выбирают из числа следующих:
−переходная характеристика (ПХ) h(t);
−импульсная переходная характеристика
(ИПХ) g(t);
−амплитудно-фазовая характеристика
(АФХ) G(jω);
−амплитудно-частотная характеристика (АЧХ) А(ω) – для минимально-фазовых систем;
−совокупность амплитудно-частотной и фазо-частотной характеристик (ФЧХ) ϕ(ω);
−передаточная функция G(p).
Полные динамические характеристики нормируют путем установления номинальной динамической характеристики и пределов (положительного и отрицательного) допускаемых отклонений от нее. Предпочтительной является такая характеристика, экспериментальное определение и (или) контроль которой могут быть выполнены с необходимой точностью и наиболее простым способом. [2]
Допускается нормирование динамических характеристик для нормальных и рабочих условий применения СИ отдельно.
Номинальную динамическую характеристику, пределы допускаемых отклонений от нее и граничные динамические характеристики можно представлять в виде чисел, формул, таблиц или графиков. Необходимо отметить, что в ГОСТ 8.009-84 отдается предпочтение нормированию полных динамических характеристик, поскольку с их помощью можно определить любую частную. Частные динамические характеристики допускается нормировать в обоснованных случаях.
Некоторые частные динамические характеристики аналоговых СИ можно рассматривать как линейные. К частным динамическим характеристикам относят любые функциона-
233

XIII Международная научно-практическая конференция «СОВРЕМЕННЫЕ ТЕХНИКА И ТЕХНОЛОГИИ»
лы или параметры полных динамических характеристик. Примерами таких характеристик являются:
−постоянная времени нарастания τИ ;
−время реакции tδ1,tδ 2 ,tδ 3 ;
−коэффициент демпфирования γ Д ;
−значение резонансной собственной круговой частоты ω0 ;
−время задержки tз ;
−мертвое время и др.
Допускается нормировать только частную динамическую характеристику в тех случаях, когда эта характеристика достаточна для учета динамических свойств СИ при его применении. [2]
Рассмотрим определение динамической погрешности СИ, используя упрощенную модель, в которой сравниваются выходные сигналы реального и идеального СИ (рисунок 1). Идеальное СИ задает желаемое преобразование сигнала, т.е. то преобразование, с помощью которого требуется выделить (получить) нужную информацию или осуществить необходимое преобразование входного сигнала. Например, может ставиться задача определения скорости изменения ФВ или среднего значения ФВ за конкретное время, или значения самой ФВ. Однако реально эти преобразования не удается выполнить точно, что приводит к возникновению динамической погрешности.
Динамическую погрешность для детерми-
нированного сигнала |
x(t ) можно определить |
||||||||||||||
по формуле |
|
|
|
|
|||||||||||
εd (t )= |
|
h(t )−y(t ) |
|
|
|
|
|
(1) |
|||||||
|
|
|
|
|
|||||||||||
|
|
|
|
|
|||||||||||
и для случайного сигнала по формуле |
|||||||||||||||
|
|
|
|
|
|
|
|
|
|
|
|
1 |
t0 |
|
|
|
|
|
|
|
|
|
|
|
|
|
|
|
|||
ε2 = |
h(t )−y(t ) |
2 = |
lim |
∫ [h(t )−y(t )]2 dt , |
(2) |
||||||||||
|
|||||||||||||||
|
ds |
|
|
|
t →∞2t |
−t0 |
|
||||||||
|
|
|
|
|
|
|
|
|
|
|
0 |
0 |
|
где y(t ) и h(t ) - выходные сигналы реального и идеального СИ соответственно; ±t0 - временные пределы усреднения.
Рис. 1 – Упрощенная модель определения погрешности измерения в динамическом режиме
Как правило, оптимизация режима работы СИ при динамических измерениях связана с желанием уменьшить динамическую погрешность и увеличить быстродействие. В свою очередь погрешности линейных искажений и погрешности из-за электронных шумов поразному зависят от частотной полосы пропускания СИ, определяющего его быстродействие.
Значимость ДП по сравнению с другими погрешностями устанавливается ГОСТ 8.00984. Динамическая погрешность рассматривается как дополнительная и считается существенной при удовлетворении неравенства
( Д )макс≥0,17 максСИ , |
(3) |
где ( Д )макс - наибольшее значение дина-
мической погрешности СИ, возможное в рабочих условиях применения СИ данного типа, максСИ - наибольшее возможное значение
погрешности СИ в рабочих условиях применения СИ данного типа, т.е. все составляющие инструментальной погрешности СИ (основной, дополнительной, динамической и погрешности взаимодействия).
Если неравенство (3) не выполняется, то динамическую погрешность можно не учитывать, а режим измерения считать статическим. [3]
Обеспечение единства измерений в условиях динамических измерений предполагает такое состояние измерений, когда результаты выражаются в узаконенных единицах, размеры которых в установленных пределах (т.е. с заданными погрешностями) равны размерам единиц, воспроизводимых эталонами. Таким образом, измерения физической величины в узаконенных единицах должны проводиться СИ, поверенным с помощью поверочной схемы, в которой единица передается «сверхувниз» с нарастающей погрешностью от первичного эталона к рабочим эталонам соответствующих разрядов. [4]
Для динамических измерений кроме единицы измерения необходимо передавать и оценивать динамические характеристики СИ рабочих эталонов.
Ряд задач по передаче единиц измерения в динамическом режиме можно решить, используя статический режим работы СИ, если последний используется в обоих режимах (с помощью статической поверочной схемы). В то же время динамические характеристики этих СИ могут быть также поверены более точными с точки зрения (как правило, более быстродействующими) СИ.
234

|
|
|
Современные техника и технологии 2007 |
|
Однако если осуществить поверку в ста- |
1 |
МИ 1951-88 ГСИ. Динамические изме- |
тическом режиме невозможно, то строят по- |
рения. Термины и определения. – М.: Изда- |
||
верочные схемы, создавая первичный эталон |
тельство стандартов, 1988. |
||
(эталонное СИ) и рабочие эталоны (образцо- |
2 |
ГОСТ 8.009-94 ГСИ. Нормируемые |
|
вые СИ). |
метрологические характеристики. – М.: Изда- |
||
|
Заметим, что кроме передачи размера |
тельство стандартов, 1994. |
|
единицы измеряемой физической величины в |
3 |
Пронкин Н.С. Основы метрологии ди- |
|
динамическом режиме почти всегда необхо- |
намических измерений: Учеб. пособие для |
||
димо измерять (фиксировать) время. Методы |
вузов. – М.: Логос, 2003. – 256 с. |
||
измерения времени хорошо разработаны и |
4 |
Грановский В.А. Динамические изме- |
|
обеспечивают высокую точность. [3] |
рения: Основы метрологического обеспече- |
||
|
|
ния. – Л.: Энергоатомиздат. Ленингр. отд-ние, |
|
|
ЛИТЕРАТУРА: |
1984. – 224с., ил. |
СИСТЕМА СБОРА ИНФОРМАЦИИ НА ОСНОВЕ I2C ИНТЕРФЕЙСА
Селезнёв А. И.
Томский политехнический университет, Россия, г. Томск, пр. Ленина, 30 E-mail: antonium@list.ru
Системы сбора, обработки информации и управления широко используются во многих сферах деятельности человека. Применение таких систем в промышленности позволяет автоматизировать производство, повысить качество продукции, а также снизить затраты. Использование систем сбора информации в различных исследованиях позволяет облегчить анализ полученных данных.
Требования, предъявляемые к системам, зависят от области их применения. Это может быть высокая точность измерения, большое количество точек измерения, высокая скорость измерения, выполнение функций поддержания какой-либо величины на определенном уровне или в заданном интервале и т. д.
На структуру и характеристики системы сильно влияет, какой интерфейс был выбран для организации связи между датчиками.
Применение SPI интерфейса сопряжено с определенными сложностями в области организации сети датчиков, так как при каждом датчике необходимо поставить микроконтроллер, что приведет к усложнению системы в целом, а так же к росту ее стоимости.
Если в качестве основного интерфейса использовать CAN, то для этого также придется использовать дополнительные микросхемы, что связано со спецификой данного интерфейса.
USB интерфейс также мало подходит для связи датчиков в сеть, так как длина линии
передачи составляет максимум 5 метров, затем необходимо ставить «хаб».
Наиболее подходит для общих применений сеть датчиков на интерфейсе I2C. В спецификации данного интерфейса предусмотрена работа многих устройств на одной шине, он достаточно широко распространен, имеется множество датчиков и микроконтроллеров
стаким интерфейсом.
Вкачестве примера рассмотрим систему сбора и обработки информации, структурная схема которой представлена на рисунке 1.
Рис. 1 В ее состав входят следующие функцио-
нальные блоки:
МК – микроконтроллер с модулем I2C; ЦД – цифровой датчик с интерфейсом I2C; Д – аналоговый датчик, либо датчик с ин-
терфейсом, отличным от I2C;
ПК – персональный компьютер.
Из приведенной схемы видно, что использование I2C интерфейса существенно упрощает конструкцию системы сбора и обработки информации, так как не возникает необходи-
235
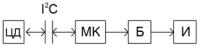
XIII Международная научно-практическая конференция «СОВРЕМЕННЫЕ ТЕХНИКА И ТЕХНОЛОГИИ»
мость в использовании специальных микро- схем-преобразователей интерфейса, драйверов, микроконтроллеров для управления их работой и т. д.
Также на структурной схеме показано, каким образом к такой системе подключаются аналоговые датчики сигналов и датчики, использующие для передачи информации об измеряемой величине интерфейс, отличный от I2C. Для этого достаточно поставить микроконтроллер, который будет играть роль передаточного звена между датчиком и I2C-шиной. Для того, чтобы подключить к такой системе датчик с аналоговым выходным сигналом, нужно использовать микроконтроллер, содержащий встроенные аналого-цифровой преобразователь и модуль I2C, а для подключения датчика, выдающего информацию об измеряемой величине в цифровом виде (например, посредством SPI-интерфейса) достаточно применить микроконтроллер, имеющий только модуль I2C.
На структурной схеме также показан один «главный» микроконтроллер, который осуществляет связь между системой сбора и обработки информации и персональным компьютером. В качестве интерфейса используем RS-232С, так как он обладает рядом достоинств, таких как малое число сигнальных линий, хорошая надежность, невысокая стоимость формирователя уровней, простота организации связи. Расстояние между приемником и передатчиком информации, а также скорость обмена данными являются приемлемыми для большинства приложений.
В ходе научной работы была спроектирована система измерения температуры, в основе принципа работы которой было положено использование интерфейса I2C для связи датчика температуры и микроконтроллера.
Структурная схема, поясняющая принцип работы полученного устройства изображена на рисунке 2.
Рис. 2 Функциональные блоки схемы:
ЦД – цифровой датчик температуры. МК – микроконтроллер.
Б– буфер.
И- индикатор
В качестве цифрового датчика температуры был использован датчик DS1621 фирмы
Dallas Semiconductor. Особенностью данного датчика является то, что часть его идентификационного адреса «вшита» изготовителем и не подлежит изменению, а другая часть может быть задана разработчиком, применяю-
щим этот датчик в своем устройстве. Это позволяет использовать несколько таких датчиков (не более 8) на одной шине, и при этом их адреса не будут совпадать. Если же необходимо использовать много таких датчиков, то на каждые 8 штук достаточно поставить по одному микроконтроллеру, таким образом получится несколько «подсетей» датчиков, причем соответствующий микроконтроллер будет играть роль «шлюза» для своей «подсети».
Вкачестве микроконтроллера был использован микроконтроллер PIC16F877 фир-
мы Microchip, имеющий встроенный модуль I2C, что позволило существенно упростить управляющую программу, так как не пришлось прибегать к программной реализации интерфейса.
Также в устройстве был применен четырехразрядный LED-индикатор с общим анодом. Для вывода информации на индикатор использовался режим динамической индикации. Так как каждый сегмент разряда потреблял ток менее 20 мА (т. е. ток, меньший, чем ток, который способен выдать микроконтроллер на каждый разряд порта ввода/вывода), то буферизация линий управления сегментами не потребовалась. Однако суммарный ток общего анода разряда в несколько раз превышал это значение, в связи с чем возникла необходимость использовать буфер для четырех линий управления напряжением на анодах разрядов индикатора.
Спроектированное устройство работает следующим образом.
При включении питания программа сна-
чала инициализирует модули и порты микроконтроллера. Затем на шину I2C выдается адрес датчика температуры, и если сигнал подтверждения от датчика не приходит, значит либо линия оборвана, либо датчик неисправен, и программа выводит на индикатор символы «- - - -», что говорит о нарушении связи с датчиком. Если же сигнал подтверждения получен, что микроконтроллер дает датчику команду, чтобы тот выдал текущую настройку своего режима работы.
Взависимости от полученной информации микроконтроллер либо настраивает датчик на нужный режим работы и затем запускает его на преобразование, либо пропускает подпрограмму настройки и сразу запускает датчик.
Затем, спустя некоторое время, происходит прерывание от таймера, и в подпрограмме обработки микроконтроллер считывает состояние датчика, и, в зависимости от бита завершения преобразования, либо считывает готовые данные, преобразует их в код семисегментного индикатора, помещает в регист-
236

Современные техника и технологии 2007
ры, выделенные для хранения символов, отображаемых на индикаторе, и выходит из прерывания, попадая в программу осуществляющую динамическую индикацию содержимого этих регистров, либо сразу выходит из прерывания, при этом программа индикации продолжает отображать значение температуры, полученное от датчика ранее.
Каждый раз, когда происходит обмен данными с датчиком, ведется проверка на наличие подтверждающего сигнала со стороны датчика, и в случае, если подтверждение не было получено на индикатор выводятся описанные ранее символы «- - - -». Это позволяет определить неисправность, если вдруг в процессе работы устройства произошло повреждение линии связи с датчиком, либо самого датчика.
Полученное устройство обладает следующими основными характеристиками:
-частота измерений – приблизительно одно измерение в секунду.
Кего достоинствам можно отнести:
-минимум внешних элементов в схеме;
-отсутствие необходимости калибров-
ки;
-невысокую стоимость конечного устройства.
Проведенные экспериментальные испытания показали, что устройство имеет высокую надежность и устойчиво в работе.
Устройство было собрано на демонстрационной плате фирмы Microchip, в процессе его разработки, а также для отладки было использовано программное обеспечение MPLAB IDE v5.70.40 и внутрисхемный отлад-
чик MPLAB ICD Debugger v1.44.
ЛИТЕРАТУРА:
1) Семенов, Борис Юрьевич. Шина I²C в
-диапазон измеряемых температур от - радиотехнических конструкциях / Б. Ю. Семе-
55 до +125 оС; |
нов. — 2-е изд., доп. — М. : СОЛОН-Пресс, |
|
- погрешность измерений составляет ± |
2004. — 223 с |
|
0.5 оС; |
2) |
www.maxim-ic.com |
|
3) |
www.microchip.com |
НЕРАЗРУШАЮЩИЙ ЭКСПРЕСС КОНТРОЛЬ КАЧЕСТВА ТЕРМООБРАБОТКИ МЕТАЛЛОВ
Солдатов И.А., Егоров Ю.П., Цехановский С.А.
Томский политехнический университет, Россия, г.Томск, пр.Ленина, 30
E-mail: asoldatof@mail.ru
В настоящее время приборы термоэлектрического контроля металлов и сплавов не получили широкого распространения из-за низкой точностьи и плохой повторяемости результатов измерения, в результате чего снижается достоверность контроля изделий из металла. Этот недостаток обусловлен зависимостью величины термоЭДС от сопротивления контакта горячего электрода с контролируемым изделием и его зависимостью от разности температуры между горячим и холодным электродами [1]. При контроле изделий необходимо обеспечить электрический контакт горячего электрода с контролируемым изделием, при этом происходит уменьшение температуры горячего электрода за счет передачи части теплоты контролируемому изделию.
Величина термоЭДС определяется по формуле[1] :
Ε=−k2 *3T*e*π2 *(ddlnερ)
где: p - удельное сопротивление, Т – температура, ε - энергия электрона.
Изменение температуры приводит к изменению показаний прибора при длительном контроле изделий, так как постоянная времени процесса нагрева и охлаждения горячего электрода является величиной конечной и в результате температура горячего электрода флуктуирует в некоторых пределах. Применение дифференциального метода измерения термоЭДС позволяет повысить стабильность показаний прибора. Для этого используют датчик состоящий из двух горячих электродов, имеющих общую систему терморегулирования. При контроле металлических изделий электрическая цепь состоит из последовательно соединенных первого горячего электрода, контрольного (эталон) образца, контролируемого изделия и второго горячего электрода (рис.1). Дифференциальная тер-
237

XIII Международная научно-практическая конференция «СОВРЕМЕННЫЕ ТЕХНИКА И ТЕХНОЛОГИИ»
моЭДС, в соответствии с правилом аддитивности, будет определяться из выражения:
Едифф = Е1 + Е2 + Ε3
Если горячие электроды изготовлены из одного материала и имеют одинаковую температуру, а контролируемое изделие изготовлено из того же материала что и эталон, то результирующая термоЭДС будет равна нулю.
Рис. 1. Электрическая цепь измерения термоЭДС.
Так как величина термоЭДС между первым горячим электродом и эталоном будет равна по модулю, но противоположна по знаку термоЭДС между контролируемым изделием и вторым горячим электродом, а термоЭДС между эталоном и контролируемым изделием равна нулю, т.к. они выполнены из одного материала, то дифференциальная термоЭДС равна нулю. При контроле изделий происходит синхронное уменьшение температуры горячих электродов, и соответственно отсутствуют условия для возникновения паразитных термоЭДС. Это свойство можно использовать при массовой разбраковке изделий на соответствие эталону. Изменение температуры горячих электродов не приводит к изменению показаний прибора. Изготовленный прибор, для контроля металлов и сплавов, с использованием двух горячих электродов в датчике термоЭДС, был использован для контроля качества термической обработки. Эталон готовится из заранее известной марки стали и подвергается той операции термической обработки, которая контролируется. Чем больше показания прибора тем больше образец отличается от эталона.
В качестве примера на рис.2 приведена зависимость дифференциальной термо-э.д.с. от температуры нагрева под закалку стали Р6М5.
Рис. 2. Зависимость дифференциальной термоЭДС от температуры нагрева под закалку стали Р6М5.
Эталоном являлся образец из стали Р6М5, закаленный от температуры 1225 °С при погружении в масло.
На рис.3 приведена зависимость дифференциальной термоЭДС от твердости для стали ШХ15, которая применяется при изготовления подшипников. В качестве эталона использовался образец из стали ШХ15 с твердостью 40 HRC.
Рис. 3. Зависимость дифференциальной термоЭДС от твердости для стали ШХ15.
Во всех случаях подготовка эталона и контролируемого образца заключалась в удалении части поверхности (0,8-1 мм) после термической обработки, что гарантировало отсутствие обезуглероженного слоя на поверхности изделий.
Основным контролирующим параметром химико-термической обработки (ХТО) является глубина насыщаемого слоя. Металлографический метод контроля относится к прямому методу определения глубины слоя. Однако, несмотря на достаточную точность и надежность, металлографический метод контроля имеет два существенных недостатка: большую длительность и необходимость подготовки металлографического шлифа, т. е.
238

Современные техника и технологии 2007
разрушения изделия. Особенно эти недостатки существенны при контроле ХТО крупногабаритных изделий: шестерен мощных редукторов, зубчатых колес и др. Для оценки возможности использования разработанного прибора для контроля глубины цементованного слоя построили зависимость дифференциальной термоЭДС от глубины слоя на образце.
Образец вырезался из зубчатого колеса Ø 900 мм, изготовленного из стали 12Х2Н4А после ионной цементации и термической обработки (закалки и отпуска). Для измерения величины термоЭДС по глубине цементованного слоя плоскую поверхность одного из зубов образца ступенчато, через 0,2 мм., сошлифовывали. В результате ступенчатого шлифования максимальная глубина сошлифованного слоя на последней ступени составила 2 мм. Изготовление зубчатого колеса и ХТО проводились на ООО «Спецремонт» г. Москва. В качестве «эталона» использовали образец, вырезанный из нецементованной части колеса. Для сравнения результатов контроля глубину цементованного слоя определили металлографическим методом на шлифе образца, подготовленного в поперечном сечении зуба. Она составила 1,7-1,8 мм.
Диферениальную термоЭДС по глубине сошлифованного слоя определяли на каждой ступени по 5 измерений. Время одного измерения не более 3 сек.
На рис.4 приведена зависимость термоЭДС от глубины сошлифованного слоя на поверхности зуба. Из рис. 4 следует, что зависимость дифференциальной термоЭДС от глубины сошлифованного слоя носит чисто
линейный характер до глубины сошлифованного слоя 1,8-1,9 мм. Для большей глубины слоя значение термоЭДС близко к 0, что свидетельствует об отсутствии различия между нецементованным «эталоном» и испытуемым образцом.
|
40 |
|
|
|
|
|
mкV |
35 |
|
|
|
|
|
30 |
|
|
|
|
|
|
., |
25 |
|
|
|
|
|
-э.д.с |
|
|
|
|
|
|
20 |
|
|
|
|
|
|
термо |
15 |
|
|
|
|
|
|
|
|
|
|
|
|
Дифф. |
10 |
|
|
|
|
|
5 |
|
|
|
|
|
|
|
|
|
|
|
|
|
|
0 |
|
|
|
|
|
|
0 |
0,5 |
1 |
1,5 |
2 |
2,5 |
Глубина слоя,мм
Рис.4. Зависимость термоЭДС от глубины сошлифованного слоя на поверхности зуба.
Таким образом, метод дифференциальной термоЭДС с использованием двух горячих электродов может быть рекомендован для проведения неразрушающего экспресс - контроля качества термообработки металлических изделий.
ЛИТЕРАТУРА:
1. Б.Г.Лившиц, В.С.Крапошин, Я.Л.Линецкий. Физические свойства металлов и сплавов, М., Металлургия, 1980 г.
УСТРОЙСТВО ГИРОСКОПИЧЕСКОЙ СТАБИЛИЗАЦИИ ЛИДАРА В ПЛОСКОСТИ ГОРИЗОНТА
Теплоухов В.В.
Томский политехнический университет,
Россия, г.Томск, пр. Ленина, 30 E-mail: dtps@lcg.tpu.ru
Лидары - это приборы для лазерного зондирования окружающей среды (определение биоресурсов моря, источников загрязнения окружающей среды, определение скорости ветра, атмосферной турбулентности, структуры облаков, влажности воздуха т.п.). Лидары имеют огромные преимущества перед акустическими локаторами и радиолокаторами, т.к. для них прозрачна вода и атмосфера, в то
время как для ультразвука серьезным препятствием является мутная вода и пена. Лидары используются как в стационарном, так и мобильном вариантах.
Настоящая работа посвящена рассмотрению метода повышения точности направления линии прицела мобильного лидара в пространстве в его рабочем режиме при зонди-
239

XIII Международная научно-практическая конференция «СОВРЕМЕННЫЕ ТЕХНИКА И ТЕХНОЛОГИИ»
ровании интересующих объектов с использованием гироскопической стабилизации.
Врабочем режиме лидара при работающем на холостом ходу двигателе автомобиля вибрационные механические воздействия существенно влияют на стабильность положения линии прицела в пространстве. Дело в том, что работающий двигатель автомобиля служит генератором электропитания функционально связанных с лидаром систем навигации, телевизионной, газоанализа, метеосистем, информационной. При этом с увеличением холостых оборотов двигателя автомобиля наблюдается к росту амплитуды колебаний в отдельных диапазонах частот.
Исходя из этого технической задачей является создание простого устройства гироскопической стабилизации лидара в плоскости горизонта и, как следствие, повышение точности направления линии прицела лидара
впространстве в рабочем режиме при зондировании объектов.
Вданной работе поставленная задача решается за счет того, что в устройстве гироскопической стабилизации лидара в плоскости горизонта имеется подвес, обладающий маятниковостью, на котором установлен гиродвигатель с вектором кинетического момента, направленного вдоль вертикали места Предлагаемое устройство позволяет обеспечить стабилизацию объекта в плоскости горизонта вследствие установки упруго-вязких элементов, обеспечивающих возможность малого углового перемещения рамы по двум ортогональным осям. При наличии угловой скорости по осям подвеса рамы с лидаром возникает момент гироскопической реакции направленный противоположно моменту вызванного внешними воздействиями. На рисунке представлена схема устройства.
Всоставе лидара 1 входят два телескопа: излучатель и приемник. Оптические элементы телескопов установлены на корпусе 2, представляющем рамную конструкцию. В состав корпуса 2 входят верхнее 3 и нижнее 4 кольца, связанные между собой укосинами 5.
Лидар 1 установлен на верхнее кольцо 3 корпуса 2, кольцо 3 через упруго-вязкие элементы (пружины 6 и демпферы 7) закреплены на кронштейне 8, закрепленном в свою очередь на полу 9 автомобиля 10.
Упругим элементом служит пружина сжатия.
Демпфер 7 представляет типовую конструкцию жидкостного демпфирующего устройства линейного типа. Он состоит из корпуса 11 в форме цилиндра, закрепленного на кольце 3 корпуса 2. Поршень 12 имеет возможность перемещаться линейно в корпусе 11 демпфера 7, при этом поршень 12 связан с
кронштейном 8 через развязывающее устройство, позволяющее этому поршню иметь небольшие угловые перемещения в корпусе 11 демпфера. Внутренняя полость корпуса 11 демпфера 7 заполнена вязкой (например, полисилоксановой) жидкостью.
Таким образом лидар 1 и оптическая система, установленные на корпусе 2, связаны с кронштейном 8 через упруго-вязкие связи. Маятниковая система, состоящая из лидара 1, оптических элементов, корпуса 2 имеет центр масс (ц.м.) ниже плоскости установки упругих элементов 6 и демпферов 7. К нижнему кольцу 4 крепится электродвигатель 14, на валу которого установлен маховик для генерирования кинетического момента Н, обеспечивающего гироскопическую силовую стабилизацию маятниковой системы. В процессе транспортирования для исключения поломок элементов подвижной части от соударения с кронштейнами 8 установлен транспортный арретир 13 (показан на рисунке условно), который жестко фиксирует в пространстве маятниковую часть механической системы.
Рисунок Предлагаемое устройство работает сле-
дующим образом. В рабочем режиме лидара1 на него действуют вибрационные механические нагрузки от работающего двигателя автомобиля, который служит генератором электропитания функционально связанных с лидаром систем (навигации, газоанализа, информационной, телевизионной, метеосистемы). Из-за наличия маятниковости механической системы (лидар 1 – корпуса 2) в любой момент времени обеспечивается вертикальное положение этой механической системы вдоль вертикали место. Введение в конструкцию подвеса рамы упруго-вязких элементов (пружин 6 и демпферов 7) позволяет производить гашение колебаний от внешних механических воздействий, например от рабо-
240

|
|
|
|
|
|
|
|
Современные техника и технологии 2007 |
|||||
тающего двигателя автомобиля на холостом |
q частотавнешнего воздействия, |
||||||||||||
ходу в рабочем режиме лидара 1. |
|
P вес корпуса с лидаром, |
|||||||||||
|
Дополнительно, наличие электродвигате- |
l |
расстояниеотцентра массы до оси |
||||||||||
ля 14 с закрепленным на его валу маховиком, |
|||||||||||||
расположения упруго-вязких опор. |
|||||||||||||
генерирующим |
кинетический момент |
Н, по- |
Амплитуда вынужденных колебаний рамы |
||||||||||
зволяет повысить эффективность стабилиза- |
|||||||||||||
с лидаром по ортогональным направлениям |
|||||||||||||
ции механической системы (лидар 1-корпус 2) |
определяется решением вышеуказанной сис- |
||||||||||||
за счет введения гироскопической стабилиза- |
темы |
дифференциальных уравнений (1) по |
|||||||||||
ции. |
|
|
|
|
каждому из направлений. |
|
|
||||||
|
В |
данном |
устройстве динамика |
работы |
|
|
|||||||
механической |
системы (лидар-рама) |
описы- |
|
|
|
|
- |
|
|
||||
|
|
|
Mв |
− Hβ& |
|
|
|||||||
вается системой дифференциальных уравне- |
|
|
|
|
|
||||||||
|
α = |
|
α |
|
|
sin( qt − λ ) |
|||||||
|
|
(κα - Jα q2 )2 + μα2 q2 |
|
||||||||||
ний: |
|
|
|
& |
|
|
|
|
|
||||
|
Jαα |
|
|
|
|
|
|
|
& |
|
|
||
|
+ μαα +καα + Р α = Mвα sin qtl − Hβ sin qt |
|
|
|
|
|
|
||||||
&& |
|
& |
|
(1) |
|
β = |
|
Mвβ |
− Hα |
|
sin( qt − λ ) |
||
&& |
+ μ |
& |
|
|
|
|
|||||||
|
|
|
(κβ - Jβ q2 )2 + μβ2 q2 |
|
|||||||||
|
Jβ β |
β β +κβ β + Plβ = Mвβ sin qt − Hα sin qt |
|
|
|
|
|
||||||
|
|
|
|
|
& |
|
|
|
|
|
|
|
|
|
где: Jα J β |
моменты инерции рамы с лидаром от- |
Из выражений (2) следует, что амплитуда |
||||||||||
|
носительно ортогональных осей установки упру- |
||||||||||||
|
колебаний будет |
тем меньше, чем больше |
|||||||||||
|
|
|
|
го-вязких опор, |
|
кинетический момент H , а так же коэффици- |
|||||||
|
μα ,μβ коэффициентыдемпфирования |
ент демпфирования μ . |
|
|
по ортогональным направления, κα ,κβ коэффициент жесткости опор ра-
мы по ортогональным направлениям, α&&,β&& угловые ускорения,
α& ,β& угловыескорости, α ,β углы корпуса с лидаром по осям ор-
тогональных направлений,
H – кинетический момент,
Mвα ,Mвβ амплитудымоментов внешних воздействий по ортогональным осям,
Таким образом, предлагаемое устройство позволяет решить задачу устранения влияния внешних вибрационных механических воздействий на положение линии прицела лидара при зондировании объектов, так как в рабочем режиме лидара внешние вибрационные механические воздействия будут одновременно гаситься.
ПОВЫШЕНИЕ ТОЧНОСТИ ЛИНИИ ПРИЦЕЛА ЛИДАРА МЕТОДОМ УГЛОВОЙ СТАБИЛИЗАЦИИ ЕГО ОСНОВАНИЯ
Теплоухов В.В.
Томский политехнический университет, Россия, г.Томск, пр. Ленина, 30
E-mail: dtps@lcg.tpu.ru
Лидары - это приборы для лазерного зондирования окружающей среды (определение биоресурсов моря, источников загрязнения окружающей среды, определение скорости ветра, атмосферной турбулентности, структуры облаков, влажности воздуха т.п.). Лидары имеют огромные преимущества перед акустическими локаторами и радиолокаторами, т.к. для них прозрачна вода и атмосфера, в то время как для ультразвука серьезным препятствием является мутная вода и пена.
Лидары используются как в стационарном, так и мобильном вариантах.
Настоящая работа посвящена рассмотрению метода повышения точности направле-
ния линии прицела мобильного лидара в пространстве в его рабочем режиме при зондировании интересующих объектов.
В рабочем режиме лидара при работающем на холостом ходу двигателе автомобиля вибрационные механические воздействия существенно влияют на стабильность положения линии прицела в пространстве.
Дело в том, что работающий двигатель автомобиля служит генератором электропитания функционально связанных с лидаром систем навигации, телевизионной, газоанализа, метеосистем, информационной. При этом с увеличением холостых оборотов двигателя
241

XIII Международная научно-практическая конференция «СОВРЕМЕННЫЕ ТЕХНИКА И ТЕХНОЛОГИИ»
автомобиля наблюдается рост амплитуды колебаний в отдельных диапазонах частот.
Суть предлагаемого метода повышение в пространстве линии прицела лидара заключается в установке последнего на раме, имеющей возможность небольших угловых отклонений вследствие установки ее на упру- го-вязких опорах, расположенных по периметру корпуса (см. рисунок) и конструктивно обеспеченной маятниковости вышеуказанной рамы.
Рисунок
Предлагаемое устройство позволяет обеспечить стабилизацию объекта в плоскости горизонта вследствие установки упругих элементов бескарданова подвеса, обеспечивающих стабилизации лидара по двум ортогональным осям. При отклонении корпуса с лидаром возникает момент, направленный противоположно моменту вызванного внешними воздействиями. В устройстве стабилизации подвес состоит из ортогонально расположенных четырех параллельно установленных упругих элементов и демпферов, на которые установлен лидар с корпусом. Эти упругие элементы с демпферами дают возможность малого углового перемещения аналогично угловым поворотам относительно осей рамок карданова подвеса
Предложенное устройство стабилизации лидара в плоскости горизонта позволяет:
1.Удерживать объект стабилизации строго вдоль вертикали места за счет маятниковости рамы.
2.Устранять колебания линии прицела лидара в диапазоне частот, возникающих при работе двигателя автомобиля на холостом ходу.
Для пояснения конструкции предлагаемого устройства на рисунке приведена его схема.
На этой схеме условно не показано крепление узлов упруго-вязкого подвеса в основании, а так же сама конструкция упруго-вязких элементов и конструкции оптической системы. Вышеизложенное не мешает пониманию сущности принципа работы предлагаемого
устройства стабилизации объекта в плоскости горизонта.
В состав лидара 1 входят два телескопа: излучатель и приемник. Оптические элементы телескопов установлены на общем корпусе 2, представляющим рамную конструкцию. В состав корпуса 2 входят (верхнее 3 и нижнее 4) кольца, связанные между собой укосинами 5.
Лидар 1 устанавливается на верхнее кольцо 3 корпуса 2, которое через пружины 6 и демпферы 7 крепится к кронштейнам 8, закрепленных в свою очередь на полу 9 автомобиля 10.
К верхнему кольцу 3 прикреплены упругий элемент 6 и демпфер 7. Упругий элемент 6 может быть выполнен в виде цилиндрической винтовой пружины сжатия или многожильной винтовой пружины сжатия, имеющей более пологую характеристику при малых габаритах, или может представлять собой рессору по типу автомобильной.
Другим концом упругий элемент 6 крепится к кронштейну 8.
Впроцессе транспортирования для исключения поломок элементов подвижной части от соударения с корпусом имеется транспортный арретир 11 (показан на рисунке условно), который жестко фиксирует в пространстве подвижную часть механической системы
Демпфер 7 представляет типовую конструкцию демпфирующего устройства линейного типа и состоит из цилиндрического корпуса, закрепленного на верхнем кольце 3; поршня 13, закрепленного на кронштейне 8. Поршень 13 линейно перемещаться в корпусе 12 демпфера, при этом поршень 13 связан с кронштейном 8 через развязывающее устройство, позволяющее поршню 13 совершать небольшие угловые перемещения в корпусе 12 демпфера. Внутренняя полость корпуса демпфера заполнена очень вязкой (например, полисилоксановой) жидкостью.
Таким образом, лидар 1, установлен через упруго-вязкие амортизаторы (пружина 6, демпфер 7) на кронштейнах 8, которые в свою очередь крепятся к автомобилю 10. Маятниковая подвижная система имеет центр масс (ц.м.) ниже плоскости расположения уп- руго-вязких амортизаторов.
Предлагаемое устройство работает следующим образом.
Врабочем режиме лидара 1 на него действуют вибрационные механические нагрузки от работающего двигателя 9 автомобиля 10, который служит генератором электропитания функционально связанных с лидаром 1 систем (навигации, газоанализа, информационной, телевизионной, метеосистемы).
242

Современные техника и технологии 2007
Из заналичия маятниковости механической системы (лидар 1 – корпуса 2) в любой момент времени обеспечивается вертикальное положение этой механической системы вдоль вертикали место. Введение в конструкцию подвеса рамы упругих элементов 6 и демпферов 7 позволяет производить гашение колебаний от внешних механических воздействий, например от работы двигателя автомобиля 9 на холостом ходу в рабочем режиме лидара 1
Такое техническое решение позволяет, во-первых, автоматически выдерживать лидар по вертикали места и, во-вторых, в рабочем режиме лидара происходит исключение механического воздействия отрабатывающего двигателя автомобиля на оптическую систему лидара вследствие фильтрации их в уп- руго-вязких элементах опор амортизаторов рамы.
Аналитически физическая картина процесса диссипации энергии внешних механических воздействий выглядит следующим образом.
В данном устройстве динамика работы механической системы (лидар-рама) описывается системой дифференциальных уравнений:
J |
|
α |
+ μ α + c α + Plα = Q sin( pt +δ ) |
|
||
|
α |
&& |
α |
& |
α |
(1) |
|
|
&& |
|
& |
+ cβ β + Plβ = Q sin( pt +δ ) |
|
J |
β β |
+ μβ β |
|
|||
|
|
|
|
|
|
|
где: Jα ,Jβ моменты инерции рамы отно-
сительно оси подвеса в ортогональных направлениях;
μα , μβ коэффициенты демпфирования; сα , сβ коэффициенты жесткости упругого
элемента;
P – вес конструкции;
p частотавнешних воздействий;
l расстояние от оси до центра масс подвижной части;
Q амплитуда внешнего периодического воздействия.
Максимальная амплитуда рамы при внешнем воздействии Q по каждому направлению независима и определяется выражением:
A = |
h |
, |
(2) |
|
( k 2 − p2 ) − 4n2 p2
где: k – собственная частота рамы, р – частота внешнего воздействия.
Из выражения (2) видно, что чем больше разница собственной частоты устройства и внешних частот механического воздействия и чем, больше коэффициент демпфирования μ , входящий в коэффициент n, тем амплиту-
да колебаний стабилизирующего устройства А меньше.
Таким образом, предлагаемое устройство позволяет решить задачу устранения влияния внешних вибрационных механических воздействий на положение линии прицела лидара при зондировании объектов, так как в рабочем режиме лидара внешние вибрационные механические воздействия будут гаситься в упругих элементах, работающих как фильтр частот, за счет существенной разницы собственной низкой частоты подвешенного механического маятника, роль которого выполняет корпус с закрепленным на ней лидаром, а так же гасится в параллельно установленных вязких демпферах достигается задача устранения влияния внешних вибрационных механических воздействий на положение линии прицела лидара при зондировании объектов. При этом следует иметь в виду, что в такой механической системе, в рабочем режиме лидара, имеем случай малых колебаний, когда собственная частота маятника не зависит от амплитуды колебаний последнего, что дополнительно повышает эффективность предлагаемой пассивной системы стабилизации.
243

XIII Международная научно-практическая конференция «СОВРЕМЕННЫЕ ТЕХНИКА И ТЕХНОЛОГИИ»
ОТСТРОЙКА ОТ ВЛИЯНИЯ ИЗМЕНЕНИЙ СКОРОСТИ ДВИЖЕНИЯ ПРИ ИЗМЕРЕНИИ ДЛИНЫ СТАЛЬНОГО КАНАТА МЕТОДОМ МАГНИТНЫХ МЕТОК
Уразбеков Е.И., Кондратенко П.В.
Томский политехнический университет пр. Ленина, 2
E-mail: claget145@mail.ru
В процессе изготовления стальных канатов, прядей и проволоки требуется измерять длину соответствующих изделий. На предприятиях торговли и предприятияхпотребителях продукции измерения применяются на участках приемки и контрольной перемотки канатов, на участках отпуска продукции покупателям.
Наиболее подходящим для целей измерения длины стального каната является метод магнитных меток [1].
Структурная схема измерителя, реализующего представленный метод, показана на рис. 1.
Рис. 1 Структурная схема измерителя длины, использующего метод магнитных меток: 1) изделие; 2) стирающий электромагнит; 3) записывающий электромагнит; 4) магнитомодуляционный преобразователь; 5) схема включения преобразователя; 6) пороговое устройство; 7) формирователь импульса записи; 8) вычислительный блок.
Способ измерения длины ферромагнитных изделий методом магнитных меток заключается в нанесении на движущееся изделие 1 импульсным электромагнитом 3 магнитных меток, считывании этих меток расположенным на фиксированном расстоянии от электромагнита магнитным преобразователем 4, нанесении каждой последующей метки в момент считывания предыдущей, подсчете числа считанных магнитным преобразователем магнитных меток, и определении длины изделия путем умножения числа посчитанных магнитных меток на базовое расстояние [2].
Как правило, при решении задачи измерения длины стальных канатов непосредственно в технологической линии их производства, измерения осуществляются при непостоянных и достаточно больших скоростях
движения, обусловленных характеристиками крутильной машины и параметрами каната, а также относительно малой длине мерной базы (менее 1 м). Таким образом, влияние скорости на точность измерений длины становится весьма существенным и может привести к погрешности измерений порядка единиц
– десятков процентов.
Главными факторами, обуславливающими влияние скорости движения изделия на результат измерения его длины, являются деформация магнитной метки и ее смещение в продольном направлении при изменении скорости. Физически это объясняется следующим. В устройствах, реализующих метод магнитных меток, для считывания магнитных меток используется магнитомодуляционный измерительный преобразователь, а на изделие наносят магнитные метки вида (полярно-
сти) SNNS либо NSSN.
Такое намагничивание применяется для усиления и локализации пространственной составляющей магнитного поля метки поперечного относительно продольной оси изделия направления. Именно эта составляющая магнитного поля метки определяет значение выходного сигнала магнитомодуляционного преобразователя. Нанесение магнитной метки указанного вида осуществляется путем воздействия на изделие магнитным полем электромагнита с Ш-образным магнитопроводом (рис. 2).
Рис. 2. Вид магнитных меток при записи на неподвижном (а) и движущемся (б) изделии: 1) изделие; 2) электромагнит
244

Современные техника и технологии 2007
На рисунке видно, что соседние участки изделия оказываются намагниченными в противоположных направлениях. Можно считать, что длина намагниченных участков в случае неподвижного изделия примерно равна межполюсному расстоянию магнитопровода a (рис. 2, а). В случае движения изделия в продольном направлении со скоростью v длина намагниченных участков становится неодинаковой.
На рис. 2, б показан вид намагниченных участков в момент окончания импульса записи магнитной метки. Первый по ходу движения намагниченный участок оказывается длиннее второго на величину b. Значение b определяется скоростью v движения изделия и длительностью T импульса записи магнитной метки:
b = v T.
Минимальная длительность импульса записи определяется длительностью переходного процесса в цепи обмотки электромагнита, а следовательно ее индуктивностью. Поскольку при нанесении магнитных меток требуется обеспечить значение индукции насыщения, а поперечный размер изделия может достигать значений порядка нескольких десятков мм, то длительность импульса записи не может быть менее десятков мс. При скоростях движения изделия порядка нескольких м/с величина b достигает значений порядка десятков мм.
На рис. 3 приведены зависимости поперечной составляющей напряженности магнитного поля метки Hy от относительного значения продольной координаты X для разных значений b.
Рис. 3. Изменение формы сигнала от магнитной метки при изменении скорости
Видно, что в случае неподвижного изделия магнитное поле метки симметрично относительно вертикальной оси. В случае наличия движения поле магнитной метки деформируется.
Количественно степень влияния скорости движения на расстояние между соседними метками определяется расстоянием между передними фронтами кривых по уровню порога срабатывания устройства. Для относительно малых значений зазора между магнитомодуляционным преобразователем и объектом, зависимость смещения фронта метки от величины b, а значит и от скорости движения, носит линейный характер и можно ориентировочно принять, что ≈ 0,7 b.
В результате продольного смещения фронта магнитной метки при возрастании скорости движения, метки наносятся реже (расстояние между соседними метками увеличивается), что может привести к заниженному значению результата измерения по сравнению с истинным значением измеряемой длины.
Существенное снижение погрешности, обусловленной изменением скорости движения объекта измерения, может быть достигнуто коррекцией базового расстояния L0 на величину поправки, зависящей от скорости движения объекта. В этом случае измеряемое значение длины Lx при скорости движения изделия v в соответствии с результатами приведенного выше анализа находится по формуле:
Lx = N (L0 + k v),
где N – число подсчитанных магнитных меток; L0 – базовое расстояние, определяемое для случая v→ 0; k – постоянный множитель; произведение k v = – пропорциональная скорости движения величина поправки, на которую корректируется базовое расстоя-
ние L0.
Величина k, имеющая размерность единицы времени, определяется прежде всего длительностью T импульса записи магнитной метки, но также зависит от геометрических параметров используемого для записи метки электромагнита, зазора, выбранным порогом срабатывания устройства считывания магнитных меток и ряда других менее значимых факторов. Поэтому для достижения высокой точности измерений длины значение k целесообразно определять экспериментально. Для приблизительной оценки значения k может быть использовано приведенное ранее равенство ≈ 0,7 b, из которого с учетом (1) вытекает, что k ≈ 0,7 T.
Мгновенное значение скорости движения v, необходимое для вычисления поправки , может быть определено путем измерения временного интервала t между соседними метками:
v=L0 /(t-k).
245

XIII Международная научно-практическая конференция «СОВРЕМЕННЫЕ ТЕХНИКА И ТЕХНОЛОГИИ»
При использовании предлагаемого метода отстройки может быть достигнута высокая точность измерения даже при малых значениях базового расстояния и большом диапазоне изменений скорости движения.
ЛИТЕРАТУРА:
[1]Уразбеков Е.И. Метод измерения длины стальных канатов с помощью нанесения
магнитных меток/ «Современные техника и технологии». Сб. статей. Томск: Изд-во ТПУ, 2006. – Т. 1. - С. 135-138.
[2] Патент РФ № 2082078, М. кл. G01B7/04. Устройство для измерения длины ферромагнитных изделий / АО ″Черногор-
нефть″. - Опубл. 20.06.1997, www.fips.ru. – 5 с.
БЕСКОНТАКТНЫЙ ДВУХКООРДИНАТНЫЙ ИЗМЕРИТЕЛЬ ПРОТЯЖЁННЫХ ИЗДЕЛИЙ БОЛЬШИХ ДИАМЕТРОВ В ПРОЦЕССЕ ИХ
ИЗГОТОВЛЕНИЯ «ЦИКАДА-3.7»
Фёдоров Е. М.
Томский политехнический университет г.Томск, пр.Ленина 2
E-mail: evgeny_fyodorov@list.ru.
В настоящее время для контроля геометрических размеров проводов, кабелей (главным образом диаметра) разработан довольно широкий спектр приборов и устройств различных типов [2]. Однако до недавнего времени оставалось проблематичным измерение диаметра и контроля некруглости (овальности) изделий больших диаметров (от 20 до 200мм) в реальном режиме времени.
Применение традиционного теневого метода в квазипараллельном пучке для измерения таких диаметров затруднительно т. к. требует использования высококачественной, а следовательно дорогостоящей, широкоапертурной оптики. Отсутствие на рынке многоэлементных приёмников соответствующей длины вынуждает использовать обычные приёмники, что делает оптическую схему прибора громоздкой и сказывается на точности измерения. Применение метода измерения мощности потока излучения так же не приемлемо из-за отсутствия достаточно стабильных источников света.
246
Рис 1. Оптическая схема прибора
С учетом результатов проведенного анализа, на фирме «ЭРМИС+» была разработана конструкция измерителя «Цикада-3.7», свободная от указанных недостатков [1]. В основе прибора заложены четыре принципиальных отличия от предыдущих конструкций:
1.Применён новый метод, основанный на измерении многоэлементным линейным фотоприемником поперечного размера изображения кабельного изделия, получаемого с помощью стандартного фотографического объектива. Для создания высокой контрастности изображения используется контровая подсветка измеряемого объекта линейкой светодиодов. Оптическая схема прибора

Современные техника и технологии 2007
представлена на рис.1. Двухкоординатное измерение диаметра обеспечивается установкой в приборе двух одинаковых измерительных систем, измерительные оси которых ортогональны.
2.Из оптической схемы исключены широкоапертурные элементы линзовой или зеркальной оптики вместо которых используется недорогой стандартный объектив при помощи которого изображение измеряемого объекта проецируется на плоскость фотоприёмника с известным масштабным коэффициентом, что позволяет используя фотоприёмники стандартной длины измерять объекты поперечником до 200 мм.
3.Для повышения достоверности измерения диаметра и для определения овальности, измерение проводится одновременно относительно двух осей поперечного сечения кабеля. Это осуществляют два измерительных канала с взаимно перпендикулярными осями.
4.Реализована совместная обработка данных двух измерительных каналов и их взаимная коррекция, чем устраняется погрешность, вызванная поперечными перемещениями измеряемого кабеля.
Вприборах использующих проекционную схему измерений диаметр рассчитывается по алгоритму, заложенному в программу расчёта. При перемещениях объекта в рабочей зоне размеры его изображений на линейках так же меняются и чтобы отследить эти изменения требуется двухкоординатное измерение. То есть когда по первому каналу измеряется диаметр объекта по другому отслеживается его положение, а каждая из линеек по очереди является откалиброванной шкалой своеобразной координатной осью.
Для совместной обработки сигналов от двух измерительных осей и правильного определения диаметров в такой системе должены быть выявлены законы по которым они рассчитывается и разработан метод настройки и юстировки прибора
На рис. 2 показан типичный видеосигнал с ПЗС линейки, который и представляет собой проекционное изображение измеряемого объекта. Для расчёта диаметра используется положения фронтов F и спадов S.
Зная параметры F и S по первой и второй координате мы можем определить:
1.размер изображения D*=S1−F1 объекта
вячейках для первой оси.
2. положение центра объекта C=
F+ S
2 относительно второй измерительной
оси. Таким образом, с известным масштабным коэффициентом, и измеренным диаметром объекта в ячейках по первой оси и его смещением по второй оси используя совместную обработку данных можно определить истинное значения диаметра контролируемого объекта.
Комплект измерителя содержит два устройства: измерительную головку и выносной блок индикации.
Измерительная головка представляет собой законченное устройство, имеющее собственный сетевой источник питания и встроенный цифровой индикатор «Диаметр/Овальность». Головка устанавливается с помощью монтажных узлов в технологической линии изготовления кабеля, труб, пищевой оболочки и др. Через рабочую зону головки проходит контролируемое изделие. Измерение производится непосредственно во время его движения, при этом на встроенном индикаторе отображается средний диаметр либо овальность.
С целью сохранения неизменным взаимного положения элементов измерительных каналов, элементы установлены на жесткой силовой раме. Для защиты от пыли и влаги оптические элементы закрыты защитными стеклами. От механических повреждений движущимся кабелем конструкция головки защищена износостойкими накладными полукольцами.
Рис 3. Внешний вид типового комплекта двухкоординатного измерителя диаметра кабеля «Цикада-3.7» (1-измерительная головка Цикада-3.71., 2-блок индикации БИ-2.62Д.,
Рис. 2 Видеосигнал многоэлементного 3,4-стойки., 5-измеряемый объект.) приёмника
247

XIII Международная научно-практическая конференция «СОВРЕМЕННЫЕ ТЕХНИКА И ТЕХНОЛОГИИ»
Установка измерительной головки осуществляется с помощью регулируемой стойки и поворотного узла. Последний позволяет быстро выводить измерительную головку из зоны движения кабеля «на ходу» и быстро возвращать её в рабочее положение.
Для удобства работы оператора технологической линии, рабочее место которого удалено от места установки измерительной головки, в комплект измерителя входит выносной блок индикации. Блок размещается на рабочем месте оператора. Связь выносного блока с измерительной головкой осуществляется по двухпроводной цифровой линии связи.
Основные характеристики измерителя:
•Диапазон |
измеряе- |
5…70 мм. |
|
мых диаметров |
|
|
|
•Погрешность |
изме- |
± 60 мкм. |
|
рения |
|
|
|
•Длительность |
цикла |
3 мс. |
|
одиночного измерения |
~220 В,50 |
||
•Питание |
измерителя |
||
– промышленная сеть |
Гц. |
Опыт разработки и практического использования проекционного устройства измерения диаметра кабеля показал, что применение измерительной схемы (рис.1) и её реализация
на современной элементной базе с использованием полупроводниковых светодиодных излучателей позволяют создать высокоэффективное измерительное устройство, удовлетворяющее требованиям производства.
Опытные образцы измерителя «Цикада 3.7» (рис.3) прошли широкую опытнопромышленную проверку при контроле диаметров цилиндрических изделий, которая подтвердила их технические характеристики и высокие эксплуатационные свойства. На основе таких измерителей могут создаваться системы контроля изделий сложной формы.
Вышеописанный прибор положил начало целой серии разработок светодиодных измерителей диаметра с улучшенными характеристиками и с зоной измерения до 200 мм, которые также востребованы отечественной промышленностью.
ЛИТЕРАТУРА:
1.Приборы технологического контроля для кабельного производства. Каталог продукции «ЭРМИС-2003». Томск, 2003.
2.Свендровский А. Р. Гладышев Ю. Г. Серия измерителей диаметра «Цикада» для протяженных круглых изделий // Новейшие технологии в приборостроении: Труды Российской научно-технической конференции. –
Томск, 1999. – Т. 2. – с. 72-75.
ИСПОЛЬЗОВАНИЕ ИНДУКЦИОННОГО МЕТОДА ПРИ ПОИСКЕ РАЗЛИЧНЫХ ДЕФЕКТОВ В КАБЕЛЬНЫХ ЛИНИЯХ
Чакилева Е.Е.
Томский Политехнический Университет
E-mail: kofein21@yandex.ru
Определение мест повреждения в кабельных линиях - это сложная взаимосвязанная система операций. Каждая операция позволяет решить конкретную задачу из всей процедуры определения места повреждения посредством использования определенных приборов.
Необходимая приборная обеспеченность зависит от вида обслуживаемых линий: силовые или связные, контроля и управления, а также от вида кабельной трассы: подземные, в коробах, в шахтах, в метро и т.д.
Определение мест повреждения кабельных линий обычно проводится в определенной последовательности:
Выделение из всех жил (пар) кабеля по-
248
врежденной жилы (пары);
•Предварительная обработка места повреждения;
•Определение зоны нахождения места повреждения дистанционными методами (измерения с одного конца);
•Поиск места трассы на местности (если необходимо);
•Поиск места повреждения на трассе кабельной линии.
Всоответствии с установившейся практикой определяют место повреждения в два приема: сначала определяют зоны повреждения кабельной линии, затем уточняется место повреждения в пределах зоны. На первом этапе определение места повреждения про-

Современные техника и технологии 2007
изводится с конца линии, на втором этапе - непосредственно на трассе. [1]
Наиболее распространенный случай – это повреждение между жилой и оболочкой кабеля или искровой пробой между жилами, т.е. однофазные повреждения, особенно для кабелей с жилами в самостоятельных оболочках.
Для непосредственного поиска на трассе кабеля мест подобных повреждения, для определения трассы и глубины залегания кабеля, для определения местоположения соединительных муфт, чаще всего используют индукционные искатели повреждений. Они, по сути, являются единственным видом приборов, пригодным для точного, с погрешностью
± (10-20) см определения места повреждения, прохода трассы кабеля и определения глубины залегания кабеля.
Метод накладной рамки – это одна из разновидностей индукционного метода. Этот метод применяют для непосредственного обнаружения места повреждения кабеля. Метод удобен при открытой прокладке кабеля; при прокладке в земле необходимо открыть несколько шурфов в зоне повреждения. Метод основан на том же принципе, что и индукционный. Генератор подключают к жиле и оболочке или между двумя жилами. На кабель накладывают рамку и поворачивают ее вокруг оси. До места повреждения будут прослушиваться два максимума и два минимума сигнала от поля пары токов. За местом повреждения при вращении рамки будет прослушиваться монотонный сигнал, обусловленный магнитным полем одиночного тока.
Сущность индукционного метода заключается в фиксации с поверхности земли с помощью приемной рамки характера изменения электромагнитного поля над кабелем при пропускании по нему тока звуковой частоты (800 – 1200 Гц) от долей ампера до 20 А в зависимости от наличия помех и глубины залегания кабеля. ЭДС, наводимая в рамке зависит от токораспределения в кабеле и взаимного пространственного расположения рамки и кабеля. Зная характер изменения поля, можно при соответствующей ориентации рамки определить трассу и место повреждения кабеля.линии. В связи с этим методы соответственно разделяются на дистанционные (относительные) и топографические (абсолютные).
Важное значение для индукционного метода имеет выбранный диапазон рабочих частот. Для всех индукционных методов, применяется так называемый звуковой (тональный) диапазон частот. Для линий, включенных в сеть, практически используются промышленная частота 50 Гц и ее нечетные
гармоники вплоть до 13-й. Для отключенных кабельных линий частотный диапазон составляет 0,4…12 кГц. [2]
Соответственно верхнюю границу частоты сигнала целесообразно выбирать равной
6500 Гц.
Погрешность определения места замыкания между жилами индукционным методом с поверхности земли не превышает ±0,5 м, а при работе на открытом кабеле составляет несколько сантиметров. Индукционный метод определения места замыкания между жилами (или замыкания двух жил на оболочку в одной точке кабеля) весьма эффективен, поскольку до места повреждения есть периодическое (в соответствии с шагом скрутки) изменение сигнала, за местом повреждения этого изменения нет, и в подавляющем большинстве случаев за местом повреждения принимаемый сигнал уменьшается в десятки раз.
Силовые линии поля тока «жила-земля» представляют собой концентрические окружности, центром которых является ось кабеля (поле одиночного тока). При использовании цепи «жила-жила» ток, идущий по прямому и обратному проводам, создает два концентрических магнитных поля, действующих в противоположных направлениях (поле пары токов). При расположении жил в горизонтальной плоскости результирующее поле на поверхности земли наибольшее, а при расположении жил в вертикальной плоскости — наименьшее. Поскольку кабели имеют скрутку жил, то в рамке, расположенной вертикально и перемещаемой вдоль трассы кабеля, будут индуцироваться ЭДС, изменяющиеся от минимума до максимума. При поиске повреждения необходимо помнить, что сигнал за местом повреждения затухает на расстоянии не более половины шага.
Рис 1. Изменение интенсивности электромагнитного поля кабеля
Посредством обнаружения магнитного
249

XIII Международная научно-практическая конференция «СОВРЕМЕННЫЕ ТЕХНИКА И ТЕХНОЛОГИИ»
поля обнаруживают наличие кабельной линии, а посредством измерения поля определяют местоположение кабельной линии, глубину ее залегания и место повреждения.
Перпендикулярное к поверхности земли расположение катушки позволяет получить резко выраженный минимум сигнала, который на практике используется для точного определения местонахождения кабеля.
Рис 2. Электрическое поле одиночного кабеля
Скрутка жил кабеля с шагом повива – от 0,5 до 3 м в зависимости от сечения жил. В соответствии с этим шагом изменяется напряженность результирующего магнитного поля на поверхности земли над кабелем.
Для эффективного обнаружения трасс кабельных линий и точного определения мест повреждения на трассе обычно используют специальные индукционные комплекты приборов, состоящие из генератора звуковых частот и индукционного приемника.
Для точного определения места повреждения генератор включают в режим непрерывной генерации и начинают двигаться вдоль кабельной линии с индукционным приемником, у которого ось поисковой катушки расположена параллельно поверхности земли и перпендикулярно направлению движения (трассе кабельной линии).
При движении с индукционным приемником вдоль трассы кабельной линии слышимость кабельной линии будет периодически ослабевать и усиливаться. Это объясняется наличием повива жил кабельной линии. Из-за повива жил преобладание на поверхности земли магнитного поля одной жилы периодически меняется на преобладание противоположного магнитного поля от другой жилы.
Над муфтами и другими неоднородностями интенсивность магнитного поля изменяется. В местах кабельных муфт расстояние между соседними жилами увеличивается, поэтому создаваемые жилами поля меньше компенсируют друг друга. Скрутка жил в этих местах отсутствует. Все это приводит к увеличению интенсивности магнитного поля над кабельной муфтой.
Вместах, где кабельная линия плавно уходит на большую глубину наблюдается плавное уменьшение интенсивности магнитного поля.
Вместе короткого замыкания между жилами кабельной линии ток от индукционного генератора меняет свое направление, структура магнитного поля вокруг кабеля изменяется и компенсация от жил проявляется более слабо. Поэтому над местом повреждения интенсивность магнитного поля усиливается
истановится нулевой после места повреждения.
Несмотря на то, что полевые индукционные искатели используются давно и относительно распространены, существует проблема применения подобного метода в технологическом цикле, непосредственно на производстве, то есть его автоматизация. Связано это, прежде всего с другими требованиями к проверке и другими условиями. Высокая скорость и отсутствие оператора, предполагает совсем иной подход, нежели к проверке кабеля при его эксплуатации.
ЛИТЕРАТУРА:
1.Привезенцев В.А. Основы кабельной техники М.: Энергия, 1975—472 с.
2.Дементьев В.С. Как определить место повреждения в силовом кабеле. М.: Энергия, 1980—73 с
250

Современные техника и технологии 2007
РАЗРАБОТКА КОРРЕЛЯЦИОННОГО ТЕЧЕИСКАТЕЛЯ
Чан Вьет Тьяу, Аврамчук В.С.
Томский политехнический университет, Россия, г.Томск, пр. Ленина, 30
E-mail: tranvietchau@yahoo.com
Оперативное и точное определение мест утечек воды из трубопровода горячего и холодного водоснабжения является актуальной задачей коммунальных служб на территории Российской Федерации, это обусловлено значительным износом водопроводных коммуникаций. Потери воды при транспортировке к потребителю достигают 30 %, основные причины этих потерь – мелкие утечки воды из трубопроводов. Локализация точного места утечки значительно снижает эксплуатационные затраты на восстановительные и земляные работы. В городах водопроводные коммуникации расположены практически повсеместно, проходят под дорожными покрытиями, подведены к зданиям, непосредственно вблизи жилых домов и других сооружений. Вовремя не обнаруженная утечка воды может привести к разрушению дорожного полотна, зданий и повлечь за собой человеческие жертвы.
В настоящее время существует два основных и широко распространенных метода поиска утечек в трубопроводах водопроводных и тепловых сетей: акустический и корреляционный. Акустический метод имеет достаточно широкое распространение, базируется на пошаговом прослушивании трубопровода (с поверхности земли если трубопровод нахдится под землей) с целью выявления места утечки, генерирующей шум. Использование приборов основанных на акустическом методе эффективно внутри зданий и на коротких трубопроводах с небольшой глубиной залегания. При больших глубинах прокладки трубопроводов или высоком уровне сторонних шумов применение таких приборов малоэффективно.
Вторым и наиболее перспективным методом поиска утечек в городских условиях является корреляционный метод, основанный на расчете взаимной корреляционной функции двух виброакустических сигналов поступающих с двух вибродатчиков установленных с двух сторон от анализируемого участка трубопровода. Взаимная корреляционная функция rXY[k] характеризует тесноту связи между значениями двух дискретных сигналов Xj и Yj со сдвигом, равным k, и вычисляется по формуле:
|
|
|
1 |
N −1−k |
|
|
|
|
||
r |
XY |
[k] = |
∑ |
X |
j+k |
Y |
j |
(1) |
||
N − k |
||||||||||
|
|
|
|
|
||||||
|
|
|
|
|
|
|
|
|||
|
|
|
|
j=0 |
|
|
|
|
|
где N – размер выборки сигналов.
Для реальных сигналов (не комплексных), представленных в дискретном виде, взаимную корреляционную функцию можно вычислить следующим образом:
-прямое преобразование Фурье [2] для данных функций;
-попарное умножение полученных результатов;
-обратное преобразование Фурье [2] для результатов умножения.
Воснову разрабатываемого течеискателя заложен корреляционный метод обнаружения утечек воды в трубопроводах и определения мест их расположения, более сложный но в то же время более точный, быстрый и достаточно эффективный. Данный метод основан на измерении виброакустического сигнала, генерируемого утечкой, с помощью двух датчиков, установленных непосредственно на трубопроводе (рис. 1). Если два датчика установить с двух сторон от предполагаемого места утечки то в этом случае можно определить разницу (задержку) t по времени распространения сигнала от утечки до одного и до второго датчика с помощью взаимной корреляционной функции. Тогда, зная скорость распространения звука по трубе v можно вычислить расстояние x от утечки до центра исследуемого участка трубы, расположенного между датчиками по формуле:
|
x = |
v |
t |
(2) |
||||||
|
|
|
|
|
|
|||||
или |
|
|
2 |
|
|
|
|
|||
|
l |
|
|
v |
t |
|
|
|||
x |
= |
− |
, |
(3) |
||||||
|
|
|
||||||||
1 |
2 |
2 |
|
|
|
|
||||
|
|
|
|
|
где x1 – растояние от утечки до датчика 1, l – растояние между датчиками.
Рис. 1. Схема трубопровода с утечкой и установленными датчиками
251

XIII Международная научно-практическая конференция «СОВРЕМЕННЫЕ ТЕХНИКА И ТЕХНОЛОГИИ»
Разрабатываемый прибор состоит из следующих компонентов: два виброаккустических датчика (виброакселлерометр), два радиомодема и программное обеспечение, предназначенное для обработки поступающих данных, установленное на ЭВМ. Модем, непосредственно подключаемый к ЭВМ, называется “master”, а второй – “slave”. Модем- “master” подключен к компьютеру через 2 COM-порта. К каждому радиомодему подключен один датчик, связь между модемами организована по радиоканалу. Схема подключения показана на рис. 2.
Рис. 2. Схема подключения Поступающие с датчиков данные дискретизируются и передаются по радиоканалу в ЭВМ, подвергаются прямому преобразованию Фурье, результаты преобразования умножаются и затем подвергаются обратному преобразованию Фурье. По графику взаимной корреляционной функции можно определить, есть ли задержка между сигналами первого и второго датчиков и найти ее величину. На рис. 3 приведен график взаимной корреляционной функции с ярко выраженной задержкой
t.
Рис. 3. График взаимной корреляционной функции
По значению задержки, скорости распространения звука по трубе и расстояния между датчиками по формуле (1) можно вычислить расстояние от середины исследуемого участка трубы до утечки, а по формуле (2) - расстояние от датчика 1 до утечки.
Исходя из описанной методики, разрабатывается программное обеспечение, которое имеет модульную структуру и состоит из следующих программных модулей:
1)интерфейс пользователя;
2)формирование команд и прием данных;
3)загрузка и сохранение анализируемых данных из файла / в фай;
3)ввод данных из звуковой карты;
4)обработка данных;
5)вывод результатов анализа и построение графиков;
6)расчет координат утечки.
Рассмотрим более подробно каждый модуль. В первом модуле реализован графический интерфейс пользователя. В модуле формирования команд и получения данных формируются команды запуска оцифровки сигналов с датчиков, калибровки модемов, а также реализована передача данных из модемов в ЭВМ. Модуль загрузки и сохранения анализируемых данных из файла / в файл преднозначен для загрузки анализируемых данных из звуковых файлов формата WAV и собственного формата. Разрабатываемый программный комплекс позволяет принимать данные не только через COM-порты но и через звуковую карту с помощью разработанного модуля ввода данных из звуковой карты, который позволяет получить цифровой звуковой поток из выбранных WaveIn-устройств с выбранной частотой дискретизации. В модуле обработки данных реализованы прямое и обратное преобразования Фурье, а также фильтрация. Модуль вывода результатов анализа позволяет выводить данные на экран ЭВМ в виде графиков.
Вкачестве средства разработки программного комплекса был выбран язык программирования Object Pascal и интегрированная среда программирования Borland Delphi.
Влитературе [3] подробно описаны особенности, рекомендации и этапы разработки программных комплексов. При написании программного комплекса были учтены эти рекомендации.
Вдальнейшем планируется провести:
-оптимизацию разработанных алго-
ритмов;
-реализацию алгоритма быстрого преобразования Фурье с произвольной длиной массива данных;
-реализацию алгоритмов фильтрации;
-разработку методики по поиску и локализации утечек в зависимости от местоположения утечки по отношению к датчикам.
Разработка корреляционного течеискателя осуществляется в рамках Межвузовского студенческого бизнес-инкубатора «Дружба», созданного при Государственном образова-
252

|
|
Современные техника и технологии 2007 |
тельном учреждении высшего профессио- |
[1] Марпл - мл. С.Л. Цифровой спектраль- |
|
нального образования «Томский государст- |
ный анализ и его приложения. /Пер. с англ. - |
|
венный университет систем управления и ра- |
М.: Мир, 1990. - 584 с |
|
диоэлектроники». Наименование научно- |
[2] Нуссбаумер Г. Быстрое преобразова- |
|
технического проекта “Прибор для обнаруже- |
ние Фурье и алгоритмы вычисления свертки. - |
|
ния мест утечек в водопроводных и тепловых |
М.: Радио и связь, 1985. - 248 с. |
|
сетях”, руководителем проекта является Ав- |
[3] Брукс Ф.П. мл. Как проектируются и |
|
рамчку В.С. |
создаются программные комплексы. Мифиче- |
|
|
|
ский человеко-месяц / Пер. с англ. |
|
ЛИТЕРАТУРА: |
Н.А.Черемных. - М.: Наука, 1979. - 152 с. |
МНОГОКАНАЛЬНОЕ УСТРОЙСТВО СБОРА ИНФОРМАЦИИ И ДАННЫХ ОПТИКОЭЛЕКТРОННОЙ ДИАГНОСТИЧЕСКОЙ СИСТЕМЫ
Чебыкина А.А., Зюбанов И.И., Миляев Д.В.
Томский политехнический университет,
Россия, г. Томск, ул. Ленина, 30. E-mail: mi_sol@mail.ru
Предлагается оптико-электронное устройство, которое применяется для диагностического исследования функциональных заболеваний пищевода. Совокупность оптикоэлектронного метода и устройства для его диагностики обеспечивает всеми необходимыми требованиями и может быть эффективным дополнительным инструментом для диагностики патологий пищевода.
При исследовании двигательной функции оптоэлектронный зонд вводят в полость пищевода. Сигнал, излучаемый ИК источником излучения, отражается от стенок пищевода. Сокращения стенок вызывают изменение интенсивности отраженного светового потока, который с помощью ИК приемников регистрируется и передается в электронный блок диагностического комплекса, который в дальнейшем усиливается, фильтруется и передается, как на самопишущие устройство, так и через АЦП по интерфейсу RS-232 на персональный компьютер. По изменению амплитуды, частоты и формы регистрируемого сигнала диагностируют функциональное нарушение пищевода.
Для работы с многоканальной информационной системой используется структура сбора данных с мультиплексированием каналов (рис.1).
Рисунок 1. Система сбора данных с мультиплексированием каналов.
Основной задачей при разработке многоканального устройства оптикоэлектронного диагностического комплекса является сбор аналоговой информации с целью преобразовании в цифровую форму и последующей передачей на персональный компьютер (ПК).
Основные характеристики устройства:
1. |
Число каналов |
7 |
2. |
Разрядность АЦП |
8/10 |
3. |
Скорость передачи |
115,2 |
данных на ПК |
кбит/с |
В разрабатываемом устройстве реализован сбор информации семью аналоговыми каналами со скоростью изменения сигналов до 10 Гц. Два канала используются для сбора информации с датчиков температур, обладающих гораздо большей инерционностью. Это позволяет нам обновлять их информацию со скоростью порядка 1 Гц. Для канала
253
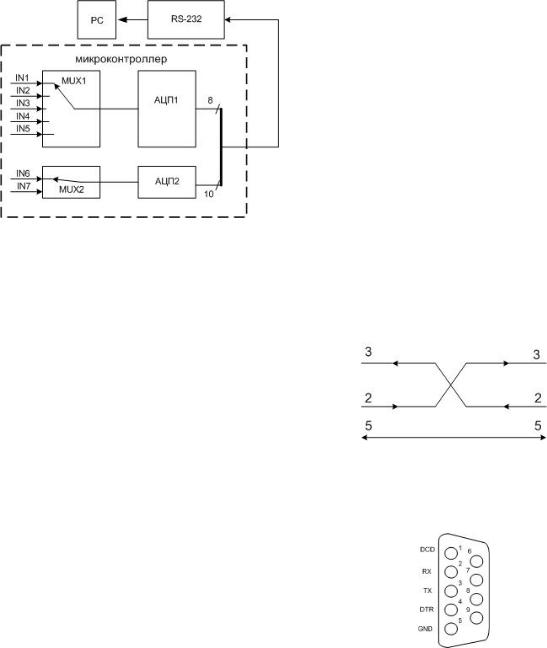
XIII Международная научно-практическая конференция «СОВРЕМЕННЫЕ ТЕХНИКА И ТЕХНОЛОГИИ»
измерения температуры точность аналогоцифрового преобразования должна быть не менее 10 разрядов. Для сбора информации с оставшихся каналов достаточна точность преобразования 8 разрядов. Связь устройства с ПК осуществляется по интерфейсу RS232. На рис.2 приведена структурная схема разрабатываемой системы сбора информации. Микроконтроллер (МК) осуществляет коммутацию аналоговых мультиплексоров MUX1, MUX2 на входы аналого-цифровых преобразователей АЦП1, АЦП2, имеющих разрядность 8 и 10 бит соответственно. Результат аналого-цифрового преобразования передается через интерфейс RS-232 на компьютер.
Рисунок 2. Схема сбора данных. Для реализации устройства будем ис-
пользовать микроконтроллер, сочетающий в себе следующие возможности:
1- встроенный 6-канальный 10разрядный АЦП с мультиплексированием входов;
2- интерфейс SPI, позволяющий объединять микроконтроллеры на одной шине;
3- малое энергопотребление;
4- низкая стоимость кристалла.
Для организации 7-канальной системы было решено использовать 2 микроконтроллера, объединив их по интерфейсу SPI.
Микроконтроллер DD2 осуществляет сбор информации с датчиков температуры. Каждую секунду в нем генерируется прерывание и осуществляется последовательное анало- го-цифровое преобразование для двух каналов. После этого данные преобразования передаются по интерфейсу SPI на микроконтроллер DD1, который находиться в режиме ожидания приема команды «начать преобразование» с компьютера. При поступлении этой команды DD1 осуществляет аналогоцифровое преобразование для 5 каналов и передает на компьютер ответный пакет данных, содержащий результаты преобразова-
ния всех 7 каналов. По окончании передачи ответного пакета DD1 снова входит в режим ожидания. Микросхема DA2 осуществляет согласование логических уровней ТТЛ c сигналами интерфейса RS-232.
Стабилитроны VD1-VD7 служат для защиты входов АЦП от перегрузки. Опорное напряжение равно напряжению питания устройства. Выходные коды АЦП для каналов 1- 7, соответственно, равны:
N8 |
= |
Uin 256 |
|
|
|
U REF |
|||||
|
|
||||
N10 |
= |
Uin 1024 |
. |
||
|
|||||
|
|
UREF |
Частота работы МК должна быть кратна скорости передачи. Микроконтроллер DD1 имеет тактовую частоту 1.8432 МГц, необходимую для работы интерфейса RS-232, что позволяет минимизировать сборы передачи информации.
Интерфейс RS-232С соединяет два устройства. Линия передачи первого устройства соединяется с линией приема второго и наоборот. Для управления соединенными устройствами используется программное подтверждение (введение в поток передаваемых данных соответствующих управляющих символов).
Данные в RS-232С передаются в последовательном коде побайтно. Каждый байт обрамляется стартовым и стоповым битами. Данные могут передаваться как в одну сторону, так и в другую (дуплексный режим).
При согласовании диагностического комплекса с компьютером, используем трехпроводную связь для двунаправленной передачи данных (рис.3).
Рисунок 3. Схема трехпроводной линии связи для RS-232.
В нашем случае мы пользуемся 9- контактным разъемом (DB9P), в котором используем 2, 3, 5 ножки (рис.4).
Рисунок 4. Разъем интерфейса RS-232 (9- контактный).
254

|
|
|
|
Современные техника и технологии 2007 |
|
2- RxD – данные, принимаемые компью- |
2. |
Гюнтер С.В. Оптико-электронная сис- |
|
тером в последовательном коде (логика от- |
тема регистрации функциональных заболе- |
|||
рицательная); |
ваний пищевода. ТПУ, 2006. – 136. |
|||
|
3- TxD – данные, передаваемые компью- |
3. |
Новиков Ю.В. Разработка устройств |
|
тером в последовательном коде (логика от- |
сопряжения для персонального компьютера |
|||
рицательная); |
типа IBM PC. – М.:ЭКОМ, 1999. – 204с. |
|||
|
5 – окончание. |
4. |
Компьютерный измеритель двига- |
|
|
|
|
тельной функции ЖКТ. |
|
|
ЛИТЕРАТУРА: |
Дылгырова В.Д., Миляев Д.В., |
||
1. |
Гутников В.С. Интегральная электро- |
Труды 12-й международной научно- |
||
ника |
в измерительных устройствах. - |
практической конференции студентов, аспи- |
||
М.:Энергоатомиздат, 1998.-304с. |
рантов и молодых ученых «Современные |
|||
|
|
|
техника и технологии», 2006г. |
СОВРЕМЕННЫЕ МЕТОДЫ ЛОКАЦИИ ВНУТРИТРУБНЫХ УСТРОЙСТВ
Шахов В.Ю., Кузнецов С. А. Солдатов А.И. Томскийполитехническийуниверситет, Россия, г.Томск, пр. Ленина30
E-mail: shakhov@sibmail.com
Важнейшее направление повышения надежности, безопасности и экономической эффективности эксплуатации магистральных нефтепроводов - внедрение новых средств автоматизации мониторинга технического состояния. Развитие этого направления особенно актуально в условиях неравномерной перекачки, при значительном износе и физическом старении некоторых участков нефтепроводов.
Повышение надежности, безопасности и эффективности эксплуатации нефтепроводов достигается различными способами, среди которых можно выделить: использование внутритрубной диагностики с последующим устранением обнаруженных дефектов, очистка внутренней поверхности трубопроводов от отложений, что снижает затраты на транспортировку нефти, применение разделителей потока при транспортировке партий нефти с различными физико-химическими свойствами, использование герметизирующих устройств, при ремонте нефтепроводов. Все эти способы требуют использования внутритрубных снарядов, движущихся с потоком нефти: диагностических устройств, скребков, разделительных поршней, герметизаторов и др.
Основная проблема, связанная с использованием внутритрубных устройств, - определение их точного местоположения при движении в трубопроводе в реальном времени, или, другими словами, проблема сопровождения снарядов. Знать положение устройства
необходимо также в случае его остановки или застревания, чтобы целенаправленно и с наименьшими затратами организовать его извлечение либо проталкивание [1].
Решение данной проблемы возможно несколькими способами. Местоположение движущегося внутритрубного снаряда можно попытаться определить, используя показания датчиков давления, установленных на нефтепроводе. В этом случае точность определения местоположения снаряда определяется расстоянием между соседними датчиками (на нефтепроводах это десятки километров), а также достоверностью их показаний.
Более технологичный способ – установка в контрольных точках акустических сигнализаторов. Например, ООО Научно-техническая фирма «ВОСТОКнефтегаз» выпускает прибор «СЕНСОР» предназначенный для акустического контроля движения и прохождения по трубопроводам очистных и диагностических снарядов в произвольных точках трассы трубопровода с поверхности грунта над трубопроводом. Принцип работы основан на акустической эмиссии движущегося внутритрубного устройства. Прибор позволяет зарегистрировать движение внутритрубного устройства в диапазоне до 2500м, однако не способен определять расстояния [2].
Рассмотренные методы являются самыми простыми по реализации, однако не позволяют дать высокую точность определения местоположения внутритрубного устройства.
255

XIII Международная научно-практическая конференция «СОВРЕМЕННЫЕ ТЕХНИКА И ТЕХНОЛОГИИ»
Приборы на основе низкочастотных электромагнитных полей позволяют с более высокой точностью определить местоположение внутритрубного устройства. Однако при использовании электромагнитных колебаний возникают трудности связанные с колоссальным экранирующим действием стальной трубы, что препятствует изготовлению локаторов на большие расстояния [3].
Подобное устройство для поиска и определения местонахождения с поверхности грунта застрявших и контроля прохождения движущихся очистных и диагностических устройств выпускает ООО Научно-техническая фирма «ВОСТОКнефтегаз» - это прибор серии «Поиск–МП». Условия устойчивого приема сигналов передатчика для «Поиск–МП-Н» (НЕФТЬ) при наружном диаметре трубопровода до 1220 мм: толщина стенки трубопровода - до 16 мм; удаление приемной антенны от передатчика - до 10 м вдоль оси трубопровода и до 6 м от продольной оси трубопровода; скорость прохождения снаряда по трубопроводу - 2 м/с [4].
Акустическая локация внутритрубных устройств на большие расстояния, затрудняется большим количеством акустических шумов в трубопроводе. Как показано в работе [5] амплитуда шума в частотном диапазоне выше 100 кГц не превышает собственных шумов аппаратуры, поэтому использование частоты УЗК 100 кГц позволяет получить приемлемую точность определения расстояния до объекта.
Осуществлять локацию на большие расстояния, а так же сопровождать внутритрубные устройства, позволяет разработка научно - производственной фирмой «ТОРИ», показанная на рис.1.
Акустический излучатель ИП-001 (рис. 1) перед запуском в нефтепровод закрепляется на последнем фланце очистного устройства. Во время движения снаряда в трубопроводе он излучает с определенной периодичностью пакеты звуковых сигналов.
Посылаемые излучателем звуковые сигналы в трубопроводе, заполненном нефтью, передаются
Рис. 1. Система сопровождения внутритрубных снарядов «ССВС-001»:
1 - нефтепровод
2 - акустический излучатель ИП-001;
3 - внутритрубный снаряд;
4.- модуль обработки и передачи сигнала МОПС-001; 5 - линия связи;
6 - центральный компьютер;
7- сигнальный кабель;
8- модуль первичного преобразования МПП-
как в волноводе и принимаются акустическим датчиком модуля МПП-001 (рис. 1), в котором происходит фильтрация акустического сигнала и его усиление до необходимой амплитуды. В дальнейшем происходит цифровая обработка полученного сигнала, выделение акустического образа, посылаемого излучателем на внутритрубном устройстве, накопление информации о ходе сопровождения, расчет скорости и местоположения снаряда. Система «ССВС-001» позволяет сопровождать внутритрубные устройства на расстояния до 100 км и имеет заявленную погрешность определения расстояния 3% [1].
К недостаткам этой системы можно отнести непрерывную работу акустического излучателя, стационарность, обусловленную фланцевым соединением модуля первичного преобразования к трубопроводу.
Использование активного эхоимпульсного ультразвукового метода позволяет решить сразу и вопрос локации внутритрубного устройства, а так же возможную задачу информационного обмена. Для этогонеобходимо правильно выбрать рабочую частоту колебаний, определить наиболее оптимальный способ ввода колебаний в рабочую среду и положение приемопередатчика на внутритрубном устройстве.
Использование активного эхоимпульсного метода позволяет реализовать систему локации, без нарушения сплошности трубопровода. Структурная схема подобного устройства представлена на рис. 2.
Акустический излучатель 8 (рис. 2) излучает, генерируемую модулем управления пачку импульсов, которая распространяясь по трубопроводу регистрируется излучателем/ приемником 2.
256

Современные техника и технологии 2007
Рис. 2. Система эхо-акустической локации внутритрубных устройств: 1 - нефтепровод
2– активный акустический излучатель/приемник;
3- внутритрубный снаряд;
4- модуль управления;
5- линия связи;
6- центральный компьютер;
7- сигнальный кабель;
8– акустический излуча-
тель/приемник; В ответ излучатель/приемник генерирует
ответный сигнал, который впоследствии фиксируется излучателем/приемником 8. Блок управления выделяет полезную составляющую сигнала, фильтруя шумовой фон и на основании полученной задержки оценивает расстояние до объекта.
Такая система собранна в виде экспериментального макета на кафедре ПМЭ ТПУ и для нее построена математическая модель, описывающая характер распространения ультразвуковых колебаний от источника, располагающегося на поверхности трубопровода к приемнику, находящемуся внутри. Предварительные экспериментальные исследования, доказали возможность определения положения устройства с точностью порядка
0,5%.
ЛИТЕРАТУРА:
1.В.В.Супрунчик, Н.М. Коновалов, М.О. Мызников. Система Сопровождения Внутритрубных Снарядов «ССВС-001». //Трубопроводный транспорт нефти -2003г.,
№12, стр.9-12.
2.патент РФ № 2137977
3.Волин М.Л. Паразитные процессы
врадиоэлектронной аппаратуре. - 2-е изд. пераб. и доп., М: Радио и связь, 1981.-296 с., ил
4.патент РФ № 2110729
5.Лапшин Б.М. Разработка и создание акустических средств контроля герметичности подводных трубопроводов. – Дисс. канд. тех. наук – Томск, ТПИ,1986.- 244с.
ПРИБОР ДЛЯ ИЗМЕРЕНИЯ ФОРМЫ ПОВЕРХНОСТИ КРУПНОГАБАРИТНЫХ ДЕТАЛЕЙ
Ширинкин А.А., Полунин А.И.
Белгородский государственный технологический университет им. В.Г. Шухова, Россия, г. Белгород. ул. Костюкова 46
E-mail: shirinkin@inbox.ru
При изготовлении крупногабаритных пространственных изделий одной из проблем является точное определение формы этого изделия в заданных сечениях. Их решение осложнено рядом особенностей, к которым относятся:
•значительные размеры объектов измерения;
•индивидуальный характер производства, способствующий созданию такого многообразия, подлежащих измерению размеров.
В настоящее время средства контроля больших длин и больших диаметров представляют собой простое копирование средств измерения, применяемых в машиностроении
для определения размеров до 500 мм, поэтому измерительные средства являются громоздкими, тяжелыми и неточными. Увеличение жесткости инструмента неизбежно вызывает увеличение его габаритных размеров и массы. Наиболее широко распространены линейные скобы, изготовленные из труб. Они применяются для размеров до 6000 мм, но при длине скоб свыше 2500 мм результаты произведенных ими измерений являются неточными. Это объясняется тем, что скобы указанной длины не имеют достаточную жесткость, вследствие чего нарушается параллельность измерительных губок и в результаты измерений вносится большая погреш-
257

XIII Международная научно-практическая конференция «СОВРЕМЕННЫЕ ТЕХНИКА И ТЕХНОЛОГИИ»
ность.
.Поэтому они является дорогостоящими, громоздкими, тяжелыми и неточными. Для контроля качества поверхности сложной формы используют специальные шаблоны.
Одним из путей, который позволит избавиться от необходимости применения различных шаблонов, является использование системы автоматизированного измерения формы поверхности крупногабаритных деталей, основанное на принципе, изложенном в
[1].
Разрабатываемая система состоит из измерительной части, устройства сопряжения с датчиками (микроконтроллера) и персонального компьютера (Рис. 1).
Рис.1. Система автоматизированного измерения формы поверхности:
1- ленивиц; 2-поддерживающий каток; 3- опорный каток; 4- микроконтроллер;
5-персональный компьютер; 6-датчик угла поворота i-го звена; 7-измеряемая поверхность; 8-ведущие колесо.
Измерительная часть представляет собой гусеницу, состоящую из звеньев. Каждое звено имеет фиксированный размер L и H (рис.2). Угол между L и H равен 90°.
Рис 2. Схема звена гусеницы.
Основная идея заключается в том, что на измерительной базе устанавливаются датчики, определяющие угол поворота i-го звена. Выполняя обкатку измеряемой детали мы получаем N показаний датчиков угла поворота. На основе этой информации, а также зная характеристики звена (т.е. длину и высоту) мы производим интерполяцию поверхности представив её в виде ряда Фурье.
Здесь Ak иBk коэффициенты ряда Фу-
рье. Для оценки неизвестных значений коэффициентов Ak иBk можно использовать ме-
тод максимального правдоподобия [2]. Вектор оцениваемых параметров:
Gτ |
= [A , |
B |
, A |
, B |
,..., |
A , B |
k |
] -размерности |
|
|
|
1 |
1 |
2 |
2 |
|
k |
|
|
|
|
k. |
Вектор |
измерений: |
Rτ |
= [R , R ,..., R ] |
- |
|||||
|
|
|
|
|
|
|
|
1 2 |
n |
|
размерности n. Математическая модель вектора измерений
Разность вектора измерений и его математической модели S(G) ( G – неизвестные
параметры), вычисленной для некоторого значения вектора G является вектором слу-
чайных величин δ = R − S(G) , распределённых по нормальному закону
P(δ G)= |
1 |
|
|
|
|
e |
− |
1 |
[R−S (G)]T KV−1 [R−S (G)] |
|
|
|
|
|
|||||
|
|
|
|
|
2 |
, |
|||
N |
|
KV |
|
|
|||||
|
|
|
|
||||||
|
(2π ) |
|
|
|
|
|
|
|
|
где KV |
– корреляционная матрица, опре- |
деляющая взаимосвязь погрешности измере-
ний Vi .
Нам необходимо найти такое значение вектора G , чтобы отклонение измеренного вектора от вычисленного имело максимальную плотность вероятности.
Максимум этой функции достигается при минимуме следующего выражения
J = [R − S(G)]T KV−1[R − S(G)].
Воспользовавшись условием нахождения минимума, получим систему k уравнений
для вычисления k |
компонент вектора оценок |
||||||||||||
G . |
|
|
|
|
|
|
|
|
|
|
|||
∂S1 |
|
∂S2 |
∂SN |
|
|
||||||||
|
|
|
|
|
|
... |
∂G |
|
|
|
|||
|
∂G |
|
∂G |
|
][R − S(G)]= 0 |
||||||||
|
1 |
|
|
|
1 |
|
|
1 |
|
||||
|
................................... [KV−1 |
||||||||||||
|
∂S |
|
∂S |
2 |
... |
|
∂S |
N |
|
|
|||
1 |
|
|
|
|
|
|
|||||||
|
|
|
|
|
|
|
|
|
|||||
|
∂GK |
∂GK |
|
|
|
|
|
||||||
|
|
∂GK |
|
||||||||||
|
|
Это |
уравнение |
|
называется уравнением |
правдоподобия. Для решения этой системы уравнений наиболее часто используют метод Ньютона, основанный на линеаризации функ-
ции S(G) . Для этого разложим S(G) относительно заданного значения G0 в ряд Тейлора
с учётом только линейных членов разложения:
R(α) = R0 + ∑k Ak sin(kα) + Bk cos(kα)
258

Современные техника и технологии 2007
|
|
|
|
∂S |
|
|
|
∂S |
|
|
|
|
|
|
|
|
|
|
|
|
|
|
1 |
... |
1 |
|
|
|
|
G1 |
|
|
|||
|
|
|
|
|
|
|
|
|
|||||||||
S(G)= |
S(G )+ |
|
|
∂G1 |
∂GK |
|
= |
||||||||||
|
|
........................ |
|
... |
|
||||||||||||
|
0 |
|
∂SN |
|
|
|
∂SN |
|
|
|
|
|
|||||
|
|
|
|
|
|
|
|
|
|
||||||||
|
|
|
|
|
|
... |
|
|
|
|
|
|
|
GK |
|
||
|
|
|
∂G |
|
|
∂G |
|
|
|
|
|||||||
|
|
|
|
|
1 |
|
|
|
|
K |
|
|
|
|
|
||
|
|
|
|
|
|
|
|
|
|
|
|
|
|
|
|
|
|
= S(G |
|
|
|
G1 |
|
|
|
|
|
|
|
|
|
|
|
||
)+ M T |
|
... |
|
|
|
|
|
|
|
|
|
|
|
||||
0 |
|
|
|
|
|
|
|
|
|
|
|
|
|
|
|
|
|
|
|
|
|
G |
K |
|
|
|
|
|
|
|
|
|
|
|
|
|
|
|
|
|
|
|
|
|
|
|
|
|
|
|
|
||
где |
M – матрица первых производных, |
вычисленных при G = G0 .
Подставим эту зависимость в уравнение правдоподобия и выразим G :
G = (MKV−1M T )−1 MKV−1 R , где R = R − S(G).
Мы получили формулу для вычисления величины подшагивания при нахождении век-
тора оценки определяемых параметров G . Вычислив первое подшагивание, определяем и вычисляем новые значения матрицы произ-
водных при G = G1 , где G1 = G0 + G1 , новое значение вектора S(G1 ) и новое значение
подшагивания. Вычисления осуществляются до тех пор, пока величина невязки не станет меньше заданной. Полученное значение и является требуемой оценкой.
Для анализа точности прибора разработана математическая модель, в которой предполагается, что форма поверхности задается в аналитическом виде
R(α) = R0 + ∑k Ak cos(kα) + Bk sin(kα)
Вначале производится вычисление точных значений измеряемых параметров. Затем выполняется их зашумление, после чего вычисляется оценка измеряемых параметров. Сравнение полученных результатов с точными значениями позволяет оценить погрешность прибора и определить факторы, влияющие на нее.
Измерение формы поверхности выполняется следующим образом: при движении измерительной части относительно исследуемой детали 7 (рис. 1) микроконтроллер 4 снимает показания датчиков 6. Персональный компьютер 5 выполняет необходимую обработку полученных. Связь ЭВМ с микроконтроллером осуществляется через последовательный или параллельный порт. Базирование измерительной части прибора относительно поверхности исследуемой детали способствует избавлению от дополнительных погрешностей измерения.
Основным достоинством разрабатываемого прибора является получение формы детали в аналитическом виде, а не сравнение с заданным шаблоном, что позволяет использовать его в строительной сфере и тяжелом машиностроении, где существует огромное множество размеров, подлежащих контролю, а изготовление для этого большого количества различных шаблонов нецелесообразно и экономически невыгодно.
ЛИТЕРАТУРА:
1.Об оценках точности алгоритмических способов опознания формы цилиндрических крупногабаритных деталей / Полунин А.И. и др.// Управляющие системы и роботы в промышленности строительных материалов.-
М.: Изд. МИСИ, БТИСМ, 1987,- С. 165-169.
2.Смирнов В.И. Курс высшей матема-
тики. Т.2. – М.; Наука, 1974, - 670с.
259