
Chainov_Ivashenko_Konstr_dvs_1 / Чайнов Иващенко - Конструирование ДВС
.pdf
условиями работы к материалу пальца предъявляют повышенные требования. После термической обработки палец должен иметь зна чительную твердость трущихся по верхностей при вязкой сердцевине.
Применяют различные способы установки поршневого пальца. Дос таточно часто используют способ с плавающим пальцем. Преимущест вом данного способа является воз можность проворачивания пальца во время работы как в бобышках, так и в поршневой головке шатуна. В ре зультате уменьшается относительная скорость скольжения пальца по срав нению со скоростью скольжения при закреплении пальца в бобышках поршня или головке шатуна. При этом уменьшаются сила сопротивле ния и выделение теплоты, которое пропорционально произведению си лы трения на скорость относительно го движения. Уменьшается износ, который при данном способе уста новки распределяется равномерно по окружности пальца, вследствие чего палец сохраняет цилиндрическую форму, а также уменьшается опас ность заедания. Плавающие пальцы устанавливаются в поршень с не большим зазором (0–0,004 мм в авто мобильных двигателях).
При другом способе установки концы поршневого пальца (или один) закреплены в поршне. Такой способ применяется в автомобиль ных и тракторных двигателях и ре же в стационарных, судовых и теп ловозных двигателях.
По третьему способу поршневой палец закреплен в головке шатуна. С помощью нагрева шатуна палец запрессовывается в его верхнюю головку.
В случае применения плавающего пальца его смещение в направлении оси может привести к повреждению рабочей поверхности цилиндра. Для
Рис. 4.26. Пружинные замки и заглушки, пре дохраняющие палец от перемещения:
а – пружинные замки; б, в – заглушки
предохранения пальца от осевого пе ремещения применяют пружинные замки или заглушки. Пружинные замки (рис. 4.26, а) выполняют обыч но в виде колец из проволоки кругло го сечения или из листовой стали. При фиксировании пустотелого пальца заглушками (рис. 4.26, б) из алюминиевого или магниевого спла ва, реже из бронзы, достигается по вышение его радиальной жесткости и улучшение отвода теплоты. Наруж ная поверхность заглушек выполня ется в виде сферы с радиусом, не сколько меньшим радиуса цилиндра.
У двухтактных двигателей с пет левой схемой газообмена заглушки предотвращают утечку воздуха из ре сивера в выпускные окна через по лый палец. У двухтактных двигате лей нагрузки от давления газов более продолжительные и односторонние, а температура выше, чем в четырех тактных двигателях, вследствие чего поршневые пальцы работают в более тяжелых условиях. Поэтому в двух тактных двигателях с поршнями из легких сплавов в бобышки устанав ливают бронзовые втулки. Запрессо ванные бронзовые втулки применя
151

Рис. 4.27. Поршневые пальцы:
а, б – цилиндрические; в–д – приближаю щиеся к форме, обеспечивающей равное со противление изгибу
ются и в поршнях автомобильных четырехтактных двигателей. Наряду с цельными пальцами в быстроход ных двигателях для уменьшения массы, а также для рационального распределения материала поршне вой палец выполняют по одной из схем, приведенных на рис. 4.27.
Смазывание пальца может осу ществляться различными способа ми: через вертикальные отверстия в бобышках, при подаче масла из зо ны бобышек и с помощью продоль ных пазов на опорных поверхно стях бобышек.
Характер нагружения пальца за висит от соотношений жесткостей пальца и элементов поршня, зазора в бобышках, величины масляного слоя в местах скольжения.
Удельная нагрузка на проек цию опорных поверхностей паль ца (табл. 4.1) определяется из со отношения
k |
Pz |
, |
(4.7) |
|
|||
|
dпl0 |
|
4.1. Допустимые значения удельных нагрузок (Н/см2 10 2), действующих на опорные поверхности поршневого пальца
|
В поршневой |
|
В бобышках поршня |
||
|
головке шатуна |
|
|||
|
|
|
|
||
Тип пальца |
|
|
|
|
|
Втулка из брон |
из чугуна |
из алюминиевого сплава |
|||
|
|||||
|
зы или баббита |
(втулок нет) |
Втулок нет |
Бронзовые втулки |
|
|
|
|
|
|
|
|
Судовые и стационарные тихоходные |
|
|||
|
|
|
|
|
|
Плавающий |
15–25 |
35–40 |
25–30 |
35–40 |
|
|
|
|
|
|
|
|
Судовые быстроходные и тепловозные |
|
|||
|
|
|
|
|
|
Плавающий |
25–80 |
32–45 |
До 50 |
До 60 |
|
|
|
|
|
|
|
|
Автомобильные и тракторные |
|
|||
|
|
|
|
|
|
Плавающий или за |
35–55 |
35–55 |
30–50 |
35–60 |
|
крепленный в шатуне |
|
|
|
|
|
|
|
|
|
|
|
|
Быстроходные форсированные |
|
|||
|
|
|
|
|
|
Плавающий |
50–90 |
50–80 |
– |
50–80 |
|
|
|
|
|
|
П р и м е ч а н и е. При применении игольчатых подшипников значение удельных нагрузок достигает 63104 Н/см2.
152

где Pz – максимальная сила от дав ления газов; l0 – длина опорной по верхности пальца в зависимости от способа закрепления пальца при нимается соответственно равной или lш (в шатуне), или 2lб (в бобыш ках).
4.4.Поршневые кольца
Взависимости от выполняемых функций кольца делятся на уплот нительные (компрессионные) и маслосъемные. Поршневые кольца уплотняют полость камеры сгора ния, частично передают теплоту от поршня в стенку цилиндра, пре пятствуют попаданию масла из картера в камеру сгорания, чем препятствуют значительному его выгоранию. Многообразие функ ций, которые выполняют кольца, с учетом особенностей конструкций поршневой группы у двигателей разных типов и назначения обусло вили большое разнообразие конст рукций как компрессионных, так и маслосъемных колец. Уплотнение осуществляется за счет прижатия кольца к цилиндру силами упруго сти и давления газов, а также дрос селирования последних при пере текании через систему торцовых и радиальных зазоров. Поскольку на частичных нагрузках давление в цилиндре уменьшается, упругость кольца должна быть достаточной для уплотнения.
Кроме того, надежность уплот нения зависит также от деформа ции цилиндра (в процессе монтажа
ипри работе), препятствующей плотному прилеганию контакти рующих поверхностей стенки ци линдра и кольца. Неровности по верхности цилиндра, а также изна шивание поршневых канавок при водят к вибрации колец в осевом и радиальном направлениях, что яв
ляется причиной их усталостного разрушения.
Выбор числа колец зависит от типа двигателя и конструкции поршня. Причем последнее от ка меры сгорания кольцо должно от водить теплоту от поршня и не под вергаться вибрации.
Первое поршневое кольцо рабо тает в наиболее тяжелых условиях. При положении поршня в ВМТ давление в канавке первого кольца близко к давлению в цилиндре, а давление в канавке второго кольца составляет около 30 % давления в канавке первого кольца.
Потери на трение в кольцах со временных двигателей составляют около 25 % всех механических по терь при работе двигателя. Напри мер, в двигателе с принудительным воспламенением с тремя поршневы ми кольцами затраты энергии на трение первого, второго, третьего колец соответственно будут 60, 30, 10 %. Для снижения работы трения без ухудшения уплотняющей спо собности колец уменьшают площадь поверхности трения путем снижения высоты кольца, а также применяют подрез (рис. 4.28, а, тип 9, 10).
При отсутствии масляного ох лаждения поршня через компрес сионные кольца отводится до 60 % теплоты, теряемой поршнем. При масляном охлаждении эта доля уменьшается до 20–25 %. Темпе ратура первого кольца достигает 200–250 С. Температуры в зоне контакта кольца с цилиндром мо гут быть существенно выше. Не разрезные жаровые кольца форси рованных двухтактных двигателей (см. рис. 4.9) имеют температуру 350 С и более. Вследствие повы шенной температуры снижается прочность материала колец, пада ет их упругость, происходит закок совывание.
153

Компрессионные кольца распо лагаются в канавках с радиальным и осевым зазорами, обеспечиваю щими утопание и подвижность ко лец в канавках. В быстроходных форсированных дизелях рекомен дуют осевые зазоры около (0,0010 – 0,0015)D. В двигателях с принуди тельным воспламенением осевой зазор выбирают около 0,05 мм.
Компрессионные кольца, имея в свободном состоянии зазор А = = (3 – 4)l между краями замка, не являются круглыми. Круглую фор му кольцо приобретает, находясь в цилиндре, на стенку которого бла годаря упругости кольцо оказывает давление порядка 0,3–0,5 МПа. В табл. 4.2 приведены некоторые характеристики компрессионных колец.
Уменьшение высоты t колец по зволяет уменьшить высоту поршня и расстояние пальца до днища. Од нако при прочих равных условиях температура поршня в этом случае будет выше. Пределом уменьшения высоты t является возможность по ломки при обработке, монтаже и эксплуатации колец.
Предельная толщина l кольца определяется напряжением при на
девании кольца на поршень. В тон костенных цилиндрах форсирован ных двигателей лучший контакт колец с цилиндром при его овали зации достигается, если кольца имеют малую жесткость, т.е. мень шей толщине l.
При использовании материала с бо' льшим модулем упругости (ков кий чугун, сталь) для снижения давления следует уменьшать l или зазор в стыке в свободном состоя нии кольца. Форма стыка (замок) бывает различной. Наиболее часто применяют кольца с прямым раз резом или под углом 45 , а в круп ных судовых малооборотных двига телях – кольца со ступенчатым замком.
Несмотря на то, что компресси онные кольца частично выполняют функции маслосъемных колец и регулируют подачу масла, их кон струкция значительно отличается от конструкции маслосъемных ко лец. На рис. 4.28, а показаны наи более распространенные типы компрессионных колец, применяе мых в автомобильных и трактор ных двигателях. При умеренном форсировании применяют кольца прямоугольной формы (рис. 4.28,
4.2. Соотношение размеров колец и их число в двигателе
|
Стационар |
Автомобильные и тракторные |
Быстроходные фор |
|||||||||||||||||
|
|
|
|
|
|
двигатели |
|
сированные дизели |
||||||||||||
Наименование |
ные судовые |
|
|
|
|
|
|
|||||||||||||
|
|
|
|
|
|
|
|
|
|
|
|
|
|
|||||||
и тепловоз |
|
дизели |
с принудительным |
двухтакт |
четырех |
|||||||||||||||
|
|
|||||||||||||||||||
|
ные дизели |
|
||||||||||||||||||
|
|
воспламенением |
|
|
ные |
|
тактные |
|||||||||||||
|
|
|
|
|
|
|
|
|
|
|
|
|
|
|
|
|||||
|
|
|
|
|
|
|
|
|
|
|
|
|
|
|
|
|||||
Число компрес |
|
|
3–5 |
|
|
|
2–3 |
|
2 |
|
|
3 |
|
|
2–3 |
|||||
сионных колец |
|
|
|
|
|
|
|
|
|
|
|
|
|
|
|
|
|
|
|
|
|
|
|
|
|
|
|
|
|
|
|
|
|
|
|
|
|
|
|||
Радиальная тол |
1 |
|
1 |
|
|
1 |
|
1 |
|
– |
|
1 |
|
|
1 |
|
– |
|||
щина l кольца |
|
|
|
|
D |
|
|
|
|
D |
|
|
|
|
|
D |
|
|||
|
|
|
|
|
|
|
|
|
|
|
||||||||||
25 |
|
35 |
|
|
22 |
|
26 |
|
|
|
25 |
32 |
|
|
||||||
|
|
|
|
|
|
|||||||||||||||
Высота t компрес |
(0,5 – 1,0)l |
(2,5 – 3,5) мм |
(1,20 – 1,75) мм |
(0,6 – 0,9)l |
– |
|||||||||||||||
сионного кольца |
|
|
|
|
|
|
|
|
|
|
|
|
|
|
|
|
|
|
|
|
|
|
|
|
|
|
|
|
|
|
|
|
|
|
|
|
|||||
Число i масло |
|
|
1–2 |
|
|
|
1 |
|
1 |
|
|
2 |
|
|
1 |
|||||
съемных колец |
|
|
|
|
|
|
|
|
|
|
|
|
|
|
|
|
|
|
|
|
|
|
|
|
|
|
|
|
|
|
|
|
|
|
|
|
|
|
|
|
|
154

Рис. 4.28. Типы поршневых колец:
а – компрессионных; б – маслосъемных
а, типы 1, 2) со скругленными тор |
(рис. 4.28, а), как менее склонных к |
||
цами (радиус скругления не менее |
закоксовыванию. |
В |
остальных |
0,3 мм). При значении литровой |
поршневых канавках целесообраз |
||
мощности около 18,5 кВт/л и выше |
но использовать |
конические или |
|
рекомендуется в качестве первого, |
так называемые "минутные" ком |
||
а иногда и первых двух применять |
прессионные кольца с углом на |
||
трапецеидальные кольца типов 6, 7 |
клона образующей |
нагруженной |
155
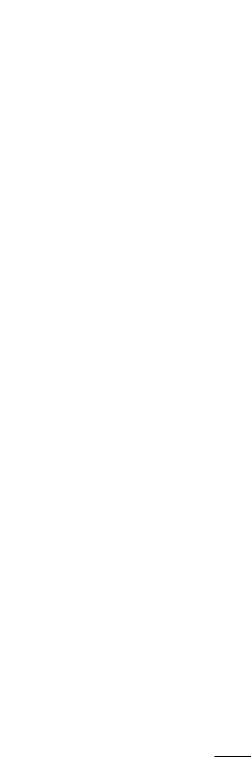
Рис. 4.29. Схемы поршневых колец крупных дизелей
поверхности 20–40(. Такие кольца создают повышенное давление на стенку цилиндра, хорошо прираба тываются.
Величина а' (см. рис. 4.28, а, тип 8) достигает у компрессионных ко лец 0,7–0,95 мм, у маслосъемных 0,9–1,1 мм. Улучшение уплотнения достигается применением колец скребкового типа 9, 10 и колец с несимметричным сечением типов 4, 5 (рис. 4.28, а), обеспечивающим скручивание колец при работе, что уменьшает их склонность к зависа нию.
У крупных судовых малооборот ных двигателей применяются ком прессионные кольца с улучшенной работоспособностью, которая дос тигается завальцовкой в боковую
рабочую поверхность бронзовых или алюминиевых кольцевых пла стин (рис. 4.29, а). Улучшению прирабатываемости способствует нанесение на рабочую поверхность кольцевых рисок (рис. 4.29, б), в которых, кроме того, хорошо удер живается масло.
Расход масла во многом опреде ляется конструкцией маслосъемных колец, давлением на стенку цилин дра, наличием на кольцах острой кромки, направленным хонингова нием зеркала цилиндра. Масло съемные кольца (см. рис. 4.28, б) из готавливаются скребковыми 15, ко робчатого типа 16, 21, а также со стоящими из нескольких элементов (кольца типов 17, 20). Маслосъем ные кольца имеют повышенное ра диальное давление на стенку ци линдра, для увеличения которого используются расширители III–IV в виде многогранных стальных лент (кольцо типа 17, см. рис. 4.28, б) или цилиндрических витых пружин (кольцо типа 21, см. рис. 4.28, б). Общее давление на стенку цилинд ра составляет около 1,1–1,5 МПа. Для отвода масла, собирающегося в углублениях, по периметру кольца фрезеруют прорези высотой (0,3– 0,45)t (кольца типа 16, 21, см. рис. 4.28, б). Соответствующую сис тему отводящих отверстий выпол няют и в корпусе поршня. Преиму ществом составных колец (кольца типа 17–20, см. рис. 4.28, б) являет ся хорошее согласование профиля рабочей поверхности элементов кольца с деформированной поверх ностью стенки цилиндра, что обес печивает при высоком радиальном давлении эффективный съем масла. Повышение гибкости кольца позво ляет уменьшить нажимное усилие кольца при обеспечении приемле мого расхода масла, сократив поте ри на трение. Доля потерь масло
156

съемными кольцами составляет 30– 60 % мощности трения всего ком плекта колец.
Для повышения износостойко сти компрессионных и маслосъем ных колец применяются специаль ные покрытия, наносимые на рабо чие поверхности, широко применя ются пористое хромирование, а так же напыление карбидохромомолиб денового слоя. Хром, обладая высо кой температурой плавления при ограниченном смазывании, менее склонен к схватыванию с металлом цилиндра. При этом бочкообразная форма кольца типа 14 (см. рис. 4.28, а) ускоряет приработку. Слой мо либдена способствует повышению противозадирных свойств кольца. Для того чтобы не наступал скол хромового покрытия, острые кром ки скругляются радиусом 0,3– 0,5 мм, а для стабилизации масло съемных качеств радиус затем со шлифовывают, обеспечивая на об разующей острую кромку. Масло съемные кольца выполняются под вижными.
Наиболее быстрый износ порш невых колец происходит в районе замка. Для повышения срока служ бы кольца делают с неравномер ным давлением по окружности. Формы эпюр давления различны: в четырехтактных двигателях макси мум давления приходится на об ласть замка; в двухтактных двигате лях для устранения попадания кон цов кольца в окна цилиндра при меняются эпюры с уменьшенным давлением в зоне замка.
Материал поршневых колец должен обладать достаточной меха нической прочностью при высоких температурах, износостойкостью, малым коэффициентом трения при движении колец по стенкам ци линдра в условиях высокой темпе ратуры и недостатка масла.
4.5. Материалы деталей поршневой группы
Материал поршня должен обес печить возможно меньшую его массу, быть достаточно прочным в диапазоне рабочих температур, иметь низкий коэффициент линей ного расширения, обладать износо стойкостью, высокой теплопровод ностью, в том числе при повышен ных температурах, иметь хорошую обрабатываемость. Важное значе ние имеет пластичность материала, а также комплексные характери стики, например, параметр E т/ (где Е – модуль упругости; т – ко эффициент линейного расшире ния; – коэффициент теплопро водности), от значения которого зависит уровень температурных на пряжений. В зависимости от назна чения двигателя и типа конструк ции поршня могут быть примене ны различные материалы.
Поршни быстроходных двигате лей многих типов, прежде всего ав томобильных и тракторных, изго товляют из легких сплавов методом отливки в кокиль или штамповкой (в том числе жидкой). В первом слу чае применяются эвтектические си лумины типа АЛ25 (10–13 % Si) и заэвтектические, содержащие при садки меди, никеля и марганца. Сле дует отметить, что поршни, отлитые традиционным способом, сдержива ют дальнейшее форсирование совре менных двигателей вследствие не достаточной термостойкости, твер дости и износостойкости.
Для повышения прочности и из носостойкости поршней применяют штамповку. Выполненные методом горячего деформирования поршни из алюминиевого сплава АК12Д с содержанием кремния 13 % имеют высокую износостойкость кольце вых канавок и меньший на 10–12 %
157

по сравнению с широко распростра ненными поршневыми деформируе мыми сплавами АК4 и АК4 1 коэф фициент линейного расширения. Однако прочностные свойства спла ва АК4 1 при нормальной темпера туре выше на 20–25 %. Следует об ратить внимание на предлагающую ся в последние годы многими разра ботчиками технологию производства поршней из алюминиевых сплавов с помощью жидкой штамповки, по зволяющей увеличить сопротивле ние усталости, повысить коррозион ную стойкость и износостойкость. При сочетании жидкой штамповки с упрочнением головки поршня кера мическими волокнами отмечается повышение временного сопротивле ния на 10–15 %.
Применение традиционных алюминиевых сплавов для изготов ления поршней ограничивается предельной температурой порядка 350 С. Поэтому наряду с легкими сплавами для изготовления порш ней применяются также различные чугуны и стали. Из легированного серого и высокопрочного чугунов выполняются поршни форсирован ных дизелей умеренной быстроход ности. При повышенной по срав нению с алюминиевыми сплавами температуре плавления чугуна уст раняется обгорание кромок на по верхностях, обращенных к камере сгорания.
В составных поршнях для изго товления головки применяют жа ростойкие стали типа 20Х3МВФ (поршни тепловозных дизелей), 20Х25Н20С2, 20Х23Н18 (поршни быстроходных транспортных дизе лей); 15ХМ; 20ХМ (поршни мало оборотных двухтактных дизелей). В составных поршнях двигателей с уменьшенным отводом теплоты в стенки были попытки применения конструкционных керамических
материалов (Si3N4; ZrО2) в качестве материала головки поршня. Одна ко низкая пластичность применяв шихся конструкционных керами ческих материалов, повышенная хрупкость и трудная обрабатывае мость при достаточно высокой це не не позволили пока широко при менять керамические материалы при изготовлении поршней.
На применение жаростойких ста лей переходят, если максимальная температура в наиболее нагретых зо нах поршня превышает 450 С. Вы соколегированные хромоникелевые стали успешно используют для изго товления накладок поршней быст роходных двухтактных дизелей, у ко торых максимальная температура го ловки достигает 900 С. В табл. 4.3 приведены некоторые теплофизиче ские и механические характеристи ки ряда материалов поршней с уче том их зависимости от температуры.
В табл. 4.4 приведены некото рые характеристики конструкци онных керамических материалов, рассматриваемых в качестве воз можных материалов для теплона пряженных элементов двигателей, а также значения некоторых ком плексных показателей:
R1 – характеризующего уровень допустимых градиентов температуры; R2 – характеризующего сопро
тивляемость термическому удару; R3 – характеризующего напря
женность при заливке керамиче ских вставок в металлические дета ли (в частности, из алюминиевых сплавов) при разности т коэффи циентов линейного расширения.
Поршневой палец изготовляют из легированной цементируемой стали. В малофорсированных двига телях применяют углеродистые ста ли марок 15 и 20; в форсированных (автомобильных, тракторных, тепло возных) палец выполняют из леги
158

4.3. Физические и механические свойства материалов поршней
Параметры |
|
|
|
|
Числовые значения |
|
|
|||||||||
|
|
|
|
|
|
|
|
|
|
|
|
|
|
|
|
|
Алюминиевый сплав АЛ25 |
|
|
|
|
|
|
|
|
|
|
|
|
|
|
||
|
|
|
|
|
|
|
|
|
|
|
|
|
|
|
||
Температура, С |
20 |
|
|
|
100 |
|
200 |
|
300 |
|
370 |
|||||
|
|
|
|
|
|
|
|
|
|
|
|
|
|
|
||
Модуль упругости Е310 5, МПа |
0,7 |
|
|
|
0,67 |
|
0,64 |
|
0,55 |
|
0,39 |
|||||
Коэффициент линейного расширения 3106, 1/ С |
19,0 |
|
|
19,5 |
|
20,0 |
|
21,0 |
|
|
– |
|||||
т |
|
|
|
|
|
|
|
|
|
|
|
|
|
|
|
|
Коэффициент теплопроводности , Вт/(м3С) |
159,0 |
|
167,5 |
|
172,0 |
|
173,8 |
|
|
– |
||||||
|
|
|
|
|
|
|
|
|
|
|
|
|
|
|
||
Предел прочности вр, МПа |
383 |
|
|
|
371 |
|
319 |
|
162 |
|
75 |
|||||
|
|
|
|
|
|
|
|
|
|
|
|
|
|
|
||
Предел текучести т, МПа |
315 |
|
|
|
305 |
|
286 |
|
142 |
|
49 |
|||||
|
|
|
|
|
|
|
|
|
|
|
|
|
|
|
|
|
,, % |
9,4 |
|
|
|
|
9,1 |
|
8,4 |
|
10,6 |
|
|
– |
|||
|
|
|
|
|
|
|
|
|
|
|
|
|
|
|
|
|
Алюминиевый сплав АК4 1 |
|
|
|
|
|
|
|
|
|
|
|
|
|
|||
|
|
|
|
|
|
|
|
|
|
|
|
|
|
|
||
Температура, С |
20 |
|
|
|
150 |
|
200 |
|
250 |
|
300 |
|||||
|
|
|
|
|
|
|
|
|
|
|
|
|
|
|
||
Модуль упругости Е310 5, МПа |
0,72 |
|
|
0,66 |
|
0,63 |
|
0,59 |
|
0,51 |
||||||
Коэффициент линейного расширения т3ΒΧΡ, 1/ С |
19,6 |
|
|
23,1 |
|
24,0 |
|
– |
|
|
|
– |
||||
Коэффициент теплопроводности , Вт/(м3С) |
142,4 |
|
148,6 |
|
150,7 |
|
155,0 |
159,0 |
||||||||
|
|
|
|
|
|
|
|
|
|
|
|
|
|
|
||
Предел прочности вр, МПа |
450 |
|
|
|
400 |
|
340 |
|
240 |
|
170 |
|||||
|
|
|
|
|
|
|
|
|
|
|
|
|
|
|
||
Предел текучести т, МПа |
380 |
|
|
|
360 |
|
300 |
|
190 |
|
140 |
|||||
|
|
|
|
|
|
|
|
|
|
|
|
|
|
|
|
|
,, % |
13,0 |
|
|
12,5 |
|
11,0 |
|
6,0 |
|
|
8,0 |
|||||
|
|
|
|
|
|
|
|
|
|
|
|
|
|
|
|
|
Сталь 20Х3МВФ |
|
|
|
|
|
|
|
|
|
|
|
|
|
|
||
|
|
|
|
|
|
|
|
|
|
|
|
|
|
|
|
|
Температура, С |
20 |
|
|
200 |
|
300 |
|
400 |
450 |
|
500 |
|
600 |
|||
|
|
|
|
|
|
|
|
|
|
|
|
|
|
|
|
|
Модуль упругости Е.10 5, МПа |
2,07 |
|
2,00 |
|
1,93 |
1,86 |
|
– |
|
1,77 |
|
1,64 |
||||
|
|
|
|
|
|
|
|
|
|
|
|
|
|
|
|
|
Коэффициент линейного расширения 3106, 1/ С |
10,0 |
|
|
– |
|
– |
12,3 |
|
– |
|
12,7 |
|
13,8 |
|||
т |
|
|
|
|
|
|
|
|
|
|
|
|
|
|
|
|
Коэффициент теплопроводности , Вт/(м3С) |
38,5 |
|
33,1 |
|
31,4 |
30,6 |
|
– |
|
29,7 |
|
29,3 |
||||
|
|
|
|
|
|
|
|
|
|
|
|
|
|
|
|
|
Предел прочности вр, МПа |
890 |
|
|
800 |
|
800 |
|
740 |
660 |
|
640 |
|
500 |
|||
|
|
|
|
|
|
|
|
|
|
|
|
|
|
|
|
|
Предел текучести т, МПа |
760 |
|
|
710 |
|
710 |
|
670 |
630 |
|
620 |
|
480 |
|||
|
|
|
|
|
|
|
|
|
|
|
|
|
|
|
|
|
,, % |
13,0 |
|
12,0 |
|
10,0 |
9,0 |
12,0 |
|
11,0 |
|
10,0 |
|||||
|
|
|
|
|
|
|
|
|
|
|
|
|
|
|
|
|
Серый легированный чугун |
|
|
|
|
|
|
|
|
|
|
|
|
|
|||
|
|
|
|
|
|
|
|
|
|
|
|
|||||
Температура, С |
20 |
|
|
|
200 |
|
300 |
|
400 |
|
500 |
|||||
|
|
|
|
|
|
|
|
|
|
|
||||||
Модуль упругости Е310 5, МПа |
1,42 |
|
|
1,37 |
|
1,32 |
|
1,27 |
|
1,22 |
||||||
Коэффициент линейного расширения 3106, 1/ С |
8,9 |
|
|
|
12,2 |
|
13,7 |
|
14,2 |
|
14,4 |
|||||
т |
|
|
|
|
|
|
|
|
|
|
|
|
|
|
|
|
Коэффициент теплопроводности , Вт/(м3С) |
54,7 |
|
|
48,8 |
|
45,4 |
|
43,0 |
|
|
– |
|||||
|
|
|
|
|
|
|
|
|
|
|
|
|||||
Предел прочности вр, МПа |
310 |
|
|
|
312 |
|
295 |
|
315 |
|
267 |
|||||
|
|
|
|
|
|
|
|
|
|
|
|
|||||
Предел текучести т, МПа |
276 |
|
|
|
258 |
|
262 |
|
266 |
|
215 |
|||||
|
|
|
|
|
|
|
|
|
|
|
|
|||||
,, % |
1,3 |
|
|
|
1,3 |
|
1,7 |
|
2,0 |
|
2,3 |
|||||
|
|
|
|
|
|
|
|
|
|
|
|
|
|
|
|
|
159

Окончание табл. 4.3
Параметры |
|
|
|
|
|
Числовые значения |
|
|
|
||||||||
|
|
|
|
|
|
|
|
|
|
|
|
|
|
|
|
||
|
Высокопрочный чугун |
|
|
|
|
|
|
|
|
|
|
|
|
||||
|
|
|
|
|
|
|
|
|
|
|
|
|
|
|
|
||
Температура, С |
|
|
|
|
20 |
|
200 |
|
300 |
|
400 |
|
500 |
||||
|
|
|
|
|
|
|
|
|
|
|
|
|
|||||
Модуль упругости Е310 5, МПа |
|
|
|
1,78 |
|
1,71 |
1,66 |
1,59 |
1,44 |
||||||||
Коэффициент линейного расширения 3106, 1/ С |
|
11,3 |
|
12,0 |
|
13,1 |
|
14,3 |
|
15,0 |
|||||||
|
|
т |
|
|
|
|
|
|
|
|
|
|
|
|
|
|
|
Коэффициент теплопроводности , Вт/(м3С) |
|
24,4 |
|
30,2 |
|
32,6 |
|
32,6 |
|
– |
|
||||||
|
|
|
|
|
|
|
|
|
|
|
|
|
|
|
|
||
Предел прочности вр, МПа |
|
|
|
|
720 |
|
740 |
|
712 |
|
655 |
|
495 |
||||
Предел текучести т, МПа |
|
|
|
|
715 |
|
695 |
|
612 |
|
537 |
|
430 |
||||
,, % |
|
|
|
|
0,3 |
|
0,7 |
|
1,6 |
|
|
4,0 |
|
8,5 |
|||
|
|
|
|
|
|
|
|
|
|
|
|
||||||
4.4. Физические и механические свойства конструкционных керамических материалов |
|
||||||||||||||||
|
|
|
|
|
|
|
|
|
|||||||||
|
Нитрид |
Нитрид |
|
Карбид |
|
Диоксид |
|
Титанат |
|||||||||
Наименование |
кремния го |
кремния ре |
|
кремния |
|
цирко |
|
алюми |
|||||||||
рячепрессо |
акционносвя |
спеченный |
|
ния |
|
|
|
ния |
|
||||||||
|
|
|
|
|
|
||||||||||||
|
ванный Si3N4 |
занный Si3N4 |
|
SiC, Sint |
|
ZrO2 |
|
Al2O3TiO2 |
|||||||||
Предел прочности при изгибе |
|
|
|
|
|
|
|
|
|
|
|
|
|
|
|
|
|
и, МПа, и температуре: |
|
|
|
|
|
|
|
|
|
|
|
|
|
|
|
|
|
500 С |
650 |
|
300 |
|
450 |
|
|
|
300 |
|
|
40 |
|
||||
1200 С |
400 |
|
300 |
|
450 |
|
|
|
– |
|
|
|
– |
|
|||
|
|
|
|
|
|
|
|
|
|
|
|
|
|||||
Предел прочности при сжатии |
2500 |
|
1500 |
|
3500 |
|
|
2000 |
|
|
550 |
|
|||||
сж, МПа, и температуре 20 С |
|
|
|
|
|
|
|
|
|
|
|
|
|
|
|
|
|
Плотность , г/см3 |
3,2 |
|
2,6 |
|
3,1 |
|
|
|
5,7 |
|
|
3,1 |
|
||||
Коэффициент теплопровод |
20,0 |
|
10,0 |
|
50,0 |
|
|
|
3,5 |
|
|
2,0 |
|
||||
ности , Вт/(м3С) |
|
|
|
|
|
|
|
|
|
|
|
|
|
|
|
|
|
|
|
|
|
|
|
|
|
|
|
|
|
|
|||||
Удельная теплоемкость с, |
2300 |
|
2000 |
|
3200 |
|
|
2300 |
|
|
2200 |
|
|||||
кДж/(м33С) |
|
|
|
|
|
|
|
|
|
|
|
|
|
|
|
|
|
Коэффициент линейного |
3,5 |
|
3,2 |
|
4,5 |
|
|
|
9,8 |
|
|
3,0 |
|
||||
термического расширения |
|
|
|
|
|
|
|
|
|
|
|
|
|
|
|
|
|
3106, 1/ C |
|
|
|
|
|
|
|
|
|
|
|
|
|
|
|
|
|
Т |
|
|
|
|
|
|
|
|
|
|
|
|
|
|
|
|
|
Модуль упругости Е310 5, МПа |
2,9 |
|
1,8 |
|
4,1 |
|
|
|
2,0 |
|
|
0,20 |
|
||||
3c |
3 |
3 |
3 |
3 |
3 3 |
|
|
3 |
3 |
|
3 |
3 |
|||||
|
46,0 10 |
20,0 10 |
160,0 10 |
|
8,0 10 |
|
4,4 10 |
||||||||||
R1 = и/E т при температуре |
640 |
|
520 |
|
240 |
|
|
|
150 |
|
|
890 |
|
||||
500 С |
|
|
|
|
|
|
|
|
|
|
|
|
|
|
|
|
|
|
|
|
|
|
|
|
|
||||||||||
R2 = и/E т при температу |
12,83103 |
5,23103 |
12,03103 |
|
0,53103 |
|
1,83103 |
||||||||||
ре 500 С |
|
|
|
|
|
|
|
|
|
|
|
|
|
|
|
|
|
|
|
|
|
|
|
|
|
|
|
|
|
|
|
||||
R3 = сж/E т |
465 |
|
440 |
|
490 |
|
|
|
820 |
|
|
1930 |
|
||||
рованных сталей марок 15ХМ, 38ХА, |
ком с получением твердости более |
||||||||||||||||
12ХН3А 18Х2Н4ВА, 20Х2Н4А и др. |
58 НRС; применяется и азотирова |
||||||||||||||||
Наружную поверхность пальцев |
ние поверхности. |
|
|
|
|
|
|
|
|
|
|||||||
цементируют на глубину 0,5–1,5 мм |
Поверхность пальца из углеро |
||||||||||||||||
с последующей закалкой и отпус |
дистой стали марки 45 закаливают |
160