
Chainov_Ivashenko_Konstr_dvs_1 / Чайнов Иващенко - Конструирование ДВС
.pdf
действует, например 1–3. Таким образом,
|
|
|
|
|
|
[k e ] [B]T [D][B]t e ; |
(2.124) |
||||||
|
|
|
|
e ] T EtT [b c |
|
b c |
|
b c |
|
]T |
|||
[G |
|
|
|
||||||||||
|
|
|
|
|
|
2(1 −) |
1 |
1 |
2 |
2 |
3 |
3 |
|
|
t |
[XY XY |
XY ]T |
|
|
|
|
||||||
|
|
|
|
|
|||||||||
3 |
|
|
|
|
|
|
|
|
|
||||
|
tl1 3 |
[px py 00 |
px py ]T . |
(2.125) |
|||||||||
|
|||||||||||||
2 |
|
|
|
|
|
|
|
|
|
Для осесимметричной задачи применяют цилиндрическую сис тему координат. Вектор деформа ции имеет дополнительную четвер тую компоненту + = u/r, поэтому
|
|
e ] |
2 T ET r |
|
|
|
|
|
[G |
[B]T [1 1 1 0]T |
|||||||
1 2− |
||||||||
|
|
|
|
|
|
пользованием соотношения r =
= N1r1 + N2r2 + N3r3 и последующим интегрированием в L координатах.
Интегрирование члена, содержа щего вектор объемных сил {P}T = = [Pr Pz], показывает, что б льшая часть объемных усилий приходится на более удаленные от оси вращения узлы. При расчете вращающихся с угловой скоростью деталей Pr = = 2r. Интегрирование члена, со держащего вектор распределенной нагрузки {p/} = [pr pz], действующей, например, по грани 1–3, также мож но выполнить с помощью L коорди нат. Окончательно выражение век тора нагрузки элемента в случае осе симметричной задачи имеет вид
|
[d P d P d |
P d |
P |
d |
P d |
|
P ]T |
|
|
|
|
|
|
|
|
||||||||||||||||
|
6 |
1 |
r |
|
|
1 z |
|
2 |
r |
|
|
2 z |
|
3 r |
|
|
3 z |
|
|
|
|
|
|
|
|
|
|
|
|||
|
|
|
|
|
|
|
|
|
|
|
|
|
|
|
|
|
|
|
|
|
|
|
|
|
|
|
|
|
|
|
|
|
l13 [(d |
|
d |
2 |
)p |
r |
(d |
d |
2 |
)p |
z |
0 0 |
(d |
3 |
d |
2 |
)p |
r |
(d |
3 |
d |
2 |
)p |
z |
]T , |
(2.127) |
|||||
|
3 |
1 |
|
|
|
|
1 |
|
|
|
|
|
|
|
|
|
|
|
|
|
|||||||||||
|
|
|
|
|
|
|
|
|
|
|
|
|
|
|
|
|
|
|
|
|
|
|
|
|
|
|
|
|
|
|
матрица деформации [B] является функцией переменных координат r, z и не может быть вынесена за знак интеграла. Для определения матрицы жесткости применяют численное интегрирование. При ближенное значение [ke] определя ется вычислением матрицы дефор мации[B]в центре тяжести элемен
та с координатами: r (r1 r2 r3 ) и
3
z (z1 z2 z3 ). Тогда 3
[k e ] [B]T [D][B] dV
V e
[B]T [D][B]2 r . (2.126)
Слагаемые выражения (2.121) могут быть определены точно с ис
где d1 = 2r1 + r2 + r3; d2 = r1 + 2r2 + r3; d3 = r1 + r2 + 2r3.
Радиальные Rr и осевые Rz ком поненты вектора сосредоточенных сил, вводимые в расчет, являются суммарными, т.е. отнесенными ко всей длине окружности =r.
В случае трехмерной задачи при использовании тетраэдального сим плексного элемента (рис. 2.9, в) компоненты матрицы [B] не изме няются внутри элемента, поэтому интегрирование при определении всех величин, входящих в уравнение (2.123), выполняется в замкнутом виде с помощью L координат:
[k e ] [B]T [D][B]V e .
Обозначая вектор объемных сил {P}T = [X Y Z] и вектор поверхно
стных сил {p/}T = [px py pz], имеем
61

|
|
|
|
T |
ET |
|
|
|
|
|
|
|
|
|
|
V e |
|
|
|
|
|
|
|
|
|
|
|
|
|
|
|||||
[G e ] |
|
|
[b c |
|
b c |
b c |
|
b c |
|
]T |
|
|
[XYZ XYZ XYZ XYZ ]T |
||||
6(1 2−) |
|
|
|
4 |
|||||||||||||
|
|
|
1 |
1 |
2 |
2 |
3 |
3 |
4 |
4 |
|
|
|
||||
124 [px py pz |
px py pz |
000 |
px py pz ]T . |
|
(2.128) |
||||||||||||
3 |
|
|
|
|
|
|
|
|
|
|
|
|
|
|
|
После того как путем решения системы уравнений (2.123) опре делены составляющие вектора {,} по формулам (2.110) и (2.114) оп ределяют деформации и напряже ния в элементах. При использова нии симплексных элементов в случае плоской (треугольный эле мент) и трехмерной (тетраэдаль ный элемент) задачи деформации и напряжения постоянны в преде лах элемента, что является недос татком этих элементов и требует значительного сгущения конечно элементной сетки в местах кон центрации деформаций и напря жений. Точность решения повы шается при переходе к конечным элементам повышенной точности (рис. 2.10).
Вопрос о том, какой формы конечные элементы лучше при менять, остается открытым. Сет ки из треугольных или тетра эдальных элементов могут быть получены с помощью автомати ческой разбивки, а для так назы ваемых блочных сеток, содержа щих четырехугольные или шести гранные элементы, алгоритмов автоматической разбивки пока нет. В то же время при одинако вом количестве элементов реше ние при использовании блочных сеток точнее, чем при использо вании триангуляционных. Одно временно квадратичные элемен ты повышают точность по срав нению с линейными.
К этапам решения задачи при определении теплового и напря
женно деформированного состоя ния детали с помощью МКЭ мож но отнести следующие.
1.Выбор расчетной схемы, вклю чая определение класса задачи (объ емная, осесимметричная, плоская, одномерная) и задание граничных условий.
2.Выбор типа конечных элемен тов, которые предполагается исполь зовать при решении, а также коор динатных функций (функций фор мы) элементов, однозначно описы вающих распределение искомого па раметра (температуры, перемеще ния) в пределах элемента.
3.Дискретизация области, зани маемой деталью в пределах выбран ной расчетной схемы, заключаю щаяся в представлении этой облас ти набором конечных элементов (разбивка на элементы).
4.Описание элементов, вклю чающее рациональную нумера цию узлов и самих элементов; определение координат узлов и особенностей расположения от дельных элементов (граничные, внутренние), их физико техниче ские и механические характери стики и др.
5.Составление системы уравне ний путем минимизации соответ ствующего данной задаче функ ционала при помощи приведенных выше соотношений.
6.Решение полученной систе мы уравнений относительно неиз вестных в узлах параметров (тем пературы, компонентов переме щения).
62

7. Вычисление всех предусмот ренных при постановке задачи па раметров для каждого элемента (температуры, деформаций, напря жений и др.) и визуализация полу ченных результатов в виде полей температур, перемещений, дефор маций и напряжений.
Вопросы программирования при решении задач МКЭ представляют самостоятельную важную и доста точно сложную задачу. В настоящее время существует достаточно много универсальных конечно элемент ных программных продуктов, среди которых получившие распростране ние такие коммерческие пакеты как ANSYS, NASTRAN, ABAQUS и др. Расчеты с использованием коммер ческих пакетов стали сравнительно несложным делом, не требующим глубоких теоретических знаний. В связи с этим часто эти расчеты про изводятся довольно формально без должной оценки достоверности по лучаемых при этом результатов.
МКЭ является приближенным. Эффективные математические мо дели должны отвечать ряду требова ний, среди которых следует назвать полноту, точность, адекватность, экономичность, робастность (устой чивость), продуктивность и нагляд ность. Применительно к конечно элементной модели рассмотрим в первую очередь точность, устойчи вость и сходимость численных реше ний. Точность определяется мерой близости численного решения к точ ному. Устойчивость определяется ростом ошибок при выполнении вы числительных операций в процессе решения задачи. Последний связан с аппроксимацией и округлением чис ленных значений, что ведет к посте пенному накоплению ошибок и по тере истинности решения. Под схо димостью понимают постепенное приближение последовательно полу
чаемых численных решений к пре дельному по мере уточнения отдель ных вычислительных параметров, в частности количества или размеров конечных элементов. При расчетах теплового и напряженно деформи рованного состояния узлов и деталей двигателя часто применяется итера ционная процедура, когда результа ты одного из этапов вычислений становятся исходной информацией последующих этапов, и здесь сходи мость вычислительного процесса имеет решающее значение. В сходя щемся вычислительном процессе точность растет по мере уточнения параметров вычислительной проце дуры.
Помимо ошибок аппроксимации и округления, свойственных вычис лениям вообще, методу конечных элементов присущи ошибки дискре тизации и ошибки, вызванные при менением базисных функций. Пер вые связаны с геометрическими раз личиями рассчитываемой детали и ее конечно элементной модели. Эти ошибки уменьшаются с уменьшени ем размеров конечных элементов и увеличением их числа. Ошибки, оп ределяемые различием между точ ным решением и решением, пред ставляемым базисными функциями, не обязательно уменьшаются по ме ре уменьшения элемента. Как отме чается, в некоторых случаях они мо гут приводить даже к расходимости вычислительного процесса.
В МКЭ в качестве базисных функций используются степенные полиномы. В этом случае точное ре шение обеспечивалось бы полным полиномом бесконечно большой степени. Сходимость вычислитель ной процедуры МКЭ обеспечивает ся, если искомая функция (напри мер, температуры) представлена внутри элемента полиномом степе ни как минимум р, если р – высший
63

порядок производной в функциона ле (в частном случае Ф(Т)). Если степень используемого полинома больше р, то можно ожидать повы шения точности, уменьшения оши бок пробной функции и увеличения скорости сходимости. Сформулиро ванное положение определяется как критерий полноты.
Кроме того, для обеспечения схо димости конечные элементы долж ны быть согласованными, иными словами, при переходе через границу смежных элементов должны быть непрерывны сама искомая функция и ее производные вплоть до (р 1) порядка включительно. Это положе ние определяется как критерий со гласованности. Установлено, что критерий полноты представляет бо лее сильное условие и его выполне ние на практике является часто дос таточным условием сходимости. В общем случае точность решения оп ределить затруднительно. Тестиро вание конечно элементной модели применительно к задаче, имеющей аналитическое решение, позволяет судить лишь о работоспособности алгоритма, программы и точности численного решения применительно к данному случаю. В общем случае, если позволяют время и средства, проводят серию расчетов на сгущае мых сетках.
Косвенным критерием оценки сходимости вычислительной проце дуры является уменьшение разницы последующих решений при сгуще нии сетки меньше установленной величины. Последняя может рас сматриваться как косвенная оценка точности численного решения.
В случае неудобства проведения расчетов на сгущающихся сетках оценка о качестве конечно эле ментной модели делается на основе единичного решения с использова нием анализа полей производных
искомой функции. На хорошо под готовленных сетках разрывы вели чин производных (например, теп лового потока) на границах элемен тов невелики.
Решение задач методом конеч ных элементов сводится к решению систем линейных алгебраических уравнений (СЛАУ). Число уравне ний в СЛАУ может быть при этом достаточно большим, достигая сотен тысяч. Поэтому большое значение имеет выбор метода решения систе мы уравнений. Симметрия и поло жительная определенность глобаль ной ленточной матрицы системы позволяют существенно сократить объем вычислений при решении СЛАУ. Методы решения СЛАУ де лятся на прямые и итерационные. Первые позволяют получить реше ние после выполнения конечного числа арифметических операций. Если при этом каждая операция вы полняется точно, то метод называют точным. Итерационные методы пре дусматривают построение последо вательных приближений к решению задачи.
Применение того или иного ме тода решения СЛАУ зависит от раз меров задачи (количества неизвест ных), а также зависит от математи ческого обеспечения при пользова нии конкретной машинной про граммой. При небольших и умерен ных размерах СЛАУ применяют прямые методы, преимуществом ко торых является ограниченный объем арифметических операций и его ап риорная оценка. Недостаток метода связывают с необходимостью хране ния в оперативной памяти ЭВМ всей матрицы системы. Итерацион ные процедуры не страдают этим не достатком. Они позволяют полно стью использовать особые свойства разреженных матриц, однако выпол нение большого числа итераций
64

приводит к б льшим затратам ма шинного времени. Для плохо обу словленных задач отмечается мед ленная сходимость. Плохая обуслов ленность матрицы СЛАУ может быть вызвана большими различиями в жесткостях компонентов неодно родной конструкции.
Среди прямых методов решения СЛАУ следует прежде всего назвать метод Гаусса, предусматривающий преобразование исходной системы уравнений к эквивалентной системе с верхней треугольной матрицей. Существует несколько вычислитель ных схем, реализующих этот метод. Среди них часто применяемый при конечно элементных расчетах метод Холецкого, один из вариантов кото рого называют методом квадратного корня. При симметричной и поло жительно определенной матрице ме тод Холецкого требует вдвое меньше вычислительных затрат по сравне нию с методом Гаусса. Из итераци онных методов следует указать на метод релаксации, а также метод со пряженных градиентов.
2.5. Выбор расчетных режимов
Поршневые двигатели, как пра вило, работают в широком диапазо не скоростных и нагрузочных режи мов при переменных механических и тепловых нагрузках. При этом теп ловое состояние деталей, возникаю щие в них напряжения и деформа ции существенно изменяются в за висимости от режимов работы дви гателя. Нагрузки на детали двигателя обусловлены действием сил давле ния газов, сил инерции, тепловым воздействием, а также связаны с раз личными видами колебаний.
При определении теплового и напряженно деформированного со стояния следует выбрать один или несколько расчетных режимов, на
которых затем будут проводиться расчеты. При этом расчетный ре жим характеризуется наиболее вы соким уровнем нагружения детали.
В настоящее время расчеты на прочность, как правило, проводят для установившегося режима. Од нако в отдельных случаях влияние неустановившихся режимов на теп ловое и напряженно деформиро ванное состояние деталей может быть учтено при выборе расчетных значений тепловых и механических нагрузок, соответствующих реаль ным условиям работы с учетом не установившихся режимов. Следует заметить, что прочность в первую очередь теплонапряженных дета лей может быть достаточно точно оценена лишь при учете всей сово купности режимов работы двигате ля в эксплуатации, принимая во внимание их продолжительность и чередование, которые существенно различны для отдельных типов двигателей в зависимости от назна чения последних.
Для всех типов двигателей рас четы теплового и напряженно де формированного состояния дета лей начинают с режима номиналь ной мощности при частоте враще
ния nном. Как правило, на этом ре жиме работы достигают макси
мальных значений температуры наиболее нагруженных в тепловом отношении деталей, а также, осо бенно в случае двигателей с надду вом, действующие на них силы дав ления газов. Наряду с этим, в пер вую очередь, для двигателей назем ного транспорта по условиям проч ности опасным может оказаться и режим максимального крутящего момента, когда при частоте враще
ния n = (0,5 0,7)nном силы давле ния газа являются максимальными.
При этом силы инерции здесь су щественно ниже, чем на номиналь
65

ном режиме, что дополнительно повышает нагрузки от газовых сил.
Для двигателей с принудитель ным воспламенением, а иногда и для высокооборотных дизелей целе сообразно проводить проверочный расчет и для режима холостого хода, соответствующего максимальной частоте вращения, допускаемой ре гулятором. При наличии последне го максимальная частота вращения холостого хода для двигателей с принудительным воспламенением составляет n = (1,05 1,10)nном, для дизелей – n = (1,05 1,07)nном.
В течение срока службы каждый двигатель работает на неустановив шихся режимах. Доля их в общей продолжительности эксплуатации в отдельных случаях может сущест венно различаться. Во всех случаях к таким режимам относятся: пуск, остановка двигателя, а также смена при работе двигателя скоростного и нагрузочного режимов. От скоро сти и степени этих изменений за висят величины тепловых и меха нических нагрузок на узлы и детали двигателя при его работе на неуста новившихся режимах. Иногда ве личины этих нагрузок оказываются более высокими, чем даже на уста новившемся режиме полной мощ ности или максимального крутя щего момента. Экспериментально установлено, что в отдельных рабо чих циклах неустановившегося ре жима максимальное давление рzн может до 1,5 раз превышать свое расчетное значение на установив шемся режиме.
Силы инерции вращающихся и особенно поступательно движу щихся масс могут также сущест венно изменяться при работе на неустановившихся режимах. Если на неустановившемся режиме уг ловая скорость коленчатого валан значительно превосходит но
минальное значение , что может иметь место при резком уменьше нии нагрузки, то это следует учи тывать при оценке сил инерции поступательно движущихся масс для проведения расчетов на проч ность.
В частности, предлагают исполь зовать коэффициент перегрузки
P (Pzн Pjzн )(Pz Pjz ),
где Рjz и Pjzн – силы инерции посту пательно движущихся масс, соот ветствующих углу поворота колен чатого вала при максимальном дав лении сгорания.
На отдельных неустановивших ся режимах величины коэффици ента перегрузки при резких изме нениях нагрузки могут достигать значений 1,3–1,5.
В связи с широким проникнове нием электроники в системы управ ления современных двигателей пе регрузки на неустановившихся ре жимах можно существенно ограни чить. Коэффициент перегрузки сле дует назначать индивидуально для рассчитываемого на прочность дви гателя и особенностей возможных режимов его работы.
2.6. Прочностная надежность и оценка прочности деталей двигателя
Под надежностью изделия (в ча стности поршневого двигателя) по нимается свойство последнего вы полнять заданные функции, сохра няя уровень технико экономиче ских показателей в определенном диапазоне в течение заданного промежутка времени или наработ ки. Надежность двигателя, включая безотказность его работы, связана со сроком службы (долговечно стью). Под сроком службы двигате
66

ля или отдельных его узлов и дета лей понимается время работы (в часах или километрах пробега транспортного средства), а также число циклов нагружения N. До пустимый срок службы двигателя называют ресурсом.
Количественно надежность технического объекта характери зуется вероятностью его безотказ ной работы Р( ). Например, при вероятности безотказной работы двигателя 0,99 за ресурсный пери од допускается 1 отказ двигателя из 100, находящихся в эксплуата ции. При этом под отказом пони мается потеря двигателем работо способности. Вероятность отказа за время
|
|
Q f ( )d , |
(2.129) |
0 |
|
где f( ) – плотность вероятности от казов.
Функции Р( ) и Q( ) связаны со отношением Р( ) + Q( ) = 1.
Вероятность безотказной работы системы Р( ) при последовательном соединении r элементов равна про изведению их вероятностей безот казной работы. При этом элементы предполагаются независимыми, а в случае одинаковости Рi( ) отдель ных элементов P( ) = Pir ( ).
Среди отказов различают посте пенные и внезапные. Прочностной надежностью называется отсутст вие внезапных отказов. Постепен ные отказы, связанные в первую очередь с изнашиванием элементов подвижных соединений, занимают особое место при оценке ресурса двигателя. В дальнейшем будут рассматриваться прочностные ас пекты обеспечения работоспособ ности поршневых двигателей.
Внезапные отказы (например, поломки) характеризуются интен сивностью отказов 1 ( – сред няя наработка на отказ). Тогда P( ) = e . Плотность вероятности отказов часто характеризуется нор мальным распределением
|
|
|
|
1 |
|
|
( )2 |
|
|
|
f ( ) |
|
|
e 2S 2 , (2.130) |
|||||
|
|
|
|
|
|||||
|
|
|
S |
|
2 |
|
|
|
|
|
|
|
|
|
|
|
|
||
где S |
|
6( i |
)2 |
– среднее квад |
|||||
|
k |
1 |
|
|
|
||||
|
|
|
|
|
|
|
|
ратичное отклонение; k – число объ ектов испытания.
Иногда лучшее описание резуль татов, например, усталостных ис пытаний дает нормально логариф мическое распределение, когда по нормальному закону распределяет ся логарифм наработки.
Надежность, особенно таких сложных изделий, как двигатели, имеет в своей основе статистиче скую природу и вероятностную ха рактеристику ее оценки. При этом в общем случае применяют стати стические методы определения ко личества возможных отказов, ис пользуя математические модели надежности. Нахождение вероят ностей безотказной работы на ста дии проектирования является дос таточно сложным.
Основным при оценке прочно стной надежности является метод определения коэффициентов запа са прочности. В общем случае под коэффициентом запаса прочности по напряжениям понимается отно шение величины предельного на пряжения пред к максимальному значению напряжения mах при ра
боте |
|
|
|
n |
пред |
. |
(2.131) |
|
|||
|
|
|
|
|
max |
|
67

Условие прочностной надежности имеет вид
n > [n], |
(2.132) |
где [n] – допустимое значение ко эффициента запаса прочности.
При постоянных во времени на грузках [n] рекомендуется порядка 1,8–2,0, а при случайных перемен ных нагрузках [n] принимают до значений 3–5.
Назначение величины коэффи циента запаса прочности является ответственным моментом при про ектировании двигателя и опирается на большой опыт испытаний и рас четов узлов и деталей двигателей различных типов и назначений. Ниже рекомендуемые величины коэффициентов запаса будут кон кретизированы применительно к отдельным базовым элементам порш невых двигателей.
Модель прочностной надежно сти элемента (детали) двигателя включает модель материала, мо дель нагружения, а также модель формы и модель разрушения.
В связи со сложной формой ос новных деталей двигателя их гео метрическое представление осуще ствляется с помощью конечно эле ментных моделей различной раз мерности. Хотя на предваритель ных этапах расчетов вариантов конструкций, где это допустимо по условиям прочности, для построе ния моделей формы могут исполь зоваться типовые элементы, такие как стержни, пластинки и оболоч ки. При практической оценке прочностной надежности деталей двигателя их материал рассматри вается как сплошная среда (конти нуум). Многочисленные экспери ментальные исследования показа ли, что использование модели сплошной среды при прочностном
анализе элементов двигателей, из готовленных из традиционных ма териалов (стали, чугуны, алюми ниевые сплавы и др.), правомерно.
При построении модели нагру жения основных деталей двигателя рассматриваются сосредоточенные, распределенные и объемные (мас совые) силы. При этом учитывается изменение этих сил в течение рабо чего цикла двигателя, а также неста ционарность режимов работы в ходе эксплуатации. Сказанное в равной мере относится к тепловым нагруз кам, которым подвержены теплона пряженные детали двигателя.
Оценка прочностной надежно сти связана с принимаемой при анализе последней моделью разру шения. При формулировании усло вий прочности при различных усло виях нагружения выделяют статиче ское, длительное статическое, мало цикловое и усталостное разруше ние. В условиях переменных тепло вых нагружений имеет место терми ческая усталость. При выборе моде ли разрушения при оценке прочно стной надежности детали двигателя следует учесть свойства материала, из которого изготовлена деталь, в первую очередь, пластичность.
При расчетах на прочность дета лей двигателя ранее широко исполь зовалось условие непревышения наибольшими напряжениями max в опасных точках величины допускае
мых напряжений [ ]: max < [ ]. Од нако такая оценка является услов
ной, так как не говорит о характере возможного разрушения, не отража ет режима работы детали, марки ма териала детали, технологии изготов ления и др.
Б льшее представление о проч ностной надежности дает величина запаса прочности n. При этом в формуле (2.131) в зависимости от условий нагружения в качестве пред
68
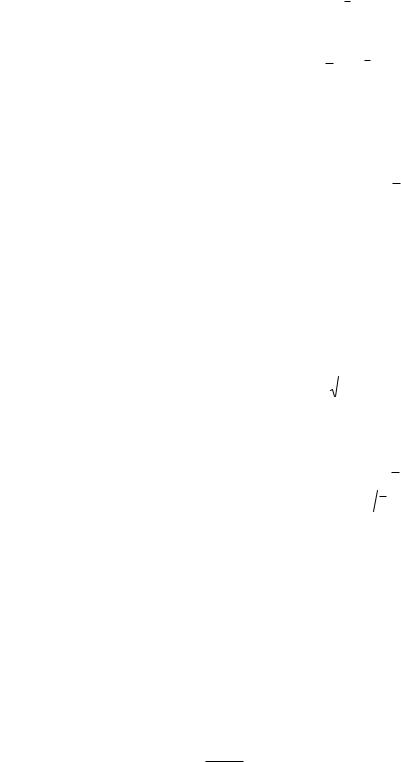
могут рассматриваться: условный предел текучести 0,2; предел проч ности (временное сопротивление)в; длительная прочность дл; предел выносливости 1; предел ползуче сти пл для базового времени . За пасы прочности являются основной характеристикой прочностной на дежности деталей, поэтому их вели чины и порядок определения долж ны соответствовать нормативной документации. Запасы прочности могут быть детерминированными и статистическими. Первые зависят напрямую от численной величины предельного и максимального рабо чего напряжений. При вычислении статистических запасов прочности оценивается достоверность указан ных напряжений. Таким образом, величина коэффициента запаса прочности зависит от вариации пред и mах, определяемых стабильностью свойств материала и технологии производства, а также стабильно стью условий эксплуатации и об служивания.
На рис. 2.12 представлены нор мальные распределения плотности фактора прочности материала 9 (на пример, предела выносливости дета ли 1д) и напряженности 2 (напри мер, амплитуды действующих напря жений а). Средние значения (мате матические ожидания) факторов прочности материала и нагрузки со ответственно обозначены 9 и 21 Пре
Рис. 2.12. Распределение плотности факторов прочности и нагрузки
вышение 9 над 2 говорит о нали чии среднего коэффициента запаса прочности
n 92 . (2.133)
Статистический коэффициент запаса прочности определяют как отношение минимального значения
9min к максимальному 2max при при нятых соответствующих уровнях
значимости q и доверительной веро ятности Р. Неравенство n ?1 свиде тельствует о предусмотренном в де тали по условиям изготовления и эксплуатации среднем запасе проч ности, а величины 9min и 2max счита ются установленными. Известно, что с увеличением коэффициента запаса прочности вероятность разру шения Рразр уменьшается. При неза висимости случайных величин 9 и 2
|
|
|
|
|
|
|
|
|
|
|
|
|
|
1 |
|
|
n 1 |
||||||
P |
|
Ф |
|
|
|
|
, (2.134) |
||||
|
|
|
|
|
|
|
|
||||
разр |
2 |
|
|
|
|
|
|
|
|
||
|
n 2 v92 v22 |
||||||||||
|
|
|
|
где v2, v9 – соответственно коэффи циенты вариации факторов нагруз ки и прочности.
Значения функции Лапласа Ф(х) n 1
на
n 2 v29 v22
ходятся из таблиц.
Коэффициент запаса обычно превышает 1, поэтому на вероят ность разрушения больше влияет разброс фактора прочности, чем разброс фактора нагружений. Та ким образом, снижение материало емкости конструкции, связанное с уменьшением коэффициента запаса прочности, требует повышения ста бильности прочностных характери стик материалов и технологических процессов изготовления, а также контроля за нагрузками (режимами работы) при эксплуатации.
69

Так как при проектировании дан ные о факторах 9 и 2 часто отсутству ют, для определения запаса прочно сти пользуются справочными данны ми по несущей способности материа ла в качестве средних значений их функций распределения. Например, коэффициент вариации прочностных свойств материала лопаток авиаци онных газотурбинных двигателей принимают v9 = 0,1, а коэффициент вариации рабочих напряжений с уче том разброса нагрузок и размеров де талей принимается v2 = 0,2–0,3.
Несмотря на б льшую объек тивность и достоверность вероят ностного подхода при оценке запа са прочности, чтобы определить его достоверные числовые значе ния, надо располагать достаточным объемом статистических данных по прочностным характеристикам ма териалов, из которых выполнены детали, а также по характеру нагру жения при работе этих деталей. Учитывая дефицит подобной ин формации, относящейся к поршне вым двигателям, при прочностных расчетах деталей проектируемых двигателей определяются детерми нированные запасы прочности, не связанные с числовой оценкой дос товерности прочностных характе ристик материала и действующих нагрузок. При этом методика опре деления запасов прочности деталь но строго оговаривается.
Для определения стандартных прочностных характеристик, кото рые требуются при расчетах запа сов прочности, проводятся испыта ния на гладких образцах в условиях одноосного напряженного состоя ния как при однократном растяже нии, так и при длительном, а также при циклическом нагружении.
Однократное нагружение рас сматривается как простейший част ный случай циклического нагруже
ния, длительность которого весьма мала, а разрушение, если оно про изойдет, будет иметь место в нуле вом полуцикле. Для многих деталей поршневых двигателей напряжен но деформированное состояние в опасных зонах является сложным (многоосным). В этом случае при оценке прочности вычисляют экви валентное напряжение и эквива лентную деформацию. Часто выби раются i и +i, определяемые по формулам (2.31). При циклическом нагружении вычисляют интенсив ность амплитуды и интенсивность среднего напряжения.
В простейшем случае работы де тали при нормальной температуре или незначительном ее повышении в условиях относительно медленного монотонного нагружения в качестве предельного напряжения принима ется предел прочности в или предел текучести т. Коэффициент запаса вычисляется при этом соответствен но по пределу прочности nв или пре делу текучести nт по формуле
nв, т |
|
в, т |
, |
(2.135) |
|
||||
|
|
max |
|
где max – максимальное рабочее на пряжение.
В поршневых двигателях так мо гут быть оценены коэффициенты за паса прочности некоторых крепеж ных элементов, нагруженных посто янными усилиями затяжки. Для уче та помимо растягивающих напряже ний также и касательных напряже ний от момента затяжки в качестве максимального рабочего напряжения следует использовать максимальное эквивалентное напряжение, напри мер, интенсивность напряжений
i max. Для деталей, работающих при повышенной температуре, в качестве
предельного напряжения принимает
70