
Chainov_Ivashenko_Konstr_dvs_1 / Чайнов Иващенко - Конструирование ДВС
.pdf
пряжений в каждом конечном эле менте и отображает результаты рас чета в виде таблиц перемещений узлов, напряжений в элементах и узлах, полей напряжений шатуна, эпюры напряжений по контуру ша туна. Контур деформированной де тали и эпюра напряжений показа ны на рис. 5.48, а, б.
Заключительным этапом расчета является оценка прочности элемен тов шатуна, выполняемая в после довательности, изложенной ранее.
Наиболее точные результаты обеспечивает расчет трехмерной геометрии, реализуемый с помо щью метода конечных элементов. На рис. 5.А (см. вкладку) показана твердотельная модель шатунного механизма, которая используется при создании конечно элементной модели. Конечно элементная сетка верхней головки шатуна показана на рис. 5.Б (см. вкладку). Исполь зовались квадратичные двадцатиуз ловые элементы. Модель содержит 80 тыс. элементов.
Расчет проводился при действии сил давления газов и инерции.
Сила давления газов приклады валась к поршню, а сила инерции – в виде объемной силы.
Так как поперечные инерцион ные нагрузки, связанные с вращени ем шатуна не учитываются, то воз можно рассчитывать 1/4 часть детали.
В расчете учитывается натяг при запрессовке бронзовой втулки.
Перераспределение нагрузок при взаимодействии шатуна, втул ки, поршневого пальца и поршня осуществлялось введением кон тактных элементов.
На рис. 5.В–5.Д (см. вкладку) показаны компоненты напряже ний: x – вдоль оси шатуна, y – перпендикулярно оси шатуна в плоскости качания шатуна, z – вдоль оси поршневого пальца при
действии суммарной сжимающей и растягивающей нагрузок.
Поля напряжений отличаются значительной неравномерностью распределения, которая не может быть учтена ни одним из описан ных выше методов расчета. На рис. 5.В, а (см. вкладку) сжимаю щие напряжения достигают значе ния 544 МПа, что объясняется из гибом поршневого пальца под дей ствием сил давления газов. Макси мальные растягивающие напряже ния возникают на внешней поверх ности головки шатуна и вызваны овализацией контура расточки в направлении оси y. Напряженное состояние стержня шатуна являет ся практически одноосным и одно родным. Однако в месте начала ра диусного перехода стержня в го ловку заметно некоторое увеличе ние сжимающих напряжений (го лубая область).
Колебания напряжений по внутренней поверхности головки объясняются недостаточно хоро шим согласованием конечно эле ментных сеток контактирующих поверхностей втулки и головки.
На рис. 5.В, б (см. вкладку) по казаны поля напряжений x при действии на шатун сил инерции. Минимальные напряжения нахо дятся снаружи в верхней части го ловки и также вызваны изгибным действием поршневого пальца. Максимальные напряжения распо лагаются на внутренней поверхно сти и вызваны овализацией расточ ки в направлении оси х. Хорошо видна также зона с растягивающи ми напряжениями. Заметна кон центрация напряжений в проточке для подвода масла.
На рис. 5.Г, а, б (см. вкладку) представлены поля напряжений y. Хорошо видны зоны концентрации напряжений в области маслоподво
231
дящей канавки и маслоподводяще го отверстия. Можно отметить, что возникающие напряжения в канав ке являются определяющими при вычислении коэффициентов запа са прочности.
На рис. 5.Д, а, б (см. вкладку) показано распределение напряже ний z (вдоль оси поршневого пальца) соответственно при дейст
вии сжимающей и растягивающей нагрузок. В обоих случаях макси мальные растягивающие напряже ния возникают в зоне концентра ции напряжений от маслоподводя щего отверстия.
Заключительным этапом расчета является оценка прочности элемен тов шатуна, выполняемая в после довательности, изложенной ранее.

Глава 6
КОЛЕНЧАТЫЕ ВАЛЫ И МАХОВИКИ
6.1. Основы конструирования коленчатых валов
Коленчатый вал – одна из наи более ответственных, напряженных и дорогостоящих деталей двигате ля.
Вал воспринимает переменные периодические нагрузки от сил дав ления газов и сил инерции поступа тельно движущихся масс, а также от сил инерции вращательно движу щихся масс.
Силы, действующие на вал, вызывают износ его шеек и под шипников, усталостные разруше ния, как правило, в местах кон центраций напряжений, а также крутильные, изгибные и осевые колебания.
Основные требования, предъяв ляемые к конструкции вала:
•высокая прочностная надеж ность, жесткость и износостой кость при относительно небольшой массе;
•высокая точность изготовле ния шатунных и коренных шеек;
•высокая твердость и степень чистоты обработки поверхности шеек;
•хорошая уравновешенность;
•для быстроходных двигате лей – разгруженность коренных шеек от центробежных сил и мест ных изгибающих моментов.
Рациональную схему коленчато го вала с определением расположе ния колен вала выбирают после эс кизных разработок, связанных с назначением и размерами двигате ля, и динамического расчета двига теля. Взаимное расположение ко лен вала зависит от тактности дви
гателя, числа, расположения и по рядка работы цилиндров.
Колена вала располагают таким образом, чтобы получить следую щее:
•равномерность чередования вспышек для получения наиболь шей равномерности хода;
•наилучшую уравновешен ность двигателя;
•равномерное нагружение эле ментов коленчатого вала (последо вательно работающие цилиндры не должны быть смежными, их следу ет располагать по возможности по обе стороны от среднего коренного подшипника);
•наименьшие напряжения от крутильных и изгибных колебаний;
•наилучшее использование энергии отработавших газов при наличии газовой турбины.
Размеры элементов колена вала определяются в основном расстоя нием между осями цилиндров, в свою очередь зависящим от диамет ра цилиндра, толщины стенок гиль зы и рубашки цилиндра, объема для охлаждающей жидкости, а также каналов для продувочного воздуха и отработавших газов в двухтактном двигателе.
При уменьшении расстояния между осями цилиндров наряду с уменьшением габаритных разме ров двигателя увеличиваются же сткость и прочность вала, однако ухудшаются условия работы под шипников вследствие уменьшения их длины.
В зависимости от размера шеек и щек, а также от числа колен валы из готовляют цельными (рис. 6.1, а), с составными коленами (рис. 6.1, б, в)
233

Рис. 6.1. Схемы коленчатых валов:
а – цельного; б, в – составного
и составными из двух или более уча стков, соединяемых фланцами, от кованными как одно целое с валом (рис. 6.1, г). Фланцы имеют центри рующие заточки или монтажные центрирующие шайбы.
Цельные валы применяют в дви гателях внутреннего сгорания всех типов.
Валы с составными коленами ус танавливают в малооборотных двух тактных двигателях, а также в звездо образных авиационных двигателях, в которых главный шатун выполнялся нередко с неразъемной кривошипной головкой, а части колена соединяют шлицами или болтом.
Наиболее часто коленчатые ва лы имеют число опор, превышаю щее на единицу число колен (пол ноопорные валы). В некоторых случаях (малофорсированные дви гатели с принудительным воспла менением, а также при оппозитном
расположении цилиндров) число опор может быть уменьшено. В та ком случае с увеличением расстоя ния между опорами для получения необходимой жесткости размеры элементов вала приходится увели чивать.
Вал состоит из колен и конце вых участков (со стороны отбора мощности и свободного переднего конца). В некоторых конструкциях отбор мощности производится с обоих концов вала. Типичная кон струкция колена вала двигателя c различной формой щек показана на рис. 6.2.
Длина колена L, диаметры ша тунной d и коренной d1 шеек зависят от диаметра цилиндра D и типа дви гателя.
Поскольку средние нагрузки на коренные шейки выше, чем на шатунные, диаметр d1 коренных шеек обычно больше диаметра d
234

Рис. 6.2. Колена вала с различной формой щек:
а – призматической; б – овальной; в – эллиптической; г – цилиндрической
шатунных шеек на 5–10 %. Как в коренных, так и в шатунных шей ках часто сверлят отверстия для уменьшения массы (это особенно целесообразно применять в ша тунных шейках), что приводит к уменьшению сил инерции вра щающихся масс. Коренные шейки чаще, чем шатунные, выполняют без полостей.
При отношении S/D, незначи тельно превышающем 1, в сочетании с увеличенными диаметрами шеек можно получить значительное пере крытие шеек = 0,5(d + d1) R. При этом повышается прочность вала и появляется возможность уменьше ния толщины b щеки без увеличения ее ширины h.
Увеличение диаметра шатунной шейки приводит к росту размеров кривошипной головки шатуна и
размеров картера. Кроме того, уве личиваются вращающиеся массы, силы инерции, а частота свободных колебаний системы валопровода уменьшается. Для максимального сокращения длины двигателя при меняют коленчатые валы, у кото рых коренная шейка совмещена со щекой. В данном случае применя ют роликовые подшипники, картер выполняют неразъемным, а вал монтируют с торца (рис. 6.3).
При выборе формы щеки учиты вают прочность и технологичность конструкции. Например, эллипти ческие щеки, приближающиеся к круглым, имеют не меньшее по сравнению с последними сопротив ление усталости при несколько меньшей массе. Овальная форма щек оптимальна с точки зрения прочности, но менее технологична
235
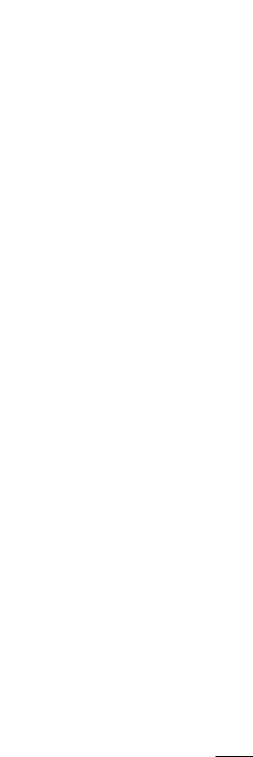
Рис. 6.3. Коленчатый вал с подшипником ка чения
по сравнению с круглой. Форма ще ки должна способствовать умень шению нагрузки на коренные шей ки от действия центробежной силы инерции. Для этого на щеках в ра диальном направлении делают ско сы в области шатунной, а иногда и коренной шеек (см. рис. 6.2).
Переходы от щек к шейкам следу ет осуществлять относительно боль шим радиусом закруглений (галте лей) для уменьшения концентрации напряжений. Увеличению радиуса галтели препятствует уменьшение ра бочей длины шейки.
В быстроходных двигателях (что бы избежать при шлифовании шеек задевания шлифовальным кругом торцовых поверхностей) шейки со прягают не непосредственно со ще ками, а со специальными чисто об работанными кольцевыми буртика ми, ограничивающими перемеще ние в осевом направлении криво шипной головки шатуна. Буртики сопрягаются со щеками галтелями радиусом r > (0,05–0,08)d. В резуль тате сопряжения шейки со щекой двумя радиусами уменьшается кон центрация напряжений.
Впроцессе работы двигателя ко ленчатый вал может совершать осе вые перемещения относительно корпуса двигателя. Одна из при чин – различные тепловые деформа ции корпуса и вала, изготовляемых из различных материалов с разным коэффициентом линейного расши рения. От осевых перемещений вал фиксируют на средней или крайней коренных шейках с помощью спе циального упорного подшипника. Осевой зазор в упорном подшипни ке составляет около 0,12–0,20 мм.
Вбыстроходных двигателях ще ки часто выполняют как одно целое
спротивовесами, уравновешиваю щими силы инерции вращающихся масс и их моменты, а также разгру жающими коренные опоры. Массы и размеры противовесов определя ются при динамическом расчете двигателя. Во многих случаях про тивовесы изготовляются отдельно.
На рис. 6.4 даны различные спо собы крепления противовесов на щеках коленчатого вала.
При креплении по схемам, по казанным на рис. 6.4, а, б, не ис ключены случаи разрыва болтов при частотах вращения коленчато го вала, превышающих расчетные. Крепления по схемам, показан ным на рис. 6.4, в–д, более надеж ны, так как предусмотрена раз грузка болтов от сил инерции. По схеме на рис. 6.4, в болты разгру жаются шпонками, работающими на срез; по схемам рис. 6.4, г, д – зубцами противовеса. Болты в данном случае работают на растя жение от силы затяжки.
Внекоторых случаях противове сы приваривают к щекам коленча того вала. Недостатком такой кон струкции является нарушение структуры материала вала, особен но при изготовлении вала из леги рованных сталей. В двигателях ав
236

Рис. 6.4. Крепление противовесов:
а, б – болтовое; в–д – повышенной надежности
томобильного и тракторного типов |
смазывания коренных и шатунных |
|
нередко противовесы устанавлива |
подшипников. Существуют раз |
|
ют не на всех щеках. |
личные способы подвода смазоч |
|
В двигателях с кривошипно ка |
ного материала к подшипниковым |
|
мерной продувкой противовесы слу |
парам коленчатых валов. При ин |
|
жат также для уменьшения под |
дивидуальном подводе масло по |
|
поршневого пространства в криво |
ступает к каждой коренной опоре |
|
шипной камере и получения требуе |
из общего коллектора (например, |
|
мого давления продувочного возду |
центральной масляной |
магистра |
ха. Иногда противовесы крайнего |
ли). При этом достигаются одина |
|
колена совмещают с устройствами |
ковые условия смазывания всех ко |
|
для гашения крутильных колебаний. |
ренных подшипников. Из наиме |
|
Наряду с обеспечением прочно |
нее нагруженных зон |
коренных |
стной надежности и высоких дина |
подшипников масло поступает для |
|
мических характеристик коленча |
смазывания шатунных подшипни |
|
того вала его конструкция должна |
ков. На рис. 6.5 показаны различ |
|
создавать благоприятные условия |
ные способы прохода масла к под |
Рис. 6.5. Подвод масла в полости коленчатого вала:
а, б – с помощью трубок; в–ж – по каналам в щеках (полости коленчатого вала закрыты за глушками)
237

шипникам коленчатого вала. Не посредственная подача масла меж ду поверхностями коренных и ша тунных шеек может осуществлять ся через косые отверстия (см. рис. 6.5, а, б), что обеспечивает ус коренную подачу масла в период пуска.
Поскольку в масле имеются при меси (частицы металла, кокса, гря зи), следует применять устройства, препятствующие попаданию этих частиц в масляный зазор подшип ников. С такой целью в маслопод водящие отверстия ставятся специ альные трубки, завальцованные или прикрепленные каким либо иным способом к стенке шатунной шей ки; трубки опущены на значитель ную глубину в полость шатунных шеек (рис. 6.5, г, ж), забирая чистое масло из центральной области.
Заглушки имеют конические фас ки и притираются к валу (рис. 6.5, г– е). Способ резьбового крепления за глушек, а также способ их завальцов ки имеет серьезные недостатки. При резьбовом креплении предел вынос ливости понижается, завальцовка за глушек (см. рис. 6.5, ж) затрудняет осмотр и очистку масляных полос тей. Часто ставят плоские заглушки на прокладках (см. рис. 6.5, в); такая конструкция отличается сравнитель ной простотой.
Для уменьшения потерь масла, находящегося в картере, вал вы полняют с гребнем, а иногда и с маслосгонной резьбой. Масло, по падающее на гребень, центробеж ной силой отбрасывается на стенки картера или на специальный отра жатель.
Существуют конструкции ко лен, в которых полости шеек снаб жены алюминиевыми вставками (см. рис. 6.5, з); по спиралям по следних циркулирует масло, отво дящее теплоту от шеек.
Для уменьшения концентрации напряжений с помощью радиусной фаски поверхности вывода смазоч ного отверстия придается специ альная форма. При наличии отвер стий в шейках вала прямая подача масла обеспечивается с помощью трубки, установленной в сквозной наклонный канал.
При осевом подводе смазочное масло подается к крайней опоре и, циркулируя по валу, последова тельно поступает к коренным и шатунным подшипникам. Описан ная схема компактна и применяет ся в форсированных двигателях специального назначения, однако требует увеличения давления мас ла в системе для компенсации по терь при прохождении масла по длине вала.
На переднем свободном конце вала (носке) устанавливают шкивы для привода вспомогательных агре гатов, шестерню или звездочку для привода распределительного вала, демпфер крутильных колебаний (при его наличии). На рис. 6.6 представлена конструкция носка с одним из вариантов устройства уп
Рис. 6.6. Свободный конец коленчатого вала
238

лотнения коленчатого вала трак торного двигателя.
На носке вала могут быть уста новлены сегментные или призма тические шпонки, которые часто выполняют роль установочных эле ментов. При этом передача крутя щего момента осуществляется с по мощью натяга при установке эле ментов привода на валу. Располо женные на носке вала детали, как правило, стягиваются болтом. В двигателях легковых автомобилей момент затяжки болта составляет 150–250 Н3м, при требовании боль шего момента болт заменяют на гайку, закручиваемую на резьбовое окончание носка вала.
Конец вала со стороны отбора мощности для соединения с гене ратором, муфтой, маховиком, вин том, упругим элементом и т.д. име ет участок со шлицами или флан цем. В хвостовой части коленчато го вала, как правило, находится узел крутильных колебаний. По этому в некоторых форсированных двигателях на хвостовике устанав ливают шестерни привода меха низма газораспределения и топлив ного насоса. Хвостовик коленчато го вала также тщательно уплотня ется с помощью различного типа манжет, например, самоподвиж ных резиновых в комбинации с маслоотражателем и маслоотводя щей канавкой. Иногда наряду с маслоотражательным буртиком на поверхности хвостовика делается маслосгонная нарезка в виде спи ральной канавки с двумя – тремя витками, обеспечивающая отвод масла от манжеты.
На рис. 6.7 представлена конст рукция хвостовика и один из вари антов уплотнения коленчатого вала транспортного двигателя.
Коренные и шатунные шейки, а также носок и хвостовик коленча
Рис. 6.7. Хвостовик коленчатого вала в сборе с маховиком и уплотнение хвостовика:
1 – маховик; 2 – вкладыш упорного под шипника; 3 – хвостовик; 4 – манжета
того вала изготавливаются с высо кой точностью. Так, в транспорт ных форсированных дизелях до пуск на диаметр шеек не превыша ет 0,02 мм. У быстроходных двига телей с принудительным воспламе нением диаметры шеек и хвостови ка коленчатого вала выдерживают ся с точностью до 0,015 мм.
Несмотря на общность ряда прин ципиальных требований, предъяв ляемых к коленчатому валу поршне вых двигателей, конструкция этой базовой детали в значительной степе ни определяется типом и назначени ем двигателя.
6.1.1. Анализ конструкций коленчатых валов
Коленчатые валы автомобиль ных двигателей выполняются как кованными из высокопрочной ле гированной стали, так и литыми из высокопрочного чугуна. На рис. 6.8 представлен коленчатый вал четы рехцилиндрового четырехтактного двигателя.
239

Рис. 6.8. Коленчатый вал с большим перекрытием шеек
При высоких частотах вращения коленчатых валов современных ав томобильных двигателей следует до биваться как можно более полного уравновешивания всех сил инерции
иих моментов. Последние зависят от числа и схемы взаимного распо ложения колен вала. Здесь можно отметить рядные четырехтактные двигатели с четным числом цилинд ров, которые свободны от неуравно вешенных моментов. Такие валы на зываются зеркальными, их примене ние способствует обеспечению низ кой виброактивности двигателя. В отличие от коленчатых валов рядных четырехтактных двигателей с чет ным числом цилиндров, валы трех
ипятицилиндровых двигателей плоскости симметрии не имеют. Для уравновешивания моментов от сил инерции требуется установка балан сировочных устройств.
Коленчатые валы V образных двигателей выполняют с удлиненны ми шатунными шейками с целью ус тановки на каждой из них двух шату нов, соединенных с поршнями лево го и правого рядов цилиндров. В дан ном случае в шатунных шейках вы полняются по два отверстия для по дачи масла к шатунным подшипни кам. На рис. 6.9 представлен коленча тый вал V образного восьмицилинд рового автомобильного дизеля, имею щий крестообразную форму располо жения кривошипов, что при угле раз вала цилиндров 90 обеспечивает рав номерное чередование вспышек.
В валах некоторых V образных двигателей между коренными опо рами располагают шатунные шей ки, сдвинутые друг относительно друга на угол, обеспечивающий рав номерность чередования вспышек (рис. 6.10).
Рис. 6.9. Коленчатый вал автомобильного дизеля
240