
Chainov_Ivashenko_Konstr_dvs_1 / Чайнов Иващенко - Конструирование ДВС
.pdf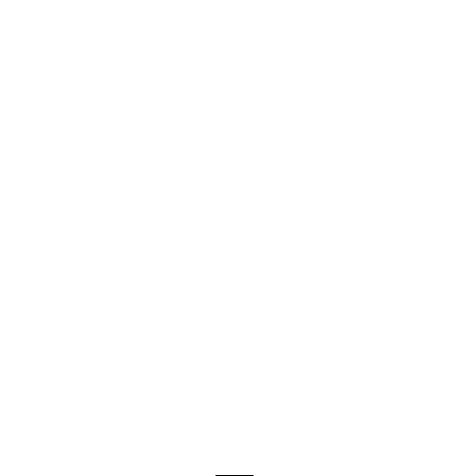
их |
применении двигатель имеет |
(рис. 8.56). При симметричных диа |
||
меньший размер вдоль оси цилинд |
граммах изменения угла–сечения |
|||
ра по сравнению с конструкциями, |
выпускных и продувочных окон ис |
|||
выполненными с подвесными кла |
пользование таких золотников по |
|||
панами и другими типами золотни |
зволяет получить фазу дозарядки и |
|||
ков. |
|
|
|
уменьшить утечку продувочной сре |
Распределение одной гильзой, |
ды. |
|||
совершающей под |
воздействием |
В двигателях с кривошипно ка |
||
кривошипа сложное |
движение |
с |
мерной продувкой используют само |
|
поворотом на некоторый угол, по |
устанавливающиеся дисковые золот |
|||
зволяет получить необходимые фа |
ники 4 (рис. 8.57), позволяющие по |
|||
зы газораспределения и непрерыв |
лучить несимметричную фазу впуска |
|||
ное перемещение гильзы относи |
горючей смеси в кривошипную ка |
|||
тельно цилиндра. Последнее ис |
меру и улучшить продувку и напол |
|||
ключает трение покоя, обеспечива |
нение цилиндра. |
|||
ет более надежное смазывание на |
При использовании золотников |
|||
ружной поверхности гильзы и луч |
всех типов упрощается конструк |
|||
шее ее охлаждение. Большая на |
|
|||
дежность работы и относительная |
|
|||
простота изготовления обеспечили |
|
|||
широкое применение одногильзо |
|
|||
вого распределения в четырехтакт |
|
|||
ных |
авиационных |
двигателях |
с |
|
принудительным воспламенением.
Вдвухтактных двигателях золот никами, управляющими щелевыми органами газораспределения, явля ются рабочие поршни.
Вдвигателях с петлевыми схема ми продувки и турбонаддувом ис пользуются качающиеся или вра щающиеся золотники 1, устанавли ваемые в выпускных патрубках
|
Рис. 8.57. Мотоциклетный двигатель с диско |
|
вым золотником на впуске: |
|
1 – картер двигателя; 2 – крышка; 3 – впуск |
Рис. 8.56. Выпускная система малооборотного |
ное окно; 4 – золотник; 5 – гайка креп |
ления золотника на ступице; 6 – шпонка; |
|
двухтактного двигателя с золотником: |
7 – ступица золотника; 8 – продувочные |
1 – втулка; 2 – блок; 3 – золотник |
каналы |
341
ция головок цилиндров и снижает ся их теплонапряженность. При гильзовом газораспределении по является возможность расположить свечу зажигания и форсунку в цен тре цилиндра.
Из большого числа определяемых при проектировании параметров следует отметить в первую очередь фазы распределения, форму и раз меры окон в стенках золотников, расстояние окон от кромок золотни ков по высоте и взаимное располо жение (по ширине) окон, размеры каналов в стенках цилиндров, радиу сы кривошипов и угол между криво шипами золотников в случае воз вратно поступательно движущихся золотников, радиусы кривошипов и
расстояние между осью гильзы и центром шарнира, если гильзы со вершают сложное движение.
Проектирование золотниковых органов газораспределения прово дят в следующем порядке. Выбира ют фазы газораспределения, близ кие к фазам аналогичных по частоте вращения клапанных двигателей, и средние скорости газов в пределах 57–70 м/с для впускных и 79– 110 м/с для выпускных окон. После этого находят величины "время–се чений" окон.
Задаваясь формой окон и пред варительными размерами окон, на ходят такое их сочетание, которое обеспечивает необходимые "время– сечения" и фазы газораспределения.

Глава 9
КОРПУСНЫЕ ДЕТАЛИ
9.1. Основы конструирования корпусных деталей и элементов крепления
Высокие требования к массогаба ритным показателям современных поршневых двигателей в большой мере могут быть удовлетворены ра циональной конструкцией корпус ных деталей двигателя. Цилиндры (блоки цилиндров), картеры (блок картеры), фундаментные рамы (опо ры коренных подшипников), детали крепления, а также масляные поддо ны, уплотняющие прокладки и ман жеты являются элементами корпуса, масса которого составляет 22–40 % (и более) массы двигателя.
В судовых и стационарных двига телях часто используется понятие остов, в состав которого включают неподвижные базовые детали двига теля, связанные крепежными эле ментами (анкерными связями) в единую жесткую систему, которая при нагружении монтажными уси лиями, силами давления газов и си лами инерции должна обеспечить минимально допустимые деформа ции, включая лимитированный уро вень вибраций наружных стенок корпуса.
Конструкция корпусных деталей с расположенными на них различ ными устройствами во многом оп ределяет внешний облик, а также габаритные размеры двигателя. Корпусные детали вместе с головка ми (крышками) и гильзами (втулка ми) цилиндров образуют закрытую, непроницаемую полость для газов, смазывающего масла и охлаждаю щей жидкости (в случае двигателей жидкостного охлаждения), в кото
рой работают кривошипно шатун ный механизм, механизм газорас пределения и другие вспомогатель ные механизмы и устройства.
К конструкции корпуса предъ являются следующие требования:
–прочность и жесткость;
–удобство монтажа деталей, уз лов и агрегатов и их технического обслуживания;
–технологичность конструкции;
–возможно меньшая материало емкость при обеспечении прочно сти и жесткости;
–обеспечение необходимых виб роакустических характеристик;
–хороший эстетический уро вень конструкции.
9.1.1. Силовые схемы корпусов поршневых двигателей
Корпус двигателя подвергается действию циклических газовых и инерционных сил, температурных нагрузок, связанных с неравномер ным распределением температуры в элементах корпуса, монтажных нагрузок, а также действию реак тивного крутящего момента, пере дающегося через опоры двигателя на его корпус. В зависимости от способа передачи сил давления га зов на элементы корпуса в первую очередь можно выделить следую щие силовые схемы.
Схема несущего блока цилиндров.
Эта схема характерна для блок кар теров автомобильных и тракторных двигателей. Здесь силы давления газов замыкаются в пределах карте ра, нагружая стенки блока цилинд ров и вызывая в них напряжения растяжения. При отсутствии встав
343
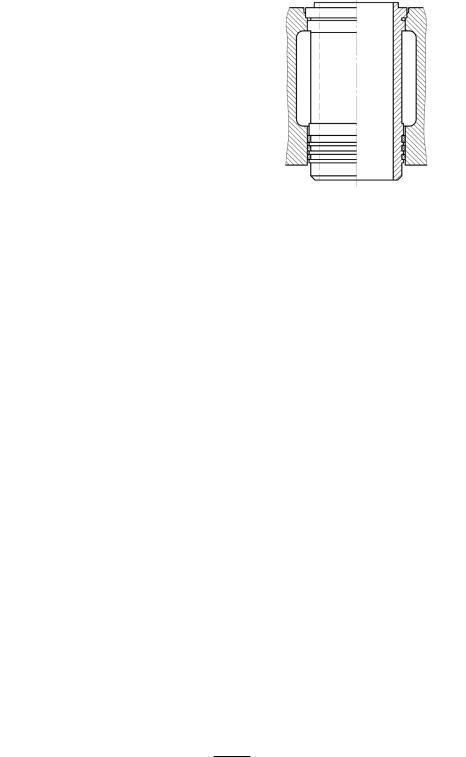
Рис. 9.1. Несущий блок цилиндров:
1 – проточка; 2 – деформированный уча сток блока при отсутствии проточки
ных гильз цилиндров, когда зерка ло цилиндра является внутренней поверхностью расточки блока, ра бочая поверхность цилиндра под вергается действию переменных усилий от давления газов. Для уменьшения деформаций рабочей поверхности цилиндра резьбовое отверстие удаляют от внутренней стенки (рис. 9.1). По данной схеме выполнены многие быстроходные, малоразмерные двигатели, в том числе двигатели различных моде лей отечественных легковых авто мобилей ВАЗ.
По схеме несущих цилиндров были выполнены некоторые двига тели воздушного охлаждения с от дельными цилиндрами, прикрепляе мыми с помощью фланцев к карте ру. Головки устанавливались на ци линдры на плотной резьбе. Схема применялась на ряде авиационных двигателей воздушного охлаждения.
При наличии вставных мокрых гильз (втулок) цилиндров действию сил давления газов подвергаются только наружные стенки блока ци линдров (рис. 9.2). Эта схема нашла применение во многих автомо бильных и тракторных дизелях. Как и в схеме несущего блока ци линдров, головка крепится к блоку цилиндров шпильками или болта ми, вворачиваемыми в верхнюю часть блока цилиндров.
Рис. 9.2. Схема с несущей наружной стенкой блока цилиндров
Схема несущих шпилек. С увели чением диаметра цилиндра и ростом форсирования по среднему эффек тивному давлению и максимальному давлению цикла для разгрузки сте нок блока цилиндров растягиваю щие усилия от давления газов вос принимаются длинными силовыми шпильками, ввернутыми в верхнюю часть картера (рис. 9.3). Данная схе
Рис. 9.3. Схема длинных несущих шпилек:
1 – головка; 2 – прокладка; 3 – блок цилин дров; 4 – бурт гильзы цилиндров; 5 – под дон; 6 – шпилька коренной опоры; 7 – под веска; 8 – стяжной болт; 9 – картер; 10 – шпилька головки цилиндров
344
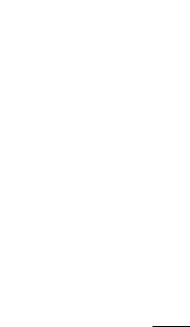
ма традиционно применялась в фор сированных двигателях специально го назначения, а затем стала исполь зоваться и в форсированных средне оборотных дизелях, включая тепло возные. При этом в отличие от из вестного отечественного двигателя 12 ЧН15/18(В 2) блок цилиндров вы полняют как одно целое с картером. Эта же схема применяется и во мно гих двигателях воздушного охлажде ния, а также в двигателях с монобло ком, когда блок и головка цилинд ров выполнены в виде одной детали.
Схема несущих анкеров. В крейц копфных двигателях при больших диаметрах цилиндров и, как прави ло, при наличии фундаментной ра мы силы давления газов восприни маются длинными анкерными свя зями, стягивающими элементы корпуса двигателя (рис. 9.4). В этом случае блок цилиндров, картер (картерная коробка) и часто фунда ментная рама нагружены в первую очередь сжимающими монтажны ми усилиями. Силовая схема счита
Рис. 9.4. Схема с несущими анкерными связями:
1 – фундаментная рама; 2 – картер; 3 – блок цилиндров; 4 – анкерная связь
ется рациональной, если действую щие усилия замыкаются на элемен тах, работающих главным образом на сжатие и растяжение.
9.1.2. Блок картеры и подвески коленчатого вала автомобильных
итракторных двигателей
Всовременных автомобильных
итракторных двигателях жидко стного охлаждения цилиндры (ру башки цилиндров) выполнены литыми совместно с картером в виде блок картера. К преимуще ствам блок картерной конструк ции корпуса относятся: проч ность, жесткость, компактность, минимальное количество уплот няемых стыков. К недостаткам можно отнести сложность отлив ки блок картера, возможность по явления заметных остаточных де формаций (требуется отжиг отли вок), необходимость замены всего дорогостоящего блок картера при появлении трещин в верхней пли те или в боковой стенке (рубашке цилиндров) одного из цилиндров.
Масса блок картера в чугунном исполнении составляет 23–37 % массы рядного двигателя с прину дительным воспламенением и 22– 26 % массы V образного дизеля. Изготовление блок картера с по мощью литья под давлением из алюминиевых сплавов позволяет до 60 % снизить массу блок картера.
Компоновка двигателя примени тельно к выбранной схеме располо жения цилиндров во многом связана с компоновкой блок картера. Суть компоновки заключается в опреде лении геометрических размеров конструкции на основании опыта предыдущих моделей и предвари тельных расчетно эксперименталь ных проработок, в том числе с при менением современных методов ин женерного анализа (в первую оче
345
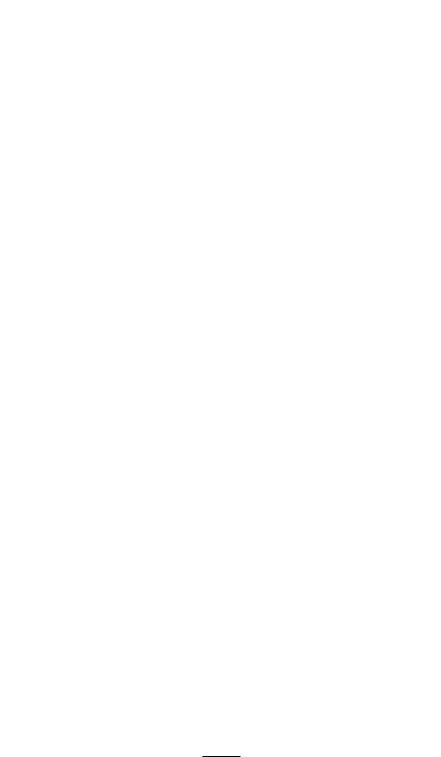
Рис. 9.5. Продольная (а) и поперечная (б) компоновки блок картера
редь, МКЭ). Накопленный опыт вы ражается в виде эмпирических соот ношений, устанавливающих разме ры элементов корпуса в зависимости от диаметра цилиндра двигателя.
На рис. 9.5 представлена схема компоновки блок картера рядного автомобильного двигателя. Опреде ляющим размером блок картера, влияющим на массогабаритные, прочностные и ряд других показате лей двигателя в целом, является рас стояние между осями соседних ци линдров L0 – межцилиндровое рас стояние (рис. 9.5, а). При наличии между цилиндрами охлаждающей
полости шириной ,охл L0 = D + 2,ст + + ,охл (здесь ,ст – толщина стенки цилиндра). Для уменьшения длины блок картера часто отказываются от охлаждающей полости между ци линдрами. В этом случае L0 = D + ,ст и достигается наименьшее отноше ние L0/D, доходящее до 1,10–1,15. В среднем L0/D составляет в рядных автомобильных двигателях с прину дительным воспламенением 1,20– 1,24 и 1,25–1,35 в рядных дизелях.
В V образных двигателях L0/D выше, что связано с установкой на
шатунных шейках коленчатого вала двух рядом расположенных шату нов. В этом случае уменьшение L0/D достигается сокращением дли ны шатунного подшипника, а также применением роликовых подшип ников. В среднем L0/D составляет 1,30–1,35 для V образного автомо бильного двигателя с принудитель ным воспламенением и 1,47–1,55 для V образных дизелей. В двигате лях с воздушным охлаждением L0 больше на 15–20 % по сравнению с двигателями жидкостного охлажде ния. Б льшие значения L0/D харак терны для тракторных двигателей.
На рис. 9.5, б представлена схема поперечной компоновки блок картера рядного автомо бильного двигателя. После нане сения осей цилиндра, коленчато го вала, а также распределитель ного вала при его нижнем распо ложении и валов других механиз мов и агрегатов наносится контур блок картера с учетом требования проворачиваемости кривошипно шатунного механизма при уста новленных на коленчатом валу противовесах. При нижнем поло
346
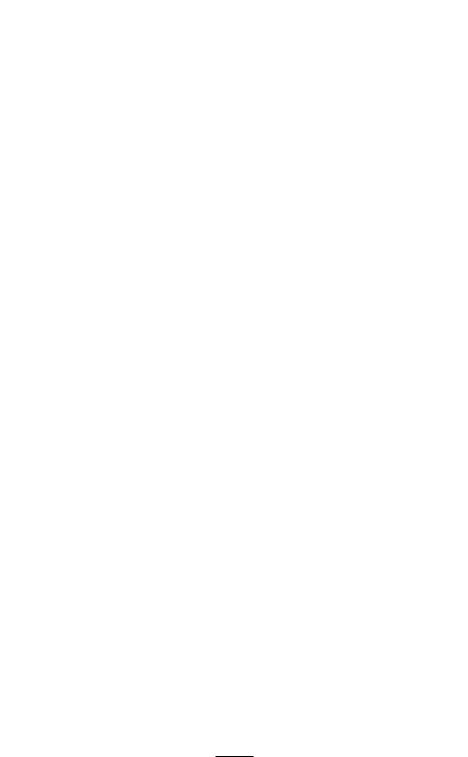
Рис. 9.6. Блок картеры V образных дизелей:
а – тракторного; б – автомобильного
жении распределительного вала следует поднять его относительно коленчатого вала как можно вы ше для уменьшения массы эле ментов механизма газораспреде ления. На поперечной компонов ке предусматривается идущий вдоль картера сверленый канал – главная масляная магистраль, ку да поступает очищенное в фильт ре смазочное масло и откуда оно по дополнительным каналам по дается к коренным опорам колен чатого вала, опорам распредели тельного вала и далее к другим местам смазки. Диаметр канала главной магистрали составляет 12–14 мм, а диаметр отводных каналов 6–8 мм.
Высота блок картера ориенти ровочно составляет Нбк = L + R +
+ Н3 + hк ,1 (где hк – расстоя ние от оси коленчатого вала до
нижней плоскости картера – плоскости разъема картера и под дона; ,1 – величина выхода го ловки поршня при положении в ВМТ из цилиндра, часто ,1 = 0). Протяженность зеркала цилиндра Lц = Нп + S (,1 + ,2), где ,2 –
выход юбки поршня при положе нии в НМТ из цилиндра; ориен тировочно ,2 = 5–15 мм.
Ширина нижней части блок картера Вк больше ширины верхней части (блока цилиндров) В. Шири на зависит от принятой схемы при вода клапанов, включая расположе ние распределительного вала, нали чия приливов под насос охлаждаю щей жидкости и другие устройства.
На рис. 9.6 (а, б) представлены блок картеры V образных автомо бильного и тракторного дизелей. В конструкции корпуса двигателя осо бое внимание уделяется жесткости верхней части блока цилиндров и нижней зоны картера, где размеща ются подшипники коленчатого вала. Под жесткостью понимается способ ность конструкции сопротивляться действию нагрузок с деформациями, не нарушающими работоспособ ность системы (двигателя). Для уменьшения деформаций гильзы ци линдра (при вставной мокрой гиль зе) должна быть обеспечена высокая жесткость верхней плиты блока ци линдров, которая не должна заметно деформироваться под действием
347

монтажной и газовой нагрузок. Вол нообразное деформирование опор ного пояса верхнего бурта гильзы под действием дискретных усилий затяжки шпилек приводит к соответ ствующей деформации гильзы с на рушением ее цилиндрической фор мы. Толщина верхней плиты блока цилиндров достигает 20 мм, толщи на боковых стенок блок картера в чугунном исполнении составляет 4– 7 мм и зависит от размеров двигате ля и уровня технологии литейного производства. Конструкции из алю миниевых сплавов имеют толщину на 1–2 мм больше по сравнению с чугунными.
Блок цилиндров включает по лость охлаждения, окружающую цилиндры (гильзы цилиндров). Протяженность полости охлаж дения (рубашки) вдоль оси ци линдра выбирается, исходя из обеспечения желаемых темпера турных полей поршня и самого цилиндра. При этом желательно получить по возможности не большой перепад температур по длине цилиндра (гильзы цилинд ра), что позволит сохранить пра вильную форму цилиндра и улуч шить условия работы поршневой группы. Верхняя часть блока ци линдров должна интенсивно ох лаждаться, и при положении поршня в ВМТ первое поршневое кольцо должно находиться в пре делах полости охлаждения ци линдра. Наибольшее снижение температуры головки поршня и зоны первого поршневого кольца будет при расположении его в НМТ в пределах полости охлаж дения цилиндра. Однако темпе ратура нижней части цилиндра может оказаться излишне низ кой. В этом случае протяжен ность охлаждающей полости це лесообразно уменьшить. С помо
щью математического моделиро вания возможно найти оптималь ное решение. Чем меньше диа метр цилиндра D, тем короче мо жет быть выполнена рубашка ох лаждения с целью получения бо лее равномерного распределения температуры по длине цилиндра. Ширина полости охлаждения не должна быть слишком малой [ориентировочно ,охл = (0,10– 0,15)D] во избежание ухудшения условий охлаждения.
Нижняя часть блок картера (собственно корпуса) должна быть весьма жесткой, обеспечивая ми нимальные смещения коренных опор коленчатого вала под дейст вием вертикальной и горизонталь ной составляющих газовой и инер ционной нагрузок. Повышение жесткости блок картера достигает ся оребрением перегородок, рас положенных в плоскостях корен ных подшипников, размещением укрепляющих ребер, связывающих полукольцевые приливы гнезд ко ренных подшипников, приливы под установку резьбовых элемен тов с боковыми стенками блок картера, понижением нижней плоскости блок картера относи тельно линии осей коренных опор коленчатого вала. В этом случае силы и моменты воспринимаются б льшим объемом материала кон струкции. Весьма эффективна ус тановка поперечных болтов, фик сирующих коренные опоры в го ризонтальном направлении. Сле дует отметить, что поперечные стяжки в области коренных опор были применены еще в известном двигателе В 2 (см. рис. 9.3). В ряде конструкций автомобильных дви гателей для повышения жесткости крышки коренных опор коленча того вала объединяются в единую раму, что также улучшает и виб
348

роакустические характеристики двигателя.
Наконец, жесткость может быть увеличена применением тун нельного картера без разъема по коренным подшипникам. В этом случае в качестве коренных опор применяются, как правило, роли ковые подшипники, что позволя ет уменьшить межцилиндровое расстояние L0. Последнее способ ствовало применению туннель ных картеров в двигателях специ ального назначения.
Коренные опоры коленчатого вала образуются с помощью подве сок 1 (рис. 9.6, б), представляющих собой съемные крышки коренных подшипников, крепящиеся к кар теру двигателя с помощью шпилек или болтов 2. Подвеска вместе с расточкой в картере образует гнез до, в которое устанавливают вкла дыши подшипника. Применение подвесок дает возможность исполь зовать легкий поддон вместо тяже лого нижнего картера, обеспечива ет удобство конвейерной сборки, легкость контроля состояния лю бого подшипника и коленчатого вала.
Подвески выполняются доста точно массивными, часто двутав рового сечения, как правило, из одинакового с картером материа ла. Основным требованием к кон струкции подвески является обес печение малых деформаций вкла дышей коренных подшипников при работе двигателя. Высота под вески Нпод (см. рис. 9.5) часто пре вышает диаметр коренной шейки d1 коленчатого вала, расстояние между осями отверстий под кре пежные болты следует по возмож ности уменьшать ориентировочно до Lпод = (1,0–1,01)D. Установка и фиксация крышек подшипников (подвесок) обеспечивается устано
вочными штифтами, направляю щими втулками, призонными бол тами и стенками пазов в картере, препятствующими боковым пере мещениям подвески. С увеличени ем нагрузок на подшипниковые узлы в V образных автомобильных
итракторных дизелях крышки ко ренных подшипников закрепля ются не только в вертикальном на правлении, но и в горизонтальном с помощью дополнительных бол тов 3 (рис. 9.6, б), которые зажима ют крышку между боковыми вер тикальными направляющими кар тера. Стык в сопряжении подвески с картером выполняется плоским или с применением треугольных шлиц, которые могут восприни мать значительные горизонталь ные усилия. Однако в сочетании с дополнительными горизонтальны ми болтами предпочтение отдается плоскому стыку. Подвески (крыш ки) крепят к картеру двумя или че тырьмя (при относительно длин ных подшипниках) шпильками или болтами. Для предотвращения ослабления резьбы при повторных ввертываниях особенно при вы полнении картера из алюминиево го сплава предпочтительно приме нение шпилек. Для обеспечения плотности посадки по стыковой поверхности резьбу следует заглуб лять, так как наличие витков у опорной поверхности может нару шить ее плоскостность.
Дальнейшее повышение жест кости коренных опор коленчатого вала и всего картера достигается объединением отдельных подве сок в одну литую раму (рис. 9.7, а) или введением дополнительной рамы, соединяемой с подвесками
икартером общими болтами (рис. 9.7, б). Высокая жесткость достигается при разъемном карте ре, когда его нижняя часть пред
349
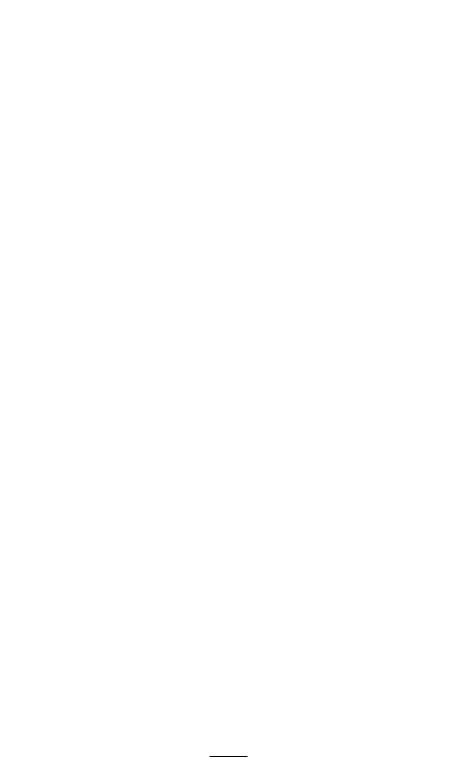
Рис. 9.7. Коренные опоры коленчатого вала:
а – в виде литой рамы; б – в виде дополнительной рамы, соединенной с подвесками и картером
ставляет собой одно целое с ко ренными опорами коленчатого вала. Снизу устанавливается лег кий поддон.
9.1.3. Картеры, блоки цилиндров
иблок картеры тепловозных
исудовых среднеоборотных двигателей
Всовременных двигателях этого класса отсутствуют, как правило, анкерные связи и предусматривает ся полная замкнутость сил от давле ния газов в пределах одной детали, как правило, картера или блок кар тера. Таким образом, корпус явля ется несущим, будучи нагруженным весьма значительными растягиваю щими усилиями, обусловленными значительными размерами цилинд ра и все возрастающим максималь ным давлением газов, достигающим 18–20 МПа. Здесь также важным требованием к конструкции являет ся жесткость, во многом опреде ляющая работоспособность двига теля в целом. Недостаточная жест кость корпуса нарушает нормаль ную работу кривошипно шатунного
идругих механизмов, вызывает по
вышенные кромочные давления в подшипниках, приводит к возник новению очагов полусухого трения с возможностью перегрева и заеда ния элементов подвижных сопря жений, создает опасность наруше ния герметичности стыков, появле ния фретинг коррозии и др.
Блок картеры тепловозных и среднеоборотных судовых двигате лей изготавливают в виде отливок (в основном чугунных) или в виде сварно литой (сварной) конструк ции. В последнем случае технологи ческий процесс сварки предъявляет особые требования к конструкции: обеспечение возможности примене ния листовых элементов и связан ные с этим ограничения в выборе формы. К недостаткам сварной кон струкции относится необходимость расположения сварных швов в мес тах изменения формы детали, что может привести к увеличению на пряжений в связи с ростом неравно мерности их распределения. К пре имуществам сварно литой конструк ции относятся меньшая масса в свя зи с уменьшением толщины стенок, б льшая прочность вследствие пре
350