
Chainov_Ivashenko_Konstr_dvs_1 / Чайнов Иващенко - Конструирование ДВС
.pdf
Рис. 5.22. Схемы нагружения главного шатуна при положе нии поршня в ВМТ:
а, б – соответственно в глав ном и боковом цилиндрах
стержня (при сборке) штифтами, специальными центрирующими вы ступами в разъеме или с применени ем сплит технологии. Ввиду нали чия опорных площадок под шатун ные болты и гайки шатунных болтов кривошипные головки имеют харак терные угловые выступы и большую неравномерность жесткости.
Вследствие ограничения внеш него размера кривошипной голов ки при обычно принимаемых диа метрах шатунной шейки коленча того вала, близких к диаметру ци линдра, резко сокращается ради альная толщина головки в зоне разъема, что приводит к уменьше
нию размера стыкового сечения. Для повышения жесткости головки и устранения вынужденного ослабле ния зоны разъема обычно увеличи вают высоту средней части крышки, выполняя ее в виде двутаврового профиля с двусторонними выемка ми вблизи нейтрального слоя крыш ки (рис. 5.23).
Отмеченные недостатки криво шипных головок с прямым разъе мом (см. рис. 5.3, а) привели к ши рокому распространению головок с косым разъемом, у которых плос кость стыков располагается под оп ределенным углом наклона к оси стержня (см. рис. 5.3, б). Согласно
201

Рис. 5.23. Виды средней части крышек шату нов:
а, б – с плавным очертанием контура; в, г – с ребрами жесткости; д – с утолщенной сред ней частью; е – двутавровый
выполненным расчетам, оптималь ные значения угла & (см. рис. 5.3) наклона плоскости разъема к оси стержня шатуна находятся в преде лах 42–50 .
В связи с появлением в косом разъеме под действием нагрузок значительных переменных сил сдвига стыковые поверхности в го ловках такого типа выполняют профильными, так как в них обра зуются несущие замкнутые элемен ты для упругого сопротивления по перечным усилиям.
Совершенствование формы го ловки достигается симметричным перераспределением радиальной тол щины несущего контура и переходом к крышке с нарастающей высотой ее сечений при приближении к зоне нижних шатунных болтов.
Несмотря на дополнительные технологические трудности изготов ления и сборки, симметричная отно сительно продольной оси шатуна форма головки больше соответствует оптимальному варианту шатунов рядного типа. При такой конструк
ции головки снижается масса и обеспечиваются достаточные проч ность и жесткость, повышается на дежность шатунных подшипников в условиях длительной работы.
Для возможности извлечения шатуна через цилиндр и одновре менно получения улучшенной фор мы несущего контура таких головок в болтовых соединениях часто не применяют гайки, а шатунные бол ты ввертываются непосредственно в шатун. Недостатком конструкций с косым разъемом является отсутст вие симметрии.
Для исключения поломок в зонах глухих резьбовых отверстий под ша тунные болты предъявляются высо кие требования к геометрии резьбы, плавности перехода боковой поверх ности и дна отверстия, шероховато сти и контролю качества материала.
Шатунные болты должны отве чать в первую очередь требованиям прочности и высокой надежности при длительной работе. Шатунные болты различных типов показаны на рис. 5.24. Переход от резьбы к стержню выполняют в виде проточ ки радиусом 1, равным не менее 0,2dp, на участке длиной не менее 0,4–0,5 диаметра резьбы. Сопряже ние стержня с головкой выполняют радиусом 3 = (0,15–0,25)dc, а пере ход к центрирующим пояскам – ра диусом 2 = (0,2–0,25)dп.
Надежность болтов обеспечива ется плавностью переходов с зада нием допусков на радиусы сопря жений (от головки болта к стержню и к центрирующим пояскам, во впадинах профиля резьбы), рацио нальной податливостью стержня болта для уменьшения изгибных напряжений в резьбе, применени ем поверхностной упрочняющей обработки (обкатки радиусов и впадин резьбы), выбором материа ла с повышенным сопротивлением
202
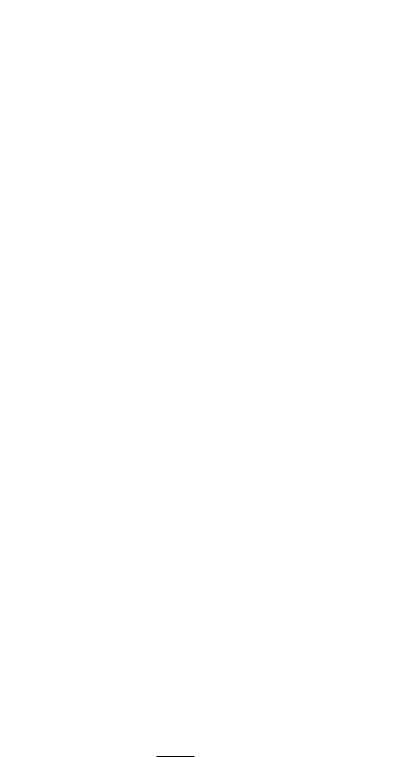
Рис. 5.24. Типы шатунных болтов
усталости при высоком сопротив лении пластическим деформациям от начальных усилий затяжки.
5.3. Особенности конструкции шатунной группы крейцкопфных двигателей
Шатуны крейцкопфных двигате лей ввиду больших размеров выпол няют со съемными и разъемными кривошипными и крейцкопфными головками морского типа (рис. 5.25) и прокладками для регулирования степени сжатия в цилиндрах и зазо ров в подшипниках.
Стержень шатуна выполняют обычно цилиндрическим с отверсти ем для подвода масла к головным подшипникам, охлаждающей жид кости в поршни. В последних кон струкциях верхнюю часть стержня выполняют не только вильчатой, но и в виде жесткой плоской пяты (рис. 5.26), на которой монтируют крейцкопфные головки, что упро
Рис. 5.25. Вильчатый шатун крейцкопфного двигателя:
1 – кривошипная головка; 2 – стержень; 3 – поршневая головка
203

Рис. 5.26. Крепление што ка в поперечине:
а, б – цилиндрическим хвостовиком соответст венно с опорной и за тяжной гайками и опор ным конусом; в – флан цем
щает изготовление шатунов и по зволяет согласовывать деформации подшипников и поперечины.
Для облегчения подгонки массы и повышения прочности все по верхности шатуна и головок под вергают механической обработке. Так как опорным поверхностям ползуна проще задать необходимые размеры, чем поршню двигателя тронкового типа, и смазать их лег че, то шатуны крейцкопфных дви гателей выполняют более коротки ми (R/L = 1/2,5–1/2,0), что умень шает высоту двигателей.
Штоки (стержни) поршней в
крейцкопфных двигателях связы вают поршень с поперечиной.
Если поршни охлаждаются во дой, то полость штока изолируют от нее защитным покрытием или трубой из меди или коррозионно стойкой стали. Охлаждающая жид кость подводится через кольцевое сечение между трубой и штоком, а отводится трубой, вмонтированной в полость штока.
Форма концов штока зависит от способа крепления его к поршню и поперечине ползуна. Шток соединя ется с поршнем с помощью фланце вого соединения, а к поперечине шток крепится цилиндрическими хвостовиками (рис. 5.26, а, б) или фланцами (рис. 5.26, в). В последнем
случае болты или шпильки разгру жаются от боковых сил шпонкой, штифтами, центрирующим бурти ком или выступом и пазом, выпол няемыми в сопрягаемых деталях.
Диаметр dшт штока выбирают в пределах (0,305–0,350)D; диаметр от верстия в штоке (0,425–0,504)dшт, длину штока в пределах (2,67–3,15)D.
Штоки изготавливают ковкой с последующей механической и тер мической обработкой до твердости 40–52 HRC.
Шток соединяется с шатуном поперечиной. Твердость поверхно сти цапфы, соединяющей попере чину с шатуном, составляет около 40–45 HRC.
Форма поперечины зависит от способа соединения ее со штоком, шатуном и конструкции ползуна. Поперечина имеет гнездо для кре пления хвостовика штока или опорную поверхность для фланца штока.
Ползуны крепят к средней части поперечины болтами, шпильками и шпонками или штифтами (рис. 5.27). Цапфы для вильчатого шатуна образуют в этом случае консоли поперечины.
В односторонних ползунах (рис. 5.28, а) трущиеся поверхно сти отличаются друг от друга раз мерами.
204

Рис. 5.27. Крепление одностороннего ползуна к поперечине болтами и шпонкой:
1 – шток; 2 – поперечина; 3 – ползун; 4 – шпонка; 5 – гайка; 6 – болт
Если для каждой поперечины используют два ползуна, установ ленные по обе стороны плоскости качания шатуна (рис. 5.28, б), то они располагаются на особых шей ках, образующих концы поперечи ны. Цапфы шатуна размещают в таких случаях между средней и концевыми частями поперечины.
Ползун воспринимает боковые усилия от шатуна и обеспечивает пря молинейное движение штока. Тру щаяся поверхность ползуна выполня ется плоской или цилиндрической.
Двусторонние ползуны (рис. 5.28, б, в) располагают по концам цапфы, благодаря чему достигается легкий доступ к подшипникам, а также воз можность использования более ко ротких шатунов и крепления стоек станины направляющими ползунов для увеличения жесткости остова дви гателя. Трущиеся поверхности ползу нов заливают баббитом.
Рис. 5.28. Ползуны:
а – односторонний; б, в – двусторонний с опорной поверхностью соответственно плоской и цилиндрической
205

Рис. 5.29. Шатуны крейцкопфного двигателя:
а – с двусторонним ползуном; б – с односторонним ползуном; 1 – поперечина; 2 – ползун; 3 – верхняя (крейцкопфная) головка; 4 – стержень (шток); 5 – прокладка; 6 – болт
Шатуны крейцкопфных двига телей с одно и двухсторонними ползунами показаны соответствен но на рис. 5.29, а, б.
Габариты поперечины определя
ются размерами мест сопряжений ее со штоком и ползуном; диаметры цапф подшипников шатунов d1 (рис. 5.30, а) выбирают в пределах (0,55–0,61)D, а длину l1 = (0,5–0,8)d1.
Рис. 5.30. Схемы для расчета на прочность и изнашивание:
а – поперечины; б – ползуна
206

5.4. Методы повышения несущей способности шатунов, материалы шатунов
Шатуны большей частью изго товляют ковкой в штампах с по следующей термической и меха нической обработкой. В качестве материала для изготовления ша тунов наиболее часто применяют углеродистую или легированную сталь.
Для шатунов форсированных двигателей целесообразно приме нять легированные стали, учитывая необходимость обеспечения доста точной циклической прочности без значительного увеличения разме ров опасных сечений, а также по лучения однородных свойств ме талла в детали после термообработ ки, т.е. достижения равномерной прокаливаемости по сечениям.
Рекомендуемые легированные стали, проверенные длительным опытом производства и эксплуата ции двигателей с учетом выбора из них умеренно легированных, сле дующие:
•для шатунов автомобильных двигателей с принудительным вос пламенением – стали 40Г, 45Г2, 40Х, 40ХН;
•для автомобильных и трактор ных дизелей – стали 18Х2Н4МА; 40ХН2МА; 40ХН3МА; возможно также применение ковкого перлит ного чугуна;
•для высоконагруженных ша тунов, имеющих достаточно боль шие размеры сечений, – стали 18Х2Н4МА, 40ХН2МА, 40Х2Н2МА, 36Х2Н2МФА, 30ХМА, 40ХФА;
•для шатунов форсированных быстроходных дизелей – стали 18Х2Н4МА, 40ХН2МА, 38Х2Н2МА, 30ГМ;
•для шатунов стационарных
ималооборотных судовых двига
телей – стали 40Х, 45Х, 40ХН, 45Г2.
Углеродистые стали находят при менение для шатунов относительно небольших размеров при умеренной их напряженности или шатунов наи более крупных размеров.
Для реализации высоких проч ностных свойств легированных сталей необходимо учитывать их повышенную чувствительность к качеству поверхности, т.е. к ее макро и микрогеометрии, со стоянию поверхностного слоя и др. При необработанной поверх ности после штамповки может быть потеряно 50–70 % цикличе ской прочности материала. При чиной такого снижения является, помимо влияния грубой обработ ки поверхности, наличие ослаб ленного слоя металла, в котором вследствие высоких повторных нагревов при штамповке и термо обработке (закалке) выгорает зна чительная часть углерода и леги рующих элементов.
Толщина так называемого обез углероженного слоя после штам повки и термообработки шатуна пропорциональна времени нахо ждения заготовки в нагреватель ной печи и определяется его раз мерами (для шатунов массой 100–150 кг она может достигать 1,0–1,5 мм).
Шатуны, выполняемые из леги рованных сталей, необходимо ме ханически обрабатывать (или за чищать) для удаления обезуглеро женного слоя или нагревать под штамповку в защитной среде. При толщине слоя до 0,3–0,4 мм, ос тающегося после зачистки или возникающего в предварительно обработанной детали после ее на грева под закалку, неблагоприят ное разупрочнение может быть полностью компенсировано обдув
207

кой поверхности стальной дробью (наклепа дробью).
При растягивающих напряже ниях в стержне более 20 МПа, ха рактерных для шатунов четырех тактных двигателей повышенной быстроходности, резко возрастает опасность развития усталостных трещин в поверхностном слое ос лабленного и поврежденного ме талла и возникновения последую щих поломок. Поэтому необходимо почти полное удаление обезуглеро женного слоя и проведение ком пенсирующей обработки чистой поверхности шатуна стальной дро бью для устранения возможного влияния остатков дефектного слоя в готовой детали.
Особое внимание следует уде лять выбору технологии обработ ки стержней главных шатунов V образных двигателей (четырех и двухтактных) ввиду появления в отдельных сечениях значитель ных напряжений изгиба от дейст вия прицепных шатунов.
Проведенные исследования и опыт эксплуатации двигателей по казали, что для шатунных болтов, а также для других болтовых соеди нений с большим усилием затяжки не следует применять легирован ные стали 18Х2Н4МА, 20ХНЗА и другие с низким содержанием угле рода, чтобы при длительной работе не накапливались пластические де формации (вытяжки) и не ослабе вали усилия затяжки.
У двухтактных двигателей при наличии в стержне только напря жений сжатия ослабляющий эф фект "черной" поверхности практи чески не проявляется, поэтому до полнительная обработка ее может быть минимальной (устранение окалины и очистка).
В отдельных случаях шатуны быстроходных двигателей изготав
ливают из легких алюминиевых и реже магниевых сплавов. Масса та ких шатунов меньше массы сталь ных на 20–25 %.
Значительный интерес для изго товления шатунов форсированных двигателей представляют титано вые сплавы. Обладая сравнимыми со сталями прочностными свойст вами, они имеют почти вдвое мень шую плотность. При этом устало стные свойства у титановых спла вов даже несколько выше, чем у сталей.
В последнее время появились титановые сплавы с повышенным содержанием алюминия (7,5–14 % массовых долей). В этом случае в сплаве выделяется интерметаллид титана Ti3Al, который упрочняет сплав и повышает его жесткостные свойства. Так, при увеличении со держания алюминия с 7,5 до 14 % массовых долей модуль упругости Е возрастает со 120 до 150 ГПа. Учи тывая, что сжимающие нагрузки, действующие на шатун, значитель но превосходят растягивающие, лучшее сопротивление напряжени ям сжатия титановых сплавов явля ется еще одним преимуществом этих материалов.
Кнедостаткам титановых спла вов следует отнести невысокую из носостойкость, склонность к пол зучести при нормальной темпера туре, бо' льшее снижение предела выносливости по сравнению со сталями при увеличении числа циклов нагружения свыше 107.
Кперспективным материалам могут быть отнесены композици онные материалы: полимерные во локнистые и металломатричные дисперсно упрочненные частица
ми керамики (Si3N4, Al2O3, B4C) размером 5–20 мкм, количество которых может колебаться от 5 до 30 % объема материала.
208

Шатунные болты разъемных го |
полняют литьем из сталей 20Л 50Л. |
||||||||||
ловок шатунов современных двигате |
Шатунные болты тепловозных двига |
||||||||||
лей изготовляют в основном из леги |
телей и быстроходных форсирован |
||||||||||
рованных конструкционных сталей, |
ных |
изготавливают |
из |
наиболее |
|||||||
малооборотных двигателей (в первую |
прочных и вязких хромоникельмо |
||||||||||
очередь двухтактных) – из углероди |
либденовых и хромоникельмолибде |
||||||||||
стых конструкционных сталей 35, 40, |
нованадиевых |
сталей |
30Х, |
35ЧЦ, |
|||||||
45 и других, а также хромоникелевых |
40ХН2МА, 40Х2Н2МА, |
38ХНЗМА, |
|||||||||
среднеуглеродистых сталей. Эти же |
36Х2Н2МФА, |
а |
автомобильных и |
||||||||
материалы используют для штоков |
тракторных двигателей – из легиро |
||||||||||
МОД. Стали 45, 50, а также хромомо |
ванных сталей 40Х, 45Х, 30ХМА, |
||||||||||
либденовые и хромоникелевые сред |
35ХМ, 40ХН2МА 40ХНМА. |
|
|||||||||
неуглеродистые стали применяют для |
Втулки верхних головок и наруж |
||||||||||
изготовления поперечин с последую |
ных обойм игольчатых подшипни |
||||||||||
щей термической обработкой. Ползу |
ков изготавливают из сталей ШХ |
||||||||||
ны малооборотных двигателей вы |
15Ш или ЭИ 347 (8Х4В9Ф2 Ш). |
||||||||||
5.2. Показатели материалов для изготовления шатунов двигателей внутреннего сгорания |
|||||||||||
|
|
|
|
|
|
|
|
||||
|
Сталь |
Сталь |
|
Сталь |
Титановый |
Алюминие |
Композит |
||||
Наименование |
40ХН2МА |
|
сплав Ti 6Al 4V |
вый сплав |
|
Д16Т + |
|||||
|
40ХН |
(SAE 4349) |
18Х2Н4МА |
(США) |
|
Д16Т |
|
|
16 % SiC |
||
|
|
|
|
|
|
|
|
|
|
|
|
Плотность , г/см3 |
7,85 |
7,85 |
|
7,95 |
4,43 |
|
2,8 |
|
|
2,9 |
|
Твердость, НВ |
200–320 |
217–333 |
|
262–400 |
255–340 |
|
105 |
|
|
|
|
|
|
|
|
|
|
|
|
|
|
|
|
Предел прочности при |
910 |
1000 |
|
940–1470 |
>930 |
|
460 |
|
|
547 |
|
растяжении в, МПа |
|
|
|
|
|
|
|
|
|
|
|
Предел текучести при |
710 |
850 |
|
710–1170 |
>862 |
|
300 |
|
|
465 |
|
растяжении 0,2, МПа |
|
|
|
|
|
|
|
|
|
|
|
Предел текучести при |
710 |
850 |
|
710–1170 |
917 |
|
285 |
|
|
– |
|
сжатии 0,2, МПа |
|
|
|
|
|
|
|
|
|
|
|
Модуль нормальной |
204 |
204 |
|
150 |
105–115 |
|
|
71 |
|
|
110 |
упругости при растяже |
|
|
|
|
|
|
|
|
|
|
|
нии E310 3, МПа |
|
|
|
|
|
|
|
|
|
|
|
Предел выносливости |
392–490 |
447 |
|
475–774 |
560 |
|
135 |
|
|
|
|
1, МПа |
|
|
|
|
|
|
|
|
|
|
|
Удельная прочность |
8,3 |
10,8 |
|
8,3–14,7 |
19,46 |
|
10,7 |
|
|
16 |
|
при растяжении |
|
|
|
|
|
|
|
|
|
|
|
/ *310 3, м |
|
|
|
|
|
|
|
|
|
|
|
0,2 |
|
|
|
|
|
|
|
|
|
|
|
Удельная прочность |
8,3 |
10,8 |
|
8,3–14,7 |
20,7 |
|
10,18 |
|
|
– |
|
при сжатии |
|
|
|
|
|
|
|
|
|
|
|
0,2/ *310 3, м |
|
|
|
|
|
|
|
|
|
|
|
Удельная жесткость |
2600 |
2600 |
|
1890 |
2370–2600 |
2530 |
|
|
3800 |
||
Е/ * 10 3, м |
|
|
|
|
|
|
|
|
|
|
|
Удельная выносли |
5–6,24 |
5,7 |
|
6–9,7 |
12,64 |
|
4,8 |
|
|
– |
|
вость 1/ *310 3, м |
|
|
|
|
|
|
|
|
|
|
|
П р и м е ч а н и е. = g, где – плотность; g = 9,81 м/с2. |
|
|
|
|
|
|
209

В качестве антифрикционных материалов для втулок используют ся следующие бронзы: оловянисто фосфористые БрОФ7,0 0,2 (НВ75 – 90), допускающие максимальные давления до 90 МПа; алюминиево железистые БрАЖ9 4 (НВ 110); оловянисто цинковые БрОЦ10 2 (НВ 110); бронза МЦХТ, легиро ванная цинком, хромом, титаном и имеющая НВ > 130.
Механические свойства некото рых материалов представлены в табл. 5.2.
5.5. Моделирование напряженно деформированного состояния, многоуровневая система математических моделей шатунной группы
5.5.1. Общие положения
Расчет напряженно деформиро ванного состояния шатуна может
быть выполнен с различной степе нью детализации особенностей кон струкции и условий нагружения. При этом применяются математиче ские модели разных уровней по глу бине и полноте отражения особен ностей формы, условий нагружения, свойств материала и др.
Эскизная разработка шатуна выполняется на основе статисти ческих данных по конструкциям, аналогичным проектируемой. Рас чет шатуна в настоящее время пре дусматривает использование как простейших методов сопротивле ния материалов в рамках одномер ной теории, так и уточненных ма тематических моделей с решением плоских и пространственных задач теории упругости численными ме тодами (модели второго и третьего уровней).
В эксплуатации шатун подверга ется действию переменных по вре мени сил, изменяющихся в широ ких пределах. На рис. 5.31 показано
Рис. 5.31. Изменение нагрузки, действующей на шатун на различных режимах:
а, б и в – по внешней скоростной характеристике (ВСХ); г – холостого хода; r – коэффи циент асимметрии цикла, r = Кmin/Кmax
210