
Управление качеством
..pdfсоответствие разрабатываемой продукции требованиям безопасности и санитарно-гигиеническим нормам, возможность сокращения номенклатуры и типоразмеров составных частей, а также дальнейшей унификации и уменьшения количества применяемых марок и сортаментов материалов, правильность оформления конструкторской документации. Такая проверка осуществляется службами нормоконтроля. Нормоконтроль является завершающей стадией разработки конструкторской документации. Одновременно осуществляется контроль технологический, при котором должны быть учтены условия предприятия-изготовителя.
Производственный контроль – контроль качества, осуществ-
ляемый при изготовлении продукции службой технического контроля. Он заключается в контроле производственного процесса и его результатов. Производственный контроль охватывает вспомогательные, подготовительные и технологические операции и должен быть организован таким образом, чтобы снизить брак в производстве, уменьшив объем доработок, потерь и отходов. При использовании рациональных методов контроля качество продукции должно улучшиться, а стоимость контроля снизиться.
Система контроля качества разрабатывается с таким расчетом, чтобы регулировать все отклонения технологического процесса, связанные с материалами, оборудованием, обслуживанием и условиями производства, которые влияют на качество продукции.
Каждому этапу технологического процесса должна соответствовать та или иная форма организации технического контроля.
Эксплуатационный контроль осуществляется, как правило,
в условиях эксплуатации после сдачи продукции потребителю. Насколько бы тщательно ни проводился контроль продукции в производственных условиях, практически невозможно учесть и воспроизвести все многообразие внешних воздействий, условий и режимов работы, встречающихся в реальных эксплуатационных условиях. Поэтому эксплуатационный контроль, проводимый путем наблюдения и сбора информации о надежности и других свойствах продукции, позволяет определить наиболее слабые места продукции, выявить основные виды разрушений и причины их возникновения, получить
121
фактические данные о показателях надежности, в частности ремонтопригодности.
Входной контроль заключается в контроле продукции поставщика, поступающей к потребителю (заказчику) и предназначенной для использования при изготовлении, ремонте и эксплуатации продукции. Он осуществляется при контроле материалов, полуфабрикатов и комплектующих изделий, поступающих на предприятие. Правильная организация входного контроля позволяет избежать выпуска дефектной продукции по причине использования недоброкачественного сырья, материалов и полуфабрикатов.
Операционный контроль состоит в контроле продукции или процесса во время выполнения или после завершения определенной операции. Он проводится на основе предварительно разработанной схемы с указанием технологических операций, во время или после которых следует операция технического контроля.
На промышленных предприятиях операционный контроль предусматривается:
♦при передаче изделий с одного участка на другой, из цеха
вцех и т.д.;
♦после технологических операций, возврат к которым для устранения несвоевременно обнаруженных дефектов связан с большими потерями и сложностью или практически неосуществим (операции, предшествующие нанесению гальванопокрытий, сборке идр.);
♦после технологических операций, на которых наиболее вероятно появление брака;
♦после операций, которые оказывают существенное влияние на качество продукции, особенно, если дефекты могут быть причиной аварии.
Приемочный контроль – это контроль готовой продукции, по результатам которого принимается решение о ее пригодности к поставке и использованию. Он является важным заключительным этапом всего процесса изготовления продукции.
В зависимости от полноты охвата контролем может быть предусмотрен сплошной или выборочный контроль.
Сплошной контроль – контроль, при котором решение о качестве продукции принимается по результатам проверки каждой еди-
122
ницы продукции. Такой контроль должен исключить возможность попадания к потребителю дефектной продукции. Сплошной контроль необходим, если дальнейшее использование недоброкачественных изделий приводит к большим убыткам или авариям. Функционально важные свойства таких изделий, как коленчатые валы и другие, должны контролироваться в каждом изделии. Однако сплошной контроль невозможен, если в процессе проверки изделие разрушается (например, при контроле показателей надежности изделий). Тогда достаточно в производстве применить выборочный контроль, при котором решение о качестве контролируемой продукции принимается по результатам проверки одной или нескольких выборок из партии.
Эффективный выборочный контроль можно организовать только на основании методов математической статистики, принимая во внимание как статистическую, так и практическую (техникоэкономическую) стороны, поскольку его применение не всегда можно считать целесообразным.
Летучий контроль является разновидностью предупредительного контроля, в ходе которого контролер или контрольный мастер Бюро технического контроля (БТК) периодически обходит закрепленные за ним рабочие места. При этом осуществляется выборочный контроль качества изготовленных рабочими деталей и проверяется соблюдение технологических процессов и дисциплины.
Разрушающий контроль применяют для получения показателей качества материалов (образцов и заготовок), деталей, узлов и машин в целом. Например, оценка механических свойств материалов проводится путем растяжения и сжатия, изгиба и кручения, воздействия коррозионной среды и др. Разрушающими методами контроля пользуются при определении показателей надежности изделий (наработка на отказ и др.). После проведения разрушающего контроля изделия становятся непригодными для дальнейшего использования по назначению.
Неразрушающий контроль осуществляется такими методами, которые не оказывают влияния на работоспособность изделия. Поэтому после проведения неразрушающего контроля изделие остается полностью пригодным к эксплуатации.
123
По степени использования измерительных средств и средств вычислительной и организационной техники выделяют измерительный контроль, характеризующийся процессами измерения параметров качества изделия на всех стадиях его жизненного цикла.
В тех случаях, когда нет необходимости в получении точных значений параметров качества продукции, а требуется провести ее идентификацию и количественную оценку численности (объем продукции, ее количество, вид, форма и т.д.), применяют регистрационный контроль. Эта форма контроля наиболее эффективно используется при контроле документации в управлении производством.
Контроль по контрольному образцу требует, как правило,
эталонирования продукции и использует сравнительный метод контроля изделия с эталонным (контрольным) образцом.
Органолептический контроль подразумевает осматривание и описание внешнего вида изделия с помощью средств обоняния, осязания, зрения человека. Он очень тесно связан с визуальным контролем – контролем внешнего вида изделия и, как правило, они применяются совместно.
Технический контроль предусматривает применение технических ручных, механизированных и автоматизированных средств в контрольных процедурах.
Особое место среди использованных на предприятии методов технического контроля отводится инспекционному контролю. Он осуществляется специально уполномоченными представителями с целью проверки эффективности ранее выполненного контроля. Инспекционный контроль не всегда сводится к повторению в том или ином объеме ранее выполненного контроля. Эффективность ранее проведенного контроля может, например, оцениваться проверкой правил выполнения контроля.
Испытания продукции – один из видов контроля качества продукции. Испытанием называется определение количественных и качественных характеристик свойств продукции в процессе функционирования, при имитации условий эксплуатации или при воспроизведении определенных воздействий на продукцию по заданной программе. В процессе испытаний изделие подвергается одному или
124

нескольким внешним воздействиям, например, вибрационным, тепловым, силовым, химическим, и производится регистрация интересующих исследователя свойств, характеризующих качество изделия: твердости, износостойкости, коррозионной стойкости и др.
Виды испытаний продукции классифицируют по признакам испытаний (табл. 2.7).
Объектами испытаний могут быть материалы, детали, узлы машин, машины и технические системы, включающие множество машин и приборов. Широко распространены испытания отдельных частей машин, в частности, испытания редукторов и коробок передач на долговечность, а также деталей машин: валов на изгиб, подшипников на изнашивание.
|
Таблица 2 . 7 |
Виды испытаний продукции |
|
|
|
Признаки испытаний |
Видыиспытаний |
Цельиспытаний |
Контрольныеиспытания |
|
Исследовательские испытания |
|
Граничныеиспытания |
Наличиебазы длясравнения |
Сравнительные испытания (идентификация) |
Точностьзначения параметров |
Определительные испытания |
|
Оценочныеиспытания |
Этапыразработки продукции |
Доводочныеиспытания |
|
Предварительные испытания |
|
Приемочныеиспытания |
Уровеньпроведения |
Ведомственные испытания |
|
Межведомственные испытания |
|
Государственные испытания |
Этапыпроцесса |
Испытанияпривходномконтроле |
|
Испытанияприоперационном контроле |
|
Приемо-сдаточныеиспытания |
Оценкауровнякачества |
Аттестационныеиспытания |
Продолжительность проведения |
Ускоренные испытания |
|
Нормальныеиспытания |
Степеньинтенсификации |
Форсированныеиспытания |
|
Сокращенные испытания |
Влияниенавозможностьпоследую- |
Разрушающие испытания |
щего использования продукции |
Неразрушающиеиспытания |
Местопроведения |
Полигонныеиспытания |
|
Эксплуатационные испытания |
125
Методом испытаний называют совокупность правил применения определенных принципов осуществления испытаний.
На многие виды испытаний существуют стандарты, устанавливающие условия испытаний, режимы, форму и размеры образцов, перечень регистрируемых параметров, правила, устанавливающие объем выборки, порядок проведения испытаний и критерии их прекращения.
Выбор режима является важным моментом при планировании испытаний, при этом под режимом испытаний понимают совокупность следующих факторов, определяющих механизм и интенсивность процессов разрушения:
♦нагрузка и напряжение;
♦скорость и частота положения нагрузок;
♦условия испытаний, температура, взаимодействие отдельных частей, свойства и количество смазки, содержание и свойства абразивных частиц и т.д.;
♦состояние окружающей среды (температура, давление, агрессивность).
Выбор режима испытаний особенно важен при ускоренных испытаниях. Режим ускоренных испытаний существенно отличается от режима нормальной эксплуатации изделия, однако оба режима должны быть связаны как качественно, так и количественно.
Основным классифицированным признаком испытаний продукции является цель испытаний.
Контрольные испытания проводятся для контроля качества продукции в процессе производства, эксплуатации и хранения. Эти испытания проводят только на натуральных образцах. К категории контрольных испытаний относят, например, предварительные и приемочные испытания. Предварительные испытания опытных образцов (партий) проводят для определения возможности их предъявления на приемочные испытания.
Контрольные испытания опытных образцов (партий), проводимые для решения вопроса о целесообразности постановки этой продукции на производство или передачи ее в эксплуатацию, называются приемочными испытаниями.
126
Исследовательские испытания необходимы для изучения опре-
деленных свойств продукции. Такими свойствами могут быть механическая прочность, износостойкость, коррозионная стойкость и др. Эти испытания можно проводить как на натурных образцах, так и на макетах. Получаемая информация о свойствах материалов и конструкций важна при освоенииновых изделий илиихмодернизации.
Граничные испытания относятся к категории исследовательских испытаний, проводимых для определения зависимости между допустимыми значениями параметров продукции и значениями параметров режимов эксплуатации. Такие испытания проводят с целью оценки предела прочности, допустимых нагрузок, скоростей, мощности и др.
Особое место среди разновидностей исследовательских испытаний занимают эксплуатационные испытания готовой продукции. Это связано с тем, что как бы тщательно ни планировались испытания, в лабораторных условиях практически невозможно воспроизвести все многообразие факторов, определяющих внешние воздействия, условия и режимы, встречающиеся в реальных эксплуатационных условиях. Для разработчика и изготовителя получаемые при испытаниях сведения позволяют судить о правильности функционирования, надежности и других показателях качества продукции.
Автоматизированный контроль качества продукции имеет своей целью повышение быстродействия и точности измерительных операций, сокращение времени на обработку и оценку результатов измерений, а также повышение объективности контрольных операций. При этом в современном производстве автоматизируются как подготовительные операции контроля, так и другие операции измерения, последующей обработки результатов измерений, их оценки, а при активном контроле и подготовки программ корректировки технологических режимов.
При пассивном контроле продукции либо пооперационно, либо комплексно автоматизация контрольных операций производится, как правило, с помощью универсальных средств многофункционального действия, либо с применением специализированных приборов, устройств, стендов и т.д.
127
Для автоматизации средств контроля используют различные системы измерительных устройств, которые классифицируются по параметрическому признаку и обладают своими особенностями, используемыми при определенных видах контроля.
Основными факторами, определяющими выбор средств контроля, являются: вид параметра, точность изготовления, величина партии, форма и размеры контролируемых деталей и экономическая эффективность применения средств контроля.
Активный контроль в автоматизированных решениях применяют, как правило, во время выполнения технологических операций или во всем процессе. При этом методы контроля деталей делят на прямые и косвенные.
При прямом методе, например, контролируют непосредственно размер обрабатываемой детали.
При косвенном – определяют параметры, косвенно связанные с основным параметром детали, например, положение обрабатываемой поверхности относительно контрольной базы или величину перемещения суппорта станка, несущего режущий инструмент.
Устройства прямого метода обеспечивают более высокую точность контроля, так как имеется возможность устранить многие составляющие погрешности контроля.
Преимуществами косвенного метода являются размещение контрольного устройства вне рабочей зоны станка и более простая конфигурация измерительной схемы, а также возможность использовать стандартизованные или типовые отсчетные устройства.
2.21. ТЕОРИЯ ОЦЕНОК И ИНТЕГРАЛЬНЫЕ ПОКАЗАТЕЛИ ОЦЕНКИ КАЧЕСТВА
Оценку уровня качества продукции проводят для следующих целей:
♦планирования и оптимизации качества продукции;
♦аттестации продукции;
♦выбора оптимального варианта продукции при разработке
ипостановке ее на производство;
128
♦анализа динамики уровня качества продукции;
♦контроля качества продукции и т. д.
Оценка проводится сравнением показателей качества продукции с базовыми показателями – показателями качества конкретных изделий (аналогов) перспективного образца, а также установленными стандартами или техническими условиями.
На первом этапе оценки набирают номенклатуру показателей качества – оценочной (оцениваемой продукции) с учетом цели оценки, условий использования продукции и анализа требований потребителей ибазовыхпоказателей.
Выбор значений базовых показателей зависит от цели проводимой оценки. Так, при контроле качества продукции целью оценки является проверка соответствия качества контролируемой продукции требованиям, установленным в технической документации, следовательно, базовыми показателями служат нормативные показатели качества. При оценке уровня качества продукции, проводимой с целью анализа динамики качества выпускаемой продукции, базовыми показателями являются показатели качества продукции, достигнутые в период, предшествующий оценке.
Более сложно решается вопрос о выборе базовых показателей при аттестации продукции на высшую, первую или вторую категории качества и определении соответствия вновь разрабатываемой продукции высшей категории качества и возможности постановки ее на производство.
Обычно базовые показатели выбираются и устанавливаются для каждого конкретного вида продукции соответствующими отраслевыми и научно-исследовательскими институтами, а также головными или центральными проектно-конструкторскими бюро на основании имеющейся в отрасли информации об аналогичной продукции и новых научных достижениях в данной области.
Следующим этапом работ по оценке является определение значений показателей качества продукции.
Для оценки деятельности фирм применяют метод самооценки. Уровень работ по качеству следует оценивать по системе жестких и многообразных критериев. Подразумевается, что система
129
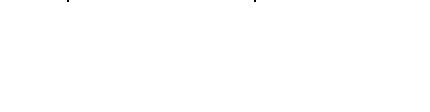
качества любой организации должна быть готова для конкуренции на рынке, она никогда не может быть закончена и предполагает непрерывное совершенствование. Компания совершенно не обязательно должна принимать участие в том или ином конкурсе по качеству, но ей предлагается механизм проведения самооценки путем использования тех же самых критериев, что используются и в национальных премиях по качеству.
Рассмотрим модель (рис. 2.15) и критерии для оценки работы фирм, исходя из главной цели: максимальное удовлетворение запросов потребителей при минимальном использовании ресурсов и постоянном совершенствовании. (Под потребителями в данном случае понимаются все, кто на законных основаниях ожидают результатов деятельности компании как в настоящий момент времени, так и в будущем.) В этой модели ключевой элемент – запросы. Фирма отвечает на эти запросы путем активизации процессов, в результате которых создается изделие. Точка, где изделия смыкаются с запросами, является точкой создания удовлетворенности потре-
бителя. Степенью удовлетворенности покупателя измеряются результаты. Кроме результатов и процессов модель также имеет такой элемент, как собственно система качества.
|
Управление |
|
Удовлетворение |
|
|
Персоналом9 % |
|
персонала9 % |
|
Лидерство |
Политика |
Управление |
Удовлетворение |
Исполнение |
10 % |
истратегия8 % |
процессом14 % |
потребителя20 % |
15 % |
|
Управление |
|
Связисобщес- |
|
|
ресурсами9 % |
|
твенностью6 % |
|
|
Организация50 |
% |
Результаты |
50 % |
Рис. 2.15. Модель оценивания
Рассмотрим (табл. 2.8), какие существуют группы критериев и как достигается максимальное количество баллов.
Пояснения: в модели выделяются 9 ключевых областей: 5 относятсяктому, какорганизованоуправлениекачеством; 4 – кегорезультатам.
130