
Практикум по организации и планированию машиностроительного произво
..pdfИз планировки определяем площадь поточной линии: площадь: 19м х 5м = 95 м2.
Выработка на 1 м2 площади
Чк..м= 376/95= 3,96 шт/м2.
Пример 2. О п р е д е л и т ь такт линии, рассчитать число рабочих мест, количество рабочих и степень их загрузки (занятости). Выбрать тип и определить основные параметры конвейера, составить таблицу распределения разметочных знаков. О п р ед ел и ть длительность цик ла обработки детали.
Исходные данные. Линия предназначенадля обработки шестерен при вода насоса, масса которых до обработки составляет 3,8 кг, диаметр — 100 мм. Программа запуска в смену — 115 шт. Продолжительность сме ны — 8 ч. Регламентированные перерывы составляют 20 мин за смену. Технологический процесс обработки детали приведен в табл. 2.2.4.
Таблица 2.2.4. Технологический процесс обработки детали
Номер |
Содержание операций |
Тип оборудования |
Н орма времени |
|
операции |
tL, мин |
|||
|
|
|||
1 |
Подрезка торцов, раста |
Токарно-револьверный |
3,9 |
|
чивание отверстий |
1П365 |
|
||
|
|
|||
2 |
Черновое обтачивание |
Токарно-винторезный 1К62 |
3,7 |
|
3 |
Чистовая обработка всех |
Токарный полуавтомат 1731 |
3,8 |
|
|
поверхностей |
|
|
|
4 |
Фрезерование зуба |
Зубофрезерный 5310 |
16,5 |
|
5 |
Зачистка заусенцев |
Верстак |
4,0 |
|
|
Сверление отверстий, |
Вертикально-сверлильный |
4,2 |
|
6 |
равнорасположенных по |
|
||
2А135 |
|
|||
|
окружности |
|
|
|
7 |
Контроль |
Контрольный стол |
3,5 |
Расстояние между станками вдоль линии их расположения прини мается:
—для мелких станков (до 1500x750) — 400 мм;
—для средних станков (от 1500x750 до 3500x2000) — 600 мм;
—для крупных станков (от 3500x2000 до 5000x3000) — 800 мм;
—для особо крупных станков (от 5000x3000 до 10000x5000) — 1200 мм. При установке станка к другому задней (тыловой) стороной рассто
яние должно быть от 400 до 1000 мм.
При установке станков вдоль стены расстояние от станка до колон

ны, находящейся у стены, или до выступающей части стены принимает ся в соответствии со следующими условиями:
а) при расположении рабочего вне промежутка между стеной и стан ком расстояние между тыльной стороной станка и стеной составляет от 400 до 800 мм;
б) расстояние от боковой стороны станкадо колонны у стены состав ляет от 400 до 800 мм.
При расположении рабочего между станками или между станком и стеной расстояние должно быть от 900 до 1500 мм в зависимости от габаритов оборудования.
Решение.
1. Определим такт поточной линии г при заданном объеме выпуска деталей, учитывая регламентированные перерывы:
Т.Ч2_Т„. 480-20 = 4 мин.
N.115
2.Рассчитаем необходимое число рабочих мест и их загрузку по опе рациям технологического процесса:
С , А |
к . , = ^ 1 0 0 [%]. |
гЧ
Фактическое количество рабочих мест на операции получаем округ лением Cpi до целого числа (табл. 2.2.5).
Таблица 2 .2 .5
Номер |
t,, мин |
|
С, |
к . ,% |
операции |
с и |
|||
1 |
3,9 |
0 ,9 8 |
1 |
98 |
2 |
3,7 |
0,9 3 |
1 |
93 |
3 |
3,8 |
0 ,9 5 |
1 |
95 |
4 |
16,5 |
4 ,1 3 |
4 |
103 |
5 |
4 ,0 |
1,00 |
1 |
100 |
6 |
4 ,2 |
1,05 |
1 |
105 |
7 |
3,5 |
0 ,8 8 |
1 |
88 |
Количество рабочих на линии — 10 чел.
3. Выберем тип поточной линии, наиболее соответствующий усло виям производства, и вид транспортных средств.
Перегрузка рабочих мест — в пределах 5% и может быть ликвидиро
вана при отладке линии. Выбираем непрерывно-поточную линию с рас пределительным конвейером, посколькутехнологические операции дол жны выполняться на рабочих местах на металлорежущем оборудовании.
4. Выберем величину шага конвейера:
1„ min = Сов + 1ПР) / Ю00 = (100 + 300) / 1000 = 0,4 м.
Если выберем 10 = 0,4 м, скорость движения конвейера будет очень низкой:
V= —=-^^ = 0,1 м/мин.
*г 4,0
Это приведет к увеличению длительности цикла обработки детали на линии. Поэтому выберем 10 = 2 м.
Окончательно скорректируем шаг конвейера после выполнения пла нировки поточной линии.
5.Определим минимально необходимое число разметочных зна ков — период конвейера Пк. Период конвейера определяется как наи меньшее общее кратное числа рабочих мест по всем операциям процес са. Период конвейера Пк = 4.
6.Выполним планировку поточной линии. Планировка представле на на рис. 2.2.3. Производственная площадь (из чертежа) S = 24,6x11,0 =
=270,6 м2.
Рис. 2.2.3. Планировка непрерывно-поточной линии с распределительным конвейером
7. Рассчитаем длину рабочей части распределительного конвейера. По планировке оборудования длина рабочего участка линии при
двухрядном расположении станков
V* = 20 м.
8. Скорректируем шаг распределительного конвейера.
Для этого выберем вид транспортного средства: ленточный транс портер с приводными и натяжными станциями.
Длина ленты транспортера конвейера
1л.к = 21р1( + |
7СО [ м ] , |
где D — диаметр натяжного устройства. Пусть D = 1,0 м, тогда |
|
1ПК = 2 20 + 3,14 |
1,0 = 43,14 м. |
Число повторений периода конвейера кпов на ленте транспортера получаем округлением до ближайшего целого числа кпов р:
кпов.Р = 1п.к/10 П = 43,14/2-4=5,39; *1,0. = 5.
Окончательно
10 = 1р.к / Пк кпов = 43,14/4 • 5 = 2,16 м.
9. Скорость движения транспортера
1 2 16
V, = — = —— = 0,54 м / мин лежит в пределах допустимых значений,
г4,0
10.Определим длительность цикла обработки детали:
|
m |
J |
9 0 |
|
|
|
Тц = г Т с |
+ — = 4,0-10+— —= 77,0 мин . |
|
|
|
|
ы |
V, |
0,54 |
|
|
Разметка конвейера и закрепление знаков за рабочими местами по |
|||||
операциям технологического процесса (табл. 2.2.6). |
|
|
|||
|
|
|
Таблица 2 .2 .6 |
|
|
Номер |
Номер |
Число разметочных |
Закрепленные |
||
Количество |
|
Величина |
|||
операции |
рабочего |
зн аков,закреплен |
знаки |
||
рабочих мест |
|
периода |
|||
|
места |
ных за рабочим |
|
|
|
1 |
1 |
1 |
4 |
1; 2; |
3; 4 |
2 |
1 |
1 |
4 |
1; 2; |
3; 4 |
3 |
1 |
1 |
4 |
1; 2; 3; 4 |
|
4 |
4 |
1 |
1 |
1 |
|
|
2 |
1 |
2 |
|
|
|
3 |
П = 4 |
3 |
|
|
|
1 |
|
|||
|
4 |
1 |
4 |
|
|
5 |
1 |
1 |
4 |
1; 2; |
3; 4 |
6 |
1 |
1 |
4 |
1; 2; |
3; 4 |
7 |
1 |
1 |
4 |
1 ; 2 ; 3 ; 4 |
11. Определим сменную выработку на одного рабочего и 1 м2 произ водственной площади.
Сменная выработка на одного рабочего
N 115
Чра6 = х?= 'Т о " 5 ш т ' в с м е н у '
Сменная выработка на 1 м2 производственной площади
N, |
115 |
q кв.м s..P |
= 0,425 пгг./м2. |
270,6 |
Пример 3. На прямоточной линии обрабатывается картер редукто ра. О п р е д е л и т ь такт линии; рассчитать число рабочих мест и число рабочих на линии; составить график-регламент работы оборудования и рабочих; рассчитать межоперационные заделы и построить их график. Исходные данные. Участок работает в две смены, суточная программа запуска 184 шт. Технологический процесс обработки картера приведен в табл. 2.2.7:
Таблица 2.2.7. Технологический процесс обработки картера
Номер |
О перация |
О борудование |
Разряд |
Н орма времени |
|
операции |
|
|
работы |
t(, мин |
|
1 |
Сверлить отверстие в плос |
Радиально-сверлиль |
2 |
2,9 |
|
кости под опорный ролик |
ный станок 2М55 |
||||
2 |
Фрезеровать торец с |
Горизонтально-фре- |
2 |
2,3 |
|
внутренней стороны |
зерный станок 6Р82Г |
||||
|
|
|
|||
|
Сверлить отверстие до |
Вертикально-свер |
|
|
|
3 |
пересечения с литым |
лильный станок |
2 |
2,7 |
|
|
каналом |
2Н135 |
|
|
|
4 |
Нарезать резьбу |
Токарно-винторез |
3 |
1,7 |
|
ный станок 1М63 |
|||||
|
|
|
|
||
5 |
Сверлить отверстие на |
Радиально-сверлиль |
2 |
2,3 |
|
проход |
ный станок 2Н-55 |
||||
|
|
|
|||
6 |
Фрезеровать торец |
Горизонтально-фре- |
2 |
1,2 |
|
зерный станок 6Р82Г |
|||||
|
|
|
|
||
7 |
Нарезать резьбу |
Токарно-винторез- |
3 |
5,1 |
|
ный станок 1М63 |
|||||
|
|
|
|
||
8 |
Цековать отверстия |
Радиально-сверлиль |
2 |
2,5 |
|
ный станок 2Н-55 |
|||||
|
|
|
|
Период комплектования R* принять равным 240 мин.
Решение.
г = ъ * ± |
480-2 = 5,2 мин. |
N 3 |
184 |
В табл. 2.2.8. приведены:
—расчетное число рабочих мест (единиц оборудования) на опера ции, полученное по формуле
С. =Ь. ■
р.г .
—принятое число рабочих мест (Cj), полученное округлением рас четного числа рабочих мест;
—загрузка рабочих мест
k3i= -^ .100 [%];
—число рабочих на линии, полученное за счет совмещения рабочи ми нескольких операций для полного использования фонда вре мени;
—периоды работы оборудования и рабочих на операциях в долях
периода комплектования.
Всего на линии занято 4 рабочих в смену.
Таблица 2.2.8. Количество рабочих мест, их загрузка и число рабочих на линии
|
Норма |
Число |
|
Загрузка |
Число |
Порядок |
Периоды работы |
|
Номер |
рабочих мест |
|||||||
оборудования |
||||||||
операции |
времени, |
|
|
рабочих |
рабочих |
совмещения |
и рабочих на |
|
мин |
|
С, |
мест, % |
в смену |
операций |
|||
|
с и |
операции |
||||||
|
|
|
|
|
||||
1 |
2,9 |
0,56 |
1 |
56 |
1 |
1-й рабочий |
0,56 R |
|
2 |
2,3 |
0,44 |
1 |
44 |
- |
1-й рабочий |
0,44 R |
|
3 |
2,7 |
0,52 |
1 |
52 |
1 |
2-й рабочий |
0,52 RK |
|
4 |
1,7 |
0,33 |
1 |
33 |
1 |
3-й рабочий |
0,33 R |
|
5 |
2,3 |
0,44 |
1 |
44 |
- |
3-й рабочий |
0,44 RK |
|
6 |
1,2 |
0,23 |
1 |
23 |
- |
3-й рабочий |
0,23 R, |
|
7 |
5,1 |
0,98 |
1 |
98 |
1 |
4-й рабочий |
1,00 RK |
|
8 |
2,5 |
0,48 |
1 |
48 |
- |
2-й рабочий |
0,48 RK |
План-график работы линии представлен на рис. 2.2.4.
Размер межоперационных оборотных заделов определяется по фор муле
J ___ 1_
,5,1 2,5,
На основе произведенных расчетов строится график (эпюра) меж операционных оборотных заделов (рис. 2.2.5), выполняется планиров ка прямоточной линии (рис. 2.2.6). Оборудование размещается с уче том прямоточности движения деталей и возможности сближения рабочих мест, обслуживаемых одним рабочим.
Пример 4. На многопредметной поточной линии изготавливаются валики диаметром 25 мм (изделие А), 32 мм (Б) и 35 мм (В). Месячная программа выпуска составляет соответственно 8,5 и 3 тыс. шт.
О п р е д е л и т ь рабочие такты поточной линии, число рабочих мест по каждой операции и их загрузку. Линия работает 23 дня в месяц в две смены по 8 ч, коэффициент 1^ = 0,085. Технологический процесс обра ботки валиков дан в табл 2.2.9.
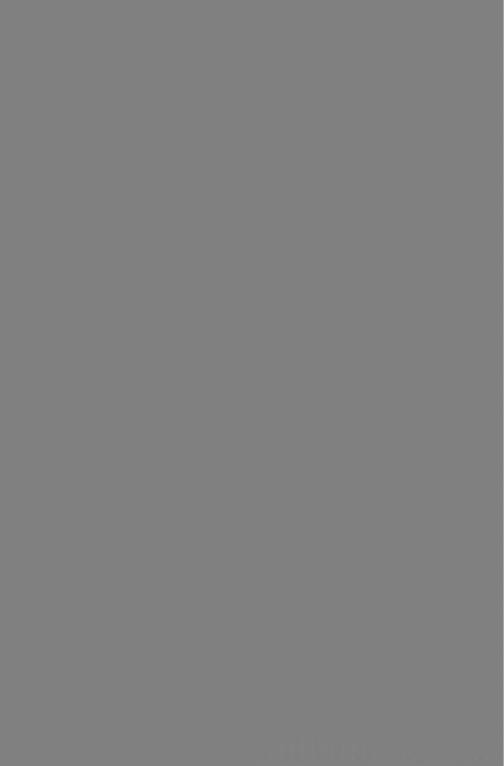
№ Условные обозначения 1 Место для складирования
2Тележка с поддонами
3Совмещение выполнения операций
S = 178,75 м2
Рис. 2.2.6. Планировка прямоточной линии
Таблица 2.2.9.Технологический процесс обработки валиков
Н аименование операций |
|
Трудоем кость операций tJ(, мин |
|
|
Б |
в |
|
|
А |
||
Подрезка торцов и зацентровка |
1,2 |
1,2 |
1,2 |
Токарная обработка |
5,7 |
8,4 |
7,2 |
Фрезерная обработка |
3,2 |
3,4 |
3,7 |
Шлифовальная обработка |
1,9 |
3,1 |
1.3 |
Итого: |
12,0 |
16,1 |
13,4 |
Решение.
1. Расчет рабочих тактов работы линии.
При расчете рабочих тактов за базовый представитель принят валик Б. Коэффициенты приведения трудоемкости детали к трудоемкости
базового представителя:
k |
Та, _ H JO _ 0 745 к |
I s =l k |
Ь - = 1 М = 0,832. |
А |
ТБ 16,1 |
ТБ |
в ТБ 16,1 |