
- •ВВЕДЕНИЕ
- •Г Л А В А 1. КЛАССИФИКАЦИЯ, НОМЕНКЛАТУРА, ПРИНЦИПЫ СОЗДАНИЯ ТЕПЛОЗАЩИТНЫХ СТРУКТУР И СВОЙСТВА СЫРЬЕВЫХ МАТЕРИАЛОВ
- •1.1. Классификация строительных материалов из ячеистых бетонов
- •1.2. Номенклатура строительных материалов из ячеистых бетонов
- •1.3. Принципы создания эффективных теплозащитных структур
- •1.3.1. Основные понятия о теплопередаче
- •1.3.2. Технологические способы создания современных теплозащитных структур
- •1.3.3. Конструктивные способы создания современных теплозащитных структур
- •1.4. Сырьевые материалы и их свойства
- •1.4.2. Кремнеземистые компоненты
- •1.4.3. Газообразователи
- •1.4.4. Пенообразователи
- •1.4.5. Корректирующие добавки и вода затворения
- •1.4.6. Сырьевая база Омской области для производства ячеистых бетонов
- •1.5. Способы активации сырьевых материалов и смесей при получении эффективных ячеистых бетонов
- •Г Л А В А 2. ТЕХНОЛОГИИ ЭФФЕКТИВНЫХ СТРОИТЕЛЬНЫХ МАТЕРИАЛОВ И ИЗДЕЛИЙ ИЗ ПЕНОБЕТОНОВ
- •2.1. Теоретические основы поризации кремнеземвяжущей массы механическим способом
- •2.2. Технология строительных материалов и изделий из неавтоклавного пенобетона
- •2.2.1. Производство пенобетонных блоков «Сиблок»
- •2.2.2. Технология пенобетона «ВНИИстром»
- •2.2.4. Производство пенобетона на технологическом комплексе ПБК–Р
- •2.3. Технология получения автоклавного пенобетона
- •2.4. Производство пенобетона по технологии «Новостром»
- •2.5. Современные технологии производства строительных материалов и изделий из пенобетона
- •2.5.1. Производство двухслойных стеновых блоков из бетонов различной плотности
- •2.5.5. Производство пенобетона «Экстрапор»
- •2.5.6. Вакуум-формовальная технология ячеистых бетонов
- •2.5.7. Технология пенобетона способом «обжатие – релаксация»
- •2.5.9. Пенобетоны сухой минерализации
- •Г Л А В А 3. ТЕХНОЛОГИИ ЭФФЕКТИВНЫХ СТРОИТЕЛЬНЫХ МАТЕРИАЛОВ И ИЗДЕЛИЙ ИЗ ГАЗОБЕТОНА
- •3.1. Теоретические основы поризации массы химическим способом порообразования
- •3.2. Технологии газобетона неавтоклавного твердения
- •3.3. Технологии материалов и изделий из газобетона автоклавного твердения
- •3.3.1. Производство газобетонных изделий на новосибирском заводе «Сибит»
- •3.3.3. Технология газобетона на омском комбинате пористых материалов «Вармит»
- •3.5.1. Материалы и изделия переменной плотности
- •3.5.2. Производство газобетонных изделий способом автофреттажа
- •3.5.3. Способ получения эффективных изделий в закрытой форме
- •3.5.4. Производство сухих газобетонных смесей
- •4.1. Проектирование состава ячеистых бетонов
- •4.1.2. Расчет состава пеногазобетона
- •4.2. Расчет и подбор технологического оборудования
- •4.2.1. Расчет технологического оборудования
- •4.2.2. Технологическое оборудование
- •4.3.1. Способы снижения водопоглощения
- •4.3.2. Отделка поверхности изделий из ячеистого бетона
- •4.4. Реконструкция предприятий силикатных изделий
- •Библиографический список
равной 350 кг/м3, который вполне можно использовать в производстве ячеистого бетона. Для керамзита фракции 4 – 8 мм по сравнению с традиционно применяемой фракцией 5 – 10 мм характерна более окатанная, близкая к сферической форма с коэффициентом формы зерна 1,15 – 1,25 и соответственно со сниженной вариативностью суммарной площади поверхности зерен заполнителя до 10% [22].
СибАДИалюминиевой пудры дисперсного ферросилиция, и нанокристаллический поризатор.
ОАО «ВНИИстромом им. П.П. Будникова» разработана технология изготовления пенополистиролбетона плотностью 250 – 400 кг/м3 на основе вспененных пол ст рольных гранул и легких гранул из ячеистого
бетона, названного пенопоритом [23]. |
|
|
|
1.4.3. Газообразователи |
|
В технолог |
газо етонных изделий в качестве |
газообразователей |
главным образом |
спользуется алюминиевая пудра |
марок ПАП–1 и |
ПАП–2, отвечающая тре ованиям ГОСТ 5494–95 «Пудра алюминиевая пигментная. ТУ» с содержанием активного алюминия 91,1 – 93,9% и временем акт вного (максимума) газовыделения в течение 3 – 4 мин от
начала смеш ван я компонентов газобетонной массы. К пудре
предъявляются тре ования по дисперсности, т.к. с дисперсностью связан процесс протекания газоо разования в ячеистобетонной смеси, которая составляет 4600 – 6000 см2/г. Максимальное выделение водорода
происходит при температуре смеси 30 – 40 °С. ля получения водной
алюминиевой суспензии используется сульфанол (алкилбензосульфат), обладающий свойствами ПАВ, из расчета 25 г на 1 л воды. Сульфанол должен удовлетворять требованиям ТУ 6–01–1001.
Использование алюминиевой пудры имеет ряд недостатков:
гидрофобность, высокая степень пыления, взрывоопасность, неудовлетворительные санитарно-гигиенические условия труда.
В качестве газообразователя также применяют пергидроль Н2О2 газопасты ГБП, «Газобетолайт», «Газобетолюкс» и «Газобетопласт»,
комплексный газообразователь, представляющий собой смесь
При применении газопасты ГБП отпадает необходимость в поверхностно-активных веществах (ПАВ), она легко смачивается и перемешивается с водой, образуя хорошую суспензию, которая равномерно распределяется в бетонной массе без агрегатирования. При одинаковой общей пористости изделий средний размер пор в теле газобетона в 2 – 2,5 раза меньше, чем в изделиях на алюминиевой пудре. Отрицательным эффектом применения газопасты по сравнению с
21
алюминиевой пудрой является удлинение сроков достижения пластической прочности на 15 – 30 мин [24].
Газообразователи «Газобетолайт», «Газобетолюкс» и «Газобетопласт» – гидрофильные пасты на основе алюминиевой пудры, полученные синтезированием многокомпонентных органических добавок (МОД), применяются в основном для приготовления газобетонов
СибАДИУ комплексного газообразователя каждый компонент смеси является газообразователем, но имеет собственную скорость образования массы газа абсолютную массу полученного газа. Реакция взаимодействия ионов силиция со щелочными компонентами смеси протекает медленнее, чем ионов алюминия, а суммарная скорость образования массы водорода у комплексного газообразователя ниже, чем скорость образования той же массы газа у алюминиевой пудры. Ферросилиций в составе вспучивающегося вещества назван газообразователем второго действия. Соотношение алюминиевой пудры ПАП–1 и дисперсного ферросилиция ФС–75 находится в пределах от 1:4 до 1:1. Общий расход комплексного газообразователя 0,25 – 0,86 кг на 1 м3 ячеистого бетона плотностью
автоклавного твердения. Выбор вида газобразователя зависит от способа его дозировки [24, 25].
Пре мущества пр менения газопаст заключаются в следующем:
отсутств |
е пылен |
я в процессе подачи газообразователя в суспензатор и |
при перемеш ван |
суспензии; исключена дополнительная операция |
|
обработки ПАВ; ускоряется гомогенизация алюминиевой суспензии; |
||
понижается осадка масс вов; повышается пластичность свежеотформован- |
||
ных масс вов; повышается устойчивость массива при транспортировке. |
||
К недостаткам можно отнести следующее: паста «Газобетопласт» не |
||
привод т |
к полному устранению раковин в массиве, а паста |
|
«Газобетолайт» меет резкий запах при приготовлении суспензии. |
Кол чество выдел вшегося водорода с течением времени от вида газопасты представлена в та л. 1.2, а кинетика газовыделения некоторых
газообразователей – на рис. 1.5 [24].
|
|
|
Таблица 1.2 |
||
Количество выделившегося водорода (см3) с течением времени |
|
||||
|
|
|
|
|
|
Вид гидрофильной газопасты |
|
Время, мин |
|
||
2 |
|
8 |
|
16 |
|
|
|
|
|||
газобетопласт (активность 78,6%) |
0 |
|
18 |
|
46 |
газобетопласт (активность 81,8%) |
2 |
|
36 |
|
58 |
газобетолайт (1% активной добавки, активность 91%) |
12 |
|
48 |
|
62 |
газобетолайт (5% активной добавки, активность 89,1%) |
17,4 |
|
62,4 |
|
69,7 |
газобетолюкс (8% активной добавки, активность 87,9%) |
21,8 |
|
60,9 |
|
66,1 |
500 – 800 кг/м3 [26].
22
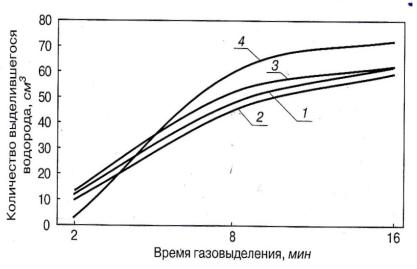
|
|
|
|
|
|
СибАДИСтепень пыления, мас. % 3,5 1,3 1 1 0,3 0,5 |
|||||
Р с. 1.5. К нетика газовыделения алюминиевых пудр |
|||||
и алюминиевых паст: |
|
|
|
||
1 – газо етолайт (1% активной добавки, активность |
|||||
91%); 2 – алюминиевая пудра ПАП–1; 3 – алюминиевая |
|||||
пудра ПАП–2; 4 – алюминиевая паста CR0006 (Индия) |
|||||
Нанокр сталл ческий |
поризатор |
(НП) |
представляет собой |
||
активированный алюм ний |
в о олочке П |
В. НП |
позволяет получать |
ячеистый бетон со средней плотностью до 300 кг/м3, общей пористостью 84%, прочностью при сжатии 0,65 МПа, при изгибе – 0,35 МПа [27].
Сравнительные |
характеристики |
некоторых |
газообразователей |
||||||
приведены в та л. 1.3, а основные свойства газобетонов |
смесей, |
||||||||
приготовленных на их основе, в табл. 1.4 [24, 25, 28]. |
|
Таблица 1.3 |
|||||||
|
|
|
|
|
|
|
|
||
Сравнительные характеристики газообразователей |
|
||||||||
|
|
|
|
|
|
|
|
|
|
Тип газообразователя |
|
П П–1 |
газобе- |
|
газобе- |
ГПБ–2 |
Schlenk |
Schlenk |
|
|
толайт |
|
толюкс |
4507W |
7504 |
||||
Активность алюминия, мас. % |
98,6 |
90,5 |
|
85 |
|
81,1 |
65,8 |
71,4 |
|
Остаток на сите № 008, мас. % |
1 |
1,5 |
|
1,5 |
|
1,7 |
2 |
1,6 |
|
Диапазон частиц, мкм |
|
10 – 60 |
9 – 40 |
|
9 – 45 |
30 – 65 |
20 – 55 |
10 – 30 |
|
Преобладающий (90%) раз- |
49,1 |
32,5 |
|
31,9 |
|
60,2 |
48,2 |
25,6 |
|
мер частиц, мкм, менее |
|
|
|
||||||
|
|
|
|
|
|
|
|
|
|
Средний размер частиц, мкм |
28,9 |
20 |
|
18,5 |
|
38,4 |
27,9 |
14,7 |
|
Удельная поверхность, м2/кг |
323,7 |
507,4 |
|
541,5 |
255,1 |
333,6 |
722,1 |
||
|
|
|
|
|
|
|
|
|
|
Продолжительность гомоге- |
3,05 |
1 |
|
1,05 |
|
1 |
0,96 |
0,8 |
|
низации, мин |
|
|
|
||||||
|
|
|
|
|
|
|
|
|
|
Время осаждения твердых |
|
88 |
24 |
|
22 |
|
64 |
57 |
53 |
частиц, мин |
|
|
|
||||||
|
|
|
|
|
|
|
|
|
|
Внешний вид суспензии после |
Бесцветная |
|
Темно-серая |
Светло-серая |
|||||
осаждения |
|
|
|||||||
|
|
|
|
|
|
|
|
|
|
Удельный расход, кг/м3 |
|
0,55 |
0,52 |
|
0,47 |
|
0,62 |
0,62 |
0,59 |
23
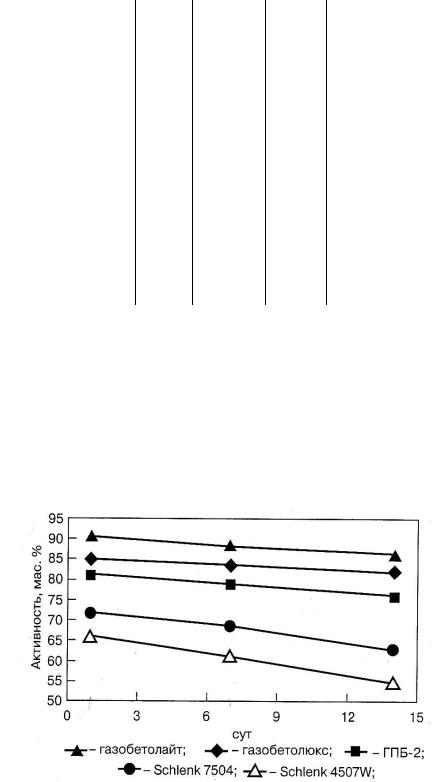
Таблица 1.4
Основные свойства газобетонов и смесей на основе некоторых газообразователей
|
Показатель |
ПАП–1 |
газобе- |
газобе- |
ГПБ–2 |
Schlenk |
Schlenk |
|
|
толайт |
толюкс |
4507W |
7504 |
|
|||
|
Время приготовления сус- |
40 |
20 |
20 |
--- |
--- |
--- |
|
|
|
|
||||||
|
СибАДИ |
|
|
|
||||
|
пензии, мин |
|
|
|
|
|
|
|
|
Начальная температура сме- |
44 – 45 |
44 – 45 |
44 – 45 |
44 – 45 |
44 – 45 |
44 – 45 |
|
|
си, о |
|
||||||
|
Расплыв смеси по Суттарду, |
12,5 |
12,5 |
12,5 |
12,5 |
12,5 |
12,5 |
|
|
см |
|
|
|
|
|
|
|
|
Время вспуч ван я Нmax, м н |
12 |
9 |
8 |
н.д. |
н.д. |
н.д. |
|
|
Плотность, кг/м3 |
477 |
560 |
500 |
530 |
530 |
510 |
|
|
Прочность при сжат , МПа |
3,57 |
5,84 |
4,31 |
4,68 |
5,51 |
5,39 |
|
|
Размер пор, мм |
0,04–3 |
0,016–1,1 |
0,014–1 |
0,02–1,5 |
н.д. |
н.д. |
|
|
Количество пор на 1 см2 |
72 |
89 |
92 |
80 |
н.д. |
н.д. |
|
|
Просадка в пер од на ора |
0,5 – 1 |
0,25 – 0,5 |
0 |
0 |
0 |
0 |
|
|
пластической прочности, мм |
|
||||||
|
Влажность по массе, % |
26,5 |
35,5 |
32 |
35 |
32,1 |
40,3 |
|
таб льность некоторых газопаст во времени приведена на рис. 1.6. С увеличением времени выдержки происходит снижение активности газопаст за счет протекающего процесса окисления. Наиболее активно этот процесс наблюдается у суспензии на пудре ПАП–1. Через сутки алюминиевая суспензия на П П–1 вследствие интенсивного окисления вскипает, а с точки зрения технологии производства она должна сохранять свои свойства 1 – 2 сут. Большей стабильностью отличается суспензия на пасте «Газобетолюкс» [28].
Рис. 1.6. Стабильность газообразователей во времени
24