
- •ВВЕДЕНИЕ
- •Г Л А В А 1. КЛАССИФИКАЦИЯ, НОМЕНКЛАТУРА, ПРИНЦИПЫ СОЗДАНИЯ ТЕПЛОЗАЩИТНЫХ СТРУКТУР И СВОЙСТВА СЫРЬЕВЫХ МАТЕРИАЛОВ
- •1.1. Классификация строительных материалов из ячеистых бетонов
- •1.2. Номенклатура строительных материалов из ячеистых бетонов
- •1.3. Принципы создания эффективных теплозащитных структур
- •1.3.1. Основные понятия о теплопередаче
- •1.3.2. Технологические способы создания современных теплозащитных структур
- •1.3.3. Конструктивные способы создания современных теплозащитных структур
- •1.4. Сырьевые материалы и их свойства
- •1.4.2. Кремнеземистые компоненты
- •1.4.3. Газообразователи
- •1.4.4. Пенообразователи
- •1.4.5. Корректирующие добавки и вода затворения
- •1.4.6. Сырьевая база Омской области для производства ячеистых бетонов
- •1.5. Способы активации сырьевых материалов и смесей при получении эффективных ячеистых бетонов
- •Г Л А В А 2. ТЕХНОЛОГИИ ЭФФЕКТИВНЫХ СТРОИТЕЛЬНЫХ МАТЕРИАЛОВ И ИЗДЕЛИЙ ИЗ ПЕНОБЕТОНОВ
- •2.1. Теоретические основы поризации кремнеземвяжущей массы механическим способом
- •2.2. Технология строительных материалов и изделий из неавтоклавного пенобетона
- •2.2.1. Производство пенобетонных блоков «Сиблок»
- •2.2.2. Технология пенобетона «ВНИИстром»
- •2.2.4. Производство пенобетона на технологическом комплексе ПБК–Р
- •2.3. Технология получения автоклавного пенобетона
- •2.4. Производство пенобетона по технологии «Новостром»
- •2.5. Современные технологии производства строительных материалов и изделий из пенобетона
- •2.5.1. Производство двухслойных стеновых блоков из бетонов различной плотности
- •2.5.5. Производство пенобетона «Экстрапор»
- •2.5.6. Вакуум-формовальная технология ячеистых бетонов
- •2.5.7. Технология пенобетона способом «обжатие – релаксация»
- •2.5.9. Пенобетоны сухой минерализации
- •Г Л А В А 3. ТЕХНОЛОГИИ ЭФФЕКТИВНЫХ СТРОИТЕЛЬНЫХ МАТЕРИАЛОВ И ИЗДЕЛИЙ ИЗ ГАЗОБЕТОНА
- •3.1. Теоретические основы поризации массы химическим способом порообразования
- •3.2. Технологии газобетона неавтоклавного твердения
- •3.3. Технологии материалов и изделий из газобетона автоклавного твердения
- •3.3.1. Производство газобетонных изделий на новосибирском заводе «Сибит»
- •3.3.3. Технология газобетона на омском комбинате пористых материалов «Вармит»
- •3.5.1. Материалы и изделия переменной плотности
- •3.5.2. Производство газобетонных изделий способом автофреттажа
- •3.5.3. Способ получения эффективных изделий в закрытой форме
- •3.5.4. Производство сухих газобетонных смесей
- •4.1. Проектирование состава ячеистых бетонов
- •4.1.2. Расчет состава пеногазобетона
- •4.2. Расчет и подбор технологического оборудования
- •4.2.1. Расчет технологического оборудования
- •4.2.2. Технологическое оборудование
- •4.3.1. Способы снижения водопоглощения
- •4.3.2. Отделка поверхности изделий из ячеистого бетона
- •4.4. Реконструкция предприятий силикатных изделий
- •Библиографический список
та закрывают, и форма передвигается конвейером возврата к началу технологической линии, где передаточной тележкой подается под заливку. Массив на поддоне проходит через резательную машину, где производится калибровка массива, горизонтальная и поперечная разрезка на изделия. Разрезка осуществляется короткими струнами, длина которых на
150 – 200 мм больше ширины массива, что обеспечивает высокую точность резки. Продольная разрезка производится при перемещении массива на поддоне через горизонтально расположенные неподвижные струны, поперечная – при вертикальном перемещении массива через
СибАДИВНИИСтромом рядом других организаций и предприятий был предложен и внедрен вибрационный способ смешения компонентов и формования изделий из ячеистобетонной смеси, т.е. вибрационная технология, преимуществами которой являются:
струны, совершающ е возвратно-поступательное движение. После
разрезки масс в на поддоне передается на тепловлажностную обработку.
Требован ям к теплоэффективным материалам ХХI в. соответствует ячеистый бетон автоклавного и неавтоклавного твердения. Ячеистый бетон
может быть |
спользован как материал для стеновых ограждающих |
|
конструкц й |
как эффективный теплоизоляционный материал, |
|
подаваемый на место |
спользования в виде раствора по трубопроводу. |
|
Согласно концепц |
Минстроя РФ проблему повышения термическо- |
го сопрот влен я ограждающих конструкций следует решать следующими средствами: повышен ем теплозащитных свойств зданий и организацией выпуска прогрессивных теплоэффективных строительных изделий и материалов; использованием энергоэкономичных систем инженерного обеспечения и учета энергозатрат; выра откой принципиально новой, прогресссивной технологии строительства, ремонта и санации зданий [3].
3.3. Технологии материалов и изделий из газобетона автоклавного твердения
В России были предложены, разработаны и внедрены бескрановая
конвейерная виброрезательная поддонная технология и оборудование для производства стеновых блоков из ячеистого бетона. Технология впоследствии получила наименование «Виброблок» [69].
1.Возможность смешивания сырьевых компонентов и формование массивов с В/Т = 0,35 – 0,45 против обычно применяемого В/Т = = 0,5 – 0,6.
2. Ускоренное и регулируемое вспучивание массива в течение 3 – 8 мин по сравнению с обычно продолжающимся вспучиванием в течение 20 – 60 мин.
81
3.Приобретение массивом необходимой для распалубки сырцовой прочности 200 – 400 г/см2 в течение 20 – 50 мин по сравнению с приобретением массивом такой же прочности при литьевой технологии в течение 90 – 240 мин.
4.Возможность перевода производства изделий из ячеистого бетона на конвейерный способ вместо обычно применяемого агрегатно-
СибАДИподдона на стол резательной машины после разрезки на специальной решетке отправляется в автоклав. В варианте «Виброблок БГ–40» отформованный массив на виброплощадке с горизонтальными колебаниями на всем протяжении технологического процесса находится на «своем» поддоне, что обеспечивает стабильный технологический процесс даже при наличии нестабильных и невысоких характеристик исходных сырьевых материалов и некоторых отклонений от установленных технологических параметров [69].
поточного способа.
5. Получение при сравнимых условиях ячеистого бетона с повышенными на 15 – 30% физико-механическими показателями по сравнен ю с изделиями, производимыми по литьевой
технолог .
6. Возможность производства изделий, отвечающих нормативным
требован ям, з сырьевых материалов, не полностью отвечающих нормат вным тре ованиям.
При поддонном спосо е производства отформованный массив от начала процесса до его выхода из автоклава и подачи на склад готовой
продукц |
наход тся на первоначальном собственном поддоне. |
|
Ведущ е зару ежные фирмы, такие как «Сипорекс» |
и «Дюрокс» |
|
(Швец я), |
«Итонг», «Хе ель», «Верхан» (Германия), |
«Кальсилокс» |
(Дания), «Селкон» (Голландия), «Чори» (Япония), «Униполь» (Польша), отказались от изготовления изделий в индивидуальных формах и перешли на резательную технологию и соответствующее оборудование, позволяющее изготовлять разноо разные виды изделий по гибкой технологии и с меньшими затратами металла на формы.
В России создано два конкурирующих вида технологических процессов и оборудования по резательной технологии – «Универсал–60» и
«Виброблок БГ–40».
В первом случае после приготовления смеси в виброили гидродинамическом смесителе, формирования массива на ударной площадке, приобретения массивом сырцовой прочности он освобождается от бортоснастки, специальным захватом переносится из собственного
Технологической особенностью отделения помола является применение оправдавшего себя совместного сухого помола известково- цементно-песчаного вяжущего, а также мокрого помола песка. Для
82
приготовления формовочной смеси с пониженным водотвердым отношением использован вибросмеситель СМЦ–40Б.
Для создания оптимальных условий газовыделения и образования ячеистой структуры в течение 5 – 10 мин после заливки смеси в формы применяется вибрационная площадка с горизонтально направленными колебаниями типа К–494. Бескрановая конвейерная линия не требует
СибАДИавтоклавов.
строительства дорогостоящих зданий с колоннами и подкрановыми путями и установки крана.
Брянск м объед нением выпущено более 30 таких технологических
линий |
под |
ндексом |
БГ–40 и 3687–Б1–ТХ |
производительностью по |
||
стеновым |
блокам |
40 |
– 60 тыс. м3/год. |
Усовершенствованными |
||
модиф кац ями «В броблок БГ–40» являются «Виброблоки»: БГ–80, |
||||||
БГ–100, БГ–200. Пр менение ескрановой конвейерной линии «Виброблок |
||||||
БКЛ–100» обеспеч вает следующие дополнительные преимущества: |
||||||
1. |
Возможность производства стеновых блоков на одной |
|||||
|
конвейерной л н и в широком диапазоне возрастающей мощности |
|||||
|
от 50 до 200 тыс. м3 в год по автоклавной и безавтоклавной |
|||||
|
технолог ям. |
|
|
|
||
2. |
Повышенную степень механизации и автоматизации производства, |
|||||
|
благодаря упрощению и сокращению числа единиц технологичес- |
|||||
|
кого оборудования и применению замкнутого формовочного |
|||||
|
конвейера. |
|
|
|
|
|
3. |
Снижение массы, а следовательно, и стоимости оборудования цеха |
|||||
|
с бескрановой конвейерной линией БКЛ–100 в 2 – 2,5 раза по |
|||||
|
сравнению с оборудованием «Виброблок БГ–80 – 200» или другим |
|||||
|
оборудованием аналогичного назначения за счет исключения из |
|||||
|
состава технологической линии такого оборудования, как |
|||||
|
подъемные рольганги, автоклавные вагонетки, манипуляторы, |
|||||
|
мостовые краны, уменьшения количества и массы поддонов, |
|||||
|
рольгангов, толкателей и др. |
|
|
|||
4. |
Применение автоклавов диаметром 2 м, позволяющих обеспечить |
|||||
|
максимальную степень их заполнения при загрузке массивов в |
|||||
|
один ярус |
без |
применения мостовых |
кранов |
снизить массу |
5. Снижение стоимости производственного корпуса на 30 – 50% за счет уменьшения его площади и объема и возможности возведения из легких самонесущих конструкций, в том числе из быстровозводимых инвентарных пролетов.
Основные характеристики различных технологических линий для производства изделий из газобетона приведены в табл. 3.1. Средняя плотность изделий, получаемых на технологической линии БКЛ–100,
83
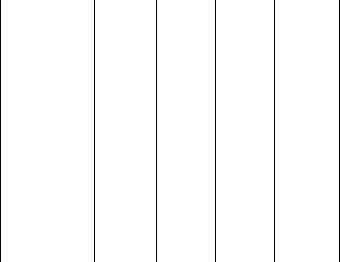
составляет 150 – 1200 кг/м3, прочность – 0,5 – 4,5 МПа, коэффициент теплопроводности – 0,06 – 0,25 Вт/(м К).
Таблица 3.1
Основные характеристики технологических линий для производства газобетона
|
Показатели |
Универсал- |
БГ-10 |
БГ-20 |
БГ-40 |
3687Б- |
БКЛ- |
|
«Силбетст- |
|
|
|
60 |
1-ТХ |
100 |
|
ройиндустрия» |
|
|||||
|
СибАДИ |
|
|
|
|||||||
|
Годовая |
|
|
|
|
|
|
|
|
|
|
|
мощность, |
80 |
10 |
20 |
40 |
60 |
100 |
|
40 |
60 |
|
|
тыс. м3 |
|
|
|
|
|
|
|
|
|
|
|
Размеры |
6000x1200 |
1546x |
3030x |
3030x |
3030x |
3030x |
|
н.д. |
н.д. |
|
|
формуемого |
x650 |
1160x |
1140x |
1140x |
1140x |
1300x |
|
|
||
|
массива, мм |
|
430 |
650 |
650 |
650 |
1460 |
|
|
|
|
|
Масса обо- |
376 |
70 |
82 |
150 |
200 |
220 |
|
550* |
665* |
|
|
рудован я, т |
|
|
|
|
|
|
|
|
|
|
|
Установ- |
|
|
|
|
|
|
|
|
|
|
|
ленная мощ- |
70 |
60 |
60 |
60 |
88 |
130 |
|
1200* |
1200* |
|
|
ность при- |
|
|
|
|
|
|
|
|
|
|
|
водов, кВт |
|
|
|
|
|
|
|
|
|
|
|
Пр мечан е. * – показатели с учетом массы мельниц и автоклавов. |
|
|
|
Фирма «Итонг» предусматривает минимальное содержание СаО в извести для получения газо етона, равное 92%, с кривой гашения, при которой 150 г извести, затворенной в 600 мл воды, обеспечивает равномерное повышение температуры с 35 до 74 С в течение 40 мин. Удельная поверхность портландцемента марок 400 – 500 должна находиться в пределах 3500 – 4000 см2/г. Отечественными нормативными документами производство извести и цемента с такими качественными показателями не предусмотрено [7].
На некоторых заводах России (Барнаул, Рязань, Люберцы) организовано серийное производство стеновых блоков из ячеистого бетона на оборудовании системы «Виброблок», при использовании которого отформованный массив изделий на складе находится на собственном поддоне, что обеспечивает устойчивость работы конвейерной линии. По такому же принципу создано оборудование для производства стеновых
блоков АО «Силбетстройиндустрия» |
бологовским заводом |
«Строммашина». |
|
3.3.1. Производство газобетонных изделий на новосибирском заводе «Сибит»
Новосибирский завод газобетонных изделий «Сибит», работающий по технологии фирмы «Итонг», выпускает стеновые мелкие и крупные блоки,
84
армированные конструкции и теплоизоляционные плиты из газобетона автоклавного твердения.
Приготовление известково-кремнеземистого вяжущего осуществляется путем сухого помола песка и извести в 2-камерной шаровой мельнице. Полученное вяжущее с помощью пневмонасосов подается в силос хранения смесительного отделения и далее в шламбассейн. Усреднение
СибАДИ |
|||
шлама в шламбассейне составляет не менее 8 ч. Плотность шлама |
|||
составляет 1,4 – 1,48 т/м3, а его текучесть – 26 – 32 см по расплыву |
|||
раствора при спытан |
с помощью прибора Суттарда. |
||
Пр готовленная масса с температурой 38 – 42 С заливается в формы |
|||
за од н |
пр ем. |
Особенностью технологии является применение |
|
стационарного газобетоносмесителя. |
|||
После зал вки формы подаются в зону действия опрокидывающей |
|||
машины, которая после созревания газобетонной массы переносит ее на |
|||
путь резательной маш ны, переворачивает на 90 , снимает опалубку |
|||
движен ем |
вверх |
по |
горизонтали, после чего массив, лежащий на |
поддоне, отправляется на резку. Освободившаяся опалубка очищается, |
|||
подается на пост смазки |
заливки. |
Резка неарм рованного массива на блоки производится по истечении 2,5 ч при прочности 0,32 – 0,36 МПа стальными проволоками в горизонтальном и вертикальном направлениях. Затем блоки на поддоне подаются в автоклав длиной 27 м и диаметром 2,75 м, где подвергаются термовлажностной о ра отке по режиму: подъем давления – 2 ч, изотермическая выдержка – 5,5 ч и снижение давления – 3 ч.
После автоклавной обработки разделение блоков производится послойно с помощью подвижного разделительного захвата готовые изделия с помощью тележки подаются на склад.
Расход материалов на 1 м3 изделий из газобетона в зависимости от класса бетона по прочности, кг: цемент М500 – 140 – 150; известь –
130 – 140; гипс – 25 – 30; алюминиевая пудра 0,35 – 0,45; вода – 350 – 430; песок – 380 – 480; сульфанол – 0,035 – 0,040. Пример производства газобетонных блоков на новосибирском заводе «Сибит» приведен в мультимедийном файле по адресу https://www.youtube.com/watch?v=qZS1mGEEAo.
3.3.2. Производство газобетона в вертикальной форме
На заводе ячеистых бетонов (г. Набережные Челны) изготовление стеновых блоков из ячеистого бетона осуществляется по следующей схеме: помол песка мокрым способом, подача шлама, цемента, извести в шламбассейны и расходные бункеры; дозирование цемента, извести и шлама осуществляется дозаторами на тензометрических датчиках с
85
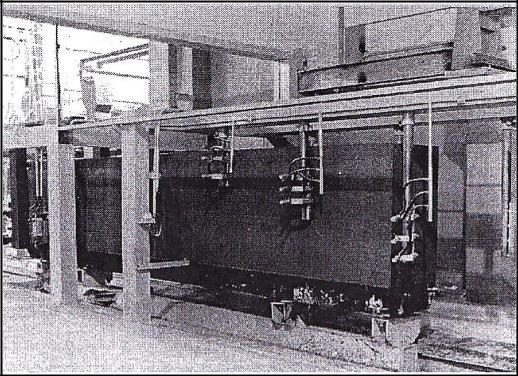
дистанционным управлением; отдозированные компоненты перемешиваются в передвижной газобетономешалке и выгружаются в вертикальную бортоснастку [70].
Вертикальная бортоснастка состоит из стационарных открывающихся бортов и сменного поддона и имеет размеры 6000х626х1300 мм. Бортоснастка снабжена механизмом фиксации и прижима бортов к
СибАДИкоторой входят: маш на для срезки горбуши; машина для боковой резки массивов; маш на для горизонтальной резки (рис. 3.3).
поддону, стыки поддон-борта имеют систему герметизации.
После набора необходимой пластической прочности открываются
борта |
поддон с верт кальным массивом при |
помощи специальной |
траверсы, подвешенной на кран, перемещается на |
линию резки, в состав |
Рис. 3.3. Резательный комплекс
Все резательные машины рассчитаны на быструю перенастройку под
выпуск блоков разных типоразмеров. При вертикальной резке массива на торцах блоков выполняются потайные карманы для удобства кладки. Для сбора и дальнейшего использования отходов резки и горбуши предусмотрен ленточный конвейер, который расположен под резательными машинами.
Разрезанные на блоки массивы с поддонами устанавливаются на автоклавную тележку и загружаются в автоклав (рис. 3.4). В одном
86