
- •ВВЕДЕНИЕ
- •Г Л А В А 1. КЛАССИФИКАЦИЯ, НОМЕНКЛАТУРА, ПРИНЦИПЫ СОЗДАНИЯ ТЕПЛОЗАЩИТНЫХ СТРУКТУР И СВОЙСТВА СЫРЬЕВЫХ МАТЕРИАЛОВ
- •1.1. Классификация строительных материалов из ячеистых бетонов
- •1.2. Номенклатура строительных материалов из ячеистых бетонов
- •1.3. Принципы создания эффективных теплозащитных структур
- •1.3.1. Основные понятия о теплопередаче
- •1.3.2. Технологические способы создания современных теплозащитных структур
- •1.3.3. Конструктивные способы создания современных теплозащитных структур
- •1.4. Сырьевые материалы и их свойства
- •1.4.2. Кремнеземистые компоненты
- •1.4.3. Газообразователи
- •1.4.4. Пенообразователи
- •1.4.5. Корректирующие добавки и вода затворения
- •1.4.6. Сырьевая база Омской области для производства ячеистых бетонов
- •1.5. Способы активации сырьевых материалов и смесей при получении эффективных ячеистых бетонов
- •Г Л А В А 2. ТЕХНОЛОГИИ ЭФФЕКТИВНЫХ СТРОИТЕЛЬНЫХ МАТЕРИАЛОВ И ИЗДЕЛИЙ ИЗ ПЕНОБЕТОНОВ
- •2.1. Теоретические основы поризации кремнеземвяжущей массы механическим способом
- •2.2. Технология строительных материалов и изделий из неавтоклавного пенобетона
- •2.2.1. Производство пенобетонных блоков «Сиблок»
- •2.2.2. Технология пенобетона «ВНИИстром»
- •2.2.4. Производство пенобетона на технологическом комплексе ПБК–Р
- •2.3. Технология получения автоклавного пенобетона
- •2.4. Производство пенобетона по технологии «Новостром»
- •2.5. Современные технологии производства строительных материалов и изделий из пенобетона
- •2.5.1. Производство двухслойных стеновых блоков из бетонов различной плотности
- •2.5.5. Производство пенобетона «Экстрапор»
- •2.5.6. Вакуум-формовальная технология ячеистых бетонов
- •2.5.7. Технология пенобетона способом «обжатие – релаксация»
- •2.5.9. Пенобетоны сухой минерализации
- •Г Л А В А 3. ТЕХНОЛОГИИ ЭФФЕКТИВНЫХ СТРОИТЕЛЬНЫХ МАТЕРИАЛОВ И ИЗДЕЛИЙ ИЗ ГАЗОБЕТОНА
- •3.1. Теоретические основы поризации массы химическим способом порообразования
- •3.2. Технологии газобетона неавтоклавного твердения
- •3.3. Технологии материалов и изделий из газобетона автоклавного твердения
- •3.3.1. Производство газобетонных изделий на новосибирском заводе «Сибит»
- •3.3.3. Технология газобетона на омском комбинате пористых материалов «Вармит»
- •3.5.1. Материалы и изделия переменной плотности
- •3.5.2. Производство газобетонных изделий способом автофреттажа
- •3.5.3. Способ получения эффективных изделий в закрытой форме
- •3.5.4. Производство сухих газобетонных смесей
- •4.1. Проектирование состава ячеистых бетонов
- •4.1.2. Расчет состава пеногазобетона
- •4.2. Расчет и подбор технологического оборудования
- •4.2.1. Расчет технологического оборудования
- •4.2.2. Технологическое оборудование
- •4.3.1. Способы снижения водопоглощения
- •4.3.2. Отделка поверхности изделий из ячеистого бетона
- •4.4. Реконструкция предприятий силикатных изделий
- •Библиографический список
4.2. Расчет и подбор технологического оборудования
4.2.1. Расчет технологического оборудования
Расчет емкости шламбассейнов. |
|
Vш = Q · n / d, |
(4.24) |
СибАДИ |
|||||
где |
Vш – объем шламбассейнов, м3; Q – часовой расход кремнеземистого |
||||
компонента |
(песка), |
т; n – запас кремнеземистого компонента, ч; |
|||
d – кол чество кремнеземистого компонента в литре шлама, кг. |
|
||||
|
|
|
|
d = и · ( ш – 1) / и – 1, |
(4.25) |
где |
|
– |
ст нная |
плотность кремнеземистого компонента, |
т/м3; |
ш – средняя плотность шлама, т/м3. |
|
||||
|
Общее кол чество шлам ассейнов принимается не менее трех: один |
||||
для загрузки, второй – для корректировки, третий – для готового шлама. |
|||||
|
Расчет кол чества форм и вагонеток. |
|
|||
|
Кол |
чество вагонеток |
|
||
|
|
|
|
Z1 = (2 · Qг / Vизд · Тоб · Кз) · Кв, |
(4.26) |
где Qг – проектная мощность предприятия, м3/год; 2 – коэффициент, |
|||||
учитывающий число вагонеток на формовке распалубке; Vизд – |
объем |
||||
изделий на одной вагонетке, м3; Тоб – нормативный годовой фонд рабочего |
|||||
времени, ч; Кз – коэффициент о орачиваемости по запариванию, Кз = 1 – |
|||||
– 1,2; Кз = 24 / Т; Т – цикл запаривания; Кв – коэффициент, учитывающий |
|||||
ремонт вагонеток, Кв = 1,05. |
|
||||
|
Количество форм |
Z2 = 1,25 · Z1 · m · Кф, |
(4.27) |
||
|
|
|
|
где 1,25 – коэффициент, учитывающий количество форм на распалубке; m – количество форм на одной вагонетке; Кф – коэффициент, учитывающий ремонт форм, Кф = 1,05.
Количество газобетономешалок |
|
Nг = Qг · · Кр / V · Тоб · n · Кв · Кз, |
(4.28) |
где Qг – проектная производительность предприятия, |
м3/год; |
– коэффициент, учитывающий потери ( = 3 – 5%); Кр – коэффициент резерва производства, Кр = 1,15 – 1,25; V – объем газобетоносмесителя, м3; Тоб – нормативный годовой фонд рабочего времени, ч; n – количество
рейсов |
газобетоносмесителя в |
час; |
Кв – коэффициент |
вспучивания; |
Кз – коэффициент заполнения (Кз = 1,03 – 1,05). |
|
|||
|
n = 60 / (2 · lmax / + tз); |
(4.29) |
||
где lmax |
Кв = 1000 / (Vц + Vп + Vг + В), |
(4.30) |
||
– максимальная длина |
пути |
пробега газобетоносмесителя, м; |
– скорость передвижения газобетономешалки, м/мин; tз – время заливки
111
форм, мин (tз = 5 – 10 мин); Vц, Vп, Vг, В – абсолютные объемы компонентов, л.
При использовании стационарного газобетоносмесителя учитываются количество и объем форм, подаваемых в час к смесителю на формовку.
Производительность автоклава определяют по формуле
СибАДИ |
||
Qа = Vизд / (Та · Тоб · Кп), |
|
(4.31) |
где Vизд – объем изделий в автоклаве, м3; Та – продолжительность цикла |
||
автоклавной обработки, включая время на загрузку |
и |
выгрузку, ч; |
Тоб – годовой фонд времени работы оборудования, ч; Кп – коэффициент, |
||
учитывающ й потери, Кп = 0,975 – 0,99. |
|
|
Кол чество автоклавов |
|
|
Nа = Qа · tа / Vа · f · Тоб, |
|
(4.32) |
где tа – продолж тельность запаривания (ТВО), ч (tа |
= |
12 – 16 ч); |
Vа – объем автоклава, м3 (l = 2 * l, d = 2 м); f – коэффициент заполнения |
||
автоклава. |
|
|
f = Vизд / Vа = 0,3 – 0,4, |
|
(4.33) |
где Vизд – объем здел й, находящихся в автоклаве. |
|
|
Количество пропарочных камер |
|
|
Nп = Qг / Vи · nг · Ко · Ки, |
|
(4.34) |
где Qг – годовая производительность, м3; Vи – объем изделий в камере без форм, м3; nг – количество рабочих дней в году; Ко – коэффициент оборачиваемости камеры (Ко = 1 – 1,2); Ки – коэффициент использования по времени, равный 0,91 [86].
4.2.2. Технологическое оборудование
Вид оборудования и его количество существенно зависят от производительности завода, которая может составлять 5, 10, 20, 40, 80, 120, 160, 200, 240 тыс. м3 изделий в год и более. Современные заводы оснащены весьма сложным и дорогостоящим оборудованием, например шаровые мельницы, измельчающие песок до тонкости цемента, автоматические дозаторы сырьевых компонентов, суспензаторы пеногенераторы, шламбассейны, турбулентные смесители объемом до 12 м3, металлические формы объемом до 8 м3, вибростолы с регулируемой частотой и амплитудой, машины для резки и прикатки ячеистого бетона, автоклавы диаметром до 3,6 м и длиной 27 м, работающие под давлением 12 атм при температуре выше 170 °С. Завод средней производительности, равной 80 тыс. м3 в год, оснащен четырьмя такими автоклавами, при производительности 240 тыс. м3 в год – 12 автоклавами.
112
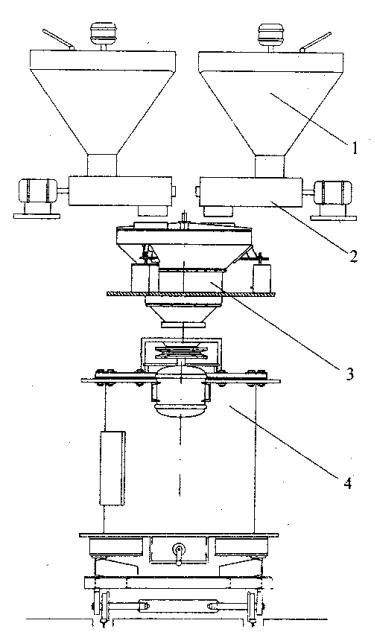
Завод небольшой производительности (5 – 20 тыс. м3 в год), выпускающий в основном неавтоклавный ячеистый бетон, содержит минимум оборудования, основные его элементы показаны на рис. 4.1 [87].
СибАДИРис. 4.1. Основное оборудование для приготовления ячеистобетонной смеси:
1 – бункер; 2 – питатель; 3 – дозатор; 4 – смеситель
Шаровые мельницы сухого или мокрого помола являются оборудованием, широко используемым в разных отраслях промышленности, они рассчитаны на разную производительность и разные режимы работы. Сухому или мокрому помолу обычно подвергают
113
кварцевый песок. Продукт мокрого помола направляется в шламбассейн, а сухого помола – в расходный бункер смесеприготовительного отделения цеха.
Мельница является необходимой при выполнении двух условий: а) завод выпускает автоклавный ячеистый бетон; б) в качестве заполнителя используется кварцевый песок.
СибАДИШламбассейн представляет собой вертикальную цилиндрическую емкость объемом в несколько десятков кубометров с осевым лопастным валом, непрерывно перемешивающим шлам, во избежание его расслоения. Увеличен ю однородности шлама способствует его барботаж сжатым воздухом. Шлам насосом подают в весовой дозатор и затем самотеком в смеситель (в газобетономешалку или пенобетономешалку). Использование шлама вместо сухого молотого песка способствует повышению однородности яче сто етонной смеси и, как следствие, сокращению расхода вяжущего, при этом уменьшаются энергозатраты на помол песка, но непрерывное перемешивание шлама требует своих затрат энергии, кроме того, шлам ассейны тре уют дополнительных производственных площадей, обслуж ван я и т.д. Вопрос выбора мокрого или сухого помола песка решается сходя з экономических соображений, мокрый помол чаще встречается на крупных заводах.
Расходный ункер – это емкость круглого или прямоугольного сечения, нижняя часть которой имеет форму усеченного конуса или усеченной пирамиды. Он располагается в смесеприготовительном отделении цеха на высоте 5 – 7 м от пола с тем расчетом, что находящийся в нем сырьевой компонент будет самотеком перемещаться в дозатор и далее в смеситель. Заполнение бункера производят с помощью пневмотранспорта или механических подъемников. Компоненты ячеистого бетона – тонкодисперсные порошки, способные слеживаться образовывать внутри бункера своды, препятствующие выгрузке сырья из бункера. Традиционным решением этой проблемы является установка вибратора на внешней стороне боковой стенки бункера. Однако данное средство, хорошо зарекомендовавшее себя в технологии тяжелых бетонов, при использовании обычных немолотых песков является малоэффективным при производстве ячеистых бетонов. Для этого в основном применяют вертикальный вращающийся вал, на котором навешаны отрезки цепей. В исходном положении цепи параллельны валу и оказывают большое сопротивление вращению, но если образуется полость под сводом, цепи отбрасываются в стороны центробежными силами и обрушают свод [87].
Для того чтобы из бункера в дозатор не попало избыточное количество материала, между ними устанавливают дополнительную единицу оборудования, называемую питателем. Известно множество типов
114
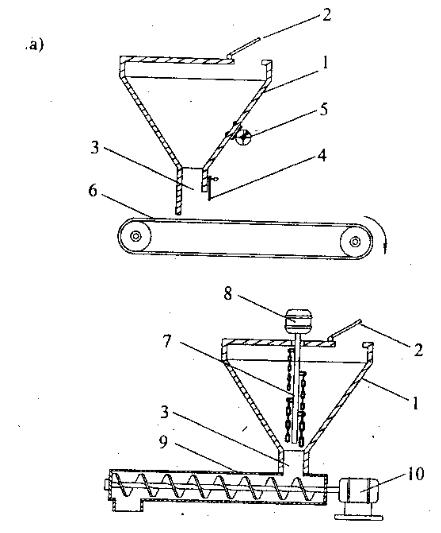
питателей: тарельчатые, ящичные и другие. Два типа показаны на рис. 4.2: это ленточный – позиция 6 (привод условно не показан) и шнековый питатель 9 с приводом 10.
|
а |
|
|
|
|
|
|
|
СибАДИ |
||
|
б |
|
|
|
|
|
Рис. 4.2. Бункеры с питателем: |
|
а – бункер с вибратором; – бункер с приводным валом; |
||
1 |
– |
корпус бункера; 2 – загрузочный люк; 3 – течка; |
|
4 |
– |
шибер; 5 – вибратор; 6 – ленточный питатель; |
7 – вращающийся цепной вал; 8 – мотор-редуктор; 9 – шнек; 10 – электропривод
В ряде случаев питатели используют в качестве объемных дозаторов, изменяя положение шибера, скорость движения ленты и шнека.
Весовые дозаторы долгое время были слабым местом в технологии бетонов, т.к. являясь достаточно сложными механическими приборами, они работали в условиях воздействия пара и цементной пыли, что быстро выводило их из строя. В настоящее время все большее распространение
115

получают дозаторы на силоизмерительных тензорезисторных датчиках, например, на датчиках ДСТ 9035, рассчитанных на нагрузку 1000 кгс (имеются и более грузоподъемные датчики). На рис. 4.3 показан вариант дозатора на тензорезисторах, предназначенного для завода небольшой производительности – от 10 до 20 тыс. м3 в год, его объем около 1 м3, максимальный вес с дозируемыми продуктами составляет 3000 кг [87].
СибАДИ
Рис. 4.3. Весовой дозатор:
1 – цилиндроконический корпус; 2 – опора дозатора; 3 – тензорезисторный датчик (ДСТ 9035); 4 – перекрытие; 5 – разгрузочный клапан; 6 – загрузочный люк
116
Дозатор опирается на три тензорезисторных датчика, преобразующих приложенное к ним усилие в электрический сигнал и соединенных с регистрирующим прибором. Дозатор имеет четыре загрузочных люка: для цемента, извести, дисперсного заполнителя и добавки. Эти компоненты в нужной последовательности и в заданном количестве загружаются в дозатор и потом, поочередно или все вместе, выгружаются в смеситель.
СибАДИПреимущество такого дозатора в отсутствии трущихся частей, влияющих
на его долговечность и точность измерения, а также в возможности выноса регистр рующего пр бора в помещение, защищенное от пыли и пара.
Поз ц рассматр ваемого весового дозатора (см. рис. 4.3):
1 – цил ндрокон ческ й корпус, выполненный из металлического листа толщиной 3 – 5 мм; 2 – опора дозатора в виде нарезной шпильки с гайкой, позволяющей регул ровать длину опоры; 3 – тензорезисторный датчик (Д Т 9035), установленный на цепной подвеске, исключающей появление горизонтальных ус л й (корпус дозатора опирается на три таких датчика); 4 – перекрыт е смесеприготовительного отделения (над смесителем); 5 – разгрузочный клапан (его привод условно не показан); 6 – загрузочный люк.
Суспензатор – это агрегат, предназначенный для приготовления газообразователя (алюминиевой суспензии). Он представляет собой герметично закрываемый сосуд о ъемом 900 л с люком, к которому примыкает стандартная жестяная бочка с алюминиевой пудрой. Суспензатор снабжен мощным центробежным насосом для вымывания пудры из бочки и барботажа суспензии (рис. 4.4).
Работа суспензатора заключается в следующем: в сосуд 1 заливают 800 л воды и засыпают 2 кг поверхностно-активного вещества (сульфанол, стиральный порошок). Затем в поворотный держатель 2 помещают бочку с пудрой 3, подводят ее к люку 4 и начинают вращать винтовую рукоятку держателя 5, в результате жестяная крышка бочки плотно прижимается к кольцевой резиновой прокладке 6, расположенной соосно люку 4 и прикрепленной к корпусу 1. После этого включают насос 7 и он через патрубок 8 отбирает жидкость из нижней части сосуда 1, под давлением подает ее в тангенциально установленный патрубок 9, барботирующий суспензию, в вертикальный патрубок 10, струя которого бьет в крышку бочки 3. После чего опять вращают рукоятку 5, бочка перемещается ниже, цилиндрический нож 11 вырезает отверстие в крышке бочки, при этом вертикальная струя жидкости попадает в бочку и начинает вымывать из нее пудру. Этот процесс продолжается 20 – 30 мин, после чего суспензия усредняется, становится однородной и ее через патрубок 12 заливают в объемный дозатор и далее в смеситель [87].
В одной бочке содержится 27 – 30 кг алюминиевой пудры, т.е. ее хватает на изготовление 30 – 40 м3 ячеистого бетона (на одну – две смены
117
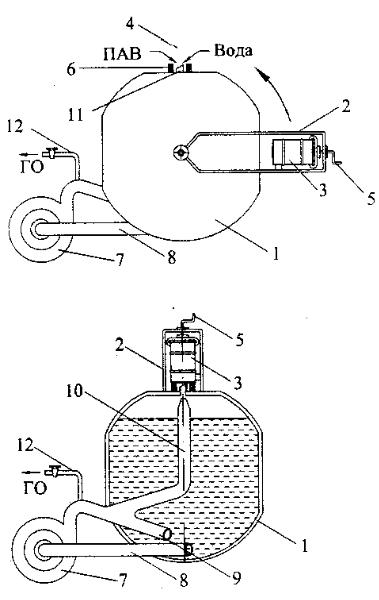
работы небольшого завода). В случае мелкого производства (возведение собственного коттеджа) алюминиевую суспензию готовят в ведре, перемешивая вручную пудру с раствором ПАВ до тех пор, пока на поверхности не останется сухой плавающей пудры (суспензию готовят из расчета на один замес).
Си бА Д
Рис. 4.4. Суспензатор для приготовленияИ алюминиевой суспензии:
1 – сосуд; 2 – держатель; 3 – бочка с пудрой; 4 – люк; 5 – рукоятка; 6 – резиновая прокладка; 7 – насос; 8 – патрубок; 9 – тангенциальный патрубок; 10 – вертикальный патрубок; 11 – нож цилиндрический; 12 – сливной патрубок
Пеногенератор предназначен для приготовления технической пены, используемой в производстве пенобетона (рис. 4.5). Обычно он содержит
118

два канала – для пенообразователя 1 (рис. 4.5, а) и для воздуха 2, которые примыкают к камере смешения 3, одна из стенок этой камеры выполнена в виде пакета мелких пеногенерирующих сеток 4, далее располагается камера диспергирования 5, заполненная металлической стружкой или путаной проволокой. В случае, если пена готовится под давлением, для
С |
7. Готовая пена |
|||
этого имеется гидравлический насос 6 и компрессор |
||||
выдается через выпускной патрубок 8 [87]. |
|
|||
|
а |
|
|
|
|
и |
|
||
|
|
бА |
|
|
|
|
|
Д |
|
|
б |
|
||
|
|
И |
||
|
|
|
||
|
|
|
||
|
|
|
Рис. 4.5. Пеногенератор: |
|
а, б – разновидности пеногенераторов для приготовления технической пены: 1 – канал для пенообразователя; 2 – канал для воздуха; 3 – камера смешения; 4 – пеногенерирующие сетки; 5 – камера диспергирования; 6 – насос гидравлический; 7 – компрессор; 8 – патрубок выпускной; б – простейший пеногенератор: 9 – насос центробежный; 10 – вентиль-дозатор
119
В простейшем случае пеногенератор не имеет отдельных каналов для подачи воздуха и пенообразователя, он не имеет также и компрессора. К камере смешивания примыкает один небольшой центробежный насос 9 (рис. 4.5, б), во всасывающий патрубок которого через вентили-дозаторы
10 подают воздух и пенообразователь. |
|
С |
3, но структура ее получается |
Пена образуется в камере смешения |
неоднородной, с крупными ячейками. Согласно закону Лапласа давление воздуха в ячейках разных размеров обратно пропорционально радиусам этих ячеек, если рассматриваемые ячейки контактируют, то разность
жидкости), при этом уменьшается свободная энергия системы, происходит так называемая коалесценсия. Укрупняющиеся пузырьки всплывают, лопаются, пена разрушается, снижается важный показатель качества
давлен й в н х пр вод т к перетеканию воздуха из маленькой ячейки в большуюпеногенерирующие, даже без разрыва перегородки (через растворение воздуха в
б |
|
пены – ее стойкость. |
|
Для предотвращен я этих негативных явлений в пеногенераторе |
|
устанавл ваются |
сетки (с ячейками менее 1 мм) и |
камера д сперг рован я пены. В результате из выпускного патрубка выходит пена с мелк ми ячейками практически одинакового радиуса, давление в соседнихОАОячейках выравнивается, стойкость пены возрастает.
Разработанный в «ВНИИстром» пеногенератор ПГ–3 выпускается трех типоразмеров производительностью до 120, 350 и
600 л/мин. Эти пеногенераторы используются в составе мобильных установок ПБУ [32].
например марки СМС–40Б, предназначенДдля изготовления ячеистых бетонов в основном способом газообразования (газобетоны). Стационарный двухбарабанный смеситель марки СМ – 578 применяется в
Смесители для приготовления ячеистого бетона могут быть стационарными или самоходными. В первом случае форму, на время
заливки, подают к смесителю краном или на тележке, во втором –
смеситель по рельсам перемещается к форме. Самоходный смеситель,
производстве пенобетона: в одном барабане в течение 5 мин готовят пену,
а в другом в течение 1 – 2 мин – раствор из вяжущего, заполнителя и воды; |
|
затем пену выгружают в барабан с раствором и перемешивают еще не |
|
менее 2 мин. |
И |
Самоходный смеситель для крупного завода имеет объем 4 – 12 м3 и |
|
более (рис. 4.6). Корпус смесителя 1 снабжен загрузочным люком 2, |
|
центральным вертикальным приводным валом 3, выпускным клапаном 4 и |
|
люком для ревизии 5. К приводному валу 3 прикреплены перемеши- |
|
вающие лопатки 6, имеется также выпускной патрубок 7. Смеситель |
|
установлен на самоходной |
раме 8, снабжен узлом динамических |
120
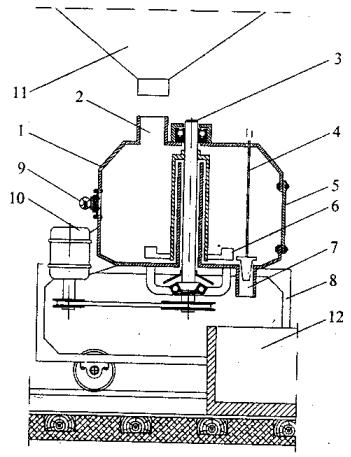
воздействий 9 и приводом 10. Узел динамических воздействий, создающий дополнительную турбулентность в ячеистобетонной смеси, может быть в виде вибратора, прикрепленного к корпусу через резиновую прокладку, или в виде поршня, создающего в смеси пульсации большой амплитуды, или в виде дополнительного быстроходного вала с перемешивающим
С |
|
|
рабочим органом. На время загрузки смеситель устанавливают так, чтобы |
||
загрузочный люк 2 оказался под течкой дозатора 11, а при заливке смеси |
||
выпускной патрубок 7 располагается над формой 12. |
||
и |
|
|
бА |
||
|
|
Д |
|
|
И |
|
Рис. 4.6. Газобетоносмеситель: |
|
1 |
– корпус; 2 – люк загрузочный; 3 – приводной вал; |
|
4 |
– выпускной клапан; 5 – люк для ревизии; 6 – лопатки |
|
смесителя; 7 – выпускной патрубок; 8 – самоходная рама; |
||
9 |
– узел динамических воздействий; 10 – электропривод; |
|
11 – дозатор; 12 – форма |
|
Для заводов небольшой производительности (5 – 20 тыс. м3 в год) разработан более простой смеситель объемом 2 м3 (рис. 4.7). Цилиндрический корпус 1 диаметром и высотой 1,5 м снабжен консольным лопастным валом с приводом 2, выпускным люком 3 и установлен на легкой автоклавной тележке 4. На время загрузки его
121
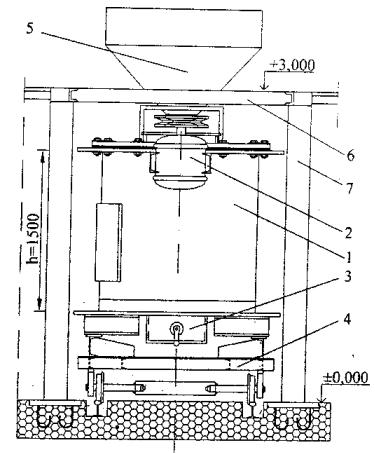
устанавливают под течкой дозатора 5, опирающегося на несущие конструкции 6 и 7 [87].
С |
|
|
|
|
|
|
|
|
|
|
|
|
|
|
|
|
|
|
|
|
|
|
|
|
|
|
|
|
|
|
|
|
|
|
|
|
|
|
|
|
|
|
|
|
|
|
|
|
|
|
|
|
|
|
|
|
|
|
|
|
|
|
|
|
|
|
|
|
|
|
|
|
|
|
и |
|
|
|
|
|
|
|
|
|
|
|
|||
бА |
|
|
|
|
|
|
||||||||
|
|
|
|
|
||||||||||
|
|
|
|
|
||||||||||
|
|
Рис. 4.7. Самоходный смеситель: |
|
|
|
|||||||||
1 – |
корпус; 2 |
– электропривод; 3 |
– выпускной люк; |
|
||||||||||
4 – автоклавная тележка; 5 – дозатор; 6, 7 – опорные |
|
|||||||||||||
несущие конструкции |
|
|
|
|
|
|
|
|
|
|
|
|||
Гидродинамический |
смеситель |
Г С–3 |
применяется |
для |
||||||||||
приготовления различных видов ячеистобетонныхДсмесей, вместимость |
||||||||||||||
смесителя – 2 м3, скорость передвижения – 15 м/мин. Смеситель |
||||||||||||||
самоходный с периферийной разгрузкой смеси [7]. |
|
|
|
|
|
|
|
|
||||||
Виброгазобетоносмеситель |
СМС–40Б |
|
предназначен |
для |
||||||||||
интенсивного перемешивания газобетонной смеси и выдачи ее в формы, |
||||||||||||||
представляет собой самоходный портал (колеяИпортала – 4200 мм), |
||||||||||||||
перемещающийся |
на |
четырех |
колесах |
по |
рельсам со |
скоростью |
||||||||
10 – 15 м/мин. Вместимость смесителя – 5 м3. |
|
|
|
|
|
|
|
|
|
|||||
Рассмотренные смесители периодического действия выдают порцию |
||||||||||||||
приготовленной смеси каждые 10 – 20 мин, ее объем должен быть равен |
||||||||||||||
объему одновременно заливаемых форм. Однако в технологии ячеистых |
||||||||||||||
бетонов применяют и |
смесители |
непрерывного |
действия, |
особенно в |
122

производстве пенобетона, поскольку пенобетонная смесь более чувствительна к увеличению объема замеса, чем газобетонная. Смеситель непрерывного действия особенно эффективен при монолитном домостроении, при заливке больших площадей теплоизоляционным бетоном (крыши, теплые полы и т.д.).
Чаще всего основой смесителя непрерывного действия является горизонтальная труба с центральным приводным лопастным валом и
рядом окон для загрузки компонентов и выгрузки готовой смеси. На рис. 4.8 показана установка для непрерывного приготовления пенобетонной смеси, которая включает в себя цилиндрический корпус 1 с
приводным лопастным валом 2 (привод условно не показан), часть |
|
цилиндр ческого корпуса 3 может иметь увеличенный диаметр и широкие |
|
С |
|
4 |
на пр водном валу (в узкой части корпуса на валу установлены |
стержни |
5, расположенные по винтовой линии). В зоне изменения |
лопаткидиаметра корпуса в нижнюю его часть врезан тангенциально расположенный патру ок 6 для подачи пены, а в конце широкой части
|
12 |
|
Жидкость |
|
|
затворения |
10 |
|
бА |
||
|
||
Д |
||
И |
Рис. 4.8. Пенобетономешалка непрерывного действия:
1 |
– корпус; 2 – лопастной вал; 3 |
– цилиндрический корпус; 4 – лопатки; |
||
5 |
– |
стержни; 6 – патрубок подачи |
пены; 7 – выпускной патрубок; |
|
8 |
– |
загрузочный люк; 9 – труба |
для |
подачи воды; 10 – пеногенератор; |
11 – дозатор; 12 – ем-кость для пенообразователя; 13, 14, 15 – бункера для сухих компонентов
123
корпуса имеется выпускной патрубок 7. В начале узкой части корпуса расположен загрузочный люк 8 для сухих компонентов пенобетона и труба для ввода воды затворения. Установка снабжена пеногенератором 10, дозаторами 11, емкостью для пенообразователя 12 и бункерами 13, 14 и 15 для сухих компонентов пенобетона [87].
СТ |
|
Для производства пенобетонных изделий применяются также |
|
упермиксер –10, пенобетоносмесители «Новостром» и ТСК–310 [7]. |
|
упермиксер СТ–10 предназначен для непрерывного приготовления |
|
пенобетонной смеси под давлением 0,4 МПа, |
производительность до |
10 м3/ч. |
|
ционный |
– производительность |
Пенобетоносмес тель «Новостром» |
5 – 7 м3/ч, давлен е сжатого воздуха для транспортировки поризованной массы 0,7 МПа.
Пенобетоносмес тель ТСК–310 обеспечивает турбулентно-кавита-
борта элементами формы должныАыть существенно меньшими, необходима
пр нц п пор зации массы, производительность 5 – 7 м3/ч.
Формы для зал вки ячеистобетонных смесей содержат те же элементы, что формы для приготовления других видов бетона (днище и
откидные |
на шарнирах), но они имеют важную особенность. |
Ячеистобетонная смесь, в отличие, например, от смеси тяжелого бетона |
|
обладает |
значительно ольшей текучестью, поэтому зазоры между |
повышенная точность изготовления форм. Иногда предусматривают установку между элементами форм специальных фигурных прокладок из термостойкой резины, выдерживающей многократную автоклавную обработку (Т>170 °С, давление доД25 атм). Иногда борта формы соединяют с днищем через тонкий упругий металлический лист. Известна форма для непрерывной заливки в виде длинного желоба, выполненного из трех ленточных транспортеров (двух вертикальных и одного горизонтального). Существует форма, у которой по верхнему ее обрезу установлена жесткая горизонтальная металлическая рама и к ней шарнирноИприкреплены борта, покрытые изнутри обычной резиной, на время заливки нижние концы бортов плотно прижимаются к поддону, а после схватывания смеси раму с бортами снимают и термообработку изделие проходит на поддоне без бортов.
Чаще всего из ячеистого бетона формуют изделия одного из трех видов: а) плитные изделия – стеновые панели и крупные блоки, плиты покрытий и перекрытий; б) ячеистобетонные массивы объемом до 8 м3, которые после схватывания, но до термообработки разрезают на блоки или панели; в) мелкие стеновые блоки, изготовляемые в формах со съемными внутренними перегородками – «гребенками».
На рис. 4.9 показана форма с откидывающимися шарнирными бортами и внутренними перегородками – «гребенками». «Гребенки»
124
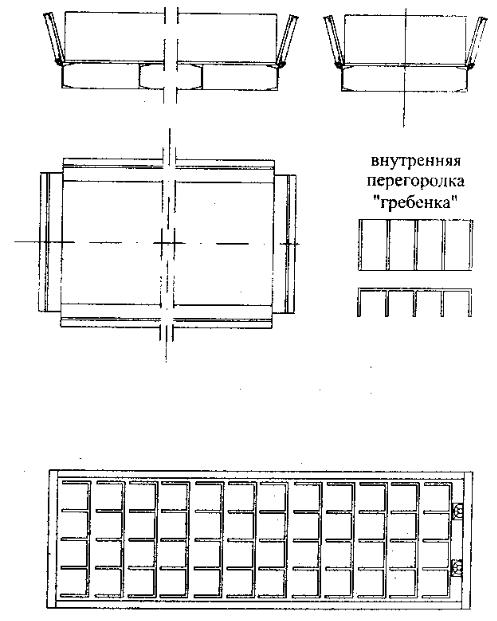
выполнены из листовой стали толщиной 2 мм при помощи электросварки. Размеры их ячеек обычно составляют 20х20 см, а высота 40 см. «Гребенки» устанавливают вплотную друг к другу сразу после заливки ячеистобетонной смеси и в зазор между последней «гребенкой» и бортом формы вставляют клинья [87].
С |
|
|
|
и |
|
|
|
|
Внутренняя |
|
|
бА |
|
||
перегородка – |
|
||
«гребенка» |
|
||
|
|
|
|
|
|
|
|
|
Д |
Форма с зарытыми бортами и установленными «гребенками»
Рис. 4.9. Форма для мелких блоковИ
Свежеприготовленная ячеистобетонная смесь обладает высокой текучестью, что достигается за счет повышенного расхода воды затворения. Для получения качественной структуры ячеистого бетона необходимо повышенное влагосодержание смеси потому, что вода расходуется не только на заполнение зазоров между зернами вяжущего и
125
заполнителя, но и на смачивание внутренней поверхности ячеек, а суммарная площадь этой поверхности огромна. Снизить водоцементное отношение без ухудшения структуры возможно за счет динамических воздействий, приводящих к тиксотропному разжижению бетонной смеси, это вибрирование, трамбование. В технологии газобетонов также используют динамические воздействия, при этом вспучивание газобетонной смеси осуществляется на виброплощадке (вибровспучивание). Для получения требуемых реологических характеристик смеси (т.е. хорошей ее текучести, обеспечивающей получение качественной ячеистой
структуры |
предотвращающей прорыв газовых пузырьков) необходимо |
||||
уменьш ть влагосодержание смеси, что приводит к ускорению |
|||||
схватыван я |
смеси |
существенному |
сокращению |
длительности |
|
С |
|
|
|
|
|
необход мой технолог ческой выдержки (до 1 – 2 ч) между формованием |
|||||
его термоо ра откой. Все это позволяет уменьшить площади, |
|||||
необход мые для вызревания изделий, |
уменьшить расходы на отопление, |
||||
освещен е |
|
цеха, сократить длительность термообработки и |
|||
удельные энергозатраты. |
|
|
|
||
изделия |
смеси с низким водотвердым |
||||
Для вспуч ван я |
газо етонной |
||||
отношен ем |
на отечественных заводах |
используют |
виброплощадки |
применения,уборкунапример СОЖ–200В, СМЖ–198 и другие, применяемые при изготовлении железо етонных изделий. Производительность виброудар-
К–469М, ЛВ–32, ЛВ–33, ЛВ–37, а также виброплощадки общего
ВибровспучиваниеАв технологии газобетона имеет и недостатки. Колебания разных участков обычнойДвиброплощадки не одинаковы по амплитуде и даже по фазе. При виброобработке тяжелого бетона это не имеет большого значения, но газобетонная смесь наиболее быстрее вспучивается в зонах наибольшей интенсивности вибрационных воздействий. При неравномерном вспучивании вода затворения интенсивно отсасывается в зоны быстрого вспучивания и дополнительно увеличивает их поризацию, в форме возникают потоки смеси с замкнутыми траекториями. Все это приводит к неоднородности изделий с появлением ослабленных зон, по которым происходит разрушение и,
ной площадки ЛВ–37 составляет 32,3 м3/ч, грузоподъемность – 20 т [2].
вибровспучивания и исключающим негативныеИпоследствия, является шок-стол, отличающийся от виброплощадки тем, что вместо вибратора с вращающимся эксцентриком содержит кулачки. Благодаря этому все точки стола всегда имеют одинаковую фазу и одинаковую регулируемую амплитуду. Частоту колебаний меняют с помощью вариатора в цепи привода. Основные детали шок-стола показаны на рис. 4.10 [87].
наоборот, утяжелению областей, которые служат мостиками холода.
Оборудованием, сохраняющим положительные качества
126
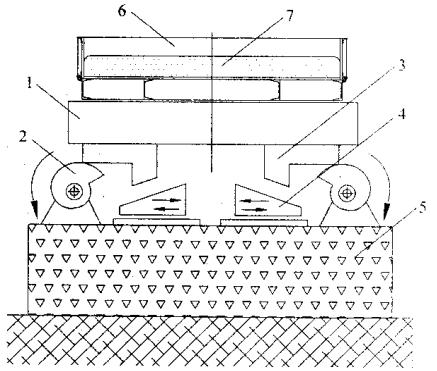
Си Рис. 4.10. Шок-стол:
1 – стол; 2 – кулачок; 3 – ударник; 4 – опора ударника; 5 – фундамент; 6 – форма; 7 – вспучивающаяся смесь
Во время технологической выдержки изделия перед термообработкой выполняют различные технологические операции: срезка и удаление
горбушки, образующейся над ортами формы в результате вспучивания |
||
газобетона; разрезание ячеистобетонного массива на отдельные изделия; |
||
уплотнение бетона вблизи одной или нескольких поверхностей изделия и |
||
бА |
||
т.д. Операция |
срезки и удаления горбушки |
раньше существенно |
усложняла технологию: во-первых, не существовало достаточно простых и |
надежных машин для срезки горбушкиДи эту операцию выполняли вручную, с низким качеством и с большими трудозатратамиИ; во-вторых, объем горбушки мог достигать 20% всего производимого газобетона и удаление отходов из зоны срезки также требовало значительных затрат труда, времени и энергии; в-третьих, не было удовлетворительных способов утилизации отхода, и зачастую вся горбушка шла в отвал, повышая материалоемкость производства и ухудшая экологическую обстановку. Поэтому с появлением прикатывающих машин не было обычных трудностей, связанных с внедрением в производство новой техники, и за короткое время они появились более чем на 30 крупнейших отечественных заводах ячеистого бетона. Первоначально машины использовались не по своему прямому назначению, не для уплотнения поверхностного слоя ячеистобетонных изделий, а только для вдавливания в форму горбушки вместо ее срезки и удаления. Первые машины имели пассивный (неприводной) прикатывающий вал, установленный на
127
стационарной П-образной раме; изделие на тележке прокатывали под валом, опирающимся на борта формы, и он своей тяжестью вдавливал горбушку в форму, реализуя безотходную калибровку изделия. Позднее появились самоходные машины с пассивным валом.
Однако сразу же обнаружились два негативных явления: на пассивный вал интенсивно налипала ячеистобетонная масса, кроме того, вал частично «сдвигал» горбушку, в результате чего на прикатанной поверхности появлялись трещины, параллельные оси вала. Обе проблемы были решены, когда появился приводной прикатывающий вал, вращающ йся со скоростью 200 – 300 об/мин. Вал скользил по ячеистому бетону, т ксотропно разжижал и дегазировал его. Недостаток способа в
том, |
что |
получался злишне |
толстый |
и |
тяжелый |
уплотненный |
|||||
С |
|
|
|
|
|
|
|
||||
поверхностный слой с резкой границей между ним и ячеистым бетоном |
|||||||||||
(при |
эксплуатац |
зделия |
уплотненная |
часть |
иногда |
отслаивалась). |
|||||
Параметры плотного слоя (его толщина и распределение плотности по |
|||||||||||
сечению) практ чески не поддавались регулированию. |
|
||||||||||
|
Кард нальное |
|
про лем прикатывающей |
машины было |
|||||||
решение |
предложено |
использовать приводной |
|||||||||
достигнуто |
тогда, |
когда |
ыло |
||||||||
синхронно вращающ йся нагреваемый вал. Согласование линейной |
|||||||||||
скорости |
|
|
|
вала и перемещения корпуса самоходной машины |
|||||||
предотвращало |
появление сдвиговых трещин, а нагрев вала до |
||||||||||
|
|
образующей |
|
|
|
|
|||||
150 – 200 °С исключал возможность налипания ячеистого бетона за счет |
|||||||||||
появления прослойки пара между поверхностью вала и влажным |
|||||||||||
прикатываемым бетоном. Такие машины с прикатывающим валом, |
|||||||||||
содержащим |
внутренние |
электронагреватели |
с |
регулируемой |
|||||||
температурой и приводАсинхронного вращения, были разработаны в 1975 – |
|||||||||||
1977 гг. Они были оборудованы узлом для частичной срезки и удаления |
горбушки, бункером для подсыпкиДна прикатываемую поверхность дисперсного материала, вентилятором для охлаждения прикатываемой поверхности, комплектом пустотообразователей для образования вентиляционных каналов под уплотненным слоем, создаваемых в процессе прикатки, штампом для нанесения на поверхность изделия рельефного
рисунка и т.д. Диаметр прикатывающего вала 380 мм, максимальная
ширина обрабатываемых изделий 2 – 3 м. Габариты машин: 2х3,75х3,58 м |
|
и 2,2х5х3,56 м соответ-ственно при массе 8,3 и 9,97 т. Основные узлы |
|
подобной машины показаны на рис. 4.11. |
И |
На поверхности пенобетонного изделия создать уплотненный слой путем прикатки сложнее, чем на газобетонном изделии. Это связано с меньшей газопроницаемостью перегородок между ячейками. Поэтому для уплотнения поверхностного слоя пенобетонных изделий предложены
128
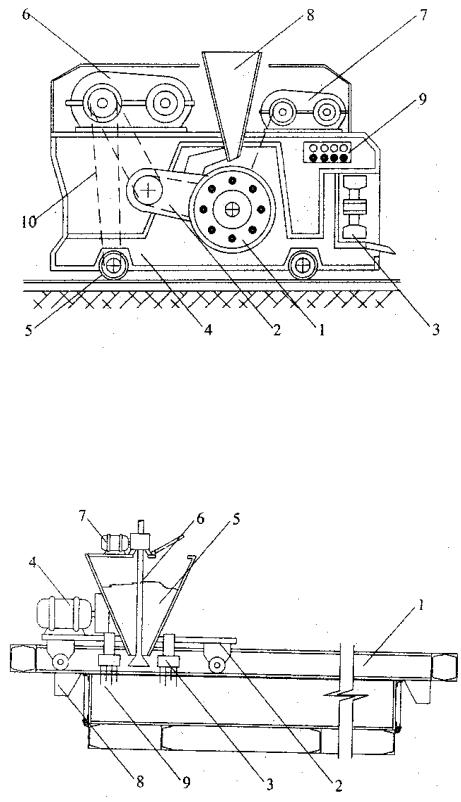
СибАР с. 4.11. Основные узлы машины для уплотнения поверхностного слоя ячеистобетонных изделий:
1 – пр катывающ й вал; 2 – поворотная каретка; 3 – узел срезки и удаления гор ушки; 4 – самоходная рама тележки; 5 – ходовые колеса; 6 – привод хода машины и вращения вала; 7 – привод вертикальных перемещений вала и узла срезки горбушки; 8 – бункер; 9 – пульт управления; 10 – шкив
Д И
Рис. 4.12. Машина для уплотнения поверхностного слоя ячеистобетонных изделий:
1 – жесткая рама; 2 – подвижная тележка; 3 – щетка; 4 – привод перемещения тележки; 5 – бункер; 6 – клапан; 7 – привод;
8 – ловитель-фиксатор; 9 – форма
129
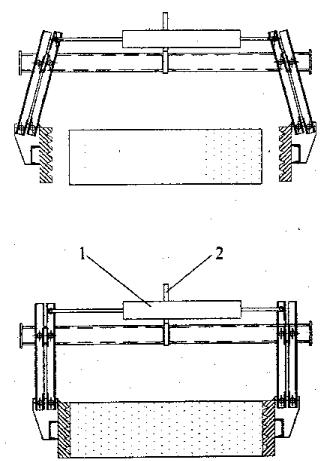
машины иного типа, основанные на разрушении ячеек в поверхностном слое изделия рабочими органами в виде приводных металлических щеток. Для того чтобы получить поверхностный слой переменной плотности, без резкой границы перехода от ячеистого бетона к плотному, применяют щетки с иглами разной длины. Один из вариантов такой машины показан
Сна рис. 4.12.
Перенос массива из формы на стол резательной машины производится специальным захватом (рис. 4.13), который снабжен гидроцилиндром 1 и имеет петлю 2 для подъема захвата с массивом. Усилие, создаваемое гидроц л ндром, рассч тано так, что массив не выскальзывает при подъемеине раздавл вается захватом.
бА Д
Рис. 4.13. Захват для подъема ячеистобетонногоИ массива:
1 – гидроцилиндр; 2 – петля подъема захвата
Машины для разрезания крупного ячеистобетонного массива
применяют чаще всего при массовом изготовлении мелких стеновых блоков. Это довольно сложные металлоемкие и энергоемкие агрегаты, их применение экономически оправдано только на крупных заводах производительностью не менее 80 тыс. м3 в год, высота машины около 2 м, ширина свыше 3 м и длина более 15 м. Машина разрезает ячеистобетонные
130
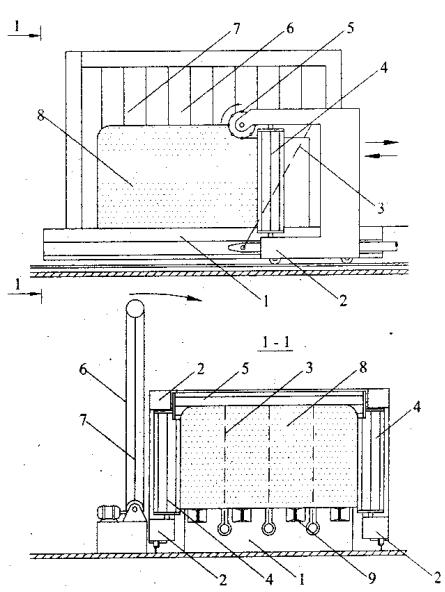
массивы размерами 6,1х1,3х0,7 м и весом 4 – 5 т. Разрезание схватившегося, но не отвердевшего массива производится струнами в двух или в трех взаимно перпендикулярных направлениях, возможна установка заданного расстояния между струнами с шагом от 50 до 100 мм, благодаря чему достигается получение широкой гаммы размеров нарезаемых
Сизделий. Основные узлы рассматриваемой резательной машины показаны на рис. 4.14: 1 – стол для ячеистобетонного массива; 2 – передвижная каретка; 3 – струны для продольной вертикальной резки массива; 4 – верт кальные ц линдрические фрезы с режущими струнами,
предназначенные для калибровки боковых поверхностей массива; и бА Д И
Рис. 4.14. Резательная машина:
1 – стол; 2 – каретка; 3 – струны продольной вертикальной резки; 4 – вертикальные фрезы; 5 – горизонтальная фреза; 6 – поворотная рама; 7 – струны поперечной резки; 8 – массив бетона; 9 – решетка
131
5 – горизонтальная цилиндрическая фреза для калибровки верхней плоскости массива (для срезки горбушки); 6 – поворотная рама с натянутыми струнами 7 для поперечной резки массива 8. Стол 1 имеет углубления, в которые укладывается жесткая решетка 9, необходимая для подъема разрезанного массива и транспортирования его на
С |
2 может дополнительно иметь струны для |
термообработку; каретка |
горизонтальной резки массива, например на плиты [87].
Резательный комплекс «Универсал–60» (СМС–300) предназначен для изготовлен я арм рованных изделий, перегородок и мелких стеновых
блоков з яче стого бетона, включает резательный агрегат СМС–301, гидропрсостоящ й з агрегата продольной резки СМС–301–01 с резательным
блоком, пр водом, рабочим столом и механизмом снятия горбушки; агрегат поперечной резки СМС–301–02 с подъемной рамой, имеющей
|
вод |
бара аны с режущей проволокой, систему уборки отходов |
от двух |
скребковых |
|
|
конвейеров; гидравлические захваты для массива |
СМС–302 (2 шт.), захваты СМС–303 (3 шт.) для решеток запаривания, форму СМС–305 (4 шт.), решетку СМС–306 (5 шт.), кондукторы СМС–307 (6 шт.) для ф кс рован я арматурных каркасов, стенды пакетирования СМС–308 (7 шт.) арм рованных каркасов, захваты СМС–309 для мелких блоков (8 шт.) [2]. А
На рабочий стол захватом СМС–302 устанавливается массив-сырец, удерживаемый бортами формы. Производят поперечную, а затем продольную разрезку. Одновременно с продольной разрезкой срезается горбушка и производится уборка отходов скребковыми конвейерами. Разрезанный массив-сырец на решеткеДСМС–306 снимается захватом СМС–302 или СМС–303.
Производительность резательного комплекса «Универсал–60» (СМС–300) при изготовлении блоков – 20 м3/ч; цикл резки – 9 мин; размеры массива: длина – 6480 мм, ширина – 1230 мм, высота – 650 мм.
На резательных комплексах РК–2М, РКИ–3, РК–3М производится резка массивов с помощью струн с навивкой. Частота колебаний струн, скорость подъема и время позиционирования в нижнем положении рамных модулей поперечной и продольной резки задается по программируемой циклограмме, что обеспечивает дорезку донной части массива. Точность резки находится в пределах ±1,5 мм. Получаемая после резки поверхность изделий с мелким рифленым рисунком способствует лучшему сцеплению кладочного и штукатурного растворов. Уплотненный поверхностный слой имеет вариотропное строение, отслаивание, которого не происходит. Технические характеристики некоторых резательных комплексов приведены в табл. 4.6 [88].
Известны также резательные машины более простой конструкции для заводов меньшей производительности, не требующие переноса массива.
132

|
|
|
|
Таблица 4.6 |
||
|
Технические характеристики резательных комплексов |
|
|
|||
|
|
|
|
|
|
|
|
Параметры |
Марка резательного комплекса |
||||
|
РК–2М |
РК–3 |
РК–3М |
|
||
|
|
|
||||
|
Номинальные размеры массива, мм |
1200x800x600 |
1200x800x600 |
1200x1200x600 |
|
|
|
Установленная мощность электро- |
|
12 |
|
|
|
|
оборудования, кВт |
|
|
|
|
|
|
|
|
|
|
|
|
|
Мощность энергопотребления, кВт |
4,4 |
7,5 |
|
7,5 |
|
|
Габаритные установочные размеры |
12x3,1x3,3 |
11x3,1x3,3 |
12x3,1x3,3 |
|
|
|
с транспортером, м |
|
||||
|
|
|
|
|
|
|
|
Производ тельность, м3/ч |
4 |
8 |
|
12 |
|
|
Количество |
|
1 |
|
|
|
|
Обслуж вающ й персонал, чел. |
|
|
|
|
|
|
одновременно разрезае- |
1 |
2 |
|
2 |
|
С |
|
|
||||
|
мых масс вов, шт. |
|
|
|
|
|
|
Базовые размеры блоков, мм: |
|
|
|
|
|
|
стеновые |
588(598)x300(295)x188(198) |
|
|||
|
перегородочные |
588(598)x300(295)x88(98) |
|
|
||
|
Автоклав – технологическое оборудование, работающее под |
|||||
давлен ем от 8 до 15 атм. |
минимизировать |
нагрузки, |
||||
|
А |
|
|
|
||
восприн маемые стенками автоклава, его делают в виде полого |
||||||
металлического цилиндра с торцовыми крышками, хотя круглое сечение |
||||||
не оптимальноЧтобыдля заполнения автоклава прямоугольными изделиями. |
||||||
Были попытки изготовления прямоугольного железобетонного автоклава с |
||||||
толщиной стенок около 1 м, но развития эта идея не получила. Усилие, |
||||||
|
|
Д |
||||
воспринимаемое стенкой автоклава, пропорционально его диаметру, что и |
||||||
ограничивает размер поперечного сечения этого агрегата. Наибольший |
||||||
диаметр автоклавов, используемых в промышленности строительных |
||||||
материалов, 3,6 м (такой размер необходим для обработки стеновых |
||||||
панелей размером «на комнату» около 3х3 м). Автоклавы |
бывают |
|||||
|
|
|
И |
тупиковые и проходные. У первого только одна крышка, на другом конце глухая торцовая стенка, у второго – две крышки. Проходной автоклав сложнее в изготовлении и дороже, но он более технологичен для крупных заводов, где с одного конца автоклава (группы автоклавов) расположено формовочное отделение, а с другого – отделение распалубки и подготовки форм к последующим заливкам.
Изделия подают в автоклав на специальных автоклавных тележках с жаростойкими буксами, перемещающимися по рельсовому пути через убирающийся мостик между автоклавом и рельсами цеха. На рис. 4.15 показан проходной автоклав [87].
Выпускаются автоклавы: диаметром 2 м, длиной 17 и 19 м в тупиковом и проходном исполнении; диаметром 2,6 м, длиной 19 м в тупиковом и проходном исполнении, а длиной 26 м в проходном
133
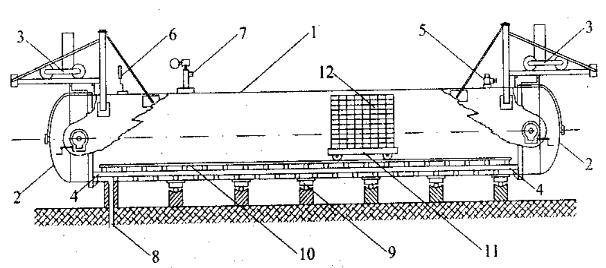
исполнении; диаметром 3,6 м, длиной 27 м в проходном и тупиковом исполнении и длиной 30 м в проходном исполнении [2].
С |
|
|
||
Рис |
|
|||
ячеистобетонныхстобетонныеизделий. Они могут быть ямными или напольными, |
||||
1 |
|
корпус; 2 – крышка; 3 |
. 4.15. Автоклав: |
|
– |
– механизм подъема и опускания |
крышки; |
||
4 |
– |
паровпускная маг страль; |
5 – паровыпускная магистраль; 6 – |
манометр; |
7 – предохран тельный клапан; 8 – конденсационная магистраль; 9 – роликовые опоры; 10 – рельсовый путь внутри автоклава; 11 – автоклавная тележка;
12 – яче |
А |
зделия |
Пропарочные камеры используют в производстве неавтоклавных
реже – туннельными. Во время термообработки изделий в камеру подают пар или другой теплоноситель.
В любом варианте камера Дпредставляет собой прямоугольную емкость, обшитую изнутри металлическим листом и закрываемую крышкой. Ямная камера предпочтительна при наличии внешнего источника пара, она не загромождает цех, снижает требования к минимальной высоте крана, загружающего и разгружающего камеру. Напольная камера больше подходит для электропропаркиИ, т.к. позволяет создать под металлическим днищем камеры канал, в который помещают электронагреватели, обслуживаемые с внешней стороны камеры.
В случае электропропарки около дна камеры монтируют несущие балки, на которые ставят формы с изделиями, а само днище выполняют с уклоном к центральной части. Горизонтальный участок металлической обшивки днища имеется только над каналом, в котором расположены электронагреватели. Залитый в камеру небольшой объем воды нагревается, испаряется, конденсируется на изделиях и обшивке камеры и снова стекает в зону нагрева. На рис. 4.16 показана трехсекционная пропарочная камера с электронагревом [87].
Стенд для формования и обработки изделий – наиболее приемлемое оборудование при небольшом объеме производства. Он состоит из неразъемной бортоснастки в форме усеченной пирамиды с
134

Си бА Д
Рис. 4.16. Камера термообработки с электронагревомИ:
1 – продольная стенка камеры; 2 – торцовая стенка; 3 – перегородка; 4 – несущая балка; 5 – горизонтальная металлическая обшивка днища; 6 – элементы обшивки, выполненные с уклоном; 7 – гидравлический затвор; 8 – канал для электронагревателей; 9 – подсыпка шлака; 10 – теплоизоляция; 11 – крышка с гребнями
прямоугольным основанием (рис. 4.17) и собственно стенда в виде металлической ванны с жесткой площадкой, расположенной в средней части ванны на уровне верхнего обреза ее бортов, кроме того, в комплект стенда входит теплоизолированный колпак, под которым происходит термообработка изделий (рис. 4.18). Под ванной расположены электронаг-
135

реватели, которые, при необходимости, могут быть заменены любым другим источником тепла.
С |
3 |
|
|
и |
|
РисбА. 4.17. Стенд для формования и термообработки изделий:
1 – стенд; 2 – неразъемная ортоснастка; 3 – электронагреватели; 4 – замок; 5 – болт; 6 – фиксатор-ловитель; 7 – основание
Положительным качеством стенда является то, что все его части весят не более 50 кг, т.е. могут использоватьсяДбез применения крана. Наибольшее усилие потребуется для того, чтобы оторвать бортоснастку от схватившегося изделия, но эта проблема легко решается с помощью автомобильного домкрата.
Стенд является оборудованием многократного и длительного использования, он не содержит сложных трущихсяИили вращающихся деталей и может служить довольно долго. На рис. 4.17 показан момент установки стенда, а на рис. 4.18 – работа на нем.
В последнее время появились автоматизированные отечественные линии «Экстраблок», СБИ–80, ПБЗ–120А и ПБУ–0,4.
На линии «Экстраблок» производительностью до 75 тыс. м3 в год выпускаются ячеистобетонные массивы высотой до 900 мм и шириной 600 мм и режутся короткой струной на поддоне формы. Длина формы от
3600 до 4200 мм.
На линии СБИ–80 производительностью до 150 тыс. м3 в год выпускаются массивы высотой 600 мм, шириной 1500 мм и длиной 6000 мм. Изделия из формы переносятся на машину поперечной резки, а затем на машину продольной резки. Массив режется короткой струной [89].
136

С |
|
Последовательность |
|
|
операций при стендовой |
||
|
технологии: |
||
и |
|
А) чистка и смазка стенда; |
|
|
Б) установка бортоснастки, |
||
|
подогрев стенда; |
||
|
В) заливка бетонной смеси; |
||
А |
Г) установка внутренних |
||
перегородок «гребенок»; |
|||
Д) вспучивание смеси; |
|||
б |
|
||
|
Е) удаление горбушки и |
||
|
снятие бортоснастки; |
||
|
|
Ж) удаление бетона, запол- |
|
|
|
няющего пазухи между |
|
|
|
«гребенкой» и бортом; |
|
|
|
З) установка теплоизоли- |
|
|
|
рующего колпака, |
|
|
|
термообработка изделий. |
|
|
|
1 – стенд; |
|
|
|
2 – бортоснастка; |
|
|
И |
||
|
|
9 – колпак; |
|
Д10 – внутренние перего- |
родки «гребенки»
Рис. 4.18. Формование и термообработка блоков на стенде
137
В состав автоматизированной технологической линии ПБЗ–120А по производству стеновых блоков из пенобетона входят: дозировочносмесительный модуль (ДСК), состоящий из дозатора и смесителя сыпучих и жидких компонентов СДЖК–3п; резательный комплекс РК–3М; установка приемки песка УПП; конвейерная линия КЛ 4x16; силос-
Снакопитель для сухих компонентов СН. Кроме того, в комплект оборудования входят ленточные и винтовые транспортеры в зависимости от принятой схемы подачи сырья, а также формооснастка [88].
Про звод тельность линии ПБЗ–120А не более 120 м3/сут, объем производства стеновых блоков по ГОСТ 21520–89 – 30 тыс. м3 в год, объем массива– 0,87 м3, продолжительность формовки массива – 11 мин, продолж тельность выдержки массива до резки – 3 – 4 ч, до штабел рован я – 10 – 12 ч, минимальный складской запас цемента и наполн теля – по 30 т каждый, установленная мощность оборудования +
воздуха (0,8 МПа) – 2500 л/ч, масса – 32 .
подогрев водыпотребление– 20 + 45 кВт, воды – 30 т/сут, потребление
Основным агрегатом ДСК является смеситель объемом 1,2 м3. Для дозировки сух х компонентов используются специальные дозаторы с винтовыми п тателями. Благодаря компактности из них можно собрать модульную секцию для применения от 1 до 4 сырьевых сыпучих материалов; шнек о еспечивает их плавную подачу в смеситель, что предупреждает заклинивание вала. Диапазон взвешивания цемента от 2 до
ПБЗ–120А обеспечиваетАтребуемое качество изделий из неавтоклавного пенобетона и состоит из трех подсистем: автоматизации процесса
400 кг, наполнителей – от 2 до 600 кг.
Автоматизированная система управления технологической линии
приготовления бетонной смеси; автоматизированного управления
конвейерной линии созревания пенобетонных массивов КЛ 4x16 и резки |
|
массивов. |
Д |
–по заданию оператора введение весовыхИдоз сыпучих и объемных доз жидких компонентов и индикацию заданных значений;
–введение временных параметров программируемой циклограммы по последовательности дозировки, загрузки и работы всех узлов смесительного модуля;
–оперативную коррекцию заданных значений дозировки и временных параметров работы внутри цикла;
–индикацию фактических значений массы и объемов дозированных компонентов;
138
– автоматическое взвешивание компонентов в соответствии с заданными значениями;
– автоматическое сблокированное управление выгрузкой компонентов через дозирующее устройство и работой смесителя по заданной циклограмме;
– индикацию работы механизмов на всех стадиях процесса и сигнализацию окончания цикла работы.
Подсистема автоматизации приготовления бетонной смеси имеет четыре реж ма работы – автоматический, полуавтоматический, ручной, дистанц онный.
В автомат ческом режиме управление всем циклом процесса |
|||
взвешиван я, доз ровки компонентов и приготовления пенобетонной |
|||
С |
|
|
|
смеси осуществляется микропроцессором. Технологические параметры |
|||
задаются оператором. Коррекция доз компонентов может выполняться как |
|||
между ц клами, так |
в ходе цикла до окончания работы |
любого из |
|
подциклов. Выгрузка готовой пенобетонной смеси осуществляется |
|||
оператором по с гналу |
|
цикла. |
|
окончания |
|
|
|
В полуавтомат ческом режиме весь цикл приготовления разбивается |
|||
на несколько подц клов. Пуск работы каждого из |
подциклов |
осуществляетсябАоператором.
В ручном режиме управление процессом дозирования компонентов и работы смесителя ведется с пульта управления по информации ламп сигнализации, отражающихся на мнемосхеме и экране дисплея.
Дистанционный режим предназначен для выполнения пусконаладки и ведется с переносного пульта. Д
Подсистема конвейерной линии созревания бетонных массивов
КЛ 4x16 предназначена для полуавтоматической транспортировки технологических форм-тележек к месту выдержки. Управление КЛ 4x16 осуществляется оператором с пульта загрузки и выгрузки. Электрооборудование, осуществляющее приводИцепных транспортеров с цепным устройством, позволяет производить автоматическое вычисление мест установки тележек, необходимые блокировки, контролировать наполнение линий.
Готовые стеновые блоки пакетируют, стягивают упаковочной лентой и погрузчиком, а затем подают на склад готовой продукции.
Технологическая линия ПБЗ–120А состоит из крупных элементов полной заводской готовности, приспособленных для перевозки и монтажа. За счет этого срок строительно-монтажных и пусконаладочных работ сокращается до 2 – 3 месяцев. Линия может быть размещена в зданиях цехов заводов ЖБИ, ДСК, а также в бывших складских и гаражных отапливаемых помещениях с высотой до 3 м и шириной пролета не менее 12 м. Благодаря конвейерной схеме не требуется грузовых кранов.
139

Для изготовления пенобетона в условиях строительной площадки широко применяются мобильные установки.
Установка ПМБ с турбулентным баросмесителем предназначена для приготовления и транспортирования пенобетонных смесей на основе минеральных вяжущих и заполнителей, пенообразователя и воды для
С |
|
|
|
|
|
|
|
|
|
устройства монолитных массивов из пенобетона средней плотностью |
|||||||||
300 – 1000 кг/м3 [2]. Оборудование эксплуатируется непосредственно на |
|||||||||
стройплощадках и в стационарных условиях при положительных |
|||||||||
температурах не н |
же 15 °С. Установка может перевозиться на прицепе |
||||||||
легкового автомоб |
ля. |
|
|
|
|
|
|
|
|
|
ами |
|
|
|
|
|
|
||
|
Установка УПБ–300 |
предназначена для приготовления и |
|||||||
транспорт рован я |
неавтоклавного пенобетона. В комплектацию |
||||||||
установки входят гор зонтальный смеситель с циклоидом, героторный |
|||||||||
насос, пеногенератор, в |
росито, |
пульт управления. Установка может |
|||||||
|
избыточного |
|
|
|
|||||
применяться при температуре окружающей среды не ниже +5 °С. |
|||||||||
|
На установках МПБУ–1 и МПБУ–2 возможно приготовление |
||||||||
пенобетона двумя |
спосо |
|
: двухстадийным |
и одностадийным, в |
|||||
зависимости от того, какой плотности пенобетон необходимо получить. |
|||||||||
Отлич тельной |
осо енностью |
|
установки |
является |
отсутствие |
||||
|
|
А |
|
|
|||||
специального насоса для подачи готовой смеси. Выгрузка осуществляется |
|||||||||
при помощи |
|
давления воздуха 0,1 МПа, создаваемого в |
|||||||
камере смешивания (рис. 4.19 и 4.20). |
|
|
|
||||||
|
|
|
|
|
|
Д |
|
||
|
|
|
|
|
|
И |
|
||
|
Рис. 4.19. Установка МПБУ–1 |
|
Рис. 4.20. Установка МПБУ–2 |
У мобильной установки ПБУ–0,4 по производству монолитного пенобетона, производимой на ЗАО «Вентиляционном заводе Лиссант», объем смесителя составляет 0,4 м3, производительность пено-генератора – 350 л/мин, производительность по пенобетону – 1,8 м3/ч,
140