
- •ВВЕДЕНИЕ
- •Г Л А В А 1. КЛАССИФИКАЦИЯ, НОМЕНКЛАТУРА, ПРИНЦИПЫ СОЗДАНИЯ ТЕПЛОЗАЩИТНЫХ СТРУКТУР И СВОЙСТВА СЫРЬЕВЫХ МАТЕРИАЛОВ
- •1.1. Классификация строительных материалов из ячеистых бетонов
- •1.2. Номенклатура строительных материалов из ячеистых бетонов
- •1.3. Принципы создания эффективных теплозащитных структур
- •1.3.1. Основные понятия о теплопередаче
- •1.3.2. Технологические способы создания современных теплозащитных структур
- •1.3.3. Конструктивные способы создания современных теплозащитных структур
- •1.4. Сырьевые материалы и их свойства
- •1.4.2. Кремнеземистые компоненты
- •1.4.3. Газообразователи
- •1.4.4. Пенообразователи
- •1.4.5. Корректирующие добавки и вода затворения
- •1.4.6. Сырьевая база Омской области для производства ячеистых бетонов
- •1.5. Способы активации сырьевых материалов и смесей при получении эффективных ячеистых бетонов
- •Г Л А В А 2. ТЕХНОЛОГИИ ЭФФЕКТИВНЫХ СТРОИТЕЛЬНЫХ МАТЕРИАЛОВ И ИЗДЕЛИЙ ИЗ ПЕНОБЕТОНОВ
- •2.1. Теоретические основы поризации кремнеземвяжущей массы механическим способом
- •2.2. Технология строительных материалов и изделий из неавтоклавного пенобетона
- •2.2.1. Производство пенобетонных блоков «Сиблок»
- •2.2.2. Технология пенобетона «ВНИИстром»
- •2.2.4. Производство пенобетона на технологическом комплексе ПБК–Р
- •2.3. Технология получения автоклавного пенобетона
- •2.4. Производство пенобетона по технологии «Новостром»
- •2.5. Современные технологии производства строительных материалов и изделий из пенобетона
- •2.5.1. Производство двухслойных стеновых блоков из бетонов различной плотности
- •2.5.5. Производство пенобетона «Экстрапор»
- •2.5.6. Вакуум-формовальная технология ячеистых бетонов
- •2.5.7. Технология пенобетона способом «обжатие – релаксация»
- •2.5.9. Пенобетоны сухой минерализации
- •Г Л А В А 3. ТЕХНОЛОГИИ ЭФФЕКТИВНЫХ СТРОИТЕЛЬНЫХ МАТЕРИАЛОВ И ИЗДЕЛИЙ ИЗ ГАЗОБЕТОНА
- •3.1. Теоретические основы поризации массы химическим способом порообразования
- •3.2. Технологии газобетона неавтоклавного твердения
- •3.3. Технологии материалов и изделий из газобетона автоклавного твердения
- •3.3.1. Производство газобетонных изделий на новосибирском заводе «Сибит»
- •3.3.3. Технология газобетона на омском комбинате пористых материалов «Вармит»
- •3.5.1. Материалы и изделия переменной плотности
- •3.5.2. Производство газобетонных изделий способом автофреттажа
- •3.5.3. Способ получения эффективных изделий в закрытой форме
- •3.5.4. Производство сухих газобетонных смесей
- •4.1. Проектирование состава ячеистых бетонов
- •4.1.2. Расчет состава пеногазобетона
- •4.2. Расчет и подбор технологического оборудования
- •4.2.1. Расчет технологического оборудования
- •4.2.2. Технологическое оборудование
- •4.3.1. Способы снижения водопоглощения
- •4.3.2. Отделка поверхности изделий из ячеистого бетона
- •4.4. Реконструкция предприятий силикатных изделий
- •Библиографический список
Г Л А В А 3. ТЕХНОЛОГИИ ЭФФЕКТИВНЫХ СТРОИТЕЛЬНЫХ МАТЕРИАЛОВ И ИЗДЕЛИЙ ИЗ ГАЗОБЕТОНА
3.1. Теоретические основы поризации массы химическим способом порообразования
СибАДИ |
||||||
В технологии газобетонных изделий стадия формования является |
||||||
ответственной |
технологической |
операцией, |
предопределяющей |
|||
формирован е пор стой структуры материала. В процессе вспучивания и |
||||||
структурообразован я газобетонных смесей необходимо соблюдение |
||||||
принципа соответств я |
скоростей |
газовыделения |
и |
увеличения |
||
реолог ческ х |
свойств смеси. Лучшими условиями |
формирования |
||||
макроструктуры |
яче стого |
етона следует считать |
такие, |
при которых |
сроки окончан я акт вного вспучивания смеси совпадают с моментом оптимальных значен й пластическовязких характеристик или же должны заканч ваться несколько раньше, чем начнется ее схватывание [44].
В момент вспуч вания наблюдаются следующие процессы: химическ й – реакц я между газоо разователем и активно действующим на него компонентом; физический – расширение в массе микро- и макропор; физико-химический – изменение реологических свойств вспучивающейся массы, о ычно представляющей собой высококонцентрированную суспензию или о разовавшийся расплав, находящийся в пиропластическом состоянии. Взаимодействие между частицами алюминиевой пудры и гидрооксидом кальция идет с выделением водорода и появлением шестиводного алюмината кальция.
Механизм вспучивания массы заключается в следующем: после соприкосновения частицы алюминиевой пудры с гидрооксидом кальция в месте контакта при температуре более 30 начинает выделяться водород. В прилегающих к частице алюминиевой пудры микрозонах выделяющийся газ давит на вязкопластичную массу, но пока усилие, развиваемое газом, не превысит предельного напряжения сдвигу t0, масса не будет вспучиваться. После того как значение предельного напряжения сдвигу массы будет меньше усилия, равного 0,032 МПа, развиваемого газом, начинается вспучивание, продолжающееся до полного израсходования алюминиевой пудры. На всем протяжении процесса вспучивания масса должна иметь достаточную пластическую вязкость п, иначе выделяющийся водород будет прорываться и уходить из массы, в результате чего происходит осадка. Наиболее полное использование газообразователя достигается в том случае, если выделение газа заканчивается ранее потери массой надлежащей подвижности, т.е. ранее достижения определенных критических значений предельного напряжения сдвигу и пластической вязкости массы. По исследованиям А.Н. Попова и
76
М.И. Хигеровича, скорость и полнота протекания физико-химических процессов в основном определяются количеством и дисперсностью газообразователя; состоянием его поверхности; текучестью, вязкостью и температурой смеси; концентрацией водородных ионов (pH) среды; интенсивностью и порядком перемешивания компонентов смеси.
Управление составом газобетонной смеси и формированием структуры газобетона должно базироваться на следующих подходах: газобетонная смесь является объектом применения закона постоянства объемного фазового состава дисперсной системы; газобетонная смесь
СибАДИнаполнителей, вводимых в состав газобетонной смеси, должна быть равной или меньшей дисперсности цемента; устойчивость газобетонной смеси при ее поризации предопределяется вязкостью поровой суспензии и величиной поверхностного натяжения жидкой фазы; газовыделение в смеси должно сопровождаться увеличением реологических свойств смеси за счет увеличения числа адгезионных контактов и связей между отдельными частицами [65].
состоит |
з двух основных частей – грубодисперсного структурного |
|
каркаса |
поровой суспензии [43]. Первая |
часть представляет собой |
грубод сперсные компоненты газобетонной |
смеси – молотый песок, |
|
негидрат рованный цемент. Твердая фаза поровой суспензии представлена |
||
частицами |
с размером в 10 – 100 раз меньше, чем размер частиц |
структурного каркаса. Это двуводный гипс, частично гидратированный цемент, стаб л з рующ е до авки, гашеная известь. Устойчивость и
реолог ческ е свойства (вязкость, предельное напряжение сдвига) газобетонной смеси предопределяются количеством и качеством поровой суспенз ; д сперсность кварцевого песка, золы ТЭЦ или других
3.2. Технологии газобетона неавтоклавного твердения
Производство неавтоклавного ячеистого бетона получило развитие практически в 60-х гг. XX в. В первый период ячеистый бетон готовили на основе портландцемента с его расходом 350 – 500 кг/м3, а впоследствии были разработаны вяжущие на основе шлаков зол.
Газобетон неавтоклавного твердения, полученный на основе пылевидных песков, имеет повышенную прочность при изгибе. Отношение Rизг/Rсж составляет 0,24 – 0,32, в то время как у бесцементного автоклавного ячеистого бетона эта величина не превышает 0,2 [57].
Процесс изготовления газобетонных изделий из песка и цемента складывается из четырех основных технологических переделов: первый – получение тонкомолотой цементно-песчаной смеси; второй – приготовление газомассы; третий – формование изделий и четвертый – термовлажностная обработка последних. При изготовлении крупных
77
стеновых блоков высотой до 3 м, шириной до 1,5 м и толщиной до 0,4 м с армированием стальным каркасом необходимо прохождение всех четырех технологических переделов. В случае изготовления мелких стеновых камней возможно исключение первого передела. Это во многом зависит от дисперсности исходного песка и требуемой марки бетона по прочности.
В работе [66] приведены рецептурно-технологические параметры СибАДИполучения неавтоклавного шлакощелочного ячеистого бетона. Для его производства используются нейтральный доменный гранулированный шлак, золы ТЭС, песок щелочной затворитель – жидкое стекло. Средняя
плотность бетона равна 800 кг/м3, прочность при сжатии – 4,8 МПа. Интенс вное твердение смеси обеспечивается при соотношении песка
и шлака, равном 0,5. Сн жение силикатного модуля жидкого стекла с 2,0 до 1,85 повышает ж знеспосо ность ячеистобетонной смеси на 15 мин.
Изготовлен е стеновых локов осуществляется по виброрезательной технолог в формах с размерами массива до 3,1х1,25х0,6 м. Способ струнной разрезки принят с учетом особенностей начального структурообразован я в свежесформованных массивах при производстве изделий з неавтоклавного ячеистого бетона [67].
Во ВНИИжелезо етоне разра отана технология для изготовления стеновых блоков из неавтоклавного ячеистого бетона на конвейерной линии системы «Уни лок ВА–3» производительностью 40 – 50 тыс. м3 изделий в год [68]. Конвейерная линия размещается в 18-метровом пролете длиной 102 – 120 м, оснащенном мостовым краном грузоподъемностью 5 т. Неавтоклавный газозолобетон на основе золошлаковых смесей ТЭС имеет среднюю плотность D400 и D600 при величине теплопроводности 0,09 – 0,15 Вт/(м· С) и удовлетворяет требованиям ГОСТ 21520–89 для мелких стеновых блоков.
В работе [65] представлены две принципиально разные технологические схемы производства мелких стеновых блоков из ячеистого бетона, в частности газобетона. Одна схема предусматривает использование передвижного смесителя и расположение форм вдоль пути движения смесителя, а вторая – установку стационарного смесителя размещение форм на конвейере выдержки со стационарными постами сборки и разборки форм. Второе технологическое решение обеспечивает более высокий уровень механизации, снижает число крановых операций рассчитано на производство изделий объемом 40 – 50 тыс. м3 изделий в год.
Смесь готовится в смесителе (рис. 3.1), который перемещается к форме и заливает ее бетонной смесью. После набора бетоном распалубочной прочности форма раскрывается и поддон с массивом краном устанавливается на стол резательной машины. Борта освобождаемой формы очищают от остатков бетона. В форму
78
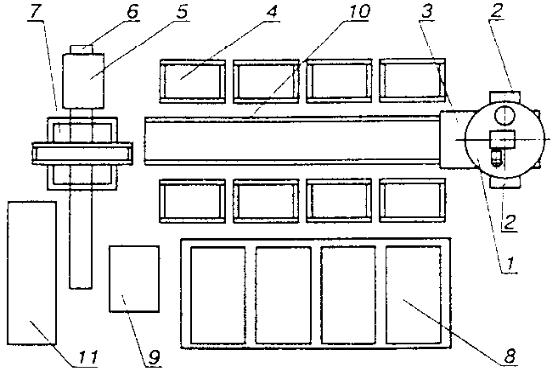
устанавливается поддон, борта закрывают, формы смазывают и направляют под заливку.
СибАДИРис. 3.1. Технологическая линия для производства мелких стеновых локов с передвижным смесителем:
1 – смеситель; 2 – заливочные течки; 3 – тележка перемещения смесителя; 4 – формы на позициях заливки и выдержки; 5 – поддон с массивом на приемной позиции резательного комплекса; 6 – конвейер подачи; 7 – машина продольнопоперечной резки; 8 – пропарочные камеры; 9 – пост складирования поддонов; 10 – пути перемещения смесителя; 11 – склад продукции
Массив на поддоне перемещается через резательную машину, разрезается, снимается краном и устанавливается для твердения.
Для проведения автоклавной обработки массив устанавливается на автоклавную тележку, а для пропарки – на стеллаж пропарочной камеры. После тепловлажностной обработки изделия снимаются захватом с технологического поддона отправляются на склад готовой продукции.
На конвейерной линии изготовления изделий из ячеистого бетона формы, установленные на двух ветвях конвейера выдержки, заливаются бетоном (рис. 3.2).
За время перемещения форм к постам распалубки бетон набирает необходимую для раскрытия бортов прочность. После раскрытия бортов поддон с массивом переносится манипулятором на резательную машину, а опалубка – на пост сборки форм. В опалубку устанавливается поддон, бор-
79
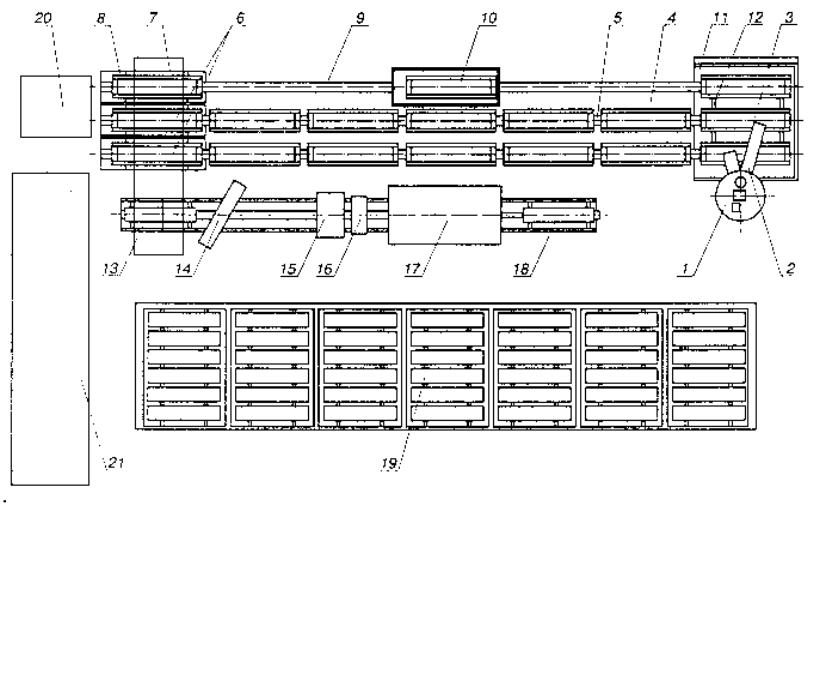
СибАДИРис. 3.2. Конвейерная линия производства мелких стеновых блоков со стационарным смесителем:
1 – смеситель; 2 – заливочные течки; 3 – формы под заливкой; 4 – формы на конвейере выдержки; 5 – конвейер выдержки; 6 – устройство для разборки форм; 7 – манипулятор переноса поддонов; 8 – форма на конвейере возврата; 9 – конвейер возврата; 10 – установка смазки форм; 11 – тележка подачи форм под заливку; 12 – пути перемещения тележки; 13 – каретка подачи массива на разрезку; 14 – установка снятия горбушки; 15 – установка горизонтальной резки; 16 – установка калибровки массива; 17 – установка поперечной резки; 18 – каретка вывоза разрезанного массива; 19 – пропарочные камеры; 20 – пост чистки и складирования поддонов; 21 – склад готовой продукции
80