
- •ВВЕДЕНИЕ
- •Г Л А В А 1. КЛАССИФИКАЦИЯ, НОМЕНКЛАТУРА, ПРИНЦИПЫ СОЗДАНИЯ ТЕПЛОЗАЩИТНЫХ СТРУКТУР И СВОЙСТВА СЫРЬЕВЫХ МАТЕРИАЛОВ
- •1.1. Классификация строительных материалов из ячеистых бетонов
- •1.2. Номенклатура строительных материалов из ячеистых бетонов
- •1.3. Принципы создания эффективных теплозащитных структур
- •1.3.1. Основные понятия о теплопередаче
- •1.3.2. Технологические способы создания современных теплозащитных структур
- •1.3.3. Конструктивные способы создания современных теплозащитных структур
- •1.4. Сырьевые материалы и их свойства
- •1.4.2. Кремнеземистые компоненты
- •1.4.3. Газообразователи
- •1.4.4. Пенообразователи
- •1.4.5. Корректирующие добавки и вода затворения
- •1.4.6. Сырьевая база Омской области для производства ячеистых бетонов
- •1.5. Способы активации сырьевых материалов и смесей при получении эффективных ячеистых бетонов
- •Г Л А В А 2. ТЕХНОЛОГИИ ЭФФЕКТИВНЫХ СТРОИТЕЛЬНЫХ МАТЕРИАЛОВ И ИЗДЕЛИЙ ИЗ ПЕНОБЕТОНОВ
- •2.1. Теоретические основы поризации кремнеземвяжущей массы механическим способом
- •2.2. Технология строительных материалов и изделий из неавтоклавного пенобетона
- •2.2.1. Производство пенобетонных блоков «Сиблок»
- •2.2.2. Технология пенобетона «ВНИИстром»
- •2.2.4. Производство пенобетона на технологическом комплексе ПБК–Р
- •2.3. Технология получения автоклавного пенобетона
- •2.4. Производство пенобетона по технологии «Новостром»
- •2.5. Современные технологии производства строительных материалов и изделий из пенобетона
- •2.5.1. Производство двухслойных стеновых блоков из бетонов различной плотности
- •2.5.5. Производство пенобетона «Экстрапор»
- •2.5.6. Вакуум-формовальная технология ячеистых бетонов
- •2.5.7. Технология пенобетона способом «обжатие – релаксация»
- •2.5.9. Пенобетоны сухой минерализации
- •Г Л А В А 3. ТЕХНОЛОГИИ ЭФФЕКТИВНЫХ СТРОИТЕЛЬНЫХ МАТЕРИАЛОВ И ИЗДЕЛИЙ ИЗ ГАЗОБЕТОНА
- •3.1. Теоретические основы поризации массы химическим способом порообразования
- •3.2. Технологии газобетона неавтоклавного твердения
- •3.3. Технологии материалов и изделий из газобетона автоклавного твердения
- •3.3.1. Производство газобетонных изделий на новосибирском заводе «Сибит»
- •3.3.3. Технология газобетона на омском комбинате пористых материалов «Вармит»
- •3.5.1. Материалы и изделия переменной плотности
- •3.5.2. Производство газобетонных изделий способом автофреттажа
- •3.5.3. Способ получения эффективных изделий в закрытой форме
- •3.5.4. Производство сухих газобетонных смесей
- •4.1. Проектирование состава ячеистых бетонов
- •4.1.2. Расчет состава пеногазобетона
- •4.2. Расчет и подбор технологического оборудования
- •4.2.1. Расчет технологического оборудования
- •4.2.2. Технологическое оборудование
- •4.3.1. Способы снижения водопоглощения
- •4.3.2. Отделка поверхности изделий из ячеистого бетона
- •4.4. Реконструкция предприятий силикатных изделий
- •Библиографический список
колодцевая кладка стен с последующей заливкой внутреннего слоя изоляционным бетоном особо малой плотности.
Второй класс (плотность 500 – 1200 кг/м3) – пенобетон, который целесообразно применять в стенах, состоящих из лицевого кирпича или другого стенового материала и внутреннего слоя из пенобетона. В этом варианте применяется съемная или несъемная опалубка для заливки
СибАДИпенобетонной смеси.
2.5. Современные технологии производства строительных материалов и изделий из пенобетона
Перспект вными способами повышения теплотехнических и эксплуатац онных характеристик стеновых изделий является получение двухслойных ограждающих конструкций с различной плотностью и прочностью по сечен ю, изготавливаемых в период их формования на технолог ческ х л н ях. Здесь можно выделить следующие направления: формирован е стеновых локов из бетонов различных групп и соответственно разл чной плотности; изготовление пенобетонных изделий с крупным пор стым заполнителем при регулировании плотности по сечению дифференцированным вибрированием; получение ячеистобетонных изделий с форсированным режимом порообразования [7].
2.5.1. Производство двухслойных стеновых блоков из бетонов различной плотности
В Самарской архитектурно-строительной академии были проведены исследования по созданию 2-слойных изделий при совмещении в них пенокерамзитобетона [54, 55].
Предлагаемая линия может быть привязана как цех действующего завода по производству сборного железобетона или автономное предприятие. Формование осуществляется «лицом вниз». Нижний несущий слой изготовляется из конструкционно-теплоизоляционного керамзитобе-тона (КБ), а верхний – из пенобетона (ПБ). Нижний слой формуется из керамзитобетонной смеси жесткостью 20 – 30 с, подвергается виброуплот-нению, при необходимости армируется, затем укладывается слой пенобетонной смеси. После схватывания цемента изделие подвергается пропариванию (рис. 2.15).
По такой технологии можно получать двухслойные стеновые материалы, обладающие мелкой равномерной пористостью и высокими эксплуатационными показателями (табл. 2.2). В процессе изготовления пенобетон, обладающий высокой подвижностью, проникает в поверхностные слои керамзитобетона на 1 – 2 см, что обеспечивает
59

|
образование |
«размытой» |
зоны контакта с улучшенным сцеплением. |
||||||||||||||||||||
|
При испытании образцов на предел прочности при сжатии отрыва слоев не |
||||||||||||||||||||||
|
происходит, а процесс разрушения аналогичен обычному пеноили |
||||||||||||||||||||||
|
керамзитобетону [55]. |
|
|
|
|
|
|
|
|
|
|
|
|
|
|
|
|
|
|
||||
СибАДИ3 |
|
|
|||||||||||||||||||||
7 |
|||||||||||||||||||||||
|
|
|
|
|
|
|
|
|
|
|
|
|
|
|
|
|
|
|
|
|
|
||
|
Рис. 2.15. Пр нц п альная технологическая схема производства |
|
|
|
|||||||||||||||||||
1, |
2, 3 |
|
многослойных стеновых блоков: |
|
|
|
|
|
|
|
|
|
|||||||||||
– расходные емкости цемента, |
керамзита различных фракций; |
|
|
|
|||||||||||||||||||
|
4 – объемно-весовые дозаторы; 5 – ленточный конвейер; 6 – дозатор для |
|
|
|
|||||||||||||||||||
|
воды; 7 – бетоносмеситель; 8 – етоноукладчик; 9 – виброплощадка; |
|
|
|
|||||||||||||||||||
|
10 – форма; 11, 12 – расходные емкости для пенообразователя |
стабилиза- |
|
|
|
||||||||||||||||||
|
тора пены; 13 – дозаторы; |
14 – пропеллерная мешалка; 15 – насос; 16, 17, |
|
|
|
||||||||||||||||||
|
18 – расходные емкости для цемента, порошкообразного наполнителя, |
|
|
|
|||||||||||||||||||
|
волокнистого наполнителя; 19 – дозаторы; 20 – ленточный конвейер; |
|
|
|
|||||||||||||||||||
|
21 – растворосмеситель; 22 – лопастной смеситель для приготовления |
|
|
|
|||||||||||||||||||
|
пенобетонной смеси |
|
|
|
|
|
|
|
|
|
|
|
|
|
|
Таблица 2.2 |
|||||||
|
|
|
|
|
|
|
|
|
|
|
|
|
|
|
|
|
|
|
|||||
|
|
|
Физико-механические показатели многослойных изделий |
|
|
|
|||||||||||||||||
|
|
|
|
|
|
|
|
|
|
|
|
|
|
|
|
|
|
|
|
|
|||
|
|
|
|
|
|
|
|
|
|
Эскиз конструкции |
|
|
|
|
|
|
|
|
|||||
|
Характеристика |
|
|
|
|
|
|
|
|
КБ |
|
|
КБ |
|
|
|
|
|
|||||
|
КБ |
|
|
|
КБ |
|
|
|
|
|
|||||||||||||
|
|
|
|
|
|
|
|
ПБ |
|
|
|||||||||||||
|
|
|
|
|
|
ПБ |
|
|
|||||||||||||||
|
|
|
|
|
|
|
|
|
|
|
ПБ |
|
|
|
|
|
|||||||
|
|
|
|
|
|
|
|
|
|
|
|
|
|
|
|
|
|
||||||
|
|
|
|
|
|
|
|
ПБ |
|
|
|
|
|||||||||||
|
|
|
|
|
|
|
|
|
|
|
|
|
|||||||||||
|
|
|
|
|
|
|
|
|
|
|
|
|
|
|
|
|
|
|
|
|
|||
1 |
|
|
2 |
|
3 |
|
|
|
4 |
|
|
5 |
|
|
|
|
6 |
|
|
||||
|
Средняя плотность, |
|
|
|
|
|
|
|
|
|
|
|
|
|
|
|
|
|
|
|
|||
|
кг/м (пропаренно- |
920 |
|
860 |
|
|
|
820 |
|
|
760 |
|
|
|
580 |
|
|
||||||
|
го) |
|
|
|
|
|
|
|
|
|
|
|
|
|
|
|
|
|
|
|
|
|
|
|
Водопоглощение |
16 |
|
17,7 |
|
|
|
19 |
|
|
20,3 |
|
|
|
21,5 |
|
|
||||||
|
(3 сут), % |
|
|
|
|
|
|
|
|
|
|
|
|
|
|||||||||
|
|
|
|
|
|
|
|
|
|
|
|
|
|
|
|
|
|
|
|
|
|
||
|
Объемная |
усадка, |
Отсутст- |
|
|
|
Отсутст- |
|
Отсутст- |
|
Отсутст- |
|
9,5 |
|
|
||||||||
|
% |
|
|
вует |
|
|
|
вует |
|
вует |
|
|
вует |
|
|
|
|||||||
|
|
|
|
|
|
|
|
|
|
|
|
|
|||||||||||
|
Прочность при сжа- |
16,5 |
|
7,7 |
|
|
|
11 |
|
|
11,8 |
|
|
|
5,9 |
|
|
||||||
|
тии, МПа |
|
|
|
|
|
|
|
|
|
|
|
|
|
|||||||||
|
|
|
|
|
|
|
|
|
|
|
|
|
|
|
|
|
|
|
|
|
|
60

Окончание табл. 2.2
|
1 |
2 |
3 |
4 |
5 |
6 |
Модуль |
сдвига, |
9851 |
8957 |
9623 |
8957 |
8514 |
МПа |
|
|||||
|
|
|
|
|
|
|
Модуль |
упругости, |
25500 |
24902 |
24519 |
22658 |
19159 |
МПа |
|
|||||
|
|
|
|
|
|
|
Расчетный коэффи- |
|
|
|
|
|
|
циент теплопровод- |
0,32 |
0,2 |
0,16 |
0,15 |
0,11 |
|
ности, Вт/(м С) |
|
|
|
|
|
СибАДИВозможность про зводства стеновых изделий из ячеистого бетона со средней плотностью 400 – 450 кг/м3 и менее является вполне реальной при разработке форсированных спосо ов поризации кремнеземвяжущей смеси с применением активных дисперсных минеральных наполнителей и мелких полиминеральных песков при меньших расходах порообразователей [11, 13, 14, 56, 57].
Про зводство 2-слойных ячеистобетонных изделий возможно также с использован ем крупного заполнителя, в качестве которого могут
использоваться гранул |
рованное пеностекло, вспученный перлит, а также |
легкие фракц керамз |
тового гравия. |
2.5.2. Про зводство ячеистобетонных изделий |
|
спосо ом форсированного порообразования |
Установлено, что при равноценных исходных составах смеси определяющими технологическими параметрами, влияющими на процесс поризации кремнеземвяжущего шлама, являются: а) при производстве газобетона: текучесть и температура шлама (40 – 45 С), скорость и продолжительность перемешивания, а также способ формования; б) при производстве пенобетона: устойчивость и кратность пен, способ подготовки пенобетонной массы.
При использовании традиционных технологий для получения ячеистых бетонов с величиной средней плотности менее 500 кг/м3 требуется значительный расход газообразователей (более 550 г/м3) и применение высокократных пен (более 10 единиц).
.В. Волженский в 80-х гг XX в. определил возможность получе-ния ячеистых бетонов, используя элементы технологии производства пено- и газобетона. Однако научно-технологических разработок по этому вопросу в последние годы практически не проводилось.
Авторы [10, 11, 12, 13, 14, 56] провели комплекс исследований по разработке рецептурно-технологических параметров производства пеногазобетона. Установлен оптимальный расход газообразователя для получения ячеистого бетона форсированным способом порообразования,
61
который находится в пределах 270 – 310 г/м3 пеногазобетона. При расходе 300 г средняя плотность пеногазобетона равна 414 кг/м3, предел прочности при сжатии – 1,3 МПа, что на 19,8 и 10,5% выше, чем соответственно при расходе 450 и 600 г алюминиевой пудры (табл. 2.3). При таких показателях порообразователей при общей пористости 81,3 – 82,8% достигается мелкая равномерно распределенная пористость в диапазоне радиусов пор
СибАДИ |
||||||||
|
0,0075 – 7,75 мкм. |
|
|
|
|
Таблица 2.3 |
||
|
|
Ф з ко-механические показатели ячеистых бетонов |
||||||
|
Вид |
Расход |
Кратность |
Средняя |
Прочность при |
ККК |
Общая |
|
|
бетона |
алюм н евой |
пены |
плотность, |
сжатии, МПа |
пористость, % |
|
|
|
пудры, г/м3 |
кг/м3 |
|
|
||||
|
Газобе- |
300 |
--- |
820 |
3,2 – 3,5 |
4,08 |
63,9 – 64,8 |
|
|
тон |
450 |
--- |
635 |
2,3 – 2,4 |
3,7 |
72 – 72,8 |
|
|
|
600 |
--- |
440 |
1,3 – 1,5 |
3,18 |
80,5 – 81,2 |
|
|
Пено- |
--- |
10 |
742 |
2,7 – 2,9 |
3,77 |
67,2 – 8,2 |
|
|
бетон |
--- |
15 |
590 |
1,7 – 1,9 |
3,05 |
74 – 74,6 |
|
|
|
--- |
20 |
430 |
1 – 1,1 |
2,44 |
80,9 – 81,7 |
|
|
Пено- |
300 |
10 |
414 |
1,2 – 1,4 |
3,14 |
81,3 – 82,8 |
|
|
газо- |
450 |
15 |
393 |
0,8 – 0,9 |
2,16 |
82,6 – 83,2 |
|
|
бетон |
600 |
20 |
385 |
0,1 – 0,14 |
0,31 |
82,8 – 83,7 |
|
С учетом последовательного использования в технологии пеногазобетона, пено- и газообразователей выполнена корректировка расхода порообразователей при расчете состава пеногазобетона. Установлено, что доля вклада механического способа порообразования в объем общей пористости пеногазобетона составляет 60 – 65%, а химического – 35 – 40% при оптимальных параметрах приготовления пеногазомассы.
Для технологического согласования процессов газовыделения и пенообразования определялась оптимальная температура воды затворения. Установлено, что оптимальной является температура воды затворения в интервале 21 – 25 . При повышении или снижении температуры у пеногазобетонных образцов наблюдается повышение величины средней плотности. Это объясняется тем, что при более низкой температуре воды процесс газообразования происходит значительно медленнее, в результате чего нарастание вязкопластичных свойств смеси происходит раньше, чем заканчивается газообразование. При более высокой температуре по отношению к оптимальной, наоборот, вспучивание смеси и образование горбушки происходит более интенсивно, вспучивание смеси начинается через 40 – 50 с, но при этом происходит разрушение технической пены.
62
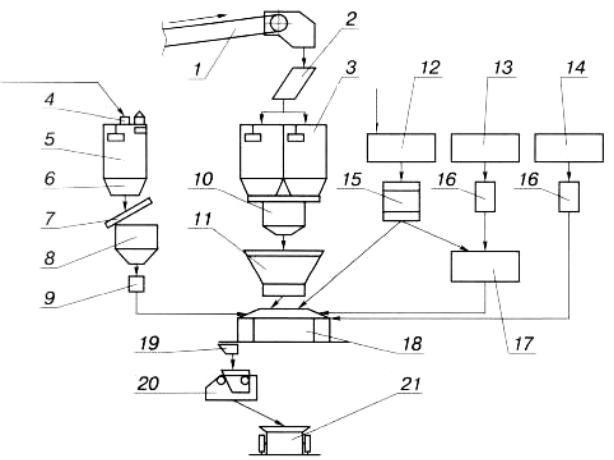
С учетом применения двухстадийной технологии приготовления ячеистобетонной смеси изучалось влияние технологической последовательности ее приготовления на свойства формовочной массы и пеногазобетона. Были рассмотрены следующие принципиально возможные варианты приготовления смеси: растворная смесь + Al-суспензия + пена; Al-суспензия + пена + растворная смесь; растворная смесь + пена + Al-
СибАДИсуспензия. Установлено, что оптимальной является схема: растворная смесь + пена + Al-суспензия. При такой технологии получен пеногазобетон со средней плотностью 410 кг/м3, что на 23 – 29% меньше, чем при других способах.
Цемент Вода
Рис. 2.16. Технологическая схема производства пеногазобетона:
1 – ленточный транспортер; 2 – загрузочная воронка; 3 – расходные бункера кремнеземистых компонентов смеси; 4 – фильтры; 5 – циклон; 6 – расходный бункер цемента; 7 – шнековый питатель; 8 – дозатор цемента; 9 – переходная воронка от дозатора цемента; 10 – дозатор кремнеземистого компонента; 11 – загрузочная воронка; 12 – емкость для воды; 13 – емкость для пенообразователя; 14 – емкость для алюминиевой суспензии; 15 – дозатор воды; 16 – дозаторы пенообразователя и алюминиевой суспензии; 17 – пеногенератор; 18 – бетоносмеситель принудительного действия; 19 – воронка выдачи пеногазобетона; 20 – бункер-накопитель; 21 – раздаточный бункер
63
Разработанная технология приготовления пеногазобетонной смеси, заключающаяся в перемешивании растворной части с технической пеной и дальнейшем перемешивании с алюминиевой суспензией, позволяет обеспечить высокий уровень общей и дифференциальной пористости и снизить при этом величину средней плотности пеногазобетона на 20 – 30%, теплопроводности – 40 – 48%, а усадку – 30 – 40% по сравнению
СибАДИ |
|
с другими способами приготовления кремнеземвяжущего шлама. |
|
Одним из перспективных направлений регулирования свойств |
|
поризованных шламов |
снижения величины средней плотности ячеистых |
бетонов является пр менение высокодисперсных минеральных и |
|
органом неральных |
наполнителей и стабилизаторов структурной |
прочности пор зованной массы, что позволяет получать пеногазобетон со средней плотностью 320 – 350 кг/м3 [7].
На базе экспер ментальных и теоретических положений разработана технолог ческая схема производства пеногазобетона, предусматривающая двухступенчатый способ подготовки пеногазобетонной смеси (рис. 2.16).
2.5.3. Про зводство пено етона способом одностадийного тур улентно-кавитационного перемешивания
Фирма «Фи ро етон» (Москва) разработала технологию и оборудование по производству высокоэффективных пенобетонов, используя способ одностадийного турбулентно-кавитационного перемешивания компонентов пенобетонной смеси [58].
Уникальность технологии состоит в возможности получения мелкодисперсной пористости с диаметром пор менее 0,8 мм. Процесс поризации осуществляется в турбулентно-кавитационном смесителе, снабженном специально разработанными лопастями минимального аэродинамического сопротивления, на концах которых расположены кавитационные насадки. Одностадийный процесс приготовления пенобетона включает в себя период гомогенизации при малых скоростях вращения вала, когда в емкость смесителя загружаются все компоненты пенобетонной смеси, период поризации при больших скоростях вращения вала.
Во время поризации за движущимися лопастями с кавитационными насадками образуются кавитационные каверны, давление в которых составляет 70 – 80% от атмосферного давления. Из-за разности давления происходит процесс засасывания воздуха с образованием и равномерным распределением по объему смеси мельчайших пузырьков воздуха, которые стабилизируются пенообразователем и армируются затем частицами цемента и песка. В процессе поризации пеномасса постепенно увеличивается в объеме и разгоняется, при этом уменьшается
64
относительная скорость прохождения лопастей через пеномассу. Для уменьшения этого эффекта на внутренней боковой поверхности емкости смесителя расположены кавитационные насадки, которые тормозят и поризуют смесь. В результате время поризации пеномассы объемом 0,5 м3 не превышает 1,5 мин. Критический размер пор 0,6 – 1 мм, уровень минерализации пен и величина давления внутри газовых пузырьков,
СибАДИ«Прогресс» в качестве пенообразователя.
которая обратно пропорциональна квадрату радиуса пузырька, обеспечивают высокую устойчивость пенобетонной смеси.
Такую смесь можно транспортировать автотранспортом до 30 км, перекач вать не только пневмонасосами, но и шнековыми насосами на 10-й этаж при скорости подачи 4 м3/ч, заливать за один прием в опалубку
слой пенобетона на всю высоту этажа. |
|
|
|
|
2.5.4. Про зводство пенобетона под давлением |
||
В |
научно-про зводственном |
предприятии |
«Помощник–Д» |
(г. Краснодар) разра отаны новая технология и установка непрерывного |
|||
приготовлен я пено етона под |
давлением с |
использованием |
|
«Суперм ксера СТ–10». Установка позволяет получать однородную массу |
пенобетона с минимально возможными размерами замкнутых пор, обеспечивающими нео ходимую среднюю плотность пенобетонной смеси при использовании лю ого доступного пенообразователя [3].
Использование «Супермиксера СТ–10» вместе с героторным растворонасосом тюменской домостроительной компанией позволило отказаться от дорогостоящего пенообразователя «Неопор» и получить
пенобетон |
с |
использованием |
отечественного |
пенообразователя |
«Пеностром» |
других [59, 60]. |
|
|
|
Технологическая линия на новороссийском заводе ЖБИ позволяет |
||||
выпускать |
пенобетонные изделия |
на синтетическом |
моющем средстве |
Технологическая схема приготовления пенобетонной смеси под давлением приведена на рис. 2.17, а пример ее приготовления в мультимедиа на сайте по адресу https://youtu.be/IxdoCXTd6j4.
Сущность технологии заключается в том, что исходная растворная смесь с помощью растворонасоса подается в высокоскоростной смеситель объемом 6 л, куда одновременно непрерывно подается пена. Смешение пены со смесью происходит под давлением в течение 1 – 2 с, после чего пенобетонная смесь по шлангу подается к месту укладки.
65
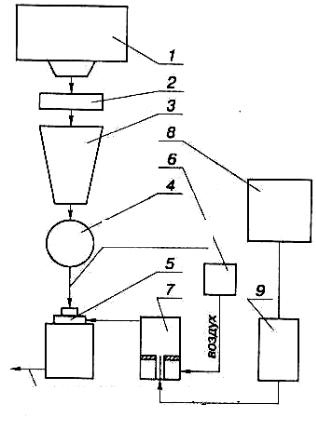
СибАДИ |
||||
Исходная смесь |
||||
|
Пена |
|
|
|
|
|
Воздух |
|
|
|
|
|
|
|
Пеноо разующая |
Раствор |
|||
смесь |
пенообразователя |
Рис. 2.17. Технология непрерывного приготовления пено етонной смеси под давлением:
1 – растворосмеситель; 2 – вибросито; 3 – бункер исходной смеси; 4 – растворонасос; 5 – стержневой смеситель; 6 – компрессор СО–7; 7 – пеногенератор; 8 – емкость раствора пенообразователя; 9 – насос
Величина давления, при котором готовится пенобетонная смесь, определяется сопротивлением ее движению в шланге и зависит от дальности и высоты подачи. При необходимости давление может поддерживаться постоянным. Пена также готовится непрерывно под давлением в высокоскоростном пеногенераторе объемом 4 л. Основу пеногенератора составляют: диск с капиллярно-пористой структурой ротор с пакетами щеток. Производительность «Супермиксера СТ–10» составляет не более 10 м3/ч, максимальное рабочее давление – не более 0,4 МПа, мощность электроприводов – 3,5 кВт, дальность подачи по горизонтали и вертикали соответственно составляет не более 100 и 50 м, габаритные размеры – 1200x650x1100 мм, масса – 150 кг, средняя плотность получаемых изделий – 300 – 1200 кг/м3.
Комплект оборудования включает: бетоносмеситель СБ–169 со скиповым подъемником; героторный растворонасос с приемным бункером; «Супермиксер СТ–10»; компрессор производительностью 12 м3/ч и
66