
- •ВВЕДЕНИЕ
- •Г Л А В А 1. КЛАССИФИКАЦИЯ, НОМЕНКЛАТУРА, ПРИНЦИПЫ СОЗДАНИЯ ТЕПЛОЗАЩИТНЫХ СТРУКТУР И СВОЙСТВА СЫРЬЕВЫХ МАТЕРИАЛОВ
- •1.1. Классификация строительных материалов из ячеистых бетонов
- •1.2. Номенклатура строительных материалов из ячеистых бетонов
- •1.3. Принципы создания эффективных теплозащитных структур
- •1.3.1. Основные понятия о теплопередаче
- •1.3.2. Технологические способы создания современных теплозащитных структур
- •1.3.3. Конструктивные способы создания современных теплозащитных структур
- •1.4. Сырьевые материалы и их свойства
- •1.4.2. Кремнеземистые компоненты
- •1.4.3. Газообразователи
- •1.4.4. Пенообразователи
- •1.4.5. Корректирующие добавки и вода затворения
- •1.4.6. Сырьевая база Омской области для производства ячеистых бетонов
- •1.5. Способы активации сырьевых материалов и смесей при получении эффективных ячеистых бетонов
- •Г Л А В А 2. ТЕХНОЛОГИИ ЭФФЕКТИВНЫХ СТРОИТЕЛЬНЫХ МАТЕРИАЛОВ И ИЗДЕЛИЙ ИЗ ПЕНОБЕТОНОВ
- •2.1. Теоретические основы поризации кремнеземвяжущей массы механическим способом
- •2.2. Технология строительных материалов и изделий из неавтоклавного пенобетона
- •2.2.1. Производство пенобетонных блоков «Сиблок»
- •2.2.2. Технология пенобетона «ВНИИстром»
- •2.2.4. Производство пенобетона на технологическом комплексе ПБК–Р
- •2.3. Технология получения автоклавного пенобетона
- •2.4. Производство пенобетона по технологии «Новостром»
- •2.5. Современные технологии производства строительных материалов и изделий из пенобетона
- •2.5.1. Производство двухслойных стеновых блоков из бетонов различной плотности
- •2.5.5. Производство пенобетона «Экстрапор»
- •2.5.6. Вакуум-формовальная технология ячеистых бетонов
- •2.5.7. Технология пенобетона способом «обжатие – релаксация»
- •2.5.9. Пенобетоны сухой минерализации
- •Г Л А В А 3. ТЕХНОЛОГИИ ЭФФЕКТИВНЫХ СТРОИТЕЛЬНЫХ МАТЕРИАЛОВ И ИЗДЕЛИЙ ИЗ ГАЗОБЕТОНА
- •3.1. Теоретические основы поризации массы химическим способом порообразования
- •3.2. Технологии газобетона неавтоклавного твердения
- •3.3. Технологии материалов и изделий из газобетона автоклавного твердения
- •3.3.1. Производство газобетонных изделий на новосибирском заводе «Сибит»
- •3.3.3. Технология газобетона на омском комбинате пористых материалов «Вармит»
- •3.5.1. Материалы и изделия переменной плотности
- •3.5.2. Производство газобетонных изделий способом автофреттажа
- •3.5.3. Способ получения эффективных изделий в закрытой форме
- •3.5.4. Производство сухих газобетонных смесей
- •4.1. Проектирование состава ячеистых бетонов
- •4.1.2. Расчет состава пеногазобетона
- •4.2. Расчет и подбор технологического оборудования
- •4.2.1. Расчет технологического оборудования
- •4.2.2. Технологическое оборудование
- •4.3.1. Способы снижения водопоглощения
- •4.3.2. Отделка поверхности изделий из ячеистого бетона
- •4.4. Реконструкция предприятий силикатных изделий
- •Библиографический список
перестройки поверхностного слоя жидкости повышается вязкость и механическое упрочнение пленки, окружающей пузырек воздуха. По мере насыщения адсорбционных слоев повышается стабильность пены. Таким образом, пенообразователи должны отвечать следующим требованиям: значительно снижать поверхностное натяжение воды; сохранять устойчивость; обеспечивать высокий показатель кратности; создавать
СибАДИвысокую дисперсность.
В значительной мере указанные свойства приобретают пены, образованные на с нтетических ПАВ. Из большого числа известных
химическ х реагентов в качестве сильных пенообразователей
рекомендуют к пр менению: терпинеолы (смеси ароматических спиртов); алкилсульфаты – RSO4Me; алкилсульфонаты – RSO3Me; алкиларилсульфо-
наты – RC6H5SO3Me.
целью повышен я структурной вязкости жидкости в пленках к ПО
добавляют загуст тели (полиакриломид, карбоксиметилцеллюлозу),
образующ е колло дные растворы. Назначение технических пен – удерживать част цы м нералов в дисперсной системе (пене) до конечного формирован я структуры готового материала (пенобетона).
М нерал зованная пенная суспензия является структурированной дисперсной системой, в которой возникает пространственный каркас из сцепленных между со ой частиц твердой фазы. Под воздействием внешних факторов (температура, время) между частицами возникают силы
различной природы, о еспечивающие прочность готового материала.
2.2. Технология строительных материалов и изделий из неавтоклавного пенобетона
2.2.1. Производство пенобетонных блоков «Сиблок»
Пенобетон в последнее время получил интенсивное развитие как в
нашей стране, так в развитых странах Запада. Преимущество
технологии – возможность использования в заводских условиях конвейерного и кассетного способов получения изделий, а также непосредственно в монолитном домостроении [46].
АО «Новостром» с участием специалистов УкрстромН проект, ХИСИ, НИИЦемент, МАДИ и других разработаны конвейерные технологические линии по производству пенобетонных блоков различных типоразмеров. Часовая производительность установок от 3 до 10 м3 бетона. Серийный выпуск линий организован на базе совместного предприятия «Сиблок» (г. Новороссийск) в виде комплектов высокой заводской готовности, что исключает дополнительную комплектацию на объектах.
42

Принципиальной особенностью линии «Сиблок» является то, что готовая пенобетонная смесь разливается в формы непрерывно движущегося конвейера (рис. 2.1).
СибАДИРис. 2.1. Механизированная линия «Сиблок»:
1 – формовочный конвейер; 2 – пенобетонный смеситель; 3 – дозатор; 4 – пеногенератор; 5, 6 – емкости вяжущего, заполнителя, воды и пенообразователя; 7 – сливная емкость; 8 – автомат-укладчик
За время движения на конвейере смесь схватывается и набирает прочность, достаточную для снятия блоков захватом-манипулятором. Эта основная особенность и определяет специальные требования к вяжущим
материалам, конец схватывания которых должен быть не более 30 мин.
Для получения изделий со средней плотностью 600 – 900 кг/м3 необходимо готовить формовочную смесь с отношением жидкой фазы к сухой смеси Ж/Т = 0,4 – 0,5, при этом водоцементное отношение (В/Ц)
составляет 0,8 выше. Применение в качестве вяжущих обычных
цементов исключается, так как при таких В/Ц конец схватывания достигается через 10 – 15 ч.
Установлено, что способностью, обеспечивающей короткие сроки схватывания при повышенных водотвердых отношениях (В/Т), обладают среднеосновные алюминаты кальция – минералы СА и С12А7 [47, 48].
43
По такому принципу специалистами ХИСИ и Южгипроцемента было предложено вяжущее БТВ–1, где в качестве алюминатной добавки используются обожженная алунитовая порода и каолин (Г.Г. Александров и др.). Аналогичное по механизму действия вяжущее разработано в МАДИ с использованием глиноземистого шлака (И.Б. Удачкин и др.).
В качестве пенообразователей в технологии «Сиблок» применяют
СибАДИтехнология и комплект о орудования для производства пенобетона [98]. На рис. 2.2 показана технологическая схема изготовления пенобетона.
водные растворы ПАВ на основе СДО (ТУ 13–0281078–02–93) или
«Поток–МЗ» (ТУ 38–507–63–98–90) с концентрациями 1 – 3%. Получена кратность пен с ш роким диапазоном от 5 до 20 и различной дисперсностью. Опт мальная кратность составила 10 – 16 с плотностью пен 70 – 100 кг/м3. Эффективность порообразования на низкократных пенах получалась больше, чем на пенах с высокой кратностью. Данное обстоятельство позвол ло существенно снизить В/Т кремнеземвяжущей смеси.
2.2.2. Технология пенобетона «ВНИИстром»
ВНИИстромом |
м. П.П. Будникова на |
основании научно- |
исследовательск х |
опытно-конструкторских |
работ разработана |
Эта установка позволяет получать конструктивно-теплоизоляционные стеновые блоки плотностью 500 – 700 кг/м3 и теплоизоляционные плиты плотностью 120 – 400 кг/м3. Можно также получать пенобетон для изготовления армированных плит перекрытия плотностью 800 – 1200 кг/м3. Для изготовления крупноразмерных изделий, например, стеновых панелей плотностью 700 – 800 кг/м3 и для использования пенобетона с такой же плотностью при монолитном строительстве для устранения повышенных усадочных явлений в состав пенобетона вводятся гранулы пенопорита, предварительно изготовленные из той же массы пенобетона.
Основными сырьевыми компонентами для изготовления пенобетона служат цемент, кварцевый песок и пенообразователь. В качестве наполнителя могут быть использованы карбонатные пески, получаемые при переработке горных пород, золошлаковые отходы тепловых электростанций другие подобные пески. Кроме того, в состав сырьевых компонентов могут быть введены различные красители для офактуривания стеновых изделий, ускорители твердения пенобетонной массы, пластификаторы и армирующие средства. В качестве пенообразователя могут быть использованы различные органические пенообразователи, получаемые на основании натурального протеина, и синтетические – при производстве моющих средств на различных химических комбинатах.
44

СибАДИ |
||||||||
|
Рис. 2.2. Технологическая схема изготовления пенобетона: |
|||||||
1 – приемный |
ункер песка; 2 – ленточный конвейер; 3 – склад цемента; |
|||||||
4 |
– |
мельница-смеситель стержневой; 5 – |
ленточный |
конвейер; |
||||
6 |
– |
ленточный питатель; 7 – |
емкость для воды затворения; |
|||||
8 |
– |
пеногенератор; |
9 – емкость |
раствора |
для |
пенообразователя; |
||
10 – пенобетоносмеситель; 11 – форма для изготовления плит |
||||||||
перекрытий; |
12 – |
конвейер для |
формования |
стеновых |
камней; |
13 – щитовая опалубка монолитного дома; 14 – насос; 15 – готовые стеновые блоки; 16 – готовые плиты перекрытий
Производство изделий из пенобетона можно организовать на действующих заводах ЖБИ и КПД. При этом используются существующие узлы приема, подачи дозирования вяжущих и заполнителей, пропарочные камеры парк форм после их модернизации. Для организации производства конструктивно-теплоизоляционных стеновых блоков плотностью 500 – 700 кг/м3 и мощностью 10 – 15 тыс. м3 в год требуется монтаж на существующих площадях пенобетонной установки, включающей стержневой смеситель, пеногенератор и пенобетоносмеситель.
Кассетную форму на 1 м3 (65 блоков размерами 398х198х188 мм) можно изготовлять на местах с использованием существующих парков
45

форм. В указанных кассетных формах также можно организовать изготовление пенобетонных теплоизоляционных плит плотностью 200 – 400 кг/м3. Возможна организация производства теплоизоляционных плит по резательной технологии. Разработаны проекты таких линий мощностью 20 и 40 тыс. м3 в год. Мультимедийный файл по производству неавтоклавных пенобетонных блоков представлен на сайте по адресу
СибАДИ |
|||
https://youtu.be/TPR4n |
uRnzg. |
|
|
|
2.2.3. Производство пенобетона на установке |
||
|
|
«Краснодарская ПБ–1» |
|
РНТЦ «Стройтехнология» совместно с кафедрой |
производства |
||
строительных |
здел й |
конструкций КубГТУ (г. Краснодар) разработаны |
|
стационарная |
мо |
льная технологические линии |
по выпуску |
пенобетонных |
здел й производительностью 8 – 20 тыс. м3 в год [49]. |
На установке «Краснодарская ПБ–1» изготовляются стеновые блоки с размерами 390x190x188 мм и средней плотностью до 900 кг/м3. Производ тельность установки составляет 5 м3/ч, установленная мощность – 12 кВт, о ъем одного замеса – 0,25 м3, габаритные размеры – не более 3000x2500x2500 мм, масса – не более 2500 кг.
Для изготовления пено етонных блоков в качестве вяжущего применяется портландцемент марки 500 и выше, а в качестве заполнителя немолотый кварцевый песок или зола-унос ТЭС. ля создания пористой структуры используется пенообразователь на основе вторичных алкилсульфатов натрия, выпускаемый на химическом заводе. В этом случае цементно-песчаный раствор получают в растворосмесителе, расположенном на БСУ завода, и транспортируют в формовочный цех. Отдозированная порция цементно-песчаного раствора загружается в бетоносмеситель принудительного действия, где она перемешивается с дополнительным количеством воды. Затем в пенобетоносмеситель с использованием датчика времени подают пену, полученную в пеногенераторе, смесь продолжают перемешивать до получения однородной ячеистобетонной смеси (рис. 2.3).
В пеногенераторе раствор пенообразователя и воздух от компрессора подаются в камеру предварительного смешивания перпендикулярно друг другу. В результате механического воздействия происходит предварительное усреднение этих двух потоков. При этом наблюдается интенсивное образование пеновоздушной смеси, которая направляется в основную часть аппарата, где происходит дробление пенных пузырьков и их стабилизация. На выходе из пеногенератора получается мелкодисперсная, однородная и устойчивая пена с плотностью 65 – 70 кг/м3, которая
46
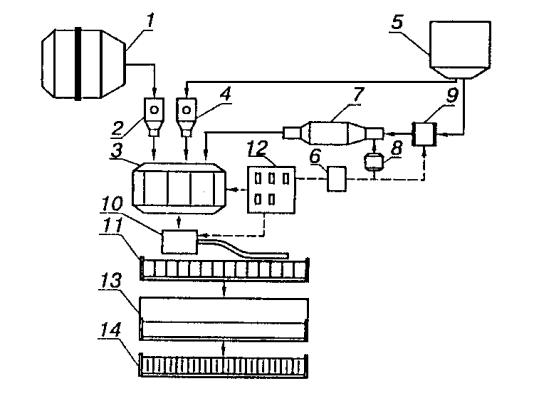
позволяет применять немолотый кварцевый песок, что существенно упрощает технологический процесс.
СибАДИРис. 2.3. Линия по производству пенобетонных блоков:
1 – растворосмеситель на БСУ; 2, 4 – дозаторы; 3 – пенобетоносмеситель; 5 – емкость для пенообразователя; 6 – датчик
времени; 7 – пеногенератор; 8 – компрессор; |
9 – насос; |
10 – винтовой насос; 11 – форма; 12 – пульт |
управления; |
13 – пост выдержки или ТВО; 14 – пост распалубки |
|
Готовая смесь с помощью винтового насоса разливается в формы, позволяющие производить распалубку поэтапно. Форма состоит из
поддона, бортов разделительных элементов для создания
формообразующих ячеек, причем один борт неподвижно закреплен на поддоне, а второй установлен с возможностью поворота относительно поддона. Ячеистобетонная смесь заливается без вибрации в ячейки с последующим разравниванием поверхности.
Формы, заполненные ячеистобетонной смесью, направляются в камеру тепловлажностной обработки или выдерживаются в естественных условиях. В последнем случае в состав массы вводится комплексная добавка-ускоритель твердения, благодаря которой изделия набирают распалубочную прочность в течение нескольких часов, в результате отпадает необходимость в затратах тепла на пропарку изделий.
47