
- •ВВЕДЕНИЕ
- •Г Л А В А 1. КЛАССИФИКАЦИЯ, НОМЕНКЛАТУРА, ПРИНЦИПЫ СОЗДАНИЯ ТЕПЛОЗАЩИТНЫХ СТРУКТУР И СВОЙСТВА СЫРЬЕВЫХ МАТЕРИАЛОВ
- •1.1. Классификация строительных материалов из ячеистых бетонов
- •1.2. Номенклатура строительных материалов из ячеистых бетонов
- •1.3. Принципы создания эффективных теплозащитных структур
- •1.3.1. Основные понятия о теплопередаче
- •1.3.2. Технологические способы создания современных теплозащитных структур
- •1.3.3. Конструктивные способы создания современных теплозащитных структур
- •1.4. Сырьевые материалы и их свойства
- •1.4.2. Кремнеземистые компоненты
- •1.4.3. Газообразователи
- •1.4.4. Пенообразователи
- •1.4.5. Корректирующие добавки и вода затворения
- •1.4.6. Сырьевая база Омской области для производства ячеистых бетонов
- •1.5. Способы активации сырьевых материалов и смесей при получении эффективных ячеистых бетонов
- •Г Л А В А 2. ТЕХНОЛОГИИ ЭФФЕКТИВНЫХ СТРОИТЕЛЬНЫХ МАТЕРИАЛОВ И ИЗДЕЛИЙ ИЗ ПЕНОБЕТОНОВ
- •2.1. Теоретические основы поризации кремнеземвяжущей массы механическим способом
- •2.2. Технология строительных материалов и изделий из неавтоклавного пенобетона
- •2.2.1. Производство пенобетонных блоков «Сиблок»
- •2.2.2. Технология пенобетона «ВНИИстром»
- •2.2.4. Производство пенобетона на технологическом комплексе ПБК–Р
- •2.3. Технология получения автоклавного пенобетона
- •2.4. Производство пенобетона по технологии «Новостром»
- •2.5. Современные технологии производства строительных материалов и изделий из пенобетона
- •2.5.1. Производство двухслойных стеновых блоков из бетонов различной плотности
- •2.5.5. Производство пенобетона «Экстрапор»
- •2.5.6. Вакуум-формовальная технология ячеистых бетонов
- •2.5.7. Технология пенобетона способом «обжатие – релаксация»
- •2.5.9. Пенобетоны сухой минерализации
- •Г Л А В А 3. ТЕХНОЛОГИИ ЭФФЕКТИВНЫХ СТРОИТЕЛЬНЫХ МАТЕРИАЛОВ И ИЗДЕЛИЙ ИЗ ГАЗОБЕТОНА
- •3.1. Теоретические основы поризации массы химическим способом порообразования
- •3.2. Технологии газобетона неавтоклавного твердения
- •3.3. Технологии материалов и изделий из газобетона автоклавного твердения
- •3.3.1. Производство газобетонных изделий на новосибирском заводе «Сибит»
- •3.3.3. Технология газобетона на омском комбинате пористых материалов «Вармит»
- •3.5.1. Материалы и изделия переменной плотности
- •3.5.2. Производство газобетонных изделий способом автофреттажа
- •3.5.3. Способ получения эффективных изделий в закрытой форме
- •3.5.4. Производство сухих газобетонных смесей
- •4.1. Проектирование состава ячеистых бетонов
- •4.1.2. Расчет состава пеногазобетона
- •4.2. Расчет и подбор технологического оборудования
- •4.2.1. Расчет технологического оборудования
- •4.2.2. Технологическое оборудование
- •4.3.1. Способы снижения водопоглощения
- •4.3.2. Отделка поверхности изделий из ячеистого бетона
- •4.4. Реконструкция предприятий силикатных изделий
- •Библиографический список
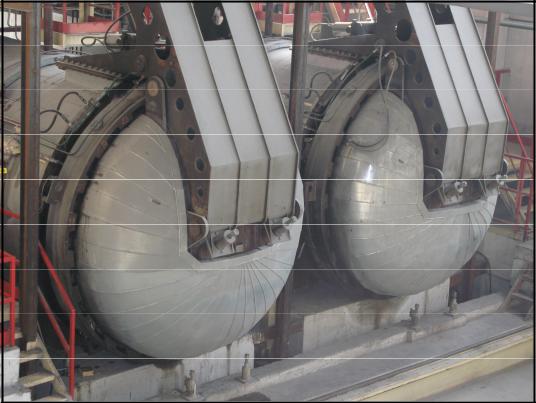
автоклаве пропаривается одновременно 15 вертикальных массивов общим объемом 64,8 м3.
СибАДИРис. 3.4. втоклавы
После автоклавирования изделия поступают на стационарную установку для разъединения слипшихся блоков, затем блоки объемом 0,72 м3 устанавливаются на деревянные поддоны размером 1000х600 мм и упаковываются в стрейч-пленку, а освободившиеся поддоны возвращаются по конвейеру возврата пустых поддонов в пролет заливки. Весь комплекс резательных машин и машин по разъединению, упаковке блоков обслуживают два человека.
На заводе выпускают стеновые блоки из газобетона со следующими характеристиками: плотность – 400 кг/м3, прочность при сжатии – 2 МПа, коэффициент теплопроводности в сухом состоянии – 0,087 Вт/(м ºС). Отклонения от заданных размеров, мм: по длине ширине – +3, по высоте – +2.
3.3.3. Технология газобетона на омском комбинате пористых материалов «Вармит»
На омском комбинате пористых материалов «Вармит», работающем по технологии фирмы «Верхан», производство газобетонных блоков осуществляется следующим образом. В стационарный газобетоносмеси-
87

|
|
|
тель (рис. 3.5) дозируют воду, затем |
||||||||||
|
|
||||||||||||
|
|
|
подают |
сыпучие |
материалы |
|
и |
||||||
|
|
|
компоненты, |
которые перемешиваются |
|||||||||
|
|
|
в течение 60 – 120 с (время |
||||||||||
|
|
|
отчитывается с момента начала подачи |
||||||||||
|
|
|
песчаной смеси в смеситель). После |
||||||||||
|
СибАДИ |
||||||||||||
|
|
|
этого |
из |
отделения приготовления |
||||||||
|
|
|
газообразователя (рис. 3.6) в смеситель |
||||||||||
|
|
|
подается алюминиевая паста «Газобето- |
||||||||||
|
|
|
лайт» и компоненты перемешиваются |
||||||||||
|
Рис. 3.5. Газобетоносмес тель |
|
ещё 40 – 60 с. |
|
|
|
|
|
|
|
|
||
|
|
|
|
Готовая |
газобетонная |
смесь |
с |
||||||
|
|
|
температурой 42 – 44 ºС через разда- |
||||||||||
|
|
|
точный рукав выгружается в форму, |
||||||||||
|
|
|
куда погружаются вибраторы и смесь |
||||||||||
|
|
|
вибрируется |
в |
течение |
60 – |
|
80 |
с |
||||
|
|
|
(рис. 3.7). Вибрационное воздействие |
||||||||||
|
|
|
вызывает |
тиксотропное |
разжижение |
||||||||
|
|
|
смеси, что интенсифицирует вспучива- |
||||||||||
|
|
|
ние массива и улучшает структуру |
||||||||||
|
|
|
формируемого газобетона. |
|
|
|
|
||||||
|
|
|
|
По |
окончании |
вибрирования |
|||||||
|
|
|
передаточный мост перемещает форму |
||||||||||
|
Рис. 3.6. Отделение приготовления |
|
|||||||||||
|
|
с газобетонной смесью в камеру |
|||||||||||
|
газообразователя |
|
|||||||||||
|
|
предварительной выдержки (рис. 3.8). |
|||||||||||
|
|
|
|||||||||||
|
|
|
Заняв требуемое положение напротив |
||||||||||
|
|
|
пустого места в камере предваритель- |
||||||||||
|
|
|
ного твердения, мост фиксируется |
||||||||||
|
|
|
двумя позиционерами. Далее захват |
||||||||||
|
|
|
поворачивается на 30º, и толкатель |
||||||||||
|
|
|
начинает перемещаться, зацепляя при |
||||||||||
|
|
|
этом |
форму |
|
выталкивая |
её |
в |
зону |
||||
|
|
|
предварительной выдержки. |
|
|
|
|
||||||
|
|
|
|
По истечении 180 – 200 мин |
|||||||||
|
|
|
предварительной выдержки при тем- |
||||||||||
|
|
|
пературе 30 – 35 ºС формы с изделием |
||||||||||
|
|
|
перемещаются |
к |
зоне |
раскрытия |
|||||||
|
|
|
бортов форм (рис. 3.9). Затем |
||||||||||
|
|
|
подъезжает толкатель формы и под- |
||||||||||
|
|
|
нимаются |
боковые |
торцевые |
опоры |
|||||||
|
|
|
|||||||||||
|
Рис. 3.7. Заливка смеси в формы |
|
узла |
открывания |
бортов, |
и |
|
борта |
|||||
|
и вибрирование |
|
фиксируются |
захватами. |
Оператор |
88
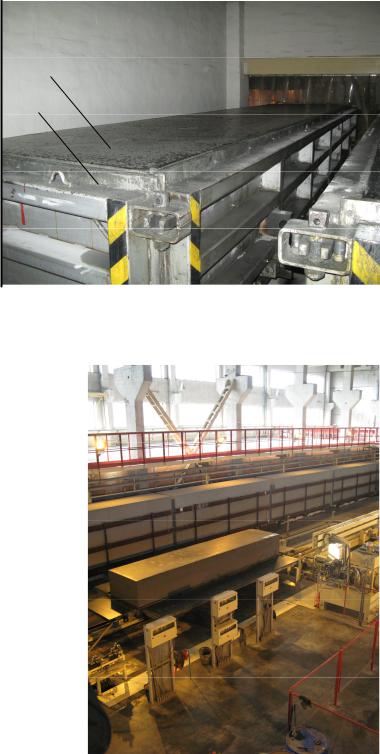
открывает |
замки формы. |
|
|
|
|
|
|||||||
Далее опускаются торце- |
|
|
|
|
|
||||||||
вые опоры, а вместе с |
|
|
|
|
|
||||||||
ними |
торцевые |
борта, |
|
|
2 |
|
|
||||||
затем боковые |
опоры |
и |
|
|
|
|
|||||||
соответствующие |
борта. |
|
|
1 |
|
|
|||||||
СибАДИ |
|
||||||||||||
Открывается позиционер, |
|
|
|
|
|
||||||||
и |
форма |
|
|
толкателем |
|
|
|
|
|
||||
выталк |
вается |
на |
уста- |
|
|
|
|
|
|||||
новку |
для |
кантован |
я, |
|
|
|
|
|
|||||
которая |
совершает |
пово- |
|
|
|
|
|
||||||
рот |
на |
90º, |
|
масс в |
по |
|
|
|
|
|
|||
транспортной |
|
|
с |
стеме |
|
|
|
|
|
||||
направляется |
на |
участок |
|
|
|
|
|
||||||
резки (р |
с. 3.10). |
|
|
|
|
|
Рис. 3.8. Камера предварительной выдержки: |
||||||
|
Резка |
масс |
ва |
осу- |
|
|
1 – форма; 2 – смесь в период вспучивания |
||||||
ществляется |
в |
автомати- |
|
|
|
|
|
||||||
ческом |
реж ме |
со |
скоростью |
|
|
||||||||
0,5 – 1 м/с |
|
|
контролируется |
|
|
||||||||
оператором с пульта управления. |
|
|
|||||||||||
Массив, перемещаясь по линии |
|
|
|||||||||||
резки, |
проходит |
через |
|
оковой |
|
|
|||||||
триммер, представляющий со ой |
|
|
|||||||||||
стойки с вертикально закреплен- |
|
|
|||||||||||
ными |
струнами |
и |
стальными |
|
|
||||||||
ножами, размещенными в опреде- |
|
|
|||||||||||
ленной |
последовательности. |
При |
|
|
|||||||||
прохождении массива через боко- |
|
|
|||||||||||
вой триммер происходит калибров- |
|
|
|||||||||||
ка ширины массива (624 ± 2 мм) и |
|
|
|||||||||||
нарезание |
пазогребневой |
системы |
|
|
|||||||||
(рис. 3.11). Отходы от резки |
|
|
|||||||||||
сбрасываются |
|
в |
емкость |
для |
|
|
|||||||
отходов (рис. 3.10) |
поступают в |
|
|
||||||||||
шламбассейн, в котором смешива- |
|
|
|||||||||||
ются с водой планетарными мешал- |
|
|
|||||||||||
ками |
до |
|
образования |
|
шлама |
Рис. 3.9. Пост распалубки изделия |
|||||||
(рис. 3.12). Плотность шлама |
|
|
|||||||||||
должна составлять 1,3 – 1,4 г/см3. |
|
|
|||||||||||
|
После этого боковой триммер смещается в сторону и его место |
||||||||||||
занимает установка резки по толщине. Вагонетка с массивом возвращается |
|||||||||||||
назад, |
проходя |
через |
установку |
резки по толщине. Струны с |
89
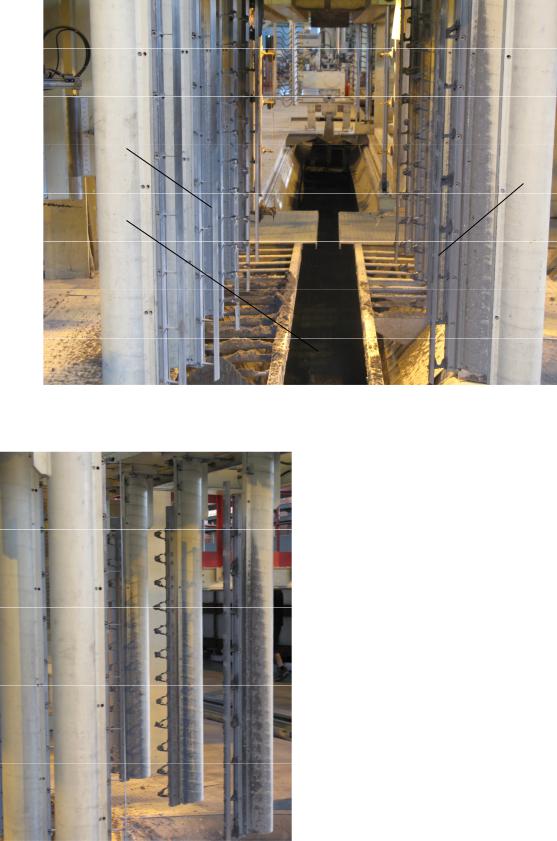
|
|
СибАДИ |
|
||||||
|
|
1 |
|
|
|
|
|
|
|
|
|
|
|
|
|
|
|
1 |
|
|
|
2 |
|
|
|
|
|
|
|
|
|
|
|
|
|
||||
|
|
Рис. 3.10. О щий вид резательного комплекса: |
|
|
|||||
|
1 – машина для устройства пазогре невой системы; 2 – емкость для отходов |
||||||||
|
|
|
пневмонатяжением, |
расположенные |
|||||
|
|
|
|||||||
|
|
|
на вертикальных |
стойках машины, |
|||||
|
|
|
режут |
массив на отдельные гори- |
|||||
|
|
|
зонтальные |
пласты |
и |
формируют |
|||
|
|
|
ширину блоков (рис. 3.13 и 3.14). |
||||||
|
|
|
При этом верхний и нижний пласты |
||||||
|
|
|
представляют собой срезку. Затем |
||||||
|
|
|
вагонетка с массивом подходит к |
||||||
|
|
|
машине поперечной резки и рама |
||||||
|
|
|
машины, на которой закреплен |
||||||
|
|
|
резательный |
|
|
фрезеровочный |
|||
|
|
|
механизм, |
начинает |
пошаговое |
||||
|
|
|
движение вниз (первый шаг соответ- |
||||||
|
|
|
ствует |
толщине |
|
горизонтального |
|||
|
|
|
пласта или ширине блока), а |
||||||
|
|
|
вакуумная площадка подводится к |
||||||
|
|
|
верхней части массива. При этом за |
||||||
|
|
|
счет |
возвратно-поступательного |
|||||
|
|
|
движения струн происходит разреза- |
||||||
|
Рис. 3.11. Устройство нарезания |
||||||||
|
ние пласта |
на |
отдельные блоки. |
||||||
|
|
пазогребневой системы |
Далее рама |
начинает |
подниматься |
||||
|
|
|
90
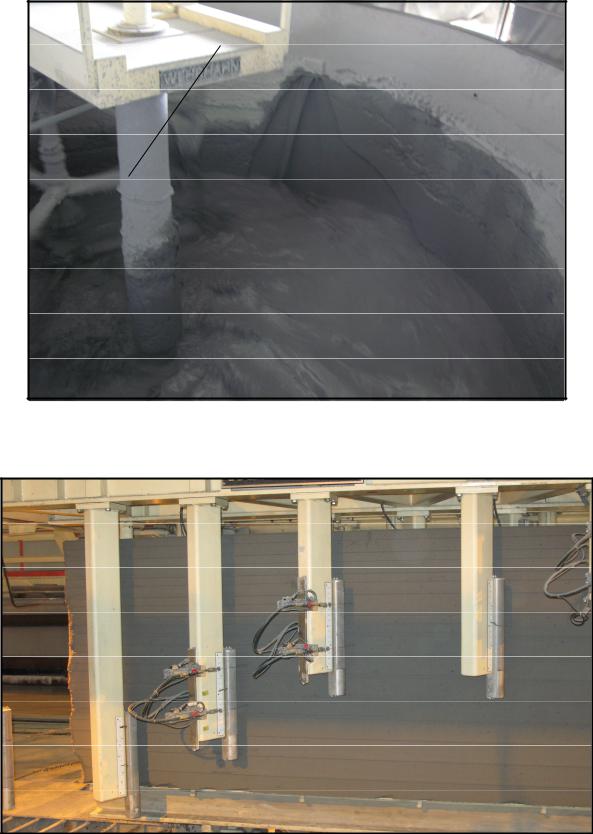
1
2
СибРис.АД3.12. Шламбассейн: И
1 – планетарный смеситель; 2 – шлам
Рис. 3.13. Газобетонный массив на продольной резке
91

1
СибАДИ |
||||
|
|
2 |
|
|
|
Р с. 3.14. Струны продольной резки: |
|
||
|
1 – вертикальные стойки; 2 – струны |
|
||
|
|
вверх. Дойдя до уровня вакуумной |
||
|
|
площадки, рама останавливается. |
||
|
|
Включается |
центробежный |
венти- |
|
|
лятор, за счет которого создается |
||
|
|
разряжение |
верхняя |
срезка, |
|
|
образовавшаяся в ходе горизонталь- |
||
|
|
ной резки, присасывается к вакуум- |
||
|
|
ной площадке. Затем рама машины |
||
|
|
вместе с вакуумной площадкой под- |
||
|
|
нимаются в исходное положение. |
||
|
|
После этого вагонетка проходит |
||
|
|
через обдувочную арку, где сжатым |
||
|
|
воздухом удаляются отходы резки, а |
||
|
|
нарезанный |
на блоки |
массив |
|
|
захватывается машиной для кантова- |
||
|
|
ния, опрокидывается в горизонталь- |
||
|
|
ное положение, укладывается на |
||
|
|
передаточную |
вагонетку и |
изделия |
|
|
загружаются в автоклав (рис. 3.4). |
||
|
|
|||
|
Рис. 3.15. Пост упаковки изделий |
После тепловой обработки ваго- |
||
|
|
нетка с готовым массивом выталки- |
вается на рельсовый путь и приводимой в действие лебедкой перемещается в зону разгрузки, откуда готовая продукция забирается автопогрузчиком,
92
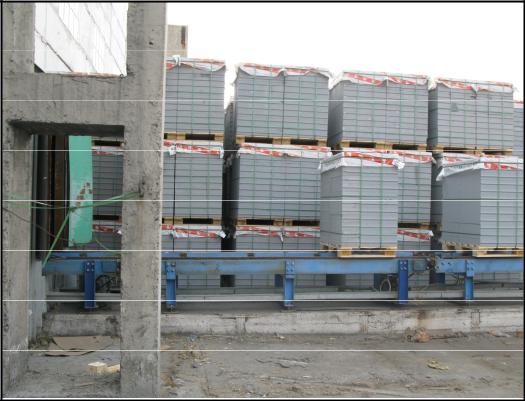
оборудованным поворотным захватным устройством, и перевозится на упаковочную линию (рис. 3.15). С помощью укладчика на поддоны надевается полиэтиленовый лист размером 1150x1620 мм, толщиной 120 мкм. Далее машина горизонтальной обвязки осуществляет стягивание полиэстеровой лентой верхнего, среднего и нижнего горизонтального рядов блоков, а машина вертикальной обвязки – два вертикальных ряда.
СибАДИУпакованные поддоны с продукцией по роликовому транспортеру выходят из цеха. В зоне разгрузки поддоны снимаются автопогрузчиком и перемещаются на склад готовой продукции. Размещение продукции производ тся в соответствии с ГОСТ 21520 по стопкам в 3 яруса по видам парт ям (р с. 3.16).
Рис. 3.16. Склад готовой продукции
На заводе выпускают газобетонные пазогребневые блоки следующих размеров, мм: 625x250x100, 625x250x200, 625x250x300, 625x250x400.
Средняя плотность блоков составляет 500 кг/м3, класс по прочности В2,5, марка по морозостойкости F50, теплопроводность – 0,12 Вт/м С, отпускная влажность не более 35%, паропроницаемость – 0,17 мг/м ч Па.
Пример производства автоклавных газобетонных блоков на омском комбинате пористых материалов «Вармит» приведен в мультимедийном файле по адресу https://youtu.be/S9mpk8eupwo, а свойства газобетона по адресу https://youtu.be/IaPHBUCD6bo.
93
3.4.Строительные материалы и изделия из автоклавного
инеавтоклавного газозолобетона
Газозолобетон представляет собой цементно-зольную смесь, в которой соотношение кремнеземистого компонента и вяжущего находится в пределах 1,8 – 2,2. При этом предпочтительнее полностью цементное
СибАДИ |
|
вяжущее (добавка извести может составлять 15 – 20%) [71]. |
|
Значительный опыт производства и применения изделий из |
|
неавтоклавного |
автоклавного газозолобетона имеется на Урале |
[72, 73, 74, 75]. |
|
УралпромстройНИИпроект и объединение «Агропромсельстрой» опробовали газозолобетон для строительства одноэтажных коттеджей при монолитном бетон ровании стен. Был предложен базовый состав газозолобетона плотностью 800 кг/м3 и прочностью 3,5 МПа, который был использован при стро тельстве дома. Расход материалов, кг/м3: цемента – 220 – 250; золы-уноса – 450 – 480; извести – до 30; алюминиевой пудры – 0,6 – 0,85; воды – 340 – 360. В доме с газозолобетонными стенами
дефектов, |
которые |
ы свидетельствовали |
о недостаточности |
теплозащ тных качеств ограждения, не обнаружено. |
|
В настоящее время акционерным обществом «Бетфор» выпускается полный комплект одно- и двухмодульных наружных стеновых панелей из газозолобетона для жилых домов серии 141–СВ. Толщина панелей – 280 мм при средней плотности 600 кг/м3 и расчетном коэффициенте теплопроводности для зоны 0,23 Вт/(м С) [75].
Дальнейшая задача в решении проблемы выпуска деталей для строительства коттеджей из газозолобетона – это освоение производства перегородочных и теплоизоляционных плит, причем последние должны иметь плотность 300 кг/м3.
Мелкоштучные изделия из газозолобетона производят следующим образом. Портландцемент и известь доставляются железнодорожным транспортом хранятся на складе. Зола-унос подается в силосный склад пневмотранспортом из автоцементовоза. Комовая известь дробится в щековой дробилке и затем размалывается в шаровой мельнице совместно с золой в соотношении известь:зола = 5:1. Тонкость помола извести должна составлять 5000 см2/г. Алюминиевая пудра или паста поступает в упаковке завода-изготовителя, рабочая алюминиевая суспензия готовится в цехе газозолобетона (рис. 3.17) [41].
В дозировочном отделении установлены расходные бункеры для сыпучих компонентов и расходные баки для воды, шлама и алюминиевой суспензии. Дозирование сухих материалов производится весовыми автоматическими дозаторами, дозирование воды, алюминиевой суспензии, шлама – объемными, в виде мерных бачков с кранами.
94

СибАДИПереработка отходов
Рис. 3.17. Принципиальная схема производства стеновых блоков из газозолобетона
95
Смесь газозолобетона приготавливается в смесителе объемом 1,8 м3. Последовательность загрузки материалов в смеситель должна осуществляться в следующем порядке: шлам отходов резки; вода; золаунос; портландцемент; золоизвестковое вяжущее; водно-алюминиевая суспензия. Продолжительность перемешивания компонентов смеси в смесителе следующая: сухие составляющие с водой – до 3 мин, потом
СибАДИдобавляется водно-алюминиевая суспензия и перемешивание продолжается в течение 1 – 1,5 мин.
В формовочном отделении ячеистобетонные массивы формуют по литьевой, ударной ли вибротехнологии. Для обеспечения прочности сырца, требуемой для резки массивов на изделия, залитые массивы предвар тельно выдерж вают при температуре не ниже +15 С в течение 3 ч. Затем спец альным захватом или по конвейеру подаются на резательную установку ез ортоснастки.
Резательной установкой производятся следующие операции: удаление горбушки с помощью конусной фрезы; продольно-горизонтальная разрезка массива; поперечная разрезка на локи. Разрезанный массив на поддоне транспорт руется на пост комплектации автоклавных тележек или пропарочную камеру. Отходы, получаемые от срезки, возвращаются в процесс производства или же после тепловлажностной обработки могут использоваться в качестве утеплителя потолочных перекрытий зданий.
Тепловлажностная о ра отка изделий производится в тупиковых или сквозных автоклавах, может также в пропарочных камерах. После автоклавирования или пропаривания готовая продукция поступает на склад.
Морозостойкость зависит от особенностей поровой структуры бетона. Равномерное распределение пор, уменьшение капиллярной пористости способствуют увеличению морозостойкости. Бетоны на цементе обладают большей морозостойкостью, чем на извести. ля снижения водопоглощения и повышения морозостойкости в ячеистой структуре желательно создание преимущественно замкнутых пор. Этому способствует вибрационная технология, позволяющая повысить однородность материала, разрушить крупные поры, снижающие морозостойкость.
Теплопроводность ячеистых бетонов зависит в основном от плотности и влажности. У бетонов со средней плотностью до 200 кг/м3 коэффициент теплопроводности составляет 0,065 – 0,07 Вт/(м º ), а у бетонов с плотностью 1000 кг/м3 – 0,21 – 0,26 Вт/(м ºС). Увеличение теплопроводности на каждый процент влажности примерно равно 7 – 8,5%. Для ячеистых бетонов характерны высокие звукоизоляционные свойства. По мере повышения плотности звукоизоляционная способность снижается [41].
Примерная схема генплана по производству мелких стеновых блоков из газозолобетона показана на рис. 3.18, а их сравнительные физикомеханические показатели – в табл. 3.2.
96
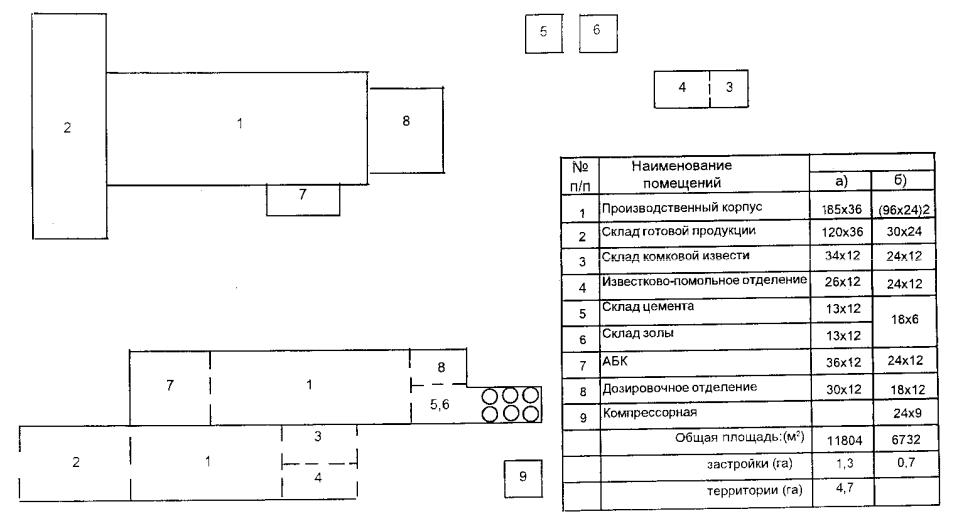
СибАДИРис. 3.18. Схема генпланаба по производству мелких стеновых блоков из автоклавного газозолобетона мощностью:
а – 100 тыс. м3/год, рефтинская ГРЭС Свердловской области;
– 20 тыс. м3/год, омская ТЭЦ–4
97
|
|
Таблица 3.2 |
|
Сравнительные физико-механические показатели газозолобетонов |
|||
|
|
|
|
Показатель |
Неавтоклавный |
Автоклавный |
|
Класс бетона по прочности на сжатие |
В 2,5 / М 35 |
В 2,5 / М 35 |
|
Марка бетона по средней плотности |
D 750 |
D 600 |
|
Марка по морозостойкости, не менее |
F 25 |
F 25 |
|
Коэффициент теплопроводности, Вт/(м ºС), не |
0,32 |
0,14 |
|
более |
|
||
|
|
|
|
Отпускная влажность, % по массе, не более |
35 |
35 |
|
Масса одного блока, кг, не более |
24 |
18 |
|
Размеры пл т перекрыт я, мм |
--- |
4200x1200x240 |
|
3200x1200x240 |
|
||
|
|
|
|
Размеры блока, мм |
200x300x400 |
188x300x588 |
|
Про зводство неавтоклавного газозолобетона |
|||
на основе золы сухого отбора омской ТЭЦ–4 |
|||
Про зводство неавтоклавного газозолобетона на основе золы сухого |
отбора омской ТЭЦ–4 осуществляется следующим образом. Дозирование цемента, золы воды производят весовыми автоматическими дозаторами (рис. 3.19) [41].
Алюминиевую суспензию готовят из расчета на суточную потребность работы производства. Щелочной компонент готовится в виде водного раствора и подается в мешалку вместе с водой затворения.
Приготовление газозолобетонной смеси производится в смесителе принудительного действия СБ–138. Последовательность загрузки сырьевых материалов в смеситель должна быть следующей: подается цемент и зола, после чего компоненты перемешиваются в течение 2 – 3 мин, потом смесь перемешивается с водой и щелочным раствором в течение 1 – 2 мин, затем с газообразователем. Общая продолжительность перемешивания смеси – около 5 мин. Готовая смесь выгружается в
самоходную тележку |
далее в форму. При этом необходимо учитывать, |
|
что перерыв между укладкой первой и последней порциями бетона не |
||
должен превышать 20 мин во избежание расслоения бетона в изделии. |
||
Бетонная смесь укладывается в форму на высоту, примерно равную 3/4 или |
||
СибАДИ4/5 высоты бортов. При изготовлении опытной партии панелей высота |
||
заливки смеси уточняется. |
|
|
Формирование изделий производится на вибростоле. Крупноразмер- |
||
ные армированные конструкции рекомендуется формировать из смеси с |
||
повышенной жесткостью с применением импульсного или прерывистого |
||
вибрирования, т.е. смесь подвергается вибровоздействиям |
в течение |
|
10 – 15 с через 1 – 2 |
мин, весь период вибровоздействий |
составляет |
5 – 10 мин, что ускоряет процесс вспучивания жесткой смеси.
98
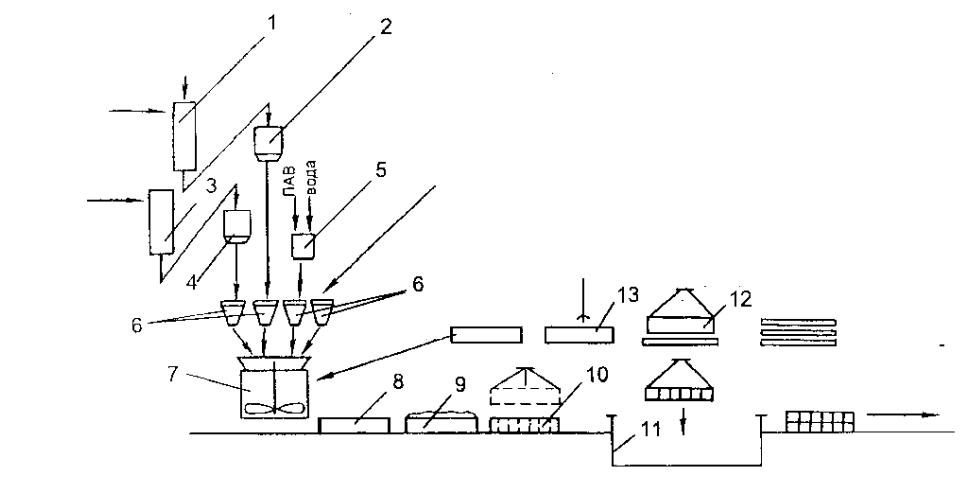
СибАДИ |
||||
Подача золы |
или |
|
|
|
цемента авто |
- и |
|
|
|
железнодорожным |
|
Вода |
Подача щелочной добавки |
|
транспортом |
|
|
|
|
|
|
Вода |
|
Смазка |
Сборка форм
Поддоны
На заливку
На склад
Рис. 3.19. Технологическая схема производства мелких блоков из неавтоклавного газозолобетона:
1 – склад цемента; 2 – расходный бункер цемента; 3 – склад золы; 4 – расходный бункер золы; 5 – смеситель алюминиевой суспензии; 6 – дозаторы; 7 – смеситель; 8 – пост заливки; 9 – пост вызревания массива; 10 – пост снятия бортов с разрезкой массива; 11 – камера пропаривания; 12 – пост чистки сборки форм; 13 – пост смазки форм
99