
1798
.pdf
81
4. Выбираем передаточное отношение зубчатой передачи u23 = 4 и определяем передаточное отношение ременной передачи
u12 u13 18,98 4,75.
u23 4
5. Определяем частоту вращения 2- го вала:
n2 n3 n23 38,2 4 152,8об/мин. 6. Находим крутящие моменты на валах:
M |
1 |
|
N1 |
|
9,55N1 |
|
9,55 7,5 |
0,099 кН м = 99 Н м; |
|
n |
|
||||||
|
|
|
725 |
|
||||
|
|
1 |
1 |
|
|
|
M2 M1 u12 рп 99 4,75 0,95 447Н м = 0,45 кН м;
M3 M1 u13 99 18,98 0,92 1729Н м = 1,73 кН м.
Тали представляют собой простые по устройству и небольшие по размерам грузоподъёмные машины. Их используют для подъёма грузов, от 0,25 до 8 т, при монтаже и ремонте автомобилей, станков, других машин и оборудования, а также на различных вспомогательных работах, сопровождаемых подъёмом грузов, узлов машин, при складских работах и т.д. В зависимости от привода тали разделяют на ручные и электрические.
Ручные тали бывают: подвесные с червячным подъёмным механизмом и передвижные тали, которые могут передвигаться по монорельсу.
Электрические тали изготавливают в виде самостоятельных машин, предназначенных для подъёма или подъёма и горизонтального перемещения, или в виде механизмов в составе однобалочных мостовых, козловых, консольных кранов. Электрическая таль (рис. 4.3) состоит из барабана 2, на который навивается канат 3 для подъёма груза 4 (груз зацепляется с помощью крюка 5), барабан приводится во вращение от электродвигателя 7 через зубчатую передачу Z1...Z4. В электрических талях для согласования высокой скорости электродвигателя с низкой частотой вращения барабана (nэ= 1460 об/мин; n6 = 8 об/мин) , а также с целью обеспечения самоторможения, т.е. удерживания поднимаемого груза при остановке электродвигателя, кроме зубчатых передач вводится червячная передача. Для горизонтального перемещения барабан с электрическим приводом монтируется на тележке, которая с помощью колёс перемещается по монорельсу, т.е. по нижнему поясу двутавровой балки. Для повышения грузоподъёмности и снижения скорости подъёма в два раза крюк не прицепляют к концу каната, а подвешивают на подвижном блоке (рис. 4.10).
Расчёт тали аналогичен расчёту лебёдки.
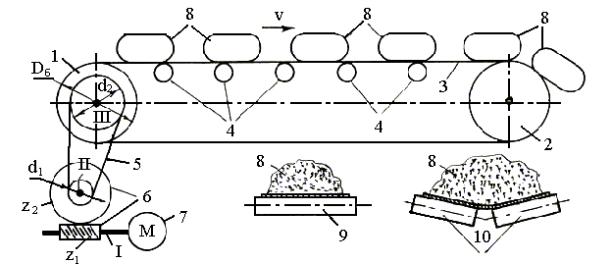
82
6.2. Ленточный транспортёр
Ленточный транспортёр, или конвейер, – это транспортная машина, которая предназначена для непрерывного перемещения твёрдых и сыпучих тел на сравнительно небольшое расстояние. Например, сыпучий груз (зерно) доставляют на погрузочно-разгрузочную площадку, а затем с помощью ленточного конвейера транспортируют его внутрь склада. С помощью ленточного конвейера можно транспортировать сыпучий груз в мешках, овощи в ящиках и т.д. Обладая малыми габаритными размерами, небольшой мощностью приводного двигателя и высокой надёжностью, ленточные конвейеры получили широкое применение в сельском хозяйстве, промышленности, горнодобывающей сфере, в складском хозяйстве и т.д.
Рис.6.2
Ленточный транспортёр состоит из следующих основных частей: 1–
ведущий барабан; 2–ведомый барабан; 3 – прорезиненная лента; 4 – поддерживающие ролики; 5 – ременная или цепная передача; 6 – червячная передача; 7 – приводной электродвигатель; 8 – транспортируемый груз.
Ведущий барабан 1 получает вращение от приводного двигателя 7 через передачи 5 и 6. Прорезиненная широкая лента 3 охватывает ведущий 1 и ведомый 2 барабаны. Верхняя ветвь ленты поддерживается роликами 4 по всей длине. Ролики 4 могут быть горизонтальными 9 и V - образными 10. Груз 8 кладут на верхнюю ветвь ленты 3, которая непрерывно движется со скоростью v. В конце транспортёра груз 8 либо подхватывается рабочим, либо падает в приёмник, а если это сыпучая масса (песок), то она сыплется в приёмную тару или на пол в кучу.
Ленточные стационарные конвейеры и переносные конвейеры изготавливают в виде самостоятельных машин. Основные технические данные ленточных стационарных конвейеров общего назначения с
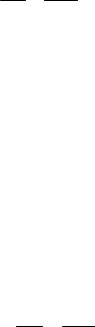
83
прорезиненной лентой: ширина ленты b = 400...1600 мм, диаметр приводного барабана db= 250...1600 мм , скорость движения ленты v= 0,6...3 м/с, расчётная производительность конвейера при горизонтальных поддерживающих роликах 9 (рис. 6.2) и плоской ленте Q = 15...1200 м3/ч, при V-образных поддерживающих роликах и желобчатой ленте Q =
25...2500 м3/ч.
Кинематический и силовой расчёты ленточного транспортёра разберём на примере. Окружное усилие на ведущем барабане (тяговая сила ленты) F=5 кН, окружная скорость барабана или скорость ленты v =0.25 м/с, диаметр барабана D6=250 мм. Произвести кинематический и силовой расчёты.
Ре ш е н и е
1.Определяем общий КПД привода транспортёра, если КПД ременной передачи рn =0,95 , а КПД червячной передачи чп= 0,6.
рn чп 0,95 0,6 0,57.
2.Определяем мощность электродвигателя. Полезная мощность транспортёра (на III валу барабана)
N3 F v 5 0.25 1.25кВт.
Мощность на валу электродвигателя
N1 N3 1,25 2,19 кВт.0,57
3. По таблицам выбираем асинхронный электродвигатель мощностью Nэ 2,2 кВт, частотой вращения nэ 1425об/мин.
4. Определяем общее передаточное отношение привода
u13 n1n3 ,
где |
n |
30 3 |
|
30 2v |
|
30 2 0,25 |
19,1об/мин. |
|||
|
|
|
|
|
|
|||||
|
3 |
|
|
D6 |
0,25 |
|||||
|
|
|
||||||||
После подстановки получим |
|
1425 |
|
|
||||||
|
|
|
|
|
u |
|
74,6. |
|||
|
|
|
|
|
|
|||||
|
|
|
13 |
19,1 |
|
|
5. Выбираем передаточное отношение ременной передачи u23 3 и определяем передаточное отношение червячной передачи
u12 u13 74,6 24,8.
u23 3
6. Определяем частоту вращения II-го вала
n2 n3 u23 19,1 3= 57,3об/мин.
84
7. Находим крутящие моменты на валах:
M |
1 |
|
N1 |
9,55 |
N1 |
9,55 |
|
2,2 |
0,015 кН м; |
|
|
|
|||||||
|
|
|
n |
1425 |
|||||
|
|
1 |
1 |
|
|
|
|
M2 M1 u12 чп 0,015 24,8 0,6 = 0,22кН м;
M3 M1 u13 0,015 74,6 0,57 = 0,63 кН м.
6.3. Шнековый транспортёр
Шнековый, или винтовой, транспортёр (конвейер) – это транспортная машина, предназначенная для перемещения сыпучих, кусковых и полужидких вязких тел. Например, шнековый транспортёр применяется для погрузки угля (или песка) в вагоны, для транспортировки металлической стружки, отходов литейного производства, для выдавливания сырой резины сквозь кольцо при изготовлении резиновых шлангов, для перемещения и выдавливания массы теста при изготовлении макарон и вермишели, кускового мяса при его рубке и при производстве колбас и т.д. В домашних условиях примером шнекового транспортёра может служить мясорубка.
Шнековый транспортёр, или винтовой конвейер, состоит из следующих основных частей: цилиндрического корпуса 1, внутри которого расположен винт или шнек 2 , состоящий из цилиндрического стержня диаметром d и винтовой ленты 5, приваренной к стержню; в корпусе 1 имеется горловина 3 для загрузки перемещаемой массы и горловина 4 для удаления перемещаемой массы; если транспортёр предназначен для выдавливания массы, то горловина 4 отсутствует, а масса выдавливается винтом через отверстия, сделанные в торце 6 корпуса; для сообщения винту 2 вращательного движения имеется передача от электродвигателя 7, состоящая из четырёх валов и шести зубчатых колёс Z1...Z6 .
Перемещаемую массу вводят через горловину 3 внутрь транспортёра. Вращающийся винт 2 захватывает своей винтовой лентой 5 поступающую массу и перемещает её вдоль оси винта со скоростью v. Если транспортер применяется для сыпучих тел, то в конце корпуса делают горловину 4, через которую уголь или песок высыпаются. Если транспортёр предназначен для выдавливания вязкой массы в резиновой или пищевой промышленности, то масса выдавливается через специальные отверстия в торце корпуса 1, принимая форму, соответствующую отверстию (или отверстиям).
Шнековые или винтовые транспортёры могут изготавливаться в виде самостоятельных машин или входить в состав машин по переработке массы. Основные технические данные шнековых транспортёров для транспортировки сыпучих грузов: диаметр шнека D=400...800 мм; длина

85
транспортёра 2...25 м; скорость перемещения груза v = 36...60 м/мин; расчётная производительность Q 2...15 м3/мин.
Кинематический и силовой расчёты шнекового транспортёра разберём на примере.
Требуется определить кинематические параметры и расчётные нагрузки шнекового транспортёра, производительность которого Q 1м3/мин; наружный диаметр винта D=400 мм; внутренний диаметр винта d=200 мм; шаг винта t=300 мм; транспортируемый материал – уголь, плотность которого 1500 кг/м3; длина винта (шнека) l=5м, общий КПД0,7; КПД передач зп 0,97.
Р е ш е н и е
Прежде всего, нужно установить зависимость между производительностью Q и частотой вращения винта n4 (т.к. винт является IV-м валом). Уголь транспортируется в кольцевом пространстве между жёлобом-корпусом 1 и цилиндрическим стержнем диаметром d.
Для транспортирования сыпучих тел обычно корпус делают открытым, а сыпучее тело транспортируют в полдиаметра. Объём угля между соседними витками винта, расстояние между которыми равно шагу
t, можно определить, если помножить площадь кольца S (D2 d2 ) на
4
длину шага t, а с учётом половины площади получим
Рис.6.3

86
V 1 S t ( D2 d2 ) t . |
||
t |
2 |
8 |
За 1 оборот винта транспортируется объём Vt , а за n оборотов в минуту – объём Q, м3/мин.
Q ( D2 d2 ) t n. |
(6.1) |
8 |
Скорость транспортирования груза v (м3/мин) можно определить из следующих соображений. Производительность – это объём сыпучего тела
за 1 минуту. Если площадь полукольца 1 S помножить на путь, который
2
проходит сыпучее тело в транспортёре за 1 минуту, т.е. скорость v, то получим искомый объём, т.е. производительность за 1 минуту
1 |
|
|
|
2 |
|
2 |
|
|
|
Q |
|
S v |
|
( D |
|
d |
|
) v. |
(6.2) |
|
|
|
|
||||||
2 |
8 |
|
|
|
|
|
|||
Если сравнить формулы (6.1) и (6.2) , то нетрудно заметить, что |
|||||||||
скорость v (м/мин). |
v t n. |
|
|
|
|
(6.3) |
|||
|
|
|
|
|
|
По корпусу шнека постоянно перемещается объём угля, равный площади полукольца на длину винта,
V 1 S .
2
Вес этой массы угля равен
G mg V g ,
где - плотность. Для угля плотность 1500 кг/м3. Сила трения (сила сопротивления движению)
формуле
F f G f V g ,
где f – коэффициент трения. Для угля по стали f = 0,4. Мощность, затрачиваемая на транспортирование,
(6.4)
(6.5)
определяется по
(6.6)
N F v, |
(6.7) |
где F – сила сопротивления, Н; v – скорость транспортирования, м/с; N – мощность, Вт .
В формуле (6.3) скорость измеряется в м/мин, поэтому для подстановки в формулу (6.7) нужно значение скорости (м/с) разделить на
60, т.е.
v t n . |
(6.8) |
60 |
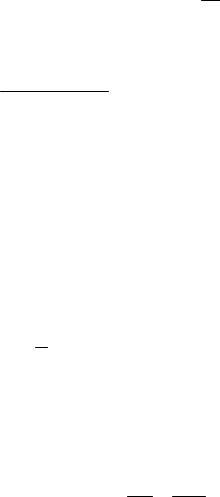
87
С учётом формулы (6.8) определим мощность (Вт)
N F t n . |
(6.9) |
60 |
1.По заданной производительности Q и геометрическим параметрам по формуле (6.1) определим частоту вращения винта
n4 |
8Q |
|
8 2 |
141,5 об/мин. |
|
D2 d2 t |
|
|
|||
(0,42 0,22 ) 0,3 |
2.Определим минутную и секундную скорости движения груза в жёлобе
|
v t n4 |
|
0,3 141,5 = 42,4 |
м/мин, |
||||||||
|
v t |
n4 |
0,3 |
141,5 |
|
0,7 м/с. |
||||||
|
|
|
|
|
||||||||
|
|
60 |
60 |
|
|
|
|
|
||||
3.Определим силу трения по формуле |
|
|
|
|
||||||||
|
|
1 |
|
|
|
f(D2 d2 ) g |
||||||
F |
f V g f |
|
|
|
S g |
|
|
|
||||
|
8 |
|||||||||||
|
|
2 |
|
|
|
0,4 (0,42 0,22 ) 5 1500 9,81=1387 H. 8
4.Определим полезную мощность, затрачиваемую на перемещение груза (угля) по шнековому транспортёру, и выберем электродвигатель
N4 F v 1387 0,7 = 970 Вт=0,97 кВт.
Определим мощность электродвигателя
N1 N4 0,97 1,4 кВт.
0,7
По таблицам выбираем электродвигатель мощностью Nэ 1,5кВт и частотой вращения nэ 1420 об/мин.
5.Определим общее передаточное отношение привода транспортёра, учитывая, что n1 nэ :
|
|
|
u |
|
|
|
n1 |
|
|
1420 |
10. |
||||||
|
|
|
|
|
|
|
|
|
|
|
|
||||||
|
|
|
14 |
|
n4 141,5 |
||||||||||||
6.Принимая передаточные отношения первой и второй передач, |
|||||||||||||||||
равными 2, т.е. u12 u23 |
2, |
определим передаточное отношение |
|||||||||||||||
конической передачи |
|
|
|
|
u14 |
|
|
|
|
|
|
10 |
|
|
|||
u |
34 |
|
u |
23 |
|
2 2,5. |
|||||||||||
|
|
||||||||||||||||
|
|
|
u |
2 |
|
|
|||||||||||
|
|
|
|
|
|
12 |
|
|
|
|
|
|
|
|
|
||
7. Определим угловые скорости на валах: |
|||||||||||||||||
|
n1 |
|
1420 |
148,7 c-1; |
|||||||||||||
|
|
||||||||||||||||
1 |
30 |
|
|
30 |
|
|
|
|
|
||||||||
|
|
|
|
|
|
|
|
|
|
|
|
|
|
|
|
|
|
|
|
|
|
|
|
|
|
|
|
|
88 |
|
|
|
|
|
|
|||||
|
|
n |
2 |
|
|
|
n1 |
|
|
|
|
1420 |
|
710 об/мин; |
|
|||||||||||||||||
|
|
|
u |
|
|
|
|
|
|
|
|
|
|
|
||||||||||||||||||
|
|
|
|
|
|
|
|
|
|
|
|
|
|
|
2 |
|
|
|
|
|
|
|
|
|
|
|
|
|||||
|
|
|
|
|
|
12 |
|
n2 |
|
|
|
|
|
|
|
|
|
|
|
710 |
|
|
|
|
||||||||
|
|
2 |
|
|
|
|
|
|
|
74,3 с-1; |
|
|||||||||||||||||||||
|
|
|
|
|
|
|
|
|
||||||||||||||||||||||||
|
|
|
|
|
|
|
|
|
|
30 |
|
|
|
|
|
|
30 |
|
|
|
|
|||||||||||
|
|
n |
|
|
|
|
n2 |
|
710 |
355 об/мин; |
|
|||||||||||||||||||||
|
|
|
|
u23 |
|
|
|
|
|
|||||||||||||||||||||||
|
|
|
3 |
|
|
|
|
|
|
|
|
|
2 |
|
|
|
|
|
|
|
|
|
|
|
|
|||||||
|
|
3 |
|
n3 |
|
|
355 |
37,2 об/мин; |
|
|||||||||||||||||||||||
|
|
|
|
|
|
|
|
|||||||||||||||||||||||||
|
|
|
|
|
|
30 |
|
|
|
|
|
|
|
|
30 |
|
|
|
|
|
|
|||||||||||
|
|
4 |
|
|
n4 |
|
|
141,5 |
14,8 с-1. |
|
||||||||||||||||||||||
|
|
|
|
|
|
|
||||||||||||||||||||||||||
|
|
|
|
|
|
|
|
|
|
30 |
|
|
|
|
|
|
30 |
|
|
|
|
|||||||||||
8. Определим крутящие моменты на валах: |
|
|||||||||||||||||||||||||||||||
|
|
|
|
|
|
|
|
M |
1 |
|
N1 |
|
|
1500 |
10 Н м; |
|
||||||||||||||||
|
|
|
|
|
|
|
|
|
|
|
|
|||||||||||||||||||||
|
|
|
|
|
|
|
|
|
|
|
|
|
|
|
|
148,7 |
|
|
||||||||||||||
|
|
|
|
|
|
|
|
|
|
|
|
|
|
|
|
|
|
|
1 |
|
|
|
|
|
|
|
|
|
|
|
|
|
|
|
M2 M1 u12 зп 10 2 0,97 19,4 Н м; |
||||||||||||||||||||||||||||||
M |
3 |
M |
1 |
u u |
23 |
2 10 2 2 0,972 |
37 Н м; |
|||||||||||||||||||||||||
|
|
|
12 |
|
|
|
|
|
|
|
|
|
зп |
|
M4 M1 u14 3зп 10 10 0,973 91,3 Н м.
6.4. Кинематический и силовой расчёты машин
Кинематический и силовой расчёты машин предназначены для определения расчётных нагрузок, воспринимаемых машинами и их элементами в процессе эксплуатации, и являются основной задачей теории механизмов и машин. Результаты расчётов служат основой для дальнейших расчётов на прочность, жёсткость и долговечность деталей машин.
Расчёты деталей машин обычно проводят для установившегося движения машины при постоянной скорости приводного двигателя. Такие расчёты называются статическими. Динамику нагрузок при расчётах деталей учитывают с помощью коэффициентов. Приведённые в предыдущих параграфах расчёты кинематические и силовые есть статические. Большинство статических нагрузок определяется просто, т.к. они пропорциональны определяющим их величинам. Вес тела пропорционален его объёму, сила трения пропорциональна нормальному давлению и т.д. Несмотря на некоторую погрешность, статические методы расчёта преобладают в машиностроении.
89
Часть III. ОСНОВЫ СОПРОТИВЛЕНИЯ МАТЕРИАЛОВ
7.ОСНОВНЫЕ ПОНЯТИЯ
7.1.Деформация тела под действием внешних сил
Встатике под действием внешних сил мы рассматриваем условие равновесия тела. Рычаги, стержни и другие тела принимались абсолютно жесткими. В действительности внешние силы вызывают изменение формы
иразмеров тела: при растяжении стержня длина его увеличивается, а диаметр уменьшается; при действии поперечной силы рычаг изгибается и т.д.
Изменения формы и размеров тел под действием внешних сил называются деформациями.
Степень деформации определяется величиной и направлением сил, размерами тела и механическими свойствами материала. Малые силы вызывают малые деформации, которыми пренебрегают. Большие силы вызывают опасные деформации и разрушения.
Для безопасной и долговечной работы машин нагрузки не должны превышать допустимых значений.
Сопротивление материалов – это раздел механики, изучающий методы расчета на прочность, жесткость и устойчивость машин и сооружений. Эти методы основываются не только на общеизвестных положениях механики, но и на экспериментальных материалах, полученных в результате испытаний материалов на прочность, упругость, пластичность и т.д.
7.2.Основные виды деформаций
При действии сил детали, изготовленные из металлов и пластмассы, могут временно деформироваться, а при снятии нагрузок – принимать первоначальную форму: изогнутый рычаг выпрямляется, а растянутый стержень сжимается и т.д.
Деформации, которые исчезают после прекращения действия внешних сил, называются упругими. Упругие деформации в металлах имеют малую величину.
Если кусок стальной проволоки сильно изогнуть, то он не восстановит свою первоначальную форму.
Деформации, остающиеся в телах после прекращения действия нагрузок, называются остаточными или пластическими.
В зависимости от направления действия сил различают деформации:
растяжение, сжатие, сдвиг, кручение и изгиб. Растяжению подвергаются
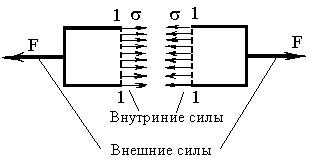
90
тросы подъемных машин, стержни и болты; сжимаются материалы зданий, фундаменты машин; сдвиг возникает в заклепках и сварных швах; кручению подвержены валы, сверла; изгибаются балки грузоподъемных устройств, валы, рессоры и другие детали.
Прикладываемые к деталям нагрузки различают: а) по характеру приложения на сосредоточенные нагрузки, которые прикладываются в точке (груз, подвешенный к балке, зубчатое колесо давит на вал, опора – на балку и т.д.), и на распределенные нагрузки, которые действуют на сравнительно большой площади или длине (трактор – на землю, крыша – на стропила и т.д.); б) по характеру действия на статические нагрузки, величина которых не изменяется в течение всего времени работы конструкции, и на динамические нагрузки, величина которых носит переменный циклический характер, при котором нагрузка изменяется от нуля до максимума и обратно (детали насосов, компрессоров, зубья шестерен и т.д.).
7.3. Внешние и внутренние силы
Все материалы состоят из молекул. При действии на тело внешних сил силы сцепления молекул, или молекулярные силы, оказывают сопротивление. Это сопротивление определяет механические свойства материалов: упругость, прочность, твердость. Если внешние силы растягивают стержень, то увеличивается расстояние между молекулами, а силы притяжения молекул стремятся вернуть все тело в исходное положение, т.е. молекулярные силы в поперечном сечении стержня
оказывают сопротивление, а их сумма равна равнодействующей внешних сил. Если внешние силы скручивают стержень или изгибают его, то внутренние силы,
т.е. молекулярные силы, в каждом сечении стержня создают момент, который уравновешивает внешний крутящий или изгибаю-
щий момент.
Величина внутренних сил, приходящихся на единицу площади внутреннего сечения детали, называется напряжением. Рассмотрим напряжения к конкретным двум случаям.
Если внешними силами F (рис.7.1) растягивать стержень, то в сечении 1-1 возникают внутренние силы , которые препятствуют растяжению.