
1798
.pdf101
Сдвиг материала в одной плоскости, при котором происходит разрушение, называется срезом. Наглядным примером среза является резание бумаги с помощью ножниц.
Лист 1 (см. рис.9.1, а) под действием силы F давит посредством стенок отверстия на стержень заклепки, вызывая на поверхности заклепки напряжение смятия см (см. рис.9.1, б). То же явление можно наблюдать и между листом 2 и нижней половиной заклепки.
Смятием называется местная деформация сжатия по площадкам передачи давления одним элементом конструкции другому.
При сжатии двух тел, которые давят друг на друга по ограниченным поверхностям, происходит смятие поверхностного слоя. Смятие – это остаточная деформация на поверхности материала, которая получается в результате действия большой силы на малой площади.
9.2. Расчеты на прочность при срезе и смятии
Вернемся к рис.9.1. Лист 1 под действием силы F давит на верхнюю половину заклепки. В результате этого на поверхности заклепки возникают напряжения смятия см. Это нормальные напряжения. Если просуммировать эти напряжения, то их сумма будет равна силе F:
см = F. |
(9.3) |
Вспомним, что напряжение – это сила, приходящаяся на единицу площади. Если известна площадь смятия, то тогда сила F будет равна произведению напряжения на площадь, т.е.
F = см Sсм . |
(9.4) |
На цилиндрическую поверхность заклепки со стороны отверстия в листе давление передается по боковой поверхности полуцилиндра afbcde (рис.9.3, а и б). Напряжения смятия распределены неравномерно по поверхности полуцилиндра. Для упрощения расчетов принимают площадь смятия, равной площади прямоугольника abce (рис.9.3, в):
Sсм = d t . |
(9.5) |
|||
Используя уравнение (9.4), можно записать условие прочности |
||||
заклепки на смятие |
F |
|
|
|
см = |
[ см], |
(9.6) |
||
|
||||
|
Sсм |
|
где [ см] – допускаемое напряжение на смятие.

|
102 |
Для заклепок |
из малоуглеродистой стали марок Ст.2 и Ст.3 |
допускаемое напряжение на смятие можно принимать равным [ см] = =300 МПа(Н/мм2).
Сдвигающим силам F на срез (см. рис.9.1 и 9.2) противодействуют напряжения , сумма которых, используя равенства (9.1) и (9.3), равна
= F, |
(9.7) |
||
или |
|
||
F = Sср. |
(9.8) |
||
Площадь среза изображена на рис. 9.3, а. Ее величина равна площади |
|||
поперечного сечения заклепки |
|
||
Scp d2 4. |
(9.9) |
||
Условие прочности на срез имеет вид |
|
||
|
F |
cp , |
(9.10) |
|
|||
|
Scp |
|
где [ ср] – допускаемое напряжение на срез.
Для заклепок из малоуглеродистых сталей можно принимать [ ср] = = 140 МПа (Н/мм2).
9.3. Расчет заклепочных соединений
Пусть листы 1 и 2 соединены заклепками 3. Каждая заклепка в таком соединении испытывает напряжение среза на площади Sср = d2/4 и напряжение смятия см на площади Sсм = dt. Будем считать, что в этом соединении установлено n заклепок.
Рис.9.4
Условия прочности на смятие и срез для одной заклепки определяются формулами (9.6) и (9.10). Для n заклепок условия прочности примут вид:
на срез |
|
F |
cp , |
(9.11) |
|
||||
|
|
nScp |
|
на смятие

|
103 |
|
|
см |
F |
cv . |
(9.12) |
|
|||
|
nScp |
|
С помощью формул (9.11) и (9.12) можно проводить три вида расчетов.
1.Проверочный расчет, который проводится с целью проверки прочности конструкции. Он выполняется по формулам (9.11) и (9.12). При этом рабочее (действующее) напряжение в заклепках сравнивается с допускаемым.
2.Проектный расчет, при котором известны диаметры заклепок d, толщина листов t и силы F. Требуется определить число заклепок, если
заданы [ ср] и [ см].
Для этого формулы (9.11) и (9.12) решают относительно числа заклепок n:
на срез
n |
|
F |
|
, |
(9.13) |
|
|
Scp cp |
|||||
|
|
|
|
|||
на смятие |
|
F |
|
|
||
n |
|
. |
(9.14) |
|||
Scм cм |
||||||
|
|
|
Может решаться иная задача, когда задано число заклепок и нужно определить их диаметр. Тогда, учитывая, что Sср = d2/4, а Sсм = dt , подставляя эти значения в формулы (9.11) и (9.12) и решая их относительно диаметра d, получаем:
на срез
d |
4F |
|
|||
n cp , |
(9.15) |
||||
на смятие |
|
|
|
|
|
d |
4F |
|
|
||
|
. |
(9.16) |
|||
n cм |
3. Определение предельной силы соединения производится с целью установить допускаемую нагрузку, которую может выдержать соединение. Для этого формулы (9.11) и (9.12) решают относительно F:
на срез
Fcp |
nS |
|
|
|
n |
d2 |
|
|
, |
(9.17) |
|
|
|
|
|||||||
np |
|
cp |
|
cp |
4 |
|
cp |
|
|
на смятие
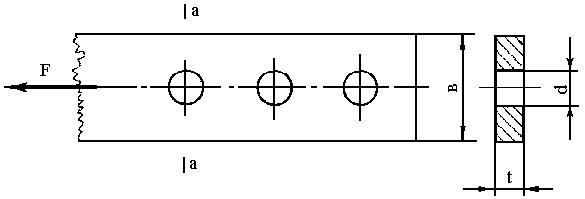
104
Fcp |
nS |
cp |
|
cp |
ndt |
cp |
. |
(9.18) |
np |
|
|
|
|
|
В этом случае безопасной нагрузкой соединения будет меньшая из
двух.
Обычно заклепочное соединение и листы стараются делать равнопрочными в целях экономии металла. Слабое сечение листа будет проходить через отверстие, например а-а (рис.9.5). Площадь этого сечения листа Sл = t(b-d). Предельная сила для листа определится по формуле
Рис.9.5
F л |
S |
л |
|
p |
t b d |
p |
, |
(9.19) |
np |
|
|
|
|
|
где [ р] – допускаемое напряжение на растяжение.
Иногда склепывают лист толщиной 2t с двумя листами толщиной t, которые накладываются на толстый лист сверху и снизу. Получается "слоеный пирог". Толстый лист сила F тянет в одну сторону, а тонкие листы – в другую. Здесь каждая заклепка срезается по двум плоскостям, т.к. получаются двойные ножницы. Площадь среза будет равна удвоенной площади поперечного сечения Sср =2 d2/4, т.к. имеется два среза. Такие заклепки называют двухсрезными. Площадь смятия под тонкими листами Sсм = 2 (t d), а под средним (толстым) листом Sсм = (2t) d.
9.4. Расчет шпоночного соединения
Шпоночные соединения применяют в том случае, когда требуется передавать крутящий момент от вала к колесу или наоборот. Роль колеса могут выполнять зубчатые колеса, шкивы, звездочки, муфты и т.п.
Шпонка является наиболее слабой деталью соединения. В машине одну из шпонок рассчитывают таким образом, чтобы она срезалась, если нагрузка превысит допустимую. Такая шпонка выполняет роль слабого звена и предохраняет машину от перегрузок.
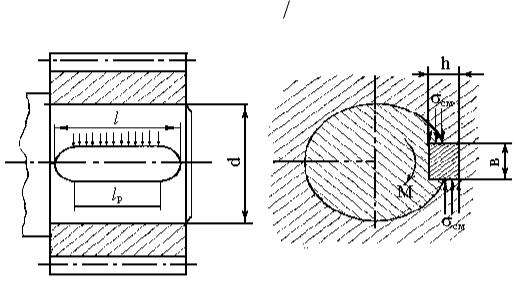
105
Размеры стандартных шпонок подобраны из условия равной прочности на срез и на смятие. Основным расчетом принят проверочный расчет на смятие.
Размеры шпоночного соединения выбирают по ГОСТ 23360-78 в зависимости от диаметра вала d.
Расчет призматической шпонки производят по формуле
см |
2M |
см , |
(9.20) |
|
|||
|
dlp h 2 |
|
Рис.9.6
где M – крутящий момент, Н·мм; d – диаметр вала, мм; lр = l-b – расчетная длина шпонки, мм; b – ширина шпонки, мм; l – длина шпонки, мм; h – высота шпонки, мм; см и [ cм] – действующее и допускаемое напряжения смятия на боковой поверхности шпонки, МПа (Н/мм2).
9.5. Расчет сварных соединений
Сварные соединения выполняют электродуговой сваркой. На рис. 9.7 представлены типичные сварные соединения. Сварка – более совершенное соединение и менее трудоемкое, чем клепаное соединение. Кроме того, в сварных соединениях отсутствуют отверстия, которые ослабляют листы.
Сварное соединение листов встык (рис. 9.7, а) более совершенно, т.к. отсутствует ступенька, но требует специальной обработки кромок листов. Высота шва в этом соединении принимается равной толщине листа.
Прочность сварного шва ниже прочности листов. Сварной шов работает на растяжение. Условие прочности имеет вид
|
F |
, |
(9.21) |
|
tl
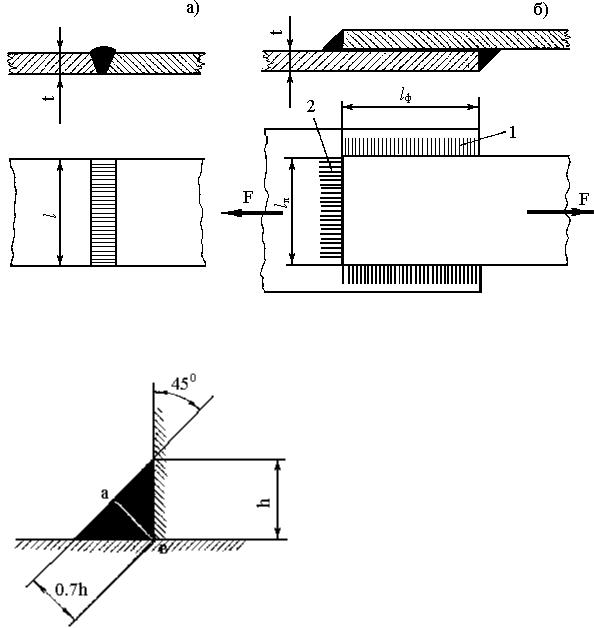
106
где [ '] – допускаемое напряжение на растяжение сварного шва.
Сварное соединение (рис.9.7, б) удобно в изготовлении, т.к. не требует подготовки кромок. Оно носит название соединения внахлестку. Сварные швы при этом называют валиковыми. Швы, которые расположены вдоль (параллельно) действия силы, называются фланговыми (обозначены цифрой 1), расположенные перпендикулярно действию силы называются лобовыми (обозначен цифрой 2).
Рис.9.7
Валиковые швы рассчитывают на прочность по срезу. Срез шва (рис.9.8) проходит по линии ав, поэтому расчетная ширина шва равна 0,7h, где h = t – высота шва, равная толщине листа (рис. 9.7, б).
Условие прочности сварного шва имеет вид
|
F |
|
F |
cp , |
(9.22) |
0,7hl |
|
||||
|
|
0,7tl |
|
где [ 'ср] – допускаемое напряжение на срез для сварного шва.
Рис.9.8
В соединении, изображенном на рис. 9.7, б, листы сварены 4-мя швами: 2-мя лобовыми и 2-мя фланговыми. Касательное напряжение среза всего сварного соединения определяется по формуле
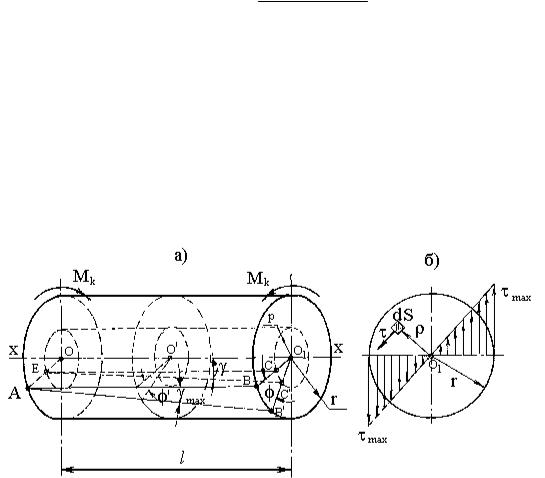
|
107 |
|
|
|
F |
сp . |
(9.23) |
0,7t 2lл 2lф |
Допускаемое напряжение для материала сварного шва выбирают равным
cp 0,6 p , |
(9.24) |
где [ р] – допускаемое напряжение на растяжение для основного материала листов.
10.КРУЧЕНИЕ
10.1.Напряжения и деформации при кручении круглого вала
Рис.10.1
Если круглый вал вращать за торцы в разные стороны, то он будет скручиваться (рис.10.1). При этом продольная линия (образующая) АВ на цилиндрической поверхности вала поворачивается на угол max , а правый торец вала поворачивается относительно левого на угол .
Если взять поперечное сечение в средине вала с центром в точке О', то угол поворота сечения ' будет меньше, чем на правом торце. Чем ближе к точке А, тем угол будет еще меньше. На левом торце угол равен нулю. Если вал порезать мысленно, как колбасу, на узкие дольки, то его можно представить как систему жестких кружков, насаженных на общую ось, которые не меняют ни форму, ни размеров, а только поворачиваются один относительно другого. Таким образом, все поперечные сечения остаются плоскими, радиусы кружков прямыми, расстояние между сечениями постоянными.
Каждый тонкий кружок можно рассматривать как слой металла. Если слои металла сдвигаются друг относительно друга, то мы имеем деформацию сдвига.

108
Степень смещения слоев металла определяется углами: закручивания
– и сдвига – .
Угол закручивания характеризует величину поворота рассматриваемого сечения (тонкого кружка) относительно неподвижного сечения ОА (левого торца вала) и определяет абсолютную величину закручивания вала или его участка.
Отношение угла закручивания вала |
к его длине l называют |
относительным углом закручивания. |
|
l . |
(10.1) |
Относительный угол закручивания характеризует жесткость вала, чем меньше , тем вал более жесткий.
Угол сдвига образуется между первоначальным положением образующей АВ и после деформации – АВ'. Наибольший угол сдвига max образуется на поверхности вала, а по мере приближения к оси вала ОО1 он уменьшается до нуля. Это показывает, что сердцевина вала мало подвержена деформации, а наибольшую деформацию воспринимают внешние слои вала. На оси вала деформация равна нулю. В целях экономии металла валы делают полыми, т.к. вынутая сердцевина вала незначительно снижает его прочность, но значительно снижает его массу.
Выразим угол сдвига max на поверхности вала через угол закручивания на правом торце. Для обоих углов дуга ВВ' единая,
поэтому |
|
||
BB' = r = l max , |
(10.2) |
||
откуда |
|
||
max |
r |
. |
(10.3) |
|
|||
|
l |
|
Если рассмотреть цилиндр радиусом внутри вала, который изображен пунктирными линиями, то угол сдвига на поверхности этого внутреннего цилиндра и угол закручивания будут связаны соотношением
|
|
. |
(10.4) |
||
|
|
||||
|
l |
|
|||
Решив уравнение (10.3) относительно и подставив в уравнение |
|||||
(10.4), получим |
|
|
|
||
|
|
|
|||
|
|
|
|
max. |
(10.5) |
|
|
|
|||
|
|
r |
|
Формула (10.5) показывает, что угол сдвига металла прямо пропорционален радиусу . Чем ближе к оси вала, тем деформация кручения (сдвига) меньше.
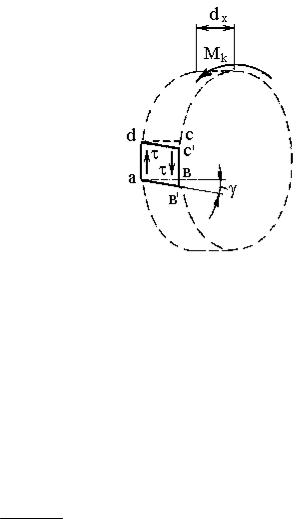
109
Рассмотрим тонкий кружок (диск) толщиной dx (рис.10.2). Правый его торец под действием крутящего момента Мк поворачивается относительно левого против часовой стрелки. На цилиндрической поверхности кружка выделим квадрат abcd. После деформации квадрат превращается в параллелограмм ab'c'd. Частицы
металла, принадлежащие правому торцу, смещаются относительно левого торца. При этом сторона квадрата bc смещается относительно стороны ad.
Сдвиг, при котором материал равномерно смещается в поперечном сечении и при котором возникают только касательные напряжения , называется чистым сдвигом. Величина bb' наибольшего смещения частиц материала по отношению к их первоначальному положению называется абсолютным сдвигом. Отношение абсолютного сдвига к длине участка ab, на котором происходит сдвиг, называется
относительным сдвигом.
bb |
tg = . |
(10.6) |
|
||
ab |
|
Угол – малая величина, поэтому тангенс угла сдвига равен углу сдвига.
Материал оказывает сопротивление. Способность упругих материалов оказывать сопротивление сдвигу характеризует модуль упругости второго рода или модуль сдвига G. Модуль сдвига находится в зависимости от модуля упругости первого рода E при растяжении
G E |
(10.7) |
2(1 ) , |
где = п/ – коэффициент поперечного сжатия (Пуассона). Для стали= 0,25. Подставив в формулу (10.7), получим
G = 0,4E. (10.8)
Модуль упругости при сдвиге меньше модуля упругости при растяжении, поэтому сдвигу материал оказывает меньшее сопротивление, чем растяжению.
Для деформации сдвига справедлив закон Гука: касательные напряжения пропорциональны относительному сдвигу в пределах упругих деформаций
= G . |
(10.9) |
Подставив значение из уравнения (10.5) в уравнение (10.4), получим
|
110 |
|
|
|
|
G max |
|
max |
|
, |
(10.10) |
|
|
||||
|
r |
r |
|
где max = G max – максимальные касательные напряжения на поверхности вала.
Формула (10.10) показывает, что касательные напряжения в поперечном сечении вала возрастают прямо пропорционально радиусу от центра до поверхности вала (рис.10.1, б).
Выберем произвольно на правом торце вала (рис.10.1, б) элементарную площадку dS на расстоянии от центра О1. Касательное напряжение на элементарной площадке dS равно . Элементарный крутящий момент относительно центра О1 равен
dM dS max |
|
dS |
max |
2dS . |
(10.11) |
|||||||
|
|
|||||||||||
|
|
|
|
|
r |
|
r |
|
||||
Если взять интеграл по площади круга S, то получим |
|
|||||||||||
M |
|
|
max |
2dS |
max |
|
S |
2dS . |
(10.12) |
|||
|
|
r |
||||||||||
Интеграл |
k |
S |
r |
|
|
|
|
|
||||
|
|
2dS Ip |
|
|
|
|
||||||
|
|
|
|
|
|
(10.13) |
||||||
|
|
|
s |
|
|
|
|
|
|
|
|
называется полярным моментом инерции.
Подставив значение Ip в формулу (10.12), получим
Mk max |
Ip |
, |
(10.14) |
|
r |
||||
|
|
|
где Ip r Wp называется полярным моментом сопротивления. Подставив
значение Wр в формулу (10.14), получим |
|
||||||
max G max . |
(10.15) |
||||||
Это есть основное уравнение при расчете на прочность. |
|
||||||
Закон Гука для поверхностного слоя вала |
|
||||||
max = G max . |
(10.16) |
||||||
Подставив в уравнение (10.16) значение max из (10.15) |
и max из |
||||||
(10.3), получим |
|
|
|
|
|
|
|
|
Mk |
G |
r |
|
|
||
|
Wp |
l |
|
||||
|
|
|
|
|
|||
или |
|
Mkl |
|
|
|
|
|
|
|
. |
(10.17) |
||||
|
|
||||||
|
|
|
GIp |
|
Это есть основное уравнение при расчете на жесткость при кручении.