
1798
.pdf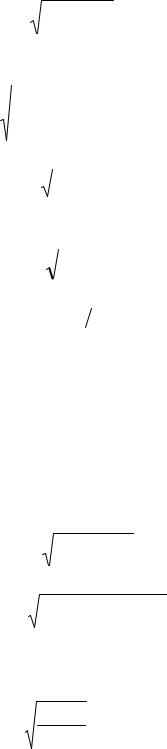
131
Валы изготавливают из пластичных материалов – сталей, поэтому проверку их прочности производят по третьей теории прочности, согласно которой эквивалентное, т.е. равнозначащее, нормальное напряжение определяется по формуле
|
э |
|
u2 4 k2 . |
|
|
|
|
|
|
|
|
(12.8) |
||||||||||
Подставив в формулу (12.8) значения и |
|
|
|
и к |
из формулы (12.6) и |
|||||||||||||||||
(12.7), получим |
|
|
|
|
|
|
|
|
|
|
|
|
|
|
|
|
|
|
|
|
|
|
|
|
|
М |
u |
|
|
2 |
|
М |
k |
|
|
2 |
|
|
|||||||
э |
|
|
|
|
|
|
|
4 |
|
|
|
, |
(12.9) |
|||||||||
|
|
|
|
|
|
|
|
|||||||||||||||
|
|
|
|
W |
|
2W |
|
|
|
|||||||||||||
или |
|
|
|
|
|
|
|
|
|
|
|
|
|
|
|
|
|
|
|
|
|
|
|
|
|
|
|
|
|
|
|
|
|
|
|
|
|
|
|
|
|||||
|
|
э |
|
|
Мu2 Мk2 |
|
|
. |
|
|
|
(12.10) |
||||||||||
Если обозначить |
|
|
|
|
|
|
W |
|
|
|
|
|
|
|
||||||||
|
|
|
|
|
|
|
|
|
|
|
|
|
|
|
|
|
|
|
|
|||
|
|
|
|
|
|
|
|
|
|
|
|
|
|
|
|
|
|
|
|
|
|
|
|
|
|
|
|
|
|
|
|
|
|||||||||||||
то получим |
|
Мэ |
|
|
|
|
|
Мu2 Мk2 |
, |
(12.11) |
||||||||||||
|
|
э |
Mэ |
W. |
|
|
|
|
|
|
|
|
(12.12) |
|||||||||
|
|
|
|
|
|
|
|
|
|
|
||||||||||||
Используя эту формулу, условие прочности при изгибе с кручением |
||||||||||||||||||||||
запишем в таком виде |
|
|
|
|
|
|
|
|
Мэ |
|
|
|
|
|
|
|
|
|
|
|
||
|
|
|
|
э |
|
. |
|
|
|
|
|
(12.13) |
||||||||||
|
|
|
|
|
|
|
|
|
||||||||||||||
|
|
|
|
|
|
|
|
|
W |
|
|
|
|
|
|
|
|
|
|
|
При пространственном нагружении вала поперечными силами в вертикальной и горизонтальной плоскостях в сечениях вала кроме крутящего момента Мк будут действовать два изгибающих момента: под действием вертикальных сил – Мх, а под действием горизонтальных сил – Му. Полный изгибающий момент определится по теореме Пифагора:
Mu |
Mx2 M y2 . |
(12.14) |
Если это значение подставить в формулу (12.11), то получим
Mэ |
Mx2 M y2 Mk2 . |
(12.15) |
По формуле (12.13) производится проверочный расчет вала.
Для определения требуемого диаметра вала нужно неравенство (12.13) решить относительно W = d3/32,
d 3 |
32Mэ |
|
. |
(12.16) |
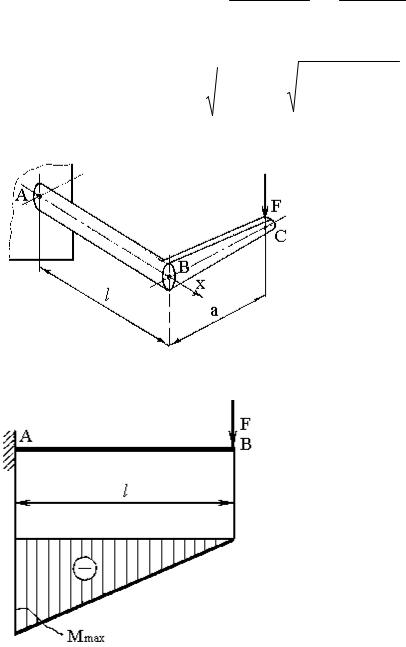
132
12.2. Примеры расчетов на прочность
Пример 1. Вал подвержен совместному действию изгиба и кручения. В опасном сечении вала возникает изгибающий момент Ми=8 кН·м и крутящий момент Мк=10 кН·м. Допускаемое нормальное напряжение [ ]=80 МПа. Определить диаметр вала.
Р е ш е н и е Согласно третьей теории прочности определяем эквивалентный
момент по формуле (12.11)
Mэ Mu2 Mk2
82 102 12,8кН·м .
По формуле (12.16) вычисляем необходимый диаметр вала
d 3 |
32Mэ |
|
3 |
32 12,8 102 |
118мм, |
|
|
|
|||||
|
|
|
80 |
|
|
|
где Мэ=12,8 кН·м = 12,8·106 Н·мм; [ ] = 80 МПа = 80 Н/мм. |
||||||
|
|
|
|
Пример 2. Вал с кривошипом |
||
|
|
|
|
подвергается действию силы F=3,5 |
||
|
|
|
|
кН. Определить диаметр вала d по |
||
|
|
|
|
третьей |
теории прочности при |
|
|
|
|
|
[ ]=160 МПа, l=50 см, а=10 см. |
||
|
|
|
|
|
|
Р е ш е н и е |
|
|
|
|
Переносим силу F из точки С в |
||
|
|
|
|
точку В. В результате получим силу |
||
|
|
|
|
F, приложенную в точке В и |
||
|
|
|
|
крутящий момент Мк относительно |
||
Рис.12.4 |
|
|
точки В (рис.12.4): |
|||
|
|
|
Мк = Fa = 3,5 100 = 350 кН·мм = 3,5 105 |
|||
|
|
|
Н·мм. |
АВ |
|
|
|
|
|
|
Вал |
будет скручиваться |
|
|
|
|
моментом Мк и изгибаться силой F. |
|||
|
|
|
|
На рис. 12.5 приведена расчетная |
||
|
|
|
схема и эпюра изгибающих моментов Ми. |
|||
|
|
|
Опасное сечение будет в точке А, где Ми |
|||
|
|
|
= Мmax и действует крутящий момент Мк. |
|||
|
|
|
Максимальный |
изгибающий момент |
||
|
|
|
равен |
|
|
Ми=Fl=3,5·500=1750кН·мм= =1,75·106Н·мм.
Рис.12.5 Определяем эквивалентный момент по формуле (12.11)
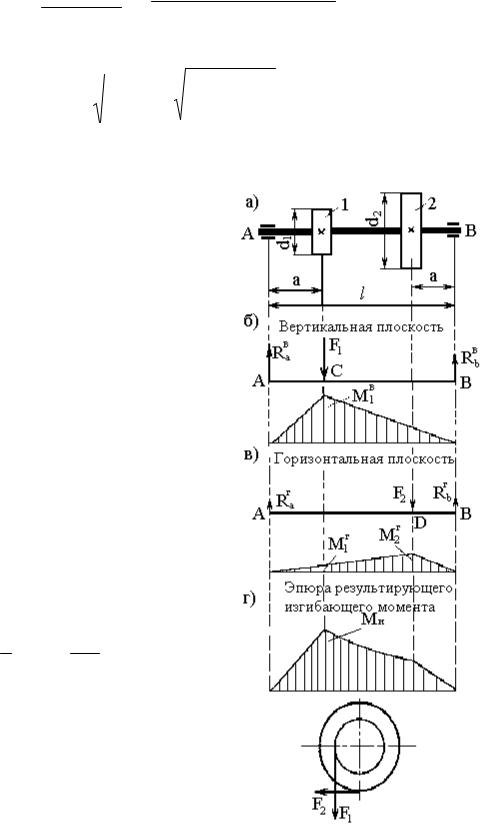
133
Mэ Mu2 Mk2
1,75 106 2 3,5 105 2 1,8 106Н·мм.
По формуле (12.16) вычисляем необходимый диаметр вала
d 3 |
32Mэ |
|
3 |
32 1,8 106 |
48,6мм. |
|
|
160 |
|||||
|
|
|
|
Пример 3. На вал насажены два шкива, диаметры которых d1=15 см, d2=30 см. Усиления приводов F1 и F2 направлены соответственно вертикально и горизонтально.
Определить по третьей теории прочности диаметр вала d, если [ ]=100 МПа, l=60
см, а=15 см, Мк=0,7кН·м.
Р е ш е н и е Крутящие моменты на шкивах 1 и 2
уравновешивают друг друга, поэтому
Мk |
|
F1d1 |
|
|
F2d2 |
. |
|
(12.17) |
|||||||||
|
|
|
|
|
|
||||||||||||
|
2 |
|
|
|
|
|
2 |
|
|
|
|
|
|
||||
Из формулы (12.17) находим |
|||||||||||||||||
|
F |
2М |
k |
|
|
|
2 0,7 106 |
9333Н, |
|||||||||
|
|
|
d |
|
|
|
|
|
150 |
|
|||||||
|
1 |
|
|
|
|
|
|
|
|
|
|
|
|
||||
|
|
|
|
1 |
|
|
|
|
|
|
|
|
|
|
|
||
|
F |
|
2М |
k |
|
|
|
2 0,7 106 |
|
4667. |
|||||||
|
|
d2 |
|
|
|
300 |
|
|
|||||||||
|
2 |
|
|
|
|
|
|
|
|
|
|
|
где Мк=0,7кН·м = 0,7·106 Н·мм; d2=30 см= 300 мм; d1=15 см=150 мм.
Определяем реакции опор в вертикальной плоскости, где сила F2=0
по формулам (11.8) и (11.10):
RbB F1 a 9333150 2333 Н; l 600
RaB F1 RbB 9333 2333 7000 Н.
Максимальный изгибающий момент в вертикальной плоскости соответствует точке С и определяется по формуле (11.12)
M1B RaBa 7000 150 10,5 105 Н·мм.
Рис.12.6
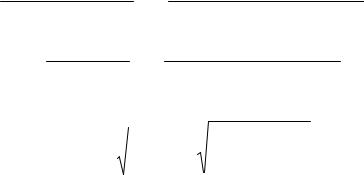
134
Определяем реакции опор в горизонтальной плоскости, где сила
F1=0.
R |
г |
F |
a |
4667 |
150 |
1167 Н; |
|
|
|||||
|
a |
2 l |
600 |
|
Rbг F2 Raг 4667 1167 3500 Н.
Изгибающий момент в точке С (так как МГ2 < МВ1)
M1г Raгa 1167 150 1,75 105 Н·мм .
Расчетный изгибающий момент в опасном сечении С
Мu (М1B)2 (М1г )2
10,52 1010 1,752 1010 10,6 105Н·мм.
Эквивалентный момент определяем по формуле (12.11)
Мэ Мu2 Мk2
10.62 1010 72 1010 12,7 105 Н·мм.
По формуле (12.16) вычисляем необходимый диаметр вала
|
|
|
|
3 |
32 12,7 105 |
|
|
d 3 |
32Mэ |
|
50,6мм. |
||||
|
100 |
||||||
|
|
|
|
|
Часть IV. ДЕТАЛИ МАШИН
13. ОСНОВНЫЕ ПОНЯТИЯ
Детали машин – наука, посвященная изучению конструкции, расчета и проектирования деталей машин и их узлов. Курс деталей машин завершает общетехническую подготовку студентов и создает базу для изучения специальных дисциплин.
Машина состоит из деталей, которые объединены в узлы. Деталь – это элементарная, неразъемная часть машины, которая изготовлена из одного материала (корпус, вал, зубчатое колесо, винт, гайка и т. д.).
Узел, или сборочная единица, – это составная часть машины, которая изготавливается отдельно в другом цехе или на другом заводе. К ним относятся: двигатели внутреннего сгорания (ДВС), электродвигатели, редукторы, узлы гидравлической и пневматической системы, муфты, подшипники качения и др.
Детали и узлы общего назначения: валы, зубчатые колеса, муфты,
подшипники, болты, винты, гайки и т. д. встречаются во всех машинах и изучаются в курсе «Детали машин». Их конструкции и расчету будут посвящены все последующие главы.
Специальные детали и узлы: шнеки, роторы, коленчатые валы и т. д. имеют специфическую конструкцию, относятся к отдельным классам
135
машин и в данном курсе не изучаются. Коленвалы изучаются в специальном курсе «Двигатели внутреннего сгорания», шнеки – в курсе «Транспортные устройства», роторы – в курсе «Турбины и компрессоры» и т. д.
Детали и узлы общего назначения в зависимости от выполняемых функций входят в состав нескольких групп:
1.Соединения – детали, которые связывают между собой части машин: заклепочные, сварные, болтовые, шпоночные, шлицевые и т. д.
2.Передачи – детали и узлы, которые предназначены для преобразования и передачи движения и энергии от двигателя к рабочему органу. К ним относятся ременные, цепные, зубчатые, червячные и др.
3.Детали и узлы, которые входят в состав передач: валы, подшипники, муфты, детали и узлы системы смазки.
Корпусные детали, резервуары, несущие системы, трубопроводы,
направляющие и многое другое рассматривается в специальных курсах.
13.1.Основные требования к деталям машин
Косновным требованиям, которые предъявляются к деталям машин, относятся: прочность и жесткость, надежность и долговечность, рациональные формы, которые обеспечивают компактность узлов и простую технологию изготовления, стоимость и экономичность.
Прочность деталей зависит от выбора материалов, подбора формы и размеров деталей, рационального выбора и расположения опор и т. д.
Жесткость деталей зависит от правильного выбора формы детали,
еедлины, вида и количества опор.
Технологичность деталей определяется затратами труда на изготовление деталей. Если обеспечивается качество деталей при минимальной трудоемкости, то такая деталь называется технологичной.
13.2. Критерии работоспособности и расчета деталей
Работоспособность – способность машин выполнять заданные функции. Критерии работоспособности деталей машин: прочность, жесткость, износостойкость, теплостойкость, виброустойчивость, надежность. Первые три критерия являются основными при расчете машин.
Прочность – главный критерий работоспособности, который обеспечивает сопротивляемость разрушению или возникновению пластических деформаций под действием нагрузок. Прочностью гарантируется надежная работа машины в течение заданного срока. Основы расчета на прочность изучают в сопротивлении материалов, а в
136
деталях машин рассматривают общие законы расчета на прочность применительно к конкретной детали.
Жесткость – способность деталей сопротивляться изменению их формы и размеров под действием нагрузок. Например, недостаточная жесткость вала вызывает его прогиб, перекос зубчатых колес, поломку зубьев и подшипников и другие неприятности. Оценка жесткости производится сравнением расчетных прогибов, углов поворота сечений, углов закручивания и др. с допускаемыми значениями.
Износостойкость – способность трущихся поверхностей деталей сопротивляться истиранию, т. е. изнашиванию. Износ приводит к изменению размеров деталей, стертая поверхность имеет другое состояние, увеличиваются зазоры, снижается прочность, возникают динамические нагрузки и вибрации. Из-за износа выходят из строя до 80 % деталей машин. Расчет деталей на износ заключается в определении для трущихся поверхностей давлений и сравнении их с допускаемыми. Износ снижается с увеличением твердости поверхностей, которые делают гладкими и обильно их смазывают.
Теплостойкость – способность деталей машины сохранять работоспособность при высоких температурах. При нагреве стальных деталей до 300...400º значительно снижаются их механические свойства, ухудшаются свойства смазочных масел, увеличивается износ и др. Тепловые расчеты в настоящем курсе не рассматриваются.
Надежность – свойство машин сохранять работоспособность в течение промежутка времени до отказа.
При работе машин возникают перебои, нарушающие работоспособность. Они называются отказами. Чем реже отказы – тем выше надежность машины. Отказ – это выход из строя машины, который требует вмешательства человека для устранения неисправности или ремонта.
Долговечность – свойство машины сохранять работоспособность в течение времени с перерывами на техническое обслуживание и ремонт до полного износа. Этот промежуток времени называется ресурсом. Когда машина износилась до предельного состояния, говорят, что она выработала свой ресурс.
13.3.Особенности расчета деталей
Всоответствии с критериями работоспособности производят расчет деталей на прочность, износостойкость и жесткость. Расчеты эти приближенные, поэтому неточность расчетов компенсируют коэффициентом запаса прочности, который показывает, во сколько раз допускаемое напряжение меньше критического или предельного

137 |
|
|
n = пр / [ ] , |
(13.1) |
|
а при известном коэффициенте запаса прочности |
|
|
[ ] = пр / n , |
(13.2) |
|
где [ ] – допускаемое напряжение; |
пр – предельное |
напряжение |
(критическое); n – коэффициент запаса прочности. |
|
|
Критерием прочности является неравенство |
|
|
[ ] |
, |
(13.3) |
показывающее, что напряжение , действующее в сечении детали, должно быть меньше или равно, но не превышать допускаемого напряжения.
Проектирование машин проводят методом постепенного приближения. Отсюда появились два вида расчетов: проектировочный и
проверочный или уточненный. |
|
Проектировочный расчет необходим для |
приближенного |
определения размеров деталей и узла в целом и создания конструктивного наброска, т. е. эскиза узла или машины. Появляется эскизная картина узла пусть с приближенными, но конкретными размерами деталей.
После этого проводят уточненный или проверочный расчет с использованием конкретных размеров деталей, составлением расчетных схем и увеличением или уменьшением размеров.
Например, при проектировочном расчете валы рассчитывают не на изгиб с кручением, а просто на кручение по приближенной формуле
d 3 |
Mk |
|
, |
(13.4) |
|
0,2 k |
|||||
|
|
|
где d – диаметр вала; Мк – крутящий момент на валу; k – допускаемое касательное напряжение.
Как видно, в формуле (13.4) не содержится длины вала, места расположения на нем подшипников, зубчатых колес или шкивов и другие сведения, которые к началу проектирования неизвестны.
Затем по формуле, которая содержит передаточное отношение передачи, крутящий момент, допускаемое напряжение и коэффициенты, определяют модуль зубчатого колеса и его размеры, т. к. они являются функцией модуля.
Далее вычерчивается зубчатое колесо, вал и его опоры. Появляются конкретная длина вала, расстояние между опорами и положение зубчатого колеса относительно опор.
Теперь вычерчивается расчетная схема, строятся эпюры крутящих и изгибающих моментов, определяются опасное сечение и эквивалентное напряжение в опасном сечении.
По формуле (13.3) проверяется прочность. Если > [ ], то диаметр вала нужно увеличить. Если << [ ], то диаметр вала нужно уменьшить. Наилучший результат, если [ ] или чуть меньше.
138
13.4. Основные материалы деталей
Наибольшее применение в качестве конструкционных материалов получили сталь и чугун. Из чугуна изготавливают корпусные детали, станины и другие несущие конструкции. Из сталей разных марок изготавливается большинство деталей машин. Реже применяют цветные металлы и пластмассы.
Сталь – это сплав железа с углеродом, содержание которого по отношению к железу менее 2 %. Низкоуглеродистые стали обладают хорошей пластичностью, т.к. они сравнительно мягкие, но меньшей прочностью и твердостью. Высокоуглеродистые стали имеют большую твердость и прочность, но они хрупкие, т.к. имеют низкую пластичность. Для улучшения качественных показателей стали в нее добавляют хром, титан, кремний, ванадий, никель и другие добавки в небольшом количестве. Такие стали называют легированными.
Широкое распространение сталь получила благодаря своим уникальным свойствам: высокой прочности, пластичности и гибкости; возможности получения заготовок деталей из поковок, отливок, проката; хорошей обрабатываемости на станках; способности к термической обработке с целью получения высокой твердости и поверхностных покрытий и т. д.
Чугун – это тоже железоуглеродистый сплав с содержанием углерода свыше 2 %. Наибольшее распространение получил серый чугун, содержащий 2,5...3,5 % углерода. В сером чугуне сталь имеет форму губки, в ячейках которой помещается графит, который ослабляет металлическую основу чугуна, а с другой стороны графит, размазываясь по трущейся поверхности, уменьшает трение и износ. Серый чугун прекрасно обрабатывается на станках, хорошо заливается в любую сложную форму. Серый чугун – хрупкий материал, имеет среднюю прочность, хорошо работает на сжатие, плохо на растяжение, изгиб и кручение, но он является дешевым литейным материалом и хорошим гасителем вибраций.
Из цветных металлов в машинах наиболее часто применяются сплавы меди и алюминия. Алюминиевые сплавы применяют для изготовления небольших корпусных деталей. Бронзы – сплавы меди с оловом, свинцом, алюминием, железом – обладают антифрикционными свойствами и применяются для изготовления подшипников скольжения, гаек и червячных колес.
Пластмассы применяют для изготовления сравнительно мелких деталей прессованием в металлические пресс–формы.
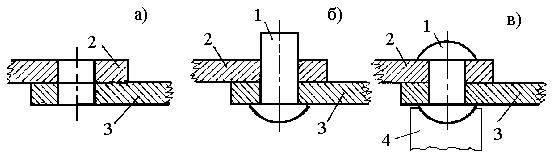
139
14. СОЕДИНЕНИЯ ДЕТАЛЕЙ
Каждая машина состоит из отдельных деталей, которые соединяются между собой, образуя неразъемные и разъемные соединения.
Неразъемные соединения невозможно разобрать, т.к. детали соединены между собой с помощью заклепок, сварки, клея и др.
Разъемные соединения можно разобрать и вновь собрать, т.к. детали соединяются между собой с помощью винтов, болтов, шпонок, штифтов и т. д.
14.1. Заклепочные, сварные и клеевые соединения
Заклепочные соединения в настоящее время почти полностью вытеснены сваркой. Они сохранились для соединения мелких деталей, тонких листовых материалов, плоских пружин и т. д. в приборостроении.
Рис. 14.1
На рис. 14.1 приведено заклепочное соединение, которое состоит из заклепки 1, листа 2 и листа 3. Заклепка является основным элементом соединения, т.к. она скрепляет листы 2 и 3. Заклепка представляет собой круглый стержень, который с одного конца имеет головку (рис. 14.1, б). Для образования заклепочного соединения листы 2 и 3 накладывают друг на друга и прижимают. Затем сверлят в них отверстие (рис. 14.1, а). В отверстие снизу вставляют заклепку (рис. 14.1, б). После этого листы с заклепкой кладут на жесткую опору 4 (рис. 14.1, в), а сверху молотком расклепывают верхний конец заклепки до образования круглой головки.
Сваркой называют технологический процесс соединения деталей с помощью разогрева стыка до высокой температуры с последующим расплавлением стыка и электрода и образованием жидкого шва, который быстро застывает и прочно скрепляет две детали. Для надежного соединения детали листы (рис. 9.7) должны быть изготовлены из низкоуглеродистой стали. В машиностроении, строительстве сварка является основным видом сборки неразъемных соединений, к которым относятся корпусные детали, строительные фермы для перекрытия зданий, котлы, резервуары, трубы и т. д.
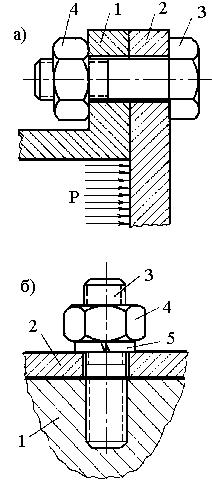
140
Клеевые соединения известны давно. С помощью клея склеивали бумагу, наклеивали обои на стены, склеивали стыки в деревянных стульях, столах, другой мебели.
Соединение деталей осуществляется за счет сил сцепления затвердевшего клея. Склеивать между собой можно детали из различных материалов: дерева, металла, пластмассы, кожи, резины, войлока, стекла, керамики, фарфора. Например, на цилиндрическую поверхность стального круга можно наклеить ткань, кожу, резину или войлок; склеить разбитую вазу или плафон; приклеить металлический номер на деревянную дверь и т. д.
К достоинствам клеевых соединений можно отнести возможность соединения деталей из разнородных материалов, не поддающихся сварке и даже склепыванию, например хрупкая керамика и ткани; герметичность соединения, например склеенные емкости. К недостаткам нужно отнести сравнительно низкую прочность и потерю ее со временем.
Рис. 14.2
14.2. Болтовые и винтовые соединения
Болтовые и винтовые соединения применяют для соединения листовых деталей, соединения корпусных деталей с помощью лапок, пружин, присоединения мелких деталей к корпусу и т. д. Основой этого соединения являются болт (винт) и гайка. Болтовые и винтовые соединения в общем случае называют резьбовыми соединениями.
Резьбовые соединения в отличие от заклепочных можно при надобности разъединить. Они относятся к разъемным соединениям.
На рис. 14.2 изображены два примера резьбовых соединений. К цилиндру 1 прикрепляется крышка 2. Они соединяются между собой болтом 3 и гайкой 4.
Второй пример. Корпус 1 соединен с крышкой 2 с помощью шпильки 3, гайки 4 и шайбы 5. Болты имеют шестигранную головку для