
1798
.pdf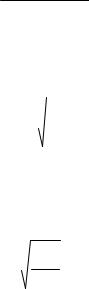
|
191 |
|
|
v |
t z1 n1 |
, |
(17.44) |
|
|||
|
60 1000 |
|
где t – шаг цепи, мм; z1 – число зубьев малой звездочки; n1 – частота вращения малой звездочки, об/мин; v – скорость цепи, м/с.
Передаточное число цепной передачи определяется аналогично
ременной и зубчатой передачам |
|
n1 |
|
z2 |
|
|
||
и |
|
|
, |
(17.45) |
||||
|
|
|||||||
12 |
|
n |
2 |
|
z |
|
||
|
|
|
1 |
|
|
где и12 – передаточное отношение между I и II валом; n1 и n2 – частоты вращения ведущей и ведомой звездочек или I-го и II-го валов, об/мин; z1 и z2 – числа зубьев ведущей и ведомой звездочек.
Число зубьев меньшей звездочки рекомендуют брать z1 ≥12 в зависимости от передаточного отношения по формуле
z1 = 29 – 2и . (17.46)
Число зубьев ведомой звездочки определяется по формуле (17.44). Наибольшее число зубьев большей звездочки рекомендуют z2 ≤120.
Числа зубьев малой и большой звездочек рекомендуют брать нечетным и некратным, чтобы не было постоянного контактирования одного зуба с одним и тем же звеном цепи.
Делительный диаметр звездочки определяют по формуле
d |
t |
|
|
|
|
|
sin 1800 / z . |
(17.47) |
|||||
Оптимальное межосевое расстояние |
|
|||||
а = (30…50)t . |
(17.48) |
|||||
Шаг цепи рассчитывают по формуле |
|
|||||
t 30,53 |
|
kN1 |
|
, |
(17.49) |
|
|
||||||
|
|
|
n1 |
|
где N1 – мощность, передаваемая передачей, кВт; t – шаг цепи, мм; k – коэффициент влияния частоты вращения n1 на износостойкость шарниров; n1 – частота вращения ведущей звездочки, об/мин.
Коэффициент влияния частоты вращения n1 определяют по формуле
n2 |
(17.50) |
k 3 1 . |
100
Срок службы цепи принимают равным Lh = 104ч.
Таблица 17.4
Основные данные роликовых цепей
Шаг цепи t, мм |
12,7 |
15,875 |
19,05 |
25,4 |
31,75 |
Разрушающая |
18,2 |
22,7 |
31,8 |
56,7 |
88,5 |
нагрузка Fр, кН |
|
|
|
|
|
192
|
|
|
|
Окончание табл. 17.4 |
|
|
|
|
|
|
|
Опорная |
50 |
71 |
106 |
|
180 |
поверхность S0, |
|
|
|
|
|
мм2 |
|
|
|
|
|
Коэффициент, учитывающий условия эксплуатации, определяют по формуле
kэ = kд · kн · kс , (17.51)
где kд – коэффициент динамической нагрузки: kд = 1 при спокойной нагрузке, kд = 1,5 при нагрузке с толчками; kн – коэффициент натяжения цепи: kн = 1 при натяжении одной из звездочек (см. рис.17.4), kн = 1,1 при натяжении нажимной звездочкой, kн = 1,25 без натяжения; kс – коэффициент вида смазки передачи: kс = 1 при непрерывном смазывании, kс=1,5 при периодическом смазывании.
Давление в шарнирах цепи определяется по формуле
p kэ F /S0 |
p . |
(17.52) |
||
Допускаемое давление (Н/мм2) в шарнирах цепи |
|
|||
p |
C |
|
40, |
(17.53) |
|
|
|||
|
Lh k kэ |
|
где С = 4 · 106 – коэффициент работоспособности; Lh = 104 ч – срок службы передачи.
Порядок расчета состоит в определении:
1.Числа зубьев ведущей звездочки по формуле (17.47), а ведомой по формуле z2=z1и12≤120.
2.Коэффициента влияния частоты вращения n1 по формуле (17.50).
3.Шага цепи t по формуле (17.49) с округлением его до стандартного ряда по табл. 17.4.
4.Скорости цепи v по формуле (17.44).
5.Окружной силы F, передаваемой цепью, по формуле (17.43).
6.Коэффициента kэ, учитывающего условия эксплуатации, по формуле
(17.50).
7.Среднего давления р в шарнирах по формуле (17.52).
8.Допускаемого давления [р] при сроке службы Lh = 104ч и коэффициента работоспособности С = 4·106 по формуле (17.53).
9.Межосевого расстояния а по формуле (17.48).
10.Сил, действующих на валы звездочек, по формуле (см. рис. 17.4) |
|
Fв 2F0 k F , |
(17.54) |
где Fв – сила, с которой цепная передача действует на валы О1 и О2 (см. рис. 17.4); 2F0 – сила натяжения ветвей цепи; k – коэффициент динамической нагрузки, зависящий от характера нагрузки и расположения угла наклона θ линии центров звездочек к горизонту: при θ=0…400
193
значение k = 1,15…1,3; при θ = 40…900 значение k = 1,05…1,15. Меньшие значения k соответствуют спокойной нагрузке, а большие – ударной.
18.ВАЛЫ И ИХ ОПОРЫ
18.1.Общие сведения
Вал – это вращающаяся деталь, несущая на себе шкивы, звездочки, зубчатые колеса и другие детали вращения, которые через вал передают крутящий момент. Вал в свою очередь устанавливается в корпусе с помощью подшипников. Подшипники являются опорами вала и одновременно направляющими вращения. Они отбирают у вала свободу осевого и радиального перемещения и, наоборот, создают свободу вращательному движению. Вал в совокупности с деталями вращения и подшипниками называют узлом вала.
Валы, как правило, имеют ступенчатую форму, т. к. каждая деталь вращения или подшипник имеют свой диаметр отверстия. Это объясняется тем, что все детали вращения и подшипники одеваются на вал последовательно. Вначале в середине вала одевается деталь с большим отверстием, затем последовательно одеваются детали с меньшими диаметрами и в последнюю очередь – деталь с наименьшим диаметром.
Узел вала (рис. 18.1) состоит из собственно вала, являющегося несущей деталью (основой), на которой установлены детали вращения: коническое колесо 1, получающее вращение, и крутящий момент от конической шестерни (на чертеже не показана); звездочки 2, на которую передается крутящий момент, и вращение от колеса 1 и подшипников качения 3, на которые опирается вал и которые способствуют вращательному движению вала благодаря тому, что они опираются на свободно катающиеся шарики. Подшипники в свою очередь установлены в корпус 4, в котором установлен вал с конической шестерней и могут размещаться валы других зубчатых передач. Цепная передача вынесена за пределы корпуса, поэтому она называется открытой, а коническая передача – закрытой. Для передачи крутящего момента с колеса на вал и с вала на звездочку применяются шпонки 5 и 6.
Участки вала 7 и 8, на которые одеты подшипники 3 и которыми вал опирается на подшипники, называются цапфами. Концевая цапфа 7 называется шипом, а 8 – шейкой.
Шипы и шейки передают радиальную нагрузку. Ими вал опирается через подшипники на корпус, как балка на двух опорах.
Участки вала 9 и 10, на которые посажены колесо 1 и звездочка 2,
называются посадочными поверхностями валов или посадочными участками.
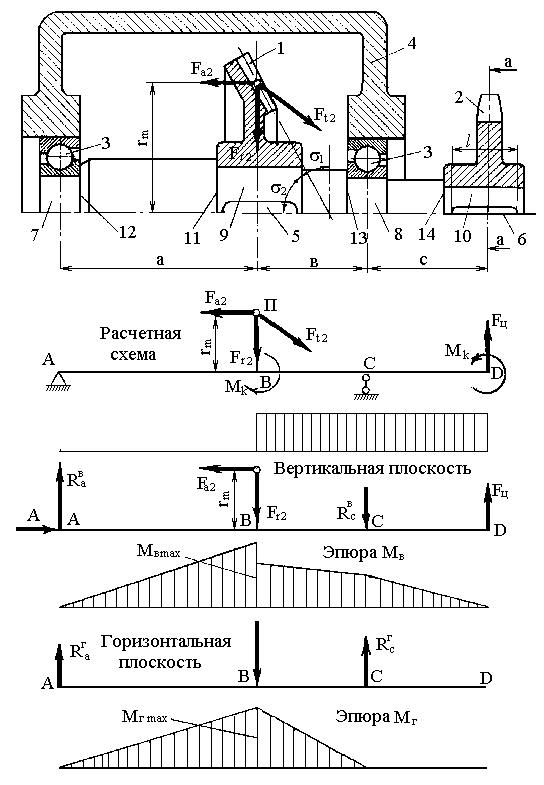
194
Рис.18.1
Уступы на валу при переходе с поверхности одного диаметра на поверхность другого диаметра называют заплечиками. Они служат для восприятия осевых сил (заплечики 11 и 12), а также для фиксации положения деталей на валу (заплечики 11 и 14) и вала в подшипниках (заплечики 12 и 13).
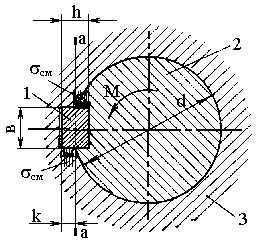
195
Порядок сборки узла вала, когда корпус разъемный и вал собирается отдельно, следующий. Коническое колесо 1 имеет наибольшее отверстие, поэтому при одевании его на вал с правого конца колесо свободно проходит через все участки вала до своего посадочного места 9, не задевая участков, т. к. их диаметры меньше отверстия в колесе. Затем одеваются подшипники 3 слева и справа. Последней одевается звездочка 2.
18.2. Шпоночные соединения
Вращающиеся детали закрепляются на валах с помощью шпоночных
ишлицевых соединений, которые служат для передачи крутящего момента от вала к детали вращения (зубчатому колесу, шкиву, звездочке, муфте) или наоборот.
Шпоночное соединение состоит из (см. рис. 18.1 и 18.2) шпонки 1, которая помещается в продольном пазу вала 2 и ступицы детали вращения 3. Шпонка имеет призматическую форму. Она плотно входит одновременно в паз вала
ипаз ступицы и запирает вал и ступицу
от возможности |
их относительного |
|
||
вращения. |
При |
сборке узла |
(см. |
|
рис.18.1) шпонку 6 закладывают в паз |
|
|||
вала, а затем надевают звездочку 2. |
|
|||
Шпонка |
не |
удерживает |
деталь |
|
вращения от осевого смещения по валу. |
Рис.18.2 |
Для осевой фиксации детали (детали 1 и 2, см. рис.18.1) на валу делают ступеньки (заплечики) 11 и 14, в упор до которых насаживаются детали 1 и 2, а для того, чтобы детали в процессе работы не сдвигались назад, их насаживают по тугой посадке, вызывающей напряжения между валом и деталью. Деталь вращения: звездочка 2 или колесо 1 туго обхватывают вал и удерживают деталь. Такие соединения называют напряженными. Кроме напряженных соединений для удержания деталей на валу применяют стопорные кольца, стопорные винты, специальные гайки и т.д.
Наряду с передачей крутящего момента шпонки выполняют роль слабого звена. Слабым звеном называют деталь, которая в случае перегрузки узла должна в первую очередь разрушиться, а остальные детали должны остаться невредимыми. По другому это звено называют предохранительным. Одну из шпонок редуктора конструктор выбирает в качестве слабого звена и рассчитывает на большее в полтора – два раза
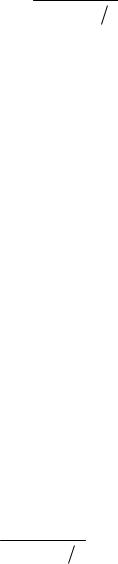
196
допускаемое напряжение, обеспечивая этим срез именно этой шпонки в случае перегрузки.
При передаче крутящего момента М (см. рис. 18.2) на боковых поверхностях шпонки возникают напряжения смятия см, которые можно определить по формуле
2M |
|
|
см d l b h 2 |
, |
(18.1) |
где l – длина шпонки (см.рис. 18.1).
Ступицы деталей вращения (колес, шкивов, звездочек) обычно изготавливают из стали и реже чугуна, а шпонки из конструкционных сталей из чистотянутых стальных призматических прутков сечением b·h. Предел прочности σb≥500 Н. Например, сталь 35 имеет σb=540 Н/ мм2; σТ=320 Н/мм2. Допускаемое напряжение на смятие: при спокойной
нагрузке |
и стальной ступице см = 100…150 Н/мм2; при чугунной |
ступице - |
см = 60…80 Н/мм2; при значительных колебаниях нагрузки |
см следует снижать на 50 %. Слабое звено нужно рассчитывать на напряжение см в два раза большее, чтобы получить опорную поверхность шпонки в полтора – два раза меньшую (конкретно в полтора – два раза меньшую длину шпонки).
Размеры сечений шпонки (ширину b и высоту h) выбирают в зависимости от диаметра d вала по ГОСТ 23360 – 78. Длину шпонки l (см. рис. 18.1, поз.6) выбирают на 5…10 мм меньше, чем длину ступицы.
Размеры стандартных шпонок подобраны из условия прочности на смятие, поэтому основным расчетом является проверочный расчет на смятие. Проверка шпонок на срез может не производиться, т. к. соотношение стандартных размеров b и h таково, что прочность сечения на срез выше, чем на смятие поверхности.
Проверочный расчет рабочих поверхностей шпонки и ступицы на смятие проводят по формуле
2M |
см , |
|
см d l b h 2 |
(18.2) |
где М – передаваемый крутящий момент, Н·м; d – диаметр вала, мм; b – ширина шпонки, мм; h – высота шпонки, мм; l – длина шпонки, мм; σсм исм - расчетное допускаемое напряжение на смятие соответственно, Н/мм2.
Если по расчету получается σсм ≥ см , то удлиняют ступицу, а если невозможно, то устанавливают две шпонки диаметрально противоположно друг другу, т.е. под углом 1800.

197
18.3. Расчет валов
Валы должны изготавливаться из прочных материалов, хорошо обрабатываться и иметь хорошую упругость. Для валов применяют среднеуглеродистые стали марок 45 и 40Х.
Основные критерии работоспособности и расчета валов – это статическая и усталостная прочность и жесткость. Основными расчетными нагрузками являются передаваемый крутящий момент Мк и момент поперечного изгиба Ми. Расчет на прочность проводится в два этапа: проектный расчет и проверочный расчет.
Проектный расчет. К началу проектирования вала известен лишь крутящий момент. Поэтому в первую очередь определяют ориентировочный (приближенный) диаметр валов по эмпирической формуле
d 3 |
Mk |
, |
(18.3) |
0,2 k |
где d – диаметр вала, мм; Мк – крутящий момент, Н·мм; [τк] = 12…25 Н/мм2 – допускаемое напряжение на кручение. Малое значение допускаемого напряжения [τк] компенсирует отсутствующие напряжения изгиба.
Расчетное значение диаметра d округляют до ближайшего стандартного в большую сторону. Этот диаметр d является минимальным для ступенчатого вала (диаметр посадочного участка 10 под звездочку 2 на
рис.18.1). Затем выбирают подшипники по внутреннему диаметру dп, ближайшие большие, чем d. После этого выбирают стандартный внутренний диаметр зубчатого колеса (см. рис. 18.1) dк, который ближайший больший, чем dп. Например, расчетный диаметр, полученный по формуле (18.3), d = 15,3 мм. Округляем его до ближайшего
стандартного ряда Ra 20: 10; 11; 12; 14; 16; 18; 20; 22; 25; 28; 32; 36; 40; 45; 50; 56; 63; 70; 75; 80; 90; 100, а далее нужно умножить на 10
написанный ряд, т.е. 110; 120; 140 и т.д. Выбранный размер d=16 мм.
Стандартный ряд внутренних диаметров подшипников: 10; 12; 15; 17; 20; 25 и далее через 5 до 100 мм. Итак, диаметр посадочного участка 10 вала под звездочку d = 16 мм. Высота уступа 14 должна быть не менее 2 мм по радиусу, а по диаметру – 4 мм (выбираем – 6 мм). Следовательно, диаметр промежуточного участка вала между звездочкой 2 и подшипником 3 dпр = d
+ 6 = 16+6 = 22 мм. Внутренний диаметр подшипника 3 выбираем из стандартного ряда dп = 25мм. Уступ 13 должен быть не менее 3 мм, а по диаметру – 6 мм. Диаметр промежуточного участка вала между подшипником 3 и коническим колесом 1 dпр = 25+6 = 31 мм. Диаметр посадочного участка 9 под коническое колесо 1 выбираем как ближайший
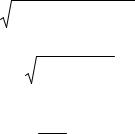
198
больший из стандартного ряда Ra20, т.е. dк= 32 мм. Диаметр цапфы 7 равен диаметру цапфы 8, т.е. dп = 25мм. Диаметр промежуточного участка вала левее конического колеса с учетом уступа 11 dпр = dк + 6 = 32+6 = 38 мм.
Аналогично рассчитывают второй, третий и т.д. валы. Затем конструктор вычерчивает эскизный проект редуктора, который позволяет определить линейные, т.е. осевые размеры валов (на рис. 18.1 – это a; b; c). Линейные размеры и диаметры вала необходимы для его проверочного и уточненного расчетов.
Проверочный расчет начинается с разработки расчетной схемы (см.
рис. 18.1). Bал изображают как балку на двух опорах A и C. К балке прикладывают силы Ft2; Fr2 и Fa2, приложенные в полюсе П конического зацепления, и силу натяжения цепной передачи Fц=2F0. Это внешние силы. Затем освобождают балку от связей (опор А и С), заменяя их реакциями Ra и Rc. Расчетные схемы выполняют в вертикальной плоскости и в горизонтальной. Строят эпюру крутящих моментов Мк и эпюры изгибающих моментов Мв в вертикальной плоскости и Мг – в горизонтальной плоскости. Далее определяют опасное сечение (точка В), в котором действуют максимальные изгибающие моменты Мв max и Мг max, и крутящий момент Мк. Максимальный изгибающий момент в точке В
Mu |
Mв2max Mг2max , |
(18.4) |
а эквивалентный момент в точке В
Mu |
Mu2 Mk2 . |
(18.5) |
Проверку прочности проводят по формуле
э Mэ 1 ,
W
где Ми – изгибающий момент в опасном сечении, т.е. максимальный, Н·мм; Мэ – эквивалентный момент, Н·мм; σэ – эквивалентное напряжение, Н/мм2;
W – осевой момент сопротивления, мм3; [σ-1] –допускаемое напряжение, Н/мм2.
При работе валы испытывают переменные (циклические) напряжения, поэтому основной вид разрушения валов – усталостное разрушение. При расчете на усталость нужно установить характер цикла изменения напряжений, действующих внутри вала. Изгибающие вал силы остаются на месте, а вал вращается, поэтому каждая точка вала при вращении подвергается переменному изгибу, изменяющемуся по симметричному циклу, напоминающему перегиб проволоки взад–вперед (когда ее хотят отломить). Такая нагрузка называется знакопеременной, а цикл изменения напряжений – симметричным от +σmax до –σmax. Напряжение при знакопеременной симметричной нагрузке обозначается σ-1. Напряжение σ-1 является предельным, а его значение приведено в табл. 18.1.
199
Допускаемое напряжение изгиба при симметричном цикле [σ-1] определяется по формуле
|
|
1 |
|
1, |
|
(18.6) |
||
|
k n |
|
|
|||||
|
|
|
|
|
|
|
|
Таблица 18.1 |
Предельные и допускаемые напряжения для материала валов |
||||||||
|
|
|
|
|
|
|
|
|
Марка |
35 |
|
45 |
|
|
45 |
40х |
|
стали, Н/мм2 |
|
|
|
|
|
|
закаленная |
закаленная |
σв |
500 |
|
600 |
|
|
850 |
1000 |
|
σ-1 |
220 |
|
260 |
|
|
340 |
400 |
|
[σ-1] |
60 |
|
70 |
|
|
90 |
100 |
где ε – масштабный коэффициент, зависящий от диаметра вала, для валов d=30…60 мм можно выбирать ε=0,82; β – коэффициент, учитывающий шероховатость поверхности, для валов можно выбирать β=0,9; kσ – коэффициент концентрации напряжений, для вала kσ=1,5; [n] = 1.8 – коэффициент запаса прочности. Если обозначить комплексный коэффициент буквой k, то
|
k |
|
|
||
|
|
|
, |
|
|
k n |
|
||||
а его величина (в среднем) может быть равной |
|
||||
k |
0,82 0,9 |
0,27. |
|
||
|
|
||||
|
1,5 1,8 |
|
|||
Тогда уравнение (18.6) перепишется в виде |
|
||||
1 k 1 0,27 1. |
(18.7) |
Данные среднего значения [σ-1] приведены в табл. 18.1.
18.4. Подшипники
Как было показано выше (см. рис.18.1), вал опирается на корпус посредством подшипников. Подшипниками называют опоры вращающегося вала. Они поддерживают вал и одновременно являются направляющими вращения. Подшипники воспринимают и передают на корпус радиальные и осевые силы, действующие на детали узла вала. Подшипники, которые воспринимают радиальные нагрузки, называют радиальными, воспринимающие осевые нагрузки, – упорными, воспринимающие одновременно радиальные и осевые нагрузки, называют радиально-упорными.
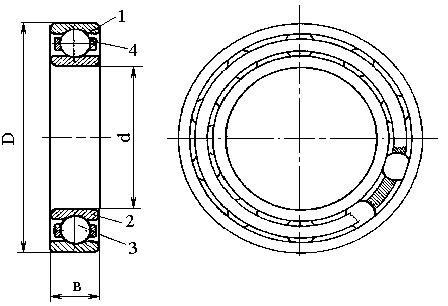
200
По виду трения различают подшипники скольжения и подшипники качения. Подшипник скольжения представляет собой бронзовую втулку, которая одевается на цапфу свободно, а в корпус запрессовывается. Поверхность цапфы скользит по поверхности подшипника, при этом возникает трение скольжения, которое приводит к износу и нагреву подшипника. Для уменьшения трения между поверхностями скольжения вводят смазку. В современных машинах применяют главным образом подшипники качения, которые имеют преимущества: низкие потери на трение, их КПД η=0,995; невысокий нагрев подшипника; возможность взаимозаменяемости при ремонте и др. От качества подшипников в значительной мере зависят надежность и качество машин.
Рис.18.3
Подшипники качения – это готовые узлы, которые состоят (рис.18.3) из наружного 1 и внутреннего 2 колец с полукруглыми желобами, называемыми дорожками качения, тел качения 3 (шариков или роликов) и сепаратора 4. Тела качения помещаются в дорожках (желобах) между наружным и внутренним кольцами. Катиться тело вращения может только по желобу, т.е. по дорожке, а в сторону выкатиться оно не может. Наружное кольцо 1 запрессовывается в корпус и остается неподвижным. Внутреннее кольцо туго одевается на вал и вращается вместе с ним. Вращающееся внутреннее кольцо увлекает за собой тела качения, которые катятся по дорожкам внутреннего и наружного колец. Таким образом, вал опирается на шарики и ролики и катится по ним. Трение качения в десятки раз меньше трения скольжения. Именно этим объясняется столь высокий КПД подшипников качения – 0,995.
Количество тел качения бывает четное – 6, 8, 10, 12 и т.д., чтобы всегда два тела качения (шарика или ролика) стояли друг против друга на