
ТРАНСВУЗ-2015.Часть 1
.pdf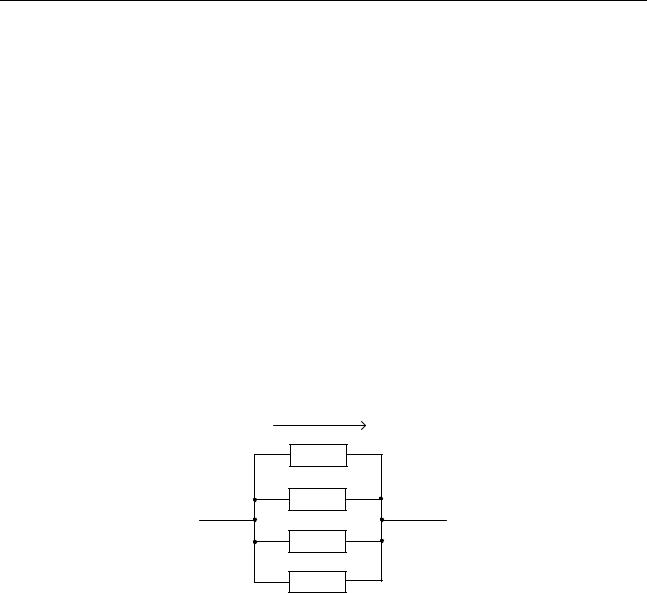
Ремонт и динамика подвижного состава
По аналогии с выражениями (3) и (4), тепловые сопротивления R12, R13, R14 определяются по следующим выражениям – R12 = R12г + R12щ, R13 = R13г + R13щ и
R14 = R14г + R14щ, причем R11 = R12 |
и R13 = R14 вследствие симметрии щетки и |
|||||||||||
щеткодержателя. |
|
|
|
|
|
|
|
|
|
|
|
|
R13г |
|
|
h1 |
; |
|
(5) |
||||||
2 |
l h |
|
||||||||||
|
|
|
|
г |
|
2 2 |
|
|
|
|
||
R13щ |
|
h4 h1 |
|
; |
|
(6) |
||||||
|
2 |
|
l h |
|
||||||||
|
|
|
|
|
щ 2 3 |
|
||||||
R13 |
h1 |
|
|
|
|
h4 |
h1 |
. |
(7) |
|||
2 l |
|
|
|
2 |
|
|||||||
|
h |
|
|
|
|
l h |
|
|||||
|
г 2 |
2 |
|
|
|
|
|
щ 2 3 |
|
Тепловые потоки P11, P12, P13, P14 разнонаправлены, вследствие чего сопротивления, встречающиеся на их пути, представляют собой цепь с параллельным соединением элементов (рис. 4).
P1
R11
R12
R13
R14
Рис. 4. Параллельное соединение тепловых сопротивлений на пути теплового потока от графита к воздуху через щеткодержатель
Общее сопротивление для площади щетки, находящейся под щеткодержателем и самого тела щеткодержателя определяем по выражению:
R1общ |
|
|
|
|
|
|
1 |
|
|
|
|
|
|
|
. |
(8) |
|
|
|
|
|
|
|
|
|
|
|
|
|||||||
|
2 |
|
|
|
|
|
|
2 |
|
|
|||||||
|
|
|
|
|
|
|
|
|
|
|
|
|
|
|
|||
|
|
|
|
|
|
|
|
|
|
|
|
|
|
|
|
|
|
|
|
|
h2 |
|
h3 h2 |
|
|
h1 |
|
h4 h1 |
|
|
|||||
|
|
|
|
|
|
|
|||||||||||
|
|
|
2 l h |
2 |
l h |
|
|
|
2 l h |
2 |
l h |
|
|||||
|
|
|
г 2 1 |
|
|
щ 2 4 |
|
|
|
г 2 2 |
|
|
щ 2 3 |
|
180
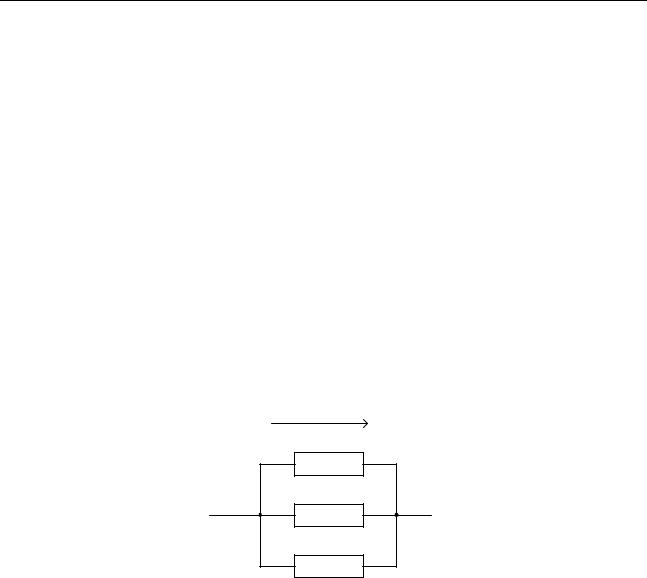
ТРАНСВУЗ – 2015
Тепловое сопротивление щетки на пути тепловых потоков P21, P22, P23, P24, P25 с верхнего торца щетки, не контактирующего с коллектором, рассчитывается по формуле:
R2общ |
|
|
|
|
|
l1 |
|
|
|
. |
(9) |
|
щ |
(2l h |
2l h |
h h ) |
|||||||
|
|
|
1 |
1 |
1 |
2 |
1 |
2 |
|
|
Тепловое сопротивление щетки на пути тепловых потоков P31, P32, P33, P34 со стороны щетки, контактирующей с коллектором, рассчитывается по формуле:
R3общ |
|
|
|
|
|
l3 |
|
|
|
. |
(10) |
|
щ |
(2l h |
2l h |
h h ) |
|||||||
|
|
|
3 |
1 |
3 |
2 |
1 |
2 |
|
|
Тепловое сопротивление на пути потока P35 не учитывается, так как поток направлен в пластину коллектора, как указано в работе [7]. Для расчета общего теплового сопротивления, необходимо найти общее сопротивление при параллельном соединении R1общ, R2общ, R3общ, как показано на рис. 5.
P1
R1общ
R2общ
R3общ
Рис. 5. Параллельное соединение тепловых сопротивлений на пути теплового потока от графита к воздуху через щеткодержатель
Из уравнения (11) можно определить сопротивление R1:
R1 |
|
1 |
|
1 |
|
1 |
. |
(11) |
|
|
|
||||||
R1общ |
R2общ |
|
||||||
|
|
|
|
R3общ |
|
Тепловое сопротивление R5 учитывает грань щетки со стороны контакта «щетка – коллектор», которое можно рассчитать по формуле:
R5 |
|
l1 l2 |
l3 |
. |
(12) |
||
|
|
||||||
|
|
|
щ |
2h h |
|
||
|
|
|
|
1 2 |
|
|
181

Ремонт и динамика подвижного состава
Уравнения для расчета тепловых сопротивлений щетки в щеткодержателе могут использоваться для составления математической модели тепловых процессов в КЩУ МПТ. Математическая модель позволяет рассчитывать превышения температур как в стационарных, так и в переходных режимах работы электродвигателя и может использоваться в системах технического диагностирования.
Список литературы
1.Glowacz, A. Recognition of Thermal Images of Direct Current Motor with Application of Area Perimeter Vector and Bayes Classifier. Measurement Science Review [Текст] / A. Glowacz, A. Glowacz, Z. Glowacz,– vol. 15, – No. 3, 2015, – pp. 119 – 126.
2.Sebok, M. Diagnostics of electric equipments by means of thermovision. Przeglad Elektrotechniczny [Текст] / M. Sebok, M. Gutten, M. Kucera.– vol. 87 (10), 2011, – pp. 313 – 317.
3.Совершенствование технологии диагностирования технического состояния коллекторно-щеточного узла тяговых электродвигателей электровозов: монография [Текст] / В. В. Харламов, П. К. Шкодун и др. – Омск, 2015. – 198 с.
4.Термографические исследования коллекторно-щеточного узла тяговых электродвигателей подвижного состава [Текст] / В. В. Харламов, П. К. Шкодун и др. // Известия Транссиба. – Омск, 2014. – № 3 (19). – С. 44 – 50.
5.Харламов, В. В. Диагностирование состояния коммутации коллекторных электродвигателей с использованием прибора ПКК-5М [Текст] / В. В. Харламов, П. К. Шкодун, А. П. Афонин // Известия Транссиба. – Омск, 2011. – № 3 (7). – С. 52 – 57.
6.Сипайлов, Г. А. Тепловые, гидравлические и аэродинамические расчеты в электрических машинах [Текст] / Г. А. Сипайлов, Д. И. Санников, В. А. Жадан. – М.: Высшая школа, 1989. – 239 с.
7.Хольм, Р. Электрические контакты [Текст] / Р. Хольм. – М.: Иностранная литература, 1961. – 464 с.
182

ТРАНСВУЗ – 2015
УДК 629.424:621.001.5
Р. С. Барашков, М. Ю. Золотовский, В. А. Минаков
МЕТОДЫ ОПРЕДЕЛЕНИЯ СТЕПЕНИ ЗАГРЯЗНЕНИЯ ЦЕНТРОБЕЖНОГО ФИЛЬТРА МАСЛЯНОЙ СИСТЕМЫ ДИЗЕЛЯ ТИПА ПД1М
При работе дизеля масло загрязняется частицами пыли, износа деталей двигателя, продуктами неполного сгорания (кокс, сажа) и окисления. Продукты загрязнения разделяются на органические и неорганические. Органические состоят из термического разложения, окисления и полимеризации масла и продуктов неполного сгорания, неорганические – из почвенной пыли и частиц износа деталей. Будучи загрязненным, масло, предназначенное для уменьшения трения, само начинает ускорять износ смазываемых им трущихся деталей, поэтому очень важно вовремя улавливать и отделять от масла посторонние примеси [1].
Для очистки масла тепловозные дизели снабжаются масляными фильтрами. В основном масляные системы тепловозных дизелей имеют три типа фильтрующих элементов: фильтр тонкой очистки (ФТО), фильтр грубой очистки (ФГО) и центробежный фильтр (ЦФ).
Наибольший эффект очистки масла достигается посредством применения ЦФ. Центробежные аппараты обеспечивают достаточную тонкость очистки масла и возможность их неоднократного применения. Под действием центробежных сил механические примеси в масле, имеющие больший удельный вес, чем само масло, отбрасываются на стенки неподвижного корпуса фильтра и откладываются на его поверхности в виде густой масляной суспензии обычно черного цвета.
Плановый периодический осмотр, при котором осуществляется чистка и ремонт ЦФ, проводится при техническом обслуживании ТО-3, вне зависимости от технического состояния самого фильтра. Выявлено, что ЦФ засоряется раньше, чем наступает время его технического обслуживания, это приводит к понижению качества очистки масла, и как следствие к увеличению износа смазываемых им деталей.
183
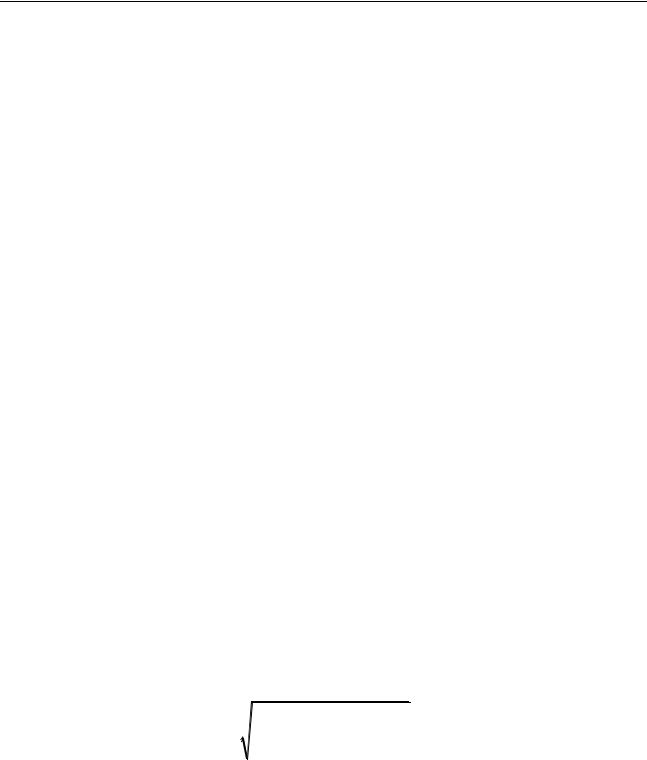
Ремонт и динамика подвижного состава
В 2013 году с «Московского отделения железной дороги ОАО «РЖД» была заявлена проблема, главной задачей которой являлась оценка технического состояния центробежного фильтра без его разборки. Для достижения этой задачи предлагается использовать следующие методы оценки технического состояния ЦФ:
–по выбегу ротора;
–по числу оборотов ротора;
–по изменению давления масла перед фильтром.
Контроль центробежного фильтра по выбегу ротора. Данный метод предполагает использование в качестве оценки технического состояния время выбега ротора после остановки дизеля. Для каждого ЦФ время (t – при чистом барабане ротора, t1 – при загрязнении барабана ротора в условиях эксплуатации) определяется опытным путем. При этом необходимо рассчитать разницу показания времени:
k |
t1 |
. |
(1) |
|
|||
|
t |
|
Отсюда следует, что при регистрации времени выбега ротора ЦФ необходимо учитывать равенство при котором, необходимо проводить работы по техническому обслуживанию ротора, сек.
t1 k t. |
(2) |
Контроль фильтра по числу оборотов ротора. Данный вид контроля основан на регистрации частоты оборотов ротора ЦФ с помощью установки считывающего устройства на блок фильтра и крепления магнитной ленты на барабан ротора. Частота оборотов в зависимости от внутреннего слоя загрязнения будет изменятся в соответствии с уравнением, мин-1 [3]:
n = |
1800 g |
|
Qp (Rц |
– rс |
) |
, |
(3) |
|
B π2 |
(R + r ) |
|||||||
|
|
|
|
|||||
|
|
|
ц |
с |
|
|
|
где g – ускорение силы тяжести, м/сек2;
Qp – производительность центрифуги, м3/ч;
Rц.− радиус внутренней поверхности ротора, мм; В – число осветления масла, см/сек;
rc – внутренний радиус слоя жидкости в роторе, мм; Ω – рабочий объем ротора.
184
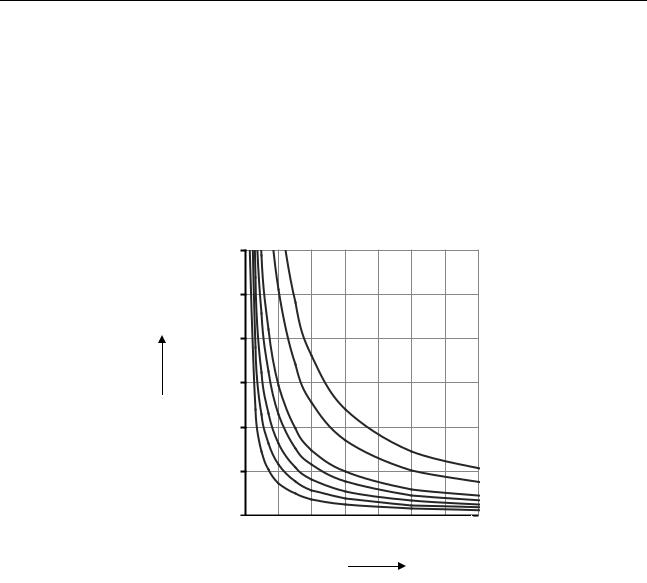
|
ТРАНСВУЗ – 2015 |
Отсюда рабочий объем ротора выражается как, мм3: |
|
= π·hp (Rц2 – rc2), |
(4) |
где hp – высота ротора, мм.
На рис. 1 представлена полученная зависимость частоты оборотов (n) от внутреннего слоя осадка в роторе (Rц – rс). Данные рассчитаны для параметров центрифуги дизеля типа ПД1М. Производительность рассматриваемой центрифуги равна 2,3 – 3 м3/ч., поэтому в расчетах представлены все варианты [4].
Основной |
|
|
|
|
|
|
Основной |
|
|
|
|
|
|
Основной |
|
|
|
|
|
|
Основной |
|
|
Q1 |
|
|
|
|
|
|
|
|
|
|
|
|
Q2 |
|
|
|
|
nОсновной |
|
|
|
|
|
|
|
Q |
Q4 |
Q3 |
|
|
|
ОсновнойQ |
5 |
|
|
|
|
|
6 |
|
|
|
|
|
|
Q7 |
|
|
|
|
|
|
Основной |
|
|
|
|
|
|
|
0 |
5 |
10 |
15 |
20 |
25 |
R
Q1 – 3 м3/ч; Q2 –2,9м3/ч; Q3 – 2,8 м3/ч; Q4 – 2,7 м3/ч; Q5 – 2,6 м3/ч;
Q6 – 2,5 м3/ч; Q7 –2,4 м3/ч
Рис. 1. Отношение числа оборотов центрифуги к радиусу отложения
Изменение частоты оборотов относительно нарастания загрязняющего слоя весьма значительна. При контроле изменения частоты оборотов ротора центрифуги, можно получить количественную оценку степени загрязненности барабана фильтра, что позволит определять рациональный период чистки ЦФ без вывода тепловоза из эксплуатации. Контроль по изменению давления масла перед ЦФ. Контроль по изменению давления масла на входе в фильтр, позволит определять загрязненность сопел центрифуги. Масло прокачивается насосом под давлением 4,5
185
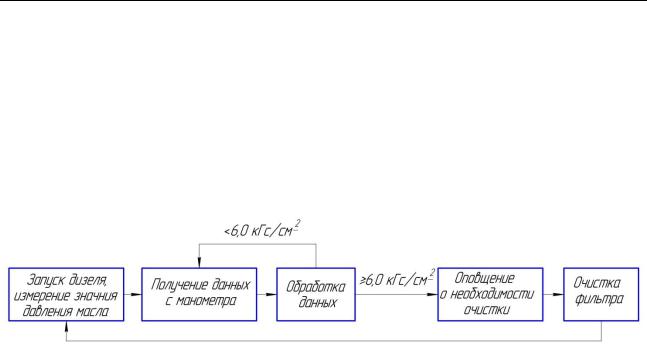
Ремонт и динамика подвижного состава
–5,5 кГс/см2, при засорении сопел давление масла возрастает и может достигать критического (6,5 кГс/см2) [4]. Часто происходит частичное засорение сопел и масло может не превышать давление 6,5 кГс/см2, при этом фильтр находится в эксплуатации, не отвечая требованиям качества очистки масла. Во избежание такого рода неисправности предлагается использование электронных датчиков давления (манометров), которые при превышении давления в 6 кГс/см2, оповещают о необходимости чистки ЦФ, в соответствии с алгоритмом на рис. 2.
Рис. 2. Алгоритм контроля давления на входе ЦФ
Таки образом, использование предложенных методов позволит достичь более качественной очистки моторного масла и снизить износ смазываемых им трущихся деталей, за счет своевременного обслуживания центробежного фильтра.
Список литературы
1. Овчаренко, С. М. Моделирование работы и оценка эффективности систем очистки моторного масла различных серий тепловозов [Текст] / С. М. Овчаренко. – Ростов-на-Дону: Вестник РГУПС. – №1, 2006 г., – С. 21 – 27.
2.Качанова, Л. С. Совершенствование очистки отработанного моторного масла центробежными аппаратами. дис. канд. тех. Наук [Текст] / Л. С. Качанова. – Азово-черноморская государственная Агро-инженерная академия. – Зерноград, 2004.
3.Григорьев, М. А. Очистка масел и топлива в автотракторных двигателях [Текст] / М. А. Григорьев. – М.: Машиностроение, 1970. – 271 с.
4. Аронов, П. М. Тепловозы ТЭМ1 и ТЭМ2 [Текст] / под ред. Е. Ф. Сдобникова. – М., «Транспорт», 1978.
186

ТРАНСВУЗ – 2015
УДК 629.4.015
К. С. Синюгин
МОДЕЛИРОВАНИЕ УСТРОЙСТВ ЭЛЕКТРИЧЕСКОЙ КОММУТАЦИОННОЙ АППАРАТУРЫ ЭЛЕКТРОПОДВИЖНОГО СОСТАВА В SIMULATIONX
Рассматривая вопросы компьютерного моделирования устройств электрической аппаратуры электроподвижного состава, приводится классификация характерных элементов и их программная реализация в среде SimulationX.
Электрические коммутационные аппараты являются ключевым элементом построения систем управления электрическим подвижным составом (ЭПС), от надежности работы которых во многом зависит надежность ЭПС в целом. В результате эксплуатации электровозов новых серий (2ЭС6, ЭП2К и других) были выявлены различные недостатки в конструкции электрических аппаратов. Как показали опыты эксплуатации электровозов традиционных и новых серий (2ЭС6, ЭП2К и других), конструкция электрических аппаратов не является совершенной, что требует проведения соответствующих исследований, направленных на устранение конструкционных недостатков, а также создание эффективных средств контроля и диагностирования при ремонте [1].
Моделирование позволяет исследовать суть сложных процессов и явлений с помощью экспериментов не с реальной системой, а с ее моделью. Известно, что для принятия разумного решения по организации работы системы не обязательно знание всех характеристик системы, всегда достаточен анализ ее упрощенного, приближенного представления [2].
Рассмотрим моделирование устройств электрической коммутационной аппаратуры ЭПС на примере групповых переключателей ПКГ-4 и ПКГ-6. В данных аппаратах можно выделить два основных узла это контакторный элемент (см. рис. 1) и привод (см. рис. 2).
Основной задачей ставим создание имитации работы деталей контакторного элемента в компьютерной программе моделирования,
187
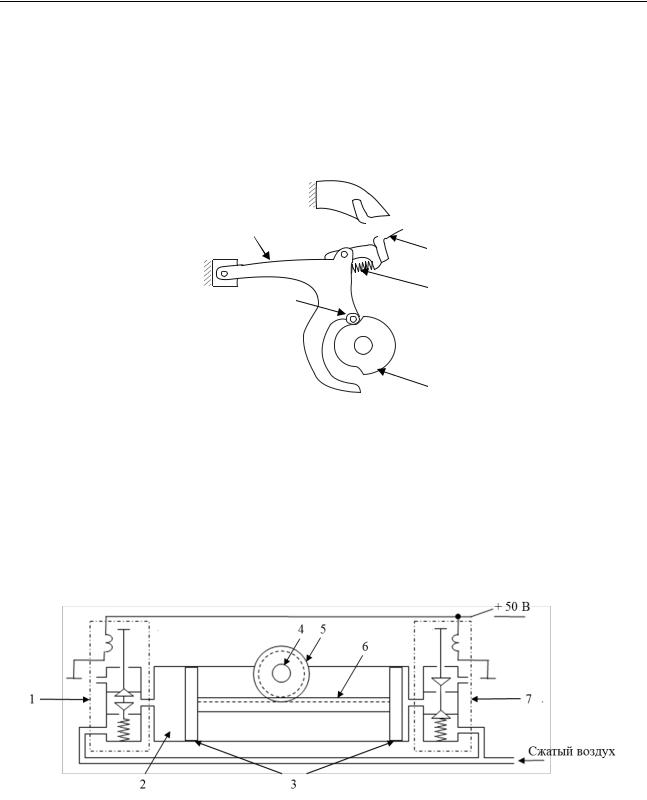
Ремонт и динамика подвижного состава
симуляции и тестирования. Это необходимо для анализа движения, корректировки данных и формулирования выводов относительно тех или иных режимов работы устройства при разных условиях. Включение элементов привода в схему, вместо упрощенной подачи усилия на кулачковый вал, дает расширенное управление переходными процессами модели аппарата.
1 2
4
3 |
5 |
|
6 7
1 – кронштейн подвижного контакта; 2 – неподвижный контакт; 3 – ролик; 4 – подвижный контакт; 5 – притирающая пружина; 6 – кулачковый вал; 7 – кулачковая шайба
Рис. 1. Упрощенная схема контакторного элемента групповых переключателей ПКГ-4 и ПКГ-6
1 – вентиль выключающего типа; 2 – пневматический цилиндр; 3 – поршни; 4 – кулачковый вал; 5 – зубчатое колесо; 6 – зубчатая рейка; 7 – вентиль включающего типа.
Рис. 2. Упрощенная схема привода групповых переключателей ПКГ-4 и ПКГ-6
188
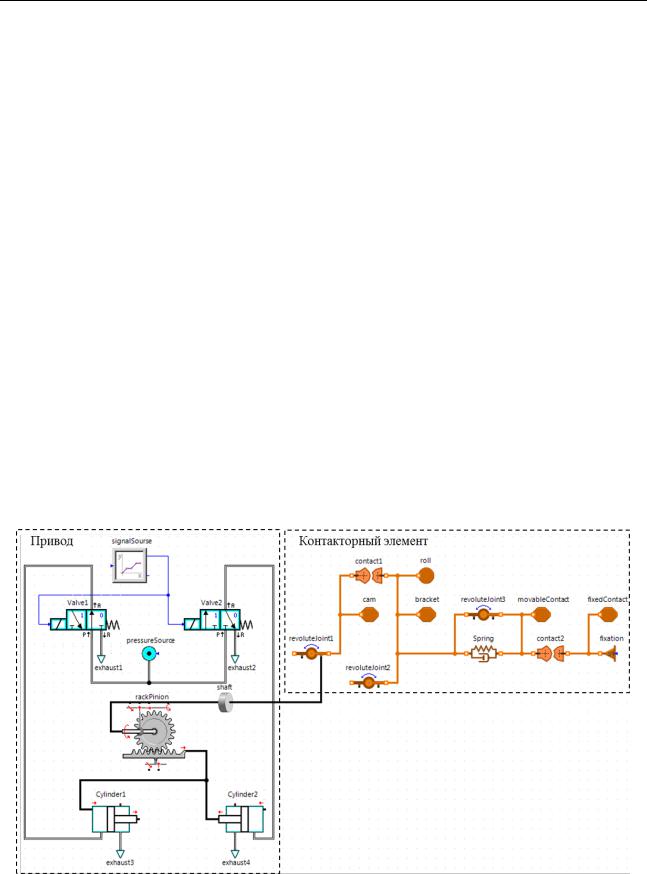
ТРАНСВУЗ – 2015
Поскольку для построения модели необходимо было связать разноплановые элементы с возможностью просматривать двухмерное движение ключевых узлов, то удачно подошла по своей простоте, удобству и функциональности программа SimulationX.
SimulationX [3] – это междисциплинарный программный комплекс (CAE– Software) для моделирования физико-технических объектов и систем, который разработан и продается на коммерческой основе фирмой ITI GmbH из Дрездена с 2000 года. SimulationX является преемником программы ITI-SIM, первая версия которой появилась в 1993 году. Ученые и инженеры, работающие в промышленности и сфере образования, используют этот инструмент для разработки, моделирования, симулирования, анализа и виртуального тестирования сложных мехатронных систем. На единой платформе программа моделирует поведение и взаимодействие различных физических объектов механики (1D и 3D), приводной техники, электрических, гидравлических, пневматических и термодинамических систем, а также магнетизма и аналоговых и цифровых систем управления.
Модель на рис. 3 состоит из стандартных элементов механики, пневматики и сигнального блока библиотеки системы SimulationX.
Рис. 3. Схема упрощенной модели групповых переключателей ПКГ-4 и ПКГ-6, построенная в SimulationX
189