
ТРАНСВУЗ-2015.Часть 1
.pdf
Ремонт и динамика подвижного состава
Для безразборного определения технического состояния и прогнозирования остаточного ресурса таких узлов наиболее технологичными и информативными средствами являются аппаратно-программные комплексы вибродиагностики – вибродиагностическое оборудование (ВДО). Такие средства могут быть различного исполнения и обладать различными функциональными возможностями [1]. Комплексы, например, могут быть стационарными, передвижными и переносными (ручными). По возможностям ВДО можно разделить на две большие группы:
1)оборудование, выполняющее контрольные функции – определяется наличие дефекта и степень его развития;
2)оборудование, выполняющие все диагностические функции по ГОСТ 20911-89 (контроль технического состояния; поиск места и определение причин отказа; прогнозирование технического состояния).
ВДО, имеющее возможности глубокого диагностирования (идентификация нескольких видов дефектов и степени их развития) и осуществляющее прогнозирование технического состояния можно отнести к классу экспертных систем.
К современному вибродиагностическому оборудованию предъявляется достаточно много серьезных требований, как в аппаратной, так и программной части. Основные требования к аппаратной части задаются метрологическими характеристиками ВДО, которое должно являться средством измерения параметров вибрации.
К основным метрологическим характеристикам можно отнести:
– динамический диапазон измерения входного сигнала;
– рабочий диапазон частот;
– неравномерность амплитудно-частотной характеристики;
– разрешающая способность вычисления спектра; и другие характеристики [2].
Важны и такие показатели оборудования, как общее количество каналов измерения, количество каналов одновременного измерения, массо-габаритные характеристики, рабочий диапазон температур и т.д.
Функциональные возможности во многом зависят и от программного обеспечения, которое условно можно разделить на две части:
– программа для измерения и предварительной обработки сигналов
– диагностическая программа для идентификации дефектов.
140

ТРАНСВУЗ – 2015
Сборщики информации, как правило, содержат только первую часть, а вторая располагается на персональном компьютере.
Стремление разработчиков сохранить преимущества сборщиков информации и при этом не потерять функциональные возможности полноценного ВДО, что особенно важно для локомотиворемонтных предприятий, привело к созданию малогабаритного (мобильного) комплекса вибродиагностики «Эксперт М».
Комплекс предназначен для измерения и анализа параметров вибрации, частоты вращения и других физических величин с целью диагностирования машин и оборудования. При установке соответствующей программы возможно использование комплекса для балансировки роторов в собственных опорах.
Особенностями комплекса являются:
–параллельный (одновременный) съем информации по 4 м каналам, что сокращает время диагностирования КМБ с пятнадцати до четырех минут (вместе с подготовительными операциями);
–получение результатов диагностирования непосредственно у объекта (неразрывная технология);
–подтверждаемость результатов диагностирования 90 % и выше;
–расширенный частотный диапазон (2 Гц – 200 кГц), позволяющий работать с датчиками акустической эмиссии;
–расширенный динамический диапазон (120 дБ);
–высокая мобильность (габариты 300 × 200 × 50 мм, масса не более 1,6 кг);
–широкий диапазон рабочих температур (– 20 С0 +50 С0);
–большое время автономной работы (не менее 8 часов);
–прослушивание вибросигналов с объекта;
–сенсорное управление;
–автотестирование устройства и программного обеспечения;
–возможность объединения комплексов в сеть.
Среди функциональных возможностей можно отметить:
–определение до 12 видов дефектов подшипников и зубчатых зацеплений;
–время диагностирования 4х точек не более 40 с.
–определение недостатка смазки и посторонних включений в смазке;
–определение частоты вращения по сигналам вибрации;
–прогнозирование времени безаварийной работы объекта;
141
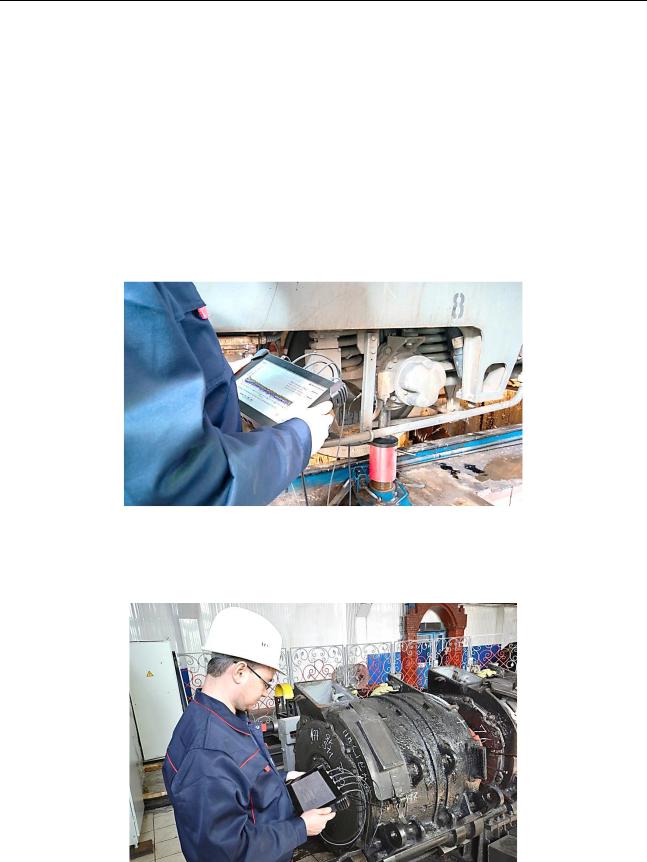
Ремонт и динамика подвижного состава
–возможность подключения датчиков температуры, давления и т.д.;
–возможность расширения количества каналов до 512;
–оперативная настройка на различные типы объектов;
–возможность поставки во взрывобезопасном исполнении «1Ех ib IIA T4
Gb»;
– вариант стационарного и встраиваемого исполнения.
При ремонте локомотивов диагностирование может осуществляться при входном контроле, например, на станции испытания тяговых двигателей, после сборки КМБ, под локомотивом при различных видах ТО и ТР (рис. 1, рис. 2).
Рис. 1. Диагностирование КМБ локомотива 2ЭС6 «Синара» комплексом «Эксперт М»
Рис.2. Диагностирование тягового двигателя на испытательной станции
142

ТРАНСВУЗ – 2015
Среди ближайших аналогов по функциональным возможностям и габаритам можно назвать анализатор вибрации CSI 2140 американской компании SCI, объявленная стоимость которого в России более 1,5 млн. руб. (в ценах октября 2014 года) за одну только аппаратную часть. Стоимость «Эксперт М» вместе с базовым программным обеспечением в разы меньше.
Свойства присущие описанному комплексу, дают основания поставить это оборудование на передовые позиции в своем классе.
Список литературы
1.Тэттэр, В. Ю. Вибродиагностика роторных механических узлов подвижного состава железных дорог [Текст] / В. Ю. Тэттэр // – Омск: ООО
«Издательский центр «Омский научный вестник»», 2011. – 120 с.
2.Тэттэр, В. Ю. Прикладные вопросы диагностирования роторных узлов по вибрации [Текст] / В. Ю. Тэттэр, А. Ю. Тэттэр // LAP LAMBERT Academic Publishing Saarbrucken. 2013. – 131 с.
УДК 629.421.1
А. П. Буйносов, К. А. Стаценко, К. С. Жижакин, А. П. Пахомов
КОНТРОЛЬ ШЕРОХОВАТОСТИ ВНУТРЕННЕЙ ПОВЕРХНОСТИ БАНДАЖЕЙ КОЛЕСНЫХ ПАР ЭЛЕКТРОВОЗОВ
Рассмотрены факторы, влияющие на прочность посадки бандажа на ободе колесного центра. Описано разработанное устройство для контроля шероховатости посадочной поверхности бандажа электровоза на карусельном станке
Перспектива роста средней технической скорости, нагрузок на ось и мощности локомотивов диктует необходимость повышения требований по отношению к колесным парам по причине возрастающих температурных режимов работы и прочностных напряжений. Повышенные усилия нажатия тормозных колодок увеличат вероятность снижения прочности соединения
143

Ремонт и динамика подвижного состава
«бандаж-колесный центр» и проворота бандажей, что в случае их сползания может привести к нарушению безопасности движения.
Основными факторы, влияющими на прочность посадки бандажа на ободе колесного центра, являются:
–величина натяга бандажа на ободе колесного центра [2…10], определяющая контактное давление элементов сопряжения, за счет которого обеспечивается прочность посадки;
–величина конусности посадочных поверхностей, определяющая площадь фактического контакта, влияющего на силу трения поверхностей и, следовательно, на прочность посадки;
–величина овальности посадочных поверхностей. Так же, как и конусность определяет площадь фактического контакта, и, значит, прочность посадки. По данным исследователей [2, 3], значения овальности и конусности бандажей в 2 раза превышающие нормативные приводят к уменьшению площади фактического контакта на 60…70 %. Величины конусности и овальности могут достигать значений, приводящих к отрицательному локальному натягу. Из-за коррозии в образовавшемся зазоре фактическая площадь контакта еще более уменьшается;
–величина шероховатости поверхностей сопряжения. Чем грубее обработаны поверхности посадки бандажа и колесного центра и выше гребешки, тем меньше будет натяг, и прочность посадки, поскольку на большую величину просядут выступы обоих поверхностей и, следовательно, потребуется меньшая температура бандажа для его ослабления. Кроме того, с увеличением шероховатости уменьшается площадь контакта трущихся поверхностей. По оценкам специалистов [2, 3] действительная площадь контакта при грубой (3 класс чистоты) обработке посадочных поверхностей снижается на 70 %;
–температура и продолжительность нагревания при насадке бандажей. При длительном нагревании в условиях высокой (более 300 °С) температуры у бандажей ухудшаются механические свойства. Будучи насаженными на обод колесного центра с большим натягом, такие бандажи испытывают значительные напряжения и развальцовываются. При этом по оценкам исследователей [2, 3] установленная инструкцией [1] максимальная температура нагрева при посадке (300 °С) завышена, а для расширения бандажа
144

ТРАНСВУЗ – 2015
на величину натяга и некоторого приращения для свободной насадки бандажа достаточно температуры 150 °С;
–истирание посадочных поверхностей в результате их относительного перемещения при циклическом нагружении. Такое истирание уменьшает натяг на участках скольжения и несущую способность соединения;
–фреттинг-коррозия поверхностей сопряжения бандажа и обода колесного центра способствует снижению прочности посадки в результате коррозионного износа.
Представляют интерес факторы, которые до проведения соответствующих исследований ошибочно рассматривались, как существенно влияющие на прочность посадки бандажа на ободе:
–количество проворотов бандажей не зависит от места расположения колесной пары под локомотивом. Случаи ослабления посадок равновероятны, как для крайних, так и для промежуточных колесных пар;
–ослабление бандажей не зависит от их толщины, то есть накопление остаточной деформации и снижение натяга при малой толщине бандажа не может быть основной причиной его ослабления;
–«смятие» металла бандажа и обода не может возникнуть даже при наиболее неблагоприятных условиях посадки. При наибольшей толщине и значении натяга напряжение на внутренней поверхности бандажа не превышает предела текучести стали и не вызывает остаточных деформаций;
–остаточное «смятие» металла бандажа от действия реакции рельса не может служить его причиной ослабления. Глубина проникновения пластической деформации значительно меньше предельно допустимой в эксплуатации;
–тепловое воздействие на бандажи не влияет на их ослабление. В результате расчетов теплового ослабления бандажей, выполненных по методике ВНИИЖТа для различных уклонов и толщин бандажа, установлено, что наибольшее снижение натяга при экстренном торможении – 0,5 мм, при длительном – 0,8 мм. Оставшийся натяг исключает возможность проворота бандажа. Столь незначительное уменьшение величины натяга при торможении объясняется зависимостью ее от разности температур посадочных поверхностей бандажа и обода, причем при тонком бандаже эта разность
145

Ремонт и динамика подвижного состава
меньше, чем при толстом бандаже. Это компенсирует воздействие фактора уменьшения фактического натяга при износе бандажа.
Из вышеперечисленного следует, что основными факторами, влияющими на прочность посадки, следует считать несоблюдение микро- и макрогеометрии посадочных поверхностей бандажа и обода при их обработке и нарушение установленной величины натяга. Эти причины при одновременном действии других факторов (нагрев бандажа в эксплуатации и т.д.) и приводят к ослаблению и провороту бандажа. Поэтому следует разработать ряд мероприятий технологического характера, направленных на обеспечение соблюдения нормированных значений натяга и геометрии посадочных поверхностей.
Существенное влияние на прочность посадки бандажей оказывает чистота обработки посадочных поверхностей. В инструкции ЦТ-329 указано, что внутреннюю поверхность бандажа следует «расточить с обеспечением шероховатости RА не более 5 мкм». Однако объективного метода контроля этого параметра инструкцией ЦТ-329 не предложено и в настоящее время для оценки чистоты обработки поверхностей применяется непосредственное сравнение с образцами (эталонами). Этот метод визуальный и поэтому субъективный.
Авторами разработано специализированное устройство для измерения посадочной поверхности бандажа на карусельном станке (рис. 1).
Рис. 1. Устройство для измерения шероховатости посадочной поверхности бандажа
146

ТРАНСВУЗ – 2015
Измерительная головка 1 типа ИРПВ, 1 класс точности ТУ 2-034-229-88, установлена с помощью зажима 2 для крепления стержней под прямым углом на трубке 3, которая с помощью болтов 4 закреплена на рейке 5, имеющей упор 6. Упор позволяет фиксировать одинаковое расстояние между измерительной головкой и контролируемой поверхностью при установке приспособления.
Для проведения измерений необходимо отвинтить гайку 7, шпильку 8 опустить до упора, гайку 9 и освободившуюся рейку 10 повернуть на 90 °.
Подвести приспособление под бандаж, установленный на станке, вернуть рейку 10 в исходное положение и с помощью гаек 7 и 11 зафиксировать устройство (рис. 1).
Установить с помощью рычага 12 стрелку измерительной головки в нулевое положение. Повернуть зажим 2 и трубку 3 вместе с державкой 13 и закрепленной в ней головкой относительно оси трубки до касания наконечником 14 поверхности бандажа, о чем можно судить по реакции стрелки. Проверить надежность зажатия винта зажима и, вращая против часовой стрелки винт микроподачи 15, произвести измерение шероховатости поверхности.
Устройство делает доступными для контроля все участки посадочной поверхности бандажа непосредственно на станке. Позволяет осуществлять плавную подводку иглы измерительной головки к изделию. Поскольку при этом соблюдаются все требования по эксплуатации измерительной головки, то предел допускаемой погрешности следует считать равным указанному в паспорте, т.е. 1 мкм.
Список литературы
1.Инструкция по формированию, ремонту и содержанию колесных пар тягового подвижного состава железных дорог колеи 1520 мм с изменениями и дополнениями, утвержденными указанием МПС России от 23.08.2000 – № К- 2273у: ЦТ/329. – М.: Транспорт, 2000. – 78 с.
2.Стаценко, К. А. Повышение долговечности колесных пар электровозов технологическими методами: Дисс. на соискание уч. ст. канд. техн. наук. [Текст] / К. А. Стаценко. – Екатеринбург, 2004. – 159 с.
147

Ремонт и динамика подвижного состава
3.Буйносов, А. П. Методы повышения ресурса бандажей колесных пар тягового подвижного состава: Дисс. на соискание уч. ст. докт. техн. наук [Текст] / А. П. Буйносов. – Екатеринбург, 2011. – 455 с.
4.Методика контроля величины натяга бандажа, обеспечивающая надежность соединения «бандаж-обод» колесного центра локомотива [Текст] / А. П. Буйносов, Е. В. Бган и др.// Вестник Курганского государственного университета. Серия: Технические науки. 2013. – № 29. – С. 23 – 27.
5.Буйносов, А. П. Определение натяга бандажа на ободе колесного
центра электровоза с помощью ультразвуковых импульсов [Текст] / А. П. Буйносов, Е. В. Бган, К. А. Стаценко // Известия Тульского государственного университета. Технические науки. 2012. – № 2. – С. 146 – 156.
6. Буйносов, А. П Повышение прочности посадки деталей с натягом сформированных колесных пар электровозов [Текст] / А. П. Буйносов, Е. В. Бган, К. А. Стаценко // Научно-технический вестник Поволжья. 2012. –
№5. – С. 118 – 120.
7.Буйносов, А. П. Повышение ресурса колесных пар электровозов
технологическими методами: Монография [Текст] / А. П. Буйносов, К.А. Стаценко. – Саарбрюккен, Germany (Германия): Изд-во «LAP LAMBERT Academic Publishing», 2012. – 215 с.
8. Буйносов, А. П. Определение натяга пары «бандаж-обод» с помощью ультразвуковых импульсов [Текст] / А. П. Буйносов, К. А. Стаценко, Н. И. Сергеев // Транспорт Урала. 2004. – № 3 (3). – С. 31 – 37.
9. Буйносов, А. П. Методика определения прочности посадки деталей с натягом у сформированных колесных пар локомотивов [Текст] / А. П. Буйносов, Е. В. Бган, К. А. Стаценко // Естественные и технические науки. 2012. – № 6. – С. 586 – 588.
10. Буйносов, А. П. Методика определения величины натяга бандажа на ободе колесного центра локомотива с помощью ультразвуковых импульсов [Текст] / А. П. Буйносов, К. А. Стаценко // Проблемы машиностроения и автоматизации. 2012. – № 4. – С. 100 – 106.
148

ТРАНСВУЗ – 2015
УДК 629.421.1
А. П. Буйносов, К. А. Стаценко, К. С. Жижакин, А. П. Пахомов
ВЛИЯНИЕ ШЕРОХОВАТОСТИ ПОСАДОЧНОЙ ПОВЕРХНОСТИ БАНДАЖА НА ПРОЧНОСТЬ ЕГО ПОСАДКИ НА ОБОДЕ КОЛЕСНОГО ЦЕНТРА
В статье исследовано влияние величины шероховатости посадочных поверхностей на прочность посадки бандажей на основании данных опытной эксплуатации. Определено допустимое значение шероховатости посадочной поверхности бандажа колесной пары в эксплуатации
На железных дорогах Российской Федерации от 2 до 6 % всех эксплуатируемых бандажей выходят из строя из-за ослабления их посадки на ободе колесного центра [1…9]. С целью определения зависимости интенсивности отказов бандажей от чистоты обработки их внутренних поверхностей велись наблюдения за 905 колесными парами грузовых электровозов, у которых величины шероховатости посадочных поверхностей были замерены устройством, разработанным авторами. У этих колесных пар согласно при формировании придерживались допустимых по инструкции ЦТ329 [10] величин овальности, конусности и натяга бандажа на ободе колесного центра. За каждым бандажом до определенного пробега велись наблюдения в эксплуатации и фиксировались случаи ослабления бандажа на колесном центре и пробег L от ремонта до проворота или ослабления бандажа на колесном центре. После отказа бандажей наблюдения прекращались.
Для определения зависимости отказов бандажей от пробега для различных величин шероховатости внутренних поверхностей бандажей RZ, полученный статистический материал был разбит на группы, соответствующие изменению величины шероховатости. Отказ бандажа при фиксированных значениях наработки является случайной величиной. Поэтому определение зависимостей этого контролируемого параметра от пробега L осуществлялись с помощью регрессионного анализа. Построение эмпирических регрессий в виде полей корреляции контролируемого параметра от пробега и их анализ показали,
149