
ТРАНСВУЗ-2015.Часть 1
.pdf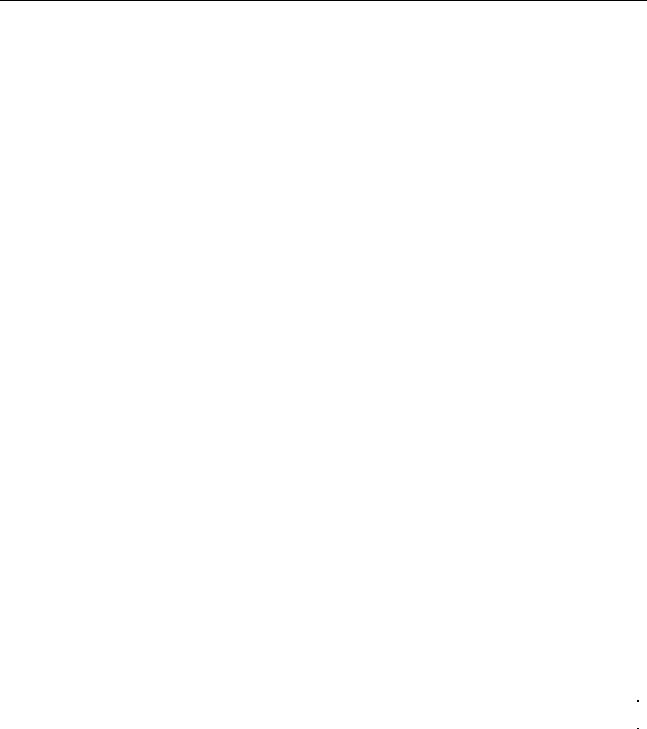
Ремонт и динамика подвижного состава
что все рассматриваемые зависимости могут быть аппроксимированы линейными функциями вида:
oi = λi L + b |
(1) |
где oi – количество отказов при фиксированном значении RZ; |
|
L – пробег от ремонта до проворота или ослабления (отказа); |
|
b – свободные члены уравнения; |
|
λi – угловые коэффициенты, определяют интенсивность отказов. Результаты расчета интенсивности отказов бандажей при различной
величине шероховатости бандажей сведены в табл. 1.
Таблица 1 Результаты расчета интенсивности отказов бандажей колесных пар
локомотивов при различной величине шероховатости их внутренних поверхностей
Номер |
Количество |
Величина |
Интенсивность |
|
исходных данных |
отказов бандажей |
|||
группы |
шероховатости RZ, мкм |
|||
(отказов), N |
λ, 1/106 км |
|||
|
|
|||
1 |
4 |
5 |
0,1211 |
|
|
|
|
|
|
2 |
13 |
10 |
0,131 |
|
|
|
|
|
|
3 |
26 |
15 |
0,1336 |
|
|
|
|
|
|
4 |
20 |
20 |
0,1354 |
|
|
|
|
|
|
5 |
9 |
25 |
0,1491 |
|
|
|
|
|
|
6 |
11 |
30 |
0,149 |
|
|
|
|
|
|
7 |
4 |
35 |
0,215 |
|
|
|
|
|
|
8 |
2 |
40 |
0,177 |
|
|
|
|
|
|
9 |
2 |
45 |
0,245 |
|
|
|
|
|
В первом приближении функцию интенсивности отказов бандажа можно представить в виде двух линейчатых отрезков, каждый из которых соответствует одному из двух характерных периодов – периодам «нормальной эксплуатации» и периоду интенсивного нарастания количества отказов:
|
λ1 (Rz ) A1 Rz B1, |
Rz |
Rz1 |
. |
(2) |
|
(Rz ) A2 (Rz R z1) B2 , |
Rz1 Rz |
|||
λ2 |
|
|
150

ТРАНСВУЗ – 2015
В выражения λ(RZ) входят пять коэффициентов А1, А2, Rz1, В1, В2, которые необходимо определить (оценить) по имеющейся экспериментальной зависимости λ (RZ). Однако часть этих коэффициентов является избыточной, так как условие непрерывности функции λ(RZ) следует граничное равенство:
|
λ1 (Rz1 ) λ2 (Rz1) . |
|
|
(3) |
Отсюда: |
|
|
|
|
|
B2 A1 Rz1 B1 . |
|
|
(4) |
Окончательно функция интенсивности отказов имеет вид: |
|
|||
|
λ1 (Rz ) A1 Rz B1, |
Rz Rz1 |
. |
(5) |
|
(Rz ) A2 (Rz R z1) A1 Rz1 B1, |
Rz1 Rz |
||
λ2 |
|
|
Здесь в выражении λ(RZ) входят уже только четыре постоянных коэффициента А1, А2, В1, Rz1, к определению которых и сводится задача аппроксимации эмпирической функции λ (RZ) теоретической функцией λ(RZ). Аппроксимация, т.е. замена эмпирической функции λ (RZ) теоретической λ(RZ), дает наиболее точные результаты в том случае, если интенсивность износа гребня, рассчитанная по функции λ (RZ) и λ(RZ), будет иметь минимальное расхождение, т.е. с учетом требований метода наименьших квадратов. Целевой функцией аппроксимации экспериментальных точек будет выражение
n |
|
2 |
|
min. |
(6) |
Z λ Rzi λi |
|
||||
i 1 |
|
|
|
|
|
При этом аппроксимация интенсивности отказов бандажей сводится к кусочно-линейной аппроксимации эмпирической функции λ (RZ), заданной n точками с координатами (RZi; λi). С учетом выражений (5) целевая функция (6) записывается в виде:
Z |
|
A R |
B |
λ |
2 |
|
A |
R |
R |
z1 |
A R |
B |
λ |
2 |
min. |
(7) |
|
1 zi |
1 |
i |
|
2 |
zi |
|
1 z1 |
1 |
i |
|
|
|
|||
|
Rzi Rz1 |
|
|
|
|
R z1 Rzi |
|
|
|
|
|
|
|
|
|
|
Целевая функция (7) зависит от четырех параметров А1, А2, В1, Rz1, однако, учитывая, что RZ1 совпадает с граничным значением линейных отрезков функции λ (RZ), область его применения ограничена набором RZ1; RZ2,
...; RZn, поэтому для понижения порядка системы неизвестных величин целесообразно зафиксировать значение RZ1 и определить локальный минимум
151

Ремонт и динамика подвижного состава
целевой функции Z, затем повторить решение при другом значении RZ1, выбрав то, которое обеспечивает наименьшее значение (глобальный минимум) целевой функции Z. Таким образом, при фиксированном значении RZ1 минимизируется функция трех аргументов Z(А1, А2, В1). При решении этой задачи был использован метод «скорейшего спуска», предложенный для численных методов решения уравнений.
Вычисления сводятся к построению последовательной группы чисел А1,К, А2,К, В1,К, где К = 2, 3, ... и так далее, исходя из групп А1,1, А2,1, В1,1, представляющих собой произвольную совокупность чисел, по возможности близкую к какому-либо из решений уравнения (7).
Группа чисел А1,К, А2,К, В1,К представляет собой значения известных коэффициентов (2).
Вычисления производятся по формулам
A1,k 1 |
A1,k |
λk |
|
Z A1,k ; A2,k ; B1,k |
|
|
||||
|
|
|
|
|
|
|||||
|
A1 |
|
|
|
|
|||||
|
|
|
|
|
|
|
|
|
|
|
A |
A |
λ |
|
|
|
Z A1,k ; A2,k |
; B1,k |
, |
(8) |
|
k |
|
|
|
|
||||||
|
|
|
|
|||||||
2,k 1 |
2,k |
|
|
|
A2 |
|
|
|
|
|
|
|
|
|
|
|
|
|
|
|
|
B1,k 1 |
B1,k |
λk |
|
Z A1,k ; A2,k ; B1,k |
|
|
||||
|
|
|
|
|
|
|||||
|
B1 |
|
|
|
|
|||||
|
|
|
|
|
|
|
|
|
|
где λk – масштабирующий коэффициент, определяемый по методу Ньютона.
λ |
|
|
|
|
|
|
|
Z A1,k ; A2,k |
; B1,k |
|
|
|
|
|
. |
(9) |
|
|
|
|
|
|
|
|
|
|
|
|
|
|
|||||
k |
|
Z A1,k ; A2,k |
; B1,k 2 |
|
Z A1,k ; A2,k |
; B1,k |
2 |
|
Z A1,k ; A2,k |
; B1,k 2 |
|||||||
|
|
|
|
||||||||||||||
|
|
|
|
|
|
|
|
|
|
|
|
|
|
|
|
|
|
|
|
A1 |
|
A2 |
|
B1 |
|
|
|
||||||||
|
|
|
|
|
|
|
|
|
|
|
|
|
|
||||
|
|
|
|
|
|
|
|
|
|
|
|
|
|
|
|
|
Частные производные функции (8) по параметрам А1, А2 и В1 вычисляем по уравнениям:
Z |
2 |
|
|
A R B λ |
|
R 2 |
|
A R R |
|
A R |
B λ |
R |
; |
|||||||||||||||
|
|
z1 |
||||||||||||||||||||||||||
A1 |
|
|
|
1 |
|
zi |
1 |
i |
|
zi |
|
|
2 |
zi |
|
1 |
z1 |
|
1 |
i |
z1 |
|
||||||
|
|
Rzi Rz1 |
|
|
|
|
|
|
|
R z1 Rzi |
|
|
|
|
|
|
|
|
|
|
|
|||||||
|
|
|
|
|
|
Z |
2 |
|
A |
R |
R |
|
A R |
B λ |
R |
R |
; |
|
|
(10) |
||||||||
|
|
|
|
|
|
|
|
|
||||||||||||||||||||
|
|
|
|
|
|
A2 |
|
2 |
|
zi |
|
z1 |
|
|
1 z1 |
1 |
|
i |
zi |
|
z1 |
|
|
|
|
|||
|
|
|
|
|
|
Rz1 Rzi |
|
|
|
|
|
|
|
|
|
|
|
|
|
|
|
|
|
|
|
|||
|
|
Z |
2 |
|
A R B λ |
2 |
|
A R R |
|
A R |
B λ . |
|
||||||||||||||||
|
|
|
z1 |
|
||||||||||||||||||||||||
|
|
B1 |
1 |
zi |
1 |
|
i |
|
|
|
2 |
zi |
|
1 |
z1 |
|
1 |
i |
|
|
||||||||
|
|
Rzi Rz1 |
|
|
|
|
|
|
|
|
R z1 Rzi |
|
|
|
|
|
|
|
|
|
|
|
152

ТРАНСВУЗ – 2015
Результаты расчета параметров зависимости интенсивности отказов бандажей от величины шероховатости их внутренних поверхностей при минимальном полученном значении целевой функции приведены в табл. 2.
Таблица 2 Результаты расчета параметров зависимости интенсивности отказов бандажей
от величины шероховатости их внутренних поверхностей при минимальном полученном значении целевой функции
|
Коэффициенты линейных функций |
|
|||
Величина |
|
λ(RZ) |
|
Целевая |
|
|
|
|
|
||
шероховатости |
|
|
|
функция |
|
A1, 1/(106 |
A2, 1/104 |
|
|||
RZ1, мкм |
В1, 1/106 км |
Z, (1/106 км)2 |
|||
км мкм) |
км мкм) |
||||
|
|
|
|||
|
|
|
|
|
|
25,71 |
0,0009 |
0,0044 |
0,0352 |
0,3125 |
|
|
|
|
|
|
Таким образом, величина RZ = 25,71 мкм – пороговая, после которой имеет место резкое возрастание удельного количества отказов. Предельно допустимой величиной шероховатости следует считать RZ = 25 мкм в соответствии с рядом числовых значений параметра шероховатости RZ . Для ее обеспечения следует использовать разработанное автором устройство, точность измерения которого, равная 1 мкм, недоступна для применяемого визуального способа контроля величины шероховатости.
Список литературы
1.Стаценко, К. А. Повышение долговечности колесных пар электровозов технологическими методами: Дисс. на соискание уч. ст. канд. техн. наук. [Текст] / К. А. Стаценко. – Екатеринбург, 2004. – 159 с.
2.Буйносов, А. П. Методы повышения ресурса бандажей колесных пар тягового подвижного состава: Дисс. на соискание уч. ст. докт. техн. наук. [Текст] / А. П. Буйносов. – Екатеринбург, 2011. – 455 с.
3.Методика контроля величины натяга бандажа, обеспечивающая надежность соединения «бандаж-обод» колесного центра локомотива [Текст] / А. П. Буйносов, Е. В. Бган и др. // Вестник Курганского государственного
153

Ремонт и динамика подвижного состава
университета. Серия: Технические науки, 2013. – № 29. – С. 23 – 27.
4. Буйносов, А. П. Определение натяга бандажа на ободе колесного центра электровоза с помощью ультразвуковых импульсов [Текст] / А. П. Буйносов, Е. В. Бган, К. А. Стаценко // Известия Тульского государственного университета. Технические науки. 2012. – № 2. – С. 146 – 156.
5. Буйносов, А. П. Повышение прочности посадки деталей с натягом сформированных колесных пар электровозов [Текст] / А. П. Буйносов, Е. В. Бган, К. А. Стаценко // Научно-технический вестник Поволжья, 2012. – № 5. – С. 118 – 120.
6. Буйносов, А. П. Повышение ресурса колесных пар электровозов технологическими методами: Монография. [Текст] / А. П. Буйносов, К. А. Стаценко. – Саарбрюккен, Germany (Германия): Изд-во «LAP LAMBERT Academic Publishing», 2012. – 215 с.
7. Буйносов, А. П. Определение натяга пары «бандаж-обод» с помощью
ультразвуковых импульсов [Текст] / А. |
П. Буйносов, К. А. |
Стаценко, |
Н. И. Сергеев // Транспорт Урала, 2004. – № 3 (3). – С. 31 – 37. |
|
|
8. Буйносов, А. П. Методика определения прочности посадки деталей с |
||
натягом у сформированных колесных |
пар локомотивов |
[Текст] / |
А. П. Буйносов, Е. В. Бган, К. А. Стаценко // Естественные и технические науки. 2012. – № 6. – С. 586 – 588.
9.Буйносов, А. П. Методика определения величины натяга бандажа на ободе колесного центра локомотива с помощью ультразвуковых импульсов [Текст] / А. П. Буйносов, К. А. Стаценко // Проблемы машиностроения и автоматизации. 2012. – № 4. – С. 100 – 106.
10.Инструкция по формированию, ремонту и содержанию колесных пар тягового подвижного состава железных дорог колеи 1520 мм с изменениями и дополнениями, утвержденными указанием МПС России от 23.08.2000 – № К- 2273у: ЦТ/329. – М.: Транспорт, 2000. – 78 с.
154

ТРАНСВУЗ – 2015
УДК 621.43.038-047.37
М. В. Яранцев, А. Ю. Коньков
РАЗРАБОТКА МЕТОДА ДИАГНОСТИРОВАНИЯ ПЛУНЖЕРНЫХ ПАР ТОПЛИВНОГО НАСОСА ВЫСОКОГО ДАВЛЕНИЯ СРЕДНЕОБОРОТНОГО ДИЗЕЛЯ
В работе предложен новый способ диагностирования плунжерной пары без разборки топливного насоса высокого давления и его демонтажа с дизеля, позволяющий определять износ прецизионных поверхностей на ранних стадиях развития. Представлены результаты расчетных и экспериментальных исследований, поясняющие суть предлагаемых решений и особенностей применения на практике.
Надежность и долговечность работы дизельного двигателя зависит от своевременного определения технического состояния его основных систем и узлов. Известно, что значительная доля отказов приходится на топливную аппаратуру (ТА), в частности на топливный насос высокого давления (ТНВД). В свою очередь на отказ плунжерных пар (ПП) приходится порядка 30 % от общего количества всех отказов насоса [1]. Основным дефектом, лимитирующим рабочий ресурс ПП, являются износы прецизионных поверхностей плунжера и втулки. Около 80 % ПП бракуется по причине абразивного износа этих поверхностей [2]. Абразивные частицы попадают во внутренние полости ПП в том числе и во время разборки ТНВД, которая необходима для проверки работоспособности ПП стендовыми способами.
Критический износ прецизионных поверхностей ПП приводит к невозможности удержания топлива в надплунжерном пространстве, что вызывает падение давления впрыска топлива и, как следствие, увеличение расхода топлива на единицу мощности двигателя. Также снижается скорость впрыскивания, дальнобойность факела топлива, что приводит к нарушению смесеобразования, повышению токсичности отработавших газов. При этом на протяжении значительной части жизненного цикла ПП ее рабочий износ практически не сказывается на характеристиках двигателя, вплоть до наступления критического [2]. Для недопущения работы дизеля с критическим износом ПП необходимы средства и методики обнаружения изменений
155
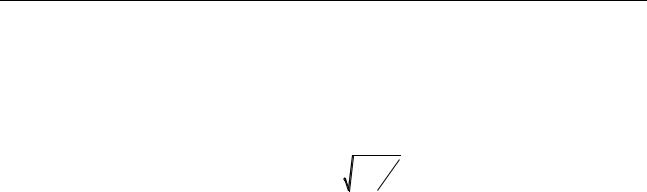
Ремонт и динамика подвижного состава
технического состояния ПП на ранних стадиях развития износа, разработка которых и является целью настоящей работы.
Исследования проводились на безмоторном стенде [3]. Известно, что количество жидкости, перетекающей через отверстие площадью F за период времени dτ, может быть найдено из уравнения
|
|
2 |
|
|
|
|
|
|
|
|
|
2 p |
|
|
|
||
Vр |
|
|
F |
|
dτ , |
(1) |
||
|
|
|
|
|
|
|
||
|
|
1 |
|
|
|
|
|
|
где μ – расходный коэффициент; |
|
ρ |
– |
плотность жидкости; |
p – разница |
давлений жидкости перед и за отверстием площадью F.
Применительно кТА: μ – расходный коэффициент сопел соплового наконечника форсунки; F – суммарная площадь сопловых отверстий соплового наконечника форсунки; ρ – плотность впрыскиваемого топлива; p – разница давления топлива в сопловом наконечнике форсунки перед отверстиями и давления топлива за отверстиями во впрыскиваемой емкости.
Этот же объем топлива можно определить при стендовых испытаниях прямым методом при заполнении заданного объема VV. Соединив исследуемый насос с некой эталонной форсункой, на которой установлен сопловой наконечник с известным расходным коэффициентом и направив впрыскиваемое через него топливо в мерную емкость, появляется возможность сопоставить расчетный объем топлива Vр с действительно имевшим место VV в тот же период времени от τ1 до τ2. Подобный подход позволяет исключить влияние активного хода плунжера на результаты проверки, так как VV всегда постоянен. Нами экспериментально было установлено, что всегда имеется невязка между расходом топлива, рассчитанным по уравнению (1) и реально поданным
количеством топлива в мерную емкость, при этом Vр всегда больше VV: |
|
V Vp VV . |
(2) |
Объясняется это тем, что расчет по (1) предполагает только один путь течения топлива – через сопловые отверстия соплового наконечника форсунки. В действительности все топливо, поступившее в надплунжерное пространство в фазе нагнетательного хода плунжера, утекает в четырех направлениях: 1) основная часть топлива направляется через сопловые отверстия форсунки в мерную емкость, это же количество топлива определяется при заполнении заданного объема прямым способом VV; 2) в линию низкого давления через дренажную магистраль форсунки в момент посадки иглы форсунки на седло;
156
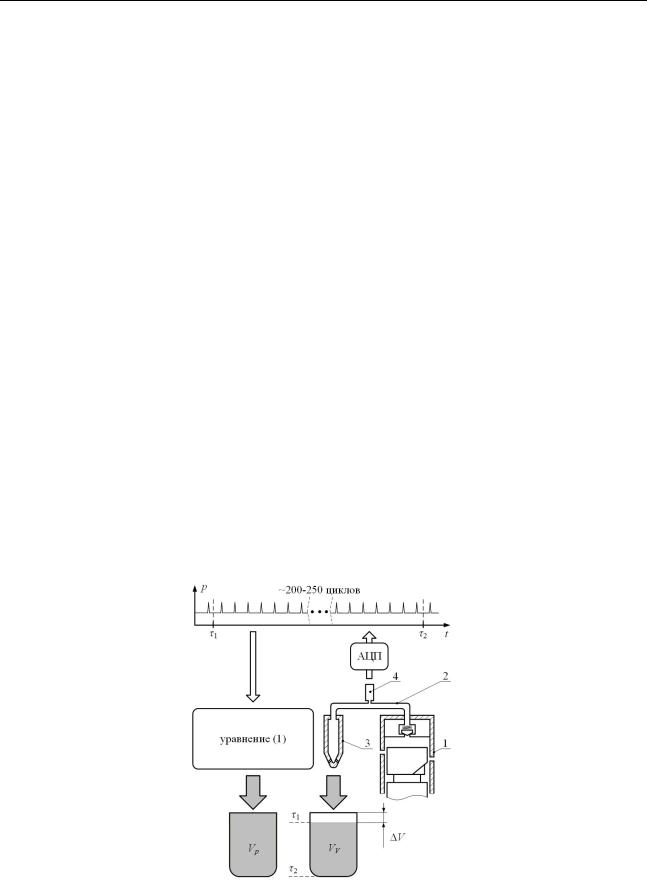
ТРАНСВУЗ – 2015
3) в линию низкого давления через окна втулки плунжера, при открытых отсечных и наполнительных отверстиях, и во время геометрической подачи топлива, при закрытых отверстиях, через золотниковую часть плунжера; 4) по компрессионной части ПП в картер с маслом во время геометрической подачи топлива. Таким образом, можно предположить, что экспериментально установленная нами разница V является суммой утечек топлива во втором, третьем и четвертом направлениях.
Чтобы исключить утечки во втором направлении была применена форсунка открытого типа с заведомо известной площадью эффективного проходного отверстия соплового наконечника (технологическая форсунка). Контролируя с высокой точностью все величины, входящие в уравнение (1), к невязке можно отнести суммарный объем топлива, утекающего в линию низкого давления через окна втулки плунжера в любой момент времени (утечки в третьем направлении) и в картер с маслом во время геометрической подачи топлива (утечки в четвертом направлении). Если обеспечить постоянство утечек топлива в третьем направлении, то по величине невязки можно судить о степени работоспособности ПП. Установлено, что при анализе отдельно взятого цикла различия в величинах объемов, определенных разными способами, ничтожно малы. Если же анализировать результаты сотен циклов, различия достигают доступных для измерения значений. Таким образом, суть предлагаемого метода определения степени работоспособности ПП можно представить схематично (рис. 1).
Рис. 1. Схема предлагаемого способа определения степени износа ПП ТНВД
157

Ремонт и динамика подвижного состава
Процедура диагностирования следующая. На штуцер проверяемого ТНВД 1 взамен штатной трубки высокого давления монтируется технологическая трубка 2, на другом конце которой за креплена технологическая форсунка 3, представляющая собой форсунку открытого типа с калиброванным распылителем. В линии высокого давления установлен датчик давления 4. Топливо через трубку впрыскивается форсункой в мерную емкость известного объема VV. С момента времени τ1, соответствующего началу подачи топлива в емкость, до момента времени τ2 заполнения этого объема, в памяти компьютера сохраняется результат аналого-цифрового преобразования сигнала давления, по величине которого численным интегрированием уравнения (1) вычисляется Vр и далее величина невязки V, а также ее процент .
На исследовательской установке была проведена экспериментальная проверка предлагаемых решений проблемы. Объектом исследования послужила ТА дизеля типа Д49: насос Д49.107СПЧ с ПП типа СПЧ-4 и форсунка Д49.85СПЧ. Результаты экспериментальных данных представлены на рис. 2.
Рис. 2. Зависимость невязки (в процентах от заданного объема VV) от вязкости топлива ν на различных скоростных и нагрузочных режимах работы ТНВД
158

ТРАНСВУЗ – 2015
Невязка на рис. 2 представлена в виде процента от объема VV. Стоит отметить, что ПП с гидравлической плотностью 5 и 7 секунд считаются новыми, а ПП с плотностью 3,5 секунды – рабочей. Установлено, что при любой частоте вращения, вязкости топлива и положении рейки насоса существует взаимосвязь между степенью износа ПП и невязкой. Данный эксперимент подтвердил, что невязка оказывается тем больше, чем более изношена ПП, однако четких тенденций не прослеживается. Поэтому возникла необходимость в детальном исследовании процесса перетекания топлива из надплунжерного пространства по всем направлениям. Ввиду того, что экспериментально определить объемы утечек топлива с необходимой точностью невозможно, было выполнено расчетное исследование.
Для исследования природы утечек топлива была разработана математическая модель, описывающая процесс впрыскивания форсункой открытого типа. Установлено, что, если принять суммарные утечки топлива из надплунжерного пространства за 100 %, то: А. 78 – 83 % (в зависимости от степени износа прецизионных поверхностей ПП) топлива утекает в открытые окна втулки плунжера на участке роста давления и в момент открытия отсечного окна; Б. 17 – 22 % утекает по прецизионным поверхностям ПП, из которых: 1) 10 – 12 % по золотниковой части плунжера в отсечное отверстие, 2) 6 – 8 % по золотниковой части плунжера в наполнительное отверстие, 3) 1 – 2 % по компрессионной части плунжера.
Для определения степени влияния различных факторов (частота вращения кулачкового вала, давление топлива в наполнительной магистрали, вязкость топлива) на величину невязки V было выполнено расчетное исследование с использованием этой же математической модели процесса впрыскивания. Установлено, что при частоте вращения кулачкового вала nв =175 мин-1 изменение давления топлива в наполнительной магистрали в рабочих пределах практически не сказывается на величине утечек топлива . Однако при увеличении частоты вращения возникает необходимость в постоянном контроле давления топлива в линии низкого давления, так как при повышении давления на 100 кПа объем утечек в среднем увеличивается на 0,5 %. Кроме этого, также было установлено, что при любой частоте вращения вязкость топлива сказывается на величине утечек тем больше, чем больше величина зазора. Поэтому при диагностировании предлагаемым способом необходимым условием является контроль вязкости топлива.
159