
ТРАНСВУЗ-2015.Часть 1
.pdf
Ремонт и динамика подвижного состава
Анализ влияния присадки «Миакрон 2000» на вязкость топлива (рис. 1, б) показал, что при концентрации присадки от 0,1 % до 0,2 % вязкость топлива увеличивается с 4,53 до 4,58 мм2/с, что может привести к ухудшению тонкости распыливания и неполному сгоранию топлива. При концентрации от 0,2 % до 0,3 % вязкость топлива уменьшается с 4,58 мм2/с до 4,45 мм2/с, в связи с этим улучшается качество распыливания топлива в камере сгорания. При концентрации от 0,3 % до 1 % вязкость топлива увеличивается от 4,45 мм2/с до 4,55 мм2/с, а затем уменьшается не значительно. Данные изменения вязкости не выходят за пределы допустимых нормируемых значений (3 – 6 мм2/с).
Анализ изменения температуры вспышки топлива при введении присадки «Миакрон 2000» (рис. 1, в) показал, что при введении присадки от 0 % до 0,1 % температура вспышки уменьшается с 86 оС до 82 оС. При введении присадки от 0,1 % до 0,25 % температура вспышки увеличивается с 82 оС до 86,3 оС. При концентрации присадки от 0,25 % до 0,4 % температура вспышки уменьшается с 86,3 оС до 85,5 оС. При дальнейшем введении присадки температура вспышки незначительно увеличивается.
Анализ влияния присадки «Миакрон 2000» на ЦЧ топлива (рис. 1, г) показал, что при концентрации присадки от 0 % до 0,1 % ЦЧ уменьшается с 49 до 47 ед.; при концентрации присадки от 0,1 % до 0,3 % ЦЧ увеличивается до 50 ед., затем ЦЧ падает до 46,5 ед. Цетановое число влияет не только на экономичность двигателя, но и на его экологические характеристики.
Анализ влияния присадки «Миакрон 2000» на фракционный состав топлива (рис. 1, д) показал, что при концентрации присадки от 0 до 1 % температура выкипания 50 % фракции составляет 290 – 298 оС, данные значения выходят за пределы допустимых нормируемых значений (255 – 280 оС), а температура выкипания 90 % топлива составляет 340 – 355 оС и находится в допустимых пределах (330 – 380 оС), что говорит о полноте сгорания топлива и уменьшении вредных выбросов в отработавших газах дизеля.
Влияние концентрации присадки «Миакрон 2000» на количество фактически смол в топливе представлено на рис. 2.
Анализ изменения количества фактических смол в дизельном топливе при введении в него присадки «Миакрон 2000» (рис. 2) показал, что при концентрации присадки до 0,4 % количество фактических смол находится в пределах нормы (менее 30 мг/100 см3). При концентрации присадки от 0,5 до
60
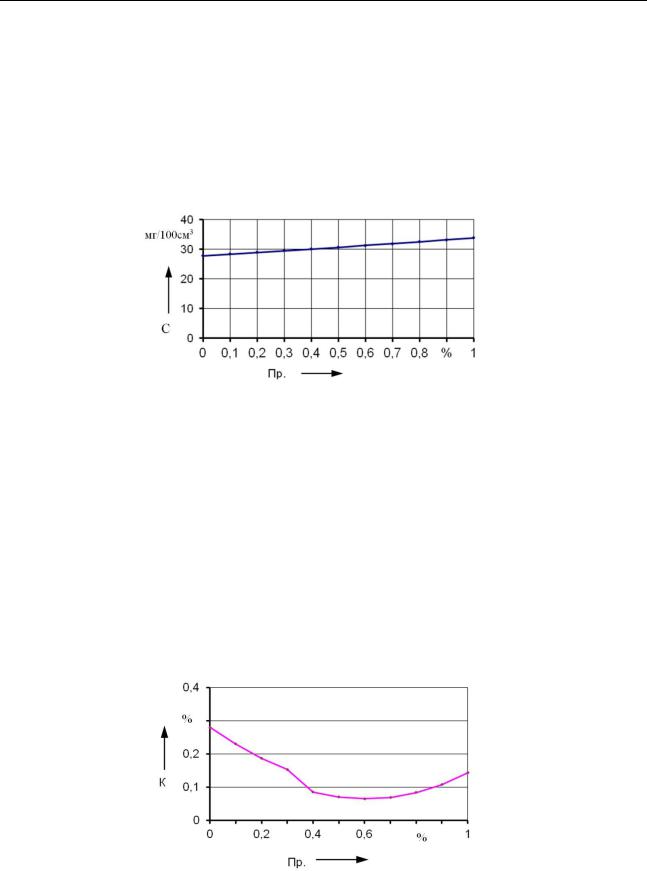
ТРАНСВУЗ – 2015
1 % количество фактических смол увеличивается и превышает допустимую норму. При повышенном содержании смолистых веществ в топливе возможны нарушения в системе питания двигателя, кроме того отложения на деталях двигателя, которые представляют собой липкие мазеобразные продукты, могут быть причиной нарушения подачи топлива, отложения на фильтрующих элементах приведут к прекращению подачи топлива в цилиндры дизеля.
Рис. 2. Изменение количества фактических смол в дизельном топливе при введении присадки «Миакрон 2000»
Анализ влияния присадки «Миакрон 2000» на количество углистого осадка в топливе (рис. 3) показал, что с введением присадки в количестве от 0,1 до 0,6 % количество кокса в топливе уменьшается с 0,280 % до 0,078 %, но при дальнейшем увеличении концентрации постепенно увеличивается до 0,145 %. Однако количество кокса не выходит за пределы допустимых нормируемых значений (0,2 – 0,3 %).
Рис. 3. Изменение коксуемости дизельного топлива при введении присадки «Миакрон 2000»
61

Ремонт и динамика подвижного состава
Результаты проведенных испытаний показали, что присадка «Миакрон 2000» в концентрации до 0,3 % по массе в отличие от других присадок, является высокоэффективной многофункциональной присадкой, улучшающей качествокак дизельного топлива, так и топлива с пониженным цетановым числом. Присадка «Миакрон 2000» в концентрации до 0,3 % по массе повышает цетановое число, понижает температуру застывания, снижает коксуемость и количество вредных выбросов в отработавших газах дизеля, что позволяет на базе отечественных дизельных топлив, получать дизельное топливо класса 4 по Техническому регламенту и соответствующие ЕВРО-4 по требованиям, предъявляемым в Странах ЕС Европейским Стандартом, EN 590:2004. Однако требуется проведение дополнительных исследований по определению экономических и экологических показателей тепловозных дизелей для полного заключения об эффективности применения присадки «Миакрон 2000» в топливо.
УДК 629.471
И. В. Пустовой
ЭЛЕКТРОННЫЙ ТУ-28Э КАК ОСНОВА PLM-СИСТЕМЫ СЛД
Встатье описано новое направление работ в группе компаний «Локомотивные технологии» (ЛокоТех) совместно с холдингом «ТрансМашХолдинг» по разработке системы управления жизненным циклом локомотивов, объектами автоматизации которой являются производственные процессы, осуществляемые в ЛокоТех в рамках договора на сервисное обслуживание локомотивов. Описан этап работ по созданию PLM-системы – внедрение электронного журнала формы ТУ-28Э (журнал учета выполненных ремонтов формы ТУ-28). Расширение функциональности электронного журнала ТУ-28Э по сравнению с бумажным ТУ-28.
Внастоящее время в группе компаний «Локомотивные технологии»
(ЛокоТех) совместно с холдингом «ТрансМашХолдинг» идет разработка системы управления жизненным циклом локомотивов. Следует отметить, что понятие «Жизненный цикл» (ЖЦ) применяется в достаточно разных интерпретациях (рис. 1.). В ЛокоТех Жизненный цикл рассматривается как ЖЦ
62
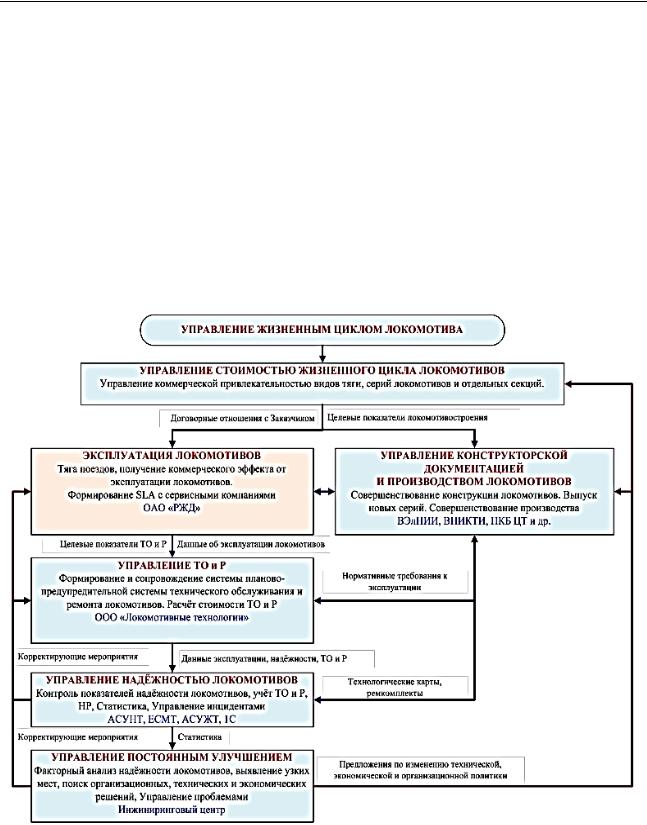
ТРАНСВУЗ – 2015
изделия (продукции): «совокупность процессов, выполняемых от момента выявления потребностей общества в определенной продукции до момента удовлетворения этих потребностей и утилизации продукта» – т.н. PLM. Однако применительно к задачам сервисного технического обслуживания и ремонта (ТО и Р) понятие ЖЦ рассматривается более узко (рис. 2): управление надежностью локомотивов через систему планово-предупредительных ТО и Р с целью существенного повышения эффективности управления сервисным ТО и Р, повышения качества планирования, управления ТО и Р, сокращение себестоимости ремонтов, повышение надежности локомотивов, создание «прозрачной» системы отчетности.
Рис. 1. Структура понятия «Жизненный цикл» локомотива (PLM-системы)
63
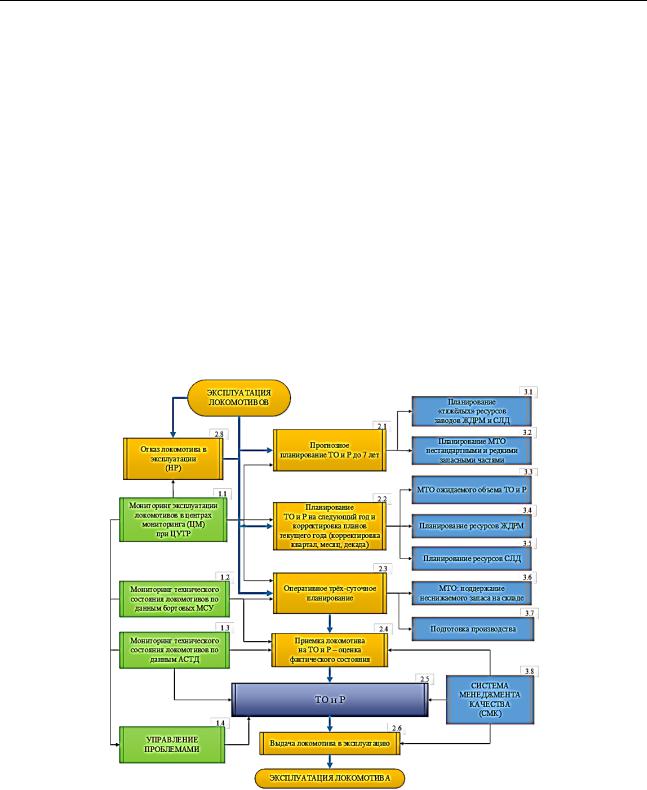
Ремонт и динамика подвижного состава
Объектом автоматизации являются следующие производственные процессы, осуществляемые в ЛокоТех в рамках договора на сервисное обслуживание локомотивов: прогнозное планирование сервисного обслуживания локомотивов, оперативное планирование сервисного обслуживания локомотивов, мониторинг и диагностирование локомотивов в процессе эксплуатации и при проведении сервисного обслуживания, проведение сервисного обслуживания, прогнозное и оперативное планирование материальнотехнического обеспечения сервисного обслуживания локомотивов, управление трудовыми ресурсами, контроль безопасности движения, формирование системы менеджмента качества,технологическое обеспечение производства, поддержание инфраструктуры в надлежащем состоянии, контроль соблюдения правил и обеспечением промышленной, экологической и пожарной безопасности, формирование плановой себестоимости ремонта, формирование бюджета ремонта, подготовки аналитической отчетности.
Рис. 2. Жизненный цикл локомотива на этапе ТО и Р
Т.к. работа по созданию PLM-системы является комплексной и достаточно объемной, то имеет смысл вести поэтапное внедрение системы. Анализ показал, что ключевым элементом является журнал учета выполненных
64
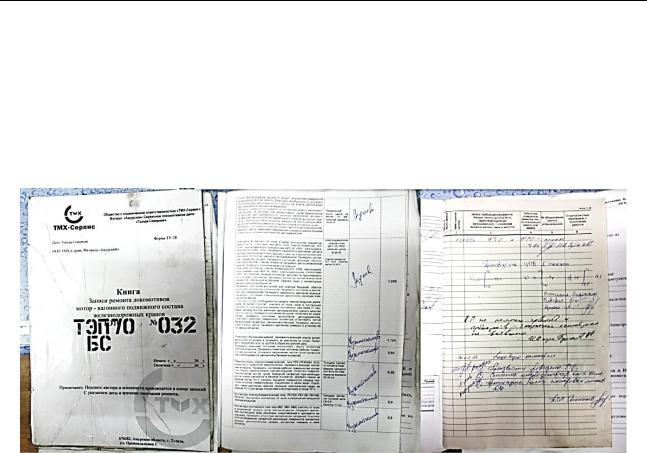
ТРАНСВУЗ – 2015
ремонтов формы ТУ-28, который ведется в каждом депо отдельно на каждый локомотив (рис. 3). Бумажный ТУ-28 не позволяет оперативно дистанционно контролировать выполняемые работы. Неудобен для проведения анализа. При этом ТУ-28 является исключительно информативным источником данных о надежности локомотива. Поэтому принято решение о создании электронного журнала – аналога бумажного: ТУ-28Э.
а – титул ТУ-28 |
б – цикловые работы |
в – доп. работы |
Рис. 3. Бумажный журнал формы ТУ-28
Функциональность ТУ-28Э будет расширена по сравнению с бумажным ТУ-28. Прежде всего, ведение ТУ-28Э будет взаимосвязано с работой склада: при выдаче материалов или запасных частей на складе будет не только указываться секция локомотива, но и работа (наряд), под который произведена выдача. ТУ-28Э также будет интегрирован со всеми элементами 1С ERPсистемы ТМХ-Сервис: кадры, зарплата, склад, оборудование, инфраструктура и др. На рис. 4. показана структура ТУ-28 (синим), смежные системы 1С (коричневым) и разрабатываемые программные модули (фиолетовым).
На рис. 5. показаны информационные потоки ТУ-28Э. На основании прогнозного планирования (рис. 1., блоки 2.1 – 2.2), данных систем мониторинга (рис.1, блоки 1.1 – 1.3, рис. 5., блок 1.2) осуществляется оперативное 3-х суточное планирование (рис. 1., блок 2.3, рис. 5., блок 1.1). После захода локомотива в депо и приемки (рис. 1., блок 2.4, рис. 5., блок 1.3) в производственно-диспетчерском отделе (ПДО) сервисного локомотивного депо (СЛД) формируется план работ (рис. 5., блок 1.4), состоящий из цикловых
65
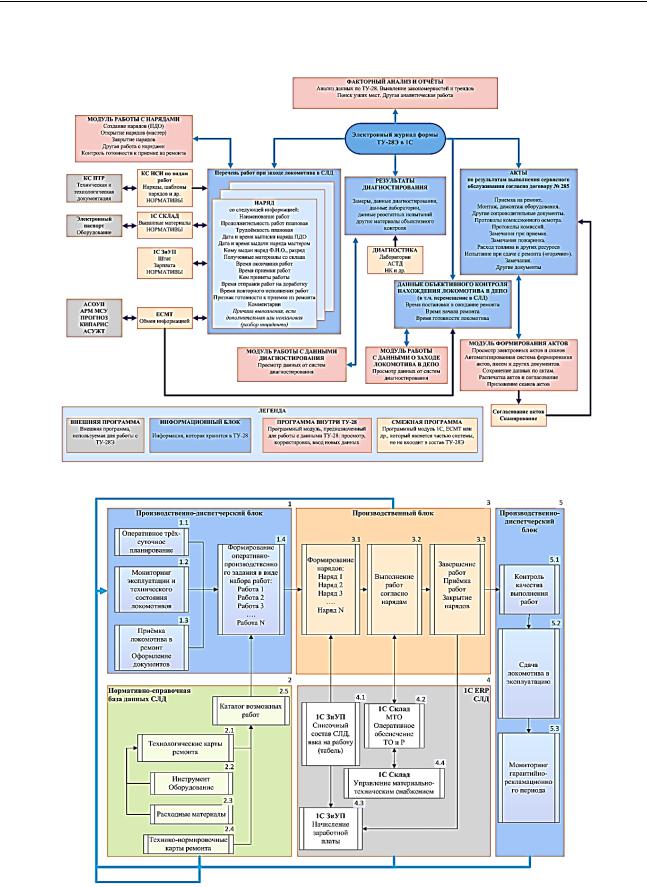
Ремонт и динамика подвижного состава
(рис. 3б.) и дополнительных (рис. 3в.) работ. Сами работы выбираются из системы нормативно-справочной информации 1С (рис. 5., блок 2).
Рис. 4. Электронный журнал ТУ-28Э
Рис. 5. Информационные потоки ТУ-28Э
66

ТРАНСВУЗ – 2015
По составленному плану работ (рис. 5., блок 1.4) мастер цеха текущего ремонта производит подвязку исполнителей (блоки 3.1 и 4.1). Во время исполнения работ (блок 3.2) полученные со склада детали подвязываются к нарядам (блоки 4.2 и 3.2). По окончании работ мастер (блок 3.3) и представитель ПДО (блок 5.1) проверяют качество выполненных работ и закрывают наряды, на основании которых в дальнейшем производится расчет заработной платы (блок 4.3). Вся информации производственного процесса сохраняется в ТУ-28Э.
В результате описанного алгоритма (рис. 5) автоматизируется управление производственным процессом сервисного локомотивного депо при одновременном формировании комплексной электронной базы данных о ТО и Р. Сформированная база данных позволяет реализовать технологию «Встроенное качество» («правильно или никак»).
Кроме того, ТУ-28Э позволяет анализировать причины появления дополнительных работ, причины перерасхода материалов, прогнозировать потребность в них. Одновременно создается система мотивации работников СЛД, за счет прозрачной нарядной системы оплаты труда.
Реализация ТУ-28Э позволит перейти к следующим этапам реализации PLM-системы ЛокоТех: оперативно-производственному планированию, автоматическому управлению неснижаемым запасом комплектующих и материалов, научным управлением надежностью локомотивов.
УДК 629.4.014
Л. В. Милютина
ВЛИЯНИЕ ИЗМЕНЕНИЯ ФИЗИКО-ХИМИЧЕСКИХ ПАРАМЕТРОВ ТОПЛИВА ПОСЛЕ ОБРАБОТКИ УЛЬТРАЗВУКОМ НА ПРОЦЕСС РАСПЫЛИВАНИЯ ТОПЛИВА
ИИНТЕНСИВНОСТЬ ЕГО ИСПАРЕНИЯ
Встатье рассмотрено влияние ультразвуковой обработки на изменение физикохимических свойств дизельного топлива, определено оптимальное время ультразвуковой обработки дизельного топлива, рассмотрено влияние изменения плотности топлива после обработки ультразвуком на процесс распыливания и интенсивность испарения топлива.
67
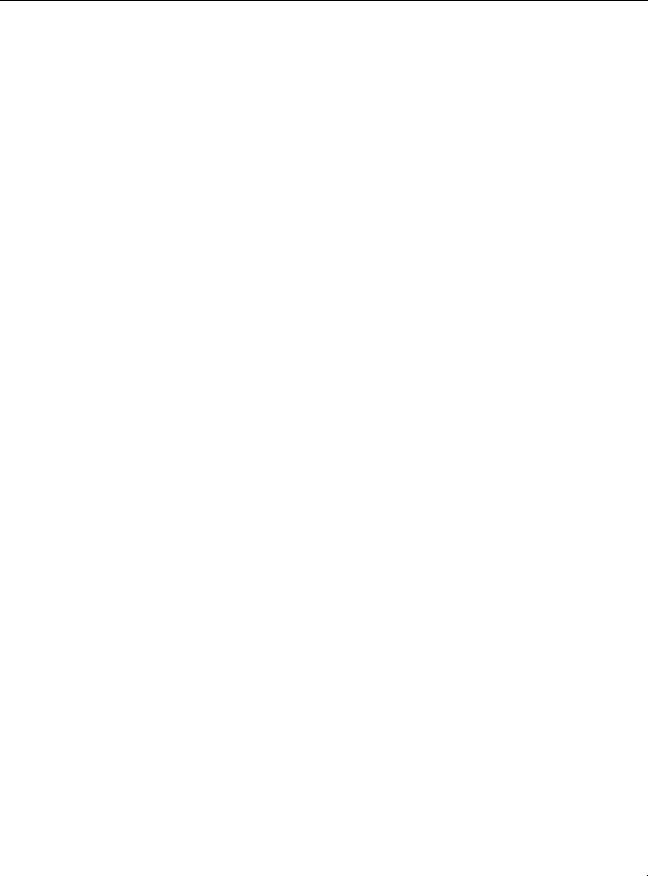
Ремонт и динамика подвижного состава
В потоке жидкости ультразвуковые колебания создают зоны переменных давлений, что приводит к появлению кавитации, обеспечивающей эффект гомогенизации. При частоте более 20 кГц ультразвуковые колебания могут разрушать асфальто-смолистые образования. В качестве генераторов ультразвуковых колебаний применяются гидродинамические и электромеханические излучатели.
Разработаны акустические аппараты различного типа для интенсификации процессов смешения и растворения: ультразвуковые гидродинамические смесители УГС – 77, акустические аппараты для сверхтонкого измельчения и очистки, ультразвуковые проходные химические аппараты типа УПХА для обработки систем жидкость – твердое тело [1, 2].
Ультразвуковые гидродинамические гомогенизаторы при производительности 1,7 м3/ч потребляют энергии в 10 раз меньше, чем клапанные гомогенизаторы.
Обработка дизельного топлива ультразвуком на установке УЗУ – 0,1 частотой 15 – 22 кГц и время обработки (15 – 60 мин) влияет на распыливающие и нагарообразующие свойства дизельного топлива.
Анализ изменения физико-химических свойств топлива, обработанного ультразвуком, представлено в табл. 1 – 2.
Таблица 1 Основные физико-химические показатели дизельного топлива
(ГОСТ 305-82), обработанного ультразвуком
Наименование |
Необработанное |
Обработанное |
|
топливо |
топливо |
|
|
|
Цетановое число |
46 |
43 |
|
|
|
Фракционный состав |
|
|
50 %,°С |
272 |
269 |
96 %,°С |
358 |
363 |
|
|
|
Вязкость при 20 °С, мм2/с |
3,05 |
3,15 |
Общее содержание серы, % |
0,128 |
0,125 |
|
|
|
Коксуемость 10 %-ного остатка, % |
0,0325 |
0,046 |
|
|
|
Плотность при 20 °С, кг/м3 |
825 |
821 |
68
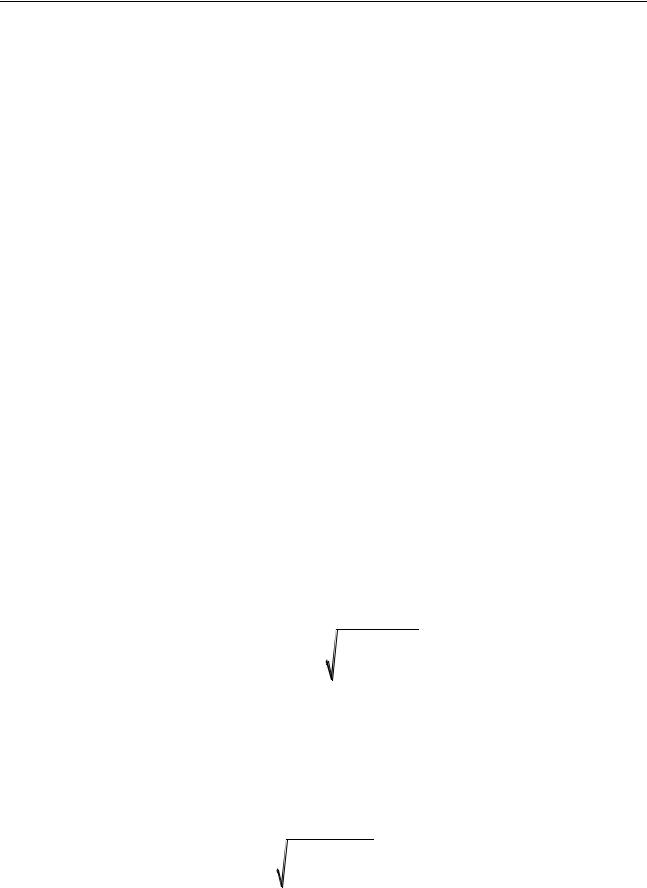
ТРАНСВУЗ – 2015
Таблица 2 Влияние продолжительности ультразвуковой обработки дизельного топлива на
его физико-химические свойства
|
Коксуе- |
Содер- |
Содер- |
|
|
|
|
Время |
жание |
жание |
|
|
|
||
мость |
Фракцион- |
Плот- |
Вяз- |
||||
обра- |
факт. |
факт. |
|||||
10 % – го |
ный состав |
ность , |
кость |
||||
ботки |
смол. |
смол. |
|||||
остатка |
t90 %, °С |
кг/м3 |
ν20, сСт |
||||
t, мин |
См, % |
ФС, |
|||||
К, % |
|
|
|
||||
|
|
мг/100 мл |
|
|
|
||
|
|
|
|
|
|
||
|
|
|
|
|
|
|
|
0 |
0,0325 |
0,76 |
11,82 |
358 |
825,0 |
3,05 |
|
|
|
|
|
|
|
|
|
15 |
0,0315 |
0,72 |
6,37 |
355 |
823,0 |
3,06 |
|
|
|
|
|
|
|
|
|
30 |
0,0345 |
0,78 |
9,00 |
362 |
822,0 |
3,08 |
|
|
|
|
|
|
|
|
|
45 |
0,0375 |
1,0 |
10,10 |
365 |
821,5 |
3,10 |
|
|
|
|
|
|
|
|
|
60 |
0,046 |
1,0 |
9,83 |
363 |
821,0 |
3,15 |
|
|
|
|
|
|
|
|
Физико-химические свойства дизельного топлива во время обработки ультрозвуком находятся в пределах нормативных значений по ГОСТ 305-82.
Как показывают исследования, процесс распыливания топлива и интенсивность его испарения оказывают решающее влияние на условия смесеобразования, воспламенения и полного сгорания топлива. На тонкость распыла топлива большое влияние оказывает скорость его истечения из сопла. Чем выше скорость истечения, тем мельче распыл топлива. Средняя скорость истечения топлива из сопла определяется по формуле, м/c:
3 |
|
2(РФ |
РГ ) |
|
|
|
|
ω 10 φ |
|
|
, |
(1) |
|||
т |
|||||||
|
|
|
|
|
где – коэффициент, равный 0,6 – 0,7; РФ – давление впрыска форсунки, МПа;
РГ – давление газов в камере сгорания в конце процесса сжатия, МПа;
т – плотность топлива, до обработки ультразвуком равна 825 кг/м3;
т – плотность топлива, после обработки ультразвуком равна 821 кг/м3.
ω 103 0, 6 |
|
2(27,5 21) |
|
75,3 м/с; |
|
825 |
|||||
|
|
|
|
69