
ТРАНСВУЗ-2015.Часть 1
.pdf
Ремонт и динамика подвижного состава
ω 103 0,6 |
|
2(27,5 21) |
|
75,5 м/с . |
|
821 |
|||||
|
|
|
|
Определяющее влияние на скорость истечения топлива, при регулировке форсунки на постоянное давление впрыска и при постоянном угле опережении впрыска, оказывает плотность топлива.
Hа процесс смесеобразования и сгорания большое влияние оказывает диаметр капель распыленного топлива.
Средний диаметр капель топлива в первом приближении может быть определен по формуле:
dcp =78,4gk |
σ |
|
, |
(2) |
|
|
|||
ω2ρ |
|
|||
|
т |
|
||
|
|
|
где g – ускорение силы тяжести, м/с2;
k – коэффициент, зависящий от силы поверхностного натяжения жидкости;
– поверхностное натяжение жидкости, Н/м;
– средняя скорость истечения топлива из сопла, м/с;
Г – плотность газовой среды, кг/м3.
Средний диаметр капли в зависит от силы поверхностного натяжения, скорости истечения топлива и плотности газовой среды. Сила поверхностного натяжения является функцией плотности топлива.
5,02 10 6 т 1,66 10 3 Н/м; |
(3) |
5,02 10 6 825 1,66 10 3 2,48 10 3 Н/м;
5,02 10 6 821 1,66 10 3 2,46 10 3 Н/м.
Плотность газовой среды в конце процесса сжатия для дизельного двигателя определяется по формуле, кг/м3:
|
|
|
|
с |
п1 |
|
|
|
|
|
|
(4) |
|
гс |
|
|||||
|
|
га |
|
, |
||
|
|
|
|
а |
|
где ρгс – плотность газа в конце процесса сжатия; рга – плотность газа в начале процесса сжатия; рс – давление газа в конце процесса сжатии; ра – давление газа в начале процесса сжатия; n1 –показатель политропы сжатия.
70
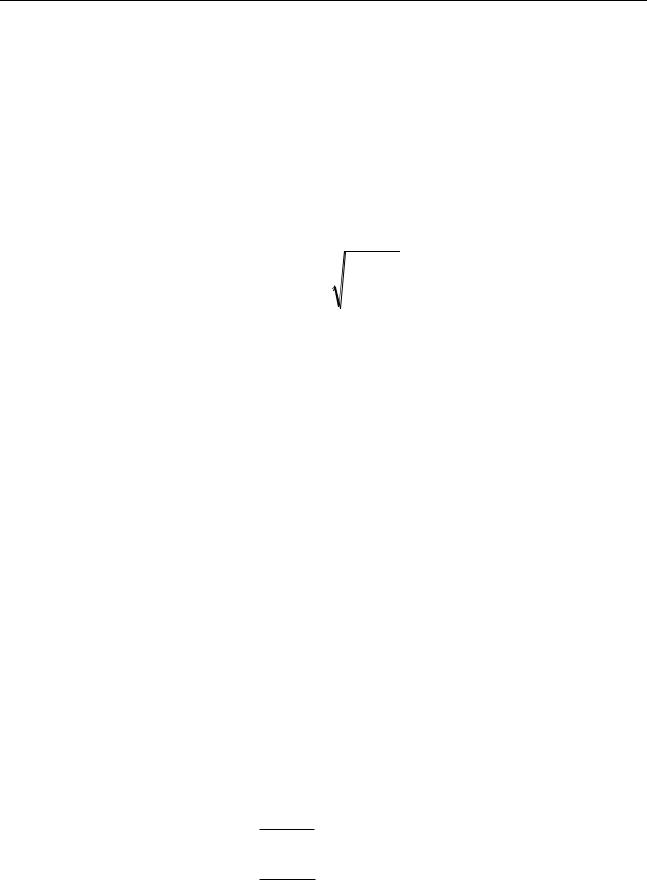
ТРАНСВУЗ – 2015
Время, необходимое для эффективного смесеобразования топлива с воздухом, зависит от диаметра капель топлива, относительной скорости капель ω0 и определяется по формуле, с:
см |
|
4,85dср |
, |
|
|||
|
|
ω0 |
где dср – средний диаметр капель, мкм;
0 – относительная скорость капли, м/с.
Относительная скорость капли рассчитывается по формуле, м/с:
ω0 0,162 |
dср ρт |
, |
|
||
|
ρгс |
(5)
(6)
Анализ процесса испарения капель топлива, с определением полного испарения капли, показывает, что на скорость испарения капли оказывает влияние: диаметр капли, плотность топлива, коэффициент диффузии паров топлива в газовую среду и давление насыщения паров топлива.
Время полного испарения капли топлива среднего диаметра определяется по формуле, ч:
|
τ0 |
d |
ср |
2 |
|
d |
ср |
2ρ |
т |
, |
(7) |
|
|
|
|
|
|
|
|
||||
|
|
К 78,5Dр Рs |
|
|
|||||||
где Dр – коэффициент диффузии, м2/ч; |
|
|
|
|
|
|
|
|
|||
Р |
– давление насыщения паров топлива, Н/м2. |
|
|
||||||||
s |
|
|
|
|
|
|
|
|
|
|
На процесс топливоподачи оказывает влияние сжимаемость топлива. Чем больше коэффициент сжимаемости топлива, тем больше период запаздывания подачи топлива, что уменьшает цикловую подачу топлива и влияет на давление распыла.
Коэффициент сжимаемости топлива определялся по формуле, 1/МПа:
|
36 10 5 |
|
|
||
|
3 . |
(8) |
|||
|
|||||
|
т |
|
|
|
36 10 5 6,41 10 13 1/МПа; 8253
36 10 5 6,51 10 13 1/МПа. 8213
71

Ремонт и динамика подвижного состава
Анализ показал, что после обработки топлива ультразвуком коэффициент сжимаемости снижается.
Дизельные топлива увеличивают свою вязкость под давлением, поэтому повышение вязкости топлива вызывает ухудшение его распыливания, что оказывает отрицательное влияние на процесс смесеобразования и сгорания топлива. Обработка дизельного топлива в течение 15 минут ультразвуком частотой 18 – 20 кГц наиболее существенно снижает нагарообразующие свойства дизельного топлива и может быть принята оптимальной.
Обработка топлива с помощью ультразвука способствует улучшению его дисперсных качеств, а явление кавитации, сопровождающее этот процесс, приводит к дополнительной активации углеводородных составляющих топлива.
Список литературы
1. Раджендран, В. К. Применение ультразвука [Текст] / В. К. Раджендран, П. Н. Паланичами. – М.: Нефтехимия. 2006. – 576 с.
2. Зубрилов, С. П. Ультразвуковая кавитационная обработка топлив на судах [Текст] / С. П. Зубрилов, В. М. Селиверстов. – М.: Наука, 1988. – 80 с.
УДК 658.51
С. В. Приображенский
5S – ИНСТРУМЕНТ БЕРЕЖЛИВОГО ПРОИЗВОДСТВА
Порядок и чистота на рабочем месте, а не „упорядоченный хаос“, являются основой всех улучшений, повышения производительности и качества в промышленном производстве и других отраслях. Только в чистой и упорядоченной среде могут производиться бездефектные, соответствующие требованиям клиентов товары и услуги и реализовываться соответствующая требованиям результативность применяемых процессов. Необходимыми предпосылками для достижения этого является методика 5S, или 5 шагов.
Эффективность управления производством сегодня становится одним из важнейших факторов конкурентоспособности предприятия.
72

ТРАНСВУЗ – 2015
Впоследнее время все большую популярность приобретает бережливое производство. Для его внедрения требуется трансформация менталитета работников и руководителей предприятий, которые обязаны научиться выявлять потери, понимать, какие действия или состояния реально являются потерями, и непрерывно работать над их устранением [1; 4].
Воснове 5S лежит ясная и в то же время инновационная идея: все, что
поддается оптимизации, должно быть оптимизировано!
Преимущества внедрения системы 5S для предприятия:
– уменьшение периода перехода к выпуску другой продукции за счет сокращения времени, затрачиваемого на поиски необходимых предметов;
– предотвращение дефектов, вызванных использованием неподходящих деталей и шаблонов;
– исключение потерь, связанных с ненужными запасами на рабочем месте;
– предотвращение травматизмов;
– содержание оборудования в чистоте. Система 5S включает в себя пять шагов.
Шаг первый – удаление ненужного: все предметы рабочей среды разделяются на три категории: нужные, не нужные срочно и ненужные. Ненужные удаляются по определенным правилам.
Нужные сохраняются на рабочем месте. Не нужные срочно располагаются на определенном удалении от рабочего места или хранятся централизованно.
Распределяются и закрепляются зоны ответственности каждого работника. Таким образом, данное удаление после внедрения планируется привести
кследующим результатам:
–сокращение ненужных запасов;
–сокращение занимаемых площадей;
–сокращение травматизма за счет освобождения производственной среды от ненужного;
–улучшение сохранности сырья, материалов, готовой продукции.
Шаг второй – упорядочение размещения предметов: по отношению к нужным предметам и предметам, не нужным срочно, вырабатываются и реализуются решения, которые обеспечивают:
73

Ремонт и динамика подвижного состава
–быстроту, легкость и безопасность доступа к ним;
–визуализацию способа хранения и контроля наличия, отсутствия или местонахождения нужного предмета;
–свободу перемещения и эстетичность производственной среды;
–эффективное использование рабочих мест, улучшение организации труда;
–сокращение потерь времени на поиски, хождения и т.п.
–сокращение травматизма из-за безопасного способа хранения предметов – создание безопасной ситуации;
–сокращение брака из-за случайного использования несоответствующих компонентов.
Шаг третий – очистка рабочего места, которая предполагает:
–определение основных источников загрязнения рабочего пространства;
– проведение анализа и определение того, кто имеет доступ к документам или деталям, к каким именно, каким образом и т.д. После анализа видно, что будет реализовано:
сокращение простоев из-за неисправности оборудования; улучшение санитарно-гигиенических условий труда; предотвращение утечек пара, газа, воздуха, воды и опасных веществ; сокращение аварий из-за неисправности оборудования; устранение причин аварий, пожаров, несчастных случаев; сокращение брака и потерь, связанных с загрязнением;
сокращение брака из-за неисправности оборудования и контрольноизмерительных приборов.
Шаг четвертый – стандартизация правил уборки, в котором выполняется:
–разработка инструкции, включающей правила пользования документами или деталями в отделах или на участках.
–определение круга лиц, которые имеют право ими пользоваться, а после внедрения получаем:
сокращение потерь за счет визуализации контроля и управления; визуализация контроля безопасности; стандартизация методов контроля.
74

ТРАНСВУЗ – 2015
Заключительный шаг – пятый – формирование привычки соблюдать чистоту и порядок. Утверждение приказом директора, разработанных на 4-м этапе, инструкций, изданных по предприятию.
С людьми, занимающими должности, которые имеют доступ к документам или деталям, проводится инструктаж по работе.
По окончанию инструктажа, подписывается документ, подтверждающий, что человек с инструктажем ознакомлен. Обязательно назначается лицо, ответственное за хранение документов или деталей. При необходимости вводится система штрафов.
Ожидаемый эффект:
–рост выработки за счет мотивированности персонала на производительный труд;
–соблюдение правил охраны труда;
–безопасное производственное поведение;
–сокращение брака из-за невнимательности или недисциплинированности персонала.
Внедрение системы 5S является первым шагом к развертыванию бережливого производства и воспитания в персонале способности осуществлять постоянное совершенствование производственной среды и поддерживать достигнутый уровень. Для повышения эффективности внедрения 5S на железнодорожном предприятии следует вводить конкурсы «Лучший цех», «Самый чистый рабочий участок» и т.д. Одновременно следует присваивать звание «Худший цех» и «Самое грязное рабочее место» для повышения дисциплины.
В ходе проведения 5S – упорядочения, проводится инвентаризация специализированной оснастки и составляется перечень не задействованного специнструмента. По ее итогам должно быть списано и отправлено на дальнейшую утилизацию изношенные и снятые с производства агрегаты и оборудование. Сумма, полученная от утилизации и переработки, и будет суммой прямого экономического эффекта.
Однако, эффект от данных мероприятий заключается не только в снижении затрат на производство, увеличения цены выпускаемой продукции за счет роста качества, снижении затрат времени на изготовление единицы
75

Ремонт и динамика подвижного состава
продукции, но и в психологической составляющей – работники будут с большим энтузиазмом и эффективностью работать на аккуратном, чистом рабочем месте.
Основным результатом является относительная экономия ресурсов, а не затрат, в первую очередь, сокращение остатков незавершенного производства за период, что ведет к экономии на кредитовании или возможности вложения ранее высвободившихся денежных средств в альтернативные мероприятия.
Для внедрения данных изменений необходим человек-лидер, занимающий руководящее положение и имеющий право принимать важные решения и нести за них ответственность. Его следует назначить «агентом изменений», тем, кто будет продвигать идею и контролировать процесс.
Перед внедрением системы требуется провести для всех руководителей подразделений однодневный семинар-тренинг. Менеджеры должны реализовать на своих рабочих местах три первых принципа системы за три месяца.
Каждые три недели они должны участвовать в индивидуально-групповых консультациях по внедрению: сначала обсуждаются накопившиеся вопросы и проблемы в аудитории (в группах по 10 – 12 человек), а затем все члены группы вместе с консультантами последовательно обходят кабинеты, рабочие места каждого члена группы. При этом решения многих проблем находятся именно в ходе таких обсуждений и посещений. Руководители легко будут перенимать опыт друг друга. Достижение результата должно проверяться по контрольному листку.
Следует изменить организационную схему управления. В первую очередь
– изменить штатное расписание. Управление производством доверить мастерам и бригадирам. Все промежуточные управленцы в лице бывших заместителей переводятся в группу развития.
Оценить эффекты от внедрения данного мероприятия до реализации системы 5S сложно. Однако, можно на основе опыта российских предприятий предположить, какими будут выгоды при успешной реализации данного проекта [3].
При успешности внедрения системы 5S возможно перейти к внедрению системы [2], которая основана на: ориентации на потребителя, всеобщем
76

ТРАНСВУЗ – 2015
контроле качества, кружках качества, системе предложений, автоматизации, дисциплине на рабочем месте, всеобщем уходе за оборудованием, повышении качества, росте производительности и разработке новой продукции. Одна из отличительных особенностей системы в том, что она направлена на разработку предложений и инноваций «снизу вверх», то есть работник делает предложение по улучшению, предложение рассматривается, принимается решение – внедрять его или нет. Далее происходит внедрение предложения, и работник поощряется за его идею (в том числе, и в виде процента от экономического эффекта).
Данные мероприятия повлекут не только несомненный материальный эффект для предприятия, но и изменения корпоративной культуры, выражающиеся в более аккуратном и внимательном отношении к собственному рабочему месту и предприятию в целом, росте рационализаторских предложений. Поощрять такие предложения следует материально (премии от 5 до 15 % от заработной платы, организация поездок, экскурсий) и морально в виде грамот, размещения фотографий на досках почета и т.д.
Список литературы
1.Володин, Р. С. Формирование архива документов по системе 5S [Электронный ресурс] / Р. С. Володин. – Форма доступа: http://www.virtpronet.ru/index.php?do=static&page=5s.
2.Имаи, М. Кайдзен: Ключ к успеху японских компаний [Текст] / М. Имаи. – М.: Альпина Бизнес Бук, 2005. – 274 с.
3.Попов, С. Г. Применение методик концепции «Бережливое производство» [Электронный ресурс] / С. Г. Попов. – Форма доступа: http://riastk.ru/mmq/adetail.php?ID=48266.
4.Растимешин, В. Е. Упорядочение / 5S – система наведения порядка, чистоты и укрепления дисциплины с участием всего персонала [Электронный ресурс] / В. Е. Растимешин, Т. М. Куприянова. – Форма доступа: http://www.tpm-centre.ru/page.php?pageId=106&menuItemTreeCode=050304.
77

Ремонт и динамика подвижного состава
УДК 629.424.083
В. К. Лепехин
ИННОВАЦИОННЫЕ ТЕХНОЛОГИИ ДИАГНОСТИРОВАНИЯ ТЯГОВОГО ПОДВИЖНОГО СОСТАВА
Статья посвящена комплексному исследованию инновационных технологий (нестандартного оборудования) и диагностирования тягового подвижного состава в сервисных локомотивных депо. Актуализированы проблемы внедрения системы ремонта тягового подвижного состава с учетом его реального технического состояния на современном этапе развития локомотиворемонтного производства.
Внедрение инновационных технологий на железнодорожном транспорте позволяет существенно снизить эксплуатационные расходы на содержание и ремонт подвижного состава, выбрать рациональную систему ремонта с учетом фактического технического состояния узлов и агрегатов оборудования, повысить надежность подвижного состава в эксплуатации. Внедрение инновационных технологий (нестандартного оборудования) в сервисное локомотивное депо (СЛД) обеспечивает быструю проверку исправности локомотива, работоспособности, правильного функционирования; поиск дефектов.
В системе технического диагностирования локомотивов используются методы, средства, системы и технологические приемы диагностики, базирующиеся на ряде понятий и определений, установленных государственными стандартами. Диагностирование – процесс установления признаков, характеризующих техническое состояние объектов (локомотивов, дизель-поездов), а также его любого элемента, по внешним признакам или параметрам с определенной точностью указания места, вида и причин дефекта, если таковой обнаружен [1].
Средствами диагностирования являются:
– стационарные компьютеры, с уникальным программным обеспечением, позволяющие диагностировать контролируемые параметры, обрабатывать и представлять информацию в цифровом и графическом виде;
78

ТРАНСВУЗ – 2015
–мобильные компьютеры, ноутбуки, позволяющие диагностировать контролируемые параметры, обрабатывать и представлять информацию в цифровом и графическом виде;
–стационарные измерительные приборы;
–мобильные измерительные приборы;
–пульты;
–стенды;
–механизированные рабочие места для разборки и сборки агрегатов и узлов, поступивших в ремонт;
–стендовое оборудование для обкатки, испытания и настройки агрегатов,
узлов;
–оборудование для балансировки вращающихся элементов машин;
–камеры и машины для обдувки и мойки агрегатов, узлов и деталей перед ремонтом;
–камеры для покраски, сушки агрегатов, узлов и деталей;
–кантователи;
–оборудование для демонтажа и монтажа агрегатов и узлов подвижного состава;
–оборудование для совместной притирки деталей и пр. [2].
В качестве примера инновационных технологий стоит назвать такие разработки ОАО «НИИТКД», как комплекс интеллектуальный производственный автоматизированный реостатных испытаний тепловозов «КИПАРИС- 5», аппаратно-программный комплекс АПК «БОРТ», стендовое оборудование для сервисного обслуживания «БОРТ», система контроля и диагностики (СКД) «Доктор-030М».
«КИПАРИС-5» является изделием нового поколения. Предназначен для диагностирования, контроля параметров, обработки и представления информации в цифровом и графическом виде; выдачи рекомендаций и указаний по настройке параметров дизель-генераторных установок (ДГУ) магистральных и маневровых тепловозов серий 2ТЭ10, 2ТЭ116, 2ТЭП70, М62, ТЭМ2, ТЭМ7, ТЭМ18, ЧМЭ3 при проведении реостатных испытаний в условиях СЛД и ремонтных заводов.
Комплекс позволяет проводить оценку технического состояния дизельгенераторной установки тепловоза при минимальном демонтаже его
79