
Pivovarennaya_inzheneria_ / Глава 6a
.pdf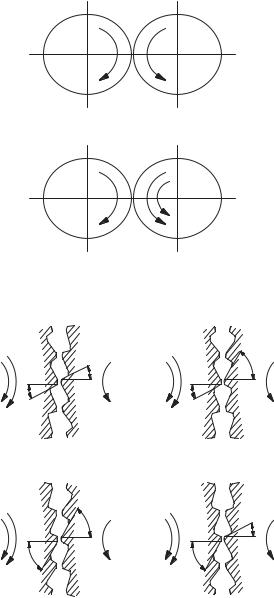
ПРОИЗВОДСТВО ПИВА |
317 |
|
|
Ориентация пары совместно рабо тающих рифленых валков относи тельно друг друга может быть различ ной и обеспечивать взаимодействие рифлей (рис. 6.10): а — «острие по острию» ; б — «острие по спинке»; в — «спинка по спинке» ; г — «спинка по острию». Чаще используют соче тание «острие по острию» и «спинка по спинке». При взаимодействии рифлей по схеме «острие по ост рию» измельчаемая частица поддер живается режущей гранью медленно вращающегося валка и измельчается режущей гранью быстровращающегося валка; при этом происходит главным образом скалывание материала, что способствует образованию крупных фракций. При взаимодействии риф лей по схеме «спинка по спинке» части цы измельчаются в более мелкие фракции. Соответствующее взаимо расположение рифлей обеспечивают той или иной ориентацией валков при установке их в дробилку.
К дроблению солода на валко вых дробилках с гладкими валками предъявляют следующие требования:
•солод не должен проскальзы вать между валками;
•солод должен раздавливаться,
но при этом не истираться.
В соответствии с указанными тре бованиями необходимо обеспечить
условия эффективной работы валков (рис. 6.11).
Первому требованию, не допуска ющему проскальзывание зерна, соот ветствует условие
µ > tg α, |
(6.3) |
где: µ — коэффициент трения части цы о поверхность валков; для су хого пивоваренного солода µ = 0,37; α – половина угла захвата (угла,
а)
а)
б)
б)
Рис. 6.9. Схемы вариантов скоростного взаимодействия валков: а и б — вращение валков с одинаковой и различной частотой
а) |
б) |
|
β |
|
β |
α |
α |
а) |
б) |
в) |
г) |
|
β |
|
α |
β |
β |
в) |
г) |
Рис. 6.10. |
Схемы взаимодействия рифлей валков |
|
при дроблении солода: |
а— «острие по острию»; б — «острие по спинке»;
в— «спинка по спинке»; г — «спинка по острию»
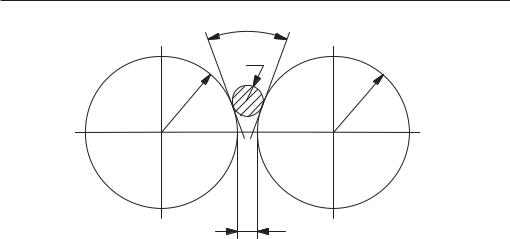
318 ПИВОВАРЕННАЯ ИНЖЕНЕРИЯ
|
2α |
|
r |
R |
R |
2b
Рис. 6.11. Схема взаимодействия зерна с валками дробилки
образованного касательными к поверхности валков в точках соприкосновения с частицей измельчаемого материала).
Если принять tg α = 0,37, то αmax ≈ 20°, а максимальный угол захвата 2α ≈ 40°.
Если сила трения недостаточно велика, то частицы материала будут лишь скользить по поверхности валков и дробления происходить не будет.
Второму требованию отвечает еще одно условие — оптимальное соотношение между размером частиц и шириной зазора между валками
R + b |
= cos α, |
(6.3) |
|
|
R + r |
||
|
|
|
где R — радиус валков, м; r — радиус измельчаемых частиц, м; b — половина ширины зазора между валками, м.
Если принять α = 20°, то cos α = 0,94.
Для качественного дробления солода необходимо обеспечить непрерывную и рав номерную подачу его на валки, периодически проверять параллельность их установки, регулировать расстояние между ними в соответствии с размерами измельчаемых час тиц. Зазор между валками регулируется в пределах 0–2,5 мм с точностью до 0,03 мм. Современные солододробилки могут быть оснащены системой автоматического регу лирования зазора между валками.
Валковые дробилки компактны и надежны в эксплуатации. Степень измельчения материала на валковых дробилках — от 3 до 10.
Ориентировочная мощность, затрачиваемая на дробление 1000 кг солода, состав ляет 4–5 кВт.
6.3.2.3. Организация дробления солода
Дробление солода может быть организовано различными способами, основные осо бенности которых рассмотрены ниже.
ПРОИЗВОДСТВО ПИВА |
319 |
|
|
Сухое дробление — наиболее простой традиционный способ дробления солода, пре дусматривающий равномерную подачу солода в дробилку, обработку солода на валках и сбор дробленого солода в промежуточном бункере.
Кондиционированное дробление — более совершенный способ дробления солода, предусматривающий предварительное увлажнение солода, выдерживание зерна, рав номерную подачу солода в дробилку, обработку солода на валках и сбор дробленого солода в промежуточном бункере.
Дробление кондиционированного солода осуществляют на обычных дробилках для сухого дробления, но перед дроблением солод предварительно увлажняют насыщен ным паром низкого давления (при избыточном давлении 0,05 МПа) или водой при температуре 30–35 °С, доводя его до нужных кондиций. Продолжительность кондици онирования составляет 1–2 мин.
Технологическая цель увлажнения солода перед дроблением заключается в повыше нии эластичности и прочности оболочек зерна, вследствие чего они в меньшей степени разрушаются при дроблении, а их объем увеличивается на 10–20%. Благодаря этому слой дробины в фильтрационном аппарате становится более рыхлым и проницаемым, что способствует увеличению производительности процесса. Кроме того, быстрее достигается полнота осахаривания, возрастают выход экстракта и конечная степень сбраживания.
При паровом кондиционировании (запаривании) влажность оболочек зерна уве личивается на ~1,2–1,5%. При этом необходимо строго следить, чтобы температура солода не превышала 40 °С, поскольку это может привести к инаивации термолабиль ных ферментов солода, в частности эндо β глюканазы.
При водяном кондиционировании влажность оболочек зерна возрастает на 2,0– 2,5%, в то время как влажность эндосперма возрастает всего на 0,3–0,5%.
Мокрое дробление солода заключается в предварительном увлажнении солода с применением большего количества воды. Продолжительность увлажнения — около 20 мин. Влажность солода при этом повышается до 18–25%. Учитывая, что при влаж ности солода более 15% для хорошего дробления достаточно однократного сжатия зерна, для мокрого дробления обычно используют двухвалковые дробилки.
Принцип мокрого дробления основан на том, что при обработке горячей водой мучнистая часть солода набухает и легко отделяется от оболочки, и даже после одно кратного сжатия в двухвалковых дробилках зерно раздавливается. При этом эластич ная оболочка почти полностью сохраняется, освобождаясь от мучнистой части.
В процессе мокрого дробления дробленый материал смешивается в заданном соот ношении с водой, в результате чего на выходе из дробилки получают готовый затор, перекачиваемый в заторный аппарат для осахаривания.
Конструктивное оформление и технологические возможности вышеуказанных спо собов дробления солода описаны ниже.
6.3.2.4. Строение систем дробления солода
Операторные модели (операторы) основных технологических систем дробления солода приведены на рис. 6.12.
Примеры функциональных схем основных систем дробления солода приведены на рис. 6.13.
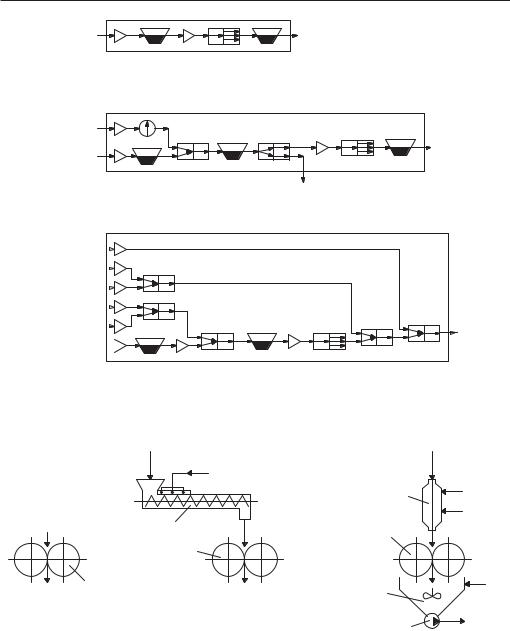
320 ПИВОВАРЕННАЯ ИНЖЕНЕРИЯ
а) |
Дробленный |
|
Солод |
||
солод |
||
|
||
|
а) |
|
б) |
|
|
Вода |
|
|
|
Дробленный |
|
Солод |
солод |
|
|
Избыточная влага |
|
|
б) |
в)
Молочная кислота
Горячая вода
Холодная вода
Горячая вода
Холодная вода
Затор
Солод
в)
Рис. 6.12. Операторы основных технологических систем дробления солода:
а, б и в — сухое, кондиционированное и дробление
а) |
б) |
в) |
|
|
Солод |
Солод |
|
|
Вода |
|
|
|
|
Увлажнение и |
Вода |
|
|
корректировка pH |
|
|
|
Молочная |
|
|
|
|
|
Солод |
Увлажнение |
Дробление |
кислота |
|
|
|
|
|
Дробление |
|
|
|
Дробление |
Приготовление |
Вода |
Дробленный |
Дробленный |
затора и его |
|
солод |
солод |
гомогенизация |
|
|
|
Транспортирование |
Затор |
|
|
|
|
а) |
б) |
в) |
|
Рис. 6.13. Функциональные схемы основных систем дробления солода: |
|
||
|
а, б и в — сухое, кондиционированное и мокрое дробление |
|
ПРОИЗВОДСТВО ПИВА |
321 |
|
|
6.3.2.5.Инженерные задачи при дроблении солода
Впроцессе дробления зернопродуктов необходимо обеспечить следующие инже
нерные задачи:
• загрузку зернопродуктов в дробильную систему;
• равномерное распределение измельчаемого материала между рабочими органа
ми дробилки;
• обеспечение условий взрывобезопасности;
• выгрузку из дробильной системы и транспортировку дробленых зернопродуктов;
• обеспечение надлежащего санитарного состояния дробильной системы и комму никаций.
Помимо этого, в дробильных системах для мокрого дробления солода необходимо обеспечить приготовление затора — смешать в определенной пропорции дробленый солод с водой, обеспечить гомогенизацию этой смеси, а при необходимости и откор ректировать в ней значение рН.
6.3.3.Оборудование для дробления солода
6.3.3.1.Классификация систем для дробления солода
Применяемое в настоящее время дробильное оборудование можно классифициро вать по следующим морфологическим признакам:
•по способу дробления (сухое, кондиционированное, мокрое);
•по функциональному назначению (помимо дробления в дробильных системах могут решаться и другие функциональные задачи — см. табл. 6.11);
•по виду основных рабочих органов (валки, молотки и пр.);
•по количеству стадий измельчения (как правило, от 1 до 3 стадий);
•по количеству основных рабочих органов (в валковых дробилках от 2 до 6 валков);
•по виду конструкционного материала и пр.
В общем виде классификацию систем дробления солода можно представить следующим образом.
Морфологический |
|
Варианты исполнения |
|
|
|
|
признак |
а |
б |
в |
г |
д |
е |
Способ дробления |
Сухое |
Кондициониро2 |
Мокрое |
|
|
|
|
|
ванное |
|
|
|
|
Функциональность |
Дробление |
Увлажнение |
Увлажнение, |
|
|
|
|
|
и дробление |
дробление, |
|
|
|
|
|
|
приготовление |
|
|
|
|
|
|
и транспорти2 |
|
|
|
|
|
|
ровка затора |
|
|
|
Вид рабочих органов |
Валки |
Молотки |
|
|
|
|
Количество стадий |
Одна |
Две |
Три |
... |
|
|
измельчения |
|
|
|
|
|
|
Количество рабочих |
2 |
3 |
4 |
5 |
6 |
|
органов |
|
|
|
|
|
|
Конструкционный |
Углеродистая |
Нержавеющая |
|
|
|
|
материал |
сталь |
сталь |
|
|
|
|

322 |
ПИВОВАРЕННАЯ ИНЖЕНЕРИЯ |
|
|
6.3.3.1.1. Дробилки для сухого дробления солода
Дробление сухого солода, влажность которого составляет обычно 5–6%, осуществляют на многопозиционных валковых дробилках.
Дробилки для сухого дробления целесообразно размещать непосредственно над варочным отделением, причем между дробилкой и заторным аппаратом устанавливают промежуточный бункер для дробленого солода, применение которого позволяет дробить солод постепенно, что способствует снижению пикового потребления электроэнергии.
Вместимость промежуточного бункера определяют с учетом того, что на 1 т дробле ного солода требуется 2,7–3,0 м3 объема бункера. Угол естественного откоса дроблено го солода — 45°, поэтому, чтобы организовать беспрепятственное опорожнение бунке ра, угол днища должен быть 65° .
Продолжительность дробления зернозасыпи на одну варку составляет обычно око ло 1 ч. Транспортирование дробленого солода из промежуточного бункера в заторный аппарат осуществляют, как правило, за 10–15 мин. Продолжительность хранения дроб леного солода в бункере должна быть минимальной для того, чтобы:
•уменьшить негативные последствия окислительных процессов, начинающихся немедленно после измельчения зерна;
•предотвратить развитие микроорганизмов в помоле (особенно после кондицио нирования).
Для сухого дробления солода чаще всего применяют двух , четырех и шестивалковые дробилки. Гораздо реже можно встретить на производстве трех и пятивалковые дробилки.
Наиболее просты по конструкции двухвалковые дробилки (рис. 6.14), которые обычно применяют на предприятиях малой мощности — мини пивоварнях.
Солод |
Солод |
||||||
Солод |
Солод |
||||||
|
|
|
|
|
|
|
|
|
|
|
|
|
|
|
|
Дробленный солод |
Дробленый солод
Дробленный солод |
Дробленый солод
Рис. 6.14. Двухвалковая дробилка
Параллельно расположенные валки дробилки закреплены в подшипниках, причем один из них вращается в неподвижных, а другой — в скользящих подшипниках, кото рые с помощью специального механизма удерживаются в нужном положении, обеспе чивая необходимый зазор между валками, составляющий обычно 0,7–0,8 мм.
Во избежание поломки дробилки при случайном попадании в нее частицы повы шенной твердости срабатывает пружинный предохранительный механизм — подвиж ный валок отжимается, и твердая частица выпадает из дробилки.

ПРОИЗВОДСТВО ПИВА |
323 |
|
|
Диаметр валков с гладкой поверхностью составляет обычно 250 мм. Частота вра щения валков около 3 с–1, а их окружная скорость составляет обычно 2,0–4,5 м/с.
Распределение солода по длине валков должно быть равномерным. При этом удельная производительность по солоду должна составлять 15–20 кг на 1 см длины валка в час. При плохо растворенном солоде удельная подача должна быть меньше, а при хорошо растворенном — выше.
Примерные результаты сухого дробления солода на двухвалковых дробилках при ведены в табл. 6.4.
|
|
|
|
Таблица 6.4 |
Примерный фракционный состав помола солода на двухвалковой дробилке |
||||
|
|
|
|
|
№ сита |
Размер отверстия, мм |
Фракция |
Содержание (%) |
|
1 |
1,270 |
Оболочки |
15,2 |
25,0 |
2 |
1,010 |
Крупа |
12,9 |
17,0 |
3 |
0,547 |
Крупная крупка |
33,9 |
29,0 |
4 |
0,253 |
Мелкая крупка |
18,1 |
15,4 |
5 |
0,152 |
Мука |
6,4 |
5,1 |
Дно |
— |
Пудра |
13,5 |
8,5 |
Итого |
|
|
100,0 |
100,0 |
Удельный объем, мл/100 г |
|
430 |
520 |
|
Зазор между валками, мм |
|
0,7 |
0,8 |
Концепция однопозиционного дробления на одной паре валков используется также при мокром дроблении, но конструкция этих дробилок и режимы работы (см. раздел 6.3.3.1.3) отличаются от вышеописанных двухвалковых дробилок для су хого дробления.
При использовании четырехвалковых дробилок (рис. 6.15) дробленый солод, прой дя через первую (рифленую) пару валков, разделяется на подвижных плоских ситах
а) |
|
|
Солод |
б) |
Солод |
|||||||
|
|
|
|
|
|
|
|
|
|
|
|
|
|
|
|
|
|
|
|
|
|
|
|
|
|
|
|
|
|
|
|
|
|
|
|
|
|
|
|
|
|
|
|
|
|
|
|
|
|
|
|
|
|
|
|
|
|
|
|
|
|
|
|
|
|
|
|
|
|
|
|
|
|
|
|
|
|
|
|
|
|
|
|
|
|
|
|
|
|
|
|
|
|
|
|
|
|
|
|
|
|
|
|
|
|
|
|
|
|
|
|
|
|
|
|
|
|
|
|
|
|
|
|
|
|
|
|
|
|
|
|
|
|
|
|
|
|
|
|
|
|
|
Шелуха |
Крупа |
Шелуха |
Крупа |
Рис. 6.15. Принципиальное устройство четырехвалковых дробилок:
а — для дробления мучнистого солода; б — для дробления стекловидного солода
324 |
ПИВОВАРЕННАЯ ИНЖЕНЕРИЯ |
|
|
на две фракции — крупу и оболочки. В зависимости от качества солода последующему дроблению на второй паре гладких валков подвергают либо одну, либо другую фракции. Зазор между первой парой валков составляет 1,5–1,6 мм, а между второй — 0,6–0,7 мм.
Если перерабатывается рыхлое мучнистое зерно хорошо растворенного солода, то вторичному размолу подвергают оболочки (рис. 6.15, а). Удельная производитель ность по солоду такой дробилки составляет около 25 кг/(см ч). Частота вращения валков первой пары составляет 3,0–3,4 с–1, а второй пары 3,3–3,7 с–1. Для лучшего со хранения оболочек обе пары валков могут быть гладкими.
Если перерабатывается твердое стекловидное зерно, то вторичному размолу под вергают крупу (рис. 6.15, б). Удельная производительность по солоду такой дробилки составляет около 20–25 кг/(см ч). Частота вращения валков первой пары составляет 2,6–3,0 с–1. Вторая пара может иметь б\льшую частоту вращения, часто ее делают диф ференцированной, например, 5,5 / 2,7 с–1. Первую пару валков изготавливают обычно с гладкой поверхностью, а вторую — с рифленой.
Частота колебаний подвижных вибросит составляет около 7,5 с–1, а амплитуда — 15–20 мм. Набор сит в дробилках может меняться в зависимости от технологических задач, поставленных перед дроблением. Для лучшего освобождения ситовой поверх ности и отбивки от них мучной пыли сита дробилок снабжают резиновыми шариками.
Четырехвалковые дробилки применяют главным образом на предприятиях сред ней мощности при дроблении как сухого, так и кондиционированного (увлажненного) солода, речь о котором пойдет в следующем разделе. Наиболее предпочтительны четы рехвалковые дробилки для получения грубого помола при использовании на предпри ятии в составе варочной установки заторно фильтрационного аппарата.
Примерные результаты дробления солода на четырехвалковых дробилках приведе ны в табл. 6.5.
Таблица 6.5
Примерный фракционный состав помола солода на четырехвалковой дробилке
№ сита |
Размер |
Фракция |
Содержание (%) при дроблении солода: |
|||
отверстия, мм |
|
сухого |
увлажненного |
|||
|
|
|
||||
1 |
1,270 |
Оболочки |
26,4 |
|
21,6 |
22,3 |
2 |
1,010 |
Крупа |
14,3 |
|
12,8 |
11,5 |
3 |
0,547 |
Крупная крупка |
29,4 |
|
32,0 |
25,7 |
4 |
0,253 |
Мелкая крупка |
13,5 |
|
16,0 |
16,9 |
5 |
0,152 |
Мука |
4,7 |
|
4,8 |
8,8 |
Дно |
— |
Пудра |
11,9 |
|
12,8 |
14,8 |
Итого |
|
|
100,0 |
|
100,0 |
100,0 |
Удельный объем, мл/100 г |
|
470 |
|
520 |
810 |
|
Зазор между валками верхней пары, мм |
1,6 |
|
1,5 |
1,10 |
||
Зазор между валками нижней пары, мм |
0,7 |
|
0,6 |
0,55 |
Конструктивное устройство четырехвалковой дробилки БДА 1М показано на рис. 6.16. Нижняя пара валков диаметром 250 мм имеет гладкую шлифованную поверхность, а верхняя — рифленую. Валки расположены параллельно и вращаются навстречу друг

ПРОИЗВОДСТВО ПИВА |
325 |
|
|
|
|
|
|
|
|
|
|
|
|
|
|
|
|
|
|
1 |
|
|
||||||||||||
|
|
|
|
|
|
|
|
|
|
|
|
|
|
|
|
2 |
|
|
||||||||||||
|
|
|
|
|
||||||||||||||||||||||||||
|
|
|
|
|
|
|
|
|
|
|
|
|
|
|
|
3 |
|
|
||||||||||||
|
|
|
|
|
||||||||||||||||||||||||||
|
|
|
|
|
|
|
|
|
|
|
|
|
|
|
|
|
|
|
|
|
|
|
|
|
|
|
|
|
|
|
|
|
|
|
|
|
|
|
|
|
|
|
|
|
|
|
|
|
|
|
|
|
|
|
|
|
|
|
|
|
|
|
10 |
|
|
|
|
|
|
|
|
|
|
|
|
|
|
|
|
|
|
|
|
|
|
|
|
|
4 |
|||
|
|
|
|
|
|
|
|
|
|
|
|
|
|
|
|
|
|
|
|
|
|
|
|
|
|
|||||
|
|
|
|
|
|
|
|
|
|
|
|
|
|
|
|
|
|
|
|
|
|
|
|
|
|
|||||
|
|
|
|
|
|
|
|
|
|
|
|
|
|
|
|
|
|
|
|
|
|
|
|
|
|
|
|
|
|
|
|
|
|
|
|
|
|
|
|
|
|
|
|
|
|
|
|
|
|
|
|
|
|
|
|
|
|
|
|
|
|
|
|
|
|
|
|
|
|
|
|
|
|
|
|
|
|
|
|
|
|
5 |
||||||||||
|
|
|
|
|
|
|
|
|
|
|
|
|
|
|
|
|||||||||||||||
|
|
|
|
|
|
|
|
|
|
|
|
|
|
|||||||||||||||||
9 |
|
|
|
|
|
|
|
|
|
|
|
|
|
|
6 |
|||||||||||||||
|
|
|
|
|
|
|
|
|
|
|
|
|
||||||||||||||||||
|
|
|
|
|||||||||||||||||||||||||||
|
|
|
|
|
|
|
|
|
|
|
|
|
|
|
|
|
|
|
|
|
|
|
|
|
|
|
|
|
|
|
8 |
|
|
|
|
|
|
|
|
|
|
|
7 |
|||||||||||||||||||||||||||||
|
|
|
|
|
|
|
|
|
|
|
|||||||||||||||||||||||||||||||
|
|
|
|
|
|
|
|
|
|
|
|
|
|
|
|
|
|
|
|
|
|
|
|
|
|
|
|
|
|
|
|
|
|
|
|
|
|
|
|
|
|
|
|
|
|
|
|
|
|
|
|
|
|
|
|
|
|
|
|
|
|
|
|
|
|
|
|
|
|
|
|
|
|
|
|
|
|
|
|
|
|
|
|
|
|
|
|
|
|
|
|
|
|
|
|
|
|
|
|
|
|
|
|
|
|
|
|
|
|
|
|
|
|
|
|
|
|
|
|
|
|
|
|
|
|
|
|
|
|
|
|
|
|
|
|
|
|
|
|
|
|
|
|
|
|
|
|
|
|
|
|
|
|
|
|
|
|
|
|
|
|
|
|
|
|
|
|
|
|
|
|
|
|
|
|
|
|
|
|
|
|
|
|
|
|
|
|
|
|
|
|
|
|
|
|
|
|
|
|
|
|
|
|
|
|
|
|
|
|
|
|
|
|
|
|
|
|
|
|
|
|
|
|
|
|
|
|
|
|
|
|
|
|
|
|
|
|
|
|
|
|
|
|
|
|
|
|
|
|
|
|
|
|
|
|
|
|
|
|
|
|
|
|
|
|
|
|
|
|
|
|
|
|
|
|
|
|
|
|
|
|
|
|
|
|
|
|
|
|
|
|
|
|
|
|
|
|
|
|
|
|
|
|
|
|
|
|
|
|
|
|
|
|
|
|
|
|
|
|
|
|
|
|
|
|
|
|
|
|
|
|
|
|
|
|
|
|
|
|
|
|
|
|
|
|
|
|
|
|
|
|
|
|
|
|
|
|
|
|
|
|
|
|
|
|
|
|
|
|
|
|
|
|
|
|
|
|
|
|
|
|
|
|
|
|
|
|
|
|
|
|
|
|
|
|
|
|
|
|
|
|
|
|
|
|
|
|
|
|
|
|
|
|
|
|
|
|
|
|
|
|
|
|
|
|
|
|
|
|
|
|
|
|
|
|
|
|
|
|
|
|
|
|
|
|
|
|
|
|
|
|
|
|
|
|
|
|
|
|
|
|
|
|
|
|
|
|
|
|
|
|
|
|
|
|
|
|
|
|
|
|
|
|
|
|
|
|
|
|
|
|
|
|
|
|
|
|
|
|
|
|
|
|
|
|
|
|
|
|
|
|
|
|
|
|
|
|
|
|
|
|
|
|
|
|
|
|
|
|
|
|
|
|
|
|
|
|
|
|
|
|
|
|
|
|
|
|
|
|
|
|
|
|
|
|
|
|
|
|
|
|
|
|
|
|
|
|
|
|
|
|
|
|
|
|
|
|
|
|
|
|
|
|
|
|
|
|
Рис. 6.16. Четырехвалковая дробилка БДА21М:
1 — бункер; 2 — питающий валик; 3 — заслонка; 4, 6 — верхняя и нижняя пара валков; 5 — сито; 7 — станина; 8 — привод; 9 — эксцентриковый вал; 10 — ограждение
к другу с различными скоростями. Для регулирования величины помола один валок каждой пары выполнен неподвижным, а другой — подвижным. Под верхней парой валков установлено сито, с помощью которого дробленый солод разделяется на фракции. Сито подвешено на плоских пружинах и получает колебательное движение через тягу от эксцентрикового вала. Привод машины осуществляется от электродвигателя по средством клиноременной передачи.
Впроцессе работы сухой солод через магнитный сепаратор и автоматические весы поступает в приемный бункер 1. Рифленый питающий валик 2, установленный в ниж ней части бункера, ровным слоем подает солод в зазор между верхними валками 4. Количество поступающего солода регулируется заслонкой 3. Верхней парой валков солод дробится, и проходом сквозь сито 5 мелкая крупка и мука ссыпаются в бункер,
ашелуха и крупная фракция сходом поступают на нижнюю пару валков 6, где опять дробятся, и ссыпаются в бункер. Для получения пробы размолотого продукта под каж дой парой валков установлены пробоотборники.
Наиболее совершенное измельчение солода обеспечивается в шестивалковой дро билке (рис. 6.17).
Вконструкциях шестивалковых дробилок применяют как гладкие, так и рифленые валки, причем сочетание их может быть различным.
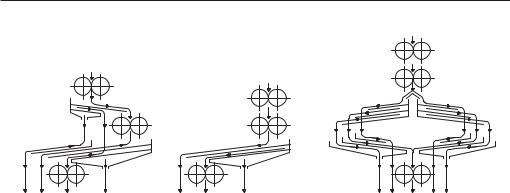
326 ПИВОВАРЕННАЯ ИНЖЕНЕРИЯ
а) |
б) |
в) |
|
|
Солодд |
||||
|
|
|
Солод
Солод
Солод
Солод
Мука Крупа Мука |
Шелуха Крупа Мука |
Мука Крупа Мука |
Шелуха |
|
а |
|
Шелуха Шелуха |
|
Шелуха |
б) |
Шелуха Шелуха |
а) |
в) |
Рис. 6.17. Принципиальное устройство шестивалковых дробилок:
а— фирмы Мeag (Германия); б — фирмы Schmidt2Seeger (Германия);в — фирмы Buehler (Германия)
Водних конструкциях валки верхней и средней пар имеют гладкую поверх ность и вращаются с одинаковой окружной скоростью. Благодаря этому на первой паре — солод, а на второй — оболочки подвергаются только сжатию, в результате чего происходит раздавливание материала, но не растирание. Валки нижней пары имеют рифленую поверхность и предназначены для раскалывания крупы.
Вдругих конструкциях валки верхней пары рифленые, а средней и нижней — глад кие, в третьих конструкциях валки всех пар рифленые, иногда с разным профилем рифлей. Параметры одного из вариантов установки валков в шестивалковой дробил ке приведены в табл. 6.6.
|
|
|
|
|
|
Таблица 6.6 |
|
Варианты размещения рифленых валков в шестивалковой дробилке |
|
||||
|
|
|
|
|
|
|
|
Перед использованием фильтрационного |
Перед использованием заторного |
||||
Пара |
аппарата (грубое дробление) |
фильтр2пресса (тонкое дробление) |
||||
Схема |
Зазор (мм) |
Схема |
|
Зазор (мм) |
||
валков |
при дроблении: |
|
||||
взаимодействия |
взаимодействия |
|
при сухом |
|||
|
|
кондициони2 |
|
|||
|
валков |
сухом |
валков |
|
дроблении |
|
|
рованном |
|
||||
|
|
|
|
|
|
|
Верхняя |
«Спинка по спинке» |
1,3–1,6 |
0,9–1,2 |
«Острие по острию» |
|
0,9–1,2 |
Средняя |
«Спинка по спинке» |
0,7–0,8 |
0,5–0,6 |
«Острие по острию» |
|
0,4–0,45 |
Нижняя |
«Острие по острию» |
0,3–0,4 |
0,2–0,4 |
«Острие по острию» |
|
0,15–0,2 |
Примерные результаты дробления солода на шестивалковых дробилках приведены в табл. 6.7.
После первой пары валков осуществляют фракционирование дробленого солода на первой группе подвижных сит, при этом сход с верхнего сита — оболочки — подают на вторую пару валков, на которых происходит не столько измельчение оболочек, сколь ко отделение от прилипших к ним частичек эндосперма, главным образом крупы.
После второй пары валков также осуществляют фракционирование на второй группе подвижных сит, при этом сход с верхнего сита — оболочки — отводят из дробилки, а крупу после первой и второй группы сит подвергают дополнительному дроблению на