
Калин Физическое материаловедение Том 6 Част 2 2008
.pdfвающуюся с водой (вазелиновое и силиконовое масла, три- и тетрахлорэтилен).
В процессе движения капель в дисперсионной среде они нагреваются, происходит гидролиз гелеобразования в их объеме. Размер получаемых микро сфер формируется на стадии диспергирования рабочего раствора в дисперсионную среду. Он зависит от диаметра капилляра и скорости истечения рабочего раствора. Наложение вибрации на струю рабочего раствора позволяет существенно снизить разброс размеров получаемых капель и повысить производительность процесса диспергирования. Изменяя частоту колебаний, диаметр капилляра и скорость истечения можно варьировать размер капель и, следовательно, гель-сфер в широком диапазоне размеров.
Термообработка микросфер. Режим сушки выбирают в зави-
симости от назначения микросфер. Для изготовления виброуплотненных твэлов требуются микросферы с высокой плотностью, поэтому сушку проводят на воздухе при минимальной температуре. В этом случае размеры кристаллитов будут минимальными и при спеканий микросфер легко получают плотность до 98 % ТП.
Если микросферы предполагается использовать для прессования таблеток, сушку проводят при высокой упругости паров воды и высокой температуре слоя гель-сфер, что обеспечивается, например, в аппарате сушки без продува воздуха. Это снижает усадку гель-сфер и одновременно обеспечивает рост кристаллов.
Высушенные гель-сферы подвергают прокаливанию при 600 – 700 С с целью более полного удаления воды, аммиака и остатков ГМТА с карбамидом.
Основное влияние на физические (удельная поверхности плотность, размер кристаллитов) и механические свойства микросфер (прочность, модуль упругости) оказывает температура прокаливания. При получении микросфер для виброуплотненных твэлов спекание ведут в атмосфере водорода при 1600 С в течение 4 ч.
Для получения твэлов с виброуплотненными сердечниками с высокой эффективной плотностью (~90 % ТП) производят микросферы трех фракций с диаметром 1200, 300 и 30 – 50 мкм в соотношении 40:10:1.Микросферы, предназначенные для прессования таблеток, должны иметь высокую плотность и небольшую прочность. Поэтому они подвергаются только прокаливанию при тем-
221
пературе 600 С. В зависимости от качества исходных микросфер и режима прессования таблетки могут иметь разную плотность и микроструктуру.
Производство виброуплотненного топлива. В России первые эксперименты по использованию виброуплотненного оксидного топлива (ВОТ) для реакторов на быстрых нейтронах были начаты в ГНЦ РФ ВНИИНМ. Затем, в связи с развертыванием исследований по перспективному замкнутому топливному циклу реакторов на быстрых нейтронах, эти исследования были продолжены в ГНЦ РФ НИИАР, где в качестве первого этапа предполагались работы по созданию автоматизированной дистанционно-управляемой линии для изготовления виброуплотненных твэлов и ТВС c целью утилизации высокофонового плутония.
По мнению разработчиков, твэлы с виброуплотненным оксидным топливом можно рассматривать как альтернативу таблеточному топливу при создании замкнутого топливного цикла реакторов на быстрых нейтронах с использованием пирохимического метода переработки отработавшего ядерного топлива – метода, обеспечивающего оптимальный путь получения гранулированного топлива для виброуплотнения.
Вотличие от традиционных водных методов переработки ядерного топлива в основу этих работ были положены принципы сухой технологии с использованием пироэлектрохимических методов переработки высокоактивного ядерного топлива в солевых расплавленных системах с получением гранулята, непосредственно пригодного для изготовления твэлов методом виброуплотнения. Так как полученный гранулят имел высокую радиоактивность, то технология его производства и изготовление виброуплотненных твэлов и ТВС были реализованы в горячих камерах, в том числе с использованием автоматизированных дистанционно управляемых процессов. Специфика состоит в том, что ВОТ спекается в процессе эксплуатации в реакторе, поэтому в настоящем разделе кратко рассмотрим принципы получения гранул оксидного топлива и его компактирование в оболочке виброуплотнением.
ВНИИАР разработан пирохимический метод (технологический процесс) получения гранул оксидного топлива – гранулята. Схема организации пирохимических процессов показана на рис. 24.127. Отличительной особенностью пирохимической технологии являет-
222
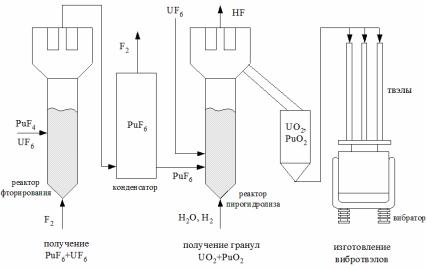
ся проведение всех операций получения осадков в одном аппарате хлораторе – электролизере. Основные стадии процесса пирохимической переработки: растворение исходных продуктов (или отработавшего ядерного топлива) в расплаве солей; выделение из расплава кристаллического диоксида плутония или электролитических диоксидов плутония и урана; обработка катодного осадка и получение гранулированного топлива.
Рис. 24.127. Схема получения гранулята UO2+PuO2
В качестве топлива использовался гранулят различного происхождения (пироэлектрохимический, золь – гель, дробленые таблетки, пирогидролизный, полученный прямой конверсией гексафторида урана в диоксид) и состава (UO2, PuO2, (U + 5 % Pu) O2, (U + 30 % Pu) O2, (U,Pu)O2 + U, (U,Pu)O2 + Gd). В качестве выгорающего поглотителя в состав топливного сердечника на стадии смешивания вводился порошок металлического гадолиния. В ходе этих работ подтверждены ранее полученные закономерности по выбору оптимального фракционного состава для достижения необходимой эффективной плотности. Разработанная технология обеспечивает неравномерность распределения компонентов топливного сердечника не хуже ±5 %.
223
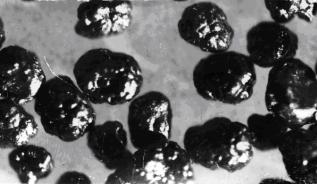
Прямой выход гранулята диоксида урана составляет 95 – 98 %. Безвозвратные потери урана не превышают 0,1 %. Опытная установка пирогидролиза с реактором КС имела производительность ~0,5 кг UО2 в час. Для коррекции кислородного потенциала топлива и устранения влияния технологических примесей в состав гранулированного топлива на стадии приготовления порции порошка на один твэл вводится геттер в виде гранул металлического урана. Частицы порошка геттера имеют форму близкую к сферической с максимальным диаметром до 100 мкм. Технологический процесс обеспечивает равномерность распределения геттера по длине топливного сердечника в пределах 5 % от номинального уровня. Содержание геттера было оптимизировано с учетом термодинамических характеристик и необходимости достижения требуемого достехиометрического кислородного потенциала топлива.
Использование топливной композиции с добавкой геттера (UPu)O2 + U позволяет полностью исключить коррозионные процессы при последующем облучении твэлов, обусловленные наличием цезия и галогенов, а также возможными технологическими примесями, что практически расширяет предел по выгоранию из-за физико-химического взаимодействия топливо-оболочка. Гранулят диоксида урана, полученный методом пирогидролиза показан на рис. 24.128.
Рис. 24.128. Гранулят диоксида урана, полученный пирогидролизом
Процесс прямой конверсии гексафторида урана в гранулированный оксид заключается в следующем. В нагретый реактор, в кото-
224
ром потоком инертного газа (или азота) снизу создается «кипящий слой» (КС) частиц («затравки») диоксида урана вводятся газообразный гексафторид и смесь паров воды и водорода. При температуре 700 – 900 °С протекает реакция пирогидролиза:
UF6 + 2H2O + Н2 UO2 + 6HF.
В результате многоциклового взаимодействия циркулирующих частиц КС с гексафторидом и последующего обесфторивания микрослоев фторидов с образованием диоксида урана частицы КС растут в виде шарообразных гранул, достигая размеров от ~100 до 1200 мкм. Необходимые для изготовления твэлов методом виброуплотнения частицы размером менее 100 мкм получают дроблением промежуточных фракций. Интенсификация процесса путем перегрева частиц за счет пропускания через КС электрического тока позволила увеличить температуру обесфторивания и спекания частиц до 1400 – 1600 °С, и сделать процесс пирогидролиза практически одностадийным. Прямой выход гранулята диоксида урана составляет 95 – 98 %, на фильтрах улавливается 2 – 5 % урана в виде пыли оксидов и оксидофторидов; безвозвратные потери урана не превышают 0,1 %. При промышленном использовании процесса пирогидролиза основная часть технологического газа (азот + водород) после конденсации фтористоводородной кислоты может быть возвращена в реактор пирогидролиза, т.е. зациклована. Гранулят диоксида урана, полученный методом пирогидролиза, характеризуется следующими показателями:
пикнометрическая плотность частиц 10,6 – 10,8 г/см3;
насыпная плотность 6,9 ± 0,1 г/см3;
текучесть 22 ± 2 г/с;
кислородный коэффициент О/М 1,995 ± 0,005;
содержание фтора < 5 × 10-3 масс %;
содержание остальных примесей соответствует ТУ на ядерное топливо.
Технология виброуплотнения. Основная цель виброуплотне-
ния гранулированного топлива в оболочке твэла – получение эффективной максимальной плотности топливного сердечника при равномерном ее распределении по длине твэла, как при использо-
вании гомогенной (UO2), так и механической (UO2 + PuO2) смеси гранул. Используют два способа изготовления: метод инфильтра-
225
ции (пропитки) каркаса для сферических частиц и высокоэнергетическое уплотнение частиц неправильной формы при одновременной загрузке всех фракций гранулята в оболочку твэла.
Изготовление твэлов с гранулированным топливом проводится по стандартной процедуре (в перчаточных боксах или защитных камерах). Основные преимущества технологии виброуплотнения и твэлов с виброуплотненным топливом: простота и надежность производственного процесса за счет меньшего количества технологических и контрольных операций, облегчающего автоматизацию и дистанционное управление; возможность использования гранулята любой формы: как гомогенного состава, так и в виде механической смеси; меньшее, по сравнению с таблеточным сердечником, термомеханическое воздействие виброуплотненного сердечника на оболочку при набросах мощности реактора; возможность изготовления твэлов произвольного профиля; ослабленные требования к внутреннему диаметру оболочек твэлов; возможность применения топливных сердечников с легко варьируемыми параметрами и на основе многокомпонентных композиций.Преимущество всей технологии производства виброуплотненного топлива могут наиболее полно проявиться при реализации пристанционного замкнутого топливного цикла реакторов на быстрых нейтронах, в котором используется высокоактивное (регенерированное) топливо.
В результате виброуплотнения эффективная плотность топливного сердечника для твэлов реакторов на быстрых нейтронах составляет 8,9 – 9,4 г/см3. Для сравнения, эффективная плотность таблетированного топлива аналогичного типа твэлов равна 8,5 – 8,6 г/см3. Неравномерность распределения эффективной плотности топливного сердечника и плутония вдоль оси не превышает 5 % номинального уровня. В реакторе БН-600 проводятся испытания ТВС с виброуплотненным уран – плутониевым оксидным топливом.
24.3.2.Структурно-фазовое состояние диоксидов
Диаграмма состояния системы уран–кислород. Система уран-кислород является одной из наиболее сложных. Она содержит, по крайней мере, 10 оксидных фаз, многие из которых имеют по несколько полиморфных модификаций. Хотя эта система иссле-
226
довалась во многих работах, все еще имеются расхождения в интерпретации отдельных частей ее диаграммы состояния.
Три оксида урана – диоксид UO2, закись-окись U3O8 и триоксид UO3 известны уже более ста лет. Исследования последних лет показали, что возможно существование монооксида UO, а также таких соединений урана с кислородом, как U4O9, U3O7, U2O5, и что эти соединения, как и три ранее известных оксида, не являются стехиометрическими, и в действительности существует разнообразие нестехиометрических форм. Было показано существование в системе U – O нескольких фаз UO, UO2, U4O9, U3O7, U3O8, -UO3,
-UO3.
При изучении системы уран – кислород обнаружено несколько гомогенных областей с переменным составом урана и кислорода. Одна из таких областей лежит, например, между составами UO2 – UO2,25. Существование стабильной фазы монооксида урана не доказано.
Монооксид урана. Низший оксид урана встречается только в виде тонких пленок на уране или включений в металл. Это хрупкое вещество серого цвета с металлическим блеском. По различным данным, его плотность составляет 13,6 – 14,2 г/см3. Монооксид имеет кубическую решетку типа NaCl. По мнению некоторых исследователей, при обычных условиях в свободном состоянии UO не существует. Основная трудность его получения связана с тем, что он устойчив только при высоких температурах.
Диоксид урана UO2 (точнее, UO2 х) – вещество темнокоричневого цвета с кристаллической структурой флюорита типа CaF2. Это нестехиометрическое соединение может иметь состав от
UO1,68 до UO2,28.
Оксиды U4O9 и U3O7 образуют самостоятельные фазы нестехиометрического состава. Для оксида U3O7 характерно наличие метастабильных тетрагональных фаз. Существует, по крайней мере, пять таких фаз, которые при температуре выше 600 С распадаются с образованием соответственно UO2 и U4O9 или U4O9 и UO2,6. При температуре выше 600 С в системе U – O в области от U4O9 до U3O8 исчезают все метастабильные тетрагональные оксиды, и в равновесии находятся фаза U4O9 и фаза с ромбической структурой закиси-окиси.
227
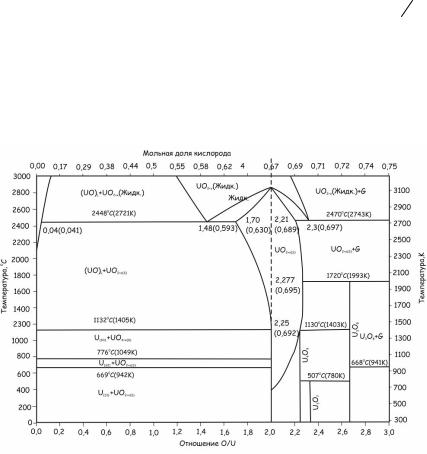
Закись-окись урана U3O8 – нестехиометрическое соединение, имеющее несколько модификаций в зависимости от условий приготовления. Цвет вещества – от зеленого до оливково-зеленого и черного. Закись-окись образуется при окислении на воздухе диоксида урана и при прокаливании на воздухе до красного каления (650 – 900 С) любого оксида урана, гидрата оксида или соли урана и летучего основания или кислоты.
Оксид U3O8 рассматривают иногда как UO2·2UO3 на основании того, что при растворении его в растворе присутствуют U4+ и 2UO22+. Однако доказано, что все атомы урана в U3O8 структурно эквивалентны и несут равный средний положительный заряд 513 .
Триоксид урана UO3 – один из промежуточных продуктов в производстве чистых солей урана, встречающихся также в некоторых окисленных урановых рудах. UO3 – оранжево-желтый порошок, существующий в одной аморфной и пяти кристаллических формах, плотностью 5,92 – 7,54 г/см3.
Фазовые равновесия в системе уран – кислород в области, прилегающей к диоксиду урана, показаны на рис. 24.129.
Рис. 24.129. Диаграмма состояния системы уран–кислород
228
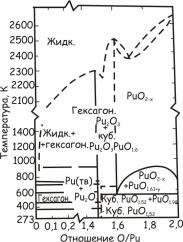
Диоксид урана плавится конгруэнтно при ~3150 К. Его область гомогенности изменяется в широких пределах в зависимости от температуры и отношения O/U. Достехиометрический диоксид урана UO2-х существует только при температурах выше 1500 К. Минимальная растворимость урана в UO2-х имеет место при монотектическом равновесии при 2740 ± 30 К и соответствует составу
1,68; растворимость х описывается выражением |
|
ln(x) = 3,678 – 12675/T. |
(24.12) |
Максимальная растворимость кислорода в UO2+х увеличивается с температурой, по крайней мере, до 1352 К, где она соответствует значению O/U = 2,28. Оксидная фаза U4O9 образуется по перитектоидной реакции при температуре 1396 ± 5 К, имеет ГЦК решетку и сравнительно узкую область гомогенности. Максимальная растворимость кислорода в этой фазе соответствует значению
O/U = 2,25.
Диаграмма состояния системы плутоний–кислород. В систе-
ме плутоний – кислород идентифицированы четыре оксидные фазы: гексагональный оксид Pu2O3 (β-Pu2O3), имеющий структуру полуторных оксидов; кубический полуторный оксид (α-Pu2O3), ста-
бильный |
при |
температурах |
ниже |
|
600 К; кубический оксид PuO1,61 и |
|
|||
диоксид плутония PuO2. Ориентиро- |
|
|||
вочная фазовая диаграмма системы |
|
|||
плутоний-кислород представлена на |
|
|||
рис. 24.130. |
|
|
|
|
Диоксид плутония имеет |
ГЦК |
|
||
структуру флюорита и для него воз- |
|
|||
можен значительный дефицит ки- |
|
|||
слорода, зависящий от температуры |
|
|||
и парциального давления кислорода. |
|
|||
Согласно последним данным, пред- |
|
|||
ставленным на рис. 24.131, где изо- |
|
|||
бражены два варианта участка диа- |
|
|||
граммы состояния системы плуто- |
|
|||
ний–кислород (1, 2, 3 – двухфазные |
Рис. 24.130. Диаграмма состояния |
|||
области |
для |
которых химические |
системы плутоний–кислород |
229
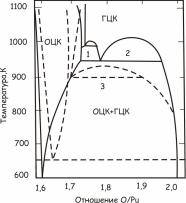
Рис. 24.131. Участок диаграммы состояния системы плутоний – кислород
потенциалы кислорода показаны на рис. 24.131), выше 1000 К фаза
PuO2-х имеет широкую область гомогенности, распространяющуюся
до состава PuO1,72. Вблизи него находится узкая двухфазная область,
состоящая из PuO2-х и фазы с решеткой OЦК, которая существует в об-
ласти составов от PuO1,70. до PuO1,61. Границы этой фазы выше 1000 К
точно не установлены. При температурах выше 650 К в равновесии с фазой PuO1,61. находится гексагональная фаза Pu2O3, область существования которой простирается до значения О/Pu = 1,5 при 1970 К.
Диаграмма состояния системы уран–плутоний–кислород.
Тройная диаграмма состояния системы U–Pu–O имеет чрезвычайно сложный характер, и она изучена лишь частично на наиболее практически важном участке, прилегающем к псевдобинарному разрезу UO2 – PuO2. На рис. 24.132 показаны участки этой диаграммы меж-
ду UO1,88 – U3O8 и PuO2 – PuO1,5 при всех концентрациях плутония в области температур от комнатной до 1073 К.
Диоксиды урана и плутония, обладающие изоморфными решетками, образуют непрерывные ряды твердых растворов. Введение диоксида плутония в диоксид урана расширяет области гомогенности последнего, включая достехиометрическую область, вследствие чего смешанные оксиды урана и плутония имеют как до-, так и застехиометрические составы, и их принято записывать в виде (U,Pu)O2±х. Восстановление смешанных диоксидов урана и плутония U1-yPuyO2±х с содержанием плутония y > 0,4 до достехиометрического состава приводит к образованию при комнатной темпера-
туре двух фаз MeO2,00 и MeO2-х. При нагреве эта двухфазная область сохраняется, в то время как границы однофазной области, где
существует фаза U1-yPuyO2±х, смещаются. Восстановление смешанных оксидов с у < 0,4 не сказывается на существовании однофазной области фазы U1-yPuyO2±х при всех температурах. Ее частичное
230