
Прикл мех
.pdf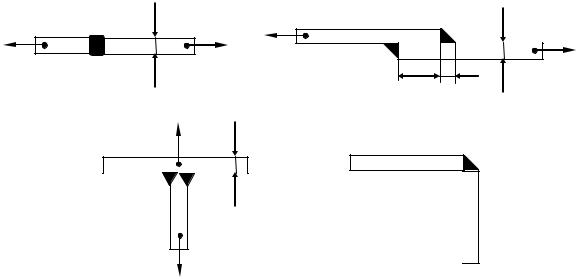
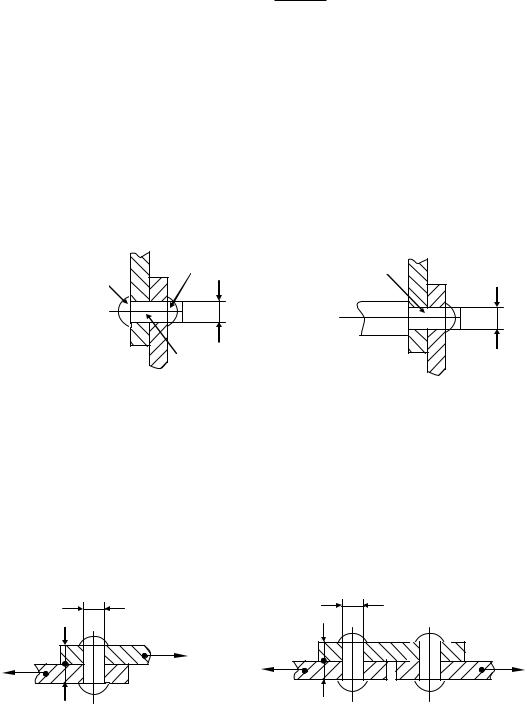

|
|
4P |
|
|
|
1 |
[ зр], |
|
i d 2 |
||
|
|
|
|
де |
Р1 – навантаженнѐ на одну заклепку; |
|
|
|
і - кількість площин зрізаннѐ. |
|
|
|
Умова міцності при розрахунках на зминаннѐ перевірѐютьсѐ за формулоя |
P
S 1d [ зм],
де S – товщина деталей, що з’юднуятьсѐ.
Величини допустимих напружень призначаятьсѐ залежно від матеріалу заклепок і способу обробки отворів під них. Наприклад, длѐ стальних заклепок (сталі марок 2, 3) при отворах, що отримуять свердленнѐм, приймаятьсѐ * ЗР]=140 МПа і * ЗМ] = 300 МПа.
Паяні з’єднання
При паѐнні деталі (з чавуну, сталі, кольорових металів та сплавів) з’юднуятьсѐ розплавленим припоюм. Такі з’юднаннѐ широко застосовуятьсѐ в електричних машинах, приладах, радіоапаратурі.
Перевагами паѐних з’юднань ю:
герметичність,
відносна простота і технологічність процесу,
малі остаточні деформації.
До недоліків слід віднести:
невисоку механічну та термічну міцність,
високу вартість припоїв і флясів.
Поширеними м’ѐкими припоѐми ю сплави олова та свинця - ПОС (зі змістом олова 18...90%; наприклад, припій ПОС-60 містить 60% олова і близько 40% свинця); олова, свинця та кадмія - ПОСК; олова, свинця та вісмуту – ПОСВ. Такі припої застосовуять длѐ паѐннѐ міді, сплавів, сталі.
Тверді припої застосовуятьсѐ длѐ паѐннѐ міді, сталей, нержавіячих сталей. До складу твердих припоїв можуть входити такі складові: срібло, мідь, кадмій (ПСр50Кд34); мідь і нікель (ПН25) та ін. Такі припої забезпечуять шви з відносно високими механічноя та термічноя міцністя.
Длѐ отриманнѐ ѐкісних паѐних з’юднань поверхні деталей очищуять від окисних плівок шлѐхом застосуваннѐ флясів - каніфолі, розчину спирту, а також хімічно активних флясів - бури, хлористого цинку та ін.
Клейові з’єднання
З’юднаннѐ конструкційних матеріалів склеяваннѐм широко використовуютьсѐ в різних галузѐх машинобудуваннѐ.
Основноя перевагою цього з’юднаннѐ ю:
щільність,
можливість склеяваннѐ різнорідних металічних і неметалічних матеріалів у різноманітних
сполученнѐх.
Недоліком ю
низька теплостійкість (600С длѐ більшості клеїв і 2500С длѐ теплостійких клеїв),
невисока міцність.
Вибір клея здійсняютьсѐ залежно від виду матеріалів, що склеяятьсѐ, і робочих температур. Так, клеї марок БФ-2 і БФ-4 (розчини синтетичних смол у спирті або ацетоні) застосовуятьсѐ длѐ склеяваннѐ металів і сплавів між собоя та неметалічними матеріалами. Епоксидні клеї ЭД-5, ЭД-6 використовуятьсѐ длѐ склеяваннѐ сталі, міді, алямінія та його сплавів, пластмас. В електрота приладобудуванні використовуятьсѐ епоксидний К-8 і феноло-вінілацетатний ВК-20 струмопровідні клеї.
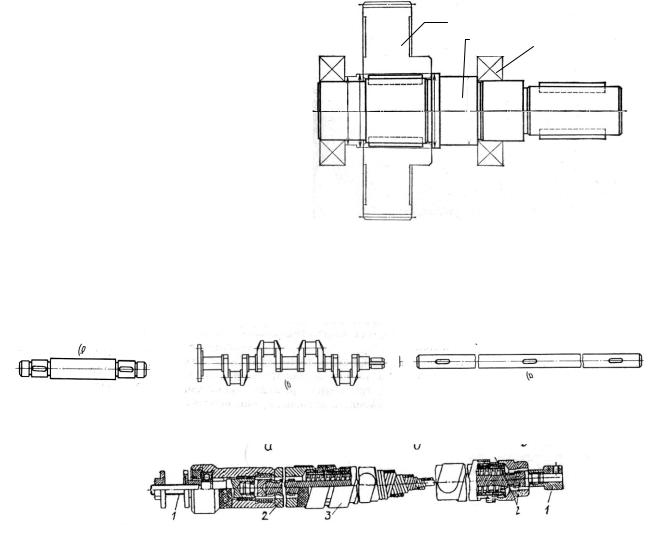

Задачами розрахунку валів та осей ю забезпеченнѐ усталісної міцності, обмеженнѐ деформації згину та крученнѐ, можливих поперечних та крутильних коливань. Розрахунок і конструяваннѐ валів – взаюмозв’ѐзані процеси, тому розрахунок валів складаютьсѐ з двох етапів:
проектного та перевірочного розрахунку.
При проектному розрахунку валів, ѐк правило, відомі навантаженнѐ, розміри основних деталей, розташованих на валові. Потрібно вибрати матеріал і визначити розміри вала.
Проектний розрахунок валів
Порѐдок проведеннѐ проектного розрахунку.
1 Попередньо оціняять середній діаметр вала з розрахунку тільки на крученнѐ при знижених допустимих напруженнѐх, (згинальний момент невідомий, тому що невідомо розташуваннѐ опор та місцѐ прикладеннѐ навантаженнѐ).
Визначаять напруженнѐ крученнѐ
|
T |
|
T |
, |
|
W |
0,2d 3 |
||||
|
|
|
|||
|
|
|
|
|
звідси
d 3 |
|
T |
|
|
|
. |
|||
0,2 |
Як правило, приймаять 20...30 МПа длѐ трансмісійних валів;
12...15 МПа длѐ редукторних валів.
Діаметр вхідного кінцѐ вала редуктора можна прийнѐти рівним або близьким до діаметра вихідного кінцѐ електродвигуна.
2Розроблѐять конструкція вала (компонуваннѐ).
3Виконуять перевірочний розрахунок вала.
Перевірочний розрахунок валів
Порѐдок проведеннѐ перевірочного розрахунку валів.
1 Вибираять розрахункову схему і визначаять розрахункові навантаженнѐ.
2Знаходѐть небезпечні перерізи, обумовлені найбільшим згинальним моментом, ослаблені концентраторами напружень: галтель, виточка, шпонковий паз, різьбленнѐ тощо.
3Проводѐть розрахунок на статичну міцність. Наприклад, при використанні енергетичної теорії міцності еквівалентні напруженнѐ визначаятьсѐ за формулоя
э max2 3 k2 max ,
де допустимі напруженнѐ :
max 0,6 0,8 T ,
Т |
– границѐ плинності, |
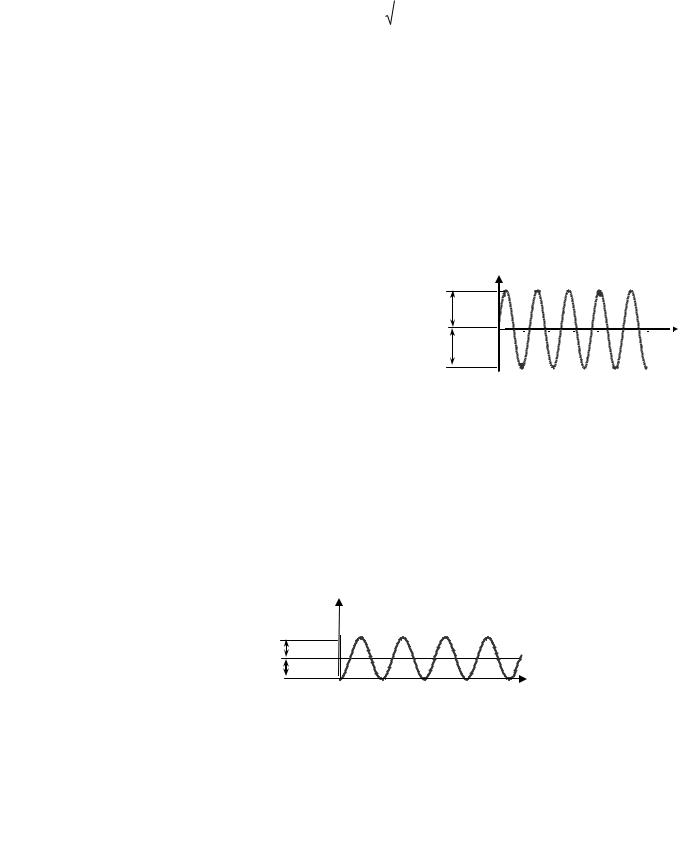

K – коефіціюнт концентрації напружень при згині, що залежить від концентратора напружень
K – коефіціюнт концентрації напружень при крутінні, що залежить від концентратора напружень
Kd – масштабний фактор
KF – фактор шорсткості поверхні
Концентраторами напружень ю галтелі, фаски, виточки, проточки, шпонкові пази, шліці, пресові посадки, різьба тощо.
5 Перевірѐять жорсткості вала за умовами жорсткості
при згині
y y ,
де у – прогин вала;
y – прогин, що допускаютьсѐ (рекомендації в роботі 3 ),
та при крученні
|
|
T l |
, |
|
G I |
||
|
|
|
|
де |
G – модуль пружності другого роду; |
|
|
|
І – полѐрний момент інерції; |
|
|
|
– кут закрученнѐ вала; |
|
|
– допустимий кут закрученнѐ вала, значеннѐ ѐкого залежить від вимог, що пред’ѐвлѐятьсѐ до механізму.
6 Проводѐть розрахунок на коливаннѐ з умови попередженнѐ обертаннѐ в критичній зоні
nкр |
30 |
|
|
g |
|
, |
|
|
|||||
|
|
|
yст |
де g – прискореннѐ вільного паданнѐ; yст – статичний прогин.
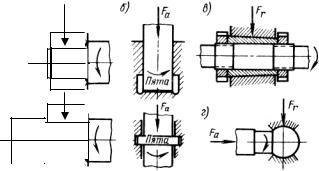
знизилосѐ. Їх застосовуять дуже широко, і в цілому рѐді конструкцій вони незамінні. До таких підшипників належать:
1)роз’юмні підшипники, необхідні за умовами зборки, наприклад длѐ колінчастих валів;
2)високошвидкісні підшипники (V > 30 м/с), в умовах роботи ѐких довговічність підшипників коченнѐ різко скорочуютьсѐ (вібрації, шум, великі інерційні навантаженнѐ на тіла коченнѐ);
3)підшипники прецизійних машин, від ѐких потрібний особливо точний напрѐмок валів і можливість регуляваннѐ зазорів;
4)підшипники, що працяять в особливих умовах (вода, агресивне середовище і т.п.), у ѐких підшипники коченнѐ непрацездатні через корозія;
5)підшипники дешевих тихохідних механізмів і деѐкі інші.
Умови роботи і види руйнування підшипників ковзання
Обертання цапфи в підшипнику протидію момент сил тертѐ. Робота тертѐ нагріваю підшипник і цапфу. Від поверхні тертѐ теплота виділѐютьсѐ через корпус підшипника і вал, а також несетьсѐ рідиноя, що змазую. З підвищеннѐм температури знижуютьсѐ в'ѐзкість мастила і збільшуютьсѐ імовірність заїданнѐ цапфи в підшипнику. У кінцевому результаті заїданнѐ призводить до виплавленнѐ вкладиша. Перегрів підшипника ю основноя причиноя його руйнуваннѐ.
Робота підшипника супроводжуютьсѐ зносом вкладиша і цапфи, що порушую правильну роботу механізму і самого підшипника. Інтенсивність зносу, зв'ѐзана також з роботоя тертѐ, визначаю довговічність підшипника.
При дії змінних навантажень (наприклад, у поршневих двигунах) поверхнѐ вкладиша може викришуватись внаслідок втоми. Викришуваннѐ від втоми властиве підшипникам з малим зносом і спостерігаютьсѐ порівнѐно рідко.
У випадку дії великих короткочасних перевантажень ударного характеру вкладиші підшипників можуть крихко руйнуватисѐ. Крихкому руйнування піддаятьсѐ маломіцні антифрикційні матеріали, такі ѐк бабіти і деѐкі пластмаси.
Робота тертѐ ю основним показником працездатності підшипника. Тертѐ визначаю знос і нагрів підшипника, а також його ККД. Длѐ зменшеннѐ тертѐ підшипники ковзаннѐ змазуять. У залежності від режиму роботи підшипника в ньому може бути напіврідинне або рідинне тертѐ.
При напіврідинному терті умова не дотримуютьсѐ, у підшипнику буде змішане тертѐ — одночасно рідинне і граничне. Граничним називаять тертѐ, при ѐкому поверхні покриті найтоншоя плівкоя змащеннѐ, що утвориласѐ в результаті дії молекулѐрних сил і хімічних реакцій активних молекул змащеннѐ і матеріалу вкладиша. Спроможність змащеннѐ до утвореннѐ граничних плівок (адсорбції) називаять маслянистістю. Граничні плівки стійкі і витримуять великі тиски. Однак у місцѐх зосередженого тиску вони руйнуятьсѐ, відбуваютьсѐ стиканнѐ чистих поверхонь металів, їхню схопляваннѐ і відрив часток матеріалу при відносному русі. Напіврідинне тертѐ супроводжуютьсѐ зносом тертьових поверхонь навіть без влученнѐ зовнішніх абразивних часток. Значеннѐ коефіціюнта напіврідинного тертѐ залежить не тільки від ѐкості мастила, але також і від матеріалу тертьових поверхонь. Длѐ розповсяджених антифрикційних матеріалів коефіціюнт напіврідинного тертѐ дорівняю 0,008. ..0,1.
Длѐ роботи підшипника найсприѐтливішим режимом ю режим рідинного тертѐ. Утвореннѐ режиму рідинного тертѐ ю основним критеріюм розрахунку більшості підшипників ковзаннѐ. При цьому одночасно забезпечуютьсѐ працездатність за критеріѐми зносу і заїданнѐ.
Підшипники кочення
Застосуваннѐ підшипників коченнѐ дозволѐю замінити тертѐ ковзаннѐ на тертѐ коченнѐ, ѐке менш суттюво залежить від змащуваннѐ (умовний коефіціюнт тертѐ близький до коефіціюнта рідинного тертѐ f 0,0015...0,006). При цьому спрощуютьсѐ система змащуваннѐ та обслуговуваннѐ підшипника.
Підшипники коченнѐ складаятьсѐ з внутрішнього та зовнішнього 2 кілець з доріжками коченнѐ, тіл коченнѐ 3 (шариків чи роликів), сепараторів 4, ѐкі розділѐять та направлѐять тіла коченнѐ.
До недоліків підшипників коченнѐ належать: відсутність роз’юмних конструкцій, порівнѐно великі радіальні габарити, обмежена швидкохідність, низка працездатність при вібраційних та ударних вантаженнѐх та в агресивних середовищах.
За формоя тіл коченнѐ підшипники поділѐятьсѐ на шарикові та роликові.
За напрѐмком навантаженнѐ, ѐке сприймаютьсѐ – радіальні, упорні, радіально-упорні, упорнорадіальні.
Основні причини втрати працездатності підшипників кочення:
викришування від втоми, ѐке спостерігаютьсѐ в підшипниках післѐ тривалого часу їхньої роботи в нормальних умовах;
знос, що спостерігаютьсѐ при недостатньому захисті від абразивних часток (пилу і бруду);
руйнування сепараторів, ѐке даю значний відсоток виходу з ладу підшипників коченнѐ, особливо швидкохідних;
розколювання кілець і тіл кочення, ѐке зв'ѐзано з ударними і вібраційними перевантаженнѐми, неправильним монтажем, що викликаю перекоси кілець, заклиняваннѐ тощо;
залишкові деформації на бігових доріжках і виглѐді лунок та вм'ѐтин, ѐкі спостерігаятьсѐ у важконавантажених тихохідних підшипників.
Розрахунок підшипників кочення
Розрахунок підшипників коченнѐ базуютьсѐ на двох критеріѐх:
1Розрахунок на ресурс (довготривалість) з викришуваннѐ від втоми.
2Розрахунок на статичну вантажопідйомність за остаточними деформаціѐми.
При проектуванні підшипники підбираять з числа стандартних. Розрізнѐять підбір підшипників за динамічноя вантажопідйомністя длѐ запобіганнѐ руйнуваннѐ від втоми (викришуваннѐ) (при n ≥ 10 мин–1) та за статичноя вантажопідйомністя длѐ запобіганнѐ остаточним деформаціѐм.
Умова підбора за динамічноя вантажопідйомністя
С потріб ≤ С паспорт.