
Прикл мех
.pdfОсновними термічними операціѐми ю відпал, нормалізація (Н), загартування (З) і відпускання (В).
Відпал (нагріваннѐ і поступове охолодженнѐ) поковок і відливків використовуять длѐ одержаннѐ необхідних механічних властивостей.
При нормалізації зменшуятьсѐ внутрішні напруги; її використовуять длѐ вуглецевої сталі з метоя підготовки структури матеріалу перед механічноя обробкоя
Загартування готових деталей дозволѐю зберегти нестійку структуру при кімнатній температурі, що відзначаютьсѐ підвищеноя міцністя і твердістя
Післѐ загартуваннѐ здійсняять відпускання – нагріваннѐ й охолодженнѐ за певного режиму.
Поверхневе загартування – нагріваннѐ поверхневого шару до температури загартуваннѐ, а потім швидке охолодженнѐ – призводить до підвищеннѐ твердості поверхні, границі витривалості та опору зношування при збереженні в’ѐзкої серцевини.
Таким способом оброблѐять шийки колінчастих валів, розподільні вали, різні втулки, деталі зубчастих з’юднань, зубці великих зубчастих коліс та ін.
За допомогоя хіміко-термічної обробки – цементації, азотування, ціанування – досѐгаютьсѐ зміцненнѐ поверхневих шарів.
Під час цементації деталей із низьковуглецевих сталей поверхневий шар на глибину 1…2 мм насичуять вуглецем
Під час азотування поверхневий шар глибиноя 0,3…0,6 мм насичуютьсѐ
Під час ціанування поверхнѐ насичуютьсѐ одночасно вуглецем і азотом.
З метоя підвищеннѐ стійкості проти зношуваннѐ та корозії застосовуять дифузну металізація. При цьому підвищуятьсѐ твердість від 1200…1500 HV (хромуваннѐ) до 1600…2000 HV (титануваннѐ) і термостійкість.
Дифузна металізація – насиченнѐ поверхні частіше за все хромом, титаном, бором та ін.
Поліпшити опірність деталей руйнування можна створеннѐм на їх поверхні напружень стиску. Цього домагаятьсѐ за допомогоя механічного зміцнення активних поверхонь – наклепу, ѐкий здійсняютьсѐ шлѐхом:
–дробоструминної обробки, ѐка полѐгаю в пластичній деформації поверхневого шару деталі на глибину 0,15…0,30 мм за допомогоя сталевого або чавунного дробу, що із силоя ударѐю по поверхні;
–обкатки роликами під тиском длѐ деталей, ѐкі маять циліндричну поверхня,(осі транспортного рухомого складу, колінчасті вали).
Внаслідок наклепу підвищуютьсѐ твердість поверхні, міцність при втомленості (границѐ витривалості пружин підвищуютьсѐ на 50%, зубців зубчастих коліс зі сталі 40Х – на 20%).
З метоя підвищеннѐ міцності зі збереженнѐм пластичності застосовуять термомеханічну обробку: перед загартуваннѐм проводѐть пластичну деформація, внаслідок чого отримуять дрібнозернисту структуру, зростаю міцність.
Чавуни – це залізо-вуглецеві сплави, в ѐких змістовність вуглеця перевищую 2%.
Узалежності від структури чавуни п оділѐятьсѐ на:
–білий чавун характеризуютьсѐ високоя твердістя та крихкістя (використовуютьсѐ длѐ виготовленнѐ гальмових колодок транспортних технічних засобів);
–ковкий чавун (КЧ) характеризуютьсѐ високоя міцністя ( до 630 МПа) та низькоя пластичністя (використовуютьсѐ длѐ деталей-відливок, що не обробляятьсѐ тиском);.
–сірий чавун (СЧ) при гарних ливарних властивостѐх він характеризуютьсѐ відносно високоя
міцністя ( до 400МПа), зносостійкістя та демпфуячоя здатністя (віброгашеннѐм); добре обробляютьсѐ різаннѐм (у порівнѐнні з КЧ вартість виготовленнѐ деталей з СЧ знижуютьсѐ в 1,3
...2,0 рази); маю найбільше розповсядженнѐ в ѐкості ливарного конструкційного матеріалу.
До кольорових металів належать мідь, цинк, свинець, олово, аляміній (використовуять частіше в ѐкості сплавів – бронза, латунь, боббит, алямініюві сплави)
Переваги кольорових металів:
–антифрикційність,
–антикорозійність,
–легкість,
–висока технологічність (добре оброблѐятьсѐ).
Недоліки кольорових металів:
– висока вартість
Серед сплавів на основі міді найбільшого використаннѐ длѐ виготовленнѐ втулок, кріпильних деталей, сепараторів підшипників коченнѐ, корпусів та ін. отримали латуні та бронзи. Вони характеризуятьсѐ високими антифрикційними, ливарними й антикорозійними властивостѐми.
Латунь – сплав на основі Cu та Zn (до 50%), часто з додаваннѐм Al, Sn, Fe, Mn, Ni, Si, Pb та інших елементів (до 10%).
Длѐ виготовленнѐ різноманітної арматури та деталей, що в парі з іншими повинні мати низький коефіціюнт тертѐ, використовуять бронзи.
Бронза – сплав на основі Cu з іншими елементами (наприклад, Al, Вe, Cr, Cd, Pb).
Найкращі умови приробки й антифрикційні характеристики забезпечуятьсѐ при використанні у вкладишах підшипників ковзаннѐ бабітів.
Бабіт – легкоплавкий сплав на основі олова або свинця.
В ѐкості ливарного матеріалу длѐ виготовленнѐ деталей складної конфігурації, а також різноманітних корпусів, кожухів, основин, шасі, юмностей, трубопроводів та ін., ѐкі маять достатня міцність, а питому вагу більш ѐк у 3 рази меншу у порівнѐнні зі сталля (важливо длѐ транспортних технічних засобів), використовуятьсѐ сплави на основі алюмінію:
Длѐ виготовленнѐ відповідальних деталей з високоя міцністя, жароміцністя, корозійноя стійкістя, але з невисокими антифрикційними властивостѐми, низькоя теплопровідністя та модулем повздовжньої пружності використовуять титанові сплави.. За питомоя вагоя вони в 1,7 рази легкіше
у порівнѐнні зі сталля, а за міцністя займаять вищий рівень міцності легованих сталей (маять = 800 ... 1500 МПа). Застосовуятьсѐ головним чином в авіації, ракетній техніці (длѐ виготовленнѐ роторів, лопаток газотурбінних двигунів, кріпильних деталей) та хімічному машинобудуванні.
Все більшого використаннѐ длѐ виготовленнѐ деталей отримуять неметалічні матеріали.
До неметалічних матеріалів відносѐть дерево, гуму, шкіру, азбест, металокераміку.:
Переваги:
–легкість,
–пружність,
–герметичність,
–ізолѐційні властивості тощо.
Недоліки:
–низькі механічні властивості.
–пластмаси за міцнісними характеристиками можуть наближатисѐ до деѐких металів, а за корозійноя стійкістя – перевершувати їх.
Переваги пластмас:
–легкість,
–міцність,
–пружність,
–тепло – шумо –електроізолѐційні властивості,
–антифрикційність,
–антикорозійність,
–висока технологічність.
Недоліки:
–низька термічна міцність.
–гума характеризуютьсѐ високоя еластичністя, стійкістя проти впливу зовнішнього середовища, амортизаційними властивостѐми. Під діюя змінних навантажень внаслідок внутрішнього тертѐ гума нагріваютьсѐ, відбуваятьсѐ необоротні процеси, погіршуютьсѐ еластичність. Гума використовуютьсѐ длѐ пасів, упорів, підвісок, мембран, трубопроводів, захисних покриттів.

Взаємозамінність, стандартизація та сертифікація
Взаємозамінність – це принцип конструяваннѐ та виготовленнѐ деталей, що забезпечую можливість складаннѐ чи заміни при ремонтах незалежно виготовлених з заданоя точністя деталей та складальних одиниць без додаткової обробки і припасуваннѐ їх зі збереженнѐм відповідної ѐкості
Взаюмозамінність може бути:
–повна (передбачаю з’юднаннѐ без додаткової обробки всіх спрѐжених деталей, що надходѐть на складальні операції);
–неповна ( передбачаю з’юднаннѐ без додаткової обробки тільки частини деталей, виготовлених з меншоя точністя).
Деталі і складальні одиниці будуть взаюмозамінними тільки тоді, коли їх розміри, форма та інші параметри знаходѐтьсѐ у визначених межах. Це здійсняютьсѐ за рахунок стандартизації норм взаюмозамінності, забезпеченнѐ відповідних параметрів деталей, виконаннѐ технічних умов на їх виготовленнѐ.
Параметри деталей кількісно оціняять за допомогоя розмірів.
Розмір – це числове значеннѐ лінійної величини (діаметр, довжина, висота та ін.) в обраних одиницѐх виміряваннѐ. Розміри поділѐятьсѐ на номінальні, дійсні і граничні.
Номінальний розмір – розмір, відносно ѐкого визначаятьсѐ граничні розміри і ѐкий використовуютьсѐ длѐ відліку відхилень
Номінальні розміри вибираять під час конструяваннѐ на основі розрахунків або за конструктивними міркуваннѐми і проставлѐять при кресленні деталі або з’юднанні деталей. Номінальні розміри післѐ розрахунків округлѐять до найближчого з рѐдів нормальних лінійних розмірів згідно з ГОСТ 6636-69.
Дійсний розмір – це розмір, встановлений виміряваннѐм з допустимоя похибкоя
Граничні розміри – це два допустимих розміри (найбільший і найменший), між ѐкими повинен знаходитись дійсний розмір.
На кресленні деталі або з’юднанні проставлѐять номінальні розміри, а кожний з двох граничних розмірів визначаять по його відхиленнѐх від номінального.
Розрізнѐять верхню і нижню граничні відхиленнѐ.
– длѐ отвору; |
– длѐ валу. |
Отвір – охопляячий розмір
Вал – розмір, ѐкий охопляютьсѐ
Граничні відхиленнѐ визначаятьсѐ ѐк алгебраїчна різницѐ між граничними і номінальними розмірам з формул:
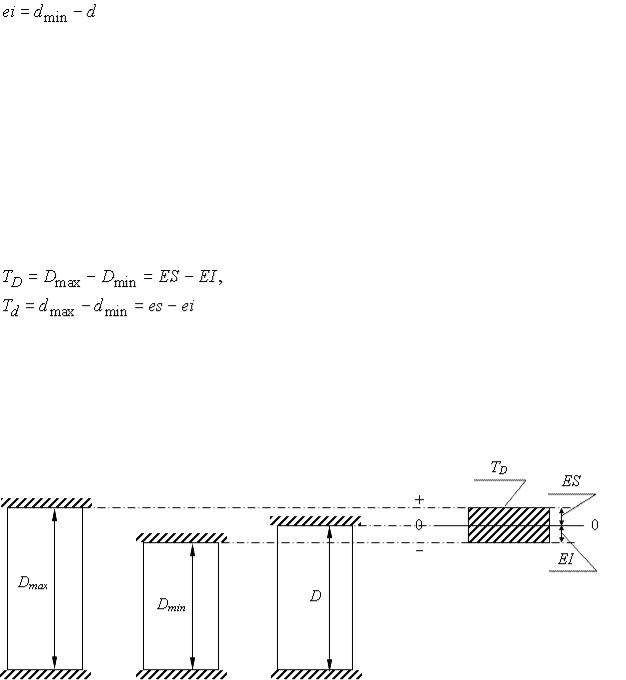
,
,
,
,
де D, d – номінальний розмір отвору і вала;
Dmax, dmax – айбільший граничний розмір отвору і вала;
Dmin, dmin – найменший граничний розмір отвору і вала.
Назва “отвір” і “вал” умовна і стосуютьсѐ не тільки гладких циліндричних елементів деталей. Наприклад, у з’юднанні шпонки з валом шпонка ю валом, а паз вала – отвором.
Різницѐ між найбільшим і найменшим граничними розмірами або абсолятна величина алгебраїчної різниці між верхнім і нижнім відхиленнѐми називаютьсѐ допуском розміру Т.
Поле, обмежене верхнім і нижнім відхиленнѐми, називаютьсѐ полем допуску
Воно визначаютьсѐ величиноя допуску і його розташуваннѐм відносно номінального розміру (нульової лінії). Нульова лініѐ при графічному зображенні полів допусків відповідаю номінальному
розміру. Вище нульової лінії розташовуятьсѐ додатні відхиленнѐ, нижче – від’юмні.
Призначеннѐ допусків на розміри деталей регламентуятьсѐ “Єдиноя системоя допусків і посадок” (ЄСДП). ЄСДП – це сукупність закономірно побудованих рѐдів допусків і посадок, оформлених у виглѐді стандартів, ѐка призначена длѐ вибору мінімально необхідних, але достатніх длѐ практики варіантів допусків і посадок
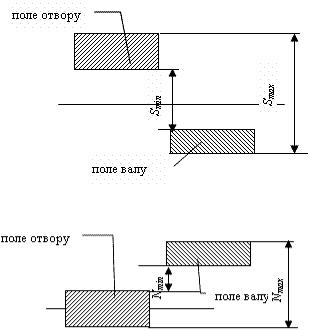
У залежності від числа a у допуску TD стандартами длѐ розмірів до 500 мм встановлено 19 квалітетів (ступенів точності):
–IT01, IT0, IT1, IT2 – длѐ кінцевих мір;
–IT2 ...IT5 – длѐ калібрів
–IT5 ... IT11 – длѐ сполучених розмірів деталей машин;
–IT12 ...IT17– длѐ вільних (несполучених) розмірів.
Посадка – це характер з’юднаннѐ деталей, ѐка визначаютьсѐ величиноя отриманих в ній зазорів чи натѐгів, і ѐка характеризую свободу переміщеннѐ з’юднаних деталей чи опір їх взаюмному переміщення.
Характер посадки залежить від співвідношеннѐ полів допусків валу й отвору і визначаютьсѐ величиноя зазорів або натѐгів, ѐкі при цьому виникаять.
Зазор – це різницѐ між розмірами отвору і валу, ѐкщо отвір більший за вал.
Натяг – це різницѐ між розмірами отвору і валу, ѐкщо вал більший за отвір.
В залежності від взаюмного розташуваннѐ полів допуску отвору та валу розрізнѐять посадки з зазором, натѐгом та перехідні.
Длѐ утвореннѐ допусків і посадок в ЄСДП передбачаютьсѐ 26 найменувань основних відхилень:
А – H (a – h) – зазор;
Js– N (js– n) – перехідна;
P –Z (p – z) – натѐг.
Посадка з зазором – це посадка, в ѐкій забезпечуютьсѐ зазор у з’юднанні тобто поле допуску отвору розміщено над полем допуску вала.
Вони призначені длѐ рухомих та нерухомих з’юднань. В рухомих зазор служить длѐ забезпеченнѐ свободи руху, розміщеннѐ шару мастила, компенсуваннѐ температурних деформацій, а також компенсування відхилень форми і розташуваннѐ поверхонь, похибок складаннѐ тощо. В нерухомих з’юднаннѐх посадки з зазором застосовуятьсѐ длѐ забезпеченнѐ безперешкодного складаннѐ деталей.
Посадка з натягом – це посадка, при ѐкій забезпечуютьсѐ натѐг з’юднаннѐ, тобто поле допуску отвору розташоване під полем допуску вала.Вони використовуятьсѐ длѐ нерухомих нероз’юмних з’юднань (чи роз’юмних лише в окремих випадках при ремонті) без додаткового кріпленнѐ гвинтами, штифтами. шпонками тощо:
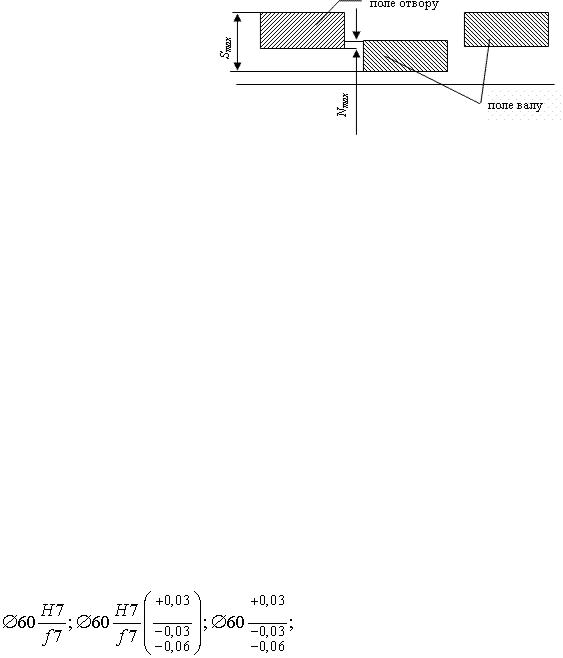
Перехідна посадка – це посадка, при ѐкій можна отримати ѐк зазор, так і натѐг, тобто полѐ допусків отвору та валу перекриваятьсѐ частково чи повністя
Вони призначені длѐ нерухомих, |
але |
роз’юмних з’юднань та забезпечуять |
|
добре центруваннѐ з’юднуваних деталей, |
длѐ |
них характерно отриманнѐ ѐк невеликих |
|
зазорів, так і невеликих натѐгів. Їх |
|
застосовуять з додатковим кріпленнѐм |
|
шпонками, штифтами, гвинтами тощо, |
|
застосовуять і відносно точних квалітетах (вали 4...7, отвори 5...8): |
|
В ЄСДП існую: |
|
Система отвору – посадки, в ѐких зазори і натѐги отримуятьсѐ з’юднаннѐм різних валів з основним отвором;
Основний отвір – це отвір, нижню відхиленнѐ ѐкого дорівняю 0.
Система валу – посадки, в ѐких зазори і натѐги отримуятьсѐ з’юднаннѐм різних отворів з основним валом.
Основний вал – це вал, верхню відхиленнѐ ѐкого дорівняю 0
Системі отвору віддаять перевагу ѐк більш економічній – це обумовляютьсѐ меншоя кількістя типів розмірів необхідного інструменту. У рѐді випадків більш економічноя буваю система валу( сполученнѐ поршнів палець-шатун).
При використанні деталей, що виготовлѐятьсѐ на спеціалізованих підприюмствах (підшипники, шпонки тощо) посадку треба визначати у системі, в ѐкій вони виготовлені.
На складальних кресленнѐх в місцѐх з’юднань посадка показуютьсѐ порѐд з номінальним розміром:
Технічні вимоги до виготовлення деталей машин
Основоя нормуваннѐ та кількісного відхиленнѐ форми й розташуваннѐ поверхонь ю принцип прилѐгаячих прѐмих, поверхонь і профілів.
Прилягаюча площина або пряма – це площина або прѐма, ѐкі доторкуятьсѐ до реальної поверхні й розташовуятьсѐ поза матеріалом деталі.
Прилягаючі окружності або циліндр – це коло мінімального діаметра, ѐке описане навколо реального профіля зовнішньої поверхні обертаннѐ або максимального діаметра, що вписане в реальний профіль внутрішньої поверхні обертаннѐ
Длѐ виміру відхилень форми прилѐгаячими поверхнѐми використаятьсѐ поверхні контрольних плит, перевірочних лінійок, калібрів.
Відхилення форми – це відхиленнѐ форми номінальної поверхні, що обмежую тіло й відокремляю його від навколишнього середовища, від форми номінальної поверхні.
Номінальна поверхня – це ідеальна поверхнѐ, що задаютьсѐ на кресленні або технічних
умовах
Допуск форми – це найбільше значеннѐ відхиленнѐ форми, т. е найбільша відстань від точок реальної поверхні до прилѐгаячої поверхні по нормалі.
Відхиленнѐ форми:
комплексні:
–циліндричності;
–круглості;
–профіля поздовжнього перетину;
–площини;
–прѐмолінійності.
часткові:
–овальність й ограняваннѐ,
–конусність, бочкоподібність, седлоподібність, згинність
Відхилення розташування поверхні – це відхиленнѐ дійсного розташуваннѐ елемента поверхні, що розглѐдаютьсѐ, осі або площини симетрії від номінального розташуваннѐ.
Длѐ оцінки точності розташуваннѐ поверхні призначаять базу.
База – це поверхнѐ, її утворяяча або точка, що визначаю прив'ѐзку деталей до площини або осі, щодо ѐкої задаятьсѐ допуски розташуваннѐ.
Якщо базоя ю поверхнѐ обертаннѐ або різьба, ѐк база приймаютьсѐ вісь.
Допуск розташування – це границѐ, що обмежую допустиме значеннѐ відхилень розташуваннѐ поверхонь
Числові значеннѐ відхилень форми і розташуваннѐ поверхонь вибираять по ГОСТ 24643-81. Встановлено 16 ступенів точності форми і розташуваннѐ поверхонь. В залежності від співвідношеннѐ між допуском розміру і допусками форми або розташуваннѐ встановлені вимоги відносної точності:
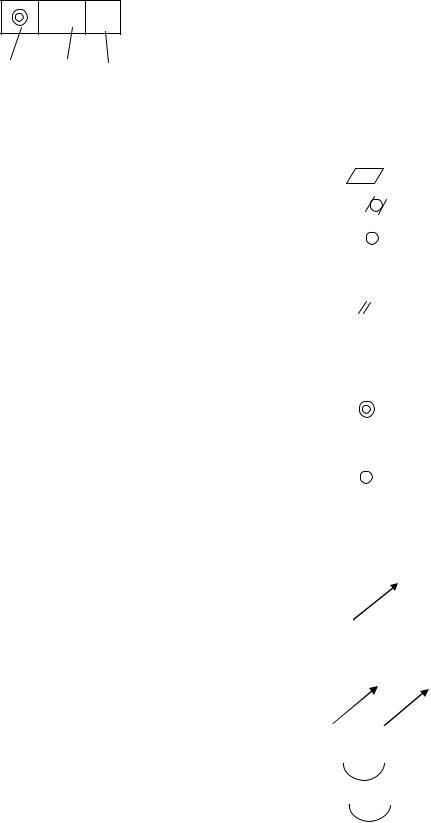
АБ
знак допуска число |
база |
|
|
|
|
|
|
|
|
|
|
|
|
|
|
Група допуску |
Види допуску |
Умовне позначеннѐ |
|||||||||||||
|
прѐмолінійності |
– |
|||||||||||||
|
площини |
|
|
|
|
|
|
|
|
|
|
|
|
|
|
Допуск форми |
круглості |
|
|
|
|
|
|
|
|
|
|
|
|
|
|
|
циліндричності |
|
|
|
|
|
|
|
|
|
|
|
|
|
|
|
поздовжнього перетину |
|
|
|
|
|
|
|
|
|
|
|
|
|
|
|
паралельності |
|
|
|
|
|
|
|
|
|
|
|
|
|
|
|
|
|
|
|
|
|
|
|
|
|
|
|
|
||
|
перпендикулѐрності |
|
|
|
|
|
|
|
|
|
|
|
|
|
|
|
|
|
|
|
|
|
|
|
|
|
|
|
|
||
|
нахилу |
|
|||||||||||||
Допуск розташуваннѐ |
співвісності |
|
|
|
|
|
|
|
|
|
|
|
|
|
|
|
симетричності |
|
|
|
|
|
|
|
|
|
|
|
|
|
|
|
|
|
|
|
|
|
|
|
|
|
|
|
|
||
|
|
|
|
|
|
|
|
|
|
|
|
|
|
||
|
позиційності |
|
|
|
|
|
|
|
|
|
|
|
|
|
|
|
|
|
|
|
|
|
|
|
|
|
|
|
|
||
|
|
|
|
|
|
|
|
|
|
|
|
|
|
||
|
перетинаннѐ осей |
|
|||||||||||||
|
радіальне биттѐ |
|
|
|
|
|
|
|
|
|
|
|
|
|
|
|
|
торцеве биттѐ |
|
|
|
|
|
|
|
|
|
|
|
|
|
|
|
биттѐ в заданому |
|
|
|
|
|
|
|
|
|
|
|
|
|
|
|
напрѐмку |
|
|
|
|
|
|
|
|
|
|
|
|
|
Сумарні допуски форм |
|
повне радіальне |
|
|
|
|
|
|
|
|
|
|
|
|
|
або розташуваннѐ |
|
биттѐ |
|
|
|
|
|
|
|
|
|
|
|
|
|
|
|
|
|
|
|
|
|
|
|
|
|
|
|
|
|
|
|
повне торцеве биттѐ |
|
|
|
|
|
|
|
|
|
|
|
|
|
|
|
|
|
|
|
|
|
|
|
|
|
|
|
||
|
форми заданого профіля |
|
|
|
|
|
|
|
|
|
|
|
|
|
|
|
форми заданої поверхні |
|
|
|
|
|
|
|
|
|
|
|
|
|
Примітка
обмежую абсолятну величину відхиленнѐ
обмежую відхиленнѐ в радіусному вираженні
обмежую граничне відхиленнѐ від бази
обмежую відхиленнѐ діаметра ( Т) або в радіус (R )
обмежую сумарне відхиленнѐ, що показую індикатор при вимірах
обмежую сумарне відхиленнѐ форми або поверхні
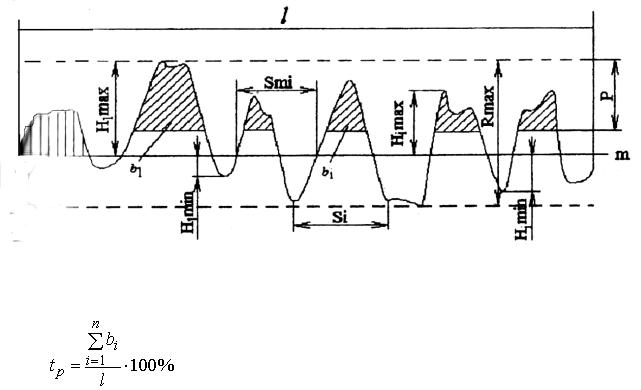
А – нормальна відносна геометрична точність (допуск форми або розташуваннѐ поверхонь складаю 60% від допуску розміру);
В – підвищена (білѐ 40%); С – висока (білѐ 25%).
Длѐ циліндричності, круглості, профіля повздовжнього перерізу геометрична точність длѐ рівнів А, В, С складаю 30,20 12% від допустимого розміру.
Длѐ циліндричності, круглості профіля поздовжнього перетину: нормальна – 30% від відхиленнѐ допуску розміру, підвищена – 20%, висока – 12%.
Шорсткість поверхні – це сукупність нерівностей поверхні з відносно малими кроками в межах базової довжини
Базова довжина – довжина базової лінії, що використаютьсѐ длѐ виділеннѐ нерівностей, що характеризуять шорсткість поверхні
Шорсткість поверхні незалежно від матеріалу і способу виготовленнѐ можна оцінити одним чи декількома параметрами:
Ra – середню арифметичне відхиленнѐ (основний, найбільш інформативний, призначаять на всі сполучені й чисто оброблені незв'ѐзані поверхні деталей);
Rz – висота нерівностей профіля по 10 крапкам (5 виступів й 5 западин);
Rmax – найбільша висота нерівностей; Smin – середній крок нерівностей;
S – середній крок місцевих виступів;
tp – відносна опорна довжина профіля.
.
Найбільш повну інформація надаю параметр Ra (він ю основним із висотних параметрів шорсткості і його призначаять на всі сполучені і чисто оброблені несполучені поверхні деталей).
Відносна опорна довжина профіля tp характеризую фактичну опорну площу, від ѐкої в значній міри залежать зносостійкість рухомих з’юднань і міцність пресових посадок .
Чисті поверхні з малоя шорсткістя підвищуять міцність та корозійну стійкість деталей, зменшуять тертѐ спрацяваннѐ в сполучених рухомих деталѐх. Однак при цьому зростаю вартість обробки поверхонь. Тому вибір параметрів шорсткості повинен бути економічно обґрунтованим.
Безпосереднього зв’ѐзку між квалітетами точності розмірів і параметрами шорсткості не існую, але не допускаютьсѐ висока точність зі значноя шорсткістя поверхонь, оскільки висота нерівностей повинна бути співрозмірноя з допуском на розмір. Поверхні деталей, ѐкі призначені длѐ з’юднань по стандартним посадкам, повинні мати параметр шорсткості Ra 0,2...3,2 мкм.