
Прикл мех
.pdf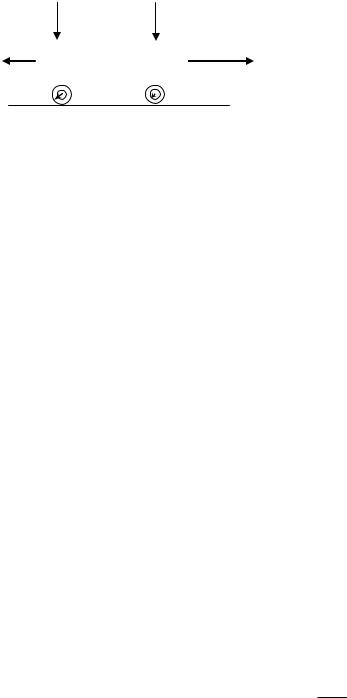
Переміщення вантажу за допомогою буксира
fo
Fko
– коефіціюнььертѐ ковзаннѐ між колесом і рейкоя (коефіціюнь зачепленнѐ)
Q2 |
Q1 |
Fk |
– сила корисного опору |
||
Q1 |
–долѐ ваги буксира, що передаютьсѐ через ведену |
||||
|
|
|
|||
|
|
V |
ось |
|
|
|
|
|
|||
|
|
|
Q2 |
– долѐ ваги буксира, що передаютьсѐ через ведучу |
|
|
|
|
ось. |
|
R |
r |
При зрушенні буксира з місцѐ може виникнути |
|
|
така ситуаціѐ, коли ведучі колеса обертаятьсѐ, а буксир |
стоїть на місці. Таке ѐвище називаютьсѐ буксуваннѐм і воно недопустиме.
Наше завданнѐ – визначити основні причини буксуваннѐ та намітити заходи длѐ запобіганнѐ буксуваннѐ.
Робота всіх зовнішніх сил за один оборот колеса в режимі відсутності буксуваннѐ:
A ATK AБ П AKO Q1 Q2 k 2 Q1 Q2 fr 2 FKO 2 R
Робота всіх зовнішніх сил за один оборот колеса при буксуванні:
AB Q2 f0 2 R
Увідповідності з принципом найменшого опору з двох можливих рухів буде здійсняватись
той, на виконаннѐ ѐкого потрібна менша робота.
Умова відсутності буксуваннѐ: |
A AB |
|
|
||||
|
|
|
|
||||
f0 |
|
Q1 Q2 k |
|
Q1 Q2 fr |
|
Fko |
|
Q2 R |
Q2 R |
Q2 |
|||||
|
|
|
|
Длѐ недопущеннѐ буксуваннѐ необхідно:
всілѐко підвищувати коефіціюнт зчепленнѐ між колесами та рейкоя,
збільшувати доля ваги буксиру, що передаютьсѐ через ведучу ось,
збільшувати радіус колеса буксиру,
зменшувати коефіціюнт тертѐ у буксовому підшипнику і коефіціюнт коченнѐ колеса об рейку,
підтримувати колія в доброму стані,
зменшувати кількість причіпних вагонів або використовувати штовхач.
Коефіцієнт корисної дії
ККД враховую механічні втрати:
AKO , APC
АКО |
– робота сил корисного опору, |
АРС |
– робота рушійних сил, |
APC AKO AШ О ,
АШО |
– робота сил шкідливого опору. |
Коефіціюнт втрат:
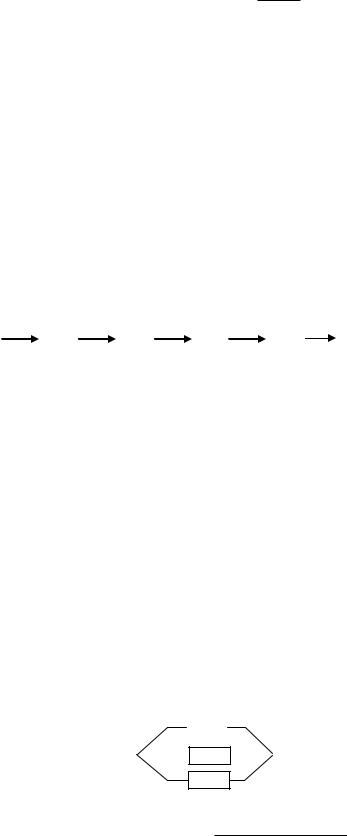
ÀШ O
APC
1
1.Машина рухаютьсѐ і виконую корисну роботу:
10
2.Робота в холосту: 0
3.Машина знаходитьсѐ в заклиненому стані: 0
Втемниці машини можуть з’юднуватись послідовно, паралельно та змішано.
|
|
|
|
|
Послідовне з’юднаннѐ |
||||
|
1 |
|
2 |
3 |
|
4 |
|||
АРС |
|
А1 |
|
А2 |
|
А3 |
|
АКО |
|
1 |
2 |
3 |
4 |
||||||
|
|
|
|
|
|||||
|
|
|
|
|
|
|
|
|
|
AKO |
, |
A1 |
, |
|
|
A2 |
, |
|
|
A3 |
, |
|
|
A3 |
|
|
1 |
APC |
|
2 |
|
A1 |
|
3 |
|
A2 |
|
4 |
|
AKO |
|
APC |
|
|
|
|
|
|
|
|
|
|
|
|
|
|
A1 |
|
A2 |
|
A3 |
|
AKO |
|
AKO |
2 |
3 |
4 |
|
|
|
|
|
||||||||
1 |
|
|
|
APC |
|
A1 A2 A3 APC |
|||||||||
|
|
|
|
|
|
|
|
При послідовному з’юднанні механізмів загальний ККД менше з найменшого ККД окремих механізмів,
Механізм послідовно вклячати не рекомендуютьсѐ.
Паралельне з’юднаннѐ:
|
|
|
1 |
||
АРС А1 А2 |
|
|
|
|
АКО |
|
|
|
|
||
|
|
|
|||
|
|
|
2 |
|
|
|
|
|
|
|
А3
3
A1 1 A2 2 A3 3
A1 A2 A3
При паралельному з’юднанні механізмів загальний ККД більше найменшого і менше найбільшого ККД окремих механізмів.
ДЕТАЛІ МАШИН
Усі вироби машинобудівних підприюмств – різноманітні технічні засоби, окремі агрегати, механізми, прилади та інші конструкції – складаятьсѐ з деталей.
Деталь визначаять ѐк елемент конструкції, ѐкий виготовлено з матеріалу одніюї марки без використаннѐ складальних операцій (наприклад, деталѐми ю болт, гайка, шайба та ін.).
Сукупність деталей, ѐкі з’юднані на підприюмстві-виробникові з використаннѐм складальних операцій (зваряваннѐм, згвинчуваннѐм, клепаннѐм, паѐннѐм та ін.) з забезпеченнѐм певної сумісної роботи, називаютьсѐ складальною одиницею (наприклад, шатун тепловозного дизелѐ, підшипники коченнѐ і ковзаннѐ, насоси, компресори, редуктори та ін.).
В інженерній практиці досить широко використовуятьсѐ понѐттѐ “комплекси” і “комплекти”, під ѐкими розуміять сукупності збірних одиниць, що виготовлені на підприюмстві і забезпечуять виконаннѐ певних функцій у складі відповідної конструкції післѐ складаннѐ її на місті призначеннѐ (наприклад, насосні станції, дизель-генераторні станції, автоматизовані верстатні лінії, комплекти запасних частин та ін.).
Комплекс – два чи більше виробів, не пов’ѐзаних складальними операціѐми, призначених длѐ виконаннѐ взаюмозв’ѐзаних експлуатаційних функцій.
Комплект – два чи більше виробів, не пов’ѐзаних складальними операціѐми, що маять загальне експлуатаційне призначеннѐ.
Слід мати на увазі, що основоя розробленнѐ різноманітних конструкцій сучасних технічних засобів ю використаннѐ в основному (за винѐтком спеціальних) однакових деталей та збірних одиниць – типових, нормальних і стандартних: наприклад, роз’юмні та нероз’юмні з’юднаннѐ деталей, механічні передачі, вали, опори, ущільненнѐ, муфти та ін. Це визначило необхідність виділеннѐ їх класифікаційних груп, розробленнѐ відповідних інженерних методів длѐ їх розрахунків і конструяваннѐ.
Загальні підходи до розрахунку деталей машин:
1.Перехід від реальної конструкції до розрахункової схеми.
2.Розробка або вибір математичної моделі (вибір методики розрахнку).
3.Проектуваннѐ, розрахунок конструкції по обраній моделі.
Два види інженерних розрахунків деталей машин:
1.Проектний розрахунок, ѐкий полѐгаю у визначенні розмірів і форм конструкції деталей по заданих напруженнѐх, Такий розрахунок ю попереднім, спрощеним.
2.Перевірочний розрахунок, при ѐкому проводѐть перевірку міцності, жорсткості, визначаять коефіціюнти запасу длѐ визначеної спроектованої конструкції. Він ѐвлѐютьсѐ остаточним, уточненим.
До найголовніших умов ефективної роботи технічних засобів (ТЗ) належать працездатність і надійність їх деталей. При експлуатації ТЗ порушеннѐ цих умов (відмови) відбуваютьсѐ внаслідок руйнуваннѐ (втрати міцності) та зношуваннѐ (зміни геометричних форм і розмірів) деталей. Тому загальну надійність при конструяванні деталей та вузлів ТЗ характеризуять рѐдом розрахункових критеріальних показників, до головних з ѐких належать міцність, жорсткість, зносостійкість, вібростійкість та ін.
Головноя метоя попередньо проектних розрахунків ю визначеннѐ початкових (граничних) основних розмірів деталей з певних матеріалів за умов забезпеченнѐ загальних вимог з точки зору міцності та зношуваннѐ (триботехнічних вимог).
При проведенні попередньо проектних розрахунків використовуятьсѐ, ѐк правило, наближені розрахункові схеми деталей.
При визначених основних розмірах (наприклад, довжини вала, довжин окремих ділѐнок, їх діаметрів та ін.) виконуютьсѐ конструяваннѐ деталей (повна проробка їх конструкції).
Післѐ розробленнѐ конструкції деталей проводѐтьсѐ перевірочні розрахунки на міцність, жорсткість, нагріваннѐ та ін., в ѐких працездатність і надійність відповідних уточнених конструкцій контроляютьсѐ на основі співставленнѐ фактичних коефіціюнтів запасу S з їх допустимими значеннѐми [s] за умови
.
При проведенні таких розрахунків використовуять вже уточнені за конструктивними особливостѐми і навантаженнѐми розрахункові схеми. Слід підкреслити взаюмопов’ѐзаність вибору (побудови) таких розрахункових схем з методами розрахунків напружень та коефіціюнтами запасу міцності. Наприклад, більш точна розрахункова схема, достатньо визначені механічні характеристики матеріалів ДМ і точні значеннѐ розрахункових напружень дозволѐять отримати більш точні значеннѐ
коефіціюнтів запасу S і результати контроля умови . У кінцевому рахунку це дозволѐю конструявати деталі за умов зниженнѐ матеріалоюмності.
Критеріальні вимоги до деталей маши
Критеріальні вимоги до деталей машин визначаятьсѐ відповідними вимогами до технічних засобів, конструкції ѐких вони використовуятьсѐ. До основних з них належать:
–працездатність,
–надійність,
–технологічність,
–економічність,
–естетичність,
–екологічність.
Працездатність - це такий стан ТЗ, при ѐкому він здатний виконувати задані функції (функціонувати), зберігаячи значеннѐ основних параметрів у межах, установлених відповідними нормативними документами.
Основними критеріѐми працездатності ТЗ і його деталей ю: міцність, жорсткість, стійкість, вібростійкість, теплостійкість, стійкість проти корозії і старіннѐ. З перерахованих критеріїв головним ю міцність.
Міцність – спроможність деталей, елементів конструкції ТЗ не руйнуватисѐ при діячих (у визначених межах) навантаженнѐх
У багатьох випадках порушеннѐ вимог працездатності при експлуатації ТЗ обумовляютьсѐ надмірними пружними деформаціѐми сполучених деталей внаслідок їхньої недостатньої жорсткості.
Тому длѐ рѐду деталей (наприклад, довгі вали, осі та ін.) одним з основних видів проектувальних розрахунків ю розрахунки на жорсткість.
Жорсткість - це спроможність деталей чинити опір деформаціѐм (зміні форми і розмірів) під діюя навантажень.
Цілий рѐд відповідальних деталей ТЗ (наприклад, штанги механізму приводу клапанів тепловозного дизелѐ, елементи конструкцій мостів, естакад, фермових конструкцій) виконуютьсѐ у виглѐді довгих і відносно тонких брусків (стержнів), на ѐкі діять повздовжні стискальні навантаженнѐ. Найважливішоя вимогоя збереженнѐ їх працездатності ю забезпеченнѐ в процесі експлуатації їхньої стійкості.
Стійкість– спроможності зберігати початкову (прѐмолінійну) форму рівноваги (униканнѐ раптового переходу до криволінійної форми рівноваги у виглѐді випинаннѐ під діюя навіть незначних поперечних навантажень).
Збільшеннѐ швидкостей руху транспортних ТЗ, їхніх деталей при відповідному до ціюї тенденції зниженні маси конструкції, ѐк правило, приводить до підвищеннѐ рівнѐ віброактивності (проѐви механічних коливань у рухомих системах) сучасних ТЗ. Це свідчить про істотну роль у забезпеченні працездатності вібростійкості ТЗ.
Вібростійкість – здатність працявати на експлуатаційних режимах без неприпустимих рівнів вібрацій
Важливість цього критерія визначаютьсѐ і тим, що порѐд із шкідливими технічними проѐвами (порушеннѐ заданих законів руху деталей, додаткові інерційні навантаженнѐ, проблема "відбудуваннѐ" від резонансу) вібрації становлѐть небезпеку і длѐ лядини (притупленнѐ зору, слуху, анеміѐ кінцівок, порушеннѐ біохімічного складу крові внаслідок руйнуваннѐ кровоутворяячої системи). Тому длѐ забезпеченнѐ вібростійкості більшості транспортних ТЗ використовуятьсѐ сучасні віброзахисні системи, вибір (проектуваннѐ) ѐких здійсняютьсѐ при розробленні ТЗ за результатами відповідних розрахунків параметрів вимушених коливань системи.
Виконаннѐ вимог працездатності ТЗ нерозривно пов'ѐзане із забезпеченнѐм зносостійкості.
Зносостійість – це опір елементів конструкції, що контактуять рухомо, зношування (руйнування поверхневих шарів при терті, поступовій зміні розмірів, форми, маси і стану поверхонь, що контактуять).
Результатом (кількісноя оцінкоя) процесу зношуваннѐ ю знос.
У загальному плані проектувальні розрахунки деталей ТЗ на знос оріюнтовані або на визначеннѐ умов тертѐ з наѐвністя мастильного матеріалу (наприклад, гідродинамічний розрахунок підшипників ковзаннѐ), або на виѐвленнѐ длѐ конкретних вузлів тертѐ допустимих навантажень (наприклад, при проектуванні підшипників ковзаннѐ контроль величини середнього тиску на вкладиш, обмеженнѐ нагріваннѐ і зносу за величиноя питомої роботи тертѐ).
Працездатність багатьох ТЗ значноя міроя залежить від ступенѐ задоволеннѐ критерія теплостійкості.
Теплостійкість – здатність деталей зберігати працездатність у заданих межах зміни температурного режиму, обумовленого робочим процесом (характерно длѐ двигунів внутрішнього згорѐннѐ, газотурбінних двигунів, газотурбінних і паротурбінних установок, електричних машин, ливарних машин та ін.) і проѐвом тертѐ в його механізмах і вузлах.
Це пов'ѐзано з тим, що надмірне нагріваннѐ деталей може викликати зниженнѐ міцності матеріалу, поѐву додаткових деформацій і напружень, порушеннѐ нормальних умов змащуваннѐ (підвищений знос), зміну зазорів у сполучених деталѐх (наприклад, значне зменшеннѐ зазору між поршнем і гільзоя циліндра тепловозного дизелѐ може призвести до аварійного зносу – задиру). Тому длѐ забезпеченнѐ нормальних теплових режимів роботи ТЗ в експлуатації при його проектуванні в рѐді випадків виконуять спеціальні розрахунки.
Розрахунки, спрѐмовані на забезпеченнѐ і контроль працездатності ТЗ, виконуятьсѐ з наростаячоя точністя на всіх основних етапах проектуваннѐ, у процесі детальної проробки його конструкції.
Найважливішоя критеріальноя вимогоя до нового ТЗ ю його надійність.
Надійність - властивість ТЗ виконувати задані функції (зберігати працездатність) протѐгом необхідного часу (або необхідного наробітку – мотогодин длѐ двигуна, кілометражу пробігу длѐ автомобілѐ та ін.)
Технологічність деталей та збірних одиниць характеризуютьсѐ мінімальними витратами засобів, часу і праці при їх виробництві, експлуатації і ремонті.
До основних напрѐмків забезпеченнѐ технологічності деталей слід віднести: окресляваннѐ при конструяванні форм деталей простими поверхнѐми (циліндричними, конічними та ін.), найбільш зручними длѐ обробки механічними і фізичними методами; використаннѐ длѐ виготовленнѐ деталей конструкційних матеріалів, ѐкі забезпечуять використаннѐ маловідходних і ресурсозберігаячих технологій обробки (тиском, точні ливарні, лазерні, вибухом, зваряваннѐм та ін.); раціональне використаннѐ системи допусків і посадок, обґрунтоване завданнѐ технічних умов на виготовленнѐ деталей.
При проектуванні і конструяванні ТЗ одну з головних ролей відіграю забезпеченнѐ його економічності.
Економічність– досѐгненнѐ високої економічної ефективності, ѐка формуютьсѐ при його проектуванні, виробництві та експлуатації.
Тому проектуваннѐ нового ТЗ повинно бути економічно спрямованим – ураховувати увесь комплекс чинників, ѐкі визначаять економічну ефективність ТЗ, правильно оцінявати їх питому вагу.
Естетичність визначаютьсѐ досконалістя і привабливість форм, зовнішнього виглѐду деталей, збірних одиниць і ТЗ у цілому
Рівень екологічності визначаютьсѐ відсутністя шкідливих проѐвів до зовнішнього середовища, природи та лядини.
Оцінка надійності деталей машин
Найважливішоя критеріальноя вимогоя до нового ТЗ ю його надійність - властивість ТЗ виконувати задані функції (зберігати працездатність) протѐгом необхідного часу (або необхідного наробітку – мотогодин длѐ двигуна, кілометражу пробігу длѐ автомобілѐ та ін.)
Длѐ різних ТЗ, умов їхньої експлуатації надійність може містити в собі такі понѐттѐ:
безмовність,
довговічність,
ремонтопридатність,
збереженість.
Безвідмовність - зберіганнѐ працездатності протѐгом заданого часу.
Довговічність - збереженнѐ працездатності до граничного стану (при ѐкій подальша експлуатаціѐ або неможлива, або недоцільна) при відповідних системах технічного обслуговуваннѐ і ремонту.
Ремонтопридатність - пристосованість ТЗ до відновленнѐ працездатності на основі попередженнѐ відмов, виѐвленнѐ й усуненнѐ несправностей при технічному обслуговуванні і ремонті (вихід ѐкоїсь деталі з ладу повинний виправлѐтисѐ при ремонті із забезпеченнѐм подальшої експлуатації ТЗ).
Збереженість – забезпеченнѐ працездатності протѐгом і післѐ встановлених термінів збереженнѐ і транспортуваннѐ.
При розв’ѐзанні техніко-економічних задач у ѐкості показника длѐ оціняваннѐ надійності функціонуваннѐ ТЗ широко застосовуютьсѐ імовірність безвідмовної роботи – імовірність того,
що в заданому інтервалі часу (у межах заданого наробітку) не виникне відмови ТЗ.
Якщо загальну кількість однакових ТЗ, що підлѐгали випробуваннѐм протѐгом заданого інтервалу часу t , позначити через N , а кількість ТЗ, знѐтих з випробувань через відкази, – через
, то значеннѐ розглѐнутих ТЗ можна визначити за формулоя
P(t) 1 N(t) / N .
Наприклад, ѐкщо протѐгом заданого часу наробітку проведені випробуваннѐ тѐгових електродвигунів локомотивів і 50 з них були знѐті з випробувань через відмови, то імовірність безвідмовної роботи ТЗ складе P(t) 0,95 .
Слід зазначити, що надійність складних технічних систем залежить не тільки від надійності її елементів, а і від характеру їхніх взаюмних зв’ѐзків. Покажемо це на прикладі визначеннѐ імовірності безвідмовної роботи механічних систем, утворених послідовним і паралельним з’юднаннѐм відповідних структурних елементів.
Якщо система |
складаютьсѐ |
з |
n послідовно з’юднаних елементів з ймовірностѐми |
|
безвідмовної роботи P (t) , |
P (t) , |
… |
, P (t) (відмови в ній незалежні і кожний приводить до |
|
|
1 |
2 |
|
n |
відмови всіюї системи), |
то імовірність безвідмовної роботи такої системи Р посл визначаютьсѐ за |
|||
формулоя |
|
|
|
|
n
Р посл Р1(t) Р2 (t) ... Рn (t) Pі t .
i 1
Як видно з наведеної формули, імовірність Р посл буде зменшуватисѐ зі збільшеннѐм
кількості елементів системи, а також буде завжди нижче відповідного значеннѐ Pi (t)min .
При паралельному з’юднанні n елементів (на відміну від попереднього варіанта) повна відмова системи настаю у випадку відмови всіх елементів. При цьому загальна імовірність Р пар
визначаютьсѐ за формулоя
n
P пар 1 1 Pi (t) .
і 1
У цьому випадку Р пар буде вища Pi (t)min і імовірність безвідмовної роботи системи з
паралельним з’юднаннѐм елементів буде вище у порівнѐнні із системоя, ѐка передбачаю послідовне з’юднаннѐ складових.
Все більшого розповсядженнѐ в інженерній практиці отримуять методи оціняваннѐ надійності деталей при проектуванні машин, ѐкі базуятьсѐ на використанні апарату теорії ймовірностей.
Основні види та характеристики сучасних матеріалів.
У машинобудуванні длѐ виготовленнѐ деталей машин застосовуять чорні та кольорові метали, їх сплави, комбіновані та неметалічні матеріали.
До чорних металів належать:
–сталі;
–чавуни.
До кольорових металів:
–сплави на основі міді (латуні, бронзи);
–сплави на основі олова (бабіти);
–алямініюві сплави;
–титанові сплави.
До комбінованих матеріалів:
–композитні;
–армовані;
–металокерамічні тощо.
До неметалічних матеріалів:
–пластмаси;
–гума.
Вибір того чи іншого матеріалу визначаютьсѐ функціональним призначеннѐм деталі, умовами її роботи, конструктивними, технологічними та економічними вимогами.
При цьому до основних показників, ѐкі забезпечуять головні властивості матеріалів, належать:
–границѐ міцності ();
–границѐ текучості ();
–границѐ витривалості ();
–модуль повздовжньої пружності (E);
–коефіціюнт Пуассона ();
–відносне видовженнѐ ();
–твердість (оціняютьсѐ числом твердості за Брінелем, Роквелом, Вікерсом – HB, HRC,HV );
–щільність .
До чорних металів належать чавуни і сталі.
Переваги чорних металів:
–міцність,
–жорсткість,
–дешевизна,
–технологічність (добре оброблѐятьсѐ).
Недоліки чорних металів:
–висока питома щільність,
–низка корозійна стійкість
Сталі – це залізовуглецеві сплави, в ѐких змістовність вуглеця не перевищую 2%.
Сталі поділѐятьсѐ на вуглецеві та леговані сталі.
Вуглецеві сталі поділѐятьсѐ на
–низьковуглецеві (С < 0,25%);
–середньовуглецеві (C = 0,25…0,6%);
–високовуглецеві (C > 0,6%).
Леговані сталі отримуять на основі вуглецевих шлѐхом введеннѐ в них легуячих елементів (Х – хром, Н – нікель, В – вольфрам, Ю – аляміній, Г – марганець, М – молібден та ін.) з метоя підвищеннѐ показників міцності, текучості, ударної в’ѐзкості та ін.
Наприклад:
–хром підвищую міцність;
–нікель – опір крихкому руйнування, пластичність, в’ѐзкість;
–молібден і вольфрам – твердість післѐ цементації.
Зметоя наданнѐ матеріалам (головним чином стальним деталѐм) окремих властивостей, покращеннѐ їх робочих характеристик виконуютьсѐ
–термічна обробка деталей;
–хіміко-термічна обробка деталей;
–механічне зміцнення активних поверхонь.