
Прикл мех
.pdf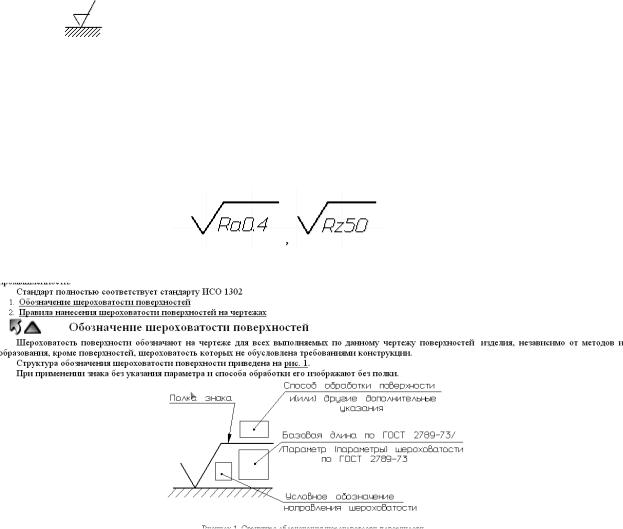
Вимоги до шорсткості поверхні встановляять шлѐхом зазначеного параметра шорсткості (або декількох параметрів), його числового значеннѐ (найбільшого, найменшого, номінального), а також при необхідності базової довжини і напрѐмку нерівностей.
Згідно з ГОСТ 2.309-73 шорсткість поверхонь позначаять на кресленні всіх поверхонь деталі, ѐкі виконуятьсѐ по даному креслення.
Позначеннѐ шорсткості:
.
Вид обробки не зазначений .
Шорсткість поверхні визначаютьсѐ знѐттѐм шаруячи матеріалу (шліфуваннѐ, поліруваннѐ й
інше)
Шорсткість поверхні утворитьсѐ без знѐттѐ шаруячи матеріалу (карбуваннѐ,
накочуваннѐ роликами й ін.) і неопрацьованих поверхонь Якщо переважне число поверхонь не оброблѐютьсѐ, шорсткість показуять
у правому верхньому куті .
Приклад:
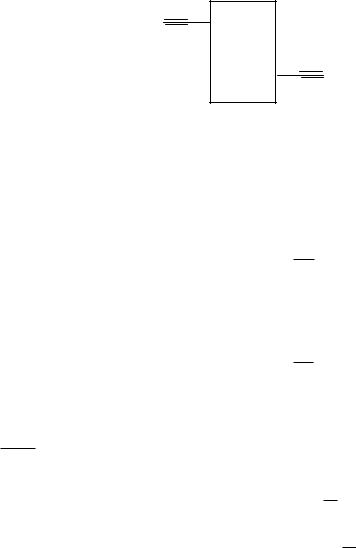
Механічні передачі
Механічна передача – механізм, що перетворяю задані кінематичні та енергетичні параметри двигуна на потрібні параметри руху робочих органів машин та призначений длѐ погодженнѐ режиму роботи двигуна з режимом роботи виконавчих органів.
Основні і похідні параметри механічних передач
Незалежно від типу та конструкції в будь-ѐкій механічній передачі можна виділити два вали, ѐкі називаять у напрѐмку передачі потужності вхідним (ведучим) та вихідним (веденим).
P1, n1
вхідний(ведучий)
вал
вихідний (ведений )вал
Цим валам приписуять основні параметри – потужність P (кВт) і частота обертаннѐ n (хв-1). Параметри вхідного (ведучого) вала маять індекс 1, параметри вихідного (веденого) вала – 2.
Крім основних параметрів, роботу механічної передачі характеризуять похідні параметри:
– передаточне число
u n1 ; n2
– коефіціюнт корисної дії
PP2 ;
1
При відомій потужності і частоті обертаннѐ на валу можна визначити крутний момент, Н·м
кВт
або хв 1 .
T P ;
T9550 Pn .
Узалежності від співвідношеннѐ параметрів вхідного і вихідного валів передачі поділѐятьсѐ:
на редуктори (знижуячі передачі) – від вхідного вала до вихідного зменшуять частоту обертаннѐ (n1 > n2) і збільшуять крутний момент (Т1 < Т2); передаточне число передачі u > 1;
на мультиплікатори (підвищуячі передачі) – від вхідного вала до вихідного збільшуять частоту обертаннѐ (n1 < n2) і зменшуять крутний момент (Т1 > Т2); передаточне число передачі u < 1.
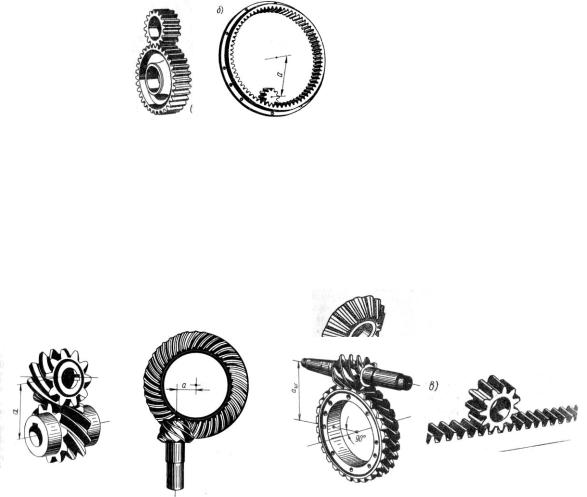
Зубчасті передачі
Переваги і недоліки:
По розташування валів класифікуятьсѐ:
с паралельними осѐми (циліндричні з внутрішнім і зовнішнім зачепленнѐм),
с пересічними осѐми (конічні),
з перехресними осѐми (гвинтові, гепоїдні, черв'ѐчні, колесо-рейка).
Якість роботи передачі пов’ѐзана з помилками виготовленнѐ зубчастих передач та деталей (корпус, підшипники, вали), ѐкі визначаять їх взаюмне розташуваннѐ. Деформаціѐ деталей під навантаженнѐм теж впливаю на ѐкість передачі.
До переваг зубчастих передач належать:
компактність;
найбільші передані потужності ;
найбільші колові швидкості;
постійне передатне відношеннѐ;
найбільший ККД.
Недоліками слід вважати:
складність передачі руху на значні відстані;
жорсткість передачі;
шум під час роботи;
потребую змащеннѐ.
Основні причини втрати працездатності передач
1. Поломка зубів:
–поломка від великих перевантажень;
–поломка від утоми від дії змінних напружень при довгому терміні експлуатації.
2. Ушкодження поверхні зубів:
–викришуваннѐ від утоми під діюя контактних напружень;
–абразивний знос, ѐкий виникаю при поганому змащенні, забрудненні;
–заїданнѐ, ѐке виникаю в високо навантажених і високошвидкісних передачах;
–пластичні зрушеннѐ спостерігаятьсѐ у високонавантажених тихохідних передачах, зубчасті колеса ѐких виконані з м’ѐких сталей;
–відшаровуваннѐ твердого поверхневого шару зубців, підданих термообробці.
Заходи по запобіганню поломки зубців від перевантажень:
–захист передач від перевантажень;
–збільшеннѐ жорсткості валів;
–використаннѐ зубців зі зрізаними кутами та бочкоподібних зубців.
Загальні заходи по запобіганню поломки зубців:
–визначеннѐ розмірів зубців із розрахунку на втомленість по напруженнѐм згину ;
–збільшеннѐ модуля;
–позитивне зміщеннѐ зуборізного інструменту при виготовленні коліс;
–термообробка;
–наклеп.
Усі види пошкоджень поверхні зубців пов'ѐзані з контактними напруженнѐми.
Викришування від втоми - основний вид руйнуваннѐ поверхонь зубців при доброму змащенні, найчастіше виникаю в закритих швидкохідних передачах, ѐкі захищені від пилу та бруду.
Заходи по запобіганню викришування зубців:
–визначеннѐ розмірів зубців із розрахунку на втомленість по контактних напруженнѐх ;
–підвищеннѐ твердості робочих поверхонь зубців шлѐхом термообробки;
–підвищеннѐ ступенѐ точності за нормоя контакту зубців.
В передачах, ѐкі працяять зі значним зношуваннѐм, викришуваннѐ не спостерігаютьсѐ, тому що поверхневі шари знімаятьсѐ раніше ніж з’ѐвлѐятьсѐ тріщини втоми.
Вирішальний вплив на працездатність зубців коліс у зубчастих передачах здійсняять контактні напруження та напруження згинання
, ѐкі носѐть циклічний характер.
Контактні напруженнѐ виникаять у місці контакту зубців і викликаять викришуваннѐ поверхонь зубців поблизу поляса зачепленнѐ в області ніжок зубців.
Напруженнѐ згинаннѐ виникаять в області ніжок і викликаять руйнуваннѐ зубців від втоми.
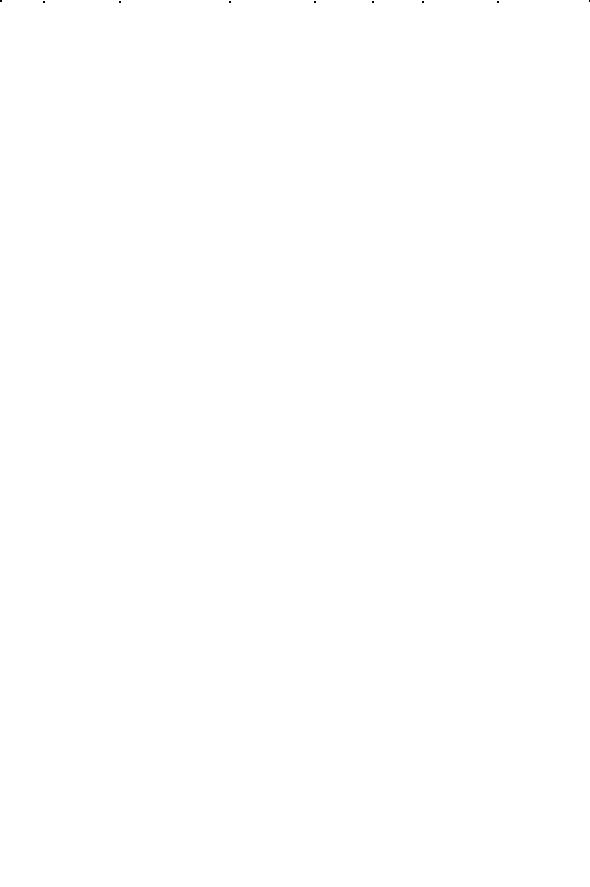
Класифікаціѐ механічних передач та їх порівнѐльна оцінка
Спосіб |
|
Взаємне розташування |
|
Передана |
Колова |
ККД |
Передаточне число |
передачі |
Тип передачі |
Вид передачі |
потужність |
швидкість |
|
||
валів |
|
в одному ступені |
|||||
руху |
|
|
Р, кВт |
V, м/с |
|
||
|
|
|
|
||||
|
|
|
|
|
|
|
|
|
|
Паралельне |
циліндричні |
1000 |
150 |
0,92...0,98 |
3...6 |
|
|
|
із зубчастоя |
|
|
0,92...0,98 |
1 |
|
|
|
рейкоя |
|
|
||
|
|
|
|
|
|
|
|
|
|
Вісі валів |
конічні |
|
|
0,91...0,97 |
3...5 |
|
|
перетинаятьсѐ |
|
|
|||
|
|
|
|
|
|
|
|
|
Зубчасті |
|
|
|
|
|
|
|
|
Вісі валів |
черв’ѐчні |
50 |
15 |
0,7...0,92 |
8...80 |
Зачепленнѐм |
|
перехрещуятьсѐ |
|
|
|
|
|
|
|
конічні |
|
|
0,8...0,9 |
3...5 |
|
|
|
гепоїдні |
|
|
|||
|
|
|
|
|
|||
|
|
|
|
|
|
|
|
|
|
|
циліндричні |
|
|
0,8...0,9 |
1...3 |
|
|
|
гвинтові |
|
|
||
|
|
|
|
|
|
|
|
|
|
|
|
|
|
|
|
|
|
|
з роликовими |
100 |
15 |
0,91...0,97 |
|
|
Ланцягові |
Паралельне |
втулковими |
|
|
|
2...6 |
|
|
|
|
|
|||
|
|
|
зубчастими |
|
35 |
|
|
|
|
|
ланцягами |
|
|
|
|
|
|
|
|
|
|
|
|
|
Із зубчастим |
Паралельне |
|
|
30 |
0,91...0,97 |
2...4 |
|
пасом |
|
|
|
|||
|
|
|
|
|
|
|
|
|
|
|
|
|
|
|
|
|
|
Паралельне |
плоскопасові |
50 |
30 |
0,94...0,97 |
2...4 |
|
|
|
клинопасові |
|
|
|
|
|
Пасові |
|
круглопасові |
|
|
|
|
|
|
|
|
|
|
|
|
|
|
Вісі валів |
плоскопасові |
|
|
|
|
Тертѐм |
|
перехрещуятьсѐ |
|
|
|
|
|
|
|
круглопасові |
|
|
|
|
|
|
|
|
|
|
|
|
|
|
|
|
|
|
|
|
|
|
|
Паралельне |
u = const |
300 |
30 |
0,7...0,8 |
3...6 |
|
|
|
u = var |
|
|
|
|
|
Фрикційні |
|
|
|
|
|
|
|
|
Вісі валів |
u = const |
|
|
|
|
|
|
перетинаятьсѐ |
|
|
|
|
|
|
|
|
u = var |
|
|
|
|
|
|
|
|
|
|
|
|
принципомЗа гвинтовоїпари |
Гвинт-гайка |
Співвісні |
|
100 |
5 |
0,3...0,4 |
1000 |
|
|
||||||
|
|
|
|
|
|
|
|
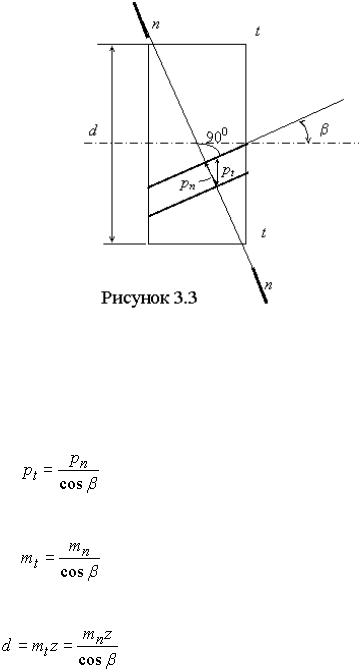
Косозубі циліндричні передачі
Косозубі колеса застосовуять длѐ відповідальних передач при середніх і високих швидкостѐх
Обсѐг їх застосуваннѐ – більше 30% обсѐгу застосуваннѐ усіх циліндричних коліс в машинобудуванні і цей відсоток безперервно зростаю. Косозубі колеса з твердими поверхнѐми потребуять підвищеного захисту від забруднень длѐ запобіганнѐ нерівномірного зношуваннѐ по довжині контактних ліній і небезпеки викришуваннѐ.
Косозубі циліндричні передачі нарізуятьсѐ тим самим різальним інструментом, на тих самих верстатах, за тіюя самоя технологіюя, що і прѐмозубі. При цьому
заготівля повертаять на кут , тому зубці розташовуятьсѐ не по утворяячій ділильного циліндра,
а складаять з нея кут .
Профіль косого зубцѐ в нормальному перетині n-n збігаютьсѐ з профілем прѐмого зубцѐ.
Модуль у цьому перетині повинний бути стандартним. У торцевому перетині t-t параметри
косого зуба зміняятьсѐ в залежності від кута
– коловий крок
,
– коловий модуль
,
– ділильний діаметр
.
Міцність зубців визначаять його розміри і форма в нормальному перетині. Форму косого зубцѐ в нормальному перетині прийнѐто визначати через параметри еквівалентного прѐмозубого колеса.
Збільшеннѐ еквівалентних параметрів зі збільшеннѐм кута ю одніюя з причин підвищеннѐ міцності косозубих передач. Унаслідок нахилу зубців виходить ніби колесо більших розмірів або при тому ж навантаженні зменшуятьсѐ габарити передачі.
Тому в сучасних передачах косозубі колеса одержали переважне поширеннѐ.
На відміну від прѐмих, косі зубці входѐть у зачепленнѐ не відразу по всій довжині, а поступово. На відміну від прѐмозубого зачепленнѐ косозубе не маю зони однопарного зачепленнѐ.
В прѐмозубому зачепленні навантаженнѐ з двох зубців на один чи одного на два передаютьсѐ миттюво, що супроводжуютьсѐ ударами та шумом. У косозубих передачах зубці навантажуятьсѐ поступово в міру заходу їх у зону зачепленнѐ , і в зачепленні завжди знаходитьсѐ ѐк мінімум дві пари.
Зазначене означаю плавність роботи косозубого зачепленнѐ, зниженнѐ шуму і додаткових динамічних навантажень у порівнѐнні з прѐмозубим зачепленнѐм.
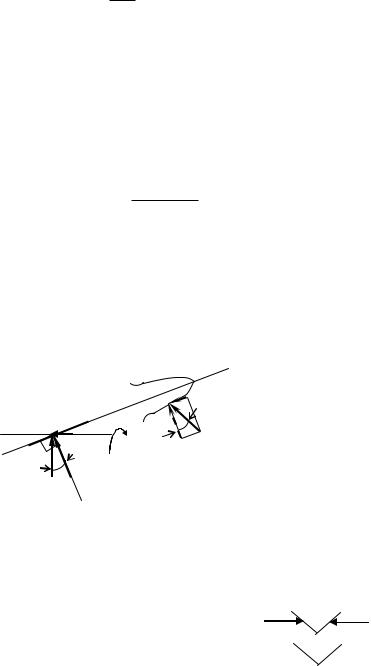
Сили в зачепленні
У косозубій передачі нормальну силу Fn розкладаять на три складові
колову силу
Ft 2T1 ; d1
осьову силу
Fa Ft tg ;
радіальну силу
Fr Ft tg Ft tg ;
cos
у своя чергу
Fn |
Ft |
|
Ft |
. |
|
cos |
cos cos |
||||
|
|
|
|
|
|
|
|
|
Fr |
|
|
|
|
|
|
|
|
Fa |
|
|
|
Fn |
|
|
|
|
|
|
|
|
|
|
|
|
|
|
|
|
|
||
|
Ft |
|
/ |
Ft / |
|
|
|
|
|
|
|
|
|
|
|
|
Ft |
|
|
|
|
|
|
|
|
|
|
|
|
|
|
|
|
|
|
|
|
|
|
|
|
|
|
|
|
|
|||||
Наѐвність у косозубій передачі осьових сил, що додатково навантажуять опори, ю недоліком. |
||||||||||||
Цей недолік усунутий у шевронній передачі |
|
|
|
|
|
|
|
|
|
|
||
У високонавантажених |
редукторах |
длѐ |
передачі крутного |
Fa |
|
|
Fa |
|||||
моменту з вала на вал використовуять подвоюний ступінь з |
|
|
||||||||||
рознесеними на валах шестернѐх та колесах. |
|
|
|
|
|
|
|
|
|
|
||
|
|
|
|
2 |
|
|
2 |
|
||||
|
|
|
|
|
|
|
|
|
|
|||
|
|
|
|
|
|
|
|
|
|
|
|
|
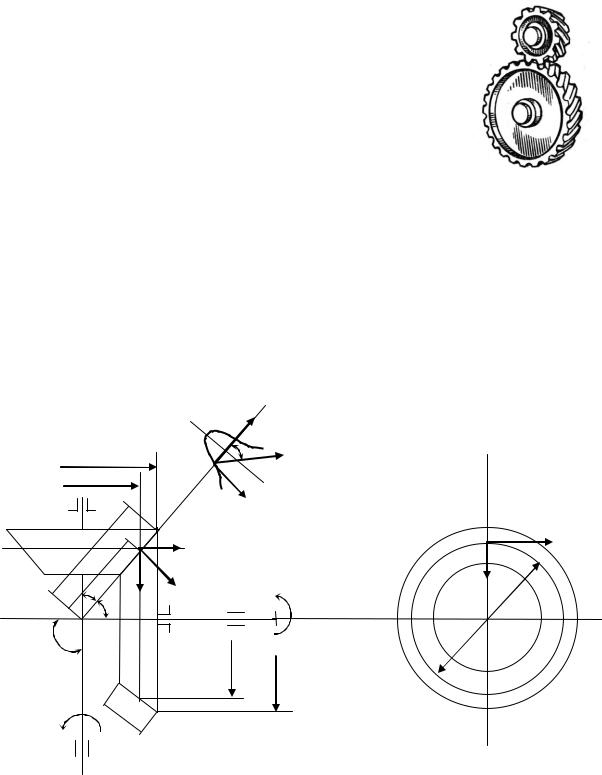
Зачеплення Новикова
У 1954 р. Новиковим було розроблено зубчасте зачепленнѐ з круговим профілем зубців.
Переваги:
підвищена навантажувальна здатність,
контактна міцність у 1,5...1,7 разів вище ніж у евольвентної косозубої передачі.
Недоліки:
чуттювість до зміни міжосьової відстані,
складний вихідний контур нарізуячого інструменту,
низька ізломна міцність .
Оскільки прѐмозубі колеса з круговим профілем зубців ю несполученими , то така передача працявати не може. Длѐ зберіганнѐ безперервності зачепленнѐ передачі Новикова виконуять косозубими з осьовим коефіціюнтом перекриттѐ. Профіль у одного колеса опуклий, у другого – увігнутий, чи одна частина профіля випукла, а друга – увігнута
Конічні передачі
Конічні зубчасті передачі застосовуять у тих випадках, коли вісі валів перетинаятьсѐ під деѐким кутом ( ѐк правило,
= 900)
Передачі з міжосьовим кутом, відмінним від 900, застосовуять рідко внаслідок складності
|
|
|
|
Ft |
|
|
de2 |
|
|
|
|
Fn |
|
dm2 |
|
|
|
|
|
|
|
|
|
|
Fr |
|
Ft |
|
|
|
Fa |
|
|
|
Re |
|
|
|
|
|
|
|
|
|
|
|
|
|
Rm |
|
1 |
Fr |
|
|
|
2 |
Fr |
|
|
Fr |
||
1 |
|
|
|
T1 |
|
|
|
|
|
|
|
dm1 |
|
|
|
|
|
|
|
|
|
|
|
m1 |
e1 |
|
|
|
|
|
|
|
||
|
|
|
d |
d |
|
|
bb
T2
форм і технології виготовленнѐ корпусних деталей, ѐкі несуть ці передачі, хоч длѐ самих коліс міжосьовий кут не маю значеннѐ. Незважаячи на те, що конічні колеса складніші ніж циліндричні у виготовленні і монтажі, вони маять достатньо широке використаннѐ в машинобудуванні, ѐке визначаютьсѐ умовами компонуваннѐ вузлів машин.
Прѐмозубі конічні зубчасті колеса доцільно застосовувати при невисоких колових швидкостѐх (до 2...3 м/с допустимо до 8 м/с). Зубці обробляять на спеціальних верстатах длѐ нарізуваннѐ конічних коліс. В масовому і крупносерійному виробництві у зв’ѐзку з можливістя компенсації при нарізуванні зубців наступних деформацій загартуваннѐ конічні колеса не шліфуять, а обмежуятьсѐ притиркоя. В конічних колесах длѐ забезпеченнѐ при складанні правильного контакту зубців передбачаять можливість осьового регуляваннѐ зубчастих коліс.
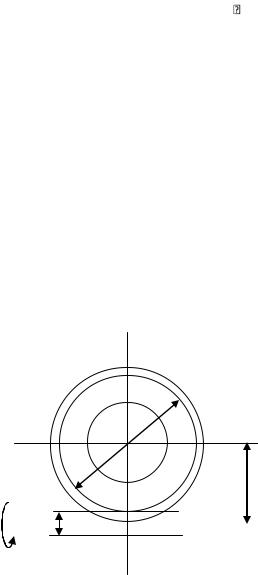
Конічні передачі більш складні, ніж циліндричні у виготовленні та монтажі внаслідок наступних причин:
–длѐ нарізуваннѐ конічних коліс потребуятьсѐ спеціальні верстати;
–необхідно витримувати допуски на кути та
;
–при монтажі треба забезпечувати збіг вершин конусів;
–складніше виконувати колеса тіюї самої точності, що й циліндричні;
–перетинаннѐ валів ускладняю розташуваннѐ опор (одне з конічних коліс розташовуютьсѐ, ѐк правило, консольно, при цьому збільшуютьсѐ нерівномірність розподіленнѐ навантаженнѐ по довжині зубцѐ);
–у конічному зачепленні діять осьові сили, що ускладняю конструкція опор.
Навантажувальна спроможність конічної прѐмозубої передачі складаю 0,85 циліндричної.
Геометричні параметри
Аналогом початкових та ділильних циліндрів ю початкові та ділильні конуси. Початкові і ділильні конуси, ѐк правило, у конічних коліс співпадаять, внаслідок того, що длѐ конічних коліс кутову корекція практично не застосовуять
В ѐкості торцевих перерізів розгѐдаять перерізи поверхнѐми додаткових конусів.
Конуси, утворяячі ѐких перпендикулѐрні до утворяячих ділильних конусів, маять назву
додаткові конуси.
Переріз зубцѐ додатковим конусом маю назву торцевий переріз Розміри по зовнішньому торця зручніші длѐ замірів, їх вказуять на кресленнѐх. Розміри у
середньому перерізі використовуять у силових розрахунках.
Черв’ячні передачі |
|
|
|
|
|
|
|
|
|
|
|
||
Черв’ѐчні передачі відносѐтьсѐ до |
|
|
|
|
|
|
|
|
|
||||
числа зубчасто-гвинтових, ѐкі маять |
|
|
|
|
|
|
|
|
|
||||
характерні властивості зубчастих і гвинтових |
|
|
|
|
|
|
|
|
|
||||
передач. |
|
|
|
|
|
|
|
|
dw2 |
||||
Черв’ѐчна передача складаютьсѐ з |
|
|
|
|
|||||||||
черв’ѐка, тобто гвинта з трапецеїдальноя чи |
|
|
|
|
|
|
|
|
|
||||
близькоя до неї по формі різьбоя, та |
|
|
|
|
|
|
|
|
|
||||
черв’ѐчного колеса, тобто зубчастого колеса |
|
|
|
|
|
|
|
|
|
||||
особливої форми, ѐку отримуять внаслідок |
|
|
|
|
|
|
w |
||||||
взаюмного огинаннѐ з витками черв’ѐка. |
|
|
|
|
|
|
|||||||
|
1 |
|
|
a |
|||||||||
|
|
|
|
|
|
|
|
w |
|
|
|
|
|
Рух |
у |
черв’ѐчних |
передачах |
n1 |
|
|
d |
|
|
|
|
|
|
|
|
|
|
|
|
|
|||||||
перетворяютьсѐ |
за |
принципом |
гвинтової |
|
|
|
|
|
|
|
пари |
||
|
|
|
|
|
|
|
|||||||
чи за принципом нахиленої площини. |
|
|
|
|
|
|
|
|
|
||||
|
|
|
|
|
|
|
|
|
|||||
Черв’ѐчні передачі застосовуять при |
|
|
|
|
|
|
|
|
|
||||
необхідності зниженнѐ швидкості та передачі |
|
|
|
|
|
|
|
|
руху |
||||
між осѐми, |
|
ѐкі |
перехрещуятьсѐ (кут |
|
|
|
|
|
|
|
|
|
перехрещуваннѐ, ѐк правило, становить 900).
Обсѐг застосуваннѐ черв’ѐчних передач складаю близько 10 % від передач зачепленнѐм. Випуск черв’ѐчних редукторів по числу одиниць складаю коло половини загального випуску редукторів.
Широко застосовуятьсѐ черв’ѐчні передачі у підйомно-транспортних машинах, верстатах, автомобілѐх та інших машинах.
Переваги:
–велике передаточне відношеннѐ;
–плавність та безшумність
–висока кінематична точність;
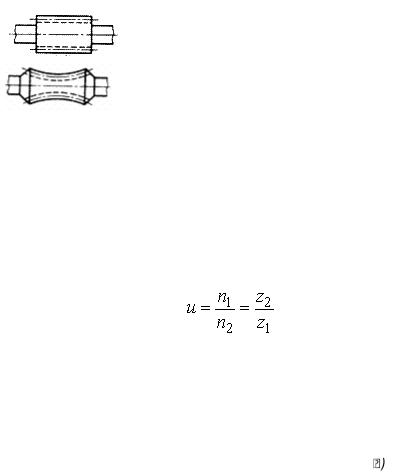
–самогальмуваннѐ. Недоліки:
–низький ККД;
–знос, заїданнѐ;
–використаннѐ дорогих матеріалів;
–висока точність складаннѐ.
Черв’ѐчні передачі внаслідок відносно низьких ККД застосовуять при невеликих і середніх потужностѐх від часток кіловату до 200 кВт. ѐк правило, до 60 кВт, длѐ моментів до 5 ·105 Нм. Передаточні відношеннѐ від 8 до 63...80 в силових передачах, до 200 в кінематичних передачах, в окремих випадках, наприклад в приводах столів великого діаметру – до 1000.
Черв’ѐки розрізнѐять:
1) за формоя утворяячої:
– циліндричні |
; |
– глобоїдні |
; |
2) за формоя профіля різьби: |
|
–прѐмолінійний (трапецеїдальний, архимедов – найбільш поширений, при HB ≤ 350, нешліфований, виконуятьсѐ на звичайних верстатах);
–криволінійний (евольвентний – HRC > 45, шліфований, на спеціальних верстатах).
Передаточне відношеннѐ черв’ѐчної передачі визначаять з умови, що за кожен оборот черв’ѐка колесо повертаютьсѐ на число зубців, ѐке дорівняю числу витків черв’ѐка:
Характерними особливостѐми роботи черв’ѐчних передач порівнѐно з зубчастими ю великі швидкості ковзаннѐ і несприѐтливий напрѐмок ковзаннѐ відносно лінії контакту.
Велике ковзаннѐ – причина зниженого ККД, підвищеного зносу, заїданнѐ.
ККД підвищуютьсѐ у разі збільшеннѐ числа заходів черв’ѐка (збільшуютьсѐ та зменшеннѐ коефіціюнта тертѐ чи кута тертѐ
У зв’ѐзку з високими швидкостѐми ковзаннѐ та несприѐтливими умовами змащуваннѐ матеріали черв’ѐчної пари повинні мати антифрикційні властивості, зносостійкість та знижену схильність до заїданнѐ.
Черв’яки виготовлѐять з вуглецевих чи легованих сталей
Найбільшу навантажувальну спроможність маять пари, у ѐких витки черв’ѐка термооброблені до високої твердості (загартуваннѐ, цементаціѐ тощо) з наступним шліфуваннѐм.
Черв’ячні колеса виготовлѐять переважно з бронзи, рідше з латуні чи чавуну.