
книги из ГПНТБ / Гельберг Б.Т. Вопросы технологии и организации ремонта оборудования
.pdf4. СБОРКА ЗУБЧАТЫХ И ЧЕРВЯЧНЫХ ПЕРЕДАЧ
Сборка зубчатых передач. При сборке отремонтированных
•механизмов очень важно обеспечить правильное сцепление зубча
тых передач, от чего в большой мере зависит качество работы этих передач и оборудования в целом. Нормальная работа зубчатой пе
редачи, собранной из шестерен, зависит от того, насколько пра вильно собраны оси валов, на которые устанавливаются шестерни,
соблюдено ли межцентровое расстояние между осями шестерен и
обеспечены ли зазоры между сопрягаемыми зубьями.
Собранную передачу в целом проверяют на краску, с тем чтобы
выявить правильность зацепления зубьев колес передачи. Технические требования на сборку зубчатых передач различ
ны. Они зависят от класса передачи, выбираемого в зависимости
от назначения и точности ее. Сборка зубчатых колес, работающих с большим числом оборотов и передающих значительные нагруз ки, выполняется с соблюдением более высоких точностных требо
ваний. Увеличение, например, зазора между зубьями шестерен
этой передачи вызывает при работе ее удары зубьев друг о друга
сбольшой силой, что приводит их к быстрому износу, а возможно,
ик поломке.
Втихоходных и малонагруженных передачах требования в от
ношении сборки могут быть снижены, так как удары зубьев при
малых числах оборотов будут менее ощутимы.
Зубчатые колеса и передачи по точности изготовления их при
ремонте должны соответствовать техническим условиям, предъяв
ляемым к передачам нового оборудования. Зубчатые передачи по
точности изготовления и сборки делятся на классы. По 1-му, высокому, классу точности изготовляются колеса и передачи, у ко торых скорость на окружности колес свыше 8 м/сек. 2-й класс установлен для прямозубых шестерен, имеющих окружную ско рость до 10 м/сек, 3-й — до 6 м/сек и 4-й— менее 2 м/сек.
Хорошо изготовленные и собранные зубчатые передачи работа
ют плавно и бесшумно. Так работают зубчатые колеса, имеющие
постоянный шаг и строго перпендикулярное расположение с мини мальным биением зубчатого венца относительно оси колеса.
Оси находящихся в зацеплении цилиндрических колес долж
ны быть параллельны, а межцентровое расстояние между ними
должно быть строго определенно. Между зубьями сцепляю щихся колес необходимо иметь зазоры, а давление зубьев веду щей шестерни на ведомую должно осуществляться путем со
прикосновения зубьев по определенной площадке, называемой
контактным пятном.
Межцентровое расстояние между опорами шестерен может из меняться вследствие износов деталей машин (шеек валов, подшип ников), как правило, в сторону увеличения. Поэтому при ремонте
металлорежущих станков нужно проверять межцентровое расстоя ние, чтобы определить пути восстановления его.
210
На рис. 128 показано определение межцентрового расстояния, в данном случае обозначенного буквой А. Его проверяют штанген циркулем 5 или штихмасом 2.
Для проведения замера необходимо в посадочные отверстия
корпуса 4 установить контрольные оправки 1 и 3.
Рис. 128. Проверка расстояния между осями ци линдрических шестерен
При замере межцентрового расстояния между валами получен ный размер между контрольными оправками надо увеличить на
радиусы оправок, если измерение производилось штихмасом, и
уменьшить на радиусы оправок, если измерение производилось штангенциркулем.
Правильность зацепления цилиндрических шестерен определя
ют при ремонте машин мягким щупом (из свинца) или по краске.
Проверка щупом производится при помощи свинцовой ленты. Ширина ленты подбирается примерно равной ширине проверяемых зубьев передачи. Толщина ленты — 0,1—0,2 мм.
Лента закладывается между зубьями, и шестерни проворачи ваются. По оттиску на ленте можно определить правильность контакта зубьев шестерен между собой. Величина зазора между
зубьями определяется замером толщины ленты микрометром или штангенциркулем.
14* |
211 |
Правильность зацепления собранных цилиндрических колес может быть проверена при монтаже по краске, для чего зубья ве дущей шестерни покрывают тонким слоем краски. Далее ведущую
шестерню проворачивают несколько раз вокруг своей оси и по от печатку на зубьях ведомой шестерни судят о правильности за цепления.
О правильности зацепления и сборки зубчатой пары свидетель ствует отпечаток (рис. 129, а). Все остальные отпечатки на рис. 129, б, в, г, д, е указывают на неправильные сборку и зацепле ние зубчатых колес.
Рис. 129. Проверка зацепления цилиндрических зубчатых
колес
Зацепление зубчатых колес, оси которых параллельны в одной плоскости, но непараллельны в другой, перпендикулярно распо
ложенной к первой, даёт отпечаток (рис. 129, б).
Зацепление зубчатых колес, оси которых непараллельны во всех плоскостях, т. е. спирально изогнуты, также дает отпечатки
(рис. 129, в, г).
Если оси зубчатых колес параллельны, но межцентровое рас
стояние увеличено или уменьшено, то оттиски будут такие, как по
казано на рис. 129, д, е.
Усилия, действующие на зубья, распределены неравномерно у шестерен, имеющих неправильное зацепление, и в процессе рабо ты это вызывает обычно шум и поломки в перегруженной части
зубьев.
Исключить возможность поломок можно, если перемонтиро вать зубчатые колеса так, чтобы оси их стали бы параллельны между собой, и сблизить, или, наоборот, развести их.
Проверка правильности зацепления конических зубчатых колес
производится также на краску или по оттиску на свинцовой
ленте.
212
При правильно изготовленной и собранной паре конических
зубчатых колес пятно касания не должно доходить до края мень шего торца зуба и до верхней кромки боковой поверхности его.
Пятно касания по своим размерам должно быть по длине зуба не менее — 60% для конических зубчатых колес 2-го класса, 50% для 3-го и не менее 40% для 4-го класса точности.
Пятно касания должно быть по рабочей высоте зуба не менее
40% для 2-го класса точности, 30% для 3-го и не менее 20% для конических зубчатых колес 4-го класса точности.
Зубчатое зацепле-
ние пары конических
зубчатых колес, хоро- |
/%%$?/ |
/ |
|||||||
шо |
изготовленных и |
4 / |
|
б) |
/ |
||||
правильно |
смонтиро- |
а) |
|
|
лЖ |
е) |
|||
ванных, даст такое пят- |
|
|
|
|
|
||||
но, как это указано на |
|
|
|
/и |
/лх// |
||||
рис. |
130, |
а. |
|
зубча- |
|
|
их!*?/ |
/%%%/ |
|
Зацепление |
|
|
|
/у |
|
||||
тых колес, при котором |
|
|
хШхЪС |
|
|||||
пятно касания имеется |
|
|
|
||||||
|
|
|
' г) |
д) |
|||||
только |
у |
носка |
(рис. |
|
1зо_ |
зубчатых колес |
|||
130, |
б) |
ИЛИ у |
ПЯТКИ |
рис |
Проверка |
зацепления конических |
|||
зубьев шестерни (рис. |
|
|
|
|
|
||||
130, |
в), |
может вызвать |
|
|
|
|
|
большой шум у работающих шестерен и даже поломку перегру женной части, т. е. носка или пятки зубьев шестерни.
Возможны случаи сборки конических зубчатых колес, когда они слишком сдвинуты или излишне удалены друг от друга. В пер
вом случае пятно касания будет таким, как на рис. 130, г, т. et слишком глубоким, а во втором — таким, как на рис. 130, д,
т. е. слишком мелким. При слишком глубоком зацеплении в про цессе работы шестерен получится заклинивание зубьев колес, а
при мелком — удар зуба о зуб шестерен, что может вызвать по
ломку зубьев шестерен.
Исправление производится следующим образом: в первом
случае ведомая шестерня удаляется от ведущей, а во втором ве домая шестерня приближается к ведущей по своим осям.
Сборка червячных передач. При монтаже червячных передач
важно обеспечить правильное зацепление червяка с червячным ко лесом. Правильность зацепления проверяется на краску, для чего на винтовую поверхность червяка наносят тонкий слой краски,
червяк вводят в зацепление с зубчатым колесом и проворачива
ют его в своих опорах несколько раз до получения отпечатков на
зубьях колеса (рис. 131).
При несовпадении средней плоскости червячного колеса и оси
червяка сдвигают червячное колесо вдоль оси, переставляя уста
новочные кольца и подрезая в случае необходимости торцы
колеса.
213
При правильном зацеплении пятно касания должно быть раз мещено по центру колеса и покрывать поверхность зуба по длине его не менее чем на 75% для передач 2-го класса точности, не ме нее чем на 55°/о для 3-го и на 40% для передач 4-го класса точ ности.
Случаи смещения отпечатка (рис. 131, а, б) свидетельствуют о том, что зацепление червяка с червячным колесом неправильно и
|
|
|
|
|
требуется |
регулирова |
|
|
|
|
|
|
ние колеса в части его |
||
|
|
|
|
|
положения. |
червяч |
|
|
|
|
|
|
Собранная |
||
|
|
|
|
|
ная пара |
подвергается |
|
|
|
|
|
|
испытанию в |
работе, |
|
|
|
|
|
|
причем |
в |
процессе |
|
|
|
|
|
работы |
проверяется: |
|
|
|
|
|
|
1) температура нагрева |
||
|
|
|
|
|
основных деталей, ко |
||
|
|
|
|
|
торая не |
должна пре |
|
|
|
а) |
б) |
В) |
вышать 40—45°; 2) лег |
||
Рис. |
131. |
Проверка зацепления |
червячной |
кость проворачивания |
|||
а — |
шестерня сдвинута вправо, б — шестерня сдви |
передачи и 3) |
шум, из |
||||
|
нута |
влево, в — нормальное зацепление |
даваемый |
работающей |
|||
|
|
|
передачи; |
|
передачей |
(он |
должен |
|
|
|
|
|
быть минимальным).
5. СБОРКА ГИДРОПРИВОДОВ
Сборку всех узлов гидроприводов так же, как и другого обо
рудования, необходимо производить аккуратно без ударов мо
лотком.
Все детали узлов не должны иметь вмятин и забоин. Забоины на сопрягающихся поверхностях крышек, корпусов и чугунных
прокладок нужно удалить шабрением по краске, притиркой по плите или по месту. Поступающие на сборку детали должны быт’
чисто промыты.
Насосы необходимо устанавливать не выше 0,5 м над уровнем масла или погружая в жидкость, что обеспечивает лучшие условия их работы.
Вал насоса надо тщательно сцентрировать с валом привода.
Неточность установки вызывает прогиб вала и преждевременный
износ ряда деталей, приводит к утечкам масла и засасыванию воз духа в систему. Надежное уплотнение места присоединения вса
сывающего трубопровода к насосу исключит возможность заса
сывания воздуха.
Маслопровод следует тщательно очистить изнутри и снаружи,
а все соединения надежно уплотнить, что исключит возможность засорения, образования вакуума и засасывания воздуха.
214
Резервуары тщательно вычищают и окрашивают маслостойкой
краской.
Концы сливных трубопроводов устанавливают, погружая в масло на глубину 70—80 мм от постоянного уровня. Слив масла по воздуху не допускается, так как при этом воздух перемешивает ся с маслом.
Проходное сечение в изгибах трубопроводов не должно умень шаться более чем на 10°/о, иначе давление на этом участке может повыситься; при этом масло нагреется и снизится напор жидкости в трубопроводе.
Маслопроводы всасывания и слива должны быть максималь
но удалены друг от друга, а концы их должны располагаться
на расстоянии не менее двух диаметров труб от дна бака. При
близком расположении трубок всасывания и слива трудно устранить образующуюся прямую циркуляцию масла, что ухуд
шает условия всасывания.
При расположении сливных маслопроводов на расстоянии от дна, меньшем двух диаметров труб, масло, поступающее че
рез них в резервуар, встречает повышенное сопротивление, ухуд
шает условия работы гидросистемы вследствие повышения дав ления в ней.
Масло в резервуар заливают фильтрованное. Фильтровать ма сло удобно, пользуясь специальной воронкой-фильтром.
Масло, работая в течение длительного времени в гидросистеме, постепенно засоряется. Поэтому масло следует периодически филь тровать, так как загрязненное масло засоряет мелкие каналы, зо лотники, клапаны, поршни, сокращает срок службы насосов, спо
собствует заеданию и образованию надиров на поршнях, цилинд
рах, золотниках.
Отсюда ясно, что фильтрующие устройства в гидроприводах имеют большое значение и содержать их нужно всегда в исправ ном состоянии.
Бумажные прокладки (для уплотнения), устанавливаемые при
сборке насосов, рекомендуется пропитать нитролаком.
Если насос собирают без установки бумажных прокладок, то
сопрягаемые поверхности деталей должны быть тщательно при гнаны, шестерни по высоте должны быть ниже высоты корпуса на
0,03—0,05 мм. Детали насоса перед сборкой тщательно промыва
ют в бензине (за исключением шарикоподшипников), а затем при сборке на торцы корпуса и фланцев наносят тонкий слой нитро лака.
Собранный насос (на нитролаке) просушивают в течение
5—8 час.
При сборке насоса возможно защемление вращающихся дета
лей, о чем свидетельствует трудность проворачивания приводного
вала вручную.
Причиной этого может быть неправильное положение конт
215
рольных штифтов в том случае, если детали изготовлены пра вильно.
Для устранения данного дефекта штифты удаляют и регулиру
ют насос на легкость вращения, затем затягивают все болты и раз
ворачивают отверстия под штифты большего диаметра.
При ремонте насосов особое внимание нужно уделять уплот няющим устройствам (рис. 132). Сальниковая набивка 1 в насосе должна исключить попадание в него воздуха через трущуюся по верхность вала 3. Уплотнителем может служить асбестовый шнур, пропитанный тавотом. При появлении в масле воздушных пузырь ков необходимо улучшить уплотнение путем подтяжки фланца 2.
Рис. 132. Шестеренчатый насос
Отремонтированный насос необходимо испытать на специаль ном стенде и проверить его производительность.
Перед сборкой лопастных насосов все детали их промывают в чистом керосине или бензине и просушивают (обдувают сжатым воздухом или протирают чистыми тряпками).
При сборке проверяют, перемещаются ли лопатки по пазам^ ротора без заеданий и качки и не выступают ли грани лопаток,,
помещенных в пазы ротора, за пределы его пазов.
Установка ротора в корпус ведется так, чтобы наклон пазов-
ротора и острия располагаемых в них лопаток были направлены
в сторону вращения ротора. Установка этих деталей в противо
положном направлении не только снижает производительность и давление насоса, но сокращает и срок его службы.
После установки всех деталей на место затягивают болты кры шки насоса (по правилам многоболтового крепления) так, чтобы ротор относительно легко и плавно провертывался вручную оде тым на вал воротком.
Перед пуском насос должен быть залит маслом.
216
Отремонтированный насос подвергают испытаниям на стенде' или непосредственно на станке, для чего его обкатывают на холо
стом ходу в течение 15—20 мин., и, если дефектов нет, испытыва
ют под нагрузкой, постепенно повышая давление.
Проверка насоса при максимальном давлении 70—80 кг/см?
допускается лишь в течение 3—5 мин.
Хорошо отремонтированный насос работает без шума, замет
ных наружных утечек масла и не вса
сывает воздух через сальник и другие соединения.
Далее насос испытывают на стенде, где проверяют его производительность.
Для этой цели включают насос, уста
новленный на специальный стенд (рис. 133), что позволяет измерить произво дительность насоса.
Насос 1 установлен над резервуа ром, откуда он засасывает масло и по
дает его через4 |
дроссель |
2 |
к крану |
3. |
Рис. |
на стенде |
(схема) |
|||
Переключая кран, направляют |
масло |
|
133. Испытание насоса |
|||||||
в мерный бак |
или обратно в |
резер |
|
|
|
|
||||
вуар. |
|
|
|
|
измеряют следующим |
образом. |
||||
Производительность насоса |
||||||||||
Кран2, |
устанавливается в положение подачи в резервуар. Затем |
|||||||||
включают электродвигатель, соединенный с насосом |
и |
дроссе |
||||||||
лем |
и создают необходимое давление, |
после чего |
кран пере |
ключают на положение подачи масла в мерный бак и одновре менно пускают в ход секундомер.
По истечении определенного промежутка времени кран перево дят в первоначальное положение, а количество поданного в бак
масла определяют по шкале на стекле 5.
Измерение, произведенное без давления при открытом дроссе ле, позволит определять объемный к. п. д. насоса, т. е. отношение количества подаваемой насосом жидкости под давлением к коли
честву подаваемой им жидкости без давления при одинаковых,
условиях работы и температуры жидкости.
Объемный к. п. д. обычно указывают при рабочем давлении
насоса на масле — веретенном 3 или турбинном Л (при темпе ратуре масла 50°).
6. СБОРКА СТАНКОВ
Качество сборки станка зависит от того, насколько правильно-
собраны его отдельные узлы и механизмы. Для каждого вида ма
шин существуют свои, особые требования по сборке, но есть и об
щие для всех машин правила ведения сборки и основные условия, которым должна удовлетворять сборка узлов и механизмов, на
иболее часто встречающихся в большинстве современного про мышленного оборудования.
217
Рис. 134а. Приспособление для проверки положения оси
шпинделя
218
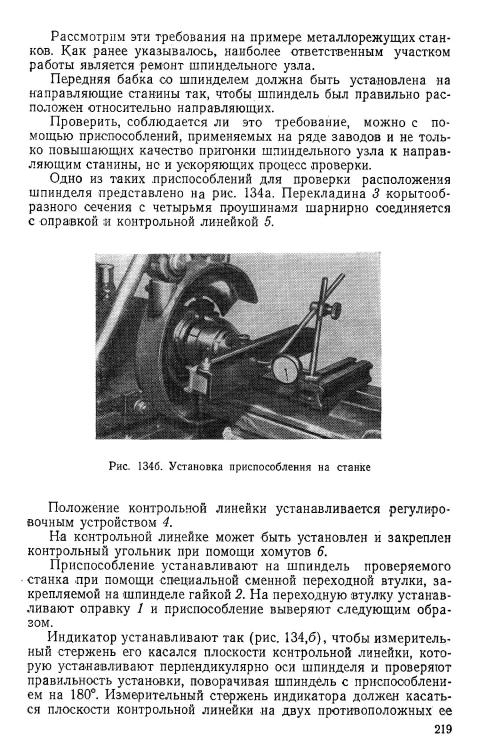