
Okrepilov Quality Management
.pdf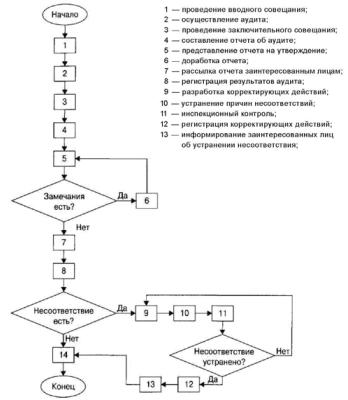
-улучшитепоточнуюдиаграммунаосновеэтогорассмотрения;
-сверьте диаграмму с фактическими этапами процесса;
-отметьте на получившейся поточной диаграмме название и местоположение процесса, дату составления диаграммы, сведения об участниках работы по составлению диаграммы и любую другую информацию, достойную внимания.
При разработке нового процесса порядок составления поточ- ной диаграммы аналогичен рассмотренному выше.
Полученная поточная диаграмма существующего (разрабаты- ваемого) процесса служит документом о фактическом (предполага- емом) протекании процесса и может быть использована для поиска
иидентификации возможностей его улучшения.
Ниже, на рис. 2.24 приведен пример [181] поточной диаграммы процесса внутреннего аудита.
Рис. 2.24. Блок-схема внутреннего аудита
271
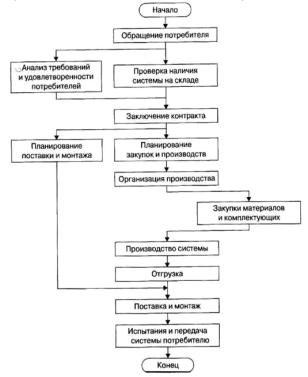
Диаграмма процесса осуществления программы
Диаграммапроцессаосуществленияпрограммы(Process Decision Program Chart – PDPC) представляет собой диаграмму, очень похо- жую на рассмотренную выше поточную диаграмму [297, 410]. PDPC отображает последовательность действий и решений, необходимых для получения желаемого результата, но может быть использована для оценки сроков и целесообразности проведения работ по выпол- нению программы, например, в соответствии со стрелочной диа- граммой Ганта, как до их начала, так и в процессе выполнения этих работ(свозможнойкорректировкойсроковихвыполнения).
На рис. 2.25 приведен пример PDPC [375], определяющей по- рядок действий и принятия решений от момента получения заказа отпотребителяидомоментапередачиемуготовойсистемыприми- нимально возможном времени.
Рис. 2.25. Диаграмма процесса осуществления программы работ при выполнении заказа потребителя на производство, поставку и монтаж системы
272
Четкое соблюдение очередности и выполнение всех этапов про- цессапозволяетминимизироватьвремя, необходимоедляосуществле- ния процесса. Это минимальное время на английском языке называ- ют«lead time» ичасто переводятнарусский языккак «мертвое время», подразумевая то время, в течение которого организация (изготовитель продукции) не только не получает прибыль, а, наоборот, вынуждена расходовать свои средства, которые будут возвращены потребителем (покупателем) толькопослетого, какпродукциябудетимприобретена.
Практика показывает, что при оформлении РDРС наиболее часто используюттолькотрисимвола(изприведенныхнарис. 2.23), аименно:
–овал (для обозначения начала и конца процесса);
–прямоугольник (для обозначения действий и операций);
–линии со стрелками (для указания направления протекания процесса).
При необходимости диаграмма осуществления программы, изображенная на рис. 2.25, может быть представлена в виде поточ- нойдиаграммы(картытехнологическогопроцесса), выполненнойс применением полного набора символов.
Поточные диаграммы процессов и РDРС широко используют- сяприрешениисложныхпроблемвобластинаучно-исследователь- ских работ, при проектировании и разработке новых видов продук- ции, выполнении крупных производственных заказов и т. п.
Матрица приоритетов
Матрица приоритетов [192, 297, 410, 445, 375] – инструмент для обработкибольшогоколичествачисловыхданных, полученныхпри построении матричных диаграмм (таблиц качества), имеющий це- лью выявление приоритетных данных.
Основное назначение матрицы приоритетов – это распределе- ние различных наборов элементов в порядке значимости, а также установление относительной важности между элементами за счет числовых значений.
Матрица приоритетов может быть построена тремя способами:
1.Аналитическийметод– применяется, когдаотносительноне- велико число критериев (не больше 6), необходимо получить пол- ное согласие всех экспертов, принимающих участие в оценке (чис- лоэкспертовнепревышает8 человек), возможныбольшиепотерив случае ошибки с расстановкой приоритетов.
2.Метод определения критериев на основе консенсуса – при- меняется, когда число экспертов составляет более 8 человек, суще-
273
ствует значительное число критериев (от 6 до 15), имеется большое число ранжируемых данных (порядка 10-20 элементов).
3. Матричный метод – применяется в основном, когда между ранжируемыми элементами есть сильная взаимосвязь, а нахожде- ние элемента с наибольшим влиянием является критичным для ре- шения поставленной задачи.
Порядокдействий, покоторымстроитсяматрицаприоритетов, длявсехтрехвариантов, восновном, одинаковый. Различиязаклю- чаются в определении значимости критериев. Рассмотрим все эти нюансы на примере [375].
Матрица приоритетов строится в следующем порядке:
1.Определяется основная цель, ради которой строится матрица приоритетов.
Пример: уменьшить количество дефектов в изделии.
2.Формируется команда экспертов, которая будет работать над поставленной задачей. Эксперты должны понимать область реша- емой проблемы и иметь представление о методах коллективной ра- боты (например, о методе «мозгового штурма» и т.п.).
3.Составляется список возможных решений поставленной проблемы. Список может быть составлен за счет применения дру- гих инструментов качества, например «мозгового штурма», диа- граммы Исикавы и пр.
Пример: список решений поставленной проблемы, сформиро- ванный командой экспертов:
– изменить технологию изготовления;
– увеличить число точек контроля;
– провести обучение мастеров;
– изменить конструкцию изделия.
4.Определяется состав критериев. Изначально он может быть достаточно большим. Матрица приоритетов будет включать в себя только часть этих критериев, т.к. в дальнейшем он сократится за счет выбора наиболее важных и существенных.
Пример: составкритериевдляоценкиприоритетностирешений:
– требуется не более 100 чел\час на реализацию решения;
– низкая стоимость реализации решения;
– количество вовлекаемого персонала не более 50 чел.;
– снижение затрат на брак не менее чем в 1,5 раза.
5.Назначается весовой коэффициент для каждого критерия. Назначение весового коэффициента производится в зависимости
от выбранного метода (рис. 2.26).
274
|
|
Критерий |
|
|
|
|
|
Весовой коэффициент |
метод |
|||||
|
|
|
|
|
|
|
|
|
|
|
|
|||
Требуется не более 100 чел/час на реализацию |
|
|
3 |
|
||||||||||
|
|
решения |
|
|
|
|
|
|
|
|
Аналитический |
|||
|
|
|
|
|
|
|
|
|
|
|
|
|||
Снижение затрат на брак не менее чем в 1,5 раза |
|
|
9 |
|
||||||||||
Низкая стоимость реализации решения |
|
|
|
|
|
9 |
|
|
||||||
Количество вовлекаемого персонала не более 50 чел. |
|
|
1 |
|
|
|||||||||
|
|
|
|
|
|
|
|
|
|
|
|
|
|
|
|
|
|
|
|
|
|
|
|
|
|
|
|
|
|
Критерий |
|
Эксперт |
Эксперт |
|
Эксперт |
|
Весовой |
|
||||||
|
|
|
|
1 |
|
2 |
|
3 |
|
|
коэффициент |
консенсуса |
||
Требуется не более 100 |
|
2 |
|
3 |
|
1 |
|
|
6 |
|
||||
Низкая стоимость |
|
|
|
|
|
|
||||||||
чел/час на реализацию |
|
1 |
|
0 |
|
0 |
|
|
1 |
|
|
|||
решения |
|
|
|
|
|
|
|
|
|
|
|
|
|
|
реализации решения |
|
|
|
|
|
|
|
|
|
|
|
Метод |
||
персонала не более 50 чел. |
|
0 |
|
1 |
|
0 |
|
|
1 |
|
||||
Количество вовлекаемого |
|
|
|
|
|
|
|
|
|
|
|
|
||
Снижение затрат на брак |
|
1 |
|
0 |
|
3 |
|
|
4 |
|
|
|||
не менее чем в 1,5 раза |
|
|
|
|
|
|
|
|||||||
|
|
|
|
|
|
|
|
|
|
|
|
|||
|
|
|
|
|
|
|
|
|
|
|
|
|
|
|
|
|
Требуется |
Низкая |
|
Количество |
|
Снижение |
|
|
|||||
|
|
не более |
|
|
|
|
||||||||
|
|
|
|
затрат на |
|
|
||||||||
|
|
100 чел/час |
стоимость |
|
вовлекаемого |
|
|
|
||||||
Критерии |
|
|
|
|
брак не |
Итого |
|
|||||||
|
на |
реализации |
|
персонала не |
|
|
|
|||||||
|
|
|
|
менее чем |
|
|
||||||||
|
|
реализацию |
решения |
|
более 50 чел. |
|
|
|
||||||
|
|
|
|
в 1,5 раза |
|
|
||||||||
|
|
решения |
|
|
|
|
|
|
|
|
|
|||
|
|
|
|
|
|
|
|
|
|
|
|
|
||
Требуется не |
|
|
|
|
|
|
|
|
|
|
|
|
|
|
более 100 |
|
х |
0 |
|
|
|
|
1 |
|
0 |
1 |
метод |
||
реализацию |
|
|
|
|
|
|
||||||||
чел/час на |
|
|
|
|
|
|
|
|||||||
решения |
|
|
|
|
|
|
|
|
|
|
|
|
|
Матричный |
решения |
|
|
|
|
|
|
|
|
|
|
|
|
|
|
Низкая |
|
|
|
|
|
|
|
|
|
|
|
|
|
|
стоимость |
|
2 |
|
х |
|
|
|
2 |
|
1 |
5 |
|
||
реализации |
|
|
|
|
|
|
|
|||||||
|
|
|
|
|
|
|
|
|
|
|
|
|
|
|
|
|
|
|
|
|
|
|
|
|
|
|
|
|
|
Количество |
|
|
|
|
|
|
|
|
|
|
|
|
|
|
вовлекаемого |
|
1 |
|
0 |
|
|
|
|
х |
|
0 |
1 |
|
|
персонала не |
|
|
|
|
|
|
|
|
||||||
|
|
|
|
|
|
|
|
|
|
|
|
|
|
|
более 50 чел. |
|
|
|
|
|
|
|
|
|
|
|
|
|
|
Снижение |
|
|
|
|
|
|
|
|
|
|
|
|
|
|
затрат на брак |
|
2 |
|
1 |
|
|
|
|
2 |
|
|
х |
5 |
|
не менее чем |
|
|
|
|
|
|
|
|
|
|||||
|
|
|
|
|
|
|
|
|
|
|
|
|
|
|
в 1,5 раза |
|
|
|
|
|
|
|
|
|
|
|
|
|
|
Рис. 2.26. Методы назначения весовых коэффициентов
Для аналитического метода:
–устанавливается рейтинговая шкала для каждого критерия;
–для каждого числового значения шкалы дается определение значимости. Для того чтобы различия в весовых коэффициентах были более заметны, обычно применяют шкалу с числовыми зна- чениями 1-3-9 (где 1 – малая значимость, 3 – средняя значимость, 9 – большая значимость).
Для метода консенсуса:
–устанавливается некоторое количество баллов, которые экс- пертыдолжныраспределитьмеждукритериями. Количествобаллов должно быть не меньше числа критериев;
–каждыйизэкспертовраспределяетназначенныебаллымежду
критериями;
275

– определяется суммарное число баллов по каждому из крите- риев. Это значение и будет являться весовым коэффициентом каж- дого из критериев.
Для матричного метода:
–критерии располагаются в виде L-матрицы;
–устанавливается шкала для попарного сравнения критериев (например, «0» – критерий А менее значим, чем критерий Б; «1» – критерийАикритерийБравнозначны; «2» – критерийАболеезна- чим, чем критерий Б);
–проводится попарное сравнение всех критериев;
–определяется весовой коэффициент каждого критерия (весо- вой коэффициент подсчитывается как сумма всех значений в стро- ке матрицы).
6. Отбираются наиболее значимые критерии.
7. Устанавливается метод подсчета значимости каждого из ре- шений матрицы приоритетов (определены на шаге 3) на основе вы- бранных критериев (определены на шаге 6).
8. Проводится оценка каждого решения по отношению к каж- дому критерию.
9. Оценка перемножается на весовой коэффициент соответству- ющегокритерия. Полученныезначениясуммируютсяпокаждомуиз решений, что дает окончательную оценку приоритетности решений. Итоговая оценка, которую содержит матрица приоритетов, может бытьоставленакакесть, илипереведенавпроценты(табл. 2.7).
Таблица 2.7
Матрицаприоритетовпопроблеме«уменьшитьколичестводефектоввизделии»
|
Требуется не |
Низкая |
Количество |
Снижение |
|
|
более 100 |
|
|||
|
стоимость |
вовлекаемого |
затрат на брак |
|
|
Критерии |
чел/час на |
|
|||
реализации |
персонала не |
не менее чем |
|
||
|
реализацию |
Итого |
|||
|
решения |
решения |
более 50 чел. |
в 1,5 раза |
|
|
|
|
|
|
|
Решения |
Весовой коэф. |
Весовой коэф. |
Весовой коэф. |
Весовой коэф. |
|
= 3 |
= 9 |
= 1 |
= 9 |
|
|
|
|
||||
Изменить |
|
|
|
|
|
технологию |
9 |
9 |
1 |
81 |
100 |
изготовления |
|
|
|
|
|
Увеличить |
27 |
27 |
9 |
27 |
90 |
число точек |
|||||
контроля |
|
|
|
|
|
Провести |
|
|
|
|
|
обучение |
27 |
81 |
1 |
9 |
118 |
мастеров |
|
|
|
|
|
Изменить |
9 |
27 |
9 |
27 |
72 |
конструкцию |
|||||
изделия |
|
|
|
|
|
276
9.4.Комплексные инструменты менеджмента качества
Вданном параграфе рассматриваются комплексные инстру- менты и методологии улучшения качества, которые позволяют результативно и эффективно осуществлять так называемые про- екты прорыва, ведущие к радикальному пересмотру и изменению существующих процессов или даже к внедрению новых процессов. Однако эти методологии и инструменты могут быть использованы также при постоянном и поэтапном улучшении имеющихся в орга- низации процессов.
FMEA методология
Метод FMEA (Failure Mode and E ects Analysis) – анализ видов и последствий отказов – это метод, применяемый при проекти- ровании продукции и производственных процессов, при помощи которого систематически идентифицируются последствия каждого отдельного компонента аварийных состояний. Непременной отли- чительной чертой в любом FMEA является рассмотрение каждого основного компонента или части системы на предмет того, каким образом он достигает аварийного состояния и как это влияет на аварийное состояние всей системы.
Анализ форм и последствий отказов обычно предполагает осу- ществление трех крупных этапов работы [445]:
1. Подготовка к работе FMEA-команды.
При подготовке к работе и в начале плановых заседаний руко- водитель FMEA-команды должен выполнить следующее:
1.1.Сформировать межфункциональную и квалифицирован- ную команду, состоящую из 5-9 специалистов.
1.2.Заранее провести короткое предварительное совещание, на котором объяснить членам команды цели предстоящего заседания, основные подходы к FMEA-анализу, а также основные роли членов FMEA-команды.
1.3.Предоставить членам FMEA-команды необходимую ин- формацию, которая должна быть ими заранее тщательно изучена.
2. Основная работа FMEA-команды.
2.1.Построение компонентной, структурной, функциональной
ипотоковой моделей объекта анализа (рис. 2.27).
2.2.Исследование моделей, при котором определяются:
–потенциальные дефекты для каждого из элементов компо- нентной модели объекта. Такие дефекты обычно связаны или с
277

Компонентная |
|
Модель |
|
|
||
модель |
|
|
|
материальных |
|
|
|
|
|||||
|
|
|
||||
|
|
Структурная |
|
потоков |
|
Функциональная |
|
|
модель |
|
|
|
модель |
|
|
|||||
|
|
|
|
|
|
|
|
|
|
|
|
|
|
Анализ причин появления дефектов (с помощью диаграмм Исикавы)
Рис. 2.27. Схема FMEA-анализа
отказом функционального элемента (его разрушением, поломкой и т.д.) или с неправильным выполнением элементом его полезных функций (отказом по точности, производительности и т.д.) или с вредными функциями элемента. В качестве первого шага рекомен- дуется перепроверка предыдущего FMEA-анализа или анализ про- блем, возникших за время гарантийного срока. Необходимо также рассматривать потенциальные дефекты, которые могут возникнуть при транспортировке, хранении, а также при изменении внешних условий (влажность, давление, температура);
–потенциальные причины дефектов. Для их выявления могут быть использованы диаграммы Исикавы, которые строятся для каждой из функций объекта, связанных с появлением дефектов;
–потенциальные последствия дефектов для потребителя. По-
скольку каждый из рассматриваемых дефектов может вызвать це- почку отказов в объекте, при анализе последствий используются структурная и потоковая модели объекта;
–возможности контроля появления дефектов. Определяется,
может ли дефект быть выявленным до наступления последствий в результате предусмотренных в объекте мер по контролю, диагно- стике, самодиагностике и др.;
–параметр тяжести последствий для потребителя – В. Это – экспертная оценка, проставляемая обычно по 10-ти балльной шка- ле; наивысший балл проставляется для случаев, когда последствия дефекта влекут юридическую ответственность;
–параметр частоты возникновения дефекта – А. Это – также экспертная оценка, проставляемая по 10-ти балльной шкале; наи-
278
высший балл проставляется, когда оценка частоты возникновения составляет 1/4 и выше;
–параметр вероятности не обнаружения дефекта – Е. Как и предыдущие параметры, он является 10-ти балльной экспертной оценкой; наивысший балл проставляется для «скрытых» дефектов, которые не могут быть выявлены до наступления последствий;
–параметр риска потребителя – RPZ. Это произведение трех перечисленных выше факторов, т. е. количественная оценка отказа
сточки зрения его значимости по последствиям, вероятности воз- никновения и вероятности обнаружения:
RPZ = В × А × Е |
(4) |
Для отказов (несоответствий, дефектов, пороков), имеющих |
|
несколько причин, определяют соответственно |
несколько RPZ |
[369]. Для RPZ должна быть заранее установлена критическая гра- ница, например, в пределах от 100 до 120. Если какие-то значения RPZ превышаютустановленноеграничноезначение, тоименнодля них следует вести доработку производственного процесса.
3. Действия после завершения работы FMEA-команды:
3.1. Результатыанализазаносятсявспециальнуютаблицу(табл. 2.8). Выявленные «узкие места» – компоненты объекта, для кото- рых RPZ будет больше 100...120, – подвергаются изменениям, то есть разрабатываются корректировочные мероприятия.
Таблица 2.8
Квалиметрические шкалы значимости потенциального отказа (В), вероятностивозникновениядефекта(А), вероятностиобнаружениядефекта(Е)
|
Фактор В |
|
Фактор А |
|
Фактор Е |
|
|
|
|
||
1 – очень низкая (поч- |
1 |
– очень низкая |
1 – почти наверняка де- |
||
ти нет проблем) |
|
|
фект будет обнаружен |
||
2 |
– низкая (проблемы |
2 |
– низкая |
2 – очень хорошее обна- |
|
решаются работником) |
|
|
ружение |
||
3 |
– не очень серьезная |
3 |
– не очень низкая |
3 |
– хорошее |
4 |
– ниже средней |
4 |
– ниже средней |
4 |
– умеренно хорошее |
5 |
– средняя |
5 |
– средняя |
5 |
– умеренное |
6 |
– выше средней |
6 |
– выше средней |
6 |
– слабое |
7 |
– довольно высокая |
7 |
– близка к высокой |
7 |
– очень слабое |
8 |
– высокая |
8 |
– высокая |
8 |
– плохое |
9 |
– очень высокая |
9 |
– очень высокая |
9 |
– очень плохое |
10 – катастрофическая |
10 – 100%-ная |
10 – почти невозможно |
|||
(опасность для людей) |
|
|
обнаружить |
279
Часторазработанныемероприятиязаносятсявпоследующуюгра- фу таблицы FMEA-анализа. Затем пересчитывается потенциальный рискRPZ послепроведениякорректировочныхмероприятий. Еслине удалось его снизить до приемлемых пределов (малого риска RPZ<40 илисреднегорискаRPZ<100), разрабатываютсядополнительныекор- ректировочныемероприятияиповторяютсяпредыдущиешаги.
3.2. Порезультатаманализадляразработанныхкорректировоч- ных мероприятий составляется план их внедрения.
Внастоящее время FMEA-анализ очень широко применяется
впромышленности Японии, США, активно внедряется в странах ЕС. Его использование позволяет резко сократить «детские болез- ни» при внедрении разработок в производство.
FMEA обеспечивает вклад в анализ такого рода, как анализ де- рева неисправностей – (Fault Tree Analysis, FТА) – анализ диаграм- мывсехвозможныхпоследствийнесрабатыванияилиавариисисте- мы. Наряду с применением по отношению к компонентам системы FMEA может использоваться и по отношению к ошибке человека; может применяться как для идентификации опасности, так и для оценкивероятности(еслитольковсистемеимеетместоограничен- ный уровень избыточности). Более подробно FMEA-анализ пред- ставлен в международном стандарте МЭК 60812 «Техника анализа надежности систем. Метод анализа вида и последствий отказа».
QFD методология («Дом качества»)
Рассмотренные выше «новые» инструменты менеджмента ка- чества лежат в основе новейшей процедуры преобразования требо- ваний потребителей сначала в параметры качества ожидаемой ими продукции, а затем в параметры качества процессов производства этой продукции. Такая процедура, разработанная и впервые при- мененная в Японии на верфи компании Mitsubishi Heavy Industries
в г. Кобэ, получила название «Развертывание функции качества»
(Quality Function Deployment — QFD). Из-за специфической формы матричной диаграммы, используемой в рамках процедуры QFD, ее часто называют «дом качества» (The Quality House) [216, 297, 410].
Идея, положенная в основу QFD, заключается в том, чтобы учитывать требования потребителя на всех стадиях производства изделий, для всех факторов, влияющих на качество. Это позволит повысить степень удовлетворенности потребителя и снизить затра- ты на проектирование и подготовку производства изделий.
Наглядным примером эффекта от применения QFD могут слу- жить результаты компании «Toyota Auto Body», которая наряду с
280