
- •ПРОИЗВОДСТВО КАБЕЛЕЙ И ПРОВОДОВ
- •ПРЕДИСЛОВИЕ
- •ОБЩИЕ СВЕДЕНИЯ О КАБЕЛЬНОМ ПРОИЗВОДСТВЕ
- •1.1. ОСНОВНЫЕ ТЕХНОЛОГИЧЕСКИЕ ПРОЦЕССЫ
- •1.2. КЛАССИФИКАЦИЯ КАБЕЛЬНОГО ОБОРУДОВАНИЯ
- •1.3. ОСНОВНЫЕ МЕХАНИЗМЫ КАБЕЛЬНЫХ МАШИН
- •1.4. ОТДАЮЩИЕ УСТРОЙСТВА
- •1.5. НАКОПИТЕЛИ
- •1.6. ТЯГОВЫЕ УСТРОЙСТВА
- •1.7. ИЗМЕРИТЕЛИ ДЛИНЫ
- •1.9. МЕХАНИЗМЫ РАСКЛАДКИ
- •1.10. МЕХАНИЗМЫ РЕГУЛИРОВАНИЯ СКОРОСТИ ПРИЕМНОГО УСТРОЙСТВА
- •1.11. ТЕХНОЛОГИЧЕСКАЯ ДОКУМЕНТАЦИЯ
- •КРУТИЛЬНЫЕ МАШИНЫ
- •2.1. ПРИНЦИП ДЕЙСТВИЯ КРУТИЛЬНЫХ МАШИН;
- •2.2. ТЕХНОЛОГИЧЕСКИЕ ПАРАМЕТРЫ ПРОЦЕССА СКРУТКИ
- •2.4. ОТКРУТКА ПРИ СКРУТКЕ
- •2.5. МАШИНЫ РАЗНОНАПРАВЛЕННОЙ СКРУТКИ
- •И НЕИЗОЛИРОВАННЫХ ПРОВОДОВ
- •3.1. СКРУТКА НЕИЗОЛИРОВАННЫХ ПРОВОДОВ ДЛЯ ЛИНИЙ ЭЛЕКТРОПЕРЕДАЧИ
- •3.4. СКРУТКА ГЕРМЕТИЗИРОВАННЫХ
- •тппгк
- •4.2. ЛЕНТО- и НИТЕОБМОТОЧНЫЕ МАШИНЫ
- •4.3.0БМ0ТКА БУМАЖНЫМИ ЛЕНТАМИ ЖИЛ СИЛОВЫХ КАБЕЛЕЙ НА НАПРЯЖЕНИЕ 1—35 кВ
- •4.4. ОСОБЕННОСТИ НАЛОЖЕНИЯ ИЗОЛЯЦИИ НА ЖИЛЫ МАСЛОНАПОЛНЕННЫХ КАБЕЛЕЙ
- •4.5. НАЛОЖЕНИЕ БУМАЖНОЙ ЛЕНТОЧНОЙ ИЗОЛЯЦИИ НА ЖИЛЫ КАБЕЛЕЙ СВЯЗИ
- •ИЗОЛЯЦИИ НА ЖИЛЫ КАБЕЛЕЙ СВЯЗИ
- •4.9. НАЛОЖЕНИЕ ВОЛОКНИСТОЙ ИЗОЛЯЦИИ НА ОБМОТОЧНЫЕ ПРОВОДА
- •5.1.3. Течение расплава полимера в дозирующей зоне экструдера
- •5.2. РАСЧЕТ ПРОЦЕССА ЭКСТРУЗИИ
- •5.2.1. Расчет количества полимера, поступающего в головку
- •5.2.2. Упрощенный расчет общей объемной производительности экструдера
- •5.3. УТОЧНЕННЫЕ МЕТОДЫ РАСЧЕТА ЭКСТРУЗИИ
- •5.4. ОСОБЕННОСТИ РАСЧЕТА ЭКСТРУДЕРОВ ДЛЯ ПЕРЕРАБОТКИ РЕЗИНОВЫХ СМЕСЕЙ
- •5.5. КЛАССИФИКАЦИЯ ЭКСТРУДЕРОВ
- •5.7. ФОРМУЮЩИЙ ИНСТРУМЕНТ И ТЕХНОЛОГИЧЕСКИЕ ПАРАМЕТРЫ ЭКСТРУЗИИ
- •НАЛОЖЕНИЕ ПЛАСТМАССОВОЙ И РЕЗИНОВОЙ ИЗОЛЯЦИИ МЕТОДОМ ЭКСТРУЗИИ
- •6.4. ОСОБЕННОСТИ НАЛОЖЕНИЯ СШИТОЙ ПОЛИЭТИЛЕНОВОЙ ИЗОЛЯЦИИ
- •>6.6. НАЛОЖЕНИЕ ПОРИСТОЙ ПОЛИЭТИЛЕНОВОЙ ИЗОЛЯЦИИ НА ЖИЛЫ КАБЕЛЕЙ СВЯЗИ
- •6.8. НАЛОЖЕНИЕ СПЛОШНОЙ ИЗОЛЯЦИИ ИЗ ФТОРОПЛАСТОВ
- •ЭМАЛИРОВАНИЕ
- •7.1. АГРЕГАТЫ ДЛЯ ПРОИЗВОДСТВА ЭМАЛИРОВАННЫХ ПРОВОДОВ
- •7.1.1. Агрегаты для производства проводов диаметром 0,015—0,09 мм
- •7.2. СПОСОБЫ И ТЕХНОЛОГИЯ ЭМАЛИРОВАНИЯ
- •ки толщиной
- •7.3. ЭМАЛИРОВАНИЕ ИЗ РАСПЛАВА СМОЛЫ
- •НЕТИПОВЫЕ СПОСОБЫ НАЛОЖЕНИЯ ИЗОЛЯЦИИ
- •8.1. ИЗОЛИРОВАНИЕ ЖИЛ КАБЕЛЕЙ СВЯЗИ ПОРИСТОЙ БУМАЖНОЙ МАССОЙ
- •8.2. ИЗГОТОВЛЕНИЕ КОАКСИАЛЬНЫХ ПАР С ШАЙБОВОЙ ИЗОЛЯЦИЕЙ
- •КАБЕЛЕЙ
- •9.3. СКРУТКА ГЕРМЕТИЗИРОВАННЫХ КАБЕЛЕЙ
- •9.4. СКРУТКА ЖИЛ КАБЕЛЕЙ СВЯЗИ В ПАРЫ И ЧЕТВЕРКИ
- •9.4.2. Скрутка жил кабелей дальней связи в четвёркй
- •9.5. ПОВЙВНАЯ СКРУТКА КАБЕЛЕЙ СВЯЗИ
- •9.6. ПУЧКОВАЯ СКРУТКА КАБЕЛЕЙ СВЯЗИ
- •ПРОЦЕССЫ СУШКИ И ПРОПИТКИ КАБЕЛЕЙ
- •10.1. СУШКА И ПРОПИТКА БУМАЖНОЙ ИЗОЛЯЦИИ СИЛОВЫХ КАБЕЛЕЙ
- •10.3. ПРИГОТОВЛЕНИЕ ПРОПИТОЧНЫХ СОСТАВОВ
- •НАЛОЖЕНИЕ МЕТАЛЛИЧЕСКИХ ОБОЛОЧЕК
- •11.1. СПОСОБЫ НАЛОЖЕНИЯ МЕТАЛЛИЧЕСКИХ ОБОЛОЧЕК
- •11.3. ТЕХНОЛОГИЧЕСКИЙ ПРОЦЕСС НАЛОЖЕНИЯ СВИНЦОВЫХ ОБОЛОЧЕК
- •11.7. ТЕХНОЛОГИЯ ПРЕССОВАНИЯ АЛЮМИНИЕВЫХ ОБОЛОЧЕК
- •11.8.2. Высокочастотная сварка оболочек
- •11.9. ГОФРИРОВАНИЕ ОБОЛОЧЕК
- •НАЛОЖЕНИЕ ОБОЛОЧЕК И ШЛАНГОВ ИЗ ПЛАСТМАСС И РЕЗИНЫ
- •12.1. НАЛОЖЕНИЕ ПОЛИЭТИЛЕНОВЫХ ОБОЛОЧЕК И ШЛАНГОВ НА ЭКСТРУЗИОННЫХ АГРЕГАТАХ
- •12.3. ОСОБЕННОСТИ НАЛОЖЕНИЯ АЛЮМОПОЛИЭТИЛЕНОВЫХ ОБОЛОЧЕК
- •НАЛОЖЕНИЕ ЭКРАНИРУЮЩИХ И ЗАЩИТНЫХ ОПЛЕТОК
- •13.1. ТЕХНОЛОГИЧЕСКИЕ ПАРАМЕТРЫ ОПЛЕТКИ
- •13.3. НАЛОЖЕНИЕ ПРОВОЛОЧНЫХ ЭКРАНОВ И ЗАЩИТНЫХ ОПЛЕТОК
- •13.4. НАЛОЖЕНИЕ ВОЛОКНИСТЫХ ЗАЩИТНЫХ ОПЛЕТОК
- •13.5. ПРОПИТКА ПРОВОДОВ
- •13.6. ЛАКИРОВКА ПРОВОДОВ
- •НАЛОЖЕНИЕ БРОНЕПОКРОВОВ
- •14.1. БРОНИРОВОЧНЫЕ МАШИНЫ
- •14.3. ТЕХНОЛОГИЯ НАЛОЖЕНИЯ ЗАЩИТНЫХ ПОКРОВОВ
- •14.4. НАЛОЖЕНИЕ ПРОФИЛЬНОЙ [ГИБКОЙ] БРОНИ
- •ВСПОМОГАТЕЛЬНЫЕ ПРОЦЕССЫ КАБЕЛЬНОГО ПРОИЗВОДСТВА
- •15.1. ПЕРЕМОТКА ПОЛУФАБРИКАТА, ЗАГОТОВКИ И ГОТОВЫХ КАБЕЛЕЙ И ПРОВОДОВ
- •15.2. РЕЗКА БУМАГИ И ПЛЕНОК НА ЛЕНТЫ
- •15.4. ИЗГОТОВЛЕНИЕ РЕЗИНОВЫХ СМЕСЕЙ
- •15.5. ПРЕДВАРИТЕЛЬНАЯ ПРОПИТКА МАТЕРИАЛОВ ЗАЩИТНЫХ ПОКРОВОВ
- •ОПЕРАЦИОННЫЙ КОНТРОЛЬ В ПРОИЗВОДСТВЕ КАБЕЛЕЙ И ПРОВОДОВ
- •16.2. ОПЕРАЦИОННЫЙ КОНТРОЛЬ
- •36.3. УПРАВЛЕНИЕ КАЧЕСТВОМ
- •17.1. ОСНОВЫ ТЕХНИКИ БЕЗОПАСНОСТИ И ПРОИЗВОДСТВЕННОЙ САНИТАРИИ
- •17.2. ОСНОВЫ ПРОТИВОПОЖАРНОЙ ТЕХНИКИ
- •ОСНОВЫ ПРОЕКТИРОВАНИЯ КАБЕЛЬНОГО ПРОИЗВОДСТВА
- •18.1. ОРГАНИЗАЦИЯ КАБЕЛЬНОГО ПРОИЗВОДСТВА — СТРУКТУРА ЗАВОДА И ЦЕХА
- •18.3. ПЛАНИРОВКА ЦЕХОВ И ОТДЕЛЕНИИ
- •18.4. ОПРЕДЕЛЕНИЕ СЕБЕСТОИМОСТИ ПРОДУКЦИИ И ТЕХНИКО-ЭКОНОМИЧЕСКИХ
- •СПИСОК ЛИТЕРАТУРЫ
Типовые технологические режимы тростки медной и медной луженой проволоки
Тип обо |
Диаметр |
про |
Часто га |
Число |
Средний |
Средиля |
Линейная |
вращения |
прово- |
диаметр |
масса про |
||||
рудования |
волоки, мм |
шпинделя, |
-лок |
катушки |
волоки на |
скорость, |
|
|
|
|
об/мин |
в»пря- |
после на |
катушке, |
м/мин |
|
|
|
|
“ди |
мотки, мм |
г |
|
ТН-100/4 |
0,12—0,13 |
1000 |
3—4 |
24 |
330 |
100±5 |
|
ТС-2 |
0,15-0,20 |
1200 |
3 - 6 |
34—50 |
330 |
1 0±5 |
|
0,20—0,30 |
500 |
3—5 |
55 |
1800 |
85+5 |
||
щеной проволоки |
и |
краем щеки катушки должно быть |
не менее |
3 мм. При обрыве или сходе одной проволоки обрывается вся прядь. После ее закрепления петлей катушка снимается с прием ного устройства.
15.4. ИЗГОТОВЛЕНИЕ РЕЗИНОВЫХ СМЕСЕЙ
Кабельные заводы, выпускающие кабели, провода и шнуры с резиновой изоляцией, имеют, как правило, собственные резино подготовительные цехи, в которых изготавливается резиновая смесь
нужной |
рецептуры. Как известно, резиновая смесь, предназначен |
ная для |
изоляции или оболочки кабелей и проводов — это много |
компонентный материал, состав которого сильно варьируется в за висимости от назначения. Различают резиновые смеси с высокими изоляционными или физико-механическими свойствами, нагревостойкие или холодостойкие, стойкие к различным агрессивным сре дам, жесткие или пластичные, с ускоренным временем вулканиза ции и т. п. Все это разнообразие свойств определяется видом и соотношением ингредиентов смеси, а также существенно зависит от способа их предварительной обработки, точной дозировки, пра вильной последовательности и качества омешения и последующей обработки полученной резиновой смеси.
Указанные операции осуществляются в резиноподготовитель ных цехах или участках кабельных заводов.
Технологический процесс изготовления резиновых смесей со стоит из следующих операций: подготовки материалов, транспорти ровании обработанных материалов к весам; дозировании материа лов; введении материалов в резиносмеситель; смешении и дополни тельной обработке резиновых смесей.
Подготовка каучуков заключается в распарке, резке, пласти кации и фильтрации.
Р а с п а р к а натурального и хлоропренового (наирита) каучу ков производится в стационарной камере с принудительной цирку ляцией горячего воздуха при 75—80°С. Время нагрева натураль ного каучука в зависимости от температуры, при которой он хра нился, находится в пределах от 8 до 36 ч: при температуре хране ния свыше 5°С — от 8 до 16 ч, при температуре хранения до
5°С — от |
16 до 36 ч. Время нагрева хлоропренового каучука 1,5— |
2 ч при |
температуре хранения до 5°С. |
Нагретый натуральный каучук р а з р е з а е т с я |
ножом |
с |
пнев |
матическим или гидравлическим приводом на куски |
массой |
не |
более |
15 кг. Нож должен обеспечивать усилие резания до 700— 1000 кН. Резка хлоропренового каучука производится механическим ножом гильотинного типа, а различные виды синтетических каучуков ре жутся на куски массой не более 15 кг.
П л а с т и к а ц и я |
натурального каучука производится |
в резино- |
|||||||
смесителе |
при 120— 140°С с добавлением |
каптакса |
(0,2 ч. |
на Ю0 ч. |
|||||
каучука) |
в |
течение 6— 10 |
мин или без |
каптакса |
при |
100— 120°С |
|||
в течение |
8— 12 |
мин. |
Дополнительная |
пластикация |
натурального |
||||
каучука |
производится |
на |
листовальных |
вальцах |
|
при |
50—70°С |
||
в течение 3—5 мин. |
|
|
|
|
|
|
|||
За счет воздействия повышенной температуры |
и разнообраз |
||||||||
ных механических |
деформаций (сдвига, сжатия, растяжения и др.), |
возникающих при обработке каучука в камере резиносмесителя или между валками, происходит частичная деструкция (разрыв длин ных полимерных молекул) каучука, сопровождающаяся уменьше нием его жесткости и соответственно увеличением пластичности.
После |
пластикации натуральный |
каучук |
подвергают |
ф и л ь |
|||||||||
т р а ц и и |
через |
три |
стальные сетки |
по |
ГОСТ |
4601-73 |
или |
||||||
ГОСТ |
12184-66 |
следующих |
номеров: две |
сетки |
№ |
09 |
или |
№ |
063 |
||||
и одну |
сетку № |
045 — для |
последующего |
применения |
в шланговых |
||||||||
смесях; одну сетку № 09 или № 063, одну сетку |
№ |
045 |
и |
одну |
|||||||||
сетку |
№ |
028 — для |
последующего |
применения |
в |
изоляционных |
|||||||
смесях. |
|
|
|
|
|
|
|
|
|
|
|
|
|
Допускается применение латунных сеток указанных номеров. Если каучук пластицировался с отделенными упаковочными листа ми, то он операции фильтрации не подвергается. Пластицированный натуральный каучук хранится в виде рулонов, опудриваемых мелом или тальковой пастой, на стеллажах или поддонах от 8 до 24 ч.
Подготовка порошкообразных материалов (мел, тальк, каолин) заключается в с у ш к е и п р о с е в е . Если сепарированный или химический мел к моменту пуска в производство имеет влажность свыше 0,5%, то он подвергается с у ш к е в струе подогретого воз духа в специальных сушилках аэрофонтанного типа. При относи тельно небольшой потребности в меле допускается применение ро торных или червячных сушилок непрерывного действия с электри ческим обогревом.
П р о с е в наполнителей (мел, тальк, каолин) осуществляется на воздушных сепарационных установках. Качество сепарации должно обеспечивать полное прохождение готового продукта через сетку № 016. Допускается просев на центробежных сеялках через капроновую ткань № 38 по ОСТ 17-46-71 или латунную сетку № 016 по ГОСТ 3584-73. Просев порошкообразных материалов, приме няемых в малых количествах и поступающих в негран.улнрованном виде, производится на сеялках щеточного типа Через капроновую ткань № 38. Допускается просев через латунные сетки следующих
материалов: серы— № |
028; ускорителей и |
противостарителей— |
|||||
№ |
018; |
красителей — № 016. |
|
|
|
|
|
|
П о д г о т о в к а м я г ч и т е л е й |
(парафин, |
мягчитель ПП |
и |
|||
другие |
воскоподобные |
материалы) |
заключается |
в расплавлении |
|||
в |
камерах для разогрева твердых мягчителей |
с электрическим, |
па |
ровым или водяным обогревом и фильтрации через стальную или латунную сетку № 016 при температуре расплава 80—90°С. Жидкие
мягчители И |
пластификаторы фильтруются через такую же сетку |
без предварительного нагрева. |
|
КанифоЛЬ |
и другие смолоподобные материалы подвергаются |
дроблению в молотковой дробилке и грубому просеву через сталь ную или латунную сетку № 25 в центробежной сеялке. Если кани
фоль, смола СФ-010А, диафен ФП поступают в |
виде чешуек, то |
они операциям дробления и просева не подвергаются. |
|
Стеариновая кислота и специальные нефтяные |
битумы предва |
рительной подготовке не подвергаются. Распаковка этих материалов производится непосредственно перед операцией взвешивания.
Каучуки всех типов подаются к весам внутрицеховым транс портом в контейнерах. Мел, тальк, каолин, графит должны транс портироваться к надвесным бункерам при помощи вакуумной пнев мосистемы. На трассах небольшой длины возможно применение ковшовых элеваторов и червячных транспортеров с последователь ным расположением секций. Для каждого материала применяют отдельную линию. Расплавленные и жидкие мягчители и пластифи каторы подаются в бачки, расположенные над весами, по трубо проводам. Все остальные порошкообразные материалы, а также измельченные смолы транспортируются к весам в контейнерах при помощи электропогрузчика. Стеариновая кислота и нефтяные би
тумы подаются |
к весам в упаковке |
предприятия-изготовителя. |
В з в е ш и в |
а н и е каучуков всех |
типов осуществляется центра |
лизованно при помощи полуавтоматических весов с последующей доставкой готовых навесок к резиносмесителям в контейнерах. Д о пускается ручная развеска каучуков непосредственно у резиносмесителя на полуавтоматических весах. Взвешивание порошкообраз ных наполнителей, технического углерода (сажи) различных марок, графита, активаторов, а также жидких и расплавленных мягчите лей производится автоматическими весами, установленными над каждым резиносмесителем. Для технического углерода (сажи) пре дусматриваются отдельные весы, которые используются также для взвешивания графита. Вулканизующие материалы, ускорители, смолы и другие материалы, не подлежащие автоматическому дози рованию, развешиваются вручную на безгиревых весах циферблат ного типа или настольных весах.
С м е ш е н и е каучуков и |
остальных ингредиентов |
резиновых |
смесей производится в закрытых резиносмесителях |
(рис. 15.8), |
|
в которых под давлением при |
определенной температуре компонен |
ты тщательно перемешиваются с целью получения однородной смеси. Это смешение осуществляется роторами неправильной формы и вращающимися с различными частотами, в результате чего вну три резиносмесителя создаются разнообразные скорости потока перемешиваемой смеси. Это способствует лучшему перемешиванию компонентов, разрушению отдельных образующихся комков, свое образному втиранию одного слоя смеси в другой.
На качество полученной смеси существенное влияние оказы вают последовательность и способы введения отдельных компонен тов в камеру смесителя. Каучук и все материалы, поступающие с автоматических весов, загружаются в резиносмеситель гермети зированным ленточным транспортером через загрузочную воронку.
Порошкообразные наполнители вводятся через отверстие в зад ней стенке загрузочной воронки, если резиносмеситель специализи
рован для смешения только изоляционных или только шланговых смесей. Если резиносмеситель используется для изготовления сме сей обоих типов, то порошкообразные наполнители должны пода ваться через загрузочную воронку герметизированным ленточным транспортером.
Технический углерод (сажа) разных марок и графит загру жаются через отверстие, расположенное в задней стенке загрузоч ной воронки. Расплавленные и жидкие компоненты смеси вводят непосредственно в камеру смесителя при помощи инжектора или насоса высокого давления.
Рис. 15.8. Схема камеры резиносмесителя.
Резиновые смеси, поступающие на вторую стадию смешения, загружаются в резиносмеситель ленточным транспортером. Допу скается ручная загрузка материлов в резиносмеситель.
Смешение и д о п о л н и т е л ь н а я о б р а б о т к а кабельных резиновых смесей производятся по одному из двух способов: сме щение в резиносмесителе, обработка на вальцах, фильтрование (кроме смесей на основе хлоропренового каучука), обработка на вальцах, охлаждение, введение вулканизующих материалов в ре зиносмесителе, обработка на вальцах, охлаждение или смешение в резиносмесителе, обработка на вальцах, фильтрование (кроме сме сей на основе хлоропренового каучука), обработка на вальцах, вве
дение |
вулканизующих материалов на вальцах, каландрование. |
^акие |
операции как смешение, обработка на вальцах (листова- |
цие), фильтрование, дополнительная обработка на вторых вальцах, производятся по одним и тем же режимам для обоих упомянутых способов.
Для смешения применяются резиносмесители типов РС250-30, рС250-20 с объемом рабочей камеры 250 дм3 и частотой вращения роторов соответственно 30 и 20 об/мин. Фрикция (соотношение ско ростей роторов одного смесителя) в этих смесителях 1 : 1,18. При меняются также резиносмесители типов РС-2 и PC № 11. В смеси телях типов РС250-30 и РС250-20 смешение осуществляется при повышенном давлении, в смесителях РС-2 и PC № 11 — при нор мальном давлении.
В качестве примера приведем режимы первой стадии смешения: изоляционные смеси марок ТСШ-ЗОА, ТСШ-35А, ПИ-35 загружают ся в резиносмеситель РС250-30 массой 250 кг в следующей после
довательности: каучуки, мелкие навески, мел, мягчитель ПП или парафин; закрывается верхний затвор и происходит перемешивание в течение 5,5 мин; затем смесь выгружается и переходят к следую щему замесу; начальная температура камеры 80—90°С, температура выгружаемой смеси 110— 120°С, общее время^ смешения, включая выгрузку, 6,5 мин. Изоляционные смеси марок ТСШ-ЗОА, ТСШ-35А загружаются в резиносмеситель PC-2 (PC N° 11) массой 250 кг в следующей последовательности: каучуки, мелкие навески, 50% мела, 50% мягчителя ПП или парафина, после чего закрывается верхний затвор и происходит перемешивание смеси в течение 5 мин при начальной температуре камеры 80—90°С; затем загружаются оставшиеся 50% мела и 50% мягчителя ПП или парафина и проис ходит перемешивание еще в течение 4 мин, после чего смесь выгру жается и осуществляется переход к следующему замесу; общее время смешения, включая выгрузку, 10 мин, температура выгружае мой смеси 100— 110°С.
Шланговая резиновая смесь марки ШН-40 загружается в рези носмеситель РС250-30 массой 230 кг в следующей последователь ности: полихлоропреновый каучук (наирит), мелкие навески, као лин, мел, технический углерод (сажа), дибутилфталат, парафин; закрывается верхний затвор и смесь перемешивается в течение 8 мин при начальной температуре камеры смесителя 70—80°С; за тем происходит выгрузка смеси; общее время смешения, включая выгрузку смеси, 9 мин, температура выгружаемой смеси 100— 110°С. При смешении, например, этой же смеси ШН-40 в смесителе РС-2 или PC № 11, введение сажи происходит в две стадии; сна чала 25%, затем 75% и парафин. Общее время смешения увели чивается до 11 мин. Выгруженная из резиносмесителя наиритовая смесь проходит операцию листования на листовальных вальцах в течение 3—4 мин при температуре валков 40—50°С, остальных резин — 60—70°С.
В а л ь ц ы (рис. 15.9) представляют собой устройство, в кото ром два валка, оси которых расположены в горизонтальной плоско сти, вращаются навстречу друг другу, причем скорости их не сколько отличаются. Вальцы используются главным образом для листования резиновых смесей, а также могут использоваться для
нагрева смеси, смешения различных частей смеси, пластикации |
сме |
|||
си и т. д. Например, |
для нагрева резиновых |
смесей |
применяются |
|
660 |
с двумя валками, длина |
рабочей |
части |
кото |
вальцы ЦД2130 ggQ |
рых 2130 мм, диаметр рабочей части валков 660 мм, рабочая ско
рость |
переднего |
валка |
28,0 м/мин, заднего 34,2 м/мин, фрикция |
между |
валками 1 |
1,22, |
производительность 140 л/цикл. |
С листовальных вальцов резиновые смеси срезаются в виде |
|||
непрерывной ленты и |
ленточным транспортером подаются для |
фильтрования в фильтр-прессы. Такой операции обычно подвергает
ся |
большинство |
резиновых |
смесей. |
Исключение |
составляют смеси |
на |
основе хлоропренового каучука. |
|
|
||
|
Ф и л ь т р - п р е с с (рис. |
15.10) |
представляет |
собой червячный |
|
пр^сс, в головке |
которого |
размещены сетки |
для фильтрования |
резиновой смеси. Эта операция имеет целью устранение возможных неоднородностей (комков), образовавшихся в процессе смешения и ухудшающих однородность, а следовательно, и физико-механиче ские и электроизоляционные характеристики смесей. Применяются
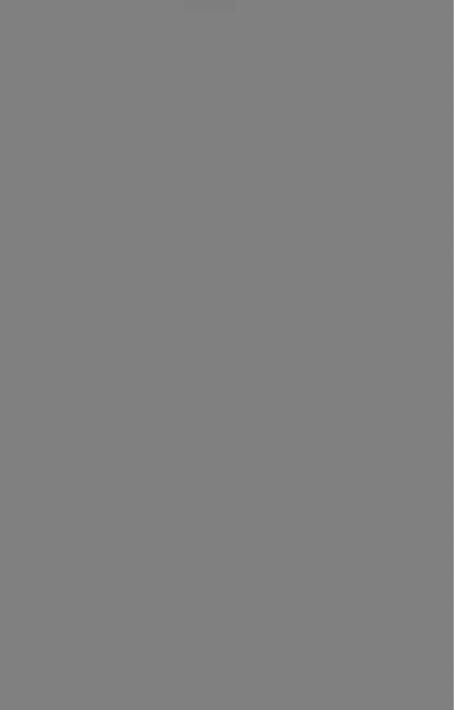
фильтр-прессы с червяками диаметром 380/450 и 300/380 мм. Ре жимы фильтрования основных изоляционных и шланговых смесей приведены в табл. 15.3.
Выходящая из фильтр-пресса резиновая смесь передается лен точным транспортером на листовальные вальцы, с которых сразу
ж е срезается |
в виде |
непрерывной ленты |
толщиной б— 10 |
мм |
и ши |
|
риной около |
600 мм. |
|
|
|
|
|
|
|
|
|
Т а б л и ц а |
15.3 |
|
Режимы фильтрования резиновых смесей |
|
|
|
|||
|
Фильтрующие |
Температура, °С |
|
|
||
|
сег^и |
|
|
|
|
|
|
|
в момент пуска |
а |
JJdUUIDI |
||
Марка смеси |
|
фильтр-пресса |
|
|
|
|
Коли |
|
|
|
|
|
|
|
Номер |
|
|
|
|
|
|
чество |
Корпус |
Головка |
Корпус |
||
|
|
Головка |
ТСШ-ЗОА |
1 |
2 ) |
|
ТСШ-35А |
1 |
09 I |
|
|
1 |
045 |
\ |
ШБМ-40А |
1 |
028 |
} |
1 |
2 |
|
|
ШБТМ-40А |
2 |
09 |
|
ШТМС-45, |
1 |
045 |
|
ШВП-50 |
|
|
|
70—80 |
40—50 |
70—80 |
30—35 |
80—90 |
50—60 |
70—80 |
30—35 |
80—90 |
50—60 |
70—80 |
30—35 |
80—90 |
50—60 |
70—80 |
30—35 |
В соответствии с порядком первого способа смешения и до полнительной обработки полученная лента поступает для охлаж дения в охлаждающую установку водой при 8—20°С и затем прфходит через бак с мыльно-стеариновой эмульсией, в состав которой входит 4% хозяйственного мыла, 2% технической стеариновой кис лоты и 94% воды. После охлаждающей установки осуществляется приемка резиновой смеси маятниковым укладчиком или устройством для резки и укладки в контейнеры. Контейнеры или поддоны с ре
зиновой смесью транспортируются |
с помощью |
электропогрузчика |
на склад. |
|
|
Резиновые смеси, содержащие |
натуральный |
каучук, хранятся |
на складе до передачи на вторую стадию смешения, во время ко» торой в смесь вводят вулканизующие материалы. В соответствии с режимом второй стадии смешения в смесителе РС250-20 происхо дит загрузка 250 кг смеси в камеру смесителя с начальной темпе ратурой 60—70°С, закрытие верхнего затвора и перемешивание в течение 1 мин, затем вводится вулканизующее вещество и в тече ние 1 мин происходит смешение. Общее время, включая выгрузку смеси, 3 мин, температура выгружаемой смеси 80—90°С. В смеси теле PC-2 (PC № 11) общее время смешения составляет 4 мин.
Выгруженная готовая наиритовая смесь последовательно обра батывается на двух листовальных вальцах в течение 2 мин при температуре валков 40—50°, а остальные смеси при 50 60°С. Подача смеси от резиносмесителя на первые и затем вторые валь цы осуществляется с помош.ью ленточных транспортеров.
Готовая смесь затем охлаждается водой при 8—20°С в охлаж^ дающей установке, а затем в виде лент, свернутых в рулон, или уложенная в виде пластин в контейнер подается на склад для хранения резиновых смесей.
По второму способу смешения и дополнительной обработки резиновая смесь после смешения в резиносмесителе, обработки (лис товая) на вальцах, фильтрования и второй обработки (листования) на вальцах подается на третьи (питательные) вальцы, предназна ченные для введения вулканизующих материалов и питания ка
ландра.
Режим введения вулканизующих компонентов на вальцах в этом случае следующий: загрузка смеси (2 мин), введение вулканиза-
Рис. 15.11. |
Схема каландра. |
|
|
/ — вальцы; |
2 — промежуточный |
транспортер; 3 — каландр; 4 — направляющий |
|
валик; 5 — охлаждающий барабан; |
6 — основной транспортер; 7 — опудриваю- |
||
щее устройство; 8 — устройство |
для |
резки полотна; 9 — гребенка; 10 — прием |
|
ное устройство. |
|
|
торов (2—3 мин), срезание смеси с валков (1 мин). Температура валков 35—40°С при разогреве смесей на основе хлоропренового каучука и 60—70°С — остальных резиновых смесей.
С третьих (питательных) вальцов смеси срезаются сдвоенными ножами и в виде полотна поступают по транспортеру в каландр (рис. 15.11).
К а л а н д р о в а н и е резиновых смесей производится с целью получения резинового полотна или ленты заданной толщины.-Темпе ратура валков каландра при каландровании резиновых смесей марок ТСШ-35, ТСШ-ЗОА, ПИ-35, ШВП-50, ШВТМ-40А, ШБМ-40А, ШТМС-45 составляет: выносного и верхнего 60—70°С, среднего 70—80°С, нижнего 15—20°С. При каландровании смесей марок ШН-40 и ШН-50 (на основе хлоропренового каучука) температура выносного и верхнего валков равна 40—50°С, среднего 45—55°С, нижнего 15—30°С. Каландрованное полотно охлаждается пропуска нием через одну-две полосы барабана с водяным охлаждением. Температура воды не должна превышать 12°С, давление 0,3— 0,4 МПа.
После охлаждения полотно срезается в виде лент определенной толщины и ширины. Производится также одностороннее опудривание каландрованного полотна мелом или тальком, излишки которых для равномерного распределения пудровочного материала снимают ся с помощью круглых вращающихся щеток.
Каландрованные смеси массой не более 250 кг принимаются в контейнеры и подаются на склад для хранения резиновых смесей или к экструдерам для их питания резиновой смесью.