
- •ПРОИЗВОДСТВО КАБЕЛЕЙ И ПРОВОДОВ
- •ПРЕДИСЛОВИЕ
- •ОБЩИЕ СВЕДЕНИЯ О КАБЕЛЬНОМ ПРОИЗВОДСТВЕ
- •1.1. ОСНОВНЫЕ ТЕХНОЛОГИЧЕСКИЕ ПРОЦЕССЫ
- •1.2. КЛАССИФИКАЦИЯ КАБЕЛЬНОГО ОБОРУДОВАНИЯ
- •1.3. ОСНОВНЫЕ МЕХАНИЗМЫ КАБЕЛЬНЫХ МАШИН
- •1.4. ОТДАЮЩИЕ УСТРОЙСТВА
- •1.5. НАКОПИТЕЛИ
- •1.6. ТЯГОВЫЕ УСТРОЙСТВА
- •1.7. ИЗМЕРИТЕЛИ ДЛИНЫ
- •1.9. МЕХАНИЗМЫ РАСКЛАДКИ
- •1.10. МЕХАНИЗМЫ РЕГУЛИРОВАНИЯ СКОРОСТИ ПРИЕМНОГО УСТРОЙСТВА
- •1.11. ТЕХНОЛОГИЧЕСКАЯ ДОКУМЕНТАЦИЯ
- •КРУТИЛЬНЫЕ МАШИНЫ
- •2.1. ПРИНЦИП ДЕЙСТВИЯ КРУТИЛЬНЫХ МАШИН;
- •2.2. ТЕХНОЛОГИЧЕСКИЕ ПАРАМЕТРЫ ПРОЦЕССА СКРУТКИ
- •2.4. ОТКРУТКА ПРИ СКРУТКЕ
- •2.5. МАШИНЫ РАЗНОНАПРАВЛЕННОЙ СКРУТКИ
- •И НЕИЗОЛИРОВАННЫХ ПРОВОДОВ
- •3.1. СКРУТКА НЕИЗОЛИРОВАННЫХ ПРОВОДОВ ДЛЯ ЛИНИЙ ЭЛЕКТРОПЕРЕДАЧИ
- •3.4. СКРУТКА ГЕРМЕТИЗИРОВАННЫХ
- •тппгк
- •4.2. ЛЕНТО- и НИТЕОБМОТОЧНЫЕ МАШИНЫ
- •4.3.0БМ0ТКА БУМАЖНЫМИ ЛЕНТАМИ ЖИЛ СИЛОВЫХ КАБЕЛЕЙ НА НАПРЯЖЕНИЕ 1—35 кВ
- •4.4. ОСОБЕННОСТИ НАЛОЖЕНИЯ ИЗОЛЯЦИИ НА ЖИЛЫ МАСЛОНАПОЛНЕННЫХ КАБЕЛЕЙ
- •4.5. НАЛОЖЕНИЕ БУМАЖНОЙ ЛЕНТОЧНОЙ ИЗОЛЯЦИИ НА ЖИЛЫ КАБЕЛЕЙ СВЯЗИ
- •ИЗОЛЯЦИИ НА ЖИЛЫ КАБЕЛЕЙ СВЯЗИ
- •4.9. НАЛОЖЕНИЕ ВОЛОКНИСТОЙ ИЗОЛЯЦИИ НА ОБМОТОЧНЫЕ ПРОВОДА
- •5.1.3. Течение расплава полимера в дозирующей зоне экструдера
- •5.2. РАСЧЕТ ПРОЦЕССА ЭКСТРУЗИИ
- •5.2.1. Расчет количества полимера, поступающего в головку
- •5.2.2. Упрощенный расчет общей объемной производительности экструдера
- •5.3. УТОЧНЕННЫЕ МЕТОДЫ РАСЧЕТА ЭКСТРУЗИИ
- •5.4. ОСОБЕННОСТИ РАСЧЕТА ЭКСТРУДЕРОВ ДЛЯ ПЕРЕРАБОТКИ РЕЗИНОВЫХ СМЕСЕЙ
- •5.5. КЛАССИФИКАЦИЯ ЭКСТРУДЕРОВ
- •5.7. ФОРМУЮЩИЙ ИНСТРУМЕНТ И ТЕХНОЛОГИЧЕСКИЕ ПАРАМЕТРЫ ЭКСТРУЗИИ
- •НАЛОЖЕНИЕ ПЛАСТМАССОВОЙ И РЕЗИНОВОЙ ИЗОЛЯЦИИ МЕТОДОМ ЭКСТРУЗИИ
- •6.4. ОСОБЕННОСТИ НАЛОЖЕНИЯ СШИТОЙ ПОЛИЭТИЛЕНОВОЙ ИЗОЛЯЦИИ
- •>6.6. НАЛОЖЕНИЕ ПОРИСТОЙ ПОЛИЭТИЛЕНОВОЙ ИЗОЛЯЦИИ НА ЖИЛЫ КАБЕЛЕЙ СВЯЗИ
- •6.8. НАЛОЖЕНИЕ СПЛОШНОЙ ИЗОЛЯЦИИ ИЗ ФТОРОПЛАСТОВ
- •ЭМАЛИРОВАНИЕ
- •7.1. АГРЕГАТЫ ДЛЯ ПРОИЗВОДСТВА ЭМАЛИРОВАННЫХ ПРОВОДОВ
- •7.1.1. Агрегаты для производства проводов диаметром 0,015—0,09 мм
- •7.2. СПОСОБЫ И ТЕХНОЛОГИЯ ЭМАЛИРОВАНИЯ
- •ки толщиной
- •7.3. ЭМАЛИРОВАНИЕ ИЗ РАСПЛАВА СМОЛЫ
- •НЕТИПОВЫЕ СПОСОБЫ НАЛОЖЕНИЯ ИЗОЛЯЦИИ
- •8.1. ИЗОЛИРОВАНИЕ ЖИЛ КАБЕЛЕЙ СВЯЗИ ПОРИСТОЙ БУМАЖНОЙ МАССОЙ
- •8.2. ИЗГОТОВЛЕНИЕ КОАКСИАЛЬНЫХ ПАР С ШАЙБОВОЙ ИЗОЛЯЦИЕЙ
- •КАБЕЛЕЙ
- •9.3. СКРУТКА ГЕРМЕТИЗИРОВАННЫХ КАБЕЛЕЙ
- •9.4. СКРУТКА ЖИЛ КАБЕЛЕЙ СВЯЗИ В ПАРЫ И ЧЕТВЕРКИ
- •9.4.2. Скрутка жил кабелей дальней связи в четвёркй
- •9.5. ПОВЙВНАЯ СКРУТКА КАБЕЛЕЙ СВЯЗИ
- •9.6. ПУЧКОВАЯ СКРУТКА КАБЕЛЕЙ СВЯЗИ
- •ПРОЦЕССЫ СУШКИ И ПРОПИТКИ КАБЕЛЕЙ
- •10.1. СУШКА И ПРОПИТКА БУМАЖНОЙ ИЗОЛЯЦИИ СИЛОВЫХ КАБЕЛЕЙ
- •10.3. ПРИГОТОВЛЕНИЕ ПРОПИТОЧНЫХ СОСТАВОВ
- •НАЛОЖЕНИЕ МЕТАЛЛИЧЕСКИХ ОБОЛОЧЕК
- •11.1. СПОСОБЫ НАЛОЖЕНИЯ МЕТАЛЛИЧЕСКИХ ОБОЛОЧЕК
- •11.3. ТЕХНОЛОГИЧЕСКИЙ ПРОЦЕСС НАЛОЖЕНИЯ СВИНЦОВЫХ ОБОЛОЧЕК
- •11.7. ТЕХНОЛОГИЯ ПРЕССОВАНИЯ АЛЮМИНИЕВЫХ ОБОЛОЧЕК
- •11.8.2. Высокочастотная сварка оболочек
- •11.9. ГОФРИРОВАНИЕ ОБОЛОЧЕК
- •НАЛОЖЕНИЕ ОБОЛОЧЕК И ШЛАНГОВ ИЗ ПЛАСТМАСС И РЕЗИНЫ
- •12.1. НАЛОЖЕНИЕ ПОЛИЭТИЛЕНОВЫХ ОБОЛОЧЕК И ШЛАНГОВ НА ЭКСТРУЗИОННЫХ АГРЕГАТАХ
- •12.3. ОСОБЕННОСТИ НАЛОЖЕНИЯ АЛЮМОПОЛИЭТИЛЕНОВЫХ ОБОЛОЧЕК
- •НАЛОЖЕНИЕ ЭКРАНИРУЮЩИХ И ЗАЩИТНЫХ ОПЛЕТОК
- •13.1. ТЕХНОЛОГИЧЕСКИЕ ПАРАМЕТРЫ ОПЛЕТКИ
- •13.3. НАЛОЖЕНИЕ ПРОВОЛОЧНЫХ ЭКРАНОВ И ЗАЩИТНЫХ ОПЛЕТОК
- •13.4. НАЛОЖЕНИЕ ВОЛОКНИСТЫХ ЗАЩИТНЫХ ОПЛЕТОК
- •13.5. ПРОПИТКА ПРОВОДОВ
- •13.6. ЛАКИРОВКА ПРОВОДОВ
- •НАЛОЖЕНИЕ БРОНЕПОКРОВОВ
- •14.1. БРОНИРОВОЧНЫЕ МАШИНЫ
- •14.3. ТЕХНОЛОГИЯ НАЛОЖЕНИЯ ЗАЩИТНЫХ ПОКРОВОВ
- •14.4. НАЛОЖЕНИЕ ПРОФИЛЬНОЙ [ГИБКОЙ] БРОНИ
- •ВСПОМОГАТЕЛЬНЫЕ ПРОЦЕССЫ КАБЕЛЬНОГО ПРОИЗВОДСТВА
- •15.1. ПЕРЕМОТКА ПОЛУФАБРИКАТА, ЗАГОТОВКИ И ГОТОВЫХ КАБЕЛЕЙ И ПРОВОДОВ
- •15.2. РЕЗКА БУМАГИ И ПЛЕНОК НА ЛЕНТЫ
- •15.4. ИЗГОТОВЛЕНИЕ РЕЗИНОВЫХ СМЕСЕЙ
- •15.5. ПРЕДВАРИТЕЛЬНАЯ ПРОПИТКА МАТЕРИАЛОВ ЗАЩИТНЫХ ПОКРОВОВ
- •ОПЕРАЦИОННЫЙ КОНТРОЛЬ В ПРОИЗВОДСТВЕ КАБЕЛЕЙ И ПРОВОДОВ
- •16.2. ОПЕРАЦИОННЫЙ КОНТРОЛЬ
- •36.3. УПРАВЛЕНИЕ КАЧЕСТВОМ
- •17.1. ОСНОВЫ ТЕХНИКИ БЕЗОПАСНОСТИ И ПРОИЗВОДСТВЕННОЙ САНИТАРИИ
- •17.2. ОСНОВЫ ПРОТИВОПОЖАРНОЙ ТЕХНИКИ
- •ОСНОВЫ ПРОЕКТИРОВАНИЯ КАБЕЛЬНОГО ПРОИЗВОДСТВА
- •18.1. ОРГАНИЗАЦИЯ КАБЕЛЬНОГО ПРОИЗВОДСТВА — СТРУКТУРА ЗАВОДА И ЦЕХА
- •18.3. ПЛАНИРОВКА ЦЕХОВ И ОТДЕЛЕНИИ
- •18.4. ОПРЕДЕЛЕНИЕ СЕБЕСТОИМОСТИ ПРОДУКЦИИ И ТЕХНИКО-ЭКОНОМИЧЕСКИХ
- •СПИСОК ЛИТЕРАТУРЫ
5.4. ОСОБЕННОСТИ РАСЧЕТА ЭКСТРУДЕРОВ ДЛЯ ПЕРЕРАБОТКИ РЕЗИНОВЫХ СМЕСЕЙ
Экструдеры для наложения резиновой изоляции или оболочки при внешнем сходстве с экструдерами для пере работки термопластичных пластмасс имеют ряд сущест венных особенностей. Эти особенности отличают как кон струкцию элементов экструдера и режимы работы, так и методы расчета их производительности.
Материалом для переработки в этих экструдерах являются невулканизованные резины, представляющие собой сложные многокомпонентные смеси различных ви дов каучука с другими ингредиентами.
Каучуки относятся к так называемым эластомерам, т. е. таким веществам, у которых преобладают высоко эластические деформации, характеризуемые определен ными временами релаксации, т. е. восстановления преж него состояния тела (например, размеров) после снятия деформирующих усилий. Высокоэластические деформа ции определяют и соответствующее состояние вещества. Это состояние присуще только высокомолекулярным со единениям (полимерам) и является промежуточным между стеклообразным фазовым состоянием полимера и вязкотекучим состоянием. Соответственно первое харак теризуется упругими деформациями, а второе — пласти ческими (необратимыми) деформациями. Пребывание полимера в том или ином агрегатном состоянии зависит от ряда факторов, главными из которых являются его химическое строение и температура.
Как упоминалось выше, для переработки в экструде рах полимер должен быть переведен в вязкотекучее со стояние. В обычных условиях каучуки находятся в вы сокоэластическом состоянии. Для их переработки и при дания конечному продукту (резиновой смеси) ряда заданных свойств, каучуки смешивают с такими компо нентами, как мягчители (пластификаторы), наполнители и др. Введение пластификаторов вызывает увеличение пластичности смеси, т. е. приближает ее к вязкотекучему состоянию. Этому способствует также пластикация каучуков (см. § 15.4), при которой за счет действия ме ханических (срезающих) деформаций и повышенной тем пературы происходят процессы, приводящие к деструк ции (разрыву) длинных молекул полимеров, сопровож дающейся увеличением пластичности материала.
Следует иметь в виду, что температура в цилинДрё и головке экструдера для переработки резиновых смесей
существенно нЦже, чем в экструдерах для переработки пластмасс. ^ Во избежание возможности вулканизации этих смесей (QM. § 6.9) внутри экструдера температур для различных типов каучуков не превышает 50—90°С.
Температура резиновой смеси, поступающей в загру зочное отверстие экструдера, для различной рецептуры колеблется 0 Пределах от 20 до 40—70°С (в зависимости от отсутствия Яли наличия предварительного подогрева).
Важно отмстить, что для переработки резиновых сме сей применяются более короткие червяки. Если их длина колеблется обычно в пределах (4—12)Д то червяки для переработки Пластмасс имеют длину (15—30) Д причем оптимальной считается длина около 24D.
Таким образом, можно сказать, что резиновая смесь, характеризующаяся по сравнению с пластмассами мень шей пластичностью и большими эластическими деформа циями, перерабатывается при сравнительно низких тем пературах И с помощью относительно коротких червяков экструдеров. Все это позволяет считать, что для объясне ния механизма перемещения резиновой смеси в цилиндре экструдера подходят положения, изложенные при рас смотрении процессов, происходящих в загрузочной зоне экструдера для переработки пластмасс. Напомним, что в основе указанных методов лежит с определенным при ближением так называемая механическая «модель винта
игайки» (см. рис. 5.2).
Сучетом изложенного производительность экструде
ра при переработке резиновых смесей определяется коли чеством смеси, заполняющей объем нарезки червяка на длине одного шага, количеством нарезок червяка, часто той вращения червяка и плотностью смеси.
Если нарезка однозаходная, то за один оборот червя ка при условии полного заполнения всей нарезки смесью в головку поступит объем смеси V, равный объему витка
нарезки |
на |
длине 1Ср одного |
шага t. В соответствии |
|
с рис. 5.12 и 5.13 имеем: |
|
|
||
V = |
Ш ср = б/гаДр/cos <р= |
Ыт(D -f- It)/cos <j>— |
|
|
- |
—{ |
e) C0SJ ^ ' (D + h] = T . ( B + h)h{t- e) . |
(5.37) |
При частоте вращения червяка п, об/с, и геометриче ских размерах, измеряемых в метрах, объем материала
<5i, м3/с, подаваемый в головку в сеКунДу при числе за ходов червяка i, равен:
Qi^=n(D+h)h(t—e)in. (5.38)
Если плотность смеси равна у, кг/м3, то производи тельность, кг/с,
Q=n(D-\~h)h(t-e)iyn. (5.39)
Последнее выражение определяет максимально воз можную .производительность червяка экструдера. Б дей ствительности реальная производительность экструдера будет существенно меньше. Это обусловлено такими факторами, как наличие противодавления, неполное за полнение нарезки червяка смесью, и, наконец, тем фак том, что имеют место окружные и осевые смещения отдельных участков в смеси, заполняющей объем нарез ки червяка, вызванные силами Р' и Р" (см. рис. 5.5). Поэтому нельзя считать, что за один оборот червяка выдавливается полностью объем витка на длине одного шага, как это было бы в идеальном случае процесса, описываемого моделью, перемещающейся по винту гай ки. Указанные факторы, снижающие производительность экструдера, можно учесть некоторым коэффициентом а, фактически имеющим смысл КПД экструдера
Q=an(D+h)h(t—e)iyn. (5.40)
Значение а может колебаться довольно значительно для разных случаев и лежать в пределах 0,1—0,3.
5.5. КЛАССИФИКАЦИЯ ЭКСТРУДЕРОВ
Экструдеры для переработки пластмасс и резиновых смесей имеют общую принципиальную конструкцию, изо браженную на рис. 5.1. Однако в зависимости от вида перерабатываемого материала, особенностей кабелей и проводов, которые изготовляются в экструдере, и других факторов конструктивное выполнение отдельных его эле ментов может быть различным.
В зависимости от взаимного положения центральных осей червяка и токопроводящей жилы или заготовки под оболочку, проходящих через головку, различают экстру
деры п р я м о т о ч н ы е , с к о с о у г о л ь н о й |
и п р я м о |
у г о л ь н о й г о л о в к а м и (рис.‘5.20). |
В кабельной |
промышленности наиболее широко применяются прямо-
216
угольные головки (рис. 5.20,а), которые весьма удобны в эксплуатации, легко выполняются откидными, что облегчает смену формующего инструмента, фильтрую щих сеток и решеток, чистку червяка и головки.
Имеет применение |
также косоугольная |
головка |
(рис. 5.20,6). Ее ось |
расположена под углом |
40—60° |
к оси червяка, что выравнивает путь расплава полимера, поступающего из цилиндра экструдера в зону формую щего инструмента. В этом ее некоторое преимущество
Рис. 5.20. Упрощенные схемы экструдеров с прямоугольной (а), ко соугольной (б) и прямоточной (в) головками.
перед прямоугольной головкой, в которой поток испыты вает поворот ,на 90°, что затрудняет центровку изоляции на жиле. Однако, для того чтобы выполнить косоуголь ную головку откидной, приходится увеличивать ее объем, в том числе и объем каналов прохождения расплава. Это связано с возможностью образования так называемых «мертвых» зон в головке, в которых скорость полимера близка к нулю, что, в свою очередь, приводит к перегре ву и разложению полимера и получению недоброкачест
венной изоляции.
Прямоточные экструдеры (рис. 5.20,в) обеспечивают наиболее благоприятное течение расплава полимера из цилиндра к формующему инструменту. В этом случае не наблюдается поворота слоев полимера на большие углы, и это обеспечивает равномерное по толщине наложение изоляции. Однако при этом дорн располагается на вра
щающемся червяке, что существенно затрудняет заправ ку жилы и чистку головки. По этой причине прямоточ ные головки в кабельной промышленности не приме няются, а используются в тех экструдерах, где нет необходимости во внутреннем отверстии дорна для про хождения жилы. Например, при экструзии полимерных пленок, нитей и т. п.
Экструдеры обычно выполняются с цилиндром, в ко тором расположен один червяк. Однако существуют кон струкции экструдеров, у которых в цилиндре расположе-
Рис. 5.21. Схема цилиндра экструдера с двумя червяками.
ны два червяка, оси которых параллельны, а выступы нарезки одного червяка входят во впадины нарезки дру гого (рис. 5.21). Такая конструкция способствует лучшей пластикации и переработке материала.
Для одновременного наложения двух или трех слоев на кабельную заготовку используются сдвоенные или строенные экструдеры. В этих агрегатах обычно различ ные материалы (для изоляции, экрана, оболочки) после довательно накладываются в одной общей головке (рис. 5.22). До поступления в общую головку материал каждого слоя перерабатывается в отдельном экструдере, совместная работа которых синхронизирована.
При двухслойном наложении материала применяются так называемые V- или Т-образные агрегаты. Оси червя ков первых расположены под углом 30—40° друг к другу, вторых — направлены навстречу (рис. 5.23).
Экструдеры для двух- и трехслойного наложения изо ляции, экранов и оболочек применяются обычно для про изводства силовых и высоковольтных кабелей с пласт массовой или резиновой изоляцией. Для производства
т
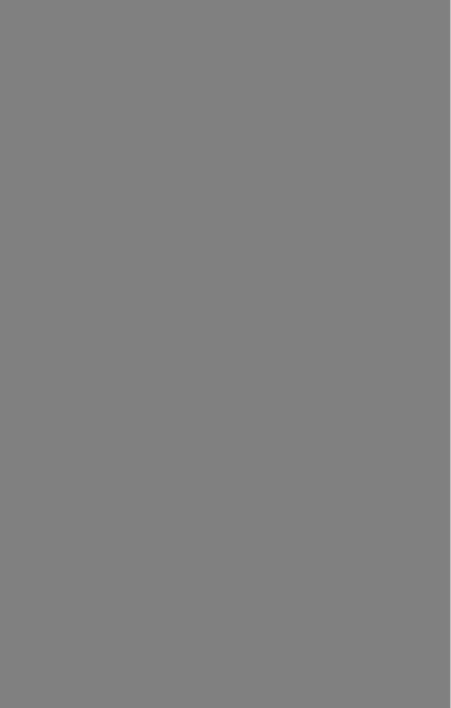
большинства кабелей и проводов’ с пластмассовой или резиновой изоляцией применяются одночервячные экс трудеры с прямоугольной головкой.
Различаются эти экструдеры диаметром червяка, ко торый является их основным техническим параметром.
Т а б л и ц а 5.2
Параметры экструзионных агрегатов при наложении полиэтиленовой изоляции, оболочки или защитного шланга
|
ME-I-45 |
НТ-601 |
МЕ-1-90 ♦МЕ-1-120 |
МЕ-1-160 |
|
Параметр |
(ВНР), |
||||
(ГДР) |
ME-1-60 |
(ГДР) |
(ГДР) |
(ГДР) |
(ГДР)
Диаметр чер вяка, мм
Диаметр по изоляции, мм
Диаметр по оболочке, мм
Частота вра щения червяка, об/мин
Максималь ная линейная скорость, м/мин Производи тельность, кг/ч
|
45 |
|
60 |
|
0 |
00 о |
0 00 |
1 |
О |
|
1 |
|
|
|
|
-— |
До |
4,0 |
|
|
14— 142 |
15— 150 |
||
|
390 |
700 |
|
|
|
45 |
|
90 |
|
90 |
120 |
160 |
1,0— 10,0 |
5,0 —30,0 |
20,0—60,0 |
До 10,0 |
До 30,0 |
До 60,0 |
6— 120 |
10— 100 |
10—90 |
600 |
200 |
70 |
200 |
300 |
500 |
В настоящее время принят унифицированный ряд диа метров червяков: 20, 32, 45, 63, 90, 125, 160, 200 мм (табл. 5.2). Остальные параметры червяка определяются в зависимости от его диаметра и от вида перерабатывае мого полимера. Ниже при рассмотрении особенностей и технологических режимов производства различных кабе лей и проводов приведены основные технические харак теристики экструдеров.
5.6. ЭКСТРУЗИОННЫЕ АГРЕГАТЫ И ПОТОЧНЫЕ КАБЕЛЬНЫЕ ЛИНИИ СОВМЕЩЕННЫХ ПРОЦЕССОВ
Экструдер является основным рабочим узлом агрега та для наложения изоляции или оболочки (табл. 5.3). Кроме экструдера в состав агрегата входит ряд узлов обеспечивающих указанный технологический процесс! Во-первых, как и в любо'м оборудовании для производ-
220
Ства кабелей и пройодов, обязательно наличие отдаю щего, тягового и приемного устройства, обеспечивающих прохождение кабельной заготовки достаточной длины через ^ головку экструдера. Кром.е того, имеется ряд устройств, необходимых для качественного осуществле ния технологического процесса (регулировка натяжения,
Т а б л и ц а 5.3
Основные параметры экструдеров при наложении полиэтиленовой изоляции, полиэтиленовых и поливинилхлоридных оболочек или защитных шлангов
Наименование параметра |
Показатель |
Отношение длины червяка к диаметру
Зазор меж ду гребнем червяка и |
внутрен |
|
ней поверхностью ципиндра не более |
||
Количество (не |
менее) и номера |
(не бо |
лее) фильтрующих |
сеток |
|
Охлаждение червяка экструдера
Охлаждение цилиндра экструдера (при на ложении оболочек или защитных шлангов)
Количество зон обогрева экструдера
Диапазон изменения частоты вращения чер вяка не менее
Диапазон изменения линейных скоростей наложения изоляции или оболочки из поли
этилена не менее Диапазон изменения линейных скоростей
наложения поливинилхлоридной оболочки не
менее Допустимые колебания установленной тем
пературы зон обогрева
От 15 до 25 0,0025 диаметра чер
вяка* 2 сетки № 018 или
028 по ГОСТ 6613-73, ГОСТ 3384-73
Водяное или масля ное**
Водяное или воздуш ное
Не менее трех зон обогрева цилиндра, од ной зоны обогрева го
ловки и одной матрицы
1:8
1:15
1:20
+5°С
*В процессе работы допускается увеличение зазора до 0,004 диаметра червяка.
**Допускается отсутствие охлаждения червяка.
подогрев заготовки, охлаждение изоляции и др.) и кон троля его параметров (измерение диаметра, температуры и т. п.).
На рис. 5.24 приведена схема агрегата для наложения пласт
массовой изоляции. |
ТакойРсшо'цяш'а^1 жи,па |
с отдающею |
у |
рои- |
ста а / поступает |
в компенсатор 3, который |
обеспечивает |
сс; |
по |
стоянное натяжение. Эго осуществляется за счет перемещения
вверх или вниз подвижных роликов. При
ослаблении |
натяжения ролик опускается |
|
вниз, |
при |
увеличении — поднимается |
вверх. |
Это |
перемещение обычно исполь |
зуют для передачи движения на тор мозное устройство отдающего барабана. После компенсатора и протирочного устройства 4 располагают прямильное устройство 5, которое применяется для
однопроволочных жил и представляет собой систему роликов, расположенных в горизонтальной и вертикальной плоско стях. Перед входом в головку экструде ра токопроводящая жила подогревается для обеспечения лучшей адгезии изоля ции к жиле и во избежание охлаждения расплава в головке. При наложении по лиэтиленовой и поливинилхлоридной изоляции жила подогревается до 100— 150°С. Это осуществляется обычно пу тем пропускания электрического тока по участкам жилы, находящимся между двумя контактными роликами 6. После выхода из головки экструдера 7 изоли рованная жила 8 поступает в охлаждаю щее устройство 10, которое обычно вы
полняется в виде ванны, наполненной циркулирующей водой. Длина ванны и температура воды в ней зависят от раз меров изоляционной жилы, скорости ее перемещения и материала изоляции.
После ванны размещается устрой ство 11 для удаления влаги с поверхно
сти изоляции путем обдува ее струей воздуха под давлением около 0,2 МПа. Для контроля и регулирования размеров накладываемой изоляции в агрегате при меняются измерители диаметра, которые могут быть контактного или бесконтакт ного типа. Контактный измеритель диа метра 12 размещают после охлаждаю
щего устройства. Он представляет собой пару роликов, между которыми прохо дит изолированная жила, б случае от клонения ее диаметра от номинального размера один из ролнко0-"'поДвижный— перемещается. Это перемеи*ение фикси руется на индикаторе, а также может использоваться для автоматического ре гулирования диаметра. В этом случае механическое перемещениеь ролика пре образуется в электрический сигнал, ко торый используется для увеличения или уменьшения (в зависимости от направ ления перемещения ролика’Датчика) ча-
стоты вращения тягового механизма 13. При высоких линейных ско
ростях изолирования и размерах охлаждающей ванны за счет инер ционности системы автоматического регулирования большие уча стки готовой продукции могут выходить за пределы нормы. Поэтому желательно размещать измерители диаметра непосредственно у вы хода из головки экструдера. Так как материал изоляции в этом месте находится в состоянии расплава, то применение контактных датчиков исключено. Поэтому здесь используются бесконтактные измерители диаметра 9, которые могут быть, например, фотоэлек
трического типа.
Тяговый механизм 13 может быть колесного или гусеничного
типа. Последний применяется при значительных усилиях протяжки при наложении изоляции значительной толщины или на жилы боль ших сечений, а также в случае использования пластичного материа ла для изоляции или оболочки. После тягового устройства может располагаться измеритель длины 14 и компенсатор 15, который
обеспечивает равномерное натяжение изолированной жилы путем регулирования скорости ее, изменяющейся по мере увеличения диа
метра по |
намотке приемного барабана. Приемное устройство 16, |
в котором |
размещается приемный барабан, может выполняться |
различной .конструкции, причем обычно в виде сдвоенного прием ника, позволяющего без остановки агрегата осуществлять прием изготовленного изделия.
Приведенная схема является типовой для экструзион ного агрегата. Для. различных конкретных технологиче ских процессов могут отсутствовать или видоизменяться те или иные узлы или вводиться дополнительные. Так, в случае наложения пластмассовой оболочки на заготов ку отсутствует прямильное устройство, подогревное устройство применяется другого типа — обогреваемая труба, внутри которой проходит заготовка. Тяговой ме ханизм используется в этом случае, как правило, гусеничного типа, причем гусеничная тяга может дополнительно устанавливаться и после отдающего устройства.
Наложение изоляции или оболочки на кабели и про вода в экструдерах дает возможность широкого совме щения отдельных технологических операций при их про изводстве. Это обусловлено тем, что процесс экструзии осуществляется непрерывно, часто на больших скоростях и обеспечивает принципиальную возможность производ ства кабелей и проводов большими длинами.
При совмещении отдельных технологических процес сов в одну последовательную цепочку достигается значи тельная экономия рабочего времени, повышается произ водительность труда как за счет исключения ряда промёжуточных операций (перемотка, установка и вы грузка приемно-отдающей тары, междуоперационная
№
Рис. 5.25. Схема поточной линии по производству изолированных полиэтиленом жил городских телефонных кабелей.
/ — рабочая |
площадка |
с |
передвижным |
приемником и |
стационарными |
контейнерами; |
2 — волочильная машина МР*9; 3 — установка |
непрерывного отжига; |
4 — компенсатор; |
5 — измеритель |
температуры; |
6 — экструдер; |
7 — фотоэлектрический измеритель диаметра; |
||
8 — ванна |
охлаждения; |
9 — высокочастотный аппарат |
сухого испытания; 10 — приемник на конусы. |
транспортировка заготовок и т. д.), так и за счет эко номии производственных площадей и рабочей силы. Кроме того, улучшаются возможности более широкой и комплексной автоматизации производственных процес сов и контроля продукции.
В настоящее время в кабельной промышленности используются поточные полуавтоматические и автомати ческие линии для производства различной кабельной продукции.
Автоматические поточные линии для производства изолированных жил городских телефонных кабелей с по лиэтиленовой изоляцией совмещают (рис. 5.25): среднее волочение медной проволоки до диаметра 0,32; 0,4 или 0,5 мм, отжиг нагартованной в процессе волочения мед ной проволоки, наложение сплошной полиэтиленовой изоляции, охлаждение изолированной жилы, контроль геометрических размеров, электрических параметров (емкость, электрическая прочность), прием изолирован
ной жилы в контейнеры. При |
этом фиксируется |
длина жилы в каждом контейнере |
и общая выработ |
ка за смену. |
|
На таких линиях достигается высокая линейная ско рость прохождения жилы через узлы линии: для медных жил диаметром 0,4 мм скорость достигает 1500— 1800 м/мин и даже до 2500 м/мин, для жил диаметром 0,32 мм— 1200—1500 м/мин. Меньшие скорости изолиро вания жил диаметром 0,32 мм связаны с технологиче скими трудностями при производстве такого диаметра жил (возможность неравномерной вытяжки, высокие требования к точному соблюдению тяговых усилий и т. п.). В перспективе все жилы с полиэтиленовой изо ляцией планируется выпускать на таких поточных линиях.
На полуавтоматической поточной линии для произ водства силовых проводов с поливинилхлоридной изоля цией осуществляются следующие технологические опера ции: изолирование токопроводящей жилы, охлаждение, контроль параметров и непрерывный прием в бухты. В технологический процесс не входит операция волоче ния проволоки, что связано с тем, что на данных линиях выпускаются силовые провода различного сечения токо проводящей жилы (в пределах 1—10 мм2), а если воло чильная машина встраивается в поточную линию, то она
обычно рассчитывается на производство токопроводящей •жилы одного заданного сечения.
Отличительной особенностью данных линий является то обстоятельство, что прием готовой продукции — изо лированной жилы осуществляется в бухты, причем по мере формирования бухты она автоматически сбрасы вается с бухтовочного приемника. На этих полуавтома тических линиях скорость прохождения жилы достигает 150—250 м/мин. Технические возможности позволяют по высить скорость до 400—600 м/мин, однако при этом необходимо дополнительно автоматизировать процесс обвязки готовых бухт, который на существующих линиях производится вручную.
На данных линиях используются экструдеры с червя ком диаметром 160 мм, производительность которых мо жет достигать 500—600 кг/ч. Однако такой производи тельности можно достигнуть при вращении червяка со скоростью более 40 об/мин, что при использовании поли винилхлоридного пластиката для изоляции приводит к перегреву на 30—40°С в зонах цилиндра и ухудшению качества изоляции за счет вспенивания пластификатора. Поэтому повышение линейных скоростей на этих поточ ных линиях связано также с разработкой новых кон струкций червяков и цилиндров экструдеров, в частности обеспечивающих отсос выделяющихся газов из зон ци линдра.
На автоматических поточных линиях для производств изолированных жил контрольных кабелей накладывается полиэтиленовая изоляция радиальной толщиной 0,6 мм на медные или алюминиевые жилы сечением 2,5—10 мм2. Совмещаются следующие технологические процессы: гру бое волочение, полуотжиг жил, наложение изоляции в экструдере, охлаждение изолированной жилы, контроль параметров, непрерывный прием изолированной жилы на барабан с автоматической сменой его по мере запол нения. Особенностью этой линии является, в частности, применение неполного отжига (полуотжига) алюминие вой проволоки, что необходимо для увеличения механи ческой прочности токопроводящих жил.
В процессе производства осуществляется его полный контроль путем измерения диаметра изолированной жи лы, электрической прочности изоляции и отсчет длины жилы, намотанной на приемный барабан. Последнее измерение особенно существенно для контрольных кабе
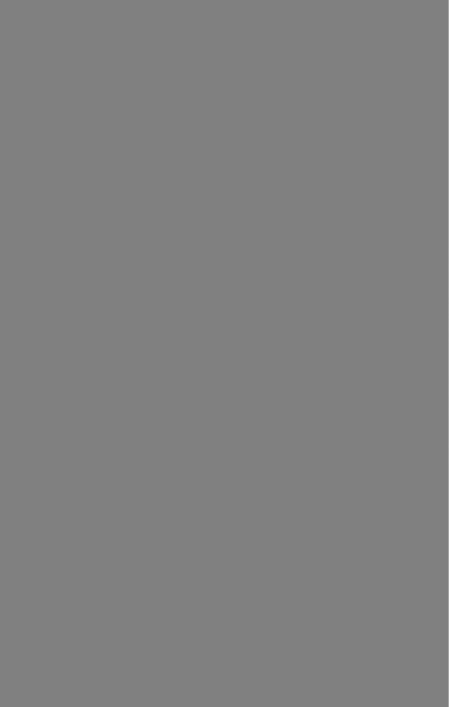
вых, круглых и секторных токопроводящих жил, отработ ка процесса разнонаправленной скрутки эти жил, приме нение цветной раскраски отдельных жил силовых кабелей и поверхностной расцветки поливинилхлоридных оболо чек и непрерывных бронирования и контроля параметров кабелей.
Для цветной раскраски жил силовых кабелей приме няется устройство, позволяющее получать на поверхно
сти |
полиэтиленовой |
изоляции продольную |
цветную |
по |
|||||||
|
|
|
|
|
лосу в |
процессе изолирова |
|||||
|
|
|
|
|
ния жилы. Это осуществля |
||||||
|
|
|
|
|
ется за |
счет использования |
|||||
|
|
|
|
|
специально |
разработанной |
|||||
|
|
|
|
|
сдвоенной головки, в которой |
||||||
|
|
|
|
|
происходит |
наложение |
ос |
||||
|
|
|
|
|
новного |
слоя |
изоляции |
на |
|||
|
|
|
|
|
жилу в экструде с червяком |
||||||
|
|
|
|
|
диаметром |
160 мм, |
а также |
||||
|
|
|
|
|
нанесение |
цветной |
|
полоски |
|||
|
|
|
|
|
из полиэтилена |
другого |
цве |
||||
|
|
|
|
|
та, подаваемого в эту же го |
||||||
|
|
|
|
|
ловку вторым |
экструдером. |
|||||
Рис. 5.26. Вертикальный экстру |
Считается наиболее удобным |
||||||||||
дер |
для |
нанесения расцветки |
сочетание |
горизонтального |
|||||||
на |
изолированные жилы. |
|
основного |
пресса |
и верти |
||||||
/ — привод; |
2 — экструдер; |
3 — го |
кального (рис. |
5.26) |
экстру |
||||||
ловка; |
4 — вертикальная |
стойка |
|||||||||
с механическим перемещением; 5 — |
дера диаметром 40 мм для |
||||||||||
приборный |
шкаф. |
|
нанесения расцветки. |
Путем |
|||||||
|
|
|
|
|
подбора |
частоты |
вращения |
червяка и давления в вертикальном экструдере можно регулировать ширину нанесенной цветной полосы и глу бину ее погружения в изоляцию жилы.
Внедрение автоматизированных участков по произ водству кабелей с пластмассовой изоляцией требует су щественного повышения качества обслуживания обору дования техническим персоналом, а также применения чистых материалов, точно соответствующих техническим требованиям. На таких участках особенно важно сведе ние к минимуму процента брака на любой операции, так как здесь осуществляется производство не одного како го-то элемента кабеля (например, токопроводящей жилы или изолированной жилы), а изготовление готового кабеля.