
524
.pdf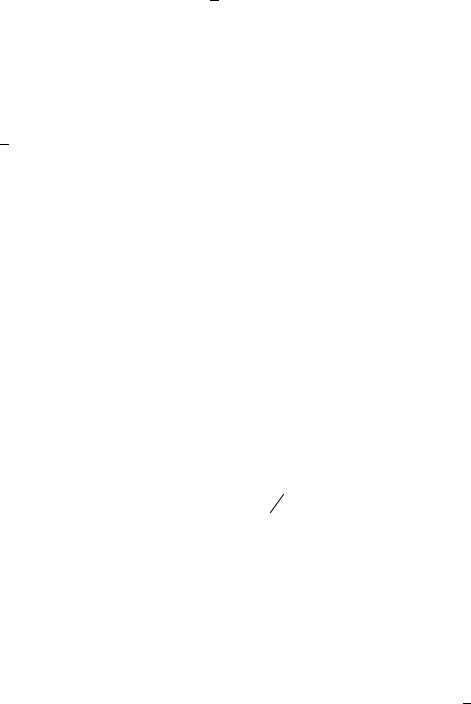
где σ – нормальное напряжение в утолщенном поперечном сечении; ω0 – предельная величина поврежденности, которая совпадает с полным разрушением; σ* – откольная прочность; Y – величина из уравнения (9).
Указанные уравнения релаксации напряжения базируются на следующих положениях: на начальных этапах основной эффект микропор состоит в уменьшении площади поверхности, через которую действует напряжение, в заключительных стадиях объединенная полость устанавливает напряжение, которое зависит от откольной пористости. Очевидно, что выражение (17) или (18) связывает величину поврежденности ω =VV V с состоянием и составом переменных и обеспечивает определение
возможного повреждения совместно с уравнениями сохранения, уравнением состояния и системой уравнений для совокупного разрушения.
Грейди [12] заметил, что процесс динамического разрыва включает как наличие структурной деформации, так и наличие энергетического равновесия. Вейбул предложил такой подход для рассмотрения присущей разрушению деформации, в котором удельные характеристики деформаций (микроразрывов) были приняты неустановленными (неопределенными), а статистическое среднее значение действительных разрывов n в единице объема предполагалось увеличивать по мере роста растягивающего напряжения σ через несколько эмпирических соотношений, таких как
n = k σm , |
(19) |
где k* и m – параметры.
Принимая во внимание соотношение Вейбула (19), Грейди [12] обеспечил критерием σс зависимость разрушающего напряжения от скорости деформации, по крайней мере, для случая хрупкого разрушения:
σс = g (k , m, Cg , E) ε |
3(m+3) , |
(20) |
где Cg – номинальная скорость деформации; E – модуль упругости; ε – единичный параметр скорости деформации.
С одной стороны, считается, что откольная прочность σ*, включенная в откольную модель порообразования, является свойством материала, а также связана с направлением деформации и скоростью растягивающего напряжения. С другой стороны, выражение релаксации напряжения (17) или (18) согласуется с уравнением сохранения энергии, уравнением состояния и системой уравнений для суммарной поврежденности с целью определения искомой величины разрушения. Суммарный удельный объем V
71
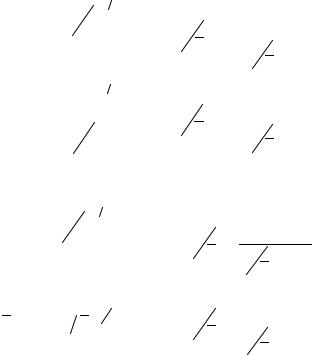
определяется с использованием уравнений сохранения количества движения
и массы. |
Следовательно, все энергетическое равновесие соблюдено, |
и поэтому |
можно говорить о возможности расчета откола в материале |
с использованием откольной модели порообразования через рассмотрение представленной структуры микроскопической деформации.
Одномерные испытания откольного разрушения проводятся в виде экспериментов с применением ударной пластины, в которых летящая пластина наносит удар по испытуемой плите при заданных условиях. При исследованиях откольной поверхности измеренные значения профильной скорости свободной поверхности цели-объекта или профильного напряжения на поверхности раздела между объектом и мягким демпфером содержат информацию о кинетике откола. Вопросы испытаний на откол пластично восстанавливающихся (упруго регенерируемых) объектов являются значимыми, но представляют трудность при согласовании с численными экспериментами мгновенных разрушений.
При дискретном моделировании одномерных испытаний по отколу для определения величины VV(x, t) нами использованы следующие системы уравнений:
|
|
|
|
|
|
|
VV |
2 3 |
|
|
|
|
|
|
|
|
|
|
|
|
|
|
||||||
|
|
|
|
|
− |
|
|
|
|
|
|
|
|
|
VV |
|
|
|
2,53 |
|
|
|
|
|||||
|
|
|
|
V |
|
σ* |
|
|
≤ |
|
|
|
|
|
||||||||||||||
|
|
|
|
|
1 |
|
|
, |
|
|
|
|
|
|
|
, |
||||||||||||
|
|
|
|
ω0 |
|
|
V |
|
|
σ* |
Y ) |
|
||||||||||||||||
|
|
|
|
|
|
|
|
|
|
|
|
1 |
+ |
3 |
|
|
||||||||||||
|
|
|
|
|
|
|
|
|
|
|
|
|
|
|
|
|
|
|
|
|
|
|
||||||
−( p + q ) + |
|
|
= |
|
|
|
|
|
|
|
|
|
|
|
|
|
|
|
( |
|
|
(21) |
||||||
S |
|
|
|
|
|
|
|
|
|
|
|
|
|
|||||||||||||||
1 |
|
|
|
|
|
|
|
|
|
|
|
1 3 |
|
|
|
|
|
|
|
|
|
|
|
|
|
|
||
|
|
|
|
|
|
|
|
|
|
|
|
|
|
|
|
|
|
|
|
|
|
|
|
|
|
|||
|
|
|
|
|
|
|
|
|
2,53 |
|
|
|
|
V |
|
|
|
2,53 |
|
|
|
|
||||||
|
|
|
|
|
|
|
|
|
|
|
|
|
|
|
|
|||||||||||||
|
|
|
|
Y |
|
|
|
|
|
|
−1 , |
|
V |
|
> |
|
|
|
|
|
|
|
, |
|||||
|
|
|
|
|
|
|
|
|
|
|
V |
(1 |
|
* |
|
) |
|
|||||||||||
|
|
|
|
|
|
|
|
VV |
|
|
|
|
|
|
|
|
+ σ |
Y |
3 |
|
|
|||||||
|
|
|
|
|
|
|
|
|
|
|
|
|
|
|
|
|||||||||||||
|
|
|
|
|
|
|
|
|
V |
|
|
|
|
|
|
|
|
|
|
|
|
|
|
или
|
|
|
|
|
|
V |
|
|
|
2 |
3 |
|
|
|
|
|
|
|
|
|
|
|
V |
|
|
|
|
|
|
|
|
|
|
|
− |
V |
|
σ |
* |
|
|||||||
|
|
|
|
1 |
|
|
|
|
|
, |
|
||||
|
|
|
ω |
|
|
||||||||||
|
|
|
|
|
|
|
|
0 |
|
|
|
|
|
|
|
|
|
|
|
|
|
|
|
|
|
|
|
|
|
|
|
−( p + q ) + S1 |
|
|
|
|
|
|
|
||||||||
= |
|
|
|
|
|
|
|
|
|
|
|||||
|
|
|
|
|
|
|
|
|
|
|
|
||||
|
|
|
|
|
|
|
|
|
|
|
|
|
|
|
|
|
|
|
Y 1,43 |
(VV |
|
V )− 16 − 0,91 |
, |
||||||||
|
|
|
|
|
|
|
|
|
|
|
|
|
|
|
|
|
|
|
|
|
|
|
|
|
|
|
|
|
|
|
|
VV |
|
|
1,43 |
6 |
, |
|
≤ |
|
|
||||
V |
|
* |
|
|
|
|
|
|
σ |
Y |
+ 0,91 |
|
|
|
|
|
|
|
(22) |
|
|
|
|
|
|
6 |
|
VV |
|
|
1,43 |
|
||
> |
|
|
, |
|||
V |
|
* |
|
|
|
|
|
|
σ |
Y |
+ 0,91 |
|
|
|
|
|
|
|
|
72
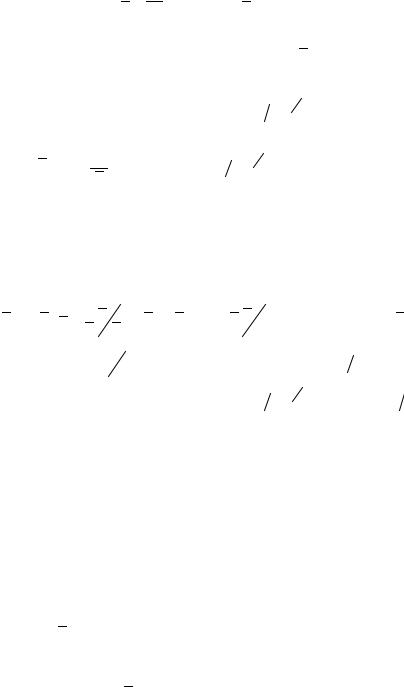
|
|
|
|
|
|
|
|
|
|
|
|
|
|
|
|
|
|
U |
− |
VS1ε1 +( |
|
|
+ q )V |
= 0 , |
|
|
|
|
|
|
|
(23) |
|||||||||||||||||
|
|
|
|
|
|
|
|
|
|
|
|
|
|
|
|
|
|
P |
|
|
|
|
|
|
|
||||||||||||||||||||||||
|
|
|
|
|
|
|
|
|
|
|
|
|
|
|
|
= 1 |
− |
VV |
|
|
(k1η+ k2η2 + k3η3 + ГU |
), |
|
|
|
|
|
(24) |
|||||||||||||||||||||
|
|
|
|
|
|
|
|
|
|
|
|
|
|
P |
|
|
|
|
|
||||||||||||||||||||||||||||||
|
|
|
|
|
|
|
|
|
|
|
|
|
|
|
|
|
|
|
|
|
|
|
|
||||||||||||||||||||||||||
|
|
|
|
|
|
|
|
|
|
|
|
|
|
|
|
V |
|
|
|
|
|
||||||||||||||||||||||||||||
|
|
|
|
|
|
|
|
|
|
|
|
|
|
|
|
|
|
|
|
|
|
|
|
|
|
|
|
|
|
|
|
|
|
|
|
|
|
|
|
|
|
|
|
|
|||||
|
|
|
|
|
|
|
|
|
= 1− |
VV |
|
|
F Y |
|
(1+λεp )n 1+bP |
(ρ |
|
ρ |
)13 − h(T −300) |
, |
|
(25) |
|||||||||||||||||||||||||||
|
|
|
|
|
|
Y |
|
|
|
|
|||||||||||||||||||||||||||||||||||||||
|
|
|
|
|
|
|
|
|
|
|
|
|
|||||||||||||||||||||||||||||||||||||
|
|
|
|
|
|
|
|
|
|
|
|
|
|
|
|
|
|
|
s |
|
|
0 |
|
|
|
|
|
|
|||||||||||||||||||||
|
|
|
|
|
|
|
|
|
|
V |
|
|
|
0 |
|
|
|
|
|
|
|
|
eq |
|
|
|
|
|
|
s |
|
|
|
|
|
|
|
||||||||||||
|
|
|
|
|
|
|
|
|
|
|
|
|
|
|
|
|
|
|
|
|
|
|
|
|
|
|
|
|
|
|
|
|
|
|
|
|
|
|
|
|
|||||||||
|
|
|
|
|
|
|
|
|
G |
= 1−VV |
F |
G0 1+bPs (ρ0 ρs )13 |
−h(T −300) , |
|
|
|
|
(26) |
|||||||||||||||||||||||||||||||
|
|
|
|
|
|
|
|
|
|
|
|
|
|
V |
|
|
|
|
|
|
|
|
|
|
|
|
|
|
|
|
|
|
|
|
|
|
|
|
|
|
|
|
|
||||||
|
|
|
|
|
|
|
|
|
|
|
|
|
|
|
|
|
P = k η+ k |
η2 + k η3 |
+ГU |
s |
, |
|
|
|
|
|
|
(27) |
|||||||||||||||||||||
|
|
|
|
|
|
|
|
|
|
|
|
|
|
|
|
|
|
s |
|
1 |
|
|
2 |
|
|
|
|
|
3 |
|
|
|
|
|
|
|
|
|
|
|
|
|
|
||||||
|
|
|
|
|
|
|
|
|
|
|
|
|
|
|
|
|
|
|
|
|
|
|
|
|
|
|
VV |
|
|
−Vs , |
|
|
|
|
|
|
|
|
|
|
|
|
(28) |
||||||
|
|
|
|
|
|
|
|
|
|
|
|
|
|
|
|
|
|
|
|
|
|
|
|
|
|
|
=V |
|
|
|
|
|
|
|
|
|
|
|
|
||||||||||
где |
|
|
|
|
|
|
|
|
|
|
|
|
|
|
|
|
|
|
|
|
|
|
|
|
|
|
|
|
|
|
|
|
|
|
|
|
|
|
|
|
|
|
|
|
|
|
|
|
|
|
|
|
|
|
|
|
|
|
− 1V |
|
|
, |
|
|
|
|
|
V |
|
|
|
|
|
|
|||||||||||||||||||||||||
ε1 |
= |
∂U |
, S1 = 2G |
ε1 |
|
|
S2 = |
S3 = − |
2 G |
|
|
, (S12 + S22 |
+ S32 )− |
2 Y |
2 ≤ 0 , |
||||||||||||||||||||||||||||||||||
|
|
|
|
|
|
V |
|||||||||||||||||||||||||||||||||||||||||||
∂X |
|
|
|||||||||||||||||||||||||||||||||||||||||||||||
|
|
|
|
|
|
|
|
|
|
3 |
V |
|
|
|
|
|
|
|
|
|
|
3 |
|
|
|
|
|
|
|
|
3 |
|
|
|
|
||||||||||||||
k1 = ρ0C02 , k2 = ρ0C02 (2β− |
Г |
2 |
), k3 = ρ0C02β |
(3β−Г), η =1−ρ0 ρs , |
|
|
|
|
|
||||||||||||||||||||||||||||||||||||||||
|
|
|
|
|
|
|
|
|
|
|
|
|
|
|
|
|
|
|
|
|
|
|
|
|
|
|
|
|
|
|
|
|
|
|
|
|
|
|
|
|
|
|
|
|
|
|
|||
Y |
1+λεp |
n ≤Y |
|
, Y = 0, для T > Tm, T =T |
(ρ |
0 |
ρ |
)23 exp |
2Г(1−ρ |
0 |
|
ρ |
) . |
||||||||||||||||||||||||||||||||||||
0 |
( |
|
|
|
|
eq ) |
max |
|
|
|
|
|
|
|
|
|
|
|
|
|
|
|
|
|
|
|
m |
m0 |
|
|
|
s |
|
|
|
|
|
s |
|
В выражении (24) уравнение состояния Грюнейзена для твердотельной составляющей, построенное на уравнении гидродинамического ударного нагружения ( D = C0 +βu ), является заимствованным, где C, Г, D и β – скорость
звука, параметр Грюнейзена, скорость ударной волны и постоянная материала соответственно, индекс 0 указывает на начальное состояние. В уравнениях (25) и (26) заимствована образующая модель твердотельной сплошной составляющей, описанная Штейнбергом, Кохраном и Гюйнаном [13]. εeqp и T –
эквивалент пластической деформации и температура соответственно, λ, n, b, h, Tm0, G0, Y0 иYmax – постоянные материала.
Величина V определяется из уравнений сохранения количества движения и массы через вычисление конечной разности:
|
|
|
|
∂ |
|
−( |
|
+ q )+ s |
|
|
|
|
|
|
P |
|
|
||||||
u |
|
= |
|
|
1 |
|
, |
(29) |
|||
|
|
|
|
|
|
|
|
|
|||
V |
|
|
|
∂X |
|
||||||
|
|
|
|
|
|
|
|
73
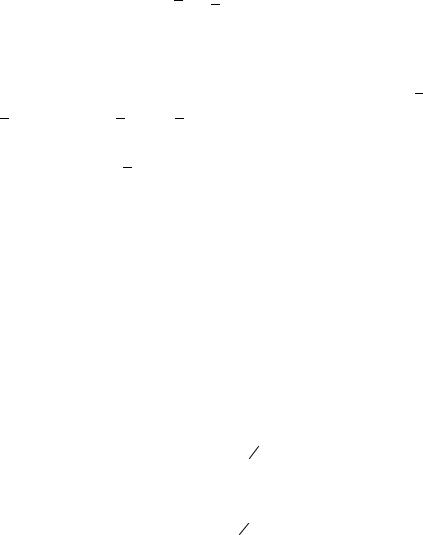
V |
|
= |
∂ |
u |
|
, |
(30) |
||||
|
|
|
|
|
|
|
|||||
V |
∂X |
||||||||||
|
|
|
|
|
|
||||||
X = X (x,t ) . |
(31) |
||||||||||
С помощью уравнений (21)–(31) |
|
вычисляются параметры |
u |
(x,t ), |
X (x,t ) , V (x,t ) , q (x,t ) , P (x,t ) , U (x,t ) и VV (x,t ) до момента достижения растягивающим напряжением значения откольной прочности. Когда величина ω(x,t ) =VV (x,t )V (x,t ) достигает значения предельной величины
разрушения ω0, разделение завершается. Откольная модель порообразования включает только два параметра: откольную прочность σ* и предельную величину разрушения ω0, которые должны быть определены экспериментально в результате испытаний на откол.
Мы предполагаем, что параметры σ* и ω0 могут быть свойствами материала, но не могут быть постоянными величинами, и должны зависеть от первоначальных и конечных состояний в откольных испытаниях. Полагая, что материал, переходя в нагруженное состояние, по своей структуре достаточной микроскопической деформации при выполнении условия локального энергетического равновесия предрасположен к откольному разрушению, Грейди [12] получил величину растягивающего напряжения:
Ps |
|
|
ρ |
2 |
(С |
|
) |
3 |
ε |
|
13 |
, |
(32) |
= 6Г |
|
|
|
|
|
||||||||
|
|
|
|
|
|
|
|
|
|
|
|
|
|
и время действия откольного разрушения (продолжительность откола):
|
|
|
6Г |
|
|
13 |
|
t |
|
= |
|
|
, |
(33) |
|
|
s |
|
ρ(C )3 ε2 |
|
|
|
где Г* – сила дробления, действующая на единицу площади поверхности образовавшегося откольного осколка; C* – скорость упругой волны.
Для идеального вязкого откола [12]
Г |
|
= |
Yεc S |
, |
(34) |
|
6 |
||||||
|
|
|
где S* – размер откольного осколка (отколовшейся части):
74

8Yε |
|
12 |
, |
(35) |
||
S = |
|
c |
|
|
||
ρε |
2 |
|
||||
|
|
|
|
|
|
εс – предельное значение объемной нагрузки, имеющее место для конечного объема полости, соответствующего величине предельного разрушения ω0 в представленной модели откола. Величина разрывающего напряжения, установленная выражением (32), соответствует растягивающему напряжению в конечном полом образовании.
Кратковременная нагрузка σТ исследуемого образца при соударении тонкой пластины с образцом представлена Грейди в работе [12]:
– для профильной скорости
σ |
= |
1 (Z |
S |
− Z |
) |
u |
max |
− |
1 (Z |
S |
+ Z |
) u |
min |
; |
(36) |
T |
|
2 |
W |
|
|
|
2 |
W |
|
|
|
||||
|
|
|
|
|
|
|
|
|
|
|
|
|
|
– для профильного напряжения
|
1 |
|
ZS |
|
|
1 |
|
ZS |
|
|
|
|
σT = |
|
−1 |
σmax − |
|
+1 |
σmin . |
(37) |
|||||
2 |
ZW |
2 |
ZW |
|||||||||
|
|
|
|
|
|
|
|
Здесь волновое сопротивление ZS (для образца) или ZW (для
прокладки – упругого демпфера) является произведением начальной плотности ρ0 материала и соответствующей волновой скорости.
Разрушающее напряжение при отколе в представленной модели откола может быть изначально оценено исходя из величины растягивающей нагрузки при динамическом разрыве, представленной выражением (36) или (37). Представляет трудность вопрос сопоставления наблюдаемых результатов разрушения упруго восстанавливаемых объектов с исчисляемым мгновенным разрушением. Величина предельного разрушения в данной модели откола принимается приближенно за величину наблюдаемого разрушения в плоскости откола, которая для вязкого откола находится в области между значениями 0,1 и 0,3.
Таким образом, разрушающее напряжение при отколе σ* и предельное разрушение ω0 в откольной модели порообразования могут быть изначально оценены, а итоговым решением будут расчетные результаты исследований откольного разрушения, полученные при решении уравнений (21)–(31) при соответствующих начальных и граничных состояниях, согласующихся с экспериментальной профильной скоростью (или напряжением) и наблюдаемой общей величиной разрушения (степенью поврежденности) в плоскости откола.
75
Список литературы
1.Curran D.R. Dynamic failur of solid / D.R. Curran, L. Seaman, D.A. Shockey // Phys. Lett. Sect. C. Phys. Rep. – 1987. – Vol. 147. – № 5–6. – P. 253–388.
2.Thomason P.F. A view on ductile fracture modeling / P.F. Thomason // Fatigue & Fracture of Engineering Material & Structure. – 1998. – Vol. 21. – P. 1105–1122.
3.Hayden H.W. Observation of localized deformation during ductile fracture / H.W. Hayden, S. Floreen // Acta Metall. – 1969. – № 17. – P. 213–214.
4.Thomason P.F. A theory for ductile fracture by internal necking of cavities / P.F. Thomason // J. Inst. Metals. – 1968. – Vol. 96. – P. 360–365.
5.Wilsdorf H.G. The ductile fracture of metals. A microstructural viewpoint / H.G. Wilsdorf // Mat. Sci. Eng. – 1983. – Vol. 59. – P. 1–39.
6.Thomason P.F. Ductile fracture of metals / P.F. Thomason. – Oxford: Pergamon Press, 1990. – 100 с.
7.Thomason P.F. Ductile spallation fracture and the mechanics of void growth and coalescence under shock-loading conditions / P.F. Thomason // Acta Mater. – 1999. – Vol. 47. – P. 3633–3646.
8.Tonks D.L. Void coalescence model for ductile damage / D.L. Tonks, A.K. Zurek, W.R. Thissell // Shock Compression of Condensed Matter. – 2001. – P. 611–614.
9.Tonks D.L. Ductile damage modeling based on void coalescence and percolation theories / D.L. Tonks, A.K. Zurek, W.R. Thissell // Met. and Mat. Appl. of Shock-wave and High-strain-rate Phenomena. – Els. Sci. B.V. – 1995. – P. 171–178.
10.A void coalescence-based spall models / Chen Danian [et al.] // Int. J. Impact Eng., 2005 (in press).
11.Cochran S.G. Spall studies in uranium / S.G. Cochran, D. Banner //
J. Appl. Phys. – 1977. – Vol. 48. – № 7. – P. 2729.
12. Grady D.E. Dynamic fracture and fragmentation / D.E. Grady, M.E. Kipp // High-pressure Shock Compression of Solids. – Springer. – Verlag New York, Inc. 1993. – P. 267–289.
13. Steinberg D.J. A constitutive model for metals applicable at high-strain rate / D.J. Steinberg, S.G. Cochran, M.W. Guinan // J. Appl. Phys. – 1980. – Vol. 51. – P. 1498–1504.
Получено 15.09.2008.
76
УДК 519.6, 629.7
М.Ю. Егоров, С.М. Егоров, Д.М. Егоров
Пермский государственный технический университет
ИССЛЕДОВАНИЕ ПЕРЕХОДНЫХ ВНУТРИКАМЕРНЫХ ПРОЦЕССОВ ПРИ ВЫХОДЕ НА РЕЖИМ РАБОТЫ РАКЕТНОГО ДВИГАТЕЛЯ НА ТВЕРДОМ ТОПЛИВЕ
Проведено комплексное численное исследование переходных внутрикамерных процессов при выходе на расчетный режим работы ракетного двигателя на твердом топливе. Рассматривается сопряженная задача, включающая в себя: описание процесса срабатывания воспламенительного устройства; прогрев, воспламенение и последующее нестационарное горение заряда твердого топлива; нестационарное трехфазное гомогенногетерогенное течение продуктов сгорания в камере сгорания и сопле ракетного двигателя; движение заглушки соплового блока. Приводятся результатычисленногоисследования.
При выходе на расчетный режим работы в камере сгорания ракетного двигателя на твердом топливе (РДТТ) возникает интенсивный ударно-волновой процесс. Он характеризуется значительной амплитудой колебаний давления идругих газодинамических параметров. Ракетный двигатель в целом и прочно скрепленный с корпусом двигателя заряд твердого топлива (ТТ) в частности жестко нагружаются. В осевом направлении заряд получает значительные перемещения, причем со сменой знака во времени. В зоне крепления заряда
скорпусом двигателя, особенно в районах переднего и заднего днищ, и в других зонах-концентраторах возникают значительные деформации и напряжения. Это может быть причиной образования трещины в заряде и, как следствие, увеличения поверхности горения и повышения давления в камере сгорания
споследующим разрушением заряда ТТ икорпуса двигателя.
Для устранения (или минимизации влияния) этих нежелательных эффектов в предлагаемой работе предпринята попытка детального комплексного численного исследования переходных внутрикамерных процессов, протекающих при выходе на расчетный режим работы РДТТ. Рассматривается сопряженная задача, включающая в себя: описание процесса срабатывания воспламенительного устройства; прогрев, воспламенение и после-
77
дующее горение заряда твердого топлива; течение продуктов сгорания в камере сгорания и сопловом блоке ракетного двигателя; движение заглушки соплового блока. Каждая из подзадач рассматривается во взаимосвязи и разрешается одновременно – на одном (по времени) шаге. Учитываются особенности процесса срабатывания воспламенительного устройства, постепенность прогрева, воспламенения, нестационарный и турбулентный режим горения заряда твердого топлива, нестационарный гомогенногетерогенный ударно-волновой характер течения в камере сгорания сложной пространственной формы и неравномерно-ускоренное движение заглушки
соплового блока. |
|
|
|
1. Срабатывание |
воспламенительного |
устройства. |
Процесс |
срабатывания воспламенительного устройства (ВУ) с перфорированным корпусом и вкладным зарядом воспламенительного состава описывается на основе экспериментально-теоретического подхода, предложенного в работе [1]. Путем решения обратной задачи внутренней баллистики для системы «ВУ – имитатор свободного объема камеры сгорания РДТТ» рассчитывается реальный (с учетом особенностей горения заряда воспламенительного состава) газоприход от ВУ.
Система дифференциальных уравнений процесса срабатывания ВУ РДТТ имеет следующий вид:
– изменение давления в корпусе ВУ:
dPв = |
Rв Tв |
vв |
Sв |
(ρвш − ρв )− m |
|
; |
(1) |
|
|||||||
dt |
|
|
|
|
|
|
|
Vв |
|
|
|
|
|
– изменение давления в камере сгорания РДТТ:
dPk = |
Rk Tk |
m. |
(2) |
|
|||
dt |
V |
|
|
|
k |
|
В (1)–(2) и далее по тексту приняты обозначения: m − массовый секундный расход (приход); P − давление; R − газовая постоянная; S − площадь поверхности горения; T − температура; t − время; V − объем; v − скорость горения; ρ− плотность.
Выражая из (1) массовый секундный расход из корпуса ВУ в камеру сгорания РДТТ m , подставляя его в (2) и разрешая полученное относительно скорости горения заряда ВУ, имеем
|
1 |
|
|
V |
dP |
V |
dP |
|
vв = |
|
|
|
в |
в + |
k |
k . |
(3) |
ш |
|
|
|
|||||
|
Sв (ρв |
− ρв ) |
Rв Tв dt |
Rk Tk dt |
|
78
Выражение (3) является основным расчетным соотношением, в котором давление в корпусе ВУ Pв , давление в камере сгорания РДТТ Pk
и их производные по времени определяются экспериментально на специально созданной лабораторной установке.
Однако такой способ определения скорости горения неудобен, так как для каждого конкретного ВУ необходимо провести эксперимент по замеру рабочего давления в корпусе ВУ и в камере сгорания РДТТ и в последующем произвести расчет. Удобнее обобщить и напрямую связать значение скорости горения заряда ВУ vв с параметрами, определяющими процесс горения
в корпусе ВУ: площадью перфорации корпуса ВУ Fкр , площадью поверхности горения заряда ВУ Sв и свободным объемом в корпусе ВУ Vв , в виде
зависимости vв = f (Fкр, Sв,Vв ).
Такого рода связи, не вникая в сущность сложного физикохимического процесса горения, можно найти в статистическом подходе, используя полиномиальные модели, а для нахождения коэффициентов полиномов применить, например, теорию планирования эксперимента. В качестве независимых факторов использовать значения параметров ВУ: Fкр, Sв,Vв . В качестве функции отклика выбрать значение скорости горения
заряда ВУ vв . В общем случае выбор вида полиномиальной модели и типа
плана обусловлен как особенностями процесса горения конкретного состава заряда в корпусе ВУ, так и необходимой степенью точности получаемого
результата. Для нахождения связи vв = f (Fкр /Vв;Sв /Vв ) (здесь количество
независимых факторов сокращено до двух) будем использовать двухфакторный некомпозиционный ротатабельный план Бокса – Бенкена [2], хорошо зарекомендовавший себя при исследовании различных технологических процессов. В соответствии с принятой матрицей планирования была проведена серия опытов на лабораторной экспериментальной установке и замерены давления в корпусе ВУ и в камере сгорания РДТТ. Далее посредством пересчета по (3) были получены значения скорости горения основного заряда ВУ. На основании этих данных (т.е. матрицы планирования) произведен расчет коэффициентов полинома, определяющего связь скорости горения заряда ВУ с основными конструктивными параметрами ВУ. Для конкретно рассматриваемого воспламенительного состава полином имеет вид
79
vв |
= 0,5726 −0,1930 X1 −0,8109 X2 −0,8723 X1 X2 |
− |
(4) |
||
|
− 0,0978 X12 +1,4665 X2 |
2 +1,8496 X1 X2 |
2 , |
|
где X1 = (Fкр /Vв −62,0)/ 57,3; X2 = (Sв /Vв −243,8) / 243,8.
По (4) определяется реальный газоприход от ВУ в камеру сгорания РДТТ. 2. Воспламенение и горение заряда твердого топлива. Описание
процесса нестационарного прогрева, воспламенения и последующего нестационарного и турбулентного горения заряда ТТ базируется на модели Мержанова – Дубовицкого с учетом влияния газовой фазы на процесс горения в конденсированной фазе (к-фазе) [3]. Будем рассматривать ТТ как твердое тело, к которому применимы известные уравнения теплопроводности
ихимической кинетики. Для удобства будем рассматривать эти уравнения
всистеме координат, связанной с поверхностью горения, направив ось от поверхности в ТТ. Считаем, что реакции в конденсированной фазе удовлетворяют закону Аррениуса. Тогда в предположении «0»-мерности порядка химических реакций данная система уравнений, описывающая процесс, имеет вид:
|
∂Tk = κ |
∂2Tk +v |
∂Tk + |
Qk |
Φ |
|
(T ); |
||||||||
|
|
|
|||||||||||||
|
∂t |
k ∂y2 |
k ∂y |
k |
c |
k |
|
k |
k |
||||||
|
|
|
|
∂β |
k |
∂β |
|
|
|
|
(5) |
||||
|
|
|
|
= v |
+Φ |
|
(T |
), |
|||||||
|
|
|
|
∂t |
∂yk |
|
|||||||||
|
|
|
|
k |
|
|
k |
|
k |
|
|
|
|||
|
|
Ek |
|
|
|
|
|
|
|
|
|
|
|
|
|
где Φk (Tk ) = Zk exp |
− |
. |
|
|
|
|
|
|
|
|
|
|
|
||
|
|
|
|
|
|
|
|
|
|
|
|
||||
|
|
R0Tk |
|
|
|
|
|
|
|
|
|
|
|
|
В (5) и далее по тексту дополнительно приняты обозначения: c − удельная теплоемкость; E − энергия активации; Q − тепловой эффект
реакции; R0 − универсальная газовая постоянная; y − координата; Z − предэкспонент; β− глубина превращения пороха; κ− коэффициент температуропроводности. Символы: k − ТТ.
До воспламенения в (5) необходимо положить vk = 0. Общепринятого условия воспламенения в настоящее время не существует. В классических работах условие горения принимается в виде βs = β =1. Это же условие
выберем и в качестве условия воспламенения.
До воспламенения начальные и граничные условия для системы (5) имеют вид:
80