
524
.pdfТаким образом, при соотношении акустических импедансов ударника и панели больше или равном 3, получаем, что ударник деформируется в 10 и более раз меньше, чем панель, и его можно считать жестким телом.
Список литературы
1.Альтшулер Л.В. Применение ударных волн в физике высоких давлений / Л.В. Альтшулер // Усп. физ. наук. – 1965. – Т. 85. – Вып. 2. – С. 197– 258.
2.Рыбаков А.П. Твердые тела в условиях давлений и температур ударного сжатия / А.П. Рыбаков. – М.: Цнииатоминформ, 1978. – 88 с.
3.Рыбаков А.П. Механика откольного разрушения / А.П. Рыбаков. –
Пермь: ПВИ РВ, 1996. – 200 с.
4. Ударно-волновые явления в |
конденсированных средах / |
Г.И. Каннель [и др. ]. – М.: Янус – К, 1996. |
– 408 с. |
5.Curran D.R. Nonhydrodynamic attenuation of shock waves in aluminum / D.R. Curran // J. Appl. Phys. – 1963. – Vol. 34. – № 9. – P. 2677–2685.
6.Новиков С.А. Напряжения сдвига и откольная прочность материалов при ударных нагрузках (обзор) / С.А. Новиков // ЖПМТФ. – 1981. – № 3. – С. 109–120.
7.Kinslow Ed.R. High velocity impact phenomena / Ed.R. Kinslow. – N.Y.; London: Acad. Press, 1970. – 586 p.
8.Kaye G.W. Tables of physical and chemical constants / G.W. Kaye, T.H. Laby. – Toronto; London; New York: Longmans: Green & Co, 1960. – 248 p.
9.Жарков В.Н. Уравнения состояния твердых тел при высоких давлениях и температурах / В.Н. Жарков, В.А. Калинин. – М.: Наука, 1968. – 312 с.
10.Van. Ed. Compendium of shock wave data / Ed. Van. J. Thiel // Lowrence Radiation Lab. – Livermore: California Univ. Press, 1966. – 1030 p.
11.LASL Shock wave Hugoniot data. – Berkely: California Univ. Press, 1980. – 948 p.
12.Morris C.E. LASL Wave profile data / C.E. Morris. – Berkely: California Univ. Press, 1982. – 120 p.
Получено 01.09.2008.
51
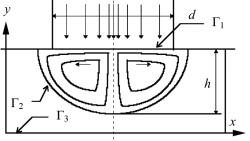
УДК 536.24:621.791.72
Г.Н. Вотинов, В.С. Постников
Пермский государственный технический университет
МОДЕЛИРОВАНИЕ ПРОЦЕССА НАСЫЩЕНИЯ СЛОЯ ЛАЗЕРНОГО МОДИФИЦИРОВАНИЯ ЭЛЕМЕНТАМИ ГАЗОВОЙ СРЕДЫ
На основе уравнений тепло- и массопереноса сформулирована и реализована двумерная математическая модель процесса импульсного лазерного модифицирования поверхности металла элементами газовой среды. Учитывается влияние конвекции Марангони на перемешивание расплава. Модель позволяет объяснить некоторые закономерности структурообразования.
Лазерная обработка материалов основана на возможности лазерного излучения создавать на малом участке поверхности высокие плотности теплового потока, необходимые для интенсивного нагрева и расплавления практически любого материала. На практике используются различные схемы внесения примеси в зону облучения, в том числе и из газовой среды. Значительные потенциальные возможности лазерной технологии далеко не всегда реализуются на практике из-за неоптимального выбора технологических параметров, таких как мощность излучения, частота импульсов и другие, для широкой номенклатуры металлов. Для выбора оптимальных режимов облучения при лазерном модифицировании поверхности возникает необходимость математического моделирования сопряженных явлений тепло- и массообмена с учетом фазового перехода, конвективного перемешивания расплавленного металла.
Рис. 1. Принципиальная схема плавления металла концентрированным пучком энергии
В настоящей работе рассматривается нестационарный процесс оплавления поверхности металла при кратковременном воздействии теплового потока большой мощности. Принципиальная схема процесса оплавления показана на рис. 1. При воздействии лазерного излучения на поверхность металла происходит ее оплавление. Пренебрегаем искажением свободной
52
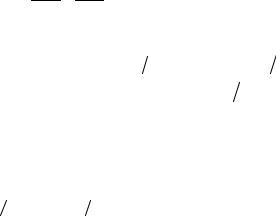
поверхности, а также любым механическим воздействием на плавящийся металл. Расчетную область размером lX × lY выбираем заведомо больше предполагаемой зоны оплавления.
Математическая формулировка задачи в двумерной постановке включает сопряженную систему безразмерных (в качестве характерных масштабов выбраны кинематическая вязкость ν0, характерная разность температур δT и вертикальный линейный размер lY) дифференциальных уравнений тепло- и массопереноса [1]:
∂ T |
+ |
∂ ψ ∂ T |
− |
∂ ψ ∂ T |
= |
1 |
|
∂ |
λ′ |
∂ T |
+ |
∂ |
|
λ′ |
∂ T |
, |
|
∂ t |
∂ y ∂ x |
∂ x ∂ y |
|
|
|
|
|
|
|
|
|||||||
|
|
|
|||||||||||||||
|
|
|
Pr |
∂ x |
|
∂ x |
|
∂ y |
|
∂ y |
|
∂ ω |
+ |
∂ψ ∂ ω |
− |
∂ψ ∂ ω |
= Gr |
∂ T + |
∂2 |
|
(ν′ ω) + |
|
|
|
|
|
|||||||||||||||||
∂ t |
∂ y ∂ x |
∂ x ∂ y |
∂ x2 |
|
|
|
|
|
|
||||||||||||||||||||||
|
|
|
|
|
∂ x |
|
|
|
|
|
|
|
|
|
|
|
|
|
|
||||||||||||
+ |
∂2 |
(ν′ ω) + 2 |
∂2ν′ ∂2ψ |
+ 2 |
∂2ν′ ∂2ψ |
−4 |
∂2ν′ ∂2ψ |
|
|
, |
|||||||||||||||||||||
|
|
|
|
|
|
|
|
|
|
|
|
|
|
|
|
|
|
|
|||||||||||||
∂ y2 |
∂ x2 ∂ y2 |
∂ y2 ∂ x2 |
∂x ∂y ∂x ∂y |
||||||||||||||||||||||||||||
|
|
|
|
|
|
|
|
|
|
|
|||||||||||||||||||||
∂ |
|
∂ ψ ∂ |
C |
|
∂ ψ ∂ |
C |
|
|
∂ |
|
|
|
∂ |
C |
|
|
|
|
∂ |
∂ |
C |
|
|
||||||||
C |
|
|
|
|
|
|
|
|
|
|
|
|
|
|
|
|
|
|
|
|
|
|
|
||||||||
|
|
+ |
|
|
− |
|
|
|
|
= |
|
|
D |
|
|
|
|
+ |
|
|
D |
|
|
, |
|||||||
∂ t |
∂ y ∂ x |
∂ x ∂ y |
|
|
|
∂ x |
∂ y |
∂ y |
|||||||||||||||||||||||
|
|
|
|
∂ x |
|
|
|
|
|
|
|
ω= − ∂2ψ − ∂2ψ ,
∂x2 ∂ y2
где T − температура; ψ − функция тока; |
Pr = ν |
0 |
χ , |
Gr = gβ δT l3 |
ν2 |
|
|
|
|
V |
Y |
0 |
|
критериальные комплексы Прандтля |
и Грасгофа; |
χ = λ0 |
(ρ0 cэ ) |
(1)
(2)
(3)
(4)
−
−
температуропроводность; ρ0 − плотность; cэ − эффективная теплоемкость, в которой учтена скрытая теплота фазового перехода Q (в соответствии с
квазиравновесной теорией двухфазной зоны); |
β = − |
1 |
|
∂ ρ |
− коэффициент |
|
|
|
|||||
|
|
V |
ρ0 ∂ T |
|
||
|
|
|
|
|||
′ |
′ |
− обезразмеренные значения |
||||
объемного расширения; λ = λ λ0 |
и ν = ν ν0 |
коэффициента теплопроводности и кинематической вязкости; λ0 и ν0 −
значения |
этих |
|
коэффициентов при |
температуре |
ликвидус TL; |
ω − завихренность; D − коэффициент диффузии; C − концентрация примеси. |
|||||
Для различных металлов порядок величины коэффициента диффузии D |
|||||
колеблется |
от |
2 |
10–9 м2/с до 10–8 м2/с |
[3]. Например, |
для расплава |
среднеуглеродистой |
стали (ν ≈ 0,6 10–6 м2/с; |
χ ≈ 6 10–6 м2/с; |
D ≈ 5 10–9 м2/с) |
53
коэффициент диффузии на три порядка меньше коэффициентов кинематической вязкости и температуропроводности. Следовательно, для расчета распределения примеси (при временах воздействия порядка нескольких миллисекунд) диффузия не играет существенной роли и ей можно пренебречь. Таким образом, считаем, что при лазерном легировании примесь перераспределяется только за счет конвекции. Уравнение (3) принимает вид
|
|
|
|
∂ C |
+ ∂ ψ ∂ C |
− ∂ ψ ∂ C |
|
= 0. |
|
|
|
(5) |
|||
|
|
|
|
∂ t |
∂ y ∂ x |
∂ x ∂ y |
|
|
|
|
|
|
|
||
|
В начальный момент времени: |
|
|
|
|
|
|
|
|
|
|||||
|
T (t = 0) =T0 (x, |
y), C(t = 0) = C0 (x, |
y), |
ω(t = 0) = 0, ψ(t = 0) = 0 . |
(6) |
||||||||||
|
Граничные условия для температуры: |
|
|
|
|
|
|
|
|||||||
|
|
|
∂ T |
|
|
|
|
|
2 |
|
|
|
|
||
|
|
|
|
|
|
|
|
|
|
|
|
||||
|
|
|
= Bi q(t, x) −(TП |
−TС) |
, |
|
∂ T |
|
|
= 0 , |
(7) |
||||
|
|
|
|
|
2 |
|
|
||||||||
|
|
|
∂ y |
Г |
αδT |
|
|
|
|
∂ n |
|
Г |
3 |
|
|
|
|
|
|
1 |
|
|
|
|
|
|
|
|
|
||
где |
Bi = |
αlY |
– критерий Био, α − коэффициент теплоотдачи излучением; |
||||||||||||
λ |
|||||||||||||||
|
|
|
|
|
|
|
|
|
|
|
|
|
|
q(t, x) − плотность потока энергии; TП и TС − температуры поверхности и окружающей среды соответственно.
Для концентрации примеси при легировании из окружающей газовой
среды
∂ C |
|
= −Bi |
(C |
−C |
), |
(8) |
|
||||||
∂ y |
|
С |
П |
|
С |
|
|
Г |
|
|
|
|
|
|
1 |
|
|
|
|
где BiC = αDC lY – концентрационное число Био.
На других границах
|
|
|
C |
|
Г3 = C0 |
|
Г3 |
(x, |
y) . |
(9) |
|||
|
|
|
|
|
|||||||||
|
|
|
|
|
|
|
|
|
|||||
Из условий непроницаемости и прилипания: |
|
||||||||||||
ψ |
|
Г |
= ψ |
|
Г = 0 , |
∂ ψ |
|
= 0 . |
(10) |
||||
|
|
|
|||||||||||
|
|
|
|||||||||||
1 |
2 |
|
|
∂ n |
Г |
|
|
||||||
|
|
|
|
|
|
||||||||
|
|
|
|
|
|
|
|
|
|
|
|
2 |
|
54

Завихренность на границах жидкой вазы:
|
ω |
|
Г = − |
lY σ0 |
|
∂ σ′ |
, ω |
|
Г = − |
∂2ψ2 |
|
|
− |
∂2ψ2 |
|
, |
(11) |
|
|
|
|
|
|
|
|||||||||||||
|
|
ρ0ν′ν0 |
2 |
∂ x |
Г |
|
Г |
|||||||||||
|
1 |
|
2 |
∂x |
|
|
∂y |
|
|
|||||||||
|
|
|
|
|
|
|
|
|
|
|
|
|||||||
′ |
− обезразмеренное значение |
|
|
2 |
|
|
|
2 |
|
|||||||||
коэффициента |
поверхностного |
|||||||||||||||||
где σ = σ σ0 |
натяжения.
Поставленная задача реализована методом сеток. Применена неявная однородная конечно-разностная схема с расщеплением двумерной задачи на последовательность одномерных, которые затем решались продольнопоперечной прогонкой по схеме сквозного счета без явного выделения границы раздела фаз. Подвижная граница раздела фаз определялась по положению изотермы T = TФ = (TS + TL)/2. При несовпадении криволинейной границы раздела фаз с узлами сетки применялись разности с переменными шагами по координатам для функции тока и завихренности. Завихренность жидкой фазы на твердых границах вычислялась с помощью двухконтурной методики В.Л. Грязнова и В.И. Полежаева [2]. Конвективные члены в уравнениях переноса (1)–(3) аппроксимировались с помощью консервативной схемы с донорными ячейками. Эта схема дискретизации конвективных членов позволяет по сравнению с другими достигать установления с наименьшими затратами машинного времени. Для решения разностного аналога уравнения Пуассона (4) применялся итерационный метод последовательной линейной верхней релаксации с оптимизацией параметра релаксации.
Вычислительный эксперимент, описанный ниже, проведен для стали У10. Плотность потока лазерного излучения принята в виде закона
нормального распределения |
по толщине лазерного пучка. Энергия |
в импульсе E = 8 Дж, радиус |
лазерного пучка r = 5 10–4 м, длительность |
импульса τ = 6 10–3 с. Коэффициент перекрытия импульсов равен 0,5, т.е. каждый последующий импульс сдвигается от предыдущего на расстояние, равное радиусу лазерного луча.
При легировании из окружающей газовой среды предполагаем известным поток примеси на поверхность расплава. Величина этого потока зависит от многих факторов, характеризующих конкретный технологический процесс и в большинстве случаев определяется только экспериментально. Поэтому представленные в данной работе результаты отображают распределение примеси в реальном процессе лишь качественно. При этом за 1 (единицу) принимается максимальная концентрация примеси
55
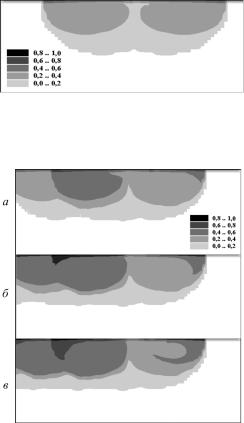
в металле в течение всего процесса обработки поверхности. Расчеты проведены на сетке размером 80×60. Результаты расчетов распределения примеси (легирующего компонента) в обработанной лазером поверхности металла (стали У10) представлены на рис. 2 и 3.
|
На начальных этапах массопе- |
|||||
|
реноса примесь сосредоточена у по- |
|||||
|
верхности расплава, причем область |
|||||
|
локального |
максимума концентрации |
||||
|
находится |
у |
кромки |
ванны |
расплава |
|
Рис. 2. Результаты расчета распределения |
(и сохраняется до конца обработки). На |
|||||
рис. 2 представлены результаты расче- |
||||||
примеси для первого импульса после |
та распределения примеси для первого |
|||||
застывания ванны расплава |
импульса после застывания расплава. |
|||||
|
||||||
|
По рис. 2 видно, что примесь |
|||||
|
проникает вглубь металла по краям |
|||||
|
ванны расплава. В силу вихревой |
|||||
|
структуры течения расплава в даль- |
|||||
|
нейшем примесь перемещается к его |
|||||
|
свободной поверхности. Но при этом |
|||||
|
вихри не захватывают придонные слои |
|||||
|
расплава, где образуется так на- |
|||||
|
зываемая зона несмешивания, обус- |
|||||
|
ловленная |
как |
движением |
границы |
||
|
раздела фаз, так и повышенной вяз- |
|||||
|
костью расплава. |
|
|
|||
Рис. 3. Результаты расчета распределения |
Последующие импульсы, про- |
|||||
изведенные |
со |
сдвигом, |
изменяют |
|||
примеси для второго (а), третьего (б) |
картину распределения примеси (см. |
|||||
и четвертого (в) импульсов после |
||||||
застывания расплава |
рис. 3), |
повышая |
максимальную |
|||
|
концентрацию |
постоянно |
вводимой |
|||
|
примеси в металле. |
Только начиная |
с четвертого импульса последующие импульсы не будут отличаться от предыдущих ни по распределению примеси, ни по концентрации.
Показанная на рис. 3 повышенная концентрация элементов газовой фазы в районе перекрытия областей лазерного воздействия хорошо иллюстрирует макростроение в слое лазерного модифицирования поверхности сталей. При импульсной лазерной обработке поверхности стали с использованием легирующего покрытия, содержащего элементы (Ti,
56
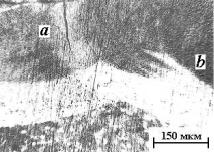
Cr, B, C), обладающие высокой реакционной способностью связывать элементы газовой среды (O, N), в структуре поверхности помимо интерметаллидов, карбидов и боридов образуется большое количество окислов. В зонах повышенной концентрации газовой примеси повышенное количество окисных соединений должно приводить к охрупчиванию структуры. Высокая скорость охлаждения создает в поверхностном слое
значительное |
напряженное |
состояние, |
релаксация которого происходит |
в зонах повышенной хрупкости структуры. |
|||
Анализ |
структурных |
дефектов |
слоя лазерного модифицирования |
показывает, что в области перекрытия областей лазерного воздействия могут возникать трещины (рис. 4), расположение которых хорошо коррелирует с расчетной областью повышенной концентрации элементов газовой среды. Показанная на рис. 4 трещина (а) располагается в пределах слоя, в котором происходило активное перемешивание легирующего состава с материалом модифицируемой стали. Развитие трещины шло от поверхности вглубь слоя вдоль границы области лазерного воздействия. Трещина распространяется не по всей границе перекрытия областей лазерного воздействия, а только в области повышенной концентрации элементов газовой среды (см. рис. 3, в).
Образование зоны |
несмеши- |
|
вания вблизи дна ванны расплава |
|
|
также можно увидеть |
на рис. 4. |
|
В процессе конвективного |
движения |
|
жидкости ванны расплава поверх- |
|
|
ностные слои этой зоны увлекаются |
|
|
движущейся жидкостью. В момент |
|
|
окончания импульса эти слои не успе- |
|
|
вают перемешаться с материалом ос- |
Рис. 4. Макроструктура слоя лазерного |
|
новного объема ванны расплава и при |
модифицирования поверхности стали У10 |
|
травлении структуры выделяются (b). |
(легирующий состав – Cr + B4C) |
Основное отличие массопереноса при внедрении примеси из газовой среды и из предварительно нанесенных покрытий [3] состоит в том, что при наличии потока поступающей примеси на поверхность количество легирующего вещества в расплаве непрерывно увеличивается, в то время как при легировании из предварительно нанесенных покрытий количество ее не меняется, а происходит только перераспределение легирующего компонента. Вследствие этого при легировании из предварительно нанесенных покрытий (заданная концентрация примеси на поверхности металла) реализуются иные структуры полей концентраций в зоне легирования.
57
Легирование из газовой среды может сопутствовать процессу легирования из предварительно нанесенных легирующих покрытий и во многих случаях является нежелательным, поскольку внесение неметаллического компонента приводит к повышению хрупкости металла. Это, в частности, объясняет тот факт, что разрушение образца (при испытаниях) происходит по краям бывшей лунки оплавления, где концентрация примеси максимальна.
Результаты экспериментального исследования структуры поверхностного слоя стали после импульсного лазерного воздействия показывают, что разработанная модель позволяет достаточно хорошо объяснить основные закономерности структурообразования. При этом особенности движения расплава, обнаруженные расчетным способом, дают ответы на некоторые вопросы, которые не имели ответа при обычных экспериментальных исследованиях.
Таким образом, предложенная математическая модель достаточно детально описывает процессы тепло- и массопереноса при импульсном лазерном воздействии на металлы и может быть использована для прогнозирования рациональных режимов лазерного воздействия в конкретных технологических условиях.
Список литературы
1. Математическое моделирование конвективного тепломассообмена на основе уравнений Навье – Стокса / В.И. Полежаев [идр.]. – М.: Наука, 1987.
2. Грязнов В.Л. Исследование некоторых разностных схем аппроксимации граничных условий для численного решения уравнений тепловой конвекции / В.Л. Грязнов, В.И. Полежаев // Препринт / ИПМ АН
СССР. – М., 1978. – 84 |
с. |
|
3. Вотинов Г.Н. |
Моделирование процесса легирования |
стали У10 |
импульсным лазером |
с использованием обмазок / Г.Н. |
Вотинов, |
В.С. Постников // Вестник ПГТУ. Прикладная математика и механика. −
Пермь, 2003. – С. 3–8.
Получено 15.09.2008.
58
УДК 583+539.4+620.1
О.Ю. Вшивков
Пермский военный институт ВВ МВД РФ
КРИТЕРИЙ ПРОБИВНОЙ СПОСОБНОСТИ ПОРАЖАЮЩИХ ЭЛЕМЕНТОВ
Предложен новый критерий определения пробивной способности поражающих элементов и вида разрушения преград в условиях импульсных ударно-волновых нагрузок.
Поведение конденсированных тел (в частности, их разрушение) имеет свои особенности при импульсном нагружении. В этом случае может произойти полный или частичный разрыв или расслаивание материала, и от нагружаемого тела вблизи его свободной поверхности отделяется откольный слой или несколько более тонких слоев материала. Данный вид динамического разрушения называется отколом, он обусловлен волновым характером происходящих в материале процессов и течений, реализующихся под воздействием импульсов нагрузки длительностью в доли микросекунды.
Такие длительности возможно осуществить при различных способах нагружения: удар пластиной [1], взрыв листового заряда взрывчатого вещества [2], интенсивный поток излучения (например, электромагнитного излучения оптического квантового генератора) [3], подрыв блока ВВ на поверхности преграды [4], а также удар поражающим элементом (пулей, снарядом, осколком), обладающим высокой удельной энергией [5]. При различных видах ударно-волнового нагружения начальные параметры ударно-волновых импульсов нагрузки близки по своим значениям. Начальные значения амплитуды ударно-волнового импульса, идущего в преграду, составляют десятки гигапаскалей, а длительности – десятые долимикросекунды.
При описании поведения преграды при импульсном нагружении можно абстрагироваться от способа нагружения преграды (т.е. способа генерирования ударно-волнового импульса) и рассматривать только процессы, происходящие в преграде под действием такого импульса. Незначительный разброс в начальных амплитудах и длительностях ударноволновых импульсов можно скорректировать, введя в рассмотрение удельное количество движения ударно-волнового импульса (удельный механический импульс)
59

J = ∫τ |
P (t )∂t , |
(1) |
0 |
|
|
где τ – длительность ударно-волнового импульса; P – давление; t – время. Для начальных параметров ударно-волнового импульса, отмеченных выше, характерное значение удельного количества движения равно 103 кг/(м·с).
В работе [6] определены критерии зависимости кинематических параметров откола от условий нагружения, параметров состояния материала и преграды:
|
δ |
|
|
|
|
|
|
|
|
|
|
= a +bη , |
W |
|
= a +bη, |
|
|
|
(2) |
||
|
H |
C |
|
|
|
|||||
|
|
|
|
|
|
|
||||
|
|
|
0 |
|
|
|
|
|
||
|
|
|
|
|
|
|
|
Jн |
|
12 |
где δ – толщина откола; |
H – толщина пластины; η = |
|
|
|
– |
|||||
ρ0 |
|
|||||||||
|
|
|
|
|
|
|
HC0 |
|
комплексный параметр условий нагрузки, Jн – удельный импульс нагрузки, ρ0 – плотность материала пластины, C0 – скорость звука, W – скорость свободной поверхности пластины. Для группы металлов значения коэффициентов a и b вместе со среднеквадратическими ошибками [6] приведены в таблице.
|
Критерии |
a |
σa |
b |
σb |
|
|
δ/H = f(η) |
0,010 |
0,035 |
1,050 |
0,146 |
|
|
|
/C0 = f (η) |
|
|
|
|
W |
0,025 |
0,021 |
0,288 |
0,088 |
В работе [6] расчеты проводились для случая нагружения материала косой ударной волной в условиях подрыва листового заряда ВВ на поверхности образца.
Механизм откола наблюдается также и при ударно-волновом нагружении конструкций и объектов военной техники в условиях проникающего (пробивного) действия на преграду пули, снаряда и других поражающих элементов, обладающих высокой удельной энергией [1, 5, 7].
Пробивное действие поражающего элемента обычно характеризуют глубиной его проникновения в преграду определенной плотности и толщины. На глубину проникновения влияют [7–10]: удельная энергия поражающего элемента в момент встречи с преградой, свойства пробиваемого материала, толщина преграды, угол встречи с преградой,
60