
- •Направление I
- •ФУНДАМЕНТАЛЬНЫЕ ОСНОВЫ ПРОЦЕССОВ СОЗДАНИЯ И ФУНКЦИОНИРОВАНИЯ АВИАЦИОННЫХ, КОСМИЧЕСКИХ И ТРАНСПОРТНЫХ СИСТЕМ
- •ПЕРСПЕКТИВЫ ВОДОРОДНОЙ ЭНЕРГЕТИКИ В АВИАЦИИ
- •К ВОПРОСУ ОБ ОПРЕДЕЛЕНИИ ДИНАМИКИ НАГРЕВА ТОРМОЗОВ ПРИ ПРОБЕГЕ САМОЛЕТА ПОСЛЕ ПОСАДКИ
- •Получение накопителей водорода на основе никеля и его сплавов
- •НАПРАВЛЕНИЯ ПО РАЗВИТИЮ ГИДРОАВИАЦИИ
- •С.В. Ульшин
- •ВЛИЯНИЕ УПРУГИХ ДЕФОРМАЦИЙ И КОЛЕБАНИЙ НА ФУНКЦИОНИРОВАНИЕ СИСТЕМЫ УПРАВЛЕНИЯ
- •ОСОБЕННОСТИ ЭЛЕКТРОХИМИЧЕСКОГО ОБРАЗОВАНИЯ КОМПОЗИТОВ Ni-B
- •В ПОСТОЯННОТОКОВОМ И ИМПУЛЬСНОМ РЕЖИМАХ ЭЛЕКТРОЛИЗА
- •А.В.Звягинцева, канд. хим. наук; В.И. Корольков, д-р техн. наук, М.И.Смородинов
- •ИССЛЕДОВАНИЕ ДВИЖЕНИЯ ЧАСТИЦ ЗАГРЯЗНИТЕЛЯ В ПОТОКЕ ЖИДКОСТИ
- •(в настоящее время в России действует «Федеральная целевая программа обеспечения БП в государственной авиации», утвержденная распоряжением правительства РФ от 06.05.2008 № 641-р)
- •ИССЛЕДОВАНИЕ ПРОЦЕССА РОТАЦИОННОГО ОБЖИМА КОЛЕСНОГО ДИСКА
- •БЕЗОПАСНОСТЬЮ ПОЛЁТОВ
- •ЧИСТОВАЯ ОБРАБОТКА ОТВЕРСТИЙ В СМЕШАННЫХ ПАКЕТАХ
- •ЭЛЕКТРОХИМИЧЕСКАЯ ИМПУЛЬСНАЯ ТЕХНОЛОГИЯ АНОДНОЙ ОБРАБОТКИ ФОЛЬГИ
- •ВОЗМОЖНОСТИ ПРИМЕНЕНИЯ 3D ПРИНТЕРА ДЛЯ ИЗГОТОВЛЕНИЯ ДЕТАЛЕЙ АВИАЦИОННОЙ ТЕХНИКИ
- •ВЛИЯНИЕ ДЕФЕКТОВ МИКРОСТРУКТУРЫ ЛИСТОВОГО ПОЛУФАБРИКАТА НА ОБРАБАТЫВАЕМОСТЬ ДАВЛЕНИЕМ
- •БЕРЕЖЛИВОЕ ПРОИЗВОДСТВО НА «АВИАСТАР СП»
- •Особенности расчета подбора СОСТАВА ТОПЛИВНЫХ компонентов в АРД
- •Новые решения в конструкции подшипника скольжения с увеличенным рабочим ресурсом
- •БЕСПИЛОТНЫЙ ВИНТОКРЫЛЫЙ ЛЕТАТЕЛЬНЫЙ АППАРАТ ПОВЫШЕННОЙ МАНЕВРЕННОСТИ
- •СТЕНДОВАЯ УСТАНОВКА ДЛЯ ОЦЕНКИ АБРАЗИВНОГО ИЗНОСА ДЕТАЛЕЙ АВИАЦИОННЫХ
- •УЗЛОВ И МЕХАНИЗМОВ
- •ПРЕИМУЩЕСТВА СООСНОЙ СХЕМЫ НЕСУЩИХ ВИНТОВ ВЕРТОЛЕТА
- •РАЗРАБОТКА ЖИДКОСТНОГО РАКЕТНОГО ДВИГАТЕЛЯ МАЛОЙ ТЯГИ ДЛЯ РАКЕТ СВЕРХЛЕГКОГО КЛАССА
- •Т.А. Башарина; В.С. Левин, В.В. Меньших, А.К. Ильина, В.С.Носова; Д.П. Шматов, канд. техн. наук
- •СХЕМЫ УПРАВЛЕНИЯ НЕСУЩИМИ ВИНТАМИ ВЕРТОЛЕТОВ И ИХ ОСОБЕННОСТИ
- •УСТРОЙСТВО ДЛЯ АНАЛИЗА РЕЗОНАНСНЫХ МОД КОЛЕБАНИЙ ЭЛЕМЕНТОВ КОНСТРУКЦИЙ
- •РАЗРАБОТКА БЕСПИЛОТНОГО СЕЛЬСКОХОЗЯЙСТВЕННОГО ЛЕТАТЕЛЬНОГО АППАРАТА
- •КОЭФФИЦИЕНТ ЗВУКОПОГЛОЩЕНИЯ ЗВУКОПОДАВЛЯЮЩИХ ОБЛЕГЧЁННЫХ СТРУКТУРИРОВАННЫХ ПАНЕЛЕЙ (ЗОСП)
- •АЛЬТЕРНАТИВНАЯ ПАРАШЮТНАЯ СИСТЕМА СПАСЕНИЯ ДЛЯ ЛЁГКОГО САМОЛЁТА
- •С.В. Фомин, студент; Е.Н. Некравцев, канд. техн. наук
- •ИССЛЕДОВАНИЕ МАССО-ЦЕНТРОВОЧНЫХ ХАРАКТЕРИСТИК СЕЧЕНИЙ
- •ОСОБЕННОСТИ ПОСТРОЕНИЯ АДАПТИВНЫХ СИСТЕМ УПРАВЛЕНИЯ СОВРЕМЕННЫХ САМОЛЕТОВ
- •С ЭТАЛОННОЙ МОДЕЛЬЮ
- •Рисунок 2 − Схема измерения по методу вписанной окружности
- •К ВОПРОСУ О МОДЕЛИРОВАНИИ ДИНАМИКИ НЕСУЩЕЙ СИСТЕМЫ ВЕРТОЛЕТА
- •АНАЛИЗ РАЗРАБОТОК В ОБЛАСТИ АВТОМАТИЗАЦИИ МОДЕЛИРОВАНИЯ ПРОЦЕССОВ ОМД
- •ПРОГРАММНО-МОДЕЛИРУЮЩИЙ КОМПЛЕКС ДЛЯ ОЦЕНКИ ХАРАКТЕРИСТИК ПИКИРОВАНИЯ САМОЛЕТА
- •АНАЛИЗ ВОЗМОЖНОСТЕЙ МОДЕЛИРОВАНИЯ УПРАВЛЯЮЩИХ ДЕЙСТВИЙ ЛЕТЧИКА ПРИ ДЕСАНТИРОВАНИИ МОНОГРУЗОВ
Military training and research center of the air force "Air force Academy"
STUDY OF DYNAMIC CHARACTERISTICS OF STEERING GEAR HYDRAULIC SYSTEM USING THE SOFTWARE PACKAGE MATLAB@SIMULINK
V.G. Razboynikov, I.A.Fedorkevich,
The article presents the results of a study of a two-chamber steering drive. The data were obtained using the software complex Matlab@Simulink.
Key words: hydraulic system, dynamic characteristics, two-chamber steering drive.
УДК 621.73
АНАЛИЗ РАЗРАБОТОК В ОБЛАСТИ АВТОМАТИЗАЦИИ МОДЕЛИРОВАНИЯ ПРОЦЕССОВ ОМД
1Л.И. Тищук,канд.техн.наук; 1К.Н. Соломонов, д-р техн. наук; 1В.В. Орлов, канд. техн. наук; 2Е.А. Листров, канд. ф.-м. наук 1Филиал Ростовского госуниверситета путей сообщения в г. Воронеж 2Воронежский государственный аграрный университет
Проведен анализ разработок в области автоматизированного проектирования процессов обработки металлов давлением. Обоснована целесообразность создания специализированных программных комплексов для моделирования пластического формоизменения заготовок.
В настоящее время перспективным направлением развития транспортного машиностроения является оптимизация процессов производства металлических изделий, разработка и совершенствование способов моделирования процессов проектирования и получения деталей различного назначения, в том числе и процессов обработки металлов давлением (ОМД). В связи с этим в литературе широко освещаются вопросы улучшения качества получаемых изделий и повышения их технологичности.
При обработке металлов давлением на качество изделий, а, следовательно, и на разработку технологических процессов существенное влияние оказывает распределение напряжений на
437
поверхности контакта инструмента и заготовки. На практике применяется способ определения контактных напряжений между двумя поверхностями с помощью пластически деформируемой измерительной прокладки. Повышение точности определения контактных напряжений достигается за счет измерения толщины прокладки непосредственно в нагруженном ее состоянии. Одним из способов измерения этой толщины является применение эхоимпульсного метода ультразвукового контроля [1]. При определении контактных напряжений в процессах осадки в условиях плоской деформации широко применяется и инженерный метод. Решение системы уравнений равновесия сегодня получено только для зоны торможения, для зон скольжения и застоя используются либо численные методы, либо приближенные решения, при этом вносится ряд допущений, что существенно снижает точность расчетов. Для аналитического расчета контактных напряжений, подчиняющихся закону трения Кулона, при осадке прямоугольной полосы создана специальная методика и на ее основе проведено уточнение существующих зависимостей для определения усилия осадки. Указанная методика значительно упрощает аналитическое решение и может быть использована, например, для расчета напряженного состояния при прокатке полосы, а также при выдавливании цилиндрической заготовки через клиновую или коническую матрицу.
Для новых технологий ковки при назначении режима протяжки необходимо учитывать формирование и развитие зон пластического течения в сечении заготовки. Для решения указанной задачи построена модель горячей протяжки стальных цилиндрических заготовок небольшого (до 300 мм) диаметра в кузнечном прессе с комбинированными бойками для получения поковок круглого сечения.
В порошковой металлургии наряду с численными методами для моделирования процесса горячей штамповки пористых заготовок на разных стадиях деформирования в закрытом и открытом штампах, который имеет много общего с классическими методами объемной штамповки, используется метод координатных сеток. Исходные заготовки прямоугольной в плане формы с центральным отверстием прессуют из порошка железа и спекают в среде проточного водорода. Спеченные заготовки разрезают в продольном направлении вдоль оси
438
прессования и на поверхность разреза наносят координатную сетку. Затем половинки образцов соединяют точечной сваркой, нагревают и штампуют на прессе с разными степенями деформации. После каждого этапа деформирования половинки образцов разъединяют и сканируют изображения координатной сетки деформированных образцов для ее дальнейшей цифровой компьютерной обработки. Затем определяют координаты узлов сетки, и на их основе рассчитывают компоненты тензора деформаций.
При периодической прокатке важным моментом в определении параметров мгновенного очага деформации является определение смещаемого валком объема металла, а также определение мгновенного и полного смещения исходного контура. В связи с этим разработана методика теоретического определения параметра геометрии очага деформации, позволяющая получать значения длины дуги контакта по всей зоне обжатия. Указанная методика позволяет также находить коэффициенты напряженного состояния при расчете энергосиловых параметров процесса при деформации полосового металла на маятниковом стане.
Одним из наиболее эффективных направлений оптимизации процессов производства металлических изделий в транспортном машиностроении и совершенствования способов моделирования процессов ОМД является разработка новых методик компьютерного моделирования.
Создание адекватных компьютерных моделей технологических процессов ОМД производилась до недавнего времени каждым исследователем самостоятельно, поэтому выбирался свой вариант постановки задачи, а на создание алгоритма, разработку, отладку и тестирование программного обеспечения зачастую уходили годы труда целого коллектива. С развитием средств вычислительной техники и снижением стоимости сертифицированного программного обеспечения для компьютерного моделирования все чаще стали применяться специальные CAD/CAE-системы [2, 3], такие, как ANSYS, ABAQUS, MARS, DEFORM и др., позволяющие выбрать не только материал из стандартной библиотеки комплекса, но и вариант постановки краевой задачи. Построение компьютерных моделей с использованием современных программных комплексов (ПК) позволяет решать разноплановые задачи: во-первых, разработки
439
технологических процессов обработки давлением перспективных конструкционных материалов в состоянии сверхпластичности, а вовторых, расчета параметров геометрии очага деформации.
Сегодня созданы мощные программные продукты, основанные на использовании метода конечных элементов (МКЭ), позволяющие моделировать полный цикл изготовления изделия, включая выполнение комплекта чертежной документации, проектирование технологических процессов и прогнозирование его показателей, а также осуществлять имитационное моделирование действующих при эксплуатации детали нагрузок, определять опасные зоны, допустимые нагрузки и вид разрушения. При этом анализ виртуального производства дает возможность выявлять ошибки и возможные дефекты в изделиях еще на стадии проектирования, что приводит к повышению качества продукции и эффективности производства.
Проектирование 3D-моделей штампового и кузнечного оборудования средствами CAE-систем не всегда поддается автоматизации и представляет собой процесс, который в зависимости от производственной практики во многом определяется опытом конструкторов и технологов. В связи с этим в настоящее время разрабатываются различные системы автоматизированного проектирования (САПР). Например, для объемной штамповки компрессорных лопаток авиационных двигателей из титановых сплавов применяется САПР штамповой оснастки, в которой сочетается классический процесс автоматизированного определения геометрии штампа с возможностью его коррекции средствами CAEсистем.
При штамповке деталей из сплавов, имеющих узкий допустимый температурный интервал деформирования, особенно важно предупредить возникновение брака в результате деформационного разогрева. Штамповая оснастка для мощных гидравлических штамповочных прессов, применяемых для штамповки алюминиевых сплавов, отличается большой массой, а изготовление гравюры штампа
– высокой трудоемкостью. Различные приемы для обеспечения точности изготовления штампа и повышения качества приводят к росту себестоимости поковок. Поэтому при разработке технологических процессов горячей объемной штамповки поковок из
440
алюминиевых сплавов используются мощные ПК DEFORM-3D, SolidWorks и SuperForge.
Важным способом повышения качества и конкурентоспособности продукции является интеграция существующих на предприятиях САПР в единую функциональную систему, с учетом взаимосвязи на этапах проектирования и разработки с другими системами.
Современные ПК, основанные на МКЭ, позволяют довольно точно моделировать различные процессы, но на практике часто требуется определять форму заготовок, порядок и режимы их нагрева для получения деталей с заданной геометрией и свойствами. Недостатком рассмотренных ПК является невозможность достижения требуемой точности размеров и формы получаемых деталей, несмотря на различные существующие способы обработки. К недостаткам также можно отнести: достаточно высокие требования к параметрам компьютерной техники, сложность и низкую скорость создания файла входных данных, длительность обучения пользователей, а также значительное время расчета и моделирования одного варианта. Например, процесс штамповки в системе SolidWorks может моделироваться несколько часов, хотя в результате такого моделирования будет получено векторное поле течения частиц металла. К тому же такие системы достаточно дороги.
В некоторых случаях, особенно на стадии проектирования и предварительного анализа технологии производства поковки целесообразно применять специализированные ПК, ориентированные на моделирование одного-двух процессов ОМД (например, получения поковок в процессах объемной штамповки и ковки). Такие ПК имеют ряд преимуществ: они просты, не требуют специальной подготовки пользователей, время расчета одного варианта незначительно. В последние годы область применения специализированных ПК активно расширяется: к «традиционным» самолето- и ракетостроению присоединяются автомобилестроение и вагоностроение.
В связи с этим ряд исследователей пришли к решению о необходимости создания собственных специализированных ПК, ориентированных на узкие конкретные задачи и лишенных недостатков мощных программных продуктов. Так, группой исследователей под руководством проф. К.Н. Соломонова был разработан простой и удобный специализированный программно-
441
технический комплекс Parshtamp [4], предназначенный для моделирования пластического формоизменения плоских заготовок.
В продолжение этих разработок создан усовершенствованный специализированный ПК EQUI, позволяющий моделировать не только картину течения металла для одноконтурных поковок в процессах, где наблюдается деформационная схема осадки [5, 6], с учетом сил трения [7], но и производить расчет многоконтурных поковок, а также визуализировать пространственную эпюру контактных давлений на всех стадиях осадки, в любом ракурсе.
Разработанный ПК EQUI быстр, прост, не требователен к характеристикам компьютерной техники. Создание файла входных данных занимает несколько минут, расчет одного варианта – несколько секунд. Высокая скорость расчетов достигается благодаря упрощению математической модели и исходной системы уравнений. Это сужает круг решаемых задач и процессов ОМД, зато дает возможность свести систему дифференциальных уравнений, описывающих напряженно-деформированное состояние материала, к несложным аналитическим зависимостям.
Благодаря указанным преимуществам разработанный ПК может успешно использоваться там, где требуются экспресс-анализ картины течения металла и быстрая оценка пластического формоизменения заготовки.
Литература 1. Тищук Л.И., Соломонов К.Н. Применение неразрушающего
контроля в процессах производства и эксплуатации транспортных систем // Авиакосмические технологии (АКТ-2013): труды XIV Всероссийской научно-технической конференции. – Воронеж: Элист, 2013. – С. 287-291.
2.Solomonov K.N. Application of CAD/CAM systems for computer simulation of metal forming processes // Materials Science Forum, 2012, v. 704-705, s. 434-439.
3.Соломонов К.Н. Автоматизированное проектирование инструмента и технологий объемной штамповки // Кузнечноштамповочное производство. ОМД, 2003, № 8, с. 42-48.
442
4.Соломонов К.Н., Федоринин Н.И., Тищук Л.И. Моделирование технологических методик пластического деформирования // Изв. Самарского НЦ РАН, 2017, № 1, с. 517-519.
5.Тищук Л.И., Соломонов К.Н., Мазур И.П. и др. Исследование картины течения металла при осадке // Вестник Магнитогорского
государственного технического университета им. Г.И. Носова, 2017,
№3, с. 37-44.
6.Соломонов К.Н., Федоринин Н.И., Тищук Л.И. Методика
построения линии раздела течения металла в процессах осадки плоских заготовок // Вестник научно-технического развития, 2016, № 2, с. 36-55.
7. Тищук Л.И., Соломонов К.Н. Влияние трения на формоизменение плоской заготовки // Изв. вузов. Черная металлургия, 2018, № 3, с. 251-253.
1Branch of Rostov State University of Railway Engineering in Voronezh 2Voronezh State Agrarian University
ANALYSIS OF DEVELOPMENT IN THE FIELD
OF AUTOMATION SIMULATION
OF METAL FORMING PROCESSES
1L.I. Tishchuk, 1K.N. Solomonov, 1V.V. Orlov, 2E.A. Listrov
The analysis of developments in the field of computer-aided design of metal forming processes. Justified the feasibility of creating specialized software complexes for simulation plastic forming of workpieces.
Key words: metal forming, computer model, software complex, CAEsystem.
УДК 621.73
НЕКОТОРЫЕ АСПЕКТЫ МЕТОДИКИ КОМПЬЮТЕРНОГО МОДЕЛИРОВАНИЯ
ФОРМОИЗМЕНЕНИЯ ПЛОСКИХ ЗАГОТОВОК
Л.И. Тищук, канд. техн. наук; Н.И. Федоринин, канд. техн. наук Филиал Ростовского госуниверситета путей сообщения в г. Воронеж
Представлены результаты компьютерного и физического моделирования формоизменения плоских заготовок цилиндрической и призматической формы на основе предложенной авторами методики.
443
Сегодня остаются актуальными вопросы производства сложноконтурных поковок из плоских заготовок для разных отраслей машиностроения, в том числе и для авиакосмической промышленности. Дорогостоящее производство качественных поковок встречает ряд трудностей, связанных с образованием различных дефектов.
САЕ-системы, используемые для моделирования процессов пластической деформации, базирующиеся в основном на методе конечных элементов [1], имеют некоторые недостатки (высокие требования к компьютерной технике, значительное время расчета, сложность создания файла входных данных), которые являются побочным эффектом их универсальности [2].
В связи с этим целесообразно создание специализированных ПК, предназначенных для решения ограниченного круга задач, например, для экспресс-анализа картины течения металла по полотну заготовки в процессах ковки и объемной штамповки [3], лишенных недостатков универсальных программных комплексов (ПК).
В основе таких ПК лежат алгоритмы, базирующиеся на закономерностях пластического течения металла по полотну плоской заготовки, которые подчиняются кинематическим схемам течения металла (КСТМ).
Традиционно рассматриваются две КСТМ, которые можно считать классическими: нормальная Головина и радиальная Тарновского [4]. В нормальной схеме линии тока (ЛТ) направлены по нормали к контуру заготовки, а в радиальной – по радиусам окружности. Тогда в соответствии с нормальной КСТМ прямоугольная пластина в ходе осадки превращается в многоугольник; в соответствии с радиальной – пластина остается прямоугольной и после осадки. Обе схемы противоречивы, т.к. не объясняют так называемые «эллипсность» и «ушки», которые наблюдаются в реальных процессах.
В процессах пластической деформации, при условиях трения, близких к реальным, течение металла подчиняется некоторой «псевдонормальной» КСТМ, в соответствии с которой ЛТ направлены перпендикулярно не к действительному, а к «условному контуру». С таким же успехом «псевдонормальную» КСТМ можно считать радиальной, поскольку ЛТ направлены по радиусам окружности,
444
которая аппроксимирует с достаточной точностью «условный контур».
Виртуальные эксперименты доказывают, что на КСТМ существенное влияние оказывает трение [5]. С увеличением трения наблюдается переход от радиальной схемы к нормальной, что косвенно подтверждает обоснованность псевдонормальной КСТМ.
Изучение формы деформированных прямоугольных пластин, используемых в указанных экспериментах, позволяет констатировать, что псевдонормальной можно считать КСТМ для всего процесса формоизменения, т.к. и реальный контур также аппроксимируется кривой второго порядка, в частности, окружностью.
Анализ зависимости КСТМ от начальной толщины заготовки и фактора трения позволяет сделать вывод, что и для тонких, и для толстых пластин она описывается показательной функцией.
Для моделирования картины течения металла [6] по плоскости контакта в процессах ковки и объемной штамповки предлагается так называемая «эквидистантная теория» («экви-теория»), основанная на трех известных принципах, реализованных в разработанных нами методике [7], алгоритмах и программном комплексе EQUI.
Алгоритмы сформированы с учетом того, что большинство деталей, применяемых в машиностроении, ввиду требований к технологичности конструкции, состоят из поверхностей вращения и многогранников. Кроме этого, подавляющее большинство заготовок многоконтурные. Ядром программного комплекса EQUI служит алгоритм построения эквидистанты, реализованный в среде визуального программирования DELPHI.
С целью изучения картины течения металла (КТМ) проведено моделирование процесса осадки плоских заготовок [8], представляющих собой в плане односвязные контуры различной конфигурации.
Исходя из анализа КТМ для односвязных контуров, можно сделать вывод, что центральные зоны заготовок, состоящих из дуг окружностей и внутренние зоны вогнутых дуг будут формироваться более активно, т.к. в этих зонах ожидается наиболее интенсивное течение металла, наименее интенсивного формообразования следует ожидать в угловых зонах, где движение частиц вдоль ЛТ менее
445
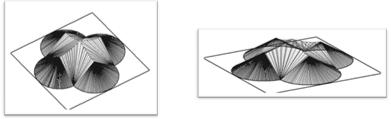
интенсивное. Анализ КТМ позволяет предположить, что заготовки в ходе деформации по форме будут приближаться к кругу.
Разработанный ПК EQUI позволяет строить пространственную эпюру контактных давлений (ПЭКД) для любых по сложности и по форме многосвязных контуров. При этом наглядность получаемого изображения обеспечивается благодаря «прозрачности» моделируемых поверхностей. Вместе с тем, удобство анализа формы ПЭКД заключается в возможности рассмотрения полученных поверхностей с разных ракурсов (рисунок 1).
Рисунок 1 - Модели эпюры контактных давлений
Для подтверждения результатов, полученных с помощью ПК EQUI, были проведены лабораторные эксперименты на пластилиновых образцах. Пластилин дешевле и «пластичнее» по сравнению с другими материалами, для его формоизменения не требуется дорогостоящее оборудование. Вопрос лишь в правомерности его использования для моделирования процессов горячей объемной штамповки и ковки.
Ранее по результатам экспериментов И.Я. Тарновского было доказано, что материал не оказывает существенного влияния на формообразование поковки в процессах осадки. К тому же С.И. Губкин отмечал, что в качестве материала для моделирования горячей штамповки возможно использование различных пластичных масс. Поэтому пластилин издавна признан исследователями как один из наиболее подходящих, удобных и дешевых материалов для моделирования процессов ОМД. Кроме того, сравнение результатов проведенных нами экспериментов на свинцовых и пластилиновых образцах показывает, что формоизменение пластилина аналогично
446
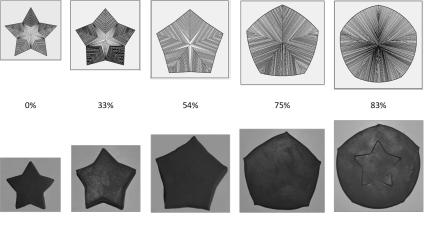
формоизменению свинца. Сопоставление результатов, полученных с помощью ПК EQUI и в ходе лабораторных экспериментов, дает их практически полное совпадение (рисунок 2).
Рисунок 2 - Сопоставление результатов компьютерного и физического моделирования
Для полноты картины и подтверждения базовых принципов, положенных в основу «экви-теории», была проведена экспериментальная проверка принципа наименьшего периметра. В дополнение и расширение области исследований, выполненных предшественниками на многократно изученных, тривиальных цилиндрических и призматических образцах с квадратным и прямоугольным основанием, проведены эксперименты на плоских заготовках в форме произвольного многоугольника в плане. Анализ результатов подтверждает принцип наименьшего периметра: любая форма поперечного сечения призматического или цилиндрического тела при осадке его в пластическом состоянии с наличием контактного трения стремится принять форму, имеющую при данной площади наименьший периметр, т.е. в пределе стремится к кругу.
С целью апробации разработанного ПК EQUI на более сложных по форме заготовках с криволинейными участками проведено
447
моделирование КТМ при осадке плоских заготовок, имеющих форму «звезда» и «четырехлистник». Анализ КТМ на начальной стадии осадки показывает, что наиболее интенсивного течения металла следует ожидать во внутренних угловых точках, т.к. в них сходится пучок линий тока, а вдоль контура с гладкими участками линии тока распределены равномерно. Результаты лабораторных экспериментов подтверждают анализ КТМ, полученный при помощи ПК EQUI.
Для анализа зависимости формоизменения плоской заготовки от начальной толщины образца проведены теоретические и экспериментальные исследования, из которых следует, что форма «тонкого» и «толстого» образцов при одинаковой степени
деформации почти полностью совпадает. |
А |
из полученных |
аналитических соотношений следует, что площадь |
образца в ходе |
|
деформации не зависит от начальной толщины. |
|
|
С целью апробации разработанной методики и обоснования рекомендаций по улучшению технологии производства поковок, а также для иллюстрации основных закономерностей формоизменения
и построения КТМ |
на |
ПАО |
«Воронежское |
акционерное |
самолетостроительное |
общество» |
выполнено |
компьютерное |
моделирование формообразования серийной поковки. По результатам моделирования предложены конкретные рекомендации.
Литература
1. Solomonov K.N. Application of CAD/CAM systems for computer simulation of metal forming processes // Materials Science Forum, 2012, v. 704-705, s. 434-439.
2.Соломонов К.Н. Автоматизированное проектирование инструмента и технологий объемной штамповки // Кузнечноштамповочное производство. ОМД, 2003, № 8, с. 42-48.
3.Лисунец Н.Л., Соломонов К.Н., Цепин М.А. Объемная
штамповка алюминиевых заготовок. – М.: Машиностроение, 2009. –
172с.
4.Костарев И.В., Соломонов К.Н. Обоснование введения радиальной схемы течения металла в процессах штамповки тонкостенных ребристых деталей из алюминиевых сплавов // Изв.
вузов. Машиностроение, 2000, № 3, с. 62-65.
5. Тищук Л.И., Соломонов К.Н. Влияние трения на
448