
Титов В.В. - Современные проблемы менеджмента
.pdf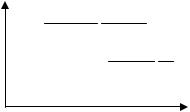
Оптимизация расписаний
Правило Джонсона (1956 г.) для работ на двух станках. Это простейший вариант – главное, чтобы не было простоя второго станка. Добиться этого можно, если на каждом шаге построения графика учитывать следующее правило: на первом (на втором) станке в первую очередь (в последнюю очередь) фиксируется работа с наименьшей длительностью операции (рис. 46).
1 |
|
|
|
|
|
работы по операциям |
|
|
|
|
|
|
|||
станки |
|
|
|
|
|
|
|
|
|
|
|
|
|
|
|
|
|
|
|
|
|
|
|
2 |
|
|
|
|
|
|
|
|
|
|
|
|
|
|
время
Рис. 46. Оптимальный график выполнения работ на двух станках
Для ситуаций с тремя и более станками оптимальное расписание построить не удается, доказанного алгоритма нет. Данная задача календарного планирования, как задача исследования операций, остается алгоритмически не решенной до сих пор, хотя имеется много приближенных алгоритмов, а самый простой – перебор.
Впервые постановка задачи календарного планирования осуществлена С. А. Соколицыным [33].
На практике же все сложнее. В чистом виде задачи календарного планирования нет. На участке производства происходит непрерывное изменение условий – появляются каждую смену новые партии деталей (новые работы), график пересматривается и т. д. Систему оперативного управления производством рассмотрим в дальнейшем.
Экспертные системы составления расписания (ЭС), или системы искус-
ственного интеллекта, являются компьютерными программами. Объединение ЭС в 1984 г. под названием ISIS – интеллект расписания и информационной системы, 1986 г. – OPIS – удобного составителя расписаний – заводская система. MARS – управление анализом расписания ресурсов, используется для создания космической системы «Челнок» NASA.
Программа General Electric выдает расписание с назначением работ по рабочим местам по дням, часам и рабочим, загрузку оборудования с указанием простоев.
Две компьютерные системы работают достаточно эффективно и известны под названием «оптимизированные производственные технологии» (ОРТ) и «Q-контроль». Обе системы закрыты (точнее, их программное обеспечение)
[35; 87; и др.].
ОРТ выявляет «узкие места», используя загрузочные расписания для всех групп оборудования (рабочих центров). Применяется математическое программирование и сетевое планирование, моделирующие алгоритмы расписывают производственный процесс на узких местах рабочих центров. Узкие места – это
200
операции, лимитирующие ход производственного процесса. Используются алгоритмы расшифровки узких мест. Интересны 10 заповедей данной системы.
1.Ресурсы рабочих мест, не являющиеся узкими, не влияют на мощности участка, цеха.
2.Задействование ресурса не является синонимом использования ресурсов.
3.Час, потерянный в «узком месте», есть час, потерянный во всей системе.
4.Час, сэкономленный не в «узком месте», есть мираж.
5.Процесс перемещения партии деталей не есть процесс обработки.
6.Процесс обработки партии деталей должен быть изменяем.
7.Мощность рабочего центра и приоритет работы необходимо рассматривать одновременно.
8.Случайное воздействие неизвестно, но оно может быть изолировано и минимизировано.
9.Заводская мощность не должна балансироваться.
10.Сумма локальных оптимумов не есть глобальный оптимум.
«Q-контроль» аналогичен «ОРТ» и дает хорошие результаты для сложных производственных условий. Разработчики изучили работу 600 цехов. Работа одного цеха моделируется каждый вечер, определяются узкие места, затем через них составляется расписание. Эффект – вдвое уменьшается длительность производственного цикла (ДПЦ) и простои оборудования.
Составление расписаний для серийного производства аналогично рассмотренному для единичного и мелкосерийного. Но в производственном процессе рассматривается длительности обработки не деталей, а партий деталей оптимального, экономического размера. В массовом производстве система «Канбан» уменьшает партии до минимума, а подача материалов и полуфабрикатов «точно вовремя» приводит к минимуму уровней запасов и незавершенному производству.
5.3. Концептуальное представление системы оперативного управления производством
Влияние системы оперативного управления производством на экономику предприятия представлено на рис. 47.
Исследование существующей системы ОУП приводят к следующему выводу. Для того, чтобы уйти от проблемы оперативного управления производством, необходимо организовать производство на принципах полной автоматизации и специализации участков производства. Тогда технологический процесс будет представлен множеством непересекающихся потоков движения деталей по операциям. Пересечение – на сборке.
Технологическая синхронизация устраняет проблему календарного планирования, но требует значительных капитальных вложений и ориентирована на массовый выпуск продукции.
201

Затраты |
Капвложения (КВ) |
|
Тек + Е × КВ, Е – норма прибыли
Приведенные затраты
Текущие издержки (Тек)
Обычные системы ОУП
Согласование |
«Канбан» |
Степень |
согласо- |
|
планов-графиков |
ванности техноло- |
|||
|
||||
произв-ва c по- |
|
гического |
процес- |
|
мощью ЭММ и |
|
са, автоматизация |
||
ЭВМ, MRP |
|
производства |
Рис. 47. Влияние системы оперативного управления на экономику предприятия
Такое производство трудно диверсифицировать при необходимости. В условиях, когда на промышленном предприятии нет средств на подобную автоматизацию, следует создать самонастраивающуюся систему, организованную на лучших элементах действующих систем, ориентированную на прогнозный и фактический спрос, стремящуюся постепенно, по мере совершенствования организации, автоматизации производства, к системам типа «Канбан» и «Точно в срок». При этом согласование маркетинговых исследований с системой ОУП может приближенно осуществляться на основе непрерывной корректировки функции спроса в самой системе ОУП. В соответствие стохастичности спроса определяются страховые запасы.
Концептуальное представление системы оперативного управления производством на основе использования моделей оптимизации и имитации
Повышение эффективности системы ОУП может быть осуществлено за счет использования в ней моделей оптимизации и имитации. Концептуально такая система может быть представлена следующим образом [33; 68; 69; 73].
Верхний уровень:
–оценка прогнозного платежеспособного спроса на 1–2 года;
–оценка платежного спроса на текущий горизонт планирования с учетом уже поступивших фактических заказов (горизонт планирования не меньше длительности производственного цикла);
202

–решение задачи объемно-календарного планирования (ОБКП) по распределению заказов по календарно-плановым периодам, техникоэкономических и финансовых показателей;
–формирование плана-графика суточного выпуска готовой продукции на сборке под обеспечение откорректированного спроса с учетом страховых запасов на сборке.
Межцеховой уровень:
–межцеховое (и межфирменное для объединений) оперативнокалендарное планирование (ОКП);
–согласование планов-графиков выпуска продукции по цехам и участкам производства (а также между фирмами объединения, корпорации), по внешней кооперации;
–планирование потребностей в ресурсах.
Уровень цеха, участка:
–оперативное управление на участках производства, построение сменносуточного графика работ по операциям технологического процесса;
–оперативный учет, согласование планов со службами материальнотехнического снабжения, подготовки производства.
5.4. Корректировка прогнозного спроса
Корректировка прогнозного спроса в системе ОУП представлена на рис. 48.
Спрос
Ранее заданный спрос
Возможные отклонения
Откорректированный спрос Отклонения
Фактический
спрос
Прошед- |
Горизонт |
Периоды |
ший пери- |
планирова- |
|
од |
ния |
|
Рис. 48. Корректировка прогнозного спроса
Суть корректировки заключается в том, что на основе фактического уровня спроса за период, примерно равный времени, на которое формируется прогноз, изменяется прогнозный уровень спроса (но характер его сохраняется).
203
При этом на основе данных, имевших место за прошедшие периоды, уточняется уровень возможных отклонений факта от прогноза.
Таким образом, на горизонт планируемого периода фиксируется прогнозный спрос – bi (например, на ближайший квартал) по изделию i.
5.5. Задача объемно-календарного планирования
Задача объемно-календарного планирования (ОБКП) для машиностроительного производства с длительностью цикла не более месяца может быть записана так:
|
|
|
min S |
при условиях: |
|
|
|
|
|
3 |
|
|
|
xiμ |
= bi, i I; |
|
|
μ = 1 |
|
|
|
аji xiμ – S Mjμ |
≤ 0, j J, μ = 1, 2, 3; |
|
|
i |
|
|
сgi xiμ – S Вrμ |
≤ 0, g G, μ = 1, 2, 3; |
|
|
i |
|
|
|
|
S ≥ 1, xiμ ≥ biμ, xiμ ≥ 0. |
|
Здесь aji – |
затраты мощности группы оборудования j на выпуск единицы про- |
||
дукции i; |
|
|
|
Mjμ = aji bi λμ , |
j J, μ = 1, 2, 3; |
||
|
i |
|
|
Mjμ |
– желаемый |
уровень использования мощностей по месяцам кварта- |
|
ла; |
|
|
|
λμ – |
уровень распределения эффективного времени работы оборудования |
по месяцам квартала;
Вgμ – желаемый уровень прямых издержек вида g G по месяцам кварта-
ла;
Вgμ = сgi bi λμ , g G, μ = 1, 2, 3;
i
сgi – прямые затраты основной заработной платы (g = 1) и материальных ресурсов вида g G, g ≠ 1, на единицу продукции i;
biμ – объем обязательных поставок продукции i |
в месяце μ; |
|
S – 1 |
– относительное максимальное отклонение фактических затрат |
|
мощности, |
основной заработной платы, ресурсов от |
«идеального» плана. |
Расчетное значение S, на 3–5 % отличающееся от 1, вполне приемлемо для практики, в которой неритмичность производства и затрат может достигать 30–40 %, что приводит к росту издержек на 3–5 %.
Задача объемно-календарного планирования позволяет распределить про-
204
изводственную программу выпуска продукции по планируемым периодам с учетом спроса в эти периоды, минимизируя отклонения загрузки оборудования, других технико-экономических показателей от равномерных во времени. Для производства желательно реализовать стратегию равномерного производства продукции и использования ресурсов. Именно такая стратегия обеспечивает минимум затрат.
Для различных производств подобная задача может уточняться. Особенно она важна для предприятий с большой ДПЦ. В этом случае необходимо задавать вектора затрат во времени по каждому изделию. В ограничениях задачи важнейшим фактором также становится время. Как это делается, мы рассмотрим на примере постановки оптимизационной модели оперативнокалендарного планирования. Очень важно отметить, что чем точнее постановка задачи объемно-календарного планирования (выбор минимальной единицы времени, представление технологического способа затрат во времени по продукции и т. п.), тем проще будет процесс принятия решений на последующих этапах принятия решений в системе ОУП.
5.6. Информационное согласование объемно-календарного и оперативно-календарного планирования
Решение задачи ОБКП xit трансформируется в xitr, i I, r R = 1, …, R*, т. е. плановому выпуску готовой продукции в периоде t ставится в соответствие план-график выпуска готовой продукции по рабочим дням r. При этом xitr задаются таким образом, чтобы равномерно по трудоемкости загрузить сборочные участки. В первую очередь в плане-графике сборки учитывается та продукция, на которую уже имеются договоры о поставках.
Горизонт планирования.
Пусть ДЦП не превышает одного месяца, следовательно, в периоде t формируется план-график выпуска готовой продукции на месяц t + 2 (рис. 49). В базовом периоде t = 0 уже осуществляется создание незавершенного производства для выпуска готовой продукции как в месяце t = 0, так и в t = 1. Горизонт же планирования расширяется за счет подключения периода t = 2. Как показано на рис. 49, согласование планов-графиков хода производства может быть осуществлено достаточно просто: под выпуск готовой продукции в периоде t = 2 в последовательности, обратной технологической, формируется график движения партий деталей по цехам, участкам, операциям.
Как показано на рис. 49, при ДПЦ около месяца процесс планирования производства затрагивает три смежных месяца. При этом если на месяц t = 2 портфель заказов еще не сформирован полностью, то производство ориентируется на прогнозный спрос, посколько из-за ДПЦ уже в периоде t = 0 приходится планировать производство, обеспечивать его материальными ресурсами, инструментом и др.
205
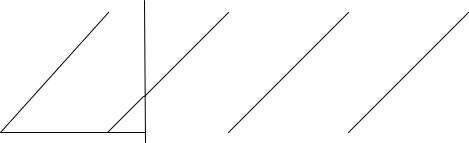
Базовый период t = 0 |
t = 1 |
t = 2 |
||||
|
|
|
|
|
|
|
|
Планы-графики |
хода |
|
|||
|
производства под выпуск |
|
||||
|
|
готовой продукции, |
|
|||
|
|
планирование |
|
|||
|
|
потребностей |
|
|||
|
|
|
|
|
||
Текущий |
|
|
|
|||
момент |
|
|
|
|||
времени |
|
|
|
|||
Рис. 49. Согласование планов ОКП во времени |
|
Формирование плана потребности сборки в деталях.
Пусть xir = xitr, t = 2 в рассматриваемом случае. Тогда, зная входимость θik
деталей k в изделие i, определяется потребность сборки в деталях, узлах:
Р*kr = θik xir. i
Страховой запас перед сборкой определен опережением в днях – Оk, отсюда
Рkτ = Р*kr , τ = r – Ok .
5.7. Организация межцехового оперативно-календарного планирования
Представим согласование плана производства на сборочных участках с другими участками (рис. 50).
Для периода t = 2 сборочный участок представим в виде календаря рабочих дней. Для каждого рабочего дня задана потребность в готовых деталях и сборочных узлах. Движение предметов труда по операциям технологического процесса до участков сборки осуществляется партиями деталей нормативного, оптимального размера nk. Поэтому от ежесуточной потребности сборки в деталях Рkτ следует перейти к потребности в партиях готовых деталей, сборочных единиц. Каждой партии деталей условно поставим в соответствие ее номер (бирку с номером, чтобы отличать их друг от друга) q = 1, 2, ...
Первая партия готовых деталей k размером nk1 = nk должна быть отправлена на сборку с завершающего участка, с которого готовые детали поступают на склад или сразу на сборку, в период времени Vk1. Зная параметры Рkτ, можно определить, на сколько суток хватит сборке партии деталей k размером nk1. Отсюда определяется следующий плановый срок поступления партии деталей на сборку Vk2.
206
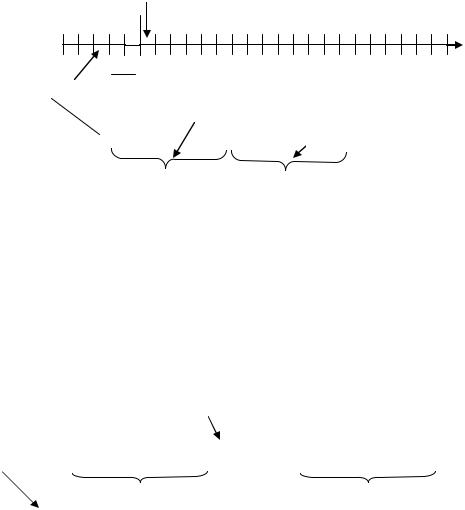
Сборочный участок, t = 2
Р*kr
τ, r
Транспортировка |
Pkτ |
|
Ok |
|
Потребность сборки закрывает |
|||
|
|
|||||||
|
|
|||||||
Завершающий |
|
|
|
|
|
1-я партия деталей, потом |
||
|
|
|
|
|
||||
|
|
|
|
|
||||
участок |
|
|
|
|
|
|
|
2-я и т. д. |
|
|
|
|
|
|
|
||
|
|
|
|
|
|
|||
|
|
|
|
|
|
|
|
… |
|
|
|
|
|
|
|
|
|
Выпуск |
|
|
|
|
|
n k1 |
|
n k2 |
|
|
|
|
|
||||
первой партии |
Vk1 |
|
|
|
|
|
|
|
деталей |
|
|
|
|
|
|
|
|
|
|
|
|
|
|
|
V k2 |
Рис. 50. Согласование сборочного процесса с другими участками производства
Организация производства на завершающем и других участках представлена на рис. 51.
|
|
|
|
|
|
|
|
Ведущая операция |
|
|
||||||
|
Срок запуска Zkq |
|
|
hkj |
Срок выпуска |
|
Vkq |
|||||||||
|
|
|
|
|
|
|
|
|
|
|
|
|
|
|
|
|
|
|
|
|
|
|
|
|
|
|
|
|
|
|
|
|
|
|
Транспортировка |
|
|
|
|
|
|
|
|
|
||||||
|
Производство |
|
|
|
|
λ kj1 |
|
|
|
|
|
λ kj2 |
|
|
||
|
|
|
|
|
|
|
|
|
|
|
|
|||||
|
|
|
|
|
|
|
|
|
|
|
|
|||||
|
|
|
|
|
|
|
|
|
|
|
|
|
||||
|
|
|
|
|
|
|
|
|
|
|
|
|
|
|
|
|
|
на другом участке |
|
Рис. 51. Схема выделения ведущей операции на участке |
|
|
|||||||||||
|
|
|
|
|||||||||||||
|
|
|
|
|
Здесь hkj – продолжительность выполнения ведущей операции партии деталей
kна лимитирующей производство группе оборудования j;
λkj1 – продолжительность обработки партии деталей k на участке с первой
до ведущей операции j;
λ kj2 – продолжительность обработки партии деталей k на участке после выполнения ведущей операции j до выхода с участка;
dk = λ kj1 + hkj + λ kj2 – длительность обработки партии деталей k на участке производства;
Zkq – срок запуска партии деталей на участке производства; Vkq – срок выпуска партии деталей с участка производства.
Традиционные методы ОУП (в том числе MRP) строят планы-графики производства по опережениям (рис. 52).
207
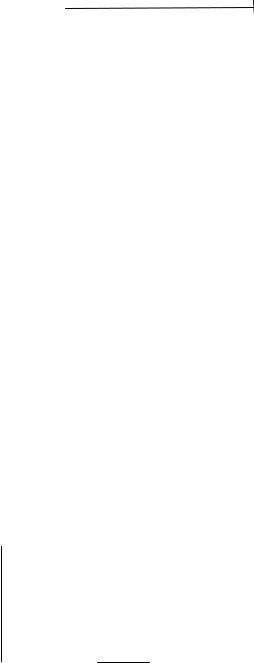
Выпускающий участок
|
|
|
|
|
|
|
|
|
|
|
|
|
|
|
|
|
|
Z3kq |
V3kq |
||
|
|
Z |
|
|
Участок 2 |
|
V2kq |
|
||
|
|
|
|
|
|
|||||
|
|
|
|
|
|
|
||||
|
|
|
2kq |
|
|
|
||||
|
|
|
|
|
||||||
|
|
Участок 1 |
|
|
|
|
|
|
|
|
|
|
|
|
|
|
|
||||
|
|
|
|
|
|
|
|
|
|
|
Z1kq |
V1kq |
|
|
|
|
Рис. 52. Традиционная схема планирования производства по опережениям
Построение плана графика с учетом загрузки ведущих групп оборудования представлено на рис. 53.
Как видим, когда выделяются только ведущие операции, то резко снижается размерность решаемой задачи, появляется возможность учесть загрузку ведущих групп оборудования, партия деталей q = 2 сдвигается во времени так, чтобы не мешать обработке партии деталей q = 1, которая ближе к завершению работ, к сборке (приоритеты могут быть и другими).
Таким образом, на основе моделирования (с использованием имитационной модели оперативно-календарного планирования) производственного процесса строится план-график движения партий деталей по участкам производства и ведущим операциям.
|
|
|
|
|
|
|
λ kj1 |
hkj |
|
λ kj2 |
|
|||||||
|
|
|
|
Zk1 |
|
|
|
|
|
|
|
|
|
|
|
Vk1 |
|
|
|
|
|
|
|
|
|
|
|
|
|
|
|
|
|
|
|||
|
|
|
|
|
||||||||||||||
|
|
|
|
|
|
|
|
|
|
|
|
|||||||
|
|
Zk2 |
|
|
|
|
|
|
|
|
|
Vk2 |
|
|||||
|
|
|
|
|
|
|
|
|
|
|
|
|||||||
|
|
|
|
|
|
|||||||||||||
|
|
|
|
|
|
|
|
|
|
|
|
сдвиг работ во времени |
|
|||||
|
|
|
|
|
|
|
|
|
|
|
|
|
||||||
Zk2 |
|
|
|
|
|
|
|
Vk2 |
|
|||||||||
|
|
|
|
|
||||||||||||||
|
|
|
|
|
|
|
|
|
|
|
|
|
||||||
|
|
Рис. 53. Согласование работ по ведущим операциям |
|
|||||||||||||||
Результат расчетов – график производства: Glkq = {nkq, Zlkq, Vlkq}, |
т. е. для |
|||||||||||||||||
каждой партии деталей задан ее норматив |
– nkq , |
срок запуска Zlkq и |
выпуска |
Vlkq по участкам производства l. При этом график производства построен с учетом загрузки ведущих групп оборудования j.
Указанная постановка оперативно-календарного планирования позволяет сформулировать оптимизационную модель ОУП.
208
5.8. Оптимизационная модель оперативно-календарного планирования
Суть задачи календарного планирования заключается в следующем. Необходимо построить план-график обработки заданного количества (партий) деталей на определенном количестве станков при фиксированной технологии производства. При этом минимизируется общее время выполнения работ или объем незавершенного производства. Это задача межцехового оперативнокалендарного планирования, т. е. производство представлено не участком, а всем предприятием.
Проблема заключается в том, как уже отмечалось, что эффективный алгоритм С. Джонсона обеспечивает оптимальное решение задачи только для производства с двумя группами оборудования. Попытки разработать эффективный алгоритм решения задачи календарного планирования для большей размерности до сих пор не привели к успеху. Задача сведена к целочисленной постановке для решения ее методом отсечения или перебором. Размерность задачи получается столь велика, что это направление исследований имеет только теоретическое значение. Поэтому та постановка задачи календарного планирования, которая будет рассмотрена далее, на наш взгляд, существенно увеличивает возможности математического программирования по решению столь важной для практики проблемы.
Обозначим через xjkqtl целочисленную переменную, принимающую значения 1 тогда, когда планируется выпуск партии q деталей k на ведущей группе
оборудования j в момент времени |
t. Через время λjk2 партия приходит на сле- |
|
дующий участок производства, сборку. Здесь l – |
технологическая последова- |
|
тельность прохождения обработки |
по ведущим |
группам оборудования (по |
участкам производства), l = 1, 2, 3, ..., l*, l* – завершающий этап производства (перед сборкой). Если запуск не планируется, то указанная переменная принимает значение 0.
В модели минимизируется уровень незавершенного производства, который обеспечивает данный производственный процесс. Между таким критерием оп-
тимизации и минимизацией |
общего времени обработки имеется тесная зависи- |
||
мость. Это видно и из самой функции цели: |
|
||
Σ ck ykt + Σ ck (Σ tx jkqtl* |
– Σ tx jkqt1) → min. |
||
k |
k |
t |
t |
Здесь ck – себестоимость детали k;
ck – средняя себестоимость партии деталей k. Необходимо выполнение следующих ограничений.
Сборочный процесс должен быть обеспечен готовыми деталями в соответствии с планом:
t
Σ Σ nkq xjkqτl* – ykt = Вkt, k K, t = 1, 2, 3, ...
τ=1 q
Здесь ykt соответствует величине готовых деталей k, которые находятся в сверхплановых запасах в момент времени t; Вkt – план потребности в деталях k на сборке нарастающим итогом на момент времени t.
209