
технология литейного производства
.pdf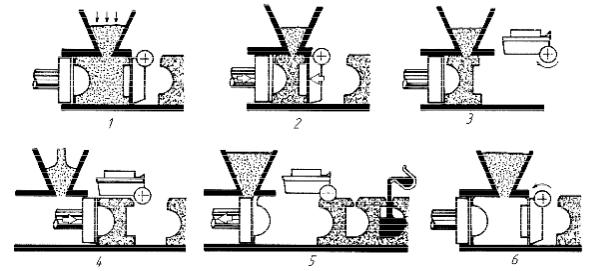
После этого опоки снимают (рис. 32, д), а форму на подопочном щитке ставят на конвейер для заливки. Перед заливкой на форму надевают жакет (рис. 32, е) и сверху кладут груз для предотвращения подъема верхней поло- вины формы под давлением жидкого металла.
Для предотвращения сдвига верхней полуформы относительно нижней,
а также для предупреждения прорыва металла по разъему формы модельные плиты для безопочной формовки обычно делаются с уступом-замком высотой 10 мм и уклоном 45о.
Безопочная формовка применяется обычно при массовом производстве мелкого литья (массой до 5 кг).
В практике получения отливок безопочной формовкой на многих заво- дах в нашей стране и за рубежом нашли применение автоматические формо-
вочные линии изготовления безопочных форм с вертикальным разъемом по технологии Дисаматик. Такая технология обеспечивает: повышение выхода годного литья; снижение затрат на зачистку литья; снижение эксплуатацион- ных расходов; более эффективное использование формовочной смеси; повы- шение точности отливок; улучшение структуры отливок и повышение каче- ства поверхностей; экономия производственных площадей; улучшение усло- вий труда благодаря опыту ДИСА в литейном деле.
Линии Дисаматик компактны, удобны в эксплуатации.
На рис. 33 приведена схема изготовления безопочных форм с верти- кальным разъемом на линии Дисаматик мод. 2110 [5].
Рис. 33. Последовательность операций формовки:
1 – надув смеси; 2 – прессование смеси; 3 – отделение поворотной пресс-плиты; 4 – сборка форм и транспортировка стопки форм; 5 – отделение пресс-плиты; 6 – закрывание формо-
вочной камеры
Операции изготовления форм на линии происходят в следующей по-
61
следовательности:
1.Надув смеси – открывается шибер и с помощью сжатого воздуха смесь вдувается в формовочную камеру. Одновременно могут включаться вибраторы на пресс-плите и на поворотной пресс-плите.
2.Прессование смеси – поворотная пресс-плита и пресс-плита, осна- щенные модельными комплектами, движутся навстречу друг другу до дости- жения заданного давления. Одновременно включаются вибраторы. Давление прессования может регулироваться для получения форм необходимой проч- ности. Продолжительность прессования может быть увеличена для повыше- ния качества формовки при сложных моделях. При этом происходит вырав- нивание внутренних напряжений в форме пред вытяжкой модели.
3.Отделение поворотной пресс-плиты – поворотная пресс-плита мед- ленно отделяется от формы и откидывается в горизонтальное положение, от- крывая формовочную камеру. Во время вытяжки модели могут включаться вибраторы. На этой операции может производиться обдув поверхности фор- мы для удаления лишней смеси. Жесткая конструкция машины и точная вы- тяжка модели практически исключают разрыв даже при сложных моделях.
4.Сборка форм и транспортировка стопки форм – пресс-плита выталки- вает новую форму из камеры. Скорость движения формы непосредственно перед ее сборкой со стопкой замедляется. По достижении необходимого уси- лия сборки пресс-плита синхронно с автоматическим конвейером форм (АКФ) перемещает всю стопку вперед на величину толщины одной формы. Прецизионный ход пресс-плиты и специальная конструкция АКФ исключают возможность несогласованности и повреждения форм.
5.Отделение пресс-плиты – пресс-плита медленно отделяется и воз- вращается в исходное положение в формовочной камере. В это же время на обе модельные плиты наносится разделительная жидкость. В процессе отде- ления могут включаться вибраторы. Одновременно может производиться за- ливка предыдущей формы.
6.Закрывание формовочной камеры – поворотная пресс-плита повора-
чивается вниз и занимает исходное вертикальное положение в формовочной камере. Исходное положение может регулироваться, что позволяет отцентри- ровать пресс-плиты относительно пескодувной щели. Толщина формы может регулироваться в широких пределах для получения оптимального соотноше- ния между количеством смеси и металла.
Основные характеристики линии 2110 представлены в табл. 8.
На линии используют формовочную смесь следующего состава, % по массе:
оборотная смесь |
92,8-96,8 |
кварцевый песок |
3,0-6,0 |
бентонитовая глина |
0,4-1,0 |
Средний размер зерна наполнителя смеси определяется требованиями к качеству поверхности отливки.
62
Средний размер зерна 0,15-0,28 по DIN. Прочность на сжатие сырой смеси 0,13 МПа. Прочность на разрыв сырой смеси 0,02 МПа. Прочность на разрушение 0,03 МПа. Уплотняемость 40 ± 2 %.
Влажность подбирается для достижения уплотняемости 40 ± 2 %. Глиносодержание по AFS 11-13 %.
Содержание активной глины более 7 %. Потери при прокаливании 3,5-7,5 %. Летучие вещества 1,5-3,0 %.
Техническая характеристика линии 2110 |
Таблица 8 |
|
|
|
|
Параметр |
Норма |
|
Размер форм, мм: |
|
|
высота |
400 |
|
ширина |
500 |
|
толщина |
100-315 |
|
Давление прессования, МПа |
0-1,2 |
|
Максимальная длина конвейера, м |
47 |
|
Время охлаждения при толщине форм 200 мм и производитель- |
61 |
|
ности 205 форм/ч, мин |
|
|
Вакуумный способ изготовления литейных форм. Вакуумная формовка
(V-процесс) имеет ряд преимуществ по сравнению с технологией литья в ра- зовые песчано-глинистые формы: повышение качества отливок; резкое уменьшение расхода исходных материалов; снижение трудоемкости процесса формообразования; отсутствие связующего в формовочном материале. Ва-
куумирование формы в процессе заливки и охлаждения металла позволяет исключить выделение газов. Что улучшает условия труда, уменьшает загряз-
нение окружающей среды и способствует сокращению капитальных затрат и эксплуатационных расходов на вентиляцию производственных помещений.
Суть способа и последовательность операций иллюстрируются на рис. 34. Модельная плита 5 с закрепленной на ней моделью 2 смонтирована на вакуумной камере 1. Полость этой камеры соединена сквозными тонкими каналами 4 с поверхностью плиты и модели.
Синтетическую пленку 3 толщиной до 0,1 мм с площадью поверхности, равной площади модельной плиты на плане в течение нескольких секунд на- гревают до перевода ее в пластическое состояние. Нагретую пленку наклады- вают сверху на модель и подключают полость камеры 1 через патрубок 6 к вакуумному насосу. Пленка плотно облегает поверхность модельной плиты и модели, точно воспроизводя ее контур. На модельную плиту с пленкой уста- навливают коробчатую опоку 7, внутренняя стенка которой имеет отверстия 10. Опока через патрубок 11 соединена с вакуум-насосом. В нее засыпают ог-
63
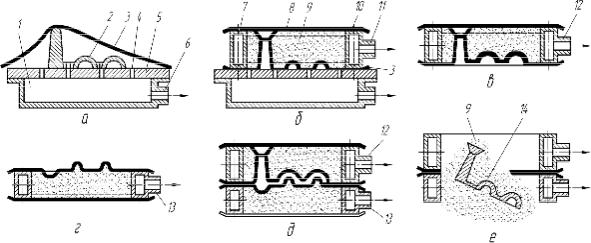
неупорный наполнитель 9, и модельную плиту вибрируют.
Далее отформовывают литниковую чашу и линейкой укладывают избы- ток песка из полуформы, выполняя ровный контрлад. На последний наклады- вают синтетическую пленку 8 (без нагрева) и подключают опоку к вакуумно- му насосу. Полуформа в результате вакуумирования приобретает необходи- мую прочность. Для съема полуформ с модельной плиты вакуумную камеру 1 отключают от вакуумного насоса. Верхнюю полуформу соединяют с нижней, которую изготавливают аналогичным способом. В процессе сборки полу- форм, заливки металлом и затвердевания отливки опоки подключены к ваку- ум-насосу. После затвердевания отливки 14 вакуум-насос отключают, и от- ливка вместе с песком вываливается из опок. Песок после охлаждения вновь используется для формовки. Уплотнение песка производится при вакууме по- рядка 50 кПа.
Рис. 34. Последовательность операций при вакуумно-пленочной формовке:
а – накладывание пленки на модельную плиту; б – изготовление верхней полуформы; в – верхняя полуформа; г – нижняя полуформа; д – форма в сборе; е – выбивка отливки; 1 – вакуумная камера; 2 – модель; 3 – пленка; 4 – отверстие в модельной плите; 5 – модельная плита; 6 – патрубок; 7 – коробчатая опока; 8 – пленка; 9 – наполнитель; 10 – отверстие в опоке; 11, 12, 13 – патрубки; 14 – отливка
На рис. 35 приведена схема линии вакуумной формовки Дисаматик.
Технология получения отливок на линии рассчитана на использование как низких, так и высоких моделей, поскольку толщина формы регулируется в за- висимости от размера модели. Модель может быть заменена в течение рабо- чего цикла. В зависимости от производственной необходимости можно изго-
тавливать большие и мелкие партии отливок из любого металла от стали до алюминия. Техническая характеристика линии приведена в табл. 9.
В состав линии входят следующие компоненты: формовочная машина 1; устройство для подачи модельных плит 2; стержнеукладчик 3; устройство для быстрой замены модельных плит 4; бункер для песка 5; вакуумная уста- новка 6; гидравлическая установка 7; установка для перемещения поддонов и
64
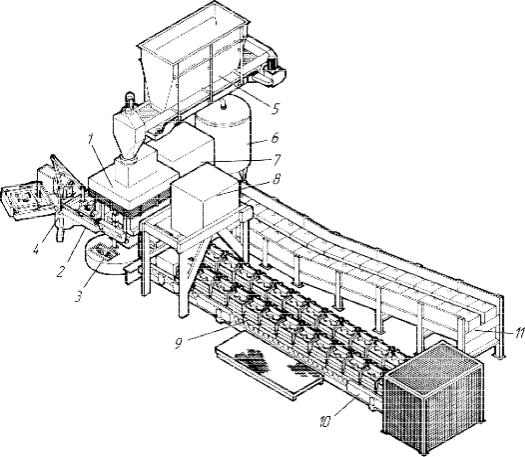
зажимов 8; зона заливки 9; линия заливки и охлаждения 10; конвейер охлаж- дения (двухдорожечный) 11.
Рис. 35. Схема линии вакуумной формовки Дисаматик:
1 – формовочная машина; 2 – устройство для подачи модельных плит; 3 – стержнеуклад- чик; 4 – устройство для быстрой замены модельных плит; 5 – бункер для песка; 6 – ваку- умная установка; 7 – гидравлическая установка; 8 – установка для перемещения поддонов и зажимов; 9 – зона заливки; 10 – линия заливки и охлаждения; 11 – конвейер охлаждения (двухдорожечный)
|
Таблица 9 |
|
Техническая характеристика линии вакуумной формовки Дисаматик |
||
Параметр |
Норма |
|
Размер форм, мм: |
|
|
длина |
720 |
|
ширина |
560 |
|
высота |
130/130-250/250 |
|
Производительность при высоте форм 150/150 мм, форм/ч |
165 |
|
Расход песка, м3/ч |
45 |
|
Расход воды для охлаждения при 15 оС, л/мин |
60 |
|
Конвейер форм: минимальная длина линии заливки и охлажде- |
12 |
|
ния, м |
|
|
|
|
|
Пластинчатый конвейер для длительного охлаждения отливок в |
48 |
|
форме: максимальная длина, м |
|
|
|
|
|
|
65 |
Материалы формы.
Наполнитель. Свойства формовочного материала определяют проч- ность форм и качество поверхности отливки. Главной особенностью формо- вочных материалов, используемых в вакуумно-пленочной формовке, является отсутствие в них связующего, поэтому огнеупорность формы зависит только от огнеупорности применяемого наполнителя. Прочность формы, полученной при разрежении, в значительной степени зависит от насыпной массы приме- няемого песка.
В свою очередь насыпная масса зависит от крупности песка, его типа (кварцевые, цирконовые и др.) и формы (угловатый или округлый), а также соотношения крупной и мелкой фракцией (табл. 10).
При использовании мелкого песка обеспечивается гладкая поверхность отливки (RZ = 18 мкм), более крупный песок имеет тенденцию к просечке
(табл. 11).
Зависимость насыпной массы песка от соотношения фракций |
Таблица 10 |
|||||||
|
|
|
||||||
Размер зерна 0,2 мм, % |
100 |
80 |
60 |
40 |
20 |
|
0 |
|
Размер зерна 0,05 мм, % |
0 |
20 |
40 |
60 |
80 |
|
100 |
|
Насыпная масса, кг/м3 |
1500 |
1700 |
1700 |
1600 |
1420 |
|
1230 |
|
Примечание. Максимальная насыпная масса 1800 кг/м3 получена при соотношении крупная фракция – мелкая фракция 70:30.
Влияние зернистости песка на параметры шероховатости отливки |
Таблица 11 |
|||||
|
|
|||||
Песок кварцевый с разме- |
Значение RZ, мкм, при толщине образца, мм |
|
||||
ром песчинок, мм |
3 |
6 |
12 |
|
24 |
|
0,315 |
просечка |
просечка |
просечка |
|
просечка |
|
0,160 |
то же |
то же |
то же |
|
то же |
|
0,063 |
50 |
50 |
« « |
|
« « |
|
смешанный |
18 |
18 |
18 |
|
25 |
|
Примечание. Степень разряжения 47 кПа. Пленка EVA толщиной 0,075 мкм.
Герметизирующие покрытия. В качестве материала для герметизации форм используются синтетическая пленка, фольга, бумага или самотвердею- щие композиты. Чаще всего применяется синтетическая пленка.
На этапе наложения на модель к пленке предъявляются следующие тре- бования: плотное прилегание нагретой пленки к модели; отсутствие разры- вов; малая зависимость пластичности пленки от длительности ее нагрева.
На этапе заливки формы требуются: малая термическая усадка пленки при контакте с нагретым жидким металлом (сжимающаяся пленка не должна обнажать слишком большой участок формы, на котором зерна песка удержи-
66
ваются только за счет вакуумирования); медленное протекание процессов де- струкции пленки при минимальной толщине слоя песка, в который проника- ют продукты деструкции (во избежание образования пригара и попадания в отливку включений песка); незначительное выделение газов в атмосферу це- ха; малая стоимость пленки.
Применяются пленки из различных синтетических материалов – поли- этилена низкой плотности (РЕ-пленка ГОСТ 10354-82), полипропилена (РР- пленка), полистирола (РS-плернка) и этилвинилацетата (EVA-пленка).
EVA-пленка имеет наиболее высокие показатели удлинения, пластиче- ской деформации, обладает способностью к деформированию и образованию складок, однако требует для деформирования определенных усилий. По сово- купности свойств EVA-пленка наиболее пригодна для использования при ва- куумно-пленочной формовке.
Огнеупорные покрытия. В качестве огнеупорного покрытия использу- ются графит, тальк, каолин, циркон, алюминиевая пудра, в качестве жидкой фазы – растворители и компоненты, которые не вступают в химическую ре- акцию с пленкой, метанол, изопропанол и этанол. Водные покрытия не ис- пользуются, так как они на пленке высыхают долго и не смачивают ее. При применении метанола и изопропанола требуются более жесткие правила тех- ники безопасности, чем при работе с этанолом; последний более перспекти- вен, хотя и дороже.
Краски большей частью наносят на пленку, покрывающую модель. В отдельных случаях красят поверхность формы после съема модели. При этом краска и песок разделены пленкой.
Контрольные вопросы.
1.Преимущества получения отливок на автоматических формовочных линиях (АФЛ) в сравнении с ручной формовкой.
2.Перечислите последовательность операции изготовления отливок на линии безопочной формовки.
3.Перечислите последовательность операции изготовления отливок на линии вакуумной формовки.
4.Обозначьте требования к формовочным смесям для автоматических формовочных линий.
5.Укажите преимущества вакуумной формовки в сравнении с формов- кой в ПГ-формах.
6.Укажите требования к модельной оснастке для АФЛ.
7.Какие материалы используют при вакуумной формовке?
8.Отметьте особенности заполнения форм расплавом при вакуумной формовке.
9.При каком из способе формовке (безопочная, опочная) применяется окрашивание форм?
67
10.При каких условиях производства применяют безопочную формов- ку?
ЛЕКЦИЯ 8.
ТЕМА: ТЕХНОЛОГИЧЕСКИЕ ПРОЦЕССЫ ИЗГОТОВЛЕНИЯ СТЕРЖНЕЙ
План лекции
1.Классификация процессов.
2.Уплотнение стержневой смеси.
3.Современные технологии изготовления стержней.
Классификация технологических процессов. Технологические процессы изготовления стержней делят на две группы. Первая группа включает в себя традиционные процессы, давно применяемые в литейных цехах. Они харак- теризуются отверждением стержней вне оснастки, как правило, с помощью тепловой сушки. Первоначальная прочность стержней достигается повышен- ной сырой прочностью стержневых смесей, высокой степенью уплотнения стержней, а также применением металлических каркасов.
Вторая группа процессов обеспечивает отверждение стержней непо- средственно в оснастке в основном за счет химического или физико- химического упрочнения материалов, входящих в состав стержневых смесей. К этой группе относятся процессы, основанные на использовании самотвер- деющих смесей или смесей, твердеющих при продувке газом-отвердителем в нагреваемой оснастке, а также процессы, основанные на использовании стержневых смесей, затвердевающих под воздействием теплоты нагреваемой оснастки.
Классификация технологических процессов изготовления стержней приведена на рис. 36.
Каждый технологический процесс имеет свою оптимальную область применения, поэтому выбор оптимального технологического процесса изго-
товления стержней представляет собой сложную задачу и связан с глубоким техническим и экономическим анализом большого числа факторов.
Традиционные технологические процессы с отверждением стержней вне оснастки. При этих процессах после уплотнения смеси и извлечения стержней из оснастки стержни сушат при 150-250 оС в сушилах в течение 1,5- 2,5 часа и более. При этом ряд стержневых смесей позволяет производить кратковременную сушку при повышенной температуре в сушиле, а также сушку в электрическом поле высокой частоты. Кроме того, некоторые стерж- ни изготовляются без отверждения. Такие стержни называют сырыми, анало- гично технологии изготовления форм по-сырому. Прочность таких стержней
68
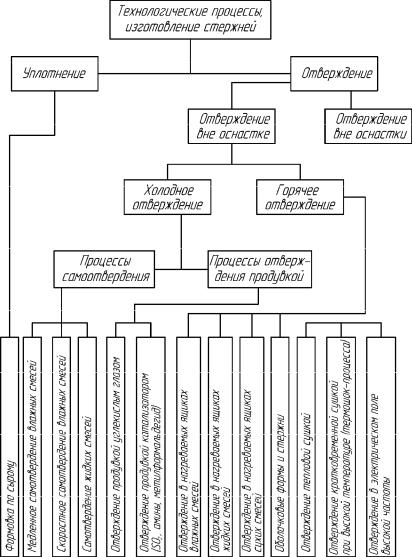
достигается лишь за счет высокой сырой прочности смесей, каркасов и высо- кой степени уплотнения.
Рис. 36. Классификация технологических процессов изготовления стержней
Технологические процессы, основанные на отверждении стержней в оснастке, обеспечивают отверждение стержней непосредственно в стержне- вых ящиках. При этом отверждение могут производиться или в предвари- тельно нагретой до необходимой температуры оснастке, или в холодной ос- настке, имеющей температуру окружающей среды.
Процессы изготовления стержней в нагреваемой оснастке подразделяют на процессы изготовления стержней из влажных и сухих (обычно песчано- смоляных), жидких и плакированных смесей. Плакированные стержневые смеси используют для формовки оболочковых стержней.
Технологические процессы изготовления стержней в холодной оснастке
69
делят на две группы. К первой группе относят процессы с использованием самотвердеющих смесей, а ко второй – процессы, основанные на отвержде- нии смеси в оснастке при их продувке. Процессы с использованием само-
твердеющих смесей подразделяют на процессы изготовления стержней из сыпучих смесей с нормальной и повышенной скоростями самозатвердевания, а также на процессы изготовления стержней из ЖСС. Отверждение смесей за счет продувки может осуществляться углекислым газом, газообразным ката- лизатором и сжатым воздухом (подогретым или с нормальной температурой).
Все процессы изготовления стержней включают в себя различные тех- нологические (рис. 37), транспортные и вспомогательные операции, из кото- рых часть операций характерна для всех технологических процессов, а часть специфична для отдельных вариантов технологических процессов изготовле- ния стержней.
Уплотнение стержневой смеси. Необходимая прочность стержней дос- тигается уплотнением смеси в стержневом ящике. Чем больше уплотняющее воздействие, тем выше прочность стержней в сыром состоянии. Особенное значение степень уплотнения стержней приобретает при использовании тра- диционных технологических процессов изготовления стержней: В этом слу- чае прочность стержней в сыром состоянии должна быть достаточной для то- го, чтобы при транспортировке и сушке стержни не деформировались и не разрушались. При недостаточном и неравномерном уплотнении снижается прочность всего стержня или его отдельных мест, образуются пористые, рых- лые участки, в результате чего ухудшается качество поверхности отливки, образуются пригар и песчаные раковины.
Неравномерность уплотнения стержней может привести также к их рас- трескиванию во время сушки в результате возникающих при этом термиче- ских напряжений. С другой стороны, нельзя переуплотнять стержни, так как могут значительно уменьшиться податливость стержней и их газопроницае- мость, что повышает опасность появления горячих трещин и газовых раковин в отливках. Степень уплотнения смеси характеризуется ее плотностью. На- сыпная плотность стержневой смеси составляет 900-1100 кг/см3, а после уп- лотнения 1450-1650 кг/см3.
Уплотнение стержневой смеси в ящиках производят вручную, вибраци- ей, встряхиванием, прессованием, пескометным, пескодувным и другими способами.
Ручное уплотнение стержней. Уплотнение смеси производят плоской ручной трамбовкой, с помощью клиновидной набойки, пневматической трам- бовкой с плоским или клиновидным наконечником, ладонью.
Последовательность основных операций при изготовлении стержней вручную в стержневых ящиках:
-в вытряхном ящике с вкладышем (рис. 38): устанавливают вкладыши
иобдувают рабочую полость ящика; ящик наполняют смесью, которую уп- лотняют трамбовками или набойками; выбивают каркасы и производят про-
70