
технология литейного производства
.pdfПри пескодувно-прессовом уплотнении (рис. 19, д) весь процесс осуще- ствляется в два этапа. Сначала в полость 1, заключенную между вертикально расположенными модельными плитами 2 и 3, формовочная смесь 4 подается пескодувным методом с помощью воздушного давления, предварительно уп- лотняясь. Затем модельная плита 3 подается поршнем влево, прессуя смесь. По окончании прессования плита 2 сначала отходит влево, затем разворачи- вается вверх, занимая положение, показанное штрихпунктиром на рисунке. Ком смеси модельной плитой 3 подается влево до упора в предыдущий ком 5, плотно прилегая к ранее изготовленным формам, после чего все формы пере- двигаются влево к заливочной установке. Весь процесс от уплотнения смеси до заливки металлом автоматизирован. Производительность автоматизиро- ванной формовочной линии составляет 360 форм в час и более (при наличии стержней – 300 форм в час).
При гравитационном уплотнении (рис. 19, е) смесь поднимается на оп- ределенную высоту в бункер 1, из которого через шибер 2 попадает в дозатор 3. Благодаря быстрому открыванию дна дозатора 4 смесь в виде компактного кома по шахте 5 свободно попадает в опоку или стержневой ящик 6. Уплот- нения только гравитационным способом недостаточно. Поэтому для доуп- лотнения применяют подпрессовку усилием (5-10)×105 Па (гравитационно- прессовый способ) или вибрацию (гравитационно-вибрационный способ).
При единичном и мелкосерийном производстве крупных отливок для уплотнения форм используют пескометный способ (рис. 19, ж). Формовочная
смесь ленточным транспортером подается на быстро вращающийся ротор с ковшом. Последний, захватывая смесь, бросает ее в опоку, установленную на модельной плите (или в стержневой ящик), производя, таким образом, уплот- нение. Пес кометная головка может перемещаться в горизонтальной плоско- сти. Управление пескометом осуществляется оператором, наблюдающим од- новременно за процессом наполнения опоки. Производительность пескометов колеблется от 6 до 50 м3/час уплотненной формовочной смеси.
При изготовлении форм импульсным методом (рис. 19, з) на модельную плиту 1 с вентами 2 (тонкие отверстия, через которые проходит воздух, но не проходит смесь) устанавливаются опока 3 и наполнительная рамка 4, после чего они заполняются формовочной смесью. Над наполнительной рамкой ус- танавливается импульсная головка 5, и вся оснастка прижимается друг к дру- гу (герметизируется). Из специальной магистрали 6 в ресивер 7 головки по- ступает сжатый воздух. При уплотнении запорный клапан 8 поднимается вверх, пропуская сжатый воздух через отверстие 9 в полость 10. Из полости 10 через отверстия 11 воздух устремляется в полость прессования 12, уплот- няя смесь 13. Пройдя через смесь, воздух уходит в атмосферу через венты 2.
При этом давление над смесью от максимального падает до атмосферного за доли секунды. Под действием сжатого воздуха смесь наполнительной рамки перемещается в опоку и уплотняется. Уплотнение производится однократным
41
импульсом.
Разновидностью импульсного воздушного уплотнения является уплот- нение взрывом. С этой целью вместо воздуха в импульсную головку, содер- жащую взрывное устройство, подается взрывчатая смесь, которая в нужный момент взрывается. Продукты взрыва направляются к формовочной смеси, уплотняя ее аналогично воздушному импульсу.
Операции при изготовлении стержней могут быть следующими. Снача- ла стержневой ящик частично заполняется смесью, слегка уплотняется, затем в него устанавливают металлическую арматуру – каркасы, необходимые для придания стержню манипуляторной прочности. После очистки излишков смеси для улучшения вентиляции стержень прокалывают душником. Если стержень подвергается сушке (связующие – формовочная глина, раститель- ные масла или другие материалы), то его извлекают из стержневого ящика, устанавливают на сушильной плите и помещают в сушило, где производят сушку с целью его упрочнения. Иногда (хотя сравнительно редко) стержни устанавливаются в форму без сушки, сырыми. Если же связующее – жидкое стекло, то стержень, подвергается продувке углекислым газом или другими реагентами. При использовании жидких самотвердеющих смесей (ЖСС) смесь в стержневом ящике выдерживается, пока прочность не достигнет не- обходимого значения. Сложные стержни изготавливают из двух и более час- тей, которые впоследствии склеивают между собой. Большую часть литейных стержней изготавливают различными машинными способами. Основные ти- пы стержневых машин: встряхивающие с поворотным столом, встряхиваю- щие с перекидным столом, вибропрессовые, мундштучные, пескодувные и пескострельные машины. Первые три типа не отличаются от машин для изго- товления форм. При изготовлении стержней на этих машинах вместо модель- ных плит и опок устанавливают стержневые ящики.
В мундштучных машинах стержневой ящик заменен сменной гильзой- мундштуком, сечение которого определяет сечение стержня. Стержень любой
длины получают выдавливанием через калиброванный мундштук машины уплотненной смеси. Уплотнение производится при возвратно-поступательном движении поршня машины или шнеком.
Схемы пескодувных и пескострельных машин представлены на рис. 20. К надувной плите снизу пневмопоршнем поднимается стержневой ящик. Ра- бочее давление воздуха составляет (5-10)×105 Па. В случае пескодувной ма- шины (рис. 20, а), сжатый воздух 1 подается на верхнюю поверхность стерж- невой смеси 2, находящийся в резервуаре 3. Смесь вместе с воздухом через вдувные отверстия 4 надувной плиты 5 машины попадает в полость стержне- вого ящика 6. Воздух через венты 7 уходит в атмосферу цеха. В пескострель- ный резервуар (рис. 20, б) вмонтирована специальная гильза 1 с щелевыми отверстиями 2, 3, вертикальными в нижней части и горизонтальными в верх- ней. Через эти отверстия воздух из ресивера в момент выстрела с большой скоростью устремляется в резервуар со смесью, выталкивая ее в полость
42
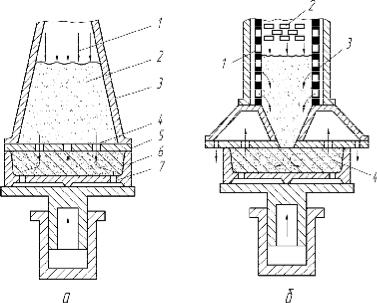
стержневого ящика 4. Стержни могут отверждаться сушкой в сушилах или непосредственно в стержневых ящиках после уплотнения. В этом случае
стержневые ящики могут быть холодными или нагреваться электрическим током или газом. В обоих случаях в качестве связующего используются син- тетические смолы. Однако при горячем отверждении основным активатором отверждения является тепло, при холодном только катализаторы отвержде- ния. Последние могут быть введены в смесь при ее приготовлении (так назы- ваемые ХТС – холодно твердеющие смеси) или после уплотнения смеси в стержневом ящике путем продувки газообразными катализаторами.
Рис. 20. Схемы пескодувной (а) и пескострельной (б)
машин для изготовления стержней
Для изготовления мелких отливок применяется безопочная формовка.
Она производится на встряхивающих машинах с допрессовкой в съемных опоках, изготовленных из легких сплавов.
Машинная формовка широко внедряется в практику работы литейных цехов не только массового и крупносерийного производства, но также мелко- серийного и даже единичного. До недавнего времени это сдерживалось в ос- новном из-за необходимости частой смены модельных плит и настройки формовочных машин при переходе на другую модельную плиту. Сейчас это
затруднение ликвидировано в связи с применением координатных модельных плит и унификацией опок.
Координатная модельная плита (рис. 21) в отличие от обычных имеет базовые отверстия для фиксации и крепления моделей. Эти отверстия распо- ложены так, что образуют сетку с равными расстояниями между осями. Для установки на эти плиты моделей по заранее определенным координатам каж-
43
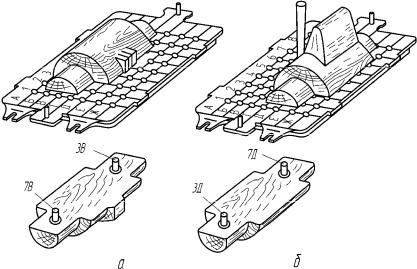
дое базовое отверстие имеет свой шифр.
На рис. 21 показаны горизонтальные оси, обозначенные цифрами, и вертикальные оси, обозначенные буквами. Тогда крайнее левое отверстие на изображенных плитах получает шифр А1, отверстие ниже его имеет шифр Б1 и т.д.
Рис. 21. Монтаж моделей на координатной плите: а – монтаж модели «низа»; б – монтаж модели «верха»
Половинки моделей, показанные на рис. 21 монтируются штифтами 3В и 7В на нижней плите, и штифтами 3Д и 7Д – на верхней.
Значительный эффект от применения машинной формовки в условиях единичного производства дает также использование быстросменных модель- ных плит (рис. 22).
Такая плита имеет рамку 1 с гнездами 5, в которых могут устанавли- ваться сменные модели 2, прикрепленные к модельным плитам-вставкам 3. Эти вставки укрепляются в общей рамке при помощи винтовых прижимов 4.
Таким образом, на модельной плите могут быть смонтированы модели для нескольких отливок. Установка такого сборного модельного комплекта занимает очень мало времени (1-2 мин), поэтому этот способ формовки ста-
новится достаточно экономичным и оправдывает себя при изготовлении даже очень мелкой партии отливок (10-20 штук).
Формовочные машины предназначены не только для механизации про- цесса уплотнения формовочной смеси, но и для извлечения моделей из уп- лотненных опок. Удаление моделей из полуформ осуществляется нескольки- ми способами.
На рис. 23 показана схема машины со штифтовым съемом. При ходе вверх четырех штифтов 4, расположенных по углам опоки 1, уплотненная по- луформа снимается с модельной плиты 3, прикрепленной к столу 5 формо-
44
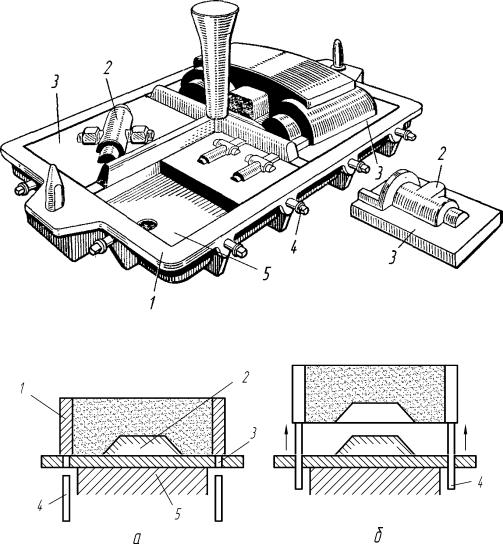
вочной машины. На рис. 23, а показано положение штифтов до съема, а на рис. 23, б после съема полуформы.
Рис. 22. Быстросменные модельные плиты
Рис. 23. Штифтовый съем опок плиты
Для прохода штифтов в модельной плите имеются специальные отвер- стия или вырезы. Отделение модели 2 от формы на машинах со штифтовым
съемом опок применяется только при формовке простых и невысоких моделей с пологими боковыми поверхностями, так как кромки глубоких полостей при съеме опоки легко могут обвалиться.
Отделение высоких моделей или моделей с вертикальными стенками производится на машинах с протяжными плитами (рис. 24, а). Модель 1 опускается вместе с опускным столом 2, а заформованная опока остается на протяжной плите 3. Существуют конструкции машин (рис. 24, б), при кото- рых стол машины 2 с модельной плитой и моделью 1 остается неподвижным,
45
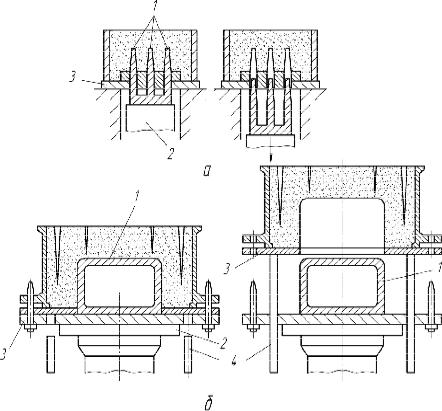
а протяжная плита 3 с установленной на ней опокой поднимается вверх при помощи штифтов 4. Протяжная плита предотвращает опасность обвала смеси в форме.
Рис. 24. Формовочная машина с протяжной плитой
При изготовлении форм с массивными земляными «выступами» и при
формовке нижних опок отделение модели от формы обычно производится на машинах с поворотной плитой или перекидным столом (рис. 25). При фор- мовке на этих машинах перед отделением модели 2 от формы опока 1 пово- рачивается на 180о и опускается на приемное устройство, которое в поворот- ных машинах находится непосредственно под плитой, а у перекидных – вы- несено в сторону.
В литейных цехах большое распространение получили литейные кон- вейеры, объединяющие в единый производственный поток ряд операций, вы-
полняемых на машинах и установках с различной степенью механизации
(рис. 26).
Литейный конвейер представляет собой множество платформ 9, непре- рывно движущихся по рельсам 10 при помощи тяговой замкнутой цепи, при- водимой в движение от приводной станции 8. Литейные формы 4 со сбороч- ных рольгангов 5, примыкающих к формовочному участку, передаются в за-
46
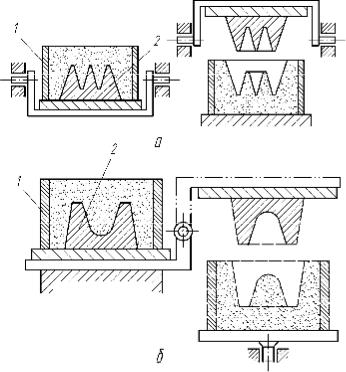
ливочное отделение. Заливка производится рабочим, находящимся на дви- жущейся платформе 1, при помощи наклона разливочного ковша 2, который поступает из плавильного отделения по монорельсу 3. Формы, залитые ме- таллом, движутся под охладительный кожух 7 и после остывания – на выбив- ную решетку 6. Выбитые отливки проваливаются в люк выбивной решетки и пластинчатым транспортером передаются в обрубное отделение. Выбитая из опок формовочная смесь проваливается через решетку на ленточный транс- портер и, пройдя сепарацию, подается в смесеприготовительное отделение.
Освобожденные опоки возвращаются на участок формовки для повторного использования.
Рис. 25. Машины с поворотной плитой (а)
ис перекидным столом (б)
Влитейных цехах нашли применение автоматические формовочные линии, на которых изготовление форм происходит без участия человека, а только под его контролем и наблюдением. На рис. 27 показана принципиаль- ная схема такой линии.
Влинию вмонтированы формовочные автоматы 3 и 5, на которых фор-
муются соответственно нижняя и верхняя полуформы. При помощи кантова- теля 4 нижние полуформы поворачиваются на 180о и передаются на транс- портерную линию 7 для установки стержней.
Сборка нижней и верхней полуформ производится механизмом 8, после чего готовые к заливке формы подаются на заливочный конвейер 9 (на рис. 27
47
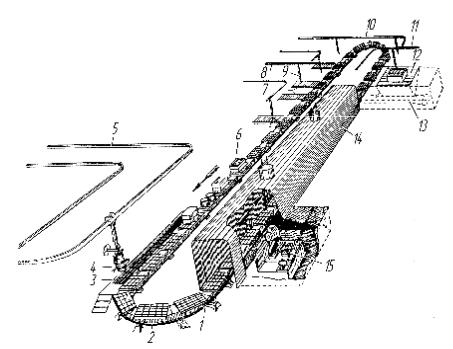
показана только его часть). Для скрепления полуформ на них накладываются грузы, а затем собранные формы подаются последовательно на заливочный участок, в зону охлаждения, на позицию 10 для удаления сплесков металла и на автоматическую выбивную установку 11.
Рис. 26. Литейный конвейер:
1 – заливочная площадка; 2 – заливочный ковш; 3 – монорельс; 4 – форма; 5 – формовоч- ные машины; 6 – рольганги; 7 – пневматический подъемник; 8 – выбивная решетка; 9 – транспортер; 10 – охладительная камера; 11 – привод; 12 – тележки; 13 – рельсы
Всовременных линиях перекладка грузов, скрепляющих полуформы, с
охладительной зоны конвейера на зону сборки осуществляется автоматически при помощи специальных механизмов грузоукладчиков.
Освобождающиеся после выбивки опоки механизмом съема и распаров- ки 12 разделяются на два потока: нижние опоки передаются на линию 13, а верхние – на линию 6. В дальнейшем процессы повторяются по описанной выше схеме.
Формовочная смесь, необходимая для изготовления полуформ, из сме- сеприготовительного отделения при помощи транспортерной ленты 1 подает- ся к бункерам с дозаторами 2, установленным над формовочными автомата- ми.
Учитывая повышенные требования, предъявляемые к формовочным смесям, применяемым на автоматизированных установках, многие формо- вочные линии изготавливаются совместно со смесеприготовительными уста- новками.
Всовременных литейных цехах осуществляются принципы комплекс-
48
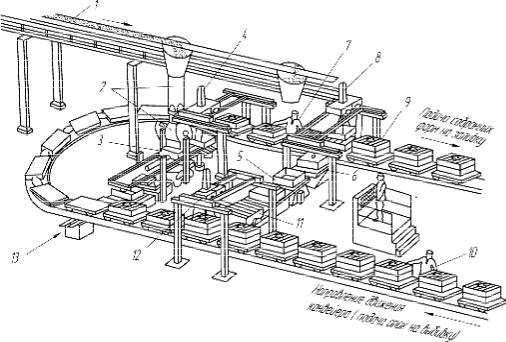
ной автоматизации. С этой целью автоматические формовочные линии объе- диняются с блок-линиями для изготовления стержней, автоматическими ли- ниями для заливки и выбивки форм, поточными линиями для очистки, зачи- стки и окраски форм.
Рис. 27. Автоматическая формовочная линия:
1 – транспортерная лента; 2 – бункер с дозатором; 3 – формовочный автомат нижних опок; 4 – механизм кантователя и подаватель нижних опок; 5 – формовочный автомат верхних опок; 6 – линия верхних опок; 7 – установка стержней; 8 – механизм сборки форм; 9 – заливочный конвейер; 10 – удаление сплесков металла; 11 – автоматическая выбивная установка; 12 – механизм съема и распаровки опок; 13 – линия нижних опок
Для обеспечения надежных связей между отдельными агрегатами, вхо- дящими в состав автоматических линий, предусматриваются соответствую- щие накопители для опок, готовых форм и др.
Внедрение автоматизации в литейном производстве ликвидирует тяже- лый ручной труд, позволяет значительно улучшить условия труда и общее санитарно-гигиеническое состояние цеха.
Контрольные вопросы.
1.В чем заключается преимущество машинной формовки перед ручны- ми способами изготовления форм?
2.По каким признакам классифицируют формовочные машины?
3.Какие существуют методы уплотнения смесей при машинной фор-
49
мовке?
4.Дайте сравнительную характеристику способам уплотнения смесей при машинной формовке.
5.Назовите способы извлечения моделей из полуформ и укажите об- ласть их применения.
6.Дайте сравнительную характеристику способам извлечения моделей из полуформ.
7.В чем заключаются специфические особенности технологического процесса машинного изготовления опочных и безопочных форм?
8.Назовите преимущества машинной формовки с использованием са- мотвердеющих смесей.
ЛЕКЦИЯ 6.
ТЕМА: ПОЛУЧЕНИЕ ОТЛИВОК ПО ГАЗИФИЦИРУЕМЫМ МОДЕЛЯМ
План лекции
1.Характеристика способа.
2.Изготовление моделей и форм.
3.Влияние технологических факторов на качество отливок.
При получении отливок в формах по газифицируемым моделям исполь- зуется разовая модельная оснастка, изготовленная из вспененного полистиро- ла – пенополистирола с плотностью до 10 кг/м3.
Перед заливкой металла такие модели выжигают, после чего образуется оболочковая форма, перед заливкой ее прокаливают.
Достоинством данного процесса является снижение трудоемкости на этапах изготовления моделей, форм, обрубки и выбивки, сокращение цикла производства отливок, расширение возможностей механизации и автоматиза- ции.
В условиях единичного и мелкосерийного производства экономия дос- тигается в результате: снижения трудоемкости изготовления модельного
комплекта благодаря ликвидации стержневых ящиков и более легкой по сравнению с деревом обрабатываемости пенополистирола; снижения трудо- емкости изготовления форм благодаря отсутствию операций извлечения мо- делей, изготовления стержней, сборки форм и их отделки; снижения трудо- емкости на операции обрубки благодаря отсутствию заливов; ликвидации брака по перекосам благодаря отсутствию в форме разъемов; понижения рас- хода жидкого металла благодаря отсутствию литейных уклонов; сокращения
цеховых грузопотоков благодаря малой массе моделей и возможности их ручной транспортировки.
50